数控加工误差补偿的关键技术与补偿技巧
数控机床几何误差
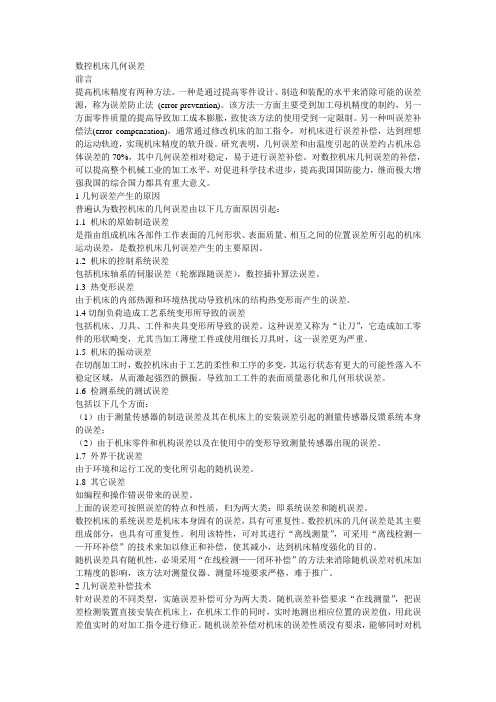
数控机床几何误差前言提高机床精度有两种方法。
一种是通过提高零件设计、制造和装配的水平来消除可能的误差源,称为误差防止法(error prevention)。
该方法一方面主要受到加工母机精度的制约,另一方面零件质量的提高导致加工成本膨胀,致使该方法的使用受到一定限制。
另一种叫误差补偿法(error compensation),通常通过修改机床的加工指令,对机床进行误差补偿,达到理想的运动轨迹,实现机床精度的软升级。
研究表明,几何误差和由温度引起的误差约占机床总体误差的70%,其中几何误差相对稳定,易于进行误差补偿。
对数控机床几何误差的补偿,可以提高整个机械工业的加工水平,对促进科学技术进步,提高我国国防能力,继而极大增强我国的综合国力都具有重大意义。
1几何误差产生的原因普遍认为数控机床的几何误差由以下几方面原因引起:1.1 机床的原始制造误差是指由组成机床各部件工作表面的几何形状、表面质量、相互之间的位置误差所引起的机床运动误差,是数控机床几何误差产生的主要原因。
1.2 机床的控制系统误差包括机床轴系的伺服误差(轮廓跟随误差),数控插补算法误差。
1.3 热变形误差由于机床的内部热源和环境热扰动导致机床的结构热变形而产生的误差。
1.4切削负荷造成工艺系统变形所导致的误差包括机床、刀具、工件和夹具变形所导致的误差。
这种误差又称为“让刀”,它造成加工零件的形状畸变,尤其当加工薄壁工件或使用细长刀具时,这一误差更为严重。
1.5 机床的振动误差在切削加工时,数控机床由于工艺的柔性和工序的多变,其运行状态有更大的可能性落入不稳定区域,从而激起强烈的颤振。
导致加工工件的表面质量恶化和几何形状误差。
1.6 检测系统的测试误差包括以下几个方面:(1)由于测量传感器的制造误差及其在机床上的安装误差引起的测量传感器反馈系统本身的误差;(2)由于机床零件和机构误差以及在使用中的变形导致测量传感器出现的误差。
1.7 外界干扰误差由于环境和运行工况的变化所引起的随机误差。
数控加工误差补偿的研究

高加工零件的加 工精度和效率, 降低 废品 率 ,具 有重要 的使 用和 推广 价值 。
数 控技 术 ; 差 补 偿 ; 床 ; 拟 补 偿 误 机 模
l 服电机和丝杆间采用柔性联轴器, 保 置。当一台加工中心在加工小的工
证 了两者 间没有 相 对转 动 。滚 珠 丝 件时 ,工 装 上一 次 可 以 装夹 几 个 工 杆 和 螺母 间预加 载 荷消 隙 。 同样 塞 件 , 编程 者不用考虑每 一个工件在编 数 控技术 自五十年 代问世以来 , 铁 调 整 的松 紧也 能给 系统 一定 的 承 !程时 的坐标 零点 , 只需按照 各 自的 而 已取得长足的进 展 , 着现代技 术的 载 和预 变形 , 加 系统 平稳性 , 随 增 因而 编程 零点进 行编程 , 后使用夹具偏 然 高速发展 ,数控加工因其精度高、柔 i数 控机床 无静 态 间隙 。 置来 移动 机 床在 每 一个 工 件上 的编 性 自动 化 及适 合加 工 复 杂零 件 的特 1 2刀具补偿 . 