汽车前处理工艺技术
汽车壳体前处理工艺
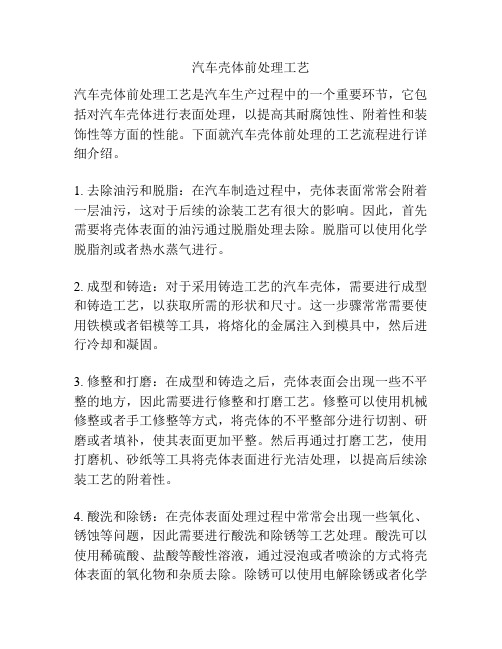
汽车壳体前处理工艺汽车壳体前处理工艺是汽车生产过程中的一个重要环节,它包括对汽车壳体进行表面处理,以提高其耐腐蚀性、附着性和装饰性等方面的性能。
下面就汽车壳体前处理的工艺流程进行详细介绍。
1. 去除油污和脱脂:在汽车制造过程中,壳体表面常常会附着一层油污,这对于后续的涂装工艺有很大的影响。
因此,首先需要将壳体表面的油污通过脱脂处理去除。
脱脂可以使用化学脱脂剂或者热水蒸气进行。
2. 成型和铸造:对于采用铸造工艺的汽车壳体,需要进行成型和铸造工艺,以获取所需的形状和尺寸。
这一步骤常常需要使用铁模或者铝模等工具,将熔化的金属注入到模具中,然后进行冷却和凝固。
3. 修整和打磨:在成型和铸造之后,壳体表面会出现一些不平整的地方,因此需要进行修整和打磨工艺。
修整可以使用机械修整或者手工修整等方式,将壳体的不平整部分进行切割、研磨或者填补,使其表面更加平整。
然后再通过打磨工艺,使用打磨机、砂纸等工具将壳体表面进行光洁处理,以提高后续涂装工艺的附着性。
4. 酸洗和除锈:在壳体表面处理过程中常常会出现一些氧化、锈蚀等问题,因此需要进行酸洗和除锈等工艺处理。
酸洗可以使用稀硫酸、盐酸等酸性溶液,通过浸泡或者喷涂的方式将壳体表面的氧化物和杂质去除。
除锈可以使用电解除锈或者化学除锈等方法,将壳体表面的锈蚀物质去除。
5. 磷化处理:在酸洗和除锈之后,需要进行磷化处理,以提高壳体表面的耐腐蚀性。
磷化处理可以使用磷酸锌或者磷酸锰等含磷酸盐溶液进行,通过浸泡或者喷涂的方式将磷化剂涂覆在壳体表面,形成一层磷酸盐的保护膜。
6. 防腐蚀涂层:最后一步是对壳体进行防腐蚀涂层处理,以提高其耐腐蚀性。
常用的防腐蚀涂层包括阳极氧化、电镀、喷涂、电泳涂装等方法,根据壳体材料的不同以及具体的要求选择适合的涂层工艺。
综上所述,汽车壳体前处理工艺是汽车生产过程中的关键步骤,它通过去除油污和脱脂、成型和铸造、修整和打磨、酸洗和除锈、磷化处理以及防腐蚀涂层等工艺流程,提高壳体表面的性能和耐腐蚀性,确保汽车壳体的质量和使用寿命。
汽车锆化前处理原理_概述说明以及解释
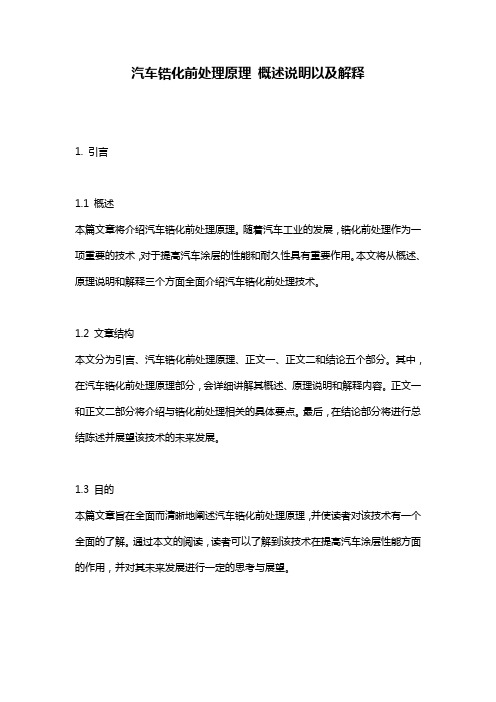
汽车锆化前处理原理概述说明以及解释1. 引言1.1 概述本篇文章将介绍汽车锆化前处理原理。
随着汽车工业的发展,锆化前处理作为一项重要的技术,对于提高汽车涂层的性能和耐久性具有重要作用。
本文将从概述、原理说明和解释三个方面全面介绍汽车锆化前处理技术。
1.2 文章结构本文分为引言、汽车锆化前处理原理、正文一、正文二和结论五个部分。
其中,在汽车锆化前处理原理部分,会详细讲解其概述、原理说明和解释内容。
正文一和正文二部分将介绍与锆化前处理相关的具体要点。
最后,在结论部分将进行总结陈述并展望该技术的未来发展。
1.3 目的本篇文章旨在全面而清晰地阐述汽车锆化前处理原理,并使读者对该技术有一个全面的了解。
通过本文的阅读,读者可以了解到该技术在提高汽车涂层性能方面的作用,并对其未来发展进行一定的思考与展望。
2. 汽车锆化前处理原理:2.1 锆化前处理概述汽车锆化前处理是指在进行汽车锆化过程之前对车辆表面进行一系列处理的过程。
这个过程的目的是确保汽车表面充分净化,并使其具备良好的附着性和耐腐蚀性,以提供最佳的锆化效果。
2.2 锆化前处理原理说明在汽车锆化前处理中,主要包括以下步骤:清洗、除油、除铁锈、活化等。
首先,清洗是为了去除表面的尘土、油污和其他杂质,常用方法有水槽清洗和喷淋清洗。
接着,除油是为了去除车辆表面可能存在的油脂、润滑剂和其他有机物,常用溶剂清洗或碱性溶液浸泡。
然后,除铁锈可以去除钢铁部分产生的氧化物,采用机械打磨或酸性溶液处理。
