热固性塑料件结构工艺性
热固性塑料
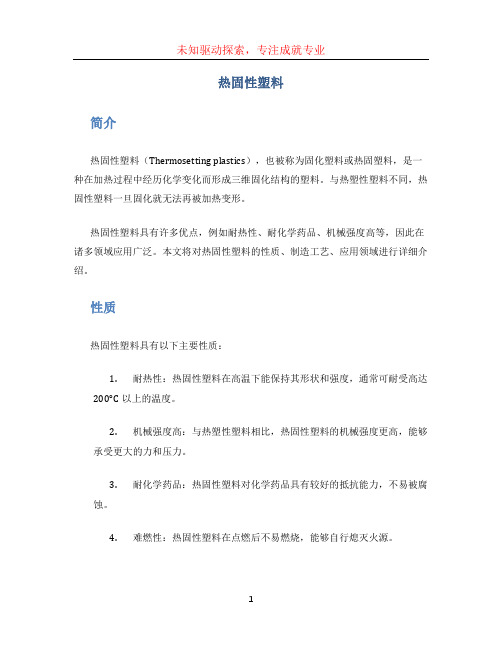
热固性塑料简介热固性塑料(Thermosetting plastics),也被称为固化塑料或热固塑料,是一种在加热过程中经历化学变化而形成三维固化结构的塑料。
与热塑性塑料不同,热固性塑料一旦固化就无法再被加热变形。
热固性塑料具有许多优点,例如耐热性、耐化学药品、机械强度高等,因此在诸多领域应用广泛。
本文将对热固性塑料的性质、制造工艺、应用领域进行详细介绍。
性质热固性塑料具有以下主要性质:1.耐热性:热固性塑料在高温下能保持其形状和强度,通常可耐受高达200°C以上的温度。
2.机械强度高:与热塑性塑料相比,热固性塑料的机械强度更高,能够承受更大的力和压力。
3.耐化学药品:热固性塑料对化学药品具有较好的抵抗能力,不易被腐蚀。
4.难燃性:热固性塑料在点燃后不易燃烧,能够自行熄灭火源。
制造工艺热固性塑料的制造工艺与热塑性塑料有所不同。
热固性塑料在加热过程中通过交联反应形成固化结构,无法再通过加热融化变形。
热固性塑料的制造主要包括以下步骤:1.原材料准备:选择适合的树脂材料作为基础,通常采用液态或固态树脂将其与填料、助剂等混合。
2.成型工艺:热固性塑料可以通过注塑、挤出、压缩成型等多种工艺进行成型。
其中,压缩成型是最常用的方法,通过将热塑性塑料放入加热的金属模具中,在高温和高压的条件下形成固化结构。
3.固化反应:成型后的热固性塑料需要进行固化反应。
固化反应可以通过热固化剂的添加或者外部加热来实现。
在固化过程中,树脂分子间发生交联反应,形成耐热的固体结构。
4.后续处理:固化完成后的热固性塑料需要进行后续处理。
这包括修整表面、去除残留的固化剂、进行表面涂层等。
应用领域热固性塑料由于其耐热性、机械强度高等特性,在许多领域被广泛应用。
下面是一些常见的热固性塑料的应用领域:1.电子电气:热固性塑料具有良好的绝缘性能,因此在电子电气行业中被广泛应用于绝缘材料、电路板等制造。
2.汽车工业:热固性塑料的高耐热性和机械性能使其成为汽车工业中的重要材料,例如用于汽车引擎部件、底盘零件等的制造。
第6章热固性塑料的主要成型加工技术
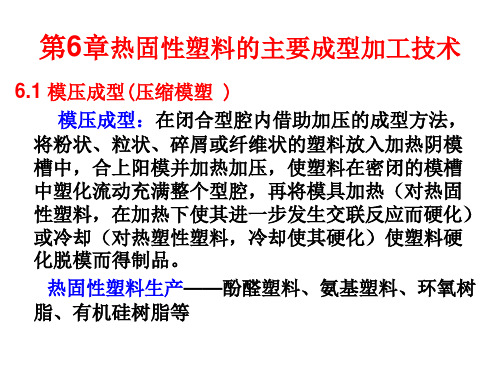
半溢式:有支承面与溢式相似,有装料室,用于小嵌件制品
无支承面与不溢式模具很相似,阴模向外倾斜3°, 阴模阳间有溢料槽
溢式模具
不溢式模具
图6-5 半溢式模具示意图 (a)有支承面 (b)无支承面
