原位颗粒对铝基复合材料组织及磨损性能的影响
TiC颗粒增强铝基复合材料耐磨性能研究

力 图使 复合 材料 达 到较 低 的强 度 、较 高 的塑性 及 良好 的 表 1复合材料设计成 份表
T b 1C m p st ae il e inc m p n n a . o o i m t r sd sg o e a o et 合 金 号
1 2 2 l V0 %Ti C Al .Cu-0 6 -1 2 i 0.Mn一 . Ce -22 . Mg . S - 6 0 01 - 3 3 l Vo % C Al 2 2 一 . Cu一 6 g . S 一 . Mn一0 01 一 0.M 一1 2 i 0 6 . Ce 4 5 1 TC V0% i 5 C 一3 Zn 2. u 8 一 2Mn 2 2 b 一 .P 58 — —2 2 L + Vo %Ti D5 5 l C LD5 3 l T C + Vo % i
主 要 成 份
L D5 LD5 2 l T C + Vo % i
表 2 复合材料在 不同状 态下的硬度值
T b2 R s l f ad e si v r u tt s a . e ut o r n s n a i s s a e s h o
所 用复 合 材料 采 用 自蔓延 高 温合 成 原位 生 成法 ,通过 合
金 中 的元 素相 互作 用 而生 成 TC颗 粒 。这 两 种 方 法生 产 i
工 艺 较 简单 ,生成 TC颗 粒 性 质稳 定 ,与基 体 之 间界 面 i
干 净 ,结 合 良好 圄 。
2 实验 结 果
( )实验 材 料 的硬 度 。合 金 的硬 度值 与 强 度及 耐 磨 1 损 性 能 之 间存 在一 定 的关 系 。一 般说 ,硬度 愈 高 ,其 力 学 性 能 愈好 ,所 以通过 测 定合 金 的硬 度 值可 以快速 了解
原位增强Al-4.5Cu合金的高温干摩擦磨损行为研究

试样 在 5 3℃ 固溶 1 3 2—1 ,6 6h 15℃时效 7h。
1 2 高温 磨损试 验 .
将复合材料试棒加工成 6 m× 8m 4m 1 m的圆销状
试样 , 端面粗 糙度 R 口为 04 m。 . 摩 擦 副 材 料 为 球 墨铸 铁 L S Q -5 -0 Z G T501 ,加 工 成
铸造 A4.C l 5 u合 金熔 体 中 , 以发生 原位 反应 , 强相 可 增
中将纯铝锭 、1 0 u A- C 合金按 A-.C 合金的化学计量 5 l 5u 4
比配好后 放入 电阻 炉 中熔 化 , 过 热 到 9 0o 无 水 反 并 5 C, 应 添加物 用 铝 箔 包 裹 分 批 加 入 熔 体 中 , 用 石 墨 棒 搅 并
T 3 1T 2 1 B 3 ;G 9 文献标 志码 A 文章编号 10 2 4 (06 0 0 1 0 0 1— 2 9 20 ) 8— 5 5— 3 中图分类号
颗粒增强铝基复合材料由于具有 比强度高 、 比刚度
高、 耐磨蚀 和导 热能 力强 等优 点 , 在航 空航 天 、 汽车工 业 等 领域 有着 广 阔 的 应 用 前 景 。特 别 是 在 刹 车 系统 ( 包 括 刹车 盘 、 车片 等 ) 发 动机 活 塞 、 制杆 、 刹 , 控 汽缸 套 、 转
维普资讯
—
—
复 合 材 料
种铸造及有色合金 20 年第 2 06 6卷第 8 期
原位 增 强 A 一. u合 金 的 高 温 干摩 擦 磨 损 行 为 研 究 I 5 4 C
梁 艳峰 周敬 恩 董晟全 杨 通
