连续铸轧
连续铸轧技术
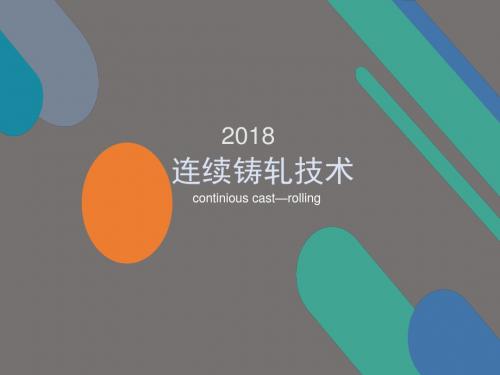
水冷速度 铸轧速度 辊套厚度
辊套材料
例
(3) 连续铸轧的设计参数
① 铸轧角
两辊铸轧中心连线和供料嘴顶 端到铸轧辊中心连线所形成的角 度,即为铸轧角,如右图所示, α一般在 5º~ 10º之间。h为铸轧 区的高度。
O h
R
铸轧角示意图
② 辊径的选择
铸轧辊径一般采取大些尺寸 为好,这样铸轧冷却得好,辊 径越大,在铸轧角一定的情况 下,铸轧区加长,有利于热交 换,辊径一般在 400~550mm 之 间
① 铸轧温度
一般比所铸轧的金属熔点高60~80℃。如果铸轧温度过低,金 属溶液冷凝在浇注系统中,如果过高,则不易成形,或板坯质 量变差。
② 铸轧速度
铸轧速度必须是无级调速。铸轧过程中冷却速度的调整主要是 靠铸轧速度,同时,水冷强度也起着配合作用。
③ 冷却强度
在铸轧过程中,单位时间,单位面积 影响冷却 速度的因 上导出热量的大小即为冷却强度。 素 液体金属 铸轧 向外导热 冷却强度 在铸轧时 速度慢 时间充分 增加 停留时间长
2018
连续铸轧技术
continious cast—rolling
连续铸轧:金属熔体在连续铸造凝固的同时进行轧 制变形的过程。 工艺特点:结晶器为两个带水冷系统的旋转铸轧辊 ,熔体在其辊缝间完成凝固和热轧两个过程,而且 是在很短时间内(2~3s)完成的。 与连铸连轧的区别:连铸连轧实质上是将薄锭坯铸 造与热轧连续进行,即金属熔体在连铸机结晶器中 凝固成厚度约 50~90mm 的坯后,再在后续的连轧 机上连续轧成板材,其铸造和轧制是两道独立的工 序。
③ 铸轧辊套的选择
a) 有足够的导热性能; b) 有较高的力学性能; c) 耐高温; d) 耐热交变应力的疲劳作用
连续铸造及其与轧制的衔接工艺

连续铸造及其与轧制的衔接工艺1. 引言连续铸造是一种现代化的铸造工艺,它与传统的间歇铸造相比具有更高的生产效率和质量控制能力。
随着工业技术的发展,连续铸造在轧制过程中的应用也越来越广泛。
本文将介绍连续铸造的基本原理和与轧制的衔接工艺。
2. 连续铸造的原理连续铸造是通过在连铸机上连续铸造金属坯料,将熔融金属倒入预先制备好的连续浇注铸模中,经过一系列冷却和凝固过程,最终形成所需的连续坯料。
连续铸造具有以下几个主要特点:•产量高:连续铸造可以实现连续、自动化生产,生产效率高于传统的间歇铸造。
•质量可控:由于冷却和凝固过程的控制,连续铸造可以获得均匀的结晶组织,从而提高材料的力学性能和物理性能。
•节省能源:连续铸造的过程中可以充分利用余热和余能,提高能源利用效率。
3. 轧制与连续铸造的衔接工艺在连续铸造生产的金属坯料经过冷却和凝固后,需要进行进一步的加工,其中轧制是最常用的一种加工方式。
轧制是利用辊轧机将金属坯料进行塑性变形,最终得到所需的板材、型材或管材。
