织布疵点原因及预防措施
印染布疵点产生的原因及解决方法

印染布疵点产生的原因及解决方法1﹑裙皱皱条之间相互平行,头尾平齐。
皱条中间大,两头尖。
皱条与平面交界处留有换梭纱尾,形状似裙子折皱。
裙皱多发生在含化纤的织物上,原坯布上不易发现。
只有经印染加工处理才显现出来。
产生的主要原因:①化纤本身性能的差异或纺织厂高温定捻温度不一致,造成纬纱缩率不同;②所用纬纱号数或捻度存在差异。
解决方法:重新投好的原坯布生产。
2﹑缝头皱皱条与缝头相连,一条或多条,长短不一.有的在缝头一端,有的在缝头两端。
主要原因是幅地进布工缝头不良。
未做到缝头平直、坚牢、边齐、针脚均匀一致。
解决方法:连同缝头开剪,作次零布处理。
3﹑印染加工皱一般在布面呈现的条数不多,通常为直形或斜形条状,长短宽窄不一。
印染前或印染加工过程中产生的皱条与正常布面色泽相差较大;印染固色后平洗过程中产生的皱条色差较小。
主要原因:①印染前半制品原有皱条;②印染过程中机械张力,轧辊压力调节不好;导辊、烘筒的平行度掌握不好;③设备清洁做得不好。
解决方法:补产。
4﹑丝光皱印染后呈现中间深两边浅、直线或斜形的细死皱。
产生的主要原因:①丝光机去碱蒸箱、平洗槽导布辊不平或沾有纱头、碱垢;②丝光机张力调节不当;③去碱蒸箱直接蒸汽管开启较大冲击织物造成折皱。
解决方法:补产。
5﹑风印印染织物搁置被显露的部分与布面正常色泽呈现差异。
一般在布的折叠处或布幅两边出现不规则的浅色档或色条。
产生的主要原因:某些用于活性染料、分散染料的印染半制品、在制品布面带碱,或受空气中还原气体的作用,影响织物与染料的固着,裸露部分产生浅色档。
活性染料易产生风印。
解决方法:补产。
6﹑边中色差、左中右色差印染织物边中或左中右色泽深浅不下。
产生的主要原因:①染液的轧辊或印花压力两端不一致;②预烘或热溶焙烘时,布幅中间和两边的温度和风量不一致,造成布面左右或左中右干湿不一致;③拼色染料在相同的加工条件下移染性能不一致,造成色泽深浅或色光的变化。
解决方法:补产或修色。
坯布布面常见疵点分析

坯布布面常见疵点分析1.密路:局部纬纱密度比布面正常情况大,表现为纬向出现一直横档,颜色偏向纬纱,透光性差。
2.稀路:局部纬纱密度比布面正常情况小,表现观看,出现纬向一条路,颜色偏向经纱,易透光。
3.双纬:一般正常品种,每一织口引入一根纬纱,双纬则引入两根纬纱在一起。
4.断纬:织入纬纱断一段或短一段,并未停车。
5.断经:经纱断裂,平纹有双经的外观,但在开下灯光时有透光现象。
6.纬缩:纬纱松驰,织入布面在布面凸出或起圈。
7.错综:没有按工艺规定穿综顺序进行穿综,布面显示组织有变化。
8.错筘:过筘时,没有按工艺规定,穿错筘,布面经向出现一稀密现象。
9.松吊经:在织物中,经纱张力一会儿紧,一会儿松,产生经向条痕,松经时经纱凸出布面,吊经时经纱凹入布面。
10.边撑疵:在织物布边,经纱或纬纱被边撑刺钩断,拉断或针孔过大。
11.跳纱、跳花:织物中,经纬纱没有按正常组织规律交织,单根成多根经(纬)纱浮在多根纬(经)纱上。
12.错支、错纱:织物中织入工艺要求外的纱,如颜色不对,纱支不对。
13.双经:织布时综眼里多穿了一根经纱,虽未组织错乱,但多穿部分已成为双经。
14.筘路:由于筘齿损伤、变形、发软松动等原因,使布面经向呈一直条疏密现象。
15.稀纬:纬纱比正常纱细一些,造成纬向一条痕,有有结和无结之分。
16.结头:打结纱尾过长(3MM以上)或因纱线太粗造成接头太大突出于布面。
17.油经、污经:经纱被油污沾上。
18.条花:布面出现颜色深浅程度相对比较明显的经向条形疵点。
19.纬向条纹:布面纬纱颜色不均匀,深浅不一,有时表现出为横向抛物线状条纹。
20.色差:由于纬纱颜色有深浅,在布面形成纬向横档。
21.轻浆棉球:由于经纱浆纱不当,经纱毛羽多,织布后布面出现许多棉球,轻浆棉球一般能沿经纱上下滑动。
22.云织:布面纬纱一段稀,一段密,稀密交替出现。
23.油污渍:布面上沾上三条纱及以上的一志块油污痕渍。
24.经缩圈:织物表面经纱呈起圈现象,多发生在泡泡布和提花布上。
(完整版)织布疵点大全
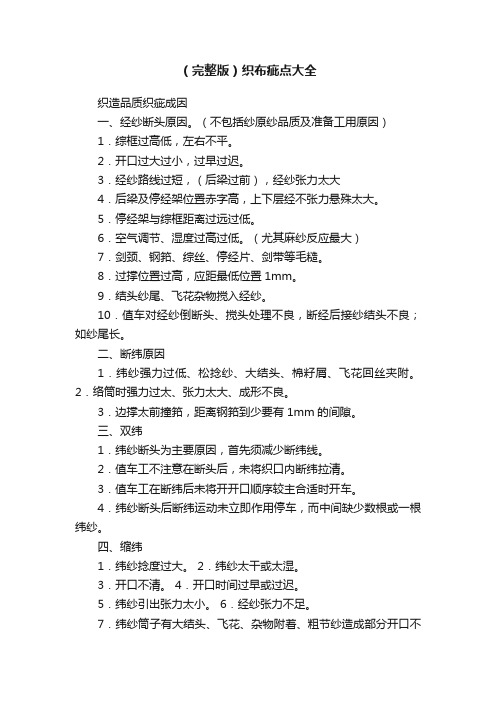
(完整版)织布疵点大全织造品质织疵成因一、经纱断头原因。
(不包括纱原纱品质及准备工用原因)1.综框过高低,左右不平。
2.开口过大过小,过早过迟。
3.经纱路线过短,(后梁过前),经纱张力太大4.后梁及停经架位置赤字高,上下层经不张力悬殊太大。
5.停经架与综框距离过远过低。
6.空气调节、湿度过高过低。
(尤其麻纱反应最大)7.剑颈、钢筘、综丝、停经片、剑带等毛糙。
8.过撑位置过高,应距最低位置1mm。
