过程检验记录
合集下载
过程检验记录

溴化环氧树脂
KBE-2025K
闭环反应的操作
操作规范
李召华
合格
过程检验记录
QR8.2.3-03
生产日期
操作工
产品名称
型号规格
检验项目
检验结果
不合格品评审处置
检验员
备注
2008-03-02
陈亮
溴化环氧树脂中间体
KBE-3020
环氧值
0.2921
李召华
合格
2008-03-06
邓亦龙
溴化环氧树脂
KBE-2025K
检验员
备注
2008-03-18
高健
溴化环氧树脂
KBE-2025K
敲料
料块大小合适
李召华
合格
2008-03-23
陈亮
中间体
KBE-2025K
环氧值
0.2875
李召华
合格
2008-03-26
赵斯权
溴化环氧树脂
KBE-2025K
醚化反应的操作
符合工艺流程的操作要求
李召华
合格
2008-03-29
高健
溴化环氧树脂
杜祥吉
溴化环氧树脂中间体
KBE-2025K
转料过程
有中间体洒落地面
加强培训教育增强其素质及责任心。
李召华
不合格
2008-02-15
曹建华
溴化环氧树脂
KBE-2025K
醚化反应的操作
操作规范
李召华
合格
过程检验记录
QR8.2.3-03
生产日期
操作工
产品名称
型号规格
检验项目
检验结果
不合格品评审处置
KBE-2025K
闭环反应的操作
操作规范
李召华
合格
过程检验记录
QR8.2.3-03
生产日期
操作工
产品名称
型号规格
检验项目
检验结果
不合格品评审处置
检验员
备注
2008-03-02
陈亮
溴化环氧树脂中间体
KBE-3020
环氧值
0.2921
李召华
合格
2008-03-06
邓亦龙
溴化环氧树脂
KBE-2025K
检验员
备注
2008-03-18
高健
溴化环氧树脂
KBE-2025K
敲料
料块大小合适
李召华
合格
2008-03-23
陈亮
中间体
KBE-2025K
环氧值
0.2875
李召华
合格
2008-03-26
赵斯权
溴化环氧树脂
KBE-2025K
醚化反应的操作
符合工艺流程的操作要求
李召华
合格
2008-03-29
高健
溴化环氧树脂
杜祥吉
溴化环氧树脂中间体
KBE-2025K
转料过程
有中间体洒落地面
加强培训教育增强其素质及责任心。
李召华
不合格
2008-02-15
曹建华
溴化环氧树脂
KBE-2025K
醚化反应的操作
操作规范
李召华
合格
过程检验记录
QR8.2.3-03
生产日期
操作工
产品名称
型号规格
检验项目
检验结果
不合格品评审处置
过程审核检查记录---来料检验

-对内/外部报怨,向相关责任部门下发《质量整改推进计划》,落实责任单位、责任人;
-纠正效果的证明(客户的质量信息反馈减少)。
√
√
√
√
√
√
八、以往顾客投诉情况、纠正措施实施情况、以往质量问题
1.是否按时落实要求的纠正措施并检查其有效性? -审核结果整改结果; -内/外部抱怨; -纠正效果的证明.
1、按时落实要求的纠正措施并检查其有
效性;
-对顾客投诉的情况,填写《质量信息反馈处置单》追溯其根源,制定《纠正或预防措施报告》、运用《顾客报怨及组织内部报怨与制造过程/产品矩形图》,形成闭环并审核结果整改结果;
工序名称
来料检验
工序编号
01
审核要点
审核记录
判定
一、过程负责人
是否指定过程负责人
已指定过程负责人
√
二、完整的输入(待加工零件、作业指导书、零件周转卡)
1.生产文件与检验文件中是否标出所有的重要技术要求,包括产品安全特性,并坚持执行?
