氧化锆热障涂层在航空发动机上的应用和发展.
中国突破高性能纳米氧化锆热障涂层技术难关

中国突破高性能纳米氧化锆热障涂层技术难关
中国突破高性能纳米氧化锆热障涂层技术难关
2013年08月06日 10:24
来源:中国国防科技信息网
近日,西安航天复合材料研究所建成高性能纳米氧化锆喷涂粉体生产线,标志着该所高性能热障涂层攻关取得重大进展。
该所发挥等离子喷涂技术工程化应用优势,以高性能纳米氧化锆喷涂粉体在大推重比航空发动机、燃气轮机和火箭发动机领域需求为背景,进行高性能热障涂层技术攻关,突破纳米结构控制技术,建成了国内最先进的粉体材料合成技术平台,建立了高性能纳米氧化锆喷涂工程化研制生产和材料标准体系,成为国内首家纳米粉体制备和涂层应用技术集成研究单位。
[责任编辑:吴雨洪] 标签:热障涂层航天氧化锆。
热障涂层在航空发动机涡轮叶片上的应用研究

V l7 o No2 A r2 1 3 p . 0 1
热障涂层在航空发动机涡轮叶片上
的应用研 究
张志强 , 文兴 , 宋 陆海 鹰 ( 中航 工 业沈 阳发 动 机 设 计研 究所 。 阳 10 1 ) 沈 0 5 1
摘要 : 从热 障涂层在 涡轮 叶片的应用需求 出发 , 究 了陶瓷热障涂层 的材 料与制 研
为金 属黏 接层 ,该 材料 即能满 足黏 接 陶瓷层 的要求 ,
是 在 零 件 表 面 沉 积 黏 接 1层 低 导 热 系数 的 材 料 , 利
的主要 因素是涡 轮叶片 的承温能力 。在涡轮 叶片燃气 流道表面喷涂热 障涂层 ,对 提高 叶片承温能力 有非常 直接 的效果 , 并对短 时间的超 温有很好 的缓 解作用 。国 外热障 涂层 在军 、 空发 动机上 已获 广泛应用 , 民航 据资 料介绍 , 可取得 5 ~5 0 10℃ 的隔热效果 。涡轮 叶片工作 温度一般都接 近其材料 的许用温度 ,此 时如果 涡轮 叶 片每降低 1 , 久寿命 约延长 1 。在结 构和冷 5℃ 其持 倍 却效果 不变的条件 下 ,采用热 障涂层技 术可 以使 叶片
2 陶瓷热障涂层的选材 与制备方法
21 陶瓷热 障涂层 ห้องสมุดไป่ตู้料 .
热 障涂层( 简称 T C 技术是 1 B) 种表面处理技术 ,
张志强筹 : 热瞪涂屠在黼空发动柏涡轮口 毙上的啦用酾夯 十
3 B /] g
属基 体 之 间增加 金属 黏接 层 ( 底层 )在 金 属 和 陶瓷之 , 间起 黏 接 和缓 冲热应 力 的作 用 。一般选 用 McAY作 r1
员, 从事航空发动机涡 轮冷却叶片设 计 tri ae h aei n nuatr gapo ho rmi tem lb re o i ubn un,t m t a adma fc i ra c a c h r a a irca n e e r l un p c f e r t g
热障涂层材料的研究和发展
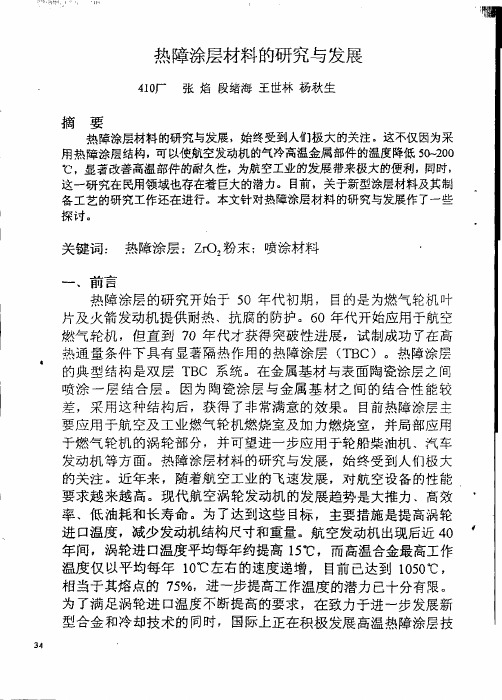
热障涂层材料的研究与发展410厂张焰段绪海王世林杨秋生摘要热障涂层材料的研究与发展,始终受到人们极大的关注。
这不仅因为采用热障涂层结构,可以使航空发动机的气冷高温金属部件的温度降低50----200℃,显著改善高温部件的耐久性,为航空工业的发展带来极大的便利,同时,这一研究在民用领域也存在着巨大的潜力。
目前,关于新型涂层材料及其制各工艺的研究工作还在进行。
