消失模铸件易出现的缺陷及消除措施
消失模铸造塌箱缺陷解决方案

一、塌箱缺陷的产生原因消失模铸造中,塌箱缺陷是一类较为常见的消失模逐渐缺陷,这类缺陷通常会发生在大件上,或者是半封闭件、内腔封闭生产中,从整个消失模铸造程序来看,它多发生在浇注或者凝固环节.塌箱缺陷也可以称为榻型缺陷,随着消失模铸造工艺日趋成熟,有关这一塌陷的产生原因以及防治方法都有研究结果.塌箱缺陷产生的主要原因有:1 .金属液“闪流”是造成塌型缺陷产生的原因之一,所谓金屈液”闪流■■就是在浇注中,部分已经流入填充消失模模样位置的金属液在受到外界作用的情况下改流到其他部位,使得原来置换出来的位置无金属液或者金属充填占据.2 .涂料的耐火度、高温强度不够,极容易产生消失模铸件塌箱缺陷。
消失模模样在浇注过程中有缓冲金属液充型和降温的作用,同时可减弱金属液冲刷铸型。
当金属液置换消失模模样而充型腔后,干砂主要就依靠涂料涂层支撑,当涂层强度不够或者耐火度不够时,局部铸型会发生溃散、坍塌,特别是大件内浇道上方极容易发生坍塌.3 .在浇注过程中,消失模模样分解产生的气体量太多且急,铸型排气速度赶不上,加上真空泵吸气不足,容易导致铸型溃散.坍塌;以上就是消失模铸造塌箱缺陷产生的原因,提示企业在生产铸造中参考上述因索结合自身操作分析消失模铸件,及时做调整.二、解决塌箱缺陷的对策与方案消失模负压燃烧空壳铸造法指在干砂负压条件下浇冒口点燃泡沫并输送少量的氧气,型内的泡沫即往深处发生迅猛的燃烧,其烟气则随抽真空系统抽走并经净化后外排,待模样烧成空壳后随即浇注高温金属液,从而获得完全无碳缺陷或基本无碳缺陷的精良铸件。
此工艺于2008年10月在桂林首次向国内外铸造行业公布并作公开演示和推广.又将此方法称为“桂林5号空壳铸造法”.然而由于各种铸件生产工艺技术参数不同,其常规装箱薄膜覆盖真空砂箱工艺方法,极易使浇冒口周边薄膜烧坏漏气,加之模样烧成空壳后型腔内真空度急速下降,致使型腔外压强远大于型内压强,极易造成塌箱.因此浇注前选定负压值要求在0∙7MPa以上。
消失模与V法的主要缺陷与应对措施

消失模与V法的主要缺陷与应对措施(一)铸造工业网昨天中国铸造科工贸消失模与V法技术培训中心张玉芳摘要:消失模与V法共同出现的质量问题及解决方法.关键词:消失模与v法质量控制解决方法:①降低原材料S、P含量,达到铸造标准,即S≤0.04以下,P≤0.03以下②提高涂料透气性,以桂林5号为例:铸钢件以100~200目石英砂比例为妥,砂粒之间间隙是透气之根本③白模质量控制在4~16kg之间,以便在高温下气化,顺利排出产生废气,减少碳渣产生。
④增加气流量,就增加真空泵功率。
气压≠气流量,气流量和气化速度对等或略大于气化量,就不容易产生气孔。
消失模与V法铸造存在的主要问题之表现、原因与解决方法主要存在的问题有以下几点:1、气孔:产生的主要原因:①原材料——S、P含量较高②涂料透气性差③白模质量太重,气化速度慢④负压气流量小⑤浇注温度偏低适当提高浇注温度,消失模气化时吸收一定温度,在热幅射作用下逐渐气化,提高浇注温度同时可适当解决掉一定气孔,能得到致密铸件。
铸铁件一般浇注温度1450~1480℃为佳,铸钢件1600~1650℃为佳。
⑥浇冒系统设置不合理合理的浇冒系统是保证铸件质量的前提,对于每一个不同的铸件要一定设置合理的浇冒系统,能立铸件勿卧放置,即要照顾铸件补缩又要防止气孔产生。
⑦脱氧不良脱氧不良直接导致气孔产生。
氧化的金属液会产生多如牛毛的气孔,白模本身是碳氢化合物氧化的金属液在氧的作用下产生细微的水珠从而气化速度放慢,细微的水气伴随金属液进入型腔,气体来不及排出,金属液达到凝固状态,从而产生较多集中在一起气孔,在铸件表面、内部都有大量渣气,所以高温脱氧以防气孔产生,低温氧化千万不能浇注。
⑧型砂粉尘太多,型砂透气性差型砂中的粉尘极大地影响型砂透气性,白模气化不能被及时抽走,气孔渣孔、碳气混合物会聚集在铸件表面,大大影响产品质量,铸件甚至报废。
