冲压模具调试板料流入量影响因素分析
冲压加工不良及对策

冲压加工不良及对策
冲压加工不良及对策通常涉及到多个方面,包括材料问题、设备问题、模具设计和制造问题,以及操作人员的技术水平等。
以下是一些常见的冲压加工问题及其可能的对策:
1.材料问题:如果使用的材料不符合要求,可能会导
致冲压件质量不稳定。
对策包括确保材料的质量和
规格符合产品设计要求,以及进行适当的材料预处
理。
2.模具设计和制造问题:模具设计不当或制造精度不
够,都会影响冲压件的质量。
对策包括优化模具设
计,确保模具的精确制造和定期维护。
3.设备问题:设备的不稳定性或精度不足会影响冲压
效果。
对策包括定期维护和校准冲压设备,确保其
稳定性和精度。
4.操作技术问题:操作人员的技术水平不足也会影响
产品质量。
对策包括提供专业培训,确保操作人员
掌握必要的技能和知识。
5.环境因素:环境温度、湿度等因素也可能影响冲压
件的质量。
对策包括控制生产环境,确保稳定的工
作条件。
每个具体的冲压加工问题都需要根据实际情况进行详细分析,采取相应的解决措施。
在处理这些问题时,通常需要跨部门合作,综合考虑不同因素的影响。
汽车冲压模具调试存在的问题及解决措施
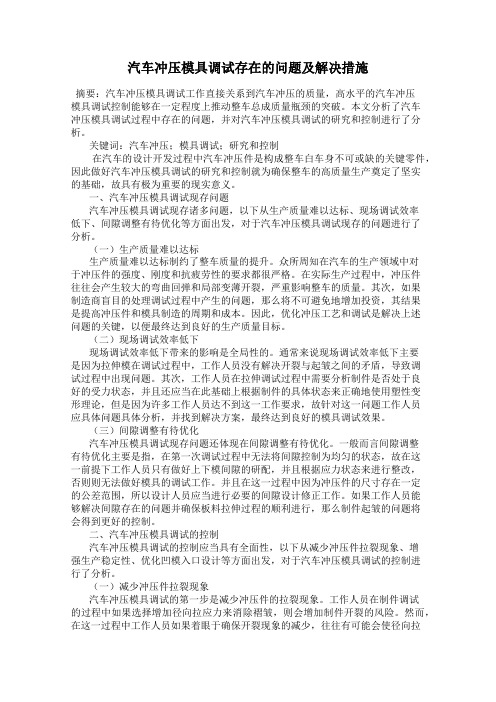
(一)门外板作为白车身的一部分,其表面质量要求更为严格,其属于浅拉延胀形模具。现以某车型后门外板为例进行具体阐述。
在门外板的生产节拍由7次提升到15次的过程中,油石检查冲压件表面出现多处瘪塘钣金波浪缺陷,如图1所示。超过封样件,单件奥迪特评审为B类缺陷,严重影响制件的质量及产能。提速后对其钣金缺陷产生的原因进行逐步分析:1)模具未改动;2)板料未更换厂家:3)设备的气垫压力已经在提速前设置好;4)新设备。
(二)增强生产稳定性
汽车冲压模具调试的关键在于增强生产的稳定性。工作人员在开始模具调试时,应当考虑到板料的规格尺寸往往会比实际需要的大不少,故针对这一情况,工作人员在增强生产稳定性的过程中应当在进行每一轮调试时都逐步的减小板料的尺寸,从而能够使其材料利用率最高。在这一过程中需要值得注意的是,因为在生产过程中仅仅只针对某一零件的规格尺寸进行钢卷的采购,所以会导致在调试后期因板料尺寸减小而造成卷料浪费,故为了降低采购成本及损失,需要做好模具的调试工作,增强生产的稳定性。
(二)现场调试效率低下
现场调试效率低下带来的影响是全局性的。通常来说现场调试效率低下主要是因为拉伸模在调试过程中,工作人员没有解决开裂与起皱之间的矛盾,导致调试过程中出现问题。其次,工作人员在拉伸调试过程中需要分析制件是否处于良好的受力状态,并且还应当在此基础上根据制件的具体状态来正确地使用塑性变形理论,但是因为许多工作人员达不到这一工作要求,故针对这一问题工作人员应具体问题具体分析,并找到解决方案,最终达到良好的模具调试效果。
二、汽车冲压模具调试的控制
