材料成型有限元案例分析
有限元模拟分析
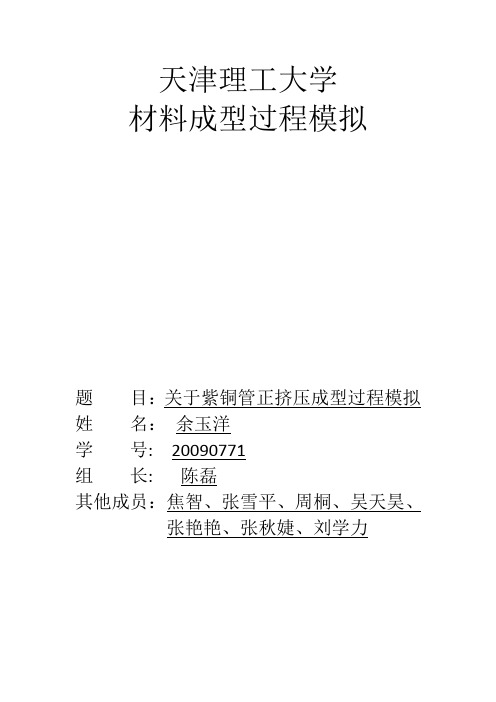
天津理工大学材料成型过程模拟题目:关于紫铜管正挤压成型过程模拟姓名:余玉洋学号: 20090771组长: 陈磊其他成员:焦智、张雪平、周桐、吴天昊、张艳艳、张秋婕、刘学力目录1、题目描述2、题目分析3、解题模拟、思路4、模拟过程5、模拟结果分析6、结论7、参考文献一、题目描述:如图1.1所示为金属紫铜坯料和挤压模具结构示意图,紫铜的应力应变关系如图1.2所示,坯料与模具之间的摩擦系数为0.15。
求挤压过程中坯料内部的应力场变化、应变场变化。
①坯料紫铜的材料参数:弹性模量:MP;泊松比:;密度:;屈服强度:。
②模具材料参数:弹性模量:MP;泊松比:;密度:;屈服强度:。
二、题目分析:三、解题模拟、思路:1、定义工作文件名和工作标题:1.1、定义工作文件名执行Utility Menu-File→Chang Jobname-20090771,单击OK按钮。
1.2、定义工作标题执行Utility Menu-File→Change Tile-yuyuyang20090771,单击OK按钮。
1.3、更改目录执行Utility Menu-File→change the working directory –D/ansys。
2、定义单元类型和材料属性:2.1、设置计算类型ANSYS Main Menu: Preferences →select Structural →OK,如图2.1.图2.12.2、选择单元类型执行ANSYS Main Menu→Preprocessor →Element Type→Add/Edit/Delete →Add →select Solid Brick 8node 185 →OKOptions…→select K3: Plane strain →OK→Close如图2.2所示,选择OK接受单元类型并关闭对话框。
图2.2定义单元类型对话框2.3、定义材料属性⑴、执行Main Menu→Preprocessor →Material Props →Material Models命令,出现Define Material Model Behavior对话框。
CAE成型 dynaform有限元分析

dynaform成型有限元分析——餐盘
学号:_____10921910102___________
姓名:______刘燕波_______________
日期:_______2012.6_______________
一、产品描述
产品图:
长:400mm
宽:250mm
厚度:2mm
凸台高度:20
四周圆角:40mm
各倒角:8mm
功能和作用:此餐盘内盛装筷子、饮料杯、米饭、馒头、菜等食物,作为学校、医院等各机关的公众食堂所用餐具,给食客带来了方便,采用不锈钢材料,容易清洗,可长久使用。
二、工艺分析
产品三维图
凸模三维图
凹模三维图
1、有限元网格模型
2、工艺参数
Tools motion curve
Binder force load curve
3、有限元参数
名称参数
材料DQSK 37
分析步数8
步长0.0007
凸模运动速度2000
网格数目坯料:14327 凸模:7339 压边力50000
三、结果及讨论
1、成型结果展示
2、分析结果
从成型结果可以看出,制件未被拉深成功,分析其原因,本人认为,由于制件比较形状复杂,拉深超过了坯料的变形极限,从而未被拉深出来,可以选用塑性比较好的材料,或者进行多次拉深,且在坯料外缘不起皱的情况下尽量选用比较小的压边力,拉深力在保证制件合格的情况下尽量大,如此改善拉深的一些参数,制件方可成型。
《基于有限元的铝合金管材挤压成形数值模拟》

