固定床反应器在化工生产中的应用综述
固定床反应器压降实验报告

固定床反应器压降实验报告
实验目的:通过对固定床反应器中的流体压降进行实验研究,了解固定床反应器的流体流动规律,掌握固定床反应器的压降特性。
实验原理:固定床反应器是一种常用的化工反应器,其反应物在固定床内进行化学反应。
在反应过程中,反应物要通过固定床,因此固定床内的流体流动和压降特性对反应的影响非常大。
实验中,我们通过在固定床中流动不同的流体,在不同的反应条件下测量流体的压降,从而研究固定床反应器中流体的流动规律和压降特性。
实验步骤:首先,准备好实验所需的设备和材料,包括固定床反应器、流量计、压力计、实验管道等。
然后,按照实验要求进行实验操作,即在不同的反应条件下,通过固定床反应器中流动不同的流体,分别测量其压降,记录实验数据。
最后,根据实验数据,进行数据分析和处理,得到固定床反应器中流体的流动规律和压降特性。
实验结果:通过实验,我们得到了固定床反应器中不同流体在不同反应条件下的压降数据,得出了固定床反应器中流体的流动规律和压降特性。
实验结果表明,固定床反应器中流体的流动规律和压降特性与反应条件、流体性质等因素密切相关,需要根据具体情况进行调整和优化,以提高反应效率和经济效益。
结论:通过本次实验,我们深入了解了固定床反应器的流体流动规律和压降特性,掌握了固定床反应器的实验操作方法和数据处理技巧,为今后进行化工反应器的设计和优化提供了参考。
- 1 -。
化工生产中常见反应器
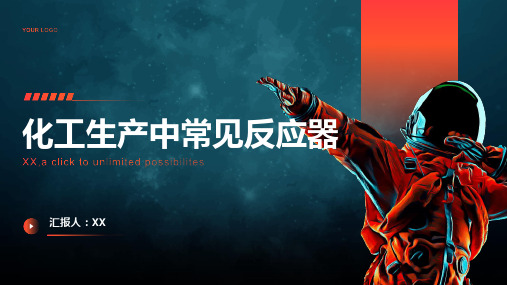
操作简便,易于控 制
广泛应用于化工、 制药等领域
流化床反应器的应用
流化床反应器在化工生产中主要用 于实现固体催化剂与液体原料的接 触和反应
在石油工业中,流化床反应器主要 用于烃类裂化反应,生产高质量的 汽油和柴油等产品
添加标题
添加标题
添加标题
添加标题
流化床反应器具有高效、节能、环 保等优点,广泛应用于石油、化工、 制药等领域
流化床反应器具有较好的混合效果, 能够使物料在反应器内均匀混合, 提高反应效率。
添加标题
添加标题
添加标题
添加标题
流化床反应器具有较高的传热效率, 能够实现快速反应和高效能量利用。
流化床反应器易于实现连续化、规 模化生产,能够提高生产效率和降 低生产成本。
反应器的应用
釜式反应器的应用
适用于多种化工生产过程,如聚合、缩合、烷基化等 可用于高温、高压、高粘度、高流速的化工生产环境 适用于大规模生产,能够提高生产效率和降低成本 操作简单,易于控制,能够实现自动化生产
管式反应器的应用
适用于高温、高压和高流速的反应 适用于大规模生产,产量高 适用于多种反应类型,如放热、吸热、气体和液体的反应 适用于高粘度、高固体含量的反应
塔式反应器的应用
适用于大规 模生产
分离和提纯 效果好
可用于多种 化学反应
操作简便, 易于控制
固定床反应器的应用
适用于大规模生产
可用于多种化学反 应
THANK YOU
汇报人:XX
特点:管式反应器通常由一组直管组成,反应物料在管内流动,通 过加热或冷却外部管壁实现温度控制。
应用范围:管式反应器广泛应用于石油、化工、制药等领域,适用 于气相、液相或固液混合相的反应。
固定床反应器名词解释

固定床反应器1. 定义固定床反应器是一种常见的化学反应器,用于进行气体相或液体相的催化反应。
