注塑模具设计资料荟萃-注塑模八腔浇注系统平衡研究
注塑模具设计:第二章:浇注系统

第二章浇注系统注塑机喷嘴中熔融的塑料,经过主流道,分流道,最后通过浇口进入到模具型腔,然后经过冷却固化,得到所需要的制品。
所以注塑模具的浇注系统是指从注塑机喷嘴到型腔为止的塑料熔体的流动通道。
因为热塑性塑料的热传导率较低,流道中冷凝的表皮对芯部熔融的塑料祈祷保温作用,所以保证了流道芯部的塑料继续流动。
来自熔融的塑料的热加上由于流动摩擦二产生的摩擦热等于高温塑料与低温模具热交换所产生的热损失。
如果增加注射速度,冷凝层由于受到流动产生的高摩擦热而会变薄。
即:高速注射与低速注射对于冷凝层厚度影响的差别是比较明显的。
这就是为什么高压、高速注射容易将型腔填充饱满的主要原因之一。
浇注系统的型制与流动性为减少与热量的损失,必须使流道的表面积与体积之比保持最小,因为具有最小表面积与最大体积的形状是圆柱形,所以圆柱形是最优越的流道形状。
主流道从注射机喷嘴到分浇为止的熔融塑料的流动通道。
1)定模部分由整体构成2)定模部分由两块模板所构成3)最普遍常用的主流道结构,是以浇口套的形式镶入模板中,为防止被喷嘴撞伤,采取淬火处理主流道的基本尺寸取决于两个方面:1,塑料的种类,所成型的制品质量和壁厚大小。
2与注射机喷嘴的几何参数有关。
浇口套的求半径比喷嘴的球半径大2~5mm,脱模斜度一般最小不低于1°,最大不超过4°。
因为,主流道的脱模斜度不能过大,否则在注塑时会产生涡流和流速过慢等现象主流道应保持光滑的表面,避免留有影响塑料流动或脱模的尖角毛刺等。
而且在主流道的末端还应设置冷料井以防止制品中出现固化的冷料(最先流入模具的塑料)。
设置冷料井,以便将这部分冷料存留起来。
这一点对分流道也同样重要。
分流道分流道可以理解为从主流道末端开始到浇口为止的塑料熔体的流动通道。
鉴于圆形截面的浇道必须设置在以分型面为界的动、定模两部分,所以对制造工艺要求较高,且启模时,分流道中经过冷却固化的塑料留在动、定模内是随机的。
所以实际制造中,U 性截面分流道或梯形截面的分流道比较常用,虽然热量损失较大一点,但加工制造比较简单,并且启模时,冷料留在动定模哪一部分,将是确定的。
基于知识的注塑模浇注系统的研究与开发浇道设计
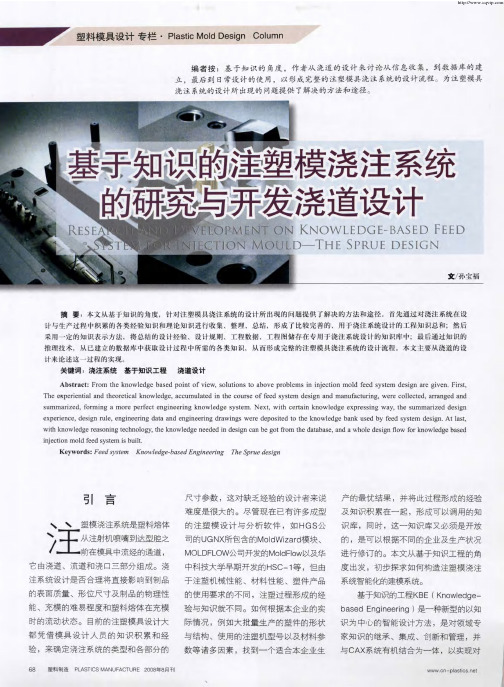
。
浇
中科 技 大 学 早 期 开 发 的 H S
于 注 塑 机 械性 能
、
C
一
1等
、
但由
度 出发
,
初步探求如何 构造 注 塑模浇注
。
! 设 计 是 否 合 理 将直 接 影 响 到 制 品
材料性能
,
塑件产 品
系统 智能 化 的建 模 系统
f质 量
、
形 位 尺 寸及 制 品 的物 理 性
的使 用要 求的不 同 验 与知识 就不 同
、
司 的 U G N X 所 包 含 的 M o l d W iz
d
w
模块
、
的
,
是 可 以根 据 不 同 的 企 业 及 生 产 状 况
。
,
M O L D F L O W 公 司 开 发 的 M o ld F Io
以及 华
,
进 行 修订 的
本文从基于 知识 工 程 的 角
流道和 浇 口 三
部分 组 成
in g k g in
le dg
e w
s
y
s te m
.
