消失模铸造缺陷的产生原理和解决方法
消失模铸造缺陷产生的原因及解决措施

消失模铸造缺陷产生的原因及解决措施一、消失模铸造缺陷的原因:1.模具设计不合理:模具的设计不合理是导致消失模铸造缺陷的主要原因之一、例如,模具的冷却系统设计不良或者模具结构不稳定,都会对铸件的形状和内部结构造成影响。
2.熔融金属冷却不均匀:熔融金属冷却不均匀也是导致消失模铸造缺陷的一个重要原因。
由于冷却速度不均匀,可能会导致铸件中出现热裂纹、气孔等缺陷。
3.模芯破损或散粘:消失模铸造过程中,如果模芯破损或散粘,会导致熔融金属进入模芯使其变形或者破裂。
4.硅溶胶合成不当:硅溶胶在消失模铸造中被用于形成陶瓷壳体,如果硅溶胶的合成过程不当,可能会导致模具的整体性能下降,从而产生各种缺陷。
5.炭化物形成不完全:在消失模铸造中,树脂炭化后形成的剩余炭化物对于确保铸件的完整性非常重要。
如果炭化物形成不完全,可能会导致铸件出现裂纹、气孔等缺陷。
二、消失模铸造缺陷的解决措施:1.设计合理的模具:在消失模铸造过程中,通过合理设计模具的冷却系统,可以提高铸件的冷却均匀性,减少缺陷的发生。
此外,模具的结构也应当稳定,以确保铸件形状和内部结构的准确性。
2.控制熔融金属温度和冷却速度:通过控制熔融金属的温度和冷却速度,可以减少热裂纹和气孔等缺陷的发生。
合理的工艺参数能够提高铸件的材质均匀性和密度。
3.检查模芯质量:在消失模铸造过程中,应该定期检查模芯的质量,以确保其完整性和稳定性。
如果发现模芯破损或者散粘,应及时更换或修复。
4.合理合成硅溶胶:在合成硅溶胶的过程中,应严格按照工艺要求进行操作。
确保硅溶胶的质量和性能,以避免模具整体性能下降。
5.控制炭化物的形成:合理控制炭化物的形成可以避免铸件的裂纹和气孔等缺陷的发生。
在树脂炭化的过程中,应注意控制炭化的温度和时间,确保炭化物的形成充分和均匀。
综上所述,消失模铸造缺陷的产生原因有模具设计不合理、熔融金属冷却不均匀、模芯破损或散粘、硅溶胶合成不当以及炭化物形成不完全等因素。
消失模铸件常见缺陷发生原因

消失模铸件常见缺陷发生原因(造型浇注)一:渣孔1:浇口杯强度不合格2:浇口杯内壁未清理干净3:浇口杯与直浇道对接时浇口杯内耐火胶泥未处理干净4:浇口杯与直浇道对接时没有把掉落在直浇道上的涂料清理干净5:直浇道与横浇道连接处没有把掉落在横浇道上的涂料清理干净6:震实力过大或振动时间过长导致涂料层震裂7:浇注前打渣不到位8:浇注时挡渣不到位9:浇注时压头太高(包嘴距离浇口杯太远)10:浇注温度太高,浇注时间太长(冲刷涂料)二:砂眼1:模型在搬运,埋箱过程中发生磕碰造成涂料层损坏2:震实力过大或振动时间过长导致涂料层震裂3:浇口杯强度不合格4:浇口杯与直浇道连接处、直浇道与横浇道连接处、内浇口与铸件连接处松动,有裂纹或粘接不牢靠5:浇道被掰弯导致涂料层破裂或被掰断6:浇注前浇口杯内部有砂三:变形1:底砂不平2:震实力过大3:振动时间不够或过长4:模型埋箱位置不合理5:负压过大四:冷隔1:负压太小2:浇注温度低,浇