磁粉检测(6~10)
磁粉检测—磁粉检测技术(无损检测课件)

第3节 磁粉检测技术
磁粉检测的基本步骤?
基本步骤
磁粉检测的基本步骤
预处理; 磁化工件; 施加磁粉或磁悬液; 磁痕分析与评定; 退磁; 后处理;
第3节 磁粉检测技术
磁粉
按磁痕观察分为荧光磁粉 和非荧光磁粉;
按施加方式分为湿法磁粉 和干法磁粉;
பைடு நூலகம்
标准试块
用途
➢ 用于检验磁粉探伤设备、磁粉和磁悬液的综合性能(系统灵敏度); ➢ 用于检测被检工件表面的磁场方向,有效磁化范围和大致的有效磁 场强度; ➢ 用于考察所用的探伤工艺规程和操作方法是否妥当; ➢ 当无法计算磁化规范时,可大致确定较理想的磁化规范 类型 ➢ A型、C型、D型和M1型四种
型试片的工件原理
将A型试片刻槽的一面紧贴(用透明胶纸粘贴紧)在被检工 件表面,当工件磁化后,工件表面的A型试片也被磁化,并 在试片刻槽处形成漏磁场,当进行湿法连续检验时,在A型 试片上可以观察到与磁场方向垂直的两条清晰圆弧形磁痕。 如果继续增大磁化电流,则圆弧形磁痕的长度就沿着刻槽增 长,磁痕高度也增加。因此,根据A型试片上的磁痕显示, 就可以判断工件表面的磁场方向和大致的有效磁场强度。
磁粉检测5-10章课程重点讲义
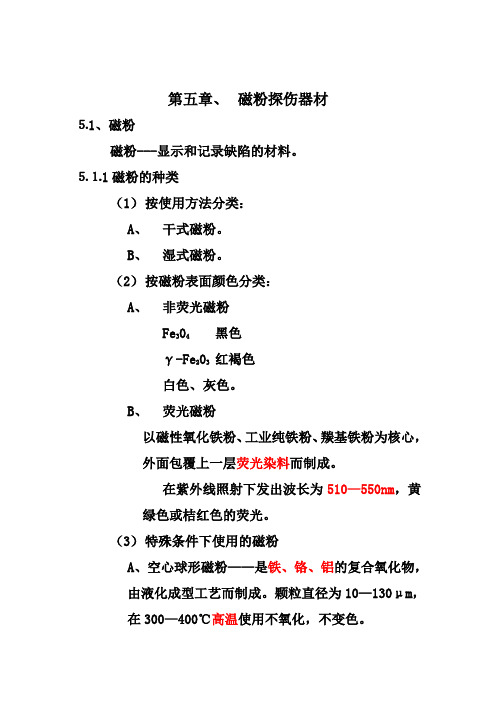
第五章、磁粉探伤器材⒌1、磁粉磁粉---显示和记录缺陷的材料。
⒌⒈1磁粉的种类(1)按使用方法分类:A、干式磁粉。
B、湿式磁粉。
(2)按磁粉表面颜色分类:A、非荧光磁粉Fe304黑色γ-Fe203红褐色白色、灰色。
B、荧光磁粉以磁性氧化铁粉、工业纯铁粉、羰基铁粉为核心,外面包覆上一层荧光染料而制成。
在紫外线照射下发出波长为510—550nm,黄绿色或桔红色的荧光。
(3)特殊条件下使用的磁粉A、空心球形磁粉——是铁、铬、铝的复合氧化物,由液化成型工艺而制成。
颗粒直径为10—130μm,在300—400℃高温使用不氧化,不变色。
⒌⒈3磁粉的性能(1)磁性A、高磁导率,μ↑B、低矫顽力, Hc↓C、低剩磁。
Br↓磁粉的磁性可用磁滞回线表示——形状狭长磁滞回线,JB4730-94,取消磁性>7g值,经过试验,磁性值大的灵敏度不一定高。
磁性值<7g时,灵敏度反而高。
国外的磁粉,磁性值小于4g,而灵敏度高。
(2)粒度磁粉的粒度——即磁粉颗粒的大小。
粒度的影响:①漏磁场对磁粉的吸附。
②悬浮性选择粒度时应考虑的因素:A、缺陷位置表面缺陷——细颗粒,近表面缺陷——粗颗粒。
B、缺陷大小缺陷大——粗颗粒,缺陷小——细颗粒。
C、不同检验方法湿法——细颗粒,干法——粗颗粒,荧光法——细颗粒。
所以,磁粉的粒度应有一定的范围:非荧光磁粉干法10—50μm最大粒度≧150μm湿法5—10μm 最大粒度≧50μm 荧光磁粉5--25μm(3)形状球形、条形、椭圆形、空心、不规则形状。
A、条形磁粉优点:易磁化、易形成磁痕。
缺点:易产生聚集、流动性差。
B、球形磁粉优点:流动性好。
缺点:不易被漏磁场磁化。
理想的磁粉是几种形状磁粉混合使用。
(4)流动性流动性有关因素:A、磁化电流种类,(AC、DC、HBC)B、工件表面状态,C、磁粉形状有关,D、湿法检测与载液有关。
(5)密度湿法—4.5g/cm3干法—8g/cm3空心球形—0.71-2.3g/cm3(6)识别度是指磁粉的光学性能,识别度: A、磁粉颜色或荧光亮度B、磁粉—工件表面,对比度。
(磁粉)标准对比

磁粉检测——问答为什么旋转磁场磁粉探伤仪不能用于剩磁法?用剩磁法检测的首要条件是能够获得足够的剩磁。
因此,当采用交流设备磁化工件时必须配有断电相位控制器。
因为交流电产生的磁场强度在不断地变化,如果不采用断电相位控制,让它能在达到最大剩磁的时限内停止磁化,就不能确保获得最大的剩磁。
而旋转磁场磁粉探伤仪是由两相正弦交变磁场形成的旋转磁场,不仅其磁场的大小在不停地变化,而且其方向也在360°范围内在不断的改变。
