磁粉探伤技术与分析
铁路货车车轮磁粉探伤方法研究

铁路货车车轮磁粉探伤方法研究引言铁路货车在运输过程中承担着重要的物流任务,如货物运输、煤炭等资源开发运输、环境保护等。
货车的稳定性和运输效率直接关系到物流运输效率和安全性。
在铁路货车运行过程中,常常会遇到车轮的磨损和裂纹等问题,给货车的稳定性和行驶安全带来极大的隐患。
因此对铁路货车车轮进行磁粉探伤具有重要的意义。
本文主要研究铁路货车车轮磁粉探伤方法,探讨磁粉探伤方法的原理、技术要点、探伤效果等方面,为铁路货车运输安全提供技术支持。
一、磁粉探伤方法的原理磁粉检验方法是利用磁通量检测材料表面和材料内部缺陷的方法。
磁粉检验方法具体分为干式磁粉、湿式磁粉和涂于表面的磁粉。
对于铁路货车车轮磁粉探伤方法,一般采用干式磁粉探伤法。
该方法是通过直流磁场或交流磁场作用于被探测的工件上,将铁粉均匀地分散在铁路货车车轮表面,形成一层薄膜。
当磁场作用到含缺陷的部位时,因缺陷处磁通量的磁阻抗变化而出现磁漏现象,磁粉透过缺陷的表面被吸附在缺陷表面,形成黑色或紫色的磁粉痕迹,从而实现对缺陷的检测。
二、磁粉探伤技术要点1. 成分的选择干式磁粉检验的磁粉是一种易于吸附和检测的细颗粒磁性粉末。
磁粉检验使用的磁粉按颜色、成分、粒度等因素可分为多种。
一般情况下,使用矿物油、纤维素、金属碳酸盐等为基础的磁粉。
磁粉必须满足以下要求:(1)颗粒细小,不影响缺陷检测的精度。
(2)颜色明显,能够与被检测工件形成明显的对比度。
(3)具有磁性,能够在磁场作用下吸附在被检测工件表面的缺陷处。
2. 磁场的制造和检测对于铁路货车车轮磁粉探伤,需要采用合适的磁场强度和方向。
一般情况下,探伤使用的磁场强度在0.2-0.6T之间。
应该注意,磁场强度越大,可能会造成磁粉的“堆积效应”,导致不准确的检测结果。
对于磁场的检测,探测磁场强度应在磁致伸缩法应用时采用磁力计进行校准。
磁力计应具备较高的测量精度和分辨率。
磁力计应按照磁场大小、磁场方向不同的要求选择合适范围的探头,以便进行测量。
磁粉检测实验报告
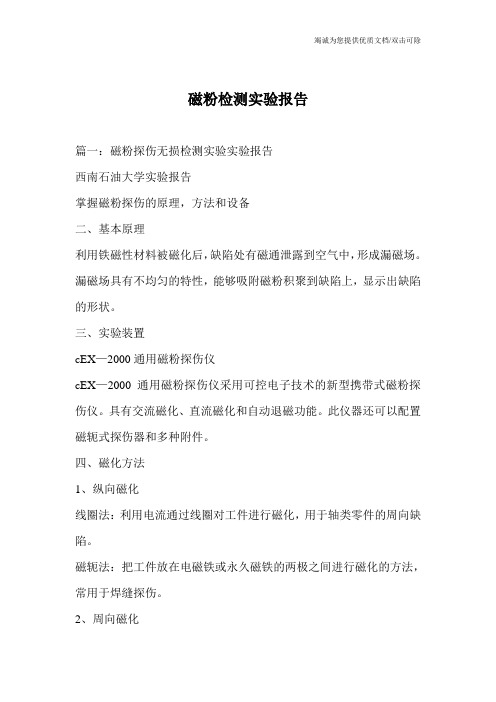
磁粉检测实验报告篇一:磁粉探伤无损检测实验实验报告西南石油大学实验报告掌握磁粉探伤的原理,方法和设备二、基本原理利用铁磁性材料被磁化后,缺陷处有磁通泄露到空气中,形成漏磁场。
漏磁场具有不均匀的特性,能够吸附磁粉积聚到缺陷上,显示出缺陷的形状。
三、实验装置cEX—2000通用磁粉探伤仪cEX—2000通用磁粉探伤仪采用可控电子技术的新型携带式磁粉探伤仪。
具有交流磁化、直流磁化和自动退磁功能。
此仪器还可以配置磁轭式探伤器和多种附件。
四、磁化方法1、纵向磁化线圈法:利用电流通过线圈对工件进行磁化,用于轴类零件的周向缺陷。
磁轭法:把工件放在电磁铁或永久磁铁的两极之间进行磁化的方法,常用于焊缝探伤。
2、周向磁化直接通电法:工件夹在探伤机的两极之间,使电流通过夹头直接流过工件,对工件进行磁化。
主要用于长型工件的探伤。
支杆法(触头法):电流通过支杆对工件局部进行磁化,用于大型工件的局部探伤。
