表面涂层技术在航空发动机上的应用
纳米陶瓷涂层作用

纳米陶瓷涂层作用全文共四篇示例,供读者参考第一篇示例:纳米陶瓷涂层是一种新型的表面涂层技术,具有超强的抗磨损、耐腐蚀、耐高温和导热性能。
纳米陶瓷涂层的制备过程中采用了纳米材料,使其具有良好的机械性能和导热性能。
它广泛应用于汽车、航空航天、电子、建筑等领域,为人们的生活和生产提供了便利。
本文将对纳米陶瓷涂层的作用进行详细介绍。
一、纳米陶瓷涂层的作用1.抗磨损:纳米陶瓷涂层具有非常高的硬度和耐磨性,能有效地减少表面磨损,延长使用寿命。
特别是在汽车行业中,纳米陶瓷涂层可以保护车身表面不受划伤和颜色褪色的影响,使车辆更加美观和耐用。
2.耐腐蚀:纳米陶瓷涂层具有很强的耐腐蚀性能,可以有效地防止金属和其他材料受到酸碱和化学腐蚀的侵蚀。
在海洋、化工、航空航天等行业中,纳米陶瓷涂层被广泛应用于金属件的防护,保证设备的正常运行。
3.耐高温:纳米陶瓷涂层具有良好的耐高温性能,可以在高温环境下保持稳定的性能。
它不仅可以保护材料不受高温氧化、热膨胀等影响,还可以有效地提高材料的使用温度,扩大其应用范围。
4.导热性能:纳米陶瓷涂层具有较高的导热性能,可以有效地提高材料的导热效果,降低材料的热阻。
在电子和通讯领域,纳米陶瓷涂层被广泛应用于散热器和导热器件中,提高设备的稳定性和性能。
1.溶胶-凝胶法:溶胶-凝胶法是一种较为简单且成本较低的制备方法,通过对可溶性金属盐和有机物进行混合,形成溶胶,然后再通过加热脱溶,形成凝胶,最后进行烧结处理,形成纳米陶瓷涂层。
2.物理气相沉积法:物理气相沉积法是一种高温高压下进行涂层制备的方法,采用真空蒸发、溅射等技术,将纳米陶瓷颗粒沉积在基材表面,形成均匀、致密的纳米陶瓷涂层。
3.化学气相沉积法:化学气相沉积法是一种在高温高压下进行化学反应,在基材表面形成纳米陶瓷涂层的方法,具有成本低、环境友好等优点,被广泛应用于工业生产领域。
1.汽车行业:纳米陶瓷涂层可以应用在汽车车身和零部件表面,提高车辆的抗磨损、耐腐蚀性能,增强车辆的外观和使用寿命。
航空发动机涡轮叶片热障涂层应用的关键技术和问题
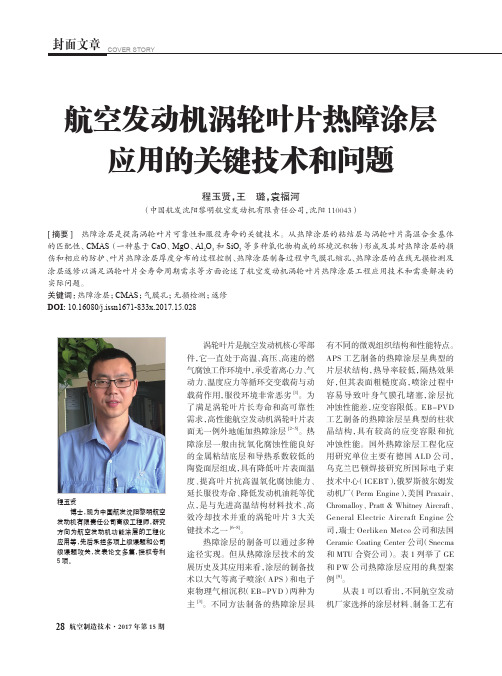
为多孔或柱状晶结构,这些结构会成 能良好,它会沿陶瓷层的微裂纹、孔 渗入(在表层的粘附往往有渗透的现
为腐蚀介质的快速扩散通道,加剧高 洞等逐渐渗入涂层内部,填充陶瓷层 象,可以形成致密层,阻止 CMAS 的
温合金基体的腐蚀)。粘结层的成分 中的空隙,降低陶瓷层的断裂韧性, 渗入);二是阻止渗入后引起的氧化
面,并在高温环境下熔融、渗入涂层 内部,成为影响先进航空发动机热障 涂层寿命的关键因素 。 [23-25]
突然下降时,热障涂层内部的 CMAS 迅速凝固,降低了热障涂层的应变容 限,从而导致涂层发生剥落。对于涡
金属粘结层作为陶瓷面层和高
CMAS 是由于大气中的灰尘、砂 轮叶片热障涂层来说,CMAS 的侵入
匹配所引起的热应力;二是提高整 机循环的峰值温度(如起飞或降落)
国内外针对 CMAS 的防护进行
个热障涂层体系的抗氧化腐蚀性能 时,这些物质形成玻璃态熔融沉积 了大量的研究 [26-29],主要有以下几