本文针对热障涂层材料的研究与发展作了一些探讨。
关键词:热障涂层:ZrO:粉末;喷涂材料~、前言热障涂层的研究开始于50年代初期,目的是为燃气轮机叶片及火箭发动机提供耐热、抗腐的防护。
60年代开始应用于航空燃气轮机,但直到70年代才获得突破性进展,试制成功了在高热通量条件下具有显著隔热作用的热障涂层(TBC)。
热障涂层的典型结构是双层TBC系统。
在金属基材与表面陶瓷涂层之间喷涂一层结合层。
因为陶瓷涂层与金属基材之间的结合性能较差,采用这种结构后,获得了非常满意的效果。
目前热障涂层主要应用于航空及工业燃气轮机燃烧室及加力燃烧室,并局部应用于燃气轮机的涡轮部分,并可望进一步应用于轮船柴油机、汽车发动机等方面。
热障涂层材料的研究与发展,始终受到人们极大的关注。
近年来,随着航空工业的飞速发展,对航空设备的性能要求越来越高。
现代航空涡轮发动机的发展趋势是大推力、高效率、低油耗和长寿命。
为了达到这些目标,主要措施是提高涡轮进口温度,减少发动机结构尺寸和重量。
航空发动机出现后近40年间,涡轮进口温度平均每年约提高15℃,而高温合金最高工作温度仅以平均每年10"(2左右的速度递增,目前已达到1050℃,相当于其熔点的75%,进~步提高工作温度的潜力已十分有限。
为了满足涡轮进口温度不断提高的要求,在致力于进一步发展新型合金和冷却技术的同时,国际上正在积极发展高温热障涂层技术。
实验表明,应用这种技术可以允许提高燃烧室温度50-200。
C,如果在涡轮叶片上等离子喷涂二氧化锆涂层,则可以提高涡轮进口温度约80。
新型热障涂层材料的开发与应用

新型热障涂层材料的开发与应用近年来,随着航空航天工业的迅猛发展,对于高温环境下工作的航空发动机的需求也越来越大。
然而,高温环境对发动机的材料造成了严峻的挑战。
为了保证发动机的正常运行,科学家们开始研发新型热障涂层材料,以在高温环境下提供保护。
热障涂层材料是一种能够在高温环境下阻挡热量传导的特殊涂层。
它可以减少发动机组件的温度,降低热应力,延长发动机的使用寿命。
传统的热障涂层材料多采用氧化铝,但其在高温下容易脱落,限制了其使用范围。
因此,科学家们开始寻找新型的、更为稳定的热障涂层材料。
一种新型的热障涂层材料是钼二硅化物。
该材料具有优异的热障性能和较低的热传导率,能够有效地隔离高温。
研究人员通过改变材料的合成方法和配方,成功地制备出了具有高结晶度和优异热稳定性的钼二硅化物热障涂层。
经过长时间的热循环试验,该涂层表现出了出色的热障性能,显示出了广阔的应用前景。
除了钼二硅化物,还有其他一些新型材料也被考虑用于热障涂层的开发。
例如,氧化锆、钼合金、发光材料等都展示了良好的抗高温性能。
这些新型材料的开发使得热障涂层材料的选择更加多样化,有助于提高航空发动机的性能。
在热障涂层材料的应用方面,航空航天工业是其中最主要的领域之一。
在现代航空发动机中,使用热障涂层材料可以有效地降低燃料消耗和排放物的产生,提高发动机的工作效率。
此外,该涂层还能够延长发动机的使用寿命,减少对于维修和更换部件的需求,进一步降低了成本。
除了航空航天工业,热障涂层材料在其他领域也有广泛的应用。
例如,在能源行业中,热障涂层材料可以提高燃烧设备的热效率,降低燃料消耗。
在电力行业中,该涂层还可以用于提高发电机组件的工作效率,减少能源损耗。
此外,热障涂层材料在汽车工业、船舶工业等领域也有一定的应用潜力。
