航空发动机叶片用热障涂层的现状
航空发动机涡轮叶片热障涂层应用的关键技术和问题
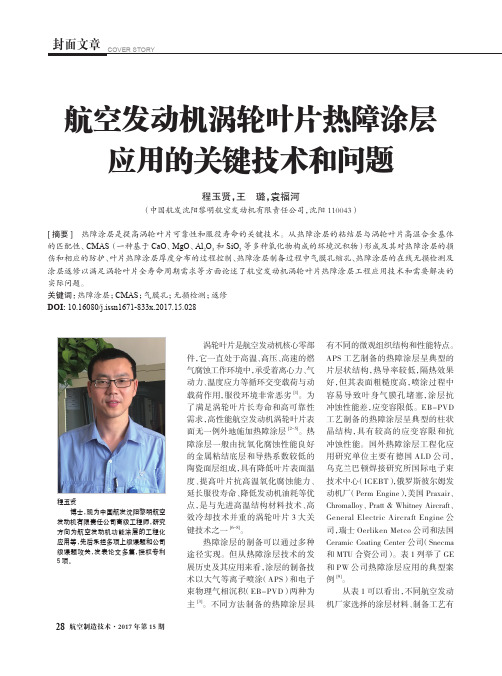
为多孔或柱状晶结构,这些结构会成 能良好,它会沿陶瓷层的微裂纹、孔 渗入(在表层的粘附往往有渗透的现
为腐蚀介质的快速扩散通道,加剧高 洞等逐渐渗入涂层内部,填充陶瓷层 象,可以形成致密层,阻止 CMAS 的
温合金基体的腐蚀)。粘结层的成分 中的空隙,降低陶瓷层的断裂韧性, 渗入);二是阻止渗入后引起的氧化
面,并在高温环境下熔融、渗入涂层 内部,成为影响先进航空发动机热障 涂层寿命的关键因素 。 [23-25]
突然下降时,热障涂层内部的 CMAS 迅速凝固,降低了热障涂层的应变容 限,从而导致涂层发生剥落。对于涡
金属粘结层作为陶瓷面层和高
CMAS 是由于大气中的灰尘、砂 轮叶片热障涂层来说,CMAS 的侵入
匹配所引起的热应力;二是提高整 机循环的峰值温度(如起飞或降落)
国内外针对 CMAS 的防护进行
个热障涂层体系的抗氧化腐蚀性能 时,这些物质形成玻璃态熔融沉积 了大量的研究 [26-29],主要有以下几
(YSZ 陶瓷面层是氧离子导体,且多 物。CMAS 熔体与涂层材料润湿性 个方面:一是阻止 CMAS 熔化后的
程玉贤 博士,现为中国航发沈阳黎明航空
发动机有限责任公司高级工程师,研究 方向为航空发动机功能涂层的工程化 应用等,先后承担多项上级课题和公司 级课题攻关,发表论文多篇,授权专利 5 项。
28 航空制造技术·2017 年第 15 期
涡轮叶片是航空发动机核心零部 件,它一直处于高温、高压、高速的燃 气腐蚀工作环境中,承受着离心力、气 动力、温度应力等循环交变载荷与动 载荷作用,服役环境非常恶劣 [1]。为 了满足涡轮叶片长寿命和高可靠性 需求,高性能航空发动机涡轮叶片表 面无一例外地施加热障涂层 [2-5]。热 障涂层一般由抗氧化腐蚀性能良好 的金属粘结底层和导热系数较低的 陶瓷面层组成,具有降低叶片表面温 度、提高叶片抗高温氧化腐蚀能力、 延长服役寿命、降低发动机油耗等优 点,是与先进高温结构材料技术、高 效冷却技术并重的涡轮叶片 3 大关 键技术之一 。 [6-8]
热障涂层的研究与应用

热障涂层的研究与应用热障涂层(Thermal Barrier Coating,TBC)是一种能够提供高温隔热保护的表面涂层,广泛应用于航空航天、能源、汽车等领域。
本文将介绍热障涂层的研究进展和应用情况。
一、热障涂层的研究进展1. 热障涂层的组成热障涂层通常由两层组成:热障层和粘结层。
热障层主要由氧化锆、氧化钇等陶瓷材料构成,具有良好的隔热性能;粘结层则用于将热障层与基底材料牢固连接。