( .西安 交通 大学 ;.西安 工业学 院) 1 2
I 硬度( B 为 20 x m, H ) 4 。在 M D 1G高温材料摩擦磨 M . 0
颗粒增强铝基复合材料的研究现状
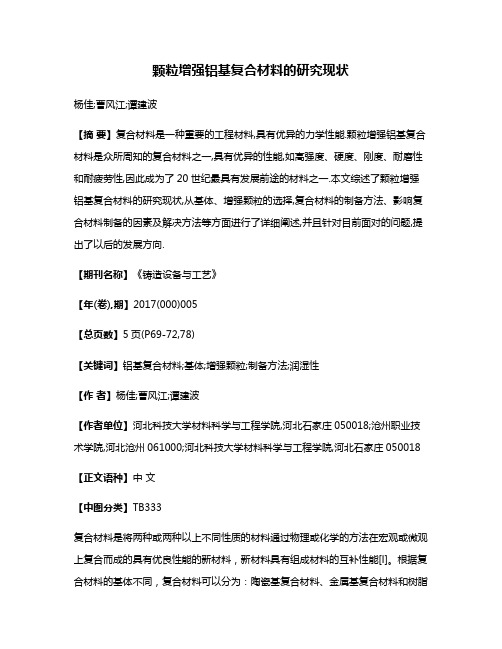
颗粒增强铝基复合材料的研究现状杨佳;曹风江;谭建波【摘要】复合材料是一种重要的工程材料,具有优异的力学性能.颗粒增强铝基复合材料是众所周知的复合材料之一,具有优异的性能,如高强度、硬度、刚度、耐磨性和耐疲劳性,因此成为了20世纪最具有发展前途的材料之一.本文综述了颗粒增强铝基复合材料的研究现状,从基体、增强颗粒的选择,复合材料的制备方法、影响复合材料制备的因素及解决方法等方面进行了详细阐述,并且针对目前面对的问题,提出了以后的发展方向.【期刊名称】《铸造设备与工艺》【年(卷),期】2017(000)005【总页数】5页(P69-72,78)【关键词】铝基复合材料;基体;增强颗粒;制备方法;润湿性【作者】杨佳;曹风江;谭建波【作者单位】河北科技大学材料科学与工程学院,河北石家庄050018;沧州职业技术学院,河北沧州061000;河北科技大学材料科学与工程学院,河北石家庄050018【正文语种】中文【中图分类】TB333复合材料是将两种或两种以上不同性质的材料通过物理或化学的方法在宏观或微观上复合而成的具有优良性能的新材料,新材料具有组成材料的互补性能[l]。
根据复合材料的基体不同,复合材料可以分为:陶瓷基复合材料、金属基复合材料和树脂基复合材料[l]。
根据复合材料的增强相不同可分为:颗粒增强复合材料和纤维增强复合材料[l]。
其中颗粒增强铝基复合材料是2l世纪最具有发展前途的先进材料之一。
该种复合材料具有高比强度、高比刚度、高比模量、低密度以及良好的高温性能,并且颗粒增强铝基复合材料耐磨、耐疲劳、热膨胀系数低、导热性能良好[2~4]。
与纤维增强铝基复合材料相比,颗粒增强铝基复合材料价格低,并且各向同性、克服了纤维损伤、微观组织不均匀和纤维与纤维接触反应带大等问题[5]。
目前常用的颗粒增强铝基复合材料的基体有纯铝和铝合金[l],常用的增强颗粒有 SiC、Al2O3、TiC、Si3N4、B4C、石墨等[6,7]。
颗粒增强铝基复合材料
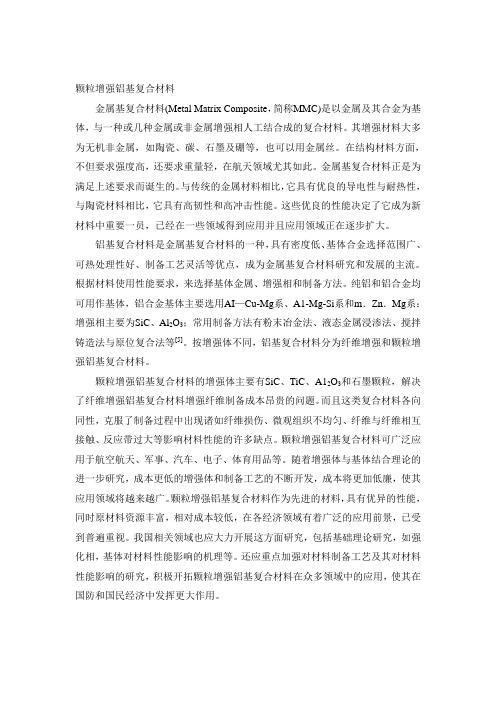
颗粒增强铝基复合材料金属基复合材料(Metal Matrix Composite,简称MMC)是以金属及其合金为基体,与一种或几种金属或非金属增强相人工结合成的复合材料。
其增强材料大多为无机非金属,如陶瓷、碳、石墨及硼等,也可以用金属丝。
在结构材料方面,不但要求强度高,还要求重量轻,在航天领域尤其如此。
金属基复合材料正是为满足上述要求而诞生的。
与传统的金属材料相比,它具有优良的导电性与耐热性,与陶瓷材料相比,它具有高韧性和高冲击性能。
这些优良的性能决定了它成为新材料中重要一员,已经在一些领域得到应用并且应用领域正在逐步扩大。
铝基复合材料是金属基复合材料的一种,具有密度低、基体合金选择范围广、可热处理性好、制备工艺灵活等优点,成为金属基复合材料研究和发展的主流。
根据材料使用性能要求,来选择基体金属、增强相和制备方法。
纯铝和铝合金均可用作基体,铝合金基体主要选用AI—Cu-Mg系、A1-Mg-Si系和m.Zn.Mg系:增强相主要为SiC、Al2O3;常用制备方法有粉末冶金法、液态金属浸渗法、搅拌铸造法与原位复合法等[5]。
按增强体不同,铝基复合材料分为纤维增强和颗粒增强铝基复合材料。
