STP75NF75详细资料
ST7540资料

ST ST7540动力线调制解调方案2008-7-30 14:14 来源:STST公司的ST7540是FSK动力线收发器,半双工异步/同步FSK调制解调器. ST7540集成了线路驱动器和5V 和3.3V线性稳压器,单电源7.5 到13.5 V工作.器件通过内部的寄存器来控制工作,可通过同步串行接口进行可编程.其它的功能包括看门狗,时钟输出,输出电流和电压控制,载波/前导检测,发送停止和信道在用与热关断等.ST7540可以采用八个不通的信道(60, 66, 72,76, 82.05, 86, 110, 132.5 kHz)进行通信,有四种不同的波特率(600, 1200, 2400, 4800)和两种精度(1 和0.5).本文介绍了ST7540的主要性能,方框图,参考设计的主要特性和评估板电路图以及所用的材料清单(BOM).ST ST7540 FSK powerline transceiverST7540 transceiver uses Frequency Shift Keying (FSK) modulation to perform a half-duplex communication on a powerline network. It operates from a 7.5 to 13.5 V single supply voltage (Vcc) and integrates a power amplifier (PA), which is able to drive low line impedance, and two linear regulators providing 5 V and 3.3 V.The ST7540 can communicate using eight different communication channels (60, 66, 72,76, 82.05, 86, 110, 132.5 kHz), four baud rates (600, 1200, 2400, 4800) and two deviations (1 and 0.5). Additional functions are included, such as watchdog, automatic control on PA output voltage and current, carrier/preamble detection and band-in-use signaling, transmission time-out, and thermal shutdown.The transceiver, which is dedicated only to physical communication, operates with a microcontroller whose aim is to manage the communication protocol stack. A reset output (RSTO) and a programmable clock (MCLK) can be provided to the microcontroller by theST7540 in order to simplify the external logic and circuitry.The host controller can exchange data with the transceiver through a serial interface, programmable to operate either in UART (CLR/T data clock not used) or in SPI mode.Communication on the power line can be either synchronous or asynchronous to the dataclock that is provided by the transceiver at the programmed baud rate.When in transmission mode (i.e. RxTx line at low level), the ST7540 samples the digitalsignal on the TxD line at the programmed baud rate and modulates it in a FSK sinusoidaloutput on the Tx_OUT line. This signal is then externally fed into the power amplifier to add current capability. The power amplifier can also introduce gain and active filtering to the signal, just using few external passive components. The resulting signal on the PA_OUT line is coupled to the power line.When in receiving mode (i.e. RxTx line at high level), an incoming FSK signal on the Rx_IN line is demodulated and the digital output is available for the microcontroller on the RxD pin.The device also recovers the synchronism of the received signal using an internal PLL. The recovered clock is present on CLR/T output.The ST7540 operating parameters can be set by means of an internal control register,accessible only through the SPI host interface.ST7540通用特性:■Half-duplex frequency shift keying (FSK) transceiver■Integrated power li ne driver with programmable voltage and current control■Programmable mains access:SynchronousAsynchronous■Single supply voltage (from 7.5V up to 13.5V)■Very low power consumption (Iq = 5mA)■Integrates 5V voltage regulator (up to 50mA) with short circ uit protection■Integrated 3.3V voltage regulator (up to 50mA) with short circuit protection■3.3V or 5V digital supply■8 Programmable transmission frequencies■Programmable baud rate up to 4800BPS■Receiving sensitivity up to 250VRMS■Suitable fo r applications in accordance with EN 50065 Cenelec specification■Carrier or preamble detection■Band in use detection■Programmable control register■Watchdog timer■8 or 16 Bit header recognition■ST7537 and ST7538 compatible■UART/SPI host interface图1.ST7540方框图The ST7540 reference design has been developed as a useful tool to demonstrate how a small, high-performance powerline node can be built using the ST7540 FSK transceiver.With this reference design, it is possible to evaluate the ST7540 features, in particular, its transmitting and receiving performances through actual communication on the power line.The ST7540 reference design may be considered to be composed of three main sections:Power supply section, specifically tailored to match powerline coupling requirementsand to operate within a wide range of the input mains voltageModem and crystal oscillator sectionLine coupling interface sectionThe coupling interface is designed to allow the ST7540 FSK transceiver to transmit and receive on the mains using 72 kHz carrier frequencies, within the European CENELEC standard A-band specified for automatic meter reading.The complete evaluation system for the ST7540 powerline communication consists of:a PC using the ST7540 Power Line Modem Demo Kit software toolone EVALCOMMBOARD hosting the ST7 microcontrollerone ST7540 reference design board (EVALST7540-1).The correct procedure for connecting the EVALST7540-1 and theEVALCOMMBOARD is as follows:1.Connect the EVALST7540-1 and the EVALCOMMBOARD2.Connect the ac mains cable to the EVALST7540-1 and the USB cable to the EVALCOMMBOARD3.Connect the EVALST7540-1 to the ac mains supply4.Connect the EVALCOMMBOARD to the PC via the USB cable.图2.包括PC, EVALCOMMBOARD和EVALST7540-1板的完整评估系统图3.EVALST7540-1板的调制解调器和耦合接口电路图图4.EVALST7540-1板电源电路图图5.Rx和Tx 滤波器电路图图6.三相架构原理框图图7.110 kHz通路的线路耦合接口电路图7.132.5 kHz通路的线路耦合接口电路材料清单(BOM):/stonline/products/literature/ds/12176/st7540.pdf和/stonline/products/literature/an/12791/evalst7540-1.pdf。
3750交换机配置手册
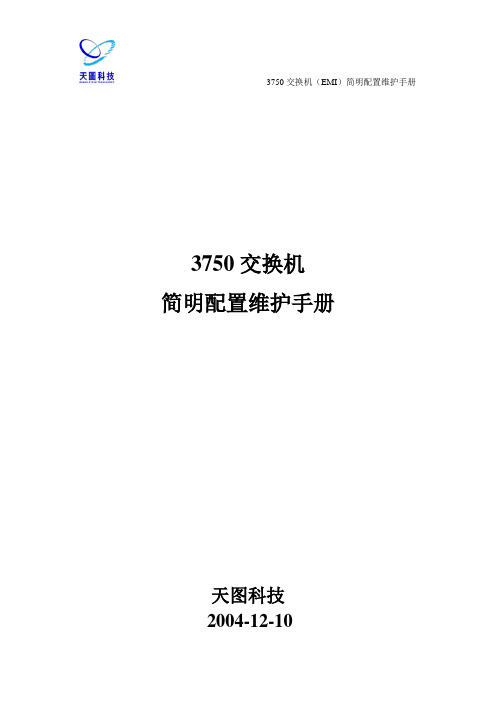
3750交换机(EMI)简明配置维护手册3750交换机简明配置维护手册天图科技2004-12-103750交换机(EMI)简明配置维护手册目录说明 (3)产品特性 (3)配置端口 (6)配置一组端口 (6)配置二层端口 (8)配置端口速率及双工模式 (8)端口描述 (9)配置三层口 (10)监控及维护端口 (12)监控端口和控制器的状态 (12)刷新、重置端口及计数器 (14)关闭和打开端口 (15)配置VLAN (16)理解VLAN (16)可支持的VLAN (17)配置正常范围的VLAN (17)生成、修改以太网VLAN (18)删除VLAN (19)将端口分配给一个VLAN (20)配置VLAN Trunks (21)使用STP实现负载均衡 (24)3750交换机(EMI)简明配置维护手册说明本手册只包括日常使用的有关命令及特性产品特性Cisco Catalyst 3750系列交换机产品概述思科新推出的Cisco Catalyst 3750系列交换机是一个创新的产品系列,它结合业界领先的易用性和最高的冗余性,里程碑地提升了堆叠式交换机在局域网中的工作效率。
这个新的产品系列采用了最新的思科StackWise技术,不但实现高达32Gbps的堆叠互联,还从物理上到逻辑上使若干独立交换机在堆叠时集成在一起,便于用户建立一个统一、高度灵活的交换系统--就好像是一整台交换机一样。
这代表了堆叠式交换机新的工业技术水平和标准。
对于中型组织和企业分支机构而言,Cisco Catalyst 3750系列可以通过提供配置灵活性,支持融合网络模式,已经自动配置智能化网络服务,降低融合应用的部署难度,适应不断变化的业务需求。
此外,Cisco Catalyst 3750系列针对高密度千兆位以太网部署进行了专门的优化,其中包含多种可以满足接入、汇聚或者小型网络骨干网连接需求的交换机。
图1 Cisco Catalyst 3750系列交换机配置●Cisco Catalyst 3750G-24TS--24个以太网10/100/1000端口和4条SFP上行链路●Cisco Catalyst 3750G-24T--24个以太网10/100/1000端口●Cisco Catalyst 3750-48TS--48个以太网10/100端口和4条SFP上行链路●Cisco Catalyst 3750-24TS--24个以太网10/100端口和2条小型可插拔(SFP)上行链路3750交换机(EMI)简明配置维护手册Cisco Catalyst 3750系列可以使用标准多层软件镜像(SMI)或者增强多层软件镜像(EMI)。
INCHANGE Semiconductor STP75NF75 说明书

现货库存、技术资料、百科信息、热点资讯,精彩尽在鼎好!INCHANGE Semiconductor isc Product Specification isc N-Channel MOSFET Transistor STP75NF75FEATURES·Drain Current –I D= 80A@ T C=25℃·Drain Source Voltage-: V DSS= 75V(Min)·Static Drain-Source On-Resistance: R DS(on) = 0.011Ω(Max)DESCRIPTIONSuitable as primary switch in advanced high-efficiency, high-frequency isolated DC-DC converters for Telecom and Computerapplications. It is also intended for any application with low gatedrive requirements .APPLICATIONS·Solenoid and relay drivers·DC motor control·DC-DC converters DC·Automotive environmentABSOLUTE MAXIMUM RATINGS(T a=25℃)SYMBOL PARAMETER VALUE UNITV DSS Drain-Source Voltage 75 VV GS Gate-Source Voltage-Continuous ±20 VI D Drain Current-Continuous 80 AI DM Drain Current-Single Pluse (t p≤10μs) 320 AWP D Total Dissipation @T C=25℃ 300T J Max. Operating Junction Temperature 175 ℃T stg Storage Temperature -55~175℃THERMAL CHARACTERISTICSUNITSYMBOL PARAMETER MAXR th j-c Thermal Resistance, Junction to Case 0.5 ℃/WR th j-a Thermal Resistance, Junction to Ambient 62.5 ℃/WINCHANGE Semiconductor isc Product Specificationisc N-Channel MOSFET Transistor STP75NF75ELECTRICAL CHARACTERISTICST C=25℃ unless otherwise specifiedSYMBOL PARAMETER CONDITIONS MINMAXUNIT V(BR)DSS Drain-Source Breakdown Voltage V GS= 0; I D= 0.25mA 75 VV GS(th)Gate Threshold Voltage V DS= V GS; I D= 0.25mA 2 4 VR DS(on)Drain-Source On-Resistance V GS= 10V; I D= 40A 0.011ΩI GSS Gate-Body Leakage Current V GS= ±20V;V DS= 0 ±100nAI DSS Zero Gate Voltage Drain Current V DS= 75V; V GS= 0V DS= 75V; V GS= 0; T j= 125℃110μAV SD Forward On-Voltage I S= 80A; V GS=01.5V ·。
QD75系列Mitsubishi通用可编程逻辑控制器用户手册说明书
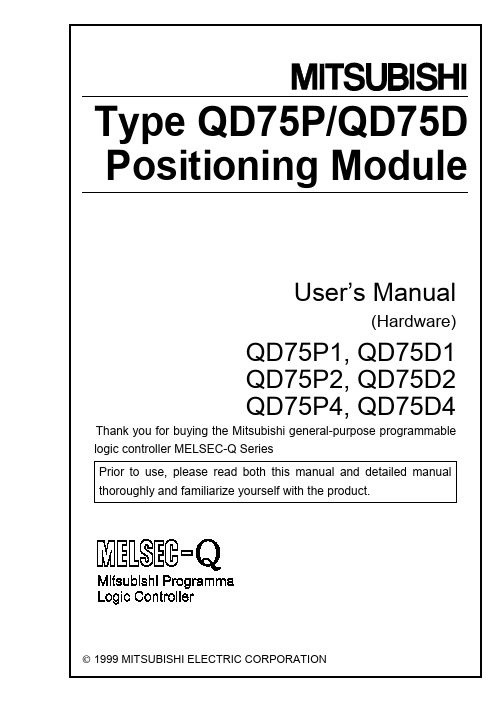