6.1.3 模压成型过程及操作
6.1.3.1 模压成型过程
成型物料的准备、成型和制品后处理三个阶段
模压成型原理
(2) 热固性与热塑性塑料注射成型不同点
热固性塑料在料筒内的塑化(料筒温度)
热固性塑料熔体在充模过程的流动(剪切
应力和充模速度)
热固性塑料在模腔内的固化(模具温度)
6.4.2 热固性塑料注射成型机
(1)注射装置
作用:将塑料均匀地塑化成熔融状态,将熔料注射到模腔内
基本形式:螺杆式和柱塞式,主要采用往复式单螺杆注射
机
螺杆——与热塑性塑料注射机区别大 (2) 螺杆驱动装置(低转速大扭矩油马达驱动螺杆旋转)
(3) 合模装置(由模板,拉杆,合模油缸等组成,合模力大)
(4) 控制系统
(5) 特殊注射机
双柱塞式注射机
图6-22 柱塞式聚酯料团注塑机 图6-21 多工位注塑机
6.4.3 热固性塑料注射成型工艺
图6-23 热固性塑料注塑成型工艺过程
C→E,交联,放Q→T物>T模, V↓
E点卸压, P↓常压
F点脱模
模压成型压力-温度-体积关系 ——:无支承面 ------:有支承面
6.1.4 模压成型工艺控制
6.1.4.1 模压压力Pm
指成型时压机对塑 料所施加的压力
pm
D2
4 Am
pg
Pm与塑料种类、模温、 制品形状有关
模压P对流动固化曲线的影响 a-50MPa b-20MPa c-10MPa
热固性塑料注塑工艺过程
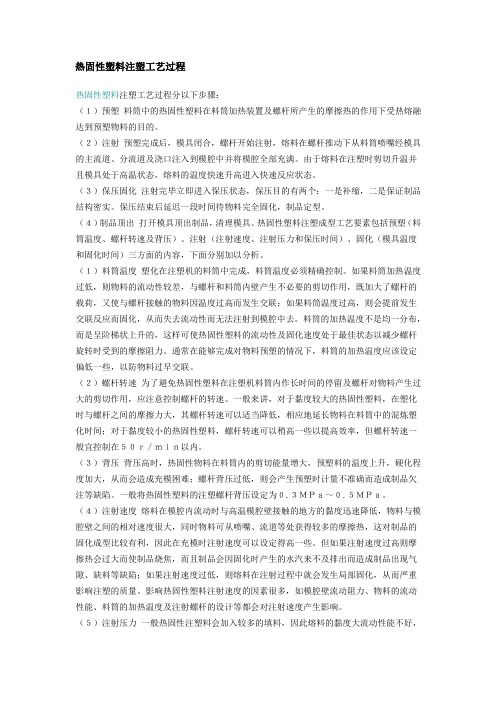
热固性塑料注塑工艺过程热固性塑料注塑工艺过程分以下步骤:(1)预塑料筒中的热固性塑料在料筒加热装置及螺杆所产生的摩擦热的作用下受热熔融达到预塑物料的目的。
(2)注射预塑完成后,模具闭合,螺杆开始注射,熔料在螺杆推动下从料筒喷嘴经模具的主流道、分流道及浇口注入到模腔中并将模腔全部充满。
由于熔料在注塑时剪切升温并且模具处于高温状态,熔料的温度快速升高进入快速反应状态。
(3)保压固化注射完毕立即进入保压状态,保压目的有两个:一是补缩,二是保证制品结构密实。
保压结束后延迟一段时间待物料完全固化,制品定型。
(4)制品顶出打开模具顶出制品,清理模具。
热固性塑料注塑成型工艺要素包括预塑(料筒温度、螺杆转速及背压)、注射(注射速度、注射压力和保压时间)、固化(模具温度和固化时间)三方面的内容,下面分别加以分析。
(1)料筒温度塑化在注塑机的料筒中完成,料筒温度必须精确控制。
