中国转炉_负能炼钢_技术的发展与展望
浅谈我国转炉炼钢技术的发展与展望

我 国 是 世 界 上 钢 铁 冶 金 起 源 最 早 的 国 家 之 ~ ,也 是 世界
我 钢 铁 生 产 企 业 为 应 埘 市 场 需 求 ,对 提 高 钢 材 的 产 量 和 品 质 ,增 加 产 品 种 类 ,提 高 性 能 ,降 低 成 本 等 要 求 也 更 加 重 视 。 根 据 这 种 市 场 需 求 ,转 炉 的 生 产 工 2 流 程 进 行 了 很 大 程 度 上
I 1 l 金 属通 报
浅 谈 我 国转 炉 炼 钢 技 术 的 发 展 与 展 望
吴 计 雨
钢 集 ¨ { 仃I q 4 公 j ] 、 l l J 东 …姒2 7 6 8 0 ( I )
摘
要 : 我 国是 世 芥 钢 铁 产量 大 国 . 转 炉 炼钢 生 产的 铜 材 产量 占我 L & I 粗 钢 产 量 的 大部 分 , 随 钢铁 冶 炼技 术 不 断进 步 ,
1 . 3 1 9 9 0 年 至 今 发 展 洁 净 钢 时 期
低 、单 炉产量高 、投 资少 、生产速度快等优点 川,被 我 钢铁
企 业所广泛应用 。
到 了九十 年代之 后 ,市场 需 求的钢材 质量 主要转 变为 洁 净 钢 ,所 以 钢 材 企 业 也 根 据 市 场 悄 况 迅 速 转 变 生 产 模 式 ,建
第 一大钢铁 生产大国 ,其 中 8 0 以上的粗 钢都是 由转炉生产。 世 界 钢 材 需 求 员 的 持 续 增 长 趋 势 , 给 发 展 中 国 家 的 铡 铁 生 提供 了一个优 良发展机会 l 。
炼钢设备技术的发展国产化亮点和趋势展望
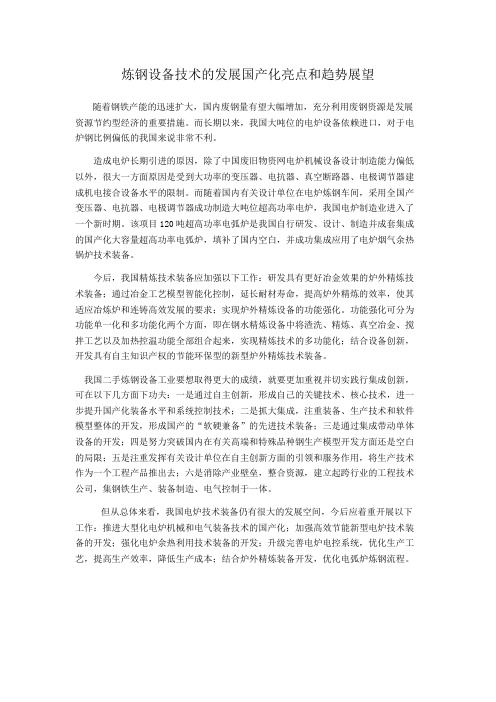
炼钢设备技术的发展国产化亮点和趋势展望随着钢铁产能的迅速扩大,国内废钢量有望大幅增加,充分利用废钢资源是发展资源节约型经济的重要措施。
而长期以来,我国大吨位的电炉设备依赖进口,对于电炉钢比例偏低的我国来说非常不利。
造成电炉长期引进的原因,除了中国废旧物资网电炉机械设备设计制造能力偏低以外,很大一方面原因是受到大功率的变压器、电抗器、真空断路器、电极调节器建成机电接合设备水平的限制。
而随着国内有关设计单位在电炉炼钢车间,采用全国产变压器、电抗器、电极调节器成功制造大吨位超高功率电炉,我国电炉制造业进入了一个新时期。
该项目120吨超高功率电弧炉是我国自行研发、设计、制造并成套集成的国产化大容量超高功率电弧炉,填补了国内空白,并成功集成应用了电炉烟气余热锅炉技术装备。
今后,我国精炼技术装备应加强以下工作:研发具有更好冶金效果的炉外精炼技术装备;通过冶金工艺模型智能化控制,延长耐材寿命,提高炉外精炼的效率,使其适应冶炼炉和连铸高效发展的要求;实现炉外精炼设备的功能强化。
功能强化可分为功能单一化和多功能化两个方面,即在钢水精炼设备中将渣洗、精炼、真空冶金、搅拌工艺以及加热控温功能全部组合起来,实现精炼技术的多功能化;结合设备创新,开发具有自主知识产权的节能环保型的新型炉外精炼技术装备。
