变速器壳体强度有限元分析与试验验证
安装中央制动器的某型变速器的后壳体设计与开发
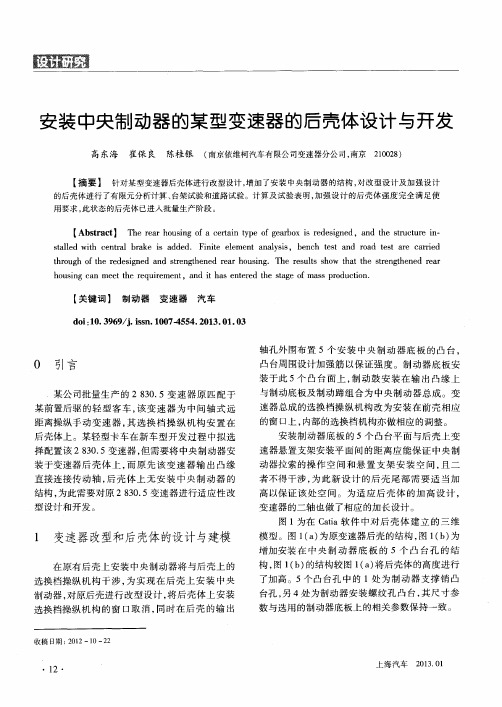
改 型设计 及 改 型 加 强 设 计 , 在 原 后 壳 体 上 增 加 了 直接 安装 中央制 动器 底 板 的结 构 , 使用 C a t i a软 件 对后 壳进 行 了三 维建模 。 ( 2 ) 对 改 型后 的后 壳 体 和 加 强 设 计 的后 壳 体 利用 有 限元 法 进 行 了分 析计 算 , 改 进 设 计 后 的 变 速器 后 壳 具 有 较 高 的 强 度 , 在 最 大 制 动 力 矩 2 3 5 0 N・ I n 的作 用 下 , 壳体最大 V o n Mi s e s等 效 应
装 于 变速器 后 壳 体 上 , 而 原 先 该 变 速 器 输 出凸 缘 直 接连 接传 动 轴 , 后 壳 体 上 无 安 装 中央 制 动 器 的
结构 , 为此需 要对 原 2 8 3 0 . 5变速 器进 行适 应性 改 型设 计 和开发 。
高 以保 证 该 处 空 间 。为 适 应后 壳体 的 加 高 设 计 ,
变速器 的二 轴也做 了相 应 的加长设 计 。
图1 为在 C a l r a软 件 中对 后 壳 体 建 立 的 三 维
1 变速器改型和后壳体的设计与建模
在 原有 后 壳上 安装 中央制 动 器将 与 后壳 上 的 选换 档操 纵 机 构 干 涉 , 为 实 现 在 后 壳 上 安 装 中 央
凸 台周 围设计 加强 筋 以保 证 强 度 。制动 器 底 板安 装 于此 5个 凸 台 面 上 , 制 动 鼓 安 装 在 输 出 凸缘 上 与制 动底 板及 制动 蹄组 合 为 中 央制 动 器总 成 。变 速器 总成 的选换 档操 纵 机 构改 为 安 装在 前 壳 相应 的窗 口上 , 内部 的选换 档机 构亦 做相 应 的调 整 。 安装 制 动器 底板 的 5个 凸台平 面 与后 壳上 变 速器 悬置 支架 安装平 面间 的距 离 应 能保 证 中央制 动器拉 索 的操 作 空 间 和悬 置 支架 安 装 空 间 , 且 二
变速器壳体强度有限元计算及结构改进分析
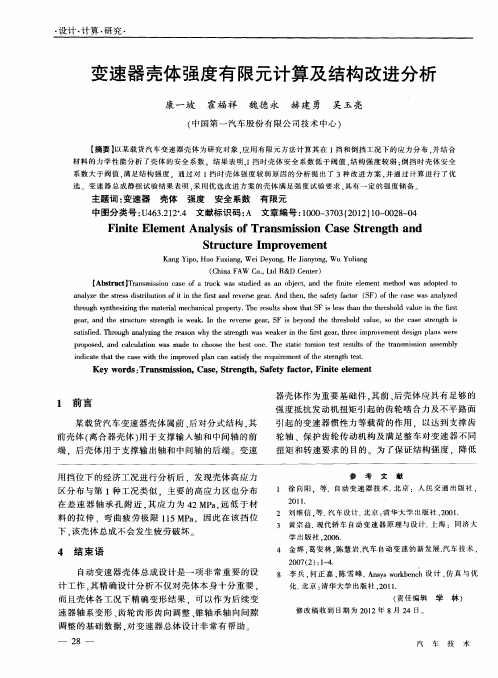
设计 - 计算 . 究பைடு நூலகம்。 研
变速器壳体 强度有 限元计算及结构 改进分析
康 一坡 霍福 祥 魏 德 永 赫 建 勇 吴 玉 亮
( 中国第 一汽 车股 份有 限公 司技 术 中心 )
【 摘要 】 载货汽车变速器壳体为研究对象 , 以某 应用有 限元方法计算其在 1 挡和倒挡工况下 的应力分布 , 并结合
器壳 体作 为重要 基础件 , 其前 、 壳体应 具有 足够 的 后 强度 抵抗 发动机 扭矩 引起 的齿轮 啮合 力及 不平路 面 引起 的变 速器惯 性力 等载荷 的作 用 .以达 到支撑 齿 轮轴 、保 护齿 轮传 动机构 及满 足整 车对变 速器 不 同 扭 矩和 转速要 求 的 目的。为 了保证 结构强 度 ,降低
限元模 型 如 图 2所示 『 3 1
