汽轮机静态试验方案
汽轮机调节系统静态试验作业指导书
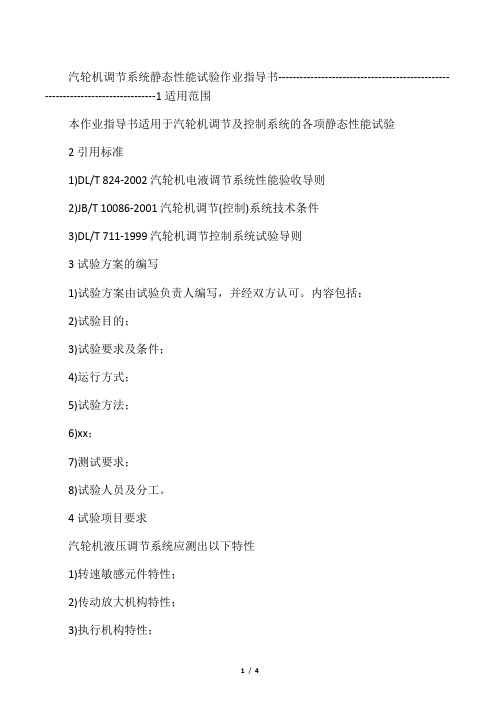
汽轮机调节系统静态性能试验作业指导书-------------------------------------------------------------------------------1适用范围本作业指导书适用于汽轮机调节及控制系统的各项静态性能试验2引用标准1)DL/T 824-2002汽轮机电液调节系统性能验收导则2)JB/T 10086-2001汽轮机调节(控制)系统技术条件3)DL/T 711-1999汽轮机调节控制系统试验导则3试验方案的编写1)试验方案由试验负责人编写,并经双方认可。
内容包括:2)试验目的;3)试验要求及条件;4)运行方式;5)试验方法;6)xx;7)测试要求;8)试验人员及分工。
4试验项目要求汽轮机液压调节系统应测出以下特性1)转速敏感元件特性;2)传动放大机构特性;3)执行机构特性;4)转速负荷特性5)绘制“四象限图”;6)测取汽门关闭时间。
汽轮机电液调节系统(DEH)的静态试验应包括仿真试验、汽门关闭时间测试、执行机构特性等仿真试验应包括如下功能:1)转速控制功能试验2)负荷控制功能试验3)压力控制功能试验4)同期功能试验5)OPC功能试验6)超速试验7)阀门活动试验8)一次调频试验9)甩负荷试验10)汽门关闭时间测试11)执行机构特性4试验记录。
1)液压调节系统应绘制四象限图及汽门关闭时间;2)电液调节系统应测取仿真试验曲线及汽门关闭时间;5试验技术报告的编写试验的技术报告是对试验的详细总结。
因此应包括下列内容:1)试验目的及范围;2)调节系统类型、动作原理、设备概况;3)测点及仪器仪表一览表,注明精度;4)试验方法及试验条件5)试验结果用表格、曲线或图示表示6)试验结果与要求的技术规范进行比较,并作出分析评价。
7)结论与建议6试验方案与试验报告的版式1)试验方案与试验报告一律采用如下版式进行排版:2)纸张大小:采用A4纸进行排版;宽21厘米,高度29.7厘米纵向排版:3)页边距:上2.8厘米,下2.8厘米,左2.5厘米,右2.5厘米;预留装订4)线0厘米,装订位置:边,页眉距上边1.5厘米,页脚距下边1.75厘米5)段落行距1.5字符高6)试验报告封面采用编号如XX-XXX-XX-XX试验报告形式:第一项服务项目顾客名称的拼音字头;第二项是编制单位;第三项文件序号;第四项是年份7)封面标题:采用研究院统一格式8)正文中标题:采用黑体四号字;正文xx标题:采用xx小四号字;9)页眉和页脚:页眉为试验报告的标题:页脚为:xx电力科学研究院汽轮机技术研究所10)页码:采用插入页面低端居中11)图表:每张图均要有图号和名称,写在图的下边;每张表均要有表号和名称,写在表的上边。
汽轮机静态试验
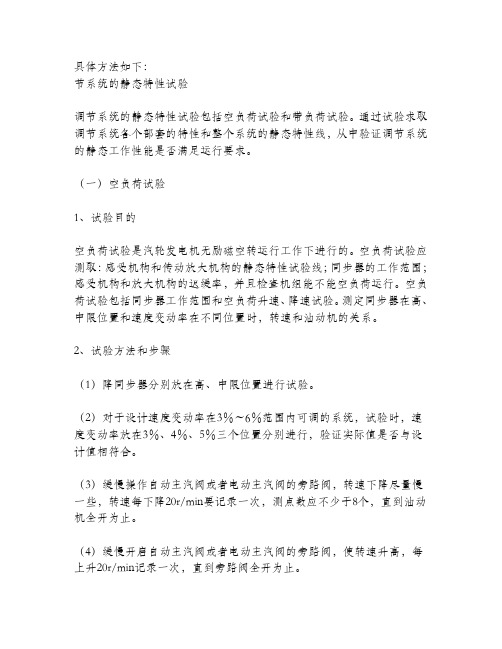
具体方法如下:节系统的静态特性试验调节系统的静态特性试验包括空负荷试验和带负荷试验。
通过试验求取调节系统各个部套的特性和整个系统的静态特性线,从中验证调节系统的静态工作性能是否满足运行要求。
(一)空负荷试验1、试验目的空负荷试验是汽轮发电机无励磁空转运行工作下进行的。
空负荷试验应测取:感受机构和传动放大机构的静态特性试验线;同步器的工作范围;感受机构和放大机构的迟缓率,并且检查机组能不能空负荷运行。
空负荷试验包括同步器工作范围和空负荷升速、降速试验。
测定同步器在高、中限位置和速度变动率在不同位置时,转速和油动机的关系。
2、试验方法和步骤(1)降同步器分别放在高、中限位置进行试验。
(2)对于设计速度变动率在3%~6%范围内可调的系统,试验时,速度变动率放在3%、4%、5%三个位置分别进行,验证实际值是否与设计值相符合。
(3)缓慢操作自动主汽阀或者电动主汽阀的旁路阀,转速下降尽量慢一些,转速每下降20r/min要记录一次,测点数应不少于8个,直到油动机全开为止。