我国二手炼钢设备工业要想取得更大的成绩,就要更加重视并切实践行集成创新,可在以下几方面下功夫:一是通过自主创新,形成自己的关键技术、核心技术,进一步提升国产化装备水平和系统控制技术;二是抓大集成,注重装备、生产技术和软件模型整体的开发,形成国产的“软硬兼备”的先进技术装备;三是通过集成带动单体设备的开发;四是努力突破国内在有关高端和特殊品种钢生产模型开发方面还是空白的局限;五是注重发挥有关设计单位在自主创新方面的引领和服务作用,将生产技术作为一个工程产品推出去;六是消除产业壁垒,整合资源,建立起跨行业的工程技术公司,集钢铁生产、装备制造、电气控制于一体。
中国电炉炼钢现状及展望资料
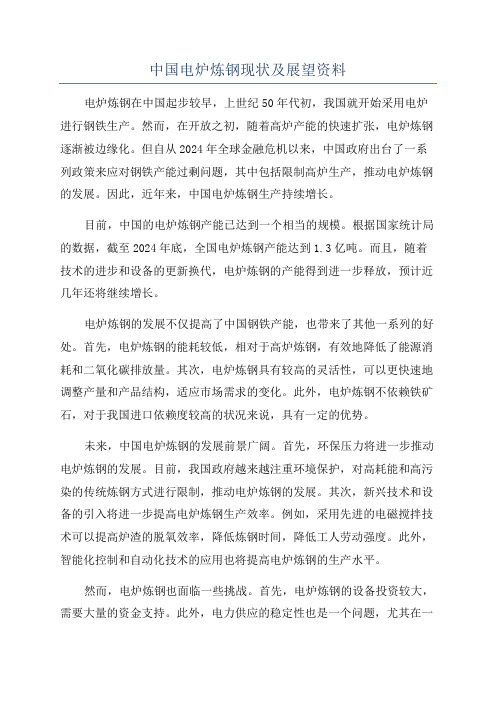
中国电炉炼钢现状及展望资料电炉炼钢在中国起步较早,上世纪50年代初,我国就开始采用电炉进行钢铁生产。
然而,在开放之初,随着高炉产能的快速扩张,电炉炼钢逐渐被边缘化。
但自从2024年全球金融危机以来,中国政府出台了一系列政策来应对钢铁产能过剩问题,其中包括限制高炉生产,推动电炉炼钢的发展。
因此,近年来,中国电炉炼钢生产持续增长。
目前,中国的电炉炼钢产能已达到一个相当的规模。
根据国家统计局的数据,截至2024年底,全国电炉炼钢产能达到1.3亿吨。
而且,随着技术的进步和设备的更新换代,电炉炼钢的产能得到进一步释放,预计近几年还将继续增长。
电炉炼钢的发展不仅提高了中国钢铁产能,也带来了其他一系列的好处。
首先,电炉炼钢的能耗较低,相对于高炉炼钢,有效地降低了能源消耗和二氧化碳排放量。
其次,电炉炼钢具有较高的灵活性,可以更快速地调整产量和产品结构,适应市场需求的变化。
此外,电炉炼钢不依赖铁矿石,对于我国进口依赖度较高的状况来说,具有一定的优势。
未来,中国电炉炼钢的发展前景广阔。
首先,环保压力将进一步推动电炉炼钢的发展。
目前,我国政府越来越注重环境保护,对高耗能和高污染的传统炼钢方式进行限制,推动电炉炼钢的发展。
其次,新兴技术和设备的引入将进一步提高电炉炼钢生产效率。
例如,采用先进的电磁搅拌技术可以提高炉渣的脱氧效率,降低炼钢时间,降低工人劳动强度。
此外,智能化控制和自动化技术的应用也将提高电炉炼钢的生产水平。
然而,电炉炼钢也面临一些挑战。
首先,电炉炼钢的设备投资较大,需要大量的资金支持。
此外,电力供应的稳定性也是一个问题,尤其在一些经济欠发达地区。
此外,传统高炉钢铁企业的转型升级也是一个挑战,包括技术人员的培训和转岗等问题。
综上所述,中国电炉炼钢在过去几年取得了显著的发展,目前已经成为我国钢铁产能的重要组成部分。
未来,随着环保压力的增大和技术的进步,电炉炼钢有望继续发展壮大。
然而,要实现电炉炼钢产能的进一步提升,需要政府的支持和钢铁企业的积极配合。
试论转炉炼钢的现状和发展

试论转炉炼钢的现状和发展摘要:转炉炼钢是我国主要的炼钢模式,目前我国绝大多数钢材均为转炉钢,并且我国生产的转炉钢占世界转炉钢的1/4左右。
近年来,我国的转炉数量不断增多,并且转炉炼钢工艺更加成熟,无论是转炉钢的产量还是转炉钢的质量都有所提升。
为了进一步提升转炉钢的产量与品质,未来需要针对那些条件较好的转炉钢厂进行改造升级,提升转炉钢厂的生产设备性能以及生产工艺水平,在保障转炉钢产量和质量的同时,降低能耗,减少对环境造成的不利影响,保障转炉炼钢的可持续发展。
基于此,本文分析了转炉炼钢的现状,并就转炉炼钢的发展进行探究,仅供大家参考。
关键词:转炉炼钢;现状;发展引言:转炉炼钢是我国主要的炼钢方式,在建国初期,平炉是我国主要的炼钢设备。
