铸件质量控制计划
铸造质量控制
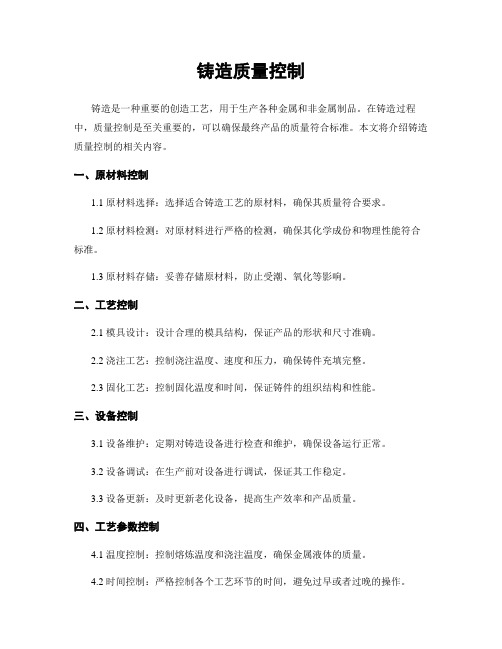
铸造质量控制铸造是一种重要的创造工艺,用于生产各种金属和非金属制品。
在铸造过程中,质量控制是至关重要的,可以确保最终产品的质量符合标准。
本文将介绍铸造质量控制的相关内容。
一、原材料控制1.1 原材料选择:选择适合铸造工艺的原材料,确保其质量符合要求。
1.2 原材料检测:对原材料进行严格的检测,确保其化学成份和物理性能符合标准。
1.3 原材料存储:妥善存储原材料,防止受潮、氧化等影响。
二、工艺控制2.1 模具设计:设计合理的模具结构,保证产品的形状和尺寸准确。
2.2 浇注工艺:控制浇注温度、速度和压力,确保铸件充填完整。
2.3 固化工艺:控制固化温度和时间,保证铸件的组织结构和性能。
三、设备控制3.1 设备维护:定期对铸造设备进行检查和维护,确保设备运行正常。
3.2 设备调试:在生产前对设备进行调试,保证其工作稳定。
3.3 设备更新:及时更新老化设备,提高生产效率和产品质量。
四、工艺参数控制4.1 温度控制:控制熔炼温度和浇注温度,确保金属液体的质量。
4.2 时间控制:严格控制各个工艺环节的时间,避免过早或者过晚的操作。
4.3 压力控制:根据产品要求控制浇注压力,确保铸件的密度和强度。
五、质量检验控制5.1 外观检验:对铸件的表面质量进行检查,包括气孔、裂纹等缺陷。
5.2 尺寸检验:测量铸件的尺寸和几何形状,确保符合设计要求。
5.3 化学成份检验:对铸件的化学成份进行分析,确保符合标准。
综上所述,铸造质量控制是确保铸件质量的关键环节,需要在原材料、工艺、设备、工艺参数和质量检验等方面进行全面控制。
惟独做好质量控制,才干生产出满足客户需求的优质铸件。
铸件质量控制计划
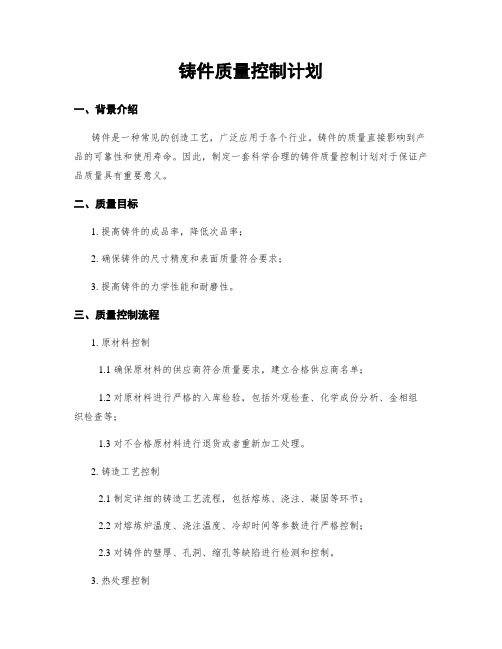
铸件质量控制计划一、背景介绍铸件是一种常见的创造工艺,广泛应用于各个行业。
铸件的质量直接影响到产品的可靠性和使用寿命。
因此,制定一套科学合理的铸件质量控制计划对于保证产品质量具有重要意义。
二、质量目标1. 提高铸件的成品率,降低次品率;2. 确保铸件的尺寸精度和表面质量符合要求;3. 提高铸件的力学性能和耐磨性。
三、质量控制流程1. 原材料控制1.1 确保原材料的供应商符合质量要求,建立合格供应商名单;1.2 对原材料进行严格的入库检验,包括外观检查、化学成份分析、金相组织检查等;1.3 对不合格原材料进行退货或者重新加工处理。
2. 铸造工艺控制2.1 制定详细的铸造工艺流程,包括熔炼、浇注、凝固等环节;2.2 对熔炼炉温度、浇注温度、冷却时间等参数进行严格控制;2.3 对铸件的壁厚、孔洞、缩孔等缺陷进行检测和控制。
3. 热处理控制3.1 制定合理的热处理工艺流程,包括加热温度、保温时间、冷却速率等;3.2 对热处理设备进行定期维护和校准,确保温度和时间的准确性;3.3 对热处理后的铸件进行硬度测试、金相组织观察等检验。
