消失模铸件塌箱缺陷产生的原因分析
消失模铸造缺陷产生的原因及解决措施

消失模铸造缺陷产生的原因及解决措施一、消失模铸造缺陷的原因:1.模具设计不合理:模具的设计不合理是导致消失模铸造缺陷的主要原因之一、例如,模具的冷却系统设计不良或者模具结构不稳定,都会对铸件的形状和内部结构造成影响。
2.熔融金属冷却不均匀:熔融金属冷却不均匀也是导致消失模铸造缺陷的一个重要原因。
由于冷却速度不均匀,可能会导致铸件中出现热裂纹、气孔等缺陷。
3.模芯破损或散粘:消失模铸造过程中,如果模芯破损或散粘,会导致熔融金属进入模芯使其变形或者破裂。
4.硅溶胶合成不当:硅溶胶在消失模铸造中被用于形成陶瓷壳体,如果硅溶胶的合成过程不当,可能会导致模具的整体性能下降,从而产生各种缺陷。
5.炭化物形成不完全:在消失模铸造中,树脂炭化后形成的剩余炭化物对于确保铸件的完整性非常重要。
如果炭化物形成不完全,可能会导致铸件出现裂纹、气孔等缺陷。
二、消失模铸造缺陷的解决措施:1.设计合理的模具:在消失模铸造过程中,通过合理设计模具的冷却系统,可以提高铸件的冷却均匀性,减少缺陷的发生。
此外,模具的结构也应当稳定,以确保铸件形状和内部结构的准确性。
2.控制熔融金属温度和冷却速度:通过控制熔融金属的温度和冷却速度,可以减少热裂纹和气孔等缺陷的发生。
合理的工艺参数能够提高铸件的材质均匀性和密度。
3.检查模芯质量:在消失模铸造过程中,应该定期检查模芯的质量,以确保其完整性和稳定性。
如果发现模芯破损或者散粘,应及时更换或修复。
4.合理合成硅溶胶:在合成硅溶胶的过程中,应严格按照工艺要求进行操作。
确保硅溶胶的质量和性能,以避免模具整体性能下降。
5.控制炭化物的形成:合理控制炭化物的形成可以避免铸件的裂纹和气孔等缺陷的发生。
在树脂炭化的过程中,应注意控制炭化的温度和时间,确保炭化物的形成充分和均匀。
综上所述,消失模铸造缺陷的产生原因有模具设计不合理、熔融金属冷却不均匀、模芯破损或散粘、硅溶胶合成不当以及炭化物形成不完全等因素。
消失模铸件常见缺陷发生原因

消失模铸件常见缺陷发生原因(造型浇注)一:渣孔1:浇口杯强度不合格2:浇口杯内壁未清理干净3:浇口杯与直浇道对接时浇口杯内耐火胶泥未处理干净4:浇口杯与直浇道对接时没有把掉落在直浇道上的涂料清理干净5:直浇道与横浇道连接处没有把掉落在横浇道上的涂料清理干净6:震实力过大或振动时间过长导致涂料层震裂7:浇注前打渣不到位8:浇注时挡渣不到位9:浇注时压头太高(包嘴距离浇口杯太远)10:浇注温度太高,浇注时间太长(冲刷涂料)二:砂眼1:模型在搬运,埋箱过程中发生磕碰造成涂料层损坏2:震实力过大或振动时间过长导致涂料层震裂3:浇口杯强度不合格4:浇口杯与直浇道连接处、直浇道与横浇道连接处、内浇口与铸件连接处松动,有裂纹或粘接不牢靠5:浇道被掰弯导致涂料层破裂或被掰断6:浇注前浇口杯内部有砂三:变形1:底砂不平2:震实力过大3:振动时间不够或过长4:模型埋箱位置不合理5:负压过大四:冷隔1:负压太小2:浇注温度低,浇注速度慢3:浇注时断流五:粘砂起瘤!:涂料祈面有裂缝2:型砂杂质过多3:底砂不平4:手动填砂不到位5:震实力小或振动时间不够6:负压过大六:气孔1:型砂杂质过多2:负压太小3:浇注速度慢4:浇注时断流5:模型在造型现场摆放时间过长未埋箱造成吸潮6:浇包太凉七:多肉1:用于绑型固定的材料未全部取出2:手动填砂不到位3:砂箱跑火八:缩凹、缩孔1:埋箱时冒口上平面不水平2:埋箱时冒口未放置于最高处3:直浇道与模型距离太近4:浇注温度高5:未按要求放置冷铁九:浇不足1:浇注温度低2:浇注速度慢3:负压太小4:砂箱跑火十:塌箱1:震实力小或振动时间不够2:负压太小3:砂箱排气不畅4:浇注速度慢5:模型在造型现场摆放时间过长未埋箱造成吸潮6:砂箱顶部吃砂量不够7:密封塑料薄膜被烧穿编制:审核:批准:。
