化学镀
化学镀技术概述

化学镀技术概述硬盘、CPU和内存被称为计算机的“三大件”。
随着计算机技术的发展,计算机硬盘逐步向小型、薄型、大容量和高速度方向发展。
在计算机硬盘中用于存储数据的是盘片,它由铝镁合金制成,然后在表面进行化学镀Ni-P或Ni-P-Cu,作为后续真空溅射磁记录薄膜的底层。
该镀层要求非磁性、低应力、表面光洁和均匀。
图5-17所示为计算机硬盘及化学镀镍后的CPU。
1.化学镀的原理和特点(1)化学镀的原理化学镀也称为无电解镀或自催化镀,在表面处理中占有重要的地位。
化学镀是指在没有外加电流通过的情况下,利用镀液中还原剂提供的电子,使溶液中的金属离子还原为金属并沉积在工件表面,形成镀层的表面处理技术。
酸性化学镀镍溶液中,还原沉积时的反应式为式中,H2PO2是还原剂。
图5-17 计算机硬盘及化学镀镍后的CPU化学镀镍溶液的组成及其相应的工作条件必须使反应只在具有催化作用的工件表面上进行,镀液本身不发生氧化还原反应,以免溶液自然分解、失效。
如果被镀金属本身是催化剂,则化学镀的过程就具有催化作用。
镍、铜、钴、铑、钯等金属都具有催化作用。
(2)化学镀的特点化学镀与电镀相比,具有如下特点:1)镀层厚度非常均匀,化学镀液的分散能力非常好,无明显的边缘效应,几乎是工件形状的复制。
所以化学镀特别适用于形状复杂的工件,尤其是有深孔、不通孔、腔体等的工件的电镀。
化学镀层非常光洁平整,镀后基本不需要镀后加工。
2)可以在金属、非金属、半导体等各种不同基材上镀覆。
化学镀可以作为非导体电镀前的导电底层镀层。
3)镀层致密,孔隙低,基体与镀层结合良好。
4)工艺设备简单,不需要外加电源。
5)化学镀也有其局限性,例如镀层金属种类没有电镀多,镀层厚度一般没有电镀高,化学镀的镀液成本一般比电镀液成本高。
2.化学镀镍化学镀镍是化学镀中应用最为广泛的一种方法。
化学镀镍多采用次磷酸盐、硼氢化物、氨基硼烷、肼及其衍生物等作为还原剂,其中次磷酸盐由于价格便宜,被广泛应用。
第五章电镀与化学镀.
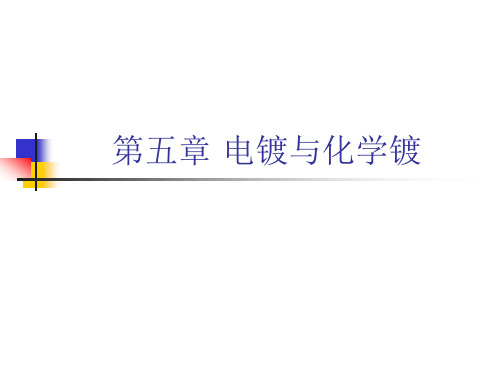
副反应消耗了部分电荷(量),使电流效率降低。 电流效率就是实际析出物质的质量与理论计算析出物 质的质量之比,即 η=(m’/ m)×100%=(m’/kIt)×100%
电镀液的分散能力:
指电镀液所具有的使金属镀层厚度均匀分布 的能力,也称均镀能力。电镀液的分散能力越好, 在不同阴极部位所沉积出的金属层厚度就越均匀。 根据法拉第电解定律可知,阴极各部分所沉积的 金属量(金属的厚度)取决于通过该部位电流的大小。 故镀层厚度均匀与否,实质上就是电流在阴极镀 件表面上的分布是否均匀。
活化液:
活化处理的实质是对工件的表面进行电解刻蚀和化学 腐蚀。 活化液的作用是用化学腐蚀和电解腐蚀的方法,去除 被镀零件表面的氧化膜和锈斑,使其露出金属本身组 织。 一般活化液都是酸性水溶液,具有较强的去除金属氧 化物的能力。活化液分为强活化液和弱活化液。
强活化液又分为硫酸型活化液和盐酸型活化液。硫酸 型活化液可采用各种金属,作用比较温和,正、反极 都可使用;盐酸型活化液比硫酸型活化液作用强烈, 也适用于各种金属,只能反极性作用。
缓冲剂:指用来稳定溶液酸碱度的物质。 阳极活化剂:镀液中能促进阳极活化的物质称 阳极活化剂。阳极活化剂的作用是提高阳极开 始钝化的电流密度,从而保证阳极处于活化状 态而能正常地溶解。 添加剂:添加剂是指不会明显改变镀层导电性, 而能显著改善镀层性能的物质。根据在镀液中 所起的作用,添加剂可分为:光亮剂、整平剂、 润湿剂和抑雾剂等。
影响电镀质量的因素
pH值的影响:
镀液中的PH值可以影响氢的放电电位,碱性夹 杂物的沉淀,还可以影响络合物或水化物的组成以及 添加剂的吸附程度。 电镀过程中,若pH值增大,则阴极效率比阳极效 率高,pH值减小则反之。通过加入适当的缓冲剂可以 将pH值稳定在一定范围。
化学镀
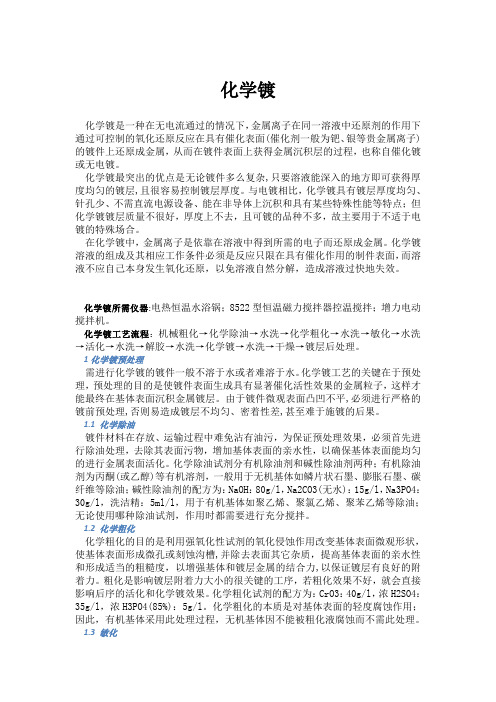
化学镀化学镀是一种在无电流通过的情况下,金属离子在同一溶液中还原剂的作用下通过可控制的氧化还原反应在具有催化表面(催化剂一般为钯、银等贵金属离子)的镀件上还原成金属,从而在镀件表面上获得金属沉积层的过程,也称自催化镀或无电镀。
化学镀最突出的优点是无论镀件多么复杂,只要溶液能深入的地方即可获得厚度均匀的镀层,且很容易控制镀层厚度。
与电镀相比,化学镀具有镀层厚度均匀、针孔少、不需直流电源设备、能在非导体上沉积和具有某些特殊性能等特点;但化学镀镀层质量不很好,厚度上不去,且可镀的品种不多,故主要用于不适于电镀的特殊场合。
在化学镀中,金属离子是依靠在溶液中得到所需的电子而还原成金属。
化学镀溶液的组成及其相应工作条件必须是反应只限在具有催化作用的制件表面,而溶液不应自己本身发生氧化还原,以免溶液自然分解,造成溶液过快地失效。
化学镀所需仪器:电热恒温水浴锅;8522型恒温磁力搅拌器控温搅拌;增力电动搅拌机。
化学镀工艺流程:机械粗化→化学除油→水洗→化学粗化→水洗→敏化→水洗→活化→水洗→解胶→水洗→化学镀→水洗→干燥→镀层后处理。
1化学镀预处理需进行化学镀的镀件一般不溶于水或者难溶于水。
化学镀工艺的关键在于预处理,预处理的目的是使镀件表面生成具有显著催化活性效果的金属粒子,这样才能最终在基体表面沉积金属镀层。
由于镀件微观表面凸凹不平,必须进行严格的镀前预处理,否则易造成镀层不均匀、密着性差,甚至难于施镀的后果。
1.1 化学除油镀件材料在存放、运输过程中难免沾有油污,为保证预处理效果,必须首先进行除油处理,去除其表面污物,增加基体表面的亲水性,以确保基体表面能均匀的进行金属表面活化。
化学除油试剂分有机除油剂和碱性除油剂两种;有机除油剂为丙酮(或乙醇)等有机溶剂,一般用于无机基体如鳞片状石墨、膨胀石墨、碳纤维等除油;碱性除油剂的配方为:NaOH:80g/l,Na2CO3(无水):15g/l,Na3PO4:30g/l,洗洁精:5ml/l,用于有机基体如聚乙烯、聚氯乙烯、聚苯乙烯等除油;无论使用哪种除油试剂,作用时都需要进行充分搅拌。
化学镀

化学镀
化学镀是指在没有外电流的作用下,利用化学方法使溶液中的金属离子还原为金属并沉积在基体表面,形成镀层的一种表面处理方法。
因此,化学镀实质是一自催化、可控的化学还原过程,还原反应只能在基体表面催化作用下进行,故化学镀又称自催化镀和无电解镀。
若待镀金属本身是反应的催化剂,则化学镀的过程就具有自动催化作用,使上述反应不断地进行,这时镀层厚度也逐渐增加。
钢铁、镍、钯、铑等都具有自动催化作用。
但对于不具有自动催化作用的工件表面,如塑料、玻璃、陶瓷等非金属材料,还需经过特殊的表面预处理,使其表面活化且具有催化作用,才能进行化学镀。
化学镀溶液的成分包括金属盐、还原剂、络合剂、缓冲剂、pH调节剂、稳定剂、加速剂、润湿剂和光亮剂等。
化学镀与电镀相比具有如下优点:不受零件形状限制,镀层厚度均匀;镀层晶粒细密,孔隙率低,耐蚀性强;不需要外加电源,设备简单,操作简便,生产清洁;能在非金属陶瓷、玻璃、塑料和半导体上施镀。
但化学镀使用温度较高,镀液内氧化剂与还原剂共存,溶液稳定性差,且镀液的维护、调整和再生均比较麻烦,故成本较高。
目前,已能运用化学镀的方法而获得金、银、铁、镍、铜、铬、钴、钯、锡等十余种金属镀层。
现代电镀网有多家电镀等相关园区的地址及联系方式,园区介绍等等,欢迎各位电镀人登陆本平台查看。
化学镀
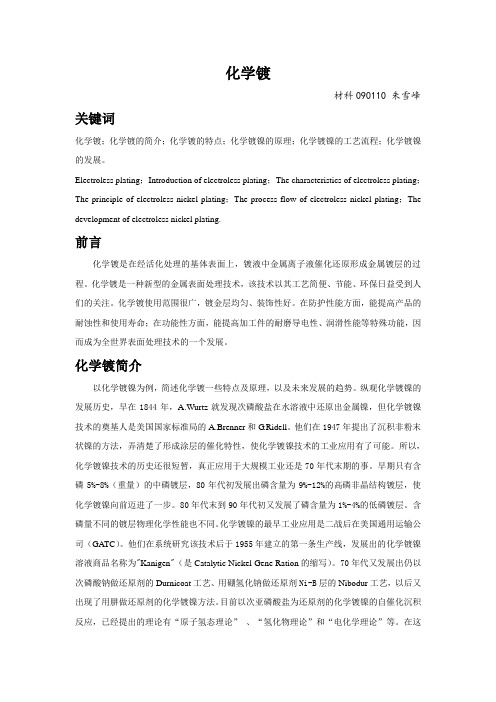
