电镀生产线自动控制系统的设计与实现_
电镀生产线自动控制系统

电镀生产线自动控制系统1 简介电镀生产线对行车的自动控制是电镀生产线自动化控制的关键,而电镀生产线按照其工艺要求和规模一般由两台以上的行车各自进行运动控制,每台行车都依据用户编好的程序进行自动控制;对于行车的自动控制,早期是采用继电器逻辑电路和顺序控制器,发展至今其控制方式以发生显著改变,主要已采用PLC 作为自动控制的核心部分,通过一系列的外接设备的输入信号以及输出信号对外接设备进行的相对应的编程控制,从而使整个控制系统更加的安全、可靠、灵活、其自动化程度高。
2 电镀生产线控制系统的总体方案设计2.1 控制方案选择可编程控制继电器接触器控制的优点:可靠性高,性能强大的功能;一个小型PLC有数百个可编程元素的用户,具有很强的逻辑编程功能,可实现各种复杂的控制功能。
与具有相同控制功能的继电器-接触器控制系统相比较,其具有相当大的优点,同时PLC通过上位机与通信网路的连接可实现集中管理,分散控制以及远程操作。
可编程控制器的安装方便,一般连接外部接线端子。
PLC的负载能力很强,能直接驱动电磁阀和普通交流接触器。
可靠性高,抗干扰能力强;中间继电器,时间继电器被广泛的使用在传统的继电器控制系统。
继电器由于接触不良,容易出现故障,而PLC的使用可以大大的减少中间继电器和时间继电器的使用,因此整个PLC控制系统中可以减少中间继电器控制系统的1 / 10——1/100接线,因此大大降低接触故障。
PLC同时自身也采取了一系列硬件和软件抗干扰措施,具有很强的抗干扰能力,平均故障间隔时间可达几万小时,在应用于工业生产总具有很强的抗干扰性,PLC已被用户公认为最可靠的工业控制设备和系统设计方案;PLC控制系统中,取代了大量的时间继电器,计数器装置,仅通过它自身的软件功能来代替,从而使设计,控制柜安装,布线工作量大大减少。
PLC梯形图程序通常采用顺序控制设计法。
这种编程方法比较有规律,易于掌握。
梯形图的复杂控制系统的设计,所需的时间要大大的少于一个时间继电器电路的设计。
电镀处理中的电镀自动化生产线设计与建设
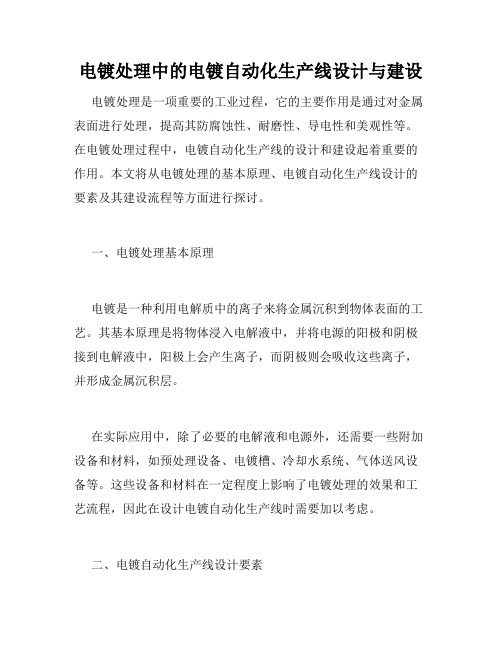
电镀处理中的电镀自动化生产线设计与建设电镀处理是一项重要的工业过程,它的主要作用是通过对金属表面进行处理,提高其防腐蚀性、耐磨性、导电性和美观性等。
在电镀处理过程中,电镀自动化生产线的设计和建设起着重要的作用。
本文将从电镀处理的基本原理、电镀自动化生产线设计的要素及其建设流程等方面进行探讨。
一、电镀处理基本原理电镀是一种利用电解质中的离子来将金属沉积到物体表面的工艺。
其基本原理是将物体浸入电解液中,并将电源的阳极和阴极接到电解液中,阳极上会产生离子,而阴极则会吸收这些离子,并形成金属沉积层。
在实际应用中,除了必要的电解液和电源外,还需要一些附加设备和材料,如预处理设备、电镀槽、冷却水系统、气体送风设备等。
这些设备和材料在一定程度上影响了电镀处理的效果和工艺流程,因此在设计电镀自动化生产线时需要加以考虑。
二、电镀自动化生产线设计要素1、生产线整体布局电镀自动化生产线的整体布局直接影响了电镀处理的效率和生产成本。
在设计布局时需要注意以下几点:(1)生产线应该尽量紧凑,方便物品的转移。
(2)应尽可能减少对人工操作的依赖,增强生产的自动化程度。
(3)合理设置物品存放位置和转移设备,减少中间加工环节和时间成本。
