工艺卡标准格式范例
现场作业工序工艺标准卡范本

3.高空坠落伤害 控制措施:先检查杆根、杆深、杆基和拉线等基础必须牢固可靠;必须认真检查登 高工具、 安全带、 后备绳。 脚扣登杆全过程系好安全带, 梯子登杆应先做冲击试验, 并采取防滑和限高措施, 派专人扶梯。 杆上工作人员工作前安全带和后备绳应挂在 牢固的构件上;杆上换位时不得失去安全保护。 4.高空落物伤害 控制措施:现场人员必须戴好安全帽;杆上工作人员不得浮置物品;工具、材料上 下应使用绳索传递或放入专用的工具袋。 杆塔下及作业点下方禁止有人逗留, 传递 人员应避开重物下方。 5.倒断杆伤害 控制措施:登杆前应先检查电杆根部、基础是否牢固,必要时对电杆培土加固或加 装临时拉线。 6.放线、紧线、撤线指挥不畅,工器具选用不当,安全措施不完善、操作方法不当 控制措施:应设专人指挥,统一信号,并保证信号畅通。 A. 所使用的工具设备强度应合格,应满足荷重要求。 B. 交叉跨越各种线路、铁路、公路,应先去的主管部门同意,做好安全措施,如 搭跨越架防止导线滑落,路口设专人持信号旗看守。 C. 严禁采用突然剪断导、地线的方法松线。 D. 紧放线前应先检查拉线、杆根、横担、导线接线管、导线接头、滑轮是否满足 紧、放线要求,工作人员不得跨在导线上或站在导线内角侧。 E. 当牵引绳索或导线卡住时,应立即停止牵引并松线不得直接用手处理,应在其 无张力情况下处理。 F. 线轴应放置牢固,放线速度要适度并有制动措施,设专人看守。 G. 用机械以旧线牵引新线时,必须处理好所有接头,保证能顺利通过滑车,无把 握的杆塔上不许有人,并用临时拉线加固。 H. 放线、撤线和紧线工作时,人员不得站在火跨在已受力的牵引绳、导线的内角 侧和展放的导、地线圈内以及牵引绳和架空线的垂直下方,防止意外跑线时抽 伤。 7.防车辆及非工作人员误入工作范围 控制措施:工作现场应该设置围栏并派专人监护,严禁非工作人员入内,设置“止 步,高压危险! ”标示牌,在公路两侧设置: “电力施工,车辆慢行! ”警示牌。 8.台架遗留物件 控制措施: 工作负责人组织工作人员对工作地点认真清理, 检查电杆及横担上是否 有遗留的电工器具等。 9 防作业人员误坠入河流 控制措施:在靠河边装设警示标志“止步,此处危险!”.
接箍加工工艺卡(范例)
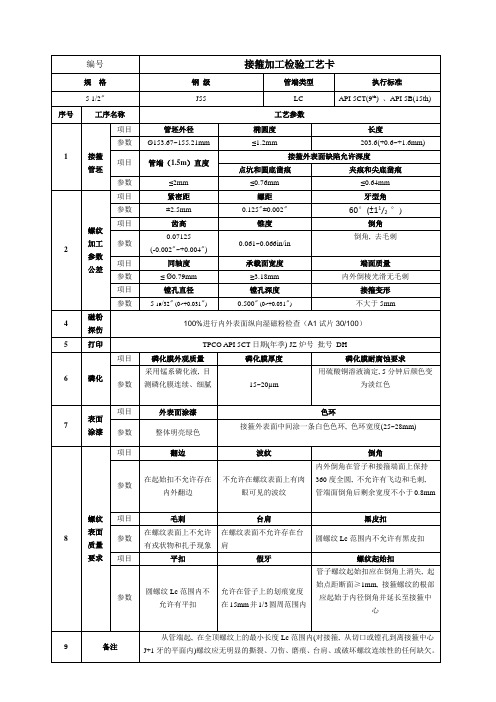
审核
日期
6
磷化
项目
磷化膜外观质量
磷化膜厚度
磷化膜耐腐蚀要求
参数
采用锰系磷化液,目测磷化膜连续、细腻
15~20µm
用硫酸铜溶液滴定, 5分钟后颜色变为淡红色
7
表面涂漆
项目
外表面涂漆
色环
参数
整体明亮绿色
接箍外表面中间涂一条白色色环,色环宽度(25~28mm)
8
螺纹表面质量要求
项目
翻边
波纹
倒角
参数
在起始扣不允许存在内外翻边
允许在管子上的划痕宽度在15mm并1/3圆周范围内
管子螺纹起始扣应在倒角上消失,起始点距断面≥1mm,接箍螺纹的根部应起始于内径倒角并延长至接箍中心
9
备注
从管端起,在全顶螺纹上的最小长度Lc范围内(对接箍,从切口或镗孔到离接箍中心J+1牙的平面内)螺纹应无明显的撕裂、刀伤、磨痕、台肩、或破坏螺纹连续性的任何缺欠。对偶然遇到的表面刮痕、轻微凹痕和表面不规则,如不影响螺纹连续性,可不必视为有害。
点坑和圆底凿痕
夹痕和尖底凿痕
参数
≤2mm
≤0.76mm
≤0.64mm
2
螺纹加工参数公差
项目
紧密距
螺距
牙型角
参数
±2.5mm
0.125"±0.002"
60°(±11/2°)
项目
齿高
锥度