汽车冲压模具调试的控制应当具有全面性,以下从减少冲压件拉裂现象、增强生产稳定性、优化凹模入口设计等方面出发,对于汽车冲压模具调试的控制进行了分析。
影响模具质量和进度的原因分析及解决办法

影响模具质量和进度的原因分析及解决办法国际金属加工网2012年01月16日一、影响模具质量的原因分析:1、影响模具质量的外部原因有:(1)产品的设计质量产品的设计应具有良好的冲压工艺性、铸造锻造工艺性等,否则,模具难以实现产品的形状和尺寸精度要求,只能用机加的方法来实现。
如FJL205C-22001动片,产品设计成尖棱尖角,造成冲压模具凹凸模崩块或开裂,模具寿命较低。
产品尺寸精度较高时,模具无法保证产品要求。
(2)产品的工艺质量冲压工艺不合理,会造成产品的形状和尺寸精度达不到要求,如整修余量过大,会造成产品断面质量差。
毛料展开尺寸计算不准确,会造成产品弯曲或拉深后尺寸精度达不到要求。
如外贸转包产品孔的精度较高,用模具整孔时,冲头易断,改用钻孔铰孔后,可以满足生产要求。
铸造工艺不合理,!产品无法浇铸成形。
铸件、锻件、橡胶件收缩率等工艺参数给得不准确,会造成模具报废或返修。
对子返修模具,产品工艺提出的故障不全或不准确,会造成模具多次返修和试模。
(3)模具老化冲压件厂目前仍有许多六、七十年代制造的模具在使用,许多模具零件磨损,寿命已到,但是由子没有新模具的制造,为满足生产需要,死马当活马医,造成模具频繁返修,多次试模。
(4)产品材料每批次产品材料的材质如硬度、厚度的微小变化,对模具的凹、凸模间隙,产品的弯曲回弹角有较大的影响;造成使用同一套模具时,上一批产品合格,下一批产品不合格;模具随着产品材料的变化而变化。
这就增加了模具的返修次数。
(5)模具材料及热处理模具关键件均为锻件,锻件质量的好坏直接影模具的寿命;锻件组织中碳化物分布是否均匀,锻件级别是否达标,造成模具在使用中易开裂、崩刃、掉块,影响试模合格率及使用寿命。
另外热处理质量也是直接影响模具质量的一个因素,淬火硬度过高,模具易开裂、掉块;过低,影响产品尺寸及模具寿命。
(6)试模的影响试模设备的精度,试模人员的技能、经验,试模问题是否暴露全面,都对试模次数有很大影响。
冲压生产中影响送料精度的因素
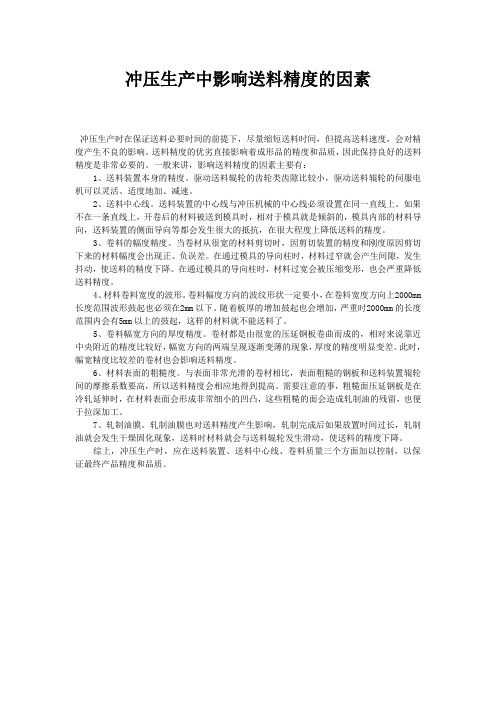
冲压生产中影响送料精度的因素冲压生产时在保证送料必要时间的前提下,尽量缩短送料时间,但提高送料速度,会对精度产生不良的影响。
送料精度的优劣直接影响着成形品的精度和品质,因此保持良好的送料精度是非常必要的。
一般来讲,影响送料精度的因素主要有:1、送料装置本身的精度。
驱动送料辊轮的齿轮类齿隙比较小,驱动送料辊轮的伺服电机可以灵活、适度地加、减速。
2、送料中心线。
送料装置的中心线与冲压机械的中心线必须设置在同一直线上。
如果不在一条直线上,开卷后的材料被送到模具时,相对于模具就是倾斜的,模具内部的材料导向,送料装置的侧面导向等都会发生很大的抵抗,在很大程度上降低送料的精度。
3、卷料的幅度精度。
