轴承套的设计说明书
轴承使用说明书
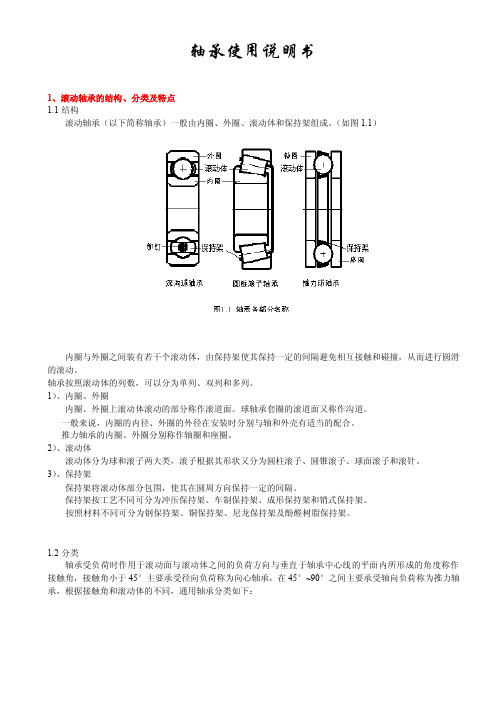
轴承使用说明书1、滚动轴承的结构、分类及特点1.1结构滚动轴承(以下简称轴承)一般由内圈、外圈、滚动体和保持架组成。
(如图1.1)内圈与外圈之间装有若干个滚动体,由保持架使其保持一定的间隔避免相互接触和碰撞,从而进行圆滑的滚动。
轴承按照滚动体的列数,可以分为单列、双列和多列。
1)、内圈、外圈内圈、外圈上滚动体滚动的部分称作滚道面。
球轴承套圈的滚道面又称作沟道。
一般来说,内圈的内径、外圈的外径在安装时分别与轴和外壳有适当的配合。
推力轴承的内圈、外圈分别称作轴圈和座圈。
2)、滚动体滚动体分为球和滚子两大类,滚子根据其形状又分为圆柱滚子、圆锥滚子、球面滚子和滚针。
3)、保持架保持架将滚动体部分包围,使其在圆周方向保持一定的间隔。
保持架按工艺不同可分为冲压保持架、车制保持架、成形保持架和销式保持架。
按照材料不同可分为钢保持架、铜保持架、尼龙保持架及酚醛树脂保持架。
1.2分类轴承受负荷时作用于滚动面与滚动体之间的负荷方向与垂直于轴承中心线的平面内所形成的角度称作接触角,接触角小于45°主要承受径向负荷称为向心轴承,在45°~90°之间主要承受轴向负荷称为推力轴承,根据接触角和滚动体的不同,通用轴承分类如下:深沟球轴承(单、双列)向心球轴承角接触球轴承(单、双列)四点接触球轴承调心球轴承向心圆柱滚子轴承(单、双、四列)轴向心滚子轴承圆锥滚子轴承(单、双、四列)滚承滚针轴承(单、双列)动调心滚子轴承轴承推力球轴承推力球轴承(单、双列)推力角接触球轴承(单、双向)推力推力圆柱滚子轴承轴推力滚子轴承推力圆锥滚子轴承承推力滚针轴承推力调心滚子轴承1.3特点1.3.1滚动轴承的优点滚动轴承虽有许多类型和品种,并拥有各自固定的特征,但是,它们与滑动轴承相比较,却具有下述共同的优点:(1)、起动摩擦系数小,与动摩擦系数之差少。
(2)、国际性标准和规格统一,容易得到有互换性的产品。
(3)、润滑方便,润滑剂消耗少。
轴承座夹具课程设计说明书
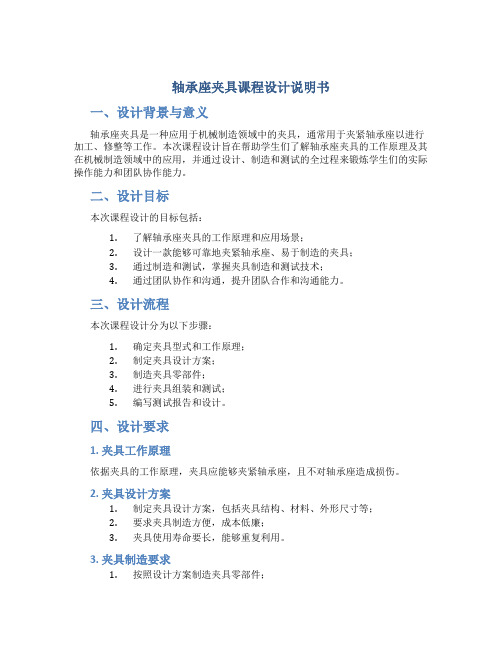
轴承座夹具课程设计说明书一、设计背景与意义轴承座夹具是一种应用于机械制造领域中的夹具,通常用于夹紧轴承座以进行加工、修整等工作。
本次课程设计旨在帮助学生们了解轴承座夹具的工作原理及其在机械制造领域中的应用,并通过设计、制造和测试的全过程来锻炼学生们的实际操作能力和团队协作能力。
二、设计目标本次课程设计的目标包括:1.了解轴承座夹具的工作原理和应用场景;2.设计一款能够可靠地夹紧轴承座、易于制造的夹具;3.通过制造和测试,掌握夹具制造和测试技术;4.通过团队协作和沟通,提升团队合作和沟通能力。
三、设计流程本次课程设计分为以下步骤:1.确定夹具型式和工作原理;2.制定夹具设计方案;3.制造夹具零部件;4.进行夹具组装和测试;5.编写测试报告和设计。
四、设计要求1. 夹具工作原理依据夹具的工作原理,夹具应能够夹紧轴承座,且不对轴承座造成损伤。
2. 夹具设计方案1.制定夹具设计方案,包括夹具结构、材料、外形尺寸等;2.要求夹具制造方便,成本低廉;3.夹具使用寿命要长,能够重复利用。
3. 夹具制造要求1.按照设计方案制造夹具零部件;2.夹具零部件的加工精度要求高,符合设计要求;3.要求夹具加工和装配精细,工艺优良。
4. 夹具测试要求1.进行夹具的静态、动态测试;2.要求测试结果准确、可靠;3.可以根据测试结果分析夹具的优缺点并提出改进建议。
五、设计注意事项1.在设计和制造夹具时,注意保证夹具的质量和安全性;2.在制定夹具测试方案时,应考虑到实际应用场景和工作条件,同时保证测试结果的可靠性和有效性;3.在测试过程中,应注意操作规范和安全;4.在撰写设计时,应认真设计和制造过程中的经验和教训,并提出改进建议和思考。
六、参考文献1.《机械制造工艺学》(第二版),冯开宇主编,机械工业出版社,2009年;2.《夹具设计手册》(第二版),崔玉祥编著,机械工业出版社,2011年;3.《夹具制造工艺学》(第三版),王德扬编著,机械工业出版社,2014年。