颗粒增强铝基复合材料的增强体主要有SiC、TiC、A12O3和石墨颗粒,解决了纤维增强铝基复合材料增强纤维制备成本昂贵的问题。
而且这类复合材料各向同性,克服了制备过程中出现诸如纤维损伤、微观组织不均匀、纤维与纤维相互接触、反应带过大等影响材料性能的许多缺点。
颗粒增强铝基复合材料可广泛应用于航空航天、军事、汽车、电子、体育用品等。
随着增强体与基体结合理论的进一步研究,成本更低的增强体和制备工艺的不断开发,成本将更加低廉,使其应用领域将越来越广。
颗粒增强铝基复合材料作为先进的材料,具有优异的性能,同时原材料资源丰富,相对成本较低,在各经济领域有着广泛的应用前景,已受到普遍重视。
我国相关领域也应大力开展这方面研究,包括基础理论研究,如强化相,基体对材料性能影响的机理等。
TiB_2颗粒对铝基复合材料变形过程的影响

TiB_2颗粒对铝基复合材料变形过程的影响原位自生Ti B2颗粒增强铝基复合材料,由于其优异的性能在航空、航天等领域得到了广泛的应用和关注,如高强度、高模量和高硬度等等。
上海交大特种材料研究中心自“十五”和“十一五”期间一直开展原位自生颗粒增强铝基复合材料的研究工作,取得了创新性的成果,成功制备得到了微纳米级的Ti B2增强颗粒。
众所周知,材料的微观组织是影响其力学性能的决定性因素,然而国内外对于Ti B2颗粒增强铝基复合材料变形机制以及复合材料变形过程中的微观组织结构演变情况的研究还不太深入。
因此,本论文对分别冷轧至60%,75%,90%和95%的四种5%Ti B2颗粒增强纯铝基复合材料进行了详细的微观组织表征和力学性能测试,以探索出复合材料的微观组织演变情况和变形机制,为在工程领域提高材料的强度提供理论指导。
采用扫描电镜、EBSD和中子衍射等技术对四个不同变形量的Ti B2/Al复合材料进行了微观结构表征。
结果表明:1.Ti B2/Al复合材料中微纳Ti B2颗粒分布呈现高密度富集在晶界和低密度弥散均匀分布在晶内两种形态。
富集在晶界的Ti B2颗粒会促进大角度晶界的形成,而弥散均匀分布微纳Ti B2颗粒会阻碍位错和晶界的移动,使复合材料中晶界的形成相比于铝合金更困难。
2.微纳Ti B2颗粒富集区应力分布集中,在变形过程中会促进再结晶的形核,然而弥散分布的微纳Ti B2颗粒会阻碍位错和晶界的运动,限制了再结晶晶粒的长大,从而形成小的再结晶晶粒。
3.变形后的Ti B2/Al复合材料中的晶粒尺寸相差极大,其中直径<2μm 的晶粒占晶粒总数的90%以上,却仅占面积的22%以下,集中分布在Ti B2颗粒富集区周围,这部分晶粒由变形小晶粒和再结晶小晶粒共同构成;而直径>2μm的晶粒占总数的10%以下,却占据有78%以上的面积。
4.Ti B2/Al复合材料中的织构体积分数和织构锐度均低于铝合金,说明微纳Ti B2颗粒对位错的滑移和晶粒的转动有阻碍作用,使复合材料的织构弱化。
激光熔覆原位自生TiC颗粒增强镍基复合涂层的组织与耐磨性
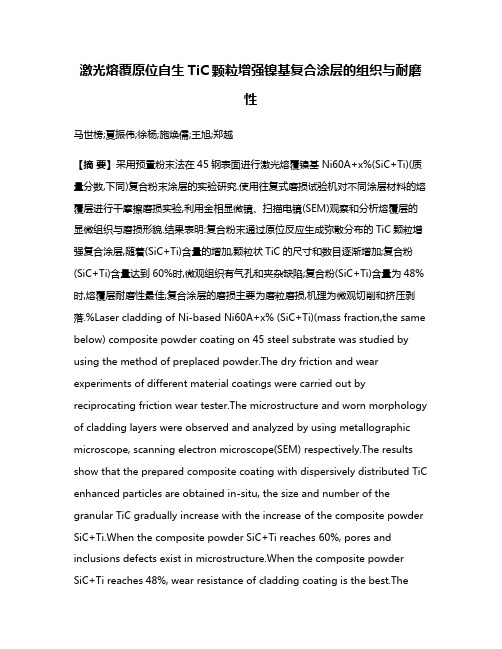
