设计潜在失效模式及后果分析(DFMEA
整车设计失效模式分析-DFMEA

有毒有害物质 检测
3
座椅VOC超标
2
按 2005/673/EC 有毒有害物质
设计
检测
3
动力系统匹配不 当
5
整车总布置报告
NVH测试
2
噪声大:
传动系统匹配不 当
4
整车总布置报告
NVH测试
4
驾驶员耳旁
噪声不合 格; 车内噪声不
顾客抱怨,引 起驾驶疲劳
6
S
合格;
行驶系统设计不 当
4
车身各总成刚度 设计值不足
1999测定;
S
制动系统设计不 合理
3
设计评审 与参考车型对比
3
制动异响
顾客抱怨制动 有异响
7
S
制动系统设计不 合理
4
设计评审 与参考车型对比
样车动态评价
4
灯光照度不 够
影响行车安 全,违反法规
9
R
灯光照明系统设 计不合理
3
计算校核设计评 审
按 GB 459994附录D测 定;
2
灯光指示和信号 报警系统设计不 3 设计评审
2
设计计算
按GB
2
T6323.6-1994
悬架匹配计算
测定;
3
FMEA日期
造型
车身造型不美观 5
不美观
造型不美观顾 客不满意
6
R
外装饰系统造型 美观
5
造型评审 造型评审
样车评价 2 样车评价 2
跑偏
制动时方向
侧滑
稳定性差 失去转向能力
9
影响乘员安全
S
制动系统泄露
3
设计评审 与参考车型对比 按 GB 12676-
DFMEA设计潜在失效模式及后果分析(Nanjing) 2013-09

G9
G8
G7
G6
G5
G4
G3
G2
G1
DFMEA策划 创建团队
输入
• 项目信息; • 项目时间进度; • 开发团队信息。
2013-9
输出
• DFMEA的零件清单; • 实施计划; • 核心团队的支持成员。
21
二. DFMEA策划及准备 STEP 2 – 创建团队 (G9-TG0)
牵头及负责人:DRE
设计潜在失效模式 设计潜在失效模式 及后果分析 DFMEA 及后果分析 DFMEA
2013-9
第一部分:FMEA发展和介绍 第二部分:DFMEA策划及准备 第三部分:DFMEA分析和实施 第四部分:注意事项和常见问题 第五部分:范例学习讨论
2013-9
2
一. FMEA发展和介绍 FMEA概念 Potential Failure Mode & Effect Analysis 潜在 “失效模式及后果分析”的首字母缩写 FMEA是一种普遍且重要的可靠性分策划及准备 DFMEA逻辑流程图:准备和实施
调研 以往的 失效模式 定义分析 范围: 方块图
准备 实施
潜在失效 后果 针对各 功能识 别潜在 失效模 式
严重度(S) 解决 问题 降低 风险
创建 DFMEA 团队
识别功能 需求
潜在失效 起因/机理
频度(O)
建议 措施
策划:确 定范围和 时间进度
G8 项目启动
G7 方案批准
G6 项目批准
G5 工程发布
G4
G3
G2
G1
战略立项
产品和 预试生产 试生产 正式投产 工艺验证
产品开发阶段:TG0 ~ TG2数据发布 工程发布 TG0发布 前期策划 DFMEA分析 确定 清单计划 DFMEA TG1版完成 DFMEA TG2版完成 DFMEA ESO版完成 TG1发布 失效分析和预防 TG2发布 根据验证结果更新 动态更新
设计失效模式及后果分析DFMEA管理程序