轧制与连续铸造的衔接工艺主要包括以下几个步骤:3.1 金属坯料的预热在连续铸造后的金属坯料中,由于冷却和凝固过程的影响,金属坯料温度较低,不利于轧制操作。
因此,需要对金属坯料进行预热处理,将其温度提高到适合轧制的范围。
3.2 理化性能测试在进行轧制前,需要对金属坯料进行理化性能测试,以确保其符合轧制要求。
测试项目包括金属材料的化学成分、力学性能和物理性能等。
3.3 轧制机的调试轧制机是进行轧制操作的关键设备,调试工作包括辊轧机的调整和辊轧力的设定,以保证轧制过程中金属坯料的塑性变形符合要求。
3.4 轧制过程的控制轧制过程中,需要对金属坯料的温度、厚度、宽度等进行实时监控和控制。
一般采用自动控制系统,通过传感器和控制算法,对轧制参数进行调整,以实现所需的轧制结果。
3.5 轧制后的检验和修整轧制后的金属板材、型材或管材需要进行质量检验,包括外观质量、尺寸精度和力学性能等。
铝合金连续铸轧和连铸连轧技术
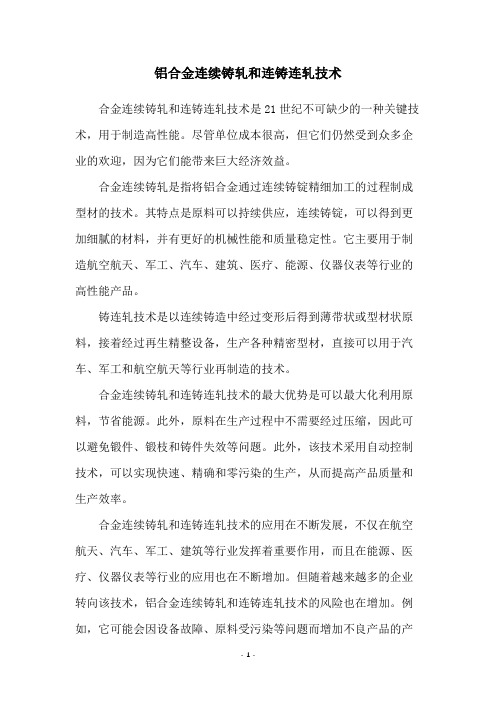
铝合金连续铸轧和连铸连轧技术合金连续铸轧和连铸连轧技术是21世纪不可缺少的一种关键技术,用于制造高性能。
尽管单位成本很高,但它们仍然受到众多企业的欢迎,因为它们能带来巨大经济效益。
合金连续铸轧是指将铝合金通过连续铸锭精细加工的过程制成型材的技术。
其特点是原料可以持续供应,连续铸锭,可以得到更加细腻的材料,并有更好的机械性能和质量稳定性。
它主要用于制造航空航天、军工、汽车、建筑、医疗、能源、仪器仪表等行业的高性能产品。
铸连轧技术是以连续铸造中经过变形后得到薄带状或型材状原料,接着经过再生精整设备,生产各种精密型材,直接可以用于汽车、军工和航空航天等行业再制造的技术。
合金连续铸轧和连铸连轧技术的最大优势是可以最大化利用原料,节省能源。
此外,原料在生产过程中不需要经过压缩,因此可以避免锻件、锻枝和铸件失效等问题。
此外,该技术采用自动控制技术,可以实现快速、精确和零污染的生产,从而提高产品质量和生产效率。
合金连续铸轧和连铸连轧技术的应用在不断发展,不仅在航空航天、汽车、军工、建筑等行业发挥着重要作用,而且在能源、医疗、仪器仪表等行业的应用也在不断增加。
但随着越来越多的企业转向该技术,铝合金连续铸轧和连铸连轧技术的风险也在增加。
例如,它可能会因设备故障、原料受污染等问题而增加不良产品的产生率。
同时,由于该技术具有高成本、复杂性和受限性,因此需要有较高的技术和财务投资。
为了充分发挥铝合金连续铸轧和连铸连轧技术的优势,提高其应用率,应当在技术、设备管理和经济管理三个方面采取有效的措施。
首先,应完善技术体系,加强技术改造,进一步提高该技术的精确度和效率;其次,应完善设备管理,加强设备的维护和检修,降低故障率;最后,应综合考虑投资成本、产品质量、技术进步等因素,实施合理的财务管理。
