Additive manufacturing with secondary processing of curve-face gears
机械设计制造及其自动化的英文

机械设计制造及其自动化的英文Mechanical design and manufacturing as well as automation are all integral parts of modern industry. In the field of mechanical engineering, design and manufacturing processes are essential for the creation and production of a wide range of products, from simple consumer goods to complex industrial machinery.Mechanical design involves the creation of detailed plans and specifications for machinery and equipment. This process requires a deep understanding of materials, mechanics, and thermodynamics, as well as the ability to use advanced computer-aided design (CAD) software. With the help of CAD tools, engineers can create 3D models and simulations to test the performance and functionality of their designs before they are manufactured.Manufacturing, on the other hand, involves the actual production of the designed machinery and equipment. This process can involve a variety of techniques, including casting, machining, welding, and assembly. With advancements in automation, many manufacturing processes are now carried out with the help of robots and other automated systems, leading to increased efficiency and reduced production costs.Automation plays a key role in both the design and manufacturing processes. Automated systems can perform repetitive tasks with high precision and accuracy, reducing the need for human intervention and minimizing the risk of errors. This is particularly important in industries where safety and quality are paramount, such as automotive and aerospace manufacturing.Overall, mechanical design, manufacturing, and automation are all critical components of modern industrial processes. Through the use of advanced technology and engineering principles, these processes continue to evolve and improve, leading to more efficient and reliable products for consumers and businesses alike.In addition to traditional manufacturing methods, additive manufacturing (also known as 3D printing) has emerged as a revolutionary process in mechanical design and manufacturing. This innovative technique allows engineers to create complex and intricate parts by building them layer by layer from digital 3D models. Additive manufacturing offers the potential for rapid prototyping, customization, and cost-effective production, making it an increasingly popular choice for a wide range of industries.Furthermore, the integration of smart technologies and the Internet of Things (IoT) has transformed the landscape of automation in mechanical design and manufacturing. Smart sensors, connected devices, and data analytics enable machines and equipment to communicate and make autonomous decisions, leading to enhanced process monitoring, predictive maintenance, and optimization of production workflows. This has resulted in improved productivity, reduced downtime, and better resource utilization.Quality control is another critical aspect of mechanical design and manufacturing. Advanced inspection techniques, such as non-destructive testing, 3D scanning, and computer vision, allow for thorough examination and validation of manufactured parts and assemblies. By ensuring the quality and reliability of products,these techniques contribute to overall customer satisfaction and safety.The field of mechanical design and manufacturing also intersects with sustainability and environmental considerations. Engineers and manufacturers are increasingly focused on developing eco-friendly processes and products, utilizing recycled materials, reducing waste, and optimizing energy usage. Sustainable practices not only benefit the environment but also resonate with consumers who are becoming more environmentally conscious.In conclusion, the advancements in mechanical design, manufacturing, and automation are driving innovation and efficiency across various industries. Through the integration of cutting-edge technologies and a commitment to quality and sustainability, the future of mechanical engineering holds the promise of even more sophisticated, reliable, and sustainable products and production processes.。
