偏心轴的冷温复合挤压工艺及模具设计
《冷挤压成型工艺及模具设计》课程大纲

《冷挤压成型工艺及模具设计》课程教学大纲一、课程名称(中英文)中文名称:冷挤压成型工艺及模具设计英文名称:Cold Extrusion Processes and Die Design二、课程编码及性质课程编码:0817761课程性质:选修课三、学时与学分总学时:24学分:1.5四、先修课程机械设计、材料成形工艺、金属学及热处理和材料成形原理等五、授课对象本课程面向材料成型及控制工程专业学生开设,也可以供材料科学与工程专业和电子封装技术专业学生选修。
六、课程教学目的(对学生知识、能力、素质培养的贡献和作用)本课程是第七学期开设的一般选修课,其教学目的主要包括:1、掌握金属材料冷挤压的变形性质和成型规律,以及冷挤压模具设计的方法;2、掌握冷挤压成型工艺及模具设计的特点及国内外发展概况,查找并掌握冷挤压技术及模具设计发展前沿的新技术的特性;3、掌握挤压成形的各种方法,能独立编制工艺规程和设计冷挤压模具,分析和解决冷挤压生产问题,具有今后从事冷挤压成型工艺和复杂模具开发与设计的能力。
表1 课程目标对毕业要求的支撑关系七、教学重点与难点:教学重点:1)本课程以介绍冷挤压成型工艺与模具为主体、以讲述两者的设计为重点;2)在全面了解与掌握挤压成形的材料原理及力学原理的基础上,重点学习冷挤压加工工序和模具的设计;3)重点学习的章节内容包括:第2章“挤压基本原理”(6学时)、第5章“冷挤压加工工序设计”(4学时)、第6章“冷挤压模具设计”(6学时)。
教学难点:1)冷挤压成型工艺及模具设计是实践性极强的课程之一,本课程将密切结合学生的生产实习、课程设计、实验课等实践环节,培养学生对冷挤压成型工艺及模具的认识及设计能力,提高授课质量与效果。
2)通过本课程学习,要求掌握冷挤压成型工艺的变形特点、应用范围、质量控制方法等,具备合理设计冷挤压成型工艺和复杂模具的实践能力。
八、教学方法与手段:教学方法:(1)采用现代化教学方法(含PPT演示,工艺动画,视频资料等),讲授冷挤压工艺的变形特点及应用领域,以提高教学效果及效率;(2)采用课堂教学与学生PPT汇报、交流讨论等方式,进行课堂互动,吸引学生的注意力、激发学生的学习热情,提高学生的学习效果。
第五章冷挤压工艺及模具设计
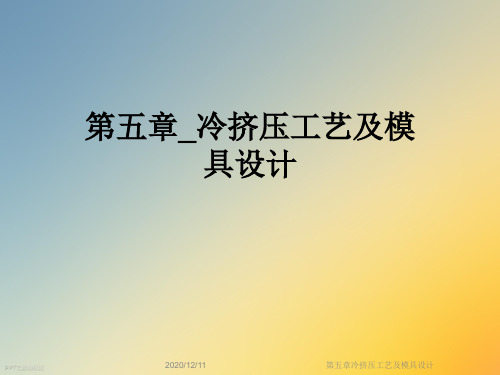
PPT文档演模板
2020/12/11
第五章冷挤压工艺及模具设计
冷挤压工艺及模具设计
•5.1 冷挤压工艺
•5.2 冷挤压模具设计 • •5.3 冷挤压模的典型结构
PPT文档演模板
第五章冷挤压工艺及模具设计
冷挤压工艺及模具设计
•5.1 冷挤压工艺
• 冷挤压是一种先进的少无切削加工工艺之一。它是在 常温下,使固态的金属在巨大压力和一定的速度下,通过模 腔产生塑性变形而获得一定形状零件的一种加工方法。冷挤 压的工艺过程是:先将经处理过的毛坯料放在凹模内,借助 凸模的压力使金属处于三向受压应力状态下产生塑性变形, 通过凹模的下通孔或凸模与凹模的环形间隙将金属挤出。它 是一种在许多行业广泛使用的金属压力加工工艺方法。
