轧机伺服液压系统
偏八辊轧机液压伺服系统调试与改进

统压力和杆腔的 背压调整适 当,作液压 自身负载控
制 。压 下 液压 缸 上 下 运 动数 次 ,确 认 是 否满 足 位 置
的主要原因。找 出原 因后笔者首先提 出将底座与卷
取机的滚动摩擦副改为滑动摩擦导轨 ,在底座侧受
滤要求特 别严格 。在调试前必须对各路管道及系统
回路 进行 清洁 度 循 环 清 洗处 理 ,油 液 清 洁 度必 须 达
f l j NA S 1 6 3 8 5 ~6 级 ,相 当于q S O 4 4 0 6 标准2 0 / 1 8 级要
求。
状态 ,利 用动态调试 仪器和微机在线调试 ,测试 出 系统的特性 ,进一步校正参数 ,确定满足设计要求
盘车 ,转动灵活、无卡 阻现象后点动电动机确认 方
向 无 误 再 进 入 循 环 泵 及 主 泵 的 调 试 。 ④ 启 动 液 压 泵 ,将 液 压 系统 压 力 调 整 N o . 5 MP a ,拧 松 相 关 排
3 . 现场改进措 施
生 产过 程 中出现 开卷 机 纠 偏 系 统液 压 缸 外 泄 漏 和 工作 辊 夹 紧 不稳 定 问题 ,具体 改进 措 施如 下 : ( I )EP C  ̄ q 偏 系 统 的 伺 服 液 压 缸 使 用一 段 时
处理板、电源板 、编程器板等组成 ,输入板共有 1 4 块 ,用于接收继 电器和光 电管来的信号。输 出板有 2块 ,1 1 2 个直流输 出点,7 2 个交流输出点 ,整机
约4 0 8 个 点 ,控 制 四个 动 力头 上 、 下左 右移 动 及 工 作 台前 后 移 动 ,该 系统 应 用极 不 广 泛 。为 此 ,我 厂 与 北 京机 床 研 究 所 下 属 机 电公 司 合作 对 K2 4 数 控 装
四辊轧机液压压下装置液压系统设计
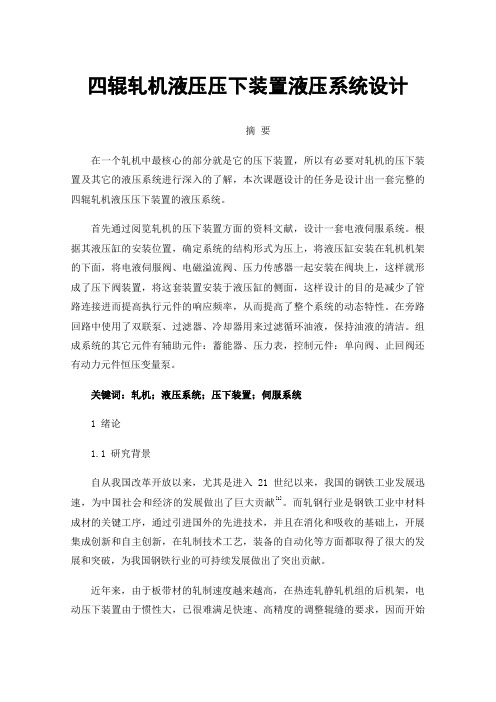
四辊轧机液压压下装置液压系统设计摘要在一个轧机中最核心的部分就是它的压下装置,所以有必要对轧机的压下装置及其它的液压系统进行深入的了解,本次课题设计的任务是设计出一套完整的四辊轧机液压压下装置的液压系统。
首先通过阅览轧机的压下装置方面的资料文献,设计一套电液伺服系统。
根据其液压缸的安装位置,确定系统的结构形式为压上,将液压缸安装在轧机机架的下面,将电液伺服阀、电磁溢流阀、压力传感器一起安装在阀块上,这样就形成了压下阀装置,将这套装置安装于液压缸的侧面,这样设计的目的是减少了管路连接进而提高执行元件的响应频率,从而提高了整个系统的动态特性。
在旁路回路中使用了双联泵、过滤器、冷却器用来过滤循环油液,保持油液的清洁。
组成系统的其它元件有辅助元件:蓄能器、压力表,控制元件:单向阀、止回阀还有动力元件恒压变量泵。
关键词:轧机;液压系统;压下装置;伺服系统1 绪论1.1 研究背景自从我国改革开放以来,尤其是进入21世纪以来,我国的钢铁工业发展迅速,为中国社会和经济的发展做出了巨大贡献[1]。
而轧钢行业是钢铁工业中材料成材的关键工序,通过引进国外的先进技术,并且在消化和吸收的基础上,开展集成创新和自主创新,在轧制技术工艺,装备的自动化等方面都取得了很大的发展和突破,为我国钢铁行业的可持续发展做出了突出贡献。
