SSMT生产工艺流程
SMT车间生产工艺流程图
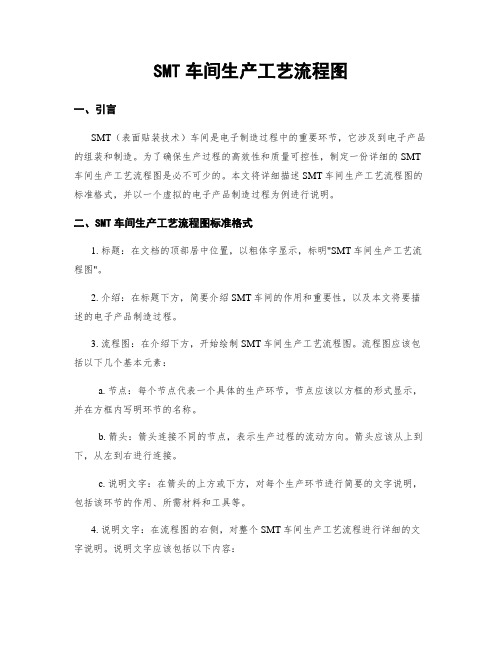
SMT车间生产工艺流程图一、引言SMT(表面贴装技术)车间是电子制造过程中的重要环节,它涉及到电子产品的组装和制造。
为了确保生产过程的高效性和质量可控性,制定一份详细的SMT 车间生产工艺流程图是必不可少的。
本文将详细描述SMT车间生产工艺流程图的标准格式,并以一个虚拟的电子产品制造过程为例进行说明。
二、SMT车间生产工艺流程图标准格式1. 标题:在文档的顶部居中位置,以粗体字显示,标明"SMT车间生产工艺流程图"。
2. 介绍:在标题下方,简要介绍SMT车间的作用和重要性,以及本文将要描述的电子产品制造过程。
3. 流程图:在介绍下方,开始绘制SMT车间生产工艺流程图。
流程图应该包括以下几个基本元素:a. 节点:每个节点代表一个具体的生产环节,节点应该以方框的形式显示,并在方框内写明环节的名称。
b. 箭头:箭头连接不同的节点,表示生产过程的流动方向。
箭头应该从上到下,从左到右进行连接。
c. 说明文字:在箭头的上方或下方,对每个生产环节进行简要的文字说明,包括该环节的作用、所需材料和工具等。
4. 说明文字:在流程图的右侧,对整个SMT车间生产工艺流程进行详细的文字说明。
说明文字应该包括以下内容:a. 车间布局:描述SMT车间的布局和设备摆放情况,包括生产线的位置和工作台的布置等。
b. 生产环节:逐个描述每个生产环节的具体操作步骤和注意事项,包括材料准备、设备调试和操作流程等。
c. 质量控制:说明每个生产环节中的质量控制点和检测方法,以确保产品质量的可控性。
d. 人员分工:描述每个生产环节中各个岗位的职责和工作内容,以及人员之间的协作关系。
e. 安全措施:列举在SMT车间生产过程中需要注意的安全事项和防护措施,以确保员工的人身安全。
三、示例:虚拟电子产品制造过程以下是一个虚拟的电子产品制造过程的SMT车间生产工艺流程图的标准格式示例:[图]说明文字:1. 车间布局:SMT车间由三条生产线组成,每条生产线包括设备摆放区、材料准备区和成品检测区。
SMT车间生产工艺流程图

SMT车间生产工艺流程图一、引言SMT(表面贴装技术)是一种电子元器件自动化贴装技术,广泛应用于电子制造业。
本文将详细介绍SMT车间的生产工艺流程图,包括原材料采购、贴片、焊接、检测等环节。
二、原材料采购1. 原材料准备:根据生产计划,采购所需的电子元器件、PCB板、焊接材料等原材料。
2. 供应商选择:选择可靠的供应商,确保原材料的质量和供货稳定性。
3. 采购流程:与供应商进行洽谈、签订采购合同,按照合同约定的时间和数量进行采购。
三、贴片工艺1. PCB板准备:将采购的PCB板送至SMT车间,进行表面处理,确保贴片粘附的质量。
2. 贴片机操作:将电子元器件通过贴片机自动精确定位,粘贴到PCB板上的预定位置。
3. 贴片质量控制:通过视觉检测系统对贴片进行质量检测,确保贴片的准确性和质量。
4. 回流焊接:将贴片后的PCB板送至回流焊接设备,进行焊接,确保电子元器件与PCB板的可靠连接。
四、焊接工艺1. 焊接准备:将焊接材料(如焊锡膏)准备好,根据焊接工艺要求,对焊接设备进行调试和校准。
2. 焊接操作:将贴片后的PCB板送至焊接设备,进行焊接操作,确保焊接的质量和可靠性。
3. 焊接质量控制:通过焊接后的视觉检测系统对焊接点进行质量检测,确保焊接的准确性和质量。