1.目的:确定与产品相关的设计过程潜在的失效模式,确定设计过程中失效的起因,确定减少失效发生或找出失效条件的过程控制变量并编制潜在失效模式分级表,为采取预防措施提供对策保存起吕2 年期限止文件终止丿机密等级密机密极机密生效日期作废日期作废人员修订履历版次修订页次修订内容修订日期0 全部初版发行1234567892.范围:本程序适用于新产品设计、产品改型以及应用环境发生变更时的样品试验阶段的FMEA分析。
3.定义:3-1.FMEA:指Failure Mode and Effects Analysis (失效模式及后果分析)的英文简称。
是一种分析技术,用以最大限度地保证各种潜在的失效模式及其相关的起因/ 机理已得到充分的考虑和论述。
3-3.DFMEA:设计潜在失效模式及后果分析。
3-4. 失效:在规定条件下(环境、操作、时间),不能完成既定功能或产品参数值和不能维持在规定的上下限之间,以及在工作范围内导致零组件损坏等现象。
3-5.严重度(S):指一给定失效模式最严重的影响后果的级别,是单一的FMEA范围内的相对定级结果。
严重度数值的降低只有通过设计更改或重新设计才能够实现。
3-6.频度(0:指失效原因/机理预计发生频度,分1到10级。
预防措施可降低发生频度。
3-7. 级别:用于区分部件、子系统、系统特性(例如:安全性/关键、重要、一般)3-8.探测度(D):评估在零部件离开制造现场前,现行控制方法对失效模式或失效模式的原因得到发现的可能性。
分为1 到10及。
检验能提高失效模式或失效原因的探测能力。
3-9.风险优先数(RPN:指严重度数(S)、频度数(0)及探测度数(D)三项数字之乘积。
4.权责:由产品开发部、生产部、工艺部门、品质部负责设计失效模式及后果分析(PFMEA的制定与管理。
开发工程师:负责DFMEA数据信息的统筹与收集。
各职能部门:负责各失效模式和后果分析相关工作配合和对策的实施。
5. 作业内容5-1.新项目立项后,在设计阶段图面设计之前产品开发工程师负责主导DFMEAJ、组实施DFMEA,并且在产品图样完成之前全部完成。
设计潜在失效模式DFMEA表

秦元礼 程济阳 黄文延 汪洋
严 重 潜在失效后果 度 S
承载力下降导致 变形,使承载物 跌落易伤人 承载力下降,易 折弯或变形
产品使用用途:成年人,快捷消费品。
特 性 别 级 现行设计 潜在失效 起因 控制预防
设计时根据测试标 准选取合理的材料 厚度 根据测试要求确定 钢带韧性 根据测试要求确定 螺丝及壁虎尺寸 根据设计要求确定 正确的开孔位置 根据设计要求确定 孔位尺寸 根据设计软件确定 合适的弧度 设计时根据运输测 试标准确定好防护 品种类及数量 设计时根据运输测 试标准确定好包装 箱纸质
第1页共1页
鑫鸿源五金塑胶制品厂
设计潜在失效模式及后果分析表(DFMEA)
产品名称: 产品编号: APQP小组: 窗帘杆 CLG-01 过程责任: 关键日期: 研发部 2011.04.04 编制人: DFMEA日期(编写): 黄文延 2011.04.14 DFMEA编号: 修订:
XHY/ENG-FMEA-001-A.0
措施执行效果 探测 度 D
3
项目
要求
潜在失 效模式
功能
钢带厚度 材料厚度不够
频 度 O
2
控制探测
组装成品的 承重模拟测 试 组装成品的 承重模拟测 试 组装成品的 承重模拟测 试 支架试装测 试 支架试装测 试 支架试装测 试
R P N
建议措施
责任人及主要控 制记录
采取的措施及 完成效果
S
O
D
R P N
8
2
4
64
7
2
3
42
8
2பைடு நூலகம்
3
48
3
2
3
18
防护品种 类及数量
电池管理系统BMS潜在失效模式及后果分析(DFMEA)

外部供电低于系统供电最 小电压
系统供电不足无法运行
5 ☆ 电源输入范围不满足指标要求
在指标范围内,选择宽范围输入 的电源模块
3
老化试验
3
45
23 BMS数据存储
数据存储
无法正常存储历史数据
历史数据无法正常保存和 分析
2 ☆ 存储芯片损坏
采用汽车级元器件设计 老化测试
3 老化试验 2 12
24
电源模块 符合技术要求
10
设计验证
1
70
34
绝缘电阻检测 功能
在充电、放电状态下对车 身与电池负极之间的电阻 进行实时检测
在充电、放电状态下,绝 缘采样值跳变
绝缘电阻检测阻值不准,造 成漏电检测误报,影响车 辆行驶
7
☆
平衡桥式绝缘方案设计中绝缘采集 回路滤波电容容值100NF偏小
新电路修改为10UF,功能要充分 进行环境实验验证,包括充电、 放电、高低温实验等
BMS温度采集电路分压电阻损坏或
温度传感器损坏
高低温测试
1 温度采集功能 温度进行实时检测,并且
7☆
精度符合技术要求
温度采集显示温度一直保 持不变,且显示数值与实 际不符
温度采集功能失效,导致 BMS无法检测到温度
BMS与温度传感器接触不良
老化测试 震动测试
2 震动试验 3 42
对电池总电压进行实时检 电池电压采集不到
对接触器失去部分控制, 导致其闭合后不能断开
电源系统一直和负载连 接,使电池一直处于放电 状态
6
高压回路接触器 对接触器实现完全控制, 对接触器失去部分控制导 电源系统和负载失去连
控制功能
包括闭合与断开
潜在失效模式及后果分析(DFMEA)