2、粘砂原因:①涂料太薄,浇注温度偏高②负压太大,气流量小③浇注速度太快,冲刷太猛④涂料耐火强度差解决方法:①铸铁件,涂料厚度一般为1.5~2.5mm,太厚影响透气性,太薄容易粘砂铸钢件在2.0~3.0mm之间,所用骨料不同看铸件材质,浇注温度合理范围铸件所需的合理温度内。
消失模铸造缺陷产生的原因及解决措施

消失模铸造缺陷产生的原因及解决措施一、消失模铸造缺陷的原因:1.模具设计不合理:模具的设计不合理是导致消失模铸造缺陷的主要原因之一、例如,模具的冷却系统设计不良或者模具结构不稳定,都会对铸件的形状和内部结构造成影响。
2.熔融金属冷却不均匀:熔融金属冷却不均匀也是导致消失模铸造缺陷的一个重要原因。
由于冷却速度不均匀,可能会导致铸件中出现热裂纹、气孔等缺陷。
3.模芯破损或散粘:消失模铸造过程中,如果模芯破损或散粘,会导致熔融金属进入模芯使其变形或者破裂。
4.硅溶胶合成不当:硅溶胶在消失模铸造中被用于形成陶瓷壳体,如果硅溶胶的合成过程不当,可能会导致模具的整体性能下降,从而产生各种缺陷。
5.炭化物形成不完全:在消失模铸造中,树脂炭化后形成的剩余炭化物对于确保铸件的完整性非常重要。
如果炭化物形成不完全,可能会导致铸件出现裂纹、气孔等缺陷。
二、消失模铸造缺陷的解决措施:1.设计合理的模具:在消失模铸造过程中,通过合理设计模具的冷却系统,可以提高铸件的冷却均匀性,减少缺陷的发生。
此外,模具的结构也应当稳定,以确保铸件形状和内部结构的准确性。
2.控制熔融金属温度和冷却速度:通过控制熔融金属的温度和冷却速度,可以减少热裂纹和气孔等缺陷的发生。
合理的工艺参数能够提高铸件的材质均匀性和密度。
3.检查模芯质量:在消失模铸造过程中,应该定期检查模芯的质量,以确保其完整性和稳定性。
如果发现模芯破损或者散粘,应及时更换或修复。
4.合理合成硅溶胶:在合成硅溶胶的过程中,应严格按照工艺要求进行操作。
确保硅溶胶的质量和性能,以避免模具整体性能下降。
5.控制炭化物的形成:合理控制炭化物的形成可以避免铸件的裂纹和气孔等缺陷的发生。
在树脂炭化的过程中,应注意控制炭化的温度和时间,确保炭化物的形成充分和均匀。
综上所述,消失模铸造缺陷的产生原因有模具设计不合理、熔融金属冷却不均匀、模芯破损或散粘、硅溶胶合成不当以及炭化物形成不完全等因素。
消失模铸造缺陷及解决措施

铸造缺陷及解决措施:1、砂眼(或白灰):是铸件的致命缺陷,重则报废。
要做到:①、浇口杯、直浇道、横浇道、内浇道与铸件封闭结合严密。
如不严密,在负压的作用下就会吸入砂子,所以装箱者一定要精心操作,把好各关口。
任何一个薄弱环节或疏忽都会造成此类缺陷。
②浇注系统多刷一遍涂料以增强其强度。
③涂料的强度、透气性、刚度、耐火度、暴热抗烈性也很重要,因为在运输、装填砂、震动时都会出现破坏、变形、开裂、脱落。
④震实时,开始幅度要小,待填满砂时再振幅大些。
⑤浇口杯无浮砂、尘土等杂物。
⑥浇注时,浇包嘴尽量靠近浇口杯,以免压力头过大。
⑦负压过大,使金属液流经开裂、裂纹处时,吸入干砂和杂物可能性加大,粘砂严重。
⑧过快的充型速度使冲刷力加大。
2、气孔:①浇注温度低,充型前沿金属液不能使泡沫充分分解汽化,未分解的残留物质来不及浮集到上面及冒口中,汽化分解生成的气体及残留物不能及时排出铸型而凝固在铸件中,另外,摸样分解不充分,液相残留物会堵塞涂料层,使热解气体排出受阻,腔内形成反压力,充型流动性下降,凝固快。
②涂料透气性差或负压不足,砂子透气性差,不能及时排除型腔内的气体及残留物,在充型压力下形成气孔。
③浇注速度慢,浇口杯未充满,暴露直浇道卷入空气,吸入杂质,形成携裹气孔和渣孔。
④浇杯容量小,金属液形成涡流,侵入空气生成气孔。
⑤浇口杯及浇注系统之间的连接处密封不好,尤其是直浇道和浇口杯。
在负压作用下很容易形成夹砂及气孔。
⑥型砂粒度太细,粉尘含量高,透气性差,负压管道内部堵塞,造成负压度失真,使型腔周围的负压值远低于指示负压,汽化物不能及时排出涂料层而形成气孔或皱皮。
⑦合理的浇注工艺和负压度。
消失模浇注工艺是以充满封闭直浇道为原则,不能忽快忽慢、紊流、断流,更不允许暴露直浇道。