圆锥滚子轴承设计说明书1
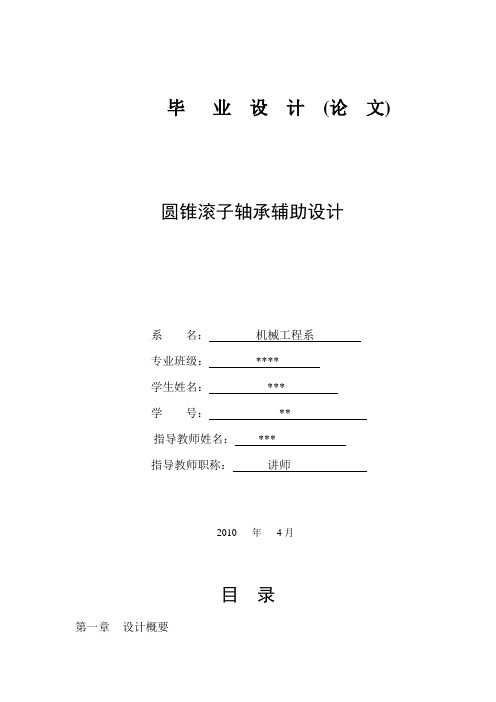
毕业设计(论文)圆锥滚子轴承辅助设计系名:机械工程系专业班级:****学生姓名:***学号:**指导教师姓名:***指导教师职称:讲师2010 年4月目录第一章设计概要1.1 系统运行平台 (6)1.1.1 CAD的概念 (6)1.1.2 VB的概念 (6)1.1.3 系统要求及模型建立 (6)1.2 IDEF0框图 (7)第二章圆锥滚子轴承设计原理 (9)2.1基本概念及术语 (9)2.2 滚动轴承类型的选择 (9)2.3 按额定动载选择轴承 (9)2.4基本额定动载荷计算 (10)第三章圆锥滚子轴承的程序设计 (12)3.1圆锥滚子轴承具体实现的方法 (12)3.2 连接数据库Access (12)3.3 根据轴承最小内径选择参数 (12)3.4 校核接触疲劳强度 (13)3.5 CAD出图 (14)第四章软件使用说明 (15)4.1 系统运行环境 (15)4.2 VB操作 (15)总结 (16)致谢 (17)参考文献 (17)圆锥滚子轴承计算机辅助设计专业班级:计算机辅助设计与制造学生姓名:***指导教师:*** 职称:讲师摘要本设计是设计一个基于圆锥滚子轴承设计的参数化系统。
其设计对象为圆锥滚子轴承。
所设计系统的功能分为对其进行参数化强度计算和参数化后自动出图两个部分。
在本设计中,圆锥滚子轴承的几何尺寸确定方法和强度计算方法主要参照《机械设计基础》,所用到的软件有Microsoft Visual Basic 6.0, Office Access2003、AutoCAD2004。
此系统在Windows XP系统中进行设计和调试并可正常运行。
关键词:圆锥滚子轴承设计参数化自动生成图形Straight bevel gear computer-aided designAbstract The design is based on the design of a straight bevel gear design parameters of the system. The design targets for the straight bevel gear. Designed by the function of the system into its parameters and parameters of strength calculation of automatically after drawing two parts. In this design, straight bevel gear geometry determine the method of calculation methods and intensity of the main reference "mechanical design basis", the software used by Microsoft Visual Basic 6.0, Office Access2003, AutoCAD2005. The system in Windows XP system design and debug and normal operation.Key words:straight bevel gear design parameters of the automatically generated graphics引言目前,国际市场轴承年销售额为300亿美元,其中我国为30亿美元,占1/10。
轴承座工艺设计说明书06
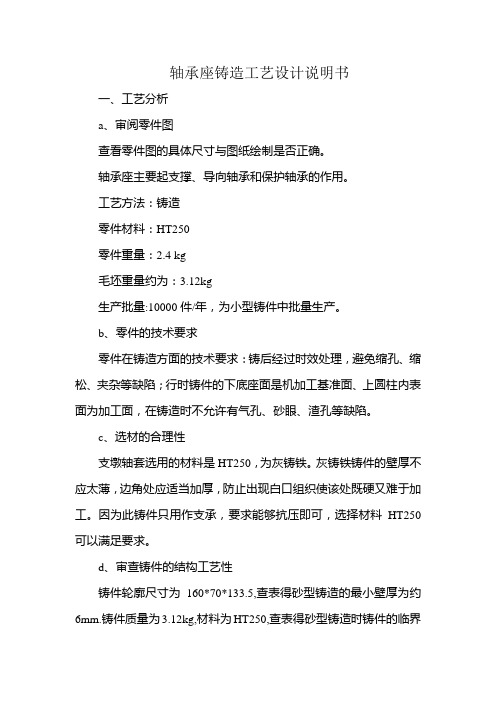
轴承座铸造工艺设计说明书一、工艺分析a、审阅零件图查看零件图的具体尺寸与图纸绘制是否正确。
轴承座主要起支撑、导向轴承和保护轴承的作用。
工艺方法:铸造零件材料:HT250零件重量:2.4 kg毛坯重量约为:3.12kg生产批量:10000件/年,为小型铸件中批量生产。
b、零件的技术要求零件在铸造方面的技术要求:铸后经过时效处理,避免缩孔、缩松、夹杂等缺陷;行时铸件的下底座面是机加工基准面、上圆柱内表面为加工面,在铸造时不允许有气孔、砂眼、渣孔等缺陷。