中心导体法:从空心管中穿过导体,使导体直接通电。
用于空心工件的内表面探伤。
平行电缆法:用于角焊缝探伤。
五、通电方式连续法:工件在磁化时,同时施加磁悬液使缺陷显示。
剩磁法:利用工件磁化后的剩磁来检验其表面缺陷。
六、电流类型及选用交流电磁化法由于“集肤效应”,对于表面开口缺陷有较高的检测灵敏度且退磁方便。
对于近表面及埋藏缺陷,直流全波整流、半波整流磁化法有较高的检测灵敏度,但要有专门的退磁装置。
七、实验步骤本实验采用支杆法磁化将八角试块表面清理干净,清理出金属光泽,Ra将磁悬液摇匀,倒少许在八角试块上,抹匀;拍照记录;将电源插头插至仪器两边插座;开启电源,电源指示灯亮;选择磁化的电源和时间,调节电流大小旋钮,使电流值在450~800ma;将支杆刺入工件接触,使支杆间距150~200mm之间;按下磁化按钮;轻微移动支杆,再次磁化;等八角试块米字线清晰呈现是停止磁化;拍照记录八角块现象;关闭电源,清理实验现场;八、磁化效果磁化前磁化后八角块中间米字型材料为铜,其余部分为碳钢。
磁粉探伤检测报告docx(一)
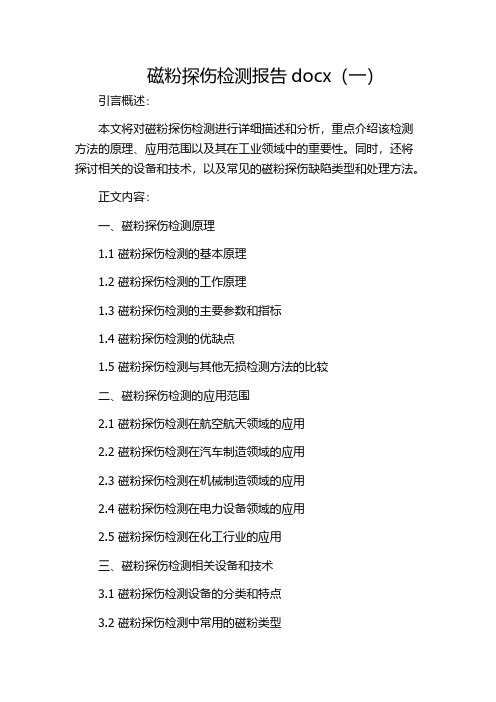
磁粉探伤检测报告docx(一)引言概述:本文将对磁粉探伤检测进行详细描述和分析,重点介绍该检测方法的原理、应用范围以及其在工业领域中的重要性。
同时,还将探讨相关的设备和技术,以及常见的磁粉探伤缺陷类型和处理方法。
正文内容:一、磁粉探伤检测原理1.1 磁粉探伤检测的基本原理1.2 磁粉探伤检测的工作原理1.3 磁粉探伤检测的主要参数和指标1.4 磁粉探伤检测的优缺点1.5 磁粉探伤检测与其他无损检测方法的比较二、磁粉探伤检测的应用范围2.1 磁粉探伤检测在航空航天领域的应用2.2 磁粉探伤检测在汽车制造领域的应用2.3 磁粉探伤检测在机械制造领域的应用2.4 磁粉探伤检测在电力设备领域的应用2.5 磁粉探伤检测在化工行业的应用三、磁粉探伤检测相关设备和技术3.1 磁粉探伤检测设备的分类和特点3.2 磁粉探伤检测中常用的磁粉类型3.3 磁粉混合方法及其调配原则3.4 磁粉铁磁材料的提纯方法3.5 磁粉探伤仪表的选型和使用四、磁粉探伤检测常见缺陷类型与处理方法4.1 表面缺陷和孔洞的检测与处理4.2 焊接缺陷的检测与处理4.3 裂纹和裂纹扩展的检测与处理4.4 金属疲劳损伤的检测与处理4.5 非金属材料缺陷的检测与处理五、磁粉探伤检测的发展和展望5.1 磁粉探伤检测技术的发展历程5.2 磁粉探伤检测的研究热点和趋势5.3 磁粉探伤检测的未来发展方向5.4 磁粉探伤检测关键技术的创新与应用5.5 磁粉探伤检测的市场前景总结:本文对磁粉探伤检测进行了全面而深入的介绍和分析。
通过了解磁粉探伤检测的原理、应用范围及相关设备和技术,我们认识到磁粉探伤检测在工业领域中的重要性和广泛应用。
同时,我们也了解到磁粉探伤检测在不同行业中的具体应用及其相关缺陷类型和处理方法。
未来,随着磁粉探伤检测技术的不断发展,相信它将在更多领域中发挥重要作用,在工业生产中起到更大的推动作用。