总的来说,新型热障涂层材料的开发与应用在航空航天工业以及其他领域具有重要意义。
这种材料可以有效地保护发动机和其他高温工作组件,提高其工作效率和使用寿命,降低能源消耗和环境污染。
涂层技术在航空发动机中的应用(一)

涂层技术在航空发动机中的应用(一)涂层技术在航空发动机中的应用1. 提高发动机效率•热障涂层(TBC)热障涂层是一种高温耐受能力极强的陶瓷涂层,在航空发动机中有广泛应用。
它可以有效降低高温燃烧室和涡轮内部的表面温度,减少热量传递到其他部件,提高燃烧效率和涡轮的使用寿命。
热障涂层采用涂敷的方式施加在发动机部件表面,形成一层隔热层,同时具备优异的耐热性、耐腐蚀性和耐磨性。
•摩擦涂层摩擦涂层是一种能够减少摩擦阻力、降低能耗和延长机械部件寿命的涂层技术。
在航空发动机中,喷涂摩擦涂层可以应用于涡轮叶片表面以减少摩擦热造成的能量损耗,提高发动机效率。
该涂层通常由涂料和固化剂组成,喷涂后会形成一层耐磨、耐热的涂层,提供涡轮叶片所需的低摩擦系数。
2. 保护发动机结构•防腐蚀涂层发动机作为飞机的核心部件,其表面容易受到腐蚀的影响。
防腐蚀涂层能够降低发动机金属部件受到酸性气体、高温、湿度等因素的腐蚀程度,提高其耐久性。
航空发动机中使用的防腐蚀涂层通常采用环氧树脂和特殊添加剂,能够有效隔离金属与外界环境,降低腐蚀速度,同时具备耐温性能。
•降噪涂层航空发动机产生的噪音是对航空乘客和地面居民造成的主要干扰。
降噪涂层是一种能够减少发动机噪音输出的技术。
该涂层通常由吸声材料和表面粗糙度调整剂构成,能够通过吸收噪音和改变噪音传播路径来降低发动机产生的噪音水平。
降噪涂层的应用可以有效改善乘客舒适度,减少航空噪声对环境的影响。
3. 增强结构强度•硬质涂层硬质涂层是一种附着在金属表面的高硬度涂层,可以提供结构件的抗磨损和抗腐蚀能力。
在航空发动机中,硬质涂层通常应用于涡轮轴承、气门、活塞等部件表面,能够减少零部件间的摩擦和磨损,提高结构件的使用寿命。
常见的硬质涂层材料包括碳化硅、氮化硼等。
•纳米涂层纳米涂层是一种厚度在纳米级别的超薄涂层,它能够提供出色的防腐蚀和防磨损性能。
航空发动机中的纳米涂层可应用于活塞环、气缸内壁等部件表面,能够减少部件摩擦和磨损,提高结构件的使用寿命。
表面涂层技术在航空发动机中的具体应用
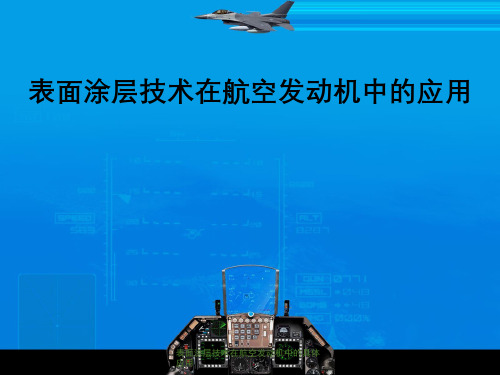
• 航空发动机压气机叶片在工作中处于高离心负 荷状态,在振动作用下最易被破坏。
表面涂层技术在航空发动机中的具体 应用
减振措施
• 在叶片结构设计上采取加凸尖、减振环、阻尼块、 带冠叶片、宽弦叶片、加强肋、削尖等减振措施。
• 采用橡胶涂层,即将橡胶涂层涂于压气机叶片燕尾 槽底部,然后将叶片装入压气机盘的燕尾槽内。
表面涂层技术在航空发动机中的具体 应用
2.航空发动机表面涂层技术分类
热喷涂涂表层面涂在层技飞术在机航空发发动动机中机的具体中的应用示意图 应用
2.航空发动机表面涂层技术分类
• 保护涂层 • 封严密封涂层 • 橡胶涂层 • 热障涂层
表面涂层技术在航空发动机中的具体 应用
2.1保护涂层
主要保护部位
表面涂层技术在航空发动机中的具体 应用
双辉等离子表面合金化技术
双辉等离子渗金属技术的基 本原理: 在使工件和源极分别产生所 谓双层辉光放电现象。辉光 放电所产生的氩离子轰击, 使源极溅射出合金元素并飞 向工件,而工件经离子轰击 被加热到高温。合金元素借 助于轰击吸附和扩散而渗入 工件表面,从而形成含有欲 渗合金元素的合金层。
