26_基于CAE分析的变速器壳体优化
自动变速器壳体设计及仿真优化
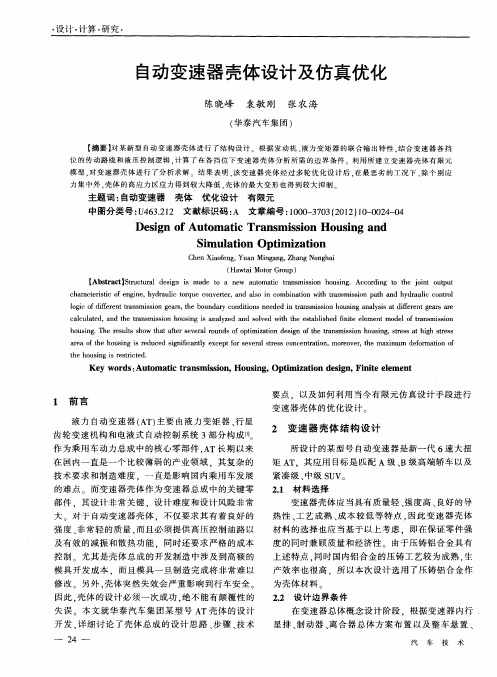
矩A T.其应用 目标 是匹配 A级 、 高端轿 车 以及 B级
c a a t r t fe gn , y r u i t r u o v n r a d a s n c mb n t n wi r n mis n p t n y ru i o to h rc e i i o n i e h d a l o q e c n e e , n lo i o i ai t ta s s i a h a d h d a l c n r l sc c o h o c l gc o i e e tt n miso e r , h o n a y c n i o s n e e n ta s s i n h u i g a ay i a i ee t e r r o i f f r n r s si n g a s t e b u d r o d t n e d d i r n mis o s n lss t f r n a s ae d f a i o n d g c l u ae ,a d t e t n mi in h u i g i n lz d a d s le i h sa l h d f i lme tmo e ft n miso a c lt d n h r s s o o s s a ay e n ov d w t t e e t b i e n t ee n d lo a s s in a s n h s i e r h u i g T e r s l h w t a f rs v r lr u d fo t z t n d sg ft e t n miso o sn ,s e sa ih sr s o sn . h e ut s o h tat e e a o n so p i a i e i n o r s si n h u i g t s thg te s s e mi o h a r a e ft e h u i g i e u e i nf a t x e t o e e a t s o c n r t n mo e v r h xmu d fr t n o r a o o sn sr d c d s i c n l e c p r s v r ls e s c n e t i , ro e ,t e ma i m e o mai f h g i y f r ao o
基于CAE技术的机械结构优化设计

基于CAE技术的机械结构优化设计摘要:随着科技的不断发展,CAE(计算机辅助工程)技术在机械结构优化设计中的应用日益广泛。
本文将详细介绍CAE技术在机械结构优化设计中的应用,包括基本概念、分析方法、参数优化和多目标优化等方面。
同时,还将探讨CAE 技术对机械结构优化设计所带来的好处和挑战,并展望未来发展的趋势。
1. 研究背景机械结构优化设计是提高产品性能、减轻产品重量、降低成本的重要手段。
传统的机械结构优化设计主要基于试验和经验,效率低下且需要耗费大量资源。
而CAE技术的出现极大地改变了这一现状,使得机械结构优化设计变得快速、高效和精确。
2. CAE技术概述CAE技术是指利用计算机来模拟和分析产品在各种工作条件下的力学性能,包括有限元分析、多体动力学仿真、流体力学分析等。
这些分析结果可以帮助工程师更好地理解和改进产品结构。
3. CAE技术在机械结构优化设计中的应用3.1 分析方法CAE技术可以通过有限元分析、多体动力学仿真等方法,对机械结构进行静态和动态的力学分析。
通过这些分析,可以评估结构的强度、刚度、振动等性能,并找出设计中的潜在问题。