磁粉探伤技术分析与判断
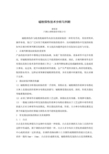
磁粉探伤技术分析与判断秦郁雯(马鞍山钢铁股份有限公司)磁粉探伤作为检查机械零件内部及表面缺陷的一种常用手段, 其原理简单, 操作容易, 现已广泛应用于机械零件缺陷的检查中。
而对磁粉探伤中发现的缺陷如何正确分析和判断比较困难。
本文就此问题理论结合实际加以总结与讨论。
1 正确判断裂纹缺陷的重要性产品的技术条件中都规定有验收标准, 如我厂使用的设备、设备零件不允许有裂纹, 即磁粉探伤的零件有裂纹而又不能消除时应报废。
因此, 正确判断零件是否有裂纹是执行技术条件的基础工作之一。
如果判断标准过宽或漏检缺陷,会造成重大事故; 反过来, 把不应报废的零件报废, 会产生严重经济损失。
两者均要避免, 做到恰如其分。
这样必须掌握好磁粉探伤原则, 并在实践中积累经验, 使认识臻于完善。
2 裂纹缺陷判断的依据(1) 磁粉图是分析裂纹缺陷的第一手资料, 其特征是: 磁粉图的形状和分布情况大体上是裂纹的形状和分布情况的描写; 磁粉图受裂纹宽度、深度、形状及裂纹导磁系数的影响。
(2) 必须了解零件在磁粉探伤前的工艺过程, 因裂纹是有来源、有规律可循的。
(3) 一般磁力探伤中所发现的裂纹形状和分布特征都取决于工艺过程中零件所受的最大正应力和零件内部情况, 所以裂纹的形成、形状、大小和分布情况都是这两个因素迭加的结果磁力探伤本身不能制造裂纹缺陷。
3 常见裂纹缺陷的特征及其规律性3.1 白点白点是在热轧和锻压合金钢中出现的一种缺陷。
白点是在钢热压力加工后的冷却过程中形成的, 属于钢的内部开裂的一种。
白点大多分布在大型轧材或锻件的近中心或离表面一定距离处, 在钢件的纵向断口上呈圆形或椭圆形的银白色斑点, 直径一般约5mm~ 10mm ; 白点往往成群出现, 磁粉探伤发现的白点是其横断面,即细小的裂纹, 裂纹边缘呈锯齿状; 白点分布大多和钢种的纤维方向平行, 有时呈辐射状, 锻件愈大愈容易产生白点。
白点对钢材的机械性能影响极大, 属于不允许缺陷。
钢材及焊缝探伤试验检测报告(磁粉探伤)
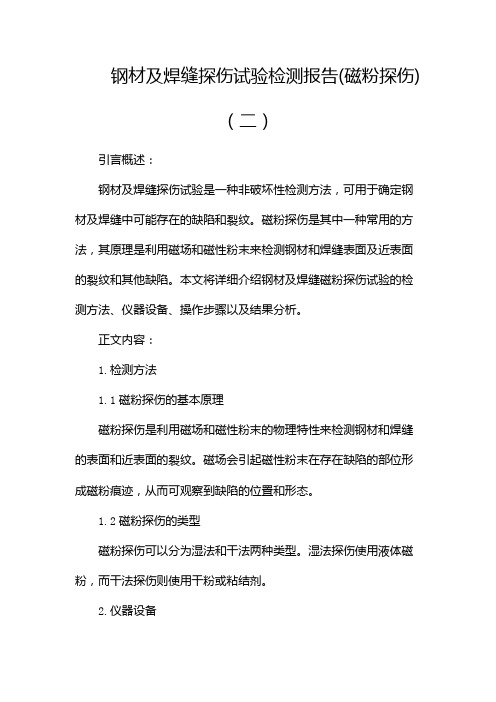
钢材及焊缝探伤试验检测报告(磁粉探伤)(二)引言概述:钢材及焊缝探伤试验是一种非破坏性检测方法,可用于确定钢材及焊缝中可能存在的缺陷和裂纹。
磁粉探伤是其中一种常用的方法,其原理是利用磁场和磁性粉末来检测钢材和焊缝表面及近表面的裂纹和其他缺陷。
本文将详细介绍钢材及焊缝磁粉探伤试验的检测方法、仪器设备、操作步骤以及结果分析。
正文内容:1.检测方法1.1磁粉探伤的基本原理磁粉探伤是利用磁场和磁性粉末的物理特性来检测钢材和焊缝的表面和近表面的裂纹。
磁场会引起磁性粉末在存在缺陷的部位形成磁粉痕迹,从而可观察到缺陷的位置和形态。
1.2磁粉探伤的类型磁粉探伤可以分为湿法和干法两种类型。
湿法探伤使用液体磁粉,而干法探伤则使用干粉或粘结剂。
2.仪器设备2.1磁粉探伤仪器磁粉探伤仪器由磁化设备、磁源和显示仪器组成。
