常见铸造缺陷分析
铸造缺陷质量分析报告

铸造缺陷质量分析报告标题:铸造缺陷质量分析报告摘要:本次报告对一批铸造件的缺陷进行了详细分析,并提供了解决方案,以提高铸件的质量和可靠性。
通过对缺陷的分类、原因分析和改进措施的制定,本报告的目标是降低缺陷率、提高产品质量,并为企业的生产过程提供指导。
一、引言铸造工艺是一种常见且重要的金属加工方式,但由于多种因素的影响,铸造件常常出现各种缺陷。
本报告对以下几种常见铸造缺陷进行了分析:气孔、砂眼、夹渣和缩孔。
二、缺陷分类和特征1. 气孔:气孔是铸造件内部的圆形或椭圆形气体空洞,在表面上通常呈孔状。
这种缺陷的特征是大小不一、分布不均匀,并且可能与材料中的气体分离有关。
2. 砂眼:砂眼是在铸造件表面形成的小凹陷或孔穴,并且通常有砂粒残留。
这种缺陷的主要原因是在型腔填充过程中砂芯未能完全固化或砂芯破裂。
3. 夹渣:夹渣是铸造件内部存在金属残留或其他非金属杂质的缺陷。
它通常表现为呈条状、点状或块状分布的较暗色物质。
4. 缩孔:缩孔是在铸造件中形成的不完全填充的孔洞,通常位于较厚的截面部分。
这种缺陷的主要原因是在凝固过程中金属收缩引起的。
三、缺陷原因分析1. 气孔:气孔的形成主要与以下因素有关:金属液中溶解的气体、型腔设计不合理、浇注过程中液态金属的气体浸润和释放等。
解决方案包括采取适当的除气处理、改进型腔设计、控制浇注工艺等。
2. 砂眼:砂眼通常与砂芯制备和浇注过程中的温度、浇注速度等相关。
解决方案包括优化砂芯制备工艺、调整浇注参数以及改善浇注系统设计等。
3. 夹渣:夹渣的原因主要与金属液的净化和过滤不足、浇注过程中金属液与非金属杂质的接触等有关。
解决方案包括加强净化处理、使用过滤器、改进浇注工艺等。
4. 缩孔:缩孔的形成与金属凝固收缩不平衡、铸造温度过低、浇注过程中金属液的顺流速度等相关。
解决方案包括优化浇注工艺、控制冷却速度等。
四、改进措施根据对缺陷原因的分析,提出了以下改进措施:1. 加强除气处理:通过采用真空或压力浇注等技术,有效去除金属液中的气体;2. 优化砂芯工艺:提高砂芯的强度和温度稳定性,避免砂芯破裂;3. 加强金属液净化:采用有效的净化剂和过滤器,去除金属液中的杂质;4. 调整浇注参数:合理控制浇注温度和速度,确保金属液充满型腔;5. 优化冷却过程:控制冷却速度,减少金属凝固收缩引起的缺陷。
常见铸件缺陷
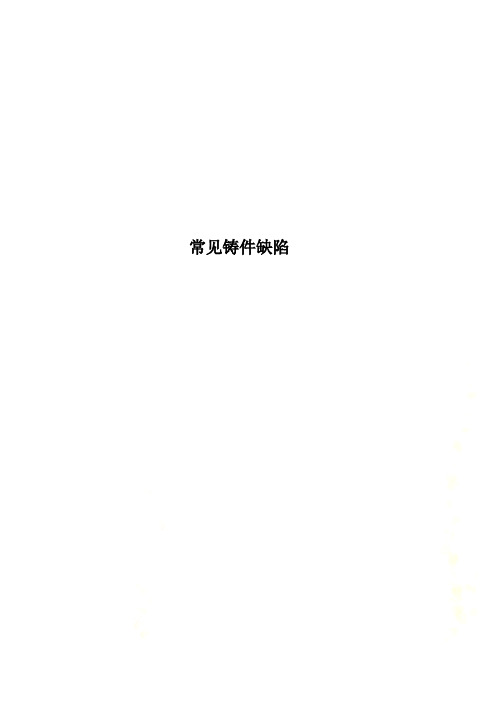
常见铸件缺陷铸件缺陷分析、铸件质量检测数据处理一、铸件缺陷分析的分类(在GB/T5611-1998《铸造名词术语》中归结为8类102种)。
二、铸件缺陷的分析。
1.气孔是气体聚集在铸件表面,皮下和内部而形成的空洞。
气孔的孔壁光滑,稍带氧化彩色,无一定形状,尺寸和位置。
⑴.侵入性,由于浇注过程中液态金属对铸型激烈的热作用,使型砂和芯砂中的发气物(水分、粘接剂和附加物)汽化、分解和燃烧,生存大量气体,以及型腔中原有的气体。