所以,无论在什么时候断电,磁场的大小和方向都是未知的,更无法保证获得稳定的最大剩磁。
因此,旋转磁场磁粉探伤仪只能用于连续法,而不能用于剩磁法。
磁粉检测——标准对比范围JB/T4730的本部分规定了承压设备磁粉检测方法及质量分级要求。
本部分适用于铁磁性材料制承压设备的原材料、零部件和焊接接头表面、近表面缺陷的检测。
与承压设备有关的支承件和结构件,如有要求也可参照本标准进行磁粉检测。
JB/4730标准只适用于压力容器无损检测,JB/4730-2005标准将适用范围扩大到锅炉压力容、压力管道等承压设备的检测,与承压设备有关的支承件和结构件磁粉检测也可参照执行。
磁粉检测程序1、预处理;2、磁化;3、施加磁粉或磁悬液4、磁痕的观察与记录;5、缺陷评级;6、退磁;7、后处理。
JB4730-1994无对应条款。
磁粉检测设备1、JB/4730-1994对工件退磁后剩磁值要求太高,既没有必要,也难于达到,故参考美国标准由原剩磁160A/m变更为240A/m。
2、JB/4730-1994无交叉磁轭方面的相应规定,由于交磁轭一次可以检测一个区域内各个方向缺陷,因此在锅炉、压力容器行业得到了广泛使用,磁粉标准修改组在我国现有交叉磁轭设备进行提升力和灵敏度试验基础上,提出了交叉电磁轭的提升力要求。
磁粉、载体及磁悬液1、对表面不规则工件(如螺纹根部)进行荧光检测时,为防止产生过度背景,宜选择较低浓度的磁悬液,因此JB/T4730-2005将荧光磁粉配制浓度下限值降低至0.5g/L。
第四章 磁粉检测

(3)缺陷位置和形状: 缺陷位置和形状: 同样的缺陷,位于表面时漏磁通↑ 同样的缺陷,位于表面时漏磁通↑;若位于距表 面很深的地方,则几乎没有漏磁通泄漏于空间。 面很深的地方,则几乎没有漏磁通泄漏于空间。 缺陷的深宽比越大,漏磁场越强。 缺陷的深宽比越大,漏磁场越强。 缺陷垂直于工件表面(缺陷切割磁力线的角度接 缺陷垂直于工件表面( 近正交) 近正交)时,漏磁场最强; 漏磁场最强; 缺陷与工件表面平行时,则几乎不产生漏磁通。 缺陷与工件表面平行时,则几乎不产生漏磁通。 缺陷夹角小于20度时, 缺陷夹角小于20度时,很难检出 度时
35000 NI = ( ± 10 %), L / D ≥ 3 L +2 D
(1)周向磁化——利用周向磁场进行磁化 周向磁化——利用周向磁场进行磁化 利用周向磁场
在工件周围建立垂直其轴向的闭合周向磁场,发现取向基本与电流方向 在工件周围建立垂直其轴向的闭合周向磁场,发现取向基本与电流方向 平行的缺陷 的缺陷。 平行的缺陷。
磁力线
I
I
B)电流通过中心导体 ) 磁痕 A)工件直接通电
优点: 优点: 可直观显示出缺陷的形状、位置与大小,并能大致确定缺陷的性能; 可直观显示出缺陷的形状、位置与大小,并能大致确定缺陷的性能; 检测灵敏度高,可检出宽度仅为 的表面裂纹; 检测灵敏度高,可检出宽度仅为0.1µm的表面裂纹; 的表面裂纹 应用范围广,不收工件大小及几何形状的限制; 应用范围广,不收工件大小及几何形状的限制; 工艺简单,检测速度快, 工艺简单,检测速度快,费用低廉
(4)辅助通电法 (4)辅助通电法
1)电缆平行磁化 法
2)铜板平行磁化法 某些工件夹持时易变形或尖端易烧损
二、磁化电流
磁粉检测使用的磁化电流有交流、直流及整流电等几种。 磁粉检测使用的磁化电流有交流、直流及整流电等几种。 交流 等几种 (1)交流磁化:应用最广 交流磁化: ☺ 交流电的趋肤效应能提高磁粉检测检验表面缺陷的灵敏度; 交流电的趋肤效应 提高磁粉检测检验表面缺陷的灵敏度; 趋肤效应能 磁粉检测检验表面缺陷 ☺ 只有使用交流电才能在被检工件上建立起方向随时间变化的 只有使用交流电才能在被检工件上建立起方向随时间变化 建立起方向随时间变化的 磁场,实现复合磁化; 复合磁化; 磁场,实现复合磁化 ☺ 与直流磁化相比,交流磁场在被检工件截面变化部位的分布 与直流磁化相比,交流磁场在被检工件截面变化部位 截面变化部位的 较为均匀 有利于对这些部位的缺陷的检测; 较为均匀,有利于对这些部位的缺陷的检测; 均匀,