轴 和 输 出轴 的轴 向旋 转 自 由度 .以满 足静 力 学 求
解 条 件 其 中旋 转 自 由度上 的支 反 力 即 为齿 轮 轴 的传 递 扭 矩 .在定 义结 果 输 出 时应 同 时定 义 此 支 反 力 的 输 出 .这样 可 方便 检 查 所 加 齿 轮 啮合 力 的 正 确 性
i dc t h tte c s t e i r v d p a a aif e r q i me to e s e gh t s. n ia et a a ewi t mp o e l n c n s ts t e u r h hh yh e n ft t n t e t h r
挡 除具 有 较 大 的速 比外 .还 具 有 与 前 进 挡 相 反 的
体强 度 . 进而 为完 善变速 器壳 体结 构提 供技 术支 持 。
2 有 限元 建 模
数据仿真驱动的产品设计流程优化
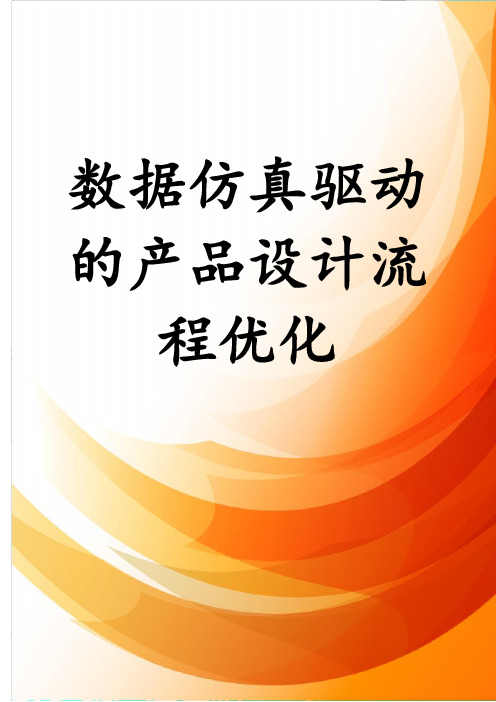
数据仿真驱动的产品设计流程优化一、数据仿真在产品设计中的应用背景随着科技的不断发展,产品设计面临着越来越复杂的挑战。
传统的产品设计流程往往依赖于经验和试错法,这不仅效率低下,而且可能导致产品质量不稳定和成本增加。
数据仿真技术的出现为产品设计带来了新的机遇。
在现代制造业中,产品的复杂性不断提高,涉及到多个学科领域的知识和技术。
例如,在汽车设计中,需要考虑机械结构、流体力学、电子系统等多个方面。
传统的设计方法很难在设计阶段全面考虑这些因素的相互影响。
数据仿真技术可以通过建立数学模型,模拟产品在不同工况下的性能表现,从而为设计师提供更全面的信息。
同时,市场竞争的加剧也要求企业能够更快地推出高质量的产品。
数据仿真可以在虚拟环境中对产品进行测试和优化,大大缩短了产品开发周期。
例如,在航空航天领域,通过数据仿真可以在设计阶段对飞行器的性能进行评估,避免了大量的实物试验,节省了时间和成本。
此外,消费者对产品的个性化需求也越来越高。
数据仿真可以帮助企业更好地了解消费者的需求,通过对用户数据的分析和仿真,设计出更符合用户需求的产品。
二、数据仿真驱动的产品设计流程1. 需求分析阶段在这个阶段,首先要收集和分析用户需求。
通过市场调研、用户反馈等方式,获取关于产品功能、性能、外观等方面的需求信息。
同时,还要考虑到产品的使用环境、法规要求等因素。
然后,利用数据仿真技术对这些需求进行量化分析。
例如,可以通过建立用户行为模型,模拟用户在不同场景下对产品的使用方式,从而更准确地确定产品的功能需求。
2. 概念设计阶段基于需求分析的结果,进入概念设计阶段。
在这个阶段,设计师会提出多个设计概念。
数据仿真可以帮助设计师对这些概念进行初步评估。
例如,可以通过建立简单的物理模型,模拟不同设计概念的基本性能,如力学性能、流体性能等。
通过对仿真结果的分析,筛选出具有潜力的设计概念,进一步细化和完善。
3. 详细设计阶段在详细设计阶段,需要对产品的各个部件进行详细设计。
机械设计基础机械系统的强度分析方法