激光熔覆原位自生TiC颗粒增强镍基复合涂层的组织与耐磨性马世榜;夏振伟;徐杨;施焕儒;王旭;郑越【摘要】采用预置粉末法在45钢表面进行激光熔覆镍基Ni60A+x%(SiC+Ti)(质量分数,下同)复合粉末涂层的实验研究.使用往复式磨损试验机对不同涂层材料的熔覆层进行干摩擦磨损实验,利用金相显微镜、扫描电镜(SEM)观察和分析熔覆层的显微组织与磨损形貌.结果表明:复合粉末通过原位反应生成弥散分布的TiC颗粒增强复合涂层,随着(SiC+Ti)含量的增加,颗粒状TiC的尺寸和数目逐渐增加;复合粉(SiC+Ti)含量达到60%时,微观组织有气孔和夹杂缺陷;复合粉(SiC+Ti)含量为48%时,熔覆层耐磨性最佳;复合涂层的磨损主要为磨粒磨损,机理为微观切削和挤压剥落.%Laser cladding of Ni-based Ni60A+x% (SiC+Ti)(mass fraction,the same below) composite powder coating on 45 steel substrate was studied by using the method of preplaced powder.The dry friction and wear experiments of different material coatings were carried out by reciprocating friction wear tester.The microstructure and worn morphology of cladding layers were observed and analyzed by using metallographic microscope, scanning electron microscope(SEM) respectively.The results show that the prepared composite coating with dispersively distributed TiC enhanced particles are obtained in-situ, the size and number of the granular TiC gradually increase with the increase of the composite powder SiC+Ti.When the composite powder SiC+Ti reaches 60%, pores and inclusions defects exist in microstructure.When the composite powder SiC+Ti reaches 48%, wear resistance of cladding coating is the best.Thewear behavior of the composite coating is abrasive wear, and the mechanism is micro cutting and extrusion spalling.【期刊名称】《材料工程》【年(卷),期】2017(045)006【总页数】7页(P24-30)【关键词】激光熔覆;原位自生;TiC;耐磨性;强化机理【作者】马世榜;夏振伟;徐杨;施焕儒;王旭;郑越【作者单位】中国农业大学工学院,北京 100083;南阳师范学院机电工程学院,河南南阳 473061;中国农业大学工学院,北京 100083;中国农业大学工学院,北京100083;中国农业大学工学院,北京 100083;中国农业大学工学院,北京 100083;中国农业大学工学院,北京 100083【正文语种】中文【中图分类】TG115.5+8激光熔覆原位自生技术是指采用激光加工工艺,利用不同元素或化合物之间熔融状态下发生化学反应,在金属基体内生成一种或几种陶瓷相颗粒,以达到改善单一金属合金性能的方法[1-3]。