倒角
参数
0.07125
(-0.002"~+0.004")
0.061~0.066in/in
倒角,去毛刺
项目
同轴度
承载面宽度
不允许在螺纹表面上有肉眼可见的波纹
生产工艺过程流转卡

1.外观
1.外观;
2.无损检测
□符合
□不符合
3.无损检测报告编号:。
□合格
□不合格
□E点
□R点
□W点
□H点
4
热处理
1热处理状态:;
2正火温度:℃;
3回火温度:℃;
4固溶温度:℃;
5保温时间:H;
6冷却方式:;
7硬 度:HB.
1.热处理状态:;
2.正火温度:℃;
3.回火温度:℃;
4.固溶温度:℃;
1.内径:mm;
2.外径:mm;
3.厚度:mm。
1.内径:mm;
2.外径:mm;
3.厚度:mm。
□合格
□不合格
□E点
□R点
□W点
□H点
4
粗车
粗车表面、前面、密封面,清除氧化皮、毛刺、毛边。按照图纸、工艺卡要求留加工余量。余量单面2mm。
1.表面、前面、密封面
。
2.余量单面mm。
1.表面、前面、密封。
生产工艺过程流转卡
订货单位
数 量
规格型号
材料批号
产品名称
锻件级别
材料牌号
生产批号
工艺过程记录
序号
工序
名称
技术要求
生产过程记录
自检记录
专检记录
检验结论
检验员
控制人员
控制点
1
下料
1.下料重量:kg;
2.将下好的料块放入待检区并标识材质、下料重量、材料批号、生产批号。
1.下料重量:kg;
2.标识:
①:材 质:
8.当始锻温度达到℃时,将毛坯放入砧面进行锻造。
9.当终锻温度达到℃时,停止锻造进行二次加热。
工 艺 卡

1、衣片反面朝上平放,与省尖平齐处开剪垫布,省尖下的两层垫布朝袖笼倒烫。省剖开点处化剪一刀口,省尖缝位朝前止口倒烫,余下胸省缝位分缝烫开,熨斗将其压烫煞,用力到位,省烫顺直,垫布修小,两层垫布修成阶梯形,两侧对称操作。2、袋口丝绺理直合并拢,吸风,居中放上无纺衬,留出侧缝缝位熨斗压烫牢固。
工艺卡
工艺卡
序号
工段
工序名称
、粘袋衬、袖笼纤条
技术质量要求
1、收胸省切线顺直,腰节下缝位0.4cm,腰节至省尖收尖。2、两胸省长短对称进出一致,条料对条格料对格,省尖不出现尖窝或省面松紧现象。3、垫布左右两侧对称,平服。4、拼小侧片缝位一致1cm,各刀口对准无偏差。5、袖笼至腋下10cm内,大身约有0.2cm吃量。6、针距14-15/3cm,切线顺松紧适宜,无跳针、断线现象。
技术质量要求
1、两胸省分缝压烫,缝位线丝绺顺直,省尖不出现尖窝或省面松紧现象。2、袋口合并无重叠无豁开,25g无纺衬粘合固定。
操作规程
1、衣片正面平放,按胸省剖开线翻折(袖笼)衣片,衣片反面朝上,根据剖开线两层衣片比齐,省尖垫入本色布,垫出省尖1cm,比剖开点下0.5-0.8cm左右。2、切线由省尖往下切,留线1cm于垫布上,按划线收省,省尖一定收尖,上下层面料受力一致。3、右片由袋位往上收胸省,其余对称操作。4、左片拼小片从袖笼往下缝制,小片居上袖笼圆顺比齐,大身略往上送量均匀吃进余下平缝到底。5、右片拼小侧片,由底摆往上缝制(底摆平齐),其余对称操作。
正式工艺卡与工序卡【范本模板】

產品名稱零件名稱座體共22 頁第 1 頁車間工序號工序名稱材料牌號金工10 銑HT150 毛坯種類毛坯外形尺寸每毛坯可制件數每臺件數鑄件90×65×85 1 1設備名稱設備型號設備編號同時加工件數立式銑床X52K 1夾具編號夾具名稱切削液專用銑夾具不加工位器具編號工位器具名稱工序工時(分) 准終單件3工步號工步內容工藝裝備主軸轉速切削速度進給量切削深度進給次數工步工時r/min m/min mm/r mm 機動輔助1 粗銑下底面至尺寸88mm 硬質合金面銑刀直徑d=80mm,齒數z=10375 70。
