特采处理办法
特采管理程序
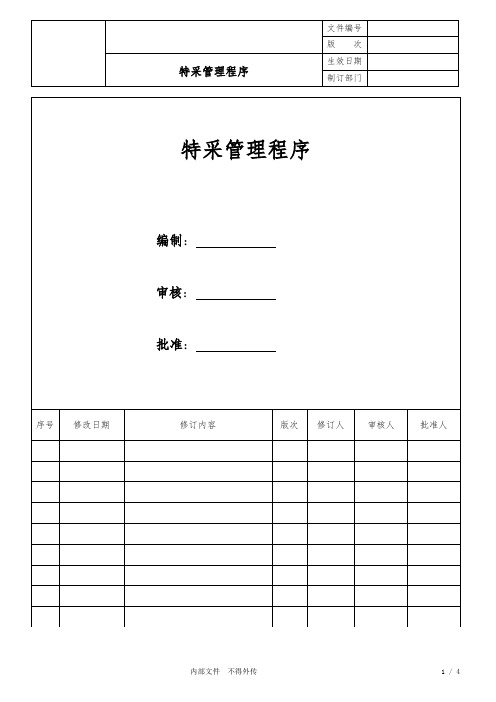
5.4 特采的纠正与预防
5.4.1特采必须规定一定的数量或时间期限,超出规定的数量或时间期限仍有同样的缺陷时,判定不合格而拒绝接受。来料数量或者成品出货数量,必须少于或等于特采审批的数量,特殊情况下,可以追加特采数量或时间期限。
5.2.2.1进料检查判定不合格时,按不合格物料处理。但供应商在收到《品质异常单》后,可向本公司提出特采申请,申请渠道根据5.1.1项的规定。
5.2.2.2对于特采允收之原物料,由IQC贴上“特采”标签,加以标识区分入库使用;如判定不可特采即作退货处理。
5.2.3外购物料、外发加工品在使用过程中发现不合格时:
4.2.3根据客户要求,负责向客户品质部提出特采申请,并将客户最终承认结果传达至相关部门。
4.3 PMC
负责特采对象品的生产安排及出货管理。
4.4 生产部
4.4.1负责对本单位不合格的半成品、成品特采申请的提出,并送各相关单位会签、审核;
4.4.2负责本单位被批准的特采申请单的配布。
4.4.3负责对本单位不合格的原因调查,制订并执行再发防止的根本对策。
5.4.2供应商及本公司内部需针对特采申请的内容采取纠正和预防措施,避免再次发生同样的不合格内容。
责任部门
流程图
输出相关文件/记录
关联部门
《特采申请单》
关联部门
品质部
管理层
《特采申请单》
品质部
“特采”标识
PMC、仓库
品质部
《特采申请单》
7.参考文件
《不合格管理程序》8.记录
外购物料、外发加工品在使用过程中发现不合格时,品质部需对不合格内容进行确认,若该缺陷对产品的装配及产品功能、外观等品质特性的影响很小,且能够满足产品的要求时,可以判定特采,但仍需向供应商发行《品质异常单》要求其改善。
特采管理办法

4.1生产部门:负责不合格产品(含退货产品、库存品)的特采申请。
4.2品管部:负责不合格原辅材料、产品的标示。
4.3各部门主管、各级领导:负责不合格品的特采评的特采处理:
5.1.2品管部依《进料检验控制程序》文件要求经检验判定属原/辅材料不合格且经会审后需进行特采处理时,则由采购部门填写『特采申请单』提出特采申请,报采购分管领导审核及总经理(或受权人)批准后,将『特采申请单』转交品管部后。品管部即可放行原/辅材料入库、投入使用。
5.2.6若属晚班时,发生不合格产品且属需紧急出货时,则由生产部门科长填写『特采申请单』经晚班品管科长、晚班生产部门带班科长签字后交晚班品管科长安排紧急放行不合格产品。其『特采申请单』由次日日班再进行各有关部门人员会签处理。
5.2.7以下情况均需提出特采处理
(1)因产品紧急出货,但属不合格产品时。
(3)经相关部门(计划科/经营部)与顾客协商后,且客户同意允收的不合格产品。
特采管理办法
1.0目的:
1.1为了当各种物料(含原/辅材料、半成品、成品)在使用时、制程中、出货前发生/存在质量问