机械设计基础机械系统的强度分析方法机械设计基础——机械系统的强度分析方法1. 引言机械系统的强度分析是机械设计中的关键环节之一,它能够评估和验证机械系统在工作过程中的承载能力和安全性。
机械系统的强度分析方法多种多样,其中最常用的包括应力分析法、有限元分析法和试验验证法。
本文将会对这几种方法进行详细探讨。
2. 应力分析法应力分析法是机械系统强度分析最常用的方法之一。
它通过理论计算和分析,确定机械系统在受力状态下的最大应力和应力分布情况。
常见的应力分析方法包括静力学分析、动力学分析和疲劳寿命分析。
通过应力分析,设计者可以确定合适的材料和结构尺寸,以满足系统的强度要求。
3. 有限元分析法有限元分析法是一种基于数值计算的强度分析方法,它是近年来发展起来的一种先进的计算机模拟技术。
有限元分析将机械系统分割为有限个小单元,利用力学和数学原理对每个小单元进行应力分析和计算。
通过分析每个小单元的应力和变形情况,可以得到整个机械系统的强度和稳定性评估结果。
有限元分析法在复杂机械系统的强度分析中具有广泛的应用。
4. 试验验证法试验验证法是机械系统强度分析的一种重要手段。
通过在实际工作环境中进行试验,直接测量机械系统的应力、位移和变形等参数,以验证设计的合理性和可靠性。
试验验证法可以对理论计算和模拟分析的结果进行验证,发现和解决可能存在的问题,并对设计进行优化。
试验验证法是机械系统强度分析中不可或缺的一部分。
5. 小结机械系统的强度分析是机械设计过程中的重要环节。
应力分析法、有限元分析法和试验验证法是目前应用最广泛的强度分析方法。
应力分析法通过理论计算分析系统的应力分布情况,有限元分析法则是一种基于数值计算的模拟方法,而试验验证法则是通过实际试验来验证和优化设计。
设计者可以根据实际情况选择合适的分析方法,以确保机械系统在工作过程中具备足够的强度和安全性。
以上是对机械系统强度分析方法的简要介绍,希望能对读者有所启发和帮助。
新型轻卡变速器壳体动静态性能分析

F/ yN
39 8 5
F, zN
1 0 096
M/ x Mr / M ( N ・m) ( mm ( m m N・ ) N-m)
1 3 30 2 3o4 8 0 7 O
l 用 有 限元 方 法 对 变 速 器 壳 体 的刚 强 度 、 睬 动 态 性 能 分 析 已经 成 为 国 内外 变 速 器 研 究 机 构 和 生产 厂 家 的 主要 手 段 。本 文 以 某 轻 卡 变 速 器 壳
C E软件 中建模 。本文 以某 型轻 卡壳 体 为研 究 对 A 象 , 用 U 软 件 建 立 壳 体 数 模 , 人 H P R 利 G 导 YE. WO K R S软件进 行几何 清理 并 划分 网格 , 成有 限 完