(4)缓慢开启自动主汽阀或者电动主汽阀的旁路阀,使转速升高,每上升20r/min记录一次,直到旁路阀全开为止。
(5)按照上述方法,把同步器放在中限位置,重新做一遍。
(6)试验中,记录:转速与油动机行程以及一次油压、二次油压、随动错油阀行程、控制油压的关系线。
(二)带负荷试验1、试验目的带负荷试验是机组并入网内运行时,通过增、减负荷来测取:油动机行程与负荷的关系;同步器行程与油动机行程的关系;油动机行程与各个调节阀开度的关系;各个调节阀开度与前后压力的关系。
检查调节系统在各个负荷下运行是否稳定,在负荷变化时有无长时间的不稳定情况出现。
试验总记录的项目:负荷、新蒸汽流量、油动机行程、调节阀开度、调节阀前后压力、调节级汽室压力、同步器行程、电网频率、新蒸汽压力和温度、真空度等。
2、试验方法和步骤(1)空负荷点的记录就用并网前的记录,因并网后,负荷很难调到零。
汽轮机静态试验方案
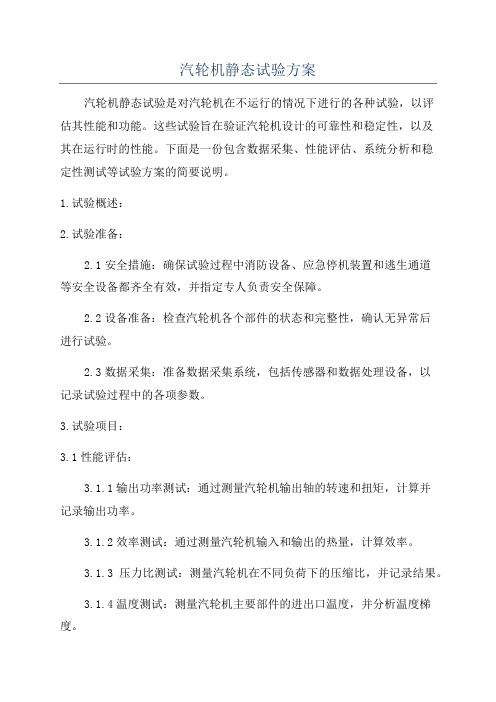
汽轮机静态试验方案汽轮机静态试验是对汽轮机在不运行的情况下进行的各种试验,以评估其性能和功能。
这些试验旨在验证汽轮机设计的可靠性和稳定性,以及其在运行时的性能。
下面是一份包含数据采集、性能评估、系统分析和稳定性测试等试验方案的简要说明。
1.试验概述:2.试验准备:2.1安全措施:确保试验过程中消防设备、应急停机装置和逃生通道等安全设备都齐全有效,并指定专人负责安全保障。
2.2设备准备:检查汽轮机各个部件的状态和完整性,确认无异常后进行试验。
2.3数据采集:准备数据采集系统,包括传感器和数据处理设备,以记录试验过程中的各项参数。
3.试验项目:3.1性能评估:3.1.1输出功率测试:通过测量汽轮机输出轴的转速和扭矩,计算并记录输出功率。
3.1.2效率测试:通过测量汽轮机输入和输出的热量,计算效率。
3.1.3压力比测试:测量汽轮机在不同负荷下的压缩比,并记录结果。
3.1.4温度测试:测量汽轮机主要部件的进出口温度,并分析温度梯度。
3.2系统分析:3.2.1空气动力特性测试:通过改变进气流量和排气背压,测量汽轮机的压比和效率变化,并绘制相应的特性曲线。
3.2.2冷却系统分析:通过测量冷却器和润滑系统的参数,评估冷却效果和润滑性能。
3.2.3热力学分析:通过测量燃烧室温度、压力和流量等参数,分析燃烧过程和热力学性能。
3.3稳定性测试:3.3.1负荷变化测试:通过改变汽轮机的负荷,测试其响应时间和稳定性。
3.3.2转速变化测试:通过改变汽轮机的转速,测试其稳态和瞬态响应。
4.试验结果分析和报告:根据试验数据,进行结果分析,比较试验结果和设计要求,评估汽轮机的性能和功能。
根据试验分析编写报告,汇总试验结果和结论,并提出改进建议。
这是一份简要的汽轮机静态试验方案,旨在对汽轮机进行详尽的测试,评估其性能和功能。
实际试验需要根据具体的汽轮机型号和设计要求,结合相关标准和规范进行详细设计和操作。
试验过程中要确保安全,及时处理异常情况,并根据试验结果进行数据分析和结论总结,为汽轮机性能改进和优化提供依据。
汽轮机调节系统静态试验

汽轮机调节系统静态试验
汽轮机调节系统静态试验是对汽轮机调节系统进行性能评估和校准的一种测试方法。
这个测试通常是在汽轮机安装和调试阶段进行,以确保汽轮机的调节系统能够稳定、准确地控制汽轮机的负荷和转速。
在汽轮机调节系统静态试验中,通常会进行以下步骤:
1.准备:在进行试验之前,需要对汽轮机和调节系统进行充分准备,包括检查
设备的连接和传感器的校准等。
2.设定目标值:确定汽轮机的目标负荷和转速等工作参数。
3.施加负荷:通过调节系统,逐步施加负荷到目标值,并记录汽轮机在不同负
荷下的运行状态和性能。
4.调整校准:根据实际测试结果,对调节系统进行必要的调整和校准,确保其
能够准确地控制汽轮机的负荷和转速,达到预期的性能要求。
5.稳态测试:在每个设定的负荷下,对汽轮机进行稳态测试,观察汽轮机的运
行稳定性和响应性能。
