减小变速器壳体的应力变形
变速器疲劳强度评估及提高措施
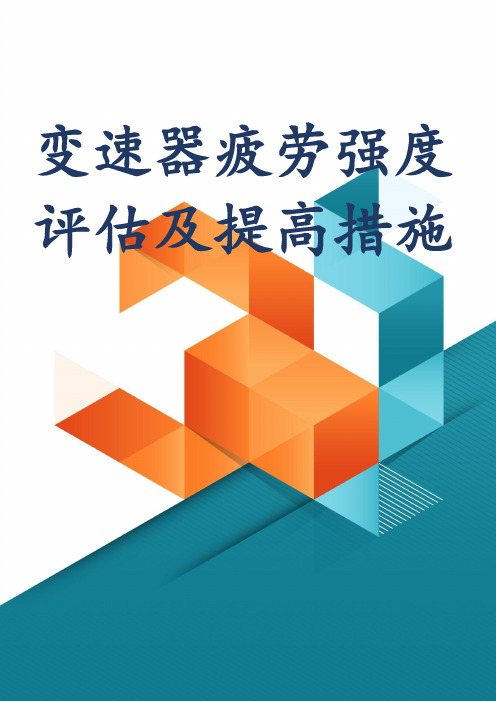
变速器疲劳强度评估及提高措施变速器疲劳强度评估及提高措施变速器是汽车重要的传动装置之一,其疲劳强度评估和提高措施对于保障汽车的可靠性和安全性至关重要。
下面将以逐步思考的方式,分析变速器疲劳强度评估和提高措施。
第一步:了解变速器的工作原理和受力情况首先,我们需要了解变速器的工作原理和受力情况。
变速器主要通过齿轮传动实现不同速度的转换。
在工作过程中,变速器会承受来自发动机的动力输出,并将其传递至车轮。
由于高速运转和长时间使用,变速器会面临较大的疲劳载荷。
第二步:进行变速器疲劳强度评估接下来,我们需要对变速器进行疲劳强度评估。
这可以通过有限元分析等方法来实现。
有限元分析能够对变速器内部各部件的应力分布和变形情况进行模拟,从而得出其疲劳寿命。
通过评估变速器的疲劳强度,我们可以了解其在使用过程中可能出现的问题,并采取相应的措施进行改进。
第三步:优化变速器结构设计根据疲劳强度评估的结果,我们可以对变速器的结构设计进行优化。
通过改变齿轮的材料、减小齿轮的尺寸、增加齿轮的强度等方式,可以提高变速器的疲劳强度。
此外,还可以采用表面强化处理、增加润滑油的冷却效果等手段来提高变速器的疲劳寿命。
第四步:加强制造工艺控制除了优化结构设计,加强制造工艺控制也是提高变速器疲劳强度的重要措施。
在变速器的制造过程中,应严格控制材料的质量,并确保零部件的加工精度和装配质量。
合理的加工和装配工艺能够减小零部件之间的间隙,提高变速器的传动效率和疲劳强度。
第五步:定期检查和维护在变速器投入使用后,定期检查和维护也是确保其疲劳强度的重要手段。
及时更换磨损严重的零部件,保持变速器良好的润滑状态,定期清洗和更换润滑油等,都可以延长变速器的使用寿命,并提高其疲劳强度。
总结:变速器疲劳强度评估和提高措施是确保汽车可靠性和安全性的重要环节。
通过逐步思考,我们可以了解变速器的工作原理和受力情况,进行疲劳强度评估,并根据评估结果优化变速器的结构设计和制造工艺控制。
变速器壳体的检验与修理

变速器壳体的检验与修理摘要变速器壳体是变速器的基础件。
变速器壳体的质量决定着变速器总成的工作性能、换挡灵活性、挡位噪声、密封性能和使用寿命。
本文讲述了变速器壳体在大修时所要进行的检查与修理工作。
关键词变速器壳体检验修理变速器壳体是变速器重要零件之一。
变速器壳体是变速器的基础件,它将变速器中的输入轴总成、输出轴总成、换挡机构总成等零部件,按一定的相互位置关系装配成一个整体,并支撑输出轴按一定的传动比关系输出转矩。
它上面有轴承座孔,承载着变速轴、变速齿轮,如果轴承座孔磨损,将影响变速器的工作。
变速器壳体采用整体式壳体,与上盖成一体,以保证变速器前后轴承孔的同心度。
变速器壳体有足够的刚度,以防止壳体的变形,保证轴和轴承工作时不会倾斜。
另外,壳体上还设有注油孔和放油孔,为了保持变速器内部为大气压力,在顶部开有通气孔,壳体设有动力输出孔、倒挡检查孔。
变速器壳体的质量决定着变速器总成的工作性能、换挡灵活性、挡位噪声、密封性能和使用寿命。
在变速器大修时要对变速器壳体进行如下检查与修理,以保证变速器工作正常。
1. 壳体螺纹孔的检验与修理壳体零件材料因强度较低、长期使用、频繁拆装或紧固不当、局部受力过大等原因,易造成壳体螺纹孔损坏。