4. 机械加工控制4.1 制定详细的加工工艺流程,包括铣削、钻孔、车削等操作;4.2 对加工设备进行定期维护和保养,确保设备的精度和稳定性;4.3 对加工件进行尺寸测量和表面质量检查,确保符合要求。
5. 检验控制5.1 制定全面的检验计划,包括外观检查、尺寸测量、力学性能测试等;5.2 对检验设备进行定期校准和维护,确保准确可靠;5.3 对不合格品进行分类和处理,追溯问题原因并采取纠正措施。
四、质量控制指标1. 铸件成品率:目标为95%以上;2. 铸件次品率:目标为5%以下;3. 尺寸精度:符合产品图纸要求;4. 表面质量:无裂纹、气孔等缺陷;5. 力学性能:符合产品技术要求。
五、质量控制记录1. 原材料检验记录,包括供应商信息、检验结果等;2. 铸造工艺参数记录,包括熔炼温度、浇注温度、冷却时间等;3. 铸件缺陷记录,包括壁厚、孔洞、缩孔等情况;4. 热处理工艺参数记录,包括加热温度、保温时间、冷却速率等;5. 热处理后铸件的硬度测试记录;6. 机械加工工艺参数记录,包括铣削、钻孔、车削等操作;7. 加工件尺寸测量和表面质量检查记录;8. 检验结果记录,包括外观检查、尺寸测量、力学性能测试等;9. 不合格品处理记录,包括分类、原因分析和纠正措施。
铸件质量控制计划
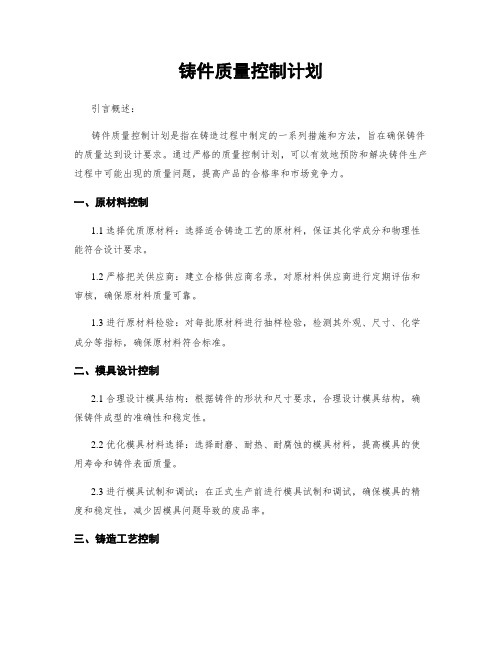
铸件质量控制计划引言概述:铸件质量控制计划是指在铸造过程中制定的一系列措施和方法,旨在确保铸件的质量达到设计要求。
通过严格的质量控制计划,可以有效地预防和解决铸件生产过程中可能出现的质量问题,提高产品的合格率和市场竞争力。
一、原材料控制1.1 选择优质原材料:选择适合铸造工艺的原材料,保证其化学成分和物理性能符合设计要求。
1.2 严格把关供应商:建立合格供应商名录,对原材料供应商进行定期评估和审核,确保原材料质量可靠。
1.3 进行原材料检验:对每批原材料进行抽样检验,检测其外观、尺寸、化学成分等指标,确保原材料符合标准。
二、模具设计控制2.1 合理设计模具结构:根据铸件的形状和尺寸要求,合理设计模具结构,确保铸件成型的准确性和稳定性。
2.2 优化模具材料选择:选择耐磨、耐热、耐腐蚀的模具材料,提高模具的使用寿命和铸件表面质量。
2.3 进行模具试制和调试:在正式生产前进行模具试制和调试,确保模具的精度和稳定性,减少因模具问题导致的废品率。
三、铸造工艺控制3.1 严格控制浇注温度:根据铸件材料和结构要求,控制浇注温度,避免因温度过高或过低导致铸件缺陷。
3.2 控制浇注速度和压力:合理控制浇注速度和压力,确保铸件充型充实,避免气孔和夹杂等缺陷。
3.3 采取适当的冷却措施:在铸造结束后,采取合适的冷却措施,避免因快速冷却或过慢冷却导致铸件内部应力过大。
四、热处理控制4.1 选择合适的热处理工艺:根据铸件的材料和使用要求,选择适合的热处理工艺,提高铸件的强度和硬度。