它由一个固定的反应床和进料和出料设备组成。
在固定床反应器中,催化剂通常以颗粒或块状填充在反应床中,进料通过固定床内流动,与催化剂发生反应,并最终得到产品。
2. 结构固定床反应器通常由以下几个主要部分组成:•反应器壳体:通常由金属或合金制成,具有足够的强度和耐腐蚀性能,以承受高温高压下的工作条件。
•反应床:位于壳体内部,用于填充催化剂和提供充分的接触面积。
催化剂可以是颗粒状、块状或其他形式。
•进料装置:用于将原料引入反应床中。
通常包括进料管道、阀门和喷嘴等。
•出料装置:用于将产物从反应床中取出。
通常包括出料管道、阀门和收集装置等。
•加热或冷却装置:用于控制反应器的温度,以保持反应的适宜条件。
•压力控制装置:用于控制反应器内部的压力,以保证安全运行。
3. 工作原理固定床反应器的工作原理可以简单描述为以下几个步骤:1.进料:原料通过进料装置引入反应床中。
进料可以是气体相、液体相或两相混合物。
2.反应:进料与催化剂在反应床中接触,发生化学反应。
催化剂提供了活性位点,促进了反应的进行。
3.产物生成:经过一定时间的反应,原料转化为产物。
产物随着流体经过固定床而逐渐形成。
4.出料:产物通过出料装置从固定床中取出,并送入下游处理单元进行分离和纯化。
5.催化剂再生:在一些催化反应中,催化剂会逐渐失活。
此时需要对催化剂进行再生或更换。
4. 特点和优势固定床反应器具有以下特点和优势:•高效性:由于固定床中填充了催化剂,反应物与催化剂之间的接触面积大,反应效率高。
•稳定性:固定床反应器在运行过程中,催化剂相对稳定地停留在床层中,不易流失和损坏。
•可控性:通过控制进料速率、温度和压力等参数,可以实现对反应过程的精确控制。
•适用性广:固定床反应器适用于多种气相和液相反应,可用于生产各种化学品和燃料等。
5. 应用领域固定床反应器广泛应用于工业生产和实验室研究中。
固定床反应器的设计计算

固定床反应器的设计计算固定床反应器是一种广泛应用于化工工业中的反应器。
它由一个固定的反应床和气体或液体通过床体流动的装置组成。
固定床反应器通常用于进行催化反应,例如催化剂的制备、氢气的生成以及石油炼制过程中的裂化反应等。
在设计固定床反应器时,需要考虑反应床的尺寸、催化剂的选择、反应温度和压力等因素。
下面将介绍固定床反应器的设计计算流程。
首先,设计固定床反应器时需要确定反应物的种类和摩尔比。
通过摩尔比可以计算出反应物的总流量以及各个组分的摩尔流量。
接下来,需要考虑反应床的尺寸和形状。
反应床通常为一根或多根管子,可以是圆柱形、方形或其他形状。
根据反应床的形状和尺寸,可以计算出反应床的体积。
在确定了反应床的尺寸后,需要选择合适的催化剂。
催化剂的选择应考虑反应的速率和选择性。
常见的催化剂有金属催化剂、氧化物催化剂和酸碱催化剂等。
选择催化剂后,需要计算催化剂的质量和体积。
在反应过程中,需要控制反应温度和压力。
反应温度对于反应速率和选择性具有重要影响。
根据反应的热力学数据和催化剂的性质,可以计算出反应的热效应和放热量。
根据反应的放热量和反应床的热传导性能,可以计算出反应床的冷却要求。
在设计固定床反应器时,还需要考虑反应物和产物的流动情况。
根据流动特性可以计算出反应床的压降和流速。
压降对于反应过程有重要影响,它影响着反应物在床体中的停留时间和反应速率。