当卷材从很宽的材料剪切时,因剪切装置的精度和刚度原因剪切下来的材料幅度会出现正、负误差。
在通过模具的导向柱时,材料过窄就会产生间隙,发生抖动,使送料的精度下降。
在通过模具的导向柱时,材料过宽会被压缩变形,也会严重降低送料精度。
4、材料卷料宽度的波形。
卷料幅度方向的波纹形状一定要小,在卷料宽度方向上2000mm 长度范围波形鼓起也必须在2mm以下。
随着板厚的增加鼓起也会增加,严重时2000mm的长度范围内会有5mm以上的鼓起,这样的材料就不能送料了。
5、卷料幅宽方向的厚度精度。
卷材都是由很宽的压延钢板卷曲而成的,相对来说靠近中央附近的精度比较好,幅宽方向的两端呈现逐渐变薄的现象,厚度的精度明显变差。
此时,幅宽精度比较差的卷材也会影响送料精度。
6、材料表面的粗糙度。
与表面非常光滑的卷材相比,表面粗糙的钢板和送料装置辊轮间的摩擦系数要高,所以送料精度会相应地得到提高。
需要注意的事,粗糙面压延钢板是在冷轧延伸时,在材料表面会形成非常细小的凹凸,这些粗糙的面会造成轧制油的残留,也便于拉深加工。
7、轧制油膜。
轧制油膜也对送料精度产生影响,轧制完成后如果放置时间过长,轧制油就会发生干燥固化现象,送料时材料就会与送料辊轮发生滑动,使送料的精度下降。
冲裁模调试时易出现的问题和调整方法

位置不正孔 图(四)内孔位置不正
尺寸过小 或有斜度
导料板
凹模位置 图(五)导料板尺寸过小或有斜度
P4/4
中心线 图(六)导料板中心线与凹模中心线错位或不平行
此处形状 为相应零 件的外形
工件
凹模 `` 实际加工位置(绿色) 图(七)凹模有倒锥度 理想加工位置(蓝色) 图(八)零件异形 尖角处容易堆积废料
工件在此处 下落受阻
实际加工位置(绿色)
理想加工位置(蓝色)
图(九)凹模落料孔没有对正
以上
二、 冲裁模调试的意义
模具按图纸技术要求加工与装配后,必须在符合实际生产条件的环境中进行试冲压生产通过试冲可以 发现模具设计与制造的缺陷并找出产生的原因,对模具进行适当的调整和修理后再进行试冲,直至模 具能正常工作。
三、 冲裁模调试的目的
① ② 鉴定模具的质量是否符合要求; 验证该模具生产的产品质量是否符合要求,确定该模具是否能交付生产使用。 帮助确定产品的成形条件和工艺过程; 模具通过试冲与调整,生产出合格产品后,可以在试冲过程中,掌握和了解模具使用性能,产品 成形条件、方法和规律,从而对产品批量生产时的工艺规程制定提供帮助。 帮助确定成形零件毛坯形状、尺寸及用料标准; 在冲模设计中,有些形状复杂或精度要求较高的冲压成形零件,很难在设计时,精确地计算出变 形前毛坯的尺寸和形状。为了要得到较精确的毛坯形状、尺寸及用料标准,只有通过反复试冲才 能确定。 帮助确定工艺和模具设计中的某些尺寸; 对于形状复杂或精度要求较高的冲压成形零件,在工艺和模具设计中,有个别难以用计算方法确 定的尺寸,如拉深的凸、凹模圆角半径等,必须通过试冲,才能准确确定。 通过调试发现问题、解决问题、积累经验,有助于进一步提高模具设计与制造水平;