改革开放以来,社会经济的快速发展,使得钢材需求量不断提升,这在很大程度上推动了炼钢产业的发展。
在此背景下,转炉炼钢也得到了快速发展的有利时机。
经过多年的发展,目前我国绝大多数钢材均为转炉钢,并且转炉炼钢工艺更加完善。
但转炉炼钢依然存在着能耗高以及环境污染严重等方面的不足,因此应积极探索更加科学的转炉炼钢发展策略,保障转炉炼钢的可持续发展。
1转炉炼钢现状分析1.1转炉钢产量和比例近年来,随着转炉数量的增加以及转炉炼钢工艺的完善,使得转炉钢的产量不断提升,相应在我国钢产量中,转炉钢所占比例也在不断增加。
在2000年以来,我国转炉钢产量增幅明显,远远领先于世界平均水平。
近年来我国转炉钢的占比始终处于80%以上,而在2016年我国转炉钢占比则达到89.9%,这一比例是电炉钢的9倍左右,由此可见,我国转炉钢的占比较高。
1.2主要技术经济指标分析1.2.1钢铁料消耗目前,在一些大中型钢铁企业转炉炼钢过程中,对钢铁料的消耗比例不断下降,2006年的平均水平1081.67kg/t,并且呈逐年下降趋势。
有的先进的钢铁企业,对钢铁料的消耗比例已经降至1060kg/t左右,这样的钢铁料消耗水平已经达到了世界先进水平。
转炉炼钢技术的发展与展望
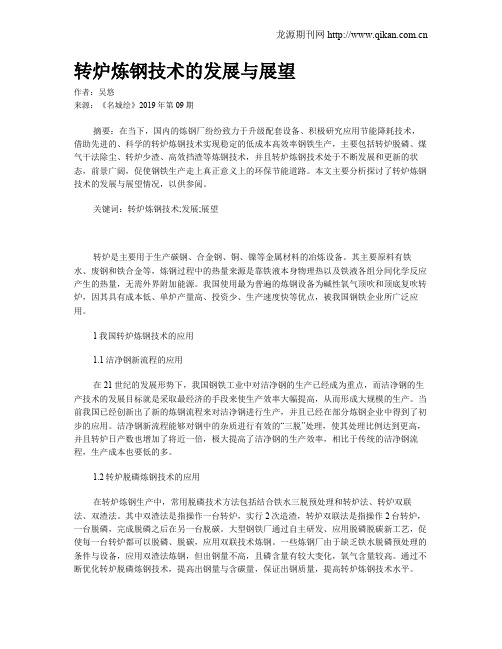
转炉炼钢技术的发展与展望作者:吴悠来源:《名城绘》2019年第09期摘要:在当下,国内的炼钢厂纷纷致力于升级配套设备、积极研究应用节能降耗技术,借助先进的、科学的转炉炼钢技术实现稳定的低成本高效率钢铁生产,主要包括转炉脱磷、煤气干法除尘、转炉少渣、高效挡渣等炼钢技术,并且转炉炼钢技术处于不断发展和更新的状态,前景广阔,促使钢铁生产走上真正意义上的环保节能道路。
本文主要分析探讨了转炉炼钢技术的发展与展望情况,以供参阅。
关键词:转炉炼钢技术;发展;展望转炉是主要用于生产碳钢、合金钢、铜、镍等金属材料的冶炼设备。
其主要原料有铁水、废钢和铁合金等,炼钢过程中的热量来源是靠铁液本身物理热以及铁液各组分间化学反应产生的热量,无需外界附加能源。
我国使用最为普遍的炼钢设备为碱性氧气顶吹和顶底复吹转炉,因其具有成本低、单炉产量高、投资少、生产速度快等优点,被我国钢铁企业所广泛应用。
1我国转炉炼钢技术的应用1.1洁净钢新流程的应用在21世纪的发展形势下,我国钢铁工业中对洁净钢的生产已经成为重点,而洁净钢的生产技术的发展目标就是采取最经济的手段来使生产效率大幅提高,从而形成大规模的生产。
当前我国已经创新出了新的炼钢流程来对洁净钢进行生产,并且已经在部分炼钢企业中得到了初步的应用。
洁净钢新流程能够对钢中的杂质进行有效的“三脱”处理,使其处理比例达到更高,并且转炉日产数也增加了将近一倍,极大提高了洁净钢的生产效率,相比于传统的洁净钢流程,生产成本也要低的多。
1.2转炉脱磷炼钢技术的应用在转炉炼钢生产中,常用脱磷技术方法包括结合铁水三脱预处理和转炉法、转炉双联法、双渣法。
其中双渣法是指操作一台转炉,实行2次造渣,转炉双联法是指操作2台转炉,一台脱磷,完成脱磷之后在另一台脱碳。
大型钢铁厂通过自主研发、应用脱磷脱碳新工艺,促使每一台转炉都可以脱磷、脱碳,应用双联技术炼钢。
一些炼钢厂由于缺乏铁水脱磷预处理的条件与设备,应用双渣法炼钢,但出钢量不高,且磷含量有较大变化,氧气含量较高。