2. 热障涂层的制备方法目前常用的热障涂层制备方法有物理气相沉积(Physical Vapor Deposition,PVD)和热喷涂(Thermal Spray)两种。
PVD方法包括真空蒸发、磁控溅射等,可以制备出致密、均匀的热障涂层;热喷涂方法包括等离子喷涂、火焰喷涂等,适用于大面积涂层的制备。
3. 热障涂层的性能研究热障涂层的性能研究主要包括热障性能、力学性能和耐热性能等方面。
热障性能是指涂层对热流的隔离能力,可以通过热流测量仪器进行测试;力学性能是指涂层的抗剥离、抗磨损等能力,可以通过拉伸试验、摩擦磨损试验等进行评估;耐热性能是指涂层在高温环境下的稳定性,可以通过高温氧化试验等进行评价。
二、热障涂层的应用情况1. 航空航天领域热障涂层在航空航天领域的应用非常广泛。
例如,热障涂层可以应用于航空发动机的涡轮叶片上,提供高温隔热保护,延长叶片的使用寿命;热障涂层还可以应用于航天器的外壳上,减少外部热流对航天器的影响。
2. 能源领域热障涂层在能源领域的应用主要集中在燃气轮机和燃煤锅炉等设备上。
热障涂层可以提高燃气轮机的燃烧效率,减少能源损失;热障涂层还可以应用于燃煤锅炉的炉膛内壁,提高燃烧效率,减少污染物排放。
3. 汽车领域热障涂层在汽车领域的应用主要体现在发动机部件上。
热障涂层可以应用于汽车发动机的活塞、气缸盖等部件上,提高发动机的热效率,减少燃油消耗;热障涂层还可以应用于汽车排气系统的排气管道上,减少排气温度,降低噪音和排放。
热障涂层在航空发动机涡轮叶片上的应用研究

V l7 o No2 A r2 1 3 p . 0 1
热障涂层在航空发动机涡轮叶片上
的应用研 究
张志强 , 文兴 , 宋 陆海 鹰 ( 中航 工 业沈 阳发 动 机 设 计研 究所 。 阳 10 1 ) 沈 0 5 1
摘要 : 从热 障涂层在 涡轮 叶片的应用需求 出发 , 究 了陶瓷热障涂层 的材 料与制 研
为金 属黏 接层 ,该 材料 即能满 足黏 接 陶瓷层 的要求 ,
是 在 零 件 表 面 沉 积 黏 接 1层 低 导 热 系数 的 材 料 , 利
的主要 因素是涡 轮叶片 的承温能力 。在涡轮 叶片燃气 流道表面喷涂热 障涂层 ,对 提高 叶片承温能力 有非常 直接 的效果 , 并对短 时间的超 温有很好 的缓 解作用 。国 外热障 涂层 在军 、 空发 动机上 已获 广泛应用 , 民航 据资 料介绍 , 可取得 5 ~5 0 10℃ 的隔热效果 。涡轮 叶片工作 温度一般都接 近其材料 的许用温度 ,此 时如果 涡轮 叶 片每降低 1 , 久寿命 约延长 1 。在结 构和冷 5℃ 其持 倍 却效果 不变的条件 下 ,采用热 障涂层技 术可 以使 叶片
2 陶瓷热障涂层的选材 与制备方法
21 陶瓷热 障涂层 ห้องสมุดไป่ตู้料 .