最后,需要考虑反应物的进料方式和产物的排放方式。
进料和排放方式应选择合适的装置,以保证反应物的均匀分布和产物的高效排放。
在设计固定床反应器时,需要综合考虑以上因素,并进行相应的计算。
通过计算可以确定反应床的尺寸和形状、催化剂的选择、反应温度和压力以及进料和排放方式。
这些计算可以保证固定床反应器的高效运行和最佳性能。
总结起来,设计固定床反应器需要考虑反应物的种类和摩尔比、反应床的尺寸和形状、催化剂的选择、反应温度和压力、反应床的冷却要求、反应物和产物的流动情况以及进料和排放方式等因素。
固定床反应器的详细介绍
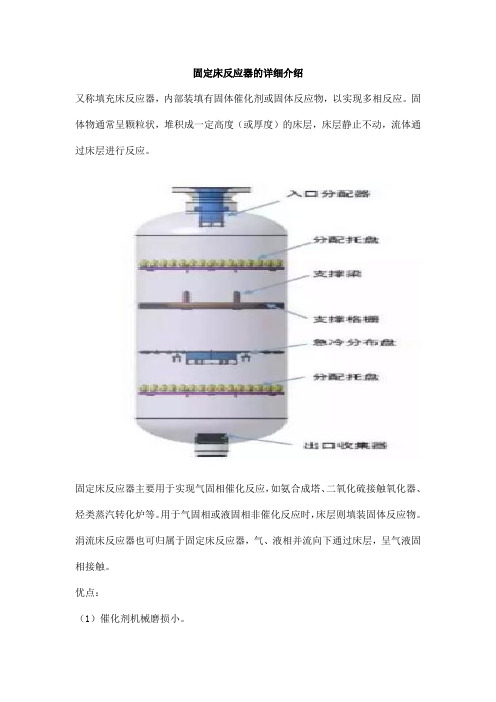
固定床反应器的详细介绍又称填充床反应器,内部装填有固体催化剂或固体反应物,以实现多相反应。
固体物通常呈颗粒状,堆积成一定高度(或厚度)的床层,床层静止不动,流体通过床层进行反应。
固定床反应器主要用于实现气固相催化反应,如氨合成塔、二氧化硫接触氧化器、烃类蒸汽转化炉等。
用于气固相或液固相非催化反应时,床层则填装固体反应物。
涓流床反应器也可归属于固定床反应器,气、液相并流向下通过床层,呈气液固相接触。
优点:(1)催化剂机械磨损小。
(2)床层内流体的流动接近于平推流,与返混式的反应器相比,可用较少量的催化剂和较小的反应器容积来获得较大的生产能力。
(3)由于停留时间可以严格控制,温度分布可以适当调节,因此特别有利于达到高的选择性和转化率。
(4)可在高温高压下操作。
缺点:(1)固定床中的传热较差。
(2)催化剂的再生、更换均不方便,催化剂的更换必须停产进行。
(3)不能使用细粒催化剂,但固定床反应器中的催化剂不限于颗粒状,网状催化剂早已应用于工业上。
目前,蜂窝状、纤维状催化剂也已被广泛使用。
固定床反应器的分类(一)按传热方式分类1、绝热式反应器绝热式固定床催化反应器在反应过程中,床层不与外界进行热量交换。
其最外层为隔热材料层(耐火砖、矿渣棉、玻璃纤维等),常称作保温层,作用是防止热量的传出或传入,减少能量损失,维持一定的操作条件并起到安全防护的作用。
绝热式反应器可分为单段绝热式反应器和多段绝热式反应器。
(1)单段绝热式反应器一般为高径比不大的圆筒体,结构简单,生产能力大,但反应过程中温度变化较大。
适合的反应:①反应热效应较小的反应。
②温度对目的产物收率影响不大的反应。
③虽然反应热效应大,但单程转化率较低的反应或者有大量惰性物料存在,使反应过程中温升小的反应。
(2)多段绝热式反应器催化剂床层的温度波动较小,但结构比较复杂,催化剂装卸困难。
多段绝热反应器按段间换热方式的不同可分为三类:①间接换热式②原料气冷激式③非原料气冷激式2、换热式反应器当反应热效应较大时,为了维持适宜的温度条件,必须利用换热介质来移走或供给热量。
固定床、流化床、移动床、浆态床比较

四种反应器形式比较一、固定床反应器(一)概念凡是流体通过不动的固体物料形成的床层面进行反应的设备都称为固定床反应器。
而其中尤以利用气态的反应物料,通过由固体催化剂所构成的床层进行反应的气固相催化反应器在化工生产中应用最为广泛。
例如石油炼制工业中的加氢裂化、歧化、异构化、加氢精制等;无机化学工业中的合成氨、硫酸、天然气转化等;有机化学工业中的乙烯氧化制环氧乙烷、乙烯水合制乙醇、乙苯脱氧制苯乙烯、苯加氢制环己烷等。