论文《负能炼钢》

我国是世界上钢产量最大的国家,同时也是资源、能耗相对匮乏的国家,推广节能降耗技术是我国钢铁工业可持续发展的关键,“负能炼钢”是炼钢节能的主要技术,我国转炉比例已经超过80%,推广“负能炼钢”对实现节能减排目标,保证钢铁工业可持续发展有重要意义。
2“负能炼Байду номын сангаас”的概念
“负能炼钢”是一个工程概念,20世纪70年代由日本钢铁厂首先提出。其含义是指炼钢过程中回收的能量(煤气和蒸汽)大于炼钢过程中实际消耗的(水、电、风、气总和)用量,通常转炉炼钢消耗的能量在15~30Kgce/t(千克标准煤/吨)钢,而回收煤气和蒸汽的能量可折合为25~35Kgce/t钢,因此,转炉工序实现负能炼钢,一方面要努力降低炼钢能耗,另一方面要加强能量回收,提高煤气和蒸汽的回收效率。
若能源消耗值大于回收能源值,工序能耗则为正值;
若能源消耗值等于回收能源值,工序能耗则为零消耗;
若能源消耗值小于回收能源值,工序能耗则负值。
如果结果为负值,则称为“负能炼钢”。我们可以通过表1来清晰的了解转炉炼钢过程中能量的消耗值与回收值比例。
表1转炉炼钢能量平衡分析表
转炉消耗能量
转炉回收能量
项目
Kgce/t
厂区内蒸汽回收余热锅炉系统
(三)优化炼钢生产工艺
为实现负能炼钢,应提高转炉炼钢生产率,进一步优化转炉的冶炼工序,达到提高产量,降低能耗和稳定铁水质量的目的。在转炉冶炼工艺上应采取相应的优化措施。
(1)在转炉冶炼过程中,提高供氧强度,缩短冶炼时间,一般来说,吹炼时间决定于供氧强度,而供氧强度受限于炉容比和吹炼、造渣工艺,炉容比为0.95~1.1m3/t,供氧强度可提高到3.5~4.0N m3/t·min,吹炼时间可缩短到15min以内。另外,提高成渣速度。提高供氧强度必须解决喷溅问题,技术关键是提高初成渣速度,同时,还要提高石灰质量,加快石灰熔化。
我国转炉炼钢技术的发展

2 0 第 2期 02年
钢
铁
技
术
・ ・ 9
平 炉 钢 产 量 降 至 9 .l万 t 仅 占 总 产 钢 量 的 27 ,
3 初步 形成 了铁 水预 处理 、转 炉 、炉 外精 炼的优 化工艺路 线 路线 3 1铁水脱硫 能力 的迅速 增 20 00年对 7 4座转 炉炼 钢 厂的统计 .铁 水脱 硫处 理能 力 已达 39 6 1万 t .实 际经脱硫 的铁 水
妤 在第 一 铁 炼
r 也增 加 槽 筛 分 。 从 喷 吹朋 煤 而 言 , 首先 要 聚 1 H无 灰 分优 质 无 煤 .这 是 提 高煤 粉 燃烧 串 , 降 { 低 燃 料 比 的 关 键 所 以 其 次 是 改 变喷 煤 粉 的划 r
度 , 以加 速 燃 烧 与 化 谜 度 , 实现 完 全 燃 烧 。
我 国转炉炼钢技 术的进 一步发展提 出 了一些建议 【 关键词 】 转炉炼钢
1 前言
下 我 国转 炉 炼钢 进 入 人发 展 时 期 .由 丁氧气 转
l6 年 .我国第 一座 3 94 0 t氧气 顶 吹转炉 炼
钢 乍问 在 首钢 建 成投 产 。其后 ,上钢 一厂 三 转 炉
炉 炼钢 的迅速 发展 ,至 19 9 6年我 国钢 产 肇首次 突
钢厂 .并 r 17 年建 成投 产 。 9 1
进^ 8 O年代 后 .在 政革开放 方针 政策 的指 引
