如何进行失效模式与影响分析资料讲解
14过程失效模式及影响分析程序

14过程失效模式及影响分析程序过程失效模式及影响分析(PFMEA)是一种用于识别和评估过程中潜在失效模式及其对产品或服务质量的影响的方法。
该方法通常用于制造业,但也可以适用于其他行业和领域。
在本文中,我们将详细介绍PFMEA的步骤和其在质量管理中的重要性。
PFMEA的步骤通常可以分为以下几个阶段:1.定义流程:首先,定义要分析的过程。
确定过程的输入、输出、活动和各个步骤的顺序。
确保所有相关的信息都被收集到。
2.识别失效模式:接下来,识别可能的失效模式。
这意味着确定在每个过程步骤中可能发生的失效或错误。
3.评估失效影响:对每个失效模式进行分析,评估其对产品或服务质量的潜在影响。
这包括确定失效概率、严重程度以及可能引起的其他影响。
4.确定前防措施:在这一阶段,确定如何避免或减轻失效模式带来的影响。
这可能包括改进过程步骤、引入检验或测试步骤、提高员工培训等。
5.评估现有控制措施:评估当前已经实施的控制措施,以防止失效发生或减轻其影响。
这可以涉及到质量管理体系和标准操作程序的审查。
6.重复前面的步骤:根据之前的评估结果,对过程重新进行评估和改进。
这可能包括对之前定义的失效模式和影响进行修订,并再次确定前防措施或现有控制措施。
PFMEA的实施可带来多个重要的优点和好处。
首先,它可以帮助组织识别和理解过程中的风险,并制定适当的控制措施。
其次,通过更好地理解过程和失效模式,组织可以采取措施来预防或减轻潜在的质量问题。
此外,PFMEA还可以提供一个系统的方法来持续改进过程,并减少产生次品或缺陷的概率。
在实施PFMEA时,需要注意以下几个方面。
首先,数据的准确性和完整性是非常重要的。
因此,确保收集到所有相关的信息和数据,以支持失效模式和影响的分析。
其次,要保持跨职能的合作和沟通。
PFMEA需要涉及多个部门和部门之间的合作,以确保全面的分析和控制措施的实施。
最后,PFMEA应该是一个持续的过程。
随着时间的推移,过程可能会发生变化,新的失效模式和影响也可能出现。
失效模式与效应分析程序FMEA资料
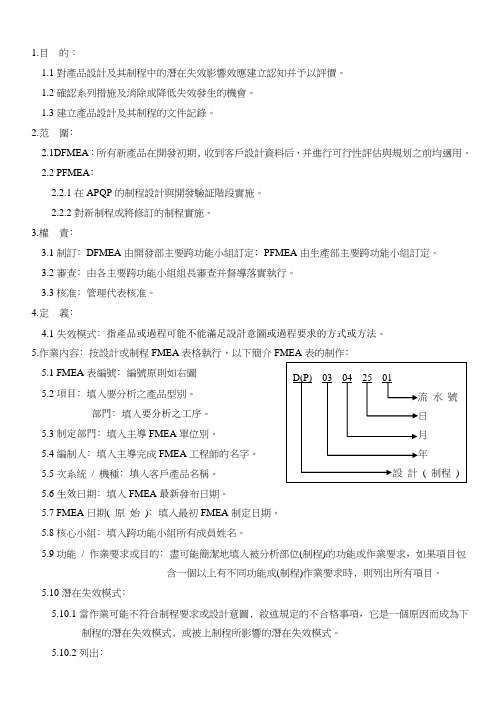
1.目的:1.1對產品設計及其制程中的潛在失效影響效應建立認知并予以評價。
1.2確認系列措施及消除或降低失效發生的機會。
1.3建立產品設計及其制程的文件記錄。
2.范圍﹕2.1DFMEA:所有新產品在開發初期﹐收到客戶設計資料后,并進行可行性評估與規划之前均適用。
2.2 PFMEA﹕2.2.1在APQP的制程設計與開發驗証階段實施。
2.2.2對新制程或將修訂的制程實施。
3.權責﹕3.1制訂﹕DFMEA由開發部主要跨功能小組訂定﹔PFMEA由生產部主要跨功能小組訂定。
3.2審查﹕由各主要跨功能小組組長審查并督導落實執行。
3.3核准﹕管理代表核准。
