西门子S7200PLC在冲床送料及加工中的应用
基于S7-200PLC的物料输送线控制系统设计毕业论文
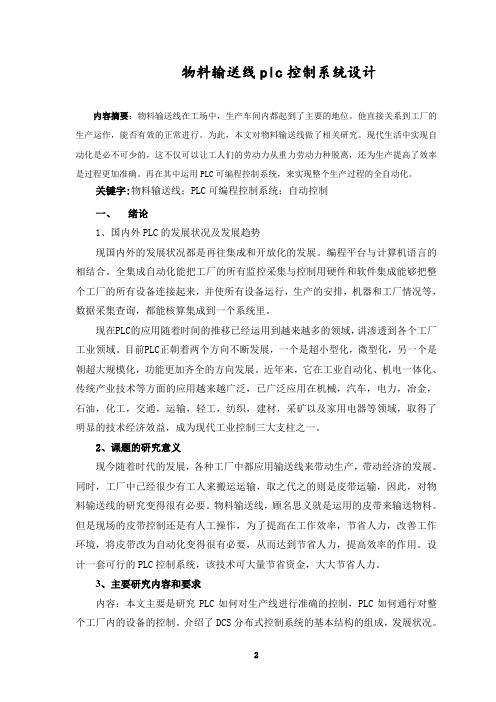
物料输送线plc控制系统设计内容摘要:物料输送线在工场中,生产车间内都起到了主要的地位。
他直接关系到工厂的生产运作,能否有效的正常进行。
为此,本文对物料输送线做了相关研究。
现代生活中实现自动化是必不可少的,这不仅可以让工人们的劳动力从重力劳动力种脱离,还为生产提高了效率是过程更加准确。
再在其中运用PLC可编程控制系统,来实现整个生产过程的全自动化。
关键字:物料输送线;PLC可编程控制系统;自动控制一、绪论1、国内外PLC的发展状况及发展趋势现国内外的发展状况都是再往集成和开放化的发展。
编程平台与计算机语言的相结合。
全集成自动化能把工厂的所有监控采集与控制用硬件和软件集成能够把整个工厂的所有设备连接起来,并使所有设备运行,生产的安排,机器和工厂情况等,数据采集查询,都能核算集成到一个系统里。
现在PLC的应用随着时间的推移已经运用到越来越多的领域,讲渗透到各个工厂工业领域。
目前PLC正朝着两个方向不断发展,一个是超小型化,微型化,另一个是朝超大规模化,功能更加齐全的方向发展。
近年来,它在工业自动化、机电一体化、传统产业技术等方面的应用越来越广泛,已广泛应用在机械,汽车,电力,冶金,石油,化工,交通,运输,轻工,纺织,建材,采矿以及家用电器等领域,取得了明显的技术经济效益,成为现代工业控制三大支柱之一。
2、课题的研究意义现今随着时代的发展,各种工厂中都应用输送线来带动生产,带动经济的发展。
同时,工厂中已经很少有工人来搬运运输,取之代之的则是皮带运输,因此,对物料输送线的研究变得很有必要。
物料输送线,顾名思义就是运用的皮带来输送物料。
但是现场的皮带控制还是有人工操作,为了提高在工作效率,节省人力,改善工作环境,将皮带改为自动化变得很有必要,从而达到节省人力,提高效率的作用。
设计一套可行的PLC控制系统,该技术可大量节省资金,大大节省人力。
3、主要研究内容和要求内容:本文主要是研究PLC如何对生产线进行准确的控制,PLC如何通行对整个工厂内的设备的控制。
西门子S7-200PLC在自动称重混料系统中的应用
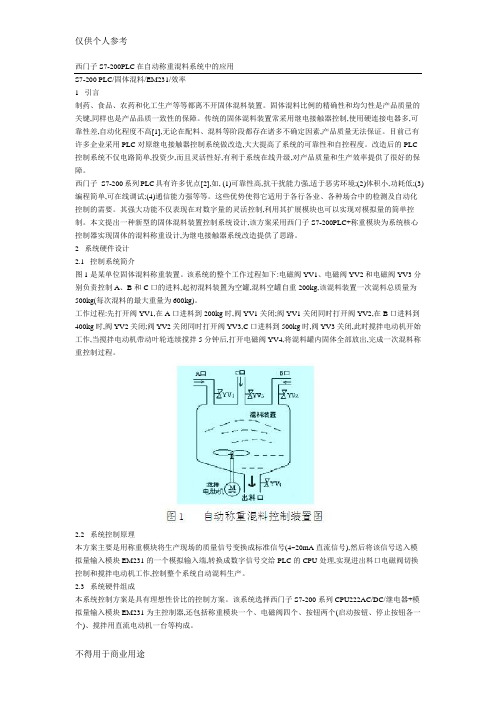
西门子S7-200PLC在自动称重混料系统中的应用S7-200 PLC/固体混料/EM231/效率1 引言制药、食品、农药和化工生产等等都离不开固体混料装置。
固体混料比例的精确性和均匀性是产品质量的关键,同样也是产品品质一致性的保障。
传统的固体混料装置常采用继电接触器控制,使用硬连接电器多,可靠性差,自动化程度不高[1],无论在配料、混料等阶段都存在诸多不确定因素,产品质量无法保证。