如果料筒加热温度过低,则物料的流动性较差,与螺杆和料筒内壁产生不必要的剪切作用,既加大了螺杆的载荷,又使与螺杆接触的物料因温度过高而发生交联;如果料筒温度过高,则会提前发生交联反应而固化,从而失去流动性而无法注射到模腔中去。
料筒的加热温度不是均一分布,而是呈阶梯状上升的,这样可使热固性塑料的流动性及固化速度处于最佳状态以减少螺杆旋转时受到的摩擦阻力。
通常在能够完成对物料预塑的情况下,料筒的加热温度应该设定偏低一些,以防物料过早交联。
(2)螺杆转速为了避免热固性塑料在注塑机料筒内作长时间的停留及螺杆对物料产生过大的剪切作用,应注意控制螺杆的转速。
一般来讲,对于黏度较大的热固性塑料,在塑化时与螺杆之间的摩擦力大,其螺杆转速可以适当降低,相应地延长物料在料筒中的混炼塑化时间;对于黏度较小的热固性塑料,螺杆转速可以稍高一些以提高效率,但螺杆转速一般宜控制在50r/min以内。
(3)背压背压高时,热固性物料在料筒内的剪切能量增大,预塑料的温度上升,硬化程度加大,从而会造成充模困难;螺杆背压过低,则会产生预塑时计量不准确而造成制品欠注等缺陷。
塑料成型的工艺性能

塑料成型的工艺性能
1.2热固性塑料成型的工艺性能
溢料间隙/mm '0. 03
0. 03〜0. 05 0. 05〜0. 08
表1-2常用塑料的流动性与溢料间隙
流动性等级
塑料类型
好
聚酰胺、聚乙烯、聚丙烯、聚苯乙烯、醋酸纤维素
中等
改性聚苯乙烯、ABS、聚甲醛、聚甲基丙烯酸甲酯
差
聚碳酸酯、硬聚氯乙烯、聚砜、聚苯醚
塑料成型的工艺性能
1.1热塑性塑料成型的工艺性能
塑料成型的工艺性能
1.2成型的工艺性能
➢ 影响热固性塑料收缩率的因素主要有原材料、模具结构、成型方法及成型工艺条件等。塑料中树脂和填料的种 类及含量,会直接影响收缩率的大小。当所用树脂在固化反应中放出的低分子挥发物较多时,收缩率较大;放 出低分子挥发物较少时,收缩率较小。在同类塑料中,填料含量多,收缩率小;填料中无机填料比有机填料所 得的塑件收缩率小,如有机填料(如木粉)的酚醛塑料的收缩率,就比相同数量无机填料(如硅粉)的酚醛塑 料收缩率大。
塑料成型的工艺性能
1.2热固性塑料成型的工艺性能
1.收缩性 同热塑性塑料一样,热固性 塑料也具有因成型加工而引 起的尺寸减小,其收缩率计 算方法与热塑性塑料相同。 产生收缩的主要原因有以下 几种。 1)热收缩 这是因热胀冷缩而引起的尺 寸变化。由于塑料线胀系数 比钢材大几倍甚至十几倍, 制件从成型加工温度冷却到 室温时,就会产生远大于模 具尺寸收缩量的收缩。它是 成型收缩中主要的收缩因素 之一。
热固性塑料的注射工艺.