(4)布局应符合流程要求,确保工作流畅和高效。
2、设备选型在电镀自动化生产线的设计过程中,设备选型是重中之重。
不同厂家的设备在使用上各有特点,通过对比各种设备的性能和使用经验,选取最合适的设备可以提高生产效率和降低成本。
(1)硬件设备:包括电解槽、冷却水系统、气体送风设备等。
(2)软件设备:包括自动化控制系统、监控设备、数据处理系统等。
(3)随机设备:包括在线检测仪器、备件等。
3、安全环保电镀处理过程中会产生一些有害物质,若不妥善处理,可能会对环境和人体健康造成损害。
因此,在设计电镀自动化生产线时需要加强安全和环保控制,在生产过程中减少有害气体和废水的产生,并采取适当的处理措施。
同时还需要设置应急救援设备和紧急处理预案,以排除人员伤亡和环境污染等可能性。
基于PLC的电镀生产线控制系统的设计 毕业设计

基于PLC的电镀生产线控制系统的设计毕业设计目录摘要: (1)关键词: (1)Abstract (1)Key words (2)引言 (2)1 电镀生产线控制系统概述 (3)1.1选题背景及意义 (3)1.2课题的国内外研究现状 (3)1.3控制系统的设计要求 (3)2 可编程序控制器(PLC)简介 (4)2.1 PLC的产生和定义 (4)2.2 PLC的分类 (5)2.2.1 按I/O点数容量分类 (5)2.2.2 按结构形式分类 (5)2.3 PLC的系统组成 (5)2.4 PLC的工作方式 (7)2.5 PLC应用领域 (9)3 系统的硬件设计 (9)3.1 电机的选择 (9)3.2 PLC机型的选择 (10)3.3 I/O分配表及其端子接线图 (10)4 系统的软件设计 (12)4.1 软件的组成及作用 (12)4.1.1 PLC内部资源 (12)4.1.2 STEP7软件使用简介 (12)4.1.3 PLC编程语言 (13)4.1.4 电镀生产线的工作流程 (14)4.2 PLC梯形图设计 (15)5 实时监控系统的设计 (16)5.1组态软件 (16)5.2 组态王软件的设计 (17)5.3 软硬件调试 (17)总结 (20)参考文献 (21)附录梯形图程序 (22)致谢 (33)基于PLC的电镀生产线控制系统设计机械电子工程专业学生徐广超指导教师王秀摘要:电镀行业是我国重要的加工行业,随着科学技术的快速发展,电镀生产线越来越趋向自动化、智能化。
该课题的研究是用西门子PLC S7-200辅以变频器对电镀自动生产线进行自动控制,依次自动完成酸洗、电镀和清洗的过程。
重点分析了系统的硬件设计、软件设计,给出了系统硬件接线图、PLC控制I/O端口分配表以及整体程序流程图,并辅以组态王进行监控等。
该基于PLC的电镀生产线控制系统具有结构简单、编程方便、操作灵活、使用安全、工作稳定、性能可靠和靠干扰能力强等特点,实现了电镀生产过程的自动化,提高了生产效率,降低了疲劳强度,能够更好的融入到现在的工业控制领域。
电镀生产线自动控制系统的设计与实现
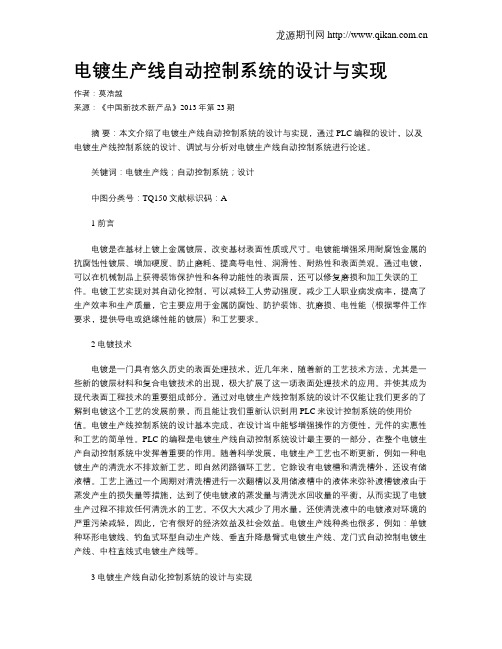
电镀生产线自动控制系统的设计与实现作者:莫浩越来源:《中国新技术新产品》2013年第23期摘要:本文介绍了电镀生产线自动控制系统的设计与实现,通过PLC编程的设计,以及电镀生产线控制系统的设计、调试与分析对电镀生产线自动控制系统进行论述。
