§3制动器的设计计算
制动器设计-计算说明书

制动器设计-计算说明书三、课程设计过程(一)设计制动器的要求:1、具有良好的制动效能—其评价指标有:制动距离、制动减速度、制动力和制动时间。
2、操纵轻便—即操纵制动系统所需的力不应过大。
对于人力液压制动系最大踏板力不大于(500N )(轿车)和700N (货车),踏板行程货车不大于150mm ,轿车不大于120mm 。
3、制动稳定性好—即制动时,前后车轮制动力分配合理,左右车轮上的制动力矩基本相等,汽车不跑偏、不甩尾;磨损后间隙应能调整!4、制动平顺性好—制动力矩能迅速而平稳的增加,也能迅速而彻底的解除。
5、散热性好—即连续制动好,摩擦片的抗“热衰退”能力要高(指摩擦片抵抗因高温分解变质引起的摩擦系数降低);水湿后恢复能力快。
6、对挂车的制动系,还要求挂车的制动作用略早于主车;挂车自行脱钩时能自动进行应急制动。
(二)制动器设计的计算过程:设计条件:车重2t ,重量分配60%、40%,轮胎型175/75R14,时速70km/h ,最大刹车距离11m 。
1. 汽车所需制动力矩的计算根据已知条件,汽车所需制动力矩:M=G/g ·j ·r k (N ·m ) 206.321j )(v S ?=(m/s 2)式中:r k —轮胎最大半径 (m);S —实际制动距离 (m);v 0 —制动初速度 (km/h)。
217018211 3.6j ??=?=(m/s 2) m=G/g=2000kg查表可知,r k 取0.300m 。
M=G/g ·j ·r k =2000·18·0.300=10800(N ·m )前轮子上的制动器所需提供的制动力矩:M ’=M/2?60%=3240(N ·m )为确保安全起见,取安全系数为 1.20,则M ’’=1.20M ’=3888(N ·m )2. 制动器主要参数的确定(1)制动盘的直径D制动盘直径D 希望尽量大些,这时制动盘的有效半径得以增大,就可以降低制动钳的夹紧力,降低摩擦衬块的单位压力和工作温度。
制动器的设计计算

制动器的设计计算制动器是用来减速和停止运动物体的一种装置。
在设计制动器时,需要考虑以下几个因素:制动力的大小、制动距离的要求、制动器材料的选型、热力学效应以及制动器的结构设计等等。
首先,要确定所需的制动力大小。
制动力是指制动器施加在运动物体上的力,它的大小决定了物体的减速度和停止的时间。
根据实际需求和应用场景,可以通过以下公式计算制动力:制动力=质量×减速度其中,质量是指运动物体的质量,减速度是要达到的减速度。
根据这个制动力,可以选择适当的制动器结构和材料。
其次,要确定制动距离的要求。
制动距离是指从开始制动到停止的距离,它的大小决定了制动器制动的效果和占用的空间。
制动距离可以通过以下公式计算:制动距离=初始速度²/(2×减速度)其中,初始速度是运动物体开始制动时的速度,减速度是物体的减速度。
根据这个制动距离,可以调整制动器结构和制动参数的设计。
然后,要选择适当的制动器材料。
制动器材料需要具备一定的强度、硬度和耐磨性,以保证制动效果和使用寿命。
常见的制动器材料包括金属、陶瓷和复合材料等。
选择合适的材料还需要考虑制动温度的影响,因为制动过程中会产生大量的热量,可能导致制动器材料的热膨胀、软化或者燃烧。
最后,要进行制动器的结构设计。
制动器的结构设计包括选择合适的制动器类型(如摩擦制动器、液力制动器和电磁制动器等),确定制动器的安装位置和方式,设计制动器的摩擦面积和接触面形状等。