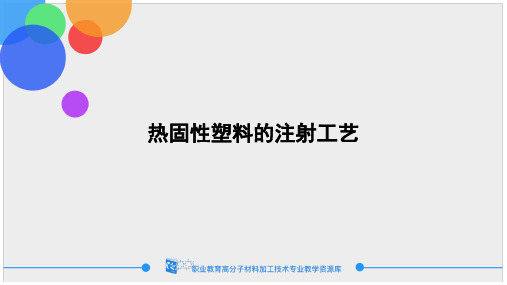
为便于操作,塑料在料筒温度下保持流动态的时间应较 长,故料筒温度应选取力矩的最小点所对应的时间为较长者的 温度为定,也就是说,料筒温度的选择一般是在能满足塑料熔 触流动的前提下,取其接近于低限的温度,以避免在注射操作 过程中发生因塑料在料筒中的交联程度超过某一范围而使注射 成型难于进行,甚至因固化程度过高而堵死螺杆。
热固性塑料的注射工艺
热固性塑料
热固性塑料的成型是将塑料先经加热逐渐熔融塑化, 同时发生化学反应,在压力和热的继续作用下,充模成型 并交联固化成为制件。热固性塑料的压制成型、传递成型 和注射成型等诸种成型加工方法,其成型原理均属于此。
热固性塑料
注射成型是将塑料从料斗输送到规定温度的料筒 中,使其受热塑化,热量来自加热装置的热传导和 螺杆旋转时塑料与料筒壁、塑料与螺杆之间的磨擦 热以及被螺杆剪切和搅拌时内部的磨擦热。
热固性塑料
当温度过低时,塑料可能尚未完全接触,当然也就不 具有注射所必须的流动性,塑料受热熔融后,随着温度的 升高或受热时间的延长,塑料粘度将明显地降低,粘度降 至某一最低点后塑料将随着温度的继续升高或加热时间的 继续延长而使交联反应增大,故粘度又将明显地增高,这 时予塑力越过最小点而上升。
热固性塑料
热固性塑料
二)螺杆转速及背压 螺杆转速是控制物料温度的一个参数。转速增大,塑 料受到的剪切作用越大,摩擦生成的热量增大。对于固化 速度较快的塑料品种可取低的转速。螺杆直径增大,摩擦 生成热也会增大,因此,随着直径增大,相应转速也要降 低。
酚醛塑料粉,当螺杆直径为40~60mm左右时,转速应 为30~80转/分。当注射玻纤增强酚醛塑料时,处于减少 对玻纤的磨损,所以用30~40转/分为宜。
热固性塑料
塑件的结构工艺性
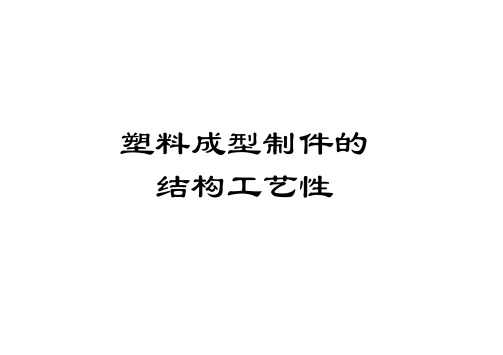
塑料成型制件的结构工艺性l塑料制件的设计是在满足使用要求的前提下,根据选用塑料的类型及其成型加工特点,确定相应而合理的成型工艺,并根据该成型工艺的特性而设计出相适应的塑料结构件。
l由于塑料有其特殊的物理机械性能,因此设计塑件时必须充分发挥其性能上的优点,避免或补偿其缺点,在满足使用要求的前提下,塑件形状应尽可能地做到简化模具结构,符合成型工艺特点。
l对于模具设计者来说,在考虑塑件的结构及有关使用要求时,还必须与成型该塑件的成型模具的相应结构结合起来考虑,既要使塑料制件能按使用要求加工出来,保证制件的质量,而又要使模具结构合理、经济。
在塑件结构工艺性设计时,应考虑以下几方面的因素:(1)塑料的各项性能特点;(2)在保证各项使用性能的前提下,塑件结构形状力求简单,且有利于充模流动、排气、补缩和高效冷却硬化(热塑性塑料制件)或快速受热固化(热固性塑料制件);(3)模具的总体结构应使模具零件易于制造,特别是抽芯和脱模机构。
一、塑料制件的选材二、塑料制件的尺寸和精度三、塑料制件的表面质量四、塑料制件的结构设计表面粗糙度表观质量形状、壁厚、斜度、加强筋、支撑面、圆角、孔、螺纹、齿轮、嵌件、铰链、标记、符号和文字等一、塑料制件的选材塑料制品的选材应考虑如下几个方面,以判断其是否能够满足使用要求。
1)塑料的力学性能,如强度、刚性、韧性、弹性、弯曲性能、冲击性能以及对应力的敏感性。
2)塑料的物理性能,如对环境温度变化的适应性、光学特性、绝热或电气绝缘的程度、精加工和外观的完满程度等。
3)塑料的化学性能,如对接触物(水、溶剂、油、药品)的耐性、卫生程度以及使用上的安全性等。
4)必要的精度,如收缩率的大小以及各向收缩率的差异。
5)成型工艺性,如塑料的流动性、结晶性、热敏性等。
对于塑料材料的这些要求往往是通过塑料的特性表进行选择和比较的。
下表列出常用塑料的特性,以供参考。
二、塑料制件的尺寸和精度1. 塑件的尺寸–总体尺寸主要取决于塑料品种的流动性Ø在一定的设备和工艺条件下,流动性好的塑料可以成型较大尺寸的塑件;反之,成型出的塑件尺寸较小。
热固性塑料的注射成型.