程零 点 。 性 ,已成为现 代先进制造 业的基础 , f 数控 加 工 中主 要 有 以下 几 种补 2 误差补偿分析 从 而在 机 械制 造企 业 的应 用 越来 越 偿方式 : 刀具长 度补偿 、刀具 半径补 2 1产生误差原因及对策 广泛。 由于制造 、安装 、受载 变形以 偿 、夹具 偏置补偿 ,它们基本上能解 j 在 加 工过 程 中 工 艺 系统会 产 及热变 形等多种 因素 的影响 , 实际 的 决加 工 过程 中因 刀具 形状 而产 生 的 生各 种 误差 从 而改 变 刀具 与工 件 数控 机 床在 运 动过 程 中不 可避 免 地 【轨迹 问题 。 1 )刀具 长度补 偿 :在对 在切 削过程 中的 相互 位置 关 系 影 要 出现各种误 差 , 以达到精 密加 工 难 个零件 编程的时候 , 首先要 指定零 响零 件 的加 工 精 度 在数 控 机床 上 的要求 。尤 其在高精 产 品的加 工 中 , I件的编程 中心 , 然后 才能建立 工件编 加工 零 件 所 产 生的 误差 主 要有 两 如何提 高零件 的 数控 加 工精 度 、减 程 坐标 系 。使 用 刀具 长 度 补偿 是 通 大类 :加 工方法误差△ G 及调安误 少误差 ,以及 对 由于各 种原 因引起 }过执 行指令来 实现的 , 同时我们给 出 }差 △ T— A 为保证 工件的加 工精 的误差进行补偿 ,也受到越来越 多 ; 个 Z坐标值 , 这样 刀具 在补偿之 后 度 误差 总 和 应不 超过 工 件加 工精 的 关注 。误差 补 偿方 法是 通 过建 立 j移 动到离工件表 面距离为 Z的地 方。
解读数控机床误差补偿关键技术及具体应用

解读数控机床误差补偿关键技术及具体应用
摘要:目前被绝大部分国外产品占领我国中高端数控机床市场,其中国内产品的在高端数控机床市场领域占有率仅为4%左右。
随着对零件加工的精密度要求越来越高的现代制造业不断发展,对高精度的数控机床的需求量将会越来越大,因此对提高我国机床产品的精度意义十分重大。
误差补偿技术是一项具有显著经济价值并十分有效的提高机床精度的手段。
国外的误差补偿技术开展得比较早,取得了不少成绩,但是在国内,误差补偿技术绝大部分还主要停留在实验室范围内,在具体应用中还不普遍。
随着我国国民经济的发展,对数控机床数量和质量的要求也越来越高。
因此,对数控机床补偿技术的研究和应用会更深入和更广泛。
关键词:数控机床;误差补偿;技术应用
1数控机床导轨误差补偿技术
1.1引起导轨导向误差的原因分析
1.1.1导轨的磨损变形
机床在工作过程中,由于导轨受到不规则的磨损变形使得导轨的直线度和扭曲度产生误差,直接影响到导轨的导向精度,从而会影响到零部件的加工精度。
导轨在机床连续的运行中受到持续的承载负荷,导轨的磨损就很难避免,如果是在粗加工的条件之下,导轨的磨损变形更加严重。
而且机床导轨的总长度上因为受到的磨损力不同,使用频率不同,所以在导轨总体上磨损的程度是不均匀的。
1.1.2导轨的热变形。
关于数控加工的误差分析及应对措施

数控加工误差包括机床、刀具、夹具、工件、切削液等多个 因素的影响,这些因素相互作用,导致加工误差的产生。
数控加工误差的类型
定位误差