《基于有限元的铝合金管材挤压成形数值模拟》篇一一、引言随着现代工业的快速发展,铝合金管材因其轻质、高强、耐腐蚀等优点,在汽车、航空、机械制造等领域得到广泛应用。
挤压成形技术是铝合金管材生产过程中的关键环节,其成形质量直接影响到产品的性能和使用寿命。
因此,对铝合金管材挤压成形过程进行数值模拟,不仅可以提高生产效率,还可以优化工艺参数,提高产品质量。
本文将基于有限元法对铝合金管材挤压成形过程进行数值模拟,以期为实际生产提供理论依据。
二、铝合金管材挤压成形原理及特点铝合金管材挤压成形是指将加热后的铝合金坯料通过模具挤压成所需形状和尺寸的管材。
其特点包括:1. 挤压过程中金属流动复杂,需考虑金属的塑性变形、热传导、摩擦等因素;2. 模具设计对产品质量和生产成本具有重要影响;3. 挤压成形过程中需严格控制温度、压力等工艺参数。
三、有限元法在铝合金管材挤压成形中的应用有限元法是一种有效的数值模拟方法,通过将连续体离散成有限个单元,求解各单元的近似解,从而得到整个结构的近似解。
在铝合金管材挤压成形过程中,有限元法可以用于模拟金属的流动、应力分布、温度变化等情况,为实际生产提供指导。
四、铝合金管材挤压成形的数值模拟过程1. 建立几何模型:根据实际生产需求,建立铝合金管材的几何模型;2. 设定材料属性:定义铝合金的材料属性,如密度、弹性模量、屈服强度等;3. 划分网格:将几何模型离散成有限个单元,为后续的数值计算做准备;4. 定义边界条件和载荷:根据实际生产情况,设定模具和坯料的接触条件、摩擦系数等边界条件,以及施加的压力、温度等载荷;5. 求解和后处理:通过有限元软件进行求解,得到金属的流动、应力分布、温度变化等情况,并对结果进行后处理,如绘制云图、曲线等。
五、结果分析与讨论通过对铝合金管材挤压成形的数值模拟,可以得到以下结果:1. 金属流动规律:模拟结果显示,金属在挤压过程中沿着模具流动,并在模具的作用下发生塑性变形;2. 应力分布情况:通过应力云图可以清楚地看到各部分的应力分布情况,为优化模具设计和工艺参数提供依据;3. 温度变化情况:模拟可以反映挤压过程中温度的变化情况,为控制产品质量提供参考;4. 挤压成形质量:通过对比模拟结果和实际生产结果,可以发现模拟结果与实际生产情况基本一致,说明数值模拟可以有效预测铝合金管材的挤压成形质量。
《基于有限元的铝合金管材挤压成形数值模拟》范文

《基于有限元的铝合金管材挤压成形数值模拟》篇一一、引言随着现代工业的快速发展,铝合金管材因其优良的物理性能和机械性能,广泛应用于航空、汽车、建筑等多个领域。
铝合金管材的挤压成形技术作为其重要的制造工艺之一,对产品的质量和性能具有重要影响。
因此,研究铝合金管材挤压成形的数值模拟技术,对于提高生产效率、优化工艺参数以及降低成本具有重要意义。
本文将基于有限元法,对铝合金管材挤压成形过程进行数值模拟,旨在为实际生产提供理论依据和指导。
二、有限元法在铝合金管材挤压成形中的应用有限元法是一种有效的数值计算方法,能够模拟复杂物理过程和材料行为。
在铝合金管材挤压成形过程中,有限元法可以模拟金属的流动、应力分布、温度变化等关键因素,为优化工艺参数和产品设计提供有力支持。
首先,通过建立铝合金管材挤压成形的有限元模型,可以实现对金属流动的精确模拟。
模型中应考虑金属的塑性变形、热传导、相变等物理过程,以及材料在不同条件下的力学性能。
此外,还需要对模型进行网格划分、边界条件设定等操作,以保证模拟结果的准确性。
其次,通过对有限元模型进行求解,可以得到挤压过程中各阶段的应力分布和温度变化情况。
这些数据可以帮助我们了解金属的流动规律和挤压过程中的潜在问题,为优化工艺参数提供依据。
三、铝合金管材挤压成形的数值模拟过程铝合金管材挤压成形的数值模拟过程主要包括前处理、求解和后处理三个阶段。