Type QD75P/QD75D Positioning ModuleUser’s Manual(Hardware)QD75P1, QD75D1QD75P2, QD75D2QD75P4, QD75D4 Thank you for buying the Mitsubishi general-purpose programmable logic controller MELSEC-Q SeriesPrior to use, please read both this manual and detailed manual thoroughly and familiarize yourself with the product.1999 MITSUBISHI ELECTRIC CORPORATIONA-1! SAFETY PRECAUTIONS !(Always read before starting use)When using this equipment, thoroughly read this manual. Also pay careful attention to safety and handle the module properly.These precautions apply only to this equipment.Refer to the User’s Manual of the CPU module to use for a description of the PLC system safety precautions.These "Safety Precautions" classify the safety precautions into two categories:"DANGER" and "CAUTION".Procedures which may lead to a dangerous condition and cause death or serious injury, if not carried out properly.Procedures which may lead to a dangerous condition and cause superficial to medium injury, or physical damage only, if not carried out properly.Depending on circumstances, procedures indicated by CAUTION may also be linked to serious results.In any case, it is important to follow the directions for usage.Store this manual in a safe place so that you can take it out and read it whenever necessary. Always forward it to the end user.[INSTALLATION PRECAUTION]CAUTION! Use the PLC in an environment that meets the general specifications contained in CPU module User's Manual to use.Using this PLC in an environment outside the range of the general specifications may cause electric shock, fire, malfunction, and damage to or deterioration of the product.! When installing the module, securely insert the module fixing tabs into the mounting holes of the base module while pressing the installation lever located at the bottom of the module downward.Improper installation may result in malfunction, breakdown or the module coming loose and dropping.Securely fix the module with screws if it is subject to vibration or shock during use.Tighten the screws within the range of specified torque.If the screws are loose, it may cause the module to fallout or malfunction.If the screws are tightened too much, it may cause damage to the screw and/or the module, resulting in fallout or malfunction.! Switch all phases of the external power supply off when mounting or removing the module.Not doing so may cause damage to the module.! Do not directly touch the conductive area or electronic components of the module.Doing so may cause malfunction or failure in the module.[WIRING PRECAUTION]CAUTION! Check the layout of the terminals and then properly route the wires to the module.! Solder connectors for external device properly.Insufficient soldering may cause malfunction.! Be careful not to let foreign matter such as sawdust or wire chips get inside the module.These may cause fires, failure or malfunction.! The top surface of the module is covered with protective film to prevent foreign objects such as cable offcuts from entering the module when wiring.Do not remove this film until the wiring is complete.Before operating the system, be sure to remove the film to provide adequate ventilation. ! Securely connect the connectors for the drive module to the connectors on the module and firmly tighten the two screws.! Be sure to fix cables leading from the module by placing them in a duct or clamping them.Cables not placed in the duct or without clamping may hang or shift, allowing them to be accidentally pulled, which may cause a module malfunction and cable damage.! When removing the cable or power supply cable from the module, do not pull the cable.When removing the cable with a connector, hold the connector on the side that isconnected to the module.Pulling the cable that is still connected to the module may cause malfunction or damage to the module or cable.! The cable used for connecting the QD75 external input/output signal and the drivemodule should not be routed near or bundled with the main circuit cable, power cable and/or other such load-carrying cables other than those for the PLC. These cables should be separated by at least 100 mm (3.94 in.). They can cause electricalinterference, surges and inductance that can lead to mis-operation.A-2Revisions* The manual number is noted at the lower left of the back cover. Print Date*Manual Number RevisionOct., 1999IB(NA)-0800063-A First editionFeb., 2000IB(NA)-0800063-B Addition"Confirmation to EMC directive"Jun., 2001IB(NA)-0800063-C ModificationAbout Manuals, Conformation to the EMCDirective and Low Voltage Instruction,2. Performance Specification, 4. PartIdentification Nomenclature, 5.Wiring Nov., 2001IB(NA)-0800063-D Addition1. Overview,2. PerformanceSpecifications, 4. Part IdentificationNomenclature, 5.2 External Interface, 5.3Wiring of the differential driver commonterminal, 6. External DimensionsThis manual confers no industrial property rights or any rights of any other kind, nor does it confer any patent licenses. Mitsubishi electric Corporation cannot be held responsiblefor any problems involving industrial property rights which may occur as a result of using the contents noted in this manual.1999 MITSUBISHI ELECTRIC CORPORATIONA-3CONTENTS1. Overview (1)2. Performance Specifications (2)3. Handling (3)3.1 Handling Precautions (3)4. Part Identification Nomenclature (4)5. Wiring (6)5.1 Wiring Precautions (6)5.2 External Interface (8)5.3 Wiring of the differential driver common terminal (10)6. External Dimensions (11)About ManualsThe following manuals are related to this product.Referring to this list, please request the necessary manuals.Related ManualManual nameManual No. (Model code)Type QD75P/QD75D Positioning Module User’s Manual SH-080058(13JR09)GX Configurator-QP Version 2 Operating Manual (SW2D5C-QD75P-E)SH-080172 (13JU19)Conformation to the EMC Directive and Low Voltage InstructionFor details on making Mitsubishi PLC conform to the EMC directive and low voltage instruction when installing it in your product, please refer to Chapter 3, "EMC Directive and Low Voltage Instruction" of the using PLC CPU module User's Manual(Hardware).The CE logo is printed on the rating plate on the main body of the PLC that conforms to the EMC directive and low voltage instructionTo make this product conform to the EMC directive and low voltage instruction, please refer to Chapter 5 “Wiring”.A-41. OverviewThis manual explains how to handle the Positioning Module, model numbers QD75P1, QD75P2, QD75P4, QD75D1, QD75D2 and QD75D4 (hereinafter collectively referred to as the QD75).After unpacking the QD75, please verify that the corresponding product as listed below is enclosed in the package.Model name Description Quantity QD75P1QD75P1 Positioning Module (1-axis open-collector output system)1 QD75P2QD75P2 Positioning Module (2-axes open-collector output system)1 QD75P4QD75P4 Positioning Module (4-axes open-collector output system)1 QD75D1 Positioning Module (1-axis differential driver output system)1 QD75D1Differential driver common terminal1QD75D2 Positioning Module (2-axes differential driver output system)1 QD75D2Differential driver common terminal1QD75D4 Positioning Module (4-axes differential driver output system)1 QD75D4Differential driver common terminal1A differential driver common terminal is packed with the QD75D1, QD75D2 and QD75D4.The user should arrange for a connector for external wiring since it is not provided in the package.* Connector type" A6CON1 (Soldering type, straight out)" A6CON2 (Crimping type, straight out)" A6CON4 (Soldering type, usable for straight out and diagonal out)* A6CON2 crimping tool" Model name: FCN-363T-T005/H" Supplier’s offices :" FUJITSU TAKAMISAWA AMERICA,INC.250E Caribbean Drive Sunnyvale, CA 94089 U.S.ATel: (1-408)745-4900" FUJITSU TAKAMISAWA EUROPE B.V.Jupiterstaat 13-15, our 2132 Hoofddorp, The NetherlandTel: (31)23-5560910" FUJITSU TAKAMISAWA EUROPE B.V. Zweiniederlassung Deutschland Schatzbogen 86 D-81829 Munchen GermanyTel: (49)89-42742320" FUJITSU TAKAMISAWA EUROPE (UK)Network House, Morres Drive, Maidenhead, Berkshire, SL6 4FHUnited KingdomTel: (44)1628-504600" FUJITSU TAKAMISAWA EUROPE B.V.127 Chemin Des Bassins, Europarc, Cleteril 94035 Cleterll 94035FranceTel: (33)145139940" FUJITSU TAKAMISAWA ASIA PACIFIC PTE LIMITED102E Pasir Panjang Road, #04-01 Citilink Warehouse Complex,Singapore 118529Tel: (65)375-8560" FUJITSU TAKAMISAWA HONG KONG CO., LTD.Suite 913 Ocean Centre, 5 Canton Road, TST, Kowloon, Hong KongTel: (852)2881-849512. Performance Specifications(1) The performance specifications for the QD75P1, QD75P2 and QD75P4SpecificationItemQD75P1QD75P2QD75P4 Number of axes 1 axis 2 axes 4 axes Maximum output pulsecount200 kpulse/sMaximum connectiondistance between servos2m (6.56ft)Applicable wire size 0.3 mm2 (when A6CON1 is used), AWG#24 (when A6CON2 is used), AWG#23 (when A6CON4 is used)Applicable connector A6CON1, A6CON2, A6CON4 (sold separately)Number of I/O occupied points32 points(I/O assignment: 32 points for intelligent function module )5 V DC currentconsumption0.40A0.46A0.58A Flash ROM write count Max. 100000 timesWeight0.15kg (0.33lb.)0.15kg (0.33lb.)0.16kg (0.35lb.)