常见的磁源有交流磁化法、直流磁化法和半自动磁化法。
2.2磁粉材料磁粉材料是进行磁粉探伤的重要组成部分。
常用的磁粉材料有干粉、液体磁粉和粘结剂。
3.操作步骤3.1准备工作在进行磁粉探伤前,需对钢材或焊缝进行清洁,确保表面没有灰尘、油脂或其他污染物。
3.2磁化根据具体要求选择合适的磁化方法,并对钢材或焊缝进行磁化处理。
3.3磁粉施加将磁粉材料均匀地施加在磁化后的钢材或焊缝表面,确保完全覆盖待检测区域。
3.4清除多余磁粉清除多余的磁粉,以免干扰后续的观察和分析工作。
4.结果分析4.1观察和记录磁粉痕迹在磁粉施加后,观察磁粉痕迹,记录其位置和形态,以确定钢材或焊缝中的缺陷。
4.2缺陷评估根据磁粉痕迹的形态和特点,对缺陷进行评估,确定其类型、大小和影响程度。
4.3结果判定将评估结果与相关标准或规范进行比对,判断钢材或焊缝的可用性和符合性。
5.总结钢材及焊缝探伤试验检测报告(磁粉探伤)旨在通过磁粉探伤方法来评估钢材和焊缝中存在的缺陷和裂纹,并根据结果进行判定和评估。
本文详细介绍了磁粉探伤的方法、仪器设备、操作步骤和结果分析,期望能为相关行业和领域的专业人士提供指导和参考。
磁粉探伤机的工作原理和检测方法
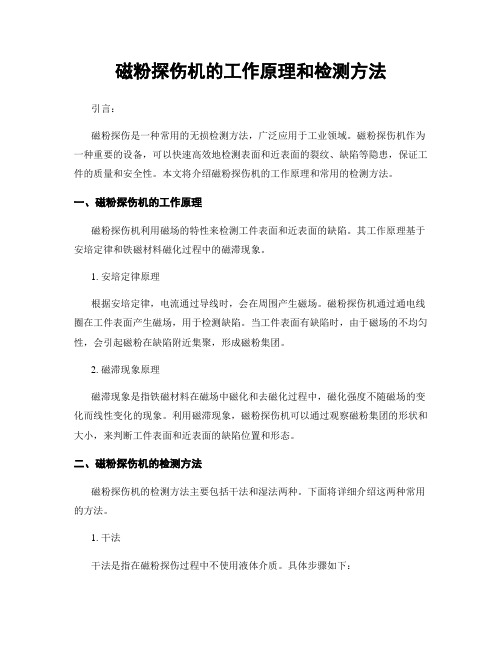
磁粉探伤机的工作原理和检测方法引言:磁粉探伤是一种常用的无损检测方法,广泛应用于工业领域。
磁粉探伤机作为一种重要的设备,可以快速高效地检测表面和近表面的裂纹、缺陷等隐患,保证工件的质量和安全性。
本文将介绍磁粉探伤机的工作原理和常用的检测方法。
一、磁粉探伤机的工作原理磁粉探伤机利用磁场的特性来检测工件表面和近表面的缺陷。
其工作原理基于安培定律和铁磁材料磁化过程中的磁滞现象。
1. 安培定律原理根据安培定律,电流通过导线时,会在周围产生磁场。
磁粉探伤机通过通电线圈在工件表面产生磁场,用于检测缺陷。
当工件表面有缺陷时,由于磁场的不均匀性,会引起磁粉在缺陷附近集聚,形成磁粉集团。
2. 磁滞现象原理磁滞现象是指铁磁材料在磁场中磁化和去磁化过程中,磁化强度不随磁场的变化而线性变化的现象。
利用磁滞现象,磁粉探伤机可以通过观察磁粉集团的形状和大小,来判断工件表面和近表面的缺陷位置和形态。
二、磁粉探伤机的检测方法磁粉探伤机的检测方法主要包括干法和湿法两种。
下面将详细介绍这两种常用的方法。
1. 干法干法是指在磁粉探伤过程中不使用液体介质。
具体步骤如下:(1)清洁工件表面,确保无杂质和油污。
(2)涂覆磁粉剂。
磁粉剂通过与工件磁场交互作用,形成磁粉集团,并沉积在缺陷表面。
(3)观察和评估磁粉集团。
使用特定的光源和磁粉观察仪对工件进行观察,根据磁粉集团的形状、大小和密度等特征,判断缺陷的位置和形态。
干法适用于对表面和近表面的缺陷进行检测,具有操作简单、成本较低等优势。
然而,干法对于微小和深埋缺陷的检测能力较弱。
2. 湿法湿法是指在磁粉探伤过程中使用液体介质。
具体步骤如下:(1)清洁工件表面,确保无杂质和油污。
(2)涂覆磁粉悬液。
