盲埋孔技术
盲埋孔技术
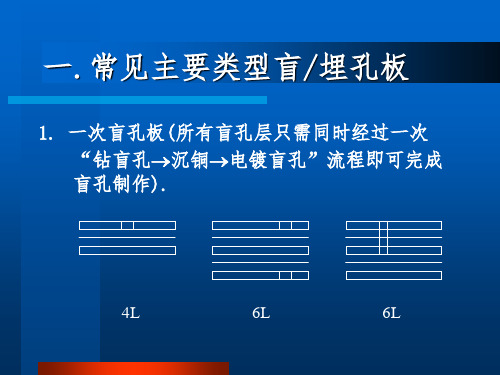
b.L1L5- 盲孔电镀: b.L1-2 & L5-6盲孔电镀: 根据lot卡及MI要求,选择电镀盲孔方法( lot卡及MI要求 根据lot卡及MI要求,选择电镀盲孔方法(lot 卡及MI会指明),根据板厚及盲孔孔径一般有 卡及MI会指明),根据板厚及盲孔孔径一般有 MI会指明),根据板厚及盲孔孔径 三种方法可选择: 三种方法可选择: - L1-2 & L5-6全铜面与盲孔一起板电. L1L5- 全铜面与盲孔一起板电. L1,L6面贴膜 整面干膜曝光(不用菲林), 面贴膜, - L1,L6面贴膜,整面干膜曝光(不用菲林), L2,L5大铜面与盲孔一起板电 大铜面与盲孔一起板电. L2,L5大铜面与盲孔一起板电. L1,L6贴干膜 用盲孔开窗点菲林曝光, 贴干膜, - L1,L6贴干膜,用盲孔开窗点菲林曝光,冲 影后,L2,L5大铜面与盲孔一起板电 大铜面与盲孔一起板电. 影后,L2,L5大铜面与盲孔一起板电.
一.常见主要类型盲/埋孔板 常见主要类型盲/
1. 一次盲孔板(所有盲孔层只需同时经过一次 一次盲孔板( 钻盲孔→沉铜→电镀盲孔” “钻盲孔→沉铜→电镀盲孔”流程即可完成 盲孔制作). 盲孔制作).
4L
6L
6L
二次盲孔板(需经过两次“钻盲孔→沉铜→ 2. 二次盲孔板(需经过两次“钻盲孔→沉铜→ 电镀盲孔”流程才可以完成盲孔制作). 电镀盲孔”流程才可以完成盲孔制作).
(3).流程解析: (3).流程解析: 流程解析 a.钻L1-2&L7- 盲孔: a.钻L1-2&L7-8盲孔: L1-2&L7- 盲孔钻带须加补偿. - L1-2&L7-8盲孔钻带须加补偿. 板边须有层数标志. - 板边须有层数标志. b.L1-2&L7-8盲孔电镀: b.L1-2&L7- 盲孔电镀: 与正常图电要求可能不一样,须依lot lot卡 - 与正常图电要求可能不一样,须依lot卡 MI要求做 要求做. 及MI要求做.
盲埋孔技术学习

埋盲孔技术
•埋 盲 孔 板 设 计 建 议
孔与线路的隔离 孔到线条及焊盘等图形间距>=0.25mm 孔内层隔离盘直径>=钻刀直径+0.6mm 放置内层隔离盘时应注意隔离盘之间间距。
常见设计失误示例:
第14页/共17页
埋盲孔技术
•埋 盲 孔 板 设 计 建 议
空白区设计要点 •内 层 不 要 留 大 面 积 的 基 材 区 , 否 则 板 内 应力不均匀,易翘曲,压板时铜箔易起 皱;
第11页/共17页
埋盲孔技术
•埋 盲 孔 板 设 计 建 议 1、金属化孔与线的连接 金属化孔通过焊盘与线连接: 设计焊环宽度=最小完成焊环宽度+孔位公差+蚀刻公差 焊盘直径=钻刀直径+2 x 最小完成焊环宽度+孔位公差+蚀刻公差
最小完成焊环宽度:0.025mm (IPC二级标准) 孔位公差:+/-0.075mm 蚀刻公差:+/-0.025mm
多次层压盲孔板