冲压模具故障的几个原因

冲压模具故障的几个原因1. 在加入制造材料进行冲压时进行仔细检查,要使用合适的材料,检查相对应的热处埋工艺是否合理。
如果冲压模具的淬火温度过高,淬火方法和时间不合理,以及回火次数和温度、肘间选择不当,都会导致模具进入冲压生产后损坏。
落料孔尺寸或深度设计不够,容易使槽孔阻塞,造成落料板损坏。
弹簧力设计太小或等高套不等高,会使弹簧断裂、落料板倾斜.造成重叠冲打,损坏零件。
冲头固定不当或螺丝强度不够.会导致冲头掉落或折断。
2. 冲压模具使用时,零件位置、方向等安装错误或螺栓紧固不好。
工作高度调整过低、导柱润滑不足。
送料设备有故障,压力机异常等,都会造成冲压模具的损坏。
如果出现异物进入冲压模具、制件重叠、废料阻塞等情况未及时处理,继续加工生产,就很容易损坏模具的落料板、冲头、下模板和导柱。
3、模具常见故障的原因及常用对策3.1、冲压毛刺大仔细检查模具和制品,分析原因,并根据不同的原因采用相应的对策。
⑴刃口磨损或崩刃,可磨刃口,研磨量应以磨利为准。
当局部需要的研磨量较多时,可采用垫片局部垫高后再磨刃口。
当崩刃超过1mm时,可采用氩弧焊补焊后研磨修复刃口或氩弧焊补焊后线切割修复刃口,也可局部线切割后镶补。
对于小凸模或小镶件崩刃较多时,可垫高后刃磨或更新凸模或镶件。
⑵、模具冲裁间隙过大或过小,即重新研磨刃口后,效果不佳,很快又出现毛边等,须对冲切断面检查,确认后重新调整模具间隙,并重新配作定位销孔。
当导柱、导套磨损,配合间隙变大时,模具冲裁间隙也会改变,导致毛刺出现,可更换导柱、导套。
⑶、冲裁搭边过小或切边材料过少时,材料被拉入模具间隙内成为毛边,可加大冲裁搭边或加大切边余量解决。
3.2、凸模折断或弯曲导致凸模失效的原因很多,应仔细检查模具和制品,分析原因,并根据不同的原因采取相应的对策。
废料阻塞、卡料、模内有异物、废物上浮、冲半料、冲孔间隙过小或间隙不均匀、卸料板导向不良或选用材质、热处理不当、卸料橡胶挤压小凸模等因素均可导致凸模断裂或弯曲。
汽车冲压模具调试料生产管理

中, 冲压 模 具 开发 是 关键 所 在 。 在模 具 开发 过 程 中 , 需要 按 模 具 制 造进 度 及 时供 应 铜 板 用 于调 试 。 试 相 对 于 调 生 产 而 言 , 求 量 小利 用率 低 , 需 不利 于 车 间生 产 组 织 和成 本 控 制 , 管理 带来 诸 多不便 。文章 通 过 对 模 具调 试 给 料 的 生 产特 点 和 规 律 进行 分析 , 对性 地提 出解 决方 案 。 针 关 键 词 : 车 : 发 : 具 : 板 : 试 汽 研 模 钢 调
