消失模铸件质量评定标准附检验方法
铸造公司原材料成品检验标准

铸造公司原材料成品检验标准铸造公司原材料、成品检验标准审批:一、原材料进厂检验对EPC消失模铸件生产中原材料:灰铸铁用生铁、球墨铸铁用生铁、硅铁、锰铁、铬铁、废钢;聚苯乙烯;石英砂和炉衬材料进厂检验规定如下:采用标准:GB/T718—2005《灰铸铁件用生铁》GB1412—85《球墨铸铁件用生铁》GB/T2272—2022《硅铁》GB/T3795—2006《电炉锰铁》GB/T5683—2022《铬铁》GB719—84《生铁化学分析用试样制取方法》GB/T4010—94《铁合金化学分析用试样的采取和制备》Q/BAML002-2022《CF4AL感应电炉酸性炉衬耐火材料》——**环宇石英砂企业标准Q/BAML001-2022《精制石英砂〔粉〕》——**环宇石英砂企业标准1、灰铸铁用生铁的检验:1.1灰铸铁用生铁的检验依据GB/718—2005《灰铸铁件用生铁》标准进行检验,其中化学成分如表1所示,要求C含量不得低于4.1%。
1.2要求对进厂每批灰铸铁用生铁进行检验。
由理化室依照GB/719—84《生铁化学分析用试样制取方法》现场抽样,并制取试样;化验分析后出具《原材料进厂检测及化学分析报告单》。
分析结果合格方能入库,不合格应明确标识,由技术部门负责人决定是让步接受还是退货后进行处理。
表1 灰铸铁用生铁〔摘自GB/T718—2005〕铁号牌号铸34铸30铸26铸22铸18铸14代号Z34Z30Z26Z22Z18Z14化学成分〔%〕C>、4.1Si>3.20~3.60>2.80~3.20>2.40~2.80>2.00~2.40>1.60~2.00>1.25~1.60Mn1组≤0.052>0.50~0.90组3组>0.90~1.30P1级≤0.062级>0.06~0.103级>0.10~0.204级>0.20~0.405级>0.40~0.90S1类≤0.03≤0.042类≤0.04≤0.053类≤0.05≤0.061.3外观质量:规整平滑,根本无毛边。
铸件质量检验标准

铸件质量检验标准铸件是一种常见的生产工艺,广泛用于各个行业和领域。
铸件质量的好坏直接影响产品的性能和可靠性,因此进行铸件质量检验至关重要。
本文将介绍铸件质量检验的标准和方法。
一、铸件质量检验的重要性铸件质量检验的目的是确保铸件的尺寸精度、表面质量和机械性能达到设计要求。
一方面,铸件的尺寸精度和表面质量直接影响产品的装配和使用;另一方面,对于承受重载或高温等极端工况的铸件来说,其机械性能的好坏关系到产品的安全可靠性。
二、铸件质量检验的标准铸件质量检验的标准包括国家标准、行业标准和企业自身标准。
国家标准是根据相关法律法规制定的,具有强制性,是衡量铸件质量的重要依据。
行业标准是在国家标准的基础上,由行业协会或行业组织制定的,作为行业内铸件质量的参考指南。
企业自身标准是企业根据生产情况和需求制定的,用于规范和管理内部质量控制。
在铸件质量检验中,常用的国家标准有《铸造铁件技术条件》、《铸铝合金件技术条件》等,而行业标准包括《汽车铝合金压铸铸件技术规范》、《船用铸铁件技术条件》等。
企业自身标准则根据企业具体的生产工艺和要求制定,例如《XX公司铸件质量检验标准》。
三、铸件质量检验的方法铸件质量检验的方法主要包括外观检查、尺寸检测和性能测试。
1. 外观检查外观检查是铸件质量检验中最简单直观的方法。
通过肉眼观察铸件的外观,检查是否有裂纹、砂眼、气孔、夹渣等缺陷。
外观检查可以用目视检查或借助放大镜进行观察。
2. 尺寸检测尺寸检测是铸件质量检验中最常见的方法。
主要是测量铸件的外形尺寸、孔径尺寸和壁厚尺寸等。
常用的尺寸测量工具有游标卡尺、内径卡尺、外径卡尺、深度尺等。
尺寸检测可以帮助判断铸件是否满足设计要求。
