开姆洛克CHEMLOK胶粘剂的性质及选用
Chemlok 6150 胶合剂技术数据表说明书
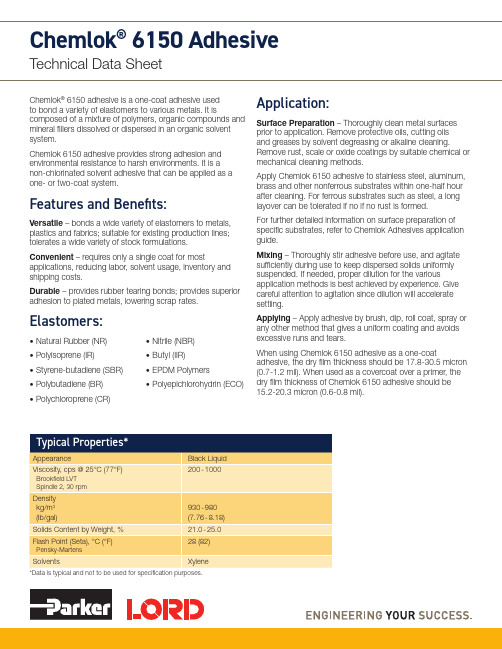
Chemlok® 6150 Adhesive Technical Data SheetChemlok® 6150 adhesive is a one-coat adhesive usedto bond a variety of elastomers to various metals. It is composed of a mixture of polymers, organic compounds and mineral fillers dissolved or dispersed in an organic solvent system.Chemlok 6150 adhesive provides strong adhesion and environmental resistance to harsh environments. It is anon-chlorinated solvent adhesive that can be applied as a one- or two-coat system.Features and Benefits:Versatile – bonds a wide variety of elastomers to metals, plastics and fabrics; suitable for existing production lines; tolerates a wide variety of stock formulations.Convenient – requires only a single coat for most applications, reducing labor, solvent usage, inventory and shipping costs.Durable – provides rubber tearing bonds; provides superior adhesion to plated metals, lowering scrap rates. Elastomers:• Natural Rubber (NR) • Nitrile (NBR)• Polyisoprene (IR) • Butyl (IIR)• Styrene-butadiene (SBR) • EPDM Polymers• Polybutadiene (BR) • Polyepichlorohydrin (ECO)• Polychloroprene (CR)Application:Surface Preparation – Thoroughly clean metal surfaces prior to application. Remove protective oils, cutting oilsand greases by solvent degreasing or alkaline cleaning. Remove rust, scale or oxide coatings by suitable chemical or mechanical cleaning methods.Apply Chemlok 6150 adhesive to stainless steel, aluminum, brass and other nonferrous substrates within one-half hour after cleaning. For ferrous substrates such as steel, a long layover can be tolerated if no if no rust is formed.For further detailed information on surface preparation of specific substrates, refer to Chemlok Adhesives application guide.Mixing – Thoroughly stir adhesive before use, and agitate sufficiently during use to keep dispersed solids uniformly suspended. If needed, proper dilution for the various application methods is best achieved by experience. Give careful attention to agitation since dilution will accelerate settling.Applying – Apply adhesive by brush, dip, roll coat, spray or any other method that gives a uniform coating and avoids excessive runs and tears.When using Chemlok 6150 adhesive as a one-coat adhesive, the dry film thickness should be 17.8-30.5 micron (0.7-1.2 mil). When used as a covercoat over a primer, the dry film thickness of Chemlok 6150 adhesive should be15.2-20.3 micron (0.6-0.8 mil).Parker LORDEngineered Materials Group 111 LORD DriveCary, NC 27511-7923USAphone +1 877 ASK LORD (275 5673)Values stated in this document represent typical values as not all tests are run on each lot of material produced. For formalized product specifications for specific product end uses, contact the Customer Support Center.Information provided herein is based upon tests believed to be reliable. In as much as Parker LORD has no control over the manner in which others may use this information, it does not guarantee the results to be obtained. In addition, Parker LORD does not guarantee the performance of the product or the results obtained from the use of the product or this information where the product has been repackaged by any third party, including but not limited to any product end-user. Nor does the company make any express or implied warranty of merchantability or fitness for a particular purpose concerning the effects or results of such use.WARNING — USER RESPONSIBILITY . FAILURE OR IMPROPER SELECTION OR IMPROPER USE OF THE PRODUCTS DESCRIBED HEREIN OR RELATED ITEMS CAN CAUSE DEATH, PERSONAL INJURY AND PROPERTY DAMAGE.This document and other information from Parker-Hannifin Corporation, its subsidiaries and authorized distributors provide product or system options for further investigation by users having technical expertise.The user, through its own analysis and testing, is solely responsible for making the final selection of the system and components and assuring that all performance, endurance, maintenance, safety and warning requirements of the application are met. The user must analyze all aspects of the application, follow applicable industry standards, and follow the information concerning the product in the current product catalog and in any other materials provided from Parker or its subsidiaries or authorized distributors.To the extent that Parker or its subsidiaries or authorized distributors provide component or system options based upon data or specifications provided by the user, the user is responsible for determining that such data and specifications are suitable and sufficient for all applications and reasonably foreseeable uses of the components or systems.