6.记录和分析:将试验结果进行记录和分析,评估汽轮机调节系统的性能是否
满足设计和要求,并进行必要的改进和优化。
通过汽轮机调节系统静态试验,可以确保汽轮机在正常运行过程中能够稳定、可靠地工作,满足工程和安全要求。
这个测试是汽轮机调试和调整的重要步骤之一。
实验三汽轮机调节系统静态特性的测试
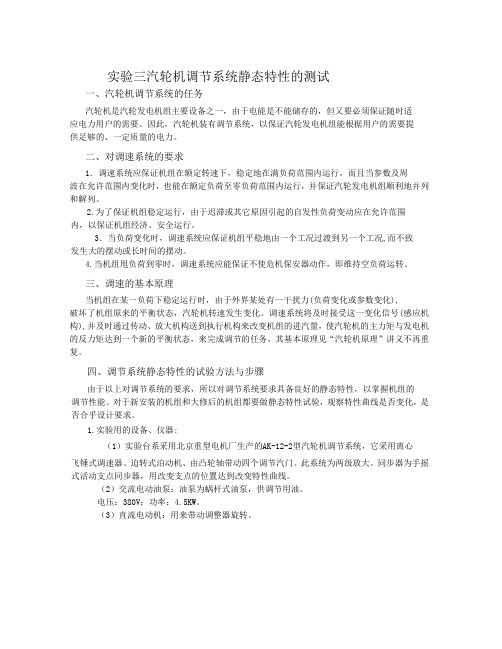
实验三汽轮机调节系统静态特性的测试一、汽轮机调节系统的任务汽轮机是汽轮发电机组主要设备之一,由于电能是不能储存的,但又要必须保证随时适应电力用户的需要。
因此,汽轮机装有调节系统,以保证汽轮发电机组能根据用户的需要提供足够的、一定质量的电力。
二、对调速系统的要求1.调速系统应保证机组在额定转速下,稳定地在满负荷范围内运行。
而且当参数及周波在允许范围内变化时,也能在额定负荷至零负荷范围内运行,并保证汽轮发电机组顺利地并列和解列。
2.为了保证机组稳定运行,由于迟滞或其它原因引起的自发性负荷变动应在允许范围内,以保证机组经济、安全运行。
3.当负荷变化时,调速系统应保证机组平稳地由一个工况过渡到另一个工况,而不致发生大的摆动或长时间的摆动。
4.当机组甩负荷到零时,调速系统应能保证不使危机保安器动作,即维持空负荷运转。
三、调速的基本原理当机组在某一负荷下稳定运行时,由于外界某处有一干扰力(负荷变化或参数变化),破坏了机组原来的平衡状态,汽轮机转速发生变化。
调速系统将及时接受这一变化信号(感应机构),并及时通过传动、放大机构送到执行机构来改变机组的进汽量,使汽轮机的主力矩与发电机的反力矩达到一个新的平衡状态,来完成调节的任务。
其基本原理见“汽轮机原理”讲义不再重复。
四、调节系统静态特性的试验方法与步骤由于以上对调节系统的要求,所以对调节系统要求具备良好的静态特性,以掌握机组的调节性能。
对于新安装的机组和大修后的机组都要做静态特性试验,观察特性曲线是否变化,是否合乎设计要求。
1.实验用的设备、仪器:(1)实验台系采用北京重型电机厂生产的AK-12-2型汽轮机调节系统,它采用离心飞锤式调速器、迫转式泊动机、由凸轮轴带动四个调节汽门。
此系统为两级放大。
同步器为手摇式活动支点同步器,用改变支点的位置达到改变特性曲线。
(2)交流电动油泵:油泵为蜗杆式油泵,供调节用油。
电压:380V;功率:4.5KW。
(3)直流电动机:用来带动调整器旋转。
汽轮机静态试验方案
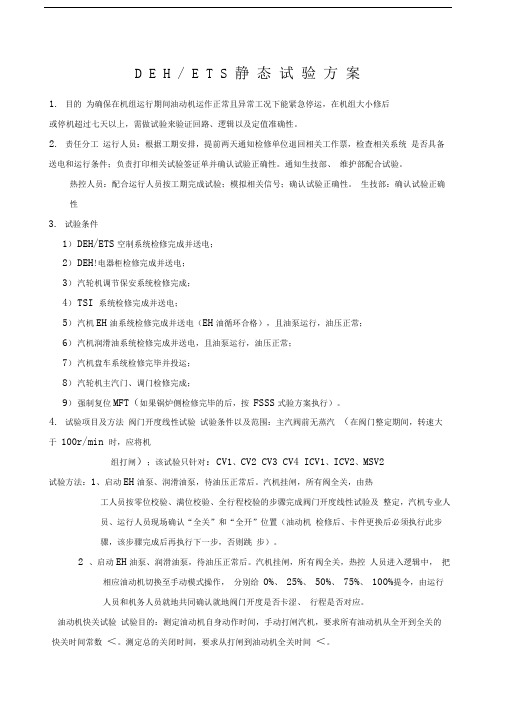
D E H / E T S 静态试验方案1. 目的为确保在机组运行期间油动机运作正常且异常工况下能紧急停运,在机组大小修后或停机超过七天以上,需做试验来验证回路、逻辑以及定值准确性。
2. 责任分工运行人员:根据工期安排,提前两天通知检修单位退回相关工作票,检查相关系统是否具备送电和运行条件;负责打印相关试验签证单并确认试验正确性。
通知生技部、维护部配合试验。
热控人员:配合运行人员按工期完成试验;模拟相关信号;确认试验正确性。
生技部:确认试验正确性3. 试验条件1)DEH/ETS空制系统检修完成并送电;2)DEH!电器柜检修完成并送电;3)汽轮机调节保安系统检修完成;4)TSI 系统检修完成并送电;5)汽机EH油系统检修完成并送电(EH油循环合格),且油泵运行,油压正常;6)汽机润滑油系统检修完成并送电,且油泵运行,油压正常;7)汽机盘车系统检修完毕并投运;8)汽轮机主汽门、调门检修完成;9)强制复位MFT(如果锅炉侧检修完毕的后,按FSSS式验方案执行)。
4. 试验项目及方法阀门开度线性试验试验条件以及范围:主汽阀前无蒸汽(在阀门整定期间,转速大于100r/min 时,应将机组打闸);该试验只针对:CV1、CV2 CV3 CV4 ICV1、ICV2、MSV2试验方法:1、启动EH油泵、润滑油泵,待油压正常后。