最后,活化是为了增加表面的粗糙度并使其更具有活性,利于后续工艺步骤的进行。
2.3 锆化前处理解释通过对汽车锆化前处理的解释,可以更好地理解其原理和作用。
首先,清洗是为了保证表面的干净,以确保后续工艺能够有效进行,并避免因杂质带来的问题。
除油则是为了去除可能存在的难溶性或附着在表面上的有机物,同时也提高了锆化液对车辆表面的湿润性。
除铁锈则可消除表面氧化物对净化层的影响,以达到更好的锆化效果。
钣金与喷漆工艺流程详解从涂装前处理到喷涂后处理的步骤

钣金与喷漆工艺流程详解从涂装前处理到喷涂后处理的步骤钣金与喷漆是汽车制造、修理行业中常见的工艺,它们可以使车身外观更加美观,提升车辆的保护性能和价值。
本文将详细介绍钣金与喷漆的工艺流程,包括从涂装前处理到喷涂后处理的全部步骤。
一、涂装前处理涂装前处理是钣金与喷漆工艺中至关重要的一步,它直接影响着后续的喷涂效果。
以下是在涂装前处理阶段需要进行的步骤:1.1 钣金修复:在涂装前,对车身表面的凹陷、破损等进行修复,保证车身的平整度和外观。
1.2 清洁与打磨:使用适当的清洁剂将车身表面的油污、尘埃等彻底清洁干净,然后经过细致打磨,去除不平整的地方,并提供光滑的基底。
1.3 填补与整形:使用填充物填充车身上存在的小孔、刮痕等,然后再次打磨,确保车身表面平整度。
1.4 上底漆:涂刷底漆,增加表面的附着力和保护性能。
二、喷涂工艺在涂装前处理完成后,接下来是喷涂工艺。
喷涂是将颜料均匀地涂刷在车身表面的过程,具体步骤如下:2.1 喷涂底漆:喷涂底漆是为了增加遮盖力,增强上色效果,提高车身的整体颜色均匀性。
底漆需要在特定的温度和湿度下进行喷涂,以确保喷涂效果。
2.2 研磨及除尘:在底漆完全干燥后,进行研磨和除尘。
研磨是为了去除不平整的表面,除尘则是为了确保车身表面干净,以便后续的涂装工作。
2.3 喷涂面漆:喷涂面漆是为了赋予车身色彩,增加亮度和光泽。
在喷涂面漆之前,需要先进行色彩的调配、测试和确认,确保得到客户满意的颜色效果。
2.4 干燥:在喷涂面漆完成后,需要进行适当的干燥过程,以确保漆面固化,达到理想的效果。
干燥过程可以采用自然干燥或者加热干燥的方式。
三、喷涂后处理喷涂后处理是为了提升车身表面的光洁度和光泽度,以及保护漆面不受外界环境的损害。
以下是喷涂后处理的步骤:3.1 手工抛光:使用抛光机械进行手工抛光,去除喷涂面漆的毛边、切割痕迹和细小的凹陷。
抛光过程中,需要控制力度和抛光剂的使用量,以免造成漆面损害。
3.2 上蜡:在手工抛光之后,使用封釉蜡进行上蜡处理。
汽车前处理和电泳工艺技术
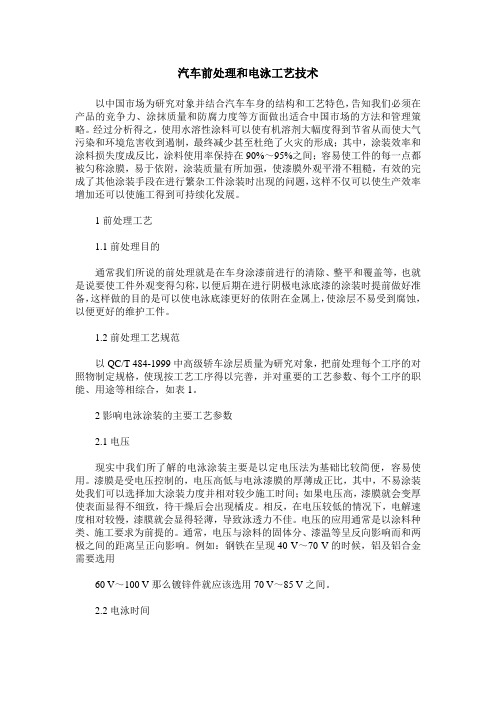
汽车前处理和电泳工艺技术以中国市场为研究对象并结合汽车车身的结构和工艺特色,告知我们必须在产品的竞争力、涂抹质量和防腐力度等方面做出适合中国市场的方法和管理策略。
经过分析得之,使用水溶性涂料可以使有机溶剂大幅度得到节省从而使大气污染和环境危害收到遏制,最终减少甚至杜绝了火灾的形成;其中,涂装效率和涂料损失度成反比,涂料使用率保持在90%~95%之间;容易使工件的每一点都被匀称涂膜,易于依附,涂装质量有所加强,使漆膜外观平滑不粗糙,有效的完成了其他涂装手段在进行繁杂工件涂装时出现的问题,这样不仅可以使生产效率增加还可以使施工得到可持续化发展。
1前处理工艺1.1前处理目的通常我们所说的前处理就是在车身涂漆前进行的清除、整平和覆盖等,也就是说要使工件外观变得匀称,以便后期在进行阴极电泳底漆的涂装时提前做好准备,这样做的目的是可以使电泳底漆更好的依附在金属上,使涂层不易受到腐蚀,以便更好的维护工件。
1.2前处理工艺规范以QC/T 484-1999中高级轿车涂层质量为研究对象,把前处理每个工序的对照物制定规格,使现按工艺工序得以完善,并对重要的工艺参数、每个工序的职能、用途等相综合,如表1。