3.2 参数优化CAE技术可以通过参数化建模和仿真分析,对机械结构的关键参数进行优化。
通过自动化的迭代过程,可以找到最佳参数组合,从而实现结构的最优化设计。
3.3 多目标优化多目标优化是指在考虑多个矛盾目标的情况下,找到最佳的设计方案。
CAE技术可以在多个目标之间进行权衡和优化,确保结构在强度、刚度、重量等方面达到最佳平衡。
4. CAE技术的优势和挑战4.1 优势CAE技术可以大大缩短试验和开发周期,节省成本和资源。
通过模拟和分析,可以在设计阶段提前发现和解决问题,减少后期改动和调整的工作量。
同时,CAE 技术还具有直观的可视化效果,有助于工程师更好地理解和沟通设计方案。
4.2 挑战CAE技术的应用需要大量的计算资源和专业知识,对工程师的要求较高。
此外,模拟与实际情况之间的差异也是一个挑战,需要工程师不断调整和改进模型以提高分析的准确性。
基于CAE分析的变速器后悬置支架优化设计

置 支架的结构 。 既减小 了后悬置支架的净质量 , 又确保 了零件性 能。
关 键 词 : E; 化 设 计 ; 悬置 支 架 CA 优 后 中图 分 类 号 : 4 3 U 6 文献标识码: A
文章编号 :6 2 5 5 2 1 1 - 0 3 0 1 7 — 4 X( 0 0 5 - 3 0)0
速器 以及传递作用在动力 总成上 的一切力 和扭矩 ; 另外 , 悬置
数值仿真方法 , 如有 限元 、 多体动力学 、 计算 流体 力学等技术 , 在产 品设计 中得到大量 的应用 。 品在初步设计完成后 , 以 产 可
基 于 C D模 型进行产 品性能的虚拟试验 , A 初步 考察其工 作应 力、 运动过程 、 寿命等 。 如果产品不能满足要求 , 可以立即返回 设计人员 进行修改或重新设计 ,从 而大大减少实物试验 的周
元 计算 方法 , 整个概念空 间进行拓 扑优 化 , 对 获得设 计对象 的 初 步拓扑结构 , 据设 计要求及生产 工艺 , 根 提取初 始的概念设
计模 型。
图 2 后悬置支架概念模型 图
变 速器后悬 置支架 的有限元模型及边界条件见图 3 有限 ,
元模 型采用线性六 面体网格 , 节单元数为 2 4 5 6 。杨 氏模量 、 0
间 , 刚性单元 (E 2连接 , 使用 RB) 以模拟悬置安装的真实位置 ,
载荷点 为发动机悬置硬点位置 ( 载荷见表 2 , )各工况的载荷数 据, 通过 A A D MS软件建立悬置 系统 动力 学仿真模型 , 行仿 进
真分析而获得 。
表 2 变速器后悬置支架在各种工况下的载 荷数据
《 装备制造技术》0 O 2 1 年第 l 期 0
基 于 G E分 析 的变 速 器 后 悬 置 支 架 优 化 设 计 A
CAE仿真技术在减速器产品设计中的应用
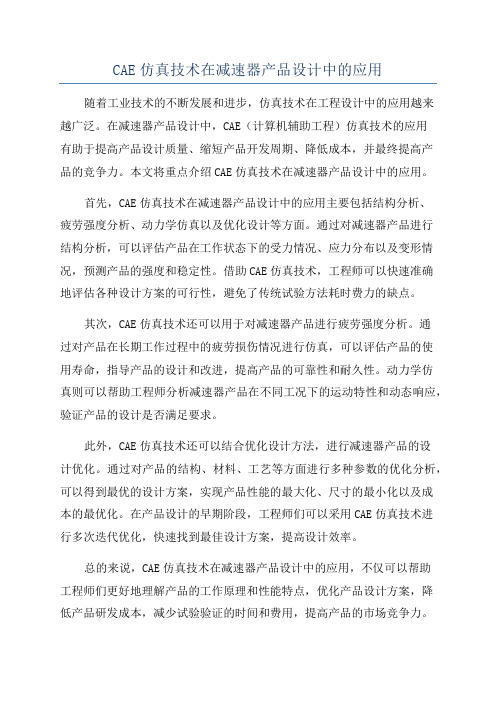
CAE仿真技术在减速器产品设计中的应用随着工业技术的不断发展和进步,仿真技术在工程设计中的应用越来越广泛。
在减速器产品设计中,CAE(计算机辅助工程)仿真技术的应用有助于提高产品设计质量、缩短产品开发周期、降低成本,并最终提高产品的竞争力。
本文将重点介绍CAE仿真技术在减速器产品设计中的应用。
首先,CAE仿真技术在减速器产品设计中的应用主要包括结构分析、疲劳强度分析、动力学仿真以及优化设计等方面。
通过对减速器产品进行结构分析,可以评估产品在工作状态下的受力情况、应力分布以及变形情况,预测产品的强度和稳定性。
借助CAE仿真技术,工程师可以快速准确地评估各种设计方案的可行性,避免了传统试验方法耗时费力的缺点。
其次,CAE仿真技术还可以用于对减速器产品进行疲劳强度分析。