©2021 Parker Hannifin - All Rights ReservedInformation and specifications subject to change without notice and without liability therefor. Trademarks used herein are the property of their respective owners.Chemlok 6150 Adhesive — Technical Data SheetOD DS4428 07/21 Rev.2Drying/Curing – Allow the applied adhesive to dry until visual examination of the film has shown that all solvent has evaporated. This will take approximately 20-40 minutes at room temperature. Drying time can be shortened by either preheating the metal inserts or oven drying after application. Metal parts may be preheated to a maximum of 65°C (150°F) prior to adhesive application. For coated parts, moderate drying temperatures should be used, but temperatures as high as 149°C (300°F) may be used for very short periods of time. Maximum air flow at minimum temperatures will give the best results.Cleanup – Use solvents such as xylene and MEK to remove adhesive before heat is applied. Once cured, removal by solvent is not possible.Shelf Life/Storage:Shelf life is one year from date of shipment when stored by the recipient in a well ventilated area at 21-27°C (70-80°F) in original, unopened container. Do not store or use near heat, sparks or open flame. Keep container tightly closed when not in use.Chemlok 6150 adhesive is moisture sensitive. Minimizeexposure of the adhesive to moisture during application and storage. Avoid excessive exposure to high humidity.Cautionary Information:Before using this or any Parker LORD product, refer to the Safety Data Sheet (SDS) and label for safe use and handling instructions.For industrial/commercial use only. Must be applied by trained personnel only. Not to be used in household applications. Not for consumer use.。
Chemlok EP5080-11 说明书

Chemlok® EP5080-11 Technical Data SheetChemlok® EP5080-11 is a non-pigmented version of Chemlok 205. Chemlok EP5080-11 is designed for use as a substrate primer under Chemlok covercoats to affix a wide variety of vulcanized and unvulcanized rubber compounds to metals and other rigid substrates. Chemlok EP5080-11 may also be used as a one-coat surface treatment to affix nitrile elastomers to metal. Features and Benefits:Versatile – can be used as a primer under a wide variety of Chemlok covercoats such as the Chemlok 220 series, Chemlok 230 series or Chemlok 6000 series.Easy to Apply – applies easily by brush, dip, spray or roll coat methods; suitable for existing production lines. Durable – provides high tear and cohesive strength, as well as excellent environmental resistance when used in combination with Chemlok covercoats.Fluid Resistant – provides excellent resistance to ASTM Oils #1 and #3 and Reference Fuel B.Convenient – requires only a single coat application to affix nitrile rubber compounds to rigid substrates during vulcanization.Application:Surface Preparation – Thoroughly clean metal surfaces prior to application. Remove protective oils, cutting oils and greases by solvent degreasing or alkaline cleaning. Remove rust, scale or oxide coatings by suitable chemical or mechanical cleaning methods.Apply Chemlok EP5080-11 to stainless steel, aluminum, brass and other nonferrous substrates within one hour after cleaning. For ferrous substrates such as steel, a longer layover can be tolerated if no rust is formed.For further detailed information on surface preparation of specific substrates, refer to Chemlok application guide. Mixing – Stir Chemlok EP5080-11 before use. Material does not require extensive mixing.If dilution is needed, use ketone-type solvents such as MEK and MIBK. Note proper dilution for the various application methods is best achieved by experience. Give careful attention to agitation since dilution will accelerate settling. Applying – Apply Chemlok EP5080-11 by brush, dip, roll coat, spray or any method that gives a uniform coating and avoids excessive runs or tears.Normally the dry film thickness of Chemlok EP5080-11 should be 5.1-10.2 micron (0.2-0.4 mil). When using over grit blasted substrates or when using it in conjunction with Chemlok 220 series covercoats, apply a dry film thickness at the high end of the range. For certain applications (i.e., swaging or smooth substrates), apply at the low end of the film thickness range.Drying/Curing – Thoroughly dry coated parts before applying the covercoat. This will take approximately 30-45 minutes at room temperature. It is best to use temperatures of 65-93°C (150-200°F) and abundant circulating air; however, forced air drying is possible at temperatures up to 149°C (300°F) for short periods of time. Maximum air flow at minimum temperatures will give the best results. After parts have dried, apply Chemlok covercoats using similarapplication methods.Chemlok EP5080-11 — Technical Data SheetParker LORDEngineered Materials Group 111 LORD DriveCary, NC 27511-7923USAValues stated in this document represent typical values as not all tests are run on each lot of material produced. For formalized product specifications for specific product end uses, contact the