原位颗粒增强铝基复合材料制备实验指导书

熔体法(DMR)制备铝基复合材料实验一、实验目的1、了解熔体反应法制备铝基复合材料实验的原理;2、掌握熔体法制备金属基复合材料的基本操作要领;3、分析(DMR)方法制备铝基复合材料的主要缺陷及形成原因。
二、实验原理熔体直接反应法(Direct Melt Reaction),又称熔体反应法,是综合了接触反应法(CR法)和混合盐反应法(LSM法)的特点发展而成的一种原位复合材料制备方法。
其基本原理是将含有增强颗粒形成元素的固体颗粒或粉末在某一温度加到熔融的铝合金中,然后搅拌使反应充分进行,从而制备内生颗粒增强的复合材料。
与LSM法不同之处在于:可以直接加入单一的盐或氧化物与金属熔体完成反应。
熔体反应法由于以现有的铝合金熔炼工艺为基础,在铝熔体中直接形成增强颗粒,并且可以直接铸造成各种形状的复合材料铸件。
熔体直接反应法具有工艺简单、无需真空和惰性气体保护系统,也无需球磨混粉和压坯成形等工序;可直接浇注成形,生产周期短、制备成本低、易于批量生产和推广;并且原材料为盐类,来源广泛且成本低,因此有广阔的应用前景。
不足之处:形成的增强相经常被盐膜覆盖,削弱了增强效果。
而且制备的颗粒增强铝基复合材料在弹性模量、抗拉强度和耐磨性较大程度提高的同时,塑性下降;反应过程中有大量气体逸出,需良好的通风装置;关于原位反应的生成温度都不确定,800℃还是750℃,没有定论;反应温度过高,对增强颗粒形貌控制不利,而且恶化了铝液质量;制备的颗粒体积分数较低;且形成的液态渣清除困难,并对坩埚及操作工具有腐蚀作用;本实验选用Al-K2ZrF6-X(X=B、B2O3 、KBF4)反应体系,以纯铝、2124铝为基体,反应生成Al3Zr+ZrB2颗粒增强铝基复合材料。
初步拟用K2ZrF6 与KBF4 等混合盐与铝基体进行原位反应,通过改变Zr:B原子比,可以得到一元或二元组合的颗粒增强相。
(1)当Zr:B原子比为1:2时,熔体中可能发生的反应为:10Al+ 6KBF4 +3K2ZrF6=3ZrB2+K3AlF6+9KAlF4 (1)(2)当Zr:B原子比为1:1时,熔体中可能发生的反应为:23Al+ 6KBF4 +6K2ZrF6=3Al3Zr+3ZrB2+2K3AlF6+12KAlF4 (2)三、实验步骤一)制备前的准备1、2124铝合金准备与称量根据原位反应需要量以及坩埚大小等因素将2124铝合金锯成适当小块状(便于融化),称量后放入坩埚,将电阻炉温度设定750 o C左右后加热升温。
颗粒增强铝基通讯复合材料研究进展

刚度高 、热稳定性好 、耐磨性 好 、抗 腐蚀 、抗 疲 劳、密度
小 、不吸潮 、不老 化等 优 点_ ,是一 种 优 良的 结构 材 料。 1 ] 它不仅满足 了航 空航天 、能 源、高精 度机床 、尖 端武 器及 汽车等高端领域对材 料高性 能的要求 ,而且材料 的各 向同 性还使得材料可 以使用 传统 的金属加 工工艺 进行加 工 。所 有这些优点都使 P AMC 在高 、精 、尖领域 以及通讯 设施 R s
高温合成 法、原位热压放热反应合成 法、放热 弥散技术 、反应 自发浸渗技术等工艺 。对各工艺做 了详细的介 绍 ,指 出了未
来 的发 展 方 向 。
关 键 词 :颗 粒 增 强 ;制 备 工 艺 ;强 制 加 入 ;原 位 反 应
中 图分 类 号 :TB 3 3
文 献 标 识 码 :A
越 大 。根 据 文献 _ 可 知 颗 粒 的 直 径 、 间 距 以 及 体 积 分 数 之 2 ]
2 1 2铸 造 法 ..