注速度慢3:浇注时断流五:粘砂起瘤!:涂料祈面有裂缝2:型砂杂质过多3:底砂不平4:手动填砂不到位5:震实力小或振动时间不够6:负压过大六:气孔1:型砂杂质过多2:负压太小3:浇注速度慢4:浇注时断流5:模型在造型现场摆放时间过长未埋箱造成吸潮6:浇包太凉七:多肉1:用于绑型固定的材料未全部取出2:手动填砂不到位3:砂箱跑火八:缩凹、缩孔1:埋箱时冒口上平面不水平2:埋箱时冒口未放置于最高处3:直浇道与模型距离太近4:浇注温度高5:未按要求放置冷铁九:浇不足1:浇注温度低2:浇注速度慢3:负压太小4:砂箱跑火十:塌箱1:震实力小或振动时间不够2:负压太小3:砂箱排气不畅4:浇注速度慢5:模型在造型现场摆放时间过长未埋箱造成吸潮6:砂箱顶部吃砂量不够7:密封塑料薄膜被烧穿编制:审核:批准:。
消失模铸造缺陷及解决措施

铸造缺陷及解决措施:1、砂眼(或白灰):是铸件的致命缺陷,重则报废。
要做到:①、浇口杯、直浇道、横浇道、内浇道与铸件封闭结合严密。
如不严密,在负压的作用下就会吸入砂子,所以装箱者一定要精心操作,把好各关口。
任何一个薄弱环节或疏忽都会造成此类缺陷。
②浇注系统多刷一遍涂料以增强其强度。
③涂料的强度、透气性、刚度、耐火度、暴热抗烈性也很重要,因为在运输、装填砂、震动时都会出现破坏、变形、开裂、脱落。
④震实时,开始幅度要小,待填满砂时再振幅大些。
⑤浇口杯无浮砂、尘土等杂物。
⑥浇注时,浇包嘴尽量靠近浇口杯,以免压力头过大。
⑦负压过大,使金属液流经开裂、裂纹处时,吸入干砂和杂物可能性加大,粘砂严重。
⑧过快的充型速度使冲刷力加大。
2、气孔:①浇注温度低,充型前沿金属液不能使泡沫充分分解汽化,未分解的残留物质来不及浮集到上面及冒口中,汽化分解生成的气体及残留物不能及时排出铸型而凝固在铸件中,另外,摸样分解不充分,液相残留物会堵塞涂料层,使热解气体排出受阻,腔内形成反压力,充型流动性下降,凝固快。
②涂料透气性差或负压不足,砂子透气性差,不能及时排除型腔内的气体及残留物,在充型压力下形成气孔。
③浇注速度慢,浇口杯未充满,暴露直浇道卷入空气,吸入杂质,形成携裹气孔和渣孔。
④浇杯容量小,金属液形成涡流,侵入空气生成气孔。
⑤浇口杯及浇注系统之间的连接处密封不好,尤其是直浇道和浇口杯。
在负压作用下很容易形成夹砂及气孔。
⑥型砂粒度太细,粉尘含量高,透气性差,负压管道内部堵塞,造成负压度失真,使型腔周围的负压值远低于指示负压,汽化物不能及时排出涂料层而形成气孔或皱皮。
⑦合理的浇注工艺和负压度。
消失模浇注工艺是以充满封闭直浇道为原则,不能忽快忽慢、紊流、断流,更不允许暴露直浇道。
浇注速度,尤其是在行车提升停顿瞬间力求平衡,不断流。
进入尾期慢慢收包,使渣、气、及汽化残留物有充分时间浮集到浇冒口中。
负压度过大,加剧金属液渗透粘砂,并造成附壁效应,不利于液相泡沫被涂层吸附,生成很多气孔。
消失模铸钢件气孔缺陷及解决措施
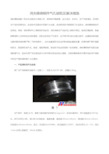