• (3) 冷挤压的变形方式 在变形程度相同的条件下, 反挤压的力大于正挤压的力。反挤压的许用变形程度比正挤 压小。
PPT文档演模板
第五章冷挤压工艺及模具设计
冷挤压工艺及模具设计
• (4) 毛坯表面处理与润滑 毛坯表面处理越好,润滑 越好,许用变形程度也就越大。
• (5) 冷挤压模具的几何形状 冷挤压模具工作部分的 几何形状对金属的流动有很大影响。形状合理时,有利于挤 压时的金属流动,单位挤压力降低,许用变形程度可以大些。
第五章冷挤压工艺及模具设计
冷挤压工艺及模具设计
•5.1.4.2 许用变形程度
• 冷挤压时,一次挤压加工所容许的变形程度,称为许 用变形程度。不同材料有不同的许用变形程度。在工艺上, 每道冷挤压工序的变形程度应尽量小于许用值,使模具承受 的单位挤压力不超过模具材料许用应力(目前一般模具材料 的许用应力为2500~3000N/mm2),确定许用变形程度数值 是冷挤压工艺计算的一个重要依据,因为冷挤压许用变形程 度的大小决定了制件所需的挤压次数。若计算出的冷挤压变 形程度超过许用值、则必须用多次挤压完成,以延长模具寿 命,避免损坏模具。
冷挤压工艺及模具设计

冷挤压工艺及模具设计
5.1.3 冷挤压毛坯的制备 5.1.3.1 冷挤压坯料形状与尺寸 挤压件的毛坯形状设计是否合理,将直接影响制件的形 状与尺寸,并且还将影响模具的寿命。冷挤压用毛坯通常都 是棒料或块料,其截面形状可根据制件的相应截面形状确定。 一般情况下,确定毛坯形状的原则是:旋转体及轴对称多角 类选用圆柱形毛坯;矩形零件可选用矩形毛坯。此外还应考 虑采用何种挤压方法,如图5-1所示,采用正挤压法时,用 实心毛坯能挤出实心件,用空心坯料能挤出空心件。反挤压 时,毛坯的形状采用实心和空心均可。
冷挤压工艺及模具设计
对于有些材料,为了确保冷挤压过程中的润滑层不被过 大的单位接触压力所破坏,毛坯要经过表面化学处理。例如 碳钢的磷酸盐处理(磷化)、奥氏体不锈钢的草酸盐处理、 铝合金的氧化、磷化或氟硅化处理、黄铜的钝化处理等。经 化学处理后的毛坯表面,覆盖一层很薄的多孔状结晶膜,它 能随毛坯一起变形而不剥离脱落,经润滑处理后在孔内吸附 的润滑剂可以保持挤压过程中润滑的连续性和有效的润滑效 果。
冷挤压工艺及模具设计
4.1.4.1 变形程度的表示方法 变形程度是表示挤压时金属塑性变形量大小的指标,其 最常用的表示方法有两种:截面收缩率和挤压面积比。 (1) 截面收缩率 式中
F0 − F1 εF = × 100% F0
(5-3)
ε F ——冷挤压的截面收缩率,见表5-1、表5-2;
F0——冷挤压变形前毛坯的横截面积,mm2; F1——冷挤压变形后工件的横截面积,mm2。
5.1.2 冷挤压的特点 5.1.2.1 冷挤压的特点主要包括以下三个方面: (1) 节约原材料,生产效率高 冷挤压是少无切削加工工艺,与切削加工相比,节约原 材料,同时,冷挤压是在压力机简单的往复运动中生产零件, 生产效率高,比切削加工高30倍。
冷挤压工艺及模具设计

冷挤压工艺及模具设计