Customer Support Center.Information provided herein is based upon tests believed to be reliable. In as much as Parker LORD has no control over the manner in which others may use this information, it does not guarantee the results to be obtained. In addition, Parker LORD does not guarantee the performance of the product or the results obtained from the use of the product or this information where the product has been repackaged by any third party, including but not limited to any product end-user. Nor does the company make any express or implied warranty of merchantability or fitness for a particular purpose concerning the effects or results of such use.WARNING — USER RESPONSIBILITY . FAILURE OR IMPROPER SELECTION OR IMPROPER USE OF THE PRODUCTS DESCRIBED HEREIN OR RELATED ITEMS CAN CAUSE DEATH, PERSONAL INJURY AND PROPERTY DAMAGE.This document and other information from Parker-Hannifin Corporation, its subsidiaries and authorized distributors provide product or system options for further investigation by users having technical expertise.The user, through its own analysis and testing, is solely responsible for making the final selection of the system and components and assuring that all performance, endurance, maintenance, safety and warning requirements of the application are met. The user must analyze all aspects of the application, follow applicable industry standards, and follow the information concerning the product in the current product catalog and in any other materials provided from Parker or its subsidiaries or authorized distributors.To the extent that Parker or its subsidiaries or authorized distributors provide component or system options based upon data or specifications provided by the user, the user is responsible for determining that such data and specifications are suitable and sufficient for all applications and reasonably foreseeable uses of the components or systems.©2021 Parker Hannifin - All Rights ReservedInformation and specifications subject to change without notice and without liability therefor. Trademarks used herein are the property of their respective owners.OD DS6040CE 04/21 Rev.1Cleanup – Clean areas with a rag as soon as possible using MEK.Shelf Life/Storage:Shelf life is one year from date of shipment when stored by the recipient at 21-27°C (70-80°F) in original, unopened container.Cautionary Information:Before using this or any Parker LORD product, refer to the Safety Data Sheet (SDS) and label for safe use and handling instructions.For industrial/commercial use only. Required to use under organized emissions. Must be applied by trained personnel only. Not to be used in household applications. Not for consumer use.Chemlok® EP5080-11是Chemlok 205的无色版本。
粘合剂CH205 CH220

一、用途:适合丁腈橡胶与金属的单涂层胶粘剂,各种金属、塑料与橡胶粘接的底涂胶粘剂。
二、特点:1、与钢、不锈钢、铝、铁、铜、铜合金等多种金属粘合性优良。
2、有防锈功能。
3、耐水、雾盐、化学品、高温、油、溶剂等,具有良好的耐腐蚀性和耐环境性。
4、适用于注模法硫化工艺。
5、涂胶后,停放时间长。
三、功能组份:有机聚合物和分散填料,溶解或分散在甲基异丁基酮、二甲苯系统中颜色:灰色不透明粘度:85~165cps含固量:重量份22~26%覆盖面积:10~20平方米/kg密度:912~982kg/立方米比重:0.91~0.97闪点:19℃稀释剂:甲基异丁基酮或甲乙酮溶剂:甲基异丁基酮或二甲苯储存期:(25℃)为开封的容器 12个月四、工艺金属表面处理:机械处理(喷砂)后脱脂,或化学处理。
搅拌:在使用之前必须充分搅拌,达到均匀混合后方可使用。
涂胶方法:浸渍法、喷涂法、刷涂法、辊涂法、转移法。
涂胶厚度:(干膜)5~12干燥:涂胶后应在清洁空气中干燥30~45分钟(室温)固化时间:取决于胶料硫化时间。
五、注意事项1、应远离热源火花及明火。
2、溶剂蒸汽有害,工作场所注意防火通风,防止长期吸入及长期皮肤接触。
一、用途:多种未硫化橡胶与涂有Chemlok205的金属粘接的热硫化型胶粘剂。
二、特点:1、高强度粘接多种未硫化橡胶与涂有CH205的金属,适用橡胶有:丁腈胶、氯丁胶、天然胶、顺丁胶、丁苯胶、异戊橡胶和聚丁二烯橡胶。
2、耐热、耐水、盐雾、化学品、油脂以及多种溶剂,并具有良好的耐腐蚀性和耐环境性。
3、干燥胶膜坚硬,适用于注模硫化工艺。
4、涂胶后,可较长时间停放。
三、性能组分:有机聚合物和分散填料,溶解在二甲苯和过氯乙烯溶剂系统中颜色:黑色,不透明粘度:135~300cps含固量:23~27%(重量份)比重:1.00~1.10闪点:28℃稀释剂:二甲苯、甲苯、氯化溶剂溶剂:二甲苯、过氯乙烯储存期:为开启容器(25℃) 24个月四、工艺表面处理:机械法(喷砂)后脱脂,或化学处理。
Chemlok 607 胶水技术数据表说明书

Chemlok® 607 Adhesive Technical Data SheetChemlok® 607 adhesive is a clear, one-coat adhesive used to bond unvulcanized silicone rubber to various substrates such as metals, glass, plastics and textiles.Chemlok 607 adhesive also bonds specialty elastomers such as fluoroelastomers, polyacrylates, epichlorohydrin and some peroxide-cured elastomers. Features and Benefits:Versatile – provides excellent bonding characteristics between a wide variety of commercially available elastomer stocks and many diverse metallic and nonmetallic substrates.Environmentally Resistant – creates strong bonds capable of withstanding salt spray, harsh chemical exposure, corrosive atmospheres and temperature extremes.Durable – provides rubber tearing bonds that are stronger than the rubber; provides high strength performance at both high and low temperatures.Easy to Apply – applies easily by brush, spray or dip methods.High Temperature Resistant – withstands temperatures up to 204°C (400°F) and below -51°C (-60°F) when bonding with fluoroelastomers or silicone. Elastomers:• Polyacrylate (ACM) • Ethylene Acrylic (AEM)• Fluoroelastomer (FKM) • Epichlorohydrin (ECH)• S ilicone (VMQ, PMQ, PVMQ) - peroxide cure• Nitrile (NBR) - peroxide cure• Hydrogenated