2影响电泳涂装的主要工艺参数2.1电压现实中我们所了解的电泳涂装主要是以定电压法为基础比较简便,容易使用。
漆膜是受电压控制的,电压高低与电泳漆膜的厚薄成正比,其中,不易涂装处我们可以选择加大涂装力度并相对较少施工时间;如果电压高,漆膜就会变厚使表面显得不细致,待干燥后会出现橘皮。
相反,在电压较低的情况下,电解速度相对较慢,漆膜就会显得轻薄,导致泳透力不佳。
电压的应用通常是以涂料种类、施工要求为前提的。
通常,电压与涂料的固体分、漆温等呈反向影响而和两极之间的距离呈正向影响。
例如:钢铁在呈现40 V~70 V的时候,铝及铝合金需要选用60 V~100 V那么镀锌件就应该选用70 V~85 V之间。
2.2电泳时间漆膜厚度与电泳时间成正比,可是如漆膜的厚度达到定值时即使时间增长厚度也不会增加,相反还会出现不良状况;反过来看,当电泳时间短,漆膜薄的时候,电泳时间需要取决于所用的电压,如果涂层质量已经得到保障,那么时间短比时间长要效果要好的多。
前处理基础知识

前处理基础知识前言汽车的前处理是表面处理的关键步骤。
车身车间拼装好的车身送到涂装车间,首先就是进行前处理,然后电泳、喷中途漆、面漆等;合适的前处理为漆膜打下一个良好的基础,进而使喷漆后车身具有优良的耐蚀性。
下面将系统介绍前处理工艺,内容包括前处理的目的、各步骤的功能,如何控制工艺过程使前处理效果最好等。
前处理概述前处理典型流程:预处理(清除污垢,锈痕)---脱脂---水洗---表调---磷化---水洗---DI水洗---电泳前处理的作用。
除油。
形成转化膜。
封孔前处理的好处。
增强漆层与底材的结合力。
这是因为金属的表面和因有磷化结晶而增大,且与漆层互相咬合。
提供一个耐蚀保护膜,增强耐蚀性。
万一漆膜损坏,锈蚀的扩展被抑制。
金属底材汽车本身常用的材料有。
冷轧板。
电镀锌板。
热镀锌板。
合金化电镀锌板。
铝板选择底材会考虑到的因素。
焊接性。
冲压成型性能。
价格。
重量、强度。
应用、设计。
耐蚀性。
与磷化的匹配(可见汽车厂采购车身材料时并不特别重视板材的可磷化性)板材的制造过程和环境对其可磷化性也会有影响,可能的影响因素有辗压比,退火温度、油污种类、数量、氧化物等。
另外某些为远洋运输而使用的防锈油不易除净,会导致磷化膜出现条纹,镀锌板微小缺陷会令随后电泳漆膜出现小孔。
当汽车厂的板材来源改变,或改变了设计,冲压油等都要注意是否与现有的前处理相匹配。
油污种类和来源进入前处理线的车身表面会有各种油污、尘土等,它们包括:来自轧钢厂:。
辗压、酸洗过程(金属盐类、铁屑)。
轧钢油(脂肪酸、腊)。
金属氧化物。
碳(退火过程产生)来自环境、运输:。
凝结物、金属氧化物。
防锈油(专用于远洋运输)来自冲压、装配过程:。
坯料清洗。
冲压油、拉伸油(剂)。
人手接触。
焊接、铜焊。
打磨、布擦(金属屑)。
胶粘剂、密封胶。
字迹2.不能形成磷化膜的表面。
电镀锌表面有一层较厚的透明铬钝化膜。
工件表面的重铬酸锌膜。
铜焊焊缝。
焊渣、焊接高温影响区。
有机涂层。
塑料。
冷轧板表面的碳化物3.不能形成磷化膜且电泳也会出问题的表面。
汽车生产涂装车间前处理磷化工艺全

汽车生产涂装车间前处理磷化工艺磷化所谓磷化处理是指金属表面与含磷酸二氢盐的酸性溶液接触,发生化学反应而在金属表面生成稳定的不溶性的无机化合物膜层的一种表面化学处理方法,所生成的膜称为磷化膜。
具有微孔结构,在通常大气条件下比较稳定,具有一定的防锈能力,用作漆膜的底层,可以显著地提高涂层的附着力和耐蚀性能。
磷化膜作为电泳涂漆之底层,在汽车行业中得到几乎百分之百的应用。
磷化处理分类磷化处理有很多分类方法,工业上较通用的有如下几种:(1) .根据组成磷化液的磷酸盐分类,有磷酸锌系、磷酸镒系、磷酸铁系。
