刀具应用几何角度的分析及.
刀具切削部分的几何形状和角度解析

三、刀具切削部分的几何角度
1、度量刀具角度的参考系
刀具静止参考系 ——用于定义刀具在设计、 制造、刃磨和测量时刀 (标注角度) 具几何参数的参考系。
刀具工作参考系 ——规定刀具进行切削加工
(工作角度) 时几何参数的参考系。
2、刀具静止参考系
基面pr ——过切削刃选定点平行 或垂直刀具安装面(或轴线)的 平面。
尖形刀尖
修圆刀尖
倒角刀尖
主讲: 骆志强
一、 刀具的组成部分
刀体 ——刀具上夹持刀条或 刀片的部分。 刀柄 ——刀具上的夹持部分。 刀头 ——担负切削工作,又 称切削部分。
二、刀具切削部分的组成
ຫໍສະໝຸດ 前刀面Aγ ——切屑沿其流出的表面。 主后刀面Aα ——与过渡表面相对的面。 副后刀面Aαˊ ——与已加工表面相对的面。 ——前刀面与主后刀面相交形 成的刀刃。 主切削刃 S ——前刀面与副后刀面相交形 副切削刃 Sˊ 成的刀刃。 ——主、副切削刃连接处的一小部分 刀尖 切削刃。(刀尖类型)
主偏角κr ——主切削平面 与假定工作平面之间的夹角。 ——副切削平 面与假定工作平面之间的夹 副偏角κr ˊ 角。 ——主切削平面 刀尖角εr 与副切削平面之间的夹角。
思考: κr 、 κr ˊ 、 εr 之间的 关系? εr =180°-( κr + κr ˊ ) (3)在切削平面中测量的角度
切削平面ps ——过切削刃选定点 与切削刃相切并垂直于基面的平 面。 正交平面po ——过切削刃选定 点同时垂直于切削平面和基面的 平面。 法平面Pn ——过切削刃选定点 并垂直于主切削刃的平面。
正交平面参考系
刀具几何角度的作用及选择原则

刀具几何角度的作用及选择原则刀具的几何角度对加工质量、切削力和切削温度等有很大的影响,正确的选择刀具几何角度可以提高切削效率和工件表面质量。
本文将从切削角、主偏角、切削刃前角和切削刃后角四个方面来探讨刀具几何角度的作用及选择原则。
一、切削角切削角是刀具主切削面与工件切削表面的夹角,一般分为正的和负的两种情况。
1.正切削角:也称为刀具顶角,是指刀具主切削面与工件切削表面夹角大于90°的情况。
正切削角有利于降低切削力和切削温度,减少刀具磨损。
因此,在切削硬材料或脆性材料时,一般选择正切削角。
但是正切削角也会增大刀具与工件接触面积,增加切削力,从而需要更大的功率投入。
2.负切削角:也称为刀具反角,是指刀具主切削面与工件切削表面夹角小于90°的情况。
负切削角能降低切削力和切削温度,提高切削稳定性和切削质量。
因此,在切削软材料或难切削材料时,一般选择负切削角。
然而,负切削角的刀具易产生振动,增加切削噪声,且不易控制切削深度。
在实际应用中,切削角的选择应根据材料的性质、切削目标和加工条件综合考虑,一般需要通过试切试验来确定最佳切削角。
二、主偏角主偏角是刀具俯仰角,是指刀具主切削面与铣削切削方向之间的夹角。
主偏角的大小会直接影响刀具的切削力和切削质量。
1.大主偏角:大主偏角可以降低刀具的切削力和切削温度,提高切削稳定性和切削质量。
大主偏角适用于切削精度要求高、切削深度相对较小、切削速度相对较低的情况。
2.小主偏角:小主偏角可以提高刀具的切削效率和切削速度,适用于切削深度相对较大、切削速度相对较高的情况。
然而,小主偏角容易导致切屑的卡刀现象,增加刀具磨损和加工表面粗糙度。
主偏角的选择应结合切削效率和切削质量的要求,同时考虑刀具的刚度和加工条件等因素。
三、切削刃前角切削刃前角是刀具切削刃前的锥度角,主要影响刀具的切削稳定性和切削质量。
1.大切削刃前角:大切削刃前角可以增加切削深度和切削范围,提高切削效率和切削速度。
刀具几何角度的基本定义与标注及工作角度解读
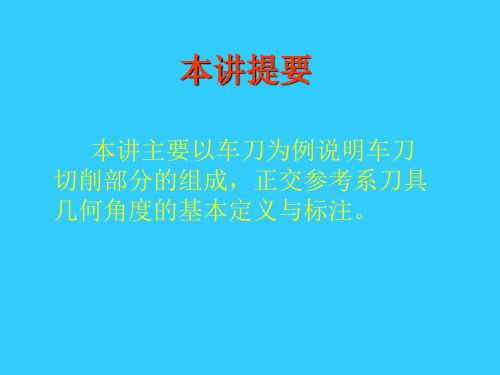
2. 正交平面参考系(pr-ps-po)