c、选材的合理性支墩轴套选用的材料是HT250,为灰铸铁。
灰铸铁铸件的壁厚不应太薄,边角处应适当加厚,防止出现白口组织使该处既硬又难于加工。
因为此铸件只用作支承,要求能够抗压即可,选择材料HT250可以满足要求。
d、审查铸件的结构工艺性铸件轮廓尺寸为160*70*133.5,查表得砂型铸造的最小壁厚为约6mm.铸件质量为3.12kg,材料为HT250,查表得砂型铸造时铸件的临界壁厚为12-15mm.壁厚越大,圆角尺寸也相应增大。
对于小型铸铁件,外圆角半径一般取2--8mm,内圆角半径一般取4--16mm。
通常,铸件圆角半径可取相邻两壁厚度平均值的1/3--1/5。
由图分析可知:原零件壁厚满足此要求。
二、工艺方案设计a、造型、造芯方法和铸型种类1、根据以上信息可知,由于零件属中批量生产,形状比较简单、壁厚比较均匀,且该材料为灰铸铁,所以确定毛坯的生产方法为砂型铸造、砂型种类选择湿型。
2、此铸件内腔形状简单,可用砂垛来形成,不用型芯铸出,既自带型芯。
自带型芯砂垛若位于下半铸型,也叫“堆砂”,应满足H/D<1(H--自带型芯铸孔高度,D--铸孔直径)此处轴承座H/D=0.85符合条件。
造型方法:湿型手工砂箱造型造芯方法:堆砂b、浇注位置的确定根据机械制造课程辅助工艺设计中关于浇注位置的确定原则;1)重要加工面应朝下或直立状态,对以圆筒类铸件内外表面要求较高一般采用直立浇注2)薄壁铸件应将薄而大的平面放在下面或侧面、倾斜。
轴套类零件加工工艺及方案
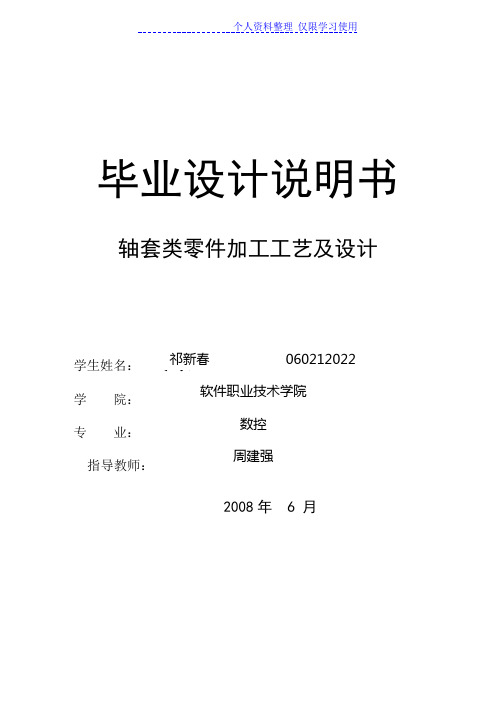
个人资料整理 仅限学习使用毕业设计说明书轴套类零件加工工艺及设计学生姓名: 学号: 学 院:专 业: 指导教师:2008年 6 月祁新春 0602120225 软件职业技术学院 数控 周建强目录1引言12数控机床的概述22.1数控及自动编程的发展简介22.1.1数控机床的发展过程:22.1.2自动编程软件的发展、联系及优越性22.2数控机床的基本组成及工作原理32.2.1数控机床的基本组成32.2.2数控机床的工作原理32.3数控机床的分类32.3.1按控制刀具与工件相对运动轨迹分类32.3.2按加工方式分类32.3.3按控制坐标轴数分类42.3.4按驱动系统的控制方式分类42.4数控机床的应用范围42.5数控机床的特点4第三章轴类零件的加工工艺5第四章轴类零件实例加工<一)64.1实体零件的生成64.2加工工艺分析74.2.1分析零件图纸和工艺分析74.2.2确定装夹方案94.2.3确定加工路线及进给路线94.2.4刀具的选择104.3选择切削用量124.3.1主轴转速的确定124.3.2进给速度的确定124.3.3背吃刀量确定124.4编程134.4.1编程技巧134.4.2编程特点154.4.3编程方法154.4.4编程步骤164.4.5实例分析165典型实例分析<二)176设计总结21附录A 加工程序 (23)参考文献30致谢311引言科学技术和社会生产的不断发展,对机械产品的性能、质量、生产率和成本提出了越来越高的要求。
机械加工工艺过程自动化是实现上述要求的重要技术措施之一。
他不仅能够提高品质质量和生产率,降低生产成本,还能改善工人的劳动条件,但是采用这种自动和高效率的设备需要很大的初期投资,以及较长的生产周期,只有在大批量的生产条件下,才会有显著的经济效益。
随着消费向个性化发展,单件小批量多品种产品占到70%--80%,这类产品的零件一般采用通用机床来加工。
而通用机床的自动化程度不高,基本上由人工操作,难于进一步提高生产率和保证质量。
工艺课程设计说明书-涡轮轴承座工艺及铣端面铣槽夹具设计
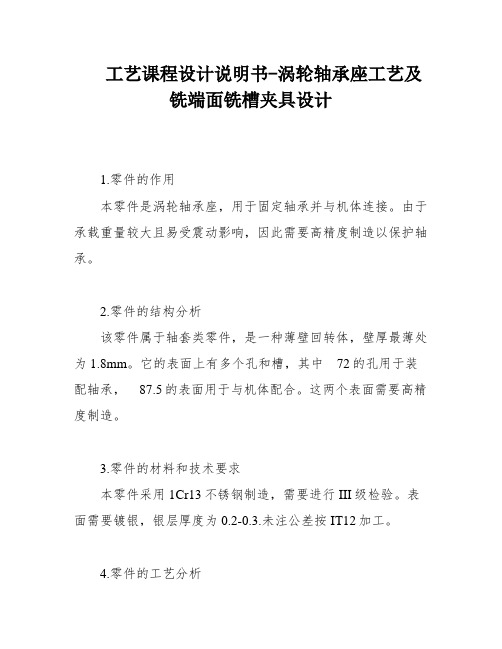
工艺课程设计说明书-涡轮轴承座工艺及铣端面铣槽夹具设计1.零件的作用本零件是涡轮轴承座,用于固定轴承并与机体连接。
由于承载重量较大且易受震动影响,因此需要高精度制造以保护轴承。
2.零件的结构分析该零件属于轴套类零件,是一种薄壁回转体,壁厚最薄处为1.8mm。
它的表面上有多个孔和槽,其中72的孔用于装配轴承,87.5的表面用于与机体配合。