HDI激光孔板 第8页/共17页
埋盲孔技术
•埋 盲 孔 板 设 计 建 议
1、层结构最好为中心对称以防止因涨缩不一致导致PCB板严重翘曲。 2、尽量使用一种芯板厚度。 3、内层尽量使用一种铜厚,芯板两面铜厚尽量一致。 4、芯板与半固化片尽量使用常用规格。 5、埋孔孔径,建议0.30mm-0.50mm,过大或过小都不利于树脂塞孔; 6、埋盲孔最小焊环0.15mm,激光盲孔,最小焊环0.10mm
第10页/共17页
埋盲孔技术
•埋 盲 孔 板 设 计 建 议
1、层结构最好为中心对称以防止因涨缩不一致导致PCB板严重翘曲。 2、尽量使用一种芯板厚度。 3、内层尽量使用一种铜厚,芯板两面铜厚尽量一致。 4、芯板与半固化片尽量使用常用规格。 5、埋孔孔径,建议0.30mm-0.50mm,过大或过小都不利于树脂塞孔; 6、埋盲孔最小焊环0.15mm,激光盲孔,最小焊环0.10mm
四层PCB之过孔、盲孔、埋孔
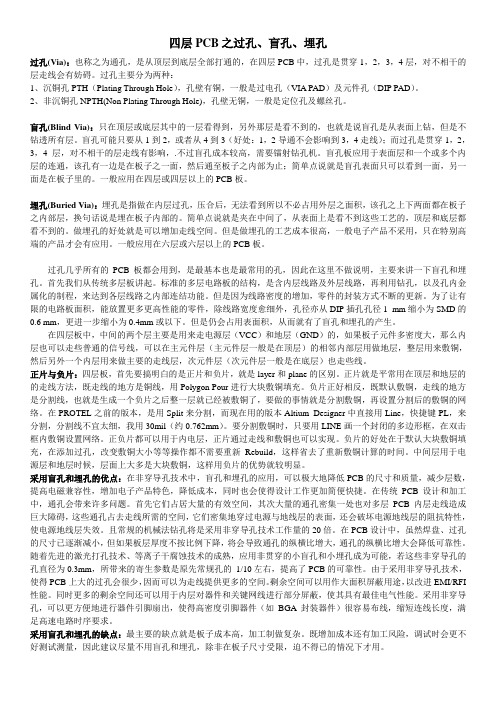
四层PCB之过孔、盲孔、埋孔过孔(Via):也称之为通孔,是从顶层到底层全部打通的,在四层PCB中,过孔是贯穿1,2,3,4层,对不相干的层走线会有妨碍。
过孔主要分为两种:1、沉铜孔PTH(Plating Through Hole),孔壁有铜,一般是过电孔(VIA PAD)及元件孔(DIP PAD)。
2、非沉铜孔NPTH(Non Plating Through Hole),孔壁无铜,一般是定位孔及螺丝孔。
盲孔(Blind Via):只在顶层或底层其中的一层看得到,另外那层是看不到的,也就是说盲孔是从表面上钻,但是不钻透所有层。
盲孔可能只要从1到2,或者从4到3(好处:1,2导通不会影响到3,4走线);而过孔是贯穿1,2,3,4层,对不相干的层走线有影响,.不过盲孔成本较高,需要镭射钻孔机。
盲孔板应用于表面层和一个或多个内层的连通,该孔有一边是在板子之一面,然后通至板子之内部为止;简单点说就是盲孔表面只可以看到一面,另一面是在板子里的。
一般应用在四层或四层以上的PCB板。
埋孔(Buried Via):埋孔是指做在内层过孔,压合后,无法看到所以不必占用外层之面积,该孔之上下两面都在板子之内部层,换句话说是埋在板子内部的。
简单点说就是夹在中间了,从表面上是看不到这些工艺的,顶层和底层都看不到的。
做埋孔的好处就是可以增加走线空间。
但是做埋孔的工艺成本很高,一般电子产品不采用,只在特别高端的产品才会有应用。
一般应用在六层或六层以上的PCB板。
过孔几乎所有的PCB板都会用到,是最基本也是最常用的孔,因此在这里不做说明,主要来讲一下盲孔和埋孔。
首先我们从传统多层板讲起。
标准的多层电路板的结构,是含内层线路及外层线路,再利用钻孔,以及孔内金属化的制程,来达到各层线路之内部连结功能。
但是因为线路密度的增加,零件的封装方式不断的更新。