3. 性能测试性能测试是铸件质量检验中最关键的方法,主要包括力学性能测试、化学成分分析和金相组织分析。
力学性能测试主要是测试铸件的拉伸、弯曲、冲击等力学性能。
化学成分分析可以确定铸件的材料成分是否符合要求。
金相组织分析可以观察铸件的金相组织结构,评估其机械性能。
消失模铸钢件检验标准[详]
![消失模铸钢件检验标准[详]](https://img.taocdn.com/s3/m/7cf9417008a1284ac85043e0.png)
消失模铸钢件检验标准1.目的规消失模铸钢件的检验标准,以使各工序过程的产品质量得以控制。
2.适用围本标准适用于消失模铸钢件的检验,图纸和技术文件并同使用。
如与国家标准和技术规冲突时,以国家标准和技术规为准。
3.引用标准GB /T 26658 《消失模铸件质量评定方法》GB /T 11352 《一般工程用铸造碳钢件》GB /T 6414 《铸件尺寸公差与机械加工余量》GB /T 11351 《铸件重量公差》GB /T 5613《铸钢牌号表示方法》GB /T 6060.1《铸件表面粗糙度比较样块》GB /T 222《钢的成品化学成分允许偏差》GB /T 223《钢铁及合金化学分析方法》GB /T 228《金属拉伸试验方法》GB /T 231.1《金属布氏硬度试验方法》/T 5000.6《重型机械通用技术条件铸钢件》/T 5000.7 《重型机械通用技术条件铸钢件补焊》/T 5000.12 《重型机械通用技术条件涂装》/T 5000.13 《重型机械通用技术条件包装》/T 5000.14 《重型机械通用技术条件铸钢件无损探伤》4.材料检验铸件牌号,化学成分和力学性能牌号: ZG230-450化学成分(质量分数%)|C≤: 0.30化学成分(质量分数%)|Si≤: 0.50化学成分(质量分数%)|Mn≤: 0.90化学成分(质量分数%)|S≤: 0.04化学成分(质量分数%)|P≤: 0.04残余元素: Cr≤0.35,Ni≤0.30,Mo≤0.20,Cu≤0.30,V≤0.05;但Cr+Ni+Mo+Cu+V≤1.00热处理|退火温度/℃: 890~910屈服强度σ0.2/MPa: 230抗拉强度σb/MPa: 450伸长率δ5(%): 22断面收缩率ψ(%): 235.外观检验5.1 铸件形状外观裸视目测。
要求外观轮廓清,圆角尺寸正确且过渡平滑美观;可允许外观轮廓30%以下欠清晰,圆角过渡不够平滑。
5.2 铸件表面缺陷在正常情况下铸件表面喷丸清理后进行检查,对照标准图谱裸视目测(取最坏部分面积100mm×60mm)。
消失模铸钢件检验标准

消失模铸钢件检验标准1.目的规范消失模铸钢件的检验标准,以使各工序过程的产品质量得以控制。
2.适用范围本标准适用于消失模铸钢件的检验,图纸和技术文件并同使用。
如与国家标准和技术规范冲突时,以国家标准和技术规范为准。
3.引用标准GB /T 26658 《消失模铸件质量评定方法》GB /T 11352 《一般工程用铸造碳钢件》GB /T 6414 《铸件尺寸公差与机械加工余量》GB /T 11351 《铸件重量公差》GB /T 5613《铸钢牌号表示方法》GB /T 6060.1《铸件表面粗糙度比较样块》GB /T 222《钢的成品化学成分允许偏差》GB /T 223《钢铁及合金化学分析方法》GB /T 228《金属拉伸试验方法》GB /T 231.1《金属布氏硬度试验方法》JB /T 5000.6《重型机械通用技术条件铸钢件》JB /T 5000.7 《重型机械通用技术条件铸钢件补焊》JB /T 5000.12 《重型机械通用技术条件涂装》JB /T 5000.13 《重型机械通用技术条件包装》JB /T 5000.14 《重型机械通用技术条件铸钢件无损探伤》4.