5.1.1 冷挤压的分类 根据金属被挤出的方向与凸模运动方向的关系,冷挤压 一般可分为正挤压、反挤压、复合挤压三种基本方式。 1.正挤压如图5-1所示,挤压时金属流动方向与凸模流 动方向相同,适用于各种形状的实心件、管件和环形件的挤 压; 2.反挤压如图5-2所示,挤压时金属流动方向与凸模运 动方向相反,适用于各种截面形状的杯形件的挤压;
h0 V坯 。 F0
(5-2)
冷挤压工艺及模具设计
5.1.3.2 坯料的制备
冷挤压坯料制作要求十分细致、严格,有一定的平面度, 表面粗糙度、精度要求。可采用剪切加工、板料落料加工、 切削加工及其它特殊方法加工,毛坯的上、下端面必须平整。
5.1.3.3 毛坯的软化热处理 对毛坯进行软化热处理的目的是降低材料硬度,提高塑 性,得到良好的金相组织,消除内应力,以降低材料的变形 抗力,提高模具的寿命和零件质量。
2.选用合适的模具材料,工作部分必须要有相当的韧 性和耐磨性,几何形状及参数要合理、准确。有利于毛坯塑 性变形、降低单位挤压力。尽量采用光滑圆角过渡,防止应 力集中。
冷挤压工艺及模具设计
3.模具的易损部位,应考虑通用性和互换性。并便于 更换、修理。 4.对于精度要求较高的挤压件,模具设计要有良好的 稳定导向装置。
冷挤压工艺及模具设计
毛坯软化热处理规范可从相关手册中查到。但是,由于 保温时间同被处理毛坯尺寸、毛坯放置方法及装炉量等诸多 因素有关,因此在实际生产流程中,应根据具体情况确定保 温时间。
在冷挤压工序之间,还应根据变形程度和冷作硬化程度 的大小适当安排工序间软化热处理工序。
对于黄铜与硬铝挤压件,挤压后务必进行消除内应力的 退火。对于要求高的碳钢和不锈钢件,挤压后也需进行消除 应力退火的工序。
冷挤压工艺及模具设计共65页

11、用道德的示腊
12、法律是无私的,对谁都一视同仁。在每件事上,她都不徇私情。—— 托马斯
13、公正的法律限制不了好的自由,因为好人不会去做法律不允许的事 情。——弗劳德
14、法律是为了保护无辜而制定的。——爱略特 15、像房子一样,法律和法律都是相互依存的。——伯克
1、最灵繁的人也看不见自己的背脊。——非洲 2、最困难的事情就是认识自己。——希腊 3、有勇气承担命运这才是英雄好汉。——黑塞 4、与肝胆人共事,无字句处读书。——周恩来 5、阅读使人充实,会谈使人敏捷,写作使人精确。——培根
冷挤压模具设计
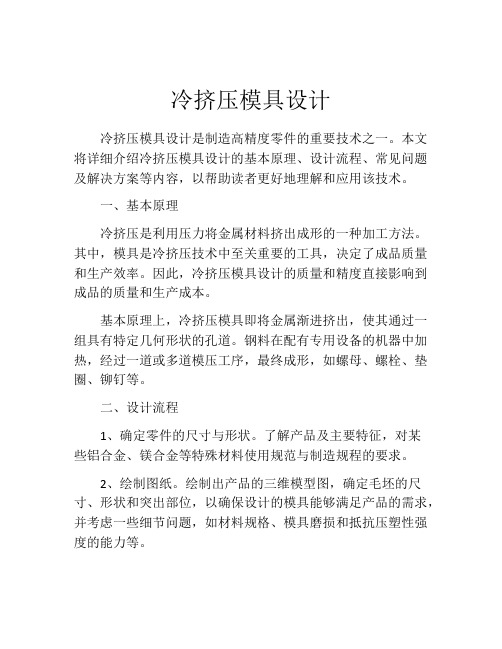
冷挤压模具设计冷挤压模具设计是制造高精度零件的重要技术之一。
本文将详细介绍冷挤压模具设计的基本原理、设计流程、常见问题及解决方案等内容,以帮助读者更好地理解和应用该技术。
一、基本原理冷挤压是利用压力将金属材料挤出成形的一种加工方法。
其中,模具是冷挤压技术中至关重要的工具,决定了成品质量和生产效率。
因此,冷挤压模具设计的质量和精度直接影响到成品的质量和生产成本。
基本原理上,冷挤压模具即将金属渐进挤出,使其通过一组具有特定几何形状的孔道。
钢料在配有专用设备的机器中加热,经过一道或多道模压工序,最终成形,如螺母、螺栓、垫圈、铆钉等。