为了让有限的电路板面积,能放置更多更高性能的零件,除线路宽度愈细外,孔径亦从DIP插孔孔径1 mm缩小为SMD的0.6 mm,更进一步缩小为0.4mm或以下。
盲埋孔PCB的制作细节描述
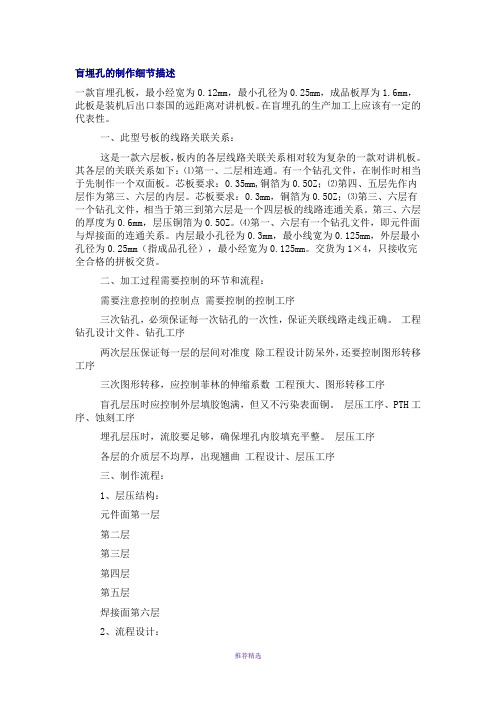
盲埋孔的制作细节描述一款盲埋孔板,最小经宽为0.12mm,最小孔径为0.25mm,成品板厚为1.6mm,此板是装机后出口泰国的远距离对讲机板。
在盲埋孔的生产加工上应该有一定的代表性。
一、此型号板的线路关联关系:这是一款六层板,板内的各层线路关联关系相对较为复杂的一款对讲机板。
其各层的关联关系如下:⑴第一、二层相连通。
有一个钻孔文件,在制作时相当于先制作一个双面板。
芯板要求:0.35mm,铜箔为0.5OZ;⑵第四、五层先作内层作为第三、六层的内层。
芯板要求:0.3mm,铜箔为0.5OZ;⑶第三、六层有一个钻孔文件,相当于第三到第六层是一个四层板的线路连通关系。
第三、六层的厚度为0.6mm,层压铜箔为0.5OZ。
⑷第一、六层有一个钻孔文件,即元件面与焊接面的连通关系。
内层最小孔径为0.3mm,最小线宽为0.125mm,外层最小孔径为0.25mm(指成品孔径),最小经宽为0.125mm。
交货为1×4,只接收完全合格的拼板交货。
二、加工过程需要控制的环节和流程:需要注意控制的控制点需要控制的控制工序三次钻孔,必须保证每一次钻孔的一次性,保证关联线路走线正确。
工程钻孔设计文件、钻孔工序两次层压保证每一层的层间对准度除工程设计防呆外,还要控制图形转移工序三次图形转移,应控制菲林的伸缩系数工程预大、图形转移工序盲孔层压时应控制外层填胶饱满,但又不污染表面铜。
层压工序、PTH工序、蚀刻工序埋孔层压时,流胶要足够,确保埋孔内胶填充平整。
层压工序各层的介质层不均厚,出现翘曲工程设计、层压工序三、制作流程:1、层压结构:元件面第一层第二层第三层第四层第五层焊接面第六层2、流程设计:工程设计时先开两个芯板,第一个芯板是1-2层,按第一个钻孔文件进行钻孔盲孔。
并按普通双面板的工艺流程制作到中检经过AOI存放;第二芯板是4-5层,开好一个芯板,按普通四层板的芯板制作工艺制作到中检经过AOI。
先将第二个芯板进行层压后,再按第二个钻孔文件钻埋孔,制作第3-6层的通孔和线路,此时按普通四层板的工艺经过除胶渣,制作3-6层的线路,到中检AOI。
盲埋孔(HDI)板制作能力及设计规范
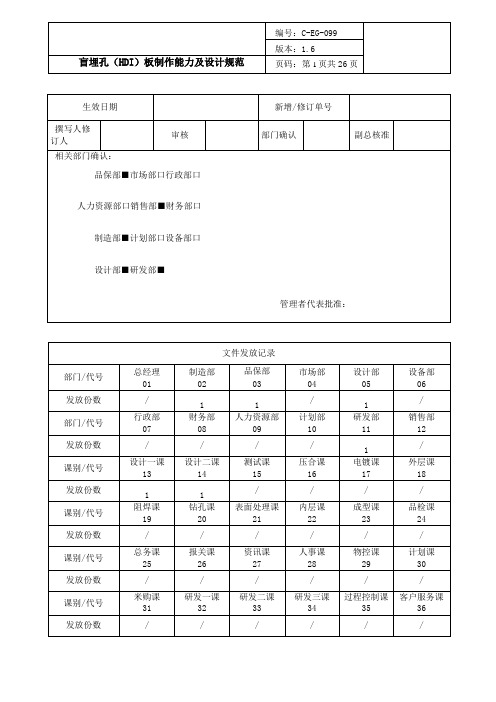
目录制订我司盲埋孔(HDI)板的流程及设计规范。
2.0范围:适用于我司“3+N+3”以内的盲埋孔(HDI)板的制作。
3.0职责:研发部:更新制作能力,制定并不断完善设计规范,解决该规范执行过程中出现的问题。
设计部:按照工艺要求设计并制作相关工具,及时反馈执行过程中出现的问题;负责对工程设计及内层菲林进行监控,及时提出相关意见或建议。
品保部:发行并保存最新版文件。