关键词:电镀生产线;自动控制系统;设计中图分类号:TQ150 文献标识码:A1 前言电镀是在基材上镀上金属镀层,改变基材表面性质或尺寸。
电镀能增强采用耐腐蚀金属的抗腐蚀性镀层、增加硬度、防止磨耗、提高导电性、润滑性、耐热性和表面美观。
通过电镀,可以在机械制品上获得装饰保护性和各种功能性的表面层,还可以修复磨损和加工失误的工件。
电镀工艺实现对其自动化控制,可以减轻工人劳动强度,减少工人职业病发病率,提高了生产效率和生产质量,它主要应用于金属防腐蚀、防护装饰、抗磨损、电性能(根据零件工作要求,提供导电或绝缘性能的镀层)和工艺要求。
2 电镀技术电镀是一门具有悠久历史的表面处理技术,近几年来,随着新的工艺技术方法,尤其是一些新的镀层材料和复合电镀技术的出现,极大扩展了这一项表面处理技术的应用。
并使其成为现代表面工程技术的重要组成部分。
通过对电镀生产线控制系统的设计不仅能让我们更多的了解到电镀这个工艺的发展前景,而且能让我们重新认识到用PLC来设计控制系统的使用价值。
电镀生产线控制系统的设计基本完成,在设计当中能够增强操作的方便性,元件的实惠性和工艺的简单性。
PLC的编程是电镀生产线自动控制系统设计最主要的一部分,在整个电镀生产自动控制系统中发挥着重要的作用。
随着科学发展,电镀生产工艺也不断更新,例如一种电镀生产的清洗水不排放新工艺,即自然闭路循环工艺。
它除设有电镀槽和清洗槽外,还设有储液槽。
工艺上通过一个周期对清洗槽进行一次翻槽以及用储液槽中的液体来弥补渡槽镀液由于蒸发产生的损失量等措施,达到了使电镀液的蒸发量与清洗水回收量的平衡,从而实现了电镀生产过程不排放任何清洗水的工艺。
任务十二 电镀生产线控制系统编程与实现
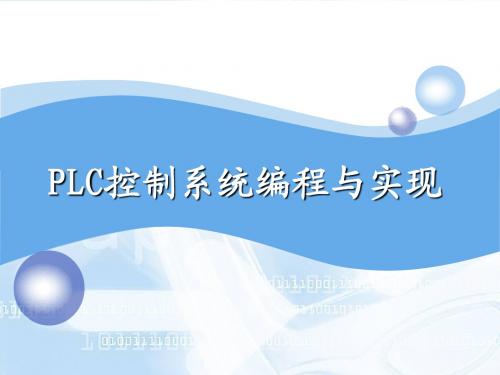
电镀生产线控制电路的PLC PLC外部接线图 图4-16 电镀生产线控制电路的PLC外部接线图
五、任务实施
2.设计程序 2.设计程序 根据控制电路的要求,在计算机中编写程序,程序设计如图4 17所示。 根据控制电路的要求,在计算机中编写程序,程序设计如图4-17所示。 所示
图4-17
电镀生产线控制电路的控制程序
热继电器
KM1 KM3 KM2 KM4
接触器KM1 接触器
热继电器
接触器KM3 接触器
停止按钮 启动按钮 上限位开关 镀槽限位开关
接触器KM2 接触器 接触器 接触器
下限位开关 回收液槽限位开关
清水槽限位开关 原点限位开关
表4-9
输入/ 输入/输出地址分配
五、任务实施
1.分配输入/输出地址,画出PLC外部接线图 分配输入/输出地址,画出PLC外部接线图 PLC 根据电路要求,PLC外部接线如图4 16所示。 根据电路要求,PLC外部接线如图4-16所示。 外部接线如图 所示
图4-15
电镀生产线示意图
四、任务分析
电镀生产线自动控制要求如下: 电镀生产线自动控制要求如下: 系统启动前吊钩及吊钩上被镀工件处于原点位置。 启动前吊钩及吊钩上被镀工件处于原点位置 1.系统启动前吊钩及吊钩上被镀工件处于原点位置。 系统启动后的工作循环为:工件放入镀槽——电镀5min——提起停放30s— 系统启动后的工作循环为:工件放入镀槽 电镀5min 提起停放30s 电镀5min 提起停放30s —放入回收液槽浸10 min 放入回收液槽浸10 min——提起停放16s 提起停放16s 放入清水槽清洗32s 放入回收液槽浸 提起停放16s——放入清水槽清洗32s 放入清水槽清洗32s——提起停 提起停 10s——专用行车返回原点。 专用行车返回原点。 放10s 专用行车返回原点 系统工作方式设置为自动循环 自动循环。 2.系统工作方式设置为自动循环。 短路保护和过载保护等必要的保护措施 设计主电路,要具有短路保护和过载保护等必要的保护措施。 3.设计主电路,要具有短路保护和过载保护等必要的保护措施。