N
t,
ith
c e rt a
le dg e le dg
s e
,
pre k
w
s s
w
a
y
,
the
s
s u m m a r m
ized dFra biblioteke s ig n
.
3e r ie n c e
d e s ig n
le
,
e n
g in
c
e e r in o
g da t a
注塑模八腔浇注系统平衡研究.pdf

3. 3. 1 AB0 段某点体积流量模型 在 AB0 段 ,熔体的损失只有内剪应力导致的流
程损失 ,其损失值计算如下 : 如图 4 所示 ,运用一维流体模型先分析流体流
2) 非自然平衡式浇注系统的特点 :分流道 、浇 口的形状及尺寸各不相同 ,型腔的尺寸和诸型腔到 主流道的距离也可能各不相同 ,在这种系统里 ,如 果各个型腔不能同时被充满 ,就很难得到尺寸精确
收稿日期 :2003 - 09 - 25 作者简介 :刘锦平 (1974 - ) ,男 ,江西高安人 ,讲师 ,硕士 ,研究方向 :塑料模具 CAD/ CAM.
在注射模的设计过程中 ,一维模型可用作为 : ①求出最佳的工艺参数 ; ②型腔中的流道平衡 ; ③ 流道中的流动平衡 ; ④确定流道系统的尺寸等. 本 课题选择一维流动模型进行分析计算. 3. 3 公式推导
已知条件 : ①各分流道长度 ②第一级分流道的 半径 ③流体进入浇注系统时的体积流量 ④塑料的 各性能参数.
1
n
-
v1C- n)
(20)
熔体流经 B1 C 段和 B2 EF 段的时间相等 , 可得
等式 :
t2 = t0 + t1
(21)
由式 (15) 、(18) 、(20) 、(21) 确定两第二级分流
道半径的关系如下 :
vB1
-
1
n-
R21 -
v1C -
n
n
=
v1E0-
nR20 -
vB1
-
2
n
n
+
塑料件模具设计--浇注系统设计

(6)轮辐式浇口
轮辐式浇口的适用范围类似 于盘形浇口,带有矩形内 孔的塑件也适用,但是它 将整个周边进料改成了几 小段直线进料。这种浇口 切除方便,流道凝料少, 型芯上部得到定位而增加 了型芯的稳定性。
31
(7)护耳式浇口
它在型腔侧面开设耳槽,熔体通过浇口冲击在 耳槽侧面上,经调整方向和速度后再进入型 腔,因此可以防止喷射现象,是一种典型的 冲击性浇口,它可减少浇口附近的内应力, 对于流动性差的塑料极为有效,浇口应设置 在塑件的厚壁处。
这种浇口的去除比较 困难,痕迹大
32
(8)点浇口
点浇口又称针点浇口或菱形浇口,是一 种截面尺寸很小的浇口,俗称小浇口。 这类浇口由于前后两端存在较大的压力 差,能较大地增大塑料熔体的剪切速率 并产生较大的剪切热,从而导致熔体的 表观粘度下降,流动性增加,有利于型 腔的充填。
33
(8)点浇口的设计形式
图a所示为直接式,直径为d的圆锥形的小端直接与塑件相 连。
图b所示为圆锥形的小端有一段直径为d、长度为l的点浇口 与塑件相连。这种形式的浇口直径d不能太小,浇口长度l 不能大长,否则脱模时浇口凝料会断裂而堵塞住浇口,影 响注射的正常进行。上述两种形式的点浇口制造方便,但 去除浇口时容易相伤塑件,浇口也容易磨损,仅适于批量 不大的塑件成型和流动性好的塑料。
非限制性浇口是整个浇口系统中截面尺寸最大的部位,它主 要对中大型筒类、壳类塑件型腔起引料和进料后的施压作用。
21
1、浇口的类型
(1)直接浇口(又称主流道形浇口)