磁粉检测作业指导书
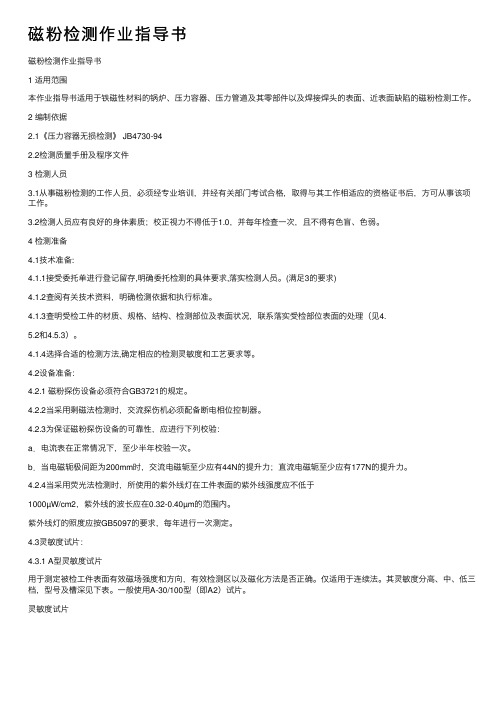
磁粉检测作业指导书磁粉检测作业指导书1 适⽤范围本作业指导书适⽤于铁磁性材料的锅炉、压⼒容器、压⼒管道及其零部件以及焊接焊头的表⾯、近表⾯缺陷的磁粉检测⼯作。
2 编制依据2.1《压⼒容器⽆损检测》 JB4730-942.2检测质量⼿册及程序⽂件3 检测⼈员3.1从事磁粉检测的⼯作⼈员,必须经专业培训,并经有关部门考试合格,取得与其⼯作相适应的资格证书后,⽅可从事该项⼯作。
3.2检测⼈员应有良好的⾝体素质;校正视⼒不得低于1.0,并每年检查⼀次,且不得有⾊盲、⾊弱。
4 检测准备4.1技术准备:4.1.1接受委托单进⾏登记留存,明确委托检测的具体要求,落实检测⼈员。
(满⾜3的要求)4.1.2查阅有关技术资料,明确检测依据和执⾏标准。
4.1.3查明受检⼯件的材质、规格、结构、检测部位及表⾯状况,联系落实受检部位表⾯的处理(见4.5.2和4.5.3)。
4.1.4选择合适的检测⽅法,确定相应的检测灵敏度和⼯艺要求等。
4.2设备准备:4.2.1 磁粉探伤设备必须符合GB3721的规定。
4.2.2当采⽤剩磁法检测时,交流探伤机必须配备断电相位控制器。
4.2.3为保证磁粉探伤设备的可靠性,应进⾏下列校验:a.电流表在正常情况下,⾄少半年校验⼀次。
b.当电磁轭极间距为200mm时,交流电磁轭⾄少应有44N的提升⼒;直流电磁轭⾄少应有177N的提升⼒。
4.2.4当采⽤荧光法检测时,所使⽤的紫外线灯在⼯件表⾯的紫外线强度应不低于1000µW/cm2,紫外线的波长应在0.32-0.40µm的范围内。
紫外线灯的照度应按GB5097的要求,每年进⾏⼀次测定。
4.3灵敏度试⽚:4.3.1 A型灵敏度试⽚⽤于测定被检⼯件表⾯有效磁场强度和⽅向,有效检测区以及磁化⽅法是否正确。
仅适⽤于连续法。
其灵敏度分⾼、中、低三档,型号及槽深见下表。
⼀般使⽤A-30/100型(即A2)试⽚。
灵敏度试⽚注:试⽚相对槽深表达式中,分⼦为⼈⼯槽深度,分母为试⽚厚度,单位为µm4.3.2 C型灵敏度试⽚当检测焊缝坡⼝等狭⼩部位,由于尺⼨关系,A型灵敏度试⽚使⽤不变时,可⽤C型灵敏度试⽚。
磁粉检测考试计算题(有答案)

计算题1.长为500mm、直径为20mm的钢制轴类试件需要检查周向缺陷,若选用连续螺线圈纵向磁化法,线圈匝数为10匝,则应选用多大的磁化电流?解:∵工件长径比L/D=500/20=25,∴L/D=15,采用在低充填因数线圈中偏心放置纵向磁化,依经验公式NI=45000/(L/D)可有I=45000/[N(L/D)]将N=10、L/D=15代入上式,可得I=300A2.有一长为200mm、直径为20mm的钢制轴类试件需检查周向缺陷。
若选用连续法线圈纵向磁化,则应施加多大的磁化电流?解:∵工件长径比L/D=200/20=10,∴不需要作修正。
采用在低充填因数线圈中心偏心放置纵向磁化,依经验公式NI=45000/(L/D)可有I=45000/[N(L/D)],∴将N=10、L/D=10代入上式,可得I=450A3.钢制轴类试件长径比为25,正中放置在匝数为10的低充填因数线圈中检查周向缺陷。
线圈半径为R=150mm,需选用多大的磁化电流?解:选用经验公式NI=(K2R)/[6(L/D)-5] 由上式可有I=(K2R)/N[6(L/D)-5],∵L/D=25>15,∴取L/D=15,将K2=1720(经验常数),R=150mm,N=10,L/D=15代入上式,可得I=303.5A 答:磁化电流应为303.5A;两次完成全检4.已知开端线圈的内半径R=150mm、宽度为L=50mm。