前处理阶段主要是建立有限元模型。
首先需要确定模型的几何尺寸、材料性能等参数。
然后进行网格划分,确保网格的密度和数量能够满足模拟精度的要求。
此外,还需要设定边界条件和初始条件,如挤压速度、温度等。
求解阶段主要是对有限元模型进行求解。
通过使用合适的求解器和方法,对模型进行迭代计算,得到各阶段的应力分布、温度变化等数据。
后处理阶段主要是对求解结果进行分析和处理。
通过绘制应力分布图、温度变化曲线等图表,可以直观地了解金属的流动规律和挤压过程中的潜在问题。
此外,还可以通过分析结果优化工艺参数和产品设计。
workbench中ls-dyna挤压成型案例
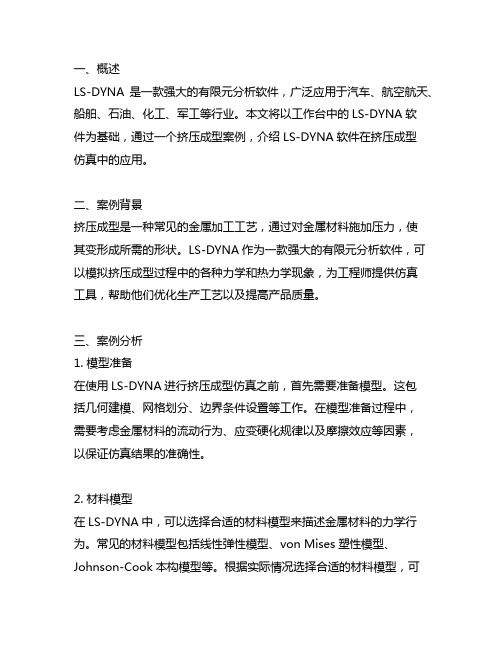
一、概述LS-DYNA是一款强大的有限元分析软件,广泛应用于汽车、航空航天、船舶、石油、化工、军工等行业。
本文将以工作台中的LS-DYNA软件为基础,通过一个挤压成型案例,介绍LS-DYNA软件在挤压成型仿真中的应用。
二、案例背景挤压成型是一种常见的金属加工工艺,通过对金属材料施加压力,使其变形成所需的形状。
LS-DYNA作为一款强大的有限元分析软件,可以模拟挤压成型过程中的各种力学和热力学现象,为工程师提供仿真工具,帮助他们优化生产工艺以及提高产品质量。
三、案例分析1. 模型准备在使用LS-DYNA进行挤压成型仿真之前,首先需要准备模型。
这包括几何建模、网格划分、边界条件设置等工作。
在模型准备过程中,需要考虑金属材料的流动行为、应变硬化规律以及摩擦效应等因素,以保证仿真结果的准确性。
2. 材料模型在LS-DYNA中,可以选择合适的材料模型来描述金属材料的力学行为。
常见的材料模型包括线性弹性模型、von Mises塑性模型、Johnson-Cook本构模型等。
根据实际情况选择合适的材料模型,可以更准确地描述金属材料的变形和破坏行为。
3. 边界条件在挤压成型仿真中,需要合理设置边界条件来模拟挤压装置对工件的施加力以及工件与模具之间的摩擦效应。
通过合理设置边界条件,可以保证仿真结果的准确性,并为工程师提供有价值的工艺优化信息。
4. 模拟分析在模型准备和材料模型确定之后,可以进行挤压成型仿真分析。
LS-DYNA可以模拟金属材料的流动行为、应变硬化及破坏过程,同时还可以考虑模具与工件之间的摩擦效应。
通过对挤压成型过程进行仿真分析,工程师可以了解工件的变形情况、应变分布以及破坏模式,为工艺优化提供参考。
5. 结果评估通过LS-DYNA进行挤压成型仿真后,需要对仿真结果进行评估。
这包括对工件的变形情况、应变分布、破坏模式以及挤压装置的受力情况等方面进行分析。
通过对仿真结果的评估,可以为工程师提供相关的工艺优化建议,帮助其改善挤压成型工艺,并提高产品质量。
有限元分析实例范文

有限元分析实例范文假设我们正在设计一个桥梁结构,希望通过有限元分析来评估其受力情况和设计是否合理。
首先,我们需要将桥梁结构进行离散化,将其分为许多小的有限元单元。
每个有限元单元具有一定的材料性质和几何形状。
接下来,我们需要确定边界条件和加载条件。
例如,我们可以在桥梁两端设置固定边界条件,然后通过加载条件模拟车辆的载荷。
边界条件和加载条件的选择需要根据实际情况和设计要求来确定。
然后,我们需要选择适当的有限元模型和材料模型。
有限元模型选择的好坏将直接影响分析结果的准确性。
材料模型需要根据材料的弹性和塑性性质来选择合适的模型。
接下来,我们可以使用有限元软件将桥梁结构的离散化模型输入计算。
有限元软件将自动求解结构的受力平衡方程,并得出结构的应力和位移分布。
通过分析这些结果,我们可以评估桥梁结构的强度、刚度和稳定性等性能。
最后,根据有限元分析结果进行设计优化。