通过对产品在长期工作过程中的疲劳损伤情况进行仿真,可以评估产品的使用寿命,指导产品的设计和改进,提高产品的可靠性和耐久性。
动力学仿真则可以帮助工程师分析减速器产品在不同工况下的运动特性和动态响应,验证产品的设计是否满足要求。
此外,CAE仿真技术还可以结合优化设计方法,进行减速器产品的设计优化。
通过对产品的结构、材料、工艺等方面进行多种参数的优化分析,可以得到最优的设计方案,实现产品性能的最大化、尺寸的最小化以及成本的最优化。
在产品设计的早期阶段,工程师们可以采用CAE仿真技术进行多次迭代优化,快速找到最佳设计方案,提高设计效率。
总的来说,CAE仿真技术在减速器产品设计中的应用,不仅可以帮助工程师们更好地理解产品的工作原理和性能特点,优化产品设计方案,降低产品研发成本,减少试验验证的时间和费用,提高产品的市场竞争力。
随着计算机技术的不断进步和发展,CAE仿真技术在减速器产品设计中的应用前景十分广阔,将会成为未来产品设计的重要工具和方法。
变速器壳体28工况仿真

变速器壳体28工况仿真变速器壳体的28工况仿真是一项重要的技术手段,它在汽车工程中具有广泛的应用。
本文将对变速器壳体28工况仿真的意义、方法和结果进行详细介绍,以期为相关领域的研究和工程实践提供指导。
变速器壳体作为汽车变速器的重要部件,其结构设计直接影响着整个变速器的性能和寿命。
28工况仿真是一种综合考虑变速器在不同工况下的受力、载荷和疲劳破坏情况的方法。
通过模拟实际使用过程中的不同工况,可以全面评估变速器壳体的强度、刚度和振动特性,为设计优化和寿命预测提供科学依据。
在进行28工况仿真时,首先需要建立变速器壳体的数值模型。
通过CAD软件对壳体的几何结构进行建模,并考虑到细节特征,如孔洞、连接结构和法兰等。
然后,根据不同的工况要求,设定相应的加载条件和边界条件。
例如,对于不同速度和转矩要求,可以设定壳体的材料和厚度,以及轴承的支撑方式等。
最后,使用有限元分析软件对模型进行分析,得到壳体在不同工况下的应力分布、变形和振动情况。
通过28工况仿真,可以获得丰富的数据和信息。
首先是壳体的应力分布和刚度特性。
这些数据可以帮助工程师评估壳体的强度和刚度是否满足设计要求,是否存在应力集中和疲劳破坏的风险。
其次是壳体的变形和振动情况。
这些数据可以用于评估壳体的动态特性和振动传递特性,为减震和降噪设计提供参考。
此外,通过对不同工况下的壳体应力和变形进行综合分析,可以预测壳体的寿命,并进行结构优化和材料选择。
变速器壳体28工况仿真为汽车工程提供了一种高效、准确和经济的设计手段。
通过仿真分析,可以降低开发成本和时间,提高产品质量和可靠性。
同时,仿真还为设计优化和全寿命周期管理提供了科学依据。
因此,在汽车工程中广泛应用变速器壳体28工况仿真是非常有意义的。
综上所述,变速器壳体28工况仿真是一项重要的技术手段,它可以全面评估变速器壳体的强度、刚度和振动特性,在汽车工程中具有广泛的应用前景。
通过建立数值模型、设定加载和边界条件,并使用有限元分析软件进行仿真分析,可以获得丰富的数据和信息,为壳体设计和寿命预测提供科学依据。
纯电动汽车变速箱壳体CAE分析及拓扑优化

优化结果表明,优化后壳体刚度和固有频率均有提高。根据拓扑 优化结果对变速箱壳体结构进行改进,通过仿真计算验证表明, 改进后的壳体提高了刚度和前两阶固有频率,使得齿轮传动精度 更高,避开了常用转速下的齿轮啮合激励频率,且改进后质量减 轻了7%,性能得到明显改善,达到设计要求。
采用仿真分析与试验相结合的方法,分别利用ABAQUS和 b对壳体动态特性进行仿真和试验研究。仿真与试 验结果对比表明,不论在自由状态还是约束状态下,计算模态振 型与试验模态振型基本吻合,且固有频率相对误差均在4%以内, 从而验证了变速箱壳体有限元模型的准确性。