消失模铸钢件气孔缺陷及解决措施消失模铸造是一种近无切削加工铸造工艺,具有铸件精度高、设计灵活、无砂芯、生产环境清洁、投资和生产成本低等优点。
此项技术在国内外发展十分迅速,各项相关技术都取得了长足进步。
消失模铸造技术在铸铝、铸铜、铸铁等材料上得到较好的应用,但在铸钢生产的应用上则相对滞后。
虽然在高锰钢、耐磨钢等钢种上也有成功应用的报道,但在实际的生产过程中,由于铸件在浇注充型过程中,金属液的流动前沿是热解的消失模产物(气体和液体),会与金属液发生反应并影响到金属液质量,如果热解产物不能顺利排出,就容易引起气孔、增碳、增氢等缺陷,使该技术的应用受到一定的限制。
消失模铸钢件的常见缺陷就是气孔,因此对其产生的原因进行分析并提出相应的防止措施,为消失模铸造技术更好地应用于铸钢件的生产提供指导是十分必要的。
一、产品现状及气孔成因我厂生产的铸钢件迷宫环(见图1),材质为ZG270-500,质量为35kg。
生产条件:每箱10件、聚苯乙烯泡塑料的密度为22g/cm3,采用水基涂料,烘干室温度为45℃左右,烘干时间为48h,冒口用AB胶粘接,垂直放置,直浇道45mm×45mm,横浇道40mm×25mm,内浇道为20mm×15mm。
底注,负压度为0.05MPa,浇注温度为1550℃,浇注时间为13~17s,浇注3min后停止抽真空,30min后落砂。
机加工后在补缩冒口处发现大量分散性气孔,出现在铸件内部和铸件表面上(见图1),最大的直径达3mm,深度达4mm,不合格品率达60%。
我们对气孔缺陷进行系统的整理和分析,认为形成的气孔主要是侵入性气孔和析出性气孔,并对产生的原因进行了较深入的探讨。
气孔的形成来源于气体。
消失模铸造铸钢迷宫环上的气孔主要是由泡沫汽化产生的气体侵入金属液析出而形成的侵入性气孔,以及钢液中带入的析出性气孔。
1.侵入性气孔的成因侵入性气孔是消失模铸钢件气孔产生的主要形式,其形成原因有以下几方面。
消失模铸件易出现的缺陷及消除措施

消失模铸件易出现的缺陷及消除措施―攀枝花钢铁研究院试验中心陈建钢1、粘砂金属液渗入型砂中,形成金属与型砂的机械混合物,其中有两种情况:一种是金属液通过涂层开裂处渗入型砂中,形成铁包砂(即机械粘砂),此种缺陷一般可以清除掉;另一种情况是金属透过涂层渗入型砂中,形成难以清除的化学粘砂。
(一)产生的原因(1)在涂层开裂的情况下,由于型砂紧实度不够,型砂颗粒过大及真空度过高产生第一种粘砂情况;(2)在涂层过薄或局部未刷到的情况下,由于金属液温度较高,真空度较大时产生第二种粘砂。
(二)防止措施(1)提高涂层的厚度和耐火度。
(2)造型时紧实力不宜过大以免破坏涂层。
(3)选择合适的负压。
(4)选用较细的原砂。
(5)浇注温度不宜过高。
(6)选择合适的压力头。
2、气孔(一)气孔的分类(1)浇注时卷入空气形成的气孔。
(2)泡沫塑料模样分解产生的气孔。
(3)模样涂层不干引起的气孔。
(4)金属液脱氧不好引起的气孔。
(二)浇注时卷入空气形成的气孔消失模铸造浇注过程中如果直浇道不能充满就会卷入空气,这些气体若不能及时排出,就有产生气孔缺陷的可能。