2.2密封封严涂层
封严涂层 为限制转子、静子之间的间隙, 不使气流泄漏,
在静子、转子叶片或封严蓖齿上涂覆软、硬涂层, 用磨损涂层的方法来保持封严。 密封涂层
有的静子叶片是插入静子内环的,二者的间隙 造成气流损失,这时可采用密封涂层封住,这要求密 封涂层耐温、抗振、柔软,长期不老化。 可磨耗封严涂层
抗磨、抗冲击涂层: 叶片榫头和盘榫槽之间涂的耐磨涂层 高压压气机叶片型面上的有机硅耐磨涂层 压气机叶片阻尼凸台上的叶片振动涂层 涡轮叶片防热盐涂层 涡轮叶片叶冠接触面硬质合金耐磨涂层
热障涂层应用
热障涂层应用
热障涂层是一种能够提供高温保护的防护涂层,在许多领域都有广泛的应用。
1. 航空航天领域:热障涂层广泛应用于航空发动机、燃烧室、航天飞行器等高温部件上,能够有效降低高温对材料的损伤。
这能够提高发动机和飞行器的耐用性和使用寿命。
2. 能源领域:热障涂层被应用于燃气轮机的燃烧室和涡轮叶片等高温部件上,可以降低高温对材料的腐蚀和热疲劳,延长燃气轮机的使用寿命。
此外,热障涂层也可应用于热电设备、核能设备等高温环境下的部件上。
3. 汽车制造业:热障涂层可应用于汽车发动机的缸体和排气歧管等高温部位,降低高温对零部件的损伤,提高发动机的效率和寿命。
4. 钢铁冶金业:热障涂层可应用于钢铁冶金过程中的高温反应容器、热处理炉等设备,保护设备免受高温和腐蚀的影响,延长设备使用寿命。
5. 建筑工程:热障涂层可应用于高温环境下的建筑物外墙或屋顶,提供保温隔热效果,节能降耗。
总之,热障涂层在许多领域都能发挥重要作用,提高材料和设备的抗高温性能,延长使用寿命,同时也能保护环境和节约能源。
航空发动机高温防护涂层材料技术发展现状与趋势
YSZ
Bond coat Substrate
Cycles to failure
2000 1900 1800 1700 1600 1500 1400 1300 1200 1100 1000
R&R 900发动机
兰色:Ti合金 桔黄色:钢(静止部分) 红色:Ni基
推重比
10
12~15
涡轮前温度: 1850~1950K
2050~2100K
叶片表面温度: >1400K
> 1500K
推重比10高压导向叶片用IC10: ≤1370K (1100℃)
高压涡轮叶片用DD6: ≤1340K (1070℃)
7~8wt%YSZ是目前使用最广的热障涂层材料 ➢ 高熔点(3000K以上) ➢ 低热导率(2~3 Wm-1K-1,块材) ➢ 较高热膨胀系数(~11×10-6K-1) ➢ 较低密度(~6.4g/cm3) ➢ 较低弹性模量(~40GPa) ➢ 高硬度(~14GPa)
热障涂层粘结层的主要制备方法
MCrAlY:
β-(Ni,Pt)Al
IDZ DD6 30um
图 表面是β-(Ni,Pt)Al单相涂层的表面及横截面形貌
Pt改性Al化物涂层(CVD渗Al及气相渗Al)
CVD法制备的(a)β-NiAl,(b)β-(Ni,Pt)Al单相涂层的表面及横截面形貌 渗Al温度 1100℃,时间 4h。
气相渗工件不同的放置方式对渗Al表面形貌影响
优点:1、避免渗剂颗粒嵌入 涂层表面
2、可以局部渗Al,尤其 适合复杂内腔渗Al, 如:气膜冷却孔内腔
关键技术:放漏渗技术? 降低气相渗温度?