消失模铸造缺陷产生的原因及解决措施

一、浇注反喷、冒黑烟产生原因:1、浇杯潮湿2、白模密度大3、粘结用胶及表面修补太多4、涂料透气性不好5、砂箱内负压太低、砂箱网堵住6、模型没烘干解决措施:1、浇杯要烘烤(600。
保温1小时)并保持干燥2、降低白模密度(22-25g∕1)3、减少粘结用胶提高白模表面质量减少修补4、合理控制涂料厚度(小件1.2mm,浇道2.0mm,大件1.5-1.8mm,浇道2.5mm),提高涂料的透气性5、增加砂箱内的负压,不低于0∙045Mpa,更换砂箱网6、降低烘房湿度(20%以下),延长烘干时间二、砂孔产生的原因:1、浇包的砂2、浇杯没放好进砂3、浇道没组粘好进砂4、涂料薄或模型破裂进砂5、局部不紧实6、面砂太多随流进砂7、负压太低解决措施:1、修补好浇包2、浇杯下面封泥条后安放稳妥3、组粘好浇道后用快干涂料或泥条涂敷4、合理涂料的厚度损坏的模型不要装箱5、局部不易振实部位要预先填水玻璃砂6、面砂高度80mm左右,浇杯高度要高于面砂高度20mm以上7、负压低产生的塌箱进砂三、碳渣产生的原因:1、白模密度大2、粘结用胶太多及表面修补太多3、砂箱内负压低抽气率低4、浇注温度低5、涂料透气性差6、成分或球化孕育不当7、浇注速度没控制好8、白模气化后残渣多9、工艺不合理解决措施:1、降低白模密度2、提高白模表面质量减少修补量及粘结胶量3、增加砂箱内负压提高抽气率反喷会产生碳渣4、提高浇注温度,减少浇注过程温度损失5、合理化碳含量控制铸钢表面增碳6、合理涂料的透气性7、合理控制铸件成分及提高球化孕育效果8、合理浇注速度使其快速充型9、模型按要求烘干10、选用共聚料I1合理工艺尽量采取顶注方式,铸钢先烧后浇四、涂料产生的缺陷:1、涂料孔洞2、强度不够3、涂料不干4、涂料易返潮5、涂料透气性6、耐火度7、涂料厚度8、涂料变质解决措施:2、提高涂料1、局部不易振实部位及尖角部位涂料脱落造成的涂料孔(一般伴随有砂孔)的常温高温强度防止变形粘砂等缺陷3、确保涂料干燥4、涂料配制合理注意返潮5、合理涂料透气性6、耐火度高涂料不剥壳低了易粘砂7、根据铸件情况确定涂料厚度8、加防腐剂等措施防止变质五、粘砂产生的原因:1、涂料强度差不够2、涂料的骨料粉粗或者砂子粗引起机械粘砂粘涂料3、高温粘砂4、涂料厚度不够5、局部振实不好粘砂6、负压与温度与涂料的技术参数不对粘砂7、模型不干解决措施:1、合理涂料配方提高涂料强度2、合理选用骨料及型砂(批量换新砂时要注意)3、根据铸件壁厚情况选择合理的浇注温度,根据模型选择涂料厚度4、不易振实部位预填砂5、根据负压涂料厚度温度合理选择参数6、确保模型干燥六、渣孔产生的原因:1、炉渣2、拦渣不好3、炉辅料4、化学反应渣5、燃烧残渣6、随流产生的渣解决措施:1、出炉前炉内浇包内除渣2、浇注时茶壶包防渣或包咀硅酸铝纤维板拦渣3、用干净无锈蚀的原料4、球化孕育后要扒渣5、白模粘结修