结构设计需要考虑制动器的尺寸、重量和安装方便性,以保证制动器能够稳定可靠地工作。
在制动器设计的过程中,还需要考虑一些其他的因素,如制动器的可靠性、维修性以及制动器和运动物体之间的适配性。
制动器的设计是一个综合考虑各种因素的过程,需要进行合理的计算和模拟分析,并结合实际的试验验证。
制动器设计及计算实例汇总
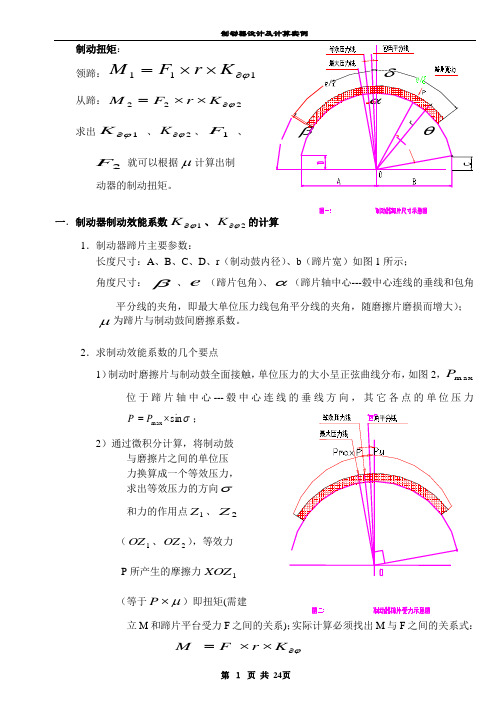
等效压力:
或
方向通过 ,
以上是固定销式求合力的方法(含合力的角度 )
摩擦力矩:
,c为常数;(另外,摩擦力矩T还可以用积分方法求: = )
=
力矩:
由制动器的几何尺寸( 、 )确定。
总等效压力:
由P与输入力F的关系可作图求出(力平衡)
故可得出:
式中BEF为制动器效率因数。
车型
制动鼓
直径
(前桥)
(前桥)
为蹄片与制动鼓间磨擦系数。
2.求制动效能系数的几个要点
1)制动时磨擦片与制动鼓全面接触,单位压力的大小呈正弦曲线分布,如图2, 位于蹄片轴中心---毂中心连线的垂线方向,其它各点的单位压力 ;
2)通过微积分计算,将制动鼓
与磨擦片之间的单位压
力换算成一个等效压力,
求出等效压力的方向
和力的作用点 、
( 、 ),等效力
0.576
0.621
0.574
0.571
0.58
0.568
0.416
0.35
0.292
0.263
0.285
0.286
0.295
摩擦片上最大单位压力位于 角处:
摩擦片上单位压力的分配:
位于与x-x成 角处。
单位压力在x、y方向上分解:
P分解为:
对整个蹄片x-x方向上合力为:
同样y-y方向上合力为:
合力角度
P所产生的摩擦力
(等于 )即扭矩(需建
立M和蹄片平台受力F之间的关系);实际计算必须找出M与F之间的关系式:
3)制动扭矩计算
蹄片受力如图3:
a.三力平衡
领蹄:
从蹄:
b.通过对蹄片受力平衡分析(对L点取力矩)
制动器设计及计算实例
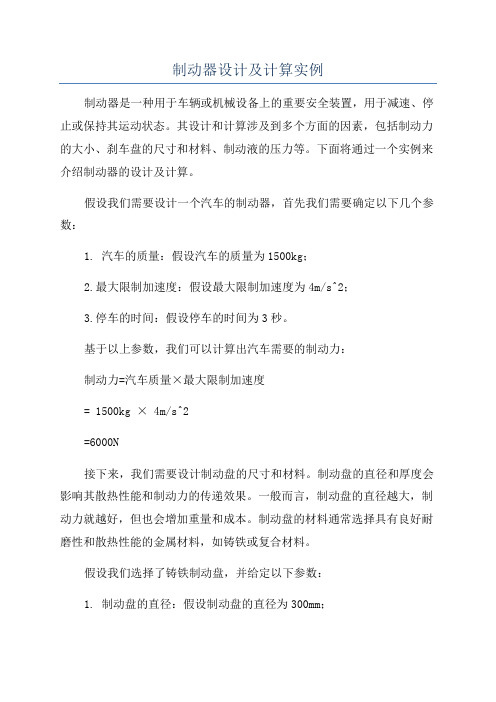
制动器设计及计算实例制动器是一种用于车辆或机械设备上的重要安全装置,用于减速、停止或保持其运动状态。
其设计和计算涉及到多个方面的因素,包括制动力的大小、刹车盘的尺寸和材料、制动液的压力等。
下面将通过一个实例来介绍制动器的设计及计算。
假设我们需要设计一个汽车的制动器,首先我们需要确定以下几个参数:1. 汽车的质量:假设汽车的质量为1500kg;2.最大限制加速度:假设最大限制加速度为4m/s^2;3.停车的时间:假设停车的时间为3秒。
基于以上参数,我们可以计算出汽车需要的制动力:制动力=汽车质量×最大限制加速度= 1500kg × 4m/s^2=6000N接下来,我们需要设计制动盘的尺寸和材料。
制动盘的直径和厚度会影响其散热性能和制动力的传递效果。
一般而言,制动盘的直径越大,制动力就越好,但也会增加重量和成本。
制动盘的材料通常选择具有良好耐磨性和散热性能的金属材料,如铸铁或复合材料。
假设我们选择了铸铁制动盘,并给定以下参数:1. 制动盘的直径:假设制动盘的直径为300mm;2. 制动盘的厚度:假设制动盘的厚度为40mm;根据制动盘的直径和厚度,我们可以计算制动盘的转动惯量:转动惯量=(1/2)×制动盘的质量×(制动盘的直径/2)^2=(1/2)×制动盘的质量×(0.15m)^2根据实际情况,制动盘的质量需要根据制动盘的材料、直径和厚度来选择。