市场部:根据此文件的能力水平接订单,及向客户展示本公司的制作能力;收集客户的需求,及时向研发部反馈市场需求信息。
4.0指引内容:4.1盲埋孔“阶数”的定义:表示其激光盲孔的堆迭次数(通常用“1+N+1”、“2+N+2”、“3+N+3”等表示)、或某一层次的最多压合次数、或前工序(含:内层一压合一钻孔)循环次数,数值最大的项目则为其阶数。
4.2盲埋孔“次数”的定义:表示一款盲埋孔(HDI)板的压合结构图中所包含的机械钻盲埋孔次数和激光钻盲埋孔次数的总和(如同一次压合后的两面均需激光钻孔,则按盲埋两次计。
但计算钻孔价钱时只按一次激光钻孔的总孔数或一次钻孔的最低消费计)。
4.3盲埋孔“阶数”和盲埋孔“次数”的示例:4.3.1纯激光钻孔的双向增层式叠孔盲埋孔(HDI)板结构图示例盲埋孔阶数1盲埋孔阶数2盲埋孔阶数3阶数表示法1+2+1阶数表示法2+2+2阶数表示法3+2+3盲埋孔次数2盲埋孔次数4盲埋孔次数6编号:C-EG-099版本:1.6盲埋孔(HDI )板制作能力及设计规范页码:第5页共26页4.3.3 简单混合型的双向增层式盲埋孔(HDI )板结构图示例(激光盲孔为错位孔)盲埋孔阶数 1 盲埋孔阶数 2 盲埋孔阶数3 阶数表示法1+2+1 阶数表示法 2+2+2 阶数表示法3+2+3 盲埋孔次数 3 盲埋孔次数 5 盲埋孔次数 7盲埋孔阶数1盲埋孔阶数2盲埋孔阶数 3盲埋孔阶数1 阶数表示法1+2+1盲埋孔次数3盲埋孔阶数2 阶数表示法2+2+2 盲埋孔次数5盲埋孔阶数3 阶数表示法3+2+3 盲埋孔次数74.3.2简单混合型的双向增层式盲埋孔(HDI )板结构图示例(激光盲孔为叠孔)4.3.4复杂混合型的双向增层式盲埋孔(HDI )板结构图示例(激光盲孔同时有叠孔和错位孔)阶数表示法1+2+1阶数表示法2+2+2阶数表示法3+2+3盲埋孔次数3盲埋孔次数5盲埋孔次数7盲埋孔阶数1 盲埋孔次数2 盲埋孔阶数2 盲埋孔次数4编号:C-EG-099 版本:1.6盲埋孔(HDI )板制作能力及设计规范页码:第6页共26页4.3.6 纯机械钻孔的双核双向增层式盲埋孔阶数结构图示例(含假层设计)4.3.7 纯机械钻孔的双核单向增层式盲埋孔阶数结构图示例盲埋孔阶数3 盲埋孔次数5盲埋孔次数1 盲埋孔次数2 盲埋孔次数3 rWFTTTTI盲埋孔阶数2 盲埋孔阶数2 盲埋孔次数3盲埋孔次数5盲埋孔次数6盲埋孔阶数14.3.5纯机械钻孔的盲埋孔次数结构图示例盲埋孔阶数1 盲埋孔阶数1 盲埋孔阶数3盲埋孔阶数1盲埋孔次数3 盲埋孔阶数2 盲埋孔次数6编号:C-EG-099 版本:1.6盲埋孔(HDI )板制作能力及设计规范页码:第7页共26页4.3.8 纯机械钻孔的双核单向增层式盲埋孔阶数结构图示例独立芯板和多次压合盲孔层混合压合时, 该独立芯板的涨缩值与盲孔层的涨缩值相 差较大,独立芯板越薄,差值越大盲埋孔次数64.3.9 复杂混合型的双向增层式盲埋孔板结构图示例14.3.10 复杂混合型的双向增层式盲埋孔板结构图示例2盲埋孔阶数3 