在单型腔模中,熔体直接流入型腔,因 而压力损失小,进料速度快,成型比 较容易,对各种塑料都能适用。它传 递压力好,保压补缩作用强,模具结 构简单紧凑,制造方便。
多型腔热流道注射模的浇注平衡分析

多型腔热流道注射模的浇注平衡分析作者:上海克朗宁技术设备有限公司王建华来源:现代塑料在一模多腔的注塑成型中,保持塑料熔体在浇注系统中的流动平衡性十分重要。
这直接影响到各型腔的填充时间、注射和保压压力,以至体积收缩率的均衡性,进而影响产品的质量。
然而,对于冷流道模具的热流道改造,由于模具的模板尺寸、型腔布置和浇口位置都已经固定,要实现自然的平衡流道系统设计已不可行。
因此,流道设计仍考虑为非平衡式流道布置,但这又势必会影响产品的质量。
如何在这种流道系统的设计中实现平衡浇注对于模具制造商而言非常关键。
近年来,许多模具制造商开始应用热流道技术,并在模具设计中预先使用Moldflow软件进行模拟分析,极大地提高了模具设计的效率和准确性。
本文以克朗宁公司改造一具拥有18模腔的瓶盖热流道注射模为例,深入分析了Moldflow 软件在优化流道设计,尤其是改善浇注平衡方面的应用。
针对该注射模从主流道到各型腔的流道长度均不相等的特点,克朗宁公司通过利用Moldflow软件优化流程中各段流道的直径,使塑料熔体从主流道进入各型腔的压力降保持相等,从而保证了熔体能够同一时间充满各型腔,实现了各个型腔制品的平衡浇注成型。
流道直径的初步设计首先,根据各浇口位置和型腔的布局,确定了如图1所示的流道分布。
然后,根据物料的特性、单个型腔的注射量和浇口位置等参数,确定相应的热流道分喷嘴的流道直径为6mm,并由此确定第二层分流道的直径也为6mm。
图1 热流道浇注系统的布置情况(其中,1-主流道喷嘴;2-第一层分流道;3-两层分流道间的中央连接流道;4-两层分流道间的两侧连接流道;5,6-第二层两侧分流道;7,8-第二层中间分流道;9-顶针式喷嘴和浇口)一般,在热流道模具中,熔体与流道壁面的热交换和流道截面所产生的摩擦热非常少,因此熔体因温度变化而导致的黏度变化相比冷流道系统也较小。
因此,在流动分析中,按熔体在各流道中剪切应力不变的理论,可以得到各级流道直径的计算式(如下述方程所示):式中,N——流道的分叉数;di——上游流道的直径,mm;di+1——下游流道的直径,mm。
010第10章注塑模浇注系统设计
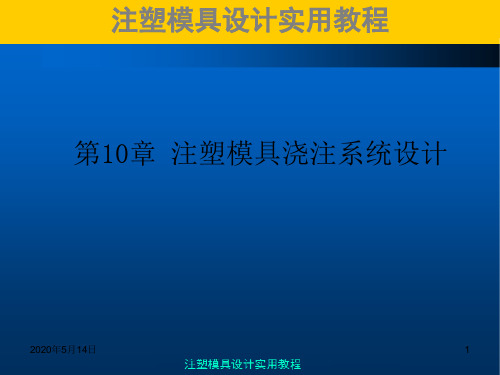
2019年2月22日
38
第10章 注塑模具浇注系统设计
10.3.2.7 伞形浇口
伞形浇口可以看作是环形浇口的特殊形式,见图10-21。伞 形浇口主要用于塑件中央有较主流道直径大的碰穿孔的场合。 1.伞形浇口优点: 1)可防止流痕发生。 2)节省流道加工。 3)具直接浇口之功用,压力损失少。 2.伞形浇口缺点: 1)浇口切离稍困难。 2)一次只能成型一个塑件。 3)塑件的孔中心必须与主流道对应。 3、设计参数:α=90º ,β=75º 。
2019年2月22日
22
第10章 注塑模具浇注系统设计
点浇口优点:
①位置有较大的自由度; ②浇口可自行脱落,留痕小; ③对桶形、壳形、盒形制品及面积较大的平板类胶件非常适用; ④浇口附近残余应力小。
点浇口缺点:
① 注射压力损失较大,浇注系 统凝料多。 ② 相对于侧浇口模,点浇口模 具结构较复杂,制作成本较大。
注塑模具设计实用教程 第10 章 注塑模具浇注系统设计
第10章 注塑模具浇注系统设计