如 D 5D Z H 4 L D Z等 , C 1 + 、 30 A + 统计牌号总计十余 种之多 。 汽车厂在采购钢板时 , 根据《 汽车金属材料 消耗 定额》 中 试到外委生产 , 从物流规划到制件配送 , 都决定着模具调 的牌号 、 厚度 、 宽度进行订货 。 基于现有车型生产情况, 对 试用料的流向, 做好此项工作应从源头介入 。 不现牌号 、 厚度 、 宽度组合进行分类 , 钢板库通常存有百 21 模 具 调 试 用料 生产 特 点 . 余种钢卷 , 总量高达数万吨。 公司设有专们机构对钢板库 ①需求量小。 调试材料为两部分用途 : 一部分用 于模 进行管理 , 其上游是采购公司 , 下游是生产 车间。 其职责 具 调 试 , 另一 部 分用 于 装 车样 件 提 供 。 具 调试 料 片规 定 模 是接收采购来的钢卷进行存储 、 保管 , 然后根据生产计划 铸造模具 20张 , 5 钢板模 10张 , 中有 10张供试装车 5 其 0 将钢卷转运到生产线 , 并接收生产线退 回的钢卷 。 按每 日 用 。即使是这样小 的需求量 ,也要根据节点进度分批提 生产汽车 20 0 , 0 辆 每辆 车用 钢板 08 计算 , . t 5 钢板库每 供 。 具 回 厂后 , 模 还需 要 进 行 5 0台份 的小 批 量试 生 产 。 根 日进 出钢卷达 1 0 左右 。由于库存总量大种类多 , 0 7 t 进 据项 目节点 , 分手工提样 、 全序提样 和预验 收三个 阶段 , 出频繁等原 因, 钢板库管理工作相对繁重 。 1 钢 板 生 产 方式 介绍 . 2 连 同小批量共计 下料 四批。 ②种类繁多。每种零件所用钢板 的牌号厚度规格各
冲压模具常见异常及排除方法PPT课件

1.確實執行刀口保養辦法
2.模具要定量翻新維護其整體精度
3.消耗性備品定期更換,並做好模具履歷的登記工作以方便壽命管制
4.更換工件,要做前置處理,並確認相關品質狀況
精品课件文档,欢迎下载,下载后可以复制编辑。 更多精品文档,欢迎浏览。
5.成型模仁磨損嚴重(見圖-12)
6.成型模仁R角未倒角拋光(包括定位R角和成型R角)
7.沖子.模仁鬆動
8.LIFT在模仁內晃動(見圖-13)
9.LIFT浮料高度不良(以成型模板厚為20.000,T=0.200,“U”型H=0.43)(見圖-14)
10.LIFT浮料強度NG(一般採用紅色以上的加重彈簧)(見圖-15)
處理對策
1.根據刀口壽命管制,檢視刀口磨損程度,更換嚴重磨損之刀口.一般來說模仁設計直面段為3.00mm,磨去2.50mm時,要考慮更換,沖子磨去4~5mm時更換之(見圖-8)
2.研磨落料刀口
5.固定鬆動之模仁或入塊
4.調整浮料彈力及高度(LIFT浮料彈力不能太強,否則極易壓傷坯料,一般選用∅6,線徑為1.0的線簧,當然也不能太弱,否則高速時不及時浮料,造成坯料被模仁拉傷)
冲压模具常见异常及排除方法
二.“U”型成形過程中常見異常 現象
2.“U”形銅絲(內側.外側,底部銅絲)(見圖-5)
1.“U”形成形高低差
3.“U”形成形間隔性高低差(見圖-4)
4.“常見異常潛在原因及處理對策
“U”形成形高低差
潛在原因
<一>落料部分
1.料條扇形,高速時影響定位.