热 障涂层( 简称 T C 技术是 1 B) 种表面处理技术 ,
张志强筹 : 热瞪涂屠在黼空发动柏涡轮口 毙上的啦用酾夯 十
3 B /] g
属基 体 之 间增加 金属 黏接 层 ( 底层 )在 金 属 和 陶瓷之 , 间起 黏 接 和缓 冲热应 力 的作 用 。一般选 用 McAY作 r1
员, 从事航空发动机涡 轮冷却叶片设 计 tri ae h aei n nuatr gapo ho rmi tem lb re o i ubn un,t m t a adma fc i ra c a c h r a a irca n e e r l un p c f e r t g
热障涂层技术在航空发动机涡轮叶片上的应用

- 18 -高 新 技 术0 前言当前,我国的航空产业高速发展,对于各种大型、新型飞机的需求不断增加。
高推重比航空发动机具有较大的推重比、良好的燃油利用性成为现今航空发动机产业重要的发展方向,为提高航空发动机的推重比提高航空发动机涡轮叶片的承温能力以使得温度更高的压缩空气能够进入到航空发动机中是航空发动机推重比提高的重要方式之一。
通过热障涂层应用将能够使得航空发动机涡轮叶片具有更高的承温能力。
1 热障涂层简述热障涂层指的是通过使用陶瓷等材料在物体表面通过喷涂等的工艺方式使其沉积在高温合金或是耐高温金属表面,通过陶瓷等耐高温材料所形成的热障涂层来隔离外部热量,降低基底的温度,据研究表明,通过应用热障涂层将能够有效提高被涂覆物体约60%的热效率。
热障涂层技术实施关键是要通过喷涂等技术将陶瓷等耐热材料以涂层形式与基体进行复合,从而使得基体具有耐高温、耐腐蚀、耐磨损性能。
热障涂层技术的发展和应用关键是要做好耐高温材料等的研究和耐高温材料喷涂和涂层的沉积用以在高温合金基体表面形成隔热障层。
热障涂层是一种表面涂覆技术,其在零部件表面所喷涂材料属于具有低导热系数的材料,在工作的过程中利用材料低热传导特性在材料内外表面形成降温,用以完成对于喷涂零部件的热屏障保护。
一般来说热障涂层所使用材料主要为陶瓷类材料,由陶瓷面层和金属黏结层沟通构成零部件表面陶瓷热障涂层。
热障涂层技术发展至今经过了多次演变,且制备设备也在不断地更新用以满足越来越高的性能指标要求。
总体来说现今应用较多也较为广泛的热障涂层制备法主要有等离子喷涂法和电子束物理气相沉积法。
等离子喷涂法具有喷涂速度快、生产效率高以及可以对多种类型和规格的零部件进行喷涂加工。
但是等离子喷涂法也存在着一定的不足,其对于复杂零部件表面的热障涂层喷涂无法取得良好的喷涂效果,且在喷涂作业中对于热障涂层喷涂的厚度和均匀度也无法进行较为良好的控制,从而导致等离子喷涂法在完成零部件表面的喷涂作业后容易出现厚度不均、表面粗糙等的缺陷。
热障涂层材料的研究和发展
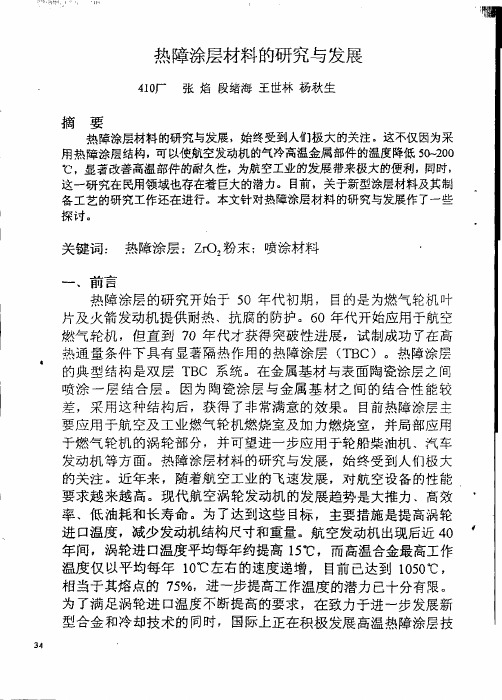
热障涂层材料的研究与发展410厂张焰段绪海王世林杨秋生摘要热障涂层材料的研究与发展,始终受到人们极大的关注。
这不仅因为采用热障涂层结构,可以使航空发动机的气冷高温金属部件的温度降低50----200℃,显著改善高温部件的耐久性,为航空工业的发展带来极大的便利,同时,这一研究在民用领域也存在着巨大的潜力。
目前,关于新型涂层材料及其制各工艺的研究工作还在进行。
本文针对热障涂层材料的研究与发展作了一些探讨。
关键词:热障涂层:ZrO:粉末;喷涂材料~、前言热障涂层的研究开始于50年代初期,目的是为燃气轮机叶片及火箭发动机提供耐热、抗腐的防护。
60年代开始应用于航空燃气轮机,但直到70年代才获得突破性进展,试制成功了在高热通量条件下具有显著隔热作用的热障涂层(TBC)。
热障涂层的典型结构是双层TBC系统。
在金属基材与表面陶瓷涂层之间喷涂一层结合层。
因为陶瓷涂层与金属基材之间的结合性能较差,采用这种结构后,获得了非常满意的效果。