6.7.4 双组分结构发泡注射成型 (夹心注射成型)
产生的背景: 对厚壁(大于5mm)刚性较高的注射件需求量增加。 传统的注射制品,因收缩率大,制品表面易出现塌 坑,影响外观与平整度, 采用高压结构发泡注射能解决上面的问题。
但模具结构复杂,费用昂贵。
34
B A
35
适合于双组分发泡制品的塑料有: HDPE、LDPE、PP、PS、ABS、PMMA、EVA、ASA、 SAN、PA及PC等。 增强塑料也可生产结构泡沫制品,常用填料有: 玻璃纤维、玻璃珠、瓷珠、重晶石和纤维填料等。
8
2.1热固性塑料在料筒内的塑化
料筒的温度必须严格控制,要求温度的均一性尽可 能高, 尽量减少熔体在料筒内的停留时间,也是保证塑化 后熔体质量的重要措施。
9
2.2.热固性塑料熔体在充模过程中的流动
由于喷嘴和模具均处在加热的高温状态,熔体流过 喷嘴和浇道时不会在通道的壁面上形成不动的固体 塑料隔热层,
38
③内层为高强度材料,外层为耐磨材料, 用于成型表面耐磨,具有低的摩擦因数、同时整体 又具有较高强度的制件。
如轴套、齿轮等零件;
④内层为导电、导磁材料,外层为绝缘材料, 可使制品内层具有导电、导磁能力,外层具有绝缘 作用,以防止电气元件壳体发生短路现象。
这些制件大量用于仪表电气、办公设备、计算机壳体等。
16
模具结构必须设置加热装置和温控系统,以利于
物料在模内化学反应的顺利进行 因热固性塑料回收困难,近年来在模具结构上开 始采用热流道模具、无浇口注射成型或细流道成 型等方法。
17
5、注射工艺及成型条件
18
热固性塑料的注 射成型过程包括:
塑化过程、 注射充模过程 固化过程
几种常用塑料的成型工艺介绍
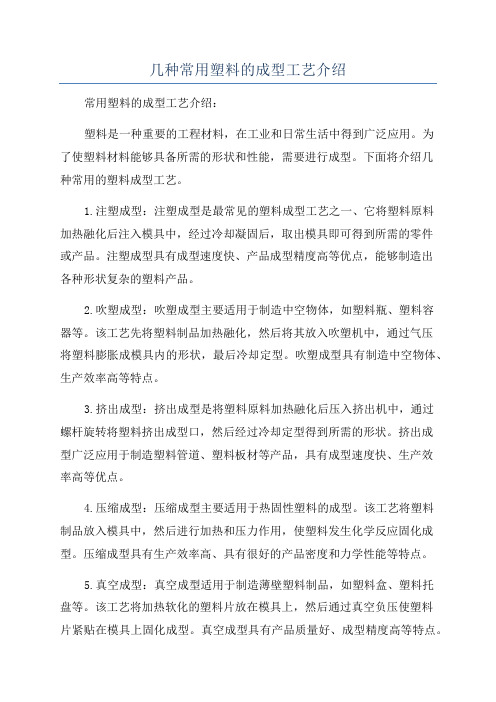
几种常用塑料的成型工艺介绍常用塑料的成型工艺介绍:塑料是一种重要的工程材料,在工业和日常生活中得到广泛应用。
为了使塑料材料能够具备所需的形状和性能,需要进行成型。
下面将介绍几种常用的塑料成型工艺。
1.注塑成型:注塑成型是最常见的塑料成型工艺之一、它将塑料原料加热融化后注入模具中,经过冷却凝固后,取出模具即可得到所需的零件或产品。
注塑成型具有成型速度快、产品成型精度高等优点,能够制造出各种形状复杂的塑料产品。
2.吹塑成型:吹塑成型主要适用于制造中空物体,如塑料瓶、塑料容器等。
该工艺先将塑料制品加热融化,然后将其放入吹塑机中,通过气压将塑料膨胀成模具内的形状,最后冷却定型。
吹塑成型具有制造中空物体、生产效率高等特点。
3.挤出成型:挤出成型是将塑料原料加热融化后压入挤出机中,通过螺杆旋转将塑料挤出成型口,然后经过冷却定型得到所需的形状。
挤出成型广泛应用于制造塑料管道、塑料板材等产品,具有成型速度快、生产效率高等优点。
4.压缩成型:压缩成型主要适用于热固性塑料的成型。
该工艺将塑料制品放入模具中,然后进行加热和压力作用,使塑料发生化学反应固化成型。
压缩成型具有生产效率高、具有很好的产品密度和力学性能等特点。
5.真空成型:真空成型适用于制造薄壁塑料制品,如塑料盒、塑料托盘等。
该工艺将加热软化的塑料片放在模具上,然后通过真空负压使塑料片紧贴在模具上固化成型。