4.2 严格控制热处理参数:在热处理过程中,严格控制温度、时间和冷却速度等参数,确保热处理效果稳定可靠。
4.3 进行热处理质量检验:对热处理后的铸件进行硬度测试、金相分析等检验,确保热处理效果符合设计要求。
五、表面处理控制5.1 选择适合的表面处理方法:根据铸件的用途和要求,选择合适的表面处理方法,提高铸件的耐腐蚀性和美观度。
5.2 严格控制表面处理工艺:在表面处理过程中,严格控制处理时间、温度和液体浓度等参数,确保表面处理效果均匀一致。
铸件质量控制计划

铸件质量控制计划引言概述:铸件质量控制计划是在铸造过程中为确保铸件质量而制定的一系列措施和方法。
它对于保证铸件的物理性能、化学成份和尺寸精度等方面的要求起着至关重要的作用。
本文将从五个大点出发,详细阐述铸件质量控制计划的重要性和实施方法。
正文内容:1. 材料选择1.1 原材料的质量要求:选择合适的铸造材料,如铁、钢、铝等,并确保其化学成份符合要求。
1.2 原材料的处理:对原材料进行预处理,包括融化、净化、除气等,以提高铸件的质量。
2. 模具设计与创造2.1 模具材料选择:选择适合铸件材料的模具材料,如石膏、砂型、金属模具等,以确保模具的稳定性和耐用性。
2.2 模具结构设计:根据铸件的形状和尺寸要求,设计合理的模具结构,以确保铸件的准确性和表面质量。
2.3 模具创造工艺:采用先进的创造工艺,如数控加工、电火花等,以提高模具的创造精度和质量。
3. 浇注工艺控制3.1 浇注温度控制:控制铸造金属的浇注温度,以确保金属充分液化和浇注过程的稳定性。
3.2 浇注速度控制:控制浇注速度,以避免金属液体的冷却不均匀温和泡的产生。
3.3 浇注压力控制:控制浇注压力,以确保金属液体充分填充模腔,并避免缺陷的产生。
4. 模具温度控制4.1 模具预热:在铸造过程中对模具进行预热,以提高金属液体的流动性和填充性。
4.2 模具冷却:在铸造过程中对模具进行冷却,以控制金属液体的凝固速度和铸件的尺寸精度。
5. 检测与检验5.1 尺寸检测:采用合适的测量工具,如卡尺、投影仪等,对铸件的尺寸进行检测,以确保其符合要求。
5.2 化学成份分析:通过化学分析仪器,对铸件的化学成份进行分析,以确保其符合标准。
5.3 物理性能测试:通过拉伸试验、冲击试验等,对铸件的物理性能进行测试,以确保其强度和韧性等符合要求。
总结:铸件质量控制计划是确保铸件质量的重要手段,它涉及材料选择、模具设计与创造、浇注工艺控制、模具温度控制以及检测与检验等方面。
通过科学合理的计划和控制措施,可以有效提高铸件的质量和可靠性,满足工程项目的需求。
压铸控制计划范例
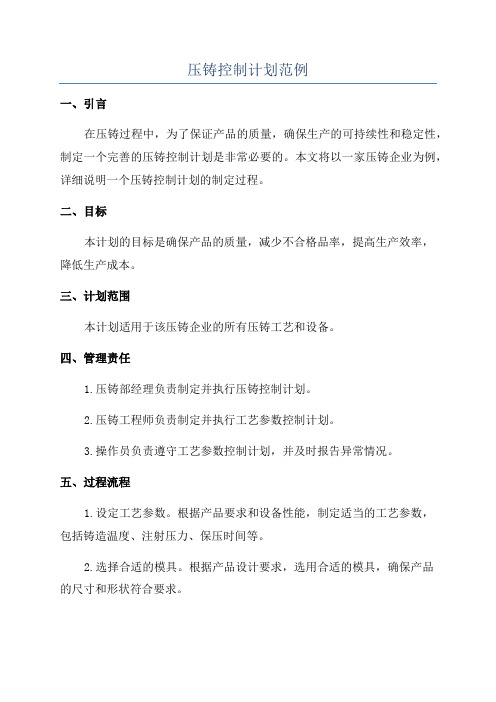
压铸控制计划范例一、引言在压铸过程中,为了保证产品的质量,确保生产的可持续性和稳定性,制定一个完善的压铸控制计划是非常必要的。
本文将以一家压铸企业为例,详细说明一个压铸控制计划的制定过程。