6 0。
8 2 1 13s 5s 設計(日期)校對(日期)審核(日期)標准化(日期)會簽(日期)標記處數更改文件號簽字日期標記處數更改文件號簽字日期產品名稱零件名稱座體共22 頁第 2 頁車間工序號工序名稱材料牌號金工20 銑HT150 毛坯種類毛坯外形尺寸每毛坯可制件數每臺件數鑄件90×65×85 1 1設備名稱設備型號設備編號同時加工件數立式銑床X52K 1夾具編號夾具名稱切削液專用銑夾具不加工位器具編號工位器具名稱工序工時(分) 准終單件3工步號工步內容工藝裝備主軸轉速切削速度進給量切削深度進給次數工步工時r/min m/min mm/r mm 機動輔助1 精銑下底面至尺寸87。
5mm 鑲齒三面刃銑刀47。
5 11。
98 1。
2 1。
0 1 4s 2s234設計(日期)校對(日期)審核(日期)標准化(日期) 會簽(日期)標記處數更改文件號簽字日期標記處數更改文件號簽字日期車間工序號工序名稱材料牌號金工30 鑽HT150毛坯種類毛坯外形尺寸每毛坯可制件數每臺件數鑄件90×65×85 1 1設備名稱設備型號設備編號同時加工件數立式鑽床Z525 1 夾具編號夾具名稱切削液專用鑽夾具不加工位器具編號工位器具名稱工序工時(分) 准終單件2工步號工步內容工藝裝備主軸轉速切削速度進給量切削深度進給次數工步工時r/min m/min mm/r mm 機動輔助1 鑽底面對角2ר9mm通孔直柄麻花鑽680 14.5 0.22 3。
工艺卡片模板100例
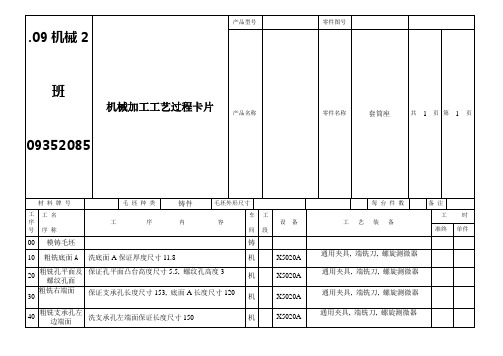
单件
设计(日期)
校对(日期)
审核(日期)
标准化(日期)
会签(日期)
标记
处数
更改文件号
签字
日期
标记
处数
更改文件号
签字
日期
机械加工工艺过程卡片
产品型号
零件图号
产品名称
零件名称
套筒座
共
1
页
第
1
页
材料牌号
毛坯种类
铸件
毛坯外形尺寸
每台件数
备注
工
序
号
工名
序称
工序内容
车
间
工
段
设备
工艺装备
工时
准终
单件
00
模铸毛坯
铸
10
粗铣底面A
洗底面A保证厚度尺寸11.8
机
X5020A
通用夹具,端铣刀,螺旋测微器
20
粗铣孔平面及螺纹孔面
保证孔平面凸台高度尺寸5.5,螺纹孔高度3
通用夹具,螺纹刀,扩孔钻,千分尺
130
检验入库
设计(日期)
校对(日期)
审核(日期)
标准化(日期)
会签(日期)
刘涛
标记
处数
更改文件号
签字
日期
标记
处数
更改文件号
签字
日期
机械加工工艺过程卡片
产品型号
零件图号
产品名称
零件名称
共
页
第
页
材料牌号
毛坯种类
毛坯外形尺寸
每毛坯件数
每台件数
备注
工
序
号
工名
序称
工序内容
车
生产工艺卡(3篇)
第1篇一、产品名称:XX产品二、产品规格:XX型号三、生产批量:XX批次四、生产日期:XXXX年XX月XX日五、生产部门:XX车间六、生产人员:XX七、工艺流程:1. 原材料准备2. 模具准备3. 注塑成型4. 产品检验5. 产品装配6. 产品包装八、原材料要求:1. 原材料名称:XX材料2. 原材料规格:XX型号3. 原材料性能:具有良好的强度、韧性、耐磨性、耐腐蚀性等4. 原材料质量要求:符合国家标准或企业标准九、模具准备:1. 模具名称:XX模具2. 模具规格:XX型号3. 模具材料:不锈钢、铝合金等4. 模具质量要求:无砂眼、裂纹、变形等缺陷十、注塑成型:1. 注塑机型号:XX型号2. 注塑温度:XX℃3. 