4.定義﹕4.1失效模式﹕指產品或過程可能不能滿足設計意圖或過程要求的方式或方法。
5.作業內容﹕按設計或制程FMEA表格執行,以下簡介FMEA表的制作﹕5.2項目﹕填入要分析之產品型別。
部門﹕填入要分析之工序。
5.3制定部門﹕填入主導FMEA單位別。
5.4編制人﹕填入主導完成FMEA工程師的名字。
5.5次系統/ 機種﹕填入客戶產品名稱。
5.6生效日期﹕填入FMEA最新發布日期。
5.7 FMEA日期( 原始)﹕填入最初FMEA制定日期。
5.8核心小組﹕填入跨功能小組所有成員姓名。
5.9功能/ 作業要求或目的﹕盡可能簡潔地填入被分析部位(制程)的功能或作業要求,如果項目包含一個以上有不同功能或(制程)作業要求時﹐則列出所有項目。
5.10潛在失效模式﹕5.10.1當作業可能不符合制程要求或設計意圖﹐敘述規定的不合格事項,它是一個原因而成為下制程的潛在失效模式﹐或被上制程所影響的潛在失效模式。
5.10.2列出﹕5.10.2.1每一潛在失效模式假設失效是將發生的﹐但不是必須發生的。
5.10.2.2盡可能敘述失效模式發生于某些作業條件下(如﹕壓力等)和在某些使用條件下(如﹕溫度,高度)。
5.10.2.3一般失效模式含如下各項﹐但不限于此﹕破損、變形、碰傷、錯位、裂紋等。
如何进行失效模式与影响分析(FMEA)
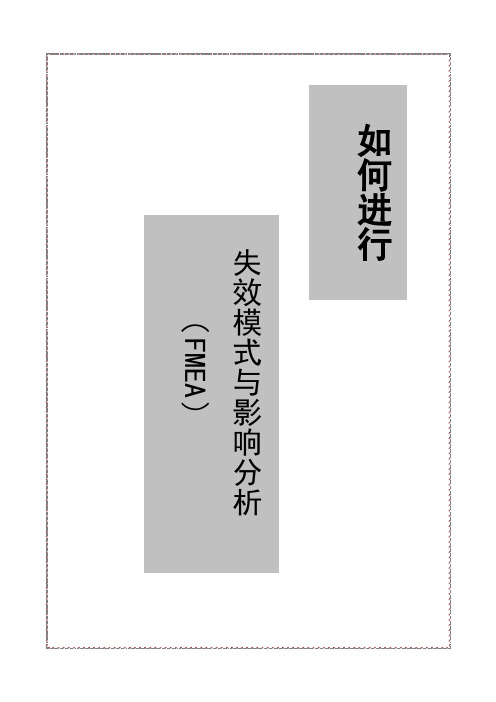
(9)有何改善方案。
3、风险优先数RPN。
RPN评估
影响/行动需求
1<RPN<50
对产品危害较小
51<RPN<100
对产品有中等危害,需进一步改善
101<RPN<1000
对产品有严重危害,需深入调查分析
4、FMEA的分类。
根据其用途和适用阶段不同,FMEA可分为:
(1)设计阶段FMEA(DFMEA-Design FMEA)。
2、松香发泡不良
发泡孔堵塞、发泡电机停止工作、松香变质
预热
1、预热温度过高
控制器故障、测定方法错误
2、预热时间过长
带速过低、传送带打滑
浸锡
1、锡面过低
未及时加锡、电机转速变化
2、浸锡时间过短
带速过度
3、浸锡进入角过小
传送带角度变化、板弯
4、锡液温度过高
控制器故障、测定方法错误
7、制作FMEA表(见第8页)。
潜在缺陷模式和影响分析是设计或制造过程中一项事前分析工作。通过FMEA可识别和评估在设计或工程中可能存在的缺陷模式及其影响,并确定能消除或减少潜在失效发生的改善措施从而防患于未然,尽可能降低各项缺陷成本,保证产品/服务问世即具有优异性能。
一、FMEA的开发与发展
20世纪50年代,美国格鲁曼公司开发了FMEA,用以飞机制造业的发动机故障预防,取得较好成果。20世纪60年代,美国宇航界实施阿波罗计划时,要求实施FMEA。
良好的测试
4
对性能有较小影响
微量缺陷1 in2000
测试可控制
5
对性能有影响
偶然性缺陷1 in500
不完全的测试控制
失效模式与影响分析FMEA