这两个表面需要高精度制造。
3.零件的材料和技术要求本零件采用1Cr13不锈钢制造,需要进行III级检验。
表面需要镀银,银层厚度为0.2-0.3.未注公差按IT12加工。
4.零件的工艺分析该零件的主要表面是63、66.5、72的孔以及87.5的外圆面,需要达到IT7级的尺寸精度和Ra0.8的表面粗糙度。
其余表面的尺寸精度为IT12,可以通过粗车或粗镗达到要求。
位置关系精度分析:除D外均布的6孔的位置度公差为.1,大段内表面的圆柱度公差为0.015,外圆凸台处与小段外圆的同轴度公差为.04.二、毛坯设计该零件为轴套类零件,采用1Cr13不锈钢制造,应采用锻造毛坯。
为减少后续机械加工的余量,节省材料,两侧内孔应预先锻造出通孔。
凸台可以通过后续的机械加工来完成。
为增强韧度和冲击强度,毛坯应选用锻件,采用模锻件,毛坯拔模斜度为5度。
毛坯的尺寸需要根据零件图上的各个尺寸以及各种加工方法的余量推出。
三、工艺路线的制定1.基准选择选择粗基准时需要遵循以下原则:1.表面处理的原则:要保证重要表面的余量均匀,可以选择不加工的表面;选择尺寸和位置比较可靠、平整光洁的表面;在同一方向上只允许使用一次。
2.精基准的选择原则:基准应该重合,可以选择不加工的表面作为基准;基准应该相同;互为基准;自为基准。
针对本零件的基准选择,应该以大段的端面作为基准来进行切削加工,在加工大端的时候,应以小端的端面作为基准来进行。
在小端和大端都进行了一定的机械加工后,凸耳已经有了一定的精度,因此在加工时可以凸耳的两面作为精基准。
角型轴承箱零件设计说明书
轴承箱零件设计说明书轴承箱零件设计目录前言…………………………………………………………………… 一、零件的分析…………………………………………………… 二、工艺规程的设计……………………………………………… (一)确定毛坯的制造形式……………………………………… (二)基准的选择………………………………………………… (三)工艺路线的拟定及工艺方案的分析……………… (四)机械加工余量、工序尺寸及毛坯尺寸的确定……… (五)各工序的定位夹紧方案及切削用量的选择…………… (六)各工序的基本工时三、工装设计分析,提出设计任务书………………………… 四、总结………………………………………………………… 五、主要参考文献……………………………………………… 前言机械制造工艺学课程设计是在学完机械制造工艺学(含机床夹具设计)和大部分专业的一门课程,并进行了生产实习的基础上进行的一个教学环节。
这是我们在进行课程设计之前对所学课程的一次深入的全面的总复习,也是一次理论联系实际的训练。
因此,它在几年的学习中占重要地位。
就我个人而言,希望通过这次课程设计,对自己今后将从事的工作,进行一次适应性训练,通过设计锻炼自己分析问题、解决问题的能力,为今后的工作打下一个良好的基础。
由于能力所限,设计中尚有许多不足之处,希望指导老师给予批评指教。
一、零件的分析 (一) 零件的作用角形轴承箱是用夹固定在轴承的箱体,通过固定轴承来实现轴承的正常运转槽50h11 与端面 100h11 为配合表面有较高的精度及表面粗糙度。
140h11 为内圆较高的定位基准Φ180H7 孔为轴承配合表面有较高的精度。
(二)零件工艺分析该零件是箱体类零件,形状不规则,加工面大,尺寸精度、形位精度、表面精度要求均较高,零件的主要技术要求分析如下:(参阅附图零件图- )(1)T1、T2 两表面对Φ180H7 孔轴线垂直度摆差不大于 0.1mm 及圆度,主要保证轴承能正确的安装在该箱体上,角形轴承箱利用自行的 50h11 的凹槽进行定位,因此要 T3、T4 的精度及槽的定位精度为0.4mm。
挖掘机销轴和轴承的设计说明书
工作装置的可靠性对液压挖掘机整机性能影响很大,工作装置在工作时的工况为低速重载,这就对轴和轴承的工作性能提出了非常高的要求,而在挖掘机设计中,工作装置的重量在能满足设计性能参数的前提下应尽可能的小,所以合理设计轴和轴承对挖掘机整机性能至关重要。