防止卷入气体的措施:(1)采用封闭式的浇注系统。
(2)浇注时维持浇口盆内有一定的液体金属以保持直浇道处于充满状态。
(3)正确掌握浇注方法,采用慢—快—慢的浇注方法。
(三)泡沫塑料模样分解产生的气孔EPS和STMMA热解后产生大量的气体,如果充型平稳,金属与模样逐层置换,这些气体就会顺利通过液体前沿与模样间的气隙经铸型排出,特别在铸型处于负压状态下更有利气体排放,铸件不易产生气孔缺陷。
但是如果充型过程产生紊流或者顶注,侧注情况下、部分模样被金属液包围后进行分解产生的气体不能从金属液中排出时就会产生缺陷,这种气孔表面有炭黑存在。
防止措施:(1)改进浇注方案,使充型过程逐层置换,不产生紊流。
(2)提高浇注温度。
(3)在不发生紊流的情况下,适当提高真空度,如果发生紊流而产生气孔时,可适当降低真空度。
浅析铸钢件消失模铸造常见缺陷与防治措施
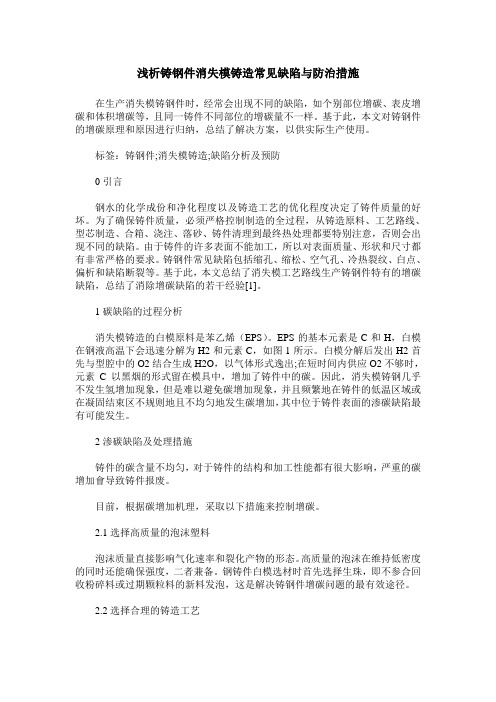
浅析铸钢件消失模铸造常见缺陷与防治措施在生产消失模铸钢件时,经常会出现不同的缺陷,如个别部位增碳、表皮增碳和体积增碳等,且同一铸件不同部位的增碳量不一样。
基于此,本文对铸钢件的增碳原理和原因进行归纳,总结了解决方案,以供实际生产使用。
标签:铸钢件;消失模铸造;缺陷分析及预防0引言钢水的化学成份和净化程度以及铸造工艺的优化程度决定了铸件质量的好坏。
为了确保铸件质量,必须严格控制制造的全过程,从铸造原料、工艺路线、型芯制造、合箱、浇注、落砂、铸件清理到最终热处理都要特别注意,否则会出现不同的缺陷。
由于铸件的许多表面不能加工,所以对表面质量、形状和尺寸都有非常严格的要求。
铸钢件常见缺陷包括缩孔、缩松、空气孔、冷热裂纹、白点、偏析和缺陷断裂等。
基于此,本文总结了消失模工艺路线生产铸钢件特有的增碳缺陷,总结了消除增碳缺陷的若干经验[1]。
1碳缺陷的过程分析消失模铸造的白模原料是苯乙烯(EPS)。
EPS的基本元素是C和H,白模在钢液高温下会迅速分解为H2和元素C,如图1所示。
白模分解后发出H2首先与型腔中的O2结合生成H2O,以气体形式逸出;在短时间内供应O2不够时,元素C以黑烟的形式留在模具中,增加了铸件中的碳。
因此,消失模铸钢几乎不发生氢增加现象,但是难以避免碳增加现象,并且频繁地在铸件的低温区域或在凝固结束区不规则地且不均匀地发生碳增加,其中位于铸件表面的渗碳缺陷最有可能发生。
2渗碳缺陷及处理措施铸件的碳含量不均匀,对于铸件的结构和加工性能都有很大影响,严重的碳增加會导致铸件报废。
目前,根据碳增加机理,采取以下措施来控制增碳。
2.1选择高质量的泡沫塑料泡沫质量直接影响气化速率和裂化产物的形态。
高质量的泡沫在维持低密度的同时还能确保强度,二者兼备。
钢铸件白模选材时首先选择生珠,即不参合回收粉碎料或过期颗粒料的新料发泡,这是解决铸钢件增碳问题的最有效途径。
2.2选择合理的铸造工艺为了防止白模气化和燃烧速度过快,模型装箱采取“能站不要躺”的原则,确保白模不会太快燃烧发气。