2019年2月22日
1
第10章 注塑模具浇注系统设计
本章学习要求
• • • • • • 熟悉注塑模具浇注系统的分类。 熟悉浇注系统的设计原则、步骤和内容。 掌握主流道设计。 掌握分流道设计。 掌握侧浇口和点浇口设计。 了解其他浇口
2019年2月22日
20
第10章 注塑模具浇注系统设计
10.3.2常用浇口及其结构尺寸
浇口形式很多,常用浇口有点浇口、侧浇口、潜伏式浇口、直接 浇口,侧浇口又包括矩形浇口、扇形浇口、薄片浇口、爪形浇口、 环形浇口、伞形浇口及二次浇口等。
2019年2月22日
21
第10章 注塑模具浇注系统设计
注塑模具浇注系统设计及工艺探讨

注塑模具浇注系统设计及工艺探讨摘要:塑料制品在人们的日常生活中扮演着十分重要的角色,注射模具由于其自身具有一次成型、精确、大批量、高效率等诸多优点成为使用范围最广的塑料制品生产手段。
而注塑模具浇注系统设计的好坏又直接影响注射模型的整体效率和质量,因此对注塑模具浇注系统设计及工艺进行探讨具有十分重要的意义。
关键字:注塑模具浇注系统设计探讨注塑模具的浇注系统,就是指注塑模具中由注射机喷嘴到型腔之间的进料通道。
它的作用是将熔体平稳的引入注塑模具型腔,并在填充过程中将压力传递到型腔的各个部分,以获得组织致密,外形清晰、表面光洁和尺寸稳定的塑件。
可以说,注塑模具浇注系统设计的合理与否,直接关系着注射模型的效率和质量。
合理的浇注系统应尽可能满足以下条件:(1)尽可能短的流道长度并且尽量减少弯曲;(2)尽可能使塑料同时到达各个浇口;(3)尽可能使各个模腔同时填充完毕且各浇口同时冷却封闭;(4)应考虑去除浇口方便,修正浇口时在塑料制品上不留影响。
一、主流道设计主流道是连接注塑机喷嘴和注塑模具的桥梁,也是熔融的塑料进入模具时最先经过的地方。
主流道通常应位于模具中心线上,与注塑机喷嘴中心保持同心。
在直角式注塑机上,由于无需沿轴线拔出凝料,流道一般设计为等截面柱形。
而在卧式或立式注塑机上,为了便于凝料能从主流道中取出,一般将主流道设计成圆锥形。
相对于分型面,主流道结构型式有垂直式、倾斜式、圆弧式和分叉式等几种。
浇口套与注塑机喷嘴接触处的圆弧度必须吻和,否则在注塑时会产生“漏胶”现象,使压力降大大增加,甚至会使冷却后的主流道塑胶无法拔出(脱模)。
因此,浇口套球而凹陷的半径应比注塑机喷嘴的球而半径大0.5一0. 8 mm。
主流道与分流道相连部分的截面积应大于分流道的截面积,否则主流道内塑料比分流道内塑料先冷却,保压压力不能有效传到模腔内。
主流道的大小与塑料进入型腔的速度及充模时间长短有着密切关系。
若主流道太大,其回收冷料多,冷却时间长,且塑料包藏的空气增多,不利于排气;如果主流道太小,则塑料冷却快,流动性降低,压力降增大,不利于填充。
旋钮注塑模具说明书 一模8腔

5
6
内形尺寸
7
8
9
10 11
19.5 R1.34 R20.3 0.75
36 2.1 0.6 表 3-4 塑件尺寸
19.5+0.41 ������1.34+0.23 ������20.3+0.41 0.75+0.23
36+0.5 2.1+0.23 0.6+0.23
4. 成型设备的选择
4.1 计算塑件的体积 根据制件的三维模型,利用三维软件直接求得塑件的体积为: V=4500.2194mm3,取 V=4.5cm3。
S=310mm,因此符合开模行程的要求。 6.6 模厚校核