注塑压力:XXMPa4. 注塑时间:XX秒5. 注塑速度:XXmm/s6. 注塑注意事项:a. 模具预热至设定温度b. 严格按照工艺参数进行注塑c. 注意注塑过程中的压力、温度、时间等参数的调整d. 注塑完成后,待产品冷却至室温十一、产品检验:1. 检验项目:外观、尺寸、性能等2. 检验标准:符合国家标准或企业标准3. 检验方法:a. 外观检验:目测、触摸、量具测量等b. 尺寸检验:卡尺、千分尺等c. 性能检验:拉伸试验机、冲击试验机等十二、产品装配:1. 装配件名称:XX部件2. 装配件规格:XX型号3. 装配顺序:先装配内部零件,再装配外部零件4. 装配方法:手工装配、机械装配等5. 装配注意事项:a. 严格按照装配图纸进行装配b. 注意装配过程中的对位、紧固等操作c. 避免装配过程中产生划痕、变形等缺陷十三、产品包装:1. 包装材料:纸箱、气泡袋、胶带等2. 包装规格:XX型号3. 包装方法:将产品放入纸箱,用气泡袋填充,封箱,贴上标签4. 包装注意事项:a. 包装过程中注意轻拿轻放,避免产品损坏b. 标签信息准确,包括产品名称、规格、生产日期、批次等c. 包装牢固,确保产品在运输过程中不受损坏十四、生产过程中应注意的问题:1. 原材料质量:确保原材料符合要求,避免因原材料质量导致产品不合格2. 模具质量:定期检查模具,发现异常及时处理3. 注塑成型:严格按照工艺参数进行注塑,避免产品出现变形、气泡等缺陷4. 产品检验:严格进行产品检验,确保产品合格率5. 产品装配:注意装配过程中的对位、紧固等操作,避免产品出现装配缺陷6. 产品包装:确保包装牢固,防止产品在运输过程中损坏十五、生产过程中异常处理:1. 原材料异常:发现原材料质量问题时,及时与供应商沟通,确保原材料质量2. 模具异常:发现模具异常时,立即停止生产,修复或更换模具3. 注塑成型异常:发现产品出现变形、气泡等缺陷时,调整注塑参数,重新注塑4. 产品检验异常:发现产品不合格时,及时通知相关部门,查找原因,进行处理5. 产品装配异常:发现装配过程中出现缺陷时,及时修正,确保产品合格6. 产品包装异常:发现包装过程中出现问题时,及时调整包装方法,确保产品安全运输本生产工艺卡适用于XX产品生产过程中的各个环节,各部门应严格按照本工艺卡执行,确保产品质量。
超声检测工艺卡(标准版)
编制人(资格): 年 月 日
审核人(资格): 年 月 日
器
材
及
参
数
仪器型号
检 测 方 法
□纵波检测 □横波检测
探头型号
评定灵敏度
dB
试块型号
扫 查 方 式
耦合剂
□水 □机油 □甘油 □工业浆糊
表 面 补 偿
dB扫描调节检 测源自面□单面双侧 □双面单侧□双面双侧 □
扫查速度
mm/s
覆 盖 面 积
%
技术要求
检 测 标 准
检 测 比 例
%
合 格 级 别
级
检测工艺编号
超 声 检 测 工 艺 卡
产 品 名 称
产品(制造)编号
工
件
部 件 名 称
板 厚
mm
部 件 编 号
规 格
mm
检 测 项 目
□焊缝 □板材 □锻件 □
材 料 牌 号
检 测 阶 段
□焊后 □返修后 □机加工后 □轧制后 □热处理后 □
表 面 状 态
焊 接 方 法
□手工焊□自动焊□氩弧焊
检 测 区 域
坡 口 型 式
现场作业工序工艺标准卡模版
