铸造缺陷分析资料
铸造缺陷质量分析报告

铸造缺陷质量分析报告标题:铸造缺陷质量分析报告摘要:本次报告对一批铸造件的缺陷进行了详细分析,并提供了解决方案,以提高铸件的质量和可靠性。
通过对缺陷的分类、原因分析和改进措施的制定,本报告的目标是降低缺陷率、提高产品质量,并为企业的生产过程提供指导。
一、引言铸造工艺是一种常见且重要的金属加工方式,但由于多种因素的影响,铸造件常常出现各种缺陷。
本报告对以下几种常见铸造缺陷进行了分析:气孔、砂眼、夹渣和缩孔。
二、缺陷分类和特征1. 气孔:气孔是铸造件内部的圆形或椭圆形气体空洞,在表面上通常呈孔状。
这种缺陷的特征是大小不一、分布不均匀,并且可能与材料中的气体分离有关。
2. 砂眼:砂眼是在铸造件表面形成的小凹陷或孔穴,并且通常有砂粒残留。
这种缺陷的主要原因是在型腔填充过程中砂芯未能完全固化或砂芯破裂。
3. 夹渣:夹渣是铸造件内部存在金属残留或其他非金属杂质的缺陷。
它通常表现为呈条状、点状或块状分布的较暗色物质。
4. 缩孔:缩孔是在铸造件中形成的不完全填充的孔洞,通常位于较厚的截面部分。
这种缺陷的主要原因是在凝固过程中金属收缩引起的。
三、缺陷原因分析1. 气孔:气孔的形成主要与以下因素有关:金属液中溶解的气体、型腔设计不合理、浇注过程中液态金属的气体浸润和释放等。
解决方案包括采取适当的除气处理、改进型腔设计、控制浇注工艺等。
2. 砂眼:砂眼通常与砂芯制备和浇注过程中的温度、浇注速度等相关。
解决方案包括优化砂芯制备工艺、调整浇注参数以及改善浇注系统设计等。
3. 夹渣:夹渣的原因主要与金属液的净化和过滤不足、浇注过程中金属液与非金属杂质的接触等有关。
解决方案包括加强净化处理、使用过滤器、改进浇注工艺等。
4. 缩孔:缩孔的形成与金属凝固收缩不平衡、铸造温度过低、浇注过程中金属液的顺流速度等相关。
解决方案包括优化浇注工艺、控制冷却速度等。
四、改进措施根据对缺陷原因的分析,提出了以下改进措施:1. 加强除气处理:通过采用真空或压力浇注等技术,有效去除金属液中的气体;2. 优化砂芯工艺:提高砂芯的强度和温度稳定性,避免砂芯破裂;3. 加强金属液净化:采用有效的净化剂和过滤器,去除金属液中的杂质;4. 调整浇注参数:合理控制浇注温度和速度,确保金属液充满型腔;5. 优化冷却过程:控制冷却速度,减少金属凝固收缩引起的缺陷。
铸造工艺流程中的铸件缺陷分析与改进策略

铸造工艺流程中的铸件缺陷分析与改进策略铸造工艺是一种重要的金属加工方法,用于制造各种形状的金属件。
然而,在铸造过程中,铸件缺陷是一个常见的问题,它会影响到铸件的质量和性能。
因此,对于铸造工艺流程中的铸件缺陷进行深入分析,并提出改进策略,对于提高铸件质量和工艺效率具有重要意义。
一、铸件缺陷的分类与原因分析在铸造工艺中,铸件缺陷可以分为表面缺陷和内部缺陷两类。
常见的表面缺陷包括气孔、砂眼、砂洞等;内部缺陷主要有夹杂物、孔洞、收缩系数不均匀等。
1.1 气孔气孔是铸造工艺中最常见的表面缺陷之一。
其形成的原因通常有两个方面,一是液态金属中溶解气体含量过高,二是在金属凝固过程中,气体生成而未能有效排除。
造成气孔的常见因素包括砂芯质量不佳、浇注温度过高、浇注速度过快等。
1.2 砂眼和砂洞砂眼是指铸件表面局部凹陷的缺陷,而砂洞是指铸件内部或边缘凹陷的缺陷。
主要原因包括模具缺陷、浇注系统设计不合理、浇注金属温度过低等。
1.3 夹杂物夹杂物是指铸件中存在的杂质,如炉渣、油污等。
其主要原因包括铁水净化不彻底、砂芯质量不佳等。
1.4 孔洞孔洞是指铸件内部存在的封闭空腔。
常见的孔洞形式包括气孔和收缩孔。
造成孔洞的原因主要有铁水中含气量高、铸型泥浆含水量高等。
1.5 收缩系数不均匀收缩系数不均匀是指铸件不同部位的收缩量不一致。
这可能会引起铸件的内部应力集中,从而导致开裂和变形。
收缩系数不均匀的原因包括铸造合金的特性、浇注温度的控制等。
二、改进策略为了减少铸件缺陷,提高铸件质量和工艺效率,以下是一些改进策略的具体措施:2.1 优化模具设计模具设计是影响铸件质量的关键因素之一。