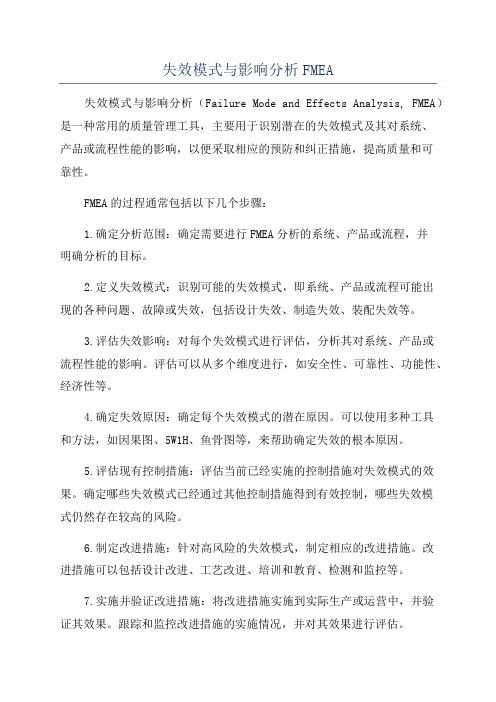
失效模式与影响分析FMEA失效模式与影响分析(Failure Mode and Effects Analysis, FMEA)是一种常用的质量管理工具,主要用于识别潜在的失效模式及其对系统、产品或流程性能的影响,以便采取相应的预防和纠正措施,提高质量和可靠性。
FMEA的过程通常包括以下几个步骤:1.确定分析范围:确定需要进行FMEA分析的系统、产品或流程,并明确分析的目标。
2.定义失效模式:识别可能的失效模式,即系统、产品或流程可能出现的各种问题、故障或失效,包括设计失效、制造失效、装配失效等。
3.评估失效影响:对每个失效模式进行评估,分析其对系统、产品或流程性能的影响。
评估可以从多个维度进行,如安全性、可靠性、功能性、经济性等。
4.确定失效原因:确定每个失效模式的潜在原因。
可以使用多种工具和方法,如因果图、5W1H、鱼骨图等,来帮助确定失效的根本原因。
5.评估现有控制措施:评估当前已经实施的控制措施对失效模式的效果。
确定哪些失效模式已经通过其他控制措施得到有效控制,哪些失效模式仍然存在较高的风险。
6.制定改进措施:针对高风险的失效模式,制定相应的改进措施。
改进措施可以包括设计改进、工艺改进、培训和教育、检测和监控等。
7.实施并验证改进措施:将改进措施实施到实际生产或运营中,并验证其效果。
跟踪和监控改进措施的实施情况,并对其效果进行评估。
通过进行FMEA分析,可以帮助组织识别和管理潜在的风险,提前采取预防措施,减少系统、产品或流程的失效概率,以实现质量和可靠性的提升。
FMEA分析可以应用于各个领域,如制造业、医疗设备、航空航天、汽车等。
FMEA的应用具有以下几个特点和优势:1.预防导向:FMEA分析主要关注于预防失效模式的发生,通过分析潜在的失效原因和影响,预测可能的失效模式,制定相应的预防措施,从而避免质量问题的发生。
2.多维度评估:FMEA分析不仅关注失效模式的影响对系统、产品或流程的影响,还可以从多个维度进行评估,如安全性、可靠性、功能性、经济性等,以全面了解失效模式的风险。
失效模式和影响效果分析

失效模式和影响效果分析
失效模式和影响效果分析(Failure Mode and Effects Analysis, FMEA) 是一种系统性的方法,用于识别和评估系统、产品或过程中的潜在失效模式及其对系统性能和用户影响的潜在效果。
该方法常被应用于各种工业领域,以提前识别和解决潜在的问题,降低风险和提高质量。
FMEA的步骤包括:
1.确定分析范围:确定分析的系统、产品或过程,明确要进
行FMEA分析的对象。
2.列举失效模式:对系统、产品或过程进行逐个分析,识别
可能出现的失效模式,并记录下来。
3.确定失效原因:对每个失效模式,分析其可能的失效原因,
考虑各种因素,如设计、制造、人为操作等。
4.评估失效影响:对每个失效模式,评估其对系统性能和用