a d b u da y c n tan s r lto fh u i s e p t td,a d si ne s a d sr n t e o a c f n o n r o sr i t eain o o sng i x ai e a n tf s n te g h p r r n e o f f m h u i g i n lz d. Be i e ,t r u h t e c l u ain o e r me h fe ue c fe c e rl v lwih o sn sa ay e sd s h o g h ac lto fg a s q n y o a h g a -e e t r t e s e d o 0 /mi h p e f1 0r 8 n,t e r lto s i t e r n miso o s nd h usn au a e ue c s h eai n h p bewe n ta s s in n ie a o i g n t r lf q n y i r su i d b o i i aa r s ls a o tta s s in a s mb y n ie e twi a u a e u n y a d t d e y c mb nng d t e u t b u r n miso se l o s ts t n t r lf q e c n h r
变速器壳体强度有限元分析与试验验证
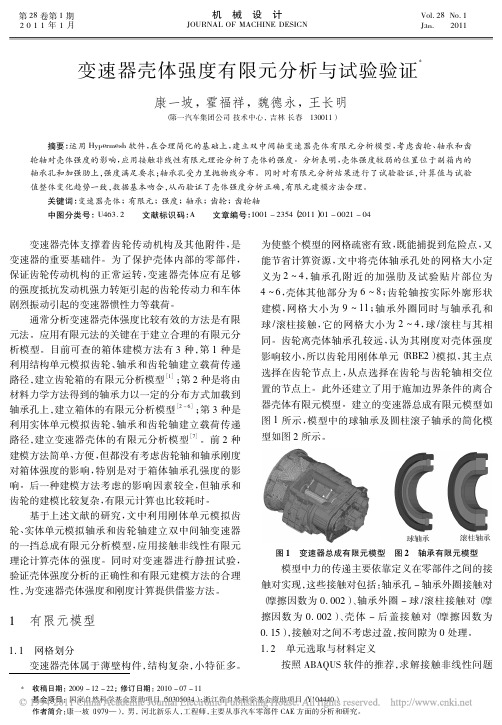
Principal) 查看。 图 4 是壳体的位移变形图,从壳体后端向前看,整
个壳体有顺时针旋转变形的趋势,相对于离合器壳体 前端固定位置的最大位移为 0. 388 mm,发生在后盖的 右上部位的固定销销孔附近,位移较小。图 5 ~ 图 7 是壳体的应力云图,最大应力值为 198. 6 MPa,发生在 壳体副箱支撑第 2 轴后轴承孔的加强肋上,靠近后盖 一侧。支撑第 2 轴后轴承孔的加强肋共有 3 条,按顺 时针排列,其他 2 条应力依次减小,最大相差 90 MPa, 可以考虑在不增加加强肋数量的同时将这 3 条加强肋 绕逆时针旋 转 一 定 角 度,使 它 们 能 比 较 均 匀 地 受 力。 副箱中的第 2 轴后轴承孔最大应力值为 96. 1 MPa,主 要是由副箱常啮合主动齿轮的轴向力引起的,可以将 放置定位盘的凹槽填平,以增加该位置的强度和刚度。 后盖轴承孔最大应力值为 152. 3 MPa,发生在后盖的 右下轴承孔上,此轴承孔的变形较大,建议布置加强肋 增加刚度。壳体主箱中的常啮合齿轮传动速比较小及 离合器壳体对主箱前端面具有支撑作用,所以计算出 的一轴前轴承孔应力和中间轴前轴承孔的应力均比较 小。主箱中间主体部分有较大的抗扭截面模量,应力 值不大,可以将主箱中间主体部位进行减薄以减小质 量,同时要注意刚度变化。
验值对比情况如图 11 所示。
图 11 计算值与试验值对比
在图 11 中,应力相对误差位于 20. 0% 以内的测 点有 8 个,其中 9 号测点的误差最小,为 2. 6% ; 误差 位于 20. 0% ~ 30. 0% 的测点有 2 个,它们是 5 号和 10 号测点,其 误 差 分 别 为 27. 8% 和 20. 8% ,5 号 测
按照 ABAQUS 软件的推荐,求解接触非线性问题
基于有限元分析的电驱动商用车减速器壳体优化设计

AUTO TIME115AUTOMOBILE DESIGN | 汽车设计1 引言新能源汽车传动系统功能是将电动机总成的动力传递到驱动车轮。