五、检测工艺1. AOI检测:采用自动光学检测设备对焊接后的PCB板进行自动光学检测,检测焊接点的质量和准确性。
2. X光检测:采用X光设备对焊接点进行非破坏性检测,检测焊接点的焊接质量和连接可靠性。
3. 功能测试:对焊接后的电子产品进行功能测试,确保产品的性能和功能符合要求。
六、包装与出货1. 包装准备:根据产品要求,选择适当的包装材料,对产品进行包装。
2. 包装操作:将经过检测的电子产品进行包装,确保产品在运输过程中不受损。
3. 出货:将包装好的产品按照订单要求进行出货,确保及时交付给客户。
七、总结SMT车间的生产工艺流程图涵盖了原材料采购、贴片、焊接、检测、包装与出货等环节。
smt生产工艺流程

smt生产工艺流程
SMT(表面贴装技术)生产工艺流程是一种使用机器将电子元器件直接贴装在印刷电路板(PCB)上的生产技术。
下面是一个典型的SMT生产工艺流程。
1. 设计和采购:在生产开始之前,设计团队将根据产品要求设计PCB。
然后,采购团队会和供应商合作,采购所需的电子元器件和原材料。
2. PCB制备:这一步骤包括将原材料切割成适当大小的PCB 板和在板上涂覆有导电层的化学物质以便制作电路。
3. 打孔:在PCB板上打上所需的孔以安装元器件。
4. 涂覆焊膏:在PCB板的焊接区域涂上焊膏,焊膏会在焊接过程中起到连接元器件和PCB的作用。
5. SMT贴装:这是整个流程中最重要的一步。
机器会自动将电子元器件从供应盘上拿起并精确地放置在PCB板的焊接区域上。
这些元器件可能包括集成电路、电容、电阻等。
6. 固定元器件:一些元器件需要在通过SMT贴装技术后进一步固定到PCB板上。
这些元器件可以通过波峰焊、热风炉或其他一些方法进行固定。
7. 焊接:在这一步骤中,通过高温加热和冷却的过程,焊膏会熔化并将元器件连接到PCB板上。
8. 清洁:在焊接完成后,PCB板会通过清洗过程去除焊剂残留物。
9. 检测和测试:在最后一步之前,生产团队会对已完成的PCB板进行严格的检测和测试,以确保其质量和功效。
10. 包装和交货:最后,已经通过检测的PCB板将被包装好,以便运输到客户的目的地。
总之,SMT生产工艺流程是一个复杂而精确的过程,通过高效地将电子元器件贴装在PCB板上,实现了电子产品的高度集成和可靠性。
SMT车间生产工艺流程图

SMT车间生产工艺流程图SMT(表面贴装技术)车间是电子制造业中重要的生产环节,其工艺流程图对于保证产品质量和提高生产效率至关重要。
下面将详细介绍SMT车间生产工艺流程图的标准格式及其内容要求。
一、工艺流程图标准格式SMT车间生产工艺流程图通常采用流程图的形式进行展示,可以使用专业绘图软件或者办公软件的流程图工具进行绘制。
标准格式包括以下几个要素:1. 标题:在图的顶部居中位置,使用大字体写明“SMT车间生产工艺流程图”。
2. 流程节点:使用矩形框表示每个工艺流程节点,节点之间使用箭头连接,箭头指向下一个节点。
每个节点上方写明节点名称,如“物料准备”、“贴片”、“焊接”等。
3. 内容描述:在每个节点下方使用小字体写明该工艺节点的具体内容描述。
描述内容应该准确、简明,包括所需物料、工艺步骤、设备要求等。
4. 并行流程:如果有多个流程节点可以同时进行,可以使用并行箭头表示,并在箭头上方写明并行节点的名称。
5. 分支流程:如果有多个选择分支的流程节点,可以使用分支箭头表示,并在箭头上方写明分支节点的名称。