目前热障涂层主要应用于航空及工业燃气轮机燃烧室及加力燃烧室,并局部应用于燃气轮机的涡轮部分,并可望进一步应用于轮船柴油机、汽车发动机等方面。
热障涂层材料的研究与发展,始终受到人们极大的关注。
近年来,随着航空工业的飞速发展,对航空设备的性能要求越来越高。
现代航空涡轮发动机的发展趋势是大推力、高效率、低油耗和长寿命。
为了达到这些目标,主要措施是提高涡轮进口温度,减少发动机结构尺寸和重量。
航空发动机出现后近40年间,涡轮进口温度平均每年约提高15℃,而高温合金最高工作温度仅以平均每年10"(2左右的速度递增,目前已达到1050℃,相当于其熔点的75%,进~步提高工作温度的潜力已十分有限。
为了满足涡轮进口温度不断提高的要求,在致力于进一步发展新型合金和冷却技术的同时,国际上正在积极发展高温热障涂层技术。
实验表明,应用这种技术可以允许提高燃烧室温度50-200。
C,如果在涡轮叶片上等离子喷涂二氧化锆涂层,则可以提高涡轮进口温度约80。
热障涂层的制备及其失效的研究现状

收稿日期:2009206201; 修订日期:2009206225作者简介:邢亚哲(19762 ),陕西岐山人,讲师,博士.研究方向:材料表面强化及器件制造.Email:x ingyazhe@gm 热障涂层的制备及其失效的研究现状邢亚哲,郝建民(长安大学材料科学与工程学院,陕西西安710064)摘要:热障涂层作为航空发动机和燃气轮机高温部件的保护涂层,其抗高温失效能力直接决定了部件的工作效率和寿命。
回顾热障涂层的发展历史及研究现状,着重介绍了热障涂层的主要制备方法及其相应涂层的结构特征,综述了各类热障涂层失效的影响因素和失效机理。
关键词:热障涂层;电子束物理气相沉积;等离子喷涂;失效机理中图分类号:TG174.44 文献标识码:A 文章编号:100028365(2009)0720922204Re se a rc h Stat us in Fa bric at ion and Fa ilure of The rmal Barrie r Co atingsXING Ya 2zhe,HAO Jian 2min(School of Mater ials Science and Engineering,Chang p an University,Xi p an 710064,China)Abst ract:Thermal barrier coatings are widely used to protect the components in aircraft and industrial gas 2turbine engines against high temperature damage.The e ne rgy efficiency and lifetime of these components are mainly dominated by the failure resistance of thermal barrier coatings in the high te mperature atmosphere.In this paper,the development and research status of thermal barrie r coatings are reviewe d.Especially,the main fabricating methods and the microstructure fe ature of the coatings,as well as the factors re sulting in the failure of thermal barrier coatings and its failure mechanisms,are summarized in detail.K e y words:Thermal barrier coatings;Electron beam physical vapor deposition;Plasma Spraying;Fa ilure mechanism随着现代工业的发展,数以百计种类型的涂层被用在各种结构材料表面,以使这些材料表面免受腐蚀、磨损、侵蚀和高温氧化等危害。