另外,通过研究壳体模态参数,发现其前两阶固有频率与常用转 速下齿轮啮合激励频率比较接近,可能引起共振现象的发生,为 多目标拓扑优化提供基础数据。3.基于变密度法建立静动态联 合多目标拓扑优化数学模型,通过Optistruct进行拓扑优化,以 设计域内单元密度为设计变量,约束优化前后体积比,以一挡及 倒挡工况下的柔度最小化和前两阶固有频率的加权响应最大化 为优化目标。
主要研究内容如下:1.详细介绍了纯电动汽车变速箱壳体的研究 背景及意义,然后阐述了纯电动汽车变速箱研究现状,接着介绍 了壳体有限元分析及拓扑优化研究现状。2.详细介绍了变速箱 壳体结构设计过程,利用CATIA和HyperMesh分别建立体一挡及倒挡工况进行静力学仿真分析。 分析结果表明,在两种工况下该壳体满足刚强度要求,并且有优 化设计空间。
纯电动汽车变速箱壳体CAE分析及拓扑 优化
随着能源问题的日益突出,节能减排在汽车行业中越来越受到重 视,因此纯电动汽车得到了快速发展。众所周知,汽车变速箱是 汽车传动系统的核心装置,而壳体性能优劣对变速箱正常工作起 着重要作用,因此壳体性能与整车性能有直接关系,应保证其满 足使用要求。
MSC Nastran与传动CAE分析相结合的商用车桥主减总成轻量化设计
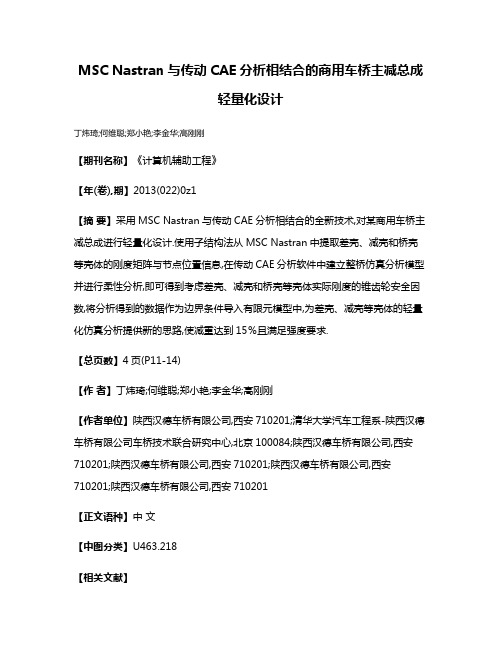
MSC Nastran与传动CAE分析相结合的商用车桥主减总成轻量化设计丁炜琦;何维聪;郑小艳;李金华;高刚刚【期刊名称】《计算机辅助工程》【年(卷),期】2013(022)0z1【摘要】采用MSC Nastran与传动CAE分析相结合的全新技术,对某商用车桥主减总成进行轻量化设计.使用子结构法从MSC Nastran中提取差壳、减壳和桥壳等壳体的刚度矩阵与节点位置信息,在传动CAE分析软件中建立整桥仿真分析模型并进行柔性分析,即可得到考虑差壳、减壳和桥壳等壳体实际刚度的锥齿轮安全因数,将分析得到的数据作为边界条件导入有限元模型中,为差壳、减壳等壳体的轻量化仿真分析提供新的思路,使减重达到15%且满足强度要求.【总页数】4页(P11-14)【作者】丁炜琦;何维聪;郑小艳;李金华;高刚刚【作者单位】陕西汉德车桥有限公司,西安710201;清华大学汽车工程系-陕西汉德车桥有限公司车桥技术联合研究中心,北京100084;陕西汉德车桥有限公司,西安710201;陕西汉德车桥有限公司,西安710201;陕西汉德车桥有限公司,西安710201;陕西汉德车桥有限公司,西安710201【正文语种】中文【中图分类】U463.218【相关文献】1.基于非线性分析软件的某重型商用车桥鼓式制动器轻量化设计 [J], 丁炜琦;郑小艳;苏武;张龙2.基于传动CAE分析与MSC.Nastran的某商用车桥主减总成正向设计 [J], 何维聪;张龙;郑小艳;郭飞航3.基于MSC Nastran及整车模型的动力总成悬置解耦分析和优化方法 [J], 樊红光;昝建明;王卓4.MSCNastran与传动CAE分析相结合的商用车桥主减总成轻量化设计 [J], 丁炜琦;何维聪;郑小艳;李金华;高刚刚;5.MSC/NASTRAN,MSC/PATRAN世界公认的CAE工业标准 [J], 无因版权原因,仅展示原文概要,查看原文内容请购买。
HEV变速器壳体开裂失效分析

HEV变速器壳体开裂失效分析作者:许立黄敏鸫李艳华韦贤毅来源:《时代汽车》2023年第19期摘要:某混动车型变速器壳体测试过程开裂,对开裂的变速器壳体从化学成分、金相、硬度、夹杂物、针孔度、扫描电镜进行检测分析,发现开裂位置存在明显的针孔缺陷。
同时扫描电镜检测微观形貌发现壳体开裂部位大量气孔富集形成密集孔洞。
从优化整车总布置,优化壳体铸造工艺降低壳体针孔度等级,改善变速器产品机构提升壳体的铸造工艺性三方面提出了壳体改善措施。