关于制造产品的作文英语
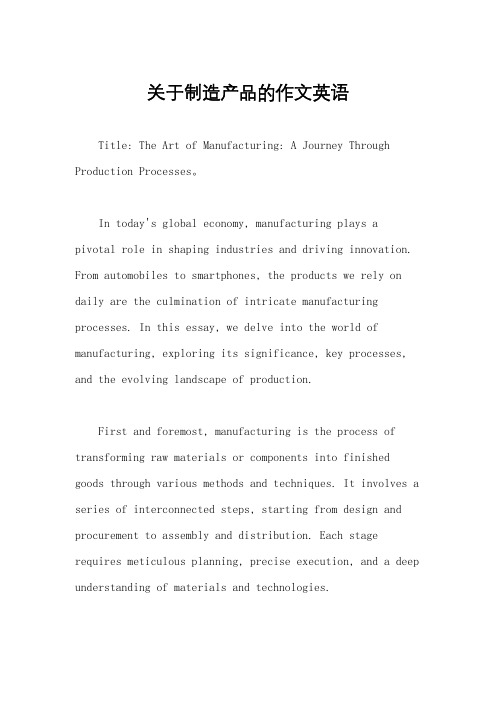
关于制造产品的作文英语Title: The Art of Manufacturing: A Journey Through Production Processes。
In today's global economy, manufacturing plays apivotal role in shaping industries and driving innovation. From automobiles to smartphones, the products we rely on daily are the culmination of intricate manufacturing processes. In this essay, we delve into the world of manufacturing, exploring its significance, key processes, and the evolving landscape of production.First and foremost, manufacturing is the process of transforming raw materials or components into finished goods through various methods and techniques. It involves a series of interconnected steps, starting from design and procurement to assembly and distribution. Each stage requires meticulous planning, precise execution, and a deep understanding of materials and technologies.One of the fundamental aspects of manufacturing is product design. Designing a product involves conceptualizing its features, functionality, and aesthetics to meet consumer needs and market demands. This phase often entails collaboration between designers, engineers, and market analysts to ensure that the final product aligns with customer preferences and industry standards.Once the design is finalized, the next step is procurement. Procurement involves sourcing raw materials, components, and equipment necessary for production. Manufacturers must establish reliable supply chains, negotiate contracts, and manage inventory to ensure uninterrupted production and cost-effectiveness.With materials in hand, the manufacturing process moves to the production floor, where various techniques are employed to shape and assemble the product. Depending on the complexity of the item, manufacturing methods may include machining, casting, molding, welding, or additive manufacturing (such as 3D printing). Automation and robotics have also revolutionized production, increasingefficiency, precision, and output while reducing labor costs.Quality control is another critical aspect of manufacturing. Throughout the production process, rigorous quality checks and inspections are conducted to identify defects, ensure compliance with specifications, and maintain product consistency. This requires the implementation of quality management systems and adherence to industry regulations and standards to uphold product integrity and customer satisfaction.Furthermore, sustainability has become a growing concern in modern manufacturing. With increasing environmental awareness and regulatory pressure, manufacturers are adopting eco-friendly practices, such as recycling, waste reduction, and energy efficiency measures. Sustainable manufacturing not only benefits the environment but also enhances brand reputation and reduces long-term operational costs.In recent years, digital technologies have transformedthe manufacturing landscape through concepts like Industry 4.0 and the Internet of Things (IoT). These advancements enable interconnected factories, predictive maintenance, real-time monitoring, and data-driven decision-making, ushering in an era of smart manufacturing. By leveraging data analytics, artificial intelligence, and machine learning, manufacturers can optimize processes, minimize downtime, and customize products to meet individual customer needs.Moreover, globalization has reshaped the manufacturing industry, leading to the outsourcing of production to countries with lower labor costs and favorable business environments. While this has expanded market access and reduced costs for many companies, it has also raised concerns about job displacement, supply chain vulnerabilities, and ethical labor practices.In conclusion, manufacturing is a multifaceted process that drives economic growth, technological advancement, and consumer satisfaction. From product design to distribution, each stage requires careful planning, innovation, andcollaboration to deliver high-quality goods efficiently and sustainably. As we navigate the challenges andopportunities of the modern manufacturing landscape, embracing innovation, sustainability, and digitalization will be key to staying competitive and meeting the needs of a rapidly evolving market.。