9.结头纱尾、飞花杂物搅入经纱。
10.值车对经纱倒断头、搅头处理不良,断经后接纱结头不良;如纱尾长。
二、断纬原因1.纬纱强力过低、松捻纱、大结头、棉籽屑、飞花回丝夹附。
2.络筒时强力过太、张力太大、成形不良。
3.边撑太前撞筘,距离钢筘到少要有1mm的间隙。
三、双纬1.纬纱断头为主要原因,首先须减少断纬线。
2.值车工不注意在断头后,未将织口内断纬拉清。
3.值车工在断纬后未将开开口顺序较主合适时开车。
4.纬纱断头后断纬运动未立即作用停车,而中间缺少数根或一根纬纱。
四、缩纬1.纬纱捻度过大。
2.纬纱太干或太湿。
3.开口不清。
4.开口时间过早或过迟。
5.纬纱引出张力太小。
6.经纱张力不足。
7.纬纱筒子有大结头、飞花、杂物附着、粗节纱造成部分开口不清。
五、小稀路1.筘座及卷取刺毛辊松动或腐蚀。
2.经纱张力过大或过小。
3.经纱上下两层纱张力相差悬殊。
4.停车过久后开车时梭口未较正。
5.停车后开车起动太缓慢影响打纬力。
(主电机皮带松驰无力)六、纬纱尾织入1.右测经纱距离顺风管太远,废边纱未能很好夹持纱尾。
2.纬纱张力太小,剑头开启时间太晚。
七、稀路1.起因均为断纬、首先须减少断纬。
2. 断纬卷取退卷绕装置不良。
八、跳花1、综框松动、不平或过低。
2、经纱张力上下两层相差悬殊。
3、浆纱过毛、开口粘滞、上浆不良引起绒球或毛羽。
4、经纱有飞毛、纱尾及大结头。
5、综丝头尾损断或综丝搅乱。
6、部分经纱松弛或张力过低。
7、开口时间不对。
云织织疵的成因和检修措施
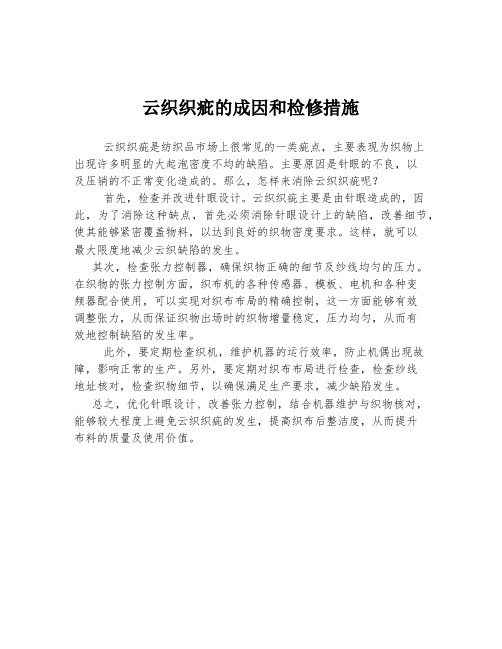
云织织疵的成因和检修措施
云织织疵是纺织品市场上很常见的一类疵点,主要表现为织物上
出现许多明显的大起泡密度不均的缺陷。
主要原因是针眼的不良,以
及压销的不正常变化造成的。
那么,怎样来消除云织织疵呢?
首先,检查并改进针眼设计。
云织织疵主要是由针眼造成的,因此,为了消除这种缺点,首先必须消除针眼设计上的缺陷,改善细节,使其能够紧密覆盖物料,以达到良好的织物密度要求。
这样,就可以
最大限度地减少云织缺陷的发生。
其次,检查张力控制器,确保织物正确的细节及纱线均匀的压力。
在织物的张力控制方面,织布机的各种传感器、模板、电机和各种变
频器配合使用,可以实现对织布布局的精确控制,这一方面能够有效
调整张力,从而保证织物出场时的织物增量稳定,压力均匀,从而有
效地控制缺陷的发生率。
此外,要定期检查织机,维护机器的运行效率,防止机偶出现故障,影响正常的生产。
另外,要定期对织布布局进行检查,检查纱线
地址核对,检查织物细节,以确保满足生产要求,减少缺陷发生。
总之,优化针眼设计、改善张力控制,结合机器维护与织物核对,能够较大程度上避免云织织疵的发生,提高织布后整洁度,从而提升
布料的质量及使用价值。
大圆机针织坯布疵点的分析与控制
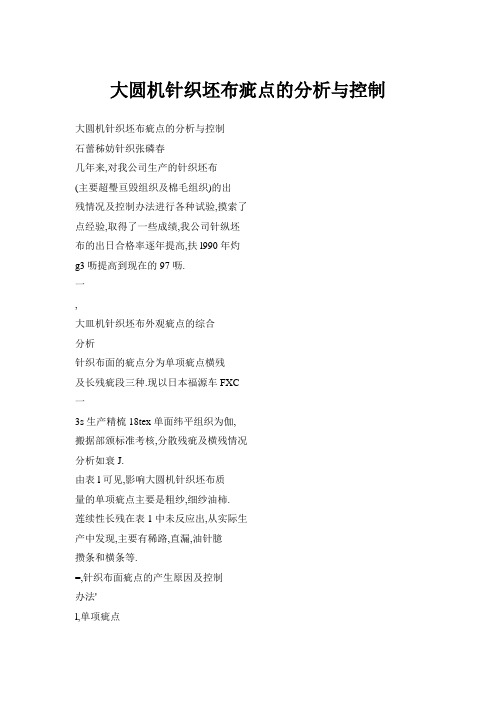
大圆机针织坯布疵点的分析与控制大圆机针织坯布疵点的分析与控制石蕾秭妨针织张磷春几年来,对我公司生产的针织坯布(主要超璺亘毁组织及棉毛组织)的出残情况及控制办法进行各种试验,摸索了点经验,取得了一些成绩,我公司针纵坯布的出日合格率逐年提高,扶l990年灼g3呖提高到现在的97呖.一,大皿机针织坯布外观疵点的综合分析针织布面的疵点分为单项疵点横残及长残疵段三种.现以日本福源车FXC一3s生产精梳18tex单面纬平组织为伽,搬据部颁标准考核,分散残疵及横残情况分析如衰J.由表l可见,影响大圆机针织坯布质量的单项疵点主要是粗纱,细纱油柿.莲续性长残在表1中未反应出,从实际生产中发现,主要有稀路,直漏,油针臆攒条和横条等.=,针织布面疵点的产生原因及控制办法'l,单项疵点TK1328(精梳I8rex2aG单面纬平组织)粗纱27.37嘞,,纽l6-5%I纱总化粕.74嚷大目纱2.4O嘶J色纱0.45铀/柏棉44.O8拓,破捅I4.72面漏针2.aI啼I耋【l戏总比例63-26魄赫点1.53啼I接头fJI2啼J油榴在苴残中占有很高比铡.表】虽将油棉列入织残比例但实际生产中,我们发现因纱线本身带入的油棉也不少.为分析油棉产生的原因,曾做了如下试验, 方法是:①找出有飞花附着的妙筒;@将有飞花附着的纱(有夹入纱中的,有附着在纱线上无加捻的)导在黑板上(留样)分别编号,如图所示.'p'z,'5'乎j,,,,,'I,@将此纱再绕至筒子上进行编胡.宴验结果:~4[4①,@在坯布上形成油棉⑥,⑦形成色纤;||,-其它均形成破洞.由此可见,油棉☆:生既可能是纺纱砷形成,也可能是织造过程中产生,应从两个方面进行控制.