变速器壳体螺纹孔损伤有注油螺塞孔、放油螺塞孔的螺纹损伤,以及壳体之间连接螺栓螺纹孔的损伤。
螺纹孔的损坏与滑牙,可采用扩孔攻丝或焊补后重新钻孔攻丝的方法修复。
2. 壳体裂纹的检验与修理变速器壳体不得有裂纹。
壳体裂纹的检验,一般采用磁力探伤机进行,或外部检视与轻轻敲击检验。
对未延伸到轴承座孔处不重要部位的裂纹,可用粘接剂粘接、螺钉填补法修复。
对重要部位的裂纹,则应进行焊接修复。
焊接时,必须先对壳体加温后再焊,防止局部内应力过大而再裂或变形。
如轴承座孔、定位销孔、螺纹孔等重要部位出现裂纹时必须更换壳体。
3.轴承座孔的检验与修理轴承座孔的磨损,将使齿轮轴线偏移和两轴线不平行,会破坏壳体与各轴承的配合关系,直接影响变速器输入、输出轴的相对位置,影响齿轮的正常工作,造成齿轮发响、跳挡等一系列故障。
自动变速器壳体设计及仿真优化
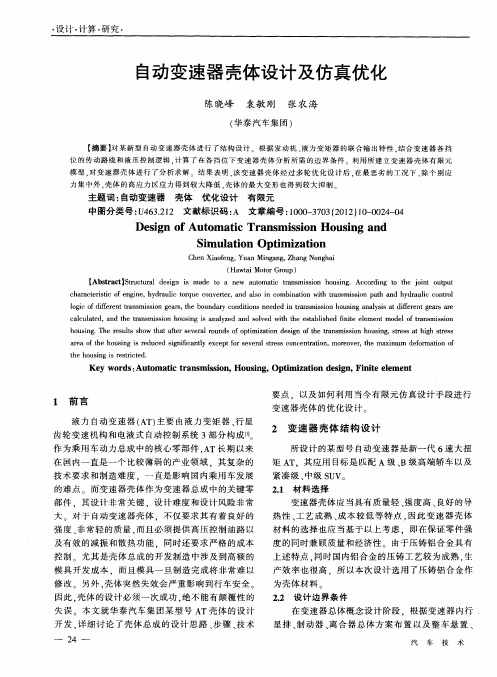
矩A T.其应用 目标 是匹配 A级 、 高端轿 车 以及 B级
c a a t r t fe gn , y r u i t r u o v n r a d a s n c mb n t n wi r n mis n p t n y ru i o to h rc e i i o n i e h d a l o q e c n e e , n lo i o i ai t ta s s i a h a d h d a l c n r l sc c o h o c l gc o i e e tt n miso e r , h o n a y c n i o s n e e n ta s s i n h u i g a ay i a i ee t e r r o i f f r n r s si n g a s t e b u d r o d t n e d d i r n mis o s n lss t f r n a s ae d f a i o n d g c l u ae ,a d t e t n mi in h u i g i n lz d a d s le i h sa l h d f i lme tmo e ft n miso a c lt d n h r s s o o s s a ay e n ov d w t t e e t b i e n t ee n d lo a s s in a s n h s i e r h u i g T e r s l h w t a f rs v r lr u d fo t z t n d sg ft e t n miso o sn ,s e sa ih sr s o sn . h e ut s o h tat e e a o n so p i a i e i n o r s si n h u i g t s thg te s s e mi o h a r a e ft e h u i g i e u e i nf a t x e t o e e a t s o c n r t n mo e v r h xmu d fr t n o r a o o sn sr d c d s i c n l e c p r s v r ls e s c n e t i , ro e ,t e ma i m e o mai f h g i y f r ao o
变速器壳体裂纹改善的研究