(YSZ 陶瓷面层是氧离子导体,且多 物。CMAS 熔体与涂层材料润湿性 个方面:一是阻止 CMAS 熔化后的
程玉贤 博士,现为中国航发沈阳黎明航空
发动机有限责任公司高级工程师,研究 方向为航空发动机功能涂层的工程化 应用等,先后承担多项上级课题和公司 级课题攻关,发表论文多篇,授权专利 5 项。
28 航空制造技术·2017 年第 15 期
涡轮叶片是航空发动机核心零部 件,它一直处于高温、高压、高速的燃 气腐蚀工作环境中,承受着离心力、气 动力、温度应力等循环交变载荷与动 载荷作用,服役环境非常恶劣 [1]。为 了满足涡轮叶片长寿命和高可靠性 需求,高性能航空发动机涡轮叶片表 面无一例外地施加热障涂层 [2-5]。热 障涂层一般由抗氧化腐蚀性能良好 的金属粘结底层和导热系数较低的 陶瓷面层组成,具有降低叶片表面温 度、提高叶片抗高温氧化腐蚀能力、 延长服役寿命、降低发动机油耗等优 点,是与先进高温结构材料技术、高 效冷却技术并重的涡轮叶片 3 大关 键技术之一 。 [6-8]
航空发动机热障涂层材料体系的研究

航空发动机热障涂层材料体系的研究航空发动机热障涂层材料体系的研究航空发动机热障涂层材料体系的研究一直是航空工程领域的关键课题。
随着发动机设计的不断进步,发动机的工作温度也越来越高,因此对热障涂层材料体系的研究和开发变得尤为重要。
热障涂层材料体系是一种能够在高温环境下保护发动机组件不受热损伤的表面涂层。
它的主要作用是降低发动机工作温度,减少热膨胀、热应力和热疲劳等问题,从而提高发动机的性能和寿命。
目前,航空发动机热障涂层材料体系的研究主要集中在两个方面:涂层材料和涂层结构。
涂层材料的研究主要包括陶瓷材料和金属材料。
陶瓷材料因其优异的耐高温性能而受到广泛关注,如氧化铝、氧化锆等。
而金属材料由于其良好的导热性能,在一些特殊应用中也被广泛使用。
研究人员通过改变材料的组分和结构,提高其抗高温氧化、抗热应力和抗热疲劳等性能,以满足航空发动机的要求。
涂层结构的研究包括单层涂层和多层涂层。
单层涂层是指将一种材料直接涂覆在基材表面,其优点是制备简单、成本较低。
然而,由于单层涂层的导热性能较差,其在高温环境下的保护效果有限。
因此,研究人员开始将多层涂层应用于航空发动机热障涂层中。
多层涂层由多种材料层叠组成,可以兼顾不同材料的优点,提高涂层的导热性能和耐热性能。
此外,航空发动机热障涂层材料体系的研究还包括涂层制备工艺的研究。
制备工艺对涂层的性能和结构有着重要影响,因此研究人员致力于寻找更加先进、高效的制备技术,如等离子喷涂、物理气相沉积等。
总而言之,航空发动机热障涂层材料体系的研究是航空工程领域的一项重要研究课题。
通过不断改进涂层材料和涂层结构的性能,并研究制备工艺的先进化,可以提高发动机的性能和寿命,为航空工程发展做出贡献。
碳化铬涂层耐磨性及应用

碳化铬涂层耐磨性及应用碳化铬涂层是一种疏水、耐磨、耐蚀的薄膜涂层,具有较高的硬度和低的摩擦系数。
它广泛应用于机械制造、汽车制造、航空航天等领域,以提高零件的耐磨性和润滑性能。