2.是否持有PFMEA、控制计划、过程作业指导书/检验指导书,
3.特殊特性标识;
-精度/状况;
-检定/能力调查。由有资质的单位进行检定
2、生产设备/工装模具能保证满足产品特定的质量要求;
-验证结果,适当时包括Cmk;
-防错功能(报警,自动断开); -维修状态。
3、生产工位、检验工位符合要求; -照明/清洁;
-人机工程;
-零件搬运/安全生产。
4、对产品调整/更换有必备的辅助器具;
1、产品数量/生产批次的大小是按需求而定,是有目的地运往下道工序;
2、产品是按要求贮存、运输方式/包装方法按产品的特性而定。
√
√
-纠正效果的证明(客户的质量信息反馈减少)。
√
√
√
√
√
√
八、以往顾客投诉情况、纠正措施实施情况、以往质量问题
1.是否按时落实要求的纠正措施并检查其有效性? -审核结果整改结果; -内/外部抱怨; -纠正效果的证明.
1、按时落实要求的纠正措施并检查其有
效性;
-对顾客投诉的情况,填写《质量信息反馈处置单》追溯其根源,制定《纠正或预防措施报告》、运用《顾客报怨及组织内部报怨与制造过程/产品矩形图》,形成闭环并审核结果整改结果;
工序名称
来料检验
工序编号
01
审核要点
审核记录
判定
一、过程负责人
是否指定过程负责人
已指定过程负责人
√
二、完整的输入(待加工零件、作业指导书、零件周转卡)
1.生产文件与检验文件中是否标出所有的重要技术要求,包括产品安全特性,并坚持执行?
2.是否持有PFMEA、控制计划、过程作业指导书/检验指导书,
3.特殊特性标识;
-精度/状况;
-检定/能力调查。由有资质的单位进行检定
2、生产设备/工装模具能保证满足产品特定的质量要求;
-验证结果,适当时包括Cmk;
-防错功能(报警,自动断开); -维修状态。
3、生产工位、检验工位符合要求; -照明/清洁;
-人机工程;
-零件搬运/安全生产。
4、对产品调整/更换有必备的辅助器具;
1、产品数量/生产批次的大小是按需求而定,是有目的地运往下道工序;
2、产品是按要求贮存、运输方式/包装方法按产品的特性而定。
√
√
过程检验记录--钢质
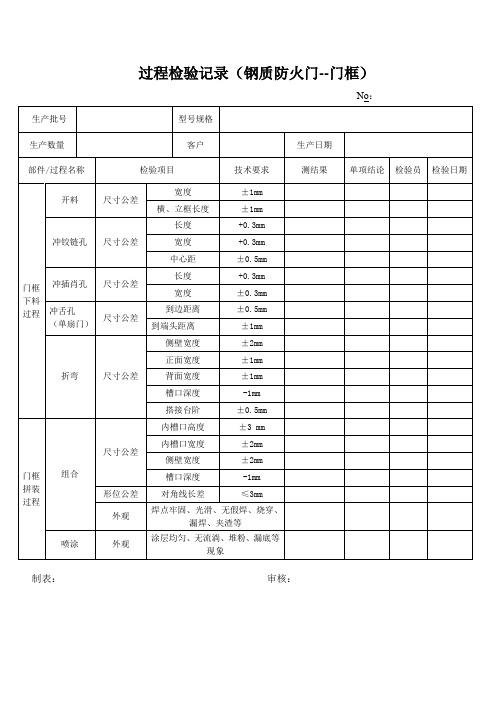
冲舌孔
(单扇门)
尺寸公差
到边距离
±0.5mm
到端头距离
±1mm
折弯
尺寸公差
侧壁宽度
±2mm
正面宽度
±1mm
背面宽度
±1mm
槽口深度
-1mm
搭接台阶
±0.5mm
门框拼装过程
组合
尺寸公差
内槽口高度
±3 mm
内槽口宽度
±2mm
侧壁宽度
±2mm
槽口深度
-1mm
形位公差
对角线长差
≤3mm
外观
焊点牢固、光滑、无假焊、烧穿、漏焊、夹渣等
尺寸公差
执手中心边距(底/面)
±0.5mm
执手中心高度
±1mm
冲铰链孔
尺寸公差
长度
+0.3mm
深度
±0.5mm
折弯
尺寸公差
左扇宽度(底/面)
±1mm
右扇宽度(底/面)
±1mm
盖缝板
盖缝板宽度
±1mm
门扇
拼装过程
装填门芯
冷压
芯材填充后门扇重量 ㎏
胶粘剂涂刷应均匀,防火门芯板之间裁口对接,其它缝隙有防火胶填满
喷涂
外观
涂层均匀、无流淌、堆粉、漏底等现象
制表:审核:
过程检验记录(钢质防火门--门扇)
No:
生产批号
型号规格
生产数量
客户
投产日期
部件/过程名称
检验项目
技术要求
检测结果
单项结论
检验员
检验日期
门扇
下料过程
开料
尺寸公差
长度(左/右)
±1mm
宽度(左/右)
(单扇门)
尺寸公差
到边距离
±0.5mm
到端头距离
±1mm
折弯
尺寸公差
侧壁宽度
±2mm
正面宽度
±1mm
背面宽度
±1mm
槽口深度
-1mm
搭接台阶
±0.5mm
门框拼装过程
组合
尺寸公差
内槽口高度
±3 mm
内槽口宽度
±2mm
侧壁宽度
±2mm
槽口深度
-1mm
形位公差
对角线长差
≤3mm
外观
焊点牢固、光滑、无假焊、烧穿、漏焊、夹渣等
尺寸公差
执手中心边距(底/面)
±0.5mm
执手中心高度
±1mm
冲铰链孔
尺寸公差
长度
+0.3mm
深度
±0.5mm
折弯
尺寸公差
左扇宽度(底/面)
±1mm
右扇宽度(底/面)
±1mm
盖缝板
盖缝板宽度
±1mm
门扇
拼装过程
装填门芯
冷压
芯材填充后门扇重量 ㎏
胶粘剂涂刷应均匀,防火门芯板之间裁口对接,其它缝隙有防火胶填满
喷涂
外观
涂层均匀、无流淌、堆粉、漏底等现象
制表:审核:
过程检验记录(钢质防火门--门扇)
No:
生产批号
型号规格
生产数量
客户
投产日期
部件/过程名称
检验项目
技术要求
检测结果
单项结论
检验员
检验日期
门扇
下料过程
开料
尺寸公差
长度(左/右)
±1mm
宽度(左/右)
过程检验记录

过程检验记录
产品名称 检验项目
技术要求
规格/型号
检验结果
外观
表面不应有影响使用上的凹点、伤痕、毛刺、 □符合 变形、裂纹、杂质、缺料、油污、气孔等缺陷 □不符合
工艺尺寸 技术要求
按作业工艺、图纸和客户要求检验
综合判定 □符合 □不符合
检验员:
日期:
产品名称 检验项目
过程检验记录
规格/型号
技术要求
检验结果
外观
表面不应有影响使用上的凹点、伤痕、毛刺、 □符合 变形、裂纹、杂质、缺料、油污、气孔等缺陷 □不符合
工艺尺寸 技术要求
按作业工艺、图纸和客户要求检验
综合判定: □符合
□不符合
□符合 □不符合 □符合 □不符合
检验员:
日期:
产品名称 检验项目
过程检验记录
规格/型号
技术要求
检验结果
外观
表面不应有影响使用上的凹点、伤痕、毛刺、 □符合 变形、裂纹、杂质、缺料、油污、气孔等缺陷 □不符合
工艺尺寸 技术要求
按作业工艺、图纸和客户要求检验
综合判定: □符合
□不符合
□符合 □不符合 □符合 □不符合
检验员:
日期:
数量 不良记录
数量 不良记录
数量 不良记录
产品名称 检验项目
技术要求
规格/型号
检验结果
外观
表面不应有影响使用上的凹点、伤痕、毛刺、 □符合 变形、裂纹、杂质、缺料、油污、气孔等缺陷 □不符合
工艺尺寸 技术要求
按作业工艺、图纸和客户要求检验
综合判定 □符合 □不符合
检验员:
日期:
产品名称 检验项目
过程检验记录
规格/型号
技术要求
检验结果
外观
表面不应有影响使用上的凹点、伤痕、毛刺、 □符合 变形、裂纹、杂质、缺料、油污、气孔等缺陷 □不符合
工艺尺寸 技术要求
按作业工艺、图纸和客户要求检验
综合判定: □符合