变速器壳体裂纹改善的研究欧阳森【摘要】汽车变速器壳体采用铝合金铸造成型,因个体较大,壁厚差异也较大,铸造过程会因各种原因产生裂纹,造成壳体泄漏.根据变速器壳体结构,结合压铸缺陷产生的原因深入分析,重点介绍增加挤压销方法,通过该方法,可以有效解决铸件裂纹缺陷,从而提高变速器壳体的可靠性和密封性.【期刊名称】《汽车工艺与材料》【年(卷),期】2018(000)001【总页数】3页(P46-48)【关键词】铸造;铝合金;挤压销;裂纹【作者】欧阳森【作者单位】湛江德利车辆部件有限公司,湛江 524400【正文语种】中文【中图分类】TG4601 前言由于铝的密度较小,强度比普通钢高而引起广泛的注意,特别是汽车工业和航空航天工业[1],但该材料的使用也容易出现各种缺陷,如欠铸、裂纹等。
裂纹缺陷是指铸件上合金基体被破坏或者断开形成细丝状的缝隙。
作为核心部件的变速器壳体,绝对不能出现裂纹问题,因为在汽车工作时,由于变速器壳体里泡有机油,如有裂纹会出现漏油风险。
裂纹缺陷产生原因很多,如产生于铸件表面的收缩裂纹,铸件在模具中被拉裂产生的裂纹,开模时的机械应力产生的裂纹等,所以要找到裂纹的产生原因需从人、机、料、法寻找末端因素。
2 要因分析裂纹的产生比较复杂,需首先判断是否由最常见的原因引起如收缩裂纹(表面氧化)、缩松裂纹、模具拉裂。
产品曾经出现的裂纹,出现在静模处。
首先从模具温度出发,是否异常产生缩裂,通过热像仪监视模具各个点的温度,观察各数据是否符合工艺要求,如果出现温度过高或过低,则可以通过检查调整冷却水管的措施改变温度,使之达到要求。
在调查后,通过确认模具温度符合要求(表1),结合热像仪反馈测量结果(图1),可以排除模具温度有异常问题,则不针对模具温度展开其他工作,以免浪费时间。
表1 模具温度确认过程确认内容确认方法要求确认结果再针对裂纹产生部位,从模流图(图2)可看出缩裂处是进料末端出现卷气造成补缩不足,把产品裂纹处切开后发现卷气处出现大缩孔(图3),产品外观冷却后表面出现裂纹(图4),用卡尺测量下缩裂处壁厚有30 mm,壁厚是产生缩裂主要原因。
机械零件变形及矫正方法

机械零件变形及矫正方法
机械零件在制造和组装过程中,可能会出现变形的情况。
这些变形会导致零件
的功能和性能受到影响,甚至使整个机械系统无法正常工作。
因此,及时发现和矫正机械零件的变形是非常重要的。
首先,我们需要了解机械零件变形的原因。
机械零件的变形可能是由于材料应力、温度变化、加工误差或装配问题等引起的。
一旦发现机械零件出现变形,我们可以采取以下几种方法进行矫正。
1. 机械矫正:对于小型变形,可以使用机械手工矫正的方法。
通过在变形处施
加适当大小的力或压力,使零件恢复到设计规格。
2. 热处理:对于材料应力引起的变形,可以采用热处理方法。
通过将零件加热
至适当温度,并进行冷却处理,可以消除或减小应力,使零件恢复原状。
3. 水平调整:一些较大的机械零件变形可能需要进行整体调整。
通过在机械系
统中添加补偿件或调整装配结构,可以达到修正变形的目的。
4. 加强设计与制造控制:为了避免机械零件变形的发生,我们需要在设计和制
造过程中注意控制材料的应力分布、温度的影响、加工精度和装配质量等相关因素。
通过优化设计和加强制造过程的质量控制,可以降低机械零件变形的风险。
需要注意的是,在矫正机械零件变形时,我们应根据具体情况选择合适的方法。