下面就分别讨论轴、轴承、轴和轴承公差配合的设计.一、轴承的设计:工作装置轴承的种类繁多,按其材料可分为铜轴承、钢轴承、复合轴承等;按其润滑方式可分为干摩擦轴承、含油轴承、不完全油膜轴承、流体膜轴承等:我厂现使用轴承的润滑方式为不完全油膜润滑,先后使用过铜、钢、铜基钢背自润滑等多种轴承。
铜轴承韧性良好,耐磨性一般,对轴有较好的保护作用,但抗变形能力较差,长时间使用后易变形,造成轴承内径扩大,导致结构件晃动;钢轴承强度高,耐磨性好,抗变形能力强,但表面热处理的工艺要求高;铜基钢背自润滑轴承兼有钢轴承和铜轴承的优点,同时油槽润滑和自润滑相结合,能有效避免轴承的烧焦,但其工艺复杂,成本较高。
轴承的设计首要考虑的是轴承的使用寿命,其寿命除烧焦外由轴承内径的磨损量来决定.磨损量主要受摩擦条件的影响,而摩擦又受承载、速度、杂质、表面粗糙度、工作温度、不同运行方式、所使用润滑剂等条件影响,因此,磨损量只能是一个理论估计值,轴套的寿命取决于各种复杂的条件。
若因供油不良,杂质渗入而使磨损急剧变化,就很难预测磨损情况.在正常情况下,铜轴承(ZcuAll0Fe3Mn2)磨损量可由下式近似得出:W=K×P×V×TW:磨损量(mm)K:摩擦系数【mm/(N/mm2·m/min·hr)】P:承载能力(N/mm2)V:线速度(m/min)T:磨损时间(hr)式中K=Ci×k,k为理想状态下的摩擦系数,K=(1~5)×10-8【mm/(N/mm2·m/min·hr)】1、Ci=C0×Cl×C2×C32、承载压力P通常所谓承载压力是指轴承承受载荷时,轴承支撑的最大载荷除以受压面积,所谓受压面积,当轴承为圆筒形时,取与轴承接触部分的载荷方向的投影面积。
轴承座设计说明范文
轴承座设计说明范文
一、概述
轴承座是机械设备中的一种重要组件,用于支撑和固定轴承,以保证其以预定的速度运转和准确地定位轴承,以满足机械设备的需要。
轴承座的设计除了要考虑载荷能力外,还要考虑它的重量、体积、加工成本、抗震性能等因素,确保最佳的性价比以及符合机械设备的使用要求。
二、轴承座设计的要素
1、材料:轴承座的材料主要是铸铁、不锈钢和铝合金等金属材料,根据轴承座的用途、工况条件和使用要求,选用合适的材料,以确保其具备较高的抗压强度、抗腐蚀能力、防潮能力等特性。
2、结构形式:根据轴承座的使用环境、工况条件和设计要求,选择合适的结构形式,如面板式、螺栓连接式、旋转式等,并考虑到轴承安装的块体结构形式,使其具有良好的负载能力和抗拉强度,从而确保座体的稳定性。
3、抗振能力:由于轴承座要支撑轴承,在受到外力作用时,容易发生振动,因此,在设计轴承座时,应考虑到设备的振动特性,结构能否有效减少振动,如采用减振垫片或金属振动补偿器等装置,使其具有良好的抗振能力。
4、加工工艺:轴承座的加工工艺主要包括热处理、机加工、抛光和表面处理等。
轴承套冲压模具设计
目录摘要 (I)Abstract ................................................................................................................ I I 前言. (III)第1章冲压模具的设计步骤和结构组成 (1)1.1冲压模具的设计要求 (1)1.2冲压模具的设计步骤及内容 (1)1.3 冲压模具的结构组成和作用 (2)第2章轴承套冲压件 (3)2.1 冲压件的结构和工艺特点 (3)2.2 冲压件的材料及性能参数 (3)2.3 冲压件的工艺性分析 (4)2.3.1 毛坯尺寸计算 (4)2.3.2 拉深系数计算 (4)2.4 冲压件的冲压工艺方案 (5)2.4.1 冲压工艺方案分析 (5)2.4.2 冲压工艺方案的确定 (5)2.5冲压件的排样 (5)2.5.1 排样的原则 (5)2.5.2 排样方案 (6)2.5.3 条料宽度 (6)2.5.4 材料利用率 (7)第3章冲压力计算 (8)3.1 冲裁力的计算 (8)3.2 拉深力的计算 (8)3.3 压边力的计算 (9)3.3.1 压边圈的采用 (9)3.3.2 压边力的计算 (9)3.4 冲裁工艺力的计算 (10)3.5 压力中心的确定 (11)第4章冲压机的选用 (12)4.1 选用冲压机的方法和原则 (12)4.2 冲压机的选用 (12)4.3 