通过优化模具结构、提高模具材料质量和表面光洁度,可以减少砂眼、砂洞等表面缺陷的产生。
2.2 控制浇注温度和速度浇注温度和速度对铸件质量有着直接的影响。
合理控制浇注温度和速度,可以降低气孔和夹杂物等缺陷的产生。
2.3 改进铸型材料和工艺选择合适的铸型材料,对铸件质量和工艺效率的提高至关重要。
分析铸造缩松缺陷形成原因及对策

分析铸造缩松缺陷形成原因及对策铸造缩孔缺陷是在铸造过程中常见的一种问题,它会给制造业带来很多麻烦和损失。
本文将分析铸造缩孔缺陷的形成原因,并提出相应的对策,以期为相关行业提供帮助和指导。
一、铸造缩孔缺陷的形成原因分析1.1 完全凝固不均匀在铸造过程中,铸件凝固是逐渐进行的,如果凝固速度不均匀,就会导致缩孔缺陷的形成。
常见的原因包括铸件的凝固时间过短、冷却速度不均匀、局部温度过高等。
1.2 金属液收缩过大铸造过程中,金属液在凝固过程中会收缩,如果收缩过大,就容易形成缩孔。
这主要是由于铸件材料的物理性质不合理,或者是铸型的设计不合理所导致的。
1.3 铸造材料含有气体铸造材料中含有气体会在凝固过程中释放出来,如果释放过快,就会形成孔洞。
常见的原因是铸造材料中含有气体的含量过高,或者是在铸造过程中没有采取有效的排气措施。
1.4 基材与液态金属的相容性差如果铸件的基材与液态金属的相容性差,就容易在凝固过程中产生裂纹和缩孔。
一般来说,基材与液态金属的相容性差会导致界面张力增大,从而影响凝固过程。
二、对策提出2.1 优化铸造工艺参数通过优化铸造工艺参数,可以降低缩孔缺陷的发生概率。
具体来说,可以调整金属液的浇注温度和速度,控制铸件的凝固时间,改进冷却系统等措施。
2.2 优化铸造材料选择合适的铸造材料也是减少缩孔缺陷的关键。
应选择具有较低的收缩率和较好的流动性的材料,以确保凝固过程中的收缩程度可控。
2.3 采取有效的排气措施在铸造过程中,采取有效的排气措施可以减少气体对铸件凝固过程的干扰,从而降低缩孔缺陷的风险。
排气措施可以包括加入剂、提高浇注温度、采取适当的连续浇注等。
2.4 提高基材与液态金属的相容性为了减少缩孔缺陷的形成,可以通过提高基材与液态金属的相容性来增加界面的稳定性。
可以通过改变基材化学成分、调整金属液的配方等方式来实现。
三、结语以上是对铸造缩孔缺陷形成原因及对策的分析。
通过优化铸造工艺、材料选择、排气措施以及提高基材与液态金属的相容性等方法,可以有效降低缩孔缺陷的发生概率,提高铸件的质量和产能。
铸造缺陷鉴别
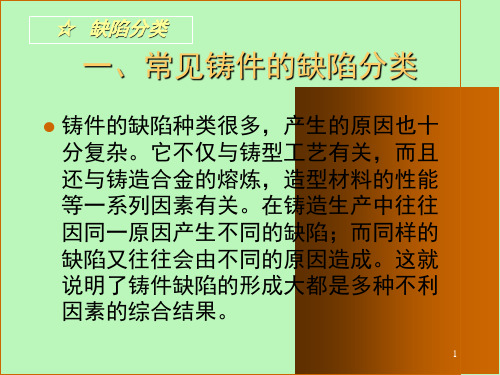
二、孔洞类铸造缺陷的鉴别
①、缩孔常见部位示意 图
17
二、孔洞类铸造缺陷的鉴别
②、缩松:铸件断面上 出现的分散而细小的 缩孔。有时借放大镜 才能发现。缩松部位 在水压试验时会渗漏 疏松:形状和缩松 相似,但孔洞更细小, 组织粗大,石墨粗大 等缺陷也可能导致铸 件组织疏松。
18
二、孔洞类铸造缺陷的鉴别
网状或脉状分布的毛 刺称脉纹。
24
三、多肉类缺陷的鉴别
2、抬 箱(抬 型): 铸件在 分型面 部位高 度和宽 度增大
25
三、多肉类缺陷的鉴别
3、涨砂: 铸件内、 外表面局 部胀大, 形成不规 则的瘤状 金属凸起 物。
26
三、多肉类缺陷的鉴别
4、冲砂: 铸件表面 上有粗糙 不规则的 金属瘤状 物,常位 于浇口附 近。在铸 件其它部 位则往往 出现砂眼。
36
六、残缺类缺陷
浇不到: 由于金 属液未 完全充 满型腔 而产生 的铸件 缺肉。
37
六、残缺类缺陷
2、缺 损:在 铸件清 理或搬 运时, 损坏了 铸件的 完整性。
38
七、尺寸、形状和重量差错类缺陷
1、变型: 由于收 缩应力 或型壁 变形、 开裂引 起的铸 件外形 和尺寸 与图纸 不符。
12
二、孔洞类铸造缺陷的鉴别
③、反应气孔:液态金 属的某些成分之间或 液态金属与铸型在界 面上发生化学反应产 生的气孔。 气孔位于铸件表皮 下,有的呈分散的针 状,有的隐藏在铸件 上部并伴有夹渣。
13
铸件气孔实例(1)
14
铸件气孔实例(2)
15
二、孔洞类铸造缺陷的鉴别