对于复杂的机械系统,可能需要专业技术人员进行分析和处理。
同时,我们还应注意不要过度矫正,以免引入新的问题或导致零件损坏。
总之,机械零件的变形对机械系统的性能和可靠性有重要影响。
通过了解变形
原因,并采取合适的矫正方法,我们可以及时修正机械零件的变形,保障机械系统的正常运行。
汽车机械式变速器的可靠性优化设计

汽车机械式变速器的可靠性优化设计摘要:随着我国经济的快速发展,汽车在人们的日常生活中已经被普遍使用,同时对于汽车各个部件的性能要求越来越高。
现在汽车变速器除了有良好的动力性能外,在一定的工作状况下质量要轻、材料要省、体积要小和成本要低,所以轻量化成为评价变速器设计水平的重要指标之一。
对于变速器设计的优化,是在保证部件的刚度和强度合适的条件下,来追求变速器齿轮和轴系质量的最小。
基于此,本文首先对汽车机械变速传动机构可靠性的优化设计的原因进行了概述,详细探讨了机械式变速器可靠性优化设计,旨在进一步提高汽车的使用性能。
关键词:汽车;机械式变速器;可靠性优化设计汽车作为目前我国最重要的交通工具之一,对人们的生活、工作带来了较大的便利。
从汽车采用内燃机作为动力装置以来,变速器成为了汽车传动机构最重要的组成部分。
变速器不仅能改变汽车的传动比,扩大车轮距和转速的范围,还可以使发动机工作在最有利的工况范围内,对汽车整体的结构稳定以及实用性能有着不可或缺的作用。
机械式变速器具有寿命长、稳定性高、成本低等优势,且得到了广泛的应用,但是其也具有体积大、换挡冲击大等劣势,如何改善机械式变速器的结构与使用性能,提高其传动的可靠性,成为了汽车设计人员和技术人员共同关注的热点。
1 进行汽车机械变速传动机构可靠性的优化设计的原因近年来,随着科学技术的发展,汽车工业也得到了空前的发展,私家汽车逐渐走进了中国的千家万户。
正是由于汽车的普遍使用,人们对汽车性能的要求越来越高。
众所周知,汽车的动力装置是以内燃机为主,而变速器是汽车传动系统不可或缺的一部分,对汽车性能有着至关重要的影响。
汽车变速器主要有以下作用:经过科学地计算与理论分析,来适当地改变汽车的传动比,使发动机处于最好的工作范围内;实现减速,让动力系统停止工作;在发动机旋转方向不变的基础上,实现汽车的倒退行驶功能。
合理地优化设计变速器可以降低汽车耗油量,同时增加汽车驾驶平稳性和可操控性,显著提高汽车性能。
自动变速器效率提升方法

自动变速器效率提升方法自动变速器是汽车的重要组成部分,它通过自动控制车辆的变速过程,提供了更加轻松和舒适的驾驶体验。
随着汽车工业的发展,人们对于自动变速器的效率要求也越来越高。
为了提升自动变速器的效率,不仅可以减少能源的消耗,还可以提高汽车的性能表现和可靠性。
本文将针对自动变速器效率提升的方法进行探讨。
一、优化变速箱结构自动变速器的结构设计对其效率有着重要影响。
可以通过优化齿轮比和传动比,减少传动过程中的能量损失,提升传动效率。
采用更加轻量化的材料和结构设计,减少自动变速器的质量,减少惯性损失和摩擦损耗,提高效率。
优化变速箱的润滑系统、冷却系统和密封系统,有效地减少功率损失和传动损耗,提升整体效率。
二、提升控制系统精度自动变速器的控制系统对于整个变速过程的精度和稳定性有着决定性的影响。
提升控制系统的精度可以有效地提升自动变速器的效率。
采用更加先进的电子控制技术,提升变速器的控制精度和响应速度,降低变速过程中的能量损失。