若要求在线圈轴线端部产生磁化磁场强度H端=60(Oe),试求磁化线圈的安匝数NI为多少?解:有限长线圈轴线端部的磁场强度为H=(NI/L)·[L/5(L2+R2)1/2] 由上式可得NI=2H(L2+R2)1/2 R=0.15m L=0.05m H=2400A/m 将已知数据代入上式可得NI=1510安匝5.钢制轴类试件长径比为10,正中放置在匝数为10的低充填因数线圈中检查周向缺陷。
线圈半径R=150mm,应选用多大的磁化电流?解:选用经验公式NI=K2R/[6(L/D)-5] 由上式可有:I=K2R/{N[6(L/D)-5]},将K2=1720(经验常数)、R=150mm、N=10、L/D=10代入上式,可得I=469A6.有一钢制轴,长400mm、直径Φ40mm,使用一段时间后,需检查此轴的疲劳裂纹。
磁粉检测(6~10)
6 磁粉检测工艺所谓磁粉工艺,是指从预处理、磁化工件、施加磁粉或磁悬液,磁痕的观察与记录、缺陷评级、退磁和后处理等的全过程。
只有正确执行磁粉探伤工艺要求,才能保证磁粉探伤的灵敏度,检出应检的缺陷。
影响磁粉探伤灵敏度的因素主要有:磁场大小和方向的选择;磁化方法的选择;磁粉的性能;磁悬液的浓度;设备的性能;工件形状和表面粗糙度;缺陷的性质、形状和埋藏深度;工艺操作;人员水平;观察条件。
磁粉探伤方法的一般选择原则:a连续法和剩磁法都可进行探伤时,优先选择连续法。
b对于湿法和干法,优先选择湿法。
c对于按磁化方法分类的六种探伤方法,选用要根据工件的形状、尺寸、探伤操作的困难程度进行。
磁粉检测的检测方法,一般根据磁粉检测所用的载液或载体不同,分为湿法和干法检测;根据磁化工件和施加磁粉或磁悬液的时机不同,分为连续法和剩磁法检测。
根据不同分类条件,磁粉检测方法的分类为表6-1所示。
表6-1磁粉检测方法分类6.1 预处理预处理:被检工件表面不得有油脂、铁锈、氧化皮或其它粘附磁粉的物质。
表面的不规则状态不得影响检测结果的正确性和完整性,否则应做适当的修理,即预处理。
如打磨,则打磨后被检工件的表面粗糙度Ra≤25μm。
如果被检工件表面残留有涂层,当涂层厚度均匀且不超过0.05mm,不影响检测结果时,经合同各方同意,可以带涂层进行磁粉检测。
此外,预处理还包括:涂敷(反差增强剂)、封堵、装配件的撤解等。
6. 2 磁化、施加磁粉或磁悬液磁化:选择磁化方法,确定磁化规范。
磁化时间为1S ~3S,停施磁悬液至少1S后方可停止磁化;1,为保证磁化效果,至少反复磁化2次(连续法)。
2,分段磁化时,必须注意相邻部位的探伤需有重叠。
3,对于单磁轭磁化和触头法磁化,均只能实现单方向磁化,在同一部位,必须作2次互相垂直的磁化探伤。
4,对于通电法包括触头法,注意烧伤问题。
5,对于交叉磁轭法,四个磁极端面与检测面之间应尽量贴合,最大间隙不应超过1.5MM。
磁粉检测技术:磁粉检测适用范围及优缺点
二、磁粉检测优缺点
1)只能适用于检测铁磁性金属材料;只能用于检测工件表面和近表面 缺陷,一般深度不超过1~2mm,不能检出埋藏较深的内部缺陷;难于 定量缺陷的深度。
2)检查缺陷时的灵敏度与磁化方向有很大关系。如果缺陷风向与磁化 方向平行,或与工件表面夹角小于二十度的缺陷就难以显现。 3)通常都用目视法检查缺陷,磁痕的判断和解释需要有技术经验和素质。 4)工件表面的覆盖层、漆层、喷丸层对检测灵敏度起不良影响。 5)磁化后具有较大剩磁的工件还要进行退磁。
4)适用于检测管材、棒材、板材、型材和锻钢件及焊接件。
二、磁粉检测优缺点
1)可检测出铁磁性材料表面和近表面(开口和不开口)的缺陷。 2)能直观地显示出缺陷的位置、形状、大小和严重程度。 3)具有很高的检测灵敏度,可检测微米级宽度的缺陷。 4)单个工件检测速度快,工艺简单,成本低廉,污染少。 5)采用合适的磁化方法,几乎可以检测到工件表面 的各个部位, 基本上不受工件大小和几何形状的限制。 6)缺陷检测重复性好,可检测受腐蚀的表面。
2)适用于检测工件表面和近表面的裂纹、白点、发纹、折叠、疏松、冷隔 、气孔和夹杂等缺陷,但不适用于检测工件表面浅而宽的划伤、针孔状缺陷 、埋藏较深的内部缺陷和延伸方向与磁感应线方向夹角小于20度的缺陷。