其传动系统主要由集成减速器、差速器、电动机的电驱动桥总成组成。
减速器能改变电动机输出的转矩、转速特性,使电动机的输出扭矩增大、输出转速下降以适应汽车的实际行驶需求。
为达到降速增扭的功能,电驱动减速器总成普遍采用三级平行轴齿轮设计。
图1是某款电驱动减速器总成,结构主要由减速器壳体、差速器总成、输入轴齿轮、中间轴齿轮、差速器齿轮、圆锥滚子轴承、油封、堵盖等零件组成。
由于电动机峰值输出扭矩大、转速高的特性,会造成减速器总成因润滑不足导致轴承烧蚀、减速器壳体破损的情况[1]。
因此需将分析设计工作前置,解决相关技术问题。
传统的减速器壳体设计往往依赖于经验与试错,设计及优化改进周期长,成本高。
本覃万龙1 黄文聪21.南宁职业技术学院 广西南宁市 5300002.柳州英勤拓蓝汽车科技有限公司 广西柳州市 545000摘 要: 随着汽车电动化的进程日益加快,电驱动城市物流商用车已成为了市场上一个重要车型。
作为城市物流车的核心零部件,减速器的性能稳定变得至关重要。
而减速器壳体在减速器运行中起到支撑保护功能,会受到多种重力负荷的作用。
在面对电驱动状态下出现的复杂转速及扭矩工况时,往往会出现减速器壳体因应力集中受损、轴承因润滑不足烧蚀等多种问题。
减速器壳体的结构设计直接影响到减速器总成的整体性能与可靠性。
本文主要采用Masta 、Particleworks 软件,对电驱动商用车的减速器壳体进行有限元分析及结构优化设计。
并搭载后桥总成进行台架试验验证。
结果证明,所优化设计的减速器壳体符合相关汽车行业标准及实际应用需求。
通过这一实用方法,提高了减速器壳体的强度、刚度及减速器总成轴承润滑能力。
为电驱动商用车的高效、稳定运行提供了保障。
也为后续电驱动后桥总成零部件开发及优化设计提供了思路。
变速器壳体28工况仿真

变速器壳体28工况仿真变速器壳体的28工况仿真是一项重要的技术手段,它在汽车工程中具有广泛的应用。
本文将对变速器壳体28工况仿真的意义、方法和结果进行详细介绍,以期为相关领域的研究和工程实践提供指导。
变速器壳体作为汽车变速器的重要部件,其结构设计直接影响着整个变速器的性能和寿命。
28工况仿真是一种综合考虑变速器在不同工况下的受力、载荷和疲劳破坏情况的方法。
通过模拟实际使用过程中的不同工况,可以全面评估变速器壳体的强度、刚度和振动特性,为设计优化和寿命预测提供科学依据。
在进行28工况仿真时,首先需要建立变速器壳体的数值模型。
通过CAD软件对壳体的几何结构进行建模,并考虑到细节特征,如孔洞、连接结构和法兰等。
然后,根据不同的工况要求,设定相应的加载条件和边界条件。
例如,对于不同速度和转矩要求,可以设定壳体的材料和厚度,以及轴承的支撑方式等。
最后,使用有限元分析软件对模型进行分析,得到壳体在不同工况下的应力分布、变形和振动情况。
通过28工况仿真,可以获得丰富的数据和信息。
首先是壳体的应力分布和刚度特性。
这些数据可以帮助工程师评估壳体的强度和刚度是否满足设计要求,是否存在应力集中和疲劳破坏的风险。
其次是壳体的变形和振动情况。
这些数据可以用于评估壳体的动态特性和振动传递特性,为减震和降噪设计提供参考。