2、缩孔:形状为不规 则的封闭或敞露的孔 洞,孔壁粗糙并带有 枝状晶,且晶粒粗大。 常出现在铸件最后凝 固的部位(热节处)
常见铸造缺陷产生的原因及防止方法

常见铸造缺陷产生的原因及防止方法铸件缺陷种类繁多,产生缺陷的原因也十分复杂.它不仅与铸型工艺有关,而且还与铸造合金的性制、合金的熔炼、造型材料的性能等一系列因素有关.因此,分析铸件缺陷产生的原因时,要从具体情况出发,根据缺陷的特征、位置、采用的工艺和所用型砂等因素,进行综合分析,然后采取相应的技术措施,防止和消除缺陷.一、浇不到1、特征铸件局部有残缺、常出现在薄壁部位、离浇道最远部位或铸件上部.残缺的边角圆滑光亮不粘砂.2、产生原因1 浇注温度低、浇注速度太慢或断续浇注;2 横浇道、内浇道截面积小;3 铁水成分中碳、硅含量过低;4 型砂中水分、煤粉含量过多,发气量大,或含泥量太高,透气性不良;5 上砂型高度不够,铁水压力不足.3、防止方法1 提高浇注温度、加快浇注速度,防止断续浇注;2 加大横浇道和内浇道的截面积;3 调整炉后配料,适当提高碳、硅含量;4 铸型中加强排气,减少型砂中的煤粉,有机物加入量;5 增加上砂箱高度.二、未浇满1、特征铸件上部残缺,直浇道中铁水的水平面与铸件的铁水水平面相平,边部略呈圆形.2、产生原因1 浇包中铁水量不够;2 浇道狭小,浇注速度又过快,当铁水从浇口杯外溢时,操作者误认为铸型已经充满,停浇过早.3、防止方法1 正确估计浇包中的铁水量;2 对浇道狭小的铸型,适当放慢浇注速度,保证铸型充满.三、损伤1、特征铸件损伤断缺.2、产生原因1 铸件落砂过于剧烈,或在搬运过程中铸件受到冲撞而损坏;2 滚筒清理时,铸件装料不当,铸件的薄弱部分在翻滚时被碰断;3 冒口、冒口颈截面尺寸过大;冒口颈没有做出敲断面凹槽.或敲除浇冒口的方法不正确,使铸件本体损伤缺肉.3、防止方法1 铸件在落砂清理和搬运时,注意避免各种形式的过度冲撞、振击,避免不合理的丢放;2 滚筒清理时严格按工艺规程和要求进行操作;3 修改冒口和冒口颈尺寸,做出冒口颈敲断面,正确掌握打浇冒口的方向.四、粘砂和表面粗糙1、特征粘砂是一种铸件表面缺陷,表现为铸件表面粘附着难以清除的砂粒;如铸件经清除砂粒后出现凹凸不平的不光滑表面,称表面粗糙.2、产生原因1 砂粒太粗、砂型紧实度不够;2 型砂中水分太高,使型砂不易紧实;3 浇注速度太快、压力过大、温度过高;4 型砂中煤粉太少;5 模板烘温过高,导致表面型砂干枯;或模板烘温过低,型砂粘附在模板上.3、防止方法1 在透气性足够的情况下,使用较细原砂,并适当提高型砂紧实度;2 保证型砂中稳定的有效煤粉含量;3 严格控制砂水分;4 改进浇注系统,改进浇注操作、降低浇注温度;5 控制模板烘烤温度,一般与型砂温度相等或略高.五、砂眼1、特征在铸件内部或表面充塞有型砂的孔眼.2、产生原因1 型砂表面强度不够;2 模样上无圆角或拔模斜度小导致钩砂、铸型损坏后没修理或没修理好就合箱;3 砂型在浇注前放置时间过长,风干后表面强度降低;4 铸型在合箱时或搬运过程中损坏;5 合箱时型内浮砂未清除干净,合箱后浇口杯没盖好,碎砂掉进铸型.3、防止方法1 提高型砂中粘士含量、及时补加新砂,提高型砂表面强度;2 模样光洁度要高,并合理做出拔模斜度和铸造圆角.损坏的铸型要修好后再合箱;3 缩短浇注前砂型的放置时间;4 合箱或搬运铸型时要小心,避免损坏或掉入砂型腔砂粒;5 合箱前清除型内浮砂,并盖好浇口.六、披缝和胀砂1、特征披缝常出现在铸件分型面处,是垂直于铸件表面,且厚薄不均匀的薄片状金属突起物. 胀砂是铸件内、外表面局部胀大,形成不规则的瘤状金属突起物.2、产生原因1 紧实度不够或不匀;2 面砂强度不够、或型砂水分过高;3 液态金属压头过大、浇注速度太快.3、防止方法1 提高铸型紧实度、避免局部过松;2 调整混砂工艺、控制水分,提高型砂强度;3 降低液态金属的压头、降低浇注速度.七、抬箱1、特征铸件在分型面处有大面积的披缝,使铸型外形尺寸发生变化.抬箱过大,造成跑火——铁水自分型面外溢,严重时造成浇不足缺陷.2、产生原因1 砂箱未紧固、压铁质量不够或去除压铁过早;2 浇注过快,冲击力过大;3 模板翅曲.3、防止方法1 增加压铁重量,特铁水凝固后再去除压铁;2 降低浇包位置,降低浇注速度;3 修正模板.