户的潜在影响,包括安全、可靠性、可用性、维修性等方
面。
5.确定风险严重性:根据失效影响和概率评估,对每个失效
模式确定其风险严重性,通常使用风险优先数(Risk
Priority Number, RPN) 进行评估。
6.提出改进措施:针对风险严重性较高的失效模式,制定相
应的改进措施,降低风险和提高系统性能。
7.实施改进措施:将制定的改进措施付诸实施,并监控其效
果。
FMEA的主要目的是通过识别潜在失效模式和潜在影响,制定预防和纠正措施,降低风险,提高系统的可靠性和性能。
这项分析可以在产品或过程的设计、开发、评估和实施阶段进行,以确保系统的质量和安全,并减少不良事件的发生。
质量管理中的失效模式与影响分析
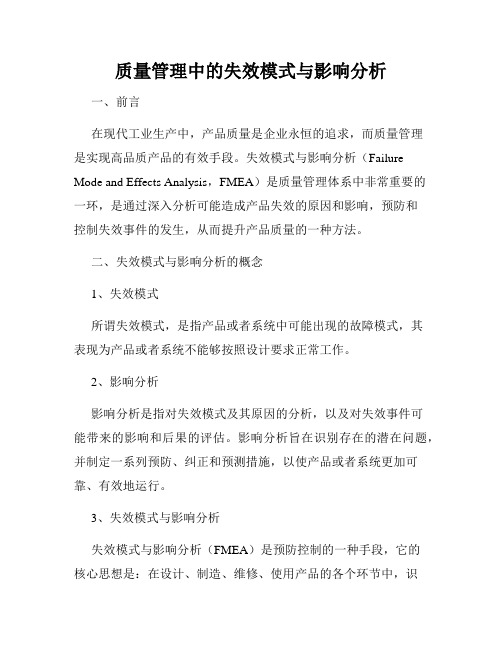
质量管理中的失效模式与影响分析一、前言在现代工业生产中,产品质量是企业永恒的追求,而质量管理是实现高品质产品的有效手段。
失效模式与影响分析(Failure Mode and Effects Analysis,FMEA)是质量管理体系中非常重要的一环,是通过深入分析可能造成产品失效的原因和影响,预防和控制失效事件的发生,从而提升产品质量的一种方法。
二、失效模式与影响分析的概念1、失效模式所谓失效模式,是指产品或者系统中可能出现的故障模式,其表现为产品或者系统不能够按照设计要求正常工作。
2、影响分析影响分析是指对失效模式及其原因的分析,以及对失效事件可能带来的影响和后果的评估。
影响分析旨在识别存在的潜在问题,并制定一系列预防、纠正和预测措施,以使产品或者系统更加可靠、有效地运行。
3、失效模式与影响分析失效模式与影响分析(FMEA)是预防控制的一种手段,它的核心思想是:在设计、制造、维修、使用产品的各个环节中,识别潜在失效模式、评估其可能影响和后果,并随后采取预防措施,从而提高产品的质量和可靠性。
三、失效模式与影响分析的步骤FMEA是一个基于团队合作的、有序的分析过程,主要分为以下步骤:1、确定需要分析的产品或者系统首先需要确定需要进行FMEA分析的产品或者系统,以及所涉及的物理和功能性方面。
2、制定失效模式制定失效模式是指对所选产品或者系统进行分析,并确定可能存在的失效模式。
在此过程中,需要考虑影响失效模式的所有因素,包括物理变形、设备磨损、操作不当、环境因素等。
3、评估失效模式的严重性在确定了失效模式后,需要评估失效模式的严重性,包括对生产和用户产生的影响等方面进行评估。
4、确定可能的原因在确定失效模式和严重性后,需要确定可能的原因,以及导致失败模式和严重性的根本原因。
5、确定纠正措施在确定了原因后,需要制定出一些纠正措施,以减少或消除可能造成失效事件的原因。
6、制定预防性措施最后,需要制定一系列预防性措施,以防止不良失效模式或原因继续存在。
fmea培训资料最新版(141页)