此外,还有在磷酸锌盐中加钙的锌钙系,在磷酸锌系中加银、加镒的所谓〃三元体系〃磷化等。
(2) .根据磷化温度分类,有高温磷化(80。
C以上)、中温磷化(50~70℃)和低温磷化(40。
C以下)。
(3) .按磷化施工方法分类,有喷淋式磷化、浸渍式磷化、喷浸结合式磷化、涂刷型磷化。
(3).按磷化膜的质量分类,有重量型(7.5g∕m2以上)、中量型(4.3g∕m2〜7.5g∕m2)、轻量型(1.1g∕m2~4.3g∕m2)和特轻量型(0.3g∕m2〜1.1g∕m2)o磷酸锌系,磷酸锌钙系,磷酸铁系磷化膜适用于涂装底层,其中以磷酸锌系磷化膜应用最为广泛。
磷酸镒系磷化膜,主要用于满足润滑性和耐磨性的要求。
磷化膜的组成和成膜机理磷化膜的组成钢铁在不同磷化液中形成的膜层的组成如表所示。
钢铁磷化膜的组成及外观类型溶液主要成分膜层主要成分膜层外观锌磷酸Zn2+,磷酸锌浅灰,深灰,黑灰色系锌系磷酸Zn2+,磷酸锌钙锌钙Ca2+,系磷酸Zn2+,磷酸锌镒锌锦Mn2+,系磷酸锦系Mn2+,磷酸锌浅灰,深灰,黑灰色磷酸铁系Fe2+,磷酸铁深灰色Me①,磷酸铁及铁的氧化物膜层为(0.1~1)g∕m2时呈彩虹色,大于1g∕m2时呈深灰色13.2.2磷化膜成膜的机理比如我们锌系磷化为例来说明磷化膜成膜机理,磷酸锌系处理溶液,通常含有磷酸、磷酸二氢锌、氧化剂和促进剂等成分,其磷化基本反应如下:Fe+2H3PO4——>Fe(H2PO4)2+2H+(基体)(磷化液)2H++02——>H20(氧化剂)Fe(H2PO4)2+02——»FeP04+H3PO4+H20(氧化剂)(沉淀)当铁与磷化液接触时,铁不断溶解,H3PO4不断消耗,并放出氢,这时铁与磷化液接触的界面处的酸度下降,PH值上升,处理液中成分发生下列反应:3Zn(H2PO4)2+4H2O——>Zn3(PO4)2∙4H20+4H3PO4(磷化液)(膜的成分)Fe+2Zn(H2PO4)2+4H2O+02——>Z∩2Fe(PO4)2∙4H20+2H3PO4+H20 (磷化液)(膜的成分)生成的不溶于水的Zn3(PO4)2∙4H20及Zn2Fe(PO4)2∙4H20覆盖在金属表面上即形成了磷化膜。
汽车含铝车身的涂装前处理工艺研究
汽车含铝车身的涂装前处理工艺研究摘要:铝车身在涂装前需要进行相应的处理,主要包括了磷化加氟和两步法,以及化学成膜,同时也使用了脱脂、表调、磷化等工序,因此需要进行考察和分析,从而全面提升涂装处理工艺技术水平。
关键词:汽车;铝车身;涂装前;处理工艺;研究随着能源和环境问题不断突出,汽车制造企业运用减轻汽车自重方式来降低油耗,目前这已经成为企业竞争力的关键。
汽车制造企业为了实现轻量化目标,改进了汽车结构,并且在保证使用性能的基础上选用了轻质材料,比如铝合金和镁合金等材料。
目前世界所有大的汽车公司都在开发铝合金车身和零部件,以及全铝汽车,但是由于板材金属具有多样性,所以带来了许多问题。
1铝车身涂装前的处理工艺分析由于车身是组合件,如果涂装不良就会发生严重腐蚀情况。
为了避免这种情况出现,需要将组合件的转化成膜进行处理,当前主要有以下三种方式。
1.1磷化加氟法当金属铝在游离酸的作用下会发生溶解,所以基体附近的pH就会升高,而磷酸盐这时会水解成为磷酸根,当磷酸根和成膜离子达到了一定溶度积时,磷化膜在工件表面的微阴极区上会产生结晶析出。
通过添加氟化物,可以使溶解出的铝离子沉淀,从而除去了多余的铝离子,这种方法有效地避免了对成膜的影响。
1.2两步法分析两步法比较适用于钝化工序生产线,通过在磷化槽当中添加金属离子,可以避免铝发生反应,然后再加入一些氧化剂和螯合剂,同时利用氟锆酸水解反应,能够使基材表面形成ZrO2和Zr。
1.3化学转化膜法分析这是一种新型的涂装前处理技术,特点是无磷、锌、镍、锰、铬等重金属排放,而且无需加热,排放量相对小,废渣也比较少,特别适合应用于铝件,同时也可以兼容铁板和镀锌板。