基面Pγ: Pγ⊥Vc 、 ∥刀具安装面(车刀) 切削平面• Ps: 与 S相切 且 ⊥Pγ 正交平面Po: Po⊥Pγ⊥Ps
3 .法剖面Pn和法剖面参考系 (pr-ps-pn)
法剖面Pn是通 过切削刃选定点, 垂直于切削刃的平 面。 法平面Pn:Pn⊥S
假定工作平面背平面参考系立体图示前角o正负图示立体图示后角o正负图示在基面内测量主偏角r副偏角rs在基面上的投影与v的反向主偏角r和副偏角r立体图示在切削平面上测量刃倾角s刃倾角s立体图示刃倾角s正负图示平面图示法角度标注一刀具的工作参考与工作角度工作正交平面参考系过s选定点垂直于合成切削速度方向相切于s且垂直于pre过s选定点垂直于pre且垂直于pse2
刀 面
(2)后刀面Aα
(3)副后刀面A`α
切 削 刃
(4)主切削刃s 主切削刃指前刀面与主后刀面相交的锋边。 (5)副切削刃s ` 副切削刃指前刀面与副后刀面相交的锋边。 (6)刀尖 刀尖可以是主、副切削刃的实际交点,也 可以是主、副两条切削刃连接起来的一小段切削刃,它 可以是圆弧,也可以是直线,通常都称为过渡刃
二、刀具标注角度参考系-----过切削刃上选定点
1 两个假定条件
(1)假定运动条件:首先给出刀具的假定主运动方向和假定进给运
动方向;其次假定进给速度值很小,可以用主运动向量vc近似代替
合成速度向量ve;然后再用平行和垂直于主运动方向的坐标平面 构成参考系。
即:假定进给运动速度Vf=0
(2)假定安装条件:假定标注角度参考系的诸平面平行或垂直于刀具 便于制造、刃磨和测量时定位与调整的平面或轴线(如车刀底面、 车刀刀杆轴线、铣刀、钻头的轴线等)。反之也可以说,假定刀具 的安装位置恰好使其底面或轴线与参考系的平面平行或垂直。
刀具几何角度测量实验报告

刀具几何角度测量实验报告实验报告:刀具几何角度测量摘要:本实验旨在通过测量刀具几何角度来了解刀具的性能及其对加工质量的影响。
实验采用光学显微镜和测量仪器进行刀具几何角度的测量,实验结果显示,切削角、主偏角和微观前后角对切削力和面粗糙度有着较大的影响,通过调整刀具几何角度来优化加工效果是十分必要的。
引言:刀具是机械加工中关键的工具之一,其性能直接影响加工质量和加工效率。
刀具几何角度作为刀具的重要性能参数,包括切削角、主偏角、微观前后角等,在切削加工过程中发挥着重要的作用。
为了更好地了解刀具几何角度的影响,本实验采用光学显微镜和测量仪器进行几何角度的测量与分析。
实验方法:本实验使用一台光学显微镜和测量仪器对刀具进行测量,其中主要包括以下步骤:1. 准备刀具及测量仪器:选择一把常用平面铣刀、高感度液压感应测力仪、三次元测量仪和激光扫描显微镜等测量仪器。
2. 测量几何角度:使用光学显微镜和测量仪器对刀具的切削角、主偏角、微观前后角等几何角度进行测量和记录。
3. 分析实验结果:对实验所得数据进行统计分析,分析切削角、主偏角、微观前后角等几何角度的影响,并结合实际加工情况进行讨论。
实验结果:通过实验所得数据的统计分析,我们发现:1. 切削角对切削力有着重要的影响,当切削角变大时,切削力也相应地增大。
2. 主偏角对刀具的刃口强度和切削性能有着显著的影响,当主偏角变大时,刀具的刃口强度会相应变弱,加工效果也会受到影响。
3. 微观前后角是影响切削力和面粗糙度的重要因素,过大或者过小都会对加工过程产生影响。
结论:通过对刀具几何角度的测量与分析,我们发现,刀具几何角度对切削力、面粗糙度和加工效果均有着显著的影响,在实际加工中需要加以注意和调整,以便更好地利用刀具的性能优势,优化加工效果。
此外,我们也认识到,几何角度的测量和调整对提高刀具性能的重要性和必要性。
刀具切削部分的几何形状和角度解析

❖ 前角γo ——前刀面与基面 之间的夹角。
❖ 后角αo ——主后刀面与切 削平面之间的夹角。
❖ 楔角βo ——前面与后面的 夹角。
思考:γo、 αo、 βo 之间的关系?