FMEA培训资料最新版(141页)FMEA(失效模式和影响分析)是一种系统的、结构化的方法,用于识别和评估产品或过程中的潜在失效模式,以及这些失效模式对最终用户的影响。
FMEA培训资料旨在帮助参与者了解FMEA的基本概念、方法和工具,以便在实际工作中应用FMEA来提高产品或过程的质量和可靠性。
一、FMEA概述FMEA是一种预防性的质量工具,它通过系统性地识别和分析潜在的失效模式,以及这些失效模式对产品或过程的影响,来降低失效风险。
FMEA通常分为两个阶段:设计FMEA(DFMEA)和过程FMEA (PFMEA)。
DFMEA关注于产品设计和开发阶段,而PFMEA关注于制造和装配过程。
二、FMEA的基本步骤1. 定义项目范围:确定要分析的系统和子系统的范围。
2. 建立团队:组建一个跨职能的团队,包括设计、工程、制造和质量等部门的代表。
3. 识别失效模式:团队成员共同识别潜在的失效模式,并记录下来。
4. 分析失效影响:评估每个失效模式对最终用户的影响,包括安全性、成本、性能和可维护性等方面。
5. 评估失效严重性:根据失效影响的严重程度,对每个失效模式进行评分。
6. 评估失效发生概率:根据失效模式的已知历史数据或专家经验,评估每个失效模式的发生概率。
7. 评估检测难度:评估检测每个失效模式的难度,包括检测方法的有效性和成本。
8. 计算风险优先级数(RPN):将严重性、发生概率和检测难度相乘,得到每个失效模式的风险优先级数。
9. 采取预防措施:根据RPN,制定和实施预防措施,以降低失效风险。
10. 跟踪和更新:定期跟踪和更新FMEA,以确保其持续有效。
三、FMEA工具和模板FMEA工具和模板可以帮助团队更有效地进行FMEA分析。
常用的FMEA工具包括:1. FMEA表格:用于记录失效模式、影响、严重性、发生概率、检测难度和RPN等信息。
2. FMEA软件:提供自动化的FMEA分析功能,包括数据输入、计算和分析报告。
如何进行失效模式与影响分析FMEA
一、FMEA的開發與發展
20世紀50年代, 美國格魯曼公司開發了FMEA, 用 以飛機制造業的發動機故障預防, 取得較好成果. 20世紀60年代, 美國宇航界實施阿波羅計劃時, 要求實施FMEA. 1974年, 美國海軍建立了第一個FMEA標準, 20世 紀70年代後期, 美國汽車工業開始運用FMEA. 20世紀80年代中期, 美國汽車工業將FMEA運用 於生產過程中. 90年代, 美國汽車工業將FMEA納入QS9000標準.
4、FMEA 的分類.
根據其用途和適用階段不同, FMEA可分為: (2) 過程FMEA(PFMEA-Process FMEA). 針對工序間可能或已知的主要壞品, 可運用PFMEA作 量化分析, 在影響壞品產生的諸因素中, 哪一個系統原 因影響最大?是否主要原因, 其他如Cpk低、生產過程異 常等均可通過采用PFMEA直觀地找出主要原因, 進行 改善以達到應用的效果.