通过智能化的控制算法和传感器系统,实现更加精准的变速匹配和动力调控,提升整体的传动效率。
四、采用先进的摩擦材料摩擦材料在自动变速器中起着重要的作用,其性能对于传动效率和可靠性有着重要影响。
采用先进的摩擦材料可以有效地提升自动变速器的效率。
采用低摩擦系数的摩擦片和摩擦材料,降低传动过程中的能量损失和磨损损耗。
采用高温耐磨的摩擦材料,提高自动变速器的高温工作性能和稳定性,进一步提升效率。
优化摩擦材料的表面处理工艺,提高其摩擦系数和耐磨性能,降低传动损耗,提升整体效率。
五、增加智能化辅助系统通过增加智能化辅助系统,可以有效地提升自动变速器的效率。
采用智能化的智能制动系统和智能动力分配系统,实现更加精准和高效的动力控制和传动调控,提高整体传动效率。
采用智能化的智能启停系统和动力回收系统,实现更加智能的动力匹配和能量回收,降低传动过程中的能量损失,进一步提升效率。
减少变形的措施

金属结构减少应力变形的措施变形在任何情况下都是不可避免的,我们根据它的变形规律从上述几个变形的原理上采取相应的对策,来减少变形,特别是在设备的大修时不能只检查结合面、配合面的磨损情况,对于相互位置精度也要详细的检查,即形位误差,发现了就要认真的修复。
我们从设计、加工、修理、使用四个方面谈减少变形的措施。
一、设计:设计时要考虑的几个重要因素,实用性、强度,还要考虑零件的刚度和制造、使用、拆卸、修理等方面的问题。
正确的选用材料,注意工艺性能,如铸造的流动性、收缩性,锻造的可锻性、冷锻性,焊接的冷裂热裂倾向,机加工的可切削性、热处理的淬透性,冷淬性等。
要合理的布置零部件,选择适当的结构尺寸,如避免尖角,棱角改为圆角、倒角,厚薄悬殊的部分可开工艺孔或加厚太薄的地方。
安排好孔洞位置,把盲孔改为通孔等。
形状复杂的零件,在可能的条件下改为组合结构,镶拼结构,改善受力状况。
在设计中注意新技术新工艺新材料的应用等,减少制造时的内应力和变形。
二、加工:采用一系列的工艺措施来防止和减少零件的变形。
对毛坯件要有足够的时间做时效处理,以消除内部应力。
可以将铸造出来的毛坯在露天的环境中存放1~2年,自然时效处理,是最好的方法,效果最好。
但是时间太长,也可以采取高温退火、保温缓冷以消除内应力,即人工时效。
还可以用震动的作用或直接配合高温时效来消除内应力。
复杂零件和精密零件在粗加工后,也要进行人工时效。
高精度的零件在加工过程中要进行人工时效。
制定零件的加工工艺时,均要在工序、工步安排上,工艺装备和操作上采取减少变形的工艺措施来减少变形。
如粗加工和精加工分开进行。
之间留出静止时间。
在加工和修理过程中减少基准面的转换,保留加工基准面留给维修时使用。
减少维修过程中因基准不一而造成的误差。
要注意预留加工余量,调整加工尺寸和预加变形量,这对于热处理的零件来说非常必要。
有些零件在知道变形规律后,可预先加以反向变形量,经热处理后两者抵消。
也可以预加应力或控制应力的产生和变化使最终变形量符合要求,达到减少变形的目的。
- 1、下载文档前请自行甄别文档内容的完整性,平台不提供额外的编辑、内容补充、找答案等附加服务。
- 2、"仅部分预览"的文档,不可在线预览部分如存在完整性等问题,可反馈申请退款(可完整预览的文档不适用该条件!)。
- 3、如文档侵犯您的权益,请联系客服反馈,我们会尽快为您处理(人工客服工作时间:9:00-18:30)。
底盘制造■
2所示)。