化学镀材科090110 朱雪峰关键词化学镀;化学镀的简介;化学镀的特点;化学镀镍的原理;化学镀镍的工艺流程;化学镀镍的发展。
Electroless plating;Introduction of electroless plating;The characteristics of electroless plating;The principle of electroless nickel plating;The process flow of electroless nickel plating;The development of electroless nickel plating.前言化学镀是在经活化处理的基体表面上,镀液中金属离子液催化还原形成金属镀层的过程。
化学镀是一种新型的金属表面处理技术,该技术以其工艺简便、节能、环保日益受到人们的关注。
化学镀使用范围很广,镀金层均匀、装饰性好。
在防护性能方面,能提高产品的耐蚀性和使用寿命;在功能性方面,能提高加工件的耐磨导电性、润滑性能等特殊功能,因而成为全世界表面处理技术的一个发展。
化学镀简介以化学镀镍为例,简述化学镀一些特点及原理,以及未来发展的趋势。
纵观化学镀镍的发展历史,早在1844年,A.Wurtz就发现次磷酸盐在水溶液中还原出金属镍,但化学镀镍技术的奠基人是美国国家标准局的A.Brenner和G.Ridell。
他们在1947年提出了沉积非粉末状镍的方法,弄清楚了形成涂层的催化特性,使化学镀镍技术的工业应用有了可能。
所以,化学镀镍技术的历史还很短暂,真正应用于大规模工业还是70年代末期的事。
早期只有含磷5%-8%(重量)的中磷镀层,80年代初发展出磷含量为9%-12%的高磷非晶结构镀层,使化学镀镍向前迈进了一步。
80年代末到90年代初又发展了磷含量为1%-4%的低磷镀层。
含磷量不同的镀层物理化学性能也不同。
化学镀镍的最早工业应用是二战后在美国通用运输公司(GA TC)。
化学镀

六.化学镀镍机制
化学镀镍实际上是镍一类金属(Ni-P;Ni-B)合金镀 层,在酸性镀液中,次磷酸盐作还原剂,可在铁、钴、钯 、铑、铂等活性金属的催化下发生镍和磷的化学共沉积, 其电化学过程包括下面的阳极过程和阴极过程。 局部阳极反应:H2PO2-+H2O-2e-→ H2PO3-+2H+ 局部阴极反应:Ni2++2e-→Ni↓ 2H++2e- → H2↑ H2PO2-+2H++e- → P ↓+2H2O 其中溢出氢气是副反应,另外,镀液还有可能发生次磷 酸盐自分解,亚磷酸镍析出等副反应,造成镀液不稳定, 所以,通常把镀液的PH值控制在4~5,或者加入合适的络 合剂和稳定剂,以保证镀液的稳定性和沉积速度。
九.化学镀溶液的维护调整
做好溶液生产管理和维护,对提高溶液的稳定性,防 止溶液自然分解,是保证镀层质量和降低成本的关键因素 。 1.首先做好镀前的预处理工作,必须把镀件清洗干净,防 止各种杂质或金属杂质带人镀液中,此杂质可能成为溶液 自发分解的触发剂,对镀液的危害最大。 2.在施镀中要控制镀件的装载量,装载量过高反应剧烈时 ,镍颗粒可能从镀层上脱落到镀液中,形成自催化还原中 心,就会加速溶液的自然分解。 3.及时添加材料调整PH值,施镀时对主盐和还原剂的消耗 最快,若不及时补充主盐和还原剂,就会影响镀层的质量 和镀液的稳定性。PH值是随着施镀的进行逐渐降低,如 不及时调整,亚磷酸盐的积累就会明显的增加,就会影响 沉积的速度和镀层的质量。