基于PLC的电镀生产线控制系统的设计
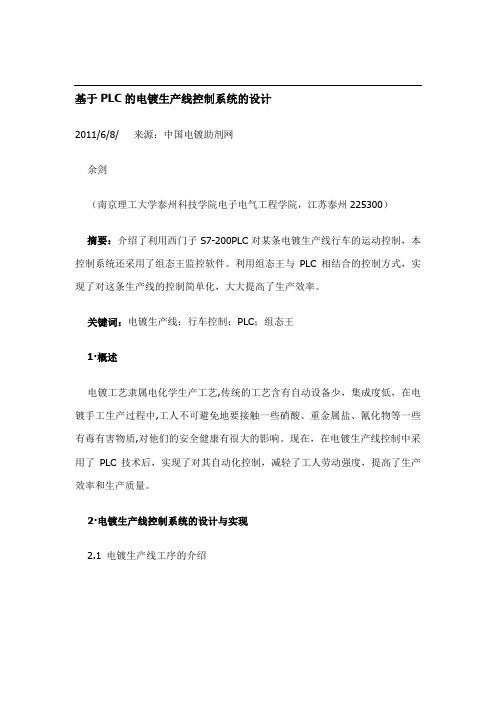
基于PLC的电镀生产线控制系统的设计2011/6/8/ 来源:中国电镀助剂网余剑(南京理工大学泰州科技学院电子电气工程学院,江苏泰州225300)摘要:介绍了利用西门子S7-200PLC对某条电镀生产线行车的运动控制,本控制系统还采用了组态王监控软件。
利用组态王与PLC相结合的控制方式,实现了对这条生产线的控制简单化,大大提高了生产效率。
关键词:电镀生产线;行车控制;PLC;组态王1·概述电镀工艺隶属电化学生产工艺,传统的工艺含有自动设备少,集成度低,在电镀手工生产过程中,工人不可避免地要接触一些硝酸、重金属盐、氰化物等一些有毒有害物质,对他们的安全健康有很大的影响。
现在,在电镀生产线控制中采用了PLC技术后,实现了对其自动化控制,减轻了工人劳动强度,提高了生产效率和生产质量。
2·电镀生产线控制系统的设计与实现2.1 电镀生产线工序的介绍电镀生产线主要由行车,电机和盛放液体的槽组成。
它的控制系统由工业级控制计算机、PLC和电器控制箱组成。
按照其工艺要求和规模一般设计由行车的运动来控制。
本文所涉及的课题将电镀的流程大致分成三大部分,镀前处理、电镀和镀后处理。
其电镀生产线的设计图如图1所示。
2.2 控制方式和要求本条电镀生产线的控制方式分为手动控制、单周期自动控制和连续循环自动控制。
2.2.1 手动控制。
要求手动按钮实现控制电镀生产线中电机的上升、下降、前进和后退动作。
2.2.2 单周期自动控制。
要求启动后,完成一次电镀工作回到原位停止。
2.2.3 连续循环自动控制。
要求启动后,完成一次电镀工作回到原位再连续循环工作。
2.2.4 单步操作。
要求每按一次启动按钮执行一个动作步。
2.3 相关硬件的选取2.3.1 传感器的选择。
接近开关可用于检验距离、尺寸控制、检测物体存在有否、检测生产包装线上有无产品包装箱等。
目前应用较为广泛的接近开关可分为:电感型、电容型、光电型、超声波型和电磁感应型。
电镀自动生产线PLC控制课程设计完整版
电镀自动生产线P L C 控制课程设计标准化管理处编码[BBX968T-XBB8968-NNJ668-MM9N]《电气与PLC控制系统设计》指导及任务书设计课题:电镀自动生产线PLC控制设计专业建筑电气与智能化学生姓名班级学号指导教师设计地点起至时间发放日期电气工程学院目录第一章概述1.1 电镀工艺的发展1.2 PLC- FX2N第二章电镀生产线总体设计说明2.1 电镀自动生产线示意图2.2 电镀自动生产线控制要求第三章控制系统设计说明3.1主电路设计说明3.2 PLC输入输出接线图设计说明3.3 控制面板元件布置图的设计 3.4 梯形图设计说明3.5 操作控制设计说明3.6 主要电器元件选择说明3.7 元器件目录表第四章设计小节概述1.1 电镀工艺的发展电镀生产作为一种传统产业自开始以来,几十年间有了极大的发展,从早期的纯手工作坊生产发展到今天的半自动甚至全自动生产,电镀工业的进步巨大的,电镀产品的种类和电镀工艺的复杂程度也是发生了极大的变化,大道汽车、飞机,小到生活用品金银首饰,各式各样的赣南工业产品都离不开电镀技术,电镀技术已发展形成一个重要的工程领域一个表面工程。