目前已有许多企业采用PLC对原继电接触器控制系统做改造,大大提高了系统的可靠性和自控程度。
改造后的PLC 控制系统不仅电路简单,投资少,而且灵活性好,有利于系统在线升级,对产品质量和生产效率提供了很好的保障。
西门子S7-200系列PLC具有许多优点[2],如, (1)可靠性高,抗干扰能力强,适于恶劣环境;(2)体积小,功耗低;(3)编程简单,可在线调试;(4)通信能力强等等。
这些优势使得它适用于各行各业、各种场合中的检测及自动化控制的需要。
其强大功能不仅表现在对数字量的灵活控制,利用其扩展模块也可以实现对模拟量的简单控制。
本文提出一种新型的固体混料装置控制系统设计,该方案采用西门子S7-200PLC+称重模块为系统核心控制器实现固体的混料称重设计,为继电接触器系统改造提供了思路。
2 系统硬件设计2.1 控制系统简介图1是某单位固体混料称重装置。
该系统的整个工作过程如下:电磁阀YV1、电磁阀YV2和电磁阀YV3分别负责控制A、B和C口的进料,起初混料装置为空罐,混料空罐自重200kg,该混料装置一次混料总质量为500kg(每次混料的最大重量为600kg)。
工作过程:先打开阀YV1,在A口进料到200kg时,阀YV1关闭;阀YV1关闭同时打开阀YV2,在B口进料到400kg时,阀YV2关闭;阀YV2关闭同时打开阀YV3,C口进料到500kg时,阀YV3关闭,此时搅拌电动机开始工作,当搅拌电动机带动叶轮连续搅拌5分钟后,打开电磁阀YV4,将混料罐内固体全部放出,完成一次混料称重控制过程。
基于PLC和步进电机的冲床自动送料系统研究.doc

基于PLC和步进电机的冲床自动送料系统研究作者所在地为我国轴承保持器架、平垫生产基地之一,冲床被大量的使用,但自动化水平较低,操作工人劳动强度大、生产效率低。
操作工人手持铁板反复移动到冲压刀具的正下方,由刀具切下一个个圆环或特制形状的铁片。
实际工作中由于铁板较重而且工人长期保持一个姿势,生产效率低且容易患上职业病。
若实现自动送料则操作工人只需更换整块铁板,加工过程中铁板的移位由机器完成,从而可实现生产效率的提高和降低工人劳动强度的双重效益。
如上描述实现自动送料需要设计一套机构夹住铁板并让其在平面(即x轴y轴)上精确移动位置,工人只需等整块铁板加工完毕换上新铁板就可,加工过程无需参与。
如果用单片机来实现该方案,要进行复杂的二次开发,需要设计接口电路、抗干扰电路及驱动电路,软件设计也较复杂。
加之难以形成大批量生产,理论上可行但现实中行不通。
PLC(Programmable Logic Controller)是在顺序控制器和微机控制器的基础上发展起来的新型控制器,它的特点是可靠性高、编程方式简单直观、功能越来越完善,使其在工业控制领域得到广泛的应用。