盲埋孔次数9PPPP盲埋孔阶数 1 盲埋孔阶数2阶数表示法 1+2+1 阶数表示法 2+2+2 盲埋孔次数 3 盲埋孔次数 6盲埋孔阶数3 阶数表示法3+2+3 盲埋孔次数9盲埋孔阶数34.4备注:1)上表中的难度系数为基于相同层次相同材料无任何盲埋孔时的普通板的难度提升值2)盲埋孔板的制作难度系数=盲孔阶数难度系数+盲孔次数难度系数3)如同时存在激光钻盲孔和机械钻盲孔,其制作难度系数=激光钻盲孔+机械钻盲孔4)如树脂塞孔的通孔需做成“Via-in-PAD”设计,需单独再增加15%的难度系数5)如存在小于0.10mm的薄芯板电镀,每张芯板分别需单独再增加5%的难度系数2)表格中打“*”的,表示是可选择的步骤,或者当前面的副流程执行该步骤时、则后面相关某步骤可不执行。
工艺盲埋孔工艺流程
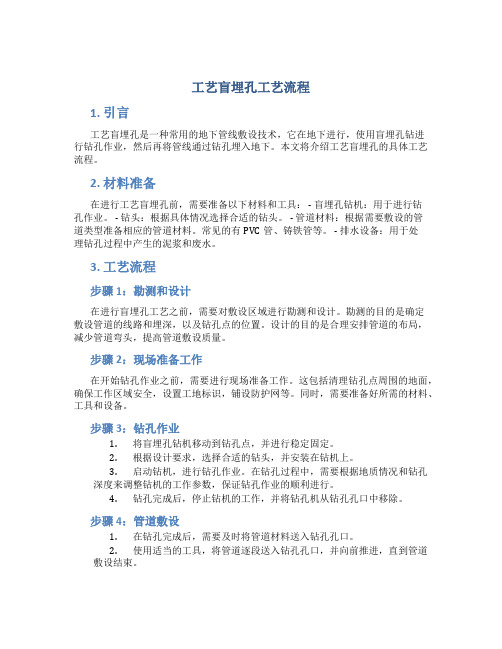
工艺盲埋孔工艺流程1. 引言工艺盲埋孔是一种常用的地下管线敷设技术,它在地下进行,使用盲埋孔钻进行钻孔作业,然后再将管线通过钻孔埋入地下。
本文将介绍工艺盲埋孔的具体工艺流程。
2. 材料准备在进行工艺盲埋孔前,需要准备以下材料和工具: - 盲埋孔钻机:用于进行钻孔作业。
- 钻头:根据具体情况选择合适的钻头。
- 管道材料:根据需要敷设的管道类型准备相应的管道材料。
常见的有PVC管、铸铁管等。
- 排水设备:用于处理钻孔过程中产生的泥浆和废水。
3. 工艺流程步骤1:勘测和设计在进行盲埋孔工艺之前,需要对敷设区域进行勘测和设计。
勘测的目的是确定敷设管道的线路和埋深,以及钻孔点的位置。
设计的目的是合理安排管道的布局,减少管道弯头,提高管道敷设质量。
步骤2:现场准备工作在开始钻孔作业之前,需要进行现场准备工作。
这包括清理钻孔点周围的地面,确保工作区域安全,设置工地标识,铺设防护网等。
同时,需要准备好所需的材料、工具和设备。
步骤3:钻孔作业1.将盲埋孔钻机移动到钻孔点,并进行稳定固定。
2.根据设计要求,选择合适的钻头,并安装在钻机上。
3.启动钻机,进行钻孔作业。
在钻孔过程中,需要根据地质情况和钻孔深度来调整钻机的工作参数,保证钻孔作业的顺利进行。
4.钻孔完成后,停止钻机的工作,并将钻孔机从钻孔孔口中移除。
步骤4:管道敷设1.在钻孔完成后,需要及时将管道材料送入钻孔孔口。
2.使用适当的工具,将管道逐段送入钻孔孔口,并向前推进,直到管道敷设结束。
3.在管道敷设的过程中,需要保持与钻孔孔口的对齐,并避免管道变形和损坏。
步骤5:测试和检查1.在管道敷设完成后,需要进行测试和检查,以确保管道的质量和安全性。
2.进行泄漏测试,检查管道连接是否牢固,排除漏水的可能性。
3.进行管道的通畅性测试,检查管道是否存在堵塞等问题。
4.对管道进行外观检查,检查管道表面是否存在破损或腐蚀。
4. 安全注意事项•在进行工艺盲埋孔工艺时,需要严格遵守相关的安全规定和操作规程。
盲埋孔板件加工工艺培训