βo=90°-( γo +αo )
(2)在基面中测量的角度
❖ 主偏角κr ——主切削平面 与假定工作平面之间的夹角。 ——副切削平
——前刀面与主后刀面相交形 ❖ 主成切的削刀刃刃S。
——前刀面与副后刀面相交形 ❖ 副成切的削刀刃刃S。ˊ
——主、副切削刃连接处的一小部分 ❖ 刀切尖削刃。(刀尖类型)
车刀的切削部分
三、刀具切削部分的几何角度
1、度量刀具角度的参考系
刀具静止参考系 ——用于定义刀具在设计、 (标注角度) 制造、刃磨和测量时刀 具几何参数的参考系。
❖ 后角αo :后刀面与基面之间的夹角为锐角,后角为正,夹角为钝 角,后角为负值。
❖ 刃倾角λs :刀尖是主切削刃上最高点时刃倾角为正,刀尖位于主 切削刃上最低点时刃倾角为负,主切削刃与基面平行时刃倾角为 零。
尖形刀尖
修圆刀尖
倒角刀尖
谢谢观赏!
13
谢谢!
刀具工作参考系 ——规定刀具进行切削加工 (工作角度) 时几何参数的参考系。
2、刀具静止参考系
❖ 基面pr ——过切削刃选定点平行 或垂直刀具安装面(或轴线)的 平面。
❖ 切削平面ps 面po ——过切削刃选定 点同时垂直于切削平面和基面的 平面。
❖ 法平面Pn ——过切削刃选定点 并垂直于主切削刃的平面。
正交平面参考系
❖ 假定工作平面pf ——通过 切削刃选定点并垂直于基面 的平面,一般其方位平行于 假定的进给运动方向。
如何合理的选取车刀的几何角度

如何合理的选取车刀的几何角度
1、前角γ0(在正交面的上测量的前刀面与基面之间的夹角)。
它表示前刀面的倾斜程度。
前角越大,刀刃越锋利,切削时就越省力。
但前角过大会削弱刀头强度,影响刀具的寿命。
前角的选取决定于工件材料、刀具材料和加工性质。
硬质合金车刀γ0通常取-5º~+25º。
2、后角α0。
在正交平面上测量的主后刀面与切削平面之间的夹角。
它表示主后刀面的倾斜程度。
后角的作用主要是减少刀具与加工表面之间的摩擦,后角越大,摩擦越小,但后角过大会削弱切削刃的强度及耐用度。
一般取α0为60~120。
3、主偏角k r。
主切削刃在基面上的投影与进给方向之间的夹角。
主偏角能影响主切削刃和刀头受力情况及散热情况。
加工强度、硬度较高的材料时,应选较小的主偏角,以提高刀具的耐用度。
加工细长工件时,应选较大的主偏角,以减少径向切削力引起工件的变形和振动。
一般取k r为300~900。
4、副偏角k r'。
副切削刃在基面上的投影与进给反方向之间的夹角。
副偏角的作用是减少副切削刃与工件已加工表面之间的摩擦。
副偏角越大,摩擦越小。
但k r过大,又会增大已加工表面的粗糙度。
一般取k r为50~150。
车刀的几何角度:。
刀具几何角度的认识及测量

刀具几何角度的认识及测量一、实验目的1. 掌握测量车刀几何角度的方法。
2. 进一步理解车刀各几何角度的定义及其标注方法。
3. 认识端铣刀、麻花钻、铰刀、扩孔钻、齿轮滚刀等典型刀具的角度。
二、实验要求1.熟悉所给的车刀结构和万能车刀量角台的使用方法。
2.用万能车刀量角台测量车刀的六个基本角度:γo、αo、λs、κr、κr’、αo’3.绘图表示所给外圆车刀的几何角度。
4.观察了解实验中所用各种典型刀具的刀具结构和角度。
图1 万能车刀量角台三、实验方法和步骤1.万能车刀量角台的使用方法本实验所用万能车刀量角台结构如图1所示。
测量每个角度时,应首先利用量角台的可调部分找到度量平面位置和构成该角的平面(或直线)的位置。
本量角台有紧固手柄2和8。