模具闭合高度为 352mm,符合注射机 150 ~ 360mm 的模厚要求。
综上所述:选取 HTF120J/TJ 型螺杆式注射成型机完全符合本模具的使用要求。 锁模力 CAE 分析图
7 浇注系统的设计
7.1 设计原则 浇注系统设计原则:
(1)浇注系统与塑件一起在分型面上,应有压降,流量和温度的分布的均衡布 置;
材料名称
型腔
型芯
聚丙烯(PP)
25′~45′
20′~45′
考虑零件形状的复杂性,型腔采用 45′脱模斜度,型芯采用 20′脱模斜度。
3.2.4 壁厚:
-5-
上海工程技术大学材料工程学院
旋钮注塑模课程设计说明书
设计合理,壁厚相对均匀,且符合最小壁厚的要求。查 P434 表 2-2-7[1],聚 丙烯最小壁厚为 0.85 mm。 3.2.5 圆角: 要从分型面位置、型芯、型腔结构来分析过渡圆角的设置。工件转角处加圆角, 最小圆角尺寸为 0.5 mm。 3.3 塑件表面质量分析
- 1、下载文档前请自行甄别文档内容的完整性,平台不提供额外的编辑、内容补充、找答案等附加服务。
- 2、"仅部分预览"的文档,不可在线预览部分如存在完整性等问题,可反馈申请退款(可完整预览的文档不适用该条件!)。
- 3、如文档侵犯您的权益,请联系客服反馈,我们会尽快为您处理(人工客服工作时间:9:00-18:30)。
收稿日期:2003-09-25作者简介:刘锦平(1974-),男,江西高安人,讲师,硕士,研究方向:塑料模具C AD/C AM.文章编号:1005-0523(2004)02-0116-04注塑模八腔浇注系统平衡研究刘锦平(华东交通大学机电工程学院,江西南昌330013)摘要:在充分考虑了非平衡浇注系统的沿程损失与局部损失的情况下,从能量角度确定了非平衡浇注系统第二级分流道和浇口半径之间的关系.关 键 词:非平衡浇注系统;沿程损失;局部损失;第二级分流道;浇口凝固中图分类号:T Q320.6 文献标识码:A0 引 言塑料制品制造工业是机械制造行业之一,塑料作为高分子化学和材料科学发展的重要成果,已成为人类不可缺少的重要生产资料.塑料制品制件在工业生产和日常生活中得到了愈来愈广泛的应用,塑料产品一般采用模塑成型方法生产,因而塑料模具常常作为一种重要的工艺装备.模具浇注系统在注塑成型过程中起着极其重要的作用,在实际生产中,为提高生产效率和节约模具制造经费,中、小型制品常采用一模多腔的方案,但是浇口可能会出现凝固现象而导致不能后续过程的顺利进料.如图1和图2所示,浇口①处发生了凝固效应[1],塑料熔体先到达浇口①而浇口②的型腔反而被充满.因此为保证各型腔制品的重量、性能等均匀一致,必须对浇注系统进行平衡分析与设计,使各型腔能在相同的时间内同时充满.1 一模八腔浇注系统分类当采用一模八腔的模具成型时,通常按浇注系统中流道布置的形式将浇注系统分为两类:自然平衡式浇注系统和非自然平衡式浇注系统:1)自然平衡式浇注系统的特点:从分流道到浇口及型腔,其形状、长度尺寸、圆角、模壁的冷却条件等都完全相同,因此熔体能以相同的成型压力和温度同时充满所有的型腔,从而可以获得尺寸相同、物理性能良好的制品.2)非自然平衡式浇注系统的特点:分流道、浇口的形状及尺寸各不相同,型腔的尺寸和诸型腔到主流道的距离也可能各不相同,在这种系统里,如果各个型腔不能同时被充满,就很难得到尺寸精确第21卷第2期2004年4月华东交通大学学报Journal of East China Jiaotong University V ol.21 N o.2Apr.,2004和性能良好的制品.2 浇注系统平衡计算的传统方法目前,在实际生产中,对于非平衡浇注系统实行人工平衡时常采用一种近似计算方法,这种方法被称为平衡系数法.