铸 造 法 是 液 态 法 ( 融 金 属 加 工 法 ) 的 主 要 方 法 ,其 熔
关键是把 固相增强 颗粒均匀 地散布 于液态铝 中 ,并使 其最 终弥散地 分布在所 形成 的固态基体 中。铸造法 按增强 材料 与金属液体的混合 方式 不同 ,可分 为搅拌铸造 、正 压铸造 、 负压铸造等方法 。 2121 . . . 搅拌铸造法 目前 所采用的有液态机械搅 拌法及半 固态机械搅 拌法 。 液态机械搅拌法是通过搅拌 器 的旋 转运动使 增强材料 均匀 分布在液体中 ,然后浇注 成型 。此 法所用设 备 简单 ,操作 方便 ,但增强颗粒不易与 基体材料 混合 均匀 ,且材 料的 吸 气较严重 。半固态搅拌法是 利用合 金在 同液 温度 区间经搅 拌后得到的流变性质 ,将 增强颗粒 搅人 半 固态 熔液 中 ,依 靠半固态金属的粘性阻止 增强颗粒 因密度 差而浮沉 来制备 复合材料 。此法能获得增 强颗粒均 匀分 布的复 合材料 ,但
- 1、下载文档前请自行甄别文档内容的完整性,平台不提供额外的编辑、内容补充、找答案等附加服务。
- 2、"仅部分预览"的文档,不可在线预览部分如存在完整性等问题,可反馈申请退款(可完整预览的文档不适用该条件!)。
- 3、如文档侵犯您的权益,请联系客服反馈,我们会尽快为您处理(人工客服工作时间:9:00-18:30)。
材料的铸态组织,其晶粒比图la的明显细小些,属
等轴晶,且大小均匀。其组织被细化的机制是:因为
Ti与灿均为面心立方晶格,所以Ti可作为晶核,使
形核率大大增加,所以使晶粒细化。可见增强相的 加入提高了复合材料的磨损性能。图lc可观察到 未加原位颗粒的A1.Cu基体合金组织,基本由蔷薇 形晶粒组成,其中含有少量的等轴晶。如图ld所 示,当在合金中加入原位灿:O,颗粒后,合金组织中 等轴晶数量有所增多,表明原位Al:o,颗粒对合金 组织具有一定的细化作用,但对合金组织球化的效 果不显著。表明晶粒形貌还与浇注温度及凝固前沿 的温度梯度、散热条件等有关。在相同的温度进行 浇注时,加入原位m:O,颗粒的刖一cu合金中的形核 数量较单纯的m.cu合金要多,但是原位颗粒的加 入不能改变晶核的长大方式,也即固液前沿的温度 梯度及散热条件没有改变,所以长大以后的晶粒组 织的形貌基本相似。比较图1b与图ld可见,图b 的晶粒更细小,且基本呈等轴晶,说明原位颗粒Tic 对组织的细化作用比m:o,的细化作用强。
万方数据
磨损质最损失增加到最大值,此时其磨损性能最差; 其后随转速的继续增加磨损量急剧降低,在400
min r/
罔4h为加入Al,O,颗粒后转速和载衍对Al:O,/AI— cu复合材料磨损量的影响,由此网可看到,对于 Al:O,/Al—cu复合材料,其磨损量随转速的增加基本 呈下降趋势(除40
N、300
Hui—IIlinl
nlat血c伽posite
h鹏been pmduced by in—situ reactiVe near-liquid
technique.Its c嬲ting rIlicmstmcture
h器be朗锄alyzed卸d
t11e sliding attIition
ch锄cter
of tIle composite h嬲been checked.711le results show that the in—situ
硎复台材料。,采用棚同的熔铸T艺骞数,制备不禽
后,机加1‘墟讲8
4 75
mm×12
7
mm,其r11端酃1}径为
mm的球冠网棒状的销试样。摩擦丁作盘由45 7洲n.内径为十16
1
钢制造.经淬火处理.表而硬廑为¨Rc“.Jt外往为
m3l
mm.JI;(度10㈨采川感