“增才制造”:以增材原理推动个性化陶瓷材料“成型—成性一体化”设计
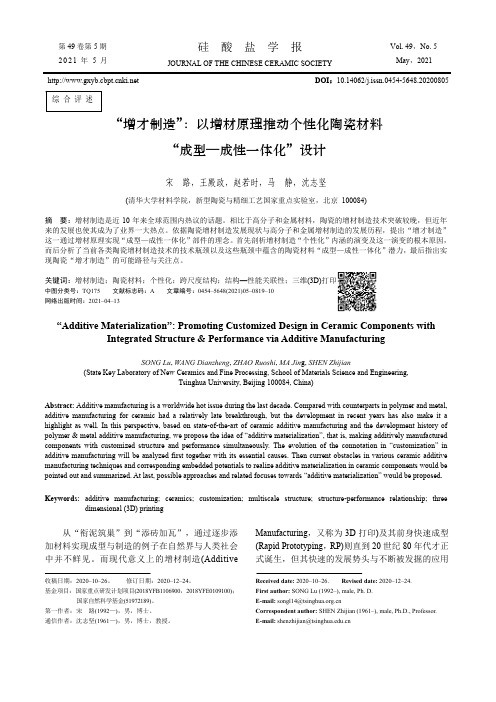
第49卷第5期2021年5月硅酸盐学报Vol. 49,No. 5May,2021 JOURNAL OF THE CHINESE CERAMIC SOCIETY DOI:10.14062/j.issn.0454-5648.20200805“增才制造”:以增材原理推动个性化陶瓷材料“成型—成性一体化”设计宋路,王殿政,赵若时,马静,沈志坚(清华大学材料学院,新型陶瓷与精细工艺国家重点实验室,北京 100084)摘要:增材制造是近10年来全球范围内热议的话题。
相比于高分子和金属材料,陶瓷的增材制造技术突破较晚,但近年来的发展也使其成为了业界一大热点。
依据陶瓷增材制造发展现状与高分子和金属增材制造的发展历程,提出“增才制造”这一通过增材原理实现“成型—成性一体化”部件的理念。
首先剖析增材制造“个性化”内涵的演变及这一演变的根本原因,而后分析了当前各类陶瓷增材制造技术的技术瓶颈以及这些瓶颈中蕴含的陶瓷材料“成型—成性一体化”潜力,最后指出实现陶瓷“增才制造”的可能路径与关注点。
关键词:增材制造;陶瓷材料;个性化;跨尺度结构;结构—性能关联性;三维(3D)打印中图分类号:TQ175 文献标志码:A 文章编号:0454–5648(2021)05–0819–10网络出版时间:2021–04–13“Additive Materialization”: Promoting Customized Design in Ceramic Components with Integrated Structure & Performance via Additive ManufacturingSONG Lu, WANG Dianzheng, ZHAO Ruoshi, MA Jin g, SHEN Zhijian(State Key Laboratory of New Ceramics and Fine Processing, School of Materials Science and Engineering,Tsinghua University, Beijing 100084, China)Abstract: Additive manufacturing is a worldwide hot issue during the last decade. Compared with counterparts in polymer and metal, additive manufacturing for ceramic had a relatively late breakthrough, but the development in recent years has also make it a highlight as well. In this perspective, based on state-of-the-art of ceramic additive manufacturing and the development history of polymer & metal additive manufacturing, we propose the idea of “additive materialization”, that is, making additively manufactured components with customized structure and performance simultaneously. The evolution of the connotation in “customization” in additive manufacturing will be analyzed first together with its essential causes. Then current obstacles in various ceramic additive manufacturing techniques and corresponding embedded potentials to realize additive materialization in ceramic components would be pointed out and summarized. At last, possible approaches and related focuses towards “additive materialization” would be proposed. Keywords: additive manufacturing; ceramics; customization; multiscale structure; structure-performance relationship; three dimensional (3D) printing从“衔泥筑巢”到“添砖加瓦”,通过逐步添加材料实现成型与制造的例子在自然界与人类社会中并不鲜见。
增材制造复杂流道水冷电机壳体对驱动电机持续功率影响的研究
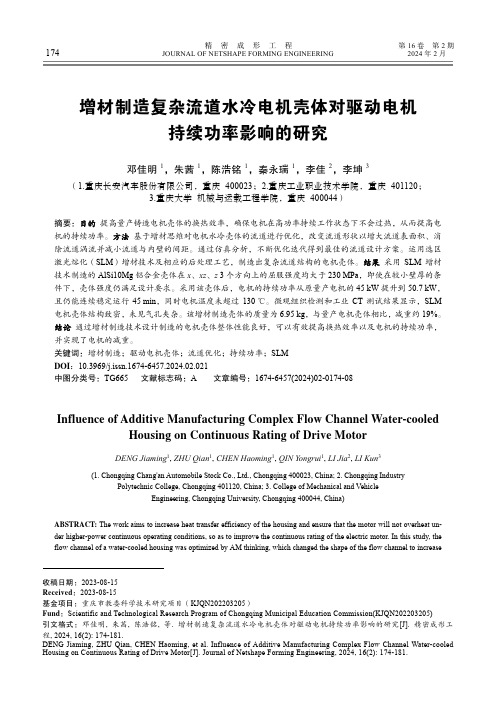
精 密 成 形 工 程第16卷 第2期 174JOURNAL OF NETSHAPE FORMING ENGINEERING 2024年2月收稿日期:2023-08-15 Received :2023-08-15基金项目:重庆市教委科学技术研究项目(KJQN202203205)Fund :Scientific and Technological Research Program of Chongqing Municipal Education Commission(KJQN202203205)引文格式:邓佳明, 朱茜, 陈浩铭, 等. 增材制造复杂流道水冷电机壳体对驱动电机持续功率影响的研究[J]. 精密成形工程, 2024, 16(2): 174-181.DENG Jiaming, ZHU Qian, CHEN Haoming, et al. Influence of Additive Manufacturing Complex Flow Channel Water-cooled Housing on Continuous Rating of Drive Motor[J]. Journal of Netshape Forming Engineering, 2024, 16(2): 174-181. 增材制造复杂流道水冷电机壳体对驱动电机持续功率影响的研究邓佳明1,朱茜1,陈浩铭1,秦永瑞1,李佳2,李坤3(1.重庆长安汽车股份有限公司,重庆 400023;2.重庆工业职业技术学院,重庆 401120;3.重庆大学 机械与运载工程学院,重庆 400044) 摘要:目的 提高量产铸造电机壳体的换热效率,确保电机在高功率持续工作状态下不会过热,从而提高电机的持续功率。
方法 基于增材思维对电机水冷壳体的流道进行优化,改变流道形状以增大流道表面积、消除流道涡流并减小流道与内壁的间距。
通过仿真分析,不断优化迭代得到最佳的流道设计方案。
增材制造技术ppt课件

编辑课件
27
“翅膀根的受力件,我们做出来136公斤,锻件1706公斤,节省 材料90%+。2010年,已经做完了性能测试,比锻件还要好。 05年做出图示零件需要5天,现在只要几小时。”
我国成为目前世界上唯一突破飞机钛合金大型主承力结构件激
光快速成形技术,并实现装机应用的国家。所做零件经过8000
小时以上的抗疲劳测试。 编辑课件
06年某飞机起落架的关键零部件,目前已经批
生产,已经受2000多个起落。
编辑课件
30
航空发动机叶盘
高温合金涡轮盘
“未来发动机就是一肚子
的整体叶盘,叶片和盘子分开
的重量太重。而我们现在可以
叶片和盘子同时出来,而且叶
片我们可以随心所欲控制组织,
让它长成柱状晶,他的高温性
能就很好,这里我们让它长成
等轴晶,低周耐疲性能就很好,
编辑课件
4
3D打印机的优势
1.制造复杂物品。(目前已显现) 2.产品多样化不增加成本。 3.生产周期短。(最大的优点) 4.零技能制造。 5.不占空间、便携制造。(战场、灾区) 6.节省材料 。 7.精确的实体复制。(3D照相馆)
编辑课件
5
民用消费级3D打印机
• 打印材料:塑料丝、少量金 属丝
• 特点:结构简单、精度低、 物品表面粗糙、不考虑力学 性能。
-王华明
编辑课件
36
增材制造金属部件有多贵
• 增材制造的金属部件每克售价10元-100元,价格在 黄金和白银之间.