6. 结束节点:在工艺流程的最后一个节点使用特殊的结束符号表示,如圆形框或者其他符号。
二、SMT车间生产工艺流程图内容要求SMT车间生产工艺流程图应该准确反映整个生产流程,并包括以下内容要求:1. 物料准备:描述从供应链中获取所需物料的过程,包括物料采购、入库、分类和检验等环节。
2. 贴片:描述贴片工艺流程,包括贴片机的设置和调试、贴片头的更换、贴片程序的加载、上料和下料等步骤。
3. 焊接:描述焊接工艺流程,包括回流焊炉的设置和调试、焊接程序的加载、焊接过程的监控和质量检验等步骤。
4. 检测:描述质量检测工艺流程,包括自动光学检测(AOI)、X光检测、功能测试等步骤。
5. 组装:描述组装工艺流程,包括组装设备的设置和调试、组装程序的加载、组装过程的监控和质量检验等步骤。
6. 包装:描述产品包装工艺流程,包括包装材料的选择、包装设备的设置和调试、包装过程的监控和质量检验等步骤。
SMT车间生产工艺流程图

SMT车间生产工艺流程图一、引言SMT(表面贴装技术)是一种电子组装技术,广泛应用于电子产品的制造过程中。
该技术通过将电子元件直接贴装在印刷电路板(PCB)上,实现电子产品的组装和制造。
本文将详细介绍SMT车间生产工艺流程图,包括以下几个步骤:物料准备、面板准备、贴装、焊接和检验。
二、物料准备1. 物料采购:根据产品的需求,采购所需的电子元件、PCB和焊接材料等。
2. 物料检验:对采购回来的物料进行检验,确保其质量符合要求。
3. 物料上架:将经过检验的物料按照规定的存放位置进行上架,方便后续的取料。
三、面板准备1. PCB准备:根据产品的设计要求,选择相应的PCB板,并进行清洁和防静电处理。
2. 贴片工艺准备:根据产品的贴片工艺要求,设置贴片机的参数和程序。
3. 钢网准备:根据贴片工艺要求,选择合适的钢网,并进行清洁和调整。
四、贴装1. 贴片机操作:将准备好的PCB板放置在贴片机上,并通过设定的程序进行贴装操作。
2. 贴片检验:对贴片完成后的PCB板进行检验,确保贴片的位置和质量符合要求。
3. 二次贴装:对于一些特殊的电子元件,需要进行二次贴装操作,以确保其正确安装在PCB板上。
五、焊接1. 回流焊接:将贴片完成的PCB板放入回流焊接设备中,通过加热和冷却的过程,将电子元件焊接在PCB板上。
2. 焊接检验:对焊接完成的PCB板进行检验,确保焊接的质量和连接可靠。
六、检验1. 外观检验:对焊接完成的PCB板进行外观检查,确保没有明显的缺陷和损伤。
2. 功能测试:对焊接完成的PCB板进行功能测试,确保电子元件的正常工作。
3. 电气测试:对焊接完成的PCB板进行电气测试,确保电路的连接和电性能符合要求。
七、总结SMT车间生产工艺流程图涵盖了物料准备、面板准备、贴装、焊接和检验等多个环节。
通过严格按照流程图进行操作,可以确保电子产品的质量和性能符合要求。
同时,也需要注意物料的质量控制和工艺参数的准确设置,以提高生产效率和产品的可靠性。
SMT车间生产工艺流程图
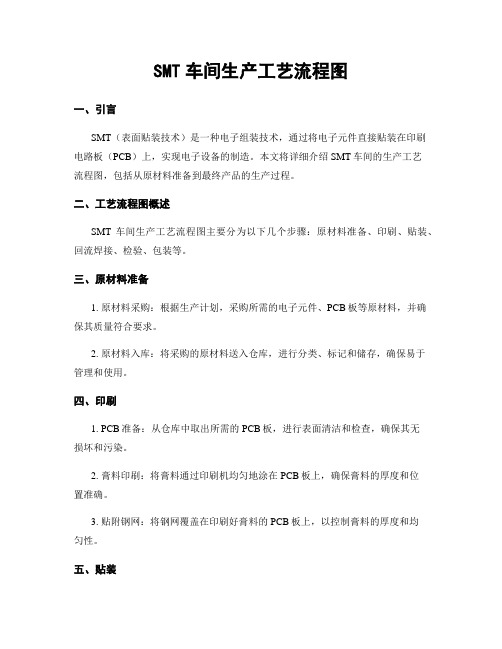
SMT车间生产工艺流程图一、引言SMT(表面贴装技术)是一种电子组装技术,通过将电子元件直接贴装在印刷电路板(PCB)上,实现电子设备的制造。
本文将详细介绍SMT车间的生产工艺流程图,包括从原材料准备到最终产品的生产过程。
二、工艺流程图概述SMT车间生产工艺流程图主要分为以下几个步骤:原材料准备、印刷、贴装、回流焊接、检验、包装等。