为了方便计算,假设制动盘的质量为20kg。
转动惯量= (1/2) × 20kg × (0.15m)^2= 0.45kg·m^2接下来,我们需要选择适当的制动液和计算所需的制动液压力。
制动液在制动器中起到传递力和控制制动器放松的作用。
制动液需要具有良好的抗压性、稳定性和耐高温性能。
假设我们选择了常用的DOT4制动液,并给定以下参数:1.制动液的抗压性比:假设制动液的抗压性比为10:1;2.需要的制动力:假设需要的制动力为6000N。
制动系统计算说明书
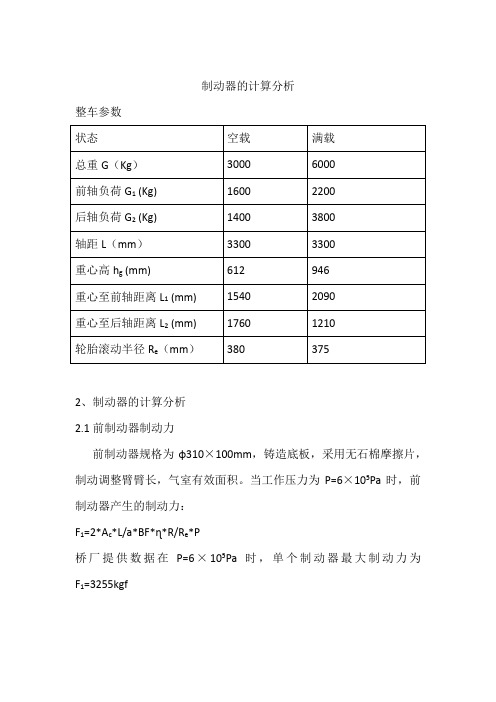
制动器的计算分析整车参数2、制动器的计算分析2.1前制动器制动力前制动器规格为ɸ310×100mm,铸造底板,采用无石棉摩擦片,制动调整臂臂长,气室有效面积。
当工作压力为P=6×105Pa时,前制动器产生的制动力:F1=2*A c*L/a*BF*ɳ*R/R e*P桥厂提供数据在P=6×105Pa时,单个制动器最大制动力为F1=3255kgf以上各式中:A c—气室有效面积L—调整臂长度a—凸轮基圆直径BF—制动器效能因数R—制动鼓半径R e—车轮滚动半径ɳ—制动系效率P—工作压力2.2后制动器制动力后制动器规格为ɸ310×100mm,铸造底板,采用无石棉摩擦片,制动调整臂臂长,气室有效面积。
当工作压力为P=6×105Pa时,前制动器产生的制动力:F2=2*A c*L/a*BF*ɳ*R/R e*P桥厂提供数据在P=6×105Pa时,单个制动器最大制动力为F2 =3467kgf2.3满载制动时的地面附着力满载制动时的地面附着力是地面能够提供给车轮的最大制动力,正常情况下制动气制动力大于地面附着力是判断整车制动力是否足够的一个标准。
地面附着力除了与整车参数有关之外,还与地面的附着系数有关,在正常的沥青路面上制动时,附着系数ϕ值一般在0.5~0.8之间,我们现在按照路面附着系数为0.7来计算前后地面附着力:F ϕ前=G 满1×ϕ+G hgL×ϕ2=2200×0.7+6000×6123300×0.72=2002kgfF ϕ后=G 满2×ϕ-GhgL×ϕ2=3800×0.7-6000×9463300×0.72=1487kgf因为前面计算的前后制动器最大制动力分别为F1=3255kgfF2=3467kgf3、制动器热容量、比摩擦力的计算分析 3.1单个制动器的比能量耗散率的计算分析 前制动器的衬片面积A 1=2×πR 1×w1180×L 1=mm 2式中(L 1=100mm 摩擦片的宽度 w 1=110°) 后制动器的衬片面积A 2=2×πR 2×w2180×L 2=mm 2式中(L 2=100m m 摩擦片的宽度 w2=) 比能量耗散率e 1=GV 124tA 1β= e 2=GV 124tA 2β=上式中:G —满载汽车总质量V 1—制动初速度,计算时取V 1=18m/s β—满载制动力分配系数 t —制动时间,计算时取t=3.06s鼓式制动器的比能量耗散率以不大于1.8W/mm 2为宜,故该制动器的比能量耗散率满足要求。
制动器设计的计算过程
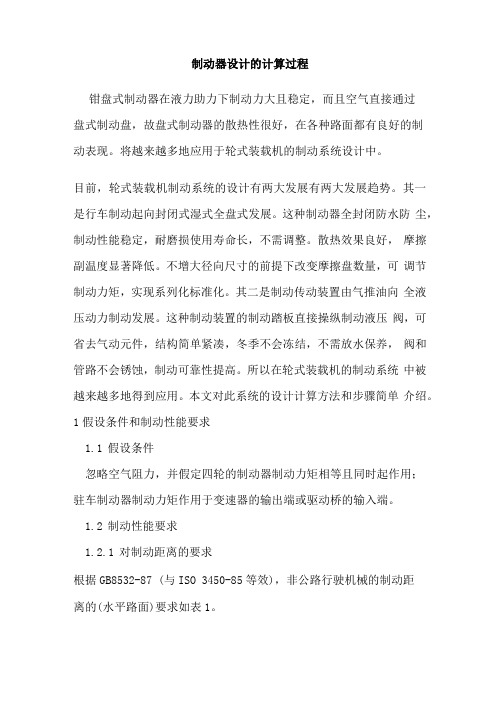
制动器设计的计算过程钳盘式制动器在液力助力下制动力大且稳定,而且空气直接通过盘式制动盘,故盘式制动器的散热性很好,在各种路面都有良好的制动表现。