20 00年我 国钢产量为 1736 22 1万 t .其 中转炉 钢 为 15339 t 01 9 万 .约 山全 国总产钢量的 8. %. 77
可 以利 } 更 多的炼 钢 余 氧 对 高炉 进 行 富氧 喷 煤 , I { 因 为 富氧 喷煤 可 以缩 短 热滞 后 时 间 。囡此 .结 合 马钢 特 点,提 倡 高风 温 .富氧 人 喷 吹 .改善 冶 炼 条什 .能获得更好 的经济效益和高炉技术经济指标 。
转炉负能炼钢

我国转炉“负能炼钢”的技术现状和发展摘要:本文介绍了我国转炉“负能炼钢”的技术现状,总结了国内负能炼钢的经验,并对负能炼钢的技术概念、工序构成、能源折算系数等问题进行了讨论。
在此基础上提出我国加快实施转炉负能炼钢水平的技术措施。
关键词:转炉、煤气回收、负能炼钢1 前言近几年随着世界经济的繁荣,钢铁消费和钢铁产量逐年递增,造成世界范围内资源和能源紧张。
根据国际上Deutsche Bank的统计,2004年国际市场焦炭价格上涨了20%,铁矿石价格上涨了16%;到2005年,世界矿价和主焦煤价格大幅度上涨,其中铁矿石上涨71%,主焦煤上涨一倍。
钢铁生产原料的大幅度涨价,使钢铁工业的利润空间缩小,钢铁工业必须进一步降低能耗水平,提高资源利用率,才可能保证持续稳定的发展。
2003年国内重点钢铁企业能耗水平和国际先进水平相比高出56kgce/t,分析钢铁生产过程中各工序的能耗水平与国外先进水平的差距,炼钢工序差距较大,达到37.7kgce/t。
因此,国内钢铁厂尽快实现负能炼钢,可使我国钢铁工业整体能耗接近国际先进水平。
2 我国“负能炼钢”的技术现状2.1“负能炼钢”的技术进步宝钢是国内最早实现“负能炼钢”的炼钢厂,1995年实现炼钢-连铸全工序负能炼钢。
最近几年,由于品种结构调整,增加了炉外精炼、电磁搅拌等新工序,使工序能耗略有上升,但仍保持负能炼钢。
图1给出近几年国内负能炼钢技术发展的状况,其成绩主要是:●1989年宝钢300t转炉实现转炉工序负能炼钢,转炉工序能耗达到-11kgce/t钢的世界领先水平;●1996年宝钢实现全工序(包括连铸工序)负能炼钢,能耗为-1.12kgce/t钢;●1999年武钢三炼钢250t转炉实现转炉工序负能炼钢;●2002~2003年马钢一炼钢、鞍钢一炼钢、本溪炼钢厂等一批中型转炉基本实现负能炼钢;●2000年12月莱钢25t小型转炉基本实现了负能炼钢。
我国转炉“负能炼钢”技术的发展趋势2.1.1 大型转炉“负能炼钢”的实践大型转炉负能炼钢技术已经完全成熟,并达到国际领先水平。
- 1、下载文档前请自行甄别文档内容的完整性,平台不提供额外的编辑、内容补充、找答案等附加服务。
- 2、"仅部分预览"的文档,不可在线预览部分如存在完整性等问题,可反馈申请退款(可完整预览的文档不适用该条件!)。
- 3、如文档侵犯您的权益,请联系客服反馈,我们会尽快为您处理(人工客服工作时间:9:00-18:30)。
第19卷第11期 2009年11月 中国冶金China Metallurgy Vol.19,No.11November 2009中国转炉“负能炼钢”技术的发展与展望刘 浏(钢铁研究总院,北京100081)摘 要:以2008年全国大、中型转炉“负能炼钢”对标竞赛的数据为基础,分析总结国内转炉“负能炼钢”的主要成绩,提出实现“负能炼钢”的关键技术,并对今后国内“负能炼钢”技术发展趋势提出具体建议。