一、磁粉检测适用范围
3)适用于检测未加工的原材料(如钢坯)和加工的半成品、 成品件及使用过的工件及特种设备。
磁粉检测磁粉检测Leabharlann 术磁粉检测适用范围及优缺点
一、磁粉检测适用范围
1)适用于检测铁磁性材料(如16MnR,20g,30CrMnSiA)工件表面和 近表面尺寸很小,间隙极窄(如可检测出长0.1mm、宽度为微米级的裂纹 )和目视难以看出的的缺陷。马氏体不锈钢和沉淀硬化不锈钢具有磁性, 因而可以进行检测。奥氏体不锈钢和奥氏体不锈钢焊条焊接的焊缝,以及 铜、铝、镁、钛合金等非磁性材料不能使用磁粉检测。
磁粉检测通用工艺规程
1. 范围适用于铁磁性材料制承压设备的原材料、零部件和焊接接头表面近表面缺陷的检测。
2.引用标准法规GB/T16673-1996 无损检测用黑光源辐射的测量JB/T4730-2005 承压设备无损检测JB/T6063-1992 磁粉探伤用磁粉JB/T6065-2004 无损检测磁粉检测用试片JB/T8290-1998 磁粉探伤机3. 检测人员3.1、磁粉检测人员上岗前, 应按照《特种设备无损检测人员考核与监督管理规则》的要求, 取得磁粉检测资格, 且只能从事相应资格的检测工作。
3.2、磁粉检测人员的矫正视力应不低于5.0, 并每年检查一次, 不得有色盲。
4. 检测设备、器材和材料4.1.设备磁粉检测设备应符合JB/T8290的规定。
4.1.1.当磁轭间距最大时, 交流电磁轭的提升力≮44N, 直流电磁轭的提升力≮177N.4.1.2、剩磁法检测时, 交流探伤机必配备断电相位控制器。
4.1.3、荧光磁粉检测时, 黑光灯在工作表面的照度≥1000μw/ , 黑光的波长λ=320nm~400nm,中心波长λ≈365nm。
黑光源应符合GB/T16673的规定。
4.1.4.退磁装置应保证退磁后表面剩磁≤0.3mT4.2.辅助器材一般包括下列器材:a)A1型、C型、D型和M1型试片, 磁场指示器;b)磁场强度计及毫特斯拉计;c)磁悬液浓度沉淀管;d)2~10倍放大镜;d)白光照度计;f)黑光灯;g)黑光辐照计。
4.3.磁粉、载液、磁悬液4.3.1、磁粉应具有高磁导率、低矫顽力和低剩磁, 并与工件表面的颜色对比度要较高。
其他要求应符合GB/T6063的规定。
4.3.2、载液为水时, 应加入防锈剂、表面活性剂及清洗剂。
载液为油时, 其运动粘度在38℃时应小于或等于3.0 /s, 使用温度小于或等于5.0 /s, 闪点不低于94℃, 且无荧光和异味。
4.3.3.磁悬液浓度范围应符合表1的规定。
测定前应充分搅匀。
表1 磁悬液浓度4.4.标准试块4.4.1、一般应选用A1-30/100, 检测狭小部位可选用C-15/50。
磁粉检测—磁粉检测基本原理(无损检测课件)
磁化规范
制定磁化规范的方法: ➢ 用经验公式计算; ➢ 用仪器测量工件表面的磁场强度; ➢ 测绘钢材磁特性曲线; ➢ 用标准试片确定大致的磁化规范。
第2节 磁粉检测的基本原理
1. 磁粉检测原理
磁粉检测原理
铁磁性材料和工件被磁化后, 由于不连续性的存在,使工 件表面和近表面的磁力线发 生局部畸而产生漏磁场,吸 附施加在工件表面的磁粉, 形成在合适光照下目视可见 的磁痕,从而显示不连续的 位置、形状和大小。
2. 使用范围
磁粉检测适用范围
铁磁性材料表面和近表面尺寸很小,间隙极窄,目视难以 看出的不连续性(长0.1mm,宽为微米级的裂纹);
未加工的原材料、加工的半成品、成品工件及在役或使用 过的零部件进行探伤,还能对板材、型材、管材、棒材、 焊接件、铸件及锻件进行探伤;
可以发现裂纹、夹杂、发纹、白点、折叠、冷隔和疏松等 缺陷。
第2节 磁粉检测的基本原理
磁化电流
为了在工件上产生磁场而采用的电流称为磁化电流。 方法:交流电、整流电、直流电和冲击电流。
磁化电流特点