近年来随着生产的发展和不同产品工艺的特殊要求,电镀生产的生产过程在有些淋雨显得相当复杂,有许多条流水线构成一套完整的生产线,这就要各流水线之前能实现互联,因而PLC技术开始引入电镀。
质量优秀的电镀产品不光需要好的电镀工艺和镀液添加剂,还需要保证电镀产品按照电镀工艺流程运行以及电镀时间,这些都是决定电镀产品质量的重要因素。
因此PLC的引入尤为重要。
1.2 PLC- FX2N三菱FXPLC是小形化,高速度,高性能和所有方面都是相当FX系列中最高档次的超小程序装置,除输入出16~25点的独立用途外,还可以适用于多个基本组件间的连接,模拟控制,定位控制等特殊用途,是一套可以满足多样化广泛需要的PLC。
特点 -系统配置即固定又灵活;-编程简单;备有可,丰富的品种;令人放心的高性能;高速运算;使用于多种特殊用途;外部机器通讯简单化;共同的外部设备。
电镀生产线控制系统的PLC程序设计指导
—260—电镀生产线控制系统的PLC 程序设计指导李哲林(内蒙古通辽市工业职业学校,内蒙古 通辽 028000)摘 要:随着我国国民经济的迅速发展,电镀与精饰的新技术,新工艺不断涌现。
电镀生产线实现的是一个复杂的工艺生产过程,需要控制电镀时间,电镀电流,电压,溶液浓度,温度,相关的周边设备控制及生产过程自动化。
本文介绍了利用三菱FX 系列PLC 对某条电镀生产线行车的运动控制程序设计的准备工作。
关键词:电镀生产线;PLC;行车控制1 什么是电镀电镀是一种电化学过程,也是一种氧化还原过程.电镀的基本过程是将零件浸在金属盐的溶液中作为阴极,金属板作为阳极,接直流电源后,在零件上沉积出所需的镀层。
电镀时,镀层金属或其他不溶性材料做阳极,待镀的工件做阴极,镀层金属的阳离子在待镀工件表面被还原形成镀层。
为排除其它阳离子的干扰,且使镀层均匀、牢固,需用含镀层金属阳离子的溶液做电镀液,以保持镀层金属阳离子的浓度不变。
电镀的目的是在基材上镀上金属镀层,改变基材表面性质或尺寸。
电镀能增强金属的抗腐蚀性(镀层金属多采用耐腐蚀的金属)、增加硬度、防止磨耗、提高导电性、润滑性、耐热性和表面美观。
2 电镀的作用利用电解作用在机械制品上沉积出附着良好的、但性能和基体材料不同的金属覆层的技术。
电镀层比热浸层均匀,一般都较薄,从几个微米到几十微米不等。
通过电镀,可以在机械制品上获得装饰保护性和各种功能性的表面层,还可以修复磨损和加工失误的工件。
3 情景描述在三十年代,某钢铁厂就具有电镀较宽带钢的专用生产作业线,使用不溶阳极,利用低品位矿石和碎矿补充电解液中的锌,采用过滤和净化循环,从而维持电镀液的成分。
1939年,Weirton steel 的镀锡作业线改用镀锌。
在此采用了Hubble Weisberg 电镀液,并添加了氨合氯化锌络盐。
弹药箱因为生锈而损坏,为使其具有耐蚀性,将镀锡作业线改为带钢作业线。
全自动电镀生产线是按照一定的工艺要求,将有关的各种电镀处理槽、行车、机架、电气系统、电源设备、抽风系统、循环过滤系统、温控加热系统、空气搅拌系统、液位控制系统、阴极移动装置等构成一个完整的多功能自动控制系统。
电镀加工自动线PLC控制系统设计.