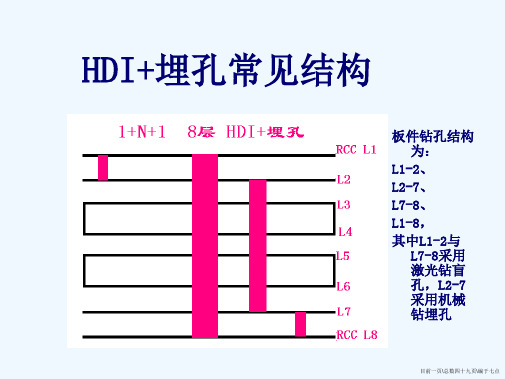
激光钻孔
激光钻孔: 1、激光参数 2、首件确认 3、检查 4、底铜厚度 5、孔型选择
目前十七页\总数四十九页\编于七点
激光钻孔后效果图
目前十八页\总数四十九页\编于七点
沉铜、电镀
沉铜、电镀 1、激光钻孔
后去毛刺 操作 2、ERP指示电 镀要求 3、铜厚
目前十九页\总数四十九页\编于七点
板件更改后叠层结构:
目前三十四页\总数四十九页\编于七点
多次层压板涨缩不一致
板件更改后的工艺流程: 1、板件的L6-10层取消两次压合。 2、板件的内层芯板预放比例只给出L2-3层的比例,
其余4-5层的内层芯板待L1-3压合后方可给出预放比 例。L6-10层的内层芯板预放比例根据L1-5层压合
后的涨缩值给出预放比例。
目前六页\总数四十九页\编于七点
开料
开料注意事项: 1、开料时核对
ERP指示与工卡。 2、板材的经纬方 向 3、开料后烘板
目前七页\总数四十九页\编于七点
内层图形
3. 內層線路製作(曝光)(Expose)
内层图芯板
的加工
2、薄板加工操作
Before Expose
Artwork (底片)
1、板件在经过多次层压后板件涨缩比例不一致
2、盲孔板经过沉铜电镀之后板件会产生涨缩的现 象
3、压合过的板件与未进行压合的板件涨缩值的区别 4、薄芯板的涨缩比例 5、不同板材之间的涨缩值区别
目前三十一页\总数四十九页\编于七点
多次层压板涨缩不一致
AC00100M板件叠层结构图:
目前三十二页\总数四十九页\编于七点
钻孔加工注 意事项:
1、根据不同 的材料选 择不同的 钻孔参数
盲埋孔讲解和总结
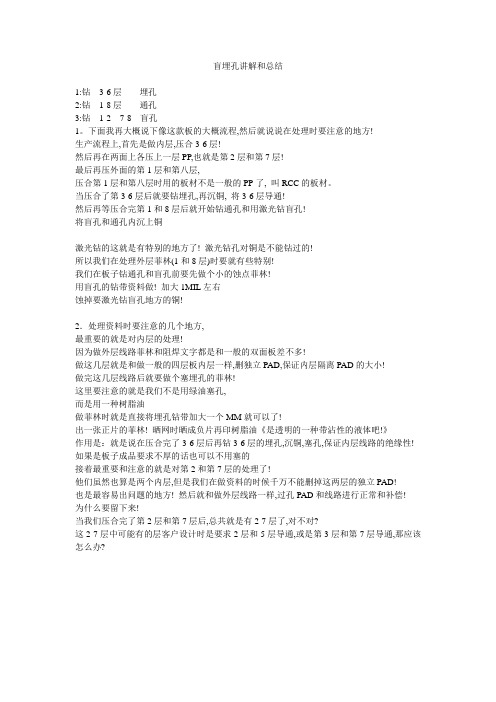
盲埋孔讲解和总结1:钻3-6层埋孔2:钻1-8层通孔3:钻1-2 7-8 盲孔1。
下面我再大概说下像这款板的大概流程,然后就说说在处理时要注意的地方!生产流程上,首先是做内层,压合3-6层!然后再在两面上各压上一层PP,也就是第2层和第7层!最后再压外面的第1层和第八层,压合第1层和第八层时用的板材不是一般的PP了, 叫RCC的板材。
当压合了第3-6层后就要钻埋孔,再沉铜, 将3-6层导通!然后再等压合完第1和8层后就开始钻通孔和用激光钻盲孔!将盲孔和通孔内沉上铜激光钻的这就是有特别的地方了! 激光钻孔对铜是不能钻过的!所以我们在处理外层菲林(1和8层)时要就有些特别!我们在板子钻通孔和盲孔前要先做个小的蚀点菲林!用盲孔的钻带资料做! 加大1MIL左右蚀掉要激光钻盲孔地方的铜!2.处理资料时要注意的几个地方,最重要的就是对内层的处理!因为做外层线路菲林和阻焊文字都是和一般的双面板差不多!做这几层就是和做一般的四层板内层一样,删独立PAD,保证内层隔离PAD的大小!做完这几层线路后就要做个塞埋孔的菲林!这里要注意的就是我们不是用绿油塞孔,而是用一种树脂油做菲林时就是直接将埋孔钻带加大一个MM就可以了!