消失模铸件表面孔眼、凹陷和网纹及防止

消失模铸件表面孔眼、凹陷和网纹及防止铸造工业网今天进铸造行业群,加微信:132****1807消失模铸件表面除上述的气孔、皱皮、积碳、亮碳、粘砂等外,也会出现同砂型铸造一样的孔眼(渣孔、砂孔、缩孔)、缩坑(凹陷)等缺陷和特有的网纹和较深的龟纹等缺陷。
(1)产生原因1.渣孔。
液体金属带入熔渣及模样裂解的固相产物不能排出而积存,漂浮在铸件表面,喷丸清理后,铸件表面仍会有渣痕的不规则的孔洞。
2.砂孔。
浇注时,干砂粒进入液体金属中,最后积集到铸件表面,其颗粒状分布,抛丸清理后,砂子未清除掉,则铸件表面形成砂粒镶嵌物,若喷掉砂粒,则表面留下眼孔。
3.缩松、缩孔及缩坑(凹陷)。
铸件与内浇道及冒口连接处的热区,由于补缩不良,形成缩孔、缩松缺陷。
铸件厚大部分由于补缩不足形成缩坑(凹陷),往往出现在最后凝固较大表面上。
4.网纹、龟纹。
模样表面珠粒间融合不良,连接处的凹沟间隙和细小珠粒纹路粗而深的龟纹(严重时形成粒珠状表面)。
细小如网状纹的为网纹,主要是因模样珠粒质量不好、粘接不良,尤其是取用泡沫塑料板(型)材加工成模样时,表面粗糙涂料渗入其间,其表面龟纹、网统复印在涂料层上,浇注后铸件表面也出现这些缺陷。
(2)防止措施1.渣孔防止措施。
金属液熔炼除渣要干净,严格挡渣操作,浇冒口系统设计应便于排渣、集渣,提高浇注温度以便渣浮集,也可选用除渣滓性能较好的浇包及设置过滤网挡渣。
2.砂孔防止措施。
模样组合粘接处必须严密,中空直浇道必须密封好;模样避免在砂箱内组合粘接,浇冒口连接处和模样转角处要圆滑过度(避免角缝而夹干砂)。
3.缩孔、缩松及缩坑(凹陷)防止措施。
提高金属液的浇冒口补缩能力,液流从冒口处经过,保持冒口最后凝固;采用发热、保温冒口;充分利用直浇道补缩(组串铸件);合理的浇冒口系统。
4.网纹、龟纹的防止措施。
改善模样表面质量,选用细小的珠粒;合适的发泡剂含量;改进发泡成型的工艺;模样干燥工艺合理,防止局部急剧过热;对模样表面修饰,在模样表面涂料上光洁材料如塑料、浸挂一层薄薄的石蜡、涂上一层硝酸纤维素涂层等都可以改善模样的表面粗糙度,使浇注出的铸件没有晶粒网状及龟纹。
消失模铸造缺陷有

消失模铸造缺陷有:铸铁件表面皱皮( 积碳) ,铸钢件增碳,反喷、气孔,尺寸超差、变形,塌箱、溃型,粘砂。
节瘤、针刺,冷隔( 对火) 、重皮、浇不到( 足) ,渣孔、砂孔、缩孔、凹陷及网纹,内部夹杂物,缩松、组织不均等,其主要影响因素如下。
1 白模( 模样) 涂料1 .1 白模( 模样) 常见缺陷及防止1 .1 .1 模样成型不完整.轮廓不清晰产生原因:( 1 ) 珠粒量不足,未填满模具型腔或珠粒充填不均匀;( 2 ) 发泡的粒子粒度不合适,不均匀;( 3 ) 模具型腔的分布,结构不合理;( 4 ) 操作时进粒子不规范。
防止措施:( 1 ) 珠粒大小要与壁厚匹配。