磁粉悬液包含磁粉和水或油剂,通过浸渍到缺陷表面形成磁粉集团。
(3)观察和评估磁粉集团。
使用特定的光源和磁粉观察仪对工件进行观察,根据磁粉集团的形状、大小和密度等特征,判断缺陷的位置和形态。
湿法相对于干法,具有更高的检测灵敏度和检测深度。
焊缝磁粉探伤评定
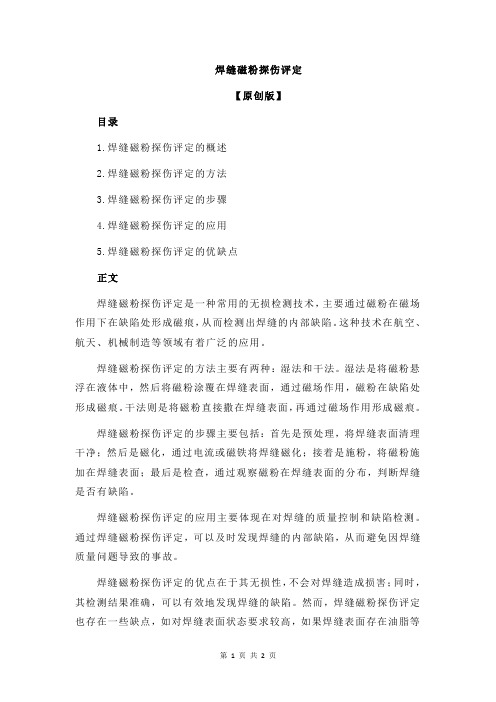
焊缝磁粉探伤评定
【原创版】
目录
1.焊缝磁粉探伤评定的概述
2.焊缝磁粉探伤评定的方法
3.焊缝磁粉探伤评定的步骤
4.焊缝磁粉探伤评定的应用
5.焊缝磁粉探伤评定的优缺点
正文
焊缝磁粉探伤评定是一种常用的无损检测技术,主要通过磁粉在磁场作用下在缺陷处形成磁痕,从而检测出焊缝的内部缺陷。
这种技术在航空、航天、机械制造等领域有着广泛的应用。
焊缝磁粉探伤评定的方法主要有两种:湿法和干法。
湿法是将磁粉悬浮在液体中,然后将磁粉涂覆在焊缝表面,通过磁场作用,磁粉在缺陷处形成磁痕。
干法则是将磁粉直接撒在焊缝表面,再通过磁场作用形成磁痕。
焊缝磁粉探伤评定的步骤主要包括:首先是预处理,将焊缝表面清理干净;然后是磁化,通过电流或磁铁将焊缝磁化;接着是施粉,将磁粉施加在焊缝表面;最后是检查,通过观察磁粉在焊缝表面的分布,判断焊缝是否有缺陷。
焊缝磁粉探伤评定的应用主要体现在对焊缝的质量控制和缺陷检测。
通过焊缝磁粉探伤评定,可以及时发现焊缝的内部缺陷,从而避免因焊缝质量问题导致的事故。
焊缝磁粉探伤评定的优点在于其无损性,不会对焊缝造成损害;同时,其检测结果准确,可以有效地发现焊缝的缺陷。
然而,焊缝磁粉探伤评定也存在一些缺点,如对焊缝表面状态要求较高,如果焊缝表面存在油脂等
物质,可能会影响检测结果。
磁粉探伤

磁粉探伤磁粉探伤利用工件缺陷处的漏磁场与磁粉的相互作用,它利用了钢铁制品表面和近表面缺陷(如裂纹,夹渣,发纹等)磁导率和钢铁磁导率的差异,磁化后这些材料不连续处的磁场将发生崎变,形成部分磁通泄漏处工件表面产生了漏磁场,从而吸引磁粉形成缺陷处的磁粉堆积--磁痕,在适当的光照条件下,显现出缺陷位置和形状,对这些磁粉的堆积加以观察和解释,就实现了磁粉探伤。
磁粉探伤,是通过磁粉在缺陷附近漏磁场中的堆积以检测铁磁性材料表面或近表面处缺陷的一种无损检测方法。
将钢铁等磁性材料制作的工件予以磁化,利用其缺陷部位的漏磁能吸附磁粉的特征,依磁粉分布显示被探测物件表面缺陷和近表面缺陷的探伤方法。
该探伤方法的特点是简便、显示直观。
磁粉探伤与利用霍耳元件、磁敏半导体元件的探伤法,利用磁带的录磁探伤法,利用线圈感应电动势探伤法同属磁力探伤方法。
主要分类磁粉探伤种类:1、按工件磁化方向的不同,可分为周向磁化法、纵向磁化法、复合磁化法和旋转磁化法。
2、按采用磁化电流的不同可分为:直流磁化法、半波直流磁化法、和交流磁化法。
3、按探伤所采用磁粉的配制不同,可分为干粉法和湿粉法。
4、按照工件上施加磁粉的时间不同,可分为连续法和剩磁法。
操作方法将待测物体置于强磁场中或通以大电流使之磁化,磁粉探伤若物体表面或表面附近有缺陷(裂纹、折叠、夹杂物等)存在,由于它们是非铁磁性的,对磁力线通过的阻力很大,磁力线在这些缺陷附近会产生漏磁。