几何误差
由于工件或刀具的位置不准确,导致加工出 的工件与理想状态下的工件参数之间的偏差 。
由于机床、刀具、夹具等设备的制造、安装 、调整不当,导致加工出的工件与理想状态 下的工件参数之间的偏差。
强化加工过程监 测与控制
未来将进一步加强加工过程 的实时监测和控制,通过高 精度的测量仪器和数据处理 方法,实现对加工过程中各 种误差的精确控制和修正, 从而提高工件的加工精度。
建立全面质量控 制体系
未来将更加注重建立全面质 量控制体系,通过采用科学 的质量管理方法和手段,确 保工件的加工质量稳定和持 续提高
工件误差
工件本身存在形状、尺寸等方面的误差,也会对 加工精度产生影响。
刀具误差
刀具在加工过程中会受到磨损、变形等因素影响 ,导致加工精度降低。
机床误差
机床本身精度不高或长期使用导致磨损,也会对 加工精度产生影响。
误差对加工精度的影响
位置误差
01
加工过程中,刀具与工件之间的相对位置不准确,导致加工出
总结与展望
总结
数控加工误差概述
数控加工过程中,由于受到多种因素 的影响,如机床、刀具、夹具、工件 、切削参数、环境因素等,不可避免 地会产生加工误差。这些误差通常表 现为形状、尺寸、位置等各方面的偏 差。
数控加工误差来源
误差来源主要包括机床系统误差、刀 具误差、夹具误差、工件误差、切削 参数误差和环境因素误差等。这些误 差在加工过程中会相互叠加,最终导 致工件的加工精度下降。
切削力误差
热误差
由于切削过程中切削力的大小、方向、作用 点等因素发生变化,导致加工出的工件与理 想状态下的工件参数之间的偏差。
数控机床的刀具补偿与补偿方法
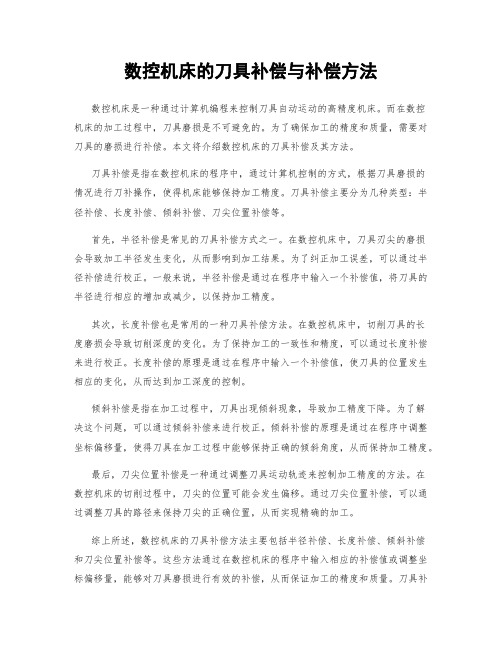
数控机床的刀具补偿与补偿方法数控机床是一种通过计算机编程来控制刀具自动运动的高精度机床。
而在数控机床的加工过程中,刀具磨损是不可避免的。
为了确保加工的精度和质量,需要对刀具的磨损进行补偿。
本文将介绍数控机床的刀具补偿及其方法。
刀具补偿是指在数控机床的程序中,通过计算机控制的方式,根据刀具磨损的情况进行刀补操作,使得机床能够保持加工精度。
刀具补偿主要分为几种类型:半径补偿、长度补偿、倾斜补偿、刀尖位置补偿等。
首先,半径补偿是常见的刀具补偿方式之一。
在数控机床中,刀具刃尖的磨损会导致加工半径发生变化,从而影响到加工结果。
为了纠正加工误差,可以通过半径补偿进行校正。
一般来说,半径补偿是通过在程序中输入一个补偿值,将刀具的半径进行相应的增加或减少,以保持加工精度。
其次,长度补偿也是常用的一种刀具补偿方法。
在数控机床中,切削刀具的长度磨损会导致切削深度的变化。
为了保持加工的一致性和精度,可以通过长度补偿来进行校正。
长度补偿的原理是通过在程序中输入一个补偿值,使刀具的位置发生相应的变化,从而达到加工深度的控制。
倾斜补偿是指在加工过程中,刀具出现倾斜现象,导致加工精度下降。
为了解决这个问题,可以通过倾斜补偿来进行校正。
倾斜补偿的原理是通过在程序中调整坐标偏移量,使得刀具在加工过程中能够保持正确的倾斜角度,从而保持加工精度。
最后,刀尖位置补偿是一种通过调整刀具运动轨迹来控制加工精度的方法。
在数控机床的切削过程中,刀尖的位置可能会发生偏移。