八、掉砂1、特征铸件表面上出现的块状金属突起物,其外形与掉落的砂块很相似.在铸件其它部位,则往往出现砂眼或残缺.2、产生原因1 模样上有深而小的凹槽,同于结构特征或拔模斜度小,起模时将砂型带坏或震裂;2 紧实度不匀,铸型局部强度不足;3 合箱、搬运铸型时,不小心使铸型局部砂块掉落.3、防止方法1 模样拔模斜度要合适、表面光洁;2 铸型紧实度高且均匀;3 合箱、搬运过程中,操作小心.九、错型错箱1、特征铸件的一部分与另一部分在分型面的接缝处错开,发生相对位移,使铸件外形与图纸不相符合.2、产生原因1 模样制作不良,上下模没有对准或模样变形;2 砂箱或模板定位不准确,或定位销松动;3 挤压造型机上零件磨损,例如正压板下衬板、反压板轴承的磨损等;4 浇注时用的套箱变形,搬运、围箱时不注意,使上下铸型发生位移.3、防止方法1 加强模板的检查和修理;定2 经常检查砂箱、模板的定位销及销孔、并合理地安装;3 检查挤压造型机的有关零件,及时调整,磨损大的要更换;4 定期对套箱整形.脱箱后的铸型在搬运时要小心.在面浇注的砂型,应该做一排砂型围一排.十、灰口和麻点1、特征铸件断口呈灰黑色或出现黑色小点,中心部位较多,边部较少,金相观察可见到片状石墨.2、产生原因1 铁水化学成分不合要求,碳、硅含量过高;2 炉前孕育的铋加入浇包内过早或过迟,或是铋量不足.3、防止方法1 正确选择化学成分,合理配料,使铁水中碳、硅量在规定范围内;2 增加铋的加入量并严格炉前孕育工艺.十一、裂纹热裂、冷裂1、特征铸件外部或内部有穿透或不穿透的裂纹.热裂时带有暗色或黑色的氧化表面断口外形曲折.冷裂是较干净的脆性裂纹,断口较平,具有金属光泽或轻微的氧化色泽.2、产生原因1 铁水中碳、硅含苞欲放量过低,含硫量过高;2 浇注温度过高;3 冒口颈过大、过短,造成局部过热严重,或重口太小,补缩不好;4 铸件在清理、运输过程中,受冲击过大.3、防止方法1 控制铁水化学成分在规定的范围内;2 降低浇注温度;3 合理设计冒口系统;4 铸件在清理、运输过程中避免过度冲击.十二、气孔1、特征气孔的孔壁光滑明亮,形状有圆形、梨形和针状,孔的尺寸有大有小,产生在铸件表面或内部.铸件内部的气孔在敲碎后或机械加工时才能被发现.2、产生原因1 小炉料潮湿、锈蚀严重或带有油污,使铁水含气量太多、氧化严重;2 出铁孔、出铁槽、炉衬、浇包衬未洪干;3 浇注温度较低,使气体来不及上浮和逸出;4 炉料中含铝量较高,易造成氢气孔;5 砂型透气性不好、型砂水分高、含煤粉或有机物较多,使浇注时产生大量气体且不易排出.3、防止方法1 炉料要妥善管理,表面要清洁;2 炉缸、前炉、出铁口、出铁槽、浇包必须烘干;3 提高浇注温度;4 不使用铝量过高的废钢;5 适当降低型砂的水分、控制煤粉加入量,扎通气孔等.十三、缩松、疏松1、特征分散、细小的缩孔,带有树枝关结晶的称缩松,比缩松更细小的称疏松.常出现在热世部位.2、产生原因1 铁水中碳、硅含量过低,收缩大;2 浇注速度太快、浇注温度过高,使得液态收缩大;3 浇注系统、冒口设计不当,无法实现顺序凝固;4 冒口太小,补缩不充分.3、防止方法1 控制铁水的化学成分在规定范围内;2 降低浇注速度和浇注温度;3 改进浇冒口系统,利用顺序凝固;4 加大冒口体积,保证充分补缩.十四、反白口1、特征铸件断口内部出现白口组织,边缘部分出现灰口.2、产生原因1 碳、硅含量较高的铁水,含氢量过高;2 炉料中带入的铬等白口形成元素过多;3 元素偏析严重;3、防止方法1 控制化学成分、碳、硅含量不宜过高;2 炉衬、包衬要烘干;型砂水分不宜过高;3 加强炉料管理,减少带入白口化元素.。
铸造缺陷汇总

形状及重 变形 6 量差错类
铸件缺陷
铸件外形扭曲改变,与图纸不符。
错型(错箱) 铸件外形在分型面处错位,一侧多肉,另一侧缺肉;
错芯
铸件内腔沿分芯面错位,一侧多肉,一侧缺肉;
舂移
铸件外形在分型面附近局部突起,形成多肉,通常是单 侧多肉,另一侧不缺肉.