高性能热障涂层在能源设备喷涂的应用
高性能热障涂层在能源设备喷涂的应用高性能热障涂层作为能源设备领域的一项重要技术革新,近年来在提高设备效率、延长使用寿命及促进节能减排方面发挥了关键作用。
本文将从六个维度探讨高性能热障涂层在能源设备喷涂的应用,包括其基本原理、技术优势、应用领域、材料进展、环境影响以及未来发展趋势。
一、基本原理与功能机制高性能热障涂层主要由陶瓷材料构成,如氧化钇部分稳定氧化锆(YSZ)等,这些材料具有优异的热绝缘性能。
涂层喷涂于能源设备的高温部件表面,如燃气轮机叶片、锅炉管道等,形成一层微米至亚微米级别的保护层。
涂层能显著降低基体材料直接暴露于高温环境下的热负荷,通过热辐射和对流机制有效隔绝热量传递,从而保护基材免受高温侵蚀,减少热应力引起的疲劳损伤,延长设备寿命。
二、技术优势与效益提升1. 提高能源效率:通过减少热损失,涂层能提升能源转换效率,尤其是在热电转换、燃烧设备中效果显著。
2. 增强耐高温性能:有效隔离高温环境,防止或延缓材料热变形和损坏,提升设备在极端工况下的可靠性。
3. 延长维护周期:降低腐蚀速率和磨损,减少停机维护时间,降低长期运营成本。
4. 轻量化设计:允许使用更薄的隔热材料或更轻的基底材料,有利于设备的轻量化和小型化设计。
三、广泛的应用领域高性能热障涂层在多个能源相关领域展现出了巨大潜力:- 电力行业:在火电站、核能反应堆的高温部件上应用,提高热效率,减少热损失。
- 航空航天:飞机发动机和喷嘴涂层,耐高温同时减轻重量,提升推力效率。
- 汽车工业:用于发动机部件,减少热损失,提高燃油经济性。
- 化工生产:高温反应器和热交换器上的涂层,增强设备耐腐蚀性和热稳定性。
四、材料科学的最新进展科研人员正不断探索和开发新型热障涂层材料,如双相或多相陶瓷材料、纳米结构涂层、以及基于陶瓷-金属复合材料的涂层,以进一步提高热绝缘性能、机械强度和化学稳定性。
特别是,引入梯度结构和功能性涂层的设计,使涂层在不同区域具备不同性能,更好地匹配复杂的工作条件。
高温氧化防护涂层的制备及其在航空航天中的应用
高温氧化防护涂层的制备及其在航空航天中的应用航空航天技术对于人类社会的发展具有极其重要的意义,因此对于航空器的设计和制造也显得尤为重要。
但是,在空中高速运动过程中,飞行器所受到的温度和氧化等因素都会对其材料的性能和寿命造成不利的影响。
因此,如何有效地防止材料遭受高温和氧化的侵害,一直是制造高性能飞行器的重要研究方向之一。
而高温氧化防护涂层的制备和应用就是在这个背景下而诞生的一种技术。
1. 高温氧化防护涂层的主要特点高温氧化防护涂层,顾名思义是在材料表面形成一层具有高温氧化防护功能的涂层。
其主要特点可以总结为以下几点:首先,高温氧化防护涂层能够有效地减少材料受到高温氧化的侵害,帮助材料在高温环境下保持良好的物理和化学性能。
其次,高温氧化防护涂层可以有助于减少高温环境下的热辐射,有利于保护材料表面的光洁和平整度。
最后,高温氧化防护涂层可以改善材料表面的化学稳定性和附着力,在极端的环境下仍能保持良好的耐久性。
2. 高温氧化防护涂层的制备方法目前,常用的高温氧化防护涂层制备方法主要包括:物理气相沉积法、湿化学沉积法、喷涂法、溅射法等。
下面将简单介绍各种方法的原理和特点。
首先,物理气相沉积法,是一种利用高温真空条件下,将涂层的原料进行沉积成薄膜的方法。
其优点在于沉积的膜具有均一的成分和晶体结构,但其缺点在于比较复杂,需要高昂的设备费用和操作成本。
其次,湿化学沉积法,是一种利用化学反应,在涂层材料表面形成稳定的化合物膜的方法。
其优点在于操作较为简单,而且能够沉积出良好的复合涂层,但其缺点在于材料的成分比较难控制。
再次,喷涂法,是一种直接将涂层喷涂到材料表面的方法。