(2) The performance specifications for the QD75D1, QD75D2, and QD75D4SpecificationItemQD75D1QD75D2QD75D4 Number of axes 1 axis 2 axes 4 axes Maximum output pulsecount1 Mpulse/sMaximum connectiondistance between servos10m (32.81ft)Applicable wire size 0.3 mm2 (when A6CON1 is used), AWG#24 (when A6CON2 is used), AWG#23 (when A6CON4 is used)Applicable connector A6CON1, A6CON2, A6CON4 (sold separately)Number of I/O occupied points32 points(I/O assignment: 32 points for intelligent function module)DC5V current consumption0.52A0.56A0.82A Flash ROM write count Max. 100000 timesWeight0.15kg (0.33lb.)0.15kg (0.33lb.)0.16kg (0.35lb.) For the general specifications of the QD75, see User's Manual for CPU module used. (3) Differential driver common terminal specifications (QD75D1, QD75D2,QD75D4 only)Applicable wire size12AWGSolid wire: 0.2 to 0.8 mm2 2 pcs.Rated multiple wireconnection size Stranded wire: 0.2 to 0.8 mm2 2 pcs.Screw tightening torque50N·cm23. HandlingCAUTION! Use the PLC in an environment that meets the general specificationscontained in CPU module User's Manual to use.Using this PLC in an environment outside the range of the generalspecifications may cause electric shock, fire, malfunction, and damage to or deterioration of the product.! When installing the module, securely insert the module fixing tabs into the mounting holes of the base module while pressing the installation leverlocated at the bottom of the module downward.Improper installation may result in malfunction, breakdown or dropping out of the module.Securely fix the module with screws if it is subject to vibration or shockduring use.Tighten the screws within the range of specified torque.If the screws are loose, it may cause fallout or malfunction.If the screws are tightened too much, it may cause damage to the screw and/or the module, resulting in fallout or malfunction.! Switch all phases of the external power supply off when mounting orremoving the module.Not doing so may cause damage to the module.! Do not directly touch the conductive area or electronic components of the module.Doing so may cause malfunction or failure in the module.3.1 Handling Precautions(1) Since the module case is made of resin, do not drop it or subject it tostrong impact.(2) The module can easily be secured to the base unit using the hookslocated at the top of the module. However, if the module is to be placed in an area that is subject to strong vibration or impact, we recommend that it is secured with module mounting screws (to be provided by the user). In this case, tighten the module mounting screws within the following torque range.Module mounting screws (M3 × 12): Tightening torque range is from 36 to48 N⋅cm.344. Part Identification Nomenclature(1) Part identification nomenclature (a) For QD75P4(b) For QD75D42)1)3)Number NameNumber Name1)LED Display3)Differential driver common terminal2)External device connector(The QD75P1, QD75P2, QD75D1and QD75D2 have the right-hand side connector only.)(2) LED display contentsDetails of indicationPoints to be confirmedErrorRUN ##AX1#AX2#AX3ERR.##AX4Extinguishment of RUN LED The hardware is faulty or watch dog timer error occurs.RUN $#AX1#AX2#AX3ERR.##AX4Lighting of RUN LED,Extinguishment of ERR. LED The module is normal.RUN $#AX1#AX2#AX3ERR.$#AX4Lighting of ERR. LEDSystem errorRUN $#AX1#AX2#AX3ERR.##AX4Extinguishment of AX1 to AX4 LEDs During axis stop,during axis standbyRUN $$AX1#AX2#AX3ERR.##AX4Lighting of AX1 (Same even if the other axis is lit)During axis operation RUN $%AX1#AX2#AX3ERR.% #AX4Flashing of ERR. LED Flashing of AX1 LED(Same even if the other axis flashes)Axis error QD75 4RUN ERR.AX4AX3AX2AX1RUN $$AX1$AX2$AX3ERR.$$AX4Lighting of all LEDsThe hardware is faultyThe symbols in the Display column indicate the following statuses: : Turns OFF, : Illuminates, : Flashes5(3) External device connector signal layoutAxis 4 (AX4)Axis 3 (AX3)Axis 2 (AX2)Axis 1 (AX1)Pin layoutPinNo.Signal name PinNo.Signal name PinNo.Signal name PinNo.Signal name 2B20Vacant 2A20Vacant 1B20PULSER B-1A20PULSER B+2B19Vacant2A19Vacant1B19PULSER A-1A19PULSER A+PULSE COM PULSE COM PULSE COM PULSE COM *32B18PULSE R-*32A18PULSE R-*31B18PULSE R-*31A18PULSE R-PULSE R PULSE R PULSE R PULSE R *32B17PULSE R+*32A17PULSE R+*31B17PULSE R+*31A17PULSE R+PULSE COM PULSE COM PULSE COM PULSE COM *32B16PULSE F-*32A16PULSE F-*31B16PULSE F-*31A16PULSE F-PULSE F PULSE F PULSE F PULSE F *32B15PULSE F+*32A15PULSE F+*31B15PULSE F+*31A15PULSE F+2B14CLRCOM 2A14CLRCOM 1B14CLRCOM 1A14CLRCOM 2B13CLEAR 2A13CLEAR 1B13CLEAR 1A13CLEAR 2B12RDYCOM 2A12RDYCOM 1B12RDYCOM 1A12RDYCOM 2B11READY 2A11READY 1B11READY 1A11READY 2B10PGOCOM 2A10PGOCOM 1B10PGOCOM 1A10PGOCOM 2B9PGO52A9PGO51B9PGO51A9PGO52B8PGO242A8PGO241B8PGO241A8PGO242B7COM 2A7COM 1B7COM 1A7COM 2B6COM 2A6COM 1B6COM 1A6COM 2B5CHG 2A5CHG 1B5CHG 1A5CHG 2B4STOP 2A4STOP 1B4STOP 1A4STOP 2B3DOG 2A3DOG 1B3DOG 1A3DOG 2B2RLS 2A2RLS 1B2RLS 1A2RLS B20B19B18B17B16B15B14B13B12B11B10B9B8B7B6B5B4B3B2B1A20A19A18A17A16A15A14A13A12A11A10A9A8A7A6A5A4A3A2A12B1FLS2A1FLS1B1FLS1A1FLS*1: The pin numbers represented by 1 indicate the pin numbers for theright side connector, while the pin numbers represented by 2 indicate the pin numbers for the left side connector.*2: For QD75P1 or QD75D1, 1B1 to 1B18 will be “vacant.”*3: When signal names are shown in upper and lower rows, the upper rowshows the signal name for the QD75P1, QD75P2 and QD75P4 and the lower row shows the signal name for the QD75D1, QD75D2 and QD75D4.65. Wiring5.1 Wiring Precautions(1) If cables to connect to QD75 absolutely must be positioned near (within 100 mm) the power line, use a general shielded cable. The shield must be grounded on the QD75 side.(The shield must be grounded onthe QD75 side.)The length between the connector and the shielded cables should be the shortest possible.[Processing example of shielded cables]Remove the covering from all shielded cables and bindthe appeared shield with a conductive tape.(2) The shielded cable for connecting QD75 can be secured in place.If the shielded cable is not secured, unevenness or movement of theshielded cable or careless pulling on it could result in damage to theQD75 or drive unit or shielded cable or defective cable connections could cause mis-operation of the unit.(3) To make this product conform to the EMC directive and low voltageinstruction, be sure to use of a AD75CK type cable clamp (manufactured by Mitsubishi Electric) for grounding to the control box.Using the AD75CK, you can tie four cables of about 7mm outsidediameter together for grounding.785.2 External InterfaceThe internal circuits of interface for connecting external devices to the QD75are shown by the schematic diagrams in the tables below (for the QD75P1 and QD75D1).(1) Input (common to QD75P1 and QD75D1)External wiringPin number Internal circuit Signal nameWiring requirement*11A1Upper-limit LS signal FLS 1A2Lower-limit LS signalRLS 1A3Near-point dog signal DOG 1A4Stop signal STOP 1A5Externalcommand signal CHG 1A61A7Common COM 1A19PULSER A+(+)1B19Manual pulse generator A phasePULSER A-(-)1A20PULSER B+(+)1B20Manual pulse generator B phasePULSER B-(-)1A11Drive unit Ready READY 1A12Drive unit Ready common RDY COM 1A81A9Zero signal PG024PG05When not using higher limit LS5 VAB0VManual pulse generator (MR-HDP01)24 V DC5 V DCWhen not using lower limit LS*21A10Zero signal commonPG0 COM*1: In the column indicating whether wiring is required, the symbol means"wiring is required" and means "wiring is required as needed."*2: Either polarity can be connected to the common (COM).