用PLC 控制步进电机实现定位控制,硬件电路设计简单、方便、快捷,编程语言形象直观,容易掌握。
步进电机又称为脉冲电机,是控制系统中的一种执行元件。
其作用是将脉冲信号变换为相应的角位移或直线位移,即给一个脉冲电信号,电动机就转动一个角度或前进一步。
步进电机的角位移量与脉冲个数严格成正比,转速与脉冲频率成正比,因此只要控制输入脉冲的数量、频率及电动机绕组通电的相序,便可获得所需的转角、转速及转动方向,实现精确定位。
该整套系统成本可控制在五千元左右,易于推广在生产实践中取得了良好的效益。
1、系统硬件设计1.1主控单元本系统选用无锡信捷XC系列的 XC3-32PLC作为主控单元,它有18个输入、14个输出,I/O共计32点。
它具有体积小、功能强、性价比高等优点,而且具有高速脉冲输出功能,可以驱动步进电机实现准确定位任务。
浅析自动送料装车的西门子S7—200系列PLC控制及组态监控

浅析自动送料装车的西门子S7—200系列PLC控制及组态监控作者:杨庆徽来源:《科学与财富》2018年第27期一、基于PLC的自动送料装车系统硬件设计1.1 系统工作原理及控制要求系统工作原理及其控制要求如下。
(1)初始状态。
红灯HL1灭,绿灯HL2亮(表示允许汽车进入车位装料)。
进料阀,出料阀,电动机M1、M2、M3皆为OFF。
(2)进料控制。
料斗中的料不满时,检测开关S为OFF,5s后进料阀打开,开始进料;当料满时,检测开关S为ON,关闭进料阀,停止进料。
图自动送料装车示意图(3)装车控制。
①当汽车到达装车位置时,SQ1为ON,红灯HL1亮、绿灯HL2灭。
同时,起动传送带电动机M3,2s后起动M2,2s后再起动M1,再过2s后打开料斗出料阀,开始装料。
②当汽车装满料时,SQ2为ON,先关闭出料阀,2s后M1停转,又过2s后M2停转,再过2s后M3停转,红灯HL1灭,绿灯HL2亮。
装车完毕,汽车可以开走。
(4)起停控制。
按下起动按钮SB1,系统起动;按下停止按钮“SB2”,系统停止运行。
(5)保护措施。
系统具有必要的电气保护环节。
控制系统要求有全自动功能、半自动功能、回原点和手动功能。
1.2 主电路设计主电路的设计对于本次自动送料装车系统设计相当重要,只有在主电路设计正确且简便的基础上,系统控制电路及软件设计才能精简方便。
根据系统的控制工艺要求,设计的电气控制系统主回路原理图所示。
图中,M1,M2,M3为三台皮带传输送料电动机,交流接触器KM1,KM2,KM3通过控制三台电动机的运行来控制三个传送带,从而进行对物料的传输。
FR1,FR2,FR3为起过载保护作用的热继电器,用于物料传输过程中当传送带过载时断开主电路。
QF1为整台设备的断路器,起到断开接通整台设备电源的作用。