碳化铬涂层的制备过程通常通过物理气相沉积技术(Physical Vapor Deposition, PVD)进行。
在真空环境中,通过将高纯度的铬靶与纯碳材料放置在靶枪中,利用靶枪中的电弧放电将铬靶和碳材料蒸发,形成带负电荷的离子束。
然后,将离子束在基材表面进行沉积,形成碳化铬涂层。
碳化铬涂层的耐磨性主要来源于其高硬度和良好的结合力。
碳化铬薄膜的硬度通常在1000~2000Hv之间,远远高于传统的金属材料。
这使得碳化铬涂层能够有效抵抗磨损、划伤等表面损伤。
此外,碳化铬与基材之间的结合力很强,能够保持涂层与基材之间的紧密结合,不易脱落。
碳化铬涂层不仅具有耐磨性,还具有优异的耐蚀性能。
由于碳化铬涂层的致密性和低的摩擦系数,它对氧化物、酸、碱等化学物质有较好的抵抗能力。
因此,碳化铬涂层在腐蚀环境下仍能保持零件的稳定性和长寿命。
在机械制造领域,碳化铬涂层被广泛应用于零件表面的耐磨处理。
例如,在模具制造中,常用碳化铬涂层来提高模具的耐磨性能,以延长模具的使用寿命。
此外,在高速切削、打磨、刻蚀等工序中,碳化铬涂层也能有效地保护刀具表面,提高切削效率和质量。
在汽车制造领域,碳化铬涂层常用于发动机缸体、活塞环、曲轴等关键零件的涂覆。
由于发动机环境的高温、高压和高摩擦特性,这些零件表面容易受到磨损和腐蚀的影响。
通过涂覆碳化铬涂层,能够有效提高发动机的工作效率和寿命。
在航空航天领域,碳化铬涂层被广泛应用于飞机发动机和涡轮机组件上。
航空发动机的高温、高压和高速工作环境对叶片和涡轮等关键零件的耐磨性能提出了较高的要求。
通过涂覆碳化铬涂层,可以提高零件的耐磨性能和使用寿命,减少维护和更换零件的次数,同时提高航空器的性能和经济效益。
总之,碳化铬涂层具有耐磨、耐腐蚀的特性,广泛应用于机械制造、汽车制造、航空航天等领域。
耐磨涂层技术在航空航天领域的进展

耐磨涂层技术在航空航天领域的进展一、耐磨涂层技术概述耐磨涂层技术是一种通过在材料表面施加一层具有耐磨性能的涂层来提高材料耐磨性的技术。
这种技术在航空航天领域具有重要的应用价值,因为航空航天设备在运行过程中往往会面临高速摩擦、高温、高压等恶劣环境,对材料的耐磨性提出了很高的要求。
耐磨涂层技术可以有效地提高航空航天设备材料的耐磨性,延长其使用寿命,提高设备的可靠性和安全性。
耐磨涂层技术的原理是通过在材料表面形成一层具有特定结构和性能的涂层,来改变材料表面的物理和化学性质,从而提高材料的耐磨性。
涂层的结构和性能可以通过选择不同的涂层材料、涂层工艺和涂层参数来进行调控。
常见的耐磨涂层材料包括金属涂层、陶瓷涂层、聚合物涂层等,不同的涂层材料具有不同的性能特点,可以根据具体的应用需求进行选择。
涂层工艺也是耐磨涂层技术的重要组成部分。
常见的涂层工艺包括物理气相沉积(PVD)、化学气相沉积(CVD)、热喷涂等。
物理气相沉积是一种通过物理过程将涂层材料沉积在材料表面的工艺,具有沉积速率快、涂层质量高、对基体材料影响小等优点。
化学气相沉积是一种通过化学反应将涂层材料沉积在材料表面的工艺,具有涂层均匀性好、涂层与基体材料结合力强等优点。
热喷涂是一种通过将涂层材料加热熔化后喷射到材料表面的工艺,具有涂层厚度大、可大面积喷涂等优点。