镀前处理中,酸洗是将金属工件浸入酸(或酸性盐)中, 除去金属表面的氧化膜、氧化皮以及锈蚀物。弱浸蚀的实 质是要剥离工件表面的加工变形层以及在前处理工序生成 的极薄的氧化物(因此也称活化),将基体组织暴露出来 以便镀层金属在其表面进行生长,因而不需要酸洗那样长 的时间。这个工序对镀层和基体的结合起到重要作用。弱 浸蚀的浸蚀溶液浓度低,浸蚀时间短(数秒至1min),多 在室温下进行。工件活化后,要立即清洗并开始实施化学 镀。 镀后处理中,热处理一方面是除氢及去应力的低温退火, 改善机械性能;另一方面形成一层钝化膜,封闭孔隙,阻 断腐蚀介质,进一步提高镀层的耐蚀性。
化学镀
无电镀14.1 无电镀(Electroless Plating)无电镀又称之为化学镀(chemical plating)或自身催化电镀(autocatalyticplating)。
无电镀是指于水溶液中之金属离子被在控制之环境下,予以化学还元,而不需电力镀在基材(substrate)上。
ASTM B374之标准定义为Autocatalyticplating -〝deposition of a metallic coating by a controlled chemicalreduction that is catalyzed by the metal or alloy being deposited〞。
其过程(process)不同于浸镀(immersion plating),它的金属镀层是连续的(continu-ous)、自身具有催化性的(autocatalytic)。
14.2 无电镀的特性优点:1. 镀层非常均匀,也就是均一性(throwing power)非常好,因它没有电流分布不均的困难,镀件内外都显出均匀,锐边及角等节状镀层(nodular deposits )情形可完全消除。
2.镀层孔率较少,其耐蚀性比电镀为佳。
3.电源、电器接线、导电棒、汇流及电器仪表都可省略,减少装架及各种附属设备。
4 可镀在非导体上(需做适当前处理)。
5 镀层具有独特的物理、化学、机械性质及磁性。
6 复合镀层(co-deposit),多元合金(polyalloy)可形成。
7 密着性、耐磨性良好。
8操作较简单。
9精密零件、管子、深孔内部可完全镀上。
应用在如轴心、半导体制造。
10制品与导体接触也可完全镀上。
缺点:1.价格较贵。
2.镀层厚度受限制(理论上应无限制)。
3.工业上应用较多、装饰性光泽较不易达成。
应用:1. 非导体的电镀,如塑料电镀。
2. 精密零件,如轴心。
3. 半导体、印刷电路板、电子零件。
4. 须特别耐蚀的化学机械零件,如管件内部。
化学镀资料
化学镀铝和铝合金有易产生晶间腐蚀,表面硬度低,不耐磨损等弱点。
在其表面进行化学镀处理,可以改善一些性能:改善耐腐蚀性,提高耐磨性,良好的耐磨性,高硬度,提高装饰性。
而纳米TiO2的加入,可以显著提高镀层的耐磨性,硬度,自润滑性,耐腐蚀性等性能。
化学镀概述化学镀:也称无电解镀,是在无外加电流的化学沉积过程。
借助合适的还原剂,使镀液中金属离子还原成金属,并沉积到零件表面的一种镀覆方法。
也叫做”自催化镀”,”无电解电镀”。
化学镀可以分为“置换法”,“接触度”,“还原法”。
一.化学镀相对电镀优点①化学镀可以用于各种基体,包括金属,非金属以及半导体。
②化学镀镀层均匀,无论工件如何复杂,只要采用合适的施镀方法,都可以在工件上得到均一镀层。
③对于可以自催化的化学镀而言,理论上可以得到任意厚度的镀层。
④化学镀所得到的镀层有很好的化学,机械,磁性性能。
⑤化学镀相对电镀而言最大的优点是镀层厚度均匀,针孔率低。
二.发展概况1.1844年,A.Wurtz通过亚磷酸盐还原镍得到了金属镍的镀层。
2.1911年,Bretean发表有关沉积过程是镍与次磷酸盐的催化过程的化学镀研究报告。
3.1916年,Roux从柠檬酸盐一次亚磷酸盐体系中得到了镀镍层,注册了第一份化学镀镍专利。
4.1944年,美国国家标准局从事轻武器改进研究的A.Brenner与G.Riddel在枪管实验中证实了次亚磷酸钠催化还原镍,1946年,1947年,两人公布了研究结果。