FMEA编号: 共 5页 , 第 1~5 页 编制人: FMEA日期(编制)2015.3.14 FMEA日期(修订) 2016.5.15 措施结果 责任及目标 建议措施 采取的措施 S O D 完成日期
RPN
胶带宽度不足 胶带宽度符合产品 要求,不可露铜线 。 绕线胶带
1、露铜线 2、造成耐压不良, 产品功能丧失 3、绕组之间安规距 离不足。
FMEA编号: 共 5页 , 第 1~5 页 编制人: FMEA日期(编制)2015.3.14 FMEA日期(修订) 2016.5.15 措施结果 责任及目标 建议措施 采取的措施 S O D 完成日期
RPN
含浸/烘烤
产品外观凡立水不 产品外观凡立水不能烘 烘干,不能粘手 干,粘手
1、磁芯、线圈松动 2、产品整机使用会 产生异音 3、绝缘度不足易产 生耐压不良或短路
1
20
含浸/烘烤
潜在失效模式及后果分析
(DFMEA)
项目名称:变压器类 核心小组: 过程 要求 功能 组长: 潜在 失效模式 潜在 失效后果 严 重 度 S 级 别 潜在失效 起因/机理 发 生 度 O 现行过程 控制预防 现行过程 控制探测 探 测 RPN 度 D 过程责任部门 :APQP小组 关键日期 : 2015.3.14
2
40
1、造成铜线上挡墙 2、安规距离不足 3、对功能无影响 5
1:选择挡墙厚度不合理 2:定义挡墙圈数不合理
2
50
理线
1、产品外观不符, 理线缠线不能超出 理线缠线超出线架凸点高 量产难度大,客户 线架凸点高度 度 装板浮高。
5
1:引出线股数太多; 2:引出线线径太大; 3:骨架凸点太低.
1:重新选择引出线股数; 5 2:重新选择引出线线径; 3:重新选择高凸点骨架.
失效模式及后果分析程序 - 新版2019(DFMEA)
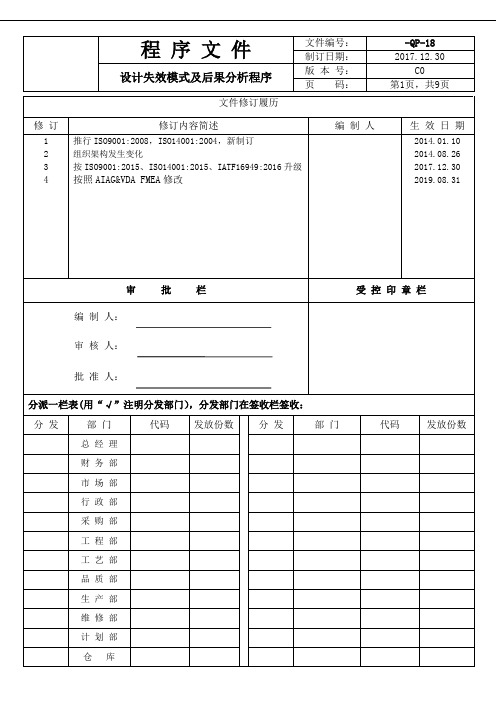
1.0目的在产品设计阶段,预先发现、评价产品可能潜在的失效与后果,及早找出能够避免或减少这些潜在失效发生的措施,并将此过程文件化,为以后的设计提供经验与参考。
2.0范围适用于产品设计中的设计失效模式及后果分析。
3.0职责3.1多方论证小组:负责制订DFMEA的各项内容及相关改进措施,建立纠正措施优先体系;当有新的失效模式出现时及时更改DFMEA。
3.2工艺部:主导多方论证小组分析并制订所有潜在失效模式及后果。
3.3各部门:参与DFMEA的制订和评估,相关纠正和预防措施的执行。
4.0定义4.1DFMEA:(Design Failure Mode& Effects Analysis)设计失效模式及后果分析.4.2顾客:顾客对DFMEA而言通常指“终端顾客”或“使用者”,但顾客也可能是法律法规要求4.3MSA:Measurement System Analysis(测量系统分析)包括准确性、线性、重复性、再现性、稳定性。
5.0流程无6.0内容6.1DFMEA制订说明:6.1.1工程部主导成立多方论证小组(即APQP策划小组);并确定DFMEA的实施项目。
多方论证小组根据客户的要求和生产加工情况,在APQP总进度中明确DFMEA项目的实施进度要求。
6.1.2多方论证小组组织品质部、工程部、生产部等相关部门的人员对整个生产流程进行评定。
6.1.3工程部针对过程失效模式和后果分析,确定相关过程的“严重度(S)”、“频度(O)”、“探测度(D)”,并通过S、O、D值的排列组合“措施优先级(AP)”,进行改进,编制DFMEA。
6.2在针对措施优先级(AP)行动时,需考虑以下因素:6.2.1严重度数高的(≥ 9)必须实施;6.2.2措施优先级(AP)为高(H)的优先实施;6.2.3措施优先级(AP)为中(M),但是易于实施,成本投入少的,优先实施。
6.2.4客户,项目小组,或者公司高层,在文件化的时候,提出采取改进措施的,给予实施;6.3工程部针对新产品、新材料、新技术应提交相关DFMEA资料。
dfmea潜在失效模式及后果分析案例