□不符合
□符合 □不符合 □符合 □不符合
检验员:
日期:
产品名称 检验项目
过程检验记录
规格/型号
技术要求
检验结果
外观
表面不应有影响使用上的凹点、伤痕、毛刺、 □符合 变形、裂纹、杂质、缺料、油污、气孔等缺陷 □不符合
工艺尺寸 技术要求
按作业工艺、图纸和客户要求检验
综合判定: □符合
□不符合
□符合 □不符合 □符合 □不符合
检验员:
日期:
数量 不良记录
数量 不良记录
数量 不良记录
过程检验记录首过程末件1

常州市青洋塑料制品有限公司
过程检验记录
记录人:QR824-05
日期/
时间
工件名称
检验数
合格数
不合格数
不合格原因/处理结果
合格率
(%)
验证时间及人员
注塑
/
修边
/
注塑
/
修边
/
注塑
/
修边
/
注塑
/
修边
/
注塑
/
修边
/
注塑
/
修边
/
注塑
/
修边
/
注塑
/
修边
/
注塑
/
修边
/
注塑
/修边/Fra bibliotek注塑/
修边
/
注塑
/
修边
/
丹阳峰日车辆配件有限公司
过程检验记录单QR/QB21-04
检验员:日期:
产品名称
设备
型号
生产车间
装配
序号
检验项目
技术要求
检验
类型
实测值
判定结果
样本1
样本2
样本3
样本4
样本5
Y
N
首末件比对
1
机构灵活性
操作轻便、不卡滞,无异响
首件
□Y
□N
过程
末件
2
外观
产品表面平整、光滑、无损伤
首件
□Y
□N
过程
末件
3
外观
无错漏、漏装现象
首件
□Y
□N
过程
末件
4
涂层
涂层表面平整、色泽一致、无起泡等
首件
□Y
过程检验记录
记录人:QR824-05
日期/
时间
工件名称
检验数
合格数
不合格数
不合格原因/处理结果
合格率
(%)
验证时间及人员
注塑
/
修边
/
注塑
/
修边
/
注塑
/
修边
/
注塑
/
修边
/
注塑
/
修边
/
注塑
/
修边
/
注塑
/
修边
/
注塑
/
修边
/
注塑
/
修边
/
注塑
/修边/Fra bibliotek注塑/
修边
/
注塑
/
修边
/
丹阳峰日车辆配件有限公司
过程检验记录单QR/QB21-04
检验员:日期:
产品名称
设备
型号
生产车间
装配
序号
检验项目
技术要求
检验
类型
实测值
判定结果
样本1
样本2
样本3
样本4
样本5
Y
N
首末件比对
1
机构灵活性
操作轻便、不卡滞,无异响
首件
□Y
□N
过程
末件
2
外观
产品表面平整、光滑、无损伤
首件
□Y
□N
过程
末件
3
外观
无错漏、漏装现象
首件
□Y
□N
过程
末件
4
涂层
涂层表面平整、色泽一致、无起泡等
首件
□Y
装配过程检验记录表

1.配线正确,布线排列整齐、走向合,导线标识清渐。
2.因操作不当对设各可能造成损害时,电气控系统应设有联镇或保护功能。
3.电器控制箱汇流排接地处应有明显的接地端子与接地标志。
4
人机界面
1.控制系统采用PLC控制,能调整各控制参数,配备独立电器、气路控制箱
2.人机界面上所显示或设置的功能及操作步骤均应准确、可靠。
5,螺钉、铆钉、那子端口不得有扭伤、锤伤等缺陷
6,焊接机上各荪牌标志应清晰耐久,其固定位置应正确、牢固、美观。