(二)特点结构简单、操作稳定、便于控制、易实现大型化和连续化生产等优点,是现代化工和反应中应用很广泛的反应器。
1、优点主要表现在以下几个方面:1)在生产操作中,除床层极薄和气体流速很低的特殊情况外,床层内气体的流动皆可看成是理想置换流动,因此在化学反应速度较快,在完成同样生产能力时,所需要的催化剂用量和反应器体积较小。
2)气体停留时间可以严格控制,温度分布可以调节,因而有利于提高化学反应的转化率和选择性。
3)催化剂不易磨损,可以较长时间连续使用。
4)适宜于高温高压条件下操作。
2、由于固体催化剂在床层中静止不动,相应地产生一些缺点:1)催化剂载体往往导热性不良,气体流速受压降限制又不能太大,导致床层中传热性能较差,也给温度控制带来困难。
对于放热反应,在换热式反应器的入口处,因为反应物浓度较高,反应速度较快,放出的热量往往来不及移走,而使物料温度升高,这又促使反应以更快的速度进行,放出更多的热量,物料温度继续升高,直到反应物浓度降低,反应速度减慢,传热速度超过了反应速度时,温度才逐渐下降。
所以在放热反应时,通常在换热式反应器的轴向存在一个最高的温度点,称为“热点”。
如设计或操作不当,则在强放热反应时,床内热点温度会超过工艺允许的最高温度,甚至失去控制而出现“飞温”。
此时,对反应的选择性、催化剂的活性和寿命、设备的强度等均极不利。
2)不能使用细粒催化剂,否则流体阻力增大,破坏了正常操作,所以催化剂的活性内表面得不到充分利用。
第六章_固定床反应器的工艺设计

第六章_固定床反应器的工艺设计固定床反应器是一种广泛应用于化工领域的反应设备,其工艺设计的主要目的是在满足反应物转化率和产品选择性的同时,考虑到反应器的稳定性、可操作性和经济性。
本文将从固定床反应器的工艺选择、反应器尺寸设计和操作条件优化三个方面进行详细讨论。
首先,在固定床反应器的工艺选择中,需要考虑反应物质的特性以及反应过程的要求。
例如,对于多相反应系统,可选择固液、固气或固液气等不同形式的反应器。
对于固液反应系统,通常采用固定床(如活性炭床)作为催化剂载体,而对于固气反应系统,常使用填充物(如陶瓷珠)来提供大表面积。
此外,还需要考虑反应物料的物理性质,如粘度、密度和颗粒大小等,以确定反应器的类型和结构。
其次,在固定床反应器尺寸设计中,主要考虑的是反应器的长径比、催化剂的活性、反应器的有效体积等因素。
反应器的长径比是一个重要的设计参数,过大的长径比会导致反应物料的流速过小,影响转化率;过小的长径比则会增加压力损失和催化剂层的温度梯度。
催化剂的活性直接影响反应速率,一般需要选择活性高、稳定性好的催化剂。
反应器的有效体积要足够大,以保证反应物集流时间足够,从而提高转化率。
最后,在操作条件优化方面,需要考虑反应温度、压力和流速等参数。
反应温度会直接影响反应速率和选择性,一般需要根据催化剂的特性和反应动力学进行调整。
反应压力主要考虑固定床压降和反应平衡的影响,需要在考虑反应速率和选择性的同时,保持固定床的稳定性。
流速则涉及反应物料的传质和传热问题,需要通过实验和模拟计算等方法进行优化。
综上所述,在固定床反应器的工艺设计中,需要综合考虑反应物质的特性、反应器尺寸和操作条件等因素,以达到高效、稳定、经济的反应过程。
在实际工程应用中,还需要结合实际生产中的具体要求和限制条件,进行合理的优化设计。