题时,且不影响产品功能或特性条件下而特别采用或紧急放行的管理,特此制定此文件。
2.0适用范围:
2.1适用于本公司进料、生产过程、成品出货时对不合格品进行特采处理的管控。
3.0定义:
3.1特采:是指因生产急需或顾客交期考虑,经相关单位或权责人员评审判定所不影响产品功能的不合格品,而特别放行、采用。
(4)经营部人员确认可出货的不合格产品。
(5)经返工返修后的产品(含退货产品)数量在50PCS(含)以上的不合格产品(客户责任除外)。
5.2不合格产品的特采处理:
5.2.1经品管人员判定属不合格产品,且生产部门科长据实际情况提出特采处理的要求时,则由生产部门科长填写『特采申请单』交品管部主管签字。
特采处理办法

5.4品技接到特采申请单时,应立即分析、调查不合格原因及是否符合特采条件并提出对策。
5.5特采未被核准时,进料以退货处理.
5.6特采被核准范围仅对该批申请数量有效.
4.职责
4.1采购负责对物料提出特采申请.
4.2品技负责研究及指出对策并指定部门处理。
4.3品管部负责稽查特采事宜.
4.4品管部门经(副)理负责特采意见不统一之协调,总经理负责最终裁决.
5.管理程序
5.1经实物质量考查验证后,其成品的功能符合要求,并符合以下条件可申请特采:
5.1.1检验内容不符合但属厂内生产急需时
5.1.2物料检验不符合厂内规格但符合顾客要求时.
5.1.3物料检验不符合规格但顾客急需时.
核准
会签
拟案
特采处理办法
文件编号
版次
1.0
机密等级
一般
页次
2/2
5.1.3物料检验不符合规格但顾客急需时.
5.1.4虽不属急需品但无其它补救措施,将使公司遭到重大损失时.
5.2申请单位采购之物料经检验不合格须特采处理时,由采购部门提出申请.
指导文件
文件编号
版次
1.0
机密等级
页次
1/2
特采管理办法
制定日期
2004
年
07
月
15
日
实施日期
2004日
1.目的
为确保进料等品质异常处理有明确标准和依据,特制定本特采处理办法。
2.适用范围
2.1生产用各种物料虽经检验判定为不合格但生产急需符合特采条件均属之
特采处理作业程序
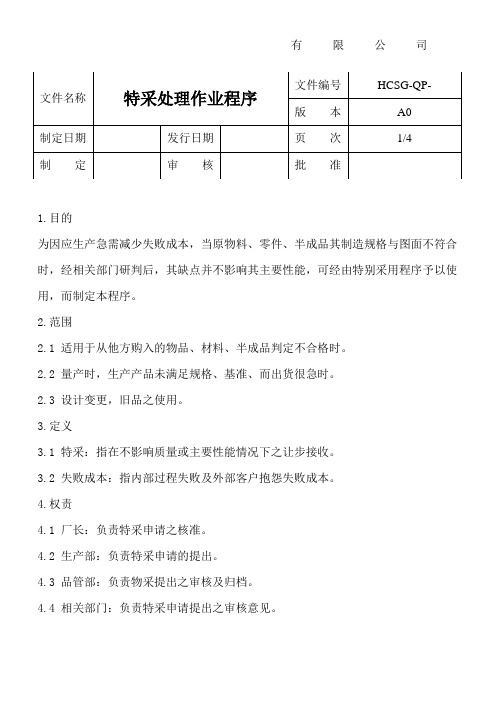
有限公司1.目的为因应生产急需减少失败成本,当原物料、零件、半成品其制造规格与图面不符合时,经相关部门研判后,其缺点并不影响其主要性能,可经由特别采用程序予以使用,而制定本程序。
2.范围2.1 适用于从他方购入的物品、材料、半成品判定不合格时。
2.2 量产时,生产产品未满足规格、基准、而出货很急时。
2.3 设计变更,旧品之使用。
3.定义3.1 特采:指在不影响质量或主要性能情况下之让步接收。
3.2 失败成本:指内部过程失败及外部客户抱怨失败成本。
4.权责4.1 厂长:负责特采申请之核准。
4.2 生产部:负责特采申请的提出。
4.3 品管部:负责物采提出之审核及归档。
4.4 相关部门:负责特采申请提出之审核意见。