如果发现一些部分的应力过大,我们可以对设计进行调整,例如增加材料厚度或增加结构的增强筋。
通过不断优化设计,我们可以得到一个满足强度和刚度要求的桥梁结构。
需要注意的是,有限元分析只是工程设计中的一个工具,分析结果需要结合实际情况和工程经验来进行判断。
有限元分析的准确性也取决于离散化的精度、边界条件和材料模型等的选择。
总之,有限元分析是一种重要的工程分析方法,可以用于评估结构的受力情况和设计是否合理。
通过有限元分析,我们可以优化结构的设计,提高结构的性能和安全性。
希望以上例子对你对有限元分析有所了解。
汽车厚板料件冲压成形的有限元模拟

汽车厚板料件冲压成形的有限元模拟摘要:本文对汽车厚板料件冲压成形进行了有限元模拟。
关键词:厚板料,冲压,有限元目前,我国汽车板料零件设计、制造水平不断提高,薄板料零件冲压成形CAE技术的应用已日趋成熟,但厚板料(厚度大于5mm)冲压成形、失效判定和回弹计算方面还没有一个明确的计算方法和分析思路,厚板料零件冲压成形CAE技术应用也远不如薄板成熟,本文对某汽车厚板料零件冲压成形进行了有限元模拟。
1三维模型的建立本文对某汽车厚板料U形件进行冲压成形分析,其三维模型见图1.1。
图1.1 三维模型2有限元分析2.1分析过程材料为钢板,弹性模量为207000MPa,泊松比为0.31,密度为7.85E-009,材料定义为塑性材料,凸模和凹模定义为刚体。
在成形过程中,施加的是位移,让板料变形。
有限元分析时采用的是壳单元,因为板料厚度小于9mm。
具体过程如下:图2.1 网格划分图2.2 接触的定义2.2应力应变分析图2.3 应力图2.4 应变由应力应变分析知,板料最大应力和最大应变部位都在U形件弯曲部位,这与实际相符。
3 结束语本文对某汽车厚板料U形件的冲压成形进行了有限元模拟,为汽车厚板件CAE提供一定的理论指导。
但本文研究深度不够,有待进一步完善。
参考文献:[1]张宝坤.冲压成型回弹模拟的影响因素[J].汽车工程师.2009(09)[2]富壮.汽车厚板料零件冲压成形分析及回弹计算.汽车工艺与材料.2011(11)[3]李奇涵,张亮等. 汽车后门外板件冲压成形CAE研究[J].长春工业大学学报(自然科学版). 2014(03)[4]徐思寿. 铸造模具中CAE技术的应用与研究[J]. 建材与装饰. 2017(22)[5]蒙敏.模具设计过程中CAE软件的应用[J]. 中国设备工程. 2017(18)赵生莲,攀枝花学院讲师邮编:617000通讯地址:四川省攀枝花学院交通与汽车工程学院联系电话:151****9861基金项目:2014年校级一般项目(2014YB20)。
弯管成型截面畸变的有限元分析
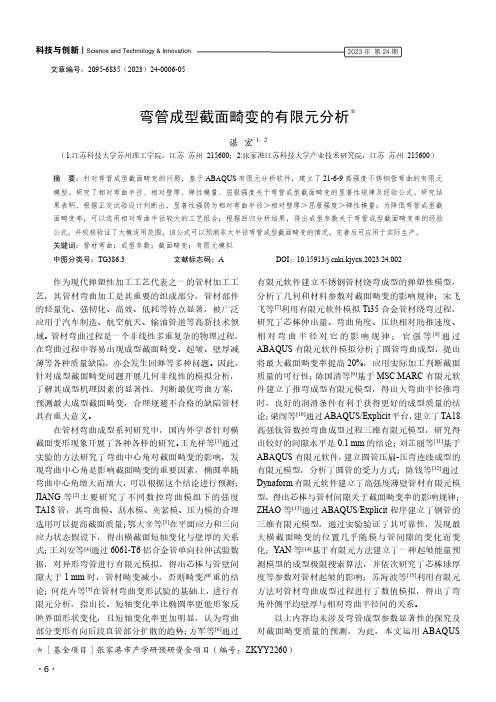
文章编号:2095-6835(2023)24-0006-05弯管成型截面畸变的有限元分析*谌宏1,2(1.江苏科技大学苏州理工学院,江苏苏州215600;2.张家港江苏科技大学产业技术研究院,江苏苏州215600)摘要:针对弯管成型截面畸变的问题,基于ABAQUS有限元分析软件,建立了21-6-9高强度不锈钢管弯曲的有限元模型。
研究了相对弯曲半径、相对壁厚、弹性模量、屈服强度关于弯管成型截面畸变的显著性规律及经验公式。
研究结果表明,根据正交试验设计判断出,显著性强弱为相对弯曲半径>相对壁厚>屈服强度>弹性模量;为降低弯管成型截面畸变率,可以选用相对弯曲半径较大的工艺组合;根据回归分析结果,得出成型参数关于弯管成型截面畸变率的经验公式,并校核验证了大概适用范围,该公式可以预测非大半径弯管成型截面畸变的情况,完善后可应用于实际生产。