上所述,铝合金连续铸轧和连铸连轧技术是21世纪不可缺少的一项关键技术,其应用范围越来越广泛,它在众多行业中发挥着重要的作用。
为了充分利用这项技术的优势,并降低使用的风险,应当采取有效措施进行技术、设备管理和财务管理。
第四章连续铸轧过程
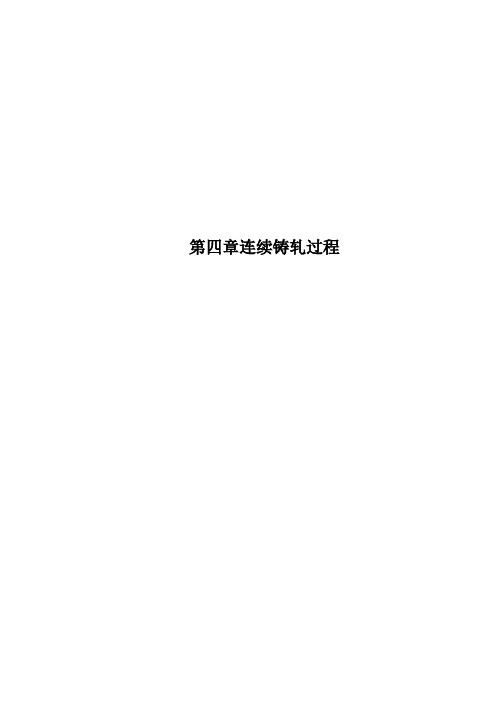
第四章连续铸轧过程第四章连续铸轧技术4.1 连续铸轧技术概论直接将金属熔体“轧制”成半成品带坯或成品带材的工艺称为连续铸轧。
这种工艺的显著特点是结晶器为两个带水冷系统的旋转铸轧辊,熔体在辊缝间完成凝固和热轧两个过程,而且在很短的时间内完成。
连续铸轧具有投资省、成本低、流程短等优点,目前,连续铸轧工艺已广泛的应用于铝合金等有色金属的生产中,在钢铁生产中的应用还处于试生产阶段。
连续铸轧技术不同于连铸连轧,后者实际上将薄锭坯铸造与热轧连续进行,即金属熔体在连铸机结晶器中凝固成厚约50-90mm 的坯后,再在后续的双机架(单机架、三机架)温连轧机上连续温轧成带坯或成品板带材,铸造和温轧是两道独立的工序。
而连续铸轧技术使连铸和轧制两个原先独立的工艺工程更加紧密地衔接在一起,已不再是一个纯粹的冶金和凝固过程,而是在连铸、凝固的同时伴随着轧制过程。
原来的全凝固压力加工规律和塑性变形规律也发生了相应的变化。
(一)铝带铸轧1951年,美国亨特一道格拉斯(Hunter—Douglas)公司首次铸轧成了铝带坯,制成了双辊式连续铸轧机。
随后,法国彼西涅(Pechiney)公司研制的3C水平式双辊铸轧机也获得成功,从那以后,铝带坯双辊连续铸轧技术和设备得到了迅速的发展。
截止到2007年底,亨特工程公司及意大利法塔亨特公司(FATA Hunter)的铸轧机已达153台,法国原普基工程公司(Pechiney Engineering)和现在的诺威力昔基工程公司(Novelis PAE)生产的3C式铸轧机,全球保有182台。
国外还有一些由其他公司和企业自制的双辊式铸轧机,主要是亨特式或3C式的变型,但产量不多,这一类铸轧机国外保有的总数也只有50多台。
我国铝带坯连续铸轧技术研究开发工作始于20世纪60年代。
1964年初进行了双辊下注式铝带坯连续铸轧模拟实验,并于同年铸轧出厚8mm,宽250mm 和400mm的铝板,1965年铸轧出宽700mm的铝带坯,1971年由东北轻合金加工厂研制成我国第一台8001Tim水平式下注式双辊铸轧机。
铝合金连续铸轧和连铸连轧技术

铝合金连续铸轧和连铸连轧技术近几年,铝合金连续铸轧和连铸连轧技术得到了广泛的关注和应用,在航空、交通、电子和生产等领域发挥着重要作用,并取得了可喜的成就。
本文介绍了铝合金连续铸轧和连铸连轧技术,总结其优点和应用领域,并展望未来发展。
首先,让我们先来介绍连续铸轧技术。