近年来,由于板带材的轧制速度越来越高,在热连轧静轧机组的后机架,电动压下装置由于惯性大,已很难满足快速、高精度的调整辊缝的要求,因而开始采用电动压下与液压压下相结合的压下方式[2]。
在现代化的冷连轧机组中,几乎已全部采用液压压下装置。
1.3 本课题主要研究内容本课题主要是设计一套四辊轧机压下装置的液压系统,以前冷轧机的压下装置是靠大功率电动机带动牌坊顶部的蜗轮蜗杆和压下螺丝来实现的,自从采用液压技术后,轧制速度提高了10倍以上,精度也大大提高了。
采用液压压下系统的轧机一旦发现误差,能以极短的时间调整辊缝。
所以有必要对轧机液压压下装置进行研究,具体内容如下:(1)首先查阅轧机压下装置液压系统方面的相关资料,了解压下装置的工作原理并对组成压下装置液压系统中的电液伺服阀有一定了解,伺服阀是液压系统中最关键的元件,是液压系统同电气系统的连接元件。
浅谈伺服阀在轧机液压系统的使用与维护
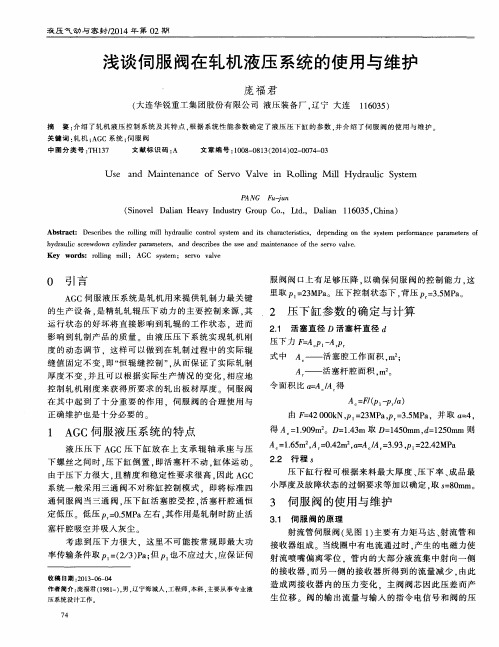
1 AG C伺 服 液 压 系 统 的特 点
液压压下 A G C压 下 缸 放 在 上 支 承 辊 轴 承 座 与 压
下螺 丝 之 间时 , 压 下 缸倒 置 , 即活 塞杆 不 动 , 缸 体 运动 。 由于 压下 力很 大 . 且 精 度 和稳 定性 要求 很 高 . 因此 AG C 系统 一 般采 用 三通 阀不 对 称缸 控 制模 式 .即将标 准 四 通 伺 服 阀 当三 通 阀 . 压下 缸 活 塞 腔受 控 . 活 塞 杆 腔通 恒
0 引 言
A G C伺服 液 压 系统 是轧 机 用来 提供 轧 制力 最 关键 的生 产设 备 . 是 精 轧 轧辊 压 下 动力 的主要 控 制来 源 . 其 运 行 状 态 的好 坏将 直 接 影 响到 轧 辊 的工 作 状 态 .进 而 影 响 到 轧制 产 品 的质 量 由液 压 压下 系 统 实现 轧 机 刚 度 的动 态调 节 .这 样 可 以做 到 在 轧制 过 程 中的实 际 辊 缝 值 固定 不 变 . 即“ 恒 辊 缝控 制 ” . 从 而保 证 了实 际轧 制 厚 度 不变 . 并 且 可 以 根据 实 际 生产 情 况 的变 化 . 相 应 地 控 制 轧机 刚度来 获 得 所 要求 的轧 出板 材 厚 度 伺 服 阀 在 其 中起 到 了十分 重 要 的作 用 .伺 服 阀 的合 理使 用 与 正 确维 护 也是 十分 必要 的。
式中
Hale Waihona Puke A — — 活塞 腔 工作 面积 , m z ;
A —— 活塞杆 腔 面积 。 m z 。
冷带轧机液压压下伺服系统模型算法控制应用研究
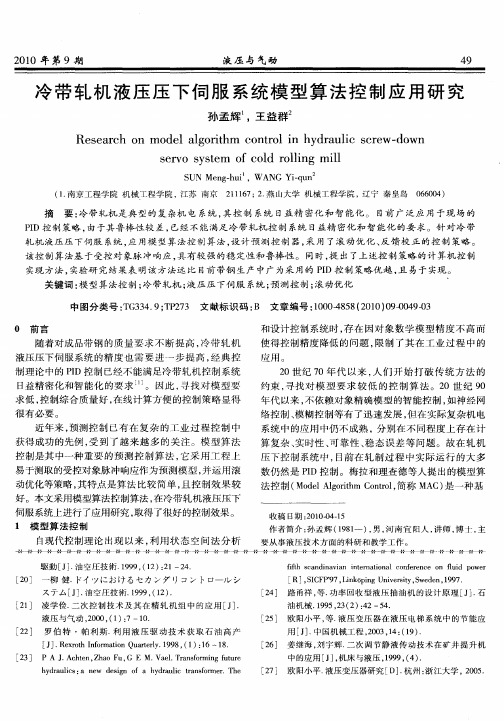
2 0世纪 7 0年代 以 来 , 们 开 始 打 破 传 统 方 法 的 人 约束 , 找 对 模 型要 求 较 低 的控 制 算 法 。2 寻 O世 纪 9 O 年代 以来 , 依赖 对 象精确 模 型 的智能 控制 , 不 如神 经 网 络控 制 、 模糊 控制 等有 了迅 速 发展 , 但在 实 际复杂 机 电 系统 中的应 用 中仍不 成熟 ,分别 在 不 同程度 上 存 在计