5.20世纪五十年代,美国通用运输公司对化学镀镍溶液组成与工艺进行系统研究。
为后来化学镀镍工业应用奠定基础。
6.1955年,开发出“Kanigen”技术;1964年,开发出“Durapositli”技术;1968年,开发出“Durnicoat”技术;1978年至1982年,开发成“诺瓦泰克”商品镀液。
7.20世纪六十年代,小规模化学镀镍工艺进入美国市场。
8.20世纪七十年代末至八十年代初,化学镀镍研究重点转向高磷镀层。
化学镀镍
化学镀工艺化学镀,又称为无电解镀。
因为在工件施镀的过程中,虽说有电子转移,但无须外接电源,工件表面镀层完全是靠化学氧化还原反应实现的。
化学镀是指在无外加电流的状态下,利用一种合适的还原剂,使镀液中的金属离子还原并沉积在基体表面上的化学还原过程。
或者说,化学镀是将零件浸入到溶液中在催化剂的作用下在表面发生的金属的沉积,是一个在界面上发生的催化沉积的过程。
因此和电镀不同,化学镀过程不需要整流电源和阳极。
金属沉积仅在零件表面上进行,电子是通过溶解于溶液中的化学还原剂提供的。
完成化学镀的过程有三种方式:(1)置换沉积利用被镀金属的电位比沉积金属负,将沉积金属离子从溶液中置换在工件表面上。
其化学反应可表述为Me1+Me2n+→Me2+Me1m+溶液中金属离子被还原沉积的同时,伴随着基体金属的溶解,当基体金属表面被沉积金属完全覆盖时,反应即自动停止。
所以,采用这种方法得到的镀层非常薄。
(2)接触沉积利用电位比被镀金属高的第三金属与被镀金属接触,让被镀金属表面富积电子,从而将沉积金属还原在被镀金属表面。
其化学反应实际上与置换沉积相同,只是Me,不是基体金属,而是第三金属。
其缺点是第三金属离子会在溶液中积累。
(3)还原沉积利用还原剂被氧化时释放出的自由电子,把沉积金属还原在镀件表面;其反应过程可表述为:Me n++Re→Me+OX式中Me——沉积金属;Re——表示还原剂;0X——表示氧化剂。
一般意义上的化学镀是指这种还原沉积化学镀。
它只在具有催化作用的表面上发生。
如果沉积金属(如镍:铜等)本身就是反应的催化剂,该化学镀过程就称为自催化化学镀,它可以得到所需的镀层厚度。
如果在催化表面上沉积的金属本身不能作为反应的催化剂,一旦催化表面被沉积金属覆盖,沉积反应就会自动终止,所以只能获得有限厚度的镀层.化学镀可以在金属、半导体和非导体材料上直接进行,由于没有电流分布的问题,在复杂零件表面可以获得厚度均匀、孔隙率低、对深孔或形状复杂的零件具有很好覆盖能力的镀层。
化学镀简介
能,晶粒细,无孔,耐蚀性好。 5. 化学镀工艺设备简单,不需要电源、输出系统及辅助
电极,操作时只需把工件正确悬挂在镀液中即可。 6. 化学镀溶液稳定性较差,寿命短,成本高。
化学镀的条件
1. 镀液中还原剂的还原电位要显著低于沉积金属的电位。 2. 镀液不产生自发分解。 3. 调节溶液PH值、温度时,可以控制金属的还原速率,
比较单纯 比较小 比较小 大 长 不均匀 导体 低
相当复杂 大 大 小 短 非常均匀 导体、非导体 高
化学镀镍的基本原理
化学镀镍的发展
1944年,Brenner和Riddell进行了第一次实验室实验,开 发了可以工作的镀液并进行了科学研究。
60~70年代,研究人员主要致力于改善镀液性能。
80年代后,镀液寿命、稳定性等得到初步解决,基本实 现镀液的自动控制。
原子氢态理论
1946年,Brenner和Ridder提出;1959年Gutgeit实验验证了该假说 1967年,苏联人对该理论又做了深入研究提出:还原镍的物质实质上就
是原子氢。
NaH2PO2→ Na++H2PO2-
1)镀液在加热时,通过次亚磷酸盐在水溶液中脱氢,形成亚磷酸根,同 时放出初生态原子氢