• 王华明利用增材制造技术生产的飞机次承力结构 件,几十公斤,成本120万.
• 外国记者John Newman 报道,中国用于增材制造 的国防研发费用约在8000万美元。
advances in manufacturing的投稿要求

Advances in ManufacturingManufacturing is an essential component of global economies, contributing to economic growth and technological progress. Over the years, technological advancements have revolutionized the manufacturing industry, leading to increased efficiency, improved quality, and reduced costs. In this article, we will explore some of the recent advances in manufacturing that have transformed the way we produce goods.Additive ManufacturingAdditive manufacturing, also known as 3D printing, is a groundbreaking technology that has gained significant attention in recent years. Unlike traditional manufacturing methods that involve subtracting materials from a solid block, 3D printing builds objects layer by layer using various materials such as plastics, metals, and ceramics.This technology enables complex and customized designs that were previously impossible or economically unviable. It has revolutionized the production process by reducing the need for expensive molds or tooling and enabling rapid prototyping. Additive manufacturing also reduces waste materials and has the potential to minimize the environmental impact associated with traditional manufacturing processes.Robotics and AutomationThe integration of robotics and automation into manufacturing processes has led to increased productivity, improved quality, and enhanced safety. Robots can perform repetitive tasks with precision, speed, and accuracy, reducing human error and increasing overall production efficiency. They can also be utilized in hazardous environments, minimizing the risk to human workers.Advancements in artificial intelligence have further improved the capabilities of robots. They can now be programmed to adapt to changing conditions, learn from experience, and interact with humans in a collaborative manner. This allows for greater flexibility in manufacturing processes and facilitates the implementation of Industry 4.0 concepts, such as smart factories and digitalized supply chains.Internet of Things (IoT)The Internet of Things (IoT) refers to the network of physical devices embedded with sensors, software, and connectivity, enabling them to collect and exchange data. In the manufacturing industry, IoT technology has transformed the way machines, products, and humans interact.By integrating IoT devices and sensors into manufacturing equipment, machines can communicate with each other and with operators in real-time. This facilitates predictive maintenance, as machines can detect and report potential failures before they occur, minimizing downtime and optimizing productivity. IoT also enables data analytics and machine learning, allowing manufacturers to gain valuable insights and optimize their operations.Advanced MaterialsThe development of advanced materials has opened up new possibilities for manufacturing industries. These materials possess unique properties, such as high strength, lightweight, flexibility, and enhanced electrical and thermal conductivity.For example, carbon fiber composites have become increasingly popular in industries such as aerospace and automotive manufacturing due to their high strength-to-weight ratio. These materials offer significant weight reduction, leading to improved fuel efficiency and reduced emissions. Similarly, advancements in nanotechnology have enabled the development of materials with enhanced properties, such as improved heat resistance or self-healing capabilities.ConclusionThe manufacturing industry is continually evolving with the help of technological advancements. Additive manufacturing, robotics and automation, IoT, and advanced materials are just a few examples of the significant progress being made. These advances have not only increased productivity and efficiency but have also opened up new possibilities for customization, sustainability, and innovation. As technology continues to advance, we can expect further disruptions and improvements in the manufacturing landscape, shaping the future of production.。
Additive manufacturing

Additive manufacturing (AM) opens up a design freedom beyond the limits of traditional manufacturing techniques. Electrical windings created through AM could lead to more powerful and compact electric motors, but only if the electrical properties of the AM printed part can be shown to be similar to conventionally manufactured systems. Until now, no study has reported on the suitability of AM partsfor electrical applications as there are few appropriate materials available to AM for this purpose.AlSi10Mg is a relatively good electrical conductor that does not have the same reported issues associated with processing pure aluminium or copper via selective laser melting (SLM). Here, experiments were conducted to test the effects of geometry and heat treatments on the resistivity of AlSi10Mg processed by SLM. It was found that post heat treatments resulted in a resistivity that was 33% lower than the as-built material. The heat treatment also eliminated variance in the resistivity of as-built parts due to initial build orientation. By conducting these tests, it was found that, with this material, there is no penalty in terms of higher resistivity for using AM in electrical applications, thus allowing more design freedom in future electrical applications.。