收 稿 日期 :000 —5 2 1 - 1 4
作者简介 : 孟辉 (9 1 )男 , 南宦 阳人 , 师 , 十 , 孙 18 ~ , 河 讲 博 主
自现 代控 制理 论 出现 以来 , 用 状 态 空 间 法分 析 利
驱 勤 [ ] 油 空 压 技 衍 .9 9 ( 2 :1 4 J. 19 , 1 ) 2 —2 .
21 0 0年 第 9期
液 压 与 气动
4 9
冷 带 轧 机 液 压 压 下 伺 服 系 统 模 型 算 法 控 制 应 用 研 究
孙 孟 辉 王 益 群 ,
Re e r h o d l ag rt m o to n h d a l c e d wn s a c n mo e l o i h c n r li y r u i s r w— o c
s r o s se o o d r li g mi e v y t m f c l o l l n l
S UN n — u .W ANG — u Me g h i Yiq n
( . 京 工 程 学 院 机 械 工 程 学 院 ,江 苏 南 京 1南
2 16 ; . 山 大学 机 械 工程 学 院 , 宁 秦 皇 岛 1 17 2 燕 辽
油 机 械 .9 5 2 ( )4 5 . 19 ,3 2 :2— 4
轧机AGC液压系统

轧机AGC液压系统、弯辊抽动伺服液压系统,活套液压控制系统,助卷辊液压系统,卷筒液压系统、侧导板液压系统、轧机AWC液压系统等等。
主要维护原则钢铁冶金液压系统泵站集中,元件种类多,要求的精度也有不同,设备属于大型复杂的生产线,可靠性要求高,加之连续作业往往没有足够检修时间对液压系统进行维护保养。
这就决定生产线的液压系统故障多而复杂,排除难度大任务重。
液压事故诊断的基本要求:正确、精确、简洁、快速、超前。
诊断技术发展,不解体化、高精度化、智能化、网络化。
液压系统出现故障时不易找出原因、排查困难,现将在工作中积累的一些经验和方法归纳,以供参考。
一是排除法,一样一样的排除,二是经验法,对生产现场很了解,对出问题的地方也有经常性的,很快就能找到出问题原因。
三是综合法,排除法和经验都一起来诊断事故,效果好更好些。
对于一般的原则:先排除外围在处理内部,伺服系统先电器后机械最后是液压。
一、望:看到什么。
1、看系统的配置是否正常,包括:泵、阀、执行元件、工作油液、滤油器、散热器等;2、看速度(流量):看执行机构运动速度是否有异常现象;3、看压力:看液压系统中各测压点的压力值大小及波动;4、看油液:观察油液容量是否合适,是否清洁,有无变质,油中是否有泡等;5、看泄漏:看液压管道各接头处、阀板结合处、液压缸端盖处、液压泵轴伸出处是否有渗漏、滴漏和油垢现象。
二、闻:听到什么。
1、听噪声:判断听到的声音是否属于噪声,噪声的源头在哪,是液压泵、马达、阀等液压件还是系统的管路或与元件连接的工作机构。
2、听冲击声:听系统的冲击声是否属于正常。
冲击声的时间:液压阀换向时冲击,还是莫名地发声。
冲击声的规律性:有节奏还是无规律。
3、听泄漏声:听油路内是否有细微不断的声音。