二、目标本计划的目标是确保产品的质量,减少不合格品率,提高生产效率,降低生产成本。
三、计划范围本计划适用于该压铸企业的所有压铸工艺和设备。
四、管理责任1.压铸部经理负责制定并执行压铸控制计划。
2.压铸工程师负责制定并执行工艺参数控制计划。
3.操作员负责遵守工艺参数控制计划,并及时报告异常情况。
五、过程流程1.设定工艺参数。
根据产品要求和设备性能,制定适当的工艺参数,包括铸造温度、注射压力、保压时间等。
2.选择合适的模具。
根据产品设计要求,选用合适的模具,确保产品的尺寸和形状符合要求。
3.准备材料。
选用合适的铸造材料,并按照配方准确称量,防止材料的异相反应和杂质的混入。
4.进行模具预热。
通过对模具进行适当的预热,确保铸造过程中温度的均匀分布。
5.铸造操作。
将准备好的铸造材料倒入模具中,控制注射温度、注射压力和注塑时间。
6.保压操作。
在注射结束后,进行保压操作,以保证铸件的密实性和尺寸精度。
7.铸件取出。
待冷却后,将铸件从模具中取出,并进行修边、打磨等工艺处理。
8.检测和检验。
对铸件进行尺寸、外观、材料成分等多个方面的检测和检验,确保产品符合设计和客户要求。
9.记录和分析。
对每一次生产过程进行记录和分析,及时发现问题并采取纠正措施。
六、控制方法1.控制工艺参数。
通过严格控制工艺参数,如温度、压力、时间等,确保产品的质量和尺寸稳定。
2.定期保养设备。
对压铸设备进行定期保养和维护,确保设备的可靠性和稳定性。
3.培训操作员。
对操作员进行培训,提高其操作技能和质量意识,降低人为错误。
4.定期检测和校准检测设备。
对检测设备进行定期检测和校准,确保测试数据的准确性和可靠性。
5.定期召开质量会议。
通过召开质量会议,总结经验,分享问题,促进团队间的沟通和合作。
铸件质量控制计划
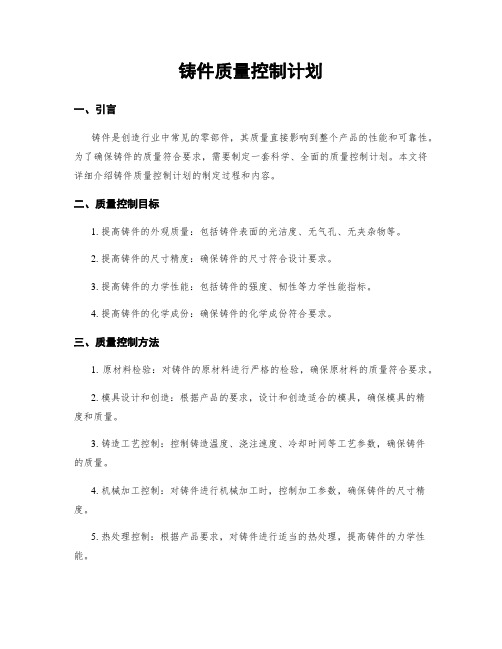
铸件质量控制计划一、引言铸件是创造行业中常见的零部件,其质量直接影响到整个产品的性能和可靠性。
为了确保铸件的质量符合要求,需要制定一套科学、全面的质量控制计划。
本文将详细介绍铸件质量控制计划的制定过程和内容。
二、质量控制目标1. 提高铸件的外观质量:包括铸件表面的光洁度、无气孔、无夹杂物等。
2. 提高铸件的尺寸精度:确保铸件的尺寸符合设计要求。
3. 提高铸件的力学性能:包括铸件的强度、韧性等力学性能指标。
4. 提高铸件的化学成份:确保铸件的化学成份符合要求。
三、质量控制方法1. 原材料检验:对铸件的原材料进行严格的检验,确保原材料的质量符合要求。
2. 模具设计和创造:根据产品的要求,设计和创造适合的模具,确保模具的精度和质量。
3. 铸造工艺控制:控制铸造温度、浇注速度、冷却时间等工艺参数,确保铸件的质量。
4. 机械加工控制:对铸件进行机械加工时,控制加工参数,确保铸件的尺寸精度。
5. 热处理控制:根据产品要求,对铸件进行适当的热处理,提高铸件的力学性能。