(2) Output (for QD75P1)External wiringPinnumberInternal circuit Signal nameWiringrequirement * 1A13Deviationcounter clearCLEAR1A14Common CLEAR COM1A15PULSE F1A16CWA phasePULSE PULSE COM1A17PULSE R1A18CCWB phaseSIGN PULSE COM(3) Output (for QD75D1)External wiringPinnumberInternal circuit Signal nameWiringrequirement * 1A13Deviationcounter clearCLEAR1A14Common CLEAR COM1A15PULSE F+1A16CWA phasePULSE PULSE F-1A17PULSE F+1A18CCWB phaseSIGN PULSE F-——Differentialdrivercommonterminal—*: In the column indicating whether wiring is required, the symbol means "wiring is required" and means "wiring is required as needed."95.3 Wiring of the differential driver common terminalWhen the differential driver output type (QD75D1/QD75D2/QD75D4) is used, an inter-common potential difference may occur between the differential driver common terminal and the differential receiver common terminal of the drive unit.To eliminate an inter-common potential difference, connect between the differential driver common terminal of the QD75D1/QD75D2/QD75D4 and the differential receiver common terminal of the drive unit.When the common terminal of the drive unit is a photocoupler connection type, it need not be connected to the differential driver common terminal of theQD75D1/QD75D2/QD75D4 since an inter-common potential difference does not exist. (For the driver unit specifications, refer to the manual of the drive unit used.)The following gives an example of wiring the differential driver common terminal of the QD75D1/QD75D2/QD75D4.Up to two wires can be connected to one differential driver common terminal. (Refer to "2. Performance Specifications" for details.)10116. External Dimensions(1) QD75P1/QD75P2/QD75P4QD75P1QD75P2QD75P4QD75P2QD75P4AX1AX2AX3AX4QD75P1AX1AX2AX1RUN ERR.AX4AX3AX2AX1RUNERR.AX2AX1RUNERR.AX127.4(1.08)90 (3.54)136 (5.35)46 (1.81)98 (3.86)Unit : mm (inch)12(2) QD75D1/QD75D2/QD75D4QD75D1QD75D2QD75D4QD75D2QD75D4AX1AX2AX3AX4QD75D1AX1AX2AX1RUN ERR.AX4AX3AX2AX1RUNERR.AX2AX1RUNERR.AX127.4(1.08)90 (3.54) 136 (5.35)46 (1.81)98 (3.86)12 (0.47)Unit : mm (inch)WarrantyMitsubishi will not be held liable for damage caused by factors found not to be the cause of Mitsubishi; machine damage or lost profits caused by faults in the Mitsubishi products;damage, secondary damage, accident compensation caused by special factorsunpredictable by Mitsubishi; damages to products other than Mitsubishi products; and to other duties.For safe use" This product has been manufactured as a general-purpose part for general industries,and has not been designed or manufactured to be incorporated in a device or system used in purposes related to human life." Before using the product for special purposes such as nuclear power, electric power,aerospace, medicine or passenger movement vehicles, consult with Mitsubishi." This product has been manufactured under strict quality control. However, when installing the product where major accidents or losses could occur if the product fails, install appropriate backup or failsafe functions in the system.U.S.A Mitsubishi Electric Automation Inc. 500 Corporate Woods Parkway Vernon Hills, IL 60061 Tel : +1-847-478-2100Brazil MELCO-TEC Rep. Com.e Assessoria Tecnica Ltda. Av. Rio Branco, 123-15 ,and S/1507, Rio de Janeiro, RJ CEP 20040-005, Brazil Tel : +55-21-221-8343Germany Mitsubishi Electric Europe B.V. German Branch Gothaer Strasse 8 D-40880 Ratingen, GERMANY Tel : +49-2102-486-0U.K Mitsubishi Electric Europe B.V. UK Branch Travellers Lane, Hatfield, Herts., AL10 8XB,UK Tel : +44-1707-276100Italy Mitsubishi Electric Europe B.V. Italian Branch Centro Dir. Colleoni, Pal. Perseo - Ingr.2 Via Paracelso 12, 20041 Agrate B., Milano, Italy Tel:+39-039-60531Spain Mitsubishi Electric Europe B.V. Spanish Branch Carretera de Rubi 76-80 08190 - Sant Cugat del Valles, Barcelona, Spain Tel:+34-935-653135South Africa Circuit Breaker Industries LTD. Private Bag 2016, Isando 1600, Johannesburg, South Africa Tel : +27-11-928-2000Hong Kong Ryoden Automation Ltd. 10th Floor, Manulife Tower, 169 Electric Road, North Point, HongKong Tel : +852-2887-8870China Ryoden International Shanghai Ltd. 3F Block5 Building Automation Instrumentation Plaza 103 Cao Bao Rd. Shanghai 200233 China Tel : +86-21-6475-3228Taiwan Setsuyo Enterprise Co., Ltd. 6F., No.105 Wu-Kung 3rd.RD, Wu-Ku Hsiang, Taipei Hsine, Taiwan Tel : +886-2-2299-2499Korea HAN NEUNG TECHNO CO.,LTD. 1F Dong Seo Game Channel Bldg., 660-11, Deungchon-dong Kangsec-ku, Seoul, Korea Tel : +82-2-3668-6567Singapore Mitsubishi Electric Asia Pte, Ltd. 307 ALEXANDRA ROAD #05-01/02, MITSUBISHI ELECTRIC BUILDING SINGAPORE 159943 Tel : +65-473-2480Thailand F. A. Tech Co.,Ltd. 898/28,29,30 S.V.City Building,Office Tower 2,Floor 17-18 Rama 3 Road, Bangkpongpang, Yannawa, Bangkok 10120 Tel : +66-2-682-6522Indonesia P.T. Autoteknindo SUMBER MAKMUR Jl. Muara Karang Selatan Block A Utara No.1 Kav. No.11 Kawasan Industri/ Pergudangan Jakarta - Utara 14440 Tel : +62-21-663-0833India Messung Systems Put,Ltd. Electronic Sadan NO:111 Unit No15, M.I.D.C BHOSARI,PUNE-411026 Tel : +91-20-7128927Australia Mitsubishi Electric Australia Pty. Ltd. 348 Victoria Road, PostalBag, No 2, Rydalmere, N.S.W 2116, Australia Tel : +61-2-9684-7777Country/Region Sales office/Tel Country/Region Sales office/TelWhen exported from Japan, this manual does not require application to the Ministry of Economy, Trade and Industry for service transaction permission.Specifications subject to change without notice.Printed in Japan on recycled paper.HEAD OFFICE : 1-8-12, OFFICE TOWER Z 14F HARUMI CHUO-KU 104-6212, JAPANNAGOYA WORKS : 1-14, YADA-MINAMI5, HIGASHI-KU, NAGOYA, JAPAN。
L7585G资料

Data SheetSeptember 2001 L7585G Full-Feature, Low-Power SLIC and SwitchFeaturess Low active powers Quiet tip/ring polarity reversals Distortion-free on-hook transmissions35 V to 60 V power supply operations14 operating states:— Forward battery active— Reverse battery active— Ground start (3)— Forward battery ring open— Reverse battery ring open— Reverse battery tip open— High impedance— Ringing (2)— Low current (2)— Disconnects Self-test in all operating statess Independent, adjustable ac and dc parameters:— Switchhook detector threshold— Loop current limit— dc feed resistance— Termination impedances Integrated ringing access relays Integrated test-in relays Integrated relay drivers Integrated ring trip detectors Thermal protections44-pin, metric quad flat package (MQFP) DescriptionThe L7585G Full-Feature, Low-Power Subscriber Loop Interface Circuit (SLIC) and Switch integrates the battery feed, test access relay, and ringing relay that are necessary to interface a codec to the tip and ring of a subscriber loop into one low-power, low-cost package. It is built using a 90V complementary bipo-lar (CBIC) process and a 320V Bipolar-CMOS-DMOS (BCDMOS) process. The device is available in a 44-pin MQFP package.The device can be connected directly to the Agere Systems Inc. T8531/T8536 16-Channel Programma-ble Codec Chip Set without the need for any ac inter-face components.Data SheetSeptember 2001 L7585G Full-Feature, Low-Power SLIC and SwitchTable of ContentsContents Page Features (1)Description (1)Architectural Diagram (3)Pin Information (4)Operating States (7)Forward Battery Active State (7)Ground Start/Tip Open State (7)Ground Start/Tip Ground State (8)Forward Battery Ring Open State (8)Ringing States (2) (8)Disconnect State (8)Forward Battery Low-Current Active State (8)High-Impedance State (8)Reverse Battery Active State (8)Reverse Battery Tip Open State (8)Ground Start/Tip Amplifier State (9)Reverse Battery Ring Open State (9)Reverse Battery Low-Current Active State (9)Absolute Maximum Ratings (T A = 25 °C) (9)Electrical Characteristics (10)On-State Switch V-I Characteristics (17)Applications (18)Tip/Ring Protection (18)NDET Under Fault Conditions (18)Power, Clocking, and Layout (18)Ring Trip (19)False On-Hook Transients (19)Application Diagram (20)Outline Diagram (21)44-Pin MQFP (21)Ordering Information .................................................22Figures Page Figure 1. Architectural Diagram (3)Figure 2. 44-Pin Diagram (MQFP) (4)Figure 3. On-State Switch V-I Characteristics (17)Figure 4. 16-Channel Line Card Solution (20)Tables Page Table 1. Pin Descriptions (5)Table 2. B0—B3 Input State Coding (7)Table 3. B4—B5 Input State Coding (7)Table 4. Operating Conditions and Powering (10)Table 5. Ring Trip Detector (10)Table 6. Battery Feed Characteristics (11)Table 7. Analog Signal Pins (12)Table 8. Transmission Characteristics (13)Table 9. Data Interface and Logic (Logic Inputs[CLK, NCS, and B0—B5] andOutputs [NDET]) (14)Table 10. Timing Requirements (CLK, B0—B5,and NCS) (14)Table 11. Relay Driver (RDO) (14)Table 12. Ringing Return Access Switch (SW1) (15)Table 13. Test-In Access Switches(SW3 and SW6) (15)Table 14. Tip and Ring Break Switches(SW2 and SW4) (16)Table 15. Tip and Ring Feedback Switches(SW2a and SW4a) (16)Table 16. Ringing Access Switch (SW5) (17)2Agere Communications Inc.Data SheetSeptember 2001L7585G Full-Feature, Low-Power SLIC and SwitchAgere Communications Inc.34Agere Communications Inc.Data Sheet September 2001L7585G Full-Feature, Low-Power SLIC and SwitchPin Information12-2571H (F)Figure 2. 