此外,通过对不同工况下的壳体应力和变形进行综合分析,可以预测壳体的寿命,并进行结构优化和材料选择。
变速器壳体28工况仿真为汽车工程提供了一种高效、准确和经济的设计手段。
通过仿真分析,可以降低开发成本和时间,提高产品质量和可靠性。
同时,仿真还为设计优化和全寿命周期管理提供了科学依据。
因此,在汽车工程中广泛应用变速器壳体28工况仿真是非常有意义的。
综上所述,变速器壳体28工况仿真是一项重要的技术手段,它可以全面评估变速器壳体的强度、刚度和振动特性,在汽车工程中具有广泛的应用前景。
通过建立数值模型、设定加载和边界条件,并使用有限元分析软件进行仿真分析,可以获得丰富的数据和信息,为壳体设计和寿命预测提供科学依据。
- 1、下载文档前请自行甄别文档内容的完整性,平台不提供额外的编辑、内容补充、找答案等附加服务。
- 2、"仅部分预览"的文档,不可在线预览部分如存在完整性等问题,可反馈申请退款(可完整预览的文档不适用该条件!)。
- 3、如文档侵犯您的权益,请联系客服反馈,我们会尽快为您处理(人工客服工作时间:9:00-18:30)。
模型中力的传递主要依靠定义在零部件之间的接 触对实现,这些接触对包括: 轴承孔 - 轴承外圈接触对 ( 摩擦因数为 0. 002) 、轴承外圈 - 球 / 滚柱接触对( 摩 擦因数 为 0. 002 ) 、壳 体 - 后 盖 接 触 对 ( 摩 擦 因 数 为 0. 15) ,接触对之间不考虑过盈,按间隙为 0 处理。 1. 2 单元选取与材料定义
关键词: 变速器壳体; 有限元; 强度; 轴承; 齿轮; 齿轮轴 中图分类号: U463. 2 文献标识码: A 文章编号: 1001 - 2354( 2011) 01 - 0021 - 04
变速器壳体支撑着齿轮传动机构及其他附件,是 变速器的重要基础件。为了保护壳体内部的零部件, 保证齿轮传动机构的正常运转,变速器壳体应有足够 的强度抵抗发动机强力转矩引起的齿轮传动力和车体 剧烈振动引起的变速器惯性力等载荷。
( 3) 基于文中模型施加单位转矩载荷,并结合道 路实车采集的变速器载荷谱,可进一步预测壳体在真 实工作环境下的疲劳损伤和寿命,为进行结构疲劳设 计提供参考。
24
机械设计
第 28 卷2] [3] [4] [5] [6] [7] [8] [9]
图 3 变速器一挡受力分析
表 1 齿轮传动力
N
主箱常啮 合齿轮对 主箱一挡
齿轮对 副箱常啮 合齿轮对 副箱减速
齿轮对
圆周力 Ft 16 449. 6 31 977. 5 50 449. 6 127 607. 9
径向力 Fr 6 177. 4 12 281. 6 19 455. 5 66 479. 5
轴向力 Fa 0. 0 0. 0
31 293. 8 31 192. 5
为了模拟壳体与后盖之间的装配过程,还需要在
拧紧螺栓上施加大小为 24 000 N 的预紧力。
边界条件施加在离合器壳体前端面的螺栓孔上,
固定螺栓孔不动; 同时还需约束齿轮轴的轴向旋转自
由度,以满足静力学求解条件。
2 结果分析与讨论
计算用 ABAQUS 软件,强度用最大主应力( Max.