该法基于各个型腔的平衡系数相等或成比例,来确定各个浇口的尺寸.其具体步骤是:已知第一级分流道直径不变、第二级分流道直径和长度相等以及浇口长度相等,仅通过改变各浇口的截面尺寸促使各个型腔能同时被塑料熔体充满.平衡计算的经验公式为[2]:K=s/a(1)式(1)中:K—浇口平衡系数;S—浇口面积;L—浇口长度;a—主流道到型腔浇口的距离该方法在实际应用中主要存在如下问题:①由上式可知,若各个型腔的形状和大小相同,离主流道越远,浇口的截面积就越大.如果浇口的截面积过大,容易造成成品与浇口的接口留有疤痕;②未考虑塑料熔体在浇口处的凝固效应;③未考虑塑料熔体的流变特性.3 八腔非平衡浇注系统的设计3.1 基本假设影响流道设计的因素很多而且十分复杂,从简化计算的角度出发提出下列假设条件:①第一级分流道的直径相等;②忽略塑料熔体的弹性,认为它是符合幂律模型的粘性流体;③塑料熔体在流道中的流动是在等温条件下进行的;④由于浇口的体积很小,故熔体充满浇口的时间可忽略不计.3.2 确定流体流动模型注射型腔内塑料流动模型[3]分析可分为一维、二维和三维分析.一维分析是二维分析的基础;二维分析是将任意形状的三维塑件模型展平成二维模型并分解成许多一维流动的基本单元进行一维分析;三维分析是在三维模型及其有限元网格的基础上进行的.二维分析主要用于确定塑料材料和注塑成型工艺参数的可行范围等以及成形过程技术上的可行性,而三维分析用于完整的成形过程(充模和保压)的图形仿真和数据分析.由流体力学知识可知,流体在管道中有两种流动形式:层流和紊流.当雷诺数[4]小于300时流体保持层流方式,否则为紊流.塑料熔体在注射温度时其雷诺数一般小于10,故塑料熔体是以层流的方式进行的,根据这个特点可选择一维模型进行分析.在注射模的设计过程中,一维模型可用作为:①求出最佳的工艺参数;②型腔中的流道平衡;③流道中的流动平衡;④确定流道系统的尺寸等.本课题选择一维流动模型进行分析计算.3.3 公式推导已知条件:①各分流道长度②第一级分流道的半径③流体进入浇注系统时的体积流量④塑料的各性能参数.待求值:第二级分流道半径和浇口半径由于非平衡浇注系统的局部对称,所以选择一模八腔的一侧如图3进行计算:3.3.1 AB0段某点体积流量模型在AB0段,熔体的损失只有内剪应力导致的流程损失,其损失值计算如下:如图4所示,运用一维流体模型先分析流体流至某一位置即点S处的情况:假设:l为流过的路径长度,Q s为瞬时体积流量,△M为△t时间内所做的功,τ为剪应力,v为速率,γ为剪切速率,K为流体稠度,n为非牛顿指数,由于剪应力所做的功即为流程损失,而且剪应力所做的功为:△M=l0τdl(2)假塑性流体是非牛顿型流体中最普遍、最常见的一种.几乎绝大多数聚合物熔体与溶液,其流动行为都接近于假塑性流体,在描述假塑性流体的经验方程中,指数方程能较好的反映粘性流体的流变711第2期 刘锦平:注塑模八腔浇注系统平衡研究 性质.该公式认为,定温下在某段剪切速率的范围内,粘性流体所受的切应力与剪切速率具有指数函数的关系.