现场作业工序工艺标准卡编号:项目名称:作业班组:编制:日期:年月日审核:日期:年月日批准:日期:年月日计划作业时间:年月日时分—时分实际作业时间:年月日时分—时分现场勘察单勘察类别新建□大修√消缺□改造其它□项目名称与现场作业工序工艺标准卡的项目名称相同勘察人员向方林、袁思云勘察日期当日到场的日期勘察地点10KV双方线61路N11号杆至N12号杆电压等级10kV现场勘察内容停电范围:10KV双方线61路N1号杆至N13号杆保留或邻近的带电线路、设备:10KV双方线61路N13号杆双方线石板上D0102刀闸下桩头及后段线路和设备带电交叉跨越情况跨越:跨10KV毛达自闭线133号至134号;27.5KV襄渝铁路宣汉-石柱槽区间上行线接触网103号至104号;27.5KV襄渝铁路宣汉-石柱槽区间下行线接触网127号至128号。
穿越:“无”作业现场的条件、环境:1、本次作业为高空作业等;2、该地段作业条件良好。
1、现场作业必须有人监护;2、工作班成员必须穿统一工作服、工作鞋;3、施工时,除工作班成员外,其他人一律站在施工安全范围外;4、工作人员杆上所用的材料及工具应由绳索传递,不得上下抛掷;5、工作期间应实行监护制,即工作人员必须要有监护人,一人工作一人监护;6、在杆上工作,必须正确使用合格的安全带和安全帽。
安全带应系在电杆或牢固的构件上,应防止安全带从杆顶脱出或被锋利物伤害。
系好安全带后必须检查扣环是否扣牢;7、早上必须进餐,严禁空腹上班。
8、在拆除导线前,必须做好临时拉线和严谨突然剪短剪断导线。
9、本次作业有配合停电作业,请作好配合联系工作。
附图:图附后勘察人员签字所有到场人员填写说明:1、“编号”:按供电所名称—年—月—日—序号编写,与编写日期一致,如石梯供电所2009年12月25日施工的第一张工序工艺卡,编号为:石梯供电所2009-12-25-012、“项目名称”:按照电压等级、线路名称、工作内容。
工艺卡片样本(DOC 28页)
工艺卡片样本(DOC 28页)工艺规范产品名称工序名称设备名称编号共 16 页 AH/TLC70-01 框扇下料工装名称编号第 1 页工序简图技术标准1、下料长度L充差≤2000mm±1mm2、下料角度90°±0.5°3、切割后型材断面应平整光洁,外表面清洁无划伤。
操作要求1、切割前检查设备运转是否正常。
2、装夹注意夹紧力适当,牢固,定位正确,切割过程中防止型材变形。
3、型材搬取,存放过程中防止型材划伤,磕碰,表面质量。
4、首件产品严格检查合格后方可生产。
检验方法1、用钢卷尺检查下料长检测工具1.钢卷尺。
2.角度尺。
不合格品处置度。
2、用角度尺检查下料角度。
3、目测外观质量。
更改记录编制批准日期批准审核日期工艺规范产品名称工序名称设备名称编号共 16 页 AH/TLC70-01 铣排水孔工装名称编号第 2 页工序简图技术标准1、排水孔为Φ5×30槽孔,每根料数量2个。
2、纵向位置允差别±3mm,排列均匀。
3、排水孔表面光洁,无毛刺、铣刀不得损坏型材腹板4、排水孔设在外轨道左侧。
操作要求1、铣料前检查设备运转是否正常。
2、注意排水孔的位置均匀和数量。
3、铣孔时避免划伤型材表面质量。
4、首件产品严格检查,合格后方可生产。
检验方法1、用卡尺测量排水孔尺检测工具1、卡尺。
2、卷尺。
不合格品处置寸。
2、用卷尺测量排水孔位置。
更改记录编制批准日期批准审核日期工艺规范产品名称工序名称设备名称编号共 16 页 AH/TLC70-01 铣边框料工装名称编号第 3 页工序简图技术标准1、边框上方仿型铣深度距离为40mm。
2、边框下方仿型铣深度距离为50mm。
3、仿型铣后,光滑无毛刺,深度距离偏差L±1mm。
4、边框左右铣切距离为68mm,距离偏差L±0.5mm。
操作要求1、工作前检查仿型铣床运转是否正常。
2、检查铣刀型号是否正确。
3、工作时型材轻取轻放,避免划伤型材表面质量。