11.成型模仁太緊
1.調整預成型間隙
處理對策
2.更換OK之成型沖子(利用檢測設備對零件進行尺寸確認)
- 1、下载文档前请自行甄别文档内容的完整性,平台不提供额外的编辑、内容补充、找答案等附加服务。
- 2、"仅部分预览"的文档,不可在线预览部分如存在完整性等问题,可反馈申请退款(可完整预览的文档不适用该条件!)。
- 3、如文档侵犯您的权益,请联系客服反馈,我们会尽快为您处理(人工客服工作时间:9:00-18:30)。
冲压模具调试板料流入量影响因素分析
摘要:压力机是模具生产、调试和冲压中最基本的设备,压力机的精度直接
影响模具生产的质量和周期,也对冲压生产产生重要影响。
压力机精度包括压力
机的平行度、垂直度、滑块和工作台的垂直度、整机刚度、滑块和工作台杆的变
形(挠度)、吨位精度等,区分各精度参数对模具和冲压件生产的影响范围和影响
程度,并采取必要的改进措施,这样可以提高模具、冲压件质量,也可以缩短模
具调试周期。
本文对冲压模具调试板料流入量影响因素进行分析,以供参考。
关键词:板料流入量;模具调试;影响因素
引言
冲压模具是一种特殊的工艺设备,用于在冲压过程中将材料(金属或非金属)
加工成零件(或半成品)。
冲压模具的质量直接影响到冲压件的质量,冲压件与厨
电产品的间隙、断差和表面质量密切相关。
因此,确定冲压模具的质量,以及模
具在生产过程中出现问题后如何来提高模具质量显得十分的重要。
冲压模具的调
试是检查模具的质量和精度。
找出并纠正模具设计制造中存在的问题,制作合格
的冲压件。
1压力机精度分析
1.1垂直度
如果模具未设定,滑块的运动路径表示垂直于压力机工作台表面的方向变化量。
如果垂直度不好,则保证模具连接。
模具连接后,上下定位导柱和导套;导向板
有瘀伤,严重者可能发生导向板脱落等事故,垂直度要求一定的要求才能顺利进
入模具。
机械压力机的每个压力点都是一个独立的偏心连杆机构,工作时有一定
的相位(也称为同步),因此根据设计,垂直度可以尤其是在高速高频冲压生产中,会影响模具。
1.2整机刚度
当在压力机工作台和滑块底部的预定范围内将均匀分布的载荷施加到与条件
力相对应的静载荷上时,将条件力分为工作台和滑块指定位置的平均相对变形、
整机加载条件力时的综合变形、框架变形、减少每个连杆、曲轴变形和连接辅助
间隙压缩、保护缸内油压缩返回距离,不能调整后期使用,变形时滑块下平面和
工作台平面之间的距离变化是恒定的。
也就是说,加载4点数字时变化一致,对
模具调试的影响有限。
2冲压模具主要问题及调试策略
2.1废料切不断可能的原因及对策
1刀片口吃深度不足;对策:增加刀刃,深度(整体不足,闭合高度减少;部
分不足,焊接边补充);2切削边长度不足。
对策:补充焊接长切削刃;3修剪冲
孔间隙;对策:切削刃间隙修复;4切削刃塌陷;对策:焊接修复切削刃。
2.2卡废料可能的原因及对策
1 .冲模边缘逃逸材料(避免);对策:切割深度小于5mm时,开始拆除,象形
图加弹别针。
2 .空刀布局不合理,刀背刀。
对策:规范废刀摆放,避免刀盘等。
3 .废刀放置不合理,有负角钩。
对策:调整废刀位置和角度,避免负角度挂钩。
4 .模具废料打滑的空间不足。
对策:增加废物溢出空间,加大块度等,调整物料
的优先顺序和角度。
5 .一些废料旋转,废料包宽度不够。
对策:设计时扩大废料包。