关键词:转炉;负能炼钢;节能降耗中图分类号:TF71 文献标识码:A 文章编号:100629356(2009)1120033207Development and Prospects of Converter N egativeE nergy Steelm aking in ChinaL IU Liu(Central Iron and Steel Research Institute ,Beijing 100081,China )Abstract :Based on the data of comparative standard competition about national large and medium converter negative energy steelmaking in 2008,analyzing and summarizing main indexes of domestic converter negative energy steel 2making ,the key technologies for realizing negative energy steelmaking are put forward ,and some concrete proposals are presented according to domestic negative energy steelmaking technology development trend.K ey w ords :converter ;negative energy steelmaking ;energy saving and consumption reducing作者简介:刘 浏(19512),男,博士,教授级高级工程师; E 2m ail :liul @ ; 修订日期:2009210205 中国是世界上最大的产钢国,同时也是资源、能源相对匮乏的国家,推广节能减排技术是保证中国钢铁工业可持续发展的关键。
“负能炼钢”是炼钢节能的主要技术,中国转炉钢比例超过90%,推广“负能炼钢”对实现节能减排目标,保证钢铁工业健康发展具有重要意义。
本文以2008年“全国重点大型耗能钢铁生产设备节能降耗对标竞赛”中转炉钢厂数据为基础,分析总结近几年国内“负能炼钢”的主要成绩,提出实现“负能炼钢”的关键技术,并对今后“负能炼钢”技术发展提出具体建议。
1 国内转炉“负能炼钢”的技术进步近几年,转炉“负能炼钢”技术的推广应用受到广泛重视并取得重大进步,表现在以下方面。
1.1 转炉工序能耗逐年降低转炉是中国最主要的炼钢方法,转炉钢产量从2000年的11068亿t ,增长到2008年的41518亿t ,平均年增长率为1915%,高于国内粗钢产量增长速度(平均增长率为1812%)。
转炉钢比例相应从2000年的8411%增长到90%左右,推广应用转炉“负能炼钢”技术具有重大的战略意义。
“负能炼钢”是一个工程概念,20世纪70年代由日本钢铁厂首先提出。
其含义是指炼钢过程中回收的煤气和蒸汽能量大于实际炼钢过程中消耗的水、电、风、气等能量总和。
如表1所示,通常转炉炼钢消耗的能量波动在15~30kg/t (钢),而回收煤气、蒸汽的能量可折合25~35kg/t (钢)。