二、设计流程1、确定零件的尺寸与形状。
了解产品及主要特征,对某些铝合金、镁合金等特殊材料使用规范与制造规程的要求。
2、绘制图纸。
绘制出产品的三维模型图,确定毛坯的尺寸、形状和突出部位,以确保设计的模具能够满足产品的需求,并考虑一些细节问题,如材料规格、模具磨损和抵抗压塑性强度的能力等。
3、确定模具类型。
根据产品的尺寸、形状和工艺要求,确定冷挤压模具的类型。
常用的冷挤压模具包括拉伸模、挤压模、钝化模、套筒模等。
4、设计模具的结构。
设计模具的结构时,需要考虑到模具主体的结构、腔体形状、孔形结构等几个方面,还需要根据压力、预压、挤出量等要素,确定可承受的载荷。
同时,还需要考虑一些实际运用中需要注意的问题,例如设定模具配合公差、调整模具的开合间隙、设定模具的定位和定向等。
5、制作模具样品。
样品制作过程中,需要考虑到模具结构的合理性,以及各种元素的配合度。
制作完成后,需要进行模具的调试、试胶、实验成型等环节,进行逐渐的调整和完善。
三、常见问题及解决方案1、模具寿命不够长。
在设计时应考虑模具的材质和硬度,通过表面热处理、高频淬火、氮化等方式进行强化处理,以延长模具的使用寿命。
2、模具容易出现磨损或变形。
在制作过程中,要合理设定模具的使用寿命,并且需要根据产品的多重要素,优化模具的设计结构,来提高其使用的稳定性。
冷挤压工艺和模具设计说明书模板

冷挤压工艺及模具设计
5.2 冷挤压模具设计
5.2.1 冷挤压模的特点
由于冷挤压时,单位挤压力较大,因此冷挤压模具的强 度、刚度及耐用度等方面其要求都比一般冲模高,它与一般 普通冲模相比,主要有以下特点: 1.模具的工作部分与上、下底板之间一般都设有足够 的支承面与足够厚度的淬硬垫板,以承受很大的压力,减少 上、下底板上的单位压力。
冷挤压时,一次挤压加工所容许的变形程度,称为许用 变形程度。不同材料有不同的许用变形程度。在工艺上,每 道冷挤压工序的变形程度应尽量小于许用值,使模具承受的 单位挤压力不超过模具材料许用应力(目前一般模具材料的 许用应力为2500~3000N/mm2),确定许用变形程度数值是 冷挤压工艺计算的一个重要依据,因为冷挤压许用变形程度 的大小决定了制件所需的挤压次数。若计算出的冷挤压变形 程度超过许用值、则必须用多次挤压完成,以延长模具寿命, 避免损坏模具。
冷挤压工艺及模具设计
3.复合挤如图5-3所示,挤压时,金属流动方向相对于 凸模运动方向,一部分相同,另一部分相反,适用于各种复 杂形状制件的挤压;改变凹模孔口或凸、凹模之间缝隙的轮 廓形状,就可以挤出形状和尺寸不同的各种空心件和实心件。
图5-1 正挤压图
5-2 反挤压图
5-3 复合挤
冷挤压工艺及模具设计
程度。
冷挤压工艺及模具设计
4.1.4.1 变形程度的表示方法 变形程度是表示挤压时金属塑性变形量大小的指标,其 最常用的表示方法有两种:截面收缩率和挤压面积比。 (1) 截面收缩率 式中
第七章冷挤压工艺与模具设计

3)模具的材料选择、加工方案和热处理规范的 确定都应合理;
4)模具的安装牢固可靠, 易损件的更换、拆卸、 安装方便;