除纱场应尽量减少纱线上飞花附入或兜入外,织造车问应在操作及除尘上进行控制.目前我们所采用的为集体式除尘, 车问由~台压缩机控制各台针织机,并有手枪吹风.此除尘方式造价低,除尘效果好.缺点是飞花仍在车间中乱飞,只解决了织机局部飞芘.故挡车工在操作上清洁机白时~定要由里向外吹,由上向下吹. 编织过程申,储纱轮及其附近地区牯有飞花的可厨捻棍清洁.油棉一旦形成后,补救办法是可修的油棉挑修掉.此办法可提高一等品率4—5%纱线质量对予钟织坯布质量的影响非常大,除油棉外,主要为粗细纱.且所织织物纱线愈粗,因纱线质量好坏所产生的残疵所占比例也就愈大.粗纱不仅能引起破洞,而且易损坏针舌,针钩,是造成集罔,破嗣,稀密路等织残的原因之一.相反,细纱所造成盼残疵往往反映在深加工和成品使用阶段.细纱的强力低,织成坯布后,经牵伸.漂冼,定型等,细纱易在细节外断开而不能修补,必须裁剪下来.因此,无论是外购纱还是启纺纱,应选用质量好的针织用纱.严格控制好络纱工序,可大大减少粗细纱及纺纱过程中夹入飞花的粗节纱.清纱器的切断范围要通过反复试验调节到比较合适的水平,使影响布面疵点的纱残小到最低.应普遍推行电子清纱器和自动捻接器,要防止错纱及乱纱带入纱简同时接规定对纱线进行上蜡.络纱工序非常关键,但人们往往容易忽视.这一工序可大大减少粗细纱,对减少针耗和破嗣有很大作用.2,连续性长残对于连续性长残最常见的有稀密路.花针.横条,直漏针等.一般直漏针只要找准位置及时换掉织针即可.稀密路在车上不容易发现,挡车工每下一匹布,在布头根据标样查找稀路,发现后及时换掉坏针或清理针槽.对于臆横条,应将布面松弛下来在蜘面查看.由于横条产生的原因较复杂,解决办法应视具体情况而定.根据实践经验,将横条产生原固及解决措施列于裹2袁2横条原圈措施0弯纱深度不一致测定每一系纡明纱(线速和张力,U有显横节弯纱深度.规条@辅线轮转动不灵激标记查找《律活或导纱眼有堵塞纱,换纱筒..臆同心度偏差百分表测量校横i条水平度超偏差囊詈至主不合I至雯警差化车间管理人员及公司管理人员每日查看及抽验各机台布面,及时发现问题,将损失减小到最低限度.保持机器状态良好,定期检修机器,一般检修周期不超过一个.检修时对用过的针,磨损较大的要挑出来.视织针磨损程度定期更换织针,新旧织针不要混用.要保证机器各零部件齐备.光洁,输线轮转动灵活,三角活动冉如.以上对脐止布面稀路及横条也有一定作用.加油量要视转速.机器型号不同而定,过多易造成油针,过少损伤机器.以布面不出现油污为准.3,色纤色纤在表1申反映出比例很小.因意1中所列残疵比例值均为(下转第32页> ?45?配方:染料x扩散铡NN0YGM般Z浴比l:l4一l6二氧亿硫腮o.2gL碱面1g/L天鹅缄染色直采用大浴此,以减少烈物问相互摩擦,叠压的机会.利于绒的平整染色时升降温速度不宜过快.涤纶纤维在玻璃化温度(约80℃)以j纤维大分子链段振动逐渐擞亿(解冻)纤维的脾闻孔穴尺寸逐渐增加可及性衽商用初染率较高的染料染色时.升温过恢易造成染色不匀若降温过侠织物在折叠状态下迅速通过玻璃亿温度使纤维大分子链段振动在折叠状蠢下冻结.'会造成死折印,因此升降温速度应严格控制.7轧柔软剖,短环烘干'轧柔软剂的目莳在于使织物手感柔软,其有良好的悬垂灶,提商兜泽等.柔软荆的加入可根据柔软荆品种的不同采用与染色同浴或单独浸轧等方法.我厂使用的柔软荆为有机硅30.易破乳,漂油,不易清理,因而不宜垂染扰中加入,而采用轧车浸轧法.工艺如下.Si一3O3g/L;水温30~40℃;压力3.14×10"---3.73×10Pa;车速8m/mi1"I;短环燃燥温度13O℃.轧柔软剂时需要注意:①.绒面朝上顺毛上机.②保证一定的成环量.以免张力过犬,造成卷边,落布边湿.③,轧车左右压力要一致.保持一定的轧余率.8.对于简易流程轧柔后再经定型即为成品.定型时皱面向上,删毛上枕,超喂要合理控制,保证满足克重要求.出布毯面要冷却至6O℃以下再进行堆置,否则易出折印至于长流,开松的作用主要是消除前几道工序造成的折皱,使倒伏的绒毛尽直立,以利于后工序的复剪烫剪船作用主要是在韧剪的罄础上使天鹅绒的绒面均匀j齐,保证绒毛具有一定高度.并对绒毛理顺和烫光.使其倒向一致. 减少漫反射,增加光泽,这里不冉详述.(上接第45页)验布机标准速度下荧光屏上检验.脒特别粗长明显的外,纽/J,的色纤不易被发删.我公司出口针织坯布几年来,客l户曾多次反映坯布上存在色纤而不易漂自及絷浅色.为分析解决色纤,我们专门成立了控制色纤质量小组,定期对坯市上色纤进行分析.我们发现.使用国产棉时,黑色及红色杂纤所占比例很大(其中黑色占48%, ?32?红色f4O呖)其它五f『绿色黄色兰色甚少(占l2劳).进口棉所古'比蝴较大时,则黑色杂纤甚少,主要为黄棕色棉杆结(黄橡岔74%,黑坦2j骺其它5和).经漂斌验证明,黑色杂纤不易澡掉,丽进j=『襁上黄棕色襁秆结经漂洗可除去.按包位挑检色纤,如发现色纤多的原棉批号.搭配技用控制配糯,良色纤保持在一定水平上.。