薄壁模样,应该用小珠粒( 最好用E P MMA、S T MMA 粒子) ;( 2 ) 调整模具型腔内结构及通气孔的布置、大小、数量;( 3 ) 手工填粒时,适当震动或手工帮助填料;用压缩空气喷枪填料时,应适当提高压力和调整进料方向。
1 .1 .2 模样熔结不良.组合松散产生原因:( 1 ) 蒸汽的热量、温度不够。
熟化时间过长;( 2 ) 珠粒粒度太小,发泡或发泡剂含量太少;( 3 ) 珠粒充型不均匀或未填满模型。
防止措施:( 1 )控制预发泡粒子比重,控制熟化;( 2 ) 增加通气的温度、时间和压力;( 3 ) 改用粒度较小的珠粒。
1 .1 .3 模样外表正常.内部呈未曾熔结颗粒产生原因:( 1 ) 蒸汽压力不足,没能进入模型中心或冷气充斥型腔:( 2 ) 成型加热时间短.发泡剂含量太少;( 4 ) 粒子过期变质。
防止措施:( 1 ) 提高模具的预热温度,且使其整体均匀;( 2 ) 提高蒸汽的压力,延长成型时间;( 3 ) 控制粒子熟化时间及发泡剂的用量;( 4 )选用保质粒料。
1 .1 .4 模样熔融.软化产生原因:( 1 ) 成型温度过高,超过了粒子的工艺规范;( 2 )成型发泡时间太长;( 3 )模型通气孔太多,太大。
防止措施:( 1 ) 降低成型发泡温度、压力;( 2 ) 缩时间;( 3 ) 调整模具型腔通气孔大小、数量、分布;1 .5 模样增大。
- 1、下载文档前请自行甄别文档内容的完整性,平台不提供额外的编辑、内容补充、找答案等附加服务。
- 2、"仅部分预览"的文档,不可在线预览部分如存在完整性等问题,可反馈申请退款(可完整预览的文档不适用该条件!)。
- 3、如文档侵犯您的权益,请联系客服反馈,我们会尽快为您处理(人工客服工作时间:9:00-18:30)。
消失模铸造缺陷的产生原理和解决方法
平静心788
2016-06-29
关注
看废品,查原因,找出解决问题的方法,然后,规范工艺纪律,使企业的效益上一个新的台阶。
本文就消失模铸造常见的:碳缺陷、冷隔、皱皮、表面多肉、进渣、进砂、塌箱、粘砂、压痕、鼠咬痕等缺陷总结出产生的原因并提出解决方案。
1 碳缺陷产生的原理和解决方法
碳缺陷是消失模铸造特有的一种缺陷,表现为塑料泡沫熔化产物残留在铸件上,占据了铁液位置,造成碳缺陷。
原因如下:
图1
1.1 负压不够
A. 工艺设计不够:有的企业片面控制粘砂,负压设计太低,如:灰铁铸件用-0.03Mpa,薄壁件勉强交货,厚大件因为气化物多,负压抽不及产生碳缺陷。
解决方法:修改工艺,提高箱内真空度。
B. 设备缺陷
(1)砂箱漏气:砂箱在负压作用下有丝丝漏气声,虽然主管道负压表真空度很高,但砂箱内负压不够,抽不及泡沫气化物,形成碳缺陷。
解决方法:焊补砂箱。
(2)砂箱纱网堵塞使负压抽不走气泡沫气化物,致使箱内负压低,形成碳缺陷。
解决方法:更换砂箱纱网。
(3)砂箱负压管道设计时截面积小,抽气流量不够, 虽然主管道负压表真空度很高,但砂箱内负压不够,抽不及泡沫气化物而形成碳缺陷。
解决方法:加大抽气管道截面积a.加粗管道b.增加负压抽气管道。
图2
(4)自动负压对接装置偏移漏气,造成箱内负压低。