关键词:管材弯曲;成型参数;截面畸变;有限元模拟中图分类号:TG386.3文献标志码:A DOI:10.15913/ki.kjycx.2023.24.002作为现代弹塑性加工工艺代表之一的管材加工工艺,其管材弯曲加工是其重要的组成部分,管材部件的轻量化、强韧化、高效、低耗等特点显著,被广泛应用于汽车制造、航空航天、输油管道等高新技术领域。
管材弯曲过程是一个非线性多重复杂的物理过程,在弯曲过程中容易出现成型截面畸变、起皱、壁厚减薄等各种质量缺陷,亦会发生回弹等多种问题。
因此,针对成型截面畸变问题开展几何非线性的模拟分析,了解其成型机理因素的显著性,判断最优弯曲方案,预测最大成型截面畸变,合理规避不合格的缺陷管材具有重大意义。
在管材弯曲成型系列研究中,国内外学者针对横截面变形现象开展了各种各样的研究。
王光祥等[1]通过实验的方法研究了弯曲中心角对截面畸变的影响,发现弯曲中心角是影响截面畸变的重要因素,椭圆率随弯曲中心角增大而增大,可以根据这个结论进行预测;JIANG等[2]主要研究了不同数控弯曲模组下的强度TA18管,其弯曲模、刮水模、夹紧模、压力模的合理选用可以提高截面质量;鄂大辛等[3]在平面应力和三向应力状态假设下,得出横截面短轴变化与壁厚的关系式;王刘安等[4]通过6061-T6铝合金管单向拉伸试验数据,对异形弯管进行有限元模拟,得出芯棒与管壁间隙大于1mm时,管材畸变减小,否则畸变严重的结论;何花卉等[5]在管材弯曲变形试验的基础上,进行有限元分析,指出长、短轴变化率比椭圆率更能形象反映界面形状变化,且短轴变化率更加明显,认为弯曲部分变形有向后段直管部分扩散的趋势;方军等[6]通过有限元软件建立不锈钢管材绕弯成型的弹塑性模型,分析了几何和材料参数对截面畸变的影响规律;宋飞飞等[7]利用有限元软件模拟Ti35合金管材绕弯过程,研究了芯棒伸出量、弯曲角度、压块相对助推速度、相对弯曲半径对它的影响规律;官强等[8]通过ABAQUS有限元软件模拟分析了圆管弯曲成型,提出将最大截面畸变率提高20%,应用实际加工判断截面质量的可行性;陈国清等[9]基于MSC.MARC有限元软件建立了推弯成型有限元模型,得出大弯曲半径推弯时,良好的润滑条件有利于获得更好的成型质量的结论;梁闯等[10]通过ABAQUS/Explicit平台,建立了TA18高强钛管数控弯曲成型过程三维有限元模型,研究得出较好的间隙水平是0.1mm的结论;刘芷丽等[11]基于ABAQUS有限元软件,建立圆管压扁-压弯连续成型的有限元模型,分析了圆管的受力方式;陈钱等[12]通过Dynaform有限元软件建立了高强度薄壁管材有限元模型,得出芯棒与管材间隙关于截面畸变率的影响规律;ZHAO等[13]通过ABAQUS/Explicit程序建立了钢管的三维有限元模型,通过实验验证了其可靠性,发现最大横截面畸变的位置几乎随模与管间隙的变化而变化;YAN等[14]基于有限元方法建立了一种起皱能量预测模型的成型极限搜索算法,并依次研究了芯棒球厚度等参数对管材起皱的影响;苏海波等[15]利用有限元方法对管材弯曲成型过程进行了数值模拟,得出了弯角外侧平均壁厚与相对弯曲半径间的关系。
- 1、下载文档前请自行甄别文档内容的完整性,平台不提供额外的编辑、内容补充、找答案等附加服务。
- 2、"仅部分预览"的文档,不可在线预览部分如存在完整性等问题,可反馈申请退款(可完整预览的文档不适用该条件!)。
- 3、如文档侵犯您的权益,请联系客服反馈,我们会尽快为您处理(人工客服工作时间:9:00-18:30)。