通过合理的工艺设计,可以提高产品的转化率和选择性,降低生产成本,提高生产效益。
固定床反应器在化工生产中的应用综述

常州工程职业技术学院固定床反应器在化工生产中的应用综述胡浩鹏精细1411摘要:固定床反应器又称填充床反应器,装填有固体催化剂或固体用以实现的一种反应器。
在现代生产中固定床反应器开始广泛应用于生产之中,主要用于化工生产、生物科研等。
它与及的区别在于固体颗粒处于静止状态。
固定床反应器主要用于实现气固相,如、二氧化硫接触氧化器、炉等。
关键词:固定床反应器、化工生产引言:近几年以来固定床反应器在化工生产及医药研究的领域里发挥着重大的作用,本文就近年来关于固定床反应器在化工生产和医药研究上作一些论述正文:固定床反应器在化工领域应用十分广泛。
基本有机化工中,乙烯氧化制环氧乙烷、乙苯脱氧制苯乙烯、乙烯水合制乙醇等反应均在固定床反应器中进行。
固定床反应器床层薄,流速低,床层内的流体轴向流动可看作是理想置换流动,因而化学反应速率较快,完成同样的生产任务所需的催化剂用量和反应器体积较小,流体停留时间可严格控制,温度分布可适当调节,有利于提高化学反应的转化率和选择性;固定床中催化剂不易磨损,可在高温高压下操作。
当然,固定床也存在一些缺点,如传热性能差;不能使用细粒催化剂(不能充分利用催化剂内表面),催化剂的再生、更换均不方便。
按照催化剂固定方式的不同,Biardi[1]等将固定床反应器分为传统型与非传统型两种。
传统型固定床是指催化剂以粒子形式进行堆积,主要有并流下行泡沫床和并流上行泡沫床;非传统型固定床是指将催化剂以某种形态负载或固定于某种结构填料上,通常使用Monolith催化剂和Katapak—Sandwich催化剂等。
1:并流下行泡沫床Solvay公司认为当气、液相并流下行时,如果同时成倍地提高工作液和氢气的流量,可以从滴流床过渡到泡沫床。
因为泡沫床的气液接触面积较滴流床有了明显的提高,所以气液相间的传质作用明显增强。
并且,这种改进不需增加辅助设备就可方便地实现。
同时,为了解决快速反应和加压条件下泡沫的淬灭、聚并,以及由此引起的床层压降波动较大、进料难以控制的问题,该专利采用惰性气体(最好是氮气)来稀释氢气,并给出了氮氢最优比。
- 1、下载文档前请自行甄别文档内容的完整性,平台不提供额外的编辑、内容补充、找答案等附加服务。
- 2、"仅部分预览"的文档,不可在线预览部分如存在完整性等问题,可反馈申请退款(可完整预览的文档不适用该条件!)。
- 3、如文档侵犯您的权益,请联系客服反馈,我们会尽快为您处理(人工客服工作时间:9:00-18:30)。
常州工程职业技术学院固定床反应器在化工生产中的应用综述胡浩鹏精细1411摘要:固定床反应器又称填充床反应器,装填有固体催化剂或固体用以实现的一种反应器。
在现代生产中固定床反应器开始广泛应用于生产之中,主要用于化工生产、生物科研等。
它与及的区别在于固体颗粒处于静止状态。
固定床反应器主要用于实现气固相,如、二氧化硫接触氧化器、炉等。
关键词:固定床反应器、化工生产引言:近几年以来固定床反应器在化工生产及医药研究的领域里发挥着重大的作用,本文就近年来关于固定床反应器在化工生产和医药研究上作一些论述正文:固定床反应器在化工领域应用十分广泛。
基本有机化工中,乙烯氧化制环氧乙烷、乙苯脱氧制苯乙烯、乙烯水合制乙醇等反应均在固定床反应器中进行。