材料检验铸件牌号,化学成分和力学性能牌号: ZG230-450化学成分(质量分数%)|C≤: 0.30化学成分(质量分数%)|Si≤: 0.50化学成分(质量分数%)|Mn≤: 0.90化学成分(质量分数%)|S≤: 0.04化学成分(质量分数%)|P≤: 0.04残余元素: Cr≤0.35,Ni≤0.30,Mo≤0.20,Cu≤0.30,V≤0.05;但Cr+Ni+Mo+Cu+V ≤1.00热处理|退火温度/℃: 890~910屈服强度σ0.2/MPa: 230抗拉强度σb/MPa: 450伸长率δ5(%): 22断面收缩率ψ(%): 235.外观检验5.1 铸件形状外观裸视目测。
要求外观轮廓清,圆角尺寸正确且过渡平滑美观;可允许外观轮廓30%以下欠清晰,圆角过渡不够平滑。
消失模泡沫模型的验收标准及质量控制程序
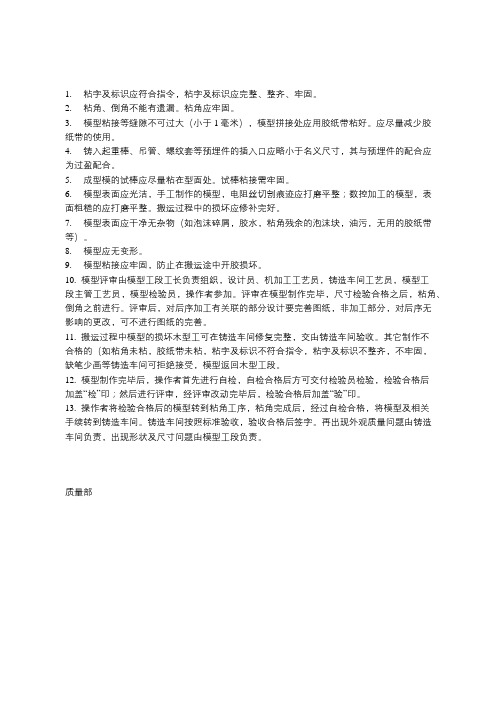
1. 粘字及标识应符合指令,粘字及标识应完整、整齐、牢固。
2. 粘角、倒角不能有遗漏。
粘角应牢固。
3. 模型粘接等缝隙不可过大(小于1毫米),模型拼接处应用胶纸带粘好。
应尽量减少胶纸带的使用。
4. 铸入起重棒、吊管、螺纹套等预埋件的插入口应略小于名义尺寸,其与预埋件的配合应为过盈配合。
5. 成型模的试棒应尽量粘在型面处。
试棒粘接需牢固。
6. 模型表面应光洁,手工制作的模型,电阻丝切割痕迹应打磨平整;数控加工的模型,表面粗糙的应打磨平整。
搬运过程中的损坏应修补完好。
7. 模型表面应干净无杂物(如泡沫碎屑,胶水,粘角残余的泡沫块,油污,无用的胶纸带等)。
8. 模型应无变形。
9. 模型粘接应牢固,防止在搬运途中开胶损坏。
10. 模型评审由模型工段工长负责组织,设计员、机加工工艺员,铸造车间工艺员,模型工段主管工艺员,模型检验员,操作者参加。
评审在模型制作完毕,尺寸检验合格之后,粘角、倒角之前进行。
评审后,对后序加工有关联的部分设计要完善图纸,非加工部分,对后序无影响的更改,可不进行图纸的完善。
11. 搬运过程中模型的损坏木型工可在铸造车间修复完整,交由铸造车间验收。
其它制作不合格的(如粘角未粘,胶纸带未粘,粘字及标识不符合指令,粘字及标识不整齐,不牢固,缺笔少画等铸造车间可拒绝接受,模型返回木型工段。
12. 模型制作完毕后,操作者首先进行自检,自检合格后方可交付检验员检验,检验合格后加盖“检”印;然后进行评审,经评审改动完毕后,检验合格后加盖“验”印。
13. 操作者将检验合格后的模型转到粘角工序,粘角完成后,经过自检合格,将模型及相关手续转到铸造车间。
铸造车间按照标准验收,验收合格后签字。
再出现外观质量问题由铸造车间负责,出现形状及尺寸问题由模型工段负责。
质量部。
消失模铸造工艺细则

消失模铸造工艺细则为了彻底摆脱箱体铸件质量不稳定,工艺和管理无章可循的被动局面,制定本细则。
本细则采用了依据“流场、热场、负压场——三场理论”设计的浇注系统、箱内浇口杯和速烧结涂料等多项技术,从而能彻底克服消失模铸造特有的“进砂”(白色缺陷)和碳渣(皱皮等黑色缺陷)提高铸件质量的致密度,防止发生漏泵,确保消失模铸件的高成品率。
一、泡沫模型制作采用聚苯乙烯材料做泡沫模型,泡沫模型在消失过程中要吸收大量的热量,如果消失方式不当,还会产生大量的游离碳,对铸件的品质造成伤害。
优质的泡沫模型就是要尽可能的少吸收铁水携带的热量,并不留痕迹的消失。
泡沫模型的标准是:1、表面质量满足用户要求的下限,不追求上限;2、强度适中,不追求高强度;3、重量越轻越好,不规定下限,不满足现状;不断摸索经验,不断追求更轻,把重量做到轻的极限。