additive manufacturing意思

additive manufacturing意思“Additive Manufacturing” 是一种先进的生产技术,也被称为3D打印技术,它可以通过连续添加材料的方式生产物品。
这种技术对制造业产生了重大影响,因为它可以生产出具有高度精确度的零部件,缩短制造周期,降低成本和延长产品的生命周期。
第一步,建模软件。
首先需要使用一些专业的建模软件来设计3D 模型,这些软件可以通过CAD或其他3D图形软件来实现。
这是3D打印领域最关键的一步,因为成品的质量和准确性完全取决于所做的模型的质量和准确性。
第二步,导入到打印机。
设计好的3D模型接着需要被导入到3D 打印机里面。
这个过程通常通过数据线或者局域网进行。
在这个过程中,需要选择打印材料,并输入相关的打印参数来确定所需的打印效果。
第三步,3D打印。
当设备已被正确地设置好,将开始相关的打印过程。
在这个过程中,打印头开始向打印床逐层添加材料。
这个过程非常缓慢,裸眼很难分辨打印头的运动轨迹。
第四步,成品处理。
打印完毕后,需要进行成品处理。
这通常包括去除支撑,打磨和上光。
在某些情况下要暴露在强紫外线下,以达到特定的产品硬度和结构。
总结来看,3D打印技术的应用在现实生活中越来越广泛。
除了设计界,它已经进入到生命科学,建筑、汽车、金融等行业中。
这种技术不仅可以快速制作静态模型,在汽车、飞机、船舶、模具、设备等交通机械制造等领域得到广泛应用。
AI等先进科技的革新,已经不断推动着科技行业的创新和提升。
3D打印技术做为新兴产业,引领着制造业的新变革。
随着技术的进步和应用的不断扩展,它的前景看起来是美好而广阔的。
- 1、下载文档前请自行甄别文档内容的完整性,平台不提供额外的编辑、内容补充、找答案等附加服务。
- 2、"仅部分预览"的文档,不可在线预览部分如存在完整性等问题,可反馈申请退款(可完整预览的文档不适用该条件!)。
- 3、如文档侵犯您的权益,请联系客服反馈,我们会尽快为您处理(人工客服工作时间:9:00-18:30)。
ORIGINAL ARTICLEAdditive manufacturing with secondary processing of curve-face gearsChao Lin 1&Yu Fan 1&Zhengwen Zhang 1&Guang Fu 1&Xijun Cao 1Received:30June 2015/Accepted:12November 2015#Springer-Verlag London 2015Abstract In order to process curve-face gears with less ma-terial,simpler processes,and high profile accuracy,a method was proposed that uses additive manufacturing (AM)as the primary process,while computer numerical control (CNC)as the secondary process,i.e.,obtaining the blanks of the curve-face gear pairs using additive manufacturing and then conducting secondary processing using five-axis CNC ma-chining.The tooth profile coordinate system of the tool,the processing coordinate system of the curve-face gear,the mod-el of rounded corner in addendum angle,the CNC machining model,and the rapid prototyping model were established by applying space gear meshing theory,five-axis CNC machin-ing principles,and fundamental theories in additive manufacturing.The tool ’s tooth profile equation,the coordi-nate transformation matrix from the tooth surface of the non-circular gear to that of the curve-face gear,the fillet surface equation,the five-axis motion equation during machining,and the coordinate transformation matrix during additive manufacturing were derived.The curve-face gear pair was machined by additive manufacturing with secondary CNC processing.Tooth surface measurement of the obtained gear pair was conducted.The results show that while materials wastage and number of processes involved are largely re-duced,the tooth surface precision of additively manufactured gear pairs is significantly improved.The design for curve-facegear pairs and the method of additive manufacturing with secondary processing of curve-face gears were proved to be effective.Keywords Face gear .CNC machining .Additive manufacturing .Variable transmission ratio .Design .Transmission1IntroductionThe curve-face gear drive is a transmission in which a non-circular gear engages with a curve-face gear,and the intersecting axis is 90°.The curve-face gear drive,which com-bined the characters of the non-circular gear drive and the conical gear drive,can realize variable transmission ratio mo-tion between the intersecting axes.The driving gear is a non-circular gear that drives the curve-face gear to achieve the variable transmission ratio motion.The curve-face gear pair is shown in Fig.1.The face gear drive is a transmission where a cylinder gear engages with a conical gear [1].Back in 1940s,Buckingham introduced face gear drive in his work.Now,after 70years,face gear drive is mainly applied in the shunt transmission structure of the main gear transmission system on helicopters [2].Its application is rare mainly because the face gears re-quire a complicated design and have low processing precision.These reasons impeded the development and application of face gears.Litvin ’s research group has made a significant contribution to the development of face gears [3–5].Besides,Yang et al.studied the gear shaping method of face gears [6].Deng et al.fabricated face gears using a five-axis computer numerical control (CNC)machine and measured and evaluated the tooth surface precision [7].Shih et al.proposed a mathematicalElectronic supplementary material The online version of this article (doi:10.1007/s00170-015-8118-7)contains supplementary material,which is available to authorized users.*Chao Linlinchao@1The State Key Laboratory of Mechanical Transmission,Chongqing University,400044Chongqing,People ’s Republic of ChinaInt J Adv Manuf TechnolDOI 10.1007/s00170-015-8118-7model of face-hobbed SBG based on a modern six-axis CNC bevel gear cutting machine [8].Cui et al.conducted accurate modeling for the fillet surface of the Arc tooth surface gear and used Gleason cutting tools to fabricate the face gear [9].Tang et al.studied the high-efficient precision grinding of face gears [10].Michele et al.conducted quasi-static analysis for face gear under torque condition [11].Claudio investigated the modification of face gears [12].Dudás et al.studied the tool for the rapid manufacturing of face gears [13].While using five-axis machine to fabricate gears,the pose position and orientation between the tool