通过刀尖位置补偿,可以通过调整刀具的路径来保持刀尖的正确位置,从而实现精确的加工。
综上所述,数控机床的刀具补偿方法主要包括半径补偿、长度补偿、倾斜补偿和刀尖位置补偿等。
这些方法通过在数控机床的程序中输入相应的补偿值或调整坐标偏移量,能够对刀具磨损进行有效的补偿,从而保证加工的精度和质量。
刀具补偿是数控机床加工过程中不可或缺的一部分,它使得机床能够适应刀具磨损的变化,同时提高了加工的效率与精度。
数控加工的误差补偿在生产中的运用分析
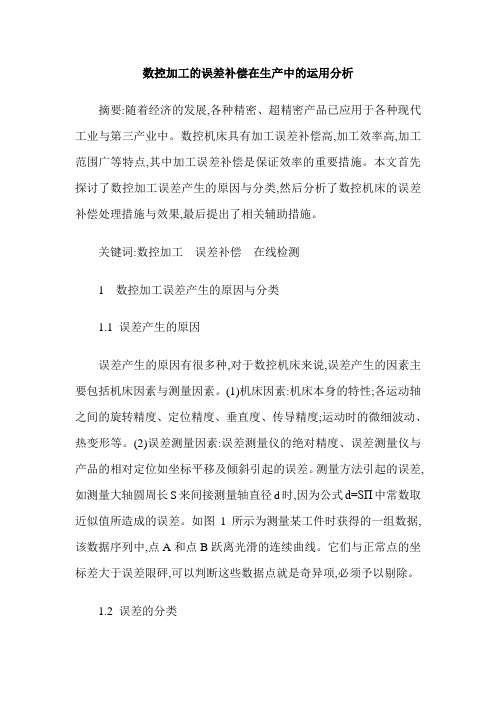
数控加工的误差补偿在生产中的运用分析摘要:随着经济的发展,各种精密、超精密产品已应用于各种现代工业与第三产业中。
数控机床具有加工误差补偿高,加工效率高,加工范围广等特点,其中加工误差补偿是保证效率的重要措施。
本文首先探讨了数控加工误差产生的原因与分类,然后分析了数控机床的误差补偿处理措施与效果,最后提出了相关辅助措施。
关键词:数控加工误差补偿在线检测1 数控加工误差产生的原因与分类1.1 误差产生的原因误差产生的原因有很多种,对于数控机床来说,误差产生的因素主要包括机床因素与测量因素。
(1)机床因素:机床本身的特性;各运动轴之间的旋转精度、定位精度、垂直度、传导精度;运动时的微细波动、热变形等。
(2)误差测量因素:误差测量仪的绝对精度、误差测量仪与产品的相对定位如坐标平移及倾斜引起的误差。
测量方法引起的误差,如测量大轴圆周长S来间接测量轴直径d时,因为公式d=SΠ中常数取近似值所造成的误差。
如图1所示为测量某工件时获得的一组数据,该数据序列中,点A和点B跃离光滑的连续曲线。
它们与正常点的坐标差大于误差限砰,可以判断这些数据点就是奇异项,必须予以剔除。
1.2 误差的分类1.2.1 几何误差包括机床、夹具、刀具的制造和磨损,尺寸链误差,机床传动链的静态和动态调整误差,产品、夹具、刀具的安装误差。
1.2.2 粗大误差粗大误差是指在一系列测量所得的数据中,经修正系统误差后如有个别数据与其他数据有明显差异,则这些数值很可能含有粗大误差。
粗大误差产生主要是由于在测量过程中系统受外界干扰不可避免会出现偶然性、突发性的测试不稳定状况。
1.2.3 系统误差系统误差是指在相同测量条件下重复测量某一被测量时,误差的大小和符号不变或按一定的规律变化,这样的测量误差称为系统误差。
系统误差对测量结果的影响较大。
因此,应认真分析,设法发现系统误差并予以消除或减小其对测量结果的影响。
对于数控机床在线检测系统来说,系统误差可以分为两类:一类是传感器系统误差,一类是机床系统误差。
数控机床误差实时补偿技术及应用

数控机床误差实时补偿技术及应用数控机床误差实时补偿技术是一种通过测量和监控机床的误差,然后通过算法和控制系统来实时修正这些误差的技术。
它可以显著提高机床的加工精度和稳定性,使得加工的零件更加精确和一致。
下面将介绍数控机床误差实时补偿技术的原理、方法和应用。
数控机床误差实时补偿技术的原理是基于机床的误差源和误差特点进行建模,并通过控制系统实时调整机床的运动轨迹来补偿这些误差。
机床的误差主要包括几何误差、动态误差和热误差等。
几何误差是由机床结构、加工刀具和工件等因素引起的,例如导轨的尺寸偏差、传动装置的误差等。