侵入液态金属内部不能逸出所产生的空洞。
(尺寸大)。
⑵.析出性,溶解在液态金属气体中,在冷却凝固过程中,由于溶解度降低而产生的。
(数量多、尺寸小)。
⑶.反应性:液态金属与铸型界面之间、液态金属与渣之间发生化学反应形成的孔洞。
2.夹砂结疤,沟槽、鼠尾(由于型砂腔表面受热膨胀引起的)。
3.粘砂(一般是厚壁部分)类别序号名称特征一、多肉类缺陷1-5冲砂砂型或砂芯表面局部型砂被金属液冲刷掉,在铸件表面的相应部位上形成粗糙、不规则的金属瘤状物。
其常位于浇口附近,被冲刷了的型砂往往在铸件的其它部位形成砂眼1-6 掉砂砂型或砂芯的局部砂块在机械力的作用下掉落,使铸件表面相应部位形成的块状金属突起物。
其外形与掉落的砂块很相识。
在铸件其它部位二、孔洞类缺陷2-1 气孔铸件内由气体形成的孔洞类缺陷。
其表面一般比较光滑,主要呈梨形、圆形和椭圆形。
一般不在铸件表面露出,大孔常孤立存在,小孔则成群出现2-2气缩孔指分散性气孔与缩孔和缩松合并而成的孔洞类铸造缺陷2-5皮下气孔位于铸件表皮下的分散性气孔。
为金属液与砂型之间发生化学反应产生的反应性气孔,形状有针状、蝌蚪状、球状、梨状等,大小不一,深度不等。
通常在机械加工或热处理后才发现2-7 缩孔铸件在凝固过程中,由于补缩不良二产生的孔洞。
形状极不规则,孔壁粗糙并带有枝状晶。
常出现在铸件最后凝固的部位2-8 缩松铸件断面上出现的分散而细小的缩孔。
借助高倍放大镜才能发现的缩松称为显微缩松。
铸造工艺流程中的铸件缺陷分析与改进策略

铸造工艺流程中的铸件缺陷分析与改进策略铸造工艺是一种重要的金属加工方法,用于制造各种形状的金属件。
然而,在铸造过程中,铸件缺陷是一个常见的问题,它会影响到铸件的质量和性能。
因此,对于铸造工艺流程中的铸件缺陷进行深入分析,并提出改进策略,对于提高铸件质量和工艺效率具有重要意义。
一、铸件缺陷的分类与原因分析在铸造工艺中,铸件缺陷可以分为表面缺陷和内部缺陷两类。
常见的表面缺陷包括气孔、砂眼、砂洞等;内部缺陷主要有夹杂物、孔洞、收缩系数不均匀等。
1.1 气孔气孔是铸造工艺中最常见的表面缺陷之一。
其形成的原因通常有两个方面,一是液态金属中溶解气体含量过高,二是在金属凝固过程中,气体生成而未能有效排除。
造成气孔的常见因素包括砂芯质量不佳、浇注温度过高、浇注速度过快等。
1.2 砂眼和砂洞砂眼是指铸件表面局部凹陷的缺陷,而砂洞是指铸件内部或边缘凹陷的缺陷。
主要原因包括模具缺陷、浇注系统设计不合理、浇注金属温度过低等。
1.3 夹杂物夹杂物是指铸件中存在的杂质,如炉渣、油污等。
其主要原因包括铁水净化不彻底、砂芯质量不佳等。
1.4 孔洞孔洞是指铸件内部存在的封闭空腔。
常见的孔洞形式包括气孔和收缩孔。
造成孔洞的原因主要有铁水中含气量高、铸型泥浆含水量高等。