三、原材料准备1. 原材料采购:根据生产计划,采购所需的电子元件、PCB板等原材料,并确保其质量符合要求。
2. 原材料入库:将采购的原材料送入仓库,进行分类、标记和储存,确保易于管理和使用。
四、印刷1. PCB准备:从仓库中取出所需的PCB板,进行表面清洁和检查,确保其无损坏和污染。
2. 膏料印刷:将膏料通过印刷机均匀地涂在PCB板上,确保膏料的厚度和位置准确。
3. 贴附钢网:将钢网覆盖在印刷好膏料的PCB板上,以控制膏料的厚度和均匀性。
五、贴装1. 自动贴片机:将电子元件从料盘中取出,并通过自动贴片机将其精确地贴装在PCB板上。
2. 人工贴片:对于一些特殊的电子元件,无法通过自动贴片机完成,需要由工人手工进行贴装。
六、回流焊接1. 进入回流焊接炉:将已完成贴装的PCB板送入回流焊接炉中,通过高温加热,使电子元件与PCB板上的焊接膏料熔化并连接在一起。
2. 冷却和固化:焊接完成后,PCB板进入冷却区域,使焊接点迅速冷却和固化,确保焊接的牢固性和可靠性。
七、检验1. 外观检查:对焊接完成的PCB板进行外观检查,确保没有焊接不良、漏焊、错位等缺陷。
2. 电气测试:通过专用测试设备对PCB板进行电气测试,检测电子元件的连接和功能是否正常。
八、包装1. 清洁和除静电处理:对通过检验的PCB板进行清洁和除静电处理,以防止静电对电子元件的损害。
2. 包装和标记:将PCB板进行适当的包装,标明产品型号、批次号等信息,以便后续的存储和交付。
九、总结本文详细介绍了SMT车间的生产工艺流程图,包括原材料准备、印刷、贴装、回流焊接、检验和包装等步骤。
smt生产线生产流程图

smt生产线生产流程图在SMT生产线生产流程图中,我们将详细介绍SMT生产线的整个生产流程,包括各个环节的具体操作和关键步骤。
SMT生产线是表面贴装技术的简称,是一种电子元器件的表面粘贴技术,广泛应用于电子产品的制造中。
下面我们将逐步介绍SMT生产线的生产流程图。
首先,SMT生产线的第一步是PCB板的贴片。
在这个环节,首先需要准备好PCB板和各种SMT贴片元器件,然后通过贴片机将元器件精确地贴片到PCB板上。
这个过程需要高精度的机器设备和精密的操作技术,以确保贴片的准确性和稳定性。
接下来是回流焊接。
在这个环节,已经完成贴片的PCB板需要进行回流焊接,以确保贴片元器件与PCB板的牢固连接。
回流焊接需要将PCB板送入回流焊炉中,通过高温回流焊接炉对PCB板进行加热,使焊膏熔化并与贴片元器件和PCB板形成牢固的焊接连接。
然后是AOI检测。
在回流焊接完成后,需要对PCB板进行自动光学检测(AOI),以检查焊接质量和元器件的安装情况。
AOI检测设备会自动扫描PCB板表面,对焊接点、元器件位置等进行检测,以确保没有焊接缺陷和元器件安装错误。
接着是功能测试。
在AOI检测完成后,需要对已经焊接完成的PCB板进行功能测试,以验证电路连接和元器件的正常工作。
功能测试通常包括电气测试和功能性测试,通过测试仪器对PCB板进行各种电气信号的检测和功能操作,以确保PCB板的正常工作。
最后是包装出货。
经过功能测试合格的PCB板需要进行包装,以便于运输和存储。
包装通常包括防静电包装和外包装,以确保PCB板在运输过程中不受损坏,并便于客户使用和存储。
以上就是SMT生产线的生产流程图,通过这个流程图我们可以清晰地了解SMT生产线的整个生产过程。
希望这个生产流程图能够对大家有所帮助,谢谢!。
SMT生产标准技术流程