44-Pin Diagram (MQFP)I P R O GDGND V CCD B0B1B2BGND FB1FB2V BAT V SP NCS NDET DGND134567*********4241403938373635344312141516171819202122133331302928272625242332V BAT B3V BAT BGND ITR VITR TXI CF1CLK A G N DV C C AR C V NR C V PV R T X L C T HV T X D C O U TD C RC F 2B 4T R N GR T SP RB 5P TT T IR T IR R N GR S WR D OAgere Communications Inc.5Data SheetSeptember 2001L7585G Full-Feature, Low-Power SLIC and SwitchPin Information (continued)Table 1. Pin Descriptions Note:On the printed-wiring board (PWB), make the leads to BGND and V BAT as wide as possible for thermal and electrical reasons. Also, max-imize the amount of PWB copper on all leads connected to this device for the lowest operating temperature.Pin Symbol Type Name/Function1CF1I/O Filter Capacitor 1. Connect a 0.22 µF, 100 V capacitor from this pin to pin CF2.2FB2IForward Battery Slowdown 2. A capacitor from FB1 to AGND and from FB2 to AGND will ramp the polarity reversal transition when quiet polarity reversal is required. If not needed, the pin can be left open.3FB1IForward Battery Slowdown 1. A capacitor from FB1 to AGND and from FB2 to AGND will ramp the polarity reversal transition when quiet polarity reversal is required. If not needed, the pin can be left open.4BGND —Battery Ground. Ground return for the battery (V BAT ) supply.5V BAT —Battery Supply. Negative high-voltage power supply.6V BAT —Battery Supply. Negative high-voltage power supply.7V SP —+10 V Supply. +10 V bias supply for switch circuitry.8NCSINot Channel Select. A low-to-high transition on this logic input stores the data on pins B0—B5 into the input latches on the SLIC. When NCS is either high or low, the SLIC is unaffected by data on pins B0—B5.9CLK I Clock. Clock input.10NDETONot Detect. When low, this logic output indicates either a ring trip or an off-hook condition, depending on the input state of the SLIC. If either the BCDMOS portion or CBIC portion of this device enters thermal shutdown, NDET will be forced low.11DGND —Digital Ground. Ground return for V CCD and relay driver flyback current.12RDO O Relay Driver. This output drives an external relay. RDO is low (relay operated) when a low input on B5 is latched into the SLIC.13RTS I Ring Trip Sense. Sense input for the ring trip detector.14RSW O Ring Lead Ringing Access Switch. Ringing relay connects this pin to pin RRNG. Con-nect this pin to pin PR through a 500 Ω current-limiting resistor.15RRNG I Ring Lead Ringing Supply. Connect this pin to the ringing supply.16PR I/O Protected Ring. The output of the ring driver and input to the transmit current sense cir-cuit. Connect to the ring of the loop through overvoltage protection.17RTI I Ring Lead Test-In. Test-in relay connects this pin to PR. Connect RTI to the ring lead of the test-in bus.18TTI I Tip Lead Test-In. Test-in relay connects this pin to PT. Connect TTI to the tip lead of the test-in bus.19PT I/O Protected Tip. The output of the tip driver and input to the transmit current sense circuit. Connect to the tip of the loop through overvoltage protection.20TRNG O Tip Lead Ringing Supply. Ringing relay connects this pin to PT. Connect TRNG to the ringing supply return.21B5IBit 5. B0—B5 determine the state of the SLIC. See Operating States.6Agere Communications Inc.Data Sheet September 2001L7585G Full-Feature, Low-Power SLIC and SwitchPin Information (continued)Table 1. Pin Descriptions (continued)Note:On the printed-wiring board (PWB), make the leads to BGND and V BAT as wide as possible for thermal and electrical reasons. Also, max-imize the amount of PWB copper on all leads connected to this device for the lowest operating temperature.Pin Symbol Type Name/Function22B4I Bit 4. B0—B5 determine the state of the SLIC. See Operating States.23B3I Bit 3. B0—B5 determine the state of the SLIC. See Operating States.24B2I Bit 2. B0—B5 determine the state of the SLIC. See Operating States.25B1I Bit 1. B0—B5 determine the state of the SLIC. See Operating States.26B0I Bit 0. B0—B5 determine the state of the SLIC. See Operating States.27V CCD —+5 V Digital dc Supply. +5 V supply for logic and switch circuitry.28DGND —Digital Ground. Ground return for V CCD .29V BAT —Battery Supply. Negative high-voltage power supply.30BGND —Battery Ground. Ground return for the battery (V BAT ) supply.31ITR I Tip/Ring Current. A current output which is proportional to the differential current flowing from tip to ring. Connect a resistor from this pin to VITR.32VITR O Tip/Ring Voltage Output. The voltage at this output is directly proportional to the differ-ential tip/ring current. A resistor from this pin to ITR sets the gain.33TXI I Transmit ac Input. Connect a 0.1 µF capacitor from this pin to VITR.34VTX O Transmit ac Output Voltage. The ac voltage at this output is 7.2 times the ac voltage at pin TXI. The dc voltage is equal to the dc voltage on pin VRTX.35VRTX O Transmit ac Reference Voltage. The dc voltage at this output (2.4 V nominal) is the dc reference for the transmit signal output VTX.36RCVP I Receive ac Signal Input (Noninverting). This high-impedance input controls the ac dif-ferential voltage on tip and ring.37RCVN I Receive ac Signal Input (Inverting). This high-impedance input controls the ac differen-tial voltage on tip and ring.38AGND —Analog Ground. Ground return for V CCA .39V CCA —+5 V Analog dc Supply. +5 V supply for analog circuitry.40LCTH I Loop Closure Threshold Input. Connect a resistor to DC OUT to set the off-hook thresh-old.41I PROG I Current-Limit Program Input. A resistor to DC OUT sets the dc current limit.42DC OUT O dc Output. This output is a voltage that is directly proportional to the differential tip/ring current.43DCRIdc Resistance. Ground for dc feed resistance of 180 Ω, or short to DC OUT for 600Ω. In-termediate values can be set with a resistor divider from DC OUT to ground, the tap of which is connected to DCR.44CF2I/OFilter Capacitor 2. Connect a 0.1 µF, 100 V capacitor from this pin to AGND and a 0.22µF, 100 V capacitor from this pin to pin CF1.Data SheetSeptember 2001L7585G Full-Feature, Low-Power SLIC and SwitchOperating StatesThe L7585 has 14 operating states. These states are selected using 4 bits, B0—B3, according to the truth table shown in Table 2. The operation of the L7585 is undefined for unassigned states. Additionally, bit B4 independently operates the test-in access contacts so that all states are available for self-test; and bit B5 independently operates a relay driver, regardless of the status of bits B0—B4. All 6 bits are loaded via the par-allel data interface and chip select lead NCS.Table 2. B0—B3 Input State CodingTable 3. B4—B5 Input State Coding Forward Battery Active States Normal talk and forward battery feed state.s All circuits are powered up and active.s Pin PT is positive with respect to pin PR (forward bat-tery).s SW2, SW2a, SW4, and SW4a closed; SW1, SW3, SW5, and SW6 open.s NDET reflects the status of the switchhook detector. Ground Start/Tip Open States Ground start idle supervision state.s Ring lead continuity test state (tone injected at the receive port) in forward battery.s Same as forward battery active state, but with SW2 and SW2a open, and the tip drive amplifier powered down.s Pin PT is high impedance (>100 kΩ).s The ring current limit is approximately equal to the value programmed for the high-current active state current limit. Current limit is achieved by reducing the ring lead voltage only (see Table 6).s NDET indicates an off-hook when the ring current (flowing into PR) is twice the value programmed for the switchhook detector in the forward battery active state.B3B2B1B0State1111Forward Battery Active1110Ground Start/Tip Open1101Ground Start/Tip Ground1100Forward Battery Ring Open1011Ringing (Battery Backed)1010Disconnect State1001Forward Battery Low-CurrentActive State1000High Impedance0111Reverse Battery Active0110Reverse Battery Tip Open0101Ground Start/Tip Amplifier0100Reverse Battery Ring Open0011Ringing (Earth Backed)0010Unassigned0001Reverse Battery