1.5 收缩系数不均匀收缩系数不均匀是指铸件不同部位的收缩量不一致。
这可能会引起铸件的内部应力集中,从而导致开裂和变形。
收缩系数不均匀的原因包括铸造合金的特性、浇注温度的控制等。
二、改进策略为了减少铸件缺陷,提高铸件质量和工艺效率,以下是一些改进策略的具体措施:2.1 优化模具设计模具设计是影响铸件质量的关键因素之一。
通过优化模具结构、提高模具材料质量和表面光洁度,可以减少砂眼、砂洞等表面缺陷的产生。
2.2 控制浇注温度和速度浇注温度和速度对铸件质量有着直接的影响。
合理控制浇注温度和速度,可以降低气孔和夹杂物等缺陷的产生。
2.3 改进铸型材料和工艺选择合适的铸型材料,对铸件质量和工艺效率的提高至关重要。
铸件中常见缺陷

铸件中常见的主要缺陷有:1.气孔这是金属凝固过程中未能逸出的气体留在金属内部形成的小空洞,其内壁光滑,内含气体,对超声波具有较高的反射率,但是又因为其基本上呈球状或椭球状,亦即为点状缺陷,影响其反射波幅。
钢锭中的气孔经过锻造或轧制后被压扁成面积型缺陷而有利于被超声检测所发现,如图2.2所示。
2.缩孔与疏松铸件或钢锭冷却凝固时,体积要收缩,在最后凝固的部分因为得不到液态金属的补充而会形成空洞状的缺陷。
大而集中的空洞称为缩孔,细小而分散的空隙则称为疏松,它们一般位于钢锭或铸件中心最后凝固的部分,其内壁粗糙,周围多伴有许多杂质和细小的气孔。
由于热胀冷缩的规律,缩孔是必然存在的,只是随加工工艺处理方法不同而有不同的形态、尺寸和位置,当其延伸到铸件或钢锭本体时就成为缺陷。
钢锭在开坯锻造时如果没有把缩孔切除干净而带入锻件中就成为残余缩孔(缩孔残余、残余缩管),如图2.3、2.4、2.5所示。
如果铸件的型模设计不当、浇注工艺不当等,也会在铸件与型模接触的部位产生疏松,如图2.28所示。
断口照片中的黑色部分即为疏松部位,其呈现黑色是因为该工件已经过退火处理,使得疏松部位被氧化和渗入机油所致。
图2.28 W18钢铸件-用作铣刀齿,采用超声纵波垂直入射多次底波衰减法发现的疏松断口照片3.夹渣熔炼过程中的熔渣或熔炉炉体上的耐火材料剥落进入液态金属中,在浇注时被卷入铸件或钢锭本体内,就形成了夹渣缺陷。
夹渣通常不会单一存在,往往呈密集状态或在不同深度上分散存在,它类似体积型缺陷然而又往往有一定线度。
4.夹杂熔炼过程中的反应生成物(如氧化物、硫化物等)-非金属夹杂,如图2.1和2.6,或金属成分中某些成分的添加料未完全熔化而残留下来形成金属夹杂,如高密度、高熔点成分-钨、钼等,如图2.29,也有如图2.24所示钛合金棒材中的纯钛偏析。
(a)(b)(c)(d)(e)图2.29 BT9钛合金锻制饼坯中的钼夹杂:(a)剖面低倍照片;(b)X射线照相底片;(c)C扫描显示(图中四个白色点状显示为同一个缺陷,是使用水浸点聚焦探头以不同灵敏度检测的结果,其他分散细小的白色点状为与该缺陷无关的杂波显示);(d)B扫描显示;(e)3D显示5.偏析铸件或钢锭中的偏析主要指冶炼过程中或金属的熔化过程中因为成分分布不均而形成的成分偏析,有偏析存在的区域其力学性能有别于整个金属基体的力学性能,差异超出允许标准范围就成为缺陷,如图2.23和2.24、2.27所示。