2
气动系统
1.气压应稳定,在额定压力工况情况下,管路系统不应有阻滞,所有气路及连接无漏气。
2.管路安装整齐美观,不应与其他零部件发生摩擦或撞,管路弯曲处应该圆滑,尽可能避免扭曲连接。
3
电气系统
5
安全防护
1焊接机应配备安全光、故障报警装置、急停保护开关、安全门等安全设施和措施,并能正常工作,确保操作者的安全。
2.整体应有安全防护装置,应能保护操作者不受物件抛出的伤害。
3.急停功能在完成紧急停止动作后,不得自动恢复功能。
4.应在电动机的明显部位标出旋转方向的指示前头:可能自动松动的零件应有可靠的防松装置。
5.零部件的连接应可靠,不得松动。
6.线路、管路应排列整齐,固定牢靠。
7
电气安全性能
1绝缘电阻:动力电路与保护接地电路之间的绝缘电阻应不少于20MΩ,控制电陆与保护接地电路之间的绝缘电阻应不小于2MΩ。
2.接地电阻:系统应有可靠的接地装置,应在明显位置装有与设备电路额定电流相适应的接地螺钉,为保证接触良好,禁止在螺钉上和导电接触面外喷涂油漆,并在附件上标注明显的接地符号。接地电阻阻值不得大于0.1MΩ。
日期
3.带电部件之间及与.外壳河应能承受正弦交流电压1760V50Hz的抗电强度试验,历时lmin,绝缘部分应无击穿、无表面闪、漏泄电流明显增大或电压突然下降等现象。
2.因操作不当对设各可能造成损害时,电气控系统应设有联镇或保护功能。
3.电器控制箱汇流排接地处应有明显的接地端子与接地标志。
4
人机界面
1.控制系统采用PLC控制,能调整各控制参数,配备独立电器、气路控制箱
2.人机界面上所显示或设置的功能及操作步骤均应准确、可靠。
5,螺钉、铆钉、那子端口不得有扭伤、锤伤等缺陷
6,焊接机上各荪牌标志应清晰耐久,其固定位置应正确、牢固、美观。
2
气动系统
1.气压应稳定,在额定压力工况情况下,管路系统不应有阻滞,所有气路及连接无漏气。
2.管路安装整齐美观,不应与其他零部件发生摩擦或撞,管路弯曲处应该圆滑,尽可能避免扭曲连接。
3
电气系统
5
安全防护
1焊接机应配备安全光、故障报警装置、急停保护开关、安全门等安全设施和措施,并能正常工作,确保操作者的安全。
2.整体应有安全防护装置,应能保护操作者不受物件抛出的伤害。
3.急停功能在完成紧急停止动作后,不得自动恢复功能。
4.应在电动机的明显部位标出旋转方向的指示前头:可能自动松动的零件应有可靠的防松装置。
5.零部件的连接应可靠,不得松动。
6.线路、管路应排列整齐,固定牢靠。
7
电气安全性能
1绝缘电阻:动力电路与保护接地电路之间的绝缘电阻应不少于20MΩ,控制电陆与保护接地电路之间的绝缘电阻应不小于2MΩ。
2.接地电阻:系统应有可靠的接地装置,应在明显位置装有与设备电路额定电流相适应的接地螺钉,为保证接触良好,禁止在螺钉上和导电接触面外喷涂油漆,并在附件上标注明显的接地符号。接地电阻阻值不得大于0.1MΩ。
日期
3.带电部件之间及与.外壳河应能承受正弦交流电压1760V50Hz的抗电强度试验,历时lmin,绝缘部分应无击穿、无表面闪、漏泄电流明显增大或电压突然下降等现象。
喷塑检验过程验证记录

7 8
结论
确认:
日备有限公司 前处理及喷塑过程检验记录表