4、听敲打声:听液压件运转时是否有敲打声。
5、听相关人员反映。
三、摸:感觉到什么。
1、摸温升:用手摸运动部件表面,检查是否发热。
2、摸振动:感觉是否有振动现象。
3、摸爬行:感觉运动件有无“爬行”现象。
热轧生产线上伺服系统的应用与维护

热轧生产线上伺服系统的应用与维护热轧厂生产的过程中,轧机系统作为其核心设备,有着重要的作用。
伺服系统是轧机的控制大脑,伺服系统分散到轧机的各个部位,有利于热轧生产线的稳定和安全。
通过对热轧生产线的伺服系统进行研究,分析其生产中的运行情况,找出存在的问题以及原因,采取有效的实施方案,从多个层面保证伺服控制系统的稳定和精确。
文章对热轧生产上的伺服系统的应用和维护进行探究,以供参考。
标签:热轧生产线;伺服系统;应用;维护液压伺服系统的控制精度高,反应速度快,并且系统具有非常大的刚性,在船舶、航空以及冶金等行业普遍的应用。
同时伺服阀对油液的污染具有非常强的敏感度,精度要求非常高,在使用和维护的过程中存在一定的难度。
在热轧生产的过程中,伺服系统会出现不正常工作的情况,需要对其进行分析,了解不正常工作的原因,提出相应的解决方案,保证热轧生产安全、稳定的开展。
1 热轧生产线上伺服系统存在的问题和原因(1)伺服系统不动作。
此种问题主要的表现是现场无动作,可以通过以下几点检查进行故障的处理。
首先,电气专业人员对伺服阀的给定电压进行检查,是否能够到达伺服阀,中间线路的绝缘性是否存在降低的情况,伺服阀的插头位置是否存在虚接、断线以及脱焊的情况。
在检查时,可以通过程序中的伺服阀进行测量验证或者借助伺服阀测试台开展检查工作。
其次,机械专业检查人员检查在检修和维护的过程中,进出油口是否存在接反情况。
如果上述检查正常,可以进行先导级或者过滤器的检查,是否存在堵塞的情况。
最后,对阀芯进行检查,是否存在卡死的情况。
(2)伺服阀存在固定输出但是出现失控情况。
此种问题通常的表现是电气输出是正常的,但是伺服阀的动作和电气不成对应关系,或者出现来回的波动。
伺服阀出现此种故障的原因有以下几点:前置级堵死或者喷嘴被堵塞等,阀芯被卡住,阀体、阀套出现变形的情况,导致伺服系统出现波动。
过滤器如果出现堵塞的情况,也会造成伺服阀输出出现失控的情况。
轧机的液压压下装置

轧机的液压压下装置液压压下装置是轧机中非常重要的组成部分,它主要用于在轧制过程中对轧辊进行压下,以使金属材料在轧制过程中得到良好的形状和尺寸。
液压压下装置一般由液压系统、主缸、液压缸、液压管路等部分组成。
下面将从这几个方面对液压压下装置作详细介绍。
一、液压系统液压系统是液压压下装置中最为核心的部分,它主要由油箱、油泵、阀门和油管等组成。
油箱主要用于储存液压油,并且在油箱中放置油滤器和油温计等,以确保液压系统中的油液清洁和温度适宜。
油泵的作用是将液压油从油箱中抽出并送入液压缸内,从而使液压缸对轧辊进行压下。
油泵一般有液压柱塞泵、液压齿轮泵和液压叶片泵等几种类型。
阀门主要用于控制液压系统中的液压油流动方向、流量和压力等参数,以实现对液压压下装置的控制。
油管主要用于将液压系统中的液压油输送到液压缸中,并且使液压油在液压缸内进行压力传递。