补尽量少6、浇包咀勤修,浇注工艺合理减少冲刷等七、塌箱产生的原因:1、负压太低2、浇注速度慢3、涂料厚度不够4、没有振实到位5、工艺设计不合理6、浇注温度解决措施:1、提高负压2、合理浇注速度3、增加涂料厚度4、不易振实部位预填砂,提高振实度5、合理设计浇注系统(避免大的水平面)6、根据铸件情况选择浇注温度八、铁豆、多肉、橘皮产生的原因:1、涂料产生气泡,露白产生铁豆2、朝下平面涂料剥离产生多肉3、局部振实不良产生粘砂多肉4、靠近模型的砂子中有杂物产生多肉5、浇温低薄壁件浇道附近橘皮解决措施:1、合理搅拌涂料,涂挂防止露白,露白的要补涂2、涂料朝下平面要注意涂料凸出剥离3、不易振实部位预填振实一定要紧实4、砂子除杂等5、薄壁件提高浇注温度。
消失模铸件易出现的缺陷及消除措施

消失模铸件易出现的缺陷及消除措施―攀枝花钢铁研究院试验中心陈建钢1、粘砂金属液渗入型砂中,形成金属与型砂的机械混合物,其中有两种情况:一种是金属液通过涂层开裂处渗入型砂中,形成铁包砂(即机械粘砂),此种缺陷一般可以清除掉;另一种情况是金属透过涂层渗入型砂中,形成难以清除的化学粘砂。
(一)产生的原因(1)在涂层开裂的情况下,由于型砂紧实度不够,型砂颗粒过大及真空度过高产生第一种粘砂情况;(2)在涂层过薄或局部未刷到的情况下,由于金属液温度较高,真空度较大时产生第二种粘砂。
(二)防止措施(1)提高涂层的厚度和耐火度。
(2)造型时紧实力不宜过大以免破坏涂层。
(3)选择合适的负压。
(4)选用较细的原砂。
(5)浇注温度不宜过高。
(6)选择合适的压力头。
2、气孔(一)气孔的分类(1)浇注时卷入空气形成的气孔。
(2)泡沫塑料模样分解产生的气孔。
(3)模样涂层不干引起的气孔。
(4)金属液脱氧不好引起的气孔。
(二)浇注时卷入空气形成的气孔消失模铸造浇注过程中如果直浇道不能充满就会卷入空气,这些气体若不能及时排出,就有产生气孔缺陷的可能。
防止卷入气体的措施:(1)采用封闭式的浇注系统。
(2)浇注时维持浇口盆内有一定的液体金属以保持直浇道处于充满状态。
(3)正确掌握浇注方法,采用慢—快—慢的浇注方法。
(三)泡沫塑料模样分解产生的气孔EPS和STMMA热解后产生大量的气体,如果充型平稳,金属与模样逐层置换,这些气体就会顺利通过液体前沿与模样间的气隙经铸型排出,特别在铸型处于负压状态下更有利气体排放,铸件不易产生气孔缺陷。
但是如果充型过程产生紊流或者顶注,侧注情况下、部分模样被金属液包围后进行分解产生的气体不能从金属液中排出时就会产生缺陷,这种气孔表面有炭黑存在。
防止措施:(1)改进浇注方案,使充型过程逐层置换,不产生紊流。
(2)提高浇注温度。
(3)在不发生紊流的情况下,适当提高真空度,如果发生紊流而产生气孔时,可适当降低真空度。
消失模铸件的缺陷与防治-塌箱

消失模铸件的缺陷与防治-塌箱
在浇注过程中铸型局部向下榻陷,金属也不能充满型腔,使铸件不能形成或局部缺肉称为塌箱。
(1)塌箱产生的原因
1)铸型顶部吃砂量过小,真空度不够,液体金属浮力使铸型顶部型砂溃散造成铸件形成不良。
2)液体金属充型上升速度过慢或停流,使模样与金属前沿间隙过大,铸型内气压与砂型压力总和大于间隙内气压,造成铸型移动和坍塌使铸件形成不良。
3)箱内的原始真空度定的太低,特别是深腔内由于模扬壁的阻隔作用,其真空度更低。