固定床反应器床层薄,流速低,床层内的流体轴向流动可看作是理想置换流动,因而化学反应速率较快,完成同样的生产任务所需的催化剂用量和反应器体积较小,流体停留时间可严格控制,温度分布可适当调节,有利于提高化学反应的转化率和选择性;固定床中催化剂不易磨损,可在高温高压下操作。
当然,固定床也存在一些缺点,如传热性能差;不能使用细粒催化剂(不能充分利用催化剂内表面),催化剂的再生、更换均不方便。
按照催化剂固定方式的不同,Biardi[1]等将固定床反应器分为传统型与非传统型两种。
传统型固定床是指催化剂以粒子形式进行堆积,主要有并流下行泡沫床和并流上行泡沫床;非传统型固定床是指将催化剂以某种形态负载或固定于某种结构填料上,通常使用Monolith催化剂和Katapak—Sandwich催化剂等。
1:并流下行泡沫床Solvay公司认为当气、液相并流下行时,如果同时成倍地提高工作液和氢气的流量,可以从滴流床过渡到泡沫床。
因为泡沫床的气液接触面积较滴流床有了明显的提高,所以气液相间的传质作用明显增强。
并且,这种改进不需增加辅助设备就可方便地实现。
同时,为了解决快速反应和加压条件下泡沫的淬灭、聚并,以及由此引起的床层压降波动较大、进料难以控制的问题,该专利采用惰性气体(最好是氮气)来稀释氢气,并给出了氮氢最优比。
这样,不仅可以稳定床层压降,还可提高催化剂的选择性。
与之相反的一种称为并流上行泡沫床。
2:并流上行泡沫床Solvay公司采用高1.4 m、直径18 mm的反应器,使用不同粒径的球形Pd —SiO:催化剂,让气液由反应器的底部进料,并流上行,通过调整气液流量比使其达到泡沫状态。
并认为并流上行泡沫床优于并流下行泡沫床,对加氢过程更为有利。
其一,与并流下行泡沫床相比,并流上行泡沫床的床层压降更小,床层稳定性更好;其二,并流上行泡沫床的气液相流速低,甚至可以和液相以化学计量比进料,就町以获取较高的单程加氢效率。
这种方法的缺点是催化剂周围的滞液量较大,加速了催化剂的失活。
还有就是Monolith固定床反应器3:Monolith固定床反应器Monolith固定床反应器是通过利用平行孑L道内载催化剂为固定床,从而达到提高三相接触效率和固定床时空收率,降低床层压降的目的。
当氢气经分布器后形成的气泡直径通常比Monolith固定床的孔道要小。
根据气液流速的变化,两相流的流型有4种,即鼓泡流、Taylor流、环状流和弹状流。
EkaNobel公司建议使Monolith孔道内的流型处Taylor流,此时对反应最为有利。
液相蒽醌工作液从反应器的顶部进料,氢气从反应器的底部进料与液相反应,未反应的部分经外循环去塔顶继续参与反应,使床层压降为零,反应器内的压力接近常数,这对于提高反应的选择性有莺要的作用。
实验证实,与传统工艺相比,该工艺的放大效果很好,工业规模对实验室规模的放大效应远小于传统工艺。
目前,该工艺已被Eka Nobel公司应用到工业生产过氧化氢中,成为Monolith固定床反应器工业化的经典范例。
最后就是Katapak催化反应器4:Katapak催化反应器Katapak是一种用于催化精馏过程的结构填料。
Piironen等率先在蒽醌的加氢过程中应用Katapak填料催化剂。
在这种反应器内气液并流下行进料,与滴流床不同的是液相为连续相,气相为分散相。