使用表单特采申请单质量异常联络单5.内容 5.1 流程图:流 程5.2 特采申请5.2.1 由生产部提出申请,并填写“特采申请单”(FM-8-09-01)详记特采理由。
5.2.2 申请特采须填入下列资料,申请日期、品名、批号、厂商、数量、缺点状况、申请理由等。
权责单位生产部 相关部门 厂长 品管部 相关文件资料检验与测试状态识别程序质量记录管制程序5.2.3 特采申请条件A.可能造成下一道工序停工待料而无法达成生产进度时。
B.原特料进厂经进料品管判定不合格,但急需上线生产时。
C.因图面尺寸规格或检查基准过于严格,虽不合格亦可使用时。
D.对于一般性通讯商品价值影响轻微时。
5.2.4以下情况不可特采A.对于安全及重要功能有影响者。
B.有售后客户抱怨之顾虑者。
C.同一状况多次发生者。
5.3特采审核及批准5.3.1 特采审核成员:由品管部及相关部门组成。
5.3.2 特采申请提出后,由特采审核成员共同会审依其职责所在,填入“特采申请单”相关意见栏并签名之后,并由厂长核准实施。
5.3.3 特采完成审核、核准后,正本存档于品管部,依需要将影印副本分发至要关部门参考。
5.3.4特采限用于其某些不合格特性在指定偏差内,并限于一这期限或数量产品的交付。
特采管理办法

拟定审核批准文件名称特采管理办法文件编号页次1/4版本A/0生效日期2015-11-28文件变更履历版次页次修订人变更内容简述修订日期A/04新版拟定2015-11-28版本文件名称特采管理办法页次A/0 2/41.目的为确保进料等品质异常处理有明确标准和依据,规范对不合格品采取的让步放行,在不影响客户最终需求的前提下,确保生产计划的顺利完成。
2.范围本办法适用于生产用原材料、供应商来料和委外加工产品品质异常处理。
3.权责3.1 IQC :负责原材料及委外加工产品质量检验,并出具《来料检验报告》;3.2采购部:负责与供方商议物料品质异常处理相关事项;3.3生产部:负责物料品质异常产生废次品数据的收集;3.4品质部:负责物料品质异常MRB提出;3.5 PMC 部:生产计划的调整;3.6财务部:负责物料品质异常产生的各类经济损失的扣款执行;4.定义特采 : 是指产品经检验不合格, 但经品质部确认不影响最终使用性能, 可作为让步接收的特别采用。
5.内容5.1 检验要求:5.1.1凡采购的生产原材料(含委外加工产品)必须检验合格后方可办理入仓和使用手续。
5.1.2 IQC必须严格按《物料检验标准》或样板、承认书、图纸执行规定的项目,按抽样办法、检验方法、对原材料(含委外加工产品)进行检验,并形成完整的检验记录,不得漏检或擅自减少抽样数量。
5.2物料品质异常处理:异常处理情形:退货、特采(分选、加工、让步、降级)等;5.3物料退货处理细则:5.3.1符合下列条件的物料,可按退货处理;1)物料存在严重质量缺陷,直接影响产品外观效果或重要指标达不到客人要求的。
2)特采成本高、特采后执行操作难度大或特采仍有客户投诉风险或客户退货风险的。
3)反馈异常问题后,48 小时内供应商没有提供有效处理方案的。