真空成型具有产品质量好、成型精度高等特点。
6.3D打印成型:3D打印成型是近年来快速发展的塑料成型工艺之一、它通过从计算机模型中将物体分解为薄层,然后逐层累积加工,最终形成所需的塑料产品。
3D打印成型具有高度灵活性和个性化定制能力,适用于制造小批量、复杂结构的塑料产品。
以上是几种常用的塑料成型工艺的介绍。
不同的工艺适用于不同的塑料材料和产品形状需求,可以根据具体需求选择合适的成型工艺。
- 1、下载文档前请自行甄别文档内容的完整性,平台不提供额外的编辑、内容补充、找答案等附加服务。
- 2、"仅部分预览"的文档,不可在线预览部分如存在完整性等问题,可反馈申请退款(可完整预览的文档不适用该条件!)。
- 3、如文档侵犯您的权益,请联系客服反馈,我们会尽快为您处理(人工客服工作时间:9:00-18:30)。
热固性产品结构工艺性
1.1、概论
热固性成形材在尺寸安定性、表面硬度、抗蠕变、耐热力、绝缘性及抗化学性上皆有极佳的物性。
有些甚至具有成形后之零收缩率,特别适用于需要极小公差之塑品。
以下先对各种热固性材料做个简介:
1、酚醛树脂
使用于电线装置、汽车零组件(传动、点火、真空助煞板)、电气开关齿轮、马达启动器、洗衣机、电冰箱、烤面包机、炒锅把手、通信器材及计算机等。
2、尿素
用于电线、照相装置、家庭用电路断路器及色浆之应用等。
3、三聚氰胺
用于碗盘器皿、电器组件及对光稳定的色浆应用。
4、三聚氰胺-酚醛树脂
特别适于需要极佳电气性质及抗电弧性上之应用,如齿轮、马达启动器开关及须用对光稳定性之器具。
5、醇酸树脂
适用于在高温时需要高绝缘性及介电强度之应用,亦可用于汽车分电盘盖、转子、开关器外壳、断路器及色浆。
6、酸二丙烯酯(DAP)
此材料在长时间高温及高湿度下,仍保有极佳的电气性质,可应用于连接器及通信组装器材。
7、聚脂类
可以粒状、团状或板状成形各种电气、建筑、运输及医药等产品。
产品之小可从1英寸到几百英寸。
以上所述之各种热固性成形材可以多种成形方法制成产品如下所列:
①、浸湿加工:补强玻纤遍布在成形模上,倒入液态树脂混合之,再予以加压加热成形之。
②、团状成形材(BMC):混合了热固性材料、填充剂及补强玻纤,常先以押出法制成圆木状或长条状以利后续之压缩成形、树脂转换成形(须要精确之塑品厚度时)或射出成形。
③、板状成形材(SMC):大多为不饱和聚脂与玻纤混合成为糊状于两PE膜中间,经输送带上之滚轮压挤成为片状,再做后续之加工成形,特别适用于大型品之制造。
④、热塑性玻纤补强射出成形:其加工法为与射出成形类似,一般之玻纤含量为20%至40%。
嵌件可,但最好避免可可可
浮凸物可可可可
筋骨最好避免可可可
内凹符号可可可不可
凸起符号可可可可
完成表面数两两两两
塑料名称成形特性
酚醛树脂成形性较好,适用于压塑成形,部分适用于挤塑成形,个别用于注射成形。
含水分,挥发物,应预热,排气,不预热者应提高模温及成形压力并注意排气;模温对流动性影响较大,一般超过160度时流动性迅速下降;收缩
及方向性一般比氨基塑料大;硬化速度一般必氨基慢,硬化时放出热量大,厚避大型塑件内部温度易过高,故易