动态误差是由机床运动过程中的惯性力、弹性变形等因素引起的,例如加工过程中的振动和共振等。
热误差是由于机床在工作过程中产生的热源,例如主轴的热膨胀和冷却液的温度变化等。
数控机床误差实时补偿技术的方法一般包括两个步骤:误差测量和误差补偿。
误差测量是通过传感器或测量仪器实时检测机床的误差,并将其反馈给控制系统。
常用的测量方法包括激光干涉法、电容法和光栅尺等。
误差补偿是在控制系统中根据误差测量结果进行数学建模和分析,并根据补偿算法调整控制指令,使得机床的运动轨迹达到期望的精度。
数控机床误差实时补偿技术在实际应用中具有广泛的应用领域。
首先,它可以应用于航空航天领域的高精度零件加工。
航空航天零件对精度和质量要求非常高,数控机床误差实时补偿技术可以有效提高加工精度,降低零件的尺寸偏差和表面光洁度,从而提高航空航天产品的性能和可靠性。
其次,它可以应用于汽车制造领域的模具加工。
模具制造对精度和一致性要求较高,数控机床误差实时补偿技术可以有效减少模具的尺寸和形状偏差,提高模具的加工质量和寿命。
此外,它还可以应用于医疗器械制造、光学仪器加工等领域。
总之,数控机床误差实时补偿技术是一种通过测量和监控机床的误差,并通过控制系统实时调整机床运动轨迹的技术。
它可以显著提高机床的加工精度和稳定性,广泛应用于航空航天、汽车制造、医疗器械等领域,为实现高精度和高质量的零件加工提供了重要的技术手段。
五轴数控机床误差补偿及精度可靠性评估

五轴数控机床误差补偿及精度可靠性评估五轴数控机床是一种高精度、高效率的加工设备,广泛应用于航空航天、汽车制造、模具制造等领域。
然而,由于各种因素的影响,五轴数控机床在加工过程中存在一定的误差。
为了提高加工精度和可靠性,需对误差进行补偿并进行评估。
五轴数控机床的误差主要包括几何误差和运动误差。
几何误差是由于机床结构的制造和组装误差、刚性变形等原因引起的,主要包括平行度误差、垂直度误差、位置误差和角度误差等。
运动误差是由于伺服系统、控制系统等原因引起的,主要包括滞后误差、迟滞误差和不平衡误差等。
这些误差会直接影响加工件的精度和表面质量,因此对误差进行补偿和控制是提高加工质量的关键。
误差补偿是通过测量和分析机床误差,通过数学模型将误差量归入控制系统,使其在加工过程中进行补偿。
起首需要对机床进行检测和测量,得到机床的误差信息。
常用的检测方法包括激光干涉仪、刚度测试仪等。
其次,通过数学建模和仿真,分析机床误差的来源和特性,建立误差补偿模型。
最后,将误差补偿模型嵌入控制系统中,实现误差的实时补偿。
误差评估是对机床的精度和可靠性进行评判和监控。
通过定期对机床进行精度测试和性能测试,可以得到机床的测量数据。
然后,对测试数据进行统计分析和处理,计算出机床的误差指标,并与加工要求进行比较。
例如,常用的误差指标包括定位误差、重复定位误差、轮廓误差等。
对于超出允许范围的误差,需要进行调整和修理,以确保机床的加工精度和可靠性。
同时,还可以接受传感器和监控系统对机床进行实时监测和预警。
通过安装传感器在关键部位,可以实时感知机床的工作状态和性能,监测其误差变化和趋势。
一旦发现异常状况,监控系统可以准时报警,并进行相关维护和处理。