本体3上有B、A刻线,可分别与立柱4的垂直刻线5和回转盘6 的任意刻度重合。
松开手柄2,可使本体3连同刻度板9一起绕立柱4 的轴线回转,还可以将刻度板调到适当高度。
松开手柄8,可使回转盘6连同刻度板一起绕水平轴线回转。
刻度板还可在支撑板7的水平槽内滑动。
在底座1的上方,刻度板可调到任意位置,即可调到与底座的顶面(刀杆定位面)平行,也可以调到与底座顶面垂直或斜交。
刻度板所在平面,可用来代表所测量角度的度量平面(基面,切削平面,主剖面——即正交平面)。
指度片10可绕其轴在刻度板上转动,其作用是用来指示所测角度的值。
刻度板每格为2°。
当刻度板位于主剖面(正交平面)位置,而指度片尖端对准刻度板0°刻线时,此时指度片E边和F(或F’)边分别平行和垂直于底座顶面,即E边代表基面,F(或F’)边代表切削平面。
若将E、F(或F’)的任意一边与被测刀面或刀刃贴合(以不漏光为限)时,即可按定义测得所需的角度值。
可见,指度片上的E或F(或F’)边在0°位置和它与刀面或刀刃贴合时的位置,分别代表了构成所测角度的两个平面(或两条直线)。
底座上有两个定位销11,在测量主偏角和副偏角时,是用来对刀杆侧面定位的。
刀具几何角度的测量实验报告

刀具几何角度的测量实验报告刀具几何角度的测量实验报告引言:刀具在机械加工领域中起着至关重要的作用。
而刀具的几何角度对于其性能和加工效果有着直接的影响。
因此,准确测量刀具的几何角度是非常重要的。
本实验旨在通过一系列测量实验,探究刀具几何角度的影响以及测量方法的准确性。
实验一:刀具的切削角度测量在切削过程中,刀具的切削角度直接影响着切削力和切削刃的寿命。
本实验使用了专用的角度测量仪器,通过将刀具固定在测量仪器上,准确测量了刀具的切削角度。
实验结果显示,切削角度的大小与切削力呈正相关关系。
较大的切削角度可以减小切削力,但过大的切削角度会导致切削刃的过早磨损。
因此,在实际加工中,需要根据具体情况选择适当的切削角度。
实验二:刀具的前角度测量刀具的前角度是指刀具刃的前面与切削面之间的夹角。
该角度的大小直接影响着切削刃的尖锐度和切削质量。
本实验使用了光学显微镜,通过观察切削刃的形态,测量了刀具的前角度。
实验结果显示,较小的前角度可以使切削刃更加尖锐,提高切削质量。
然而,过小的前角度会导致切削刃容易损坏。
因此,在实际加工中,需要根据材料的硬度和切削条件选择适当的前角度。
实验三:刀具的后角度测量刀具的后角度是指刀具刃的后面与切削面之间的夹角。
该角度的大小对切削刃的排屑性能和切削质量有着重要影响。
本实验使用了扫描电子显微镜,通过观察切削刃的形态,测量了刀具的后角度。
实验结果显示,较小的后角度可以改善切削刃的排屑性能,提高切削质量。
然而,过小的后角度会导致切削刃的容易断裂。
因此,在实际加工中,需要根据切削材料的特性选择适当的后角度。
实验四:刀具的侧后角度测量刀具的侧后角度是指刀具刃的侧面与切削面之间的夹角。
该角度的大小对切削刃的切削力和切削质量有着重要影响。
本实验使用了数字显微镜,通过测量切削刃的形态,准确测量了刀具的侧后角度。
实验结果显示,适当的侧后角度可以减小切削力,提高切削质量。
然而,过大的侧后角度会导致切削刃的易损性增加。
- 1、下载文档前请自行甄别文档内容的完整性,平台不提供额外的编辑、内容补充、找答案等附加服务。
- 2、"仅部分预览"的文档,不可在线预览部分如存在完整性等问题,可反馈申请退款(可完整预览的文档不适用该条件!)。