4)供应商需要我司特采使用,但无相关风险承诺,及无法承担特采费用和风险的。
5)经过业务与客户沟通无法接受的质量缺陷,则按退货处理。
特采作业管理程序
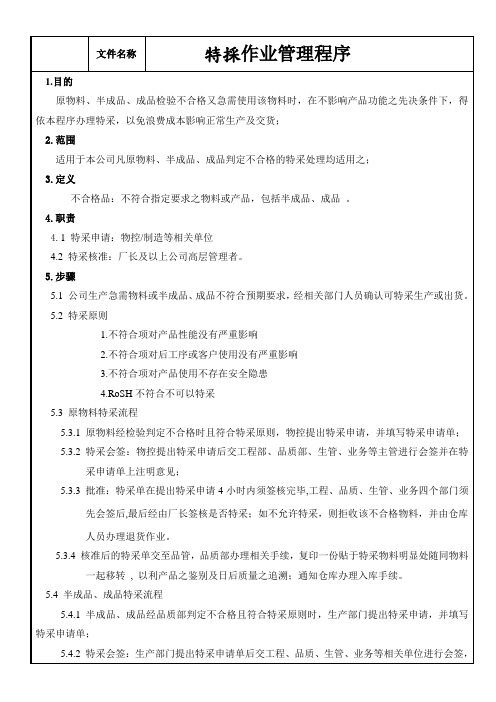
5.步骤
5.1公司生产急需物料或半成品、成品不符合预期要求,经相关部门人员确认可特采生产或出货。
5.2特采原则
1.不符合项对产品性能没有严重影响
2.不符合项对后工序或客户使用没有严重影响
3.不符合项对产品使用不存在安全隐患
4.RoSH不符合不可以特采
格品管制程序》
7.相关表单
7.1【特采申请单】
7.2【退料单】
5.3.1原物料经检验判定不合格时且符合特采原则,物控提出特采申请,并填写特采申请单;
5.3.2特采会签:物控提出特采申请后交工程部、品质部、生管、业务等主管进行会签并在特采申请单上注明意见;
5.3.3批准:特采单在提出特采申请4小时内须签核完毕,工程、品质、生管、业务四个部门须先会签后,最后经由厂长签核是否特采;如不允许特采,则拒收该不合格物料,并由仓库人员办理退货作业。
5.3.4核准后的特采单交至品管,品质部办理相关手续,复印一份贴于特采物料明显处随同物料一起移转,以利产品之鉴别及日后质量之追溯;通知仓库办理入库手续。
5.4半成品、成品特采流程
5.4.1半成品、成品经品质部判定不合格且符合特采原则时,生产部门提出特采申请,并填写特采申请单;
5.4.2特采会签:生产部门提出特采申请单后交工程、品质、生管、业务等相关单位进行会签,并在申请单上注明意见;
5.4.3批准:特采单在提出特采申请4小时内须签核完毕,工程、品质、生管、业务四个部门须先会签后,厂长签核是否特采;如不允许特采,则由生产安排对产品返工处理,对不能返工的不良则申请报废。
5.4.4批准后的《特采申请单》交品质部进行相关处理(相关检查记录注明特采,并记下《特采申请单》编号,不合格相关通知处置栏注明特采);品质部取消对象产品不合格标识(半成品作特采标识,成品作合格标识)特采允收之半成品、成品、应由品质部予以记录,以利日后品质追溯;
MRB特采作业管理办法

MRB特采作业管理办法1.0 目的1.1建立不良品信息沟通及处理平台,及时处理不良品,加强品质管控;1.2快速合理的进行品质缺陷判定,明确品质责任承担;2.0范围2.1 本文件适用于生产急用但与品质标准存在差异,需承担客诉风险之物料,且制造加工单位(含供应商)自身无法处理的物料管理,包括下述内容:2.1.1进料类【外协加工/采购物料经检验判退物料】;2.1.2制程在途类【制程加工在途物料/半成品及配件经检验判退物料】;2.1.3仓储类【仓储半成品及配件等物料经检验判退物料】;3.0 权责3.1 MRB小组组长:判定不合格物料处理结果以及责任承担单位;3.2 MRB小组成员:参与不合格物料评估并执行MRB决议,明确品质异常经济责任承担;4.0 管理办法内容4.1 MRB小组成员4.1.1 MRB小组组长—品质部经理;4.1.2 