汽机挂闸,所有阀全关,由热工人员按零位校验、满位校验、全行程校验的步骤完成阀门开度线性试验及整定,汽机专业人员、运行人员现场确认“全关”和“全开”位置(油动机检修后、卡件更换后必须执行此步骤,该步骤完成后再执行下一步,否则跳步)。
2 、启动EH油泵、润滑油泵,待油压正常后。
汽机挂闸,所有阀全关,热控人员进入逻辑中,把相应油动机切换至手动模式操作,分别给0%、25%、50%、75%、100%提令,由运行人员和机务人员就地共同确认就地阀门开度是否卡涩、行程是否对应。
油动机快关试验试验目的:测定油动机自身动作时间,手动打闸汽机,要求所有油动机从全开到全关的快关时间常数<。
汽轮机调节系统静态试验
汽轮机调节系统静态试验汽轮机调节系统静态试验是指通过对汽轮机的调节系统进行一系列的试验,以确定其静态性能以及是否符合设计要求。
下面将从试验内容、试验过程以及试验意义三个方面来详细介绍汽轮机调节系统静态试验。
试验内容:汽轮机调节系统静态试验主要包括以下几个方面的内容:1.系统响应试验:对于控制系统的响应速度和稳定性进行测试,通过对输入信号的变化,观察系统的输出信号变化情况,以确定系统的响应速度是否满足要求。
2.调节器静态特性试验:对调节器的静态特性进行测试,包括调节器的增益、死区等参数的检测,以确定调节器的性能是否符合设计要求。
3.电液伺服调节试验:对电液伺服调节装置进行试验,观察伺服机构的动作情况以及输出是否与输入信号一致,以确定伺服装置的性能是否符合要求。
4.液压缸静态特性试验:对液压缸的运动特性进行测试,包括液压缸的输出力和位移等参数的检测,以确定液压缸的性能是否满足要求。
5.系统稳定性试验:通过对整个调节系统进行稳定性试验,观察系统在不同负荷和工况下的稳定性情况,以确定系统是否能够满足运行要求。
试验过程:汽轮机调节系统静态试验通常按照以下步骤进行:1.准备工作:确保试验设备和仪器的正常运行,对试验对象进行检查和维护,确保试验的顺利进行。
2.测量参数设定:根据试验要求,设定试验参数和测量点,包括控制信号、输入负荷、系统输出等。
3.调节器静态特性试验:通过改变调节器的输入信号,观察输出信号的变化情况,并记录相关数据。
4.电液伺服调节试验:通过改变输入信号,观察伺服机构的动作情况,并记录相应数据。
5.液压缸静态特性试验:通过改变液压缸的输入信号,观察液压缸的输出力和位移情况,并记录相关数据。
6.系统稳定性试验:通过改变负荷和工况,观察系统的运行状态和输出信号的稳定性情况,并记录相关数据。
7.数据分析和评估:根据试验结果,对系统的静态性能进行分析和评估,判断系统是否满足设计要求。
试验意义:汽轮机调节系统静态试验的目的是评估调节系统在静态工况下的性能,判断系统是否满足设计要求。
1号机组RUNBACK静态试验方案
2号机组RUNBACK静态试验方案1、设备概况中国水电崇信发电公司2×660MW系哈尔滨汽轮机机有限责任公司生产的NZK660-24.2/566/566汽轮机,型式:超临界、中间再热、直接空冷凝汽式汽轮机发电机,发电机为哈尔滨电机厂有限责任公司生产的QFSN-660-2发电机,水-氢-氢冷却方式汽轮发电机;DCS、DEH系统是上海福克斯波罗有限公司I/A Series。
2、试验目的检验机组在正常运行时的增压风机、送风机、引风机、一次风机、和给水泵中的一台发生故障跳闸且备用设备无法联锁启动而使机组出力受到限制时,自动控制系统将机组负荷快速由高负荷(大于RUNBACK 触发负荷)按预定的速率向预定的RUNBACK目标负荷顺利过渡的能力,RUNBACK 功能试验是对机组自动控制系统性能和功能的强烈考验。
3、RUNBACK过程机组控制在协调方式,机组负荷大于RUNBACK 触发负荷(300MW),给水泵、送风机、引风机、一次风机、增压风机这五种辅机出现跳闸,但备用设备无法联锁启动而使机组出力低于负荷请求时,RUNBACK 触发后根据相应的RUNBACK 目标负荷切、投燃料。
将增压风机、送风机、引风机、一次风机、和给水泵开关至“试验”位合闸,检查RB逻辑是否正常、动作是否正常。