4)浇注过程中由于模样气化产生大量气体,排气过程中,真空度下降且造成砂子流动,损坏涂层使砂子进入型腔。
5)砂温过高(大于70℃),把模样烫坏导致垮砂。
(2)主要防治措施
1)增加铸型顶部吃砂量及在铸型顶部放置压铁,防止液体金属浮力过大造成铸型上面溃散。
2)采用合适的真空度(即浇注前真空度不低于—0.06Mpa、浇注后真空度不低于—
0.05Mpa)及密封措施,以保证型砂的强度。
负压系统有足够大的排气能力。
3)采用强度高透气性好的涂料。
4)选用较粗的原砂增加砂子的透气性。
5)合理地设计浇注系统。
直浇道面积大于内浇道面积,直浇道不能与铸件距离太近,内浇道长度至少为25mm。
6)选用低密度的泡沫塑料(低于26kg/m3)和减少热熔胶的使用量,减少蒸发量。
7)砂温不高于70℃。
必看技术消失模铸造塌箱缺陷问题分析及解决方案
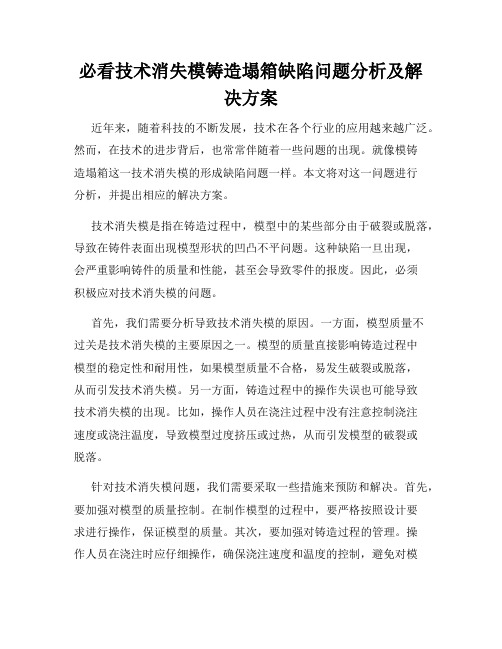
必看技术消失模铸造塌箱缺陷问题分析及解决方案近年来,随着科技的不断发展,技术在各个行业的应用越来越广泛。
然而,在技术的进步背后,也常常伴随着一些问题的出现。
就像模铸造塌箱这一技术消失模的形成缺陷问题一样。
本文将对这一问题进行分析,并提出相应的解决方案。
技术消失模是指在铸造过程中,模型中的某些部分由于破裂或脱落,导致在铸件表面出现模型形状的凹凸不平问题。
这种缺陷一旦出现,会严重影响铸件的质量和性能,甚至会导致零件的报废。
因此,必须积极应对技术消失模的问题。
首先,我们需要分析导致技术消失模的原因。
一方面,模型质量不过关是技术消失模的主要原因之一。
模型的质量直接影响铸造过程中模型的稳定性和耐用性,如果模型质量不合格,易发生破裂或脱落,从而引发技术消失模。
另一方面,铸造过程中的操作失误也可能导致技术消失模的出现。
比如,操作人员在浇注过程中没有注意控制浇注速度或浇注温度,导致模型过度挤压或过热,从而引发模型的破裂或脱落。
针对技术消失模问题,我们需要采取一些措施来预防和解决。
首先,要加强对模型的质量控制。
在制作模型的过程中,要严格按照设计要求进行操作,保证模型的质量。
其次,要加强对铸造过程的管理。
操作人员在浇注时应仔细操作,确保浇注速度和温度的控制,避免对模型造成过大的压力或温度影响。
此外,还可以通过改进模型的结构设计,增加其稳定性和耐用性,减少技术消失模的风险。
除了预防措施外,当技术消失模问题发生时,我们也需要及时采取相应的解决方案。
首先,要尽快发现技术消失模的问题,以便能够及时采取控制措施,避免问题进一步扩大。
其次,可以采用补模的方法来修复受损的模型部分,恢复其原有形状和功能。
最后,要进行严格的质量检查,确保修复后的铸件质量符合要求。
总之,技术消失模是模铸造中常见的缺陷问题之一,对铸件质量和性能有着直接影响。
为了解决这一问题,我们需要加强对模型质量的控制,改进铸造过程的操作管理,以及及时采取解决方案。
通过这些措施的综合应用,我们将能够有效预防和解决技术消失模的问题,提高铸件的质量和可靠性。
消失模常见缺陷与对策
消失模常见缺陷与对策平台消失模常见缺陷与对策局部塌模:局部塌模特征:在内部或外部凹角处浇筑后出现包状突起物,突起物表面粘砂,这些看似沙包的突起物很难清理下来。
清理下来后发现有铁质断面与本体相连,同时在铸件外观上伴有涂料皮子渣孔。
产生原因:凹角处填砂不实,在负压的作用下形成空腔,铁水充型时,由于铁水压力,破坏了涂料层,流到空腔里。