Nitrile (HNBR) - peroxide cure Application:Surface Preparation – Thoroughly clean metal surfaces prior to application. Remove protective oils, cutting oils and greases by solvent degreasing or alkaline cleaning. Remove rust, scale or oxide coatings by suitable chemical or mechanical cleaning methods.Carefully prepare nonmetallic surfaces. Fabric is usually desized by a scouring operation. Glass can be cleaned in an alkaline bath. Clean plastic surfaces with a solvent.For further detailed information on surface preparation of specific substrates, refer to Chemlok Adhesives application guide.Mixing – Pour the adhesive into a receptacle and dilute with methanol or ethanol as required. Average dilution ratios of 1:1 to 3:1 solvent to adhesive will provide the optimum adhesion and maximum coverage with minimum product use.Pour out only enough adhesive to use for a short periodof time, as rapid evaporation occurs in open containers. Porous substrates, such as heavy fabrics, may require more extensive dilution in order to prevent excessive pick-up.Applying – Apply adhesive in a uniformly thin coat by brush, spray or dip methods. Bond strength can be compromised by repeated brushing or improper dipping drainage.When coating fabrics, use a dry pick-up level of 0.05-1.0%, based on the dry weight of the fabric. Spray applications ensure that the adhesive is effectively applied to the fabric surface. For fabrics that are dipped or brushed, diluting the adhesive will help prevent fabric stiffness caused by excessive pick-up levels. For information on using dyes and fluorescing additives with Chemlok 607 adhesive, contactyour Parker LORD Technical Service Representative.Parker LORDEngineered Materials Group 111 LORD DriveCary, NC 27511-7923USAValues stated in this document represent typical values as not all tests are run on each lot of material produced. For formalized product specifications for specific product end uses, contact the Customer Support Center.Information provided herein is based upon tests believed to be reliable. In as much as Parker LORD has no control over the manner in which others may use this information, it does not guarantee the results to be obtained. In addition, Parker LORD does not guarantee the performance of the product or the results obtained from the use of the product or this information where the product has been repackaged by any third party, including but not limited to any product end-user. Nor does the company make any express or implied warranty of merchantability or fitness for a particular purpose concerning the effects or results of such use.WARNING — USER RESPONSIBILITY . FAILURE OR IMPROPER SELECTION OR IMPROPER USE OF THE PRODUCTS DESCRIBED HEREIN OR RELATED ITEMS CAN CAUSE DEATH, PERSONAL INJURY AND PROPERTY DAMAGE.This document and other information from Parker-Hannifin Corporation, its subsidiaries and authorized distributors provide product or system options for further investigation by users having technical expertise.The user, through its own analysis and testing, is solely responsible for making the final selection of the system and components and assuring that all performance, endurance, maintenance, safety and warning requirements of the application are met. The user must analyze all aspects of the application, follow applicable industry standards, and follow the information concerning the product in the current product catalog and in any other materials provided from Parker or its subsidiaries or authorized distributors.To the extent that Parker or its subsidiaries or authorized distributors provide component or system options based upon data or specifications provided by the user, the user is responsible for determining that such data and specifications are suitable and sufficient for all applications and reasonably foreseeable uses of the components or systems.©2021 Parker Hannifin - All Rights ReservedInformation and specifications subject to change without notice and without liability therefor. Trademarks used herein are the property of their respective owners.Chemlok 607 Adhesive — Technical Data SheetOD DS3151E 03/21 Rev.6Drying/Curing – Allow applied adhesive to air-dry forapproximately 10-30 minutes at room temperature. Porous substrates may require a longer time for the solvent to completely evaporate. Allow for longer drying times during humid conditions. The parts can be dried at elevated temperatures; excellent bonding properties have been achieved by drying at 104°C (220°F) for 15 minutes.Adhesive-coated parts may be bonded immediately after air-drying.Open steam, autoclave and other curing methods willproduce good bonds with Chemlok 607 adhesive. Maintain intimate contact between the compound and the bonding surface.Oven or post-cures can enhance bond strength because the bonded parts are exposed to higher temperatures for longer