当将导磁性良好的磁粉(通常为磁性氧化铁粉)施加在物体上时,缺陷附近的漏磁场就会吸住磁粉,堆集形成可见的磁粉痕迹,从而把缺陷显示出来。
第一步:预清洗所有材料和试件的表面应无油脂及其他可能影响磁粉正常分布、影响磁粉堆积物的密集度、特性以及清晰度的杂质。
第二步:缺陷的探伤磁粉探伤应以确保满意的测出任何方面的有害缺陷为准。
使磁力线在切实可行的范围内横穿过可能存在于试件内的任何缺陷。
第三步:探伤方法的选择1:湿法:磁悬液应采用软管浇淋或浸渍法施加于试件,使整个被检表面完全被覆盖,磁化电流应保持1/5~1/2秒,此后切断磁化电流,采用软管浇淋或浸渍法施加磁悬液。
- 1、下载文档前请自行甄别文档内容的完整性,平台不提供额外的编辑、内容补充、找答案等附加服务。
- 2、"仅部分预览"的文档,不可在线预览部分如存在完整性等问题,可反馈申请退款(可完整预览的文档不适用该条件!)。
- 3、如文档侵犯您的权益,请联系客服反馈,我们会尽快为您处理(人工客服工作时间:9:00-18:30)。
磁粉探伤技术分析与判断
秦郁雯
(马鞍山钢铁股份有限公司)
磁粉探伤作为检查机械零件内部及表面缺陷的一种常用手段, 其原理简单, 操作容易, 现已广泛应用于机械零件缺陷的检查中。
而对磁粉探伤中发现的缺陷如何正确分析和判断比较困难。
本文就此问题理论结合实际加以总结与讨论。
1 正确判断裂纹缺陷的重要性
产品的技术条件中都规定有验收标准, 如我厂使用的设备、设备零件不允许有裂纹, 即磁粉探伤的零件有裂纹而又不能消除时应报废。
因此, 正确判断零件是否有裂纹是执行技术条件的基础工作之一。
如果判断标准过宽或漏检缺陷,会造成重大事故; 反过来, 把不应报废的零件报废, 会产生严重经济损失。
两者均要避免, 做到恰如其分。
这样必须掌握好磁粉探伤原则, 并在实践中积累经验, 使认识臻于完善。
2 裂纹缺陷判断的依据
(1) 磁粉图是分析裂纹缺陷的第一手资料, 其特征是: 磁粉图的形状和分布情况大体上是裂纹的形状和分布情况的描写; 磁粉图受裂纹宽度、深度、形状及裂纹导磁系数的影响。
(2) 必须了解零件在磁粉探伤前的工艺过程, 因裂纹是有来源、有规律可循的。
(3) 一般磁力探伤中所发现的裂纹形状和分布特征都取决于工艺过程中零件所受的最大正应力和零件内部情况, 所以裂纹的形成、形状、大小和分布情况都是这两个因素迭加的结果磁力探伤本身不能制造裂纹缺陷。
3 常见裂纹缺陷的特征及其规律性
3.1 白点
白点是在热轧和锻压合金钢中出现的一种缺陷。
白点是在钢热压力加工后的冷却过程中形成的, 属于钢的内部开裂的一种。
白点大多分布在大型轧材或锻件的近中心或离表面一定距离处, 在钢件的纵向断口上呈圆形或椭圆形的银白色斑点, 直径一般约5mm~ 10mm ; 白点往往成群出现, 磁粉探伤发现的白点是其横断面,
即细小的裂纹, 裂纹边缘呈锯齿状; 白点分
布大多和钢种的纤维方向平行, 有时呈辐射状, 锻件愈大愈容易产生白点。
白点对钢材的机械性能影响极大, 属于不允许缺陷。