预防方法:1. 改变埋箱角度,保证充型效果2. 使用树脂砂(潮模砂、糊精砂、干性油砂,)局部充填,保证干砂充填效果3. 必要时采用人工辅助填砂烫摸:缺陷特征:铸件局部透皮或局部壁厚变薄或变厚或表面有老鼠尾状条纹突起。
产生原因:1. 砂箱残砂没有扒开,过于集中,热砂子烫坏白膜。
2. 埋箱砂砂温过高,3. 摆模距离过近预防方法:1. 扒平沙箱内残留的热砂子,铺上埋箱砂,保持补填的埋箱砂有一定厚度2. 检测砂温,当埋箱砂温度大于75度时,应停止操作3. 控制摆模距离,防止在浇注第一件时,铁水的高温烫坏第二个白膜塌箱缺陷特征:浇注后铸件大面积塌陷产生原因:1、负压场分配不合理2、泄压过早3、浇注时间过慢4、负压没接上预防方法:1. 合理分配负压场,必要时使用蛇皮管及管路把负压引入黄模内腔2. 规定泄压时间,避免操作者提前泄压3. 浇注时满足工艺要求的时间4. 浇筑前使用手捅一下砂箱,如果发现密封薄膜下面砂子是软的,应立刻检查负压接口,处理好后,才能浇注。
粘砂:缺陷特征:铸件表面热区处,凹角处占有砂砾,抛丸后局部如同上了一层白霜。
清理困难。
如不能去除导致铸件报废产生原因:1、黄模涂层局部脱落2、浇注温度高3、涂层厚度不够4、骨料耐火度差预防方法:1、涂料的润湿性是涂料的一个重要指标,润湿性不好涂料起皮子2、挂涂工艺改进,要做到两点其一挂涂后滴流,涂料不流淌下滴时,应马上送进烘干房3、黄模转运工序要避免磕碰,磕碰后涂料与白膜分离4、架车应有防护装置,如捆绑空气棉条或保温海绵管5、补涂是发现涂层虚连,应去除后再补涂蚊咬缺陷特征:铸件上出现如同蚊子叮咬的包状凸起,多半出现在白膜挂涂时的水平方向产生原因:1. 涂料的润湿性较差,隔水性欠缺,挂涂后再滴流阶段本次挂涂的涂料把上一次的涂料浸湿,使上一次的涂层与白膜分离,在重力作用下局部下沉,形成包状空腔。
消失模铸造常见缺陷问题总结.docx
1.模型制作在消失模铸造工艺中,模型制作是一个非常重要的环节.EPS 原料的选择、模型的加工工艺、尺寸精度、模型生度、浇注时热解产物多少等因索的控制,是获得优质铸件的前提。
现有的中小企业模型制作有以下几种方式:(1)用包装EPS板材切割、粘接而成。
(2)自制模具,委托外厂加工。
(3)自制简易的预发成型设备。
采用上述方法制作模型,普遍存在不重视模样密度变化的现象,特别是模型在委托外厂加工时水分不易控制,经常性出现浇注时铁水从浇口中反喷或铸件出现冷隔、浇不足等现象。
为此在生产过程中应加强对模型密度的检睑,增加对模型的烘干时间等方法;EPS珠粒经工艺实验选定后,不能随意改变原料生产厂家;预发时用称量工具控制珠粒密度,改变凭人工经验控制珠粒密度的方法;采取上述方法后,使问题得到了解决.2.振动存在的问题振动紧实是消失模铸造的四大关键技术之一,振动的作用是使干砂在砂箱中产生动态流动,提高干砂的充填性及其密度,防止出现铸造缺陷。
在干砂振动充填时,比较理想的状况是,干砂在振动过程中进行有序流动,在保证模型不变形的前提下,均匀地充填到模型的各个部位,使砂箱内型砂获得较高和较均匀的充填密度.中小企业的消失模铸造振动台多为自制设备,在振动时,最常见的现象是由于振动操作不当,造成模样变形、涂料层开裂等,从而造成相应的铸造缺陷.有些振动台本身由于激振力过大、同一组电机的偏振块不平衡也易造成模样变形.为此,主要应调整激振力、振幅和振动时间;对于尺寸较大而结构简单的铸件,可将六个电机的三维振动改为双电机的垂直或水平振动; 特别是通过检测仪器对振动台的各参数加以检测和调整,使之达到设计的要求。