2具体工序分析2.1磷化加氟情况分析首先,是脱脂情况分析。
脱脂工序具有很好的清洗效果,能够清洗铝材的表面油脂,还具有腐蚀溶解能力,有利于后续成膜。
在实际应用过程中需要控制铝材腐蚀状态,避免出现铝表面过度侵蚀和发黑情况。
汽车涂装车间工艺流程
在汽车制造业中,喷涂技术是不可或缺的组成部分,在汽车保护中起着非常重要的作用。
常见的汽车零部件包括汽车车身喷涂、汽车车轮喷涂、汽车车轮喷涂、汽车保险杠喷涂等,但各部件的涂装工艺不同,但一般相似。
那么,汽车涂装现场有什么过程呢?今天,创智涂装为你揭露汽车涂装现场的三工艺流程吧!1.前处理工艺汽车涂装车间工艺流程为了获得高质量的涂层效果和良好的防腐性能,涂层前必须进行表面处理,包括清洁油、锈、氧化皮等杂质,以及必要的表面化学处理和转化。
预处理过程可以提高涂涂涂层的附着性和耐腐蚀性能,充分发挥涂涂层的防护效果,充分发挥涂涂层的防护效果,以及涂涂层的使用寿命。
目前,我国许多汽车工厂涂装自动化生产线采用的工艺流程:热水洗-预脱脂-主脱脂-喷水洗-浸水洗-表调-磷化-喷水洗-浸水洗-钝化-循环去离子水洗-循环去离子水洗-新鲜去离子水洗总的来说,前处理分为脱脂、表调、磷化和钝化4个部分,4个部分之间有水洗,防止杂质进入下一个工艺部分造成交叉污染。
2.底粉线工艺通过输送链将工件送至喷粉室的喷枪位置,准备喷涂作业。
静电发生器通过枪口上的电极针向工件的空隙释放出高压静电(负极),这种高压静电使从。
汽车涂装车间工艺流程从枪口喷出的粉末和压缩空气的混合物,以及电极周围空气和电极周围空气的混合物被电离(负电荷)(负电荷)。
工件通过吊架和输送链接地(接地电极),使喷枪和工件之间形成电场。
粉末在电场力和压缩空气压力的双重推动下到达工件表面,通过静电引力在工件表面形成均匀的涂层。
3.喷漆线工艺喷涂漆是表面处理的产品或半成品的表面处理,包括被测试的合格产品或半成品。
涂装起到防锈、防腐、美观、标志的作用。
前处理是必要的,后处理是必要的,此时要对要喷漆的产品进行全面的检查,对可修复的缺陷进行修整,补救。
汽车涂装车间工艺流程喷漆工艺流程简图打磨→除尘→喷嘴喷漆→打磨→除尘→喷漆两次(第三次,步骤同上)。
工件出入口采用工件仿制门和气封,减少油漆雾侵入其他地区的整个喷雾室的微负压式设计,配合废气处理装置,根据能够有效减少油漆雾造成的污染的工件涂装特征,采用独特的底部水漩+水幕设计,有效提高油漆雾和水的混合概率,提高油漆雾的捕捉效率水循环设计为大循环大循环水循环设计,水资源可再利用,水资源可再利用,节水约5%,节约5%,降低废水处理成本,降低废水处理成本。
涂装前处理基本工艺流程
涂装前处理基本工艺流程涂装前处理包括除油、除锈、磷化三个部分.磷化是中心环节,除油和除锈是磷化之前的准备工序,因此,在生产实践中,既要把磷化工作作为重点,又要从磷化质量的要求出发,抓好除油和除锈工作,尤其要注意他们之间的相互影响.1、除油除锈优质的磷化膜只有在彻底去除了油物、锈、氧化皮等异物的工件表面上形成。
因为残留在工件表面的油污、锈蚀、氧化皮等会严重阻碍磷化膜的生长。
此外,还会影响涂层的附着力,干燥性能、装饰性能和耐蚀性能,彻底去除这些异物是磷化的必要条件.除油和除锈是磷化之前的两个基本工序,相对而言,油比锈的危害性大,而且有油的工件直接影响除锈速度,所以,除锈应在除油的基础上进行,但对于油少锈多的工件也可以将除油与除锈两个基本工序合二为一,在一个槽中同时完成除油除锈工序,可缩短生产线,降低设备和厂房投资费用,但处理质量不如分槽好,对要求不高的场合可采用。
采用此工序后,除油剂也应选择酸性药剂和除锈剂配套使用。
除锈仍采用盐酸,盐酸除锈速度快,除锈干净彻底,对氧化皮也有很好的去除功能,且又是常温使用,弊病是盐酸除锈酸雾较大,有害健康,环境污染严重。