白点的磁粉图形呈幼虫状或断线状, 开裂中部粗大, 两端尖细。
白点的特点是形成了零件材料基体开裂, 因而积聚磁粉浓厚而紧密。
防止白点出现的措施是减少钢中的氢气, 即炼钢时将钢中的氢气含量减少至最少限度, 可通过选择干燥、纯净的炉料实现。
有条件的可采用真空熔炼和真空处理钢水, 或利用去氢退火减少钢锭中的氢含量。
3.2 淬火裂纹
钢中的冶金缺陷、压力加工中形成的裂纹或白点、晶粒粗大、精加工留下的尖角及刀痕以及热处理加热温度过高和冷却不当均会引起淬火裂纹。
淬火裂纹特点是粗大、呈投射状开裂, 一般中部肥大, 两头尖细而弯曲, 裂口四周无氧化颜色, 无脱碳现象。
淬火裂纹一般比较深, 积聚磁粉很急剧, 磁粉堆积很浓厚。
淬火中, 零件表面受拉应力, 中心受压应力, 此时一种情况是裂纹在零件的表面, 一般较深、较粗; 另一种情况是容易在零件的最大拉应力部位产生内裂, 并向中心部位发展。
若零件淬火时表面受拉应力, 中
心不受力, 此时形成网状或阶梯状裂纹, 裂纹的延伸方向和感应圈运动的方向垂直。
当零件形状复杂, 淬火裂纹经常发生在横截面急剧变化处, 如薄壁与厚壁相交处或有孔、槽、沟处。
总之, 必须分析零件在热处理中的应力分布状况和所发现的裂纹的形状、大小、分布情况, 然后加以比较, 做出结论。
3.3 铸造裂纹
铸造裂纹可分为热撕裂、热裂纹和冷裂纹三种。
3.3.1 热撕裂
热撕裂是在接近于金属和合金凝固点温度下形成的。
对钢和铸铁来说是金属或合金在生成珠光体前的收缩受到阻碍所造成的。
热撕裂主要是钢材的线收缩所致, 在各种钢材中, 铬镍钢的线收缩最大, 而锰钢、镍钢次之, 碳钢较小, 灰铸铁最小, 故铬镍钢热撕裂敏感性大, 锰钢和镍钢次之, 碳钢较小, 灰铸铁热撕裂已属罕见。
热撕裂的分布与铸件及铸模形状有关。
热撕裂的外形是短而粗, 大部分呈弯曲状, 中部肥大, 尾部尖细而弯曲。
3. 3.2 冷裂纹
冷裂纹是铸件在冷却过程中, 各部分冷却速度不同而致。
其形状狭窄而弯曲, 常发生在铸件壁厚变化较大的部位。
冷裂纹的发生与铸件形状和材料导热系数有关。
导热系数愈大, 冷裂倾向愈小, 如有色金属铸件因导热系数大很少发现冷裂现象, 而铸钢、高合金钢、高碳钢因导热系数小而具有较大的冷裂倾向。
3.3.3 热裂纹
热裂纹是指铸件热加工过程中形成的裂纹, 一般是由铸造缺陷在退火、正火、淬火过程中发展起来的, 主要是温差应力所致。
3.4 锻造裂纹
金属在锻造过程中发生流变, 因各部分受力不同, 变形程度不同, 锻造裂纹与锻件的内部缺陷关系极大。
如锻坯皮下有气泡时易形成锻造裂纹, 这种锻造裂纹常出现在锻件表面; 又如锻坯上存在缩孔或夹杂物时, 也容易造成锻造裂纹, 缩孔形成的裂纹一般较长, 出现在锻件的心部, 属于内裂, 而夹杂物或夹层形成的裂纹细长, 分布无规律。
3.5 磨削裂纹
当砂轮和工件接触面较大、砂轮过钝、进给量过大、工件表面散热性能差、循环冷却不当时, 将致使工件表面各部位磨削应力变化较大, 促使工件渗碳层的压应力状态受到严重破坏, 工件表面由压应力状态转化为拉应力状态, 当应力超过工件本身的强度极限时, 使零件表面产生裂纹。