常见压铸件缺陷及解决方法

常见压铸件缺陷及解决方法(总10页)--本页仅作为文档封面,使用时请直接删除即可----内页可以根据需求调整合适字体及大小--常见压铸件缺陷及解决方法一、流痕其他名称:条纹。
特征:铸件表面上呈现与金属液流动方向相一致的,用手感觉得出的局部下陷光滑纹路。
此缺陷无发展方向,用抛光法能去处。
产生原因:1、两股金属流不同步充满型腔而留下的痕迹。
2、模具温度低,如锌合金模温低于150℃,铝合金模温低于180℃,都易产生这类缺陷。
3、填充速度太高。
4、涂料用量过多。
排除措施:1、调整内浇口截面积或位置。
2、调整模具温度,增大溢流槽。
3、适当调整填充速度以改变金属液填充型腔的流态。
4、涂料使用薄而均匀。
二、冷隔,水纹其他名称:冷接(对接),水纹。
特征:温度较低的金属流互相对接但未熔合而出现的缝隙,呈不规则的线形,有穿透的和不穿透的两种,在外力的作用下有发展的趋势。
产生原因:1、金属液浇注温度低或模具温度低。
2、合金成分不符合标准,流动性差。
3、金属液分股填充,熔合不良。
4、浇口不合理,流程太长。
5、填充速度低或排气不良。
6、比压偏低。
排除措施:1、适当提高浇注温度和模具温度。
2、改变合金成分,提高流动性。
3、改进浇注系统,加大内浇口速度,改善填充条件。
4、改善排溢条件,增大溢流量。
5、提高压射速度,改善排气条件。
6、提高比压三、擦伤其他名称:拉力、拉痕、粘模伤痕。
特征:顺着脱模方向,由于金属粘附,模具制造斜度太小而造成铸件表面的拉伤痕迹,严重时成为拉伤面。
产生原因:1、型芯、型壁的铸造斜度太小或出现倒斜度。
2、型芯、型壁有压伤痕。
3、合金粘附模具。
4、铸件顶出偏斜,或型芯轴线偏斜。
5、型壁表面粗糙。
6、涂料常喷涂不到。
7、铝合金中含铁量低于%。
排除措施:1、修正模具,保证制造斜度。
2、打光压痕。
3、合理设计浇注系统,避免金属流对冲型芯、型壁,适当降低填充速度。
4、修正模具结构。
5、打光表面。
6、涂料用量薄而均匀,不能漏喷涂料。
常见压铸件缺陷及解决方法
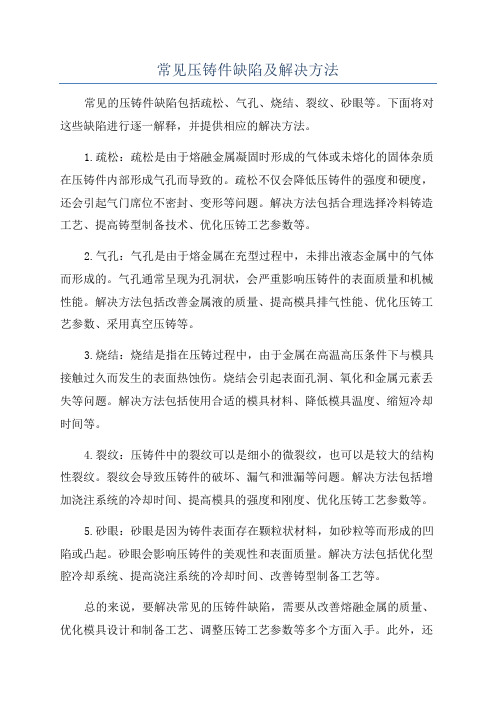
常见压铸件缺陷及解决方法常见的压铸件缺陷包括疏松、气孔、烧结、裂纹、砂眼等。
下面将对这些缺陷进行逐一解释,并提供相应的解决方法。
1.疏松:疏松是由于熔融金属凝固时形成的气体或未熔化的固体杂质在压铸件内部形成气孔而导致的。
疏松不仅会降低压铸件的强度和硬度,还会引起气门席位不密封、变形等问题。
解决方法包括合理选择冷料铸造工艺、提高铸型制备技术、优化压铸工艺参数等。