涂层参数对耐磨涂层的性能也有重要影响。
涂层参数包括涂层厚度、涂层密度、涂层硬度等。
涂层厚度过薄可能导致涂层耐磨性不足,涂层厚度过厚可能会影响涂层与基体材料的结合力。
涂层密度和硬度也是影响涂层耐磨性的重要因素,合适的涂层密度和硬度可以提高涂层的耐磨性。
二、耐磨涂层技术在航空航天领域的应用1. 发动机部件航空发动机是航空航天设备的核心部件,其工作环境非常恶劣,需要承受高速摩擦、高温、高压等多种因素的影响。
耐磨涂层技术在航空发动机部件上的应用可以有效地提高发动机部件的耐磨性,延长其使用寿命。
例如,在涡轮叶片上应用耐磨涂层可以提高涡轮叶片的抗磨损能力,减少叶片的磨损和腐蚀,提高发动机的效率和可靠性。
氮化钛涂层工艺

氮化钛涂层工艺氮化钛涂层工艺是一种常用的表面处理技术,广泛应用于各个领域。
本文将介绍氮化钛涂层的工艺流程、特点以及应用,并探讨其在不同领域中的潜力和前景。
氮化钛涂层工艺是一种通过在材料表面形成氮化钛膜来提高材料性能的方法。
这种工艺主要包括预处理、涂覆和后处理三个步骤。
首先,预处理阶段是为了清洁和准备基材表面,以确保涂层的附着力和质量。
其次,涂覆阶段是通过物理气相沉积或化学气相沉积等方法,在基材表面形成氮化钛膜。
最后,后处理阶段是为了提高涂层的致密性和耐磨性,常常采用热处理和表面改性等方法。
整个工艺流程需要严格的操作控制和设备保障,以确保涂层的质量和性能。
氮化钛涂层具有许多独特的特点,使其在各个领域得到广泛应用。
首先,氮化钛涂层具有极高的硬度和耐磨性,能够有效保护基材表面不受外界环境和摩擦的损伤。
其次,氮化钛涂层具有良好的耐腐蚀性能,能够抵抗酸碱腐蚀和高温氧化等侵蚀。
此外,氮化钛涂层还具有良好的导热性和导电性,能够提高材料的传热和导电性能。
最重要的是,氮化钛涂层具有良好的生物相容性和生物活性,可以应用于生物医学领域,如人工关节、牙科材料等。
在航空航天领域,氮化钛涂层广泛应用于飞机发动机叶片、涡轮叶片和航空轴承等关键部件上。
由于氮化钛涂层的高温耐磨性和耐腐蚀性能,能够有效提高发动机的工作效率和寿命,降低维修成本。
在汽车工业中,氮化钛涂层可应用于汽车活塞、汽缸套等零部件上,提高其耐磨性和耐腐蚀性,延长发动机的使用寿命。
此外,氮化钛涂层还可以应用于切削工具、模具等工具材料上,提高其耐磨性和切削性能,提高加工效率和质量。
除了工业领域,氮化钛涂层还有广阔的应用前景。
在医疗领域,氮化钛涂层可以用于人工关节、牙科种植体等医疗器械上,提高其生物相容性和耐腐蚀性,降低患者的痛苦和并发症的发生。
在能源领域,氮化钛涂层可以应用于太阳能电池板、燃料电池等设备上,提高其光电转换效率和稳定性,推动清洁能源的发展。
此外,氮化钛涂层还可以应用于电子器件、光学镜片等领域,提高其耐磨性和耐腐蚀性,提高产品的性能和寿命。
航空航天材料的表面处理技术研究
航空航天材料的表面处理技术研究航空航天领域一直是人类探索未知、追求进步的前沿阵地。
在这个充满挑战和创新的领域中,航空航天材料的性能和质量至关重要。
而材料的表面处理技术,则是提升材料性能、保障航空航天设备安全可靠运行的关键环节之一。