N、20 N、30
{I^{”、J
毋为0
mz的sP200I电f分析天平称城测定钠试
(I)将’n耢(小于50岬),石器粉(小于75
"1).^l粉(小于75岬,)按一定比例往混耪机内混合
均匀,井压制成加一x20…15一的预栅块{;}
H{:将H}埚巾的椰锅台金升温至990℃.儿J彳J疑钟
原位反应生成*c颗牲.适当搅拌使j#蜓加均匀地分
艰将规定监的琐热的便糊块JK人此台金熔体・I・.湎过
hjⅥi J‘}l
烊的Jff撇峨ht损煲 脚拟试验所川的II:旭n分圳址10
N、40 ∥_n…400∥-●1¨1
N.谜度分别肚l∞∥m…、2㈣∥川¨、3(10
∞1Ⅲ^目堪铸¥##的∞女
万方数据
态组织,其晶粒大,呈蔷薇状,且大小不均;而图lb 是经原位反应近液相线铸造所得的Tic/7075复合
图2所示是Tic/7075复合材料及灿:0,/Al—Cu 复合材料的xRD衍射图。图2a是TiC/7075复合材 料的x射线衍射谱,根据衍射谱中各衍射峰值所对 应的20角,查PDF卡片后发现,其中主要是灿、TiC 两种物相的x射线衍射特征峰;图2b所示是舭:O,/ 刖.cu复合材料的x射线衍射谱,根据衍射谱中各 衍射峰值所对应的20角,查PDF卡片后发现,其中 主要是灿、cuAl:及灿:03等3种物相的x射线衍射 特征峰。说明原位反应确实生成了Tic颗粒及 m,O,颗粒。 2.2颗粒Tic和舢:O,对材料磨损性能的影响 图3为颗粒Tic对材料磨损性能的影响,图3a 为未加TiC颗粒时转速和载荷对7075铝合金磨损 量的影响,由此图可见,随着转速的增加,7075铝合 金的磨损量逐渐增高,这说明随着转速的增加,基体 材料的磨损量均增大,基体材料的磨损性能较差。 图3b为加入Tic颗粒后转速和载荷对Tic/ 7075复合材料磨损量的影响,由此图可看到,对于 Tic/7075复合材料在4种不同载荷的情况下,其磨 损量随转速的变化趋势基本相同,即磨损量先随转 速的提高而增加,当转速增加到200r/min左右时,
雠
丽
茸●骣警
衍射角20H。) a—TiC,7cr75合金复合材料
转速,(r・nlin。’)
_堋5铝合金
∞
倒 氍
{ ●
骣 盥
衍射角2口,(。) b_^J20/灿一cu合金复合材料
图2
b_.Ti洲5复合材科
图3转速和薮荷对材料磨损量的影响(颗粒为Tic)
转述,(r・min。)
TiC厂聊O及A120,/舢一Cu复合材料XRD衍射图
原位颗粒对铝基复合材料组织及磨损性能的影响
许 萍1,王峰2,王彦青1,刘慧敏1
(1.内蒙古工业大学材料科学与工程学院,内蒙古呼和浩特01005l; 2.内蒙古工业大学机械学院,内蒙古呼和浩特010051)
摘要:采用原位反应近液相线铸造法制备铝基复合材料,分析其铸态组织,测试不同条件下铝基合金的滑动磨损特 性。结果表明,原位Tic和A120,颗粒对铝合金的铸态组织均具有细化作用。在同等条件下(转速或压力相同)复合 材料的磨损性能优于基体材料,这说明原位颗粒的加入显著提高了材料的磨损性能,复合材料比基体的磨损性能提 高了1.5—4倍;且复合材料的磨损量随着载荷的增加而增大,随着转速的升高而减小,它在高速低载条件下表现出 较好的摩擦磨损特性。 关键词:原位颗粒;铝基复合材料;摩擦磨损
中图分类号:’l'G146.2;1粥3l
文献标识码:A
文章编号:100r7—7235(2011)05—0058一05ide
admti伽s佃Inicmsbm咖他and attri60n
proper哆of
xu PiIl91,wANG
al删【Ilj.m哪啪trix c伽pDsite
200 r/min~200
r/min条件外),而且在相