即有:非牛顿流体流变方程:τ=kγ2(3)浇注系统的流变学方程[4]:γ=(3n +1n )Q πR 3(4)能量守衡可知:M =12mv 2s -12mv 2A(5)由式(2)、(3)、(4)、(5)可以解得:Q s =[Q 2-nA-(2-n )z 0R 4-3n01]12n (其中:z 0=π2k (3n +1nπ)n)(6)由式(6)可以确定B 0处的体积流量Q B 0和相应的速率v B 03.3.2 转弯B 处的局部损失h f 以及Q B 1、Q B 2h r =2.6v22g(7)熔体在B 0流经B 1和B 2时有如下关系:Q B 0=2Q B 1+Q B 2(8)3312v 2B 0=2312v 2B 1+12v 2B 1+12v 2B 2+23h f (9)v 和Q 的关系如下所示:v =QπR2(10)由式(7)、(8)、(9)、(10)可以解得:Q B 1=H 0Q B 0(其中:H 0=1.3-gR 01+2-1.3g(R 4R 41)+2)(11)Q B 2=[1-2H 0]Q B 0(12)由式(11)、(12)可以确定B 1和B 2处的速率v B 1和v B 2.由于熔体在B 2E 0段与AB 0段流动情况相似,故同样由式(6)、(10)、(12)可得当熔体流至E 0点时的速度为:v E 0=[v 2-nB 2-(2-n )Z 0R 4-3nL 3]12-n (13)3.3.3 流动过程模拟以及第二级分流道半径确定为使熔体同时流至C 和F 两浇口处,必须使这两段的时间相等,其流动过程可模拟为如图5和图6的两个过程:1)熔体流经B 2E 0段所需的时间t 0牛顿第二定律可知:πR 20τ=dv dt(14)由式(3)、(4)、(10)、(14)可以解得:t 0=1m 0R 2-n0(1-n )(v 1-nE-v 1-nB2(其中:m 0=3n +1nπK )(15)2)熔体流经E 1F 段所需的时间t 1首先必须计算出在E 1和F 两点的速度:由流道的结构可知:v E 1=12v E 0(16)F 点的速度计算类似于B 2E 0段的E 0点速度计算,由式(13)可得:v F =[v 2-nE 1-(2-n )Z 0R 4-3n2L 4]12-n(17)该段时间与B 2E 0段时间计算相似,由式(15)可得:t 1=1m 0R 2-n 2(1-n )(v 1-nE1-v 1-nF)(18)3)熔体流经B 1C 所需的时间t 2同理由式(13)可得熔体在C 点的流动速度为:v C =[v 2-nB 1-(2-n )Z 0R 4-3n1L 1]12-n(19)同理由式(15)可得熔体流经B 1C 所需的时间:t 2=1m 0R 2-n 2(1-n )(v 1-nB1-v 1-nC)(20)熔体流经B 1C 段和B 2EF 段的时间相等,可得等式:t 2=t 0+t 1(21)由式(15)、(18)、(20)、(21)确定两第二级分流道半径的关系如下:v 1-nB 1-v 1-nC R 2-n1=v 1-nE 0-v 1-nB2R 2-n+v 1-nE 1-v 1-nF R 2-n2(22)因此,综合上述各式,采用递推法并利用计算机程序便可以确定二级分流道半径.4 一模八腔浇口尺寸计算在保证熔体同时到达各浇口的情况下,根据式(22)可确定二级分流道的半径.因为熔体在两浇口处的流速不同,而且又要使塑料熔体在相同的时间内充满各个型腔(这里假设具有相同外形和尺寸的型腔),因此,要采用不同的浇口尺寸.其推导过程811 华东交通大学学报 2004年如下:假设在浇口上C 和F 点对应的点为C 1和F 1.