各辅助工序必须确保以下的工艺条件:1、珠粒优良,发泡剂含量:>6%;2、管道蒸汽压力稳定,无冷凝水>5kg/c㎡;3、压缩空气压力<5kg/c㎡;4、正压间歇式预发机预发珠粒,预发密度<15g/L;不准有死珠粒,必要时过筛分离出死珠粒,重复预发。
成型工序操作者,确定以下环节的工艺指标,实现由凭感觉操作到数字操作。
1、最佳的珠粒密度,最佳的预发倍率,最佳的熟化时间,最佳的熟化条件。
2、模具预留间隙,最佳的充型压力。
3、最佳的蒸汽压力,最佳的加热时间。
4、冷却时间。
5、其它可以获得最轻泡沫模型的操作技巧。
制成的泡沫模型在摆放的时候要防止发生变形和人为损坏。
二、模型的验收和管理设立专职检查员,对泡沫模型做检查和相关数据的测定;检查包括:1、表面质量的检查;主要检查珠粒的融合情况,表面有无损坏和变形。
2、重量的检查;泡沫模型重量的差异,直接影响铸件的质量。
泡沫模型的检查分两次进行,即:先检查模片的重量,再检查组合后模型的重量。
模片重量的检查和组合后模型重量的检查,是两个概念。
铸件质量检验标准
—
—
—
—
—
—
—
—
0.64
0.72
0.80
0.9
1.0
1.1
1.2
1.4
1.6
1.8
2.0
2.2
2.6
2.8
3.2
3.6
4.0
4.6
5
6
7
7
8
9
10
11
13
1600
2500
4000
6300
2500
4000
6300
10000
—
—
—
—
—
—
—
—
—
—
—
—
—
—
—
0.24
0.26
0.28
0.32
0.36
0.40
0.46
0.50
0.56
0.64
0.70
0.78
0.9
1.0
1.1
1.3
1.4
1.6
1.8
2.0
2.2
2.6
2.8
CF3M
ASTM
A351
0.03 1.5 1.5 17~21 0.04 0.04 9~13 2~3
CF8M
ASTM
A351
0.08 1.5 1.5 18~21 0.04 0.04 9~12 2~3
CG3M
ASTM
A351
0.03 1.0 2.0 18~20 0.035 0.03 11~15 3~4
铸件的质量检验方法及标准PPT课件
—铸造工艺与技Байду номын сангаас训练
一、铸件质量检验概述
根据用户要求和图样技术条件等有关协议的规定,用目测、量具、仪 表或其他手段检验铸件是否合格的操作过程称为铸件检验。
铸件质量检验的依据是:铸件图、铸造工艺文件、有关标准及铸件交 货验收技术条件。
二、铸件的质量等级
检验后,根据铸件的质量情况可分为下列三类:
(3)铸件质量偏差的检测 1)铸件质量偏差检测术语见表11-4。 2)铸件公称质量的确定 3)铸件质量公差等级和公差数值的确定 4)铸件质量偏差的检验和评定程序
(4)铸件浇冒口残余量的检验 (5)铸件表面和近表面缺陷的目测检验 用肉眼或借助于低倍放大镜,检查暴露在铸件表面的 宏观缺陷,同时检查铸件的生产标记是否正确齐全。检 查时应判定铸件对于检查项目是否合格,区分合格品、 返修品和废品。 (6) 铸件内腔质量的检验
2. 铸件内在质量的检验 铸件内在质量是指一般不能用肉眼直观检查出来的铸 件内部状况和达到用户要求的程度。检验内容包括铸件 的化学成分、物理和机械性能、金相组织以及存在于铸 件内部的孔洞、裂纹、夹杂物等缺陷。 铸件内在质量的检验方法和检验内容见表11-5。
3. 质量检验报告 检验人员在接受检验任务之后,将按照有关的检验项 目和试验规范对有关产品进行检验。检验结束后必须开具 质量检验报告,提供相关数据。 质量检验报告一般包括以下内容: 被测试样的产品名 称、试样名称、测试项目、委托单位或部门、委托日期、 测试日期、测试环境、测试人员、校核、审核、批准人员、 测试仪器、设备、测试标准、测试方法、测试数据、测试 结果。