北华航天工业学院材料成型有限元分析作者所在系部:材料工程系作者所在专业:材料成型及控制工程作者姓名:宋明明完成时间:2012.5.23目录案例一、感应热处理案例有限元模拟及分析 (3)案例二、管材产品挤压成型案例模拟及分析 (5)案例三拉深产品挤压成型案例模拟及分析 (7)案例四、连杆锻压成型案例模拟及分析 (10)案例五、锥齿轮模锻成型案例模拟及分析 (13)案例六、热锻开坯案例有限元模拟及分 (16)案例七、机加工切削案例有限元模拟及分析 (19)案例八、轧制板材案例有限元模拟及分析 (22)案例九、自制锥形锻件模拟及分析 (24)案例十、热处理与锻压连续加工工艺模拟及分析 (27)案例一:感应热处理案例有限元模拟及分析一、材料成型方案的拟定。
1、拟成型零件用材:坯料的材料为炉膛的材料为几何形状如下图所示:2、加工工艺拟定热处理条件:材质AISI-1045钢,温度1000℃。
模具用材AISI-H13钢3、有限元前处理设置4、加工成型仿真运算5、有限元后处理分析1)模具结构对成型结果的影响分析坯料的两端必须突出(如上图,两端直径大于坯料直径),即系统的热交换面是封闭的。
炉膛内径与坯料表面的距离越近,热量传递的越快;炉膛内表面与坯料表面的投影面积越大,热量传递的越快。
2)加工成型参数对成型结果的影响分析在一定程度上,炉膛温度越高,热量传递的越快;热传递系数越大,热量传递的越快;随着温度的升高,晶粒会明显长大,最后得到粗大晶粒的组织,使金属的强度、硬度、塑性、韧性等机械性能都显著降低。
3)模具结构优化及加工工艺优化对零件成型改进的建议应合理控制坯料与炉膛间的距离以及设置合理的热传导系数,避免因传热过快,导致坯料温度过高;对于加工工艺,应提前给坯料预热,有利于奥氏体均匀化。
4)感应加热对材料组织有何影响(材料初始态组织为铁素体+珠光体,1000℃奥氏体化后组织变为奥氏体)?随着加热温度的增加,其显微组织发生明显的变化。
奥氏体晶粒尺寸对冷却后的相变产物有重要影响。
奥氏体晶粒越粗大,其稳定性越高,冷却后形成的非扩散产物也越多。
同时,在高温下合金元素的充分溶解,有利于提高过冷奥氏体的稳定性,也有利于针状铁素体等非平衡组织的形成。
当加热温度较低时,材料的组织形态为珠光体和多边形铁素体。
同时,随着奥氏体化的温度增高,增加了碳氮化合物的溶解,有利于微合金元素的沉淀强化作用,有利于提高材料的强度和韧性5)热处理对材料力学性能有何影响?1)感应加热时,钢的奥氏体化是在较大的过热度(Ac3以上80~150摄氏度)进行的,因此晶核多,且不易长大,淬火后组织为系隐晶马氏体。
表面硬度高,比一般淬火高2HRC~3HRC,而且脆性较低。
2)表面层淬火得马氏体后,由于体积膨胀在工件表面层造成较大的残余压应力,显著提高工件的疲劳强度。
小尺寸零件可提高2~3倍,大件也可提高20%~30%。
3)因加热速度快,没有保温时间,工件的氧化脱碳少。
另外,由于内部为加热,工件的淬火变形也小。
4)加热温度和淬硬层厚度(从表面到半马氏体区的距离)容易控制,便于实现机械化和自动化。
6)制作加工成型动画案例二、管材产品挤压成型案例模拟及分析一、材料成型方案的拟定。
1、拟成型零件用材:坯料用材为上下模材料为AISI-H13钢。
零件形状如下坯料直径100mm,内径40mm,高60mm,见图(a)。
上模为环形,外径100mm,内径40mm,高30mm,见图(b)。
下模侧壁厚10mm,底厚200mm,外径120mm,内径100mm,底部孔径50mm,见图(c)。
顶杆长160mm,直径40mm,见图(d)。
图(a)图(b图(c)图(d)2、加工工艺的拟定管壁厚5mm,室温挤压,速度2mm/s3、有限元前处理设置4、加工成型仿真运算5、有限元后处理分析1)模具结构对成型结果的影响分析凹模没有设置圆角,均是尖锐的直角,这不利于金属的流动,而且增大了摩擦,尖角对金属还有剪切作用,不利于管的挤压。