( 1) 由 仿 真 结 果 可 知,变 速 器 壳 体 满 足 强 度 要 求 ,壳 体 的 薄 弱 位 置 位 于 壳 体 副 箱 内 的 轴 承 孔 ,以 及 支撑轴承孔 的 加 强 肋 上,这 些 位 置 应 作 为 壳 体 强 度 设计的重 点 部 位。计 算 与 试 验 对 比,测 点 应 力 计 算 值 与 试 验 值 整 体 变 化 趋 势 一 致 ,数 值 基 本 吻 合 ,验 证 了壳体强度分析的正确性及有限元模型的有效性, 表明以变速器总成为单位的壳体强度分析具有一定 的可靠性。
抛物线分布,这种形式的载荷分布是由齿轮轴弯曲变
2011 年 1 月
康一坡,等: 变速器壳体强度有限元分析与试验验证
23
形、轴承径向和翘曲变形共同引起的。当轴承孔的径 向刚度较小时,上面的抛物线载荷会消失,下面的仍将 继续存在。轴承孔受力与轴承外圈受力大小相等,方 向相反。
图 8 轴承受力分布形式
3 试验验证
按照 ABAQUS 软件的推荐,求解接触非线性问题
* 收稿日期: 2009 - 12 - 22; 修订日期: 2010 - 07 - 11 基金项目: 国家自然科学基金资助项目( 50305034) ; 浙江省自然科学基金资助项目( Y104440) 作者简介: 康一坡( 1979—) ,男,河北新乐人,工程师,主要从事汽车零部件 CAE 方面的分析和研究。
22
机械设计
第 28 卷第 1 期
应选用修正 2 阶四面体单元 C3D10M[7]。 零部件的材料假设为各向同性的线弹性材料,变
速器壳体 和 离 合 器 壳 体 材 料 为 HT250,其 弹 性 模 量 1. 39 × 105 MPa,泊松比 0. 156; 轴承材料为 GCr15,其弹 性模量 2. 19 × 105 MPa,泊 松 比 0. 30; 齿 轮 轴 材 料 为 20CrMnTi,其弹性模量 2. 12 × 105 MPa,泊松比 0. 278。 1. 3 受力分析与工况确定
双中间轴变速器的结构特点是 2 个中间轴总成 关于第 1 轴和第 2 轴呈对称分布,这就使得第 1 轴和 第 2 轴上的齿轮径向力相等,使得这 2 个轴只承受转 矩不承受弯矩。图 3 是变速器处于一挡时的受力示 意图,图中的 齿 轮 传 动 力 移 到 了 相 应 的 齿 轮 节 点 外 侧显示。根 据 齿 轮 传 动 受 力 分 析 公 式[8],以 及 变 速 器最大输入转矩和齿轮啮合参数计算的齿轮传动力 如表 1 所示。
基于上述文献的研究,文中利用刚体单元模拟齿 轮、实体单元模拟轴承和齿轮轴建立双中间轴变速器 的一挡总成有限元分析模型,应用接触非线性有限元 理论计算壳体的强度。同时对变速器进行静扭试验, 验证壳体强度分析的正确性和有限元建模方法的合理 性,为变速器壳体强度和刚度计算提供借鉴方法。
1 有限元模型
1. 1 网格划分 变速器壳体属于薄壁构件,结构复杂,小特征多。
验值对比情况如图 11 所示。
图 11 计算值与试验值对比
在图 11 中,应力相对误差位于 20. 0% 以内的测 点有 8 个,其中 9 号测点的误差最小,为 2. 6% ; 误差 位于 20. 0% ~ 30. 0% 的测点有 2 个,它们是 5 号和 10 号测点,其 误 差 分 别 为 27. 8% 和 20. 8% ,5 号 测
第 28 卷第 1 期 2011 年1 月
机械设计
JOURNAL OF MACHINE DESIGN
Vol. 28 No. 1 Jan. 2011
*
变速器壳体强度有限元分析与试验验证
康一坡,霍福祥,魏德永,王长明
( 第一汽车集团公司 技术中心,吉林 长春 130011)