连续铸轧是把铸态的毛坯在双辊铸轧机上连续铸轧的一种特殊的铸轧技术。
它不仅可以在一条生产线上完成整体模块的加工,还可以连续涂层、连续切削、连续横切,从而实现大批量生产,提高生产效率。
此外,它还可以提高材料的性能,降低成本,但是操作起来比较复杂,容易出错。
连铸连轧技术,也称为热轧技术,是将铁水经连续送料炉溅射、蒸发冷凝池或冷却池自动加工成一定规范形状的毛坯精加工成所需规格和性能的钢材的一种特殊的技术。
它有很多优点:操作简单,精度高,材料质量好,成品率高,生产效率高,投资少,特别适用于量大、精度高的产品的生产,有较好的经济效益。
铝合金连续铸轧和连铸连轧技术可用于制造高性能的铝空心结构件、铝芯轴以及汽车零部件等铝合金结构件。
它具有节能、环保、能耗低、操作方便等优势,应用于航空航天、汽车、电子电器、医疗器械等领域可以节约资源,提高工作效率。
未来,随着技术的发展,铝合金连续铸轧和连铸连轧技术将更加成熟,获得更多的关注和应用。
同时,随着用户消费趋向的变化,针对不同类型的产品,研究者也会发展出更多新型的生产工艺,以期在节能、环保、成本等方面取得更好的效果。
综上所述,铝合金连续铸轧和连铸连轧技术是近几年中取得可喜成绩的一种先进技术,它具有节能、环保、成本低等优势,将带给我们更多的经济和社会效益。
未来,铝合金连续铸轧和连铸连轧技术将朝更高层次发展,为人类社会做出更多的贡献。
铸轧是连续性生产
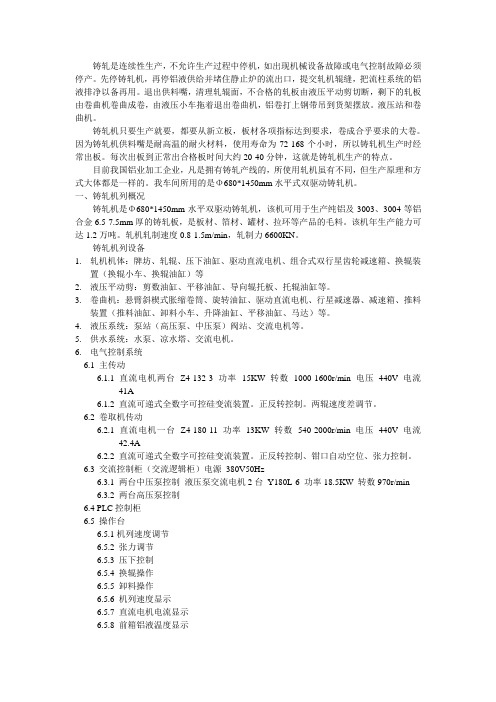
铸轧是连续性生产,不允许生产过程中停机,如出现机械设备故障或电气控制故障必须停产。
先停铸轧机,再停铝液供给并堵住静止炉的流出口,提交轧机辊缝,把流柱系统的铝液排净以备再用。
退出供料嘴,清理轧辊面,不合格的轧板由液压平动剪切断,剩下的轧板由卷曲机卷曲成卷,由液压小车拖着退出卷曲机,铝卷打上钢带吊到货架摆放。
液压站和卷曲机。
铸轧机只要生产就要,都要从新立板,板材各项指标达到要求,卷成合乎要求的大卷。
因为铸轧机供料嘴是耐高温的耐火材料,使用寿命为72-168个小时,所以铸轧机生产时经常出板。
每次出板到正常出合格板时间大约20-40分钟,这就是铸轧机生产的特点。
目前我国铝业加工企业,凡是拥有铸轧产线的,所使用轧机虽有不同,但生产原理和方式大体都是一样的。
我车间所用的是Φ680*1450mm水平式双驱动铸轧机。
一、铸轧机列概况铸轧机是Φ680*1450mm水平双驱动铸轧机,该机可用于生产纯铝及3003、3004等铝合金6.5-7.5mm厚的铸轧板,是板材、箔材、罐材、拉环等产品的毛料。
该机年生产能力可达1.2万吨。
轧机轧制速度0.8-1.5m/min,轧制力6600KN。
铸轧机列设备1.轧机机体:牌坊、轧辊、压下油缸、驱动直流电机、组合式双行星齿轮减速箱、换辊装置(换辊小车、换辊油缸)等2.液压平动剪:剪数油缸、平移油缸、导向辊托板、托辊油缸等。