periods of time than during press-cure.Exposing the bonded part to high temperatures without proper conditioning at lower temperatures is detrimental to bond performance. This conditioning is especially important for end-use bond temperatures that exceed 204°C (400°F).Chemlok 607 adhesive bonds are resistant to manydestructive environments. Electroplating or anodizing metal parts after fabrication will not harm the bond.Shelf Life/Storage:Shelf life is two years from date of shipment when stored by the recipient at 21-27°C (70-80°F) in original, unopened container. Do not store or use near heat, sparks or open flame.Cautionary Information:Before using this or any Parker LORD product, refer to the Safety Data Sheet (SDS) and label for safe use and handling instructions.For industrial/commercial use only. Must be applied by trained personnel only. Not to be used in household applications. Not for consumer use.。
Chemlok 6150一种用于粘合各种弹簧到金属的表面处理剂说明书

Chemlok® 6150 Technical Data SheetChemlok® 6150 is a one-coat surface treatment usedto affix a variety of elastomers to various metals. It is composed of a mixture of polymers, organic compounds and mineral fillers dissolved or dispersed in an organic solvent system.Chemlok 6150 provides high strength systems with environmental resistance to harsh environments. It is a non-chlorinated solvent surface treatment that can applied as a one- or two-coat system.Features and Benefits:Versatile – affixes a wide variety of elastomers to metals, plastics and fabrics; suitable for existing production lines; tolerates a wide variety of stock formulations. Convenient – requires only a single coat for most applications, reducing labor, solvent usage, inventory and shipping costs.Durable – provides high tear and cohesive strength; demonstrates superior performance with plated metals, lowering scrap rates.Elastomers:• Natural Rubber (NR) • Nitrile (NBR)• Polyisoprene (IR) • Butyl (IIR)• Styrene-butadiene (SBR) • EPDM Polymers• Polybutadiene (BR) • Polyepichlorohydrin (ECO)• Polychloroprene (CR)Application:Surface Preparation – Thoroughly clean metal surfaces prior to application. Remove protective oils, cutting oils and greases by solvent degreasing or alkaline cleaning. Remove rust, scale or oxide coatings by suitable chemical or mechanical cleaning methods.Apply Chemlok 6150 to stainless steel, aluminum, brass and other nonferrous substrates within one-half hour after cleaning. For ferrous substrates such as steel, a longer layover can be tolerated if no rust is formed.For further detailed information on surface preparation of specific substrates, refer to Chemlok application guide. Mixing – Thoroughly stir Chemlok 6150 before use,and agitate sufficiently during use to keep dispersed solids uniformly suspended. If needed, proper dilutionfor the various application methods is best achieved by experience. Give careful attention to agitation since dilution will accelerate settling.Applying – Apply Chemlok 6150 by brush, dip, roll coat, spray or any other method that gives a uniform coating and avoids excessive runs and tears.When using Chemlok 6150 as a one-coat surface treatment, the dry film thickness should be 17.8-30.5 micron (0.7-1.2 mil). When used as a covercoat over a primer, the dry film thickness of Chemlok 6150 should be15.2-20.3 micron (0.6-0.8 mil).Chemlok 6150 — Technical Data SheetParker LORDEngineered Materials Group 111 LORD DriveCary, NC 27511-7923USAValues stated in this document represent typical values as not all tests are run on each lot of material produced. For formalized product specifications for specific product end uses, contact the Customer Support Center.Information provided herein is based upon tests believed to be reliable. In as much as Parker LORD has no control over the manner in which others may use this information, it does not guarantee the results to be obtained. In addition, Parker LORD does not guarantee the performance of the product or the results obtained from the use of the product or this information where the product has been repackaged by any third party, including but not limited to any product end-user. Nor does the company make any express or implied warranty of merchantability or fitness for a particular purpose concerning the effects or results of such use.WARNING — USER RESPONSIBILITY . FAILURE OR IMPROPER SELECTION OR IMPROPER USE OF THE PRODUCTS DESCRIBED HEREIN OR RELATED ITEMS CAN CAUSE DEATH, PERSONAL INJURY AND PROPERTY DAMAGE.This document and other information from Parker-Hannifin Corporation, its subsidiaries and authorized distributors provide product or system options for further investigation by users having technical expertise.The user, through its own analysis and testing, is solely responsible for making the final selection of the system and components and assuring that all performance, endurance, maintenance, safety and warning requirements of the application are met. The user must analyze all aspects of the application, follow applicable industry standards, and follow the information concerning the product in the current product catalog and in any other materials provided from Parker or its subsidiaries or authorized distributors.To the extent that Parker or its subsidiaries or authorized distributors provide component or system options based upon data or specifications provided by the user, the user is responsible for determining that such data and specifications are suitable and sufficient for all applications and reasonably foreseeable uses of the components or systems.