金属夹杂物 铸件中存在不同金属夹杂物
原料混料。
1、型腔内沙粒没清净。
1、浇铸前型腔内砂粒清理干净; 2、浇冒口处保持清洁; 3、加强砂型强度; 4、调整浇铸工艺,调整温度和浇铸速度; 5、合理选择浇冒口位置。
检查合模力或增压情况,调整压射增压机构,使压射增 压峰值降低。
1、改进铸件结构设计,壁厚力求均匀,平滑过渡,铸 件内腔圆角够大; 2、工艺设计合理,尽量减少铸件收缩阻力; 3、适当降低浇注温度; 4、提高模温; 5、缩短开模及抽芯时间; 6、严格控制有害杂质,锌合金降低铅,锡,镉,铁的含 量,铝合金降低锌,铜,铁的含量。
铸造缺陷汇总
序 缺陷类 号型
种类
特征
产生原因
易出现部位
避免措施
反应气孔
析出气孔 1、 气孔
侵入气孔
卷入气孔
飞翅(飞边,
披峰)
2
多肉类铸 件缺陷 毛刺
抬型(抬箱)
冷裂
热裂
白点(发裂) 裂纹,冷
3 隔类铸件
缺陷
冷隔
拉模
4 表面缺陷 流痕 皱皮 缩陷
1、反应气孔一般为针孔。有时反应气孔形成皮下气 孔,位于铸件表层,形状呈针头形或细长圆形。
属本色。
泡,在凝固 过程中气泡未能及时排出而形成气孔 。
3、侵入气孔多呈梨形或椭圆形,位于铸件表层或近 表层,比较集中,尺寸较大,孔壁光滑,表面常呈氧 化色或蓝色。
铸件常见铸造缺陷
铸造常见缺陷特点
缺陷名称:砂眼(加工后)
铸造常见缺陷特点
缺陷名称:铸字不清 缺陷特点: 产生原因:型腔铸字部分起 模不畅,型砂粒度太粗
铸造常见缺陷特点
缺陷名称:披缝 缺陷特点:铸件表面在分模 面处旳规则缩陷。 产生原因: 砂型或砂芯分模 面处旳飞边未清除
铸造常见缺陷特点
铸造常见缺陷特点
缺陷名称:缩孔(大而集中 旳空洞 ) 缺陷特点:铸件厚、断面处 出现形状不规则旳孔眼,孔 旳内壁粗糙。 产生原因:冒口设置不正确 ;合金成份不合格,收缩过 大;浇注温度过高;铸件设 计不合理,无法进行补缩
铸造常见缺陷特点
缺陷名称:疏松(细小而分 散旳空隙) 缺陷特点:铸件厚、断面处 出现形状不规则旳孔眼,孔 旳内壁粗糙。 产生原因:冒口设置不正确 ;合金成份不合格,收缩过 大;浇注温度过高;铸件设 计不合理
铸造常见缺陷特点
缺陷名称:黑皮 缺陷特点:加工面有加工不 到旳地方 产生原因:铸件加工量不足, 铸件变形,夹偏
铸造常见缺陷特点
缺陷名称:黑皮(其二)
铸造常见缺陷特点
缺陷名称:气孔 缺陷特点:铸件内部或表面 有大小不同旳孔眼,孔旳内 壁光滑,多呈圆形。 产生原因:砂型太紧或型砂 透气性差;型砂太湿;砂芯 通气孔堵塞;浇注系统不正 确,气体排不出去
缺陷名称:表面多肉 缺陷特点:铸件表面有多出 旳部分。 产生原因:砂型或砂芯旳相 应部分掉肉。
铸造常见缺陷特点
缺陷名称:表面多肉肉(其 二)
铸造常见缺陷特点
缺陷名称:缺肉(缺料) 缺陷特点:铸件表面有缺乏 一块,可能造成报废。 产生原因:浇冒口切除时带 掉一块;
铸造常见缺陷特点
缺陷名称:表面缩凹 缺陷特点:铸件表面有缩凹。 产生原因:铸件内部收缩
铸造缺陷及其对策
某铸件在浇注过程中,由于模具表面存在油污和杂质,导 致金属液中混入杂质,最终在铸件表面形成明显的夹渣。
解决方案
保持模具表面干净整洁,避免油污和杂质混入金属液;采 用过滤网或过滤器等措施,去除金属液中的杂质。
裂纹案例
裂纹
在铸造过程中,由于铸件结构不合理、模具温度不均匀或金属液冷 却过快等原因,导致铸件中产生裂纹。
夹渣
总结词
夹渣是由于铸造过程中熔渣混入金属液中,在铸件凝固时未能及时浮出而形成的 夹杂物。
详细描述
夹渣通常表现为不规则的块状或颗粒状,大小不一,对铸件的机械性能和使用寿 命有一定影响。夹渣的形成与金属液的净化程度、浇注系统和模具的设计等因素 有关。