Low-CurrentActive State0000High ImpedanceBit StateB41Test-in contacts off.0Test-in contacts on.B51Relay driver off.0Relay driver on.Agere Communications Inc.7Data SheetSeptember 2001 L7585G Full-Feature, Low-Power SLIC and SwitchOperating States (continued)Ground Start/Tip Ground States Ground start busy supervision state.s Same as ground start/tip open state but with SW1 closed.Forward Battery Ring Open States Tip lead continuity test state (tone injected at the receive port) in forward battery.s Same as forward battery active state, but with SW4 and SW4a open, and the ring drive amplifier powered down.s Pin PR is high impedance (>100 kΩ).s Tip current limit is twice the low-current active state current limit.s NDET indicates an off-hook when the tip current (flowing out of PT) is twice the value programmed for the switchhook detector in the forward battery active state.Ringing States (2)s Normal ringing state.s Tip and ring drive amplifiers are powered down.s SW1 and SW5 closed; SW2, SW2a, SW3, SW4, SW4a, and SW6 open.s NDET reflects the status of the ring trip detector.s Bit B3 indicates whether the ringing voltage applied to the ringing bus is either battery backed (B3 = 1) or earth backed (B3 = 0). Although B3 has no direct effect on the state of the SLIC, it can be used by the ring trip detector to enhance ring trip detection.Disconnect States All circuits are powered up and active.s SW2, SW2a, SW4, and SW4a closed; SW1, SW3, SW5, and SW6 open.s PT and PR are at the same potential to deny current to the loop.Forward Battery Low-Current Active States Normal talk and forward battery feed state.s All circuits are powered up and active.s Pin PT is positive with respect to pin PR (forward bat-tery).s SW2, SW2a, SW4, and SW4a closed; SW1, SW3, SW5, and SW6 open.s NDET reflects the status of the switchhook detector.s Current limit is lowered to approximately 0.66 times the normal limit.High-Impedance States Disconnect state.s Tip and ring drive amplifiers are powered down (all bias currents off).s Pins PT and PR are high impedance (>100 kΩ).s SW1, SW2, SW2a, SW3, SW4, SW4a, SW5, and SW6 open.s NDET is undefined.Reverse Battery Active States Normal talk and reverse battery feed state.s Same as forward battery active state, but PR is posi-tive with respect to PT.Reverse Battery Tip Open States Ring lead continuity test state (tone injected at the receive port) in reverse battery.s SW2 and SW2a open and the tip drive amplifier pow-ered down.s Pin PT is high impedance (>100 kΩ).s Pin PR is held between –1.7 V and –2.3 V for PR currents less than ±20 mA. PR current limit is the SW4 break switch current limit (250 mA < I < 85 mA).s NDET indicates an off-hook when the ring current (flowing out of PR) is twice the value programmed for the switchhook detector in the reverse battery active state.8Agere Communications Inc.Data SheetSeptember 2001L7585G Full-Feature, Low-Power SLIC and SwitchOperating States (continued)Ground Start/Tip Amplifier States Current limiting is achieved by reducing ring lead voltage only. This state is the same as Ground Start/ Tip Open, but with SW2 and SW2A closed and the tip amplifier powered up.s Ring lead current limit is approximately the difference of the high-current active state limit and the current flowing out of the tip lead.s On-hook transmission not to exceed –3 dBm with up to 5 mA flowing out of the tip lead (maximum current flow into the tip lead is permissible). Larger signal and/or current may cause distortion.s NDET indicates an off-hook when the current flowing out of the tip plus the current flowing into the ring is twice the value programmed for the switchhook detector.Reverse Battery Ring Open States Tip lead continuity test state (tone injected at the receive port) in reverse battery.s Same as reverse battery active state, but with SW4 and SW4a open, and the ring drive amplifier powered down.s Pin PR is high impedance (>100 kΩ).s Tip current limit is twice the low-current active state current limit.s NDET indicates an off-hook when the tip current (flowing into PT) is twice the value programmed for the switchhook detector in the reverse battery active state.Reverse Battery Low-Current Active State s Normal talk and reverse battery feed state.s Same as forward battery active state, but PR is posi-tive with respect to PT.s Current limit is lowered to approximately 0.66 times the normal limit.Absolute Maximum Ratings (T A = 25 °C) Stresses exceeding the values listed under absolute maximum ratings may cause permanent damage to the device. This is an absolute stress rating only. Func-tional operation of the device at these or any other con-ditions in excess of those indicated in the operational sections of this data sheet is not implied. Exposure to absolute maximum rating conditions for extended peri-ods of time may adversely affect device reliability.Note:Analog voltages are referenced to AGND, digital (logic) volt-ages are referenced to DGND, and battery voltages are ref-erenced to BGND. The IC can be damaged unless allground connections are applied before and are removedafter all other connections. Furthermore, when powering thedevice, the user must guarantee that no external potentialcreates a voltage on any pin of the device that exceeds thedevice ratings. Some of the known examples of conditionsthat cause such potentials during powering are the following:1) an inductor connected to tip and ring that can force anovervoltage on V BAT through external components if theV BAT connection chatters; and 2) inductance in the V BATlead that could resonate with the V BAT filter capacitor tocause a destructive overvoltage.Parameter Value Unit +5 V dc Supplies (V CCA andV CCD)–0.5 to +7.0V +10 V dc Bias Supply (V SP)–0.5 to +15V Office Battery Supply (V BAT)–63 to +0.5V Logic Input Voltage–0.5 toV DDD + 0.5VLogic Input Clamp Diode Cur-rent, per Pin±20mALogic Output Voltage–0.5 toV DDD + 0.5VLogic Output Current, per Pin(excluding relay driver)±35mA Operating Temperature Range–40 to +125°C Storage Temperature Range–40 to +125°C Relative Humidity Range 5 to 95%RH Ground Potential Difference(BGND to AGND)±3VGround Potential Difference(DGND to AGND)±3VAgere Communications Inc.910Agere Communications Inc.Data Sheet September 2001L7585G Full-Feature, Low-Power SLIC and SwitchElectrical CharacteristicsIn general, minimum and maximum values are testing requirements. However, some parameters may not betested in production because they are guaranteed by design and device characterization. Typical values reflect the design center or nominal value of the parameter; they are for information only and are not a requirement. Minimum and maximum values apply across the entire temperature range (–40 °C to +85 °C) and entire battery range (–35 V to –60 V). Unless otherwise specified, typical is defined as 25 °C, V CCA = +5.0 V, V CCD = +5.0 V, V SP = +10 V, V BAT = –48 V. Positive currents flow into the device.*Not to exceed 26 grams of water per kilogram of dry air.†This parameter is not tested in production; it is guaranteed by design and device characterization.1. The ringing source may be either of the following:a)The ringing source consists of the ac and dc voltages added together (battery-backed ringing); the ringing return is ground. In this case,bit B3 will always be a 1 when ringing is applied.b)The ringing source consists of only the ac voltage (earth-backed ringing); the ringing return is the dc voltage. In this case, bit B3 willalways be a 0 when ringing is applied.2. NDET must also indicate ring trip when the ac ringing voltage is absent (<5 Vrms) from the ringing source.3. Pretrip ringing must not be tripped by a 10 k Ω resistor in parallel with an 8 µF capacitor applied across tip and ring.Table 4. Operating Conditions and PoweringParameterMin Typ Max Unit Temperature Range –40—85°C Humidity Range 5—95*%RH Supply Voltages:V CCA V CCD V SP V BATV CCA —V CCD D GND —A GND4.754.758.0–35——5.05.010–48—— 5.55.512.0–60±0.5±0.25V V V V V V Supply Currents (all states, no loop current):I CCA + I CCD (+5 V)IV SP (+10 V)I BAT (–48 V)——— 4.945–3.17.0200–4.0mA µA mA Total Power Dissipation (all states, no loop current)(V CC = +5 V; V SP = +10 V; V BAT = –48 V)—175200mWPower Supply Rejection (tip/ring and transmit)†:V CCA (500 Hz—3 kHz; 50 mVrms ripple)V CCD (500 Hz—3 kHz; 50 mVrms ripple)V SP (500 Hz—3 kHz; 250 mVrms ripple)V BAT (500 Hz—3 kHz; 50 mVrms ripple)3045454540———————dB dB dB dB Thermal †:Thermal Resistance (still air)Operating T JC————47155°C/W °CTable 5. Ring Trip DetectorParameterMin Typ Max Unit Voltage at input that will cause ring trip after appropriate zero crossings.