極少1 in1500000 小概率1 in150000 缺陷較少1 in15000 微量缺陷1 in2000 偶然性缺陷1 in500 一般1 in100 較多1 in50 大量1 in10 非常多1 in5 可靠的測試 比較可靠的測試 良好的測試 測試可控制 不完全的測試控制 較低水平的控制 低水平的控制 難於控制 很難控制
6.各過程重要不良模式及推進原因如下表:
過程 爐前檢查 不良模式 1.元件腳氧化 2.PCB划傷 1. 松香比重過低 浸松香助劑 2. 松香發泡不良 預熱 1. 預熱溫度過高 2. 預熱時間過長 1. 錫面過低 浸錫 2. 浸錫時間過短 4. 錫液溫度過高 推定原因 保存不當、元件來料不良 作業方法不當、PCB來料不良 未及時添加新助劑、未及時清理舊助劑、測 定方法錯誤 發泡孔堵塞、發包電機停止工作、松香變質 控制器故障、測定方法錯誤 帶速過低、傳送帶打滑 未及時加錫、電機轉速變化 帶速過度 控制器故障、測定方法錯誤
失效模式与影响分析
失效模式与影响分析失效模式与影响分析(英文:Failure mode and effects analysis,FMEA),又称为失效模式与后果分析、失效模式与效应分析、故障模式与后果分析或故障模式与效应分析等,是一种操作规程,旨在对系统范围内潜在的失效模式加以分析,以便按照严重程度加以分类,或者确定失效对于该系统的影响。
FMEA广泛应用于制造行业产品生命周期的各个阶段;而且,FMEA在服务行业的应用也在日益增多。
失效原因是指加工处理、设计过程中或项目/物品(英文:item)本身存在的任何错误或缺陷,尤其是那些将会对消费者造成影响的错误或缺陷;失效原因可分为潜在的和实际的。
影响分析指的是对于这些失效之处的调查研究。
基本术语失效模式(又称为故障模式)观察失效时所采取的方式;一般指的是失效的发生方式。
失效影响(又称为失效后果、故障后果)失效对于某物品/项目(英文:item)之操作、功能或功能性,或者状态所造成的直接后果。
约定级别(又称为约定级)代表物品/项目复杂性的一种标识符。
复杂性随级数接近于1而增加。
局部影响仅仅累及所分析物品/项目的失效影响。
上阶影响累及上一约定级别的失效影响。
终末影响累及最高约定级别或整个系统的失效影响。
失效原因(又称为故障原因)作为失效之根本原因的,或者启动导致失效的某一过程的,设计、加工处理、质量或零部件应用方面所存在的缺陷严重程度(又称为严重度)失效的后果。
严重程度考虑的是最终可能出现的损伤程度、财产损失或系统损坏所决定的,失效最为糟糕的潜在后果[1]。
历史从每次的失效/故障之中习得经验和教训,是一件代价高昂而又耗费时间的事情,而FMEA 则是一种用来研究失效/故障的,更为系统的方法。
同样,最好首先进行一些思维实验。
二十世纪40年代后期,美国空军正式采用了FMEA[2]。
后来,航天技术/火箭制造领域将FMEA用于在小样本情况下避免代价高昂的火箭技术发生差错。
其中的一个例子就是阿波罗空间计划。
失效模式与影响分析(FMEA)
可能给错药 药物名称或外表 厂商制造原 造成病人伤 相似 因 害
1
1
10
10
三、举例
4.分析失效模型和影响因素 表4.3 护士到病人单位给药 失效模式 原因 结果 S 1.护士太 可能给错 护士没有核对 匆忙。2. 药造成病 10 病人身份 病人没有 人伤害 识别手圈 1.无法识 给药途径 药物给药途径 别医嘱。 错误造成 10 错误 2.缺乏相 影响结果 关知识。
护士对药 卡 到备药间 备药 到病人病 房给药
三、举例
4.分析失效模型和影响因素
4.1 护士给药 表4.1护士核对给药纪录单