SMT生产标准技术流程SMT(Surface Mount Technology)是一种电子元器件表面粘贴技术,广泛应用于电子产品的生产。
SMT生产标准技术流程是确保SMT生产过程质量和产能的重要指南。
下面是SMT生产标准技术流程的一般步骤:1. 设计审核:在SMT生产之前,设计团队对PCB(Printed Circuit Board)进行审核,确保其符合SMT生产的要求。
这一步骤包括检查PCB布线、元器件封装尺寸和元器件位置等。
2. 元器件采购:在SMT生产之前,采购团队根据设计要求采购所需的元器件,确保其品质和供货周期。
3. 印刷:使用印刷机将焊膏印刷到PCB上,确保焊膏的均匀性和质量。
4. 贴片:使用贴片机将表面贴装元器件粘贴到PCB上,确保元器件粘贴的准确性和质量。
5. 焊接:通过回流炉或波峰焊接机对元器件进行焊接,确保焊接焊点的质量和可靠性。
6. 质量控制:在整个SMT生产过程中,质量控制团队进行严格的产品质量检验,确保产品符合客户要求和标准。
7. 包装和发货:完成SMT生产后,将产品进行包装,并按照客户要求进行发货。
以上是SMT生产标准技术流程的一般步骤,每个步骤都需要严格执行,并且需要定期进行技术改进,以确保生产的质量和效率。
通过严格遵循SMT生产标准技术流程,可以提高产品的质量和竞争力,满足客户的需求。
SMT生产标准技术流程的严格执行是确保电子产品质量和稳定性的关键之一。
让我们进一步深入探讨SMT生产标准技术流程的重要性以及每个步骤的关键性。
首先,设计审核是SMT生产流程的关键一步。
在这个阶段,设计团队需要对PCB进行详细的审核,确保其布线符合SMT生产要求,元器件封装尺寸、位置等符合标准。
由此可以确保在后续的生产过程中能够顺利进行,避免设计上的问题导致生产出现困难或质量问题。
此外,设计审核阶段也为后续的元器件采购提供了指导,确保元器件的选择能够满足设计要求。
元器件采购是另一个至关重要的环节。
- 1、下载文档前请自行甄别文档内容的完整性,平台不提供额外的编辑、内容补充、找答案等附加服务。
- 2、"仅部分预览"的文档,不可在线预览部分如存在完整性等问题,可反馈申请退款(可完整预览的文档不适用该条件!)。
- 3、如文档侵犯您的权益,请联系客服反馈,我们会尽快为您处理(人工客服工作时间:9:00-18:30)。
SMT生产工艺流程
MT基本工艺构成要素包括:丝印(或点胶),贴装(固化),回流焊接,清洗,检测,返修
1、丝印:其作用是将焊膏或贴片胶漏印到PCB的焊盘上,为元器件的焊接做准备。
所用设备为丝印机(丝网印刷机),位于SMT生产线的最前端。
2、点胶:它是将胶水滴到PCB的的固定位置上,其主要作用是将元器件固定到PCB板上。
所用设备为点胶机,位于SMT生产线的最前端或检测设备的后面。
3、贴装:其作用是将表面组装元器件准确安装到PCB的固定位置上。
所用设备为贴片机,位于SMT 生产线中丝印机的后面。
4、固化:其作用是将贴片胶融化,从而使表面组装元器件与PCB板牢固粘接在一起。
所用设备为固化炉,位于SMT生产线中贴片机的后面。
5、回流焊接:其作用是将焊膏融化,使表面组装元器件与PCB板牢固粘接在一起。
所用设备为回流焊炉,位于SMT生产线中贴片机的后面。
6、清洗:其作用是将组装好的PCB板上面的对人体有害的焊接残留物如助焊剂等除去。
所用设备为清洗机,位置可以不固定,可以在线,也可不在线。
7、检测:其作用是对组装好的PCB板进行焊接质量和装配质量的检测。