解决方法:检查负压对接装置。
(5)水循环真空泵缺水:无水密封引起负压低。
解决方法:检查水源供水。
(6)砂箱上口有浇注垃圾(塑料薄膜。
铁和砂混合物),使塑料薄膜封不严砂箱,抽真空时漏气,形成碳缺陷。
解决方法:清理砂箱上口浇注垃圾。
图3
(7)橡胶管道与砂箱和负压阀门接口处漏气,箱内负压降低,形成碳缺陷。
解决方法: 用塑料薄膜堵漏。
(8)塑料薄膜抽到主管道内,阻挡气流畅通过,形成碳缺陷。
解决方法:一旦发现负压管道真空度不够,其他原因排除后,检查滤砂罐。
1.2 浇注过程引起负压不够
(1)浇口杯底部塑料薄膜在铁液浇注时被烫破,使箱内负压降低。
形成碳缺陷。
解决方法: 浇口杯底部用泥条隔离塑料薄膜,避免烫破塑料薄膜。
(2)浇注时浇包没有对准浇口杯,使铁液洒到浇口杯外,因散砂厚度不够,铁液烫破塑料薄膜,使箱内负压降低,形成碳缺陷。
解决方法:增加散砂厚度,铁液对准浇口杯浇注。
(3)浇注速度慢或断流时,大量空气进入型腔,使塑料泡沫液化物氧化,产生大量气体,负压抽出流量赶不上塑料泡沫气体产生的量,使多余气化物占据了铁液位置,形成碳缺陷。
解决方法:浇注时,铁液应始终充满浇口杯。
(或直浇道)
1.3 铁液碳含量过高
解决方法:降低碳当量。
1.4 白模密度过大
为了追求白模表面质量,忽识了白模密度控制。
解决方法:控制预发密度及烘干工艺。
1.5 涂料透气性差
解决方法:更换涂料配方或使用(三门峡阳光)商品涂料。
2 冷隔缺陷的产生原理和解决方法
冷隔,就是铁液温度低造成的,导致铸件打压漏气,表面质量差。
造成铁液温度低有以下三个方面。
2.1 铁液温度没浇注前温度已经低了
铸件表现为:铸件大面积冷隔。
解决方法:提高浇注温度。
2.2 浇注操作不合理,导致铁液在铸件上降温太快
(1)浇注流速慢:刚开始浇注时流进的铁液,要熔化浇道部分,损失大量的热量!这股凉铁液流到铸件任何部位都是冷隔。
图4
解决方法:在不反喷的情况下,加快浇注速度。
(2)浇注时断流:铁液断流后,先浇注铁液降温,后浇注铁液如果不能和原铁液熔融,就会出现冷隔。
图5
解决方法:避免断流。
(3)反喷引起:由于黄模没有烘干或白模密度太大或涂料透气性差,浇注时出现反喷,影响浇注工正常浇注,致使铁液流速小或断流,出现铸件冷隔。
图6
解决方法:增加黄模烘干时间;降低白模密度;增加涂料透气性。
2.3 浇注系统设计不合理
内浇道引入位置不合理,使铁液流道太长,铸件出现冷隔。
解决方法:正确设计浇注系统,并加设冷铁液储存包。
3 皱皮缺陷的产生原理和解决方法
皱皮的产生是两股及多股铁液对接熔融不良造成(又叫对火),严重时有空洞出现。
铸件打压漏气。
图7
图8
A. 浇注速度过快,铁液飞溅卷起泡沫塑料,形成碳渣影响铁液熔融。
解决方法:控制浇注速度。
适当阻流。
增大负压解决皱皮缺陷不合适。
B. 铁液温度低, 两股铁液对接熔融不良,
解决方法:增加浇注温度
皱皮和冷隔的共同处:是温度低时缺陷一样,区别是:温度高时冷隔没了但皱皮存在。
4 铸件表面多肉缺陷的原理及解决方法