航空航天材料在极端的环境条件下工作,如高温、高压、高真空、强烈的辐射和高速气流等。
这些苛刻的条件对材料的性能提出了极高的要求。
为了满足这些要求,材料的表面处理技术应运而生。
常见的航空航天材料表面处理技术包括化学处理、物理处理和涂层技术等。
化学处理方法如酸洗、碱洗和磷化等,可以去除材料表面的氧化物、油脂和杂质,改善材料的表面清洁度和耐腐蚀性。
物理处理方法则有机械打磨、抛光和喷砂等,能够改变材料表面的粗糙度和形貌,提高其疲劳强度和耐磨性。
涂层技术在航空航天材料表面处理中发挥着重要作用。
热喷涂涂层技术通过将金属、陶瓷或聚合物等材料加热至熔融或半熔融状态,然后高速喷射到基材表面,形成一层牢固的涂层。
这种涂层可以提供良好的耐磨、耐腐蚀和隔热性能。
例如,在航空发动机的叶片上喷涂耐高温涂层,可以显著提高叶片的工作温度和使用寿命。
电镀和化学镀也是常用的表面处理方法。
电镀是通过电解的方式在材料表面沉积一层金属镀层,如铬、镍、锌等。
化学镀则是在无外加电流的情况下,利用化学反应在材料表面沉积金属或合金镀层。
这些镀层可以改善材料的导电性、耐磨性和装饰性。
激光表面处理技术是一种先进的表面处理方法。
它利用高能量密度的激光束对材料表面进行快速加热和冷却,从而改变材料表面的组织结构和性能。
激光淬火可以提高材料表面的硬度和耐磨性;激光熔覆则可以在材料表面制备出高性能的合金涂层。
离子注入技术是将高能离子注入到材料表面,从而改变材料表面的化学成分和组织结构。
这种技术可以显著提高材料的表面硬度、耐磨性和耐腐蚀性。
在航空航天领域,材料的表面处理技术不仅要满足性能要求,还需要考虑到重量、成本和可靠性等因素。
例如,在飞机结构中,为了减轻重量,需要采用轻薄但性能卓越的表面涂层;而在卫星等空间设备中,由于太空环境的特殊性,对材料表面的耐辐射和真空性能要求极高。
涂层技术在航空航天材料领域的应用
保 障 , 别是在 热障 、 严、 特 封 耐磨 、 氧 抗 化等方面起到了很关键的作用。
统 工程 , 应用 现 代科 学技术 众 多领 它 域 的最 新成 就 , 科学 技术 与 国家基 是 础 工业 紧密 结合 的 产物 , 是一 个 国 也
家科学 技 术和 工业 水平 的重要 标志 。 航空 、 天产 业涉 及 国 内外成 千上 万 航 家企 业和 科研 单位 , 表着 国 家 民族 代
\
和必换件 中使用 了大量 的涂层材料 , 因 此, 表面 技术在航 空发动机 的修复和 经 济运行 中发挥着至关重要 的作用。 航空发 动机是特 种功能涂 层应用
的重 要领 域 , 1 3 其 / 多表面需要 使用特 种功能涂层主要包括高温热 障涂层 、 复
00 ‰ , 比国外 其他 国家 比重 较偏 .9 对
强化 与修 复产 品 的研 发, 成 了系列 形 化、 标准 化和 工程 化 的较为 完整 科学
在 国外的航空 发动机修理 中被广泛地
应用 于风扇 叶片、 轮叶片 等部件上 , 涡
等恶劣 工况条 件下 的使 用要 求。 因此 , 表 面技术对 提高发动机的效率 、 燃油消 耗率 、 部件 的可靠性 和使 用寿命 发挥 零
大的社会 和经济效益 。 资料表 明 , 国 美