其优点在于材料的热膨胀系数比较匹配,而且成本较低,但其缺点在于喷涂涂层的质量和粘附度很难保证。
最后,溅射法,是一种通过离子轰击目标材料,将其表面的原子分离并沉积到基材表面的方法。
其优点在于能够沉积出均匀的膜层,而且可以对材料表面进行微观调控,缺点在于难以控制沉积过程中的晶粒结构。
- 1、下载文档前请自行甄别文档内容的完整性,平台不提供额外的编辑、内容补充、找答案等附加服务。
- 2、"仅部分预览"的文档,不可在线预览部分如存在完整性等问题,可反馈申请退款(可完整预览的文档不适用该条件!)。
- 3、如文档侵犯您的权益,请联系客服反馈,我们会尽快为您处理(人工客服工作时间:9:00-18:30)。
2010年第36卷第6期Vol.36No.6Dec.2010氧化锆热障涂层在航空发动机上的应用和发展孙福波,涂泉(贵州红湖机械厂,贵州561116)摘要:介绍了氧化锆热障涂层(TBCs)的特性、制备方法及其特点,分析了TBCs在航空发动机上的应用情况,并对TBCs技术的发展做出了展望。
关键词:氧化锆热障涂层;航空发动机;热端部件;高温防护ApplicationandDevelopmentofZirconiumOxideThermalBarrier CoatingonAeroengineSUNFu-bo,TUQuan(GuizhouHonghuMachineryPlant,Guizhou561116,China)Abstract:Thecharacteristicandmanufacturingmethodofthezirconiumoxidethermal孙福波(1962),男,工程师,从事航空发动机热障涂层、耐磨涂层、封严涂层的工程应用研究。
收稿日期:2010-04-22barriercoating(TBCs)wasintroduced.TheapplicationofTBCswasanalyzedontheaeroengin e.TheprospectofTBCstechnologywasalsoperformed.Keywords:zirconiumoxidethermalbarriercoating;aeroengine;hotsectioncomponent;high-temperatureprotection1引言对氧化锆热障涂层(TBCs)的热温度,推重比10一级发动机要推重比15一求达到100~150℃,级发动机要求达到150~200℃,同时,还要求TBCs具有抗高温腐蚀和高温氧化的作用,抗氧化温度达到1250℃。
本文对TBCs的特性和不同制备方法以及在航空发动机上的应用情况和发展需求进行了阐述。
代航空发动机的关键技术之一,一般由金属黏结层和陶瓷面层组成。
作为热障涂层的陶瓷材料具低热导率、低辐射率和有高熔点、高反射率等特点,采用电子束物理气相沉积EB-PVD技术和等离子喷涂技术制备,喷涂在发动机热端部件(如火焰筒、加力燃烧室、涡轮叶片)的表面,将部件与高温燃气隔绝开来,以降低部件的工作温度,并保证部件免受燃气的高温腐蚀与冲蚀。
目前,TBCs应用最多的是氧研究始于20世纪40年代末,于60年代初应用在JT8D发动机燃随着发烧室内壁。
到80年代末,动机推重比的提高,发动机热端而相关材料的承温能力有限,因此,TBCs作为减少冷却气体、延长部件寿命的1种重要工艺手段而受到重视。
进入21世纪,对TBCs隔22.1基本特性和制备方法基本特性TBCs亦称热屏蔽涂层,是现孙福波等:氧化锆热障涂层在航空发动机上的应用和发展54/55化钇部分稳定的氧化锆(ZrO2)材料。
该材料的涂层具有在氧化性介质中十分稳定,热导率和电导率低,抗熔融金属介质侵蚀能力强等特点,与金属或碳接触的使用温度为1700~2090℃。
TBCs一般不使用纯ZrO2粉末。