3.卷曲机:悬臂斜楔式胀缩卷筒、旋转油缸、驱动直流电机、行星减速器、减速箱、推料装置(推料油缸、卸料小车、升降油缸、平移油缸、马达)等。
4.液压系统:泵站(高压泵、中压泵)阀站、交流电机等。
5.供水系统:水泵、凉水塔、交流电机。
6.电气控制系统6.1 主传动6.1.1 直流电机两台Z4-132-3 功率15KW 转数1000-1600r/min 电压440V 电流41A6.1.2 直流可递式全数字可控硅变流装置。
正反转控制。
两辊速度差调节。
6.2 卷取机传动6.2.1 直流电机一台Z4-180-11 功率13KW 转数540-2000r/min 电压440V 电流42.4A6.2.2 直流可递式全数字可控硅变流装置。
连续铸轧
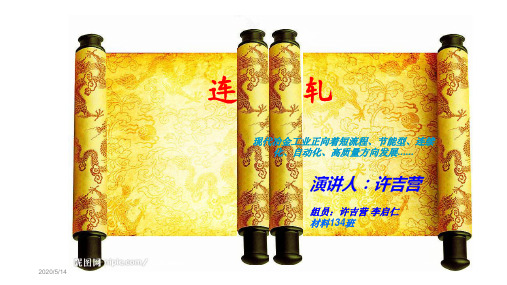
横波
在板面出现横向的微波纹,严重的可用手摸出,甚至有轻微的 层状出现。 解决措施: (1) 提高铸轧速度,使铸轧区温度高一些,特别是提高铸轧辊和 供料嘴端接触处的温度,使液穴外围的氧化膜拉断,缩短和铸轧 辊接触时间,相对提高该处温度; (2) 前箱金属液面太高,使液体金属静压力过大,液穴向辊间隙 伸展,造成金属未被轧制时降温很多。流动性不好,故出现横波 或轻微的层状。降低金属液面高度会立刻奏效; (3) 提高金属铸轧温度,提高金属的流动性.也是有效措施。
正常铸轧时金属液面高度示意图
上图表示正常铸轧时金属液面高度示意图,其中h 表示铸轧区高度。液面高度经验公式如下:
H=y+h1+h2
经验得知: h1为铸轧区 高度的1/3, 附加高度h2 为5—10mm
式中 H——正常铸轧时金属液面高度; y——供料嘴到底浇道高度; h1——金属液穴高度; h2——附加高度。
五.铸轧的热平衡条件
• 铸轧温度 • 铸轧速度 • 冷却速度
六.铸轧缺陷及其防止
• • • • • • •
条痕 孔洞 横波 白条 黑皮 板面不平 边部不齐
条痕
在铸轧板面的固定位置出现未被轧辊轧上的条痕,有时呈不连续状态。 这是由于在该位置的供料嘴被氧化膜堵塞,使该处不能流出金属,只靠 接近堵塞处两侧供给液体金属,不等到这部分液体金属补充到板面缺少 金属的地方,就被轧辊轧上,未被充填金属的板面即出现发亮的条痕。 供料嘴被严重堵塞时,由于供液体金属不足,会出现一条较宽的未被轧 着的铸态条带。 解决措施:
四、铸轧的基本条件
1、浇注系统预热温度
铸轧浇注系统包括控制金属液面 高度的前箱、横浇道、供料嘴底座和 供料嘴四部分。此部分必须具备良好 的保温性能,保证铸轧的正常进行。 经整体装配并调试好后,入炉进行预 热。预热温度为300℃左右,保温4h 以上。 如果预热不好,液体金属失热过 多,不能进行铸轧,即使勉强开了头, 也会因为供料嘴内有凝块而中断铸轧。