冲压机技术参数校核 (13)第5章冲压模具设计 (14)5.1 冲压模的总体设计 (14)5.2 凸凹模工作部分尺寸计算 (14)5.2.1 冲裁部分凸凹模刃口尺寸计算 (14)5.2.2 拉深部分凸凹模工作部分尺寸计算 (15)5.3 拉深冲孔凸凹模的结构设计 (17)5.4 拉深凸模的结构设计 (18)5.5 拉深凹模的结构设计 (19)5.6 冲孔凸模的结构设计 (20)5.7凸模固定板的结构设计 (21)5.8落料拉深凸凹模的结构设计 (22)5.9 压边圈及其固定圈的结构设计 (23)5.10 落料凹模的结构设计 (25)5.11 卸料板的结构设计 (26)5.12 其它零件的结构设计 (27)第6章冲压模具的安装 (29)6.1 模具零件的固定方法 (29)6.1.1 凸模的固定 (29)6.1.2 落料拉深凸凹模的固定 (29)6.1.3 导柱导套的固定 (29)6.1.4 模柄的固定 (30)6.1.5 各销的固定与配合公差 (30)6.2 装配要求 (30)6.2.1本模具的装配过程如下 (31)6.2.2 典型零件的装配要求 (31)6.3 本模具的工作过程及结构特点 (32)6.3.1 本模具的工作过程 (32)6.3.2 模具结构的特点 (33)结论 (34)谢辞 (35)参考文献 (36)轴承套冲压模具设计摘要本次毕业设计是为轴承套零件设计能制作出符合要求的模具。
- 1、下载文档前请自行甄别文档内容的完整性,平台不提供额外的编辑、内容补充、找答案等附加服务。
- 2、"仅部分预览"的文档,不可在线预览部分如存在完整性等问题,可反馈申请退款(可完整预览的文档不适用该条件!)。
- 3、如文档侵犯您的权益,请联系客服反馈,我们会尽快为您处理(人工客服工作时间:9:00-18:30)。
设计说明书一零件的分析(一)零件的作用此轴承套是机械加工中常见的一种零件,在各类机器中应用很广泛,主要起支撑或导向作用。
(二)零件的工艺分析此轴承套的主要加工表面为外圆表面和内孔表面,主要的技术要求为:表面粗糙度要求,尺寸精度要求,位置精度要求。
具体分析如下:1.Φ34js7mm的外圆表面。
表面粗糙度Ra=6.3um,尺寸精度为Φ34±0.0125mm,此外圆相对于轴心线的圆跳动公差为0.01mm2.Φ22H7mm的内孔。
此内孔主要工作表面,粗糙度要求较高为Ra=1.6um,尺寸精度为Φ220021 .0mm。
3.Φ42mm的左端面与轴心线的垂直度公差为0.01mm。
4.Φ4mm孔等次要加工表面及内孔。
工艺规程设计(一)确定毛坯的制造形式零件材料为ZQSn6-6-3,因为轴承套在工作时主要起支撑轴承的作用,考虑到机器工作的连续性要求及零件的粗糙度、尺寸精度要求较高,所以选用热轧圆棒料作为毛坯。
(二) 基准的选择1. 粗基准的选择对于这种一般的零件而言,选择毛坯外圆作为粗基准即可。
2. 精基准的选择精基准的选择是相对于粗基准而言的。
对于此轴承套精基准的选择主要考虑到左端面与轴心线的垂直度要求、Φ34js7mm 的外圆与轴心线的圆跳动要求以及外圆和内孔的尺寸精度要求。
所以在加工外圆时用左端面和内孔作为精基准,用心轴定位,两顶尖装夹即可。
加工内孔时用已加工过的外圆表面作为精基准即可保证内孔的尺寸精度要求。
(三) 制定工艺路线工序一:按上工艺草图车至尺寸,6个零件同时加工,尺寸均相同; 工序二:用软卡爪夹住Φ42mm 外圆,找正钻孔Φ20.5mm 成单件: 工序三:1.用软卡爪夹住Φ35mm 外圆2.车左端面,取总长40mm 至尺寸3.车孔Φ2212.008.0--mm4.车内槽Φ24mmx16mm 至尺寸5.铰孔Φ22H7mm 至尺寸6.倒角工序四:1.工件套心轴,装夹于两顶尖之间 2.车Φ34js7mm 至尺寸 3.车阶台平面6至尺寸 4.倒角工序五:以端面和孔定位,钻Φ4mm孔工序六:检验入库(四)机械加工余量、工序尺寸及毛坯尺寸的确定此轴承套的材料为ZQSn6-6-3,零件的最大径向尺寸为42mm,查《工艺手册》得,机械单边加工余量1.5。
因为此轴承套为6件同时加工,割断刀尺寸为2mm,毛坯零件轴向尺寸为40.5mm,轴向单边加工余量为1.5mm,所以零件的毛坯尺寸可定为:Φ45mmx260mm。