交流电磁化湿法检验,对工件微小缺陷检测灵敏度高; 交流电的深入深度低于整流电和直流电; 交流电用于剩磁法检验时,应加装断电相位控制器; 交流电磁化连续法——有效值电流,剩磁检验——峰值电流; 整流电流中交流分量越大,检测近表面较深缺陷的能力越小; 单相半波整流电磁化干法检验,对工件近表面缺陷检测灵敏度高; 三相全波整流电可检测工件近表面较深的缺陷; 直流电可检测工件近表面最深的缺陷; 冲击电流只能用于剩
磁化规范
制定磁化规范考虑的因素 ➢ 工件的材料、热处理状态和磁特性——确定采用连续法还
是剩磁法及相应的磁化规范; ➢ 工件尺寸、形状、表面状态和欲检缺陷的几何形状和位
- 1、下载文档前请自行甄别文档内容的完整性,平台不提供额外的编辑、内容补充、找答案等附加服务。
- 2、"仅部分预览"的文档,不可在线预览部分如存在完整性等问题,可反馈申请退款(可完整预览的文档不适用该条件!)。
- 3、如文档侵犯您的权益,请联系客服反馈,我们会尽快为您处理(人工客服工作时间:9:00-18:30)。
6 磁粉检测工艺所谓磁粉工艺,是指从预处理、磁化工件、施加磁粉或磁悬液,磁痕的观察与记录、缺陷评级、退磁和后处理等的全过程。
只有正确执行磁粉探伤工艺要求,才能保证磁粉探伤的灵敏度,检出应检的缺陷。
影响磁粉探伤灵敏度的因素主要有:磁场大小和方向的选择;磁化方法的选择;磁粉的性能;磁悬液的浓度;设备的性能;工件形状和表面粗糙度;缺陷的性质、形状和埋藏深度;工艺操作;人员水平;观察条件。
磁粉探伤方法的一般选择原则:a连续法和剩磁法都可进行探伤时,优先选择连续法。
b对于湿法和干法,优先选择湿法。
c对于按磁化方法分类的六种探伤方法,选用要根据工件的形状、尺寸、探伤操作的困难程度进行。
磁粉检测的检测方法,一般根据磁粉检测所用的载液或载体不同,分为湿法和干法检测;根据磁化工件和施加磁粉或磁悬液的时机不同,分为连续法和剩磁法检测。
根据不同分类条件,磁粉检测方法的分类为表6-1所示。
表6-1磁粉检测方法分类6.1 预处理预处理:被检工件表面不得有油脂、铁锈、氧化皮或其它粘附磁粉的物质。
表面的不规则状态不得影响检测结果的正确性和完整性,否则应做适当的修理,即预处理。
如打磨,则打磨后被检工件的表面粗糙度Ra≤25μm。
如果被检工件表面残留有涂层,当涂层厚度均匀且不超过0.05mm,不影响检测结果时,经合同各方同意,可以带涂层进行磁粉检测。
此外,预处理还包括:涂敷(反差增强剂)、封堵、装配件的撤解等。
6. 2 磁化、施加磁粉或磁悬液磁化:选择磁化方法,确定磁化规范。
磁化时间为1S ~3S,停施磁悬液至少1S后方可停止磁化;1,为保证磁化效果,至少反复磁化2次(连续法)。
2,分段磁化时,必须注意相邻部位的探伤需有重叠。
3,对于单磁轭磁化和触头法磁化,均只能实现单方向磁化,在同一部位,必须作2次互相垂直的磁化探伤。
4,对于通电法包括触头法,注意烧伤问题。
5,对于交叉磁轭法,四个磁极端面与检测面之间应尽量贴合,最大间隙不应超过1.5MM。
连续拖动检测时,检测速度应尽量均匀,一般不应大于4M/MIN。
6球罐纵缝检测时,行走方向要自上而下,环焊缝向左向右都行。
7,对于线圈法,工件尽量放进线圈内进行磁化,线圈法的有效磁化区是从线圈端部向外延伸到150MM的范围内。
焊缝的探伤,可按照JB4730-2005中的附录B进行磁化。
8,施加磁粉或磁悬液:喷、洒、浇,就是不能刷;不能流得过快;必须先湿润。
6.2.1 连续法(一)概念:在磁化的同时,施加磁粉或磁悬液,同时观察(二)适用范围:①形状复杂的工件;②剩磁BR (或矫顽力HC)较低的工件;③检测灵敏度要求较高的工件;④表面覆盖层无法除掉(涂层厚度均匀不超过0.05MM)的工件。
(三)操作要点:①先用磁悬液润湿工件表面;②磁化过程中施加磁悬液,磁化时间1S-3S;③磁化停止前完成施加操作并形成磁痕,时间至少1S;④至少反复磁化两次。
(优缺点自己看)6.2.2剩磁法(一)概念:停止磁化后,施加磁粉或磁悬液。