活化:
为了使待镀件获得充分活化的表面,以催化化学镀反应的进行。
化学镀铜基本原理
• 化学镀铜概述:
化学镀铜是电路板制造中的一种工艺,通常也叫沉铜, 是一种自身催化性氧化还原反应。首先用活化剂处理,使 绝缘基材表面吸附上一层活性的粒子通常用的是金属钯 (ba)粒子(钯是一种十分昂贵的金属),铜离子首先在 这些活性的金属钯粒子上被还原,而这些被还原的金属铜 晶核本身又成为铜离子的催化层,使铜的还原反应继续在 这些新的铜晶核表面上进行。
- 1、下载文档前请自行甄别文档内容的完整性,平台不提供额外的编辑、内容补充、找答案等附加服务。
- 2、"仅部分预览"的文档,不可在线预览部分如存在完整性等问题,可反馈申请退款(可完整预览的文档不适用该条件!)。
- 3、如文档侵犯您的权益,请联系客服反馈,我们会尽快为您处理(人工客服工作时间:9:00-18:30)。
1.化学镀的发展化学镀的发展史主要就是化学镀镍的发展史。
虽然早在1844年A.Wurtz就发现次磷酸盐在水溶液中还原出金属镍,但化学镀镍技术的奠基人是美国国家标准局的 A.Brenner和G.Ridell。
他们在1947年提出了沉积非粉末状镍的方法,弄清楚了形成涂层的催化特性,使化学镀镍技术工业应用有了可能性。
所以,化学镀镍技术的历史还很短暂,真正大规模工业还是70年代末期的事。
早期只有含磷5%-8%(重量)的中磷镀层,80年代初发展出磷含量为9%-12%的高磷非晶结构镀层,使化学镀镍向前迈进一步。
80年代末到90年代初又发展了磷含量为1%-4%的低磷镀层。
含磷量不同的镀层物理化学镀性能也不同。
化学镀镍的最早工业应用是二战后在美国通用运输公司(GATC)。
他们在系统研究该技术后于1955年建立的第一条生产线,发展出的化学镀镍溶液商品名称为"Kanigen"(是Catalytic Nickel Gene Ration学缩写)。
70年代又发展出仍以次磷酸钠还原剂的Durnicoat工艺、用硼氢化钠做还原剂Ni-B层的Nibodur工艺,以后又出现了用肼做还原剂的化学镀镍方法。
化学镀镍技术的核心是镀液的组成及性能,所以化学镀镍发展史中最值得注意的是镀液本身的进步。
在60年代之前由于镀液化学知识贫乏,只有中磷镀液配方,镀液不稳定,往往只能稳定数小时,因此为了避免镀液分解只有间接加热,在溶液配制、镀液管理及施镀操作方面必须十分小心,为此制定了许多操作规程给以限制。
此外,还存在沉积速度慢、镀液寿命短等缺点。
为了降低成本,延长镀液使用周期,只好使镀液“再生”,再生的实质就是除去镀液中还原剂的反应产物,次磷酸根氧化产生的亚磷酸根。
当时使用的方法有弃去部分旧镀液添加新镀液、加FeCl3或Fe2(SO4)3以沉淀亚磷酸根(形成Na2[Fe(OH)(HPO3)2])·20H2O黄色沉淀)、离子交换法等,这些方法既麻烦又不适用。
70年代以后多种络合剂、稳定剂等添加剂的出现,经过大量的试验研究、筛选、复配以后,新发展的镀液均采用“双络合、双稳定”、甚至“双络合、双稳定、双促进”配方,这样不仅使镀液稳定性提高、镀速加快,更主要的是大幅度增加了镀液对亚磷酸根容忍量,最高达600-800g/LNa2HPO3·5H2O,这就使镀液寿命大大延长,一般均能达到4-6个周期,甚至10-12个周期,镀速达17-25μm/h。
这样,无论从产品质量和经济效益角度考虑,镀液已不值得进行“再生”,而直接做废液处理。
近来,为了改革镀层质量、减少环境污染,已改用新型有机稳定剂,不再使用重金属离子,从而显著提高了镀层的耐蚀性能。
目前,化学镀液均已商品化,根据用户要求有各种性能化学镀的开缸及补加浓缩液出售,施镀过程中只需按消耗的主盐、还原剂、pH调节剂及适量的添加剂进行补充,使用十分方便。