将越来越多地应用于轮式装载机的制动系统设计中。
目前,轮式装载机制动系统的设计有两大发展有两大发展趋势。
其一是行车制动起向封闭式湿式全盘式发展。
这种制动器全封闭防水防尘,制动性能稳定,耐磨损使用寿命长,不需调整。
散热效果良好,摩擦副温度显著降低。
不增大径向尺寸的前提下改变摩擦盘数量,可调节制动力矩,实现系列化标准化。
其二是制动传动装置由气推油向全液压动力制动发展。
这种制动装置的制动踏板直接操纵制动液压阀,可省去气动元件,结构简单紧凑,冬季不会冻结,不需放水保养,阀和管路不会锈蚀,制动可靠性提高。
所以在轮式装载机的制动系统中被越来越多地得到应用。
本文对此系统的设计计算方法和步骤简单介绍。
1假设条件和制动性能要求1.1假设条件忽略空气阻力,并假定四轮的制动器制动力矩相等且同时起作用;驻车制动器制动力矩作用于变速器的输出端或驱动桥的输入端。
1.2制动性能要求1.2.1对制动距离的要求根据GB8532-87 (与ISO 3450-85等效),非公路行驶机械的制动距离的(水平路面)要求如表1。
表1非公路行驶机械的制动距离最高车速(km/h)最大质量(kg)行车制动系统的制动距离(m)辅助制动系统的制动距离(m)二32/ 0 W32000 V2/68+(V2/124) . (G/32000) V2/39+ (V2/130). (G/32000)三32000 V2/44 V2/30W32 / 0 W32000 V2/68+(V2/124) . (G/32000) +0.1(32-V) V2/39+ (V2/130) . (G/32000) +0.1(32-V)三32000 V2/44+0.1(32-V) V2/30+0.1(32-V)* V——制动初速度(Km/h) G——整机工作质量(kg)1.2.2对行车系统的性能要求除了满足制动距离要求外,还要求行车制动系统能满足装载机空载在25% (14.0)的坡度上停住。
制动器的设计计算

§3 制动器的设计计算3.3制动蹄上的压力分布规律与制动力矩的简化计算1.沿蹄片长度方向的压力分布规律用解析方法计算沿蹄片长度方向的压力分布规律比较困难,因为除了摩擦衬片有弹性容易变形外,制动鼓、制动蹄以及支承也都有弹性变形。
通常在近似计算中只考虑衬片径向变形的影响,其他零件变形的影响较小,可以忽略不计。
制动蹄可设计成一个自由度和两个自由度的(见图37)形式。
首先计算有两个自由度的增势蹄摩擦衬片的径向变形规律。
为此,取制动鼓中心O点为坐标原点,如图37所示,并让y 1坐标轴通过制动蹄的瞬时转动中心A 1点。
制动时,由于摩擦衬片变形,制动蹄在绕瞬时转动中心A 1转动的同时,还顺着摩擦力作用方向沿支承面移动。
结果使制动蹄中心位于点,因而可以想象未变形的摩擦衬片的表面轮廓(EE 1O l 线)就沿方向移人制动鼓体内。
显然,衬片表面上所有点在这个方向上的变形是相同的。
例如,位于半径,上的任意点的变形就是线段。
因此,对于该点的径向变形为1OO 1OB 1B '11B B 1'11111cos Ψ≈=B B C B δ由于 和ο90)(111−+=Ψαϕmax 11'11δ==OO B B 于是得到增势蹄的径向变形1δ和压力为1q )sin(11max 11ϕαδδ+≈)sin(11max 1ϕα+=q q (43)式中 1α——任意半径1OB 和轴之间的夹角;1y 1ϕ——最大压力线与轴之间的夹角;1OO 1x 1ψ——半径和线之间的夹角。