二、主缸主缸是液压压下装置中的一个重要部件,它主要由液压缸筒、活塞、活塞杆、活塞密封等组成。
液压缸筒一般由优质的合金钢材料制造而成,并且经过热处理和精密加工等工艺,以确保其具有足够的强度和刚性。
活塞是主缸内部的运动部件,它的作用是在液压压下装置工作时对轧辊进行压下,从而使金属材料在轧制过程中得到压制和塑性变形。
活塞杆是连接活塞和液压缸筒的部件,它的结构要求具有足够的强度和刚性,以承受液压压下装置工作时产生的巨大作用力。
活塞密封是主缸内部的关键部件,它的作用是防止液压缸内的液压油泄漏,并且保证液压系统的密封性和工作可靠性。
四、液压管路液压管路是液压压下装置中非常重要的部分,它主要由液压管、接头、接头密封等组成。
液压管一般由优质的碳钢管或不锈钢管制造而成,并经过加工和抛光等工艺,以确保其具有足够的强度和耐腐蚀性。
接头主要用于连接液压管和液压缸、液压泵、阀门等部件,使液压油能够顺畅流动。
接头密封一般采用油封圈、O型圈等密封件,它的作用是防止液压管路中的液压油泄漏,并且保持液压系统的密封性和工作可靠性。
中板轧机HGC伺服液压缸的结构设计

中板轧机 HGC伺服液压缸的结构设计现代的热轧生产线中配置了许多不同的液压系统,液压油缸作为液压系统的执行机构也被大量使用。
根据热轧生产线设备配置不同所用液压油缸的数量、种类和型式而有所差异,按照油缸所使用的部位不同来分就有几十种之多。
其中就有许多液压伺服系统中使用的液压缸,一般称为伺服液压缸。
由于设备结构参数以及控制要求的不同,对伺服液压缸的要求也不一样,不同系统伺服液压缸的组成、结构、规格、材料都不尽相同,所以基本上都是非标设计。
伺服液压系统是液压技术的高精尖领域,其伺服液压缸与普通液压缸的设计及参数要求有许多不同之处,它是为控制设计的,更看重动态性能。
在伺服系统中它会直接影响了系统的动态响应,控制精度,稳定性等等。
具体来讲,伺服油缸与传统油缸以下不同:在功用方面:传动液压缸作为动执行元件,用于驱动工作负载,实现工作循环运动,满足常规运动速度及平稳性要求;伺服液压缸作为控制执行元件用于高频下驱动负工作负载,实现高精度、高响应伺服控制。
在强度及结构方面:1.强度传动液压缸满足工作压力和冲击压力下工作要求;伺服液压缸满足工作压力和高频冲击压力下工作要求,因此其厚度尺寸往往是超过正常的强度设计计算值,偏于安全,即比普通液压缸的壁厚要失。
2.刚度传动液压缸一般无特别要求;伺服液压缸要求高刚度,即活塞杆的细长比要很小,否则执行元件的唱有频率念下降得承出下降很多,,缸的底座不仅能够满足支承缸的受力要求,3.稳定性传动液压缸满足压杆稳妥定性要求;伺服液压缸满足压杆高稳定性要求。
4.导向传动液压缸要求有良好的导问性能,满足重载或偏载要求;伺服液压缸要求有良好的导向性能,满足高频下的重载、偏载要求。
5.连接间隙传动液压缸连接部位配合良好无较大间隙;伺服液压缸连接部位配合优良,不允许存在游隙。
6.缓冲传动液压缸高速运动时应能满足在行程终点时缓冲;伺服液压缸不碰缸底不需要考虑缓冲装置。
7.安装传动液压缸只需考虑缸体与机座、活塞杆与工作机构的连接;伺服液压缸除了考虑缸体与机座、活塞杆与工作机构的连接,还要考虑传感器及伺服控制阀组的安装。