自2 0 年开 始 , 03 涂层 产 业 的年产 值 已
键。 作为 大飞机 的“ 心脏 ”航 空发动机 , 是 一 项十分 复杂 的高科 技系 统工 程 , 同时也是 目前 制约我 国飞机 制造业 发 展 的“ 瓶颈 ” 发动 机 材料 是 大飞 机研 。 制关 键技 术 中的 关键 , 空发 动机 使 航 用了 1 0 0 0 多个 部件 , 0 有许多易 损件 和 必换件需要在大修周期 中更换 , 易损件
等离子喷涂技术在航空发动机上的应用
一
( )主动 磨 削涂 层 ( 料 ) 1 磨 般是坚 硬的抗磨 损灰 色氧化铝涂
层 ,喷涂在封 严篦齿上 。随着转子
钛 合金不耐磨 ,寿命 仅l O ,而在 凸台上喷涂 一层02 mm厚的碳 化钨涂 层 Oh .5
维普资讯
墨三苎 斯c 要 堡 l咖
gc。y hl T以g e o
等 子 涂 术 航 发 机 的 离 喷 技 在 空 动 上 应用
沈阳黎 明航空发动机集团有限责任公司 ( 宁 10 4 ) 常秋梅 段绪海 辽 10 3
等离子喷涂技 术属于表面工程中热喷涂技术之一 , 其主要特征是以等离子 焰流为喷涂热源 。由于等离子 焰 流具有温度高 、能量集 中和喷涂气氛可控等特 点,是各 种难熔材料 的良好热 源 ,而且粉末材料在 焰流 中的飞行
—
特点及用途 适用于4 0C以下钛合 金叶片 和 5 ̄ 空气导管
( )可磨 耗 涂层 要求 涂 层软 2
而 易磨 ,并具有润 滑性能 、抗冲击 性能 、抗 热振性能 ,以及与 基体有
碳化钨 ( 8 WC 8:Co 2 1)
D P
冠
、
适 用 于 8 0 以下 涡 轮 叶片 叶 4℃
高 压 涡 轮 后 机 匣
良好 的结 合性 能 。表 2 为推 荐使 用
的涂层 。
镍铬硼硅 ( i NC r i BS)
D P F( 火焰 )
适 用于9 0 0 ℃以下风扇 叶片阻尼 凸台
3 热障涂层 .
现在 ,航空 涡轮发动机 的发 展
碳化铬 ( C r ) 3 C2
参 加 磊 工热工
陶瓷、金属表面的MS涂层技术
陶瓷、金属表面的MS涂层技术陶瓷、金属表面的MS涂层技术作者:谢华锟译航空发动机中的生产技术从喷气发动机开始应用以来,人们一直在不断努力进步发动机的性能。
以进步喷气发动机推力、燃料消耗比为特点的高性能及环境适应性要求,一年比一年高。
为满足(适应)这些高性能的要求,对发动机本身的轻量化、透平发动机的高温化及压缩机的高压化等提出了更高的要求,在生产技术上也需有大的发展。
生产技术决定了竞争力,表面改性技术是竞争力中的关键。
(1)表面改性(功能膜形成)技术为适应高温化,在新材料开发、表面改性(功能膜形成)技术开发、冷却结构设计和生产技术开发上都得到了发展。
在航天航空领域中,喷气发动机等金属零部件上的功能膜形成技术有CVD、PVD、电镀、喷涂、堆焊等,这些技术的缺点是设备投资大,对技能的依靠性强,且有些工艺需增加清洗、制作掩膜等预处理工序及除往掩膜、边界处理等后处理工序,有些还会产生热变形、膜体剥落等题目,不适于流水线生产。
(2)新功能膜成形技术IHI和三菱电机开发了一种能集成在机械加工生产线、可制备各种功能膜的新型成形技术,即在放电涂层技术的基础上对模具及工具加工表面进行涂层的新技术。