随着工业的发展,环境保护和劳动条件的改善已成为人们共同关心的问题.因此,在选择药剂时应考虑环境保护的需要。
所以选择除油剂时要求配制简单,去污能力强,不含常温下难清洗的氢氧化钠,硅酸盐,OP乳化剂等成分,常温下易水洗,不含毒性物质,不产生有害气体,劳动条件好;选择除锈剂时要求内含促进剂,缓蚀剂和抑制剂,能提高除锈速度,防止工件产生过腐蚀和氢脆,能较好的抑制酸雾。
尤其值得重视的是酸雾抑制,酸洗除锈过程中产生的酸雾,不仅腐蚀设备和厂房,污染环境,而且可引起人们牙齿腐蚀,牙结膜发红,流泪,疼痛,咽喉干燥,咳嗽等症状,所以,有效抑制酸雾,不但是环保的需要,还是本单位自身的需要.考虑上述要求,经筛选,除油和除锈剂我们采用了祥和磷化公司的XH—16C除油除锈添加剂与验算配制而成,常温下使用,处理时间10—30min,它能提高除锈速度,防止工件产生过腐蚀和氢脆,能较好的抑制酸雾。
汽车生产车间涂装工艺前处理全
汽车生产车间涂装工艺前处理目前涂装是汽车耐腐蚀和装饰的最经济而有效的方法,而涂装前表面处理(又称前处理)的好坏又是直接影响涂层使用寿命和装饰效果的重要环节。
喷漆前表面处理的目的是去除被涂物表面上的所有污物(如浊污、铁锈、氧化皮、灰尘、型砂、焊渣、盐碱斑等)和用化学的方法生成一层有利于提高涂层的防腐蚀性的非金属转化膜,以保证涂层具有良好的防腐蚀性能和装饰性能。
采用同样的油漆材料,而仅仅是表面处理不同,其耐腐蚀效果可以相差数倍,可见表面处理对整个涂层质量影响之大。
表面处理,因金属件和非金属件,处理的杂质和处理方法的不同而不同。
对于金属件的功用主要是除油、除锈和改变工件的表面状态。
其主要由预清理、脱脂、磷化.水洗组成。
1、预清理一般来讲,任何材质的工件在进入前处理之前,均应进行预清理,用于除去那些采用清洗的方式不能除去的过度的污物。
如工件表面的氧化皮、铁锈、焊渣、铁屑、泥砂、干涸的油污以及其它污物。
预清理可以大大地降低对其后的前处理的污染,减轻前处理各工艺槽的负担。
早期的预清理一般是采用人工的方法进行,采用砂纸打磨去锈,除去机械杂质,用擦布蘸溶剂或水性清洗剂擦拭。
目前,国内一些大型汽车公司普遍在预清理工位增加手工高压水枪冲洗工位。
用含清洁剂的温水,在6bar左右的压力下用手工喷枪,对车身内外进行一次冲洗,主要对车身内部、夹缝、空腔结构等容易积聚灰粒的部位进行初步清洗。
特别是车身内地板,影响电泳漆膜质量的灰粒油污90%分布于车身内地板上。
采用手工高压水枪冲洗后的车身,大约可减少30%左右的灰粒,有利于降低对前处理槽的污染,延长槽液的使用寿命。
2、脱脂脱脂就是将白车身工件表面上的油污除去。
因为工件在储运过程中可能要用防护油的保护,在前面冲压加工时可能会用到拉延油,在切削加工时要接触乳化液,热处理时可能接触冷却油,工件上还经常会有操作者手上的油迹和汗迹,工件上的油脂还总是和灰尘等杂质掺合在一起的。
工件上的各种油污不仅阻碍了磷化膜的形成,而且还影响涂层的结合力、干燥性能、装饰性能和耐蚀性能。
- 1、下载文档前请自行甄别文档内容的完整性,平台不提供额外的编辑、内容补充、找答案等附加服务。
- 2、"仅部分预览"的文档,不可在线预览部分如存在完整性等问题,可反馈申请退款(可完整预览的文档不适用该条件!)。
- 3、如文档侵犯您的权益,请联系客服反馈,我们会尽快为您处理(人工客服工作时间:9:00-18:30)。
分析项目:
Free
acid 游离酸 Total acid 总酸 Accelerator (e.g. Nitrite) 促进剂 Zinc 锌离子 Manganese 锰离子 Nickel 镍离子 Iron 铁离子 Fluoride (Aluminium) 氟离子(铝离子)
19
磷化膜性能
n L =m Co Cx
1
2
3