《连续铸造及其与轧制的衔接工艺》课件

1)连铸坯内部绝热技术和烧嘴加热技术相结合。 2)火焰切割机附近采用板坯边部加热装置。可采用电磁感应 加热或煤气烧嘴加热。
连续铸造及其与轧制的衔接工艺
1.3 连铸生产工艺 注意防止各种缺陷的产生,严格控制浇注温度,化学成分要求严格。控制
Mn/Si和Mn/S。 拉坯速度-重要的工艺参数。 根据钢种不同,控制二次冷却区的冷却强度,控制各种缺陷的产生。
连续铸造及其与轧制的衔接工艺
2连铸与轧制的衔接工艺 2.1钢坯断面规格及产量的匹配衔接
连续铸造及其与轧制的衔接工艺
1.1连续机类型 按铸坯断面形状分:厚板坯、薄板坯、大方坯、小方坯、
圆坯、异型坯、椭圆坯连铸机。 按铸坯运行轨迹分:立式、立弯式、垂直-多点弯曲式、
垂直-弧形、多半径弧形(椭圆形)、水平式、旋转式连 铸机。 1.2连铸机组成 钢水运转装置(钢水包、回转台)、中间包及更换装置、 结晶器及其振动装置、二冷区夹持辊及冷却水系统、拉引 矫直机、切断设备、引锭装置。
《连续铸造及其与轧制的衔 接工艺》
连续铸造及其与轧制的衔接工艺
1连续铸钢技术 将钢水连续注入结晶器,待钢水凝成硬壳后从结晶器出口
连续拉出或送出,经喷水冷却,全部凝固后切成坯料或直送 轧制工序。
(1)钢水在结晶器内得到迅速而均匀的冷却凝固,细晶 区较厚,柱状晶不发达。
- 1、下载文档前请自行甄别文档内容的完整性,平台不提供额外的编辑、内容补充、找答案等附加服务。
- 2、"仅部分预览"的文档,不可在线预览部分如存在完整性等问题,可反馈申请退款(可完整预览的文档不适用该条件!)。
- 3、如文档侵犯您的权益,请联系客服反馈,我们会尽快为您处理(人工客服工作时间:9:00-18:30)。
炉内金属按照铸轧的要 求控制温度。经精炼处 理后的液态金属,通过 流槽进入浇道系统,并 控制液面高度。当液体 金属靠本身压力作用, 从供料嘴顶端溢出,随 即进入一对内部通冷却 水的旋转铸轧辊缝中被 轧制成板。
铸轧板
静置炉
导向辊
铸轧辊 前箱
钎子 流槽
小塞子 供料嘴 横浇道 小塞子
在a-a’点立即冷却形成薄壳、随着 金属的热量不断地被铸轧辊导出, 液体金属不断结晶;随着铸轧辊向 上转动,在a-a’至b-b’范围内进行 着铸轧。在b-b’横截面上金属已经 完全凝固,接着金属便进入了固态 轧制的状态。当金属被轧制至c-c’ 面时,整个铸轧过程即告结束,cc’面的宽度即为铸轧板坯的厚度。 由a-a’面到b-b’面的高度,即为铸 轧区高度。
1981年中国冶金工业部铝加工实验厂制成了 650×1600mm双辊倾斜式铸轧机;
50多年来,铝合金带坯的连续铸轧技术长足进展,到 2000年底,全球约有400台连续铸轧机在运转,产能 3600kt。
常见的缺陷与防止
连续铸轧及其基本条件? 连续铸轧常见的缺陷与防止?