裂纹
总结词
裂纹是铸造过程中由于金属液的冷却收缩而产生的缝隙,通 常表现为细长的线性缺陷。
加强生产过程监控
对生产过程进行实时监控,及时发现并处理异常 情况。
3
提高员工技能水平
加强员工技能培训,提高员工操作技能和安全意 识。
引入先进技术与管理方法
引进现代化铸造设备
采用自动化、智能化的铸造设备,提高生产效 率和产品质量。
推行精益生产管理
引入精益生产管理理念和方法,优化生产流程, 降低生产成本。
建立完善的质量管理体系
建立完善的质量管理体系,确保产品质量符合标准要求。
05
铸造缺陷的修复与处理
焊接修复
总结词
焊接修复是一种常见的铸造缺陷修复方法,适用于修复裂纹、断裂等缺陷。
详细描述
焊接修复通过将焊料熔化填充铸造缺陷,冷却后形成坚固的连接,实现对铸造缺陷的修复。焊接修复 具有操作简便、快速、成本低等优点,但需注意焊接过程中可能产生的热影响区和焊接应力,可能导 致新的缺陷或变形。
铸造缺陷
3)抬箱:铸件在分型面处存在着极为严重的飞边,即 有厚片状的、表面光滑的、周边不规则的金属凸出物,其厚 度有时与铸件所增加的高度相等,这种缺陷称为抬箱。
抬箱缺陷产生的原因是:砂型的压铁重量太轻;或上、 下型夹紧不当,液态金属静压力过高等。
4)跑火:又称型漏,“火”代表金属液,是指金属液 充型 超过分型面进入上砂型后,分型面处,由于种种原因有泄漏 口使金属液决口流出型外。
二次渣滓,是指金属液在浇包内挡住或除去一次渣滓 后,进行浇注直至充型过程中,由于金属液的二次氧化或其 它各种原因而形成的渣滓。
图10-12为球铁曲轴在上型中的上表面产生的夹渣,这
种夹渣声称为“黑渣”。黑渣由多种氧化物组成(MgO、 FeO、Al2O3、SiO2稀土氧化物),是一种二次渣滓的夹 渣缺陷,实际上是氧化膜的夹杂类缺陷。
有色金属铸件中,常出现金属夹杂物缺陷。主要防止措 施是:保证金属炉料的纯净度,防止混入外来金属。
2)夹渣:是指铸件内部或表面有外来的非金属夹杂 物,统称为“渣滓”。
夹渣的目视特征是:形状极不规则的孔穴内,包容着渣 滓。
按形成时间的先后,有一次渣滓和二次渣滓两类:
一次渣滓,是指合金冶炼或熔炼时的冶金熔渣(氧化渣、 还原渣、酸性渣、碱性渣等)或熔剂所形成渣滓;或金属 液同炉衬、包衬相互作用生产的渣滓;或金属液炉前处理 (孕育或变质等)生成的渣滓。
3)解释“膨胀缺陷”的“膨胀-应力理论”认 为:膨胀缺陷经过三个阶段。即:
a.砂型表面受热迅速膨胀,
b.砂型表层脱离砂型本体而凸起,
c.砂型表层(干砂层)破裂、金属侵入而造成夹 砂。
夹砂产生倾向 = 铸型表层膨胀力/高湿度弱砂带 强度。
高湿度弱砂带的热湿拉强度越低,产生夹砂的 倾向越大。
铸造的主要缺陷及防止
铸造的主要缺陷及防止1、缺肉缺肉将导致铸件局部加工不起来,造成零件壁厚不均,甚至影响配合或密封。
造成缺肉的原因有许多因素,如工人在清理过程中,打磨量过大;组芯时型芯下偏;模具尺寸超差等。
2、砂眼砂眼是在铸件内部或表面冲塞着型砂的孔洞类缺陷。
主要由于型砂或芯砂强度低;型腔内散砂未吹尽;铸型被破坏;铸件结构不合理等原因产生的。
防止砂眼的方法是:提高型砂强度;合理设计铸件结构;增加紧实度。
3、气孔气孔是气体在金属液结壳之前未及时逸,在铸件内生成的孔洞类缺陷。
气孔的内壁光滑,明亮或带有轻微的氧化色。
铸件中产生气孔后,将会减少其有效承载面积,且在气孔周围会引起应力集中而降低铸件地抗冲击性和抗疲劳性。
气孔还会降低铸件的致密性,致使某些要求承受水压试验的铸件报废。