L = 水洗水的消耗 (l/m?表面) m = 带出量 (l/m?表面) n = 水洗区的水洗槽数量 Co = 最后脱脂槽的浓度 (g/l) Cx = 最后水洗槽的浓度 (g/l)
举例:
m = 10 ml/m?表面 Co = 25 g/l Cx = 0.01 g/l 稀释比例=1:2500
20
基准值
目视 GB 6807-86 电镜 1000倍
钝化的机理
由钝化封闭磷化膜孔隙
孔隙的底部被钝化 磷化膜表面铬化反应
磷化膜 基材 基材
21
钝化的类型
类型
特征
情形
在欧洲,美国得到广泛 使用
C r-V I/ C r-III D eo x yl yt e4 1 逐步在减少 C r-III D eoxyl yt e 7030 无C r6+ Z rF 62D eoxyl yt e 54 N C 无铬体系,无机物 PV PA Parcolene 90 无铬体系,有机聚合物 D I w at er 无添加剂
23
无铬钝化剂
Deoxylyte 54 NC
优点:
无致癌物质 不需单独的废水处理 具有同含铬钝化剂相当的处理效果 对铝材的处理效果更佳 通过离子交换处理,水洗水能循环使用 含锆化学品 配槽浓度:0.25% 在室温下也能工作 须用不锈钢设备
24
特性:
水洗水
脱脂 水洗
水洗水计算方程式 (简化式)
31
故障处理 (二)
在回答这些问题时,应依照下列各点进行检查: 1.检查技术条件,即槽液的参数 2.检查测试方法。例如准确地检查溶液的点数,就可以 知道所使用的标准溶液的浓度是否有误 3.检查槽液的温度和压力。必要时,可用手工温度计 检测,因为测温仪表可能有误差 4.检查基体金属,是否更换了防锈油或润滑剂 5.检查生产用的材料,化学药剂,油漆,和溶剂的质量 6.检查所用的水,很可能恰好遇到水质问题 7.检查工艺过程,各工序的压力、水洗槽的溢流量
在德国汽车工业中使用 得较广泛 在美国得到广泛使用 在日本使用得比较普遍
22
无铬钝化剂
Parcolene 90
原理:在磷化膜表面形成一层100埃的聚合物覆盖膜。 这层覆盖膜能与磷化膜螯合,并与油漆 交叉连接。 作用:1.封闭磷化膜孔隙,提高耐腐蚀性能。 2.为后续油漆提供一个微酸性的表面,加强油漆与底材 的结合力。
3
污物的种类及来源
•电镀和酸洗(金属盐,铁粉末) •轧制和预润滑油(脂肪酸,蜡) •金属氧化物 •表面碳粉(退火处理) •CRS的碳化物 •平板清洗 •冲压润滑油/ 拉伸液 •操作 •焊接,焊接剂,铜焊 •研磨,擦洗,金属污物 •粘合剂和密封胶 •金属记号笔印
金属加工
冲压和装配
冷凝和金属氧化 运输油和热处理 防锈油
环境和运输
4
脱脂剂的组成
• 无机盐和碱
有机成分 消泡剂 络合剂 表面活性剂
5
影响清洗效果的因素
清洗剂的种类 浓度 化学品
处理方法 机械作用 (浸渍,喷淋)
处理温度 基材和污染物
处理温度
处理时间
处理时间 槽液污染程度
6
泡沫问题 引起泡沫的因素: 温度 阴离子乳化剂的带入 喷淋压力 非离子乳化剂的带入 非离子型消泡剂的分解 (例如:油水分离器,离心分离器)
27
现场服务和槽液管理
日常检查项目
磷化前的检查 检查车身板材的生锈,氧化情况 检查污染情况-悬链的滴落水、油污、密封胶、拉伸油等 确保预清洗是完全的 磷化的检查 检查喷嘴和泵的压力 检查计量泵,磷化渣的情况 检查喷嘴的图形 温度的检查或校对 磷化后的检查 检查磷化膜的外观是否均匀,生锈 检查车身上渣的附着情况 避免打磨后的“ 露底”,避免受到污染
表调工位: pH值 总碱
1. 水洗工位在必要时, 检测pH值, 电导, 污染度; 2. 除了上述参数外, 物理参数需检查, 如: 压力, 温度等;
30
故障处理 (一)
如果在磷化膜表面突然出现了问题, 而在此之前又是很令人满意的话, 那么, 首先必须提出三个假设的问题:
什么东西发生了变化? 变化的程度如何? 为什么会发生这种变化?