三、铸造生产检验过程
检验工作不应以检验为目的,而应作为改善铸件质量的有效方法。铸造生产 的检验可分为彼此密切相关的三个阶段,见表11-2。
国家标准《消失模铸件质量评定方法》解读
表 面粗糙度R <1 2 . 5 m。 ( 3 )铸件尺 寸公差 铸 件尺寸公差见 表 1 。 ( 4 ) 内部缺 陷 经 过X射 线 探伤 ,底 片根 据 AS T M E 4 4 6 -2 0 1 1 判 定 。气孔 二级 以 内 ,砂 ( 渣 )眼二 级 以 内 ,缩皱 二 级 以 内可 以接受 。树 枝状缩 皱 和任何 裂纹 以及 三级 以上 的气孔夹 杂物均为废 品 。 2 . 2 阀门 ( 盖) 图2 为 l 0 0 mm阀盖简 图 。 日本 水 道 协会 认 证 的 3 0 0 r n _ r n 以下的 阀门 ( 盖)消失模铸 件要求如 下。
1 o 0 mm阀盖 的主 要 尺寸 公 差 见 表2 , 3 0 0 mm
以下 阀盖未 注 明特殊 要求 的通用 尺寸公差见 表3 。
( 4 ) 材质
F C D 4 5 . 1 0 ,R ≥4 5 0 N / r n m ,A≥1 0 % ,球化 率 >
8 0 %,石 墨大d x 2 0 t x m以上 。 ( 5 ) 耐压试 验 ( 水 压2 0 k g / c m2 )
型消失 模铸 件质 量 进行 仔 细分析 ,以及对 国 内消失 模 铸 件进 行 了大 量调 查 ,在此 基础 上对 消失模 铸 件质 量 作 了准确 的定 位 。
2 消失模铸件质量定位
消 失模 铸件 应 为一种 精 密铸件 ,而 不应 视 为一 般
砂 型铸件 。 下 面分 析两 个专 门为消失 模铸 造设 计 的 国外铸 件 的技 术要求 ,可看 出消失模铸件应 具备 的特 点 。 2 . 1 拨 叉 拨 叉是 美 国通用 汽车 公 司专 门为 消失模 铸 造工 艺 设 计 的铸 件 , 图纸 标 明 “ Dr a w i n g d i me n s i o n e d a n d t o l e r a n c e d f o r l o s t oa f m p r o c e s s o n l y ” 字 样 , 材 质 为
消失模铸造质量管理考核标准
消失模铸造质量管理考核标准你知道吗?消失模铸造就像是在做超级精细的手工活儿。
比如说,我们要做一个小城堡的模型,这个小城堡得又好看又结实。
那怎么保证做出来的东西是好的呢?这就需要质量管理考核标准啦。
在这个考核标准里呀,有一个很重要的部分就是材料的选择。
就像我们搭积木,如果积木的质量不好,那搭出来的城堡可能就歪歪扭扭,甚至会倒。
消失模铸造也是这样,要是选的泡沫材料不好,那最后做出来的铸造品就会有问题。
比如说,有的泡沫要是太软了,在制作过程中就容易变形。
就像我们捏橡皮泥,如果橡皮泥太软,想捏个小兔子,可能捏着捏着就变成一团了。
所以呀,在考核的时候,会看材料是不是符合要求,有没有选对硬度合适、质量好的泡沫。
还有呢,制作过程中的每一个小步骤都得看紧喽。
这就好比我们画一幅画,从画轮廓开始,到一点点上色,每一步都很关键。
在消失模铸造里,从把泡沫做成想要的形状,到在上面涂特殊的涂料,每一步都得按照规定来。
比如说涂涂料的时候,如果涂得不均匀,就像我们给画涂颜色,一块深一块浅,那最后铸造出来的东西表面就不光滑,会坑坑洼洼的,就像月球表面一样,一点也不漂亮。
工人叔叔阿姨们的操作熟练程度也是考核的重点呢。
这就像我们玩游戏,玩得多了就熟练了,就能玩得又快又好。
如果工人叔叔阿姨操作不熟练,就可能会出错。
我给你们讲个故事呀。
有一次,一个新的工人叔叔在做消失模铸造的时候,因为不太熟练,在把泡沫模型放到特定的地方的时候,不小心碰坏了一点。