热控人员将各大辅机中除RB以外有可能引起跳闸的条件退出保护,将机组负荷强制为600MW,强制机组运行方式为协调控制。
3.1单台引风机跳闸RB静态试验步骤1、联系运行人员将增压风机、磨煤机、送风机、引风机、一次风机、和给水泵开关至“试验”位合闸;2、运行人员投入RB按钮;3、运行人员停运A引风机;4、检查F、E、C磨煤机及B给水泵是否动作正常。
若不正常,热控人员检查内部逻辑,重新试验直至动作正常,若动作正常,按A引风机RB步骤做B引风机RB。
3.2单台送风机跳闸RB静态试验步骤1、联系运行人员将增压风机、磨煤机、送风机、引风机、一次风机、和给水泵开关至“试验”位合闸;2、运行人员投入RB按钮;3、运行人员停运A送风机;4、检查F、E、C磨煤机及B给水泵是否动作正常。
汽轮机调节系统静态特性试验一
汽轮机调节系统静态特性试验一、目的3 T8 o8 h1 I2$ E9 J' D为检验机组大修后调速保安系统的性能,为机组创造安全、可靠的启动条件,特制定本试验规定。
6 p/ N" u# W! C二、引用标准:7 Q$ V4 D N/ ~- W0 KDL5011—1992电力建设施工及验收技术规范汽轮机组篇JB37—1990汽轮机调节系统技术条件$$ K:}0 K6 o; u; vJB1273—1986汽轮机控制系统性能试验规程DL/T 711-1999汽轮机调节控制系统试验导则5 H3 ], Z/ A:?T9860型xx汽轮机厂资料三、试验项目, C& ^+ t1 g:{& v+ `*F9 P"z6 U" Q1、汽轮机调节系统静态特性试验(包括静止试验、空负荷试验、带负荷试验)和保安系统试验。
2、汽轮机调节系统动态特性试验。
! h7 M7 C( H3 q5 }/ [8 e& _四、试验测量项目及仪表精度4 ~! c:^5 T' I( H$ x* S! m' R" g9 C$ i' E2 y9 a4 `/表1调节系统静态特性试验的测量变量和仪表精度序号测量变量仪表精度1功率±0.2%2转速±0.1%3蒸汽流量±0.5%4主蒸汽压力±1%, Y" A- z) m:Z# I5主蒸汽温度±5℃6调节级后蒸汽压力±1%7抽汽蒸汽压力±1%8调速汽阀油动机行程±1%1 T8 G2 M1 w:O3 D( U9可调整抽汽油动机行程±1%u+ c9 u6 A9 a/ m& L0 S* E10抽汽速关阀行程±1%7j( B, d. u- g11调节系统主油压±0.5%12调节系统调节油压±0.5%4 z u, r' f. E5 ]+ P, d! s13保护系统安全油压±0.5%7 \' L* |0 F& s- J% J14调节、保护系统油温度±1℃15同步器±1%表9调节系统动态特性试验的测量变量和仪表精度序号测量变量仪表精度1发电机定子电流±2%9 b. q$ y9 I7 U2发电机有功功率±0.5%+ N! ^; d5 i# _8 r8 w3转速±0.1%8 o4 p+ E4 G% C6 \+M% P0 @* u4同步器±1%5主蒸汽压力±1%4 E% P) b( h" {% V" d36主汽调节汽阀油动机行程±1%- A)P) q, a6 Z; q4 E2 b7可调整抽汽油动机行程±1%, u$ O5 s, S9 m) c3 {+ {8抽汽速关阀行程±1%7# i% V/ C& L' X9调节系统调节油压±0.5%10保护系安全油压±0.5%五、试验; e1 x- a1 J) \- s5 w, \- M:L8 d$ K1 Q3 s) d/ _4 ]4 e% e一、调节系统静态特性试验⑴静止试验试验方法:; t4 l6 @* ~& |. A6 H6 o①将同步器(转速给定)分别设定在额定转速、105%额定转速和95%额定转速的位置上,连续变化(不得停留或反向操作)转速模拟信号,控制调节汽阀油动机开启至最大,再反向连续变化转速模拟信号,控制调节汽阀油动机由最大关至最小,记录相关数据。
(2)汽轮机静态、动态试验项目
汽轮机静态、动态试验项目