±2.5±3±3.5V Voltage at input that will cause immediate ring trip.±12±15±18V Ringing Source 1:Frequency (f)dc Voltage ac Voltage 19–39.56020——28–57105Hz V Vrms Ring Trip (NDET = 0)2, 3:Loop Resistance Trip Time NDET Valid2000——————20080Ωms msAgere Communications Inc.11Electrical Characteristics (continued)Table 6. Battery Feed Characteristics1.The longitudinal current is independent of dc loop current.2.Current limit, I LIM , is programmed by a resistor, R PROG , from pin I PROG to pin DC OUT . R PROG = 1.667 x (I LIM – 4); R PROG in k Ω and I LIM in mA. The current limit versus loop voltage has a slope of 10 k Ω. The low-current mode current limit is approximately 0.66 times the high current limit. The ground start ring lead ground current limit is approximately equal to the high current limit and has a slope of about 5 k Ω.3. In transmission applications, for compliance with TR-57, ground start ring lead I-V characteristics at high battery, it is expected that the high-current active current limit will be set to 28 mA.4. Loop closure detector current, I LCD , is programmed by a resistor, RLCTH, from pin LCTH to pin DC OUT . RLCTH = 2.5 x I LCD ; RLCTH in k Ω and I LCD in mA. I LCD is the tip to ring (forward battery) or ring to tip (reverse battery) current at which the loop closure detector indi-cates an off-hook.5. dc feed resistance may be adjusted between 180 Ω and 600 Ω using a resistor divider between DC OUT and DCR. The open loop differen-tial voltage may also be increased by applying a negative voltage to pin DCR. See dc Gains, pin DCR.6. DC OUT gain depends on the resistor RGX1 from pin VITR to pin ITR. This gain assumes 8250 Ω, the recommended value. Positive cur-rent is defined as the differential current flowing from PT to PR.7. Positive voltage on pin DCR has no effect on the PT/PR voltage.8. At tip and ring, assuming 82.5 Ω protection resistors.9. At tip and ring with matched 82.5 Ω protection resistors when feedback is connected for either 600 Ω or 900 Ω termination impedance.ParameterSymbol Min Typ Max Unit Tip or Ring Drive Current =dc + Longitudinal + Signal Currents —65——mA ac Signal Current—10——mArms Longitudinal Current Capability per Wire 1—8.515—mArmsdc Loop Current Limit 2 (R LOOP = 100 Ω):I LIMProgrammability Range5—45mA Current Limit with V BAT = –51.5 V and R PROG = 64.9 k Ω444256mA Low-current Mode 2 (R LOOP = 100 Ω,V BAT = –51.5 V, and R PROG = 64.9 k Ω)2527.530mAGround Start Ring Grounded (R LOOP = 100 Ω) Current Limit 3:V BAT = –51.5 V, R PROG = 64.9 k Ω384347mA Loop Closure Current Detector Threshold 4Programming AccuracyI LCD ——±7%Open Loop Voltages (DCR = 0 V):Common-mode Voltage Differential Voltage ——|V BAT + 7.0|(V BAT + 1.8)/2|V BAT + 6.5|—|V BAT + 6.0|V V Disconnect State PT/PR Voltage|PT-PR|——±100mV Ground Start Ring Lead Open or Shorted to Ground:PT and CF1 Voltage —–1.7–2.0–2.3V dc Feed Resistance:DCR GroundedDCR Connected to DC OUT 5—130480150505170630ΩΩdc Gains:PT/PR Current to DC OUT Voltage 6:Forward Battery Reverse BatteryDCR Voltage 7 to PT/PR Differential Voltage —–1181183.13——3.33–1321323.53V/A V/A —Loop Resistance Range 8(3.17 dBm overload into 600 Ω):I LOOP = 20 mA at V BAT = –51.5 V—18901930—ΩLongitudinal to Metallic Balance—IEEE ® Std. 455:50 Hz to 1 kHz 1 kHz to 3 kHz —589487066——dB dB Metallic to Longitudinal (harm) Balance:200 Hz to 4 kHz—35——dB12Agere Communications Inc.Electrical Characteristics (continued)Table 7. Analog Signal Pins1.This parameter is not tested in production; it is guaranteed by design and device characterization.2.VTX offset is measured with respect to pin VRTX.3. Positive voltages from 0 V to V CCA are permitted at input DCR; however, voltages above 0 V have no effect on either the dc feed resis-tance or tip/ring voltage.ParameterMin Typ Max Unit DC OUT :Output Offset (no loop current)Output Drive CurrentOutput Voltage Swing (+0.25 mA/–3 mA load):Maximum MinimumOutput Short-circuit Current Output Load Resistance Output Load Capacitance 1—0.25V BAT –10—5————————±200–3.0V CCA 0.5±20—50mV mA V V mA k ΩpF VITR and VTX:Output Offset (no loop current)2Output Drive CurrentOutput Voltage Swing (±1 mA load):MaximumMinimum (VITR)Minimum (VTX)Output Short-circuit Current Output Load Resistance Output Load Capacitance 1—±1–10±3.5–3.5—4—————————±100—V CCA —V CCA – 1.0±20—50mV mA V V V mA k ΩpF VRTX:Output VoltageOutput Drive CurrentOutput Short-circuit Current Output Load Capacitance 1 2.2±500—— 2.4——— 2.6—±1550V µA mA pF RSW:Impedance to Ground 3——M ΩDCR:Input Voltage Range 3Input Bias Current Input Impedance –8—500———0±1—V µA k ΩTXI:Input ImpedanceInput Voltage Compliance Input Clamp Voltage 75±0.4±0.4—————±0.8k ΩV V RCVP and RCVN:Input Voltage Range Input Bias Current Input Impedance–2.5—10———V CCA ±1.5—V µA M ΩPT and PR:Overvoltage (from external source; continuous)——±265V FB1 and FB2:ac Output ImpedanceOutput Short-circuit Current —±27——10±34k ΩµA CF1 and CF2:Output Impedance 1180—375k ΩAgere Communications Inc.13Electrical Characteristics (continued)Transmit direction is tip/ring to VTX. Receive direction is RCVP(N) to tip/ring.Table 8. Transmission Characteristics1.Set by external components in conjunction with the T7531A/T7536 codecs. Any complex impedance R1 + R2 || C between 200 Ω and 1200 Ω can be synthesized.2.Return loss and transhybrid loss are functions of device gain accuracies and the external hybrid circuit. Guaranteed performance assumes 1% tolerance external resistors and capacitors.3.This parameter is not tested in production; it is guaranteed by design and device characterization.4.VTX gain depends on the resistor RGX1 from pin VITR to pin ITR. This gain assumes an ideal 8250 Ω, the recommended value. Positive cur-rent is defined as the differential current flowing from PT to PR. The transmit signal at VTX is measured with respect to pin VRTX.ParameterMin Typ Max Unit ac Termination Impedance 1200—1200ΩReturn Loss 2:200 Hz—500 Hz 500 Hz—3400 Hz2529————dB dB Total Harmonic Distortion (200 Hz—4 kHz)3:Off-hook On-hook ————0.31%%Transmit Gain (f = 1 kHz)4:PT/PR Current to (VTX—VRTX)–291–300–309V/A Receive Gain (f = 1 kHz):(RCVP—RCVN) to (PT—PR)1.9422.06—Gain vs. Frequency (transmit and receive)3(600 Ω termination; 1 kHz reference):200 Hz—300 Hz 300 Hz—3.4 kHz 3.4 kHz—20 kHz 20 kHz—266 kHz–0.3–0.05–3.0—000—0.050.050.052.0dB dB dB dB Gain vs. Level (transmit and receive; 0 dBV reference)3:–50 dB to +3 dB –0.0500.05dB Transhybrid Loss 2:200 Hz—500 Hz 500 Hz—3400 Hz2529————dB dB Idle-channel Noise (tip/ring; 600 Ω termination):Psophometric C-message 3 kHz Flat ——————–771320dBmp dBrnC dBrn Idle-channel Noise ((VTX—VRTX); 600 Ω termination):Psophometric C-message 3 kHz Flat ——————–771320dBmp0dBrnC0dBrn0EMC, per EN 300 386-2 and EN61000-4-6 (3 Vrms, 80% mod-ulation, 105 kHz—80 MHz, 150 Ω source impedance)3——–40dBm, 600 Ω。
STEP7-5.5组态拓扑

STEP7-5.5组态拓扑SIMATIC 拓扑编辑器拓扑编辑器具有一系列功能,可用于设置、互连和诊断包括端口在内的所有 PROFINET 设备的属性。
可提供下列功能和信息:●项目中所有 PROFINET 设备及其端口的显示●使用计算的信号运行时间,为每个端口组态电缆长度和组态电缆类型●通过本地识别各个 PRORINET 设备来互连数据●每个单独端口的 PRORINET 设备的诊断信息●通过在线/ 离线比较节点数据,简化默认检测●从图形视图调用诊断(模块信息)●导入网络拓扑“表格视图” (Tabular view) 选项卡左侧区域中的“互连表格”列出了所有组态的PROFINET 设备及其端口。
在顶部的选择区,右侧部分列出了可用于拓扑互连的所有 PROFINET 设备。
通过“过滤器” (Filter)下拉列表,可以从下列显示选项中进行选择:●“显示所有端口” (Show all ports):列出互连的端口以及非互连的端口●“显示互连端口” (Show interconnected ports) :只列出互连的端口●“显示非互连端口” (Show non-interconnected ports):只列出非互连的端口“图形视图” (Graphic view) 选项卡显示项目中的 PROFINET 设备及其互连。
在顶部右侧的微缩视图中,可以使用滚动条来选择PROFINET IO 系统的部分及其放大系数。
为更改 PROFINET IO 系统的部分,使用鼠标将框拖到希望看清细部的区域。
在线/ 离线比较左侧区域“组态的拓扑(离线)” (Configured topology (offline)) 中的“在线/ 离线比较” (Online/offline comparison) 选项卡列出了组态的 PROFINET 设备及其接口和端口以及相关联的邻近端口。
右侧“检测到的拓扑(在线)” (Detected topology (online)) 显示了 PROFINET IO 系统的在线视图及其运行时间的互连。
STEP7V55中文版简介5%d6%d0%ce%c4%b0%e6%bc%f2%bd%e9

SIMATIC编程软件件用于SIMATIC S7 / M7 / C7的STEP 7 V5.5编程软安装与使用注意事项该注意事项中包含的信息相对于其它文档来说是最新的。
请仔细阅读,此文本中包含了有关STEP 7 V5.5的安装与使用信息。
对该版本的重要修订以斜体显示,并标有注释“从该版本开始新增的内容”。
请注意,对于A4格式,所要打印文件的左右边距都设置成25 mm。