结果最后铸造出来的东西就缺了一块,就像小蛋糕被人咬了一口似的。
所以呀,工人叔叔阿姨们得经过训练,操作熟练了才能保证做出来的东西是好的。
另外,成品的检验也是很重要的一环。
这就像是我们做完作业要检查一样。
铸造出来的东西得看看有没有裂缝,有没有哪里形状不对。
要是有问题就得想办法改进。
比如说,有个铸造出来的小零件,本来应该是方方正正的,可是检验的时候发现有个角是圆的,这就是不合格的,得重新做呢。
- 1、下载文档前请自行甄别文档内容的完整性,平台不提供额外的编辑、内容补充、找答案等附加服务。
- 2、"仅部分预览"的文档,不可在线预览部分如存在完整性等问题,可反馈申请退款(可完整预览的文档不适用该条件!)。
- 3、如文档侵犯您的权益,请联系客服反馈,我们会尽快为您处理(人工客服工作时间:9:00-18:30)。
GB/T xxxx-200x1. 主题内容与适用范围本标准规定了300kg以下消失模铸造的铸铁件、铸钢件的质量分级、评定方法、检验方法,以及检验规则、标志、包装、运输和储存。
个人收集整理勿做商业用途本标准适用于消失模铸造生产企业、铸件用户对消失模铸件生产、使用的质量分级、评定和检验。
2. 引用标准GB5612 铸铁牌号表示方法GB5613-85 铸钢牌号表示方法GB6414-86 铸件尺寸公差GB/T1135-89铸件质(重)量公差GB6060.1-85铸件表面粗糙度比较样块3. 技术要求3.1 消失模铸件外观质量评定3.1.1 铸件形状外观铸件外形轮廓、圆角等按其正确、美观程度分为5级。
1级:外观轮廓清晰,圆角尺寸正确且过渡平滑美观;2级:外观轮廓30%以下欠清晰,圆角过渡不够平滑;3级:外观轮廓50%以下欠清晰,圆角50%以下未制作出;4级:外观轮廓70%以下欠清晰,圆角未制作出;5级:外观轮廓不清晰,铸造圆角未制作出,粘结线(面)凹凸不平。
3.1.2 铸件表面缺陷3.1.2.1 表面夹杂物(夹砂、夹渣等)由于脱落型砂、涂料、金属渣及模型分解产生的固液相产物等,进入铸件,残存于铸件表面,形成了铸件表面夹杂物缺陷。
个人收集整理勿做商业用途根据铸件最坏部位100mm×60mm的面积内存在大的夹杂物的大小、数量,将其分为无级(参见图1)。
1级:缺陷3点以下,直径2mm深度≤1mm(图1a);2级:缺陷5点以下,直径3mm深度≤1.5mm(图1b);3级:缺陷5点以下,直径5mm深度≤2mm(图1c);4级:缺陷8点以下,直径7mm深度≤3mm(图1d);5级:缺陷严重(图1e)。
(a) (b)(e)图1表面夹杂物(夹砂、夹渣等)一般情况下,消失模铸件表面夹杂物缺陷应控制在二级以内,有特殊要求情况下要达到一级和特级(无任何夹杂物)。
个人收集整理勿做商业用途3.1.2.2 表面气孔由于泡沫塑料模型分解产生气体及浇注时裹入气体或涂层未干水气化形成的气体等残留在铸件表面形成表面气孔(或气坑)缺陷。
个人收集整理勿做商业用途根据铸件表面气孔最严重部位100mm×60mm的面积内气孔数目多少、大小及深度分为无级(参见图2)。
1级:表面气孔数少于4点,孔径≤φ1mm深度≤1mm(图2a);2级:表面气孔数少于8点,孔径≤φ1mm深度≤1mm(图2b);3级:表面气孔数少于10点,孔径≤φ2mm深度≤2mm(图2c);4级:表面存在密集气孔,但深度较浅,孔径较小(图2d);5级:表面存在密集气孔,孔径大且较深(图2e)。
(a) (b)(c) (d)(e)图2 表面气孔一般情况下,消失模铸件表面气孔缺陷应控制在二级以内,四、五级为废品。
3.1.2.3 表面皱皮铸铁件在浇注过程中,泡沫塑料模型气化分解的固、液相产物堆积在铸件表面形成橘皮状碳质缺陷,以及由于液态金属充型温度不良,造成铸件表面皱皮缺陷。