2)加工成型参数对成型结果的影响分析摩擦参数越大,越不利于金属的流动,管的长度也就越短3)模具结构优化及加工工艺优化对零件成型改进的建议给凹模开设合适的圆角,便于金属流动,容易挤出;对于加工工艺,应在坯料表面涂抹润滑油,减小摩擦阻力,是金属更易流动。
4)分析模具结构对材料变形的影响?模具应有足够的强度和刚度,要在冷热交变应力下正常工作;模具工作部分零件材料应具有高强度、高硬度、高耐磨性,并有一定的韧性,和表面质量。
轮廓形状合理的凹模不仅可以改善金属在凹模中的流动状态,增加塑性区内变形的均匀性从而提高材料的力学性质和产品的使用性能,而且可以显著降低成形所需的力能消耗,从而减小所需设备的吨位。
5)载荷、变形量、应力分布、流变方向等因素在加工过程中充当何种角色,发挥何种作用?使坯料沿着给定的方向流动挤压成型。
6)制作模拟动画案例三、拉深产品挤压成型案例模拟及分析1、拟成型零件用材:坯料的材料为上下模材料为AISI-H13钢零件形状如下坯料直径130mm,高10mm,见图1.上模直径30mm,高60mm,见图2.下模外径150mm,内径50mm,球形半径25mm,倒角为5mm,见图3。
压料板厚20mm,外径140mm,内径30mm坯料上模下模压边圈2、加工工艺拟定板厚10mm,室温挤压,速度5mm/s3、有限元前处理设置4、有限元后处理分析5、有限元后处理分析1)模具结构对成型结果的影响分析下模圆角过小,不利于金属流动,不利于拉深;压边力过大,增大了摩擦阻力,同样不利于金属流动,不利于拉深。
2)加工成型参数对成型结果的影响分析摩擦参数设置的越大,越不利于金属的流动,坯料拉裂的可能性越大3)模具结构优化及加工工艺优化对零件成型改进的建议给凹模开设合适的圆角,便于金属流动,容易挤出;对于加工工艺,应给凹模平面润滑,这样使毛坯凸缘处材料的流动阻力降低。
给模具表面进行以适当润滑,使拉伸变形阻力大大下降。
4)分析模具结构对材料变形的影响?拉深过程中的主要缺陷是起皱和拉裂,起皱易出现在凸缘部分及凸缘与侧壁交界部,这是拉深时由于较大的切向压应力使板料失稳造成的,生产中常采用压边圈的方法予以防止。
拉裂一般出现在直壁与底部的过度圆角处,当拉应力超过材料的抗拉强度时,此处将被拉裂。
1)限制拉深系数拉深系数越小,表明变形程度越大,拉深应力力越大,容易产生拉裂废品。
2)凹凸模工作部分应加工成圆角一般,凹模圆角半径一般约为5~10t,凸模圆角半径一般约为0.7~1t。
3)合理的凸凹模间隙间隙过小,容易拉穿;间隙过大,容易起皱。
一般,凸凹模之间的单边间隙为1~1.2t。
4)减小拉深时的阻力压边力应合理不应过大;凸、凹模工作表面要有较小的表面粗糙度;在凹模表面涂润滑剂以减小摩擦。
5)载荷、变形量、应力分布、流变方向等因素在加工过程中充当何种角色,发挥何种作用?使坯料沿着给定的方向流动挤压成型。
6)制作模拟动画案例四、连杆锻压成型案例模拟及分析一、材料成型方案的拟定1、拟成型零件用材:坯料的材料为上下模材料为零件几何形状如下图上模下模坯料2、加工工艺拟定始锻温度1000℃,终锻温度800℃,锻压速度5mm/s3、有限元前处理设置4、加工成型仿真运算5、有限元后处理分析1)模具结构对成型结果的影响分析本模具没开设飞边槽,不利于多余金属的流动,增大了金属对上下模的打击,有可能使模锻开裂。
2)加工成型参数对成型结果的影响分析热传递系数要设置合理,有利于金属组织的生成。
3)模具结构优化及加工工艺优化对零件成型改进的建议开设飞边槽,是金属更易流动,充满整个型腔。
模锻件所有两表面转接处均需圆弧过渡,圆弧过渡易于金属流动,锻造时使金属易于充满整个型腔。
4)分析锻模结构及锻模对材料变形的影响?1)尽量避免椎体或斜面结构。
锻造具有锥体或斜面结构的锻件,需要制造专用工具,锻件成形也比较困难,从而使工艺过程复杂,不便于操作,影响设备使用效率,应尽量避免。