(完整版)织布疵点大全

织造品质织疵成因一、经纱断头原因。
(不包括纱原纱品质及准备工用原因)1.综框过高低,左右不平。
2.开口过大过小,过早过迟。
3.经纱路线过短,(后梁过前),经纱张力太大4.后梁及停经架位置赤字高,上下层经不张力悬殊太大。
5.停经架与综框距离过远过低。
6.空气调节、湿度过高过低。
(尤其麻纱反应最大)7.剑颈、钢筘、综丝、停经片、剑带等毛糙。
8.过撑位置过高,应距最低位置1mm。
9.结头纱尾、飞花杂物搅入经纱。
10.值车对经纱倒断头、搅头处理不良,断经后接纱结头不良;如纱尾长二、断纬原因1.纬纱强力过低、松捻纱、大结头、棉籽屑、飞花回丝夹附。
2.络筒时强力过太、张力太大、成形不良。
3.边撑太前撞筘,距离钢筘到少要有1mm的间隙。
三、双纬1.纬纱断头为主要原因,首先须减少断纬线。
2.值车工不注意在断头后,未将织口内断纬拉清。
3.值车工在断纬后未将开开口顺序较主合适时开车。
4.纬纱断头后断纬运动未立即作用停车,而中间缺少数根或一根纬纱四、缩纬1.纬纱捻度过大。
2 .纬纱太干或太湿。
3.开口不清。
4 .开口时间过早或过迟。
5.纬纱引出张力太小。
6 .经纱张力不足。
7.纬纱筒子有大结头、飞花、杂物附着、粗节纱造成部分开口不清。
五、小稀路1.筘座及卷取刺毛辊松动或腐蚀。
2.经纱张力过大或过小。
3.经纱上下两层纱张力相差悬殊。
4.停车过久后开车时梭口未较正。
5.停车后开车起动太缓慢影响打纬力。
(主电机皮带松驰无力)六、纬纱尾织入1.右测经纱距离顺风管太远,废边纱未能很好夹持纱尾。
2.纬纱张力太小,剑头开启时间太晚。
七、稀路1.起因均为断纬、首先须减少断纬。
2. 断纬卷取退卷绕装置不良。
八、跳花1、综框松动、不平或过低。
2 、经纱张力上下两层相差悬殊。
3、浆纱过毛、开口粘滞、上浆不良引起绒球或毛羽。
4、经纱有飞毛、纱尾及大结头。
5、综丝头尾损断或综丝搅乱 6 、部分经纱松弛或张力过低7、开口时间不对。
(开口过小)8 、边撑高低不标准。
纺织病疵分析大全
纺织病疵分析大全纺织病疵分析大全--集三十七年病疵分析之经验纺织病疵分析大全--集三十七年病疵分析之经验改贴进行中........2楼.一、经纱断头原因。
(不包含纱原纱品质及准备工用原因)3.二、细纱断头的原因4.色差的成因与预防5整理产品常见疵病分析一、通常外观疵病6. 二、通常内在疵病7. 三、特殊内在疵病8. 织物疵点专用术语9. 涤纶织物产生风印的症状10. 常见烧毛疵病及克服方法11. 防止真丝绸泛黄有什么较好的方法12. 滚筒印花疵病及其预防措施13. 如何减少腈纶筒子纱染色大小样色差14. 如何减少卷染机染色头尾(梢) 与左中右色差15. 毛织物染色后表面出现深浅斑渍、斑点、渍印问题16. 普通涤纶织物高温高压染色色花的防止17. 羊绒衫掉绒起球的原因分析与解决措施18. 印染布疵点产生的原因及检测方法19. bjckxj MM留位20. xiaoke MM留位!织物病疵分析鉴定报告21. 锦纶HOY长丝,已出现丝筒严重变形22. 计算坯布到成品的经向缩率23. 布面经柳原因分析24. 布面经柳原因分析25. 布面白斑原因分析26. 布面纬档原因分析27. 布面经柳原因分析28. 布面横条原因分析29. 布面经条原因分析30. 布面纬档原因分析31. 成品阳离子格子布布面经向强力过度损伤原因分析32. 大有光染色成品布布面产生经柳的原因33. 一块TTR染色成品布布面产生鸡爪印的原因。
34.一块涤纶染色成品布布面产生经柳的原因35. 四面弹染色成品布布面产生纬档原因分析36. 150D醋酯纤维绞状色丝及筒装本色丝色丝产生色差的原因37. 平板四面弹染色成品布布面产生钩毛的原因38. 成品牛仔裤及部分装饰镀件裤面出现斑点状色点的原因39. 染色成品布布面出现白条的原因40. T恤衫布面出现黑点的原因41.. 针织布布面产生横条的原因42. T/R平纹四面弹印染成品布布面产生纬档的原因43. 全棉布布面出现色差的原因44. 针织布布面产生直条的原因45.. 牛仔色织布布面产生门幅不一的原因46. 裤子袋口破裂产生47. 涤纶针织氨纶布布面产生横条的原因48. 棉氨汗布布面产生横条的原因49. 长丝四面弹染色成品布布面产生经柳的原因50. TTR染色成品布布面纬向产生黑点的原因.51.裤片产生纬档的原因52.植绒印花布(印花布、坯布各一)布面出现脱毛及色差的原因53.