关键词:铝合金壳体失效分析针孔度改善措施近年来,随着国家战略的引导和人们生活品质提高的需要,纯电动汽车和混动汽车获得了快速发展。
而汽车重量对混动汽车燃油经济性和纯电动汽车的续航里程起着决定性作用,车重每降低100kg,油耗可减少0.7L/100km[1]。
根据业内的共识,簧下质量减重降油耗效果显著优于簧上质量,在动力底盘零件设计过程中,为了降油耗产品工程师会依据CAE分析结果,将零件尽可能减薄,譬如文中提到的将某混动车型变速器壳体的壁厚减薄,这往往带来一些新的问题。
除了優化产品结构,汽车降低能耗的途径主要是使用新型轻量化材料。
压铸铝合金因为优异的材料性能、加工的稳定性和比强度高等优点,成为汽车轻量化的热门材料。
高强韧铝合金压铸件从上世纪90年代起开始批量应用,近年来铝合金压铸件逐步替代铸铁,用量逐年增加,并广泛应用于汽车变速器壳体、发动机部件和汽车轮毂等等。
随着汽车工业技术的进步,大部分铝合金制造的汽车零部件向壁薄、高强度、高质量、高可靠性方向发展。
德国莱茵铝合金公司研究的新型压铸铝合金:Magsimal-59、Silafont-36与Castasil-37,通过控制Fe元素的含量,实现标准圆棒试样在铸态下断后延伸率达到17%,并成功应用于汽车车门制造。
王海东等对Al-Si-Mg系合金中添加微量元素Ti时,能有效细化晶粒,显著提供铝合金的抗拉强度和屈服强度,添加微量Zr或Sr元素,铝合金的力学性能显著改善,为制造铝合金汽车车身、吸能件提供了解决方案[2-3]。
- 1、下载文档前请自行甄别文档内容的完整性,平台不提供额外的编辑、内容补充、找答案等附加服务。
- 2、"仅部分预览"的文档,不可在线预览部分如存在完整性等问题,可反馈申请退款(可完整预览的文档不适用该条件!)。
- 3、如文档侵犯您的权益,请联系客服反馈,我们会尽快为您处理(人工客服工作时间:9:00-18:30)。
基于CAE分析的变速器壳体优化Optimization of transmission Housing Based onCAE Analysis姜志明(上海汽车变速器有限公司产品工程部上海201800)摘要: 本文以某公司自主研发的DCT变速器壳体多工况下的优化设计为例,论述了变速器壳体优化设计的详细流程,通过有限元的拓扑优化设计平台,为变速器壳体优化设计提供了较好的理论依据,在多种工况下可以极快地找到产品优化区域结构形状,提高了产品的研发质量与效率。
关键词: 变速器壳体设计静态分析模态分析拓扑优化Abstract:This thesis is based on the example of optimization design of a double-clutch transmission (DCT) housing developed under several load cases. This thesis focuses on detailed optimal design procedures of transmission housing through CAE topology optimization design platform, which not only provides good theoretical basis for optimization design of the transmission housing, but also can quickly obtain structure shape of the product 's optimization area with different load cases. Thus, the product R&D quality and efficiency can be improved. Key words: Transmission, Housing design, Static Analysis, modal analysis, Topology Optimization1前言变速器壳体为变速器的关键零件,其内安装着变速器齿轮、轴、轴承等重要零部件,通过壳体使变速器固定到整车上。