学号:14113500522毕业设计(论文)题目:电镀加工自动线PLC控制系统设计作者郑鸣届别 2015 系别机械工程学院专业机械电子工程指导老师李荣华职称副教授完成时间 2015年5月20日摘要本文以电镀自动生产线控制系统设计为研究对象,以其电镀专用行车为控制对象,对其电镀的工艺要求和控制要求进行了分析,采用理论研究的方法,设计了一套基于PLC的电镀车间专用行车自动控制系统。
本系统选用三菱FX2N-64MR-001型号的PLC来进行控制,通过PLC输出信号接触器的触点动作,来控制三台异步电动机的运行,从而实现对行车的水平运动和吊钩的垂直运动的控制,考虑到电镀、上升、下降等运动时行车和吊钩需要准确停位。
在程序设计时为了便于对设备进行调整和检修,设计了手动程序以实现对行车和吊钩的点动控制,对于自动控制程序的设计,其工作过程是典型的顺序控制,采用步进指令能很好的实现对其控制。
通过软件仿真可以看出所设计的控制系统很好的实现了电镀的工艺要求和控制要求,可以方便完成自动和手动之间的切换,体现出PLC控制系统具有调试方便、适应性强的优点。
关键字:电气控制、PLC、行车控制、电镀ABSTRACTThe electroplating automatic production line to control system design to study, with its specialized operations to control traffic. the electroplating technology and control of the claim was analysed and the theory of the research methods, design a web based on the plc electroplated impression of the special traffic control system; The system for mitsubishi fx2n - 64mr -001 kind of the plc to control, the output signal of the plc contacts with some action to control motor three asynchronous operation, the level of the motion and the hook vertical motions of the operations,rising and falling, the motion and the hook to the right stop. in programming, to facilitate the adjustment of equipment and design a manual procedures for the implementation and hook at the control, the automatic control of the design, it is typical of the order of control and use the step into the instructions to the very good with the controls. Through software simulations can see that the system of the electroplating technology and control, you can easily finish automatic and manual switch between that of the plc control system for the adaptable.Key words:electric control;programmable logic control;control of vehicle motion;electroplate目录摘要 (1)第一章绪论 (4)1.1 电镀生产线简介 (4)1.2 电镀行车控制系统的种类 (4)1.2.1 继电接触器控制系统 (4)1.2.2单片机控制系统 (5)1.3电镀行车及专用行车的简介 (6)1.3.1电镀行业的简介 (6)1.3.2行车的简介 (7)1.3.3电镀行车控制系统的发展与现状 (7)1.4电镀加工自动线PLC控制系统设计内容 (8)1.4.1设备基本情况 (8)1.4.2 拖动系统 (9)1.5 电镀加工自动线PLC控制系统设计要求 (9)第二章控制系统总体方案及系统硬件设计 (10)2.1 电镀车间专用行车PLC控制系统方案选择 (10)2.1.1 拖动方案 (10)2.1.2 槽位选择方案 (10)2.1.3 信号检测装置选择 (10)2.1.4 指示显示方案 (10)2.2 电镀车间专用行车PLC控制系统主电路 (10)2.3 保护方案选择 (11)2.4 抗电源干扰措施 (11)2.5 控制系统的接地设计 (12)第三章控制系统软件设计 (13)3.1 控制系统动作流程框图 (13)3.2 系统控制流程图 (13)3.3 PLC选型 (14)3.4 I/O点分配 (16)第四章测试调试 (19)5 参考文献 (21)致谢 (22)第一章绪论1.1 电镀生产线简介随着我国国民经济的迅速发展,电镀与精饰的新技术和新工艺不断涌现。
零件电镀生产线PLC控制系统设计
毕业设计(论文)开题报告课题零件电镀生产线PLC控制系统设计一课题背景及意义1.课题的背景国内电镀生产线的发展状态电镀生产线从手工操作,逐步向机械和自动化方向发展。
我国在这方面的发展是比较快的。
在60年代,我国大多数的电镀生产,仍以手工操作为主。
而现在的不少企业甚至是乡镇企业,已有了比较好的电镀自动线。
在借助国外先进技术的基础上,现在已经开发了各种类型的微型电脑控制电镀自动线,上海近500家电镀厂、点,已经有370多条电镀自动线,并有25条从外国引进的自动线,可见我国的电镀生产,正在向自动化方向发展。
其中比较好的自动线的行车起步、制动、运行平稳,电机采用无极变速或配备变频调速后,定位准确,用聚氨酯作行车运行轮,运行时惯性小,噪声低,制动性好。