因此,实现“负能炼钢”一方面要努力降低炼钢能耗,另一方面要加强回收,提高能量回收效率。
表1 转炉炼钢能量平衡T able 1 E nergy b alance during converter steelm aking 项目转炉消耗能量/(kg ・t -1)%项目转炉回收能量/(kg ・t -1)%氧气9.7334蒸汽10.530电8.0228煤气24.570煤气 5.1518氩气 1.726氮气0.863其它 3.1511合计28.63100合计35100 如图1所示,随着中国钢产量迅速增长,转炉炼钢工序能耗和吨钢综合能耗不断降低。
以2003年数据为基础:国内重点钢铁企业能耗水平比国际先中国冶金第19卷进水平高出56kg/t ,其中炼钢工序能耗差距最大,达到3717kg/t 。
因此,尽快实现转炉“负能炼钢”可促进国内钢铁工业整体能耗达到国际先进水平。
图1 2000-2008年中国钢产量与能耗变化Fig.1 Change of domestic steel output and energyconsumption from 2000to 2008 总结国内“负能炼钢”的技术发展,分为以下3个阶段:(1)技术突破期(20世纪90年代):1989年宝钢300t 转炉实现转炉工序负能炼钢,转炉工序能耗达到-11kg/t (钢);1996年宝钢实现全工序(包括连铸工序)负能炼钢,能耗为-1112kg/t (钢)。
(2)技术推广期(1999-2003年):1999年武钢三炼钢250t 转炉实现转炉工序负能炼钢;2002-2003年马钢一炼钢、鞍钢一炼钢、本溪炼钢厂等一批中型转炉基本实现负能炼钢;2000年12月莱钢25t 小型转炉初步实现负能炼钢。
但多数钢厂“负能炼钢”的效果均不太稳定。
(3)技术成熟期(2004-):近几年,国内钢厂更加注重转炉“负能炼钢”技术,许多钢厂已能够较稳定地实现“负能炼钢”。
特别是100t 以上的中型转炉,实现“负能炼钢”的钢厂日益增多。
国内“负能炼钢”技术的迅速发展得益于以下三方面:一是炼钢工艺结构的优化:随着国内新建100t 以上大、中型转炉的增多,配备了煤气、蒸汽回收与余热发电等设施,为“负能炼钢”打下设备基础;二是“负能炼钢”工艺不断完善,多数钢厂已初步掌握“负能炼钢”的基本工艺;三是2005年,国家统计局将电力折算系数调整为电热当量值(即1kW ・h =011229kg )替换原来沿用的电煤耗等价值(即1kW ・h =01404kg )。
炼钢能耗统计值降低,利于实现“负能炼钢”。
1.2 不少大、中型转炉已实现“负能炼钢”2008年“国家重点大型耗能钢铁生产设备节能降耗对标竞赛”,国内16家转炉钢厂共计62座100t 以上大、中型转炉参加比赛。
由于是对标竞赛,各厂家统计数据的口径有差别,一定程度影响了竞赛结果。
如宝钢仍沿用传统的“电煤等价”折算系数,统计能耗偏高。
但竞赛结果也能反映出国内大、中型转炉“负能炼钢”的业绩和水平。
图2给出参赛的62座转炉“负能炼钢”的业绩。
其中多数钢厂已实现转炉“负能炼钢”。
图2 2008年转炉“负能炼钢”竞赛指标对比Fig.2 Comparison of competition indexes of converter negative energy steelm aking in 20081.3 少数钢厂实现炼钢2连铸全工序负能生产目前国内已有少数钢厂实现炼钢2连铸全工序负能生产。