1OB 1OO 下面再计算有一个自由度的增势蹄摩擦衬片的径向变形规律。
此时摩擦衬片在张开力和摩擦力的作用下,绕支承销中心A 1转动γd 角(见图37(b))。
摩擦衬片表面任意点沿制动蹄转动的切线方向的变形即为线段,其径向变形分量是线段,在半径延长线上的投影,即线段。
由于1B '11B B '11B B 1OB 1BB γd 角很小,可以认为,则所求的摩擦衬片径向变形为°=∠90'111B B Aγγγδd B A B B C B ⋅===sin sin 11'11111 考虑到,则由等腰三角形可知R OB OA =≈1111OB A γαsin /sin /11R B A = 代入上式,得摩擦衬片的径向变形和压力分别为γαδd R sin 1=αsin max 11q q = (44)综合上述可以认为:对于尚未磨合的新制动蹄衬片,沿其长度方向的压力分布符合正弦曲线规律,可用式(43)和式(44)计算。
制动器选择计算公式
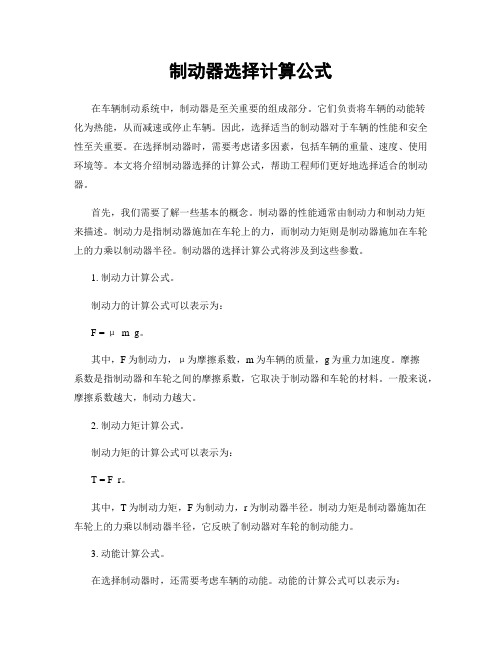
制动器选择计算公式在车辆制动系统中,制动器是至关重要的组成部分。
它们负责将车辆的动能转化为热能,从而减速或停止车辆。
因此,选择适当的制动器对于车辆的性能和安全性至关重要。
在选择制动器时,需要考虑诸多因素,包括车辆的重量、速度、使用环境等。
本文将介绍制动器选择的计算公式,帮助工程师们更好地选择适合的制动器。
首先,我们需要了解一些基本的概念。
制动器的性能通常由制动力和制动力矩来描述。
制动力是指制动器施加在车轮上的力,而制动力矩则是制动器施加在车轮上的力乘以制动器半径。
制动器的选择计算公式将涉及到这些参数。
1. 制动力计算公式。
制动力的计算公式可以表示为:F = μ m g。
其中,F为制动力,μ为摩擦系数,m为车辆的质量,g为重力加速度。
摩擦系数是指制动器和车轮之间的摩擦系数,它取决于制动器和车轮的材料。
一般来说,摩擦系数越大,制动力越大。
2. 制动力矩计算公式。
制动力矩的计算公式可以表示为:T = F r。
其中,T为制动力矩,F为制动力,r为制动器半径。
制动力矩是制动器施加在车轮上的力乘以制动器半径,它反映了制动器对车轮的制动能力。
3. 动能计算公式。
在选择制动器时,还需要考虑车辆的动能。
动能的计算公式可以表示为:E = 0.5 m v^2。
其中,E为动能,m为车辆的质量,v为车辆的速度。
动能是车辆的速度和质量的函数,它反映了车辆在运动过程中所具有的能量。
综合考虑以上几个公式,我们可以得出制动器选择的计算公式:T = μ m g r。
根据这个计算公式,我们可以计算出所需的制动力矩,从而选择适合的制动器。
需要注意的是,实际的制动器选择还需要考虑到制动器的类型、材料、散热能力等因素,这些因素将对制动器的性能产生重要影响。
除了上述的计算公式外,还有一些其他因素需要考虑。
例如,制动器的热容量、制动器的响应时间、制动器的耐久性等。
这些因素将对制动器的选择产生重要影响,工程师们在选择制动器时需要综合考虑这些因素。
- 1、下载文档前请自行甄别文档内容的完整性,平台不提供额外的编辑、内容补充、找答案等附加服务。
- 2、"仅部分预览"的文档,不可在线预览部分如存在完整性等问题,可反馈申请退款(可完整预览的文档不适用该条件!)。
- 3、如文档侵犯您的权益,请联系客服反馈,我们会尽快为您处理(人工客服工作时间:9:00-18:30)。