©2021 Parker Hannifin - All Rights ReservedInformation and specifications subject to change without notice and without liability therefor. Trademarks used herein are the property of their respective owners.OD DS6002CE 07/21 Rev.2Drying/Curing – Allow Chemlok 6150 to dry until visual examination of the film has shown that all solvent has evaporated. This will take approximately 20-40 minutes at room temperature. Drying time can be shortened by either preheating the metal inserts or oven drying after application. Metal parts may be preheated to a maximum of 65°C (150°F) prior to application of Chemlok 6150. For coated parts, moderate drying temperatures should be used, but temperatures as high as 149°C (300°F) may be used for very short periods of time. Maximum air flow at minimum temperatures will give the best results.Cleanup – Use solvents such as xylene and MEK toremove Chemlok 6150 before heat is applied. Once cured, removal by solvent is not possible.Shelf Life/Storage:Shelf life is one year from date of manufacture whenstored by the recipient in a well ventilated area at 21-27°C (70-80°F) in original, unopened container. Do not store or use near heat, sparks or open flame. Keep container tightly closed when not in use.Chemlok 6150 is moisture sensitive. Minimize exposure to moisture during application and storage. Avoid excessive exposure to high humidity.Cautionary Information:Before using this or any Parker LORD product, refer to the Safety Data Sheet (SDS) and label for safe use and handling instructions.For industrial/commercial use only. Required to use under organized emissions. Must be applied by trained personnel only. Not to be used in household applications. Not for consumer use.Chemlok® 6150是一种单涂表面处理剂,可以帮助和促进各式各样的弹性体附着至各种金属。
Chemlok 7701 说明书

Chemlok® 7701 Technical Data SheetChemlok® 7701 is a solvent-based surface treatment for use on various vulcanized and thermoplastic polymeric materials. Chemlok 7701 chemically alters the surface of the rubber, making it more receptive to processing. Do not apply to metal surfaces.Chemlok 7701 is used in conjunction with a broad range of LORD Adhesives, including epoxy and urethane adhesives, for bonding cured rubber. It improves attachment to a variety of cured and thermoplastic polymeric materials, including natural rubber, synthetic polyisoprene, SBR, butyl, polybutadiene, neoprene, EPDM, nitrile, polyurethane, styrene-butadiene block copolymers, styrene isoprene rubbers and polyvinyl chloride.Features and Benefits:Versatile – functions as a cleaner and surface conditioner; treats a wide variety of elastomer functional materials. Easy to Apply – applies easily by wipe, brush, dip or flood methods.Convenient – requires no mixing.Improved Performance – improves performance on cast urethanes and cured rubber.Fast Drying – surface treatment flashes off within five minutes or less.Environmentally Resistant – promotes increased environmental resistance by allowing the treated surface to be more easily wet.Application:Surface Preparation – Remove contaminants from rubber surface using a solvent wipe.Applying – Apply Chemlok 7701 by wipe, brush, dip or flood methods. Spray application is not recommended due to the reactivity of the material.Transfer the minimum amount of material necessary for the application into a new, clean container.• Wiping (preferred method)Apply Chemlok 7701 using a clean cotton rag. Change the rag frequently as it becomes contaminated with materials picked up from the surface being treated.• BrushingApply Chemlok 7701 using a bristle or foam brush. Check foam-type brushes for compatibility before use. Use bristle brushes from man-made materials. Do not allow brushes with metal handles or metal collars to come in contact with Chemlok 7701.