MRB小组成员—生产部经理、计划科主任、采购科主任、技术部经理、相关业务员;4.1.3必要时将临时邀请相关人员;4.2物料异常产生及MRB提出4.2.1公司所有外协加工/采购物料由品质部IQC人员予以检验,如发现来料与品质标准存在差异,但属于生产急用之物料,由采购科/计划科填写《紧急放行单》,品质部召集召开MRB会议;4.2.2制程在途与仓储异常物料,本车间无法修补的,由车间填写《产品质量异常信息反馈单》反馈至品质部,由品质部判定是否召集召开MRB会议;4.3 MRB评估4.3.1计划科:提供客户交期、计划编制、出货排程及补单安排;4.3.2 生产部:提供异常物料所造成进度影响,明确执行单位能否协助代加工/挑选,并承诺完成时间;4.3.3 技术部:评估异常物料能否正常使用,并提供技术支持;4.3.4 采购科:供应商信息沟通,供应商生产状况及供应商之回复,明确MRB产生费用归属,回复供应商返工之完成时间并办理退货、补货手续;4.3.5 业务部:客户沟通及确认;4.3.6 品质部:明确异常物料品质影响程度,判定结果【特采/返工/代加工/挑选/退货/正常使用】,判定责任承担单位并跟进MRB执行结果确认;4.3.7责任承担按《品质异常经济责任承担管理办法》实施;4.4 MRB评估决议及决议执行4.4.1 MRB评估内容须达成决议【特采/返工/代加工/挑选/退货/正常使用】并由品质部以《MRB评审记录表》记录存档,并通过公司邮箱传递相关部门;4.4.2 MRB小组成员须在《MRB评审记录表》签名确认;4.4.3 属生产部协助供应商代加工/挑选,则由生产部记录耗损的成本【工时/材料】,并填写《返修耗时/耗料记录表》上报采购科/财务部门;4.4.4 属品质部MRB全检执行挑选或代加工的(包括本厂制程产生的不良),由品质部负责将MRB产生费用及责任进行划分,并填写《返修耗时/耗料记录表》上报采购科/财务部,财务部执行扣款;4.5 MRB执行结果监督及确认4.5.1 品质部对MRB决议执行之结果予以监督,并判定是否符合要求;4.6 MRB全检组成人员4.6.1品质部品检科下属检验人员为主要实施人员;4.6.2 生产执行车间属MRB临时实施人员;4.7 实施4.7.1《MRB作业管理办法》自颁发日起实施;5.0 附件5.1《产品质量异常信息反馈单》;5.2《MRB评审记录表》;5.3《返修耗时/耗料记录表》;5.4《紧急放行单》;5.5《品质异常经济责任承担管理办法》;。
MRB特采作业管理办法
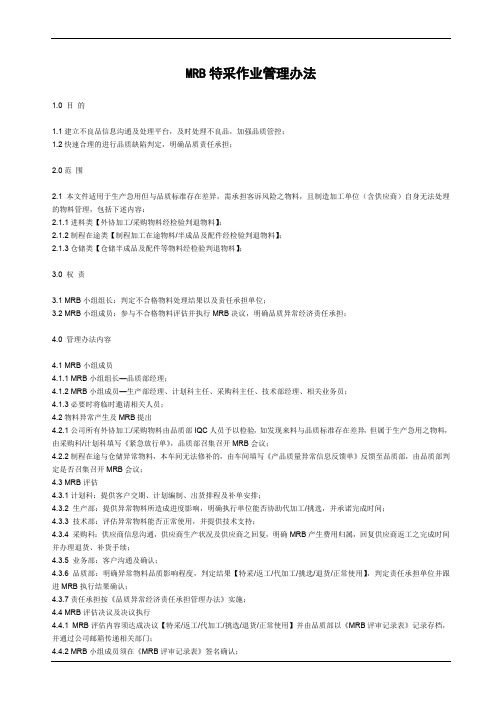