6 .废料槽角度不够(模具内部大于25度,2级大于20度)。
外侧大于20度,二级大于15度。
对策:加大废料滑移角,使用纸板。
2.3建立加工模板和参数库
模具制造技术需要长期积累沉积物,在高级工程师的帮助下建立处理模板和
数据库,使新技术人员能够运用成功的经验,快速开发相对简单的程序。
在编程
规范中,必须明确机床类型、刀具选择、路径方向、加工裕量和其他切割参数,
以及加工过程。
3板料流入量影响因素分析
3.1成形压力
成形压力是指凹模与压边圈作用于板料的压力,冲压过程中在该压力的作用
下使得板料与模具之间产生正压力及接触应力,对板料产生流动阻力,从而控制
板料的流动。
冲压时,如果成形压力过大,则板料阻力过高,流动不顺畅,导致
板料流入量较少,最终零件冲压开裂;相反,成形压力过小往往会导致板料过多
地流入模具型腔,成形结束后轻则变形不足,重则导致零件起皱,严重的还会造
成模具型腔内叠料,造成合模后模具受挤压损坏。
为研究不同成形压力对板料流
入量的影响,本文采用控制变量法,在保证其他参数不变的情况下分别模拟了设
计压力增大或减小10%时板料的流入量变化情况,结果如图1所示,图中x为成
形压边力变化,y为流入增量。
由图1可知,随着成形压力的提高,板料的流入
量逐渐减小,且呈线性变化趋势,当压力减小约10%时,板料流入增量约
0.693mm,相比整体62.31mm的流入量来说,成形压力对其影响较小,仅占原始
设计工艺总流入量的1.1%。
图1成形压力对板料流入增量的影响
3.2拉延筋凹槽圆角半径对流入量的影响
原始设计拉延筋凹槽圆角半径为5mm,本文对拉延筋圆角半径分别增加及减
少20%,即拉延筋凹槽圆角半径为4~6mm,模拟了零件冲压后的流入量变化情况,随着拉延筋凹槽圆角半径的增加,板料的流入量逐渐减小,与成形压力对流入增
量的影响相近,拉延筋凹槽圆角半径对流入增量的影响亦呈线性趋势变化。
从影响强度来看,明显拉延筋凹槽圆角半径的影响更大。
当拉延筋凹槽圆角半径增加10%时,板料流入量变化约3mm,而当成形压力改变10%时,板料流入量变化约0.8mm,影响程度仅为拉延筋凹槽圆角半径的1/4左右。
3.3结果
(1)成形压力、摩擦因数及拉延筋参数等对冲压板料流入量有着不同程度的影响,其中拉延筋凹槽圆角半径影响最大,而成形压力则影响最小,拉延筋凹槽圆角半径的影响为成形压力的4倍,冲压模具调试中可根据流入量改变需求大小来进行相应的调整。
(2)各影响因素中,10%的改变量下,摩擦因数与拉延筋高度对流入增量的影响呈二次函数变化,而成形压力与拉延筋凹槽圆角半径则会导致流入增量呈线性变化。
4结束语
随着厨电市场竞争的加剧,大型厨电制造厂对冲压模具提出了质量要求。
目前,在以前的设计中,除了提高模具工艺和设计的合理性外,冲压模具的调试过程在很大程度上决定了模具的质量。
因此,如何提高调试效率和质量,减少冲压模具和零部件的问题,是本文的主旨,也是冲压模具调试未来的发展方向。
参考文献
[1]张永泰.基于汽车冲压模具设计制造与维修分析[J].产业创新研
究,2019(10):276-277.
[2]蒋磊,龚剑,王龙,王大鹏,石田浩.基于产品质量特性的冲压模具工序集成技术开发与应用[J].汽车工艺与材料,2019(10):6-15.
[3]乔晓勇.车身覆盖件模具磨损机理及寿命预测研究[D].湖南大学,2017.。