2.气孔:气孔是由于熔金属在充型过程中,未排出液态金属中的气体而形成的。
气孔通常呈现为孔洞状,会严重影响压铸件的表面质量和机械性能。
解决方法包括改善金属液的质量、提高模具排气性能、优化压铸工艺参数、采用真空压铸等。
3.烧结:烧结是指在压铸过程中,由于金属在高温高压条件下与模具接触过久而发生的表面热蚀伤。
烧结会引起表面孔洞、氧化和金属元素丢失等问题。
解决方法包括使用合适的模具材料、降低模具温度、缩短冷却时间等。
4.裂纹:压铸件中的裂纹可以是细小的微裂纹,也可以是较大的结构性裂纹。
裂纹会导致压铸件的破坏、漏气和泄漏等问题。
解决方法包括增加浇注系统的冷却时间、提高模具的强度和刚度、优化压铸工艺参数等。
5.砂眼:砂眼是因为铸件表面存在颗粒状材料,如砂粒等而形成的凹陷或凸起。
砂眼会影响压铸件的美观性和表面质量。
解决方法包括优化型腔冷却系统、提高浇注系统的冷却时间、改善铸型制备工艺等。
总的来说,要解决常见的压铸件缺陷,需要从改善熔融金属的质量、优化模具设计和制备工艺、调整压铸工艺参数等多个方面入手。
此外,还需要采用适当的检测手段,如金相分析、X射线检测、超声波检测等,对压铸件进行质量检验,及时排除可能存在的缺陷。
铸造缺陷鉴别
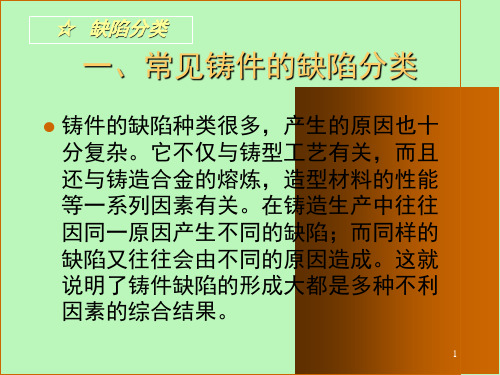
二、孔洞类铸造缺陷的鉴别
①、缩孔常见部位示意 图
17
二、孔洞类铸造缺陷的鉴别
②、缩松:铸件断面上 出现的分散而细小的 缩孔。有时借放大镜 才能发现。缩松部位 在水压试验时会渗漏 疏松:形状和缩松 相似,但孔洞更细小, 组织粗大,石墨粗大 等缺陷也可能导致铸 件组织疏松。
18
二、孔洞类铸造缺陷的鉴别
网状或脉状分布的毛 刺称脉纹。
24
三、多肉类缺陷的鉴别
2、抬 箱(抬 型): 铸件在 分型面 部位高 度和宽 度增大
25
三、多肉类缺陷的鉴别
3、涨砂: 铸件内、 外表面局 部胀大, 形成不规 则的瘤状 金属凸起 物。
26
三、多肉类缺陷的鉴别
4、冲砂: 铸件表面 上有粗糙 不规则的 金属瘤状 物,常位 于浇口附 近。在铸 件其它部 位则往往 出现砂眼。
36
六、残缺类缺陷
浇不到: 由于金 属液未 完全充 满型腔 而产生 的铸件 缺肉。
37
六、残缺类缺陷
2、缺 损:在 铸件清 理或搬 运时, 损坏了 铸件的 完整性。
38
七、尺寸、形状和重量差错类缺陷
1、变型: 由于收 缩应力 或型壁 变形、 开裂引 起的铸 件外形 和尺寸 与图纸 不符。
12
二、孔洞类铸造缺陷的鉴别
③、反应气孔:液态金 属的某些成分之间或 液态金属与铸型在界 面上发生化学反应产 生的气孔。 气孔位于铸件表皮 下,有的呈分散的针 状,有的隐藏在铸件 上部并伴有夹渣。
13
铸件气孔实例(1)
14
铸件气孔实例(2)
15
二、孔洞类铸造缺陷的鉴别
2、缩孔:形状为不规 则的封闭或敞露的孔 洞,孔壁粗糙并带有 枝状晶,且晶粒粗大。 常出现在铸件最后凝 固的部位(热节处)