MRB特采作业管理办法1.0 目的1.1建立不良品信息沟通及处理平台,及时处理不良品,加强品质管控;1.2快速合理的进行品质缺陷判定,明确品质责任承担;2.0范围2.1 本文件适用于生产急用但与品质标准存在差异,需承担客诉风险之物料,且制造加工单位(含供应商)自身无法处理的物料管理,包括下述内容:2.1.1进料类【外协加工/采购物料经检验判退物料】;2.1.2制程在途类【制程加工在途物料/半成品及配件经检验判退物料】;2.1.3仓储类【仓储半成品及配件等物料经检验判退物料】;3.0 权责3.1 MRB小组组长:判定不合格物料处理结果以及责任承担单位;3.2 MRB小组成员:参与不合格物料评估并执行MRB决议,明确品质异常经济责任承担;4.0 管理办法内容4.1 MRB小组成员4.1.1 MRB小组组长—品质部经理;4.1.2 MRB小组成员—生产部经理、计划科主任、采购科主任、技术部经理、相关业务员;4.1.3必要时将临时邀请相关人员;4.2物料异常产生及MRB提出4.2.1公司所有外协加工/采购物料由品质部IQC人员予以检验,如发现来料与品质标准存在差异,但属于生产急用之物料,由采购科/计划科填写《紧急放行单》,品质部召集召开MRB会议;4.2.2制程在途与仓储异常物料,本车间无法修补的,由车间填写《产品质量异常信息反馈单》反馈至品质部,由品质部判定是否召集召开MRB会议;4.3 MRB评估4.3.1计划科:提供客户交期、计划编制、出货排程及补单安排;4.3.2 生产部:提供异常物料所造成进度影响,明确执行单位能否协助代加工/挑选,并承诺完成时间;4.3.3 技术部:评估异常物料能否正常使用,并提供技术支持;4.3.4 采购科:供应商信息沟通,供应商生产状况及供应商之回复,明确MRB产生费用归属,回复供应商返工之完成时间并办理退货、补货手续;4.3.5 业务部:客户沟通及确认;4.3.6 品质部:明确异常物料品质影响程度,判定结果【特采/返工/代加工/挑选/退货/正常使用】,判定责任承担单位并跟进MRB执行结果确认;4.3.7责任承担按《品质异常经济责任承担管理办法》实施;4.4 MRB评估决议及决议执行4.4.1 MRB评估内容须达成决议【特采/返工/代加工/挑选/退货/正常使用】并由品质部以《MRB评审记录表》记录存档,并通过公司邮箱传递相关部门;4.4.2 MRB小组成员须在《MRB评审记录表》签名确认;4.4.3 属生产部协助供应商代加工/挑选,则由生产部记录耗损的成本【工时/材料】,并填写《返修耗时/耗料记录表》上报采购科/财务部门;4.4.4 属品质部MRB全检执行挑选或代加工的(包括本厂制程产生的不良),由品质部负责将MRB产生费用及责任进行划分,并填写《返修耗时/耗料记录表》上报采购科/财务部,财务部执行扣款;4.5 MRB执行结果监督及确认4.5.1 品质部对MRB决议执行之结果予以监督,并判定是否符合要求;4.6 MRB全检组成人员4.6.1品质部品检科下属检验人员为主要实施人员;4.6.2 生产执行车间属MRB临时实施人员;4.7 实施4.7.1《MRB作业管理办法》自颁发日起实施;5.0 附件5.1《产品质量异常信息反馈单》;5.2《MRB评审记录表》;5.3《返修耗时/耗料记录表》;5.4《紧急放行单》;5.5《品质异常经济责任承担管理办法》;。
- 1、下载文档前请自行甄别文档内容的完整性,平台不提供额外的编辑、内容补充、找答案等附加服务。