摘要: 运用 Hypermesh 软件,在合理简化的基础上,建立双中间轴变速器壳体有限元分析模型,考虑齿轮、轴承和齿 轮轴对壳体强度的影响,应用接触非线性有限元理论分析了壳体的强度。分析表明,壳体强度较弱的位置位于副箱内的 轴承孔和加强肋上,强度满足要求; 轴承孔受力呈抛物线分布。同时对有限元分析结果进行了试验验证,计算值与试验 值整体变化趋势一致,数据基本吻合,从而验证了壳体强度分析正确,有限元建模方法合理。
通常分析变速器壳体强度比较有效的方法是有限 元法。应用有限元法的关键在于建立合理的有限元分 析模型。目前可查的箱体建模方法有 3 种,第 1 种是 利用结构单元模拟齿轮、轴承和齿轮轴建立载荷传递 路径,建立齿轮箱的有限元分析模型[1]; 第 2 种是将由 材料力学方法得到的轴承力以一定的分布方式加载到 轴承孔上,建立箱体的有限元分析模型[2 - 6]; 第 3 种是 利用实体单元模拟齿轮、轴承和齿轮轴建立载荷传递 路径,建立变速器壳体的有限元分析模型[7]。前 2 种 建模方法简单、方便,但都没有考虑齿轮轴和轴承刚度 对箱体强度的影响,特别是对于箱体轴承孔强度的影 响。后一种建模方法考虑的影响因素较全,但轴承和 齿轮的建模比较复杂,有限元计算也比较耗时。
在变速器试验过程中,变速器壳体没有出现裂纹 或发生断裂,说明壳体有一定的强度储备,满足强度要 求,这与有限元分析结果也是一致的。
4 结论
图 9 应变片粘贴位置
图 10 变速器台架试验
对比用的测点试验应力值由每个测点两次测量的
最大应变值进行平均并应用虎克定律得到,测点计算
应力值可直接从有限元计算结果中读取,计算值与试
Principal) 查看。 图 4 是壳体的位移变形图,从壳体后端向前看,整
个壳体有顺时针旋转变形的趋势,相对于离合器壳体 前端固定位置的最大位移为 0. 388 mm,发生在后盖的 右上部位的固定销销孔附近,位移较小。图 5 ~ 图 7 是壳体的应力云图,最大应力值为 198. 6 MPa,发生在 壳体副箱支撑第 2 轴后轴承孔的加强肋上,靠近后盖 一侧。支撑第 2 轴后轴承孔的加强肋共有 3 条,按顺 时针排列,其他 2 条应力依次减小,最大相差 90 MPa, 可以考虑在不增加加强肋数量的同时将这 3 条加强肋 绕逆时针旋 转 一 定 角 度,使 它 们 能 比 较 均 匀 地 受 力。 副箱中的第 2 轴后轴承孔最大应力值为 96. 1 MPa,主 要是由副箱常啮合主动齿轮的轴向力引起的,可以将 放置定位盘的凹槽填平,以增加该位置的强度和刚度。 后盖轴承孔最大应力值为 152. 3 MPa,发生在后盖的 右下轴承孔上,此轴承孔的变形较大,建议布置加强肋 增加刚度。壳体主箱中的常啮合齿轮传动速比较小及 离合器壳体对主箱前端面具有支撑作用,所以计算出 的一轴前轴承孔应力和中间轴前轴承孔的应力均比较 小。主箱中间主体部分有较大的抗扭截面模量,应力 值不大,可以将主箱中间主体部位进行减薄以减小质 量,同时要注意刚度变化。
为使整个模型的网格疏密有致,既能捕捉到危险点,又 能节省计算资源,文中将壳体轴承孔处的网格大小定 义为 2 ~ 4,轴承孔附近的加强肋及试验贴片部位为 4 ~ 6,壳体其他部分为 6 ~ 8; 齿轮轴按实际外廓形状 建模,网格大小为 9 ~ 11; 轴承外圈同时与轴承孔和 球 / 滚柱接触,它的网格大小为 2 ~ 4,球 / 滚柱与其相 同。齿轮离壳体轴承孔较远,认为其刚度对壳体强度 影响较小,所以齿轮用刚体单元( RBE2) 模拟,其主点 选择在齿轮节点上,从点选择在齿轮与齿轮轴相交位 置的节点上。此外还建立了用于施加边界条件的离合 器壳体有限元模型。建立的变速器总成有限元模型如 图 1 所示,模型中的球轴承及圆柱滚子轴承的简化模 型如图 2 所示。
图 4 壳体位移云图
图 5 壳体应力云图( 一)
图 6 壳体应力云图( 二)
图 7 后盖应力云图
以上计算的应力均未超过变速器壳体材料的抗拉
强度极限 250 MPa,所以在一挡工况下,壳体强度是安