铸造缺陷种类

铸造缺陷种类
1、气孔缺陷。
铸铁件在凝固过程中未能逸出的气体留在铸件内部形成的小孔洞,内壁光滑,有气体。
表面一般情况下呈球状或椭球状,对于超声波具有较高的反射率,因此可以通过超声波进行检测。
2、缩松、缩孔缺陷。
铸铁件在冷却凝固时,体积收缩,在最后凝固的时候得不到充足的铁液的补充便会形成空洞状的缺陷,内壁粗糙,周围多伴有许多杂质和细小的气孔。
缩松呈现细小而分散的空隙,缩孔呈现大而集中的空洞。
3、偏析缺陷。
指铁合金在冶炼过程中或铁金属在熔化的过程中因为成分分布不均而形成的成分偏析,有偏析存在的区域其力学性能和整个金属的力学性能有较大的差别。
4、裂纹缺陷。
铸铁件中的裂纹主要时由于金属材料的强度难以支撑金属在冷却凝固时的收缩应力,这与金属中的合金含量、铸铁件的形状设计和铸造工艺有很大的关系。
5、冷隔缺陷。
这是指在浇注铁液时,由于飞溅、浇注中断或来自不同方向的两股金属流相遇,液态金属表面冷却形成的半固态薄膜留在铸铁件内而形成的一种隔膜状的面积型缺陷。
- 1、下载文档前请自行甄别文档内容的完整性,平台不提供额外的编辑、内容补充、找答案等附加服务。
- 2、"仅部分预览"的文档,不可在线预览部分如存在完整性等问题,可反馈申请退款(可完整预览的文档不适用该条件!)。
- 3、如文档侵犯您的权益,请联系客服反馈,我们会尽快为您处理(人工客服工作时间:9:00-18:30)。
名称
缺陷特征
产生原因分析
名称
缺陷特征
产生原因分析
浇不到
铸件残缺或轮廓不完整,边角圆且光亮
• 流动性差,浇注温度低
• 铸件设计不合理,壁太薄
• 浇时断流或浇注速度过慢
• 浇注系统截面过小
裂 纹
在铸件转角处或厚薄壁交接处条状裂纹
• 铸件壁厚不均匀,收缩不一致
• 合金含硫和磷过高
• 型(芯)砂的退让性差
• 型砂的耐火性差
• 浇注温度高
• 型砂紧实度不够,型腔表面不致密
变 形
铸件发生弯曲或扭曲变形
• 落砂过早或过晚
• 铸件壁厚不均匀
• 铸件形状设计不合理
粘 砂
表面或内腔附有难以清除的砂粒
• 定位销或记号不准
气 孔
孔洞内表光滑,大孔孤立存在、小孔成群出现
• 铸型透气性差,紧实度过高
• 铸型太湿、起模涮水过多。芯子、浇包未烘干
• 浇注系统不正确,气体排不出去
• 砂芯通气孔堵塞
偏 芯
铸件内孔位置、形状和尺寸发生偏移
• 子变形
• 下芯时位置不准确
• 砂芯固定不良,浇注时被冲偏
砂 眼
内部或表面带有砂粒的孔洞
• 浇注温度过高
冷 隔
边缘呈圆角状的缝隙
• 铸件壁过薄
• 合金流动性差
• 浇注温度低、浇注速度慢
缩 孔
最后凝固处形状不规则的孔洞、内腔极粗糙
• 铸件结构设计不当,有热节
• 浇注温度过高
• 冒口设计不合理或冒口过小
错 型
铸件在分型面处发生错移
• 合型时定位不准
• 造型时上、下模有错移
• 上、下型未夹紧