航空发动机叶片关键技术发展现状分析
航空发动机叶片关键技术发展现状分析 航空发动机不断追求高推重比,使得变形高温合金和铸造高温合金难以满足其越来越高的温度及性能要求,因而国外自上世纪70年代以来纷纷开始研制新型高温合金,先后研制了定向凝固高温合金、单晶高温合金等具有优异高温性能的新材料;单晶高温合金已经发展到了第3代。上世纪80年代,又开始研制了陶瓷叶片材料,在叶片上开始采用防腐、隔熱涂层等技术。 1.变形高温合金叶片 1.1叶片材料 变形高温合金发展有50多年的历史,国内飞机发动机叶片常用变形高温合金中随着铝、钛和钨、钼含量增加,材料性能持续提高,但热加工性能下降;加入昂贵的合金元素钴之后,可以改善材料的综合性能和提高高温组织的稳定性。其中最常用的是铬镍变形高温合金叶片。 1.2制造技术 叶片是航空发动机关键零件它的制造量占整机制造量的三分之一左右。航空发动机叶片属于薄壁易变形零件。如何控制其变形并高效、高质量地加工是目前叶片制造行业研究的重要课题之一。随着数控机床的出现,叶片制造工艺发生重大变化,采用精密数控加工技术加工的叶片精度高,制造周期短,国内一般6~12个月(半精加工);国外一般3~6个月(无余量加工)。 2.铸造高温合金叶片 2.1叶片材料 半个多世纪来,铸造涡轮叶片的承温能力从1940s年代的750℃左右提高到1990s年代的1700℃左右,应该说,这一巨大成就是叶片合金、铸造工艺、叶片设计和加工以及表面涂层各方面共同发展所作出的共同贡献。北京航空材料研究所、钢铁研究总院、沈阳金属所是铸造高温合金的研制单位。 2021年,国内在一些新材料(如定向凝固高温合金、单晶高温合金、金属间化合物基高温合金等)的研制和应用上,也逐步跟上了世界先进水平的步伐。但是与之相关的材料性能数据较为缺乏,给材料应用、航空发动机选材与设计带来极大的困难。 2.2制造技术 真空熔炼技术。真空熔炼可显著降低高温合盒中有害于力学性能的杂质和气体含量,而且可以精确控制合金成分.使合金性能稳定。 熔模铸造工艺。国内外熔模铸造技术的发展使铸造叶片不断进步,从最初的实心叶片到空心叶片,从有加工余量叶片到无余量叶片,再到定向(单晶)空心无余量叶片,叶片的外形和内腔也越来越复杂;空心气冷叶片的出现既减轻了叶片重量,又提高了叶片的承温能力。 定向凝固技术。该技术的发展使铸造高温合金承温能力大幅度提高从承温能力最高的等轴晶合金到最高的第三代单晶合金,其承温能力约提高l50℃。 铸造合金固有的较低屈服强度和疲劳性能,往往不能满足叶片设计要求,近年来,出现了“细晶铸造工艺”等技术,即利用铸型及浇铸温度控制、凝固过程中机械电磁叫板、旋转铸造以及加入形核剂等方法,实现晶粒细化的。 3.超塑性成形钛合金叶片 3.1叶片材料 目前,Ti6Al4V和Ti6Al2Sn4Zr2Mo及其他钛合金,是超塑性成形叶片等最为常用的钛合金。飞机发动机叶片等旋转件用钛合金作为材料。 对于CO2排放及全球石油资源枯竭的担心,促使人们提高飞机效率、降低飞机重量。尽管复合材料的应用有增长趋势,却有制造费用高、不能回收、高温性能较差等不足。钛合金仍将是飞机发动机叶片等超塑性成形部件的主要材料。 我国耐热钛合金开发和应用方面也落后于其他发达国家,英国的600℃高温钛合金IMI834已正式应用于多种航空发动机,美国的Ti-1100也开始用于T55-712改型发动机,而我国用于制造压气机盘、叶片的高温钛合金尚正在研制当中。