无论在流道间还是催化剂层,气液间的有效传质明显增强。
在催化剂层的轴向返混现象较严重,但反应效率较高,并不影响反应器总的性能。
而Frank等建议最好采用并流上行的操作方式。
5:固定床反应器的数学模型由于轴向流固定床反应器中混合气体的流动过程对化学反应过程和反应器的性能有很大影响,因而反应器内部流场的研究和数学模拟对于优化化学反应过程和优化反应器的设计有重要意义。
为了在催化剂床层中实现气体流动速率的均匀分布,陈金娥[2]等旧1对大型轴向流固定床反应器内流场进行数学模拟。
在包含多孔介质区域和无多孔介质的自由空间区域内建立一个统一流场和统一的基本方程组,采用半人工瞬变分方法在半交错不等距非正交曲线贴体混合网格中进行数值计算,给出一个大型轴向流固定床反应器内流场的计算结果。
鲁文质[3]等通过对合成气一步法制二甲醚(DME)反应特点的研究,对固定床反应器用一维模型进行了数学模拟计算,得出如下结论:在25 700 h一空速下,反应器内温度分布较均匀,甲醇合成催化剂活性较低,而甲醇脱水反应进行程度相对较高;在保证反应器热点温度不超过催化剂使用温度时,可通过增大反应管的管径、提高反应压力、降低空速和提高反应气进口温度来促进DME产物生成;反应进口气中应避免含有CO:和H:O,氢碳比小于9时,提高氢碳比对DME 生成有利;提高甲醇合成剂在催化剂中的比例,还可进一步提高催化剂活性;各影响条件对反应结果的影响大小依次为反应压力、空速、催化剂组成、氢碳比、原料气进口温度、CO:和H:o的浓度。
反应压力对DME产率影响较大,空速对反应器热点温度和CO转化率影响较大,催化剂配比对DME选择性影响较大,而氢碳比主要影响CO的转化率。
原料气进口温度、CO:和H:O的浓度对反应结果影响不大。
王志亮[4]等H1建立了轻烃醚化外循环式反应器的拟均相一维模型,考察了催化剂床层分段、各段循环比的变化、外循环段与绝热段结合及原料入口温度对反应器尺寸和床层轴向温度分布的影响。
考察了异丁烯和甲醇在磺酸基团树脂催化剂上生成MTBE的醚化反应,该反应在液相中进行,属于可逆放热反应。
当反应温度高时,除了主反应外还会发生副反应,即混合c。
烃中的正丁烯或/和2一丁烯与甲醇反应生成甲基正丁基醚或/和甲基仲丁基醚,从而影响主产品的质量。
对此类放热反应,如果原料浓度较高致使反应放热量较大时,通常情况下选用外冷列管式反应器或外循环式反应器,两者相比列管式反应器催化剂装填较困难。
外循环式反应器利用大量反应产物的循环移走反应热,降低催化剂床层的热点温度。
通过调整循环比使反应在较低的温度范围内进行,进而提高可逆放热反应的平衡转化率,减少副产物的生成。
通过模拟发现调节循环比和循环方式可有效的解决上述问题,并最终确定了外循环和绝热相结合的方式。
王军等[5.6]对热管式气液固三相固定床鼓泡反应器的传热性能进行了研究。
在一内径50 mill,高800 m/n的床内充以多孔填料,内插一根不锈钢热管,用并流向上的热水和氮气进行传热研究。
热管是一种具有高导热性能的传热元件。
通过实验得到r热管式气液固三相固定床鼓泡反应器的传热能力随气相速率增大而逐步增加的结论;在气相速率达到某一值后,气相速率对传热量影响不大;并采用最小二乘法拟合得到了实验条件下固定床鼓泡反应器床层与热管加热段管壁之间传热系数传热经验关联式,将其用于热模实验,基本能够满足实验要求。