浇注速度,尤其是在行车提升停顿瞬间力求平衡,不断流。
进入尾期慢慢收包,使渣、气、及汽化残留物有充分时间浮集到浇冒口中。
负压度过大,加剧金属液渗透粘砂,并造成附壁效应,不利于液相泡沫被涂层吸附,生成很多气孔。
浅析铸钢件消失模铸造常见缺陷与防治措施
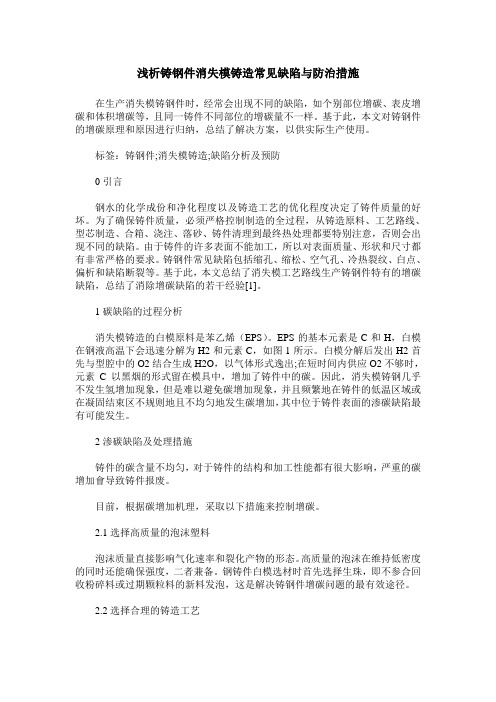
浅析铸钢件消失模铸造常见缺陷与防治措施在生产消失模铸钢件时,经常会出现不同的缺陷,如个别部位增碳、表皮增碳和体积增碳等,且同一铸件不同部位的增碳量不一样。
基于此,本文对铸钢件的增碳原理和原因进行归纳,总结了解决方案,以供实际生产使用。
标签:铸钢件;消失模铸造;缺陷分析及预防0引言钢水的化学成份和净化程度以及铸造工艺的优化程度决定了铸件质量的好坏。
为了确保铸件质量,必须严格控制制造的全过程,从铸造原料、工艺路线、型芯制造、合箱、浇注、落砂、铸件清理到最终热处理都要特别注意,否则会出现不同的缺陷。
由于铸件的许多表面不能加工,所以对表面质量、形状和尺寸都有非常严格的要求。
铸钢件常见缺陷包括缩孔、缩松、空气孔、冷热裂纹、白点、偏析和缺陷断裂等。
基于此,本文总结了消失模工艺路线生产铸钢件特有的增碳缺陷,总结了消除增碳缺陷的若干经验[1]。
1碳缺陷的过程分析消失模铸造的白模原料是苯乙烯(EPS)。
EPS的基本元素是C和H,白模在钢液高温下会迅速分解为H2和元素C,如图1所示。
白模分解后发出H2首先与型腔中的O2结合生成H2O,以气体形式逸出;在短时间内供应O2不够时,元素C以黑烟的形式留在模具中,增加了铸件中的碳。
因此,消失模铸钢几乎不发生氢增加现象,但是难以避免碳增加现象,并且频繁地在铸件的低温区域或在凝固结束区不规则地且不均匀地发生碳增加,其中位于铸件表面的渗碳缺陷最有可能发生。
2渗碳缺陷及处理措施铸件的碳含量不均匀,对于铸件的结构和加工性能都有很大影响,严重的碳增加會导致铸件报废。
目前,根据碳增加机理,采取以下措施来控制增碳。
2.1选择高质量的泡沫塑料泡沫质量直接影响气化速率和裂化产物的形态。
高质量的泡沫在维持低密度的同时还能确保强度,二者兼备。
钢铸件白模选材时首先选择生珠,即不参合回收粉碎料或过期颗粒料的新料发泡,这是解决铸钢件增碳问题的最有效途径。
2.2选择合理的铸造工艺为了防止白模气化和燃烧速度过快,模型装箱采取“能站不要躺”的原则,确保白模不会太快燃烧发气。
消失模铸钢件气孔缺陷及解决措施
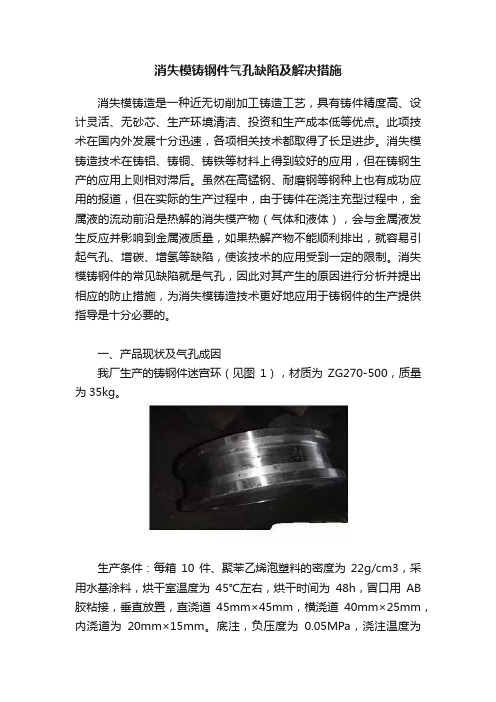
消失模铸钢件气孔缺陷及解决措施消失模铸造是一种近无切削加工铸造工艺,具有铸件精度高、设计灵活、无砂芯、生产环境清洁、投资和生产成本低等优点。
此项技术在国内外发展十分迅速,各项相关技术都取得了长足进步。
消失模铸造技术在铸铝、铸铜、铸铁等材料上得到较好的应用,但在铸钢生产的应用上则相对滞后。
虽然在高锰钢、耐磨钢等钢种上也有成功应用的报道,但在实际的生产过程中,由于铸件在浇注充型过程中,金属液的流动前沿是热解的消失模产物(气体和液体),会与金属液发生反应并影响到金属液质量,如果热解产物不能顺利排出,就容易引起气孔、增碳、增氢等缺陷,使该技术的应用受到一定的限制。
消失模铸钢件的常见缺陷就是气孔,因此对其产生的原因进行分析并提出相应的防止措施,为消失模铸造技术更好地应用于铸钢件的生产提供指导是十分必要的。
一、产品现状及气孔成因我厂生产的铸钢件迷宫环(见图1),材质为ZG270-500,质量为35kg。
生产条件:每箱10件、聚苯乙烯泡塑料的密度为22g/cm3,采用水基涂料,烘干室温度为45℃左右,烘干时间为48h,冒口用AB 胶粘接,垂直放置,直浇道45mm×45mm,横浇道40mm×25mm,内浇道为20mm×15mm。
底注,负压度为0.05MPa,浇注温度为1550℃,浇注时间为13~17s,浇注3min后停止抽真空,30min后落砂。
机加工后在补缩冒口处发现大量分散性气孔,出现在铸件内部和铸件表面上(见图1),最大的直径达3mm,深度达4mm,不合格品率达60%。