这样可以防止机床在加工过程中出现严峻误差,保证加工质量和工作安全。
总结起来,五轴数控机床误差补偿和精度可靠性评估是提高加工质量和效率的重要手段。
通过对机床误差的测量、建模和补偿,以及对机床精度和可靠性的评估和监控,可以实现机床加工精度的提高和工作可靠性的保证。
- 1、下载文档前请自行甄别文档内容的完整性,平台不提供额外的编辑、内容补充、找答案等附加服务。
- 2、"仅部分预览"的文档,不可在线预览部分如存在完整性等问题,可反馈申请退款(可完整预览的文档不适用该条件!)。
- 3、如文档侵犯您的权益,请联系客服反馈,我们会尽快为您处理(人工客服工作时间:9:00-18:30)。
为 以下两 方 面 : 第一 , 当 刀 具 因磨 损 或 换 刀 而 引 起 刀 具
半径 变化 时 。 只 需 按 变 化 量 修 改 相 应 的偏 置 参 数 , 而 不
必 重 新 编程 ; 第二 , 当零 件 加 工需 要 多 个 工序 完 成 时 ,
一
般 只 要 粗 加 工 后 为 精 加 工 工 序 预 留加 工 余 量 ,加 工
数 控 加 工 误 差 补 偿 的 关 键 技 木 与 补 偿 技 巧
口 张志 梅 口 安虎 平
兰州 7 3 0 0 7 O 1 . 兰 州 交 通 大 学 后 勤 管理 处
2 . 兰州 城 市 学 院 培 黎 工 程 技 术 学 院摘
要: 以数 控加 工 中误 差 补偿 方 法技 巧 为研 究 对 象 , 通 过 分 析 数 控 加 工 原 理 和 编 程技 术 . 探 讨 了刀 具 半 径 补 偿 的主
补 偿 和校 正 。 从 而使编 程 工作 直接 按零 件 图进 行 , 而 不 必 考 虑 刀 具 的 磨 损 及 尺 寸 变 化 等 因 素 。其 优 点 可 概 括
余 量 的 预 留 可 通 过 修 改 刀 具 偏 置 参 数 实 现 , 也 不 必 为 粗 、 精加 工 各 编制 一 套 程序 , 即粗 、 精 加 工 采 用 一 个 相 同 程 序 。 如 图 1所 示 , 实线 为所 需加 工 的零 件轮廓 , 即 编程 轨 迹 , 虚 线 为刀 具 中心 轨 迹 , 根据内 、 外 轮 廓 的 不 同有 不 同的偏 置方 向。 根据 I S O标准 , 当 刀 具 中 心 轨 迹 沿其 前进 方 向位 于编程 轨迹 右边 时 . 为右刀 补 . 用 G4 2
了进 一 步 处理 刀具 磨 损 误 差 的基 本 措 施 和 补 偿 技 巧 。结 果 可 为优 化 编 程 、 提 高加 工精 度 和 效 率 . 提 供 可操 作 性 强 的 方 法 。
关键词 : 数控加工 刀 位 补偿 多 刀几 何 补偿 误 差 补 偿 文章编号 : 1 o o 0 — 4 9 9 8 f 2 0 1 3 1 0 8 — 0 0 6 5 — 0 3
一
1 刀 具 半 径 补 偿
1 . 1 刀 具 半 径 补 偿 方 法 及 特 点
刀 具 半 径 补 偿 通 常 有 两 种 方 法 .即 B刀 补 法 和 C
刀补 法 。
( 1 )B 刀 补 法 。 该 方 法 是 指 工 件 相 邻 两 段 轮 廓 加
工 的 刀 具 中 心 轨 迹 的 段 间 都 以 圆 弧 方 式 连 接 ,如 图 1