图1 变速器盖图2 变速器座体法。
1.变速器盖
(1)原加工方式
图 3
m的精加工余量。
精
2008年 第 11 期
99
底盘制造
面平面度超差。
(2)改进后的加工方式 针对前面两种加工中存在的问题,为了减小加工后工件的应力变形,特制作了加工此工件的专用夹具(见图4)及防转动带槽主压板(见图5)。
图4 专用夹具
图5 防转动带槽主压板
具体的加工方法为:在机床上找正、固定好夹具(原加工用刀具不变)。
粗加工时,找正工件,防转动带槽主压板压紧,在工件的顶端加一个粗加工用辅助压紧压板,以低转速、大进给量实施粗加工,留精加工余量0.3 0.4m m。
精加工时,卸掉工件顶端粗加工辅助压板,让工件略冷却2 3min,使粗加工所产生的应力释放,然后采用较高转速、小进给量实施精加工。
通过此方法的实施,加工后的工件加工面平面度经测量稳定保持在0.02 0.03m m之间,从而解决了此零件在金属切削加工过程中的应力变形难题。
2.变速器座体
(1)原加工方式 加工时采用X5035立铣,在机床工作台上按图6所示的方向压紧,用盘铣刀加工,由于盘铣刀刀刃与工件的接触面积较大,因而在加工中产生应力随之较大,加之其他因素的影响,导致工件加工面平面度严重超差。
图 6
(2)改进后的加工方式 为解决这一加工问题,经对工件自身结构及上述加工方法进行仔细研究、分析后,采取分段加工、逐渐冷却
释放加工应力的方法。
仍采取上述加工方法对工件进行粗加工,留精加工余量1.5 2m m,然后将粗加工后的工件在自然环境放置两天左右,让应力进行释放。
改变加工设备,由立铣改为立车,减小刀具与工件的接触面积,改盘铣刀为卧式车床用半精车、精车刀具。
加工前先精研立车工作台表面,然后以四件为一组,将工件固定在立车工作台面上,仍采用立铣加工时的压紧方式进行半精加工,留量0.3 0.4m m,最后改变转速进行精加工。
由于加工方法及刀具的改变,减小了加工中的加工应力,使工件的加工面平面度稳定保持在0.02 0.03m m之间,达到了设计要求,
从而解决了加工中应力太大、加工面平面度超差的问题。
毛坯内在应力的解决
虽然以上方法解决了由于金属切削加工过程中产生应力导致工件加工面平面度超差而达不到设计要求的难题,但在组装过程中仍出现了平面度严重超差的问题。
经多方对工件超差数据仔细分析后,将原因确定在工件毛坯自身的问题上。
毛坯成形后,在自然界的时效时间太短,在浇铸毛坯时自身的内应力没有释放,而加工前又没有采取人工的去应力(时效)手段,导致已加工合格的工件产生应力变形。
为解决此问题,首先对工件毛坯进行了10 20m i n抛丸去应力处理,然后将工件加工至设计尺寸,过一周后对其进行测量,情况有所改观,但加工面平面度仍存在应力变形问题。
改用热处理的方法对毛坯进行加工前去应力处理,并在程序上进行严格控制。
在工件进炉前对加热炉底进行清扫,要求炉底干净、平整,工件入炉后应平铺靠实并用垫块对局部垫实,防止加热时工件变形。
使炉温升到540 560ºC,保温3 3.5h,随炉冷至260ºC以下后出炉,放置于干燥场地空冷至常温。
然后用防应力变形金属切削加工方法将工件加工至设计要求,过一周后测量加工面平面度、尺寸,结果全部在设计要求范围内,从而解决了由毛坯本身的应力而导致的加工件在最终组装时产生的变形。
查询号200811019关键词:变速器壳体 应力变形 毛坯
Web: Web Info。