发生硬化不均及过热。
氨基塑料常用于压塑,挤塑成形,硬化速度快,尤其如尿甲醛料等不宜挤塑大型塑件,挤塑时收缩大;含水份及挥发物多,易吸潮而结块,使用时要预热,并防止再吸湿,但过于干燥则流动性下降。
成形时有分解物及水分有酸性,
模具应镀洛防止腐蚀,必须注意排气;性脆,嵌件周围易应力集中,尺寸稳定性差;成形温度对塑件影响较大,
温度过高易发生分解,变色,气泡,开裂,变形,色泽不均,过低流动性差,欠压,不光泽,故应严格控制,
一般大型,形状简单塑件取低,小件复杂取高。
流动性好,硬化速度快,因此预热及成形温度要适当,装料,
合模及加压速度要快。
储存期长,储存温度高将引起流动性迅速下降。
料细,比容大,料中充气多。
用预压锭
成形大塑件时易发生波纹及流痕,因此一般不采用。
有机硅塑料流动性好,硬化速度慢,适用压塑成形,要较高温度压制;压塑成性后要高温固化处理。
硅酮塑料主要用于低压挤塑成形,封装电子组件等一般成形
毋论所用之热固性材料为何,其设计有一些通则,产品设计者可以好好利用,使成品更好,更具经济效益。
1、分模线
成形无溢料及使可见的分模线减到最低是产品生产的要求,所以尽可能使分模线位于产品不显眼之处及避免轮廓线或层次状的分模线发生是制造商的目的。
如望远镜依次嵌叠之断面模具不仅会增加模具成本、维修困难且提高了表面之加工费用。
图1所示,为分模线好坏设计之比较。
不佳佳
图1 分模线的设计
如果分模线必须位于产品之侧壁的话,没有一点小小的错合0.25mm~0.4mm,几乎不可能建成此样的模具,如图2所示,或者可能的话加上一0.25mm珠缘饰以解决此问题,如图3。
不佳佳
图2 在分模线,错合之设计
不佳佳
图3分模线之珠缘饰设计
为了使产品表面加工容易及从模穴中拿出塑品时不伤及模面,可在分模线处设计0.4~0.8mm之半径弧,如图4。
图4 分模线之半径弧设计
垂直之装饰或是凹槽之设计须于分模线2~2.4mm前停止,以使溢料能容易清移,如图5所示。
不佳佳
图5 凹槽之设计
2、凹陷(槽)
为了使设计无凹陷,外部的凹槽成形(如图6),可以利用液压式的边圆筒或活动的凸轮来控制模具断面的分合。
这些方法成本较高且模具内之模穴数亦有限制,另外亦须考虑到于分离断面上,所造成之溢料清除问题。
图6 外部凹槽之设计
内凹槽之成形(如图7),则需要可移动的模块或液压式圆筒。
在某些情况下,内凹槽无法成形。
这时就须要机械加工来帮助了,当然,所增加之模具维修费用及表面加工费用自是相当可观。
图7 内凹槽之设计
3、陡边角
为了塑品之安全及美观,其四周常有圆弧之设计,而正确的使用半径对产品影响极大。
不管是内陡边角或外陡边角,其设计通则为半径0.8~1.6mm,太小的话如0.25mm之半径,很容易损坏陡边角。
较大之半径设计则可帮助塑料流动,防止应力集中、增加产品强度与外观及减少模具维修之费用。
有一点要注意的是尽量勿在合模线的地方设陡边角。
4、横截面区
避免横截面区太薄,因为会造成流动困难、容易包气及残余应力使得产品翘曲、收缩。
然而,横截面区若是太厚,则熟化有困难,解决之道是将此区予以铸空(图8)。