2)避免几何体的交接处形成空间曲线。
3)避免加强肋、凸台、工字形、椭圆形或其他非规则截面及外形。
4)合理采用组合结构5)载荷、变形量、应力分布、流变方向等因素在加工过程中充当何种角色,发挥何种作用?使坯料沿着给定的方向流动锻压成型案例五、锥齿轮模锻成型案例模拟及分析一、材料成型方案的拟定1、拟成型零件用材:坯料的材料为上下模的材料为零件几何形状如下图所示:上模下模坯料2、加工工艺拟定始锻温度1000℃,终锻温度800℃,锻压速度5mm/s3、有限元前处理设置4、加工成型仿真运算5、有限元后处理分析1)模具结构对成型结果的影响分析本模具没开设飞边槽,不利于多余金属的流动,增大了金属对上下模的打击,有可能使模锻开裂2)加工成型参数对成型结果的影响分析热传递系数要设置合理,有利于金属组织的生成。
3)模具结构优化及加工工艺优化对零件成型改进的建议开设飞边槽,是金属更易流动,充满整个型腔。
模锻件所有两表面转接处均需圆弧过渡,圆弧过渡易于金属流动,锻造时使金属易于充满整个型腔。
4)分析锻模结构及锻模对材料变形的影响?1)尽量避免椎体或斜面结构。
锻造具有锥体或斜面结构的锻件,需要制造专用工具,锻件成形也比较困难,从而使工艺过程复杂,不便于操作,影响设备使用效率,应尽量避免。
2)避免几何体的交接处形成空间曲线。
3)避免加强肋、凸台、工字形、椭圆形或其他非规则截面及外形。
4)合理采用组合结构5)载荷、变形量、应力分布、流变方向等因素在加工过程中充当何种角色,发挥何种作用?使坯料沿着给定的方向流动锻压成型6)制作模拟动画案例六、热锻开坯案例有限元模拟及分析一、成型方案的拟定1、零件用材:坯料的材料为TITANIUM 6Al-4V上下模材料为AISI-D3坯料直径为50mm,长为200mm零件与胎具装配如右图2、加工工艺拟定锻造温度1100℃,锻造速度2mm/s3、有限元前处理设置4、加工成型仿真运算5、有限元后处理分析1)模具结构对成型结果的影响分析胎具要设置合理,不宜过大2)加工成型参数对成型结果的影响分析标称咬要设置合理,不宜过大,是金属组织获得较好的力学性能3)模具结构优化及加工工艺优化对零件成型改进的建议应增加再热次数,锻造得更加均匀,金属组织更好。
4)分析热锻对材料的影响?热变形是在再结晶温度以上的塑性变形,热变形时加工硬化与再结晶过程同时存在,而加工硬化又几乎同时被再结晶消除。
所以与冷变形相比,热变形可使金属保持较低的变形抗力和良好的塑性,可以用较小的力和能量产生较大的塑性变形而不会产生裂纹,同时还可以获得较高的力学性能的再结晶组织。
但是,热变形是在高温下进行的,金属在加热过程中表面易产生氧化皮,精度和表面质量较低。
5)载荷、变形量、应力分布、流变方向等因素在加工过程中充当何种角色,发挥何种作用?使坯料沿着给定的方向流动锻压成型6)制作模拟动画案例七、机加工切削案例有限元模拟及分析一、材料成型方案的拟定1、拟成型零件用材:坯料的材料为刀具材料为坯料与刀具零件图如右图:2、加工工艺拟定表面切削速度100m/min,切削深度1mm,进给速度0.5mm/rev,环境温度20℃,摩擦系数0.6,热传导系数45N/sec/mm/℃,工具磨损应用Usui模型计算,a=0.0000001,b=8553、有限元前处理设置4、加工成型仿真运算5、有限元后处理分析1)模具结构对成型结果的影响分析刀尖半径要大于切削深度2)加工成型参数对成型结果的影响分析切削厚度越大,摩擦系数越小,变形变小随着切削速度的提高,积屑瘤逐渐增大,刀具的实际前角加大,切削力朱家尖减小3)模具结构优化及加工工艺优化对零件成型改进的建议应增加使用冷却液,降低切削温度4)分析切削对材料的影响?切削力:在切削过程中,切削力直接影响切削热、刀具磨损与使用寿命、加工精度和已加工表面质量。