分别确定个加工表面的机械加工余量、工序尺寸及毛坯尺寸如下:(五)确定切削用量及基本工时工序一:按工艺草图车至尺寸,6个同时加工。
本工序采用计算法确定切削用量,具体分析如下:1.加工条件:工件材料:ZQSn6-6-3人工时效热处理,热轧圆棒料。
加工要求:粗车轴套各外圆至尺寸,表面粗糙度要求值为Ra200um加工设备:CA6140卧式车床刀具:刀片材料为硬质合金YT5,刀杆尺寸为16mmx25mm,Kr=90°, γ=15°, α=8°,r=0.5mmε2.计算切削用量1已知毛坯长度方向的加工余量为7mm,因为此毛坯已经考虑到割断后的6零件的加工余量,因此端面可以全部加工。
可以分两次加工,ap=3mm计。
2.确定进给量f:根据《切削用量简明手册》,和加工条件以及工件直径为45mm,得f=0.4~0.5mm/r。
按CA6140车床说明书取f=0.5mm/r3.计算切削速度:根据《切削用量简明手册》,和加工条件可得vc=67~73m/min,取vc=70m/min4.确定主轴转速n:n=1000x70/3.14x45=495r/min,据CA6140车床说明书取n=500r/min.所以实际切削速度为vc=500x45x3.14/1000=70.65m/min。
4.计算切削工时:车削基本时间Tb=LjZ/nfap=45/500x0.5x3=0.06min所以车削端面所需时间为Tm=3Tb=3x0.06=0.18min5.粗车外圆至Φ42mm确定切削用量:外圆单边余量为1.5mm,所以取ap=1.5mm可一次切除。
根据《切削用量简明手册》,和加工条件以及工件直径为42mm,得f=0.4~0.5mm/r。
按CA6140车床说明书取f=0.5mm/r。
根据《切削用量简明手册》,和加工条件可得vc=67~73m/min,取vc=70m/min所以主轴转速n=1000x70/3.14x42=530r/min, 据CA6140车床说明书取n=500r/min.所以实际切削速度为vc=500x42x3.14/1000=65.94m/min。
车削基本时间Tb=LjZ/nfap=42/500x0.5x3=0.056min5.粗车外圆至Φ35mm确定切削用量:外圆单边余量为3.5mm,所以取ap=3mm可二次切除。
根据《切削用量简明手册》,和加工条件以及工件直径为35mm,得f=0.4~0.5mm/r。
按CA6140车床说明书取f=0.5mm/r。
根据《切削用量简明手册》,和加工条件可得vc=67~73m/min,取vc=70m/min 所以主轴转速n=1000x70/3.14x35=637r/min, 据CA6140车床说明书取n =710r/min.所以实际切削速度为 vc =710x35x3.14/1000=78.03m/min 。
车削基本时间Tb =LjZ/nfapi==35/710x0.5x3x2=0.066min 。
工序二:此工序是钻Φ20.5mm 的孔。
1.加工条件:工件材料:ZQSn6-6-3人工时效热处理,热轧圆棒料。
加工要求:钻Φ20.5mm 的孔。
加工设备:CA6140卧式车床刀具:Φ20.5mm 麻花钻,刀具材料为高速钢钻头2.确定切削用量:根据工件材料,刀具的材料以及麻花钻的尺寸查《手册》得f=0.52~0.64 mm/r ,取f=0.56mm/r 。
由手册得f=0.56mm/r 刃磨形式为标准,d=20.5mm 时vc=12m/min ,切削速度的修正系数Ktv=1.09,Kcv=1,故:v=12x1.09x1=13.08m/min.所以n=1000x13.08/3.14x20.5=203.2 r/min 。
根据Z525钻床说明书,可选择n=272 r/min 。
所以实际切削速度vc=272x20.5x3.14/1000=17.5 m/min.车削基本时间Tb=L/nf=257/272x0.56=1.69min 工序三:工件材料:ZQSn6-6-3人工时效热处理,热轧圆棒料。
加工设备:CA6140卧式车床 刀具:Φ22H7mm 铰刀。
1.车端面。
切削用量的确定:此工步的轴向加工余量为0.5mm ,所以取ap=0.5mm ,可一次加工。