- 3、如文档侵犯您的权益,请联系客服反馈,我们会尽快为您处理(人工客服工作时间:9:00-18:30)。
目录1刀具几何角度 (1)1.1正交平面参考系 (1)1.2刀具的静态角度 (2)1.2.1几种车刀几何角度图例 (3)1.3.1角度变化原因 (4)1.3.2角度变化规律 (7)2车刀前角的分析与应用 (9)2.1前角在加工中的作用 (9)2.2前角大小的应用 (12)2.3刃磨前角时的角度参考值 (16)3车刀后角的分析与应用 (16)3.1粗车时后角大小的分析与应用 (16)3.2精车时后角大小的分析与应用 (17)3.3加工脆性材料时后角的分析与应用 (19)3.4实例 (20)4车刀主偏角的分析与应用 (21)4.1主偏角为90°车刀的分析与应用 (21)4.2主偏角为75°车刀的分析与应用 (24)4.3主偏角为45°车刀的应用 (25)5车刀的其他角度的分析与应用 (26)5.1车刀的副偏角 (26)5.2刃倾角的分析与应用 (27)结论 (29)致谢 (30)参考文献 (31)摘要在机械加工中,金属切削刀具的几何参数的合理选择直接影响到机械加工的质量、刀具耐用度、生产效率和加工成本。
因此,机械加工中,正确选用刀具角度以及如何获得所选刀具角度的大小,尤其显得重要。
俗话说:“三分工艺,七分刀具”,这充分说明刀具角度在机械加工中的突出地位。
一把刀具切削性能的好坏主要取决与制造刀具的材料、刀具的结构、刀具切削部分的几何参数。
其中刀具材料固然重要,但刀具材料和刀具结构确定之后,刀具切削部分的几何参数对切削性能的影响就成为十分重要的因素。
这些几何角度对车削过程影响很大,其中尤其是以前角、后角、主偏角、刃倾角、副偏角κ'r影响更为重要,科学合理的选择车刀的几何角度,对车削工艺的顺利实施,保证工件的加工质量起着决定性的作用。
下面就着手分析刀具的几何角度及在加工中的应用。
关键词:前角;后角;主偏角;刃倾角;副偏角1刀具几何角度车刀是车工的主要切削刀具,但它也可以用于其他的切削加工,如镗削加工、铣削加工、刨削加工、钻削加工等。
在切削加工中,车刀角度的好与不好,将直接影响加工生产率和加工质量,因此充分认识和了解车刀的结构及其相关要素。
1.1正交平面参考系刀具要从工件上切下金属,就必须具备一定的切削角度,这些角度决定了刀具切削部分各表面的空间位置,为了确定刀具上刀面及切削刃在空间的位置,首先应建立空间参考系。
用来确定刀面和刀刃空间位置的正交平面参考系(如图1-1),即切削平面(Ps)、基面(Pr)、正交平面(Po)。
图1-1 正交平面参考系测量平面的定义名称定义基面过车刀主切削刃上某一选定点,并于该点切削速度方向垂直的平面切削平面过车刀主切削刃上某一选定点,并于工件的过渡表面相切的平面正交平面过车刀主切削刃上某一选定点,同时垂直于切削平面和基面的平面1.2刀具的静态角度刀具在正交平面参考系中定义的静态角度有前角(γ)、后角(α0)、主偏角(κr)、副偏角(κ'r)、刃倾角(λs)、副后角(α′o)六个基本角度,如图(1-2)。
1.在正交平面内测量的角度有:(1)前角:前刀面与基面之间的夹角(2)后角:后刀面与切削平面之间的夹角(3)楔角:前刀面与后刀面之间的夹角2.在基面内测量的角度有:(4)主偏角:主切削刃在基面上的投影与进给运动方向的夹角(5)副偏角:副切削刃在基面上的投影与背离进给运动方向的夹角(6)刀尖角:主切削刃和副切削刃在基面上的投影之间的夹角3.在切削平面内测量的角度(7)刃倾角:主切削刃与基面之间的夹角1-2车刀切削部分主要角度1.2.1几种车刀几何角度图例【例1】90°外圆车刀角度,如图1-3所示。