FU1为熔断器,起过电流保护作用1.3 控制电路图220V交流电源经QF1总电源开关,熔断器FU1,接到控制回路断路器QF5,接至直流电源A1输入,经直流电源A1将220V交流电转成24V直流电,供应后续电路使用。
冲床自动送料机的PLC控制

冲床自动送料机的PLC控制作者:周会来源:《卷宗》2015年第12期摘要:本文介绍的冲床与PLC控制自动送料在生产生活中的需要,介绍了PLC自动送料的构成思路,设计要求,编程方法,程序图等。
是一种用于冷挤压套圈类零件的送料机器,是冲床进行技术改造的理想附机。
对自动送料采用了PLC控制系统的设计进行描述,在企业和公司得到广泛的运用,它在社会上有着很高的使用价值。
关键词:冲床;PLC;机械手;自动控制1 引言随着经济的发展国内有的送料机构由冲床工作台通过连杆弹簧驱动滑块在滑道上水平滑动,将斜道上下来的料,通过隔料机构推到模具中心,并联动打板将冲好的料拨掉,往复运动的一整套机构比较简单,无输送机构,联动可靠,制造容易。
但机械手不能将料提升、夹紧,料道倾斜放置靠料自重滑下,如规格重量变动,则料道上工件下滑速度不一致,易产生叠料,推料机构没有将料夹紧,定位不正,废品率较高,使用也不安全。
结合国产冲床工作特点,采用机械手与输送机构配合为主要装置,再配合采用自动卸料安全保护,设计了具有较大应用价值和推广意义的自动送料机。
在社会上有着很大的发展前景。
2 结构设计1、用途:冲床是板料冲压生产的主要设备,可用于冲孔、落料、切边、弯曲、浅拉伸和成形等工序,广泛应用于国防、航空、汽车、拖拉机、电机、电器、仪表、医疗器械、日用五金等行业中。
工作原理:使用机械旋转运动,通过连杆机构传动力,到主轴上使主轴形成向下运动,从而形成冲力,使工件在模具中产生规定的变形而达到加工的。
该送料机主要由机架(包括撑脚、电器箱、角铁架)、输送机(包括电机、变速箱、滚筒、输送带、料台、料道、隔料机构、挡料机构等)、机械手(包括提升缸、夹紧缸、滑板、支架、连杆铰链等)、供油装置(包括油箱、液压泵等)、卸料机构和安全保护装置等部分组成图1。
2、该冲床自动送料机结构图如图1所示。
机架主要连接冲床,装置机械手并使其在一定轨道上滑行,装置输送机构,电气元件。
西门子PLC在高炉上料的应用演示文档

高炉上料系统顺序控制动作流程
初始状态 小车上行,到位停止,延时 两探尺从0下探,下降高度到给定值,炉内缺料 小车下行,到位停止,延时 开均压阀、开大钟,开到位停止,延时 中间仓开 布料槽布料,延时,炉料布完 否 关均压阀、关大钟、到位停止 闸门开到位 是 开小钟,到位停止,延时 延时25S 开报警
目 录
高炉简介 高炉上料的控制方式 系统控制要求 控制方案的选择 PLC控制器选型 料车上料系统 高炉料钟装料系统 探尺系统 高炉上料系统顺序控制动作流程 自动监控系统的程序梯形图 程序功能说明 程序设计仿真
高炉简介