产品名称 序号 1 2 3 4 5 6 规格型号 检验要求 装框前检查零部件无变形,装框时个零部件之间要有大于或等于2mm的间 隙,不得相互挤压撞击,清点数量,做好记录。装框完成后整体重量不得 大于起吊允许重量。 碱性脱脂浸泡时间为10-15分钟,起槽时工件表面形成不间断水膜即为合格 。游离碱度25-45点即为合格,此参数每隔2小时检测一次。 除锈浸泡时间为8-10分钟,视工件生锈情况而定。起槽时检查工件表面有 无未除掉的锈迹和氧化层,无则合格。槽液检测参数为总酸度,总酸度 350-450点即为合格,此参数每隔2小时检测一次。 中和处理浸泡时间时间为5-8分钟。 表调处理浸泡时间为30秒-1分钟。检测参数为PH=8-9。 磷化处理浸泡时间为8-10分钟,工件表面形成瓦灰色磷化膜。检测参数为 PH=3.0-3.5,总酸度为25-40点,游离酸度为1.1-1.9点,总酸度/游离酸度 比一般为20/1,促进剂为1.5-4.5点,磷化膜厚度要求在1.5-4.5微米之 间,以上相关参数在各自范围内即为合格,此槽参数每隔2小时检测一次。 各清洗槽清洗时间为1-2分钟,要求为活水清洗。 喷粉各项参数符合要求;塑粉颜色符合要求;烘烤温度为185度,时间为15 分钟;目测表面有无喷塑质量缺陷,如露底、电击、吐粉、颗粒等明显质 量问题,用膜厚仪检测塑层厚度,塑层厚度在50-100微米之间即为合格。 合格( ),接收。 不合格( ),退回返工处理。 数量 检查日期 实测结果 检验员 判定 备注
过程检验记录表
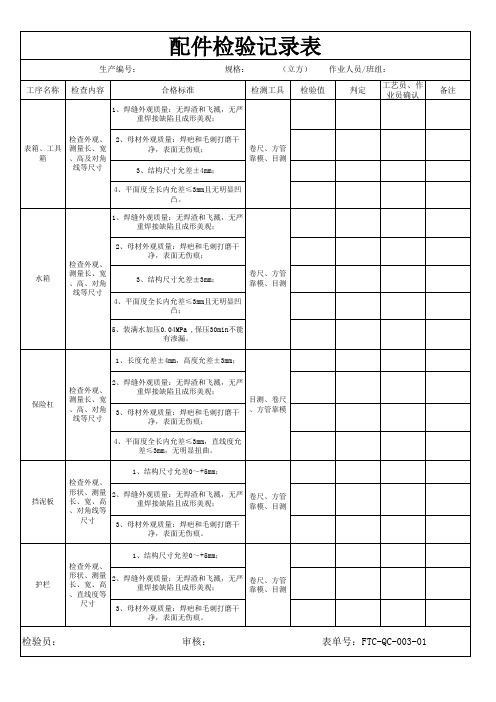
1、纵向直线度≤2mm/m,全长内≤ 10mm;
2、翼板平面度≤2mm/m,全长≤5mm;
3、翼板与腹板的垂直度≤1.5mm。
方管靠模、 卷尺、角尺
、目测
检验员:
审核:
表单号:FTC-QC-003-01
Байду номын сангаас
5、装满水加压0.04MPa ,保压30min不能 有渗漏。
备注
1、长度允差±4mm,高度允差±3mm;
保险杠
2、焊缝外观质量:无焊渣和飞溅,无严
检查外观、
重焊接缺陷且成形美观;
测量长、宽
目测、卷尺
、高、对角 3、母材外观质量:焊疤和毛刺打磨干 、方管靠模
线等尺寸
净,表面无伤痕;
4、平面度全长内允差≤3mm,直线度允 差≤3mm,无明显扭曲。
挡泥板
1、结构尺寸允差0~+5mm;
检查外观、
形状、测量 长、宽、高 、对角线等
2、焊缝外观质量:无焊渣和飞溅,无严 重焊接缺陷且成形美观;
卷尺、方管 靠模、目测
尺寸
3、母材外观质量:焊疤和毛刺打磨干
净,表面无伤痕。
护栏
1、结构尺寸允差0~+5mm;
检查外观、
形状、测量 长、宽、高 、直线度等
2、焊缝外观质量:无焊渣和飞溅,无严 重焊接缺陷且成形美观;
卷尺、方管 靠模、目测
4、平面度全长内允差≤3mm且无明显凹 凸。
1、焊缝外观质量:无焊渣和飞溅,无严 重焊接缺陷且成形美观;
水箱
检查外观、 测量长、宽 、高、对角
线等尺寸
2、母材外观质量:焊疤和毛刺打磨干 净,表面无伤痕;
3、结构尺寸允差±3mm;
4、平面度全长内允差≤3mm且无明显凹 凸;