因为在注塑成型过程中,塑料流体的为层流,r 1和r 2分别为二级分支1和2的浇口半径,和为浇口体积流量.因此在浇口C 1处有:Q C 1=r 1R 1Q c(23)同理可得F 1处有:Q F 1=r 2R 2Q F(24)要保证塑料熔体在相同的时间内充满各个型腔,由式(23)和(24)可得:r 1r 2=Q F Q C 3R 1R 2(25)由式(10)、(17)和(19)可得知Q C 和Q F .故两浇口的半径关系也就很容易确定.5 实 验针对上述的理论推导,进行了相应的模具浇注系统设计.本实验选择S Z -30/25注射成型机,以热塑性塑料丙希晴-丁二烯-苯乙烯(ABS )为注塑原料,前、中和后筒温度分别加热至190℃、175℃和165℃.分别以不同的时间段(设为t 1、t 2、…tn ,下标n 为自然数,t 1<t 2<…<t n )为基准,进行注塑操作而得到一系列不同阶段的塑料产品.该实验采取了十个时间段,前四个时间段如图7所.t 1时间段表示的是塑料熔体的某一初始注射段,t 2时间段表明了塑料熔体同时到达八个浇口,t 3和t 4时间段初步表明了塑料熔体能够同步进料,不存在凝固现象.第二、第三注射过程如图8图9所示都各采取了三个时间段,由图可得知塑料产品是由小到大的过程,各个时间段得到八个相同的产品,没有出现浇口凝固现象.6 结 论通过简化非平衡浇注系统体系流动模式并作相应的假设,推导出计算分流道及浇口半径的公式,使其具有以下特点:1)塑料熔体同时到达八个型腔浇口处,从而消除了浇口的凝固;2)使非平衡浇注系统第二级分流道和浇口尺寸计算更简捷;3)避免多次试模修模.参考文献:[1]K wai 2sang Chin ,w ong T N.knowledge 2based Evaluation for theC onceptual Design Development of Injection M olding Parts[J ].Engineering Applic.Artif.Tntell.1996,9(4):359-375.[2]李德群.塑料成型工艺及模具设计[M].北京:机械工业出版社,1994.[3]董立武,李德群.注塑模C AD 计算功能的实用化研究[D].武汉:华中科技大学,1999.[4]张景松,候友夫.流体力学[M].徐州:中国矿业大学出版社,1993.The B alance Study of the Eight C avities I njection MoldLI U Jin 2ping(School of Mechanical and E lectronic Engineering ,East China Jiaotong University ,Nanchang 330013,China )Abstract :A fter evaluating the route loss and the local loss of the imbalance injection system ,the article con firms the re 2lation of the second grade branch radius from the scope of energy.K ey w ords :Imbalance Injection system ;R oute loss ;Second grade radius911第2期 刘锦平:注塑模八腔浇注系统平衡研究 。