指令 实现 ; 反 之 , 则 为左 刀补 , 用 G4 1指 令 实 现 。
侧 有 一 个 偏 移 量 , 方 能 得 到 所 需 要 的 工 件 轮 廓 形
状 。根 据 零 件 轮 廓 编 制 的程 序 和 预 先 设 定 的偏 移 参 数, 数 控 装 置 能 实 时 生 成 刀 具 中心 运 动 轨 迹 , 这 种 功 能 称 为 刀 具 半 径 补 偿 功 能 。 不 同 情 况 下 刀 具 偏 移 方 向 和 偏移 量 的大小 应 该 不 同 , 合 理确 定 补 偿 量 和 补偿 指 令 是保 证加 工精 度 的关 键技 术 之一 。 虽然 实 际 轮 廓较 为 复 杂 , 但 根 据 零 件 轮 廓 相 对 于 实体 的位 置 不 同可 分 为 内轮 廓 与 外轮 廓 两 种 , 内 轮 廓 位 于 实体 的 内侧 , 外 轮 廓 位 于 实 体 的 外 侧 。 根 据 数 控 加 工 编程 原理 , 为 了能加 工 出所需 零件 轮廓 形 状尺 寸 , 在 进 行 内轮廓 加 工 时 , 刀 具 中 心 必 须 向 零 件 内 侧 偏 移
中 图分 类 号: T H1 6 1 . 5
文献标识码: A
金属 切 削加 工是 依 据有 关加 工工 艺 要求 在机 床上 控 制 刀 具 与 工 件 之 间相 对 运 动来 完 成 零 件 成 形 的过 程 .数控 加工 是将 零件 加 工工 艺 过程所 需 刀具 与2 1 2 件 之 间 的 相 对 位 移 量 及 各 种 操 作 用 数 字 化 信 息 代 码 程 序表示 , 在 数 控 系统 的 控 制 下 发 出各 种 指 令 , 通 过 伺 服 系 统 驱 动 执 行 件 来 控 制 刀 具 加 工 运 动 轨 迹 以 获 得 所 需 要 的 工 件 轮 廓 。 数 控 程 序 是 以 刀 尖 圆 弧 中 心 或 刀 具 中心 为基 准 . 按 零件 轮 廓形 状 和尺 寸要 求 编制 。 数控 机床 在 加 工 中所 控 制 的是 刀 具 中心 的轨 迹 。 而 切 削 是 靠 刀 刃来 逐 渐切 出工 件 的轮 廓 。因此 , 为 了加 工 出所 需 要 的工 件 轮廓 。 实 际加 工 时 刀具 必 须 要 相 对 于工 件
要 依 据及 处 理 实 际 问题 的技 术 难 点 , 给 出 了有 关 难 点 问题 的解 决 办 法 : 对 多刀 加 工 编 程 时 刀 具 几 何 补 偿 参 数 的 获 取 和 刀
具偏 置参 数 设 置进 行 了 系统 阐述 , 提 供 了刀 具 补 偿 参 数 表 的 设 定 方 法 ; 对 刀 具 磨 损 误 差 的 补 偿 方 法 和 途 径进 行 讨 论 . 给出
中 圆弧 A B 所示 , 其优 点是算 法 简单 , 容 易 实 现 。其 缺
个偏 置量 ( 粗加 工时 , 其 偏 置 量 等 于 刀 具 半 径 与 半
精 加 工 和 精加 工 余 量 之 和 ) ; 在 进行 外 轮 廓 加 工 时 , 刀
具 中心必 须 向零件 外侧 偏 移一 个偏 置 量 。 应 用 数 控 系 统 的 补 偿 功 能 可 对 刀 具 半 径 进 行 自动