我们对气孔缺陷进行系统的整理和分析,认为形成的气孔主要是侵入性气孔和析出性气孔,并对产生的原因进行了较深入的探讨。
气孔的形成来源于气体。
消失模铸造铸钢迷宫环上的气孔主要是由泡沫汽化产生的气体侵入金属液析出而形成的侵入性气孔,以及钢液中带入的析出性气孔。
1.侵入性气孔的成因侵入性气孔是消失模铸钢件气孔产生的主要形式,其形成原因有以下几方面。
消失模铸造缺陷产生的原因及解决措施
一、浇注反喷、冒黑烟产生原因:1、浇杯潮湿2、白模密度大3、粘结用胶及表面修补太多4、涂料透气性不好5、砂箱内负压太低、砂箱网堵住6、模型没烘干解决措施:1、浇杯要烘烤(600°保温1小时)并保持干燥2、降低白模密度(22-25g/L)3、减少粘结用胶提高白模表面质量减少修补4、合理控制涂料厚度(小件1.2mm, 浇道2.0mm, 大件1.5-1.8mm, 浇道2.5mm),提高涂料的透气性5、增加砂箱内的负压,不低于0.045Mpa,更换砂箱网6、降低烘房湿度(20%以下),延长烘干时间二、砂孔产生的原因:1、浇包的砂2、浇杯没放好进砂3、浇道没组粘好进砂4、涂料薄或模型破裂进砂5、局部不紧实6、面砂太多随流进砂7、负压太低解决措施:1、修补好浇包2、浇杯下面封泥条后安放稳妥3、组粘好浇道后用快干涂料或泥条涂敷4、合理涂料的厚度损坏的模型不要装箱5、局部不易振实部位要预先填水玻璃砂6、面砂高度80mm左右,浇杯高度要高于面砂高度20mm以上7、负压低产生的塌箱进砂三、碳渣产生的原因:1、白模密度大2、粘结用胶太多及表面修补太多3、砂箱内负压低抽气率低4、浇注温度低5、涂料透气性差6、成分或球化孕育不当7、浇注速度没控制好8、白模气化后残渣多9、工艺不合理解决措施:1、降低白模密度2、提高白模表面质量减少修补量及粘结胶量3、增加砂箱内负压提高抽气率反喷会产生碳渣4、提高浇注温度,减少浇注过程温度损失5、合理化碳含量控制铸钢表面增碳6、合理涂料的透气性7、合理控制铸件成分及提高球化孕育效果8、合理浇注速度使其快速充型9、模型按要求烘干10、选用共聚料11、合理工艺尽量采取顶注方式,铸钢先烧后浇四、涂料产生的缺陷:1、涂料孔洞2、强度不够3、涂料不干4、涂料易返潮5、涂料透气性6、耐火度7、涂料厚度8、涂料变质解决措施:1、局部不易振实部位及尖角部位涂料脱落造成的涂料孔(一般伴随有砂孔)2、提高涂料的常温高温强度防止变形粘砂等缺陷3、确保涂料干燥4、涂料配制合理注意返潮5、合理涂料透气性6、耐火度高涂料不剥壳低了易粘砂7、根据铸件情况确定涂料厚度8、加防腐剂等措施防止变质五、粘砂产生的原因:1、涂料强度差不够2、涂料的骨料粉粗或者砂子粗引起机械粘砂粘涂料3、高温粘砂4、涂料厚度不够5、局部振实不好粘砂6、负压与温度与涂料的技术参数不对粘砂7、模型不干解决措施:1、合理涂料配方提高涂料强度2、合理选用骨料及型砂(批量换新砂时要注意)3、根据铸件壁厚情况选择合理的浇注温度,根据模型选择涂料厚度4、不易振实部位预填砂5、根据负压涂料厚度温度合理选择参数6、确保模型干燥六、渣孔产生的原因:1、炉渣2、拦渣不好3、炉辅料4、化学反应渣5、燃烧残渣6、随流产生的渣解决措施:1、出炉前炉内浇包内除渣2、浇注时茶壶包防渣或包咀硅酸铝纤维板拦渣3、用干净无锈蚀的原料4、球化孕育后要扒渣5、白模粘结修补尽量少6、浇包咀勤修,浇注工艺合理减少冲刷等七、塌箱产生的原因:1、负压太低2、浇注速度慢3、涂料厚度不够4、没有振实到位5、工艺设计不合理6、浇注温度解决措施:1、提高负压2、合理浇注速度3、增加涂料厚度4、不易振实部位预填砂,提高振实度5、合理设计浇注系统(避免大的水平面)6、根据铸件情况选择浇注温度八、铁豆、多肉、橘皮产生的原因:1、涂料产生气泡,露白产生铁豆2、朝下平面涂料剥离产生多肉3、局部振实不良产生粘砂多肉4、靠近模型的砂子中有杂物产生多肉5、浇温低薄壁件浇道附近橘皮解决措施:1、合理搅拌涂料,涂挂防止露白,露白的要补涂2、涂料朝下平面要注意涂料凸出剥离3、不易振实部位预填,振实一定要紧实4、砂子除杂等5、薄壁件提高浇注温度。