制动器的设计计算3.1制动蹄摩擦面的压力分布规律从前面的分析可知,制动器摩擦材料的摩擦系数及所产生的摩擦力对制动器因数有很大影响。
掌握制动蹄摩擦面上的压力分布规律,有助于正确分析制动器因数。
在理论上对制动蹄摩擦面的压力分布规律作研究时,通常作如下一些假定:(1)制动鼓、蹄为绝对刚性;(2)在外力作用下,变形仅发生在摩擦衬片上; (3)压力与变形符合虎克定律。
1.对于绕支承销转动的制动蹄如图29所示,制动蹄在张开力P 作用下绕支承销O '点转动张开,设其转角为θ∆,则蹄片上某任意点A 的位移AB 为AB =A O '·θ∆由于制动鼓刚性对制动蹄运动的限制,则其径向位移分量将受压缩,径向压缩为AC AC =AB COS β 即 AC =A O 'θ∆COS β 从图29中的几何关系可看到A O 'COS β=D O '=O O 'Sin ϕ AC =O O 'Sin ϕθ∆⋅因为θ∆⋅'O O 为常量,单位压力和变形成正比,所以蹄片上任意一点压力可写成 q=q 0Sin ϕ (36)亦即,制动器蹄片上压力呈正弦分布,其最大压力作用在与O O '连线呈90°的径向线上。
2.浮式蹄在一般情况下,若浮式蹄的端部支承在斜支座面上,如图30所示,则由于蹄片端部将沿支承面作滚动或滑动,它具有两个自由度运动,而绕支承销转动的蹄片只有一个自由度的运动,因此,其压力分布状况和绕支承销转动的情况有所区别。
现分析浮式蹄上任意一点A 的运动情况。
今设定蹄片和支座面之间摩擦足够大,制动蹄在张开力作用下,蹄片将沿斜支座面上作滚动,设Q 为其蹄片端部圆弧面之圆心,则蹄片上任意一点A 的运动可以看成绕Q 作相对转动和跟随Q 作移动。
这样A 点位移由两部分合成:相对运动位移AB 和牵连运动位移BC ,它们各自径向位移分量之和为AD (见图30)。
AD =AB COS β+BC COS(ϕ-α) 根据几何关系可得出AD=(θ∆·OQ +BC Sin α) Sin ϕ+BC COS αCOS ϕ式中θ∆为蹄片端部圆弧面绕其圆心的相对转角。
令 θ∆·OQ +BC Sin ϕ=C 1BC COS α=C 2在一定转角θ∆时,1C 和2C 都是常量。
同样,认为A 点的径向变形量AD 和压力成正比。
这样,蹄片上任意点A 处的压力可写成q=q 1Sin ϕ+q 2COS ϕ 或 q=q 0Sin(ϕ+ϕ0)也就是说,浮式蹄支承在任意斜支座面上时,其理论压力分布规律仍为正弦分布,但其最大压力点在何处,难以判断。
上述分析对于新的摩擦衬片是合理的,但制动器在使用过程中摩擦衬片有磨损,摩擦衬片在磨损的状况下,压力分布又应如何呢?按照理论分析,如果知道摩擦衬片的磨损特性,也可确定摩擦衬片磨损后的压力分布规律。
根据国外资料,对于摩擦片磨损具有如下关系式fqv K W 11=式中 W 1——磨损量;K 1——磨损常数;f——摩擦系数;q ——单位压力;v ——磨擦衬片与制动鼓之间的相对滑动速度。
通过分析计算所得压力分布规律如图31所示。
图中表明在第11次制动后形成的单位 面积压力仍为正弦分布αsin 132=q 。
如果摩擦衬片磨损有如下关系:2222v fq K W = 式中 2K ——磨损常数。
则其磨损后的压力分布规律为αsin C q =(C也为一常数)。
结果亦示于图31。
应该指出,由上述理论分析所获得的结果与实际情况比较相近,也就是说,用上述压力分布规律计算所得的摩擦力矩与实际使用中所得摩擦力矩有极大的相关性。