其它像纤维增强钛基复合材料、抗燃烧钛合金、Ti-Al金属间化合物等虽都立项开展研究,但离实际应用还有一个过程。 3.2制造技术 早在上世纪70年代,钛合金超塑性成形技术就在美国军用飞机和欧洲协和飞机中得到了应用。在随后的十年中,又开发了军用飞机骨架和发动机用新型超塑性钛合金和铝合金。在军用飞机及先进的民用涡扇发动机叶片等,均用超塑性成形技术制造,并采用扩散连接组装。 4.新型材料叶片 4.1碳纤维/钛合金复合材料叶片 美国通用公司生产的GE90-115B发动机,叶身是碳纤维聚合物材料,叶片边缘是钛合金材料,共有涡扇叶片22片,单重30~50磅,总重2000磅。能够提供最好的推重比,是目前最大的飞机喷气发动机叶片,用于波音777飞机,2021年9月在美国纽约现代艺术馆展出。 4.2金属间化合物叶片 尽管高温合金用于飞机发动机叶片已经50多年了,这些材料有优异的机械性能,材料研究人员,仍然在改进其性能,使设计工程师能够发展研制可在更高温度下工作的、效率更高的喷气发动机。不过,一种新型的金属间化合物材料正在浮现,它有可能彻底替代高温合金。 因为高温合金在高温工作下时会生成一种γ相,它是使材料具有高温强度、抗蠕变性能和耐高温氧化的主要原因。因此,人们开始了金属间化合物材料的研究,金属间化合物,密度只有高温合金一半,至少可以用于低压分段,用于取代高温合金。 2021年,美国通用公司、精密铸件公司等申请了一项由NASA支持的航空工业技术项目(AITP),通过验证和评定钛铝金属间化合物(TiAl,Ti-47Al-2Nb-2Cr,原子分数)以及现在用于低压涡轮叶片的高温合金,使其投入工业生产中。与镍基高温合金相比,TiAl金属间化合物的耐冲击性能较差;将通过疲劳试验等,将技术风险降至最低。
航 空 发 动 机 叶 片 涂 层
航空发动机叶片涂层技术一.涡轮叶片是先进航空发动机核心关键之一航空发动机被称为现代工业“皇冠上的明珠”,航空发动机是飞机的“心脏”,价值一般占到整架飞机的20%-25%。
目前,能独立研制、生产航空发动机的国家只有美、英、法、俄、中5个。
但是,无论“昆仑”、“秦岭”发动机、还是“太行”系列,我国航空发动机的水平距离这一领域的“珠穆朗玛”依然存在不小的差距。
美、俄、英、法四个顶级“玩家”能够自主研发先进航空发动机。
西方四国由于对未来战场与市场的担忧,在航空发动机核心技术上一直对中国实施禁运和封锁。
技术难关有很多。
本人认为涡轮叶片是先进航空发动机的核心技术之一。
随着航空航天工业的发展,对发动机的性能要求越来越高,要使发动机具有高的推重比和大的推动力,所采用的主要措施是提高涡轮进口温度。
国外在20世纪90年代,要求涡轮前燃气进口温度达1850-1950K。
美国在IHPTET计划中要求:在海平面标准大气条件下,航空燃气涡轮机的的涡轮进口温度高达2366K。
涡轮进口温度的提高要求发动机零件必须具有更高的抗热冲击、耐高温腐蚀、抗热交变和复杂应力的能力。
对于舰载机,由于在海洋高盐雾环境下长期服役,要求发动机的叶片的耐腐蚀性更高;常在沙漠上飞行的飞机,发动机的叶片要具有更好的耐磨蚀。
众所周知:镍基和钴基高温合金具有优异的高温力学和腐蚀性能,广泛用于制造航空发动机和各类燃气轮机的涡轮叶片(blade and vane)。
就材质来看:各国的高温合金型号虽各不相同,但就相近成分的高温合金来说,其性能相近(生产工艺方法不同有也造成性能有大的差异)。
好的高温合金的使用温度也只有1073K左右,为达到前面所说的要求温度,采用的方法有二:一是制成空心的叶片。
空心叶片自20世纪60年代中期出现以来,经历了对流冷却、冲击冷却、气膜冷却以及综合冷却的发展历程,使进气口温度高出叶片材料约300—500℃,内腔的走向复杂化和细致化。
这一步的改进仍难满足需要,且英国发展计划将取消冷却。
热障涂层高温抗氧化性能研究的现状及发展