因为纯ZrO2粉末在高温下的晶型转变会使其发生较大的体积变化而产生剥蚀现象。
在加热过程中,伴随着约7%的体积收缩;而在冷却过程中,则产生超过7%的体积收缩。
在每次加热和冷却过程中,ZrO2随着晶型转变而发生的体积收缩是不可逆的。
每一循环残存的不可逆的体积变化经积累,形成很大的热应力,使其发生开裂和剥落而失效。
因此,ZrO2不能用于1000℃以上的抗热震涂层,如图1所示[1]。
图1ZrO2在加热和冷却过程中的晶型转变与体积变化研究发现,6%~8%Y2O3部分稳定的ZrO2,在温度为1300℃时仍保持立方晶体,十分稳定,并能在更高的使用温度(≥1350℃)下使用。
ZrO2晶形转变的体积应力最小,因而耐热震性能更好,因此Y2O3-ZrO2已成为现代航空发动机应用的先进TBCs材料。
3热障涂层制备方法及各种方法的优缺点发动机涂层制备技术主要包括等离子喷涂、电子束物理气相沉积和离子注入。
等离子喷涂包括大气等离子喷涂、层流等离子喷涂、真空等离子喷涂、轴向送粉等离子喷涂,溶液等离子喷涂是最新发展的涂层制备技术。
3.1大气等离子喷涂等离子喷涂技术主要用于导向叶片。
3.1.1大气等离子涂层形成[2]大气等离子平台涂层的形成过程如图2所示。
(a)(b)图2涂层原理及结构(1)粉材进入热源高温区,被加热、熔化,形成熔滴。
(2)熔融粒子被等离子射流推动,向前飞行。
(3)熔融粒子以较大的动能冲击基材表面,与基材碰撞,熔滴飞溅变形。
(4)熔滴冷凝收缩,交错黏结。
3.2等离子喷涂特点(1)优点。
射流温度高,能喷涂一切有固定熔点的材料;射流速度大,涂层结构力比较高;被喷涂的工件不受限制(复杂零件除外),温度低于200℃,基体一般不变形,也不发生组织变化。
(2)缺点。
涂层与基体的黏结仍以机械结合为主,不宜承受振动、冲击等重负荷;操作环境较恶劣,要求采取劳动保护和环境保护措施;影响涂层质量的因素多,且难以对涂层质量进行非破坏性检查。
3.3电子束物理气相沉积电子束物理气相沉积技术(EB-PVD)属于溅射镀,主要用于工作叶片。
EB-PVD是指在真空状态下,利用具有高能量密度的电子束轰击沉积材料(金属、陶瓷等),使之熔化、蒸发,并在基体上凝结沉积,形成涂层———具有有序结构、彼此分离的柱状晶体。
该技术具有很高的沉积速率和较好的工艺可重复性。
3.3.1 优点(1)结合强度高。
涂层沉积在真空状态下进行,有利于防止基体与涂层材料被污染和氧化,沉积的柱状晶体与基体底层结合牢固,质量较高。
(2)具有柱状晶体结构。
晶体的生长方向和晶界方向均垂直于基体表面,与等离子喷涂层的片层状结构完全不同。
其抗剥落寿命比等离子喷涂的提高7倍,如图3所示[3]。
(3)涂层致密、硬度高。
涂层硬度提高,耐磨性比等离子喷涂2010年第36卷第6期Vol.36No.6Dec.2010的高2倍。
图3热障陶瓷涂层柱状晶结构(4)涂层表面光洁。
经EB-PVD沉积的TBCs,表面粗糙度低,Ra≈2.1μm,不需要进行光饰处理。
3.3.2缺点(1)热导率高。
涂层十分致密,热传导性能提高,绝热屏蔽效果降低。
(2)成本高,沉积速度慢,特别是难于沉积mm级的厚涂层。
而对TBCs的要求是增大厚度,以提高绝热和热屏蔽能力。
(3)与等离子喷涂相比,喷涂速率较低。
3.4溶液等离子喷涂溶液等离子喷涂(SPS法)降采用锆酸盐溶液作为原料,将雾化的微细液滴馈送入等离子焰流中,经蒸发、破碎、胶凝、沉淀、热解、烧结等,在基体上沉积出具有纳米结构的TBCs。
其工艺流程如图4所示。
图4以SPS法制备纳米涂层的工艺流程其制备的TBCs特点如下:(1)能获得nm级晶体。
涂层的晶体尺寸为10~30nm。
随着陶瓷粒子细化至nm级,其性能大幅提高。