- 2、"仅部分预览"的文档,不可在线预览部分如存在完整性等问题,可反馈申请退款(可完整预览的文档不适用该条件!)。
- 3、如文档侵犯您的权益,请联系客服反馈,我们会尽快为您处理(人工客服工作时间:9:00-18:30)。
文件名称 特采处理办法
修订日期 2011 年 3 月 17 日 21 编号 版次 初版
一、目的: 为生产急需和减少成本,当原物料、半成品、成品制造规格与原计 划要求不符时,经相关单位研判后,其缺点并不影响其主要性能,可经 由特别采用程序予以使用。
二、范围: 本公司之进料﹝含托外加工﹞即自制品于发生不合格情况均适用。
4
页次3/4
制定单位 管理处
文件名称 特采处理办法
修订日期 2011 年 3 月 17 日 21 编号 版次 初版
2.3 准予特采之处理: 当准予特采时,所花费相关费用或客户投诉等填入「特采申请 单」 ,由采购单位向协力厂商从货款中扣除。 2.4 记录:凡经特采批准,其质量特性应记录。
六、参考资料: 1. 不合格品管制办法。 2. 采购办法。 3.进料检验办法。 七、附件: 1. 特采申请单。 2. 质量异常处理单。 八、保存期限: 一年。
三、定义: 1.特采:指在未影响质量或主要性能情况下特别采用。 2.重工:指瑕疵品需要重新加工。 四、权责: 参考特采流程。
五、内容: 1. 作业流程:
4
页次1/4
制定单位 管理处
文件名称 特采处理办法
修订日期 2011 年 3 月 17 日 21 编号 版次 初版
流
程
权责单位
相关说明
生产过程各阶段之用料或 半成品不符合规格时提出
4
页次4/4
表
单
特采申请理由 说明填写
客户 生产部
特采申请单 质量异常处理单
审核意见 提出
生产部 品管处
特采申请单
否
核
示
是
总经理
裁决特采
录
生产部 品管处
4
页次2/4
制定单位 管理处
文件名称 特采处理办法
修订日期 2011 年 3 月 17 日 21 编号 版次 初版
2﹒执行方法: 2.1 特采申请: 2.1.1 由生产部提出申请,并填写「特采申请单」详记理由。 2.1.2 申请特采须填入下列资料:申请日期、品名、数量、缺 点状况、申请理由及预防措施。 2.1.3 特采申请时机: (1)可能造成公司停产,而无法达成 生产进度时。 (2)原物料进厂,经检验不合格,但急需上线生产时。 (3)因图面尺寸规格或检验基准过于严格 , 但不合格亦可使用 时。 (4)对于一般性及商品价值影响轻微时。 2.1.4 特采之限制: (1)对于安全及重要性能有影响者。 (2)有售后客户抱怨之顾虑者。 (3)同一状况多次发生者。 2.2 特采审核及裁示: 2.2.1 特采审核人员:由生产部、仓储中心、销售部组成。 2.2.2 特采申请提出后,由上述成员共同会审,依其职责所在填 入「特采申请单」相关意见栏并名之。 2.2.3 特采完成审核、裁示后,正本由仓储中心保存,并依需要 影印分发制有关单位参考。