6. 检测与测试:使用适当的检测和测试方法,对铸件进行质量检验,确保铸件的质量符合要求。
四、质量控制流程1. 原材料检验流程:a. 对原材料进行外观检查,检查是否有明显的缺陷。
b. 进行化学成份分析,确保原材料的化学成份符合要求。
c. 进行物理性能测试,包括硬度、抗拉强度等指标的测试。
2. 模具设计和创造流程:a. 根据产品要求,设计模具的结构和尺寸。
b. 创造模具,并进行精度检验,确保模具的精度符合要求。
3. 铸造工艺控制流程:a. 设定铸造温度、浇注速度、冷却时间等工艺参数。
b. 进行铸造过程监控,记录关键参数,确保铸件的质量。
4. 机械加工控制流程:a. 设定机械加工参数,包括切削速度、进给量等。
b. 进行机械加工过程监控,记录加工参数和尺寸精度。
5. 热处理控制流程:a. 根据产品要求,选择适当的热处理工艺。
b. 进行热处理过程监控,确保铸件的力学性能符合要求。
铝合金压铸件控制计划

铝合金压铸件控制计划1.引言2.原材料采购选择优质的铝合金原料对于保证产品质量至关重要。
首先,要选择有良好信誉的供应商,并与之建立长期合作关系。
其次,要对进货的铝合金原料进行全面的物理与化学性能检测,确保其符合产品要求。
最后,在采购过程中,要严格控制原材料的质量、规格和数量,防止出现偷工减料等问题。
3.生产工艺控制3.1铝液的准备铝液是压铸件的原材料,其温度、成分和纯度直接影响产品的质量。
在铝液的准备过程中,应确保炉温达到设定温度,并在加工过程中定期检测铝液的成分和纯度,以及温度的稳定性。
3.2模具的设计与制作模具是铸造过程中的关键因素之一,其设计和制作需要经验丰富且具有高精度的技术人员。
在模具设计和制作过程中,要根据产品的要求和工艺要求,选择合适的材料和加工工艺。
同时,在模具加工过程中,要进行严格的检测和测量,确保模具的精度和质量。
3.3压铸过程控制压铸是铝合金压铸件的成型过程,在压铸过程中,要严格控制铝液的温度、压力和铸造时间。
同时,还要监控压铸机的工作状态,确保其正常运行。
3.4后处理在铝合金压铸件的后处理过程中,包括去除余脱模剂、清洗、修整和热处理等环节。
这些环节需要严格按照工艺要求进行操作,并进行必要的质量检测和测量,以确保产品的精度和质量。
4.设备检测设备的检测是压铸件质量控制的重要环节。
首先,要定期对压铸机进行维护和保养,确保其正常运行。
其次,在每一批产品生产之前,要对压铸机进行调试和校验,确保其精度和稳定性。
同时,还要对成品进行抽样检测和测量,对不合格品进行追踪和整改。
5.质量管理体系为了提高铝合金压铸件的质量,应建立完善的质量管理体系。
首先,要制定详细的工作操作规范和质量检测标准,确保每个环节的工作都按照规定进行。
其次,要建立质量跟踪和评价机制,对每一批产品进行质量检测和评估,及时发现问题并采取措施进行改进。
6.结论。
铸造质量控制