因此,涂层十分致密,表面粗糙度很低,涂层与基体的结合强度及涂层自身的力学性能大大提高。
(2)具有均匀的nm级和μm级孔隙。
这使看似非常致密的纳米涂层成为十分微细的“蜂窝”多孔结构,因而具有很好的绝热性能。
(3)热稳定性好。
nm级晶粒的氧化物陶瓷,在高温为578℃1073K)时显示出优异的抗晶粒长大的能力和热稳定性,产生抗晶界溶解的阻力,能在升高温度时有效地抑制晶粒长大,具有奇特的“钉扎效应”。
(4)产生纵向裂纹。
纳米陶瓷涂层产生微细的纵向裂纹,不存在等离子喷涂态涂层的片层颗粒和片层晶界,与EB-PVD沉积的柱状晶结构的性能相似,具有很高的抗高速燃气冲刷能力和由此能力产生的抗剪切应力和弯曲应力的能力,提高了TBCs沿平行于界面的方向产生剥落的能力。
SPS法制备纳米热障陶瓷涂层技术是1项新兴技术,尚不完善和成熟,一些理论问题还有待探讨,是否能满足第5代发动机的研制要求有待进一步研究。
4应用与展望4.1应用4.1.1性能要求发动机研制对TBCs性能的要求如下。
(1)耐高温。
发动机热效率与涡轮机燃气进口温度(即燃气初温)密切相关。
现代航空发动机涡轮燃气进口温度已达1700℃,这就对TBCs耐高温性能提出了更高的要求。
(2)绝热性好。
发动机热端部件用高温合金(如高温镍基合金)的工作温度已达1100℃左右。
提高发动机燃气初温主要通过空气冷却和绝热涂层2种途径,而空气冷却又会降低发动机的热效率。
显然,采用具有低热导率的陶瓷涂层对高温合金基体进行绝热保护是十分重要的措施。
(3)耐热震性好。
TBCs必须能够承受从高温到低温的温度周期性变化,以及热疲劳性和热冲击性。
温度范围变化越大,冷却速度越高,则涂层应力越大、开裂甚至剥落的可能性越大。
(4)化学稳定性强。
TBCs在高温下,耐氧化,耐高速燃气的腐蚀和冲蚀,并且不会与基体材料发生有害的化学反应。
(5)涂层密度低。
TBCs为低密度热障材料,含有大量微细孔隙,不仅质轻,绝热性好,而且对裂纹和热冲击的敏感性也较小。
(6)结合强度高,使用寿命长。
TBCs与基体金属之间必须有高的结合强度,以保证在有效的使用期内涂层不会剥落和失效。
TBCs的使用寿命包含2层意思:第1,在工作温度下持续暴露的时间,这对于发动机续航和远航能力十分重要;第2,涂层失效的大修时间,即总的使用寿命,这对于减少维修、提高经济效益颇为重要。
4.1.2材料要求(1)黏结底层材料。
常用的黏结底层材料是MCrAlY(M=Ni,Co,(孙福波等:氧化锆热障涂层在航空发动机上的应用和发展56/57液体等离子喷涂技术制备纳米ZrO2基TBCs是未来的发展方向,用SPS法沉积的ZrO2基纳米热障陶瓷涂层,综合了EB-PVD法和APS法的优点,克服了各自的缺点,有可能成为第4代和第5代航空发动机用的TBCs。
加Hf、Th等合金元素。
(2)氧化物类陶瓷面层材料即高纯Al2O3和经稳定化处理的ZrO2基陶瓷材料。
目前,在航空发动机上使用最普遍的是氧化钇部分稳定的氧化锆粉末材料。
4.1.3应用效果(1)提高了发动机功率和热效率。
例如:涡轮叶片背涂覆1厚27μm的TBCs,可使高温叶片的表面温度由1055℃降低到866℃减少因采用强制空气冷却而消耗喷涂TBCs的涡轮叶的叶片热量。
片,可以降低40%从而提高发动机热效率;这亦相当于降低了高温合金的受热温度,从而可进一步提高涡轮的燃气初温,进一步提高发动机功率(2)降低了燃油消耗。
降低了热耗,使燃油消耗降低约1.3%如美国250架喷气式飞机的全部1年高压涡轮叶片喷涂TBCs后,即可节约航空燃油3.78万m3,即每架飞机节约151m3/(年.架)。
(3)延长了使用寿命和大修期。
发动机热端部件喷涂TBCs后,使用寿命提高3~4倍,从而大大延长了发动机大修期,减少了停机和维修所带来的损失。