失效模式 结果 S 没有依照处 1.医嘱遗失。 给药记录单没有 方给药可能 10 2.书写医嘱 更新 影响病人结 时分心 果 1.书写医嘱 时不注意。 没有依照处 2.写后的医 方给药可能 给药时间不正确 嘱没有双重 10 影响病人结 核对。3.没 果 有计算机处 方系统 原因 O 5 D 5 RPN 改善措施 250
O
D RPN 改善措施
1.加强培 训。2.病 10 人佩戴手 圈
1
1
5
5
250
三、举例
5. 评判结果 失效模式 给药记录单没有更新 RPN 250
给药时间不正确 药物不正确 药物名称或外表相似
护士没有核对病人身份
250 250 10
10
药物给药途径错误
250
三、举例
6.根本原因分析 6.1列出最需要改善的失效模式: 给药记录单没有更新、给药时间不正确、药物不 正确、药物给错途径 6.2 对相应失效模式分析原因。
三、举例
3. 分析流程 主题1:病人辨识和输血流程:
制作及佩 戴手圈 采血和 备血 检验科 流程 送血到 病房 核对 病人
- 1、下载文档前请自行甄别文档内容的完整性,平台不提供额外的编辑、内容补充、找答案等附加服务。
- 2、"仅部分预览"的文档,不可在线预览部分如存在完整性等问题,可反馈申请退款(可完整预览的文档不适用该条件!)。
- 3、如文档侵犯您的权益,请联系客服反馈,我们会尽快为您处理(人工客服工作时间:9:00-18:30)。
1、哪一种缺陷可能發生. 2、這种缺陷會造成什麼影響. 3、這种影響的嚴重性有多大. 4、是哪种原因導致失效. 5、失效發生的概率有多大.
6、當前的過程控制方法. 7、檢測失效的能力. 8、風險優先數為多少. 9、有何改善方案.
二、FMEA的特點及作用
3、風險優先數RPN.
RPN 評估
影響/行動需求
嚴重性S: 對應於某潛在缺陷影響的嚴重程度 發生概率O: 對應於原因與缺陷模式比例的評估 可偵測性D: 在客戶處發生缺陷的可能等級, 即在本 公司可發現此缺陷的可能性 RPN表示風險優先數---Risk Priority Number RPN=S.O.D
六、FMEA的計分標準如下表
分值
01 02 03 04 05 06 07 08 09 10
三、FMEA實施步驟
01.繪製流程圖及風險性評估. 02.確定各過程的分析水准. 03.明確各過程要求的品質、公
差等. 04.作成加工過程方塊圖. 05.針對每一加工工序, 列舉發
生的不良模式. 06.整理造成不良原因之不良模
式, 選定作為檢討對象的不 良模式. 07.用柏拉圖分析不良發生的可 能原因. 08.將不良模式及原因記入FMEA 表格.
過程缺陷模式和影響分析表
項目 核心團隊
過程責任
負責工程師 關 鍵日 期
FMEA編號
FMEA初始日期
作成
確認
頁 碼第 頁
修訂日期
承認
共
頁
潛在缺 潛在缺 嚴 項目/功能 陷模式 陷影響 重
度
潛在缺 陷原因
發生 概率
現在 的設 計控
可偵 R 知性 P
N
制
建議采取 的措施
責任者/目 標完成日
行動結果 采取的行動 S O D RPN
工序/産品性能會降低但安全 一般1 in100
較低水平的控制
工序/産品性能會降低
較多1 in50
低水平的控制
很嚴重以致無法修復或使用 大量1 in10
難於控制
非常嚴重(帶有提示的影響) 非常多1 in5
很難控制
安全性或可靠性故障(無提示) 幾乎全部>1 in2 幾乎無法控制
典型缺陷原因、缺陷模式和影響如下表所示:
如新產品設計、新工序設計, 可以預先進行FMEA, 盡可能周全地考慮產品規格、工序操作水平、工 序能力等因素, 使設計符合規定要求 。
二、FMEA的特點及作用
4、FMEA 的分類.
根據其用途和適用階段不同, FMEA可分為:
(2) 過程FMEA(PFMEA-Process FMEA).