车辆的运行,溶液的温度、PH及添加剂的自动补充,已有用微电脑自动控制,但我国的电镀生产设备与国外的先进国家相比,还有比较大的差距,相对而言,手工操作还是比较多的,有些厂的机械设备还比较陈旧,自动化程度不高。
现阶段我国的电镀生产线,主要应该考虑行车运行平稳,定位准确,设备耐用,生产效率高,确保电镀质量高,质量好。
现在有些企业在设计电镀自动线时,要求一条自动线有多种功能,例如既能镀铁零件,还能镀锌压铸件;既能镀装饰铬镀层,又能仿镀金和仿铜镀层。
其实,有些槽子排在内线基本上不用,行车在这些不用的槽子上面走来走去,既降低生产效率,又影响产品质量。
有些电镀线中安排了许多清洗槽和辅助槽;有些辅助槽过宽,使一条电镀线排得很长,同样会降低生产效率和产品质量。
总之,我国的电镀生产线要向国际上最先进的方向发展,但现阶段应在讲究实用、实效的基础上求先进,循序渐进,逐步提高我国电镀生产的先进水平。
国外电镀生产线的发展状态美国,日本等国的电镀自动线比我国先进,如日本大友电舍株式会社的电镀车间,各种镀液中的主要成分都是由电脑自动检测和自动控制及补充,操作的各种参数温度、PH值、电流等都由电脑自动测定和自动调节,行车的运行完全无人操作。
- 1、下载文档前请自行甄别文档内容的完整性,平台不提供额外的编辑、内容补充、找答案等附加服务。
- 2、"仅部分预览"的文档,不可在线预览部分如存在完整性等问题,可反馈申请退款(可完整预览的文档不适用该条件!)。
- 3、如文档侵犯您的权益,请联系客服反馈,我们会尽快为您处理(人工客服工作时间:9:00-18:30)。
…… D+ K3 D120
%偏差模糊量化值7(a+3);
ANB
D* K7 D120 LPP ….. D+ K3 D124 LD M8000
%偏差变化模糊化值b+3; %7(a+3)+b+3得到模糊控制值的位置;
DMOV D120 D128
ANB
D+ D124 D128 ANB MOVE D128 AC1 MOVE &D300 AC2
4.1.3 行车速度控制程序
电镀速度控制程序是自动运行一部分,是保证系统时间优化的关键所在,由于采用 了智能控制算法,程序控制的设计变的复杂,涉及到和模糊控制的结合应用,每次运行 时的参数设置、数据的采集与处理、智能算法的设计实现以及控制输出等部分。
PLC 的行车工作过程是当行车需要行走时,行车得到目标槽位信息后,就不停通过 光电感应开关采集位置数据,与预置值比较,那么计算误差及误差变化并判断大小,模 糊控制程序对偏差和偏差变化进行模糊化处理,然后计算输出量所在速度并查表,根据 查出的参数进行去模糊化并进行运算,得出输出量,给出一定合理的速度行驶。其程序
bit1 0:输入变化量报警无 1:输入变化量报警有效
b15
8 7 6 5 4 3 2 1 b0
000000110
256 128 64 32 16 8 4 2 1
M150~ M165(24 =16)
00000000001000000
M165
M156
M152 M151 M150
图 4.2 DECO 指令功能
Fig 4.2 Instruction function of DECO
样的,只是其基地址不同,分别为D300,D302,D304。而其处理的程序是相似的,它 们在模糊控制表中的值最后分别存放在了D132,D134和D136中,把这些值乘以各自的 比例因子调整后即可放入PID控制指令的回路表中执行输出。
PID计算模块
48
三菱FX2N的指令内带PID指令。PID指令可同时多次执行(环路数目无限制),但一 定要注意运算使用的软元件号不能重复。为了让PID运算以预想的采样频率工作,PID 指令必须用在定时发生的中断程序中或者用在主程序中,被定时器所控制以一定频率执
43
4.1.2 转速测量程序
图 4.4 行车运动程序 Fig 4.4 Driving moving program
如第二章所述本课题采用数字式转速测量方法,采用PLC测量电机转速可以保证测 量的稳定性和高精度。目前,PLC实现脉冲信号的测量主要是用PLC的高速计数单元来 实现。但是,带有高速计数功能的PLC成本昂贵。为了使用普通PID模块实现高速脉冲的 计数, 采用了专用的软高速计数指令, 利用多周期频率测量方法, 测量N周期的待测信 号的时间间隔, 再用此时间间隔除以N得到周期, 然后求出频率 既保证了测量的精度, 又简化了程序。程序流程如下
数ACT设定,bit1\bit2和bit5均为“0”时,只占有S3开始的20点)
控制用的参数的设定值在PID运算前必须预先通过MOV等指令写入。另外,指定停
电保持区域的数据寄存器时,编程控制器的电源OFF之后设定值仍保持。
S3 采样时间(Ts)
S3+1 动作方向ACT bit0 0:正动作
1:反动作
编程首先定义动作执行条件,首先设置 PLC 内部中间继电器 M151-M158 分别作为行车
进退,上升,下降,延时,完成标志的动作执行条件.,当中间继电器置 1 时,表示该行车
动作被选择,为 0 时不选择。即当寄存器中数字为 1 时,行车执行行走动作;数字为 2
时,行车执行上升动作;数字为 3 时,行车执行下降动作;数字为 4 时,行车执行延时
成行车动作状态表,如图 4.3 所示。
图 4.3 行车动作状态表 Fig 4.3 State chart of driving action
当读取数值时,先比较是否大于 10,如大于 10 就代表行车准备进退动作,将数值 除于 10 后,商为目标槽位,余数为将被 DECO 解码的动作执行条件。而行车运行方向, 即是进还是退,则将目标槽位,与通过计数的槽位进行比较,如果目标槽位大于通过计 数感应的槽位数,M175 置一,则行车前进,反之 M177 置一,行车后退.程序如图 4.4:
47
Uij =D100+D[7(a+3)+b+3]
式中 Uij (I,j=0…6)表示第i行第j列输出控制量的所对应的地址,读出这个地址中的值乘 以规则因子得到解模糊值。
在查询模糊控制表时,由于查询的 ΔKP 、ΔKI 、ΔKD 。的条件都是误差和误差变化,
因而同一个误差和误差变化对应于一个连续的空间,查到了一个值,另外两个就可查到, 然后存入回路表,调用指令就求得了输出控制量。 程序实现的主要部分如下
LDD<> D50 D54
%如果D50不等于D52,则计算偏差和偏差变化;
DMOV D50 D58
……….