3.涂料使用存在问题在消失模铸造工艺中,使用涂料可提高模样的刚度和强度,使EPS模样与铸型隔离,防止粘砂及铸型埸陷;在浇铸过程中允许模样高温分解产物及时顺利地通过涂层排出.涂料一股由耐火材料、粘结剂、悬浮剂等组成,各组成物的比例对涂料的性能有很大影响.但一些企业对涂料组成的作用不十分清楚,随意改动涂料配方和配制工艺,或由于缺少某组成物时继续配制使用,导致涂料性能大大下降;有些企业在模样浸涂烘干工序中存在问题,有时为了缩短时间,在第一次涂料未干的情况下就进行下一次浸涂,导致模型内部未充分干燥,其中存在若水分;而夏季只采用晾晒方法,工艺上存在着不稳定性,造成浇注时反喷或产生气孔;涂层厚度没有注意到根据铸件不同、浇注温度和铁水压头的变化有所变化•只有注意并解决了上述问题,并在操作细节上下功夫,就不会产生由于涂料而产生的铸造缺陷.4.浇注过程存在问题消失模铸造在浇注时,为了排出气体和模样气化残渣,直浇道要有足够的高度以使金属液有足够的压头以推动金属液流稳定快速充型,确保铸件表面完整清晰。
消失模铸造缺陷的产生原理和解决方法完整版
消失模铸造缺陷的产生原理和解决方法标准化管理处编码[BBX968T-XBB8968-NNJ668-MM9N]消失模铸造缺陷的产生原理和解决方法2016-06-29看废品,查原因,找出解决问题的方法,然后,规范工艺纪律,使企业的效益上一个新的台阶。
本文就消失模铸造常见的:碳缺陷、冷隔、皱皮、表面多肉、进渣、进砂、塌箱、粘砂、压痕、鼠咬痕等缺陷总结出产生的原因并提出解决方案。
1 碳缺陷产生的原理和解决方法碳缺陷是消失模铸造特有的一种缺陷,表现为塑料泡沫熔化产物残留在铸件上,占据了铁液位置,造成碳缺陷。
原因如下:图11.1 负压不够A. 工艺设计不够:有的企业片面控制粘砂,负压设计太低,如:灰铁铸件用-0.03Mpa,薄壁件勉强交货,厚大件因为气化物多,负压抽不及产生碳缺陷。
解决方法:修改工艺,提高箱内真空度。
B. 设备缺陷(1)砂箱漏气:砂箱在负压作用下有丝丝漏气声,虽然主管道负压表真空度很高,但砂箱内负压不够,抽不及泡沫气化物,形成碳缺陷。
解决方法:焊补砂箱。
(2)砂箱纱网堵塞使负压抽不走气泡沫气化物,致使箱内负压低,形成碳缺陷。
解决方法:更换砂箱纱网。
(3)砂箱负压管道设计时截面积小,抽气流量不够, 虽然主管道负压表真空度很高,但砂箱内负压不够,抽不及泡沫气化物而形成碳缺陷。
解决方法:加大抽气管道截面积a.加粗管道b.增加负压抽气管道。
图2(4)自动负压对接装置偏移漏气,造成箱内负压低。
解决方法:检查负压对接装置。
(5)水循环真空泵缺水:无水密封引起负压低。
解决方法:检查水源供水。
(6)砂箱上口有浇注垃圾(塑料薄膜。
铁和砂混合物),使塑料薄膜封不严砂箱,抽真空时漏气,形成碳缺陷。
解决方法:清理砂箱上口浇注垃圾。
图3(7)橡胶管道与砂箱和负压阀门接口处漏气,箱内负压降低,形成碳缺陷。
解决方法: 用塑料薄膜堵漏。
(8)塑料薄膜抽到主管道内,阻挡气流畅通过,形成碳缺陷。
解决方法:一旦发现负压管道真空度不够,其他原因排除后,检查滤砂罐。
消失模铸造缺陷的影响因素及防止措施.