消失模铸件表面光滑平整,是客户和铸造厂家共同的愿望。
如果工艺控制不当或生产管理失控,就会出现表面如癞蛤蟆皮状丘疹。
针刺。
如蚊虫叮咬包状等铸件表面多肉缺陷。
即影响外观质量,又增加了打磨工作量。
4.1 丘疹状缺陷
丘疹状缺陷是由于白模或黄模在烘干过程中温度失控引起三次发泡。
特征是:铸件表面呈珠粒样均匀凸起,象癞蛤蟆皮样丘疹,凸起面积大并密集,凸起上部光滑无刺,如果是壳体类铸件,凸起部分在外表面。
解决办法:控制烘房温度,避免局部过热。
4.2 针刺缺陷
针刺缺陷是由于负压过高引起,遍布铸件表面, 如果是壳体类铸件,凸起部分内外表面均匀分布,凸起上部有刺状。
解决办法:控制负压。
图9
4.3 包状缺陷
图10
包状缺陷是涂料进烘房后湿热过大起泡形成,铸件表面如蚊子叮咬人后起的包,铸件内外可见。
解决办法:待黄模表面涂层水份少时,再关闭烘房门加热。
4.4 垃圾状缺陷
垃圾状缺陷是由于白模在打磨飞边毛刺时,所产生的泡沫垃圾由于静电原因吸附于白模上,在浸涂时,白模遇水释放塑料泡沫垃圾,并混于涂料上层,塑料泡沫垃圾少时,铸件上不明显,积累的多时,就影响到铸件外观。
其特征是:泡沫垃圾堆积到一定区域,伴有整个珠粒形状铁豆。
解决方法:a过滤涂料;b涂挂前用气吹掉白膜上面泡沫垃圾。
4.5 涂料引起表面缺陷
涂料发酵引起黄模表面起泡,铸件表面有丘疹状缺陷,和三次发泡丘疹状区别是:起泡不密集。
(加入图片)
解决方法:a当班涂料当班用完。
b更换涂料配方或使用三门峡阳光涂料。
5 进渣缺陷的原理和解决方法
进渣(泡沫塑料碳渣见皱皮),有以下几种:炉渣(耐火骨料和熔渣)。
覆盖剂渣。
涂料渣。
泥条等。
5.1 熔炼工序产生进渣
A. 中频炉垃圾含金属锈皮及耐火材料熔渣和骨料渣,铸件上形状为不规则渣孔,熔渣呈黑色,骨料渣呈白色。
图11
图12
B. 浇包耐火材料的热熔物(熔渣也有叫糖渣),铸件表面呈现黑色渣。
图13
C. 覆盖剂渣是用珍珠岩做覆盖剂或除渣剂,遇热膨胀,落在浇包上口或铁液表面,随铁液进入型腔内,铸件表面呈白色球状渣孔
解决方法:(1)使用档渣棉挡渣,(2)使用茶壶包隔离渣,(3) 浇包上部使用压缩气吹干净后再浇注。
(4)浇注时用小铁棍在包口拨渣。
(5)炉内和包内使用高效除渣剂除渣。
(6)使用陶瓷过滤片或纤维过滤网隔离渣。
(7)浇注系统设计聚渣包聚渣。
(8)使用茶壶包时,每包浇注前,先把包口渣打干净或先倒出少量铁液,使渣随铁液流出。
5.2 涂料(或泥条) 渣
A. 由局部塌箱损坏涂料层导致涂料上浮
解决方法:见局部塌箱
B. 由于空心直浇道内径热胶粘接不牢进涂造成,
解决方法:严格白模组模工艺。
C. 塑料泡沫浇口杯涂料层被铁液冲破随铁液进入型腔。
解决方法:塑料泡沫浇口杯比白模多涂刷2—3次,或使用耐火陶瓷浇口杯。
图14
特点:涂料渣外形呈薄壁状,颜色呈灰黑色。
D. 泥条进入是由于封浇口杯用泥条悬于直浇道口内,被铁液冲入型腔,渣孔形状呈泥条状,颜色呈灰黑色。
解决方法:放浇口杯后,清理悬于直浇道内口的泥条。