采用该新涂层技术,金属陶瓷薄膜、厚的金属堆焊层以及金属陶瓷和金属的混合层都能形成。
由于利用了放电能量,故称之为MS涂层(微弧涂层)。
在此技术基础上,进而开发出了适用于各种零部件的功能薄膜或堆焊层。
MS涂层技术MS涂层技术是采用含金属或陶瓷等成分的电极进行放电表面处理,形成耐久性、耐磨性优异的高质量功能薄膜技术。
由于不需要熟练操纵职员和前后处理工序,适合于自动化生产线;又因不需要昂贵的蒸发炉等设备,简化了制造工程,用度大大降低。
(1)MS涂层的原理将由涂层材料粉末做成的电极与被处理材料放进尽缘油中加电压,此时,电极与被处理材料间开始脉冲放电(每秒约1万次),电极材料逐渐向基体迁移,材料溶融接合,形成薄的陶瓷涂层或厚的金属堆焊层。
- 1、下载文档前请自行甄别文档内容的完整性,平台不提供额外的编辑、内容补充、找答案等附加服务。
- 2、"仅部分预览"的文档,不可在线预览部分如存在完整性等问题,可反馈申请退款(可完整预览的文档不适用该条件!)。
- 3、如文档侵犯您的权益,请联系客服反馈,我们会尽快为您处理(人工客服工作时间:9:00-18:30)。
表面涂层技术在航空发动机上的应用
南京航空航天大学
表面涂层技术是指将有机、无机或混合涂层采用刷涂、浸泡、喷涂等方法涂覆于构件表面上,从而改善构件表面性能的一门技术。
表面涂层能够对构件起到防护、密封、抗磨、抗冲击、减振、隔热等作用,而且技术工艺简单,可维修性好,大大提高了发动机构件可靠性,延长了发动机使用寿命,因此在航空发动机中得到了广泛应用。
1.保护涂层
管路、附件、叶片、机匣、帽罩等发动机构件直接和大气接触,容易受到大气中水分、尘埃、盐、二氧化硫的侵蚀,因此,其不锈钢和钛合金材料的表面膜易发生局部腐蚀即点蚀。
涡轮叶片和燃烧室受到高温燃气冲刷,在热应力以及燃气中S 和O 元素的作用下发生化学反应,其晶界生成碳化物,造成贫铬区,在酸性物质作用下,材料表面沿晶面开裂,产生晶粒脱落即干腐蚀,经长期高温氧化形成氧化膜,氧化到一定程度之后,材料表面呈片状破裂或网状剥落,造成微损伤,受到微损伤的构件在振动作用下,会产生微裂纹,微裂纹扩展可导致构件断裂。
抗磨、抗冲击涂层等保护涂层可对构件起到改善工作条件、提高可靠性和延长使用寿命的作用。
抗磨、抗冲击涂层,包括叶片榫头和盘榫槽之间涂的耐磨涂层,高压压气机叶片型面上涂的有机硅耐磨涂层,压气机叶片阻尼凸台上涂的防止运转振动时叶片间相互撞击、摩擦、磨损的叶片振动涂层,涡轮叶片防热盐涂层等。
表1 列出了几种常用的保护涂层。
2.封严与密封涂层
为了提高发动机效率,减少热损失,转、静子之间的间隙要小。
转动件在工作中由于受离心负荷和热气流温度场的影响而向外伸长,因此会和静子碰磨,从而危及发动机的安全。
为限制转、静子之间的间隙,又不使气流泄漏,在静子、转子叶片或封严蓖齿上涂覆软、硬涂层,用磨损涂层的方法来保持封严。
例如WP6 发动机压气机前轴承机匣涂覆的封严涂层,涡轮第 2 级导向叶片的封严环等。
有的静子叶片是插入静子内环的,二者的间隙造