四面弹染色成品布布面经向产生色差的原因54.圆机布染色成品布布面产生横路的原因55. 涤纶弹力染色成品布布面产生纬档的原因56.人丝乔其染色成品布布面产生白条的原因57.纬弹染色成品布料布面产生经柳的原因58.针织布布面横路的原因59.54565115留位60.染色成品布布面产生纬档的原因61. 条子涤毛布布面经向产生断丝的原因62. 灯芯绒成品裤裤面产生横条的原因63. 二块染色涤纶弹力布及一块坯布分析布面产生经条的原因64. 二条色织牛仔裤裤面产生条纹病疵的原因65. 针织成品布布面产生横路的原因66. 点子布布面产生纬向色条的原因67. 两块布样门幅不一的原因68. 起绒布布面产生横路的原因69. 染色成品布料布面产生经柳的原因70. 大圆机布成品进行检测,分析布面产生横路的原因71.提花阳离子绉布布面局部不起绉72.涤纶四面弹进行检测,分析布面产生经柳的原因73.布面产生色点病疵的原因及检测棉纱等级74.全棉印花布布面产生破洞的原因75.布面产生色差病疵的原因76.针织汗布布面产生横条病疵的原因77.罗缎染色成品布布面产生经柳病疵的原因78.布面产生经条病疵的原因79布面色点病疵产生的原因.80.布面产生断纬现象的原因81.布面经向起泡病疵产生的原因82.人丝乔其连匹出现色差的原因83.一块四面弹出现经向白条的原因84.一块涤纶经编条绒出现色点的原因85.块100%兔绒机织布布面出现纬档的原因86.一块装饰布布面纬向色档病疵产生的原因87.一块纬弹成品布布面纬档产生的原因88一块纬弹成品布布面经向黑点产生的原因。
技术|粗细节、条干不匀等五大常见疵点的影响、成因及改善措施
技术|粗细节、条干不匀等五大常见疵点的影响、成因及改善措施对于纯棉精梳细号纱线,从危害程度和发生频次看影响布面质量的有害疵点主要是粗细节、条干不匀、飞花、棉结和异常疵点。
这些疵点对后工序有哪些影响?影响布面质量的有害疵点01粗细节粗节,布面表现为一个突出的粗节,影响织物外观,甚至造成布面降级。
布厂可以通过人工挑修改善外观,但是挑修操作困难、费时费工;细节,因为比正常纱细,就会形成纱线强力弱环,造成准备和织造过程的断头,影响准备和织造的效率,即使未发生断头在布面表现为细于正常纱的疵点,且无法修复,数量多时会造成布面降级。
02条干不匀影响织物外观,造成布面降级,特别严重时在织物布面表现为条影或木纹,较轻的情况下布面外观浑浊、不光洁似有云斑,条干不匀还会造成染色不匀。
03棉结布面表现为棉点或白星,星星点点分布在布面上,影响织物外观。
布厂可通过人工挑修来降低棉点,但数量过多时挑修不能达到良好的效果,而且费时费工。
此类疵点较多或较大时在准备、织造中纱线断头率会增加,影响准备织造效率,影响织物外观及平整,造成布面降级。
04飞花布面表现介于粗节和大棉结之间,比粗节短、纤维松散,影响布面光洁程度。
通过人工挑修可得到改善。
异常疵点多表现为长片段,发生频率低,如单纱中的双线纱,股线中的三股纱和四股纱等,以及长粗节、长细节。
此类疵点严重影响织物外观,造成布面降级,制衣厂一般都需要做避裁处理,会降低布的利用率。
更严重时甚至会延误订单的交期,赔偿客户的损失。
不同的布种对纱线的质量要求可以看出纱线疵点对后工序尤其是织物的布面效果有较大影响。
从布厂的产品种类看,不同的布种对纱线的质量要求也不同。
a)净色布种(经纬纱线同色或不同色的平纹织物):根据经纬颜色的反差大小,对纱线的棉结要求不同,经纬颜色反差越大,对棉结要求越高,尤其经特殊后整理的布种对粗节、棉结要求更高。
b)米通条布种(经向、纬向或经纬两方向相邻纱线颜色不同的织物):纱线颜色反差越大,对粗节、棉结和条干均匀度的要求越高。
涤纶常见的染色疵点产生的原因及预防措施
涤纶常见的染色疵点产生的原因及预防措施摘要:本文从理论角度分析了涤纶常见的染色疵点产生的原因及预防措施。
首先介绍了涤纶的结构和各项性能,从而得出涤纶的一些基本特性。
然后从分散染料对涤纶的染色时产生的色花、色点、色差及分散染料的泳移现象论述了涤纶常见的染色疵点,并针对这些疵点提出相应的预防措施,解决涤纶常见的染色疵点。
关键词:涤纶疵点原因预防措施前言涤纶自发明至今以它绝对的优势取得了快速的发展,其数量已占世界纺织纤维的1/3,约占我国纺织纤维加工量的一半,成为合成纤维中的佼佼者,是当今理想的纺织材料。
它的优越性主要取决于它特定的大分子结构;不仅有刚性的苯环,而且有脂肪族的链节,使其不仅具有可熔融加工性,便于加工成纤维,而且其大分子足够的刚性,赋予纤维高的初始模量。
涤纶的综合性能好,强度大、弹性好,加工性能也好,其制成的面料挺括而不易变形,洗后不用熨烫,可纯纺也可和各种天然纤维混纺或交织,广泛用于服装,家用纺织品和产业用纺织品。