and the workpiece can be adjusted during machining.The interference between the tool and the workpiece can be avoided.Only one setup will be required to complete the whole machining process.The processing precision,quality,and efficiency of the tooth surface can be improved.Additive manufacturing is regarded as a new technology that overturns traditional machining techniques,which makes it a focus in the field of manufacturing.There are large num-bers of investigators conducting researches concerning addi-tive manufacturing.Vlasea et al.presented a novel rapid lay-ered manufacturing approach based on a combined additive manufacturing (AM)process and a UV-based microsyringe deposition (μSD)technique to be used in the fabrication of bio-ceramic structures with controlled micro-sized channels for bone and osteochondral tissue regeneration [14].Strano et al.proposed a new design and optimization method for the additive manufacturing of support structure [15].Brøtan proposed a method to improve the precision of additive manufacturing [16].Monzón et al.presented a summary and review of actions carried out so far by different organizations and projects,based on the work of several road maps and workshops,with the aim of developing new standards in this particular field [17].Järvinen et al.studied the support struc-ture obtained from metal laser sintering [18].Additive manufacturing can be used in the rapid prototyping of the complex tooth surface and can fabricate gears with any tooth profile with less material,simplerprocesses,and no requirement on exclusive machines and tools.However,currently,the surface precision of additive manufacturing is low.Therefore,this study proposes a combined additive manufacturing and five-axis CNC machining processing method for curve-face gear pair.This method will first apply additive manufacturing to obtain the blank of the gear pair (the blank is thickened on the basis of the standard tooth surface).Then,the five-axis CNC machine will be used in the second-ary processing of the gear pair.The thickened tooth surface will be milled to finish the machining process.The advantage of this method is that it can combine the benefits of two pro-cessing methods:additive manufacturing can save materials and simplify processes,and five-axis CNC machining will guarantee the precision of the tooth surface so that the engi-neering requirement for the gear pair can be satisfied.In this paper,AM-5-CNC stands for the abbreviation of the com-bined processing method of additive manufacturing and five-axis CNC machining.2Design of curve-face gear2.1The standard tooth surface mode of curve-face gear The non-circular gear can be presumed to be the tool used for fabricating the curve-face gear.As shown in Fig.2,r bk is the base radius of the tool,θok is the cutter angle,which is deter-mined by the corresponding angle of spread of the tooth width on the base circle.The tooth surface model of the curve-face gear discussed in this paper is derived by using envelope of the tool base on generating theory.Thus,the tooth profile of the tool will be discussed first.The tooth profile of the tool is symmetrical,so only half of the tooth profile is required and the other half can be derived through its symmetry property.The left tooth pro-file equation of the tool can be expressed as follows:r k !u k ;θk ðÞ¼r bk cos θok þθk ðÞþθk sin θok þθk ðÞ½ r bk sin θok þθk ðÞ−θk cos θok þθk ðÞ½ u k126643775ð1Þwhere r bk =r k cos αu and αu is the tool pressure angle.θok ¼π.2z k −inv αuIn order to describe the movement relationship of the non-circular gear and the face gear,the following four coordinate systems can be established based on space gear meshing the-ory:s (X s Y s Z s ),s ′(X s ′Y s ′Z s ′),f (X f Y f Z f )and f ′(X f ′Y f ′Z f ′).Coor-dinate systems s ′(X s ′Y s ′Z s ′)and f ′(X f ′Y f ′Z f ′)are rigidly con-nected.Their relative positions are described byauxiliaryFig.1The curve-face gear pair fabricated by the combined processing methodInt J Adv Manuf Technolcoordinate systems from S s ′to S f ′.Here,θ1and θ2are the rotation angles of the non-circle gear and the curve-face gear,as shown in Fig.3.The coordinate transformation matrices S s ′to S f ′are repre-sented as follows:M f 0s 0¼M f 0f M fs M ss 0¼cos θ1sin θ10−r 0ðÞ−cos θ2sin θ1cos θ1cos θ2sin θ2R sin θ2sin θ1sin θ2−cos θ1sin θ2cos θ2R cos θ200126643775ð2ÞThe gear surface equation can be derived by transforming tool tooth profile from the non-circular gear coordinate system s ′to the face-curve gear coordinate system f ′.Then,the tooth surface equation of the face gear can be obtained as follows:r 2!u k ;θk ðÞ¼M f 0s0r k !u k ;θk ðÞð3Þn 2!¼L f 0s 0n 0!¼L f 0s 0∂r 0!∂θk Â∂r 0!∂u k ∂r k !∂θk Â∂r k !∂u kð4Þwhere L f 0s 0is the third-order principal minor of M f 0s 0.In the coordinate system O f 0,the relative velocity v f 0s 0 !f 0ðÞcan be expressed asv f 0s 0!f 0ðÞ¼θ1!−θ2! ÂM f 0s 0r k !ð5ÞThe engagement equation can be derived from the aboveequation as follows:n 2⋅ !v f 0s0 !f 0ðÞ¼f u k ;θk ;θ2ðÞ¼0ð6ÞThe tooth surface vector of the face gear can be obtainedthrough solving the above equation as follows:r 2!¼r 2!