粘结层分界面的应力。而且当址优先氧化完毕后,BC 层中的其他元素氧化形成大颗粒氧化物,出现了尖晶 石类的产物,如图5所示。加之TGO膜加厚,产生较大 的应力。最终引起涂层失效,如图6所示。所以TGO是 一把双刃剑,在TBC服役初期起正作用,后期则是导致 涂层失效的根本原因¨9J。因此,抑制TGO的生长是改 善TBC疲劳性能、提高TBC寿命的重要手段。
嚣匝
圈
图3 EB—PVD沉积的热障涂层的破坏模式 3 TBC涂层系统失效机理研究
3.1 TBC失效机理 虽然热障涂层的制备与研究已经有20多年的历
史,然而无论是使用结果还是试验结果均表明,热障涂
万方数据
层过早剥落失效现象仍然存在。热障涂层剥落失效机 理主要有:①TGO的形成是一个体积膨胀过程,因此形 成TGO时会出现残余应力,冷却到环境温度时,应力会 进一步增大,导致涂层失效;②随着温度的改变,陶瓷 层会发生相变与烧结,增加涂层内的应力;③陶瓷烧结 过程会导致体积的显著变化和材料性能的改变,引起 平面压应力,产生垂直于分界面的裂纹;④陶瓷层自身 是多孔性介质。强度低,在温度和外载荷的交互作用 下,发生断裂、脱落;⑤基体与涂层的热膨胀行为不一 致,导致热梯度或温度梯度,进而产生内应力;⑥由于 涂层一基体两种物质的热膨胀系数不匹配及材料固有 性能上差别【l 3.14】,产生应力集中;⑦外力碰撞损伤,当 异物碰撞陶瓷层时,由于损伤可能导致TBC剥落。然 而,近些年来,人们通过对长期高温氧化气氛中服役的 TBC进行了分析。得出一个共同的观点¨卜171:TGO是 热障涂层在长期高温氧化环境下引起涂层失效不可忽 视的关键因素,如图4所示。
conference。Anaheim,CA,1993.369-374.
[3]ChaIlg K C,Wer w J,Chen C.Oxidation behavior of thermal
新型热障涂层材料的研发与性能优化
新型热障涂层材料的研发与性能优化随着航空、航天、能源等领域的不断发展,热障涂层材料越来越重要。
它们是一种用于减少高温环境下材料热损失的涂层,广泛应用于航空发动机叶片、燃烧室内衬、热交换器和燃气轮机叶片等部件上。
但是,随着现代工业和科技的不断进步,对热障涂层材料的性能要求也越来越高。
因此,新型热障涂层材料的研发和性能优化变得尤为重要。
第一,研发新型热障涂层材料的需求热障涂层材料在航空、航天、能源等领域中,有着不可替代的重要作用。
但随着现代科技的不断发展,更高的性能要求也在不断提出,例如高温抗氧化性、高温低热传递、高韧性、高耐磨性等等。
而传统的热障涂层材料已经无法满足这些要求,因此需要研发新型热障涂层材料。
第二,新型热障涂层材料的分类新型热障涂层材料包括光子晶体、纳米材料、复合材料、金属基材料、氧化物材料等。
这些材料都具有较高的性能,但它们的应用和实践还需要与传统材料进行比较和研究,以确定其性能和适用性。
第三,对新型热障涂层材料的性能优化针对新型热障涂层材料的缺点和优点,可以通过以下方式进行性能优化:1. 不断进行材料的研究和测试,以保证热障涂层材料的稳定性、热慢变性等性能。
2. 提高材料的抗氧化性和耐热性能,以保证热障涂层材料的长期使用寿命。
3. 研究和发展新的热障涂层材料的生产、制备和加工工艺,以降低成本、提高热障涂层材料的质量和性能。
4. 增强热障涂层材料的损伤诊断和评估技术,以预测和评估热障涂层材料的损伤和寿命,提升使用可靠性。
第四,新型热障涂层材料的应用新型热障涂层材料不仅能够应用于航空发动机叶片、燃烧室内衬、热交换器和燃气轮机叶片等部件上,还能应用于其他领域,例如石油化工、电力设备、医疗和船舶等领域。
这些材料可在高温和极端环境下发挥重要的作用,使机械设备能够更加可靠和稳定地运行,从而提高生产效率和使用安全性。
总结新型热障涂层材料的研发和性能优化是一个重要的课题,需要不断地进行材料的研究、测试和开发。