高炉:用于冶炼液态铁水的主要设备,其 横断面一般为圆形的炼铁竖炉,用钢铁作 炉壳,里面砌耐火砖内衬。高炉本体自上 而下分为炉喉、炉身、炉腰、炉腹、炉缸 五部分,护喉之上设置装料设备
探尺系统
高炉在冶炼的过程中,利用探尺探明炉内料面高 低的情况。探尺是一个铸钢圆柱体重锤,由卷扬 机通过钢绳牵引经滑轮和链条将探尺伸入高炉炉 膛内。 值班室根据炉内冶炼要求,例如定出料线2.0米, 即料长下降到2.0米时就要往炉内装料。假如由于 装料机械故障或者其它环节出毛病没有及时装料 而实际料面继续下降,出现“亏料”现象,当实 际料亏低于选择的料线0.5米时发出亏料警告信号, 同时发出闪光信号。
Q0. 5
M1.0 Q0.6 Q1.0 I0.5 M1.1 M1.1 Q0.7 Q1.1 I1.3 Q2.0 T39 Q2.1 Q0.4 M1.2 Q0.5 Q2.3 T33
Q0.5
Q0.7
Q2.1
I1.1
T41
Q0.6 Q1.0
I1.0
I0.6
M1.1
T40
I1.4
Q1.1
Q0.7 Q1.1
基于PLC的冲床自动送料装置控制系统设计
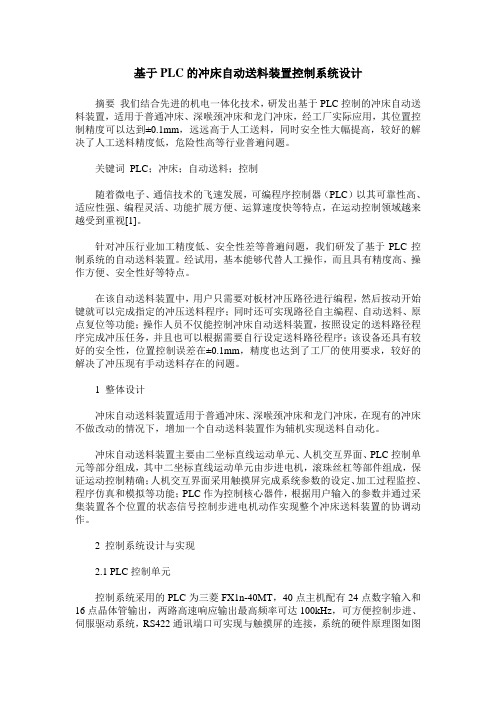
基于PLC的冲床自动送料装置控制系统设计摘要我们结合先进的机电一体化技术,研发出基于PLC控制的冲床自动送料装置,适用于普通冲床、深喉颈冲床和龙门冲床,经工厂实际应用,其位置控制精度可以达到±0.1mm,远远高于人工送料,同时安全性大幅提高,较好的解决了人工送料精度低,危险性高等行业普遍问题。
关键词PLC;冲床;自动送料;控制随着微电子、通信技术的飞速发展,可编程序控制器(PLC)以其可靠性高、适应性强、编程灵活、功能扩展方便、运算速度快等特点,在运动控制领域越来越受到重视[1]。
针对冲压行业加工精度低、安全性差等普遍问题,我们研发了基于PLC控制系统的自动送料装置。
经试用,基本能够代替人工操作,而且具有精度高、操作方便、安全性好等特点。
在该自动送料装置中,用户只需要对板材冲压路径进行编程,然后按动开始键就可以完成指定的冲压送料程序;同时还可实现路径自主编程、自动送料、原点复位等功能;操作人员不仅能控制冲床自动送料装置,按照设定的送料路径程序完成冲压任务,并且也可以根据需要自行设定送料路径程序;该设备还具有较好的安全性,位置控制误差在±0.1mm,精度也达到了工厂的使用要求,较好的解决了冲压现有手动送料存在的问题。
1 整体设计冲床自动送料装置适用于普通冲床、深喉颈冲床和龙门冲床,在现有的冲床不做改动的情况下,增加一个自动送料装置作为辅机实现送料自动化。
冲床自动送料装置主要由二坐标直线运动单元、人机交互界面、PLC控制单元等部分组成,其中二坐标直线运动单元由步进电机,滚珠丝杠等部件组成,保证运动控制精确;人机交互界面采用触摸屏完成系统参数的设定、加工过程监控、程序仿真和模拟等功能;PLC作为控制核心器件,根据用户输入的参数并通过采集装置各个位置的状态信号控制步进电机动作实现整个冲床送料装置的协调动作。