θk ;θ2ðÞð7Þ3Additive manufacturing3.1Principle of additive manufacturingAdditive manufacturing (AM)is a technique that fabricates solid components through accumulating materials layer by pared with traditional manufacturing techniques,additive manufacturing is a method that accumulating mate-rials from bottom to top.AM requires no traditional tools,clamps,or multiple processes.It can rapidly and accurately fabricate any components with complex structures based on the 3D design data by using only one device and 10∼30%time and 20∼35%cost of the traditional manufacturing meth-od [10].So the “free manufacturing ”could be realized,and problems of fabricating components with complex structures could be solved.This new technique provides a novel method for the manufacturing of curve-face gears.EOS M280powder laser printer employs DMLS (direct metal laser sintering).Its basic principle is as follows:using laser to selectively melt solid powder and superposing the solidified material layer by layer and eventually forming com-ponents with the required shapes.The whole process involves CAD model building and data processing,powder paving,laser melt,and post-processing.The principle of additive manufacturing with DMLS technique is shown in Fig.4.3.2Pre-processingThe required data should be prepared before processing.The data is presented as the STL format that contains the CAD model.Software such as Pro/E,UG,Catia,Cimatio,Solid Edge,and MDT can provide the STL data format which can be recognized by the slicing software in the DMLS manufacturing system.It is inadequate to complete the processing merely by out-put the data in STL format.The model should be repaired and the support structure should be added.In real application,the models are usually partitioned into triangular mesh model.Fig.2The tooth profile of the toolpitchcurvesofgearFig.3The processing coordinate system of the curve-face gearInt J Adv Manuf TechnolSince there is a plane on one side of each fabricated gear,no support will be required in the present study.After finishing the above work,processing simulation can be conducted in the slicing software,where slicing can be conducted at regular intervals along the height direction of the shaping in order to extract the contour of the interface and to exam whether there are defects in the model and if the added support is feasible.The magnitude of the interval can be chosen according to the requirement for the precision and productivity of the fabricated components.The larger the interval is,the higher the precision can be achieved,but the longer time is needed.The interval is ranged from0.01to 0.03mm,and normally around0.02mm under which smooth molding surface can be obtained.After selecting the slice in-terval,the particle size of the sintered materials should be corresponding to the interval.The thickness of each layer should not be larger than the particle size.3.3Rapid prototyping machineThe rapid prototyping machine chosen for the fabrication of the curve-face gear pair was EOS M280.The structure of its working part is shown in Fig.5.The basic parameters are shown in Table1.In M280,there are four CNC axes that realize the fabrication of additive manufacturing.Its motion axes involve workpiece motion axis,scraper motion axis,and galvanometer motion axis.The workpiece motion axis con-tains translational motion Z t along axis Z.The scraper motion axis contains translational motion Y t along axis Y.The galva-nometer motion axis contains translational motion X t and ro-tational motion X r along axis X.3.4Processing coordinate systemThe fixed coordinate system of the rapid prototyping ma-chine O J0(x J0,y J0,z J0),the workpiece coordinate system O J1(x J1,y J1,z J1),the scraper coordinate system O J2(x J2, y J2,z J2),and the galvanometer coordinate system O J3(x J3,-y J3,z J3)were established.The workpiece coordinate sys-tem was fixed on the workpiece.After the processing began,the workpiece coordinate system O J1(x J1,y J1,z J1) moves a distance of Z in the fixed coordinate system O-J0(x J0,y J0,z J0),i.e.,the translation vector for the work-piece is(0,0,z)in the machine coordinate system.The scraper coordinate system O J2(x J2,y J2,z J2)moves a dis-tance of Y in the fixed coordinate system O J0(x J0,y J0, z J0),i.e.,the translation vector for the scraper is(0,y,0) in the machine coordinate system.Meanwhile,due to the rotation of the galvanometer,the galvanometer coordinate system O J3(x J3,y J3,z J3)first rotates for an angle ofγaround its axis X J3,and then moves along axis X J3for a distance of X t.Through the above analysis,the transformation matrix from the workpiece coordinate system to the rapid prototyping machine coordinate system O J0(x J0,y J0,z J0) can be obtained as follows:platformFig.4The principle of additive manufacturing withDMLSFig.5Processing coordinate system of rapid prototyping machineTable1Basic parameters of rapid prototyping machine M280Sensor status Characteristic vectorMaximum forming size250×250×325mmType of laser transmitter Yb-fiber200W;400WOptical system F-theta-lens high-speed scanningScanning speed Maximum speed7m/sFocal length100–500μmPower supply32AMaximum power8.5kWLayer thickness20μmProduct size2200mm×1070mm×2290mmCAD data STLInt J Adv Manuf TechnolT J1J0¼000000000010x y z126643775ð8ÞThe transformation matrix from the scraper coordinate sys-tem to the fixed coordination