据不完全统计,目前世界上至少有两百种以上的成熟化学镀镍配方,一些有代表性出售镀液的公司有:美国的M&T Chemicals Ltd., Allied-Kelite Div., Witco Chemical Corp., Enthone Inc., Shipley Company, Hidility Co. Wear- Cote International Inc.;英国的W. Canning Materials Ltd., Harshaw Chemicals Limited;德国的Friedr. Blasberg Gmbh. &Co. K G, Auto Tech;日本的上村株式会社、奥野株式会社等。
我国化学镀工业目前正逐步走向成熟。
从1959年美国召开第一届化学镀镍学术会议以后,陆续发表了大量的论文及专利,还出版了有关专著,如G.G.Gawrilov:Chemical (Electroless)Nickel-plating 1974;G.O.Mallory: Electroless Plating Fundment als and Application 1990。
美国电化学学会秋季年会(暨美国固体电路制造学会年会),于1989年开始建立化学镀学术研究报告专集,由此可见化学镀学术研究的普遍性。
由于电子计算机、通信等高科技产业的迅猛发展,为化学镀技术提供了巨大的市场。
80年代是化学镀技术的研究、开发和应用飞跃发展时期,西方工业化国家化学镀镍的应用,在与其他表面处理技术激烈竞争的形势下,年净增长速率曾在到15%;这是金属沉积史上空前的发展速度。
预期化学镀技术将会持续高速发展,平均年净增速率将降至6%,而进入发展成熟期。
我国的化学镀市场与国际相比起步晚、规模小,但近十几年发展极期迅速,不仅有大量的论文发表,还举行了全国性的专业会议,相信在今后几年内会越来越广泛的应用该项技术,并逐步走向稳定和成熟。
2 化学镀研究现状化学镀由于其独有的特点,所以从诞生之日起,就引起了各国研究者的广泛关注。
迄今为止,化学镀的研究焦点由当初的化学镀镍已经辐射到了多种金属与合金的镀覆工艺及原理的研究,如化学镀Cu、Co、Pa、Au、Fe-W-B等。
化学镀液中采用的还原剂种类已由单一的次亚磷酸钠发展到甲醛、硼氢化物、联氨、乙酚酸、氨基硼烷及它们的衍生物等。
化学镀液在使用过程中由于存在杂质、固体微粒,所以很容易自然分解而失效,为了很好地解决这类问题,从而激起了许多研究者寻找及研制稳定剂的兴趣。
目前所用的稳定剂主要有三类:硫脲等含硫化合物;重金属离子如Pb2+、Bi2+、Cd2+等;含氧酸盐如钼酸盐等。
随着科技的发展,各种新材料层出不穷,化学镀为了适应这种发展的需要,所涉及的基体材料已由钢铁扩展到了不锈钢、铝及铝合金、塑料、玻璃、陶瓷等,而且应用的基体形状由比较规则的块体、板材发展到了各种不规则的微粒,从而进一步地拓宽了化学镀的研究领域。
对化学镀镀层的前期研究主要着眼于耐磨及耐蚀性能,而现在有不少研究是针对其电学、磁学性能。
随着化学镀在工业上的应用范围和生产规模不断扩大以及人们环保意识的日益增强,化学镀废液所导致的环境污染已经越来越受到人们的重视,所以研究化学镀液的净化和再利用就成了一个比较时新的研究方向,并且已取得了一些研究成果。
3 化学镀的应用3.1 化学镀镍的应用化学镀镍通常是指酸性化学镀Ni-P合金,而实际上化学镀镍是一个大家族的统称,对于化学镀层的选取取决于各种不同的用途。
化学镀镍合金层因种类与成分的差异,使其表现出各种不同的性能,大大地扩充了应用的领域。
3.1.1 化学镀Ni-P合金Ni-P合金镀层随着磷含量的不同(1%~14%)而分为低磷、中磷和高磷三种,其物理、电学性能以及表面特征差别很大。
此外,对镀层进行不同条件下的热处理也会使其性能有较大的改变。