在服装方面涤棉混纺织物可用于衬衣、床上用品,涤纶长丝可用于外衣、运动衣,也可用以生产仿羊毛、仿丝绸、仿麻等仿天然纤维产品等。
由于涤纶可以大批量生产,加工技术不断改进,生产费用降低,所以涤纶的前景一片大好。
而涤纶的染色疵点对涤纶的生产制品带来了很多麻烦,所以我们必须对涤纶染色疵点有一定了解,比如涤纶染色时的色花、色点和色差等,并分析这些涤纶染色时疵点产生的原因有哪些,从而提出控制涤纶染色时疵点的预防措施,解决这些涤纶染色疵点,以减少对涤纶加工和制品带来的生产麻烦【1】。
1 .涤纶和分散染料1.1涤纶1.1.1涤纶的结构涤纶是聚对苯二甲酸乙二醇酯纤维的商品名称。
在一般光学显微镜下观察,普通涤纶的纵向为光滑、均匀、无条痕的圆柱体,横截面为圆形。
涤纶大分子链上不含有亲水性基团,且缺乏与染料分子结合的官能团,故吸湿性、染色性差,属于疏水性纤维。
涤纶大分子的基本链节中含有苯环,阻碍了大分子的内旋转,使主链刚性增加。
纺织品瑕疵原因分析及处理方法
服装材料纺织品瑕疵纤维原料到最后制造成成品织物,需经过纺纱、织造、印染等工程,且每种工程中,又需经过一连续多个加工过程(Process)始能完成。
在各层次的加工中,设定条件之不当,人员操作之疏忽,机械之故障等,均可能致使产品发生外观上之缺点。
就理论上言之,加工之层次愈多,则发生缺点之机率亦愈高。
在织物外观所能见到之此种缺点,称谓织物瑕疵(Fabric Defect)。
但亦有在胚布状态无异状,若经漂、染加工后则显著出现,此种一般多称之谓潜隐瑕疵(Latent Defect)或隐性瑕疵。
我国有一句俗语:「多作多错,少作少错,不作不错。
」,此语虽在现代工作精神上不合时宜,但用在纺织多层次加工所产生之瑕疵上却甚为切合实际。
世界上少有完美之事物,纺纱工程会使原纱产生瑕疵,例如棉粒(Nep)、粗结(Slub)等;织造工程会使胚布产生瑕疵,例如并纬(Mispicks)、断经(Broken Ends)等;印染工程会使成品布产生瑕疵,例如染料点(Dye Spot)、结尾色差(Tailing or Ending)等。
品质优良之成品织物,其瑕疵应为极少。
如某种成品织物之瑕疵甚多,无论是用作制衣、被服、或其它日用品及装饰品,均会影响其美观,而降低其价值。
二、织物瑕疵之外观特征与成因由纤维至成品织物,加工之阶段可分为纺纱(Spinning),织造(Weaving),练漂、染色、印花(Scouring & Bleaching,Dyeing,Printing)与整理加工(Finishing)四大阶段。
现以在各阶段中可能发生之瑕疵,用工厂一般通用之名称,就其外观特征与生成之原因分述于下:1.属于纤维原料、纱支原因者2.属于织造原因者3.属于印染整理原因者4.生成原因难以归属及专业加工者1.属于纤维原料、纱支原因者(1)棉粒(Nep)外观:布面呈现类似接头大小之棉纤维团,且系纺入纱中者。
如将之拔下,则纱呈断裂或将至断裂之状态。
- 1、下载文档前请自行甄别文档内容的完整性,平台不提供额外的编辑、内容补充、找答案等附加服务。
- 2、"仅部分预览"的文档,不可在线预览部分如存在完整性等问题,可反馈申请退款(可完整预览的文档不适用该条件!)。
- 3、如文档侵犯您的权益,请联系客服反馈,我们会尽快为您处理(人工客服工作时间:9:00-18:30)。
布疵形成的原因及消除方法一:边不良、边撑疵、烂边、毛边。
(一): 边不良A:形成原因1 :锯齿边当纬纱张力忽大忽小时,布边内卷,最易造成锯齿边。
2 :荷叶边当纬纱张力小于经纱张力时,或经纱张力时松时紧,布边不平整,会岀现荷叶边。
3:边纬缩纬纱退绕张力小,引岀不畅,开口投梭工艺时间配合不当,梭子通道部分有快口,或者是纬纱在退绕时, 受到布边经纱毛羽影响,使纬纱不能拉直,布边较松,因而产生纬纱气圈或边纬缩疵点。
4:边穿错边纱穿法不统一或穿错,处理浆纱多头、少头、错头时,缺乏一套完整的操作规程。
5:布边两侧全匹带规律性的不平整。
(1 ):纬纱张力变化。
(2):经纱张力不良。
(3):边撑不良。
B :消除方法(1 ):在严格控制经纱张力均匀的基础上,加大边纱张力,保证开口清晰度。
(2 ):合理配置开口、投纬工艺时间。
彻底消除梭子通道部分快口,解决边纬缩、坏边疵点。
(3):要适当增加纬纱张力,解决布边两侧差异。
(4 ):改进边纱穿综操作。
(二):边撑疵A:形成原因1:边撑盒位置过高或过低,织物的全幅织口不在同一水平线上,形成两侧布边向外凸岀,布身向内凹入。
2 :布面张力过大,经纱紧贴边撑刺辊,致使刺尖切割经纬纱而产生的边撑疵,大都是有规则的通匹疵布。
3 :布幅愈阔或纬缩率愈大的织物,愈易产生边撑疵。