变速器工作时,变速器壳体承担着极其复杂的载荷,又因变速器壳体本身的结构形状复杂,使得受力分析复杂,对于结构强度不好的壳体,想通过人工计算优化出合理的结构形状,是很难实现的事,通过目前成熟的CAE分析正好可以解决这一问题,它通过拓扑优化方法能够在给定的设计空间内寻求最佳的材料分布,可采用壳单元或者实体单元来定义设计空间,并用Homogenization(均质化)和Density(密度法)方法来定义材料流动规律。
通过OptiStruct 中先进的近似法和可靠的优化方法,可以搜索到最优的加载路径设计方案,此外,利用OptiStruct 软件包中的OSSmooth工具,可以将拓扑优化结果生成为IGES等格式的文件,以便在CAD系统中进行方便地输入。
2变速器工作情况2.1变速器壳体工况此变速器壳体在悬置考核时,需承受31个工况考核要求,其中25(reverse extreme torque 逆向极限扭矩)、30(Extreme dynamic forward torque动态向前转矩)、31(Extreme dynamic reverse torque极端动态反向转矩)三工况以离合器壳体通过与发动机连接作为约束,通过给安装变速器离合器壳体的扭矩支撑架及安装于离壳体的支撑架施加力(如图1所示),分析结果显示在该变速器离合器壳体的通风窗口区域主应力超差(如图2所示),为此需对该壳体进行优化设计以满足综合应力要求。
该区域各工况应力大小如下表所示:图1 图2 工况 综合应力(MPa )第一主应力(MPa)考核要求 25 110 120 综合应力小于240MPa 及第一主应力小于160MPa30 130 50 31175173.33 变速器壳体优化空间的建立与验证3.1变速器壳体优化空间的实体三维建立离合器壳体通风窗口区域处因受安装限制,因此通风窗口处本身直接建立优化空间是很有限,必须另找优化空间。
结合装配加工等情况,依次在原设计产品(图3)上建立不可设计空间(图4)、可设计空间(图5)及组合三维(图6)。
图3 图4 图5 图63.2变速器壳体优化空间有限元模型的建立将上述建好的组合三维模型导入CAE 软件中,建立有限元三维网络。
为了保证有限元优化处可设计空间与变速器壳体不可设计空间三维网格力的传递,二网格结合处必须共结点,否则,力不能达到正确传递。
3.3变速器壳体优化空间的验证可设计空间除了满足变速器安装性能外还必须保证优化后壳体的应力达到壳体考核目标值,因此,须对包括整个设计空间在内的实体考虑进来后,对应力分析进行一次评估,只有通过评估后的优化空间才有优化意义。
经过分析计算,加上设计空间范围处的窗口的各应力如下:工况 综合应力(MPa )第一主应力(MPa)考核要求2593 106 综合应力小于240MPa 及第一主应力小于160MPa30 110 82 31120130通过上表显示较差的31工况其主应力仍有30MPa应力可变动空间,别的工况设计应力可变动空间更大,可见此设计空间的定义是合理的。
4 变速器壳体优化空间有限元模型边界条件等的建立4.1添加材料创建出各相连接的金属材料,可参考手册等。
4.2设置属性划分优化区域及非设计区域,因为拓扑优化区域是由属性来识别的,所以通过多个属性可区分设计及非设计区域,本例中将所示的大块设置为设计区域,其他为非设计区域。