另外,气孔对铸件的耐腐蚀性和耐热性也有不良的影响。
产生原因一般是金属液除气不良;另一方面是铸型或型芯发气侵入金属液造成的。
防止气孔产生的有效方法是:降低金属液中的含气量,增大砂型的透气性,以及在型腔的最高处增设出气冒口;对铸型或型芯进行烘烤,减少其发气量。
4、粘砂铸件表面上粘附有一层难以清除的砂粒称为粘砂。
粘砂既影响铸件外观,又增加铸件清理和切削加工的工作量,甚至会影响机器的寿命。
(例如铸齿表面有粘砂时容易损坏,泵或发动机等机器零件中若有粘砂,则影响燃料油、气体、润滑油和冷却水等流体的流动,并会沾污和磨损整个机器。
)防止粘砂的方法是:在型砂中加入煤粉,以及在铸型表面涂刷防粘砂涂料等。
5、夹砂夹砂是在铸件表面形成的沟槽和疤痕缺陷,在用湿型铸造厚大平板类铸件时极易产生。
铸件中产生夹砂的部位大多是与砂型上表面相接触的地方,型腔上表面受金属液辐射热的作用,容易拱起和翘曲,当翘起的砂层受金属液流不断冲刷时可能断裂破碎,留在原处或被带入其它部位。
铸件的上表面越大,型砂体积膨胀越大,形成夹砂的倾向性也越大。
防止夹砂的方法是:避免大的平面结构。
6、胀砂浇注时在金属液的压力作用下,铸型型壁移动,铸件局部胀大形成的缺陷。
- 1、下载文档前请自行甄别文档内容的完整性,平台不提供额外的编辑、内容补充、找答案等附加服务。
- 2、"仅部分预览"的文档,不可在线预览部分如存在完整性等问题,可反馈申请退款(可完整预览的文档不适用该条件!)。
- 3、如文档侵犯您的权益,请联系客服反馈,我们会尽快为您处理(人工客服工作时间:9:00-18:30)。
冷裂
热裂和冷裂(2)
冷隔(1)
局 部 放 大
叶片机座 冷隔缺陷
冷隔(2)
典型的冷隔特 征
分类(6)
大 类
序 号
缺陷名称
特征
粘砂足指在铸件表面上,全部或部
14
表
粘砂
分覆盖一层金属(或金属氧化物)与砂 (或涂料)的混合物(或化合物),或一
面
层烧结的型砂,致使铸件表面粗糙
缺 陷
15
粗糙度不良
产品表面粗糙度未达到产品接受标 准
及 24 重量不符
重量超出规定公差范围。
重
量 25 差
变形
由于模样、铸型形状发生变化,或在铸造 或热处理过程中因冷却或收缩不均等原因 而引起的铸件几何形状和尺寸与图面不符
错 类 26
错箱
铸件的一部分或另一部分在分型面上错开, 发生相对的位移
缺 陷 27
偏芯
由于砂芯的位置发生了不应有的变化,而 引起铸件的形状和尺寸与图样不符
形状尺寸不符
变形
我公 司变 形实 例
错箱
上下箱 铸型在 分型面 错开, 致使铸 件轴孔 壁厚有 明显偏
差
偏芯
坭芯偏移致使孔的一 遍加工不出
偏心严重、口 部单边12mm
偏芯缺陷包括坭 芯上浮情况一!
坭芯上浮致使上箱壁厚没有
分类(10)
大 类
序 号
缺陷名称
特征
夹 28 杂 类 29 缺 陷 30
中
框
起
部
位
均
为
飞
翅
飞翅(飞边、披缝)(2)
由于清理位置 狭小,此处的 披缝难于清理
毛刺(脉纹) 典型的坭芯脉纹特征
抬箱(型)
抬箱(型)往往 伴随着厚大的分 型面披缝,抬箱 会致使铸件尺寸 超差,重量加重
胀砂(箱)
胀砂缺陷示意图
多肉(1)
砂型起破导致产品 多肉
产品
正常
产品 形状 多肉
多肉(2)
在铸件表面、内部形状不规则的孔洞。孔 洞不光滑,孔洞全部或部分填充着型砂。
缩松(1)
加工面暴漏的缩 松目视特征
缩松出现的 铸件断面位
置
缺陷放大 图
缺陷的 金相照
片
缩松(2)
加工 面缩 松特 征特
写
渣孔
砂孔
大块 砂块 掉落 形成 的砂 孔
型腔未 清理干 净形成 的砂孔
砂子易从直浇道、 明冒口、出气片掉 入,需防范!!!