消失模铸件表面孔眼、凹陷和网纹及防止
消失模铸件表面孔眼、凹陷和网纹及防止铸造工业网今天进铸造行业群,加微信:132****1807消失模铸件表面除上述的气孔、皱皮、积碳、亮碳、粘砂等外,也会出现同砂型铸造一样的孔眼(渣孔、砂孔、缩孔)、缩坑(凹陷)等缺陷和特有的网纹和较深的龟纹等缺陷。
(1)产生原因1.渣孔。
液体金属带入熔渣及模样裂解的固相产物不能排出而积存,漂浮在铸件表面,喷丸清理后,铸件表面仍会有渣痕的不规则的孔洞。
2.砂孔。
浇注时,干砂粒进入液体金属中,最后积集到铸件表面,其颗粒状分布,抛丸清理后,砂子未清除掉,则铸件表面形成砂粒镶嵌物,若喷掉砂粒,则表面留下眼孔。
3.缩松、缩孔及缩坑(凹陷)。
铸件与内浇道及冒口连接处的热区,由于补缩不良,形成缩孔、缩松缺陷。
铸件厚大部分由于补缩不足形成缩坑(凹陷),往往出现在最后凝固较大表面上。
4.网纹、龟纹。
模样表面珠粒间融合不良,连接处的凹沟间隙和细小珠粒纹路粗而深的龟纹(严重时形成粒珠状表面)。
细小如网状纹的为网纹,主要是因模样珠粒质量不好、粘接不良,尤其是取用泡沫塑料板(型)材加工成模样时,表面粗糙涂料渗入其间,其表面龟纹、网统复印在涂料层上,浇注后铸件表面也出现这些缺陷。
(2)防止措施1.渣孔防止措施。
金属液熔炼除渣要干净,严格挡渣操作,浇冒口系统设计应便于排渣、集渣,提高浇注温度以便渣浮集,也可选用除渣滓性能较好的浇包及设置过滤网挡渣。
2.砂孔防止措施。
模样组合粘接处必须严密,中空直浇道必须密封好;模样避免在砂箱内组合粘接,浇冒口连接处和模样转角处要圆滑过度(避免角缝而夹干砂)。
3.缩孔、缩松及缩坑(凹陷)防止措施。
提高金属液的浇冒口补缩能力,液流从冒口处经过,保持冒口最后凝固;采用发热、保温冒口;充分利用直浇道补缩(组串铸件);合理的浇冒口系统。
4.网纹、龟纹的防止措施。
改善模样表面质量,选用细小的珠粒;合适的发泡剂含量;改进发泡成型的工艺;模样干燥工艺合理,防止局部急剧过热;对模样表面修饰,在模样表面涂料上光洁材料如塑料、浸挂一层薄薄的石蜡、涂上一层硝酸纤维素涂层等都可以改善模样的表面粗糙度,使浇注出的铸件没有晶粒网状及龟纹。
消失模铸造缺陷有
消失模铸造缺陷有:铸铁件表面皱皮( 积碳) ,铸钢件增碳,反喷、气孔,尺寸超差、变形,塌箱、溃型,粘砂。
节瘤、针刺,冷隔( 对火) 、重皮、浇不到( 足) ,渣孔、砂孔、缩孔、凹陷及网纹,内部夹杂物,缩松、组织不均等,其主要影响因素如下。
1 白模( 模样) 涂料1 .1 白模( 模样) 常见缺陷及防止1 .1 .1 模样成型不完整.轮廓不清晰产生原因:( 1 ) 珠粒量不足,未填满模具型腔或珠粒充填不均匀;( 2 ) 发泡的粒子粒度不合适,不均匀;( 3 ) 模具型腔的分布,结构不合理;( 4 ) 操作时进粒子不规范。
防止措施:( 1 ) 珠粒大小要与壁厚匹配。
薄壁模样,应该用小珠粒( 最好用E P MMA、S T MMA 粒子) ;( 2 ) 调整模具型腔内结构及通气孔的布置、大小、数量;( 3 ) 手工填粒时,适当震动或手工帮助填料;用压缩空气喷枪填料时,应适当提高压力和调整进料方向。
1 .1 .2 模样熔结不良.组合松散产生原因:( 1 ) 蒸汽的热量、温度不够。
熟化时间过长;( 2 ) 珠粒粒度太小,发泡或发泡剂含量太少;( 3 ) 珠粒充型不均匀或未填满模型。
防止措施:( 1 )控制预发泡粒子比重,控制熟化;( 2 ) 增加通气的温度、时间和压力;( 3 ) 改用粒度较小的珠粒。
1 .1 .3 模样外表正常.内部呈未曾熔结颗粒产生原因:( 1 ) 蒸汽压力不足,没能进入模型中心或冷气充斥型腔:( 2 ) 成型加热时间短.发泡剂含量太少;( 4 ) 粒子过期变质。
防止措施:( 1 ) 提高模具的预热温度,且使其整体均匀;( 2 ) 提高蒸汽的压力,延长成型时间;( 3 ) 控制粒子熟化时间及发泡剂的用量;( 4 )选用保质粒料。