一、汽机启动前的试验:
1、循环水泵试运及联锁试验、凝汽器循环水过水试验。
2、凝结泵试运及联锁试验。
3、射水泵试运及联锁试验、抽真空试验。
4、给水泵试运及联锁试验。
5、轴加风机试运。
6、高压油泵、交流润滑油泵、直流油泵试运、投盘车试验。
7、电液调系统静态特性测定与试验。
二、保安系统静态试验:
1、汽轮机挂闸、打闸
2、DEH打闸试验。
3、控制台停机试验。
4、ETS控制屏停机试验
5、低真空保护试验。
6、轴位移保护试验。
7、低油压联锁保护试验。
8、1、2、3、4#瓦、推力瓦温度高保护试验。
9、1、2、3、4#瓦、推力瓦回油温度高保护试验。
10、胀差保护试验。
12、1、2、3、4#瓦振动大保护试验。
13、发电机故障保护试验。
三、启动后动态试验:
1、定速手动打闸试验。
2、自动主汽门,调节汽门严密性试验。
3、OPC超速、电超速、机械超速试验。
4、并网带负荷试验。
5、除氧器汽侧投入试验。
6、真空严密性试验。
7、甩负荷试验。
8、汽轮机惰走时间测定。
金晖调试
2012/10/28。
- 1、下载文档前请自行甄别文档内容的完整性,平台不提供额外的编辑、内容补充、找答案等附加服务。
- 2、"仅部分预览"的文档,不可在线预览部分如存在完整性等问题,可反馈申请退款(可完整预览的文档不适用该条件!)。
- 3、如文档侵犯您的权益,请联系客服反馈,我们会尽快为您处理(人工客服工作时间:9:00-18:30)。
汽轮机静态试验方案DEH/ETS静态试验方案1.目的为确保在机组运行期间油动机运作正常且异常工况下能紧急停运,在机组大小修后或停机超过七天以上,需做试验来验证回路、逻辑以及定值准确性。
2.责任分工运行人员:根据工期安排,提前两天通知检修单位退回相关工作票,检查相关系统是否具备送电和运行条件;负责打印相关试验签证单并确认试验正确性。
通知生技部、维护部配合试验。
热控人员:配合运行人员按工期完成试验;模拟相关信号;确认试验正确性。
生技部:确认试验正确性3.试验条件1)D EH/ETS空制系统检修完成并送电;2)D EH继电器柜检修完成并送电;3)汽轮机调节保安系统检修完成;4)T SI系统检修完成并送电;5)汽机EH油系统检修完成并送电(EH油循环合格),且油泵运行,油压正常;6)汽机润滑油系统检修完成并送电,且油泵运行,油压正常;7)汽机盘车系统检修完毕并投运;8)汽轮机主汽门、调门检修完成;9)强制复位MFT(如果锅炉侧检修完毕的后,按FSSS试验方案执行)。
4.试验项目及方法4.1阀门开度线性试验试验条件以及范围:主汽阀前无蒸汽(在阀门整定期间,转速大于100r/min时, 应将机组打闸);该试验只针对:CV1、CV2 CV3 CV4 ICV1、ICV2、MSV2试验方法:1、启动EH油泵、润滑油泵,待油压正常后。
汽机挂闸,所有阀全关,由热工人员按零位校验、满位校验、全行程校验的步骤完成阀门开度线性试验及整定,汽机专业人员、运行人员现场确认“全关” 和“全开”位置(油动机检修后、卡件更换后必须执行此步骤,该步骤完成后再执行下一步,否则跳步)。
2 、启动EH油泵、润滑油泵,待油压正常后。
汽机挂闸,所有阀全关,热控人员进入逻辑中,把相应油动机切换至手动模式操作,分别给0% 25% 50% 75% 100%提令,由运行人员和机务人员就地共同确认就地阀门开度是否卡涩、行程是否对应。
4.2油动机快关试验试验目的:测定油动机自身动作时间,手动打闸汽机,要求所有油动机从全开到全关的快关时间常数<0.15s。
测定总的关闭时间,要求从打闸到油动机全关时间<0.4s。
试验方法:汽轮机挂闸,开启各阀门,然后手动打闸。
试验记录:通过SOE记录查看汽轮机各阀门从全开到全关(从打闸指令到全关)所经过的时间。
4.3手动机械遮断(就地):汽轮机挂闸后,手拉机头停机机构。
4.4手动停机按钮(控制台):汽轮机挂闸,手打集控室停机按钮。
4.5 DEH转速传感器故障:汽轮机挂闸,然后由热工人员拔卡件,模拟DEH专感器故障。