金属液面低,氧化 膜本身受压力较小, 不易破坏,板面质量 较佳。但金属液面过 低时,则板面由于金 属不足而易产生空洞 缺陷。
正常
金属液面高,压力 增加,使氧化膜变薄, 极易破坏。轻者板面 出现氧化黑皮;严重 时,造成铸轧中断。
正常铸轧时金属液面高度示意图
H y h1 h2
经验得知:h1为铸轧区高度的1/3,附加高度h2为5-10mm。
全凝固压力加工规律和塑性变形本构关系也发生了相 应变化,该项技术已经成为一种新的边沿科学。
直接将金属熔体“轧制”成半成品带坯或成品
带材的工艺称为连续铸轧。 这种工艺的显著特点使其结晶器为两个带水冷 却系统的旋转铸轧棍,熔体在辊缝间完成凝固 和热轧两个过程,而且是在很短的时间内。
1. 连续铸轧工艺的基本原理
连续挤压
2.铸轧的基本条件
浇汁系统预热温度
铸轧浇注系统包括控 制金属液面高度的前 箱、横浇道、供料嘴 底座和供料嘴四部分. 作为液体金属流过的 通道,必须具备良好 的保温性能,使液体 金属不过多地散热,保 持铸轧的正常进行。
铸轧板
静置炉
导向辊
铸轧辊 前箱
钎子 流槽
小塞子 供料嘴 横浇道 小塞子
整个浇注系统内,不应有潮气、油膜、氧化渣 以及其他杂物存在。 经整体装配并调试好后,入炉进行预热。预热 温度为300℃左右,保温4h以上。 浇注系统如果预热不好,液体金属失热过多, 不能进行正常铸轧,即使勉强开了头,也会因 供料嘴内由凝块而中断铸轧。因此浇汁系统预 热温度是铸轧的基本工艺参数。
3.3 冷却速度
在铸轧过程中,单位时间、单位面积上导出热量 的大小谓之冷却强度。
冷却强度除和铸轧辊的水冷强度有关外,和铸轧 速度、铸轧区高度以及辊套材料也有很大关系。 铸轧速度慢,就意味着液体金属在铸轧区停留的 时间长、有充分时间向外导热。
4. 铝板连续铸轧
连续铸轧从20世纪50年代以来一直在有色金属、特别是铝 带的生产上得到了广泛的应用; 1951年美国亨特· 道格拉斯(Hunter-Douglas)公司设计 制造成功首台双辊铝带连续制造机;
3.2 铸轧速度
铸轧开始时,为了进一步预热浇铸系统,铸轧速 度要很高,一般为正常铸轧速度的一倍半以上。
随着预热的进行,供料嘴内温度均匀,就要逐渐 增加冷却水量和降低铸轧速度,这个阶段液体金 属不能成形,金属会贴在铸轧辊上成为碎片;铸 轧速度降到一定数值时,板坯开始局部立起,并 不断扩展至整个断面……
连续铸轧
现代冶金工业正想着短流程、节能型、
连续化、自动化、高质量方向发展……
随着连铸技术的进一步发展、出现了连续坯热送热装、
直接轧制技术和薄板坯连铸连轧技术,使连铸和连轧
这两个原先独立存在的工艺过程更加紧密地衔接在一
起,因此连铸已不再是一个纯粹的冶金和凝固过程, 而是在连铸、凝固的同时伴随着轧制过程。
铸轧的基本条件
金属的液面高度
整个浇注系统是一个连通器。前 箱内液面水平高度就决定着供料 嘴出口处液体金属压力的大小。
若液面低,供应金属的压力过小, 则铸轧板面易于产生孔洞; 若液面过高,金属静压力过大,或在铸轧扳面上出现被 冲破的氧化皮,影响板面质量;或使液体金属进入辊隙, 造成铸轧中断。
3. 铸轧的热平衡条件
所谓连续铸轧的热平衡,就是进入整个铸轧系 统的热量要等于从铸轧系统导出的热量。如果 失去这个热平衡,连续铸轧将无法进行,或者 液体金属冷凝在挠注系统中。 影响铸轧热平衡条件的有:铸轧温度、铸轧速 度和冷却速度。
3.1 铸轧温度的 选定,必须充分考虑液体金属从炉内经流槽入前 箱,再进人浇道系统,最后从供料嘴送至铸轧辊. 在整个流样中温度的散失。必须保证为适应铸轧 要求的金属流动性,铸轧温度选得过低,使金届 容易冷凝在浇访系统中:选得过高,则容易不成 形,或板坯质量变差。