出一张正片的菲林! 晒网时晒成负片再印树脂油《是透明的一种带沾性的液体吧!》作用是:就是说在压合完了3-6层后再钻3-6层的埋孔,沉铜,塞孔,保证内层线路的绝缘性! 如果是板子成品要求不厚的话也可以不用塞的接着最重要和注意的就是对第2和第7层的处理了!他们虽然也算是两个内层,但是我们在做资料的时候千万不能删掉这两层的独立PAD!也是最容易出问题的地方! 然后就和做外层线路一样,过孔PAD和线路进行正常和补偿!为什么要留下来!当我们压合完了第2层和第7层后,总共就是有2-7层了,对不对?这2-7层中可能有的层客户设计时是要求2层和5层导通,或是第3层和第7层导通,那应该怎么办?。
- 1、下载文档前请自行甄别文档内容的完整性,平台不提供额外的编辑、内容补充、找答案等附加服务。
- 2、"仅部分预览"的文档,不可在线预览部分如存在完整性等问题,可反馈申请退款(可完整预览的文档不适用该条件!)。
- 3、如文档侵犯您的权益,请联系客服反馈,我们会尽快为您处理(人工客服工作时间:9:00-18:30)。
埋盲孔技术
•埋盲孔板设计建议
1、层结构最好为中心对称以防止因涨缩不一致导致PCB板严重翘曲。 2、尽量使用一种芯板厚度。 3、内层尽量使用一种铜厚,芯板两面铜厚尽量一致。 4、芯板与半固化片尽量使用常用规格。 5、埋孔孔径,建议0.30mm-0.50mm,过大或过小都不利于树脂塞孔; 6、埋盲孔最小焊环0.15mm,激光盲孔,最小焊环0.10mm
埋盲孔技术
•埋盲孔板设计建议
1、层结构最好为中心对称以防止因涨缩不一致导致PCB板严重翘曲。 2、尽量使用一种芯板厚度。 3、内层尽量使用一种铜厚,芯板两面铜厚尽量一致。 4、芯板与半固化片尽量使用常用规格。 5、埋孔孔径,建议0.30mm-0.50mm,过大或过小都不利于树脂塞孔; 6、埋盲孔最小焊环0.15mm,激光盲孔,最小焊环0.10mm
埋盲孔技术
•埋盲孔板设计建议
1、层结构最好为中心对称以防止因涨缩不一致导致PCB板严重翘曲。 2、尽量使用一种芯板厚度。 3、内层尽量使用一种铜厚,芯板两面铜厚尽量一致。 4、芯板与半固化片尽量使用常用规格。 5、埋孔孔径,建议0.30mm-0.50mm,过大或过小都不利于树脂塞孔; 6、埋盲孔最小焊环0.15mm,激光盲孔,最小焊环0.10mm
埋盲孔技术
•埋盲孔板设计建议
1、金属化孔与线的连接 金属化孔通过焊盘与线连接: 设计焊环宽度=最小完成焊环宽度+孔位公差+蚀刻公差 焊盘直径=钻刀直径+2 x 最小完成焊环宽度+孔位公差+蚀刻公差 最小完成焊环宽度:0.025mm (IPC二级标准) 孔位公差:+/-0.075mm 蚀刻公差:+/-0.025mm 当间距允许时常以加泪滴盘的 方式保证焊盘与线的安全电气 连接。
埋盲孔技术
• • • • 什么是埋盲孔 埋盲孔的加工方式 埋盲孔工艺特别控制点 埋盲孔设计建议
ห้องสมุดไป่ตู้
埋盲孔技术
•什么是埋盲孔?