防止措施:(1及时加润滑油,保证模具工作表面光滑; (2修改模具结构,出模斜度,取模样工艺; (3延长模具冷却时间。
1.1.12飞边、毛刺
产生原因:模具在分型面处配合不严或操作时
收稿日期:2006-05-09
Abstract:A detailed description was made on the factors causing defects in EPC process production such as metal spraying, blow hole, too big dimension deviation, deformation, etc. The defect reasons were analyzed and relevant prevention measures were proposed. The principles were introduced for selecting dried sand system,
图4中等壁厚蠕墨铸铁件炉前三角试块
Fig.4Suggested wedge specimen for on-spot
control of vermicular iron castings with medium
thickness
75
A-A
40
A
V型缺口
A
180
!!!!!!!!!!!!!!!!!!!!!!!!!!!!!!!!!!!!!!!
(1.学林科技开发服务部铸造研究室,浙江
杭州
310012; 2.凯斯特化工有限公司,浙江
杭州311106; 3.
- 1、下载文档前请自行甄别文档内容的完整性,平台不提供额外的编辑、内容补充、找答案等附加服务。
- 2、"仅部分预览"的文档,不可在线预览部分如存在完整性等问题,可反馈申请退款(可完整预览的文档不适用该条件!)。
- 3、如文档侵犯您的权益,请联系客服反馈,我们会尽快为您处理(人工客服工作时间:9:00-18:30)。
消失模铸件塌箱缺陷产生的原因分析
消失模铸造中,塌箱缺陷是一类较为常见的消失模铸件缺陷,该缺陷往往发生在大件(大平台件更突出)或者是内腔封闭、半封闭件的生产中,从整个消失模铸造流程角度来看,该缺陷一般多发生在浇注或者凝固环节。
塌箱缺陷有时也被称为塌型缺陷或者铸型溃散,随着消失模铸造工艺应用的日趋成熟,有关塌箱缺陷的产生原因和防治办法已经有了相对详尽的研究结果,研究结果证实,塌箱缺陷的产生原因并非单方面的,下面就塌箱缺陷的产生原因做出以下总结:
a. 在浇注过程中,消失模模样分解产生的气体量太多且急,铸型排气速度赶不上,加上真空泵吸气不足,容易导致铸型溃散、坍塌;
b. 金属液“闪流”是造成塌型缺陷产生的原因之一,所谓金属液“闪流”就是在浇注中,部分已经流入填充消失模模样位置的金属液在受到外界作用的情况下改流到其他部位,使得原来置换出来的位置无金属液或者金属充填占据。
该类问题多发生在顶注、铸件存在大平面、一型多模样这几种情况;
c. 如果金属液的浮力过大,会使铸型上部型砂容易变形,可能导致局部溃散;一般情况下,铸型顶部吃砂量小,负压度不够,可能造成铸件成型不良,甚至不能成型;
d. 涂料的耐火度、高温强度不够,极容易产生消失模铸件塌箱缺陷。
消失模模样在浇注过程中有缓冲金属液充型和降温的作用,同时可减弱金属液冲刷铸型。
当金属液置换消失模模样而充型腔后,干砂主要就依靠涂料涂层支撑,当涂层强度不够或者耐火度不够时,局部铸型会发生溃散、坍塌,特别是大件内浇道上方极容易发生坍塌。
以上为消失模铸件塌箱缺陷产生的各种原因,生产中企业可以参考上述原因并结合自身相关操作分析出消失模铸件塌箱缺陷产生的真正原因,并及时做出调整工作。