針對工序間可能或已知的主要壞品, 可運用PFMEA作 量化分析, 在影響壞品產生的諸因素中, 哪一個系統原 因影響最大?是否主要原因, 其他如Cpk低、生產過程異 常等均可通過采用PFMEA直觀地找出主要原因, 進行 改善以達到應用的效果.
S(嚴重性)
O(發生概率) D(可偵測性)
對客戶或工序無影響
極少1 in1500000 可靠的測試
客戶可能忽略的缺陷
小概率1 in150000 比較可靠的測試
對性能有微小影響
缺陷較少1 in15000 良好的測試
對性能有較小影響
微量缺陷1 in2000 測試可控制
對性能有影響
偶然性缺陷1 in500 不完全的測試控制
作成
確認
頁 碼第 頁
修訂日期 承認 共頁
嚴 項目/功能 潛在缺 潛在缺 重
陷模式 陷影響 度
潛在缺 陷原因
程控 知性 N
制
建議采取 的措施
責任者/目 標完成日
行動結果 采取的行動 S O D RPN
備注:1.S代表嚴重度;2.O代表發生概率;3.D代表可偵知性;4.RPN代表風險評分
二、FMEA的特點及作用
4、FMEA 的分類.
根據其用途和適用階段不同, FMEA可分為:
(3) 設備維護的FMEA(EFMEA-Equipment FMEA).
如新設備投入運行前, 我們可以預先進行EFMEA分析, 考慮由於設備可能造成的產品品質問題及可靠性問題 等原因, 采取預防措施消除不良因素.
1<RPN<50
對產品危害較小
51<RPN<100
101<RPN<10 00
對產品有中等危害, 需進一 步改善
對產品有嚴重危害, 需深入 調查分析
二、FMEA的特點及作用
4、FMEA 的分類.
根據其用途和適用階段不同, FMEA可分為:
(1) 設計階段FMEA(DFMEA-Design FMEA).
09.以影響程度、發生頻度、可偵測性、 對設備的熟悉程序為判據, 對缺陷模 式進行等級, 分I、II、III、IV等.
10.估計不良嚴重性、發生概率及當前的 可偵測性, 計算RPN.
11.明確如何改善嚴重性、發生概率及測 試性.
12.實施改善方案.
13.收集數據, 實施改善並確認效果.
14.修定FMEA文件, 根據改善效果重排RPN.
備注:1.S代表嚴重度;2.O代表發生概率;3.D代表可偵知性;4.RPN代表風險評分
七、過程FMEA應用實例
現以波峰焊接過程各因素對首次通過率的影響為例進 行PFMEA.
1.確定工序流程及風險性評估 .
流程
爐前檢查 ↓
浸松香助劑 ↓
預熱 ↓
15.如果必要從第11步開始新的改善循環.
四、FMEA實施時機
當設計新系統、產品或工序時. 當現有設計或工序發生變化時. 當現有設計、工序將被用於新的場所時. 完成一次糾正行動后. 對設計FMEA, 當系統功能被確定, 但特定設備 選擇前. 對工序FMEA, 當產品圖紙及作業指導完成時.
五、影響程度評估及風險優先數計算
如何进行失效模式与影响分析
二、FMEA的特點及作用
1、FMEA的特點.
FMEA的特點是將失效的嚴重性、失效發生 的可能性、失效檢測的可能性三個方面進行 量化, 通過量化, 可將影響功能及品質的可能 問題提前進行預防, 防患於未然.
二、FMEA的特點及作用
2、FMEA的作用.
FMEA首先是一种統計分析工具,它可在設計、生 產、交付的各階段開始之前即進行有效控制. FMEA可幫助我們確認:
典型缺陷原因 典型缺陷模式
材料選定不正確
斷裂
設計壽命評估不當
變形
潤滑不足
松
維護指引不足
泄漏
環境太差
粘貼
算法不正確
短路
破裂
典型缺陷影響
噪聲 不穩定的操作
外觀不良 不穩定 斷續操作 無法動作 操作能力削弱
設計缺陷模式和影響分析表
項目 核心團隊
設計責任
負責工程師 關 鍵日 期
FMEA編號
FMEA初始日期