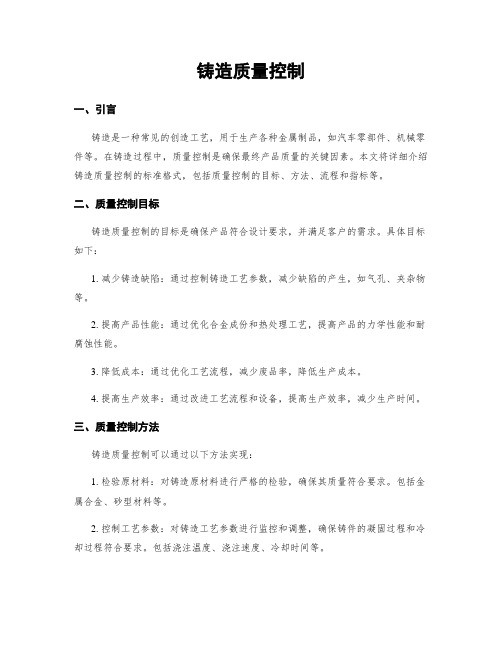
铸造质量控制一、引言铸造是一种常见的创造工艺,用于生产各种金属制品,如汽车零部件、机械零件等。
在铸造过程中,质量控制是确保最终产品质量的关键因素。
本文将详细介绍铸造质量控制的标准格式,包括质量控制的目标、方法、流程和指标等。
二、质量控制目标铸造质量控制的目标是确保产品符合设计要求,并满足客户的需求。
具体目标如下:1. 减少铸造缺陷:通过控制铸造工艺参数,减少缺陷的产生,如气孔、夹杂物等。
2. 提高产品性能:通过优化合金成份和热处理工艺,提高产品的力学性能和耐腐蚀性能。
3. 降低成本:通过优化工艺流程,减少废品率,降低生产成本。
4. 提高生产效率:通过改进工艺流程和设备,提高生产效率,减少生产时间。
三、质量控制方法铸造质量控制可以通过以下方法实现:1. 检验原材料:对铸造原材料进行严格的检验,确保其质量符合要求。
包括金属合金、砂型材料等。
2. 控制工艺参数:对铸造工艺参数进行监控和调整,确保铸件的凝固过程和冷却过程符合要求。
包括浇注温度、浇注速度、冷却时间等。
3. 检测铸件缺陷:使用无损检测技术,如X射线检测、超声波检测等,对铸件进行缺陷检测,及时发现和修复缺陷。
4. 进行力学性能测试:对铸件进行拉伸、弯曲等力学性能测试,确保产品的力学性能符合要求。
5. 进行化学成份分析:对铸件进行化学成份分析,确保合金成份符合要求。
6. 进行金相组织分析:对铸件进行金相组织分析,了解铸件的组织结构和缺陷情况。
四、质量控制流程铸造质量控制的流程包括以下步骤:1. 设计铸造工艺:根据产品要求和材料特性,设计合适的铸造工艺,包括模具设计、浇注系统设计等。
2. 检验原材料:对铸造原材料进行检验,确保其质量符合要求。
3. 控制工艺参数:根据设计要求,控制铸造工艺参数,如浇注温度、浇注速度等。
4. 监控铸造过程:通过实时监控铸造过程中的温度、压力等参数,确保铸造过程的稳定性。
5. 进行缺陷检测:对铸件进行缺陷检测,如X射线检测、超声波检测等,发现并修复缺陷。
- 1、下载文档前请自行甄别文档内容的完整性,平台不提供额外的编辑、内容补充、找答案等附加服务。
- 2、"仅部分预览"的文档,不可在线预览部分如存在完整性等问题,可反馈申请退款(可完整预览的文档不适用该条件!)。
- 3、如文档侵犯您的权益,请联系客服反馈,我们会尽快为您处理(人工客服工作时间:9:00-18:30)。
铸件质量控制计划
1.目的:
对进厂铸件进行检验并对其实施有效控制。
2.适用范围:
公司涉及的所有铸件供货厂家。
3.职责:
3.1质量管理部:
3.1.1 负责计划的编制、下发并按时间节点组织实施、并出具相应的报告;
负责对整改后的质量改进情况进行验证并整理成验证报告发相关责任单位;
3.1.2负责根据实施计划进行产品抽样,出具试验报告并对存在的问题要求相关责任单位进行整改;
3.1.3负责对责任单位进行考核。
3.2 各供货厂家及生产单位:
3.2.1 负责配合质量管理部开展工作;
3.2.2负责对质量管理部提出的问题进行原因分析、制定措施,形成《质量整改措施表》,并按时
间节点进行整改,避免质量问题的重复发生。
4. 质量控制过程方面:
4.1质量要求
4.1.1表面质量:检验的依据是铸件的有关标准、技术条件和图样。
铸件的表面质量主要包括铸件的表面缺陷、尺寸精度、质量偏差、形状偏差、表面粗糙度和铸件表面清理质量等。
为保证铸件的表面质量,应规定每批铸件100%的检验其表面缺陷。
检验要求一般规定如下:
A.铸件非加工表面上的浇冒口应清理得与铸件表面同样平整。
B.在铸件上不允许有裂纹、通孔、穿透性的冷隔和穿透性的缩松、夹渣缺陷。
C.铸件非加工表面的毛刺、披缝应清理至与铸件面同样平整。
D.铸件加工表面,不允许有裂纹、毛刺、划伤等缺陷存在。
E.作为加工基准面和测量基准的铸件表面,必须平整。
F.变形的铸件允许整形(校正),然后逐个检验是否有裂纹。
4.1.2尺寸方面:为保证铸件满足使用性能的要求,在检验铸件尺寸时应遵循以下规定:
A.铸件的尺寸和几何形状应符合零件图的要求,若无特殊规定时,铸件尺寸公差应符合指定精
度等级的公差要求。
B.铸件进厂尺寸检验按GB/T2828.1-2003中的检验水平Ⅱ执行,接收准则为(0,1)。
C.铸件进厂,按铸件图纸要求,抽检其主要尺寸,若铸件尺寸不合格时,则不进行理化检验,
按不合格品控制程序执行。
4.1.3表面清理质量:
A.铸件外表面上,一般不允许有粘砂、氧化皮和影响零件装配及影响外表美观的缺陷。
B.铸铁件内腔应无残留砂芯块,芯骨和飞翅、毛刺等肉类缺陷。
C.铸件几何形状必须完整,非加工面上的清理损伤不应大于该处的尺寸偏差。
D.有特殊情况外,铸件表面允许存留的浇冒口、毛刺,多肉残余量应按表1的要求进行。
E.有特殊清理要求的铸件,应另附图说明要求。
4.1.4材质方面:根据本公司实际生产情况,铸铁件以金相组织作为验收依据。
铸钢件以化学成分、金相组织、力学性能同时作为验收依据,一项不合格则判定为不合格。
不同铸造合金的材质检验标准如下:
A.球墨铸铁件的质量检验规则按照GB/T1348-2009的规定执行。
B.一般工程用铸造碳钢件的质量检验规则参照GB/T11352-2009的规定执行。
C.图纸中对铸件的硬度有要求的需做硬度检验,硬度应符合图纸要求。
D.试样的取样方法:
Ⅰ.从铸件本体切取试样。
试样自铸件指定部位(一般选在铸件上受力最大的部位)上截取,能比较真实地反映该部位铸件本身的力学性能。
Ⅱ.附铸试样。
为不损伤铸件本体可采用试样与铸件在同一铸型内铸成。
试样与铸件一样均与浇注系统相连,或作铸件某一指定部分的延续。
附铸试样只有在试样与铸件有可能实现相
同的冷却速度的情况下值得推荐应用,一般情况下少采用附铸试样。
4.2附表及供方上半年质量信息联系单
表1 浇冒口、毛刺、多肉等允许残留量值
编制:张东坡审核:醋伟强批准:醋伟强。