目录安装注意事项1发货清单2硬件要求3软件要求3.1运行环境3.2需要的存储空间3.3与其它软件产品的兼容性3.3.1Rational ClearCase配置管理工具3.3.2使用其它软件产品时的网络设置3.4在线文档4安装4.1安装STEP 7 V5.54.2升级旧版STEP 74.3STEP 7 V5.5许可证密钥4.4删除STEP 7 V5.54.5安装时的其它注意事项4.5.1使用滚轮鼠标4.5.2使用PC/PG通信卡时的注意事项使用注意事项(版本注释)5新版软件的新特性和所作的修改6组态和操作软件时的注意事项6.1STEP 7如何满足IEC标准6.2常规注意事项6.3使用网络驱动器6.4多用户操作6.5多重项目6.6交换不同版本的STEP 76.7库文件和实例项目6.8SIMATIC管理器6.9使用符号名6.10硬件配置(中央机架)6.11硬件配置(PROFIBUS DP)6.12硬件配置(PROFINET IO)6.13冗余I/O:通道间隔冗余6.14硬件诊断6.15MPI / PROFIBUS网络设置6.16SIMATIC M76.17梯形图、功能块图、语句表和参考数据6.18翻译文本6.19管理多语言文本6.20将S5程序转换成S7程序6.21将TI程序转换成S7程序6.22容错系统6.23使用外文字符集时的注意事项6.24使用SIMATIC Logon的注意事项6.25命令接口6.26TCI –工具调用接口6.27MS Windows 7操作系统的特性7文档注意事项8使用STEP 7中文版时的重要特性安装注意事装注意事项项以前请务本注意事项中包含您在安装STEP 7 V5.5时所需的重要信息,在安装该软件以前以前必详细阅读该注意事项。
1756系列

1756系列1756 系列 ControlLogix PAC是新一代高性能的集成的控制平台,它在简单易于使用的环境下,实现了卓越的性能,堪称业内典范。
最近Rockwell Automation还推出了完整的DCS解决系统,卓越的PLANT PAx系统。
ControlLogix控制器最大存储容量目前可达32兆,支持过程密集型的应用和快速运动控制应用。
可以根据应用要求,选用不同存储容量的控制器。
CompactFlash卡可做程序的移动存储。
多种处理器、多种通讯模块和I/O可以混合使用,不受限制。
不需要处理器执行I/O 的桥接和路由,随着系统的增大,可用网络把控制分布到另外的机架端子基座 1794-TB3PLC框架 1756-A13前连接器40针 1756-TBCH前连接器20针 1756-TBNH空槽填补模块 1756-N2PLC电源模块 1756-PA75模拟量输入模块 1756-IR6I1756-IF16模拟量输出模块 1756-OF8ControlNet通讯电缆 1784-RG6(304.8米)TAP连接器 1786-TPS终端电阻 1786-XTBNC接头 1786-BNCControlNet电缆制作工具 1786-CTK模拟量输入RTD 1756-IR6I模拟量输入TC` 1756-IT6I模拟量输出AO 1756-OF8接线端子 1756-TBCH接线端子 1756-TBNH空槽盖板 1756-N2终端电阻 1786-XTAB电源模块1756-PA72,1个,AB电源模块1756-CNBR,1个。
AB开关量输出模块1756-OB32,2个。
AB开关量输入模块1756-IB32,2个。
AB模拟量输入模块1756-IF16,2个。
AB垫电阻输入模块1756-IR6,1个网络分接头 1786-TPS同轴电缆(1卷305米) 1786-RG624v直流电源 1606-XLS480E-3AB交换机 1783-US05T1756-IB321756-PA75/B 电源1756-L61 B CPU1784-CF64 A 存储卡1756-BA2 电池1756-A10 底槽1756-CNB/E 通讯1756-IB32/B 数字量输入模块1756-OB32/A 数字量输出模块1756-HSC/A 计数模块1756-TBCH 前端连接器1756-ENBT A 以太网模板1756-IF8/A 模拟量输入模块1756-OF4 模拟量输出模块1756-SST-DP DP PROFIBUS模板1786-TPS CONTROLNET分接器1786-XT CONTROLNET终端电阻。
- 1、下载文档前请自行甄别文档内容的完整性,平台不提供额外的编辑、内容补充、找答案等附加服务。
- 2、"仅部分预览"的文档,不可在线预览部分如存在完整性等问题,可反馈申请退款(可完整预览的文档不适用该条件!)。
- 3、如文档侵犯您的权益,请联系客服反馈,我们会尽快为您处理(人工客服工作时间:9:00-18:30)。
1/11June 2003NEW DATASHEET ACCORDING TO PCN DSG20023123 MARKING: P75NF75 @STB75NF75STP75NF75 STP75NF75FPN-CHANNEL 75V - 0.0095 Ω - 80A TO-220/TO-220FP/D²PAKSTripFET™ II POWER MOSFETs TYPICAL R DS (on) = 0.0095 Ωs EXCEPTIONAL dv/dt CAPABILITY s 100% AVALANCHE TESTEDsSURFACE-MOUNTING D 2PAK (TO-263) POWER PACKAGE IN TAPE & REEL (SUFFIX “T4”)DESCRIPTIONThis MOSFET series realized with STMicroelectronics unique STripFET™ process has specifically been de-signed to minimize input capacitance and gate charge. It is therefore suitable as primary switch in advanced high-efficiency, high-frequency isolated DC-DC converters for Telecom and Computer applications. It is also intended for any applications with low gate drive requirements.APPLICATIONSs SOLENOID AND RELAY DRIVERS s DC MOTOR CONTROL s DC-DC CONVERTERSs AUTOMOTIVE ENVIRONMENT TYPE V DSS R DS(on)I D STB75NF75STP75NF75STP75NF75FP75 V 75 V 75 V<0.011 Ω<0.011 Ω<0.011 Ω80 A 80 A 80 A(*)ABSOLUTE MAXIMUM RATINGSPulse width limited by safe operating area.(*) Refer to SOA for the max allowable current values on FP-type due to Rth value(1) I SD ≤80A, di/dt ≤300A/µs, V DD ≤ V (BR)DSS , T j ≤ T JMAX (2) Starting T j = 25 o C, I D = 40A, V DD = 37.5VSymbolParameterValueUnitSTB75NF75 STP75NF75STP75NF75FP V DS Drain-source Voltage (V GS = 0)75V V DGR Drain-gate Voltage (R GS = 20 k Ω)75V V GS Gate- source Voltage± 20V I D Drain Current (continuous) at T C = 25°C 8080(*)A I D Drain Current (continuous) at T C = 100°C 7070(*)A I DM (•)Drain Current (pulsed)320320(*)A P tot Total Dissipation at T C = 25°C 30045W Derating Factor2.00.3W/°C dv/dt (1)Peak Diode Recovery voltage slope 12V/ns E AS (2)Single Pulse Avalanche Energy 700mJ V ISO Insulation Withstand Voltage (DC)------2000V T stg Storage Temperature-55 to 175°CT jOperating Junction TemperatureSTB75NF75 STP75NF75 STP75NF75FP2/11THERMAL DATAELECTRICAL CHARACTERISTICS (T case = 25 °C unless otherwise specified)OFFON (*)DYNAMICD 2PAK TO-220TO-220FP Rthj-case Thermal Resistance Junction-caseMax 0.53.33°C/W Rthj-ambT lThermal Resistance Junction-ambientMaximum Lead Temperature For Soldering Purpose ( 1.6 mm from case, for 10 sec.)Max62.5300°C/W °CSymbol ParameterTest ConditionsMin.Typ.Max.Unit V (BR)DSS Drain-sourceBreakdown Voltage I D = 250 µA, V GS = 075V I DSSZero Gate VoltageDrain Current (V GS = 0)V DS = Max RatingV DS = Max Rating T C = 125°C 110µA µA I GSSGate-body Leakage Current (V DS = 0)V GS = ± 20 V±100nASymbol ParameterTest ConditionsMin.Typ.Max.Unit V GS(th)Gate Threshold Voltage V DS = V GS I D = 250 µA 234V R DS(on)Static Drain-source On ResistanceV GS = 10 VI D = 40 A0.00950.011ΩSymbol ParameterTest ConditionsMin.Typ.Max.Unit g fs (*)Forward Transconductance V DS = 15 VI D =40 A20S C iss C oss C rssInput Capacitance Output Capacitance Reverse Transfer CapacitanceV DS = 25V, f = 1 MHz, V GS = 03700730240pF pF pF3/11STB75NF75 STP75NF75 STP75NF75FPSWITCHING ONSWITCHING OFFSOURCE DRAIN DIODEPulsed: Pulse duration = 300 µs, duty cycle 1.5 %.(•)Pulse width limited by safe operating area.Symbol ParameterTest ConditionsMin.Typ.Max.Unit t d(on)t r Turn-on Delay Time Rise TimeV DD = 37.5 VI D = 45 A R G =4.7 Ω V GS = 10 V (Resistive Load, Figure 3)2525ns ns Qg Q gs Q gdTotal Gate Charge Gate-Source Charge Gate-Drain ChargeV DD = 60 V I D = 80 A V GS = 10V1172747160nC nC nCSymbol ParameterTest ConditionsMin.Typ.Max.Unit t d(off)t fTurn-off Delay Time Fall TimeV DD = 37.5 VI D= 45 A R G =4.7 Ω V GS = 10 V (Resistive Load, Figure 3)6630ns nsSymbol ParameterTest ConditionsMin.Typ.Max.Unit I SD I SDM (•)Source-drain CurrentSource-drain Current (pulsed)80320A A V SD (*)Forward On Voltage I SD = 80 AV GS = 01.5V t rr Q rr I RRMReverse Recovery Time Reverse Recovery Charge Reverse Recovery CurrentI SD = 80 Adi/dt = 100A/µs V DD = 25 V T j = 150°C (see test circuit, Figure 5)13266010ns nC AELECTRICAL CHARACTERISTICS (continued)STB75NF75 STP75NF75 STP75NF75FPSTB75NF75 STP75NF75 STP75NF75FPSTB75NF75 STP75NF75 STP75NF75FP6/11Fig. 3: Switching Times Test Circuits For ResistiveFig. 5: Test Circuit For Inductive Load Switching7/11STB75NF75 STP75NF75 STP75NF75FPDIM.mm.inch.MIN.TYP. MAX.MIN.TYP. TYP .A 4.4 4.60.1730.181A1 2.49 2.690.0980.106A20.030.230.0010.009B 0.70.930.0280.037B2 1.14 1.70.0450.067C 0.450.60.0180.024C2 1.21 1.360.0480.054D 8.959.350.3520.368D180.315E 1010.40.3940.409E18.50.334G 4.88 5.280.1920.208L 1515.850.5910.624L2 1.27 1.40.0500.055L3 1.4 1.750.0550.069M 2.43.20.0940.126R 0.40.016V20°8°0°8°D 2PAK MECHANICAL DATASTB75NF75 STP75NF75 STP75NF75FP8/11DIM.mm.inch.MIN.TYP. MAX.MIN.TYP. TYP .A 4.4 4.60.1730.181C 1.23 1.320.0480.051D 2.40 2.720.0940.107E 0.490.700.0190.027F 0.610.880.0240.034F1 1.14 1.700.0440.067F2 1.14 1.700.0440.067G 4.95 5.150.1940.203G1 2.40 2.700.0940.106H21010.400.3930.409L216.400.645L328.901.137L413140.5110.551L5 2.65 2.950.1040.116L615.2515.750.6000.620L7 6.20 6.600.2440.260L9 3.50 3.930.1370.154DIA3.753.850.1470.151TO-220 MECHANICAL DATASTB75NF75 STP75NF75 STP75NF75FP10/11DIM.mm inchMIN.MAX.MIN.MAX.A010.510.70.4130.421B015.715.90.6180.626D 1.5 1.60.0590.063D1 1.59 1.610.0620.063E 1.65 1.850.0650.073F11.411.60.4490.456K0 4.8 5.00.1890.197P0 3.9 4.10.1530.161P111.912.10.4680.476P2 1.9 2.100750.082R50 1.574T0.250.35.0.00980.0137W23.724.30.9330.956DIM.mm inchMIN.MAX.MIN.MAX.A33012.992B 1.50.059C12.813.20.5040.520D20.20.795G24.426.40.960 1.039N100 3.937T30.4 1.197BASE QTY BULK QTY10001000REEL MECHANICAL DATA* on sales typeTUBE SHIPMENT (no suffix)* TAPE AND REEL SHIPMENT (suffix ”T4”)*D2PAK FOOTPRINTTAPE MECHANICAL DATASTB75NF75 STP75NF75 STP75NF75FP Information furnished is believed to be accurate and reliable. However, STMicroelectronics assumes no responsibility for the consequences of use of such information nor for any infringement of patents or other rights of third parties which may result from its use. No license is grantedby implication or otherwise under any patent or patent rights of STMicroelectronics. Specifications mentioned in this publication are subject to change without notice. This publication supersedes and replaces all information previously supplied. STMicroelectronics products are notauthorized for use as critical components in life support devices or systems without express written approval of STMicroelectronics.The ST logo is registered trademark of STMicroelectronics® 2002 STMicroelectronics - All Rights ReservedAll other names are the property of their respective owners.STMicroelectronics GROUP OF COMPANIESAustralia - Brazil - Canada - China - Finland - France - Germany - Hong Kong - India - Israel - Italy - Japan - Malaysia - Malta - Morocco - Singapore - Spain - Sweden - Switzerland - United Kingdom - United States.11/11。