【例2】镗孔车刀角度图,如图1-4所示。
图1-4 镗孔车刀几何角度1.3角度变化及其变化规律1.3.1角度变化原因上述六个基本角度,即前角、后角、副后角、主偏角、副偏角、刃倾角是在两个假设条件下定义出来的,即运动条件和安装条件。
例如图1-5所示的切槽刀的γ0 、 α0 就是下面两个假设条件下定义出来的。
图1-5 切槽刀的γ0 、 α0①只有工件旋转运动,没有车刀进给运动;②切槽刀安装时,其刀刃和工件中心等高,其刀身轴线和工件轴线垂直。
在这种条件下,其通过刀刃O 点的切削速度v 的方向垂直向上,通过刀刃O 点的基面Pr 成水平位置,切削平面Ps 成垂直位置。
而前角、后角就在主剖面Po 内表示出来。
但车刀在工作时,这两个假设条件会被突破。
要切下金属层,不仅有主运动,还必须有进给运动,这是其一;另外,车刀安装时也不可能百分之百地使刀尖和工件中心等高、刀身轴线和工件轴线垂直,总是将车刀装高了或装低了。
到此假设条件突破后,就会使车刀按照假设条件磨出的角度发生变化,以上以切槽刀为例分析角度变化情况。
1突破安装条件①当车刀装高时,如图1-6所示。
图1-6车刀装高时γ0 、α0的变化从图看出有三者发生了变化;其一,切削速度v方向发生了变化。
由于刀刃装高于工件中心,此时通过刀刃上一点的切削速度应在该点与工件半径垂直。
这样切削速度就由假设条件下的垂直位置变成倾斜位置。
其二,几面位置由水平变化成倾斜。
根据基面的规定可知,此时的基面为垂直Ve的工作基面(Pre)。
其三,切削平面由垂直位置变成倾斜位置。
根据切削平面的规定可知,则此时的切削平面为Ve方向并和加工表面相切的平面,即工作切削平面(Pse)。
由于上面这些基准面变化,也就导致了前角γ0、后角α、发生变化,刃磨的前角变为工作基面于前刀面之间的夹角,即工作前角(γOe)。
刃磨后角变为工作切削平面与后刀面之间夹角,即工作后角(αoe)。
②当车刀装低时,如同1-7所示。
也导致γ0发生变化:刃磨前角变成工作前角,刃磨后角变成工作后角。
图1-7 切槽刀装低时γ0 、α0变化2突破运动条件不仅有主运动,而且还有进给运动,如图1-8所示。
图1-8 有进给运动时角度变化当有进给运动时,其切削速度的方向变成由v和f两速度的合成速度v e方向,即由垂直位置变成倾斜位置。
根据基面的平面规定,则基面由水平位置成倾斜位置为图中的Pr变成工作基面Pre。
同理,则切削平面由垂直位置变成倾斜位置为图中的Ps变成工作切削平面Pse。
由于基面和切削平面的位置发生变化,也就导致前角和后角发生变化,刃磨的前角变成工作前角γoe,刃磨的后角变成工作后角αoe。
由上述讨论就可以得出影响车刀角度变化的原因:车刀工作时,由于车刀安装位置发生变化和进给运动的影响,而突破了定义车刀角度的假设条件,从而导致基准平面的位置发生变化,而导致车刀角度发生变化。
既然,车刀工作时,刃磨的角度要发生变化,这必然会影响刀具的性能,进而影响切削加工。
因此,必须进一步研究角度的变化规律,并掌握这些角度变化规律,以便于我们正确地使用好车刀。
1.3.2角度变化规律1.车刀安装时变化规律①车刀装高于工件中心时,如图1-6所示。
前角变大为:γoe=γ0+θ。
后角变小为:α oe=αo-θ。
式中θ—增大或减小角度,可用下式计算,从图中直角三角形可得sinθ=2h/d;h—刀具装高值,mm;d—工件直径,mm;结论:刀具装高时,刀具角度变化规律是前角增大、后角减小。