个人收集整理勿做商业用途根据铸件表面皱皮最严重部位100mm×60mm的面积内皱皮的严重程度,分为无级(参见图3)。
1级:很轻微皱皮(对火)(图3a);2级:轻微皱皮(图3b);3级:中度皱皮(图3c);4级:重度皱皮(图3d);5级:严重皱皮(图3e)。
(a) (b)(c) (d)(e)图3 表面皱皮一般情况下,二级以内为合格铸件,4、5级为不良铸件。
3.1.2.4 冷隔(对火)分多路充型的液体金属相遇后由于温度低而不能很好地熔合形成对接明显的痕迹。
在100mm×60mm面积内,按冷隔(对火)严重程度,分为五级(图4)。
1级:轻微冷隔(对火)(图4a);2级:轻度冷隔(对火)(图4b);3级:中度冷隔(对火)(图4c);4级:重度冷隔(对火)(图4d);5级:严重冷隔(对火)(图4e)。
4、5级为不合格铸件。
(a) (b)(c) (d)(e)图4 冷隔(对火)3.1.2.5 表面龟纹铸件表面喷丸处理后,有时还留有珠粒的痕迹,称之为龟纹。
如果珠粒间隙过深,涂料浸入,浇注后则形成较深的网状痕迹,则形成消失模铸件表面的一种特殊缺陷。
个人收集整理勿做商业用途在100mm×60mm面积内,按龟纹大小、深度分为五级(图5)。
1级:均匀分布,细小的网状纹路,但深度为0(图5a);2级:细小而均匀分布,痕迹深度≤0.2mm(图5b);3级:直径较大(φ≤2mm),痕迹深度≤0.5mm(图5c);4级:直径大(φ≤3mm),痕迹深度≤1.0mm(图5d);5级:粗大龟纹,痕迹深度>1.0mm(图5e)。
2级以内为优质铸件,表面龟纹允许用强力喷砂改进。
(a) (b)(c) (d)(e)图5 表面龟纹3.1.2.6 粘砂液体金属渗入涂层及砂型中,形成砂、涂料和金属混合物,粘附在铸件表面,严重时成为所谓“铁包砂”,很难清理。
个人收集整理勿做商业用途在100mm×60mm面积内,根据粘砂程度不同分为五级(图6)。
1级:基本无粘砂(图6a);2级:轻度粘砂(可磨修)(图6b);3级:中度粘砂(可磨修)(图6c);4级:重度粘砂(磨修较困难)(图6d);5级:严重粘砂及铁包砂(清理极困难)(图6e)。
(a) (b)(c) (d)(e)图6粘砂表面粘砂为2级以内为优质铸件,粘砂一般可通过打磨改善。
3.1.2.7 金属突出物(粘结线痕迹、结瘤、针刺)金属突出物包括铸件表面形成的分型面粘结线凸起部分、由于紧实不良金属渗过涂料裂纹形成的结瘤(一般可清理掉)、由于涂层表面孔洞造成的铸件表面突出麻点(针刺)。
个人收集整理勿做商业用途按最坏部位100mm×60mm视野内金属突出物(主要是粘结线痕迹)程度分为五级(图7)。
1级:粘结线痕迹很窄很轻,无针刺(图7a);2级:粘结线痕迹宽度≤1mm,高≤1mm,无针刺、结瘤(图7b);3级:粘结线痕迹宽度≤2mm,高≤2mm,轻度针刺,无结瘤(图7c);4级:粘结线痕迹宽度≤3mm,高≤3mm,轻度针刺,无结瘤(图7d);5级:粘结线痕迹宽度≥5mm,高>3mm,或有中度针刺,或有结瘤存在(图7e)。
图7金属突出物(粘结线痕迹、结瘤、针刺)金属突出物可以通过打磨修整,一般不作为废品,优质消失模铸件表面金属突出物应在2级以内。
3.1.2.8 浇冒口去除痕迹切割浇冒口留下的痕迹,分为五级(图8)。
1级:痕迹细、均、平滑(图8a);2级:轻度痕迹(图8b);3级:中度痕迹(图8c);4级:重度痕迹(图8d);5级:严重、高低不平痕迹或切割造成低于铸件平面(图8e)。
(e)图8浇冒口去除痕迹切割痕迹高于铸件平面可以打磨改善,切割痕迹低于铸件平面,铸件报废或修补。
3.1.2.9 焊补(修补)面积一些铸件表面缺陷,在用户同意下允许焊补(或修补),在100mm×60mm面积内,按焊补面积大小分为五级(图9)。