总之,其设计原则为使横截面区减到最小,而不减少其所需要的结构强度。
图8 横截面区之设计
5、锥度或倾斜角
塑品之内壁及外壁需要锥度或倾斜角,对普通之浅深度塑品,边壁上之锥度为0.25°较好。
对于超过152mm之极深度塑品,则锥度为0.025㎜/㎜较好。
若为玻纤填充,低收缩之材料成形,则零锥度即可。
当有深的屏障或浮凸物时,则3°~5°之锥度需给与之。
6、肋骨
结构肋骨通常加于大的平底、背部或平板以增加强度。
肋骨之设计依所用之热固材料不同而不同。
对玻纤补强聚脂材料而言,其厚度或深度并没有特别之限制,典型的浅肋骨可为2.3mm厚及自由的倾斜角,超过25.4㎜之深肋骨则为3.2㎜厚及自由的倾斜角。
对其它热固性材料,成形后收缩及翘曲常常是个问题,加上肋骨可增加强度,减少翘曲及增加成形流动性,尤其是对独立的浮凸物或厚断面部份,其功能犹如流道。
一般肋骨之高度与宽度设计通则为:肋骨底部之宽度需小于所附物之壁厚;肋骨之高度若超过所附厚度之3倍会造成形上之困难,在此种情况下,最好是用两个以上较短之肋骨且两肋骨底部之中心距需2倍于肋骨之底部宽,如图9所示。
图9 筋骨之设计好坏比较
7、浮凸物
浮凸物穿过螺栓或衬垫用以补强孔洞或组装。
肋骨之设计原则亦适用于浮凸物,其高度不可超过其直径两倍以上。
位于边壁的倾斜角及浮凸物之底部半径皆须够大,如此才容易从模穴中取出且强度足够。
如果增加浮凸物之高度不可避免,则于浮凸物之外直径上,加上3个肋骨以增加其强度。
当浮凸物是被用来做组装时,其高度需非常精确以使组装达水平,可用机械研磨之方法以助之。
为了避免额外的加工来达到完美的连接,用3个浮凸物来组合之如图10所示。
如果塑品须能平立或组立在平坦之表面上,则在每一角边上需有0.4mm高度之平凸起面(图11),浮凸物之肉厚断面至少须等于小孔洞之直径大小。
肉厚(㎜) 直径(㎜)
1.6 1.6
6.35 3.2
12.7 4.8 8、孔洞或开口
压制方向
h2
d
2
h
1
d1d
h
塑料品种
最小孔径竖向压塑横向压塑挤塑和注塑
一般技术上的可能不通孔通孔不通孔通孔不通孔通孔
断裂。
所以对半穿孔而言,其深度不可超过插销直径之2.5倍(图12)。
若是全穿孔,则需用粗细插销,即其中一枝较另一枝为粗,以防两插销之错合(图13)。
须注意为了加强插销的力量,在孔穿与模面之接触点,要有足够大之半径及加大的孔眼边如图14所示。
图12 半穿孔之正确设计图13 全穿孔之正确设计
图14 足够大之半径或孔眼边
由于塑料在穿孔处常会造成缝合线,所以孔洞不可离侧壁太近及两孔洞间之距离不可太小,其限制规格可参考表2。
9
螺纹孔洞之制法,可先予模具内置入或塑品成形后趁热插入。
一般所用之螺纹其精细度为最少每25.4㎜32个螺纹,直径大于6.35mm,且深度为其直径之2到2.5倍。
要注意的是侧壁厚度需足够,以防止螺纹丝插入后造成塑品破裂。
平坦之表面及直线的侧壁是最难成形控制的。
翘曲是影响精确尺寸控制的最大因素,尤其是当肉厚断面有层次的改变时,翘曲通常正比于材料收缩之总和。
一般对成品之直壁及投影表面,其尺寸公差之要求为0.08~0.1㎜/㎜,如图15所示。
图15 平坦表面所需之尺寸公差。