以前有人认为制动摩擦衬片压力分布均匀的设想并不合理。
3.2制动器因数及摩擦力矩分析计算 如前所述,通常先通过对制动器摩擦力矩计算的分析,再根据其计算式由定义得出制动器因数BF 的表达式。
现以鼓式制动器中制动蹄只具有一个自由度运动为例,说明用解析法导出制动器因数的思路过程:(1)定出制动器基本结构尺寸、摩擦片包角及其位置布置参数,并规定制动鼓旋转方向; (2)参见3.1节确定制动蹄摩擦片压力分布规律,令q=q 0Sin ϕ;(3)在张开力P 作用下,确定最大压力0q 值。
参见图32,δϕ所对应的圆弧,圆弧面上的半径方向作用的正压力为ϕqRd ,摩擦力为ϕfqRd 。
把所有的作用力对O '点取矩,可得ph=⎰210ϕϕq RMsin 2ϕd ϕ-⎰21ϕϕfq R(R-Mcos ϕ)sin ϕd ϕ据此方程式可求出0q 的值;(4)计算沿摩擦片全长总的摩擦力矩 T f =⎰21ϕϕfq R 2 sin ϕd ϕ=0fq R 2(cos 1ϕ-cos 2ϕ)(5)由公式(28)导出制动器因数。
由于导出过程的繁琐,特别是浮式蹄,因此这里仅将常用各类制动器因数的计算式列出供参考。
1.支承销式领—从蹄制动器 单个领蹄的制动蹄因数BF Tl )(1fB ra A rh fBF T -'= (37)单个从蹄的制动蹄因数BF T2)(2fB ra Arh fBF T +'= (38)上两式中2sin2sin4cos sin 30300a a a A αα-=2cos2cos13ααra B '+=以上各式中有关结构尺寸参数见图33。
整个制动器因数BF 为21T T BF BF BF += 2.支承销式双领蹄制动器12T BF BF = BF Tl 可由式(37)求得。
3.浮式领—从蹄制动器(斜支座面)对于浮式蹄,其蹄片端部支座面法线可与张开力作用线平行(称为平行支座)或 不平行(称为斜支座)。
参见图34。
平行支座可视作斜支座的特例,即图34中︒=0ψ,因此,这里给出最一般的情况。
单个斜支座浮式领蹄制动蹄因数BF T33T BF =)/()(22H f fG F E f fD +-+ (39) 单个斜支座浮式从蹄制动蹄因数BF T44T BF =)/()(22H f fG F E f fD ++- (40) 上两式中()ββsin )/(cos ]///[''r c f r o f r a r c D s s ⋅+⋅++=ββsin )]/(//[cos )/(''r o f r a r c r c f E s s ⋅++-⋅=)]/(/[2/sin 4sin '000r o f r a F s ⋅++=ααα (41)ββsin cos 's f G +=)sin cos ('ββ--=s f F Hψtan '+=s s f fs f 为蹄片端部与支座面间摩擦系数,如为钢对钢则s f =0.2~0.3。
β角正负号取值按下列规则确定:当2/0αγ>,β为正;2/0αγ<,β为负。
这样浮式领从制动器因数为43T T BF BF BF += 4.浮式双领蹄(斜支座面)制动器32T BF BF = 3T BF 可按式(39)计算 5.浮式双增力蹄制动器浮式双增力蹄,其结构布置为:支座面都不倾斜,属平行支座,即︒=0ψ。
参见图35。
此时,s s f f ='。