2 控制系统设计与实现2.1 PLC控制单元控制系统采用的PLC为三菱FX1n-40MT,40点主机配有24点数字输入和16点晶体管输出,两路高速响应输出最高频率可达100kHz,可方便控制步进、伺服驱动系统,RS422通讯端口可实现与触摸屏的连接,系统的硬件原理图如图1所示。
S7_200PLC程序的设计举例
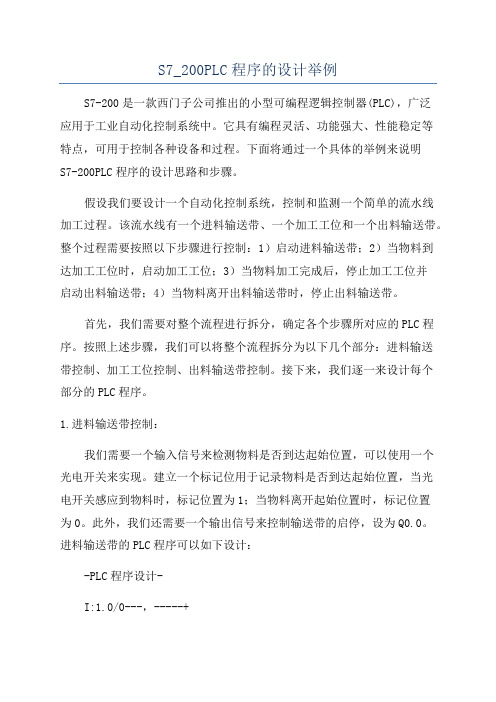
S7_200PLC程序的设计举例S7-200是一款西门子公司推出的小型可编程逻辑控制器(PLC),广泛应用于工业自动化控制系统中。
它具有编程灵活、功能强大、性能稳定等特点,可用于控制各种设备和过程。
下面将通过一个具体的举例来说明S7-200PLC程序的设计思路和步骤。
假设我们要设计一个自动化控制系统,控制和监测一个简单的流水线加工过程。
该流水线有一个进料输送带、一个加工工位和一个出料输送带。
整个过程需要按照以下步骤进行控制:1)启动进料输送带;2)当物料到达加工工位时,启动加工工位;3)当物料加工完成后,停止加工工位并启动出料输送带;4)当物料离开出料输送带时,停止出料输送带。
首先,我们需要对整个流程进行拆分,确定各个步骤所对应的PLC程序。
按照上述步骤,我们可以将整个流程拆分为以下几个部分:进料输送带控制、加工工位控制、出料输送带控制。
接下来,我们逐一来设计每个部分的PLC程序。
1.进料输送带控制:我们需要一个输入信号来检测物料是否到达起始位置,可以使用一个光电开关来实现。
建立一个标记位用于记录物料是否到达起始位置,当光电开关感应到物料时,标记位置为1;当物料离开起始位置时,标记位置为0。
此外,我们还需要一个输出信号来控制输送带的启停,设为Q0.0。
进料输送带的PLC程序可以如下设计:-PLC程序设计-I:1.0/0---,-----+当输入I:1.0/0检测到物料到达起始位置时,输出O:0.0/0为1,启动输送带;当检测到物料离开起始位置时,输出O:0.0/0为0,停止输送带。
2.加工工位控制:加工工位需要一个输入信号来检测物料是否到达工位,同样可以使用光电开关来实现。
建立一个标记位用于记录物料是否到达工位,当光电开关感应到物料时,标记位置为1;当物料离开工位时,标记位置为0。
此外,我们还需要一个输出信号来控制工位的启停,设为Q0.1、加工工位的PLC程序可以如下设计:-PLC程序设计-I:1.0/1---,-----+O:0.1/0---+-----+-()当输入I:1.0/1检测到物料到达工位时,输出O:0.1/0为1,启动工位;当检测到物料离开工位时,输出O:0.1/0为0,停止工位。