1 .1 .4 模样熔融.软化产生原因:( 1 ) 成型温度过高,超过了粒子的工艺规范;( 2 )成型发泡时间太长;( 3 )模型通气孔太多,太大。
防止措施:( 1 ) 降低成型发泡温度、压力;( 2 ) 缩时间;( 3 ) 调整模具型腔通气孔大小、数量、分布;1 .5 模样增大。
必看技术消失模铸造塌箱缺陷问题分析及解决方案
必看技术消失模铸造塌箱缺陷问题分析及解决方案近年来,随着科技的不断发展,技术在各个行业的应用越来越广泛。
然而,在技术的进步背后,也常常伴随着一些问题的出现。
就像模铸造塌箱这一技术消失模的形成缺陷问题一样。
本文将对这一问题进行分析,并提出相应的解决方案。
技术消失模是指在铸造过程中,模型中的某些部分由于破裂或脱落,导致在铸件表面出现模型形状的凹凸不平问题。
这种缺陷一旦出现,会严重影响铸件的质量和性能,甚至会导致零件的报废。
因此,必须积极应对技术消失模的问题。
首先,我们需要分析导致技术消失模的原因。
一方面,模型质量不过关是技术消失模的主要原因之一。
模型的质量直接影响铸造过程中模型的稳定性和耐用性,如果模型质量不合格,易发生破裂或脱落,从而引发技术消失模。
另一方面,铸造过程中的操作失误也可能导致技术消失模的出现。
比如,操作人员在浇注过程中没有注意控制浇注速度或浇注温度,导致模型过度挤压或过热,从而引发模型的破裂或脱落。
针对技术消失模问题,我们需要采取一些措施来预防和解决。
首先,要加强对模型的质量控制。
在制作模型的过程中,要严格按照设计要求进行操作,保证模型的质量。
其次,要加强对铸造过程的管理。
操作人员在浇注时应仔细操作,确保浇注速度和温度的控制,避免对模型造成过大的压力或温度影响。
此外,还可以通过改进模型的结构设计,增加其稳定性和耐用性,减少技术消失模的风险。
除了预防措施外,当技术消失模问题发生时,我们也需要及时采取相应的解决方案。
首先,要尽快发现技术消失模的问题,以便能够及时采取控制措施,避免问题进一步扩大。
其次,可以采用补模的方法来修复受损的模型部分,恢复其原有形状和功能。
最后,要进行严格的质量检查,确保修复后的铸件质量符合要求。
总之,技术消失模是模铸造中常见的缺陷问题之一,对铸件质量和性能有着直接影响。
为了解决这一问题,我们需要加强对模型质量的控制,改进铸造过程的操作管理,以及及时采取解决方案。
通过这些措施的综合应用,我们将能够有效预防和解决技术消失模的问题,提高铸件的质量和可靠性。
- 1、下载文档前请自行甄别文档内容的完整性,平台不提供额外的编辑、内容补充、找答案等附加服务。
- 2、"仅部分预览"的文档,不可在线预览部分如存在完整性等问题,可反馈申请退款(可完整预览的文档不适用该条件!)。
- 3、如文档侵犯您的权益,请联系客服反馈,我们会尽快为您处理(人工客服工作时间:9:00-18:30)。
消失模铸件易出现的缺陷及消除措施―攀枝花钢铁研究院试验中心陈建钢1、粘砂金属液渗入型砂中,形成金属与型砂的机械混合物,其中有两种情况:一种是金属液通过涂层开裂处渗入型砂中,形成铁包砂(即机械粘砂),此种缺陷一般可以清除掉;另一种情况是金属透过涂层渗入型砂中,形成难以清除的化学粘砂。
(一)产生的原因(1)在涂层开裂的情况下,由于型砂紧实度不够,型砂颗粒过大及真空度过高产生第一种粘砂情况;(2)在涂层过薄或局部未刷到的情况下,由于金属液温度较高,真空度较大时产生第二种粘砂。
(二)防止措施(1)提高涂层的厚度和耐火度。
(2)造型时紧实力不宜过大以免破坏涂层。
(3)选择合适的负压。
(4)选用较细的原砂。
(5)浇注温度不宜过高。
(6)选择合适的压力头。
2、气孔(一)气孔的分类(1)浇注时卷入空气形成的气孔。
(2)泡沫塑料模样分解产生的气孔。
(3)模样涂层不干引起的气孔。
(4)金属液脱氧不好引起的气孔。
(二)浇注时卷入空气形成的气孔消失模铸造浇注过程中如果直浇道不能充满就会卷入空气,这些气体若不能及时排出,就有产生气孔缺陷的可能。
防止卷入气体的措施:(1)采用封闭式的浇注系统。
(2)浇注时维持浇口盆内有一定的液体金属以保持直浇道处于充满状态。