成气流损失,这时可采用密封涂层封住,这要求密封涂层耐温、抗振、柔软,长期不老化。
表2 和表3 列出了部分封严、密封涂层的概况。
3.橡胶涂层
航空发动机压气机叶片在工作中处于高离心负荷状态,在振动作用下最易被破坏,所以对叶片减振非常重要。
叶片振动的形式包括强迫振动、颤振、旋转失速和随机振动,为保证发动机安全工作,就要使压气机叶片振动不致过大,为此,在叶片设计上可采取加凸尖、减振环、阻尼块、带冠叶片、宽弦叶片、加强肋、削尖等减振措施。
为了改善压气机工作特性,扩大稳定工作范围,使发动机有良好的起动和加速性能,在非设计点状态下不发生喘振,在压气机设计中还可采用可转进口导流叶片、可转静子叶片、可变弯度的进口导流叶片、进气处理机匣和放气带等。
国外的发动机也有的采用了橡胶涂层,即将橡胶涂层涂于压气机叶片燕尾槽底部,然后将叶片装入压气机盘的燕尾槽内。
橡胶涂层属于高弹性分子材料,振动时可吸收能量,有明显的阻尼作用,且耐磨、耐老化,密封性好,使用寿命长、易更换、便于维护,能够明显提高叶片的使用寿命。
表 4 列出了部分橡胶涂层概况。
4.热障涂层
大量试验证明,热障涂层热变形小、耐蚀、耐磨、密封性好,用在发动机高温部件上可提高发动机效率和延长发动机使用寿命,已成为航空发动机设计和维护的关键技术之一。
美国PW 公司在J T3D 和J T38D 发动机
的风扇叶片、压气机叶片、燃烧室、涡轮叶片等处采用了热障涂层,目前,已将热障涂层发展到了第 3 代,应用了大推重比发动机PW4000 上。
英国RR 公司的Spey 发动机有200 多个零件使用了热障涂层,尤其是在第1~3 级涡轮叶片叶冠上均使用了热障涂层,从而改善了叶片可靠性,提高了发动机效率。
美国GE公司,在20 世纪70 年代中期,将热障涂层广泛用于延长燃烧室和加力燃烧室组件的使用寿命;80年代,等离子喷涂热障涂层的应用已经扩展到高压涡轮导向叶片。
为提高发动机燃烧室可靠性,防止发生热变形进而产生裂纹,英国RB211 发动机燃烧室衬套表面采用了热喷氧化锆涂层,从而极大地提高了燃烧室的使用寿命。
随着航空航天技术的发展,中国的隔热高温涂层技术也有了长足进步,热障涂层早就应用于发动机燃烧室、喷口、涡轮叶片等处。
如WP7 发动机火焰筒使用了高温珐琅涂层。
又如WP6 发动机第1级涡轮叶片的榫齿延伸段曾发生断裂,采用钴铬镍
热喷耐磨涂层有效排除了这一故障。
目前中国热障涂层使用的最高温度可达1350 ℃。
表5 列出了部分热障涂层的概况。
发动机设计技术的发展要求涡轮叶片承受更高的温度,在叶片材料的性能难以提高的情况下,只有靠发展热障涂层来解决这一问题。
近些年来,热障涂层技术已成为涡轮叶片设计的一个重要组成部分。
国外著名的航空发动机公司对热障涂层在涡轮叶片上的应用进行了大量试验,并进行了热障涂层厚度、性能、材料、裂纹、疲劳、剥落机理、隔热等专项研究。
为了研究高温部件的力学特性,英国RR 公司和美国NASA 采用等离子喷涂的热障涂层技术研制成功了温度为1000 ℃的高温应变计。
5.结语
涂层技术是表面工程技术的一个分支,其中的防锈、防冰、防雾、阻燃、耐油等涂层都在发动机上得到了应用,对提高发动机可靠性起到了一定作用。