它的特点是裂纹细窄、密而短小且浅, 而淬火裂纹则比较宽粗而且较深。
3.6 焊接裂纹
焊接是局部加热, 从冷态开始至加热熔化, 熔池温度可达2 000 ℃以上, 其周围又是冷态金属, 两者温差极大, 使工件产生大的内应力和变形, 严重者产生裂纹, 即焊接裂纹。
减少焊接裂纹的方法是焊前预热,
3.7 发纹
发纹是冶金缺陷(气孔、非金属夹杂物) 在变形焊后缓冷或焊后退火。
过程中发展而形成的。
发纹的发生与零件的形状有关, 直线状和圆柱状零件最容易产生发纹。
发纹的形状一般呈直线状, 沿金属流线分布。
大多数情况下, 发纹能用肉眼观察到。
由硫化物引起的发纹呈亮灰色, 由氧化物引起的发纹无色。
3.8 非金属夹杂物
对于一些杆状零件, 磁粉探伤中发现非金属夹杂物是经常的事。
非金属夹杂物的磁粉图与发纹类似, 一般呈直线状, 只有极个别的情况下呈稍微的弯曲形状。
非金属夹杂物沿金属的纤维方向分布, 尚未发现垂直于或与金属纤维方向呈某一角度的非金属夹杂物。
它积聚磁粉比较浅、淡, 它的尾部一般不大尖细, 这是与裂纹不同的。
非金属夹杂物没有破坏材料的连续性, 因而属于允许疵病。
4 分析裂纹缺陷的一般步骤
4.1 了解情况
首先了解磁粉图的形状和分布情况、零件加工工艺过程、零件材质及工作状态等。
4.2 进行分析
把发现的缺陷分成两类: ①裂纹主要指淬火、锻造、铸造、焊接裂纹, 某些重要零件还有磨削裂纹等缺陷, 属于不允许缺陷; ②发纹和非金属夹杂物为允许缺陷, 只是它们的允许程度不同, 必须视具体情况具体分析。
当发现不允许缺陷时, 需立即报告主管部门, 并会同有关单位作出报废决定。
4.3 复检或做补充试验
对以上工作发生怀疑时可以进行复检或做补充试验。
5 具有覆盖层零件的探伤
5.1 工件被磁性金属覆盖层覆盖
工件被磁性金属覆盖层覆盖时不宜于用磁粉探伤法探伤。
镀铁、镀镍、镀钴及其合金将使工件表面覆盖层具有高的导磁率, 被缺陷阻滞而弯曲了的磁力线将透过表面覆盖层, 而不易造成漏磁场, 致使工件表面层下缺陷不易检出。
5.2 工件被非磁性金属覆盖层覆盖
工件被非磁性金属层覆盖时仍可用磁粉探伤法探伤。
镀锌、镀锡、镀锑、镀铜等使工件表面覆盖层具有较小的导磁率,不会或很少影响表面缺陷造成的漏磁场, 不会影响缺陷的检出。
5. 3 工件被非金属覆盖层覆盖
工件被非金属覆盖层覆盖, 如磷化或氧化, 其导磁率也很小, 对磁粉探伤的效果不会有大的影响, 但对磷化或氧化来说, 因表面呈兰色和黑色, 不能再用黑色磁粉, 应改用白色或红色磁粉。
据资料介绍,表面覆盖了非金属覆盖层检查钢件表面的非金属夹杂物不再灵敏, 甚至检查不出来。
5.4 喷丸或喷砂
工件喷丸或喷砂后因不改变表面性质,只是使表面变形或改变表面的应力状态, 故不影响磁粉探伤, 探伤又往往在喷丸或喷砂之后进行。
为此,在进行磁粉探伤检测工作要结合工件的材质、加工状态和表面状况选择合适的磁化电流和磁化方法,结合合理的磁化规范才能更准确的做好磁粉检测工作。