7
两侧导向筋强度不 足
CAE分析,导向筋 强度合理化 增加加强筋,提 高强度 连接处配合方式 选择合理
8
撞击导致结构破坏
8
连接处密封性差
密封性
手柄密封性 软管与软管连 不满足客户要 接管的密封性 求,影响手柄吸 差 尘效率 9 连接处密封性不足 增加密封件
裸机通过 重要部位断 需通过球 球击测试, 产品无法再使 裂(尤其是机 击测试 功能正常, 用 壳) 无断裂 电池包2000 电池包松脱或 次插拔寿命 电池使用效率 测试后挂靠 低 不牢 通过整机配 电池包撞墙 测试 机壳配合处断 裂
3
105
排除电池包倒扣位, 各暂定一个插拔力范 围。例3-5 kgf 1.参照样机考虑加弹 簧或弹片式减振结构
尺寸链分析计算保证尺 寸精度 尺寸链分析计算保证尺 寸精度 尺寸链分析计算保证尺 寸精度
检测插拔力 1.单边间隙 0.4mm以上 2.参照园林产 品
保证下盖与进 气口橡胶套翻 边配合无间隙 尘桶和下盖橡 胶密封圈尺寸 保证无间隙 分离管密封圈 翻边与尘桶之 间单边0.2mm过 盈 导流锥与橡胶 圈压装0.3mm过 盈 进气口与风机 橡胶套之间配 合单边过盈 过渡配合,IQC 尺寸全检 气阀密封圈喇 叭口做大,有 段直边配合 进气端两颗螺 丝柱保证高度 方向精度 密封圈与通风 盘内孔有单边 0.2mm过盈,检 测旋转力度 面接触部位开 槽加O型圈
8
A
1.塑件壳体加强筋 1.合理布设筋板 布设不合理 2.连接处强度薄 2.零件连接处强度 弱处加固 过于薄弱 1.机壳未做圆滑过 渡,磨损过大 2.电池包倒扣弹簧 疲劳 1.机壳参照园林 产品做圆滑过渡 2.选用成熟的电 池包 1.参照园林产品 机壳限位筋位强度 设计 2. 不够 配合尺寸计算累 积公差 1.参照园林产品 机壳与电池包卡扣 设计 2. 配合不当有干涉 配合尺寸计算累 积公差 机壳与电池包配合 配合尺寸计算累 间隙不当或无弹性 积公差 减震结构
- 1、下载文档前请自行甄别文档内容的完整性,平台不提供额外的编辑、内容补充、找答案等附加服务。
- 2、"仅部分预览"的文档,不可在线预览部分如存在完整性等问题,可反馈申请退款(可完整预览的文档不适用该条件!)。
- 3、如文档侵犯您的权益,请联系客服反馈,我们会尽快为您处理(人工客服工作时间:9:00-18:30)。
格式版本/修改状态:F/0 文件版本/修改状态:A/0
现行设计 潜在失效原 级别 因 控制预防 频 探测 控制探测 度 度 RPN 建议措施 责任人
初始编制日期 修订日期 共 页 页码: 实施结果 采取措施 完成日期 严重 度 频度
第
页
探测 度
RPN
编 制:
审 核:
批 准:
更改履历表
文件版本/ 修改状态 更改内容
生效日期
历次更改的记录,采用划改的细小变更不需要填写, 由划改人员在划改处签字确认(包括修改日期);重 大变更必须进行版本更新,并填写变更内容。
名称:设计潜在失效模式及பைடு நூலகம்果分析(DFMEA)
项目级别:系统□ 子系统□ 产品名称 零件号 功能 要求 潜在失效模式 车型 零部件□ 设计职责:技术中心 编制者: 关键日期: 潜在失效后 果 严重度 核心小组成 员 部 门 姓 名 电 话 工艺 质量 模具
文件编号:QR/HT-C2-018 项目经理