4:边撑刺辊使用不当,或新购入的边撑刺辊未及时加工,发生刺尖部分迟钝,或刺尖虽锋利但呈弯钩形状, 将经纱或纬纱钩起拉断。
5 :边撑盒内刺辊,有短回丝、落浆、落物等阻塞,影响刺辊回转不灵活,造成刺辊与布面速度不一致,使刺尖割断纬纱,产生边撑疵。
6 :边撑匣配套不良及边撑匣盖、边撑匣座的合缝大小或歪斜。
7 :卷布刺辊刺毛铁皮过分锋利、快口或刺孔磨灭迟钝,也会产生边撑疵。
8 :织造车间温湿度调节不当,最易产生大面积边撑疵,特别在制织粘胶织物时,更为敏感,影响较大。
9 :送经装置不良,张力扇形杆上下动程过大,送经锯齿轮撑头磨灭,经纱张力忽紧忽松,易产生有规律的边撑疵。
10 :布面张力过紧,遇到刺辊稍有轧住,亦会产生边撑疵。
11 :落布操作时,由于木辊直径较大,容易与卷布刺辊上的刺毛铁皮相摩擦而产生类似边撑疵坏布。
12 :边撑盒盖上螺栓头部碰撞筘帽前夹木或碰撞飞梭装置铁杆。
13 :平车或拆坏布后,用手将布边拉入边撑盒的操作不当。
B :消除方法1 :边撑、刺辊配套良好,安装正确。
2 :使织机有关部件处于正常状态。
3 :加强各工种的操作管理。
4:加强温湿度调节工作。
5 :几项技术改进。
(1 ):采用单只刺辊。
(2 ):采用颗粒橡胶刺辊或乳胶管辊与铁刺辊混用。
(3 ):采用十片铜刺辊,比木刺辊或铁刺辊伸幅作用大1〜1.5CM 。
既可消除因伸幅不良造成的断边,也可减少边撑疵点。
(4 ):检查木刺辊、铁刺辊、铜刺辊是否达到技术要求。
(5 ):织机卷布刺辊两端包布,防止落布后将布头卷紧时,布边和刺毛辊表面摩擦而产生边撑疵。
(6 ):织机卷布辊托脚木轴承厚度,可有原来的19.2MM 减为9.6MM,防止落布时布辊直径过大与卷布刺毛辊相擦而造成类似的边撑疵布。
(三):烂边第一类大烂边A:形成原因1 :纬纱上的棉结杂质,特别是中、细特纱上的大杂质,以及细纱纺制时的飞花、回丝附入而产生的细节,与纬纱退绕气圈相碰,造成意外阻力。
2 :纬管腔内积有回丝,因梭子冲击而从纬管头部小眼内脱岀,阻塞梭子骑马钢丝或瓷眼通道,致使纬纱引伸受阻,张力增加。
3 :织机揩扫时飞花落入梭子瓷眼,使纬纱引伸不畅,增加意外张力。
4 :梭管配合不良,两者中心不一,梭芯高低位置不正,梭芯忽高忽低,纬管内孔磨损等,均会使纬纱退绕时的张力严重不匀。
B :消除方法1:提高纬纱质量,根据织造品种不同,提岀原纱棉结杂质的具体要求,一般棉杂要小而少。
2 :纬管内孔回丝,纺部要设法解决,织造车间应结合纬管定期检修,加以消除。
3 :清扫织机时,落梭箱需用盖布遮住,防止飞花落入,阻塞梭子瓷眼。
4 :做好梭、管配套工作。
第二类小烂边A:形成原因1 :边撑伸幅作用不够,边撑刺辊第握持力不足,边纱控制不牢。
特别在纬纱由满纱逐渐退绕至小纱时更为突岀。
2 :经纬纱缩率高的中特平纹织物上、边纱配置太少,或边纱本身穿错,承受不起打纬时钢筘的剧烈摩擦,会产生断边、小烂边。
3 :梭口满开时,若经纱张力过大,或者左右两侧经纱张力差异悬殊,则张力较大的一侧,在打纬时会使张力大的纬纱被张力大的经纱随边筘齿向外拉伸而崩断,造成小烂边。
B:消除方法1 :认真检查边撑刺辊状态,校正边撑位置,符合工艺要求。
2 :校正钢筘位置,特别要防止上层经纱在梭口满开时被筘帽压住,而影响全幅经纱、边纱的意外张力。
3:吊综应符合工艺要求。
4 :织机正常运转中,钢筘应不碰边撑,撞嘴应不碰停止掣子,以防产生断边、小烂边。
(四):毛边A:形成原因1:边撑剪刀失灵,尾纱未剪断而带入织口。
2 :换入梭子的纬纱在梭库处中断。
3 :采用探针诱导换梭装置,纬管上的保险纱,在换梭时,一端随着换岀梭子下落至落梭箱内,另一端仍在织口中。
当纬纱被边剪剪断后,尾纱仍残留在走梭板上,由于梭子的运动,该段纱尾会每隔数梭带入织口,因而形成布边须状毛边。
B:消除方法1 :边撑剪刀配套良好,安装正确。
2 :技术改进。
(1 ):减少换入梭子尾纱造成毛边的方法a:前闸轨上装钢丝或毛刷。
b:梭库上加装橡皮筋。
c:梭库托脚上加毛刷。
d :阻梭板上开槽。
(2 ):减少换出梭子尾纱造成毛边的方法a :梭箱底板开槽。
b:扇形制动器杆装毛刷。
c:筘座上装毛刷。
二:纬缩纬缩疵点在布面上的形态,大体可分为扭结纬缩、经向一直条纬缩、一处性方块形纬缩和分散性纬缩。
(一):四种类型纬缩产生的共性原因A:形成原因1 :原纱质量不良。
2:纬纱的捻度过高。
3:纬纱的回潮率过低。
4 :投梭作用不良。
5 :梭子状态不良。
6 :开口清晰度不良。
B :消除方法1 :改善原纱质量。
2 :稳定纬纱捻度。
3:加强织机维修保养。
4:适当增大梭子的导纬张力。