(二)适用范围:①矫顽力Hc在1000A/m以上,并保持剩磁Br在0.8T以上的工件,一般如经过热处理的高碳钢和合金结构钢(淬火、回火、渗碳、渗氮、局部正火);低碳钢、处于退火状态或热变形后的钢材都不能采用剩磁法;②成批的中小型零件进行磁粉检测时;③因工件几何形状限制连续法难以检验的部位。
(三)操作要点:①磁化结束后施加磁悬液;②磁化后检验完成前,任何磁性物体不得接触被检工件;③磁化时间一般控制在0.25-1S;④浇磁悬液2–3遍,或浸入磁悬液中10—20S,保证充分润湿;⑤交流磁化时,必须配备断电相位控制器。
(优缺点自己看)6.2.3湿法(一)概念:将磁粉悬浮在载液中进行磁粉探伤。
(二)适用范围:①连续法和剩磁法;②灵敏度要求较高的工件,如特种设备的焊缝;③表面微小缺陷的检测。
(三)操作要点:①磁化前,确认整个检测表面被磁悬液润湿;②可用喷、浇、浸等方法施加;③检测面上的磁悬液的流速不能过快;④水悬液时,应进行水断试验。
(优缺点自己看)6.2.4干法(一)概念:以空气为载体用干磁粉进行探伤。
(二)适用范围:表面粗糙工件的局部检查及灵敏度要求不高的工件.(三)操作要点(1)工件表面要干净和干燥,磁粉也要干燥.(2)工件磁化时施加磁粉,并在观察和分析磁痕后再撤去磁场.(3)将磁粉吹成云雾状,轻轻飘落在被磁化工件表面上,形成薄而均匀的一层.(4)在磁化时用干燥的压缩空气吹去多余的磁粉,风压,风量和风口距离都要掌握适当,不要吹掉已形成的磁痕.(四)优缺点P.1056.3 磁痕观察、记录与缺陷评级1 磁痕观察非荧光磁粉检测时,磁痕的观察应在可见光下进行,通常工件被检表面可见光照度应大于等于1000lx;当现场采用便携式设备检测,由于条件所限无法满足时,可见光照度可以适当降低,但不得低于500lx。
荧光磁粉检测时,磁痕的在黑光灯下进行,工件表面的辐照度大于或等于1000μW/cm2,并应在暗室或暗处进行,暗室或暗处可见光照度应不大于20lx。
检测人员进入暗区,至少经过3min的黑暗适应后,才能进行荧光磁粉检测。
观察荧光磁粉检测显示时,检测人员不准戴对检测有影响的眼镜。
当辨认细小磁痕时,应用2倍~10倍放大镜进行观察。
2 缺陷磁痕显示记录磁痕的显示记录可采用照相、录相和可剥性塑料薄膜等方式记录,同时用草图标示。
3 缺陷评级按JB/T4730.4-20054 退磁4.1 概念:退磁是去除工件中剩磁、使工件材料磁畴重新恢复到磁化前那种杂乱无章状态的过程。
探伤退磁就是将剩磁减小到不影响使用或下道工序加工的操作4.2 原理:将工件置于磁场强度足以克服材料矫顽力H C的交变磁场中,产生磁滞回线,当交变磁场的幅值渐渐递减时,磁滞回线的轨迹也越来越小,工件中的剩磁Br也越来越小接近于零。
也就是换向衰减同时进行。
4.3 必须进行退磁的几种情况:①当检测需要多次磁化时,如上一次磁化将会给下一次磁化带来不良影响;②工件的剩磁会对以后的机械加工产生不良影响;③工件的剩磁会对测试或计量装置产生不良影响;④工件的剩磁会对焊接产生不良影响;⑤其他必要的场合。
4.4 退磁方法和设备常用的有交流退磁和直流退磁。
另外,还有高温退磁工件加热到居里点以上,这是一种最有效的退磁方法交流退磁:(一)通过法:①线圈不动工件移动,衰减磁场到零②工件不动线圈移动,衰减磁场到零。
(二)衰减电流(磁场)法:①线圈、工件都不动,衰减电流到零;②两电极夹持工件,衰减电流到零;③两触头接触工件,衰减电流到零;④交流电磁轭通电时离开工件,衰减磁场到零;⑤扁平线圈通电时离开工件,衰减磁场到零。
直流退磁:(一)换向衰减法:不断改变电流方向,并逐渐减小电流至零。
(二)超低频电流退磁:0.5-10Hz,衰减电流或在线圈中通过。
(三)剩磁测定:退磁效果可用磁场强度计测定,剩磁应不大于0.3mT(或240A/m)。
4.5 退磁注意事项自己看书P110页6.5 后处理和合格工件的标记6.5.1 后处理后处理:包括磁粉、磁悬液的清洗处理,水悬液如工件有防锈要求须做脱水防锈,如使用封堵应取除,反差增强剂应清洗掉,不合格工件应隔离。