所用设备有放大镜、显微镜、在线测试仪(ICT)、飞针测试仪、自动光学检测(AOI)、X-RAY检测系统、功能测试仪等。
位置根据检测的需要,可以配置在生产线合适的地方。
8、返修:其作用是对检测出现故障的PCB板进行返工。
所用工具为烙铁、返修工作站等。
配置在生产线中任意位置。
一、单面组装:
来料检测=> 丝印焊膏(点贴片胶)=> 贴片=> 烘干(固化)=> 回流焊接=>清洗=> 检测=> 返修
二、双面组装:
A:来料检测=> PCB的A面丝印焊膏(点贴片胶)=> 贴片=> 烘干(固化)=>A面回流焊接=> 清洗=> 翻板=> PCB的B面丝印焊膏(点贴片胶)=> 贴片=>烘干=> 回流焊接(最好仅对B面=> 清洗=> 检测=> 返修)
此工艺适用于在PCB两面均贴装有PLCC等较大的SMD时采用。
B:来料检测=> PCB的A面丝印焊膏(点贴片胶)=> 贴片=> 烘干(固化)=>A面回流焊接=> 清洗=> 翻板=> PCB的B面点贴片胶=> 贴片=> 固化=>B面波峰焊=> 清洗=> 检测=> 返修)
此工艺适用于在PCB的A面回流焊,B面波峰焊。
在PCB的B面组装的SMD中,只有SOT或SOIC (28)引脚以下时,宜采用此工艺。
三、单面混装工艺:
来料检测=> PCB的A面丝印焊膏(点贴片胶)=> 贴片=>烘干(固化)=>回流焊接=> 清洗=> 插件=> 波峰焊=> 清洗=> 检测=> 返修
四、双面混装工艺:
A:来料检测=> PCB的B面点贴片胶=> 贴片=> 固化=> 翻板=> PCB的A面插件=> 波峰焊=> 清洗=> 检测=> 返修
先贴后插,适用于SMD元件多于分离元件的情况
B:来料检测=> PCB的A面插件(引脚打弯)=> 翻板=> PCB的B面点贴片胶=>贴片=> 固化=> 翻板=> 波峰焊=> 清洗=> 检测=> 返修
先插后贴,适用于分离元件多于SMD元件的情况
C:来料检测=> PCB的A面丝印焊膏=> 贴片=> 烘干=> 回流焊接=>插件,引脚打弯=> 翻板=> PCB的B面点贴片胶=> 贴片=> 固化=> 翻板=> 波峰焊=>清洗=> 检测=> 返修A面混装,B面
贴装。
D:来料检测=> PCB的B面点贴片胶=> 贴片=> 固化=> 翻板=>PCB的A面丝印焊膏=> 贴片=> A面回流焊接=> 插件=> B面波峰焊=> 清洗=> 检测=>返修A面混装,B面贴装。
先贴两面SMD,回流焊接,后插装,波峰焊E:来料检测=> PCB的B面丝印焊膏(点贴片胶)=> 贴片=> 烘干(固化)=>回流焊接=> 翻板=> PCB的A面丝印焊膏=> 贴片=> 烘干=回流焊接1(可采用局部焊接)=> 插件=> 波峰焊2(如插装元件少,可使用手工焊接)=> 清洗=>检测=> 返修A面贴装、B面混装。
五、双面组装工艺
A:来料检测,PCB的A面丝印焊膏(点贴片胶),贴片,烘干(固化),A面回流焊接,清洗,翻板;PCB的B 面丝印焊膏(点贴片胶),贴片,烘干,回流焊接(最好仅对B面,清洗,检测,返修)
此工艺适用于在PCB两面均贴装有PLCC等较大的SMD时采用。
B:来料检测,PCB的A面丝印焊膏(点贴片胶),贴片,烘干(固化),A面回流焊接,清洗,翻板;PCB的B 面点贴片胶,贴片,固化,B面波峰焊,清洗,检测,返修)此工艺适用于在PCB的A面回流焊,B面波峰焊。
在PCB的B面组装的SMD中,只有SOT或SOIC(28)引脚以下时,宜采用此工艺。