个人收集整理勿做商业用途1级:焊补面积≤5%(图9a);2级:轻度焊补,焊补面积≤20%(图9b);3级:中度焊补,焊补面积≤50%(图9c);4级:大面积焊补,焊补面积≤80%(图9d);5级:视野内全部焊补(图9e)。
3.1.2.10 铸件表面铸造缺陷的评定方法用视觉对照图谱评定,选定最坏部位面积100mm×60mm,在正常情况下铸件表面喷丸清理后进行检查。
3.1.3 铸件表面粗糙度表面粗糙度是指在较小间距、峰谷所组成的微观几何形状特性。
在取样长度内轮廓偏距绝对值的算术平均值,单位为μm,记为Ra。
个人收集整理勿做商业用途为便于现场检测铸件表面粗糙度,用比较样块进行对比评定。
消失模铸件表面粗糙度分为五级。
1级:Ra≤6.3μm;2级:Ra≤12.5μm;3级:Ra≤25μm;4级:Ra≤50μm;5级:Ra≤100μm。
2级以内为优质铸件,4级以上为不良消失模铸件。
3.2 铸件尺寸精度表1为国家标准规定的铸件尺寸公差(GB6414-86)的部分数据。
消失模铸件按其尺寸精度分为五级。
每级相当于GBCT的尺寸精度范围如下。
1级:尺寸公差GBCT6级及6级以内;2级:尺寸公差GBCT7级及8级以内;3级:尺寸公差GBCT9级及9级以内;4级:尺寸公差GBCT10级及10级以内;5级:尺寸公差GBCT10级及10级以上。
表1 铸件尺寸公差GB6414-86铸件基本尺寸公差等级CT大于至345678*********100.180.260.360.520.741.01.52.02.84.2—10160.200.280.380.540.781.11.62.23.03.4—16250.220.300.420.580.821.21.72.43.24.6625400.240.320.460.640.901.31.82.63.65.0740630.260.360.500.701.01.42.02.84.05.68631000.280.400.560.781.11.62.23.24.4691001600.300.440.620.881.21.82.53.65.07101602500.340.500.701.01.42.02.84.05.68112504000.400.560.781.11.62.23.24.46.2912400630—0.640.901.21.82.63.65710146301000——1.001.42.02.84.068111610001600 —1.62.23.24.6791318一般情况下,消失模铸件尺寸精度(包括厚度尺寸精度)应为2级以内,即应达到GBCT8级以内。
3.3 铸件重量精度消失模铸件重量精度等级共分五级,各级别相当于国家标准(GBMT)铸件重量公差级别如下。
1级:相当于GBMT4级以内;2级:相当于GBMT5~6级;3级:相当于GBMT7~8级;4级:相当于GBMT9~10级;5级:相当于GBMT10级以上。
表2 GBMT铸件质量公差部分数值(GB/T11351-89)铸件质(重)量kg质(重)量公差等级45678910质(重)量公差数值%>0.4~1 681012141618>1~456810121416>4~104568101214>10~40345681012>40~10023456810>100~400—234568消失模铸件重量公差一般应控制在GBMT5~8级。
3.4 铸件内部缺陷铸件内部缺陷是指铸造过程形成的铸件内部的气孔、砂(渣)孔、缩孔(松)、裂纹等缺陷。
3.4.1 气孔在38.1mm×38.1mm面积内,根据孔洞的大小及数量分为五级,最大气孔直径不得大于2.54mm。
1级:轻微(图10a);2级:轻度(图10b);3级:中度(图10c);4级:重度(图10d);5级:严重(图10e)。