根据《切削用量简明手册》,和加工条件以及工件直径为42mm ,得f=0.4~0.5mm/r 。
按CA6140车床说明书取f =0.5mm/r 。
根据《切削用量简明手册》,和加工条件可得 vc=67~73m/min,取vc=70m/min 所以主轴转速n=1000x70/3.14x42=530r/min, 据CA6140车床说明书取n =500r/min.所以实际切削速度为 vc =500x42x3.14/1000=65.94m/min 。
车削基本时间Tb =LjZ/nfap=42/500x0.5x0.5=0.33min得f=0.4~0.5mm/r 。
按CA6140车床说明书取f =0.5mm/r 。
根据《切削用量简明手册》,和加工条件可得 vc=67~73m/min,取vc=70m/min 所以主轴转速n=1000x70/3.14x42=530r/min, 据CA6140车床说明书取n =500r/min.所以实际切削速度为 vc =500x42x3.14/1000=65.94m/min 。
车削基本时间Tb =LjZ/nfap=42/500x0.5x0.5=0.33min2.扩孔至Φ220.120.008--mm 。
1.加工条件:工件材料:ZQSn6-6-3人工时效热处理,热轧圆棒料。
加工要求:扩至Φ220.120.008--mm 。
加工设备:CA6140卧式车床刀具:扩孔钻,刀具材料为高速钢钻头2.确定切削用量:根据扩孔钻的直径和工件的硬度可以查表的f=1.0~1.2mm/r,取f=1.0mm/r, 手册得f=1.0mm/r刃磨形式为标准,d=22mm时vc=17m/min,切削速度的修正系数Ktv=1.09,Kcv=1,故:v=17x1.09x1=18.53m/min.所以n=1000x18.53/3.14x22=268 r/min。
根据C616说明书,可选择n=320 r/min。
所以实际切削速度vc=320x22x3.14/1000=22.01 m/min.车削基本时间Tb=L/nf=40/320x1=0.125min3.车内槽确定切削用量:此工步的单边加工余量为1mm,所以取ap=1mm,可一次加工。
根据《切削用量简明手册》,和加工条件以及工件直径为24mm,得f=0.3~0.4mm/r。
按CA6140车床说明书取f=0.3mm/r。
根据《切削用量简明手册》,和加工条件可得vc=67~73m/min,取vc=67m/min所以主轴转速n=1000x67/3.14x22=969r/min, 据CA6140车床说明书取n=900r/min.所以实际切削速度为vc=900x22x3.14/1000=62.17m/min。
车削基本时间Tb=LjZ/nfap=16/900x1x0.3=0.06min4.铰孔确定切削用量:此工步的单边加工余量为0.03mm,所以取ap=0.03mm,可一次加工。
根据《切削用量简明手册》,和加工条件以及工件直径为22mm,得f=0.3~0.4mm/r。
按CA6140车床说明书取f=0.3mm/r。
根据《切削用量简明手册》,和加工条件可得vc=67~73m/min,取vc=70m/min所以主轴转速n=1000x70/3.14x22=1011r/min, 据CA6140车床说明书取n=1120r/min.所以实际切削速度为vc=1120x22x3.14/1000=77.37m/min。
车削基本时间Tb=LjZ/nfap=24/1120x0.3x0.03=2.3min工序41.车外圆确定切削用量:此工步的单边加工余量为0.5mm,所以取ap=0.5mm,可一次加工。
根据《切削用量简明手册》,和加工条件以及工件直径为34mm,得f=0.4~0.5mm/r。
按CA6140车床说明书取f=0.41mm/r。
根据《切削用量简明手册》,和加工条件可得vc=85~90m/min,取vc=90m/min所以主轴转速n=1000x90/3.14x34=843r/min, 据CA6140车床说明书取n=900r/min.所以实际切削速度为vc=900x34x3.14/1000=96.08m/min。