如表2所示,武钢、太钢、沙钢、济钢等钢厂已实现全工序负能生产;邯钢、莱钢、鞍钢第三炼钢连轧厂、酒钢等钢厂已接近实现全工序负能生产。
这是近几年国内“负能炼钢”技术发展的重要标志。
43第11期刘 浏:中国转炉“负能炼钢”技术的发展与展望表2 2008年国内转炉钢厂炼钢2连铸全工序负能生产概况T able2 Domestic negative energy production situ ation during whole process of converter steelm akingand continuous casting in2008钢厂容积/t工序能耗/(kg・t-1)煤气回收量/(m3・t-1)蒸汽回收量/(kg・t-1)精炼工序能耗/(kg・t-1)连铸工序能耗/(kg・t-1)综合能耗/(ke・t-1)已实现沙钢3×180-14.2799.8689.04-14.27武钢3×250-22.67103.0787.91 2.99 6.91-12.77济钢3×120-11.366793.2828.18 3.96 3.91-3.4967太钢2×180-24.6211699.816.14 5.74-2.74接近实现邯钢3×100-5.170.6558 3.6 3.2 1.7莱钢3×120-6.2578.4825.36 3.86 4.41 2.02鞍钢2×260-7.61690.04 3.9 6.59 2.88酒钢2×120-9.0765979.75 4.06 4.74 国内铁水预处理的工序能耗波动在014~018 kg/t(钢)(多数厂已计算在转炉工序能耗中)。
精炼工序能耗波动在2199~35181kg/t(钢),平均为8199kg/t(钢)。
竞赛数据反映出的一个重要事实是:精炼工序能耗并不随精炼工艺的复杂程度和精炼钢水比例增加而增大,如武钢三炼钢品种繁多,真空精炼比高,但精炼工序能耗仅为2199kg/t(钢)。
这说明今后随着炉外精炼工艺的优化,精炼工艺能耗水平可望大幅度降低。
国内连铸工序能耗波动在312~31128kg/t (钢),平均为1016kg/t(钢)。
进一步提高连铸生产效率可使连铸工序能耗降低到10kg/t以下。
综上所述,在转炉“负能炼钢”的基础上,通过工艺优化提高生产效率,国内大多数钢厂可实现炼钢2连铸全工序负能生产。
2 “负能炼钢”的关键技术总结参赛单位实现转炉“负能炼钢”的基本经验,提出以下“负能炼钢”关键技术。
2.1 提高生产效率是实现“负能炼钢”的基础各钢厂实现“负能炼钢”的基本经验可以看出:提高转炉生产效率对于实现“负能炼钢”具有重大意义。
以转炉每公称吨位每年的产钢量(万t/公称t ・年)作为转炉生产效率指标,与转炉工序能耗和吨钢电耗作图,如图3、4所示。
从图中可以看出:(1)提高转炉生产效率,使转炉工序能耗线性降低。
对于大、中型转炉当转炉生产效率>0.85万t/ (公称t・年),可实现转炉“负能炼钢”;(2)提高转炉生产效率,使转炉吨钢电耗进一步降低;(3)提高转炉生产效率,使吨钢氧耗进一步降低。
2.2 强化转炉煤气回收强化煤气回收是实现转炉“负能炼钢”的基本保53中国冶金第19卷障。