(3)正确掌握浇注方法,采用慢—快—慢的浇注方法。
(三)泡沫塑料模样分解产生的气孔EPS和STMMA热解后产生大量的气体,如果充型平稳,金属与模样逐层置换,这些气体就会顺利通过液体前沿与模样间的气隙经铸型排出,特别在铸型处于负压状态下更有利气体排放,铸件不易产生气孔缺陷。
但是如果充型过程产生紊流或者顶注,侧注情况下、部分模样被金属液包围后进行分解产生的气体不能从金属液中排出时就会产生缺陷,这种气孔表面有炭黑存在。
防止措施:(1)改进浇注方案,使充型过程逐层置换,不产生紊流。
(2)提高浇注温度。
(3)在不发生紊流的情况下,适当提高真空度,如果发生紊流而产生气孔时,可适当降低真空度。
(4)提高涂层和型砂透气性。
(四)模样涂层不干引起的气孔涂层烘干不够、模样含有水分或发泡剂含量过高,浇注时会产生大量的气体,甚至产生反喷,这种情况下容易产生气孔,有时也易形成侵入性气孔。
防止措施:(1)模样必须干燥。
(2)涂层必须干透。
(3)型砂必须是干砂。
(五)模样粘结剂引起的气孔模样组合粘接时,采用的粘结剂发气量过大,在金属液充型过程中,局部会产生大量的气体,如果不及时排出就会产生气孔。
防止措施:(1)选用低发气量的模样粘结剂。
(2)在保证粘牢前提下,粘结剂用量越少越好。
3、缩孔和缩松金属由液态变为固态时发生体积收缩,包括液态收缩、凝固收缩及固态收缩。
固态收缩只引起体积轮廓的变化,而凝固收缩与液态收缩如无足够的金属液补给,则必然产生缩孔。
防止措施:(1)增加补缩冒口的体积并采用合理的冒口形状。
(2)提高冒口内金属液的温度。
(3)配合使用冷铁。
(4)浇注球墨铸铁时,浇注后立即增大负压,提高铸型刚度。
4、皱皮(一)按皱皮外观的分类(1)波纹状皱皮。
(2)滴流状皱皮。
(3)冷隔状皱皮。
(4)夹渣状皱皮。
(二)皱皮形成的原因铸铁皱皮是在浇注时聚苯乙烯分解的产物,既有苯乙烯单体的气体也有液态的二聚物,三聚物等。
在液相中存在再聚合物,这当中形成一种粘稠的沥青状的液体,这种液状分解物残留在涂层的内侧,一部分被涂层吸收,一部分在金属与涂层之间形成一层薄膜,这层薄膜在还原气氛下形成细片状或皮屑状的结晶残碳,即光亮碳。
这种密度较低的光亮碳与铁液润湿性极差,因此在铸件表面形成碳沉积。
(三)防止措施(1)采用低密度的热溶胶、EPS 或STMMA、EPMMA等作为模样材料。
(2)合理地设置浇注系统,使其有利于模样分解产物、分散分布或集中顶部排于冒口之中。
(3)提高浇注温度和浇注速度。
(4)提高真空度。
(5)提高涂层和铸型的透气性。
(6)降低合金碳当量,减少自由碳数量。
(7)改进铸件结构,模数大的厚实零件则须设置集渣冒口。
5、珠粒状缺陷泡沫塑料模样表面珠粒间结合不良,涂料渗入珠粒间。
清理后,铸件表面形成类似模样表面珠粒纹路的龟纹,严重时形成粒状铸件表面。
另一种情况是模样干燥时局部急剧受热或温度过高造成珠泡鼓起,浇注后,模样的这种表面被复印下来形成一种消失模特有的缺陷。
防止措施:改善泡沫塑料模样的表面质量,选用细小珠粒,采用合适的发泡剂含量,改进发泡成形工艺及模样干燥工艺,防止局部急剧过热,对模样表面进行修饰等。
6、夹杂物(1)铸件内夹杂物的区分:非金属夹杂物均为无规则块状物,分布在铸件内部。
型砂夹杂物一般呈白色,其余呈黑色。
通过电镜分析,型砂夹杂物和涂料夹杂物的主要成分是SiO2 ,而金属渣夹杂物和泡沫塑料模样热解产生的夹杂物主要成分是碳。
(2)型砂夹杂物:在浇注过程中,铸型型砂被冲入金属中不能排出,存在铸件内部形成白色的颗粒状的夹杂物。
防止措施:制备均匀、连续的涂层。
②模样与内浇道圆滑过渡,尽量防止尖角砂块的存在。
③组模的结合部必须保持严密,尽可能不在砂箱内进行组合操作。
(3)涂料夹杂物:浇注过程中涂层被破坏剥落,进入金属液中;渗入模样组合部位的涂料被液流冲刷掉,也进入金属液中,铸件凝固后形成的缺陷,涂料夹杂物往往是黑色块状。
防止措施:①提高涂层强度。
②模样组合时,结合部位要进行严密处理,防止涂料渗入模样的缝隙中。