同条件(相同载荷)下,Al:O,/Al—Cu复合材料的磨损 量始终低于基体的磨损量。这说明相同磨损条件 下,Al:o,/A1.cu复合材料的磨损性能要优于Al—cu 合金的,且转速越高,这种优势越明显。 由图3和图4可看出,在相同转速下载荷对 7075合金、Tic/7075复合材料及A1.Cu合金、A120,/ Al—Cu复合材料磨损量的影响。随着载荷的增加,四 种材料的磨损量均呈上升趋势。这是因为低载荷 时,复合材料中的硬质颗粒具有承载属性,当软基体 在外力作用下被磨损后,颗粒将凸显在试样表面上, 承受大部分载荷,有利于阻止软基体直接参与摩擦 过程,所以低载荷时复合材料具有较好的磨损性能, 但随着载荷的增大,磨面上的颗粒将在高的表面切 应力作用下发生破碎,同时表层上一些与基体结合 不牢同的颗粒也会从接触面上剥落下来,颗粒因断 裂或者脱落不能承受载荷,导致摩擦面直接与基体 合金接触,使得磨损加剧。由此表明复合材料适合 在低载荷摩擦条件下应用。 由图3、图4还可看出,复合材料始终比基体合 金的磨损量小,而且基体合金磨损量的上升幅度明 显比复合材料的大得多。譬如由图3可见,当转速
Fen92,wANG Y卸一qin91,uu
0f
(1.S洲硝ma删Sdenoe柚d勘-gi鹏e而唱,I加盯M伽190Iia Ul删ty,H枷010惦l,嘶; 2.s州of Medh岫I b晒鹏盯萱ng,嘶M帅窖0lia uniw商ty T|曲肿Io野,Hu岫oI olo惦l,蛐)
Abst瑚Ict: pha8e c嬲ting muⅡlinum
r/min),在
r/min时磨损量达到峰值;随着转速继续增大。
磨损表面温度升至足够高,形成氧化膜,完整而致密 的氧化膜作为保护层可隔离摩擦副的直接接触,从 而使磨损量随转速的进一步增加而降低。氧化加 剧,氧化层增厚,隔离摩擦副接触的作用进一步增 强,故磨损量进一步降低。 图4为颗粒Al:O,对材料磨损性能的影响,图 4a为未加Al:O,颗粒时转速和载荷对A1.cu合金磨 损量的影响,由此图可见,随着转速的增加,基体合 金的磨损量逐渐增高,这说明随着转速的增加.基体 材料的磨损量均增大,基体材料的磨损性能较差。
TiC锄d
灿203 p枷cles c粕refine 锄ce pmpe啊of the comp鸺ite
tatiIlg
me c鹪tingⅡlicmstmcture of the aluIIIinum auoy;the wear他sist一 is bener the
veloc时,it
is
me龃tllat
tll锄that ofⅡ嫩ri】【alloy under tlle s砌e load粕d酚 additi∞of in—situ panicles increases tlle we盯resistance
composite;attrition lose
金属基复合材料通常是把金属材料的优良塑性
并获得了长足发展,这是由于颗粒增强铝基复合材 料具有高的比强度、比刚度,优良的高温力学性能和 耐磨性,并且价格便宜,适于批量生产等优点,在航
和增强体承受载荷的能力结合起来¨4’。在各种金
属基复合材料中,颗粒增强铝基复合材料受到青睐 收稿日期:加11一03—0l
n寸磨损量最小,此时其磨损性能最好,这说明
TiC/7075复合材料在高速下表现}{_;较好的摩擦磨损 特性。由此可见。Tic/7075复合材料在高速的情况 下磨损性能较好。分析认为,在干摩擦条件下,大量 摩擦热使摩擦副接触表面的形变Ⅸ域发生回复和再 结晶,硬度下降,从而抵消形变强化作用,导致磨损 质量损失增大(转速在100
to
obvio吣ly;tlle we盯resist锄ce