ANB D- D62 D66 ANB LPS DMOVE D66 D74
%求得速度偏差; %得到偏差变化;
ANB
D- D70 D74
AENO DMOVE D66 D70 LPP DMOVE D58 D62
在这固定流程,行车是按着程序员所指定的路径行走,流程图见附录 B。 将每一个步骤化为十进制数,并对应一个数据寄存器,每一个步骤执行的动作和所 行走的目标槽位组合成十进制数据事先存入数据寄存器中,形成一个行车运动状态表。 一个步骤结束,下一个步骤开始,从而演变为按顺序读取每一个数据寄存器。先利用变 址寄存器v0作为偏差值,因此利用变址功D1000V0 可以获得用于保存下一个工序即步骤 的对应寄存器地址,利用三菱FX2N指令DECO,将数据译码,从而对应执行其动作。图 4.1为流程图
45
流程图如图 4.6 所示[57] 速度控制程序启动 程序初始化 测速子程序
测速是否
N
完成
Y
计算速度偏差和偏 差变化
偏差和偏差变化模 糊化
查模糊控制表取输 出值
解模糊
跳出本程序
参数存入PID回路表 PID运算
输出控制量U
系统动作
图 4.6 行车速度控制流程图 Fig 4.6 Speed control flow chart of Driving
44
初始化
立即方式读出端口状态
信号上升沿检测
是否有上升沿
是
否
计时是否超过时
间窗
是 计算转速
脉冲计数器清零时 间窗定时器重启
否 脉冲计数器加 1
图 4.5 测量速度流程图 Fig 4.5 speed measure flow chart
首先使用立即刷新方式读出端口状态, 立即刷新方式可以在执行这条语句的同时, 将外部端口当时的状态读入到PLC内部相应的I/O变量。上升沿检测, 即将此次端口状态 与上一次此端口状态相比较, 如果上一次为0 这一次为1, 则认为在此端口产生了一次 上升沿。判断计时是否超过时间窗, 是将时间窗定时器与时间窗的进行比较。时间窗定 时器一旦启动便开始对PLC 内部标准1mS 的时钟进行计数来实现计时, 一旦启动后定 时器的计时不依赖于程序的执行。脉冲计数器就是在PLC内存中用于存储待测信号脉冲 个数的变量。每次检测到待测信号上升沿到来时, 将此变量加1。每次计时超过时间窗 时, 计算完转速后将此变量清零。
行采样时间必须设置输入到PID运算中。
每个PID回路有两个输入量,给定值SV和过程变量PV。给定值通常是一个固定的值,
给定值和过程变量都可能是现实世界的值,它们的大小、范围和工程单位都可能不一样。
PID指令在对这些量进行运算以前,必须把他们转换成标准的浮点型实数。转换的第一
步是把16位整数值转成浮点型实数值,下面的指令序列提供了实现这种转换的方法:用于
电编码器的分辨率,对输入量e模糊化处理,量化为7个等级;同理偏差变化的量化也是
如此,将其也量化为7个等级;输出控制量为 ΔKP 、 ΔKI 、 ΔKD 根据其各自的基本论域
已经量化在模糊控制表中。 这里需要首先确定模糊控制表在中的存贮格式,为了便于查询查找,模糊控制表必
须按顺序存储,由模糊控制表的特点来看,整个模糊控制查询表可以看成的矩阵,如果 求得了误差的模糊量化值为a(a=-3,…,3),误差变化的模糊量化值为b(b=-3,…,3),并 且假定整个模糊控制表的矩阵开始地址为D100,那么输出控制量的地址我们就可以用下 式表示:
%相对地址送指针AC1; %基地址D300送指针AC2;
LD M8000
I+ AC1 AC2
ANB DMOVE *AC2 D132 …… DMOVE *AC2 D134 …… DMOVE *AC2 D136
%绝对地址中的值送D132 %绝对地址中的值送D134 %绝对地址中的值送D136
Hale Waihona Puke …….在上边的程序中,由于 ΔKP 、 ΔKI 、 ΔKD 的存放是连续的,因而其相对地址是一
本系统是采用三菱 FX2N 型号,因此 PLC 程序使用 GX DEVELOP8 专业软件进行 编程。触摸屏是三菱 GOT 系列,其编程软件为 GT DESGIN V2.
4.1 电镀控制系统程序的设计
4.1.1 行车运行流程编程
在直线式电镀自动生产线中,行车的基本动作有:前进、后退、钩上升、钩下降等 四种;除此之外还有延时上升、延时下降、延时前进等延时动作,总计有十余种。