• DippingImmerse parts in Chemlok 7701. Place treated parts on a rack to allow excess material to drip off and the solvent to flash off.To prevent contamination, discard excess material; do not return excess material to original container.The treatment is complete after the solvent flashes off (<5 minutes). Rinsing is not necessary. The best performance is achieved by assembling parts shortly after the solvent has flashed off. However, effective performance has been obtained on parts stored under controlled conditions. Parts can be retreated, as necessary.Cleanup – Use ethyl acetate for clean up. In the event of aspill, use large quantities of water to flush the area.Chemlok 7701 — Technical Data SheetParker LORDEngineered Materials Group 111 LORD DriveCary, NC 27511-7923USAValues stated in this document represent typical values as not all tests are run on each lot of material produced. For formalized product specifications for specific product end uses, contact the Customer Support Center.Information provided herein is based upon tests believed to be reliable. In as much as Parker LORD has no control over the manner in which others may use this information, it does not guarantee the results to be obtained. In addition, Parker LORD does not guarantee the performance of the product or the results obtained from the use of the product or this information where the product has been repackaged by any third party, including but not limited to any product end-user. Nor does the company make any express or implied warranty of merchantability or fitness for a particular purpose concerning the effects or results of such use.WARNING — USER RESPONSIBILITY . FAILURE OR IMPROPER SELECTION OR IMPROPER USE OF THE PRODUCTS DESCRIBED HEREIN OR RELATED ITEMS CAN CAUSE DEATH, PERSONAL INJURY AND PROPERTY DAMAGE.This document and other information from Parker-Hannifin Corporation, its subsidiaries and authorized distributors provide product or system options for further investigation by users having technical expertise.The user, through its own analysis and testing, is solely responsible for making the final selection of the system and components and assuring that all performance, endurance, maintenance, safety and warning requirements of the application are met. The user must analyze all aspects of the application, follow applicable industry standards, and follow the information concerning the product in the current product catalog and in any other materials provided from Parker or its subsidiaries or authorized distributors.To the extent that Parker or its subsidiaries or authorized distributors provide component or system options based upon data or specifications provided by the user, the user is responsible for determining that such data and specifications are suitable and sufficient for all applications and reasonably foreseeable uses of the components or systems.©2021 Parker Hannifin - All Rights ReservedInformation and specifications subject to change without notice and without liability therefor. Trademarks used herein are the property of their respective owners.OD DS6073CE 01/21 Rev.0Shelf Life/Storage:Shelf life is six months from date of shipment when stored by the recipient at 21-27°C (70-80°F) in original, unopened container.Avoid storage in lighted areas. Store material in original container or UV-filtering plastic or glass container. Do not store in metal containers. Store Chemlok 7701 in a cool, dark area away from oil, grease, sawdust, floor sweepings, easily oxidized organic compounds, ammonia, amines, ammonia salts, and metallic materials. Do not contaminate with water or alcohol.Cautionary Information:Before using this or any Parker LORD product, refer to the Safety Data Sheet (SDS) and label for safe use and handling instructions.For industrial/commercial use only. Required to use under organized emissions. Must be applied by trained personnel only. Not to be used in household applications. Not for consumer use.Chemlok® 7701 是一款溶剂型表面处理剂,用于各种硫化和热塑性聚合物材料。
开姆洛克

开姆洛克205#
添加时间:
2004-3-16
产品功能:
有1kg, 3.5kg, 17kg三种规格:粘合丁腈橡胶与金属的单涂层胶粘剂,各种金属,塑料与橡胶粘接的底涂胶粘剂。与钢,不锈钢,铝,铁,铜,铜合金等多种金属粘合性优良。
产品名称:
开姆洛克238#
添加时间:
2004-3-16
产品功能:
有1kg, 3.5kg, 17kg三种规格:热硫化型胶粘剂用于粘接非极性弹性体与涂有CH205的金属或其它基材,也可用于非极性弹性体之间粘接。特别适用于未硫化丁基胶或三元乙丙胶与涂有CH205的金属热硫化粘合。适用橡胶还有:天然胶,丁苯胶,氯丁胶和丁腈胶等未硫化橡胶。也能用于上述胶种的硫化橡胶的热硫化粘合。
产品名称:
开姆洛克220#
添加时间:
2004-3-16
产品功能:
有1kg, 4kg, 20kg三种规格:它是多种未硫化橡胶与涂有Chemlok205的金属粘接的热硫化型胶粘剂。适用橡胶有:丁腈胶,氯丁胶,天然胶,顺丁胶,丁苯胶,异戊橡胶和聚丁二烯橡胶。
产品名称:
开姆洛克233#
添加时间:
2004-3-16
产品功能:
有1kg, 4kg, 20kg三种规格:它是多种橡胶与涂有Chemlok205的金属粘接的热硫化型胶粘剂。适用橡胶有:丁腈胶,氯丁胶,天然胶,顺丁胶,丁苯胶,异戊胶,丁基胶,氯醇胶,三元乙丙胶及混炼型聚氨酯。被粘基材除涂有CHEMLOK205的金属外,还有织物,玻璃,陶瓷和塑料。
产品名称:
产品名称:
开姆洛克5150#
添加时间:
2004-3-16
产品功能:
有1kg, 15kg两种规格:它是未硫化氟橡胶与金属等多种基材热硫化型胶粘剂。适用性广,能将多种未硫化氟弹性体与多种基材通过热硫化粘合,也可粘接同种已硫化氟橡胶。基材有:碳钢,不锈钢,铜和铝等金属。
开姆洛克成分

开姆洛克成分分析哎呀呀,今天咱来聊聊开姆洛克这个玩意儿的成分分析哈。
开姆洛克呢,它可是在好多领域都有重要作用的哦。
咱先看看它里面都有些啥成分吧。
这就像是一个大拼图,得一块一块地去研究。
这里面有一种成分就挺关键的,就像是团队里的核心人物一样。
它决定了开姆洛克的一些重要性能呢。
没有它呀,可能开姆洛克就不是现在我们熟悉的那个样子啦。
还有一些其他成分呢,它们就像是配角,但也是不能少的呀。
它们和那个关键成分相互配合,一起让开姆洛克发挥出它的厉害之处。
你说这成分分析是不是很有意思呀?就像我们去了解一个人的性格特点一样。
每个成分都有它自己的脾气和作用呢。
有时候我就在想呀,要是这些成分能开口说话,它们会说些啥呢?是不是会争着说自己有多重要呀,哈哈。
而且呀,研究开姆洛克的成分分析可不是一件简单的事儿哦。
得有专业的知识和技术才行呢。
就好像我们要解开一个很复杂的谜题,得一步步慢慢来。
那些搞研究的人呀,可真是不容易。
他们得花好多时间和精力去琢磨这些成分。
不过呢,也正是因为他们的努力,我们才能更好地了解开姆洛克呀。