李东风[7]等一1通过建立数学模型,对分子筛催化剂上液相法合成异丙苯装置(100 ka/a)的烃化反应器进行了设计与优化。
他们采用多段绝热床反应器,液相丙烯和苯均可分为多股分别通人各床层底部,循环液也可分为多股通入每一床层。
由于较大的苯烯比可获得较高的选择性和较长的催化剂寿命,采用丙烯分段进料对于烷基化反应有利。
优化的结果表明,烃化反应器宜采用带有外循环的三段绝热固定床反应器,丙烯平均分为3股进料,苯单股进料,循环液全部返回反应器入口,循环量应保证床层内流体流动处于湍流状况。
适宜的操作条件为:温度150~180 oc,压力3.0 MPa,进料苯烯摩尔比6:l,苯空速4 h~,循环比6。
当然还有固定床反应器在一些新领域的应用与发展。
下面讲述一下床反应器在新领域的应用与发展6:新领域的发展刘红[8]等旧1制备了用于固定床反应器的负载型Ts—1分子筛催化剂,并以苯酚羟基化为探针反应研究了载体、钛含量和预处理剂等对负载型TS—1分子筛催化性能的影响,考察了固定床反应器中苯酚羟基化反应的工艺条件,结果表明,酸性较强的载体会加剧H:O:的分解,导致苯酚的转化率和H:O:的有效利用率下降;在所研究的ZSM一5、Ti02、A120,、Zr02、Si02和硅藻土载体中,硅藻土的催化性能最好;催化剂活性与骨架钛含量有关;用HNO,、KAc、NaAc、NH4Ac和NH4CI处理过的催化剂,活性和选择性均提高,而用NH3·H20、Na2C03和Na,PO。
等碱性物质处理后,催化剂活性下降;溶剂、反应温度、原料空速和苯酚与H:O:摩尔比对苯酚羟基化反应有很大影响,以丙酮为溶剂,在苯酚与H20:摩尔比为3、反应温度为84℃、WHSV为8.46h。
的反应条件下,苯酚转化率、H:O:转化率、苯二酚选择性及H:O:的有效利用率分别达27.2%、94.8%、97.7%和75.1%。
曹凯[9]等一1对苯胺催化加氢制环己胺列管式固定床反应器进行优化设计。
建立了苯胺催化加氢制环己胺固定床反应器的二维拟均相模型,并用数值计算软件Mathconnex对模型进行求解,实现了苯胺催化加氢制环己胺列管式固定床反应器的优化设计与操作。
采用二维拟均相模型可有效地描述苯胺催化加氢制环己胺列管式固定床反应器的特征;影响转化率的主要因素是反应器的轴向温度分布,反应器的管径和氢气与苯胺物质的量对反应器轴向温度分布有较大影响,是设计反应器和优化操作的重要参量;根据计算结果设计的反应器在优化条件下操作稳定,能耗降低,热点温度远低于采用导热油冷却的反应器,产品的副产物少,收率可达95%以上,具有较好的经济效益。
邢福祥[10]设计了一种用于气体净化的平板式固定床反应器。
该反应器通过数片内置的装填有固体反应物的网板,在低功率风机作用下完成气固反应和气体吸收,从而达到气体净化和处理的目的。
该平板型固定床反应器具有结构简单、操作方便、床层阻力低、能耗小、净化效率高等优点,可方便地通过抽插网板来更换或再生固体反应物。
由于网板平面平行于气流方向,反应阻力非常小。
应用结果表明,该设备比直筒式反应器的净化效率高20%,用于吸收密闭空间内的酸性气体时,功率消耗较直筒式反应器节省3.8 kWh,特别适合一些受环境条件变化而带来普通反应器床层阻力急剧升高的气固反应过程,值得在一些气体净化崩;湿等领域推广和应用。