6.5.2 合格工件的标记1 标记注意事项2 合格成品工件的标记打钢印刻印电化学腐蚀挂标签6.6 超标缺陷磁痕显示的处理和复验6.7 检测记录和检测报告原始记录的重要性,与工艺卡的关系,记录和报告的关系,记录和报告的格式。
1,使用干粉检测时,应使磁粉均匀地洒在试件表面上,然后再通适当的磁化电流(X) 2,周向磁化的零件退磁,一般应先使用一个比周向磁场强的纵向磁场进行磁化,然后沿纵向退磁. (O) 3,直流退磁主要是采用逐渐减小磁场或改变电流方向来实现(X) 4,工件磁粉检测后下一道工序是加热到600℃消除应力热处理,就可以不退磁(X) 5,一般表面粗糙的工件在磁化及施加磁粉或磁悬液的同时,完成磁痕观察记录及缺陷评定. (X) 6,工件退磁时所用磁场强度至少要等于或大于磁化时的最大磁场强度Hm,并退磁时间不宜过短,一般应大于50s. (X) 7,剩磁法中磁粉的施加是当试件被磁化且移去外磁场后进行的. (O) 8,干法比湿法更利于近表面缺陷的检出,采用荧光磁粉探伤时常用干法检测(X) 9,连续法可用于评价剩磁法检出的磁痕显示属于表面还是近表面缺陷显示(X) 10,交叉磁轭既可用于干法,又可用于湿法;既可用于连续法又可用于剩磁法(X) 11,连续法检测时,无论采用何种方法,工件表面的切向磁场强度应不下于2400A/m. (O) 12,对同一工件进行纵向磁化,使用高填充因素线圈所需的安匝数较少. (O) 13,对于应力腐蚀裂纹进行磁粉检测,一般应选择连续干法. (X) 14,退磁就是消除工件内的剩磁的工序. (O)7 磁痕分析与质量分级磁痕的显示分为相关显示、非相关显示和伪显示。
相关显示:磁粉检测时由缺陷(裂纹、未熔合、气孔、夹渣等)产生的漏磁场吸附磁粉形成的磁痕显示通常称之为相关显示。
一般也叫做缺陷显示。
非相关显示:由磁路截面突变以及材料磁导率差异等原因产生的漏磁场吸附磁粉形成的磁痕显示,称为非相关显示。
非相关显示产生的原因:①磁极和电极附近的漏磁场,鉴别方法:改变磁极极位置,不再出现;②工件截面突变,鉴别方法:根据工件的几何形状同一部位反复出现;③磁写,两个已磁化的工件相接触或已磁化的工件与铁磁性材料接触、碰撞致使此部位的磁场改变形成漏磁场;④工件磁导率不均匀,包括两种材料交界面(用PT验证);⑤磁化电流过大,金属流线显示出来;⑥局部冷作硬化;⑦金相组织不均匀(导致磁导率变化)。
伪显示:不是由漏磁场吸附磁粉形成的磁痕显示,也叫假显示。
伪显示产生的原因①工件表面粗糙,磁粉堆积;②表面油污等粘附磁粉;③氧化皮、锈蚀、油漆皮滞留磁粉;④浓度过大,施加方式不当造成背景过度;⑤工件上形成排液沟滞留磁粉。
伪显示的鉴别:擦除后重新检验不再出现。
7.4 相关显示1 原材料缺陷磁痕显示2 热加工产生的缺陷磁痕显示3 冷加工产生的缺陷磁痕显示4 使用后产生的缺陷磁痕显示5 电镀产生的缺陷磁痕显示6 常见缺陷磁痕显示比较缺陷磁痕缺陷磁痕大体可分为三类:①工艺性质缺陷的磁痕;②材料夹渣带来的发纹磁痕;③夹杂气孔带来的点状磁痕。
各种磁痕的特征是:①锻造折迭和锻裂:这类缺陷的磁痕有一些聚集较浓呈孤状或曲线状,呈现部位与工艺有关,多出现在尺寸突变处,易在过热部位或在预锻拔长过程中形成对折。
②淬火裂纹:磁痕形状浓度较高、线状棱角较多。
多发生在零件应力容易集中的部位(如孔、键、槽以及截面尺寸突变处);③磨削裂纹:一般呈网状或平行线状,有的还会出现龟裂磁痕;④焊接裂纹:磁痕多呈弯曲有鱼尾状,尤其焊道边缘的裂纹常因与其边缘下凹所聚集的磁粉相混,不易观察,需将凹面打磨平滑,后仍有磁粉堆积,可作缺陷判断;⑤铸造裂纹:磁痕在应力大的部位裂开,形状较宽;⑥疲劳裂纹:磁痕以疲劳源为起点向两侧发展一般呈曲线状;⑦白点:磁痕特征一般在圆的横断面一定距离等圆周部位分布,呈现无规律的较短线状;⑧发纹:材料夹渣在轧制过程中沿轴向形成的缺陷。