4.6汽轮机超速》3300rpm (电气超速)4.6.1汽轮机挂闸,热工人员拆除DEH至ETS转速跳闸回路硬接线,并在DEH 逻辑中模拟汽轮机转速(三取二,每次只能同时模拟两个),汽轮机跳闸。
恢复转速性号和硬接线。
4.6.2汽轮机挂闸,热工人员退出DEH至ETS转速跳闸软回路,并在DEH逻辑中模拟汽轮机转速(三取二,每次只能同时模拟两个),汽轮机跳闸。
恢复转速性号和投入跳闸软回路。
4.6.3汽轮机挂闸,热控人员在TSI机柜模拟汽轮机转速》3300rpm(三取二,每次只能模拟两个),汽轮机跳闸。
4.7轴向位移非常高(w— 1.65mm >1.20mm):汽轮机挂闸,然后由热工在TSI机柜模拟轴向位移非常高,汽轮机跳闸。
4.8高缸胀差非常高(w— 6.60mm > 11.60mn):汽轮机挂闸,然后由热工在TSI机柜模拟高缸胀差非常高,汽轮机跳闸。
4.9低缸胀差非常高(w— 8.00mm > 30.00mm):汽轮机挂闸,然后由热工在TSI机柜模拟低缸胀差非常高。
4.10汽机/发电机轴振非常高》250um试验方法:汽轮机挂闸,然后由热控人员在TSI机柜模拟一点高》125um同时模拟另一点》250um,延时2秒汽轮机跳闸。
4.11 支持轴承金属温度非常高》121C(1#至6#轴承三取二,7#、8#轴承单点温度高跳):汽轮机挂闸,然后由热工人员就地用电阻箱或信号发生器模拟支持轴承温度高信号,汽轮机跳闸。
备注:热控人员在就地接入信号源后需投入该点保护后再模拟升温,且升速率必须w 8 C /S。
4.12 推力轴承金属温度非常高》110C :汽轮机挂闸,然后由热工人员就地用电阻箱或信号发生器模拟推力轴承温度非常高信号(正向四取二,反向四取二,在模拟过程中升速率w 8C /S ) o 4.13凝汽器真空非常低》-71KPa:4.13.1汽轮机挂闸,热控人员强制10MAG10CP302/303/30为“0” ;热控人员用压力发生器就地模拟10MAG20CP302/303/30卅关任两个开关w -71KPa,且同时模拟10MAG20CP301-83KPa,然后通过压力发生器泄压,模拟10MAG20CP301-83KPa,10MAG20CP302/303/30开关任两个开关》-71KPa,汽轮机跳闸,如此反复,直至10MAG20CP302/303/30全部试验完成,解除10MAG10CP302/303/304 强制。
4.13.2汽轮机挂闸,热控人员强制10MAG20CP302/303/30为“0” ;热控人员用压力发生器就地模拟10MAG10CP302/303/30卅关任两个开关w -71KPa,且同时模拟10MAG10CP301-83KPa,然后通过压力发生器泄压,模拟10MAG20CP301-83KPa,模拟10MAG10CP302/303/30卅关任两个开关》-71KPa,汽轮机跳闸,如此反复,直至10MAG10CP302/303/30全部试验完成,解除10MAG20CP302/303/304虽制。
以上试验完成后,就地确认压力开关接头恢得正常后,进行下一步试验。
4.14润滑油压力非常低w 0.07MPa汽轮机挂闸,解除交流油泵联锁,直流油泵停电,全停润滑油泵,并记录润滑油压降动作值时,汽轮机是否跳闸,试验正常后启动油泵。
4.15汽机安全油压力低w 3.9MPa汽轮机挂闸,退出EH油压低保护以及EH油泵联锁,停运EH油泵。
并记录安全油压降至动作值时,汽轮机是否跳闸,试验正常后启动油泵,恢得EH油压低保护。
4.16抗燃油压力非常低w 7.8MPa汽轮机挂闸,解除EH油泵的联锁,全停EI 油泵,并记录EH油压降至动作值时,汽轮机是否跳闸,试验正常后启动油泵,4.17锅炉主燃料跳闸:运行人员试验位置启动送、引风机,启动空预器,热工人员满足相关吹扫条件,旁路油泄漏试验进行锅炉吹扫复位(具体操作按FSS试验方法执行),汽轮机挂闸,然后手动MFT(如未进行吹扫复位,热控直接解除MFT言号),汽轮机跳闸。