5)模具导向良好, 以保证制件的公差和模具寿命 ;
7.5.2 冷挤压凸、凹模设计 (1)凸模
•a)
b)
c)
层和三层结构式。
•组合凹模的选择 单位压力(p凹/MPa) 凹模形式
≤1000~1200
整体凹模
简图
1200<p≤1400~1600 二层组合凹模
1400<p≤2200~2500 三层组合凹模
②二层组合凹模
③三层组合凹模
•二层组合凹模
•三层组合凹模
④组合凹模压合方法 a)加热压合(热装)
将外圈加热到适当温度, 套装到内圈上, 待外圈冷 却后将内圈压紧。热装时可不必加工出斜度。 b)强力压合
3)确定各图的直径 ①外圆外径d3, 由步骤2, 已知 d3=a31d1=4×66=264 d3取260mm
②内圆半径d2 d2=a21×d1 a21根据a31的取值, 查右图•两层组合凹模的a31与a21的关系
4)确定组合凹模的轴向、径向过盈量c2和u2.β2.δ2为过 盈量系数
β2=0.008 δ2=0.16 则
(4)径向挤压
•a)
b)
•冷模锻零件
•a)毛坯 b)零件
•
a)
b)
•
径向挤压
•
a)毛坯 b)零件
• (5)实例挤压方式的选择 • 工件的冷挤压成形工艺方案有以下三种: • ①采用圆柱毛坯,径向挤压成形凸缘部分;反挤压成形筒部。 • ②采用圆柱毛坯,预成形杯形;正挤压达到工件要求。 • ③采用圆柱毛坯,复合挤压一次成形。(采用)
- 1、下载文档前请自行甄别文档内容的完整性,平台不提供额外的编辑、内容补充、找答案等附加服务。
- 2、"仅部分预览"的文档,不可在线预览部分如存在完整性等问题,可反馈申请退款(可完整预览的文档不适用该条件!)。
- 3、如文档侵犯您的权益,请联系客服反馈,我们会尽快为您处理(人工客服工作时间:9:00-18:30)。
偏心轴的冷温复合挤压工艺及模具设计
一、概述
偏心轴是指轴心不在几何中心的轴,其制造难度较大。
传统的挤压工艺难以满足偏心轴的制造要求,因此需要采用冷温复合挤压工艺。
二、冷温复合挤压工艺
冷温复合挤压工艺是指在挤压过程中,先采用冷挤压的方式将材料压制成初形状,然后再进行温挤压,使其达到最终形状。
该工艺具有以下优点:
1. 可以有效降低材料变形率,提高材料的力学性能。
2. 可以减少挤压过程中的应力和变形,提高挤压品的表面质量。
3. 可以控制挤压温度,避免材料的热变形和晶粒长大。
三、模具设计
1. 偏心轴的模具设计需要考虑到偏心度、壁厚和挤压力等因素。
2. 模具的结构应该合理,能够有效控制材料的流动和变形。
3. 模具的材料应该具有高强度、高硬度和高耐磨性,以保证模具的使用寿命。
四、案例分析
某公司需要生产偏心轴,采用冷温复合挤压工艺进行生产。
通过模具设计和工艺优化,成功生产了符合要求的偏心轴产品。
该产品的力学性能和表面质量均达到了设计要求。
五、结论
偏心轴的制造需要采用冷温复合挤压工艺和合理的模具设计。
这种工艺可以有效提高材料的力学性能和表面质量,同时能够控制材料的流动和变形。
模具的设计应该合理,材料应该具有高强度、高硬度和高耐磨性。