披缝)
铸型间隙处的片状金属物
多 2 毛刺(脉纹) 形状不规则刺状金属物,出现在型芯裂缝处;
肉 类
3
抬箱(型)
分型面部位高度增大伴有厚大分型面披缝
缺 4 胀箱(砂)
表面局部增大,形成不规则金属突起物
陷
铸型(坭芯)由于各种原因局部损坏(缺
5
多肉
失)导致铸件此部位存在金属突起物
飞翅(飞边、披缝)(1)
图
气孔
不规则的。有单个存在也有多个聚集存
在。颜色为白色或带有一定暗色。孔壁
常伴有一层氧化皮。
常存在于铸件厚大断面、铸件壁厚交接
缩孔
部位。形状不规则,孔壁粗糙、晶粒粗
大。
气孔(1):气孔的形状
气孔(2):按位置分类
表 面 气 孔
内部气孔
皮下 气孔
按形成原因或形成机理分类: A. 侵入气孔; B. 裹携气孔(或卷入气孔); C. 析出气孔; D. 内生式反应气孔; E. 外生式反应气孔
铁豆 夹砂 结疤
在铸件内部或表面有包含金属小珠的孔眼
指在铸件表面上,有一层金属瘤状和片状 物,在金属瘤片和铸件之间夹有一层型砂。
分类(1)
根据GB/T 5611-1988《铸造术语》规定,将铸造缺陷 分为八大类。102种。
① 多肉类缺陷 ② 孔洞类缺陷 ③ 裂纹、冷隔类缺陷 ④ 表面缺陷 ⑤ 残缺类缺陷 ⑥ 形状及重量差错类缺陷 ⑦ 夹杂类缺陷 ⑧ 性能、成分、组织不合格
分类(2)
大 类
序 号
缺陷名称
特征
1
飞翅(飞边、 产生在铸件分型面、坭芯间隙处、坭芯与
常见铸造缺陷判定
2014.06.18
概念
1、铸造缺陷是铸造生产过程中,由于种种原因, 在铸件表面和内部产生的各种缺陷的总称;
2、铸件缺陷是导致铸件性能低下、使用寿命短、 报废和失效的重要原因;
3、分析铸件缺陷的形貌、特点、产生原因及其形 成过程,目的是防止、减少和消除铸件缺陷。消除 或减少铸件缺陷是铸件质量控制的重要组成部份;
16
流痕
由于型腔表面流刷的涂料不平整致使铸件 表面出现涂料高低不平的痕迹
粘砂
分机械粘砂 和化学粘砂
两种
粗糙度不良
不符要 求部位
符合 要求 部位
流痕
铸件明显留有刷涂料时的 刷痕
分类(7)
大 类
序 号
缺陷名称
特征
表 17
皱皮
铸件表面不规则的粗粒状或皱褶状 疤痕
面
表现为整个铸件表面覆盖着类似天
缺 陷
分类(5)
大序 类号
裂 11 纹 冷 隔 12 类 缺 陷 13
缺陷名称
热裂 冷裂 冷隔
特征
在铸件上有穿透或不穿透的裂纹, 开裂处金属表皮氧化。
在铸件上有穿透或不穿透的裂纹, 开裂处金属表皮不氧化。
在铸件表面有未完全融合的缝隙或 洼坑,其交接边缘是光滑的。
热裂和冷裂(1) 热裂
图6-1 铸钢件的外热裂
缩孔(1)
客户的投诉
热节缩孔
种
缩孔(2)
冒口颈缩孔
内浇口缩孔
分类(4)
大 类
序 号
缺陷名称
特征
孔8 洞 类9 缺 陷 10
缩松 渣孔 砂孔
在铸件内部存在的微小不连贯的缩孔,聚 集在一处或多处,晶粒粗大,各晶粒间存在
着间隙。
在铸件表面、内部形状不规则的孔洞。孔 洞不光滑,孔洞全部或部分填充着渣子。
18
鳄鱼皮(桔皮)
花麻面状的凹斑,在圆柱体(铸件) 表面布满了尺寸均匀、连续分布的
麻点
皱皮
铸
皱
件
皮
上
示
皱
意
皮
图
鳄鱼皮(桔皮)
鳄鱼 皮
(桔 皮)
分类(8)
大 类
序 号
缺陷名称
特征
19
残
缺 20 类
缺 21
陷
22
浇不足 漏箱 少肉 损伤
由于金属液未完全充满型腔而使铸件产生 的残缺。
浇注过程中,金属液由砂型内部流至砂型 外部造成铸件部分或大部缺损。
由于模具或型腔原因造成铸件部分缺损
打箱、搬运、清理或热处理时,损坏了铸 件的完整性
浇不足
由于铁水流动 性不足或浇注 系统截面积太 小等原因造成 铸件部分结构
未充满
漏箱
由于漏 箱致使 产品上 表面未 完全填
充
少肉
损伤
外 力 作 用
分类(9)
大 类
序 号
缺陷名称
特征
形 状
23
形状尺寸不符
铸件形状及实测尺寸不符合图面要求,超 出公差。
冷铁和模具不吻 合引起的铸件多
肉
多肉产生的原因:
1、模具原因。 2、砂(芯)型起破。 3、砂(芯)型损坏 4、砂芯和砂型相接 表面不吻合
5、冷铁和模具不吻 合。
6、砂(芯)局部部 位为充满。
。。。。。。
分类(3)
大 类
序 号
缺陷名称
特征
孔 洞
6
类
缺
陷7
在铸件表面、内部或近表面处存在的大
小不等光滑孔洞。形状有圆的、长的及