-表调较弱; -与底材有关; -金属表面处理过;-工件干燥; -高游离酸; -低促进剂;
14
促进剂的作用机理
氢气的去极化
防止在工件表面形成阻碍磷化膜生成的氢气泡, 使磷化膜均匀,致密。
Fe2+的氧化
Fe2+被氧化成Fe3+,然后形成磷化渣被除去。
15
磷化工艺对膜重的影响
影响因素: ♣ ♣ ♣ ♣ ♣ ♣ ♣ ♣ Total acid Free acid Acid ratio Accelerator Phosphate/Nitrate ratio Temperature Treatment time Activation 总酸 游离酸 酸比 促进剂 磷酸根/硝酸根的比 温度 处理时间 表调作用
12
磷化液的组成
阴离子: –Phosphat (PO43-) –Nitrate (NO3-) –Sulfate (SO42+) –Chloride (Cl-) –Fluoride (F-) –Complex Fluoride (SiF62-)
13
磷化液的组成
促进剂: – Nitrate (NO3-) – Nitrite (NO2-) – Chlorate (ClO3-) – Hydrogen peroxide (H2O2)
32
故障处理 (三) 8.检查操作人员的工作是否正确 9.检查烘炉温度。温度是否达到了要求?仪表和记录 是否准确? 10.检查磷化设备的喷嘴有无堵塞,是否调整,工件 在工序间是否保持湿润 11.检查线速度有无变化? 12.检查现场使用中的材料是否正确 13.检查是否坚持遵守了维修制度 14.检查槽液是否负载过度或比例失去平衡 15.检查工件种类是否变化,若是,应重新设计夹具和 设备调整
34
工件干燥 水洗不充分
常见故障的处理 (二)
表调工位 表调无效或 低效;采取的措施 槽液使用寿命较短-检查加料系统; 设备是否正常/提高表调剂浓度; -检查水质; 优先使用纯水/软化水; -检查pH值;(pH>8.5) -检查溢流; 每周更新一次槽液,1-8周更换; -检查循环量和 预混和槽的搅拌; -检查总碱;(前道工序的带入)
汽车前处理技术
1
前处理线-汽车工业
供水
1 2 3 4 5
集液沟
过滤器或 淤泥清理机
油水分离器
8 11 9 10
6
7
压滤机
排水沟
2
前处理典型工艺
工位 1。喷淋预脱脂 2。脱脂 3。脱脂 4。喷淋水洗 5。浸渍水洗 6。表调 7。磷化 8。喷淋水洗 9。浸渍水洗 10。纯水洗(钝化) 11。新鲜纯水喷淋 时间 1-3分钟 1-3分钟 1-3分钟 0.5-1分钟 1分钟 1分钟 3分钟 0.5分钟 1分钟 1分钟 0.5分钟 温度 50-65℃ 50-65℃ 50-65℃ 常温 常温 常温 40-55℃ 常温 常温 常温 常温 压力 1.5-3 bar 1.5-3 bar 1.5-3 bar 1.5-2.5 bar 1-2 bar 1-2 bar 0.8-1.2 bar 1-2 bar 1-2 bar 1-2 bar 0.5-1.5 bar
33
常见的故障处理(一)
脱脂工位 脱脂不彻底 -水花/磷化后斑点
采取的措施 -提高游离碱至上限; -增加表面活性剂的含量; -提高温度至上限; -增加喷淋压力或循环量; -调整喷嘴; -进行预擦洗; -在车身车间加强对车身的清洗; -适当提高第一水洗的总碱度; -增加工位之间的喷湿喷嘴; -排放槽液,进行更新;
35
常见故障的处理 (三)
磷化工位 膜重太重 可能的原因 -表调失效; -游离酸太低; -温度太高; -总酸太高; -严重的表面处理;-底材活性的变化; -磷化槽液循环太弱; -温度太低; -高游离酸; -工件干燥; -促进剂太低;(CRS) -表调太强; -底材内在的问题;
膜重太轻
晶粒尺寸太大
16
磷化液中的有害离子
Aluminium Lead Chrome Tin Molybdenum Arsenic
(Cr3+/Cr6+)
铝 铅 铬 锡 钼 砷
17
油漆对磷化膜的要求 封闭,致密的磷化层 均匀,细小的磷化膜 无挂灰 柔软性 耐腐蚀性
18
磷化槽液的分析
28
现场服务和槽液管理 样板试验 磷化膜膜重; 磷化膜的P-比; 磷化膜的晶粒尺寸; 磷化膜的晶貌形态;
29
现场服务和槽液管理
槽液的参数测定 脱脂工位: 总碱 游离碱 总碱/游离碱 磷化工位: 游离酸 总酸 促进剂 锌/镍/锰/(氟) 磷化渣 钝化工位: pH值 浓度
喷淋:反应1>反应2;浸渍:反应2>反应1
11
磷化液的成分
阳离子: –Zinc (Zn2+) –Nickel (Ni2+) –Manganese ;) –Magnesium (Mg2+) –Copper (Cu2+) –Iron (Fe2+) –Cobalt (Co2+)