(3)金属溶渣夹杂物:浇注时,金属液带入溶渣不能排出留在铸件内部形成的黑色块状夹渣。
防止措施:①加强扒渣和挡渣操作。
②采用底注包或茶壶包浇注。
③采用过滤网过滤金属液。
(4)模样热解产物夹杂物:由于模样高温热解后形成一部分固相和液相产物不能及时排出,残留在铸件内部形成消失模特有的黑色块状产物夹渣。
防止措施:①采用低密度EPS、STMMA等材料。
②浇、冒口系统利于排渣。
③提高浇注温度。
7、节瘤在负压浇注的消失模铸件表面常见均匀分布半圆突出物及较大的瘤状突出物。
有些突出物很难清除,严重时会影响铸件表面质量甚至造成铸件报废。
(一)产生的原因(1)由于模具表面有铸造缺陷(气孔、缩松等)或排气塞(孔)孔眼过大,致使模样表面存在突出物,在负压浇注下,铸件表面形成金属突出物。
(2)涂层内表面存在密布的小气孔或局部形成大气泡,在负压浇注下,铸件表面形成同样大小的金属突出物。
(3)型砂填充不良,在负压作用下,涂层下部干砂出现空洞,金属液通过涂层裂缝进入铸型空洞形成节瘤。
(二)防止措施(1)改善模具表面质量,泡沫塑料模样表面存在突出物应修光滑。
(2)保证涂料质量,发酵的涂料不能使用,涂料粘度应适当。
(3)改进涂刷工艺,防止拐角处出现气泡。
(4)型砂填充和紧实良好,特别注意背砂面的填砂紧实。
(5)振实后抽真空,然后再振实,在涂层下部出现的空洞经过振动紧实可以填实。
8、铸钢件的增碳采用消失模生产铸钢件时,铸件会发生表面增碳、体积增碳、局部增碳等不同情况。
增碳缺陷主要发生在w(C)≤0.45%的铸钢中,一般增碳质量分数在,0.08~0.4%之间。
铸钢件的增碳存在很大的不均匀性,相同钢液成分的不同铸件,相同铸件的不同部位增碳量也是不同的。
它和模样材料、内浇道位置、浇注速度的大小等有关。
铸钢件的增碳使得铸件机加工性能变差,给焊接、热处理带来不利影响,甚至铸件废品。
(一)产生的原因在浇注过程中,模样在高温钢液的作用下发生热解,部分热解产物排除型外,另一部分热解产物聚积在涂层和钢液间或模样与钢液的间隙中。
碳在液态、液! 固和固相线以下的钢液中的扩散系数分别为(6 ~8)×10-9m2/s、×10-9m2/s 和×10-14m2/s。
可见自由碳在钢液和凝固界面上的扩散活力远大于在充型和冷凝过程中的扩散系数,存在着碳向钢液中的对流传质和扩散传质,最终造成铸钢件增碳。
(二)防止措施影响铸钢件增碳的因素较多,根据不同情况采取不同的工艺措施减少增碳。
(1)模样采用SAMMA、EPMMA或低密度的EPS,以减少热解产物的含碳量。
(2)提高浇注速度,尽可能与模样的气化速度相平衡,减少热解产物与钢液的接触时间。
(3)增加涂层的透气性与热解产物的润湿能力,使热解产物尽可能多的排出型外。
(4)选择合适的真空度,高真空度可加速热解产物的排出,但真空度过高易造成附壁效应和严重湍流,使铸钢件增碳加剧。
(5)采用底注式浇注系统,从薄壁处引入内浇道,有利于热解产物积聚在冒口内,降低铸钢件的增碳。
(6)料中加入氧化成分,可减少铸件的表面增碳。
(7)用含有氧化剂的泡沫塑料模,国外利用该办法已解决了铸钢件增碳问题。
(8)用真空消失模和熔模相结合的铸造方法,可以生产出不增碳的铸钢件。
9、铸钢件的热裂热裂是铸钢件常见的铸造缺陷,与传统的砂型铸造相比,消失模铸钢件热裂产生的部位和原因有其自己的特点(一)产生的原因在浇注过程中,部分热解产物透过涂层排出,另一部分热解产物随着钢液的向上充型逐渐上移,当铸件截面突然变薄时,充型钢液湍流严重,卷入钢液中的热解产物量增多,而最上部没有冒口,这些被热解产物污染的钢液不能排除在冒口内,钢液增碳严重,随着钢液中含碳量的增加,铸钢的线收缩系数增大,铸件内应力加剧。
浇注完后,真空度保持较高,型砂强度大,严重阻碍铸件收缩,在拉肋的作用下,连板的平面上产生裂纹。
(二)防止措施(1)降低原钢液中的含碳量,浇注后铸件的含碳量应达到技术要求(2)采取相应的工艺措施降低铸件的增碳量。
(3)选择合适的真空度,缩短保压时间。
(4)制定正确的脱氧工艺,降低钢液中的含铝量,减少热裂倾向。