②车刀低于工件中心时,如图1-7所示。
前角变小为:γoe=γ0-θ。
后角变大为:α oe=αo+θ。
结论:刀具装低时,刀具角度变化规律是前角减小、后角增大。
在生产实践中,我们在使用车刀时就有利于用这一规律。
比如在粗车圆柱形工件时总把车刀装高一点,使其前角增大,使切削轻快、省力,从而提高了生产效率。
而在精加工时,总把车刀装低一些,以增大后角,可减小后刀面对工件表面的挤压和摩擦。
有利于工件加工表面的质量得到保证。
实例1.在车削外圆锥时,经过多次调整小滑板转角,但任然不能校正,再用圆锥套规涂色法检测锥体时,发现两端显示剂擦去,中间不接触。
当重新装夹刀具,使车刀刀尖严格对准工件轴线,再次加工,发现锥面显示剂擦去;在车削内圆锥时,发现中间显示剂擦去,而两端没有擦去,当车刀严格对准工件轴线时,锥面显示剂擦去。
出现以上两种情况的原因,则是因车刀刀尖没有严格对准工件轴线,而形成双曲线误差所致。
因此,车削锥面时,车刀安装的高低,将影响锥面精度。
所以车削圆锥时,一定要把车刀的刀尖严格的对准工件中心。
2.有进给运动时变化规律①横向进给运动时,如图1-9所示。
图1-9 γoe、αo、μ计算图前角变大为:γoe =γ0+μ后角变小为:α oe=αo-μ式中μ—增大或减小的角度,tanμ=f/ν。
在图中由ν、νe、f所构成的直角三角形中设:ν—切削速度,其值为 d;f—进给量。
那么 tanμ=f/πd结论:有进给运动时,刀具角度的变化规律是前角增大、后角减小。
②纵向进给运动时,如图1-10所示为90°车刀纵向车外圆情况。
图1-10 纵向进给运动角度变化由于有纵向进给运动,则切削速度由垂直位置变为偏西的νe(合成速度),导致基面Pr由水平变成上斜的Pre,切削平面Ps由垂直变成偏斜的Pse,从而使前角、后角发生变化。
前角变大为:γoe =γ0+μO后角变小为:α oe=μO-αo式中μ—增大或减小的角度,其值可由式tanμ=f/πd 计算;πd —切削速度(即工件每转线速度);F—每转进给量。
结论:有纵向进给运动时,刀具角度的变化规律是前角增大、后角减小。
由以上研究得出:只要有进给运动,车刀前、后角的变化规律是前角增大,后角减小。
2 车刀前角的分析与应用在生产实践中,我们所磨出的前角,在车削工件时产生严重的“扎刀”现象,而损坏了零件的加工表面,完不成加工任务。
有的车刀前角,在车削工件时非常笨重、吃力;有的总是车不光工件……这些现象。
如何避免或解决,我将作以下探讨。
2.1前角在加工中的作用前角在切削加工中的第一个作用就是影响切削力的大小,造成切削功率消耗的不同,进而影响加工成本。
1.影响切削力老工人师傅有个说法:“力量大小看前角”。
意思是说,切削中所产生大小不同的切削力,主要取决于所磨出的前角大小。
根据分析研究,前角不仅对切削力有影响,而且还是刀具几何角度中对切削力影响最大、最重要的一个因素。
,如图用前角大小不同的两把刀具,在相同的条件下切削相同的切削层 ac2-1所示情况说明。
由于前刀面倾斜程度不同,推挤切削层的作用力方向发生变化,使剪切面OM也随之变化。
当γ0小时,如图2-1(a)前刀面倾斜程度极小,其作用力方向深入金属内部,剪切角ø小,剪切面平坦而变大,导致变形增大,使变形抗力大。
(a)γ0小(b)γ0大图2-1 不同前脚大小对变形影响当γ0大时,如图2-1(b),前刀面倾斜程度大,其作用力Fr方向作用于切削层表面,剪切角ø大,剪切面变小,变形量小,则变形抗力小。