其制动器因数为53T T BF BF BF +=BF T3可按式(39)计算,而 )/)()((3225a r BF ac H f fG F E f fD BF T T ⋅++-+= (42)上式中有关D ,E ,F ,G ,H 各值可按式(41)计算,但s s f f ='。
6.支承销双增力蹄制动器 其结构图如图36所示。
可以看出其第一蹄片相当于平行支座浮式蹄,第二蹄片为绕支承销转动的蹄。
其总的制动器因数按照定义写成如下形式:)/)(/(///2121p F F F P F p F P F BF ax ax d d d d +=+=按照上述分析,P F d /1可按式(39)计算,而ax d F F /2可按式(37)计算,p F ax /可按下式计算,即)/)(/(//1a r P F a c P F d ax +=7.固定凸轮式(S 形凸轮)气制动器固定凸轮式气制动器结构上属绕支承销式领—从蹄制动器,因其凸轮只能绕固定轴转动,作用于领蹄和从蹄上的张开力户不等,使得领蹄的效能有点下降,而从蹄的效能略有增加。
这样,固定凸轮式气制动器的总的平均制动器因数可由下式来计算: 21214T T T T BF BF BF BF BF +⋅=式中的BF T1可由式(37)来计算,BF T2可由式(38)来计算。
8.楔式气制动器楔式气制动器从结构原理上属浮式蹄。
单气室楔式制动器可认为是浮式领从蹄制动器,双气室楔式制动器则是浮式双领蹄制动器,它们各自的制动器因数,可根据前面有关公式计算。
有关制动器摩擦力矩的计算,则可根据各制动器之制动器因数再按式(28)计算。
3.3制动蹄上的压力分布规律与制动力矩的简化计算 1.沿蹄片长度方向的45压力分布规律用解析方法计算沿蹄片长度方向的压力分布规律比较困难,因为除了摩擦衬片有弹性容易变形外,制动鼓、制动蹄以及支承也都有弹性变形。
通常在近似计算中只考虑衬片径向变形的影响,其他零件变形的影响较小,可以忽略不计。
制动蹄可设计成一个自由度和两个自由度的(见图37)形式。
首先计算有两个自由度的增势蹄摩擦衬片的径向变形规律。
为此,取制动鼓中心O 点为坐标原点,如图37所示,并让y 1坐标轴通过制动蹄的瞬时转动中心A 1点。
制动时,由于摩擦衬片变形,制动蹄在绕瞬时转动中心A 1转动的同时,还顺着摩擦力作用方向沿支承面移动。
结果使制动蹄中心位于1O 点,因而可以想象未变形的摩擦衬片的表面轮廓(EE l 线)就沿1OO 方向移人制动鼓体内。
显然,衬片表面上所有点在这个方向上的变形是相同的。
例如,位于半径1OB ,上的任意点1B 的变形就是'11B B 线段。
因此,对于该点的径向变形为1'11111cos ψ≈=B B C B δ由于 90)(111-+=ψαϕ 和 max 11'11δ==OO B B于是得到增势蹄的径向变形1δ和压力1q 为 )sin(11max 11ϕαδδ+≈)sin(11max 1ϕα+=q q (43)式中 1α——任意半径1OB 和1y 轴之间的夹角; 1ϕ——最大压力线1OO 与1x 轴之间的夹角; 1ψ——半径1OB 和1OO 线之间的夹角。
下面再计算有一个自由度的增势蹄摩擦衬片的径向变形规律。
此时摩擦衬片在张开力和摩擦力的作用下,绕支承销中心A 1转动γd 角(见图37(b))。
摩擦衬片表面任意点1B 沿制动蹄转动的切线方向的变形即为线段'11B B ,其径向变形分量是线段'11B B ,在半径1OB 延长线上的投影,即线段1BB 。