就物理性能来说,Ni-P合金的耐蚀性、耐磨性能优良,因而使其在汽车的发动机、化学药品运输槽车以及采矿和石油、天然气等工业得到了广泛的应用。
在电学性能方面,含磷量在5%~15%的Ni-P合金镀层呈现非晶型结构状硬盘态,具有高电阻系数、低温度电阻系数(TCR)和非磁性,使其在电子元器件行业得到了一定的应用,而且利用高磷含量Ni-P合金镀层的非磁性,大量用于铝制的基底镀层、电子仪器、半导体电子设备防电磁波干扰的屏蔽层等。
化学镀Ni-P合金在复合材料的制造上也有一定的应用,如用粉末冶金方法制造的SiC/Fe金属基复合材料,由于SiC粒子与Fe基体界面的物理、化学性质差异太大,因而两者的复合性能很差,可通过在粒子表面化学镀覆Ni-P 合金来改善两者的复合性能。
3.1.2 化学镀Ni-B合金和Ni-P合金镀层一样,Ni-B合金镀层的性能随硼含量的改变而变化,低硼含量(0.2%~3%)合金镀层最适用于工业应用。
低硼含量的合金镀层具有高的电导率、低的接触电阻以及良好的钎焊性能,所以Ni-B合金镀层特别适合在电子元器件行业的应用,而且Ni-B合金镀层在不少场合已经部分或全部代替了金的使用。
含硼量偏高的Ni-B合金镀层具有很高的硬度,当对其进行热处理还会进一步地提高其硬度,如含硼2%的Ni-B合金镀层,其努氏硬度大约为750Knoop,而将其进行250℃×1h的热处理,可将其硬度提高到约1150Knoop。
Ni-B合金还可以实现Ni-B-Al2O3、Ni-B-SiC化学复合镀,能获得耐磨、减摩以及附着强度优良的镀层,所以被大量的应用于各种机械的耐磨零部件、模具等,从而延长了各种机械以及模具的使用寿命。
3.1.3 其它化学镀镍合金其它种类的化学镀镍有:Ni-P合金的化学复合镀,如Ni-P-MoS2、Ni-P-SiC 等,其主要应用在耐磨性要求较高的场合;具有软磁性能的Ni-Fe-P镀层、磁盘内记录媒体的Co-Ni-P镀层以及垂直记录媒体的Co-Ni-Re-P镀层;具有优良耐蚀性、耐磨性、抗磁性以及低电阻抗的Ni-Cu-P镀层等。
3.2 化学镀铜的应用化学镀铜自1947年HNarcus首次报导以来,已形成了比较成熟的工艺。
但以往的研究在还原剂的选择上始终局限于甲醛(HCHO),因甲醛有令人难以忍受的气味,并且在镀覆过程中还会释放有害气体,所以很有必要寻求一种新型的还原剂。
目前,在甲醛的替代物的研究上已取得了较大的进展,已报导的替代物有次亚磷酸盐(如NaH2PO2)、乙酚酸、DMAB(二甲基乙酰胺酸)等。
其中以次亚磷酸盐作为还原剂的化学镀铜液,其镀层表面要比用甲醛作还原剂而获得的镀层更光滑,且前者在镀速及镀层组成、结晶形态方面也显示出后者所不具有的优势。
化学镀铜层由于其良好的延展性、电学特性以及无边缘效应,使其在塑料金属化,特别是在电子工业中得到了广泛的应用。
采用次亚磷酸钠作还原剂的化学镀铜新工艺可获得针状结晶的镀铜层,如果将其应用在多层印刷电路板的制造上,与各种树脂基体有很高的附着强度;并且将化学镀铜与化学镀镍结合起来应用时,可以制造各种对电磁波屏蔽要求较高的场合。
而且化学镀铜也可以用来包覆粉末并结合粉末冶金方法来制造复合材料。
3.3 其它化学镀技术的应用3.3.1 化学镀钯与化学镀金化学镀钯及钯合金在某些应用上已经发展成了化学镀金的一种更经济的代替工艺。
钯与金有着不同的沉积硬度与熔点,但是两者都有优越的抗氧化性能、在高温高湿的氛围中性能稳定。
化学镀钯主要应用于双列式封装电路(DIPs)以及其它的各种混合电路中,但随着科技的发展,电路以及各种仪器会更加复杂化、微型化,化学镀钯由于其钎焊性以及其它某些性能逊色于化学镀金,所以在这些场合化学镀金仍占有不可替代的地位。
但由于化学镀金成本高昂,所以寻求高效以及在满足性能的条件下获得尽可能薄的镀金层的工艺将是一个很好的发展方向。