4.18发电机故障:汽轮机挂闸,然后由电气模拟发信号,汽轮机跳闸。
4.19主汽阀入口蒸汽温度过低:4.19.1汽轮机挂闸,热控人员模拟负荷>40%汽轮机跳闸。
4.19.2热控人员强制10LBA10CT00坏点,汽轮机挂闸,热控人员就地用信号发生器模拟10LBA10CT003^ 480E,模拟负荷60%然后热控人员模拟10LBA10CT002为478C,汽轮机跳闸;解除10LBA10CT00坏点4.19.3热控人员强制10LBA10CT00坏点,汽轮机挂闸,热控人员就地用信号发生器模拟10LBA10CT002为480E,模拟负荷60%然后热控人员模拟10LBA10CT003^ 478E,汽轮机跳闸;解除10LBA10CT00坏点。
4.19.4汽轮机挂闸,热控人员就地用信号发生器模拟10LBA10CT002/003为501 T热控人员模拟负荷100%汽轮机不跳闸。
4.20高排金属温度非常高》427C (四取二):汽轮机挂闸,然后由然后由热工人员就地用信号发生器模拟温度高信号(在模拟过程中升速率w 8 C /S)4.21低缸排汽温度非常高》107C(汽机侧,电机侧分别三取二):10MAC20CT304>804.21.110MAC20CT301/302/303任两点>107C,汽轮机跳闸,热控人员恢复信号4.21.2汽轮机挂闸,由运行人员发出汽轮机运行信号,开启高中压主汽阀。
热控人员进入逻辑中,开启高中压调节阀,热控人员就地模拟10MAC10CT304>80, 同时模拟10MAC10CT301/302/303任两点>107C,汽轮机跳闸,所有油动机快速全关,热控人员恢复信号。
A汽动给水泵组试验方案1.目的为确保在机组运行期间油动机运作正常且异常工况下能紧急停运,在机组大小修后或停机超过15天以上,需做试验来验证回路、逻辑以及定值准确性。
2.责任分工运行人员:根据工期安排,提前三天通知检修单位退回相关工作票,检查相关系统是否具备送电和运行条件;负责打印相关试验签证单并确认试验正确性。
通知生技部、维护部配合试验热控人员:配合运行人员按工期完成试验;模拟相关信号;确认试验正确性。
生技部:确认试验正确性3.试验条件1)M EH/MET控制系统检修完成;2)M EH继电器柜检修完成并送电;3)汽轮机调节保安系统检修完成;4)M TSI系统检修完成并送电;5)汽机EH油系统检修完成并送电(EH油循环合格),且油泵运行,油压正常;6)汽机给水泵组润滑油系统检修完成并送电,且油泵运行,油压正常;7)前置泵检修完成并具备运行条件,并在试验位置启动前置泵;8)强制复位MFT(如果锅炉侧检修完毕的后,按FSSS试验方案执行)。
9)热控人员强制真空低跳闸信号。
4.试验项目及方法4.1汽泵进口流量低:挂闸汽动给水泵汽轮机,热控人员强制再循环流量阀超驰关为零,由运行人员操作再循环流量阀,当阀位低于50%寸,延时15秒,汽动给水泵组跳闸。
4.2汽动给水泵汽轮机推力瓦温度高高(八取一,》110C):挂闸汽动给水泵汽轮机,热控人员就地用信号发生器模拟XAA10CT008至XAA10CT01仲任一点> 110C,汽动给水泵组跳闸。
4.3汽动给水泵汽机轴承温度高高(四取一,》110C):挂闸汽动给水泵汽轮机,热控人员就地用信号发生器模拟XAA10CT01至XAA10CT01任一点》110C, 汽动给水泵汽轮机跳闸。
4.4汽动给水泵泵本体温度保护(四取一):4.4.1挂闸汽动给水泵汽轮机,热控人员就地用信号发生器模拟LAC10CT005 LAC10CT00中任一点温度》90C。
汽动给水泵汽轮机跳闸。
4.4.2挂闸汽动给水泵汽轮机,热控人员就地用信号发生器模拟LAC10CT007 LAC10CT00中任一点温度》95T。
汽动给水泵汽轮机跳闸。
4.5前置泵入口门未开且关:挂闸汽动给水泵汽轮机,热控人员强制前置泵入口电动门调试位,由运行人员远方关闭前置泵入口电动门,前置泵跳闸,汽动给水泵汽轮机跳闸,热控人员恢复前置泵入口电动门调试位。