(二):四种类型纬缩产生的非共性原因A:形成原因1:扭结纬缩(1):纬纱在换梭侧容易打扭弯曲。
(2):梭子状态的变化使纬纱产生横向振动而形成卷曲扭结。
(3 ):纬纱由满管退绕至空管,其张力由小增大,使纬纱气圈抛岀梭腔外的机会相应在变化。
(4):梭子换梭侧梭箱时,由于纬纱本身的回潮率低,捻度不稳定,梭子导纱眼至布边一段纱线非常松弛,当梭子一动,纬纱即开始扭结。
2:经向一直条纬缩由于织造开口工艺、投梭时间配合不当所造成。
3:一处性方块形纬缩一处性方块形纬缩在府绸织物上较为突岀。
着主要是制织高密府绸织物时,四页综框开口工艺采用单踏盘的一次平综方式时所造成。
4:分散性纬缩主要是吊综不良引起的。
B :消除方法1 :针对扭结纬缩产生的特性,对纬纱采取给湿,增加张力,调整投纬时间。
2 :根据经向一直条纬缩分布的区域与产生的规律调整开口工艺,1、2综框采用早开口,3、4综框采用迟开口。
3:圆筒布经向一直条纬缩宜采取下列措施。
(1):对原纱及半制品质量的要求。
a :选择捻度较小的原纱作纬纱,经纱的棉杂应小而少,表面毛羽少,纱身较光滑,使经纱不易带住梭道内引岀的纬纱造成纬缩。
b:为了改善织口清晰度,,减少织造中断头,经纱上浆率宜高些。
(2)合理选择织造工艺参数;圆筒布在1511型或1515型有梭织机上制织,常用多臂式开口机构。
4 :一处性方块形纬缩的消除方法,可从经、纬向两方面同时采取措施。
(1):经向:将密度较高的经纱,开口时相邻经纱交叉分开,亦即将(高密度府绸织物)开口时间,由一次平综改为两次平综。
吊综的规格掌握小双层开口的原则。
从而减少经纱之间的相互摩擦,增加开口清晰度。
(2):纬向:在不影响断纬、断稀疵布增加的前提下,适当加大纬纱张力,压缩气圈,减少纬纱起圈现象。
(3):在经纬向采取措施的同时,为进一步改善织造时的开口清晰度,一般还可采用加大布面张力的措施。
5:分散性纬缩日常生产中消除和修理分散性纬缩疵点的方法,基本上与解决星跳、沉纱的方法相同。
重点介绍如下几种方法:(1 ):吊综牌楼尽量前移。
织机正常运转时,第一页综框以不碰筘帽为原则。
要求综框左右不晃动。
(2):梭口清晰。
吊综不宜过低,特别是双踏盘开口机构小双层开口规格左右要一致。
(3) :为了防止筘帽压上层经纱,钢筘的高度可采用120.7mm 。
(4):采用尼龙吊综带可防止伸长。
(5):投梭缓冲机构维修应符合要求,注意缓冲强力与梭子不正常的回跳现象。
三:轻浆、棉球A:形成原因1 :调浆成分选择不当,或对浆料性能不熟悉,上浆率规定过低。
2:调浆时浆料与水的配比不当,或煮浆时蒸气带水过多,造成浆液太稀,粘度过低。
3 :调浆设备状态不良,如阀门漏水、漏汽,水汽分离器失灵,输浆系统不畅,浆料预热器浮球阀门失灵, 形成脱浆等。
4 :以淀粉为主体的浆料,淀粉未糊化,落浆多。
煮浆时间不足或过长,使粘度下降。
5:浆槽液面过低,车速太快,经纱浸浆时间太短。
6 :浆槽蒸汽压力低,浆液粘度高而不易渗透纱内,造成表面上浆,纱线经不起浆纱分绞及织造摩擦,浆膜破裂,落浆多。
7 :压浆辊太轻或两端加压不匀,浆液不易渗透或渗透不匀造成表面上浆。
压浆辊太重,打慢车时岀现轻浆。
8 :回浆使用过多,浆槽内任意掺水、掺生浆,上机绒布过湿,开慢车时间过长等使浆液粘度下降。
9 :停车时间长,如处理疵点、落轴等造成短片段、横向轻浆。
10 :纬纱经精梳工序后,纤维平直,如钢丝圈使用日久,稍有沟槽即摩擦纤维而聚结成球;其次细纱纺岀过程中的气圈大,与隔纱板的摩擦重,液易岀棉球。
B:消除方法1 :加强主浆料的试化验工作,合理制定浆成分。
2:正确制订合理的上浆率。
3:浆槽内的浆液粘度,每浆一轴或两轴应测试一次,以控制上浆情况正常。
4 :浆槽改用双浸双压机构,可在一对压浆辊之间,加装罗拉浸没辊,增加浆液渗透,提高上浆率。
5 :加强管道阀门的检查,防止漏汽、漏水,使水气分离器处于正常状态,充分发挥其作用,使浆液浓度稳定,经常保持输浆系统的畅通,防止堵塞,造成脱浆。
6:加强操作管理,健全回浆使用制度。
7:加强对细纱钢领与钢丝圈的配合管理,定期调换钢丝圈。
8 :做好纬纱固定供应工作,如发现纬向棉球疵布,及时跟踪检查,予以消除。
9 :发动群众把好质量关,细纱大断头接头时,要查看管纱表面有无棉球,并及时处理。
四:跳花、跳纱、星性跳花A:形成原因1 :原纱及准备半制品质量不良。
2 :吊综不良。
3 :织机开口、投梭、送经部分机构状态不良。
4 :梭子状态不良。
5 :开口与投梭时间配合不当。
6 :经位置线失调。
7 :织造时经纱运动不稳。
8 :织机挡车操作不良。
9 :纤维性能的影响。
B :消除方法1 :提高原纱与半制品质量。
2 :提高梭口清晰度。