你知道吗,开姆洛克的成分分析还会影响到它的使用呢。
就像我们穿衣服得根据场合选一样,不同的成分组合适合不同的情况。
有时候可能就因为成分上的一点点差别,开姆洛克的用途就完全不一样啦。
这可真是神奇呢。
再来说说这成分分析的过程吧,那可真是像一场冒险。
研究人员得小心翼翼地去探索,生怕错过了什么重要的细节。
他们就像侦探一样,一点点地去寻找线索,然后把这些线索拼凑起来,最后得出一个完整的答案。
哎呀呀,说了这么多,我都有点口渴啦。
不过呢,关于开姆洛克成分分析,我还能说好多好多呢。
总之呀,这是一个很有趣也很有意义的事儿。
它让我们能更好地利用开姆洛克,让它为我们的生活和工作带来更多的便利和好处。
以后要是再碰到开姆洛克,我就会想起今天说的这些啦。
哈哈,是不是很有意思呀?好啦,今天就先聊到这里啦,下次再接着聊别的有趣的事儿哦。
- 1、下载文档前请自行甄别文档内容的完整性,平台不提供额外的编辑、内容补充、找答案等附加服务。
- 2、"仅部分预览"的文档,不可在线预览部分如存在完整性等问题,可反馈申请退款(可完整预览的文档不适用该条件!)。
- 3、如文档侵犯您的权益,请联系客服反馈,我们会尽快为您处理(人工客服工作时间:9:00-18:30)。
开姆洛克C H E M L O K胶粘剂的性质及选用 Coca-cola standardization office【ZZ5AB-ZZSYT-ZZ2C-ZZ682T-ZZT18】开姆洛克(CHEMLOK)系列胶粘剂的性质及选用一,前言开姆洛克胶粘剂系美国洛德(LORD)公司产品,问世30年来,以粘结强度高,质量稳定,使用方便,而饮誉世界,广泛应用于各种橡胶与金属的粘合。
二,常用品种及分类情况分为三类:1底涂型,2,面涂型,3,单涂型,(1)能粘结多种金属:铸铁,碳钢,不锈钢,合金钢,铝,铝合金,铜,铜合金。
(2)与面涂型胶粘剂有良好的粘结性。
(3)有良好的防锈性能,能保护金属表面。
(4)有良好的耐环境性。
(5)亦可作为NBR的单涂型胶粘剂,即粘结金属与NBR时,一般不需再选用面涂型胶粘剂。
2,面涂型胶粘剂的特点(1)通过正确选用,能粘结各种通用橡胶。
(2)与底涂型胶粘剂(CH205)粘结性能优异。
由于面涂型胶粘剂与金属的粘结效果不是很好,或者即使有些品种,如常用的CH220,初期粘结强度亦很高,足以产生橡胶内聚破坏的结合力,但粘结件耐环境性,稳定性不足,因此,使用面涂型胶粘剂之前,金属表面一般宜先涂底涂型胶粘剂,确保与金属优良的粘合,确保粘结件的耐环境性,耐久性。
由一种底涂型胶粘剂和一种面涂型胶粘剂,便组成了洛德公司(LORD)所谓的双涂体系。
3,单涂型胶粘剂单涂体系或单涂型胶粘剂的特点:(1)与多种金属的粘结优良。
(2)通过正确的选用,能粘结所有的橡胶。
由于单涂型胶粘剂不需底涂,便可获得可靠的橡胶/金属粘结件,工艺上比较方便,因此比较受工厂欢迎。
值得注意是,虽然单涂型胶粘剂与金属的粘结优与面涂型胶粘剂,但不如底涂型胶粘剂。
同时单涂型胶粘剂粘结件的耐环境性,耐久性也不如双涂系列(底涂+面涂)。
三,性能与特点第一个特点适用面广,品种多进30个见表(1)硫化粘结各种橡胶与多种金属粘合,如铁,钢,不锈钢,合金钢,铝,铝合金,铜,铜合金等。
(2)硫化粘结各种橡胶与多种织物,纤维,如人造丝,尼龙,涤纶,玻纤,芳纶,碳纤维等。
粘合橡胶与织物常用的胶粘剂有四种:CH402,CH233,CH250,CH607。
前三种含少量非挥发性异氰酸酯,主要用于粘结通用橡胶与织物,后者为硅烷类,用于粘结硅橡胶,氟橡胶与织物。
(3)硫化粘结异种生胶或硫化胶,其中异种硫化橡胶之间的再次硫化粘结,洛德名之说“后硫化粘结”。
该技术适用于大多数通用橡胶,可选用的胶粘剂有:CH233,CH234B,CH236,CH238,CH252。
(4)硫化粘结各种橡胶与硬质塑料,硬质尼龙,。
粘结硅胶,氟胶时,可选用CH607。
粘结通用型橡胶时,可以选用以CH205底涂胶(CH205能与多种塑料粘结)。
第二个特点粘结强度高质量稳定粘结NBR,NR,BR,SBR,CR,EPDM,IIR等通用橡胶,都可确保获得橡胶内聚破坏的粘结强度,按HG4-852-81扯离强度测试,一般在4—8MPa左右,高时可达10MPa。
由于试验时,一般都发生橡胶破坏。
即使粘结特种胶如PU,CHC,CHR,CSM,FR,VMR等也能获得较好的粘结效果。
第三个特点耐环境性优良除了CH607的耐热性能低于它所能粘结的FR,VMQ以外,其它的粘合剂都优它所能粘结的橡胶。
油制品,如油封,胶管法兰接头时宜选用它俩。
第四个特点毒性较低使用方便除溶剂(甲苯,二甲苯,酮,乙醇等)为挥发性外,其余高聚物,化合物都为非挥发性物质。
故毒性低于异氰酸酯。
使用方便体现在:(1)单组份包装。
(2)储存期长,一般1--2年。
(3)适用于各种涂胶方式:刷涂,浸涂,喷涂,辊涂。
(4)金属件涂胶干燥后,可停放较长时间,只要不从新污染,不影响粘结效果。
(6)化,间接蒸汽,直接蒸汽,常压,中压,连续硫化。
(6)在模具中耐预热能力强,大多数开姆洛克胶粘剂在模具中于120—150℃温度下,预热10分钟,不会消弱粘结能力。
四,凯姆洛克的粘结原理(1)在低模量的橡胶与高模量的金属之间,胶粘剂应成为一个模量梯度层,以减少粘结件受力时的应力集中,因此胶粘剂层应有一定的厚度。
底涂胶粘剂模量总是大于面涂胶粘剂模量,而面涂胶粘剂模量一般都大于橡胶。
(2)底涂型胶粘剂,或单涂型胶粘剂之间,以胶粘剂与橡胶之间,通过相互扩散和共交联作用而实现粘结。
胶粘剂和橡胶界面之间的相互扩散对于优良的粘结是十分重要的。
充分的相互扩散,能在胶粘剂和橡胶之间形成一个完全连续的过渡层。
设计胶粘剂时应首先考虑到相互扩散能力。
并使在交联反应发生之前有足够的相互扩散时空。
(3)在设计胶粘剂时,应有下列次序发生。
A,底涂型,面涂型胶粘剂内部交联及共交联。
B,底涂型胶粘剂与金属产生吸附C,胶粘剂和橡胶产生共交联,橡胶交联。
橡胶与纤维,织物材料的粘结与此类似。
五,选用原则首先确定采用双涂还是单涂,要求高的产品或金属表面处理工艺不严的工在确定了单涂或双涂体系后,在选择具体品种时,至少要考虑10项因素:1,胶种,胶种不同粘结难易程度也不同。
通用橡胶的粘结性能差异,可用可粘性指数表示,极性橡胶优于非极性橡胶,开姆洛克与橡胶粘结规律如下:(CH233,CH234B,CH236,CH238CH250,CH252,CH257),CH220,CH205。
NBR可选用上述任何一种胶粘剂,在大部分情况下,只用CH205即完全满意的粘结。
CR,NR,SBR,BR等则必须用CH220(以CH205作底涂胶)或其它粘结性更高的品种,单用CH205则不行。
IIR,EPDM等则一般非用比CH220粘结性更强的品种,才能达到满意的效果。
2,橡胶硬度橡胶硬度对粘结难易性也有一定的影响。
对于NR,SBR,BR等橡胶,CH220/CH205双涂体系适用硬度范围大致为XHS=40--85,对于NBR,CH205使用范围也大致如此,也有工厂在使用中发现CH205可满意的粘结XHS=25的NBR。
在此硬度范围之外的胶料,一般选用粘结性更强的胶粘剂,即NBR选用CH220/CH205,甚至CH233/CH205等。
3,硫化剂类型同一种胶采用不同类型的硫化剂时,应选用不同的胶粘剂如:NBR 硫黄硫化体系选用CH205。
过氧化物硫化体系选用CH607,EPDM 硫黄CH236,CH238。
过氧化物CH607,CH246。
树脂CH252,CH238。
常用的适用过氧化物硫化的为CH238,CH246,CH252,CH607,CH608,其余常用品种以适应硫黄硫化为主。
4,硫化体系在常规,半有效(SEV)及有效硫化体系(EV)中,一般采用常规硫化体系(S>份)的胶料比较容易粘结,可采用CH220/CH205双涂体系。
SEV/EV硫化体系的胶料CH220/CH205不一定适用,故以选用比CH220更好的胶粘剂。
5,硫化速度一般都可确保胶粘剂固化反应起步早于橡胶硫化反应或两者同步发生,应注意胶料的焦烧期尽可能长些。
对于硅胶来说一般CH608的反应速度高于CH607,因此对于硫化温度下t1/2较短的过氧化物硅胶胶料,以及一些不需二段硫化的胶料,应考虑CH608。
6,门尼粘度由于开姆洛克胶粘剂干燥后胶膜胶硬(尤其是CH220/CH205)因此胶料门尼粘度低,有助于胶粘剂——胶料之间的密切接触及相互扩散,有利于粘结。
7,含油量胶料中低于20份时一般不发生问题,如含油量高于20份时,双涂体系以选用CH238为宜,单涂体系以CH252为好,这两种胶粘剂对高油量配方粘结效果好。
8,硫化方式橡胶与金属胶粘剂的一个重要性质是在受热的条件下耐冲刷性。
耐冲刷性差的胶粘剂,容易污染模具,造成粘模,使产品难于脱模,甚至由于胶粘剂冲离金属件表面而引起粘结失败。
这些现象在平板硫化中尚不十分严重,但在移模硫化和注模硫化过程中,则比较常见。
因此在采用后二种硫化方式时,宜选用CH220/CH205双涂体系或CH257单涂体系。
平板硫化则可视具体情况而定。
此外,一些采用直接蒸汽硫化的产品,如胶辊等,应避免选用含有异氰酸酯的品种,如CH250,CH252等。
9,产品使用要求开姆洛克胶粘剂的耐环境性一般都优于橡胶,但不同开姆洛克品种之间存在着一些差异,要求耐溶剂性的产品选用BN为好,要求高耐油性产品以CH252为宜,要求高耐热性产品应选用CH233/CH205或CH252。
10,CH220/CH205双涂体系该体系问世最早,已有30余年,仍是所有品种中最受欢迎,用量最大的品种,后续的改良品种,虽然粘结能力等某些方面超过了CH220,但在工艺稳定性,储存稳定性,耐胶料冲刷性等方面,尚无突出之处,因此,建议尽量优先考虑选用该体系。
六工艺要点正确选用胶粘剂品种后,工艺很关键,5个环节1,金属表面处理,除锈,脱脂,去污,可采用机械法,和化学法。
2,搅拌,出了CH218,CH607及CH608等少数几个品种为溶液体系外,其余为介散体系,由溶剂,可溶性化合物,聚合物及无机盐,填料组成。
在储运过程中沉淀,在使用前应十分注意充分搅拌,务使各种材料达到均匀分散,以半小时搅拌5分钟为好,3,稀释,由于国内涂胶一般都采用刷涂法,因此不需稀释。
在以下情况需稀释(1)由于储存期长,(2)采用喷涂法:2重量份胶粘剂/1重量份溶剂。
4,涂胶,可根据涂胶次数大略估计,以最常用的CH220/CH205位列,粘结NR,SBR,BR等通用橡胶时,只要胶粘剂粘度未超出规定范围,CH205只需涂一遍,当CH220涂一遍时,扯离强度一般为4---5MPa,CH220涂两遍后,扯离强度可达5---8MPa或更好些。
因此可根据要求决定涂的遍数。
(涂胶越厚粘结强度越高)。
5,干燥,干燥条件为:时温 30---60分钟70---80℃ 20---30分钟冬季最好能用热风机强制干燥,另外,开姆洛克胶粘剂涂胶干燥后,如果能在120℃烘10--15分钟,不但有利于彻底驱赶残留溶剂,还可提高胶粘剂膜在模腔内的耐冲刷性。
七,粘结结果评价及失败原因破坏分为4种类型:R---橡胶破坏,RC---橡胶与胶粘剂间破坏,CP---胶粘剂内聚破坏(面涂与底涂间破坏),M---胶粘剂与金属间破坏,若粘结件同时发生多种类型破坏,SR---斑点状橡胶破坏,金属表面附胶是斑点状。
TR---簿层橡胶破坏,金属表面附很簿而均匀橡胶层。
HR---厚层橡胶破坏,金属表面附较厚层橡胶。
SB---橡胶扯断。
粘结破坏类型及原因。