4.3 连接关系建立使用RBE2单元将离合器壳、主壳体、发动机壳体等相关工作零部件连接起来。
4.4 建立边界条件根据发动机的工况,对发动机进行六自由度的全约束。
4.5 施加载荷根据25、30、31工况分别给相关零件施加载荷。
4.6 建立工况利用上两步所创建出的边界条件及载荷分别组合起来创建出25、30、31三种工况。
4.7 建立拓扑优化变量使进入Optimization 模块Topology 菜单选择设计区域属性,类型选择PSOLID 创建优化变量,进入Draw 面板设置拔模方式为SPLIT 选择从中心面往外两侧拔模,如图所示,Obstacle 选择非设计区域属性。
4.8 建立优化响应进入response 面板分别建立类型为Volumefrac、Weighted Comp的连个相应,其中Weighted Comp 在Loadstep 中将25、30、31三种工况都选中且权重均衡。
4.9建立优化约束进入Dconstraints 面板选择上一步所建立的类型为Volumefrac 的响应,设置其上限值0.3。
4.10 建立优化目标进入Objective 面板,选择第4.8步所创建的类型为Weighted Comp 的响应设置其目标为最小。
4.11 提交求解保存.fem 文件,设置合适的内存空间后调用OptiStruct解算器进行求解。
4.12 优化结果后处理经过4步的迭代,结果收敛。
打开HyperView 查看结果,将单元密度阀值设置为0.3 ,结果如图7所示。
图7返回HyperMesh窗口,在后处理Post 面板将第4步结果读入,并使用OSSmooth 命令将优化后的单元格光顺成ISO 曲面,ISO 曲面阀值同样取0.3。
5变速器壳体模型再建5.1 模型再建参考输出的结果曲面,利用CAD 软件重建三维模型,如图8及图9所示:图8 图95.2 重建后的模型验证5.2.1三种工况下力学性能对比验证工况综合应力(MPa ) 第一主应力(MPa)优化前加设计空间优化后 优化前 加设计空间优化后 25 110 93 101 120 106 110 30 130 110 120100 82 91 31 175120145173.31301495.2.2模态分析验证分别对优化前及优化后整个变速器壳体组件约束后进行模态分析,优化前及优化后模型的前三阶振形对应的固有频率如下表所示,可见优化后模型其刚度值有提高。
66.1概念设计阶段时的应用变速器壳体概念设计时,可将变速器壳体的轴承等基本的特征建立,并建立好齿轴相关的安装空间,将这些建好的特征作为不可设计空间,再建立大的区域作为可设计空间(图10所示)。
根据变速器的工况作为输入条件进行约束,对可设计空间进行拓扑优化。
通过拓扑优化出的结果(图11、图12所示),可以寻找得到壳体的最优结构及加强筋分布合理的概念设计(图13)。
图10 图11 图12 图13 7结论1)产品设计优化时应尽可能获取大的产品设计空间,只有设计空间大,满足设计要求的希望就越大,越容易达到设计目标。
2)采用CAE 拓扑优化的结果虽在显示上还是比较粗糙的,但它提供了产品优化设计材料合理分布的区域,实际的结构还需要考虑很多方面的问题,如成本、工艺等。
3)经过分析比较,经过CAE 拓扑优化设计的新壳体较原壳体在性能上有很大提升,满足了设计要求,说明该方法是可靠合理的,为产品特别是变速器壳体等异形件类优化设计提供了一种有效的方法。
8 参考文献[1] 于开平,周传月,谭惠丰等。
HyperMesh 从入门到精通[M]。
北京:科学出版社,2005(数码工程师系列丛书)[2] 胡纪滨、王杰、周毅。
液压机械变速器箱体有限元分析与改进 [J]。
机械设计,2006,23(11):46-48。