随着电子技术的发展与人们对电子产品小型化、高度集成化的要求, 为提高PCB板布线密度,埋盲孔技术应运而生
埋盲孔技术
• 埋孔(Buried Vias):埋孔只有内层之间走线的过孔类型,从 PCB表面看不出来 • 盲孔(Blind Vias):盲孔是将PCB内层走线与外层走线相连的 过孔类型,不穿透整个板子
埋盲孔技术
•埋盲孔的加工方法
A、机械深度钻孔法 借助机械钻孔,采用定深钻孔方式,钻盲孔,达到外层与内层连通的方 法 缺点:产量低,一次只能加工一片,加工难度大,可靠性较低
1-3盲孔板
1-2盲孔板
埋盲孔技术
• 埋盲孔的加工方法
B、顺序层压法 通过多次压合,逐次将埋孔、盲孔、通孔做出 缺点:多次压合,涨缩不易控制,工艺流程长,无法制作交叠埋盲孔
埋盲孔技术
工艺能力 层次:18层max 最小孔径:0.10mm(激光钻孔) 0.15mm(机械钻孔) 厚径比:<12:1(机械钻孔),>0.75:1(激光钻孔)
埋盲孔技术
•埋盲孔设计建议
制作难度与成本,HDI激光埋盲孔板均高与多次层压埋盲孔 板.尽量避免设计交叠埋盲孔.
多次层压盲孔板
HDI激光孔板
埋盲孔技术
•埋盲孔板设计建议
金属化孔与大铜面的连接 a、直接连接 b、隔热盘连接(为了减少散热,使 热量更集中于焊锡) 开口宽度>=0.125mm 设计焊环宽度要求与金属化孔与线连 接的要求相同。 内径=钻刀直径+2x设计焊环宽度
埋盲孔技术
•埋盲孔板设计建议
孔与线路的隔离 孔到线条及焊盘等图形间距>=0.25mm 孔内层隔离盘直径>=钻刀直径+0.6mm 放置内层隔离盘时应注意隔离盘之间间距。 常见设计失误示例:
埋盲孔技术
•埋盲孔板设计建议
空白区设计要点 –内层不要留大面积的基材区,否则板内应 力不均匀,易翘曲,压板时铜箔易起皱; –外层线路要尽量均匀,不要留大面积的基 材区(可用铺辅助无功能的方盘填充), 否则电镀不均,PTH孔径、线路铜厚会相差 较大。
大面积基材,NG
设置铜皮,OK
2-4,4-8盲孔板
2-4盲孔板
埋盲孔技术
• 埋盲孔的加工方法
C、HDI增层法 以激光钻孔的方法,一层一层增加,为逐层压合法的升级片 缺点:设备要求高,电镀能力要求高,成本高
1+1+N+1+1结构 L1-2,L2-3盲孔
埋盲孔技术
• 中富埋盲孔工艺,采用逐次增层法与激光钻孔增层法 • 工艺控制
A、有专门的FA小组,统计多次压合系数,减小压合涨缩导致品质问题 B、X-ray打靶机与OPE冲孔机,保证各层对准度 C、高精度CNC钻孔机,保证钻孔精度 D、埋盲孔采用树脂塞孔工艺,减小爆板与孔无铜风险 E、CCD自动平行光曝光机,制作精细线条与高精度对位 F、填孔电镀工艺,提高HDI激光盲孔可靠度,并提高可焊接性。