system O J0(x J0,y J0,z J0)can be obtained as follows:T J2J0¼000001000000x y z126643775ð9ÞThe transformation matrix for the galvanometer in the fixed coordinate system O J0(x J0,y J0,z J0)is as follows:T J3J0¼10000−cosγsinγ00sinγcosγ0000126643775ð10ÞThe position change relationship between the galvanome-ter and the workpiece during processing can be established based on the above coordinate transformation.3.5Additive manufacturing processThe curve-face gear pair obtained in the present study was thickened by1mm on the basis of the original model,i.e., an allowance of1mm was reserved for the secondary five-axis CNC machining,as shown in Fig.6.Before the fabrication process,the molding chamber had to be preheated.When the fabrication began,the workbench moved to its original position.A layer of metal powder was paved on the workbench.Then,certain amount of inert gas was passed into the molding chamber.The processing would automatically start as soon as the oxygen content in the mold-ing chamber was lower than a certain value.The metal powder was irradiated by computer-controlled laser beams so that the shape of solidified metal can coincide with the layered geo-metric model of the component.Then,the workbench moved downward for a distance of one layer’s thickness.Another layer of metal powder will be paved and the above process would be repeated.Eventually,the required components could be obtained.Figure7shows the fabrication process.The total volume of the face gear and the non-circular gear is223,747.70and71,229.94mm3,respectively.The total fabrication time was about33h if the scanning speed was7m/s.Currently,there were four types of powder materials in our lab:stainless steel,die steel,titanium alloy,and nickel-base superalloys.The die steel was cho-sen as the workpiece material considering that the die steel has high hardness,strength and wear resistance, and adequate toughness.The layer thickness was 0.01mm.The total height of the curve-face gear was 29.20mm,and the total number of layers was2920. The total height of the non-circular gear was22mm, and the total number of layers was2200.Wire cutting was required after fabrication in order to obtain the need-ed components.The additive manufactured gear pair is shown in Fig.8.4Five-axis CNC secondary processing4.1Secondary clampingThe fringe of the baseplate was slightly tilted due to the unevenly distributed heat input on the baseplate during additive manufacturing[19].So the wire cutting process might have some influence on the dimension of the bottom of the gears.Besides,since the precision of wire cutting is relatively poor,the baseplate cannot be used as the locating surface.The secondary clamping is difficult because the clamping datum has to bedetermined.Fig.6Comparison of the additive manufacturing model with theoriginal model(a) Additive manufacturing(b) EOS M280 (c) Wire cuttingFig.7a Additive manufacturing.b EOS M280.c Wire cutting Int J Adv Manuf Technol4.1.1Secondary clamping of non-circular gearTwo schemes were designed for the clamping of the non-circular gear.Scheme 1A key groove was fabricated on the spindle thatwas for the positioning of the non-circular gear.The key groove could be used for the positioning of the tooth in the secondary processing.On the end face of the spindle,a line that passes through the center and parallels the bottom plane of the key groove was drawn (Scheme 1).Scheme 2Inner gear fixture was installed to clamp the non-circular gear.A shaft hole was fabricated for sec-ondary positioning.Then,the tooth surface could be machined (Scheme 2).Scheme 1was chosen for its lower cost.Its detailed imple-mentation can be illustrated as follows:the non-circular gear was positioned via a supporting shaft and a bolt.The direction of the slender groove on the supporting shaft was parallel to the bottom plane of the key groove.A probe was used to exam the slender groove and to ensure that the clamped component coincided with the CNC model,so that precise tool setting could be achieved,as shown in Fig.9.4.1.2Secondary clamping of curve-face gearSince the bottom surface of the face gear was removed from the baseplate through wire cutting,it had a low precision and hence was unable to be the datum plane of the secondary positioning.Therefore,the bottom surface of the face gear should first be processed.Due to the staircase effect in additive manufacturing [20],the vertical surface has the highest precision.Thus,the three-jaw chuck could be used to clamp the face gear.The shaft hole and the upper surface of the face gear can be the datum for clamping and milling of the face gear.Since the tooth surfacewould prop the three-jaw chuck,three 50-mm-thick gauge blocks were positioned on the chuck.After completing the milling of the bottom surface,the bottom surface and the shaft hole were taken as the datum to clamp and mill the face gear.A probe was used to investigate the bolt hole so that the clamped component coincided with the CNC model and ac-curate tool setting could be realized,as shown in Fig.10.4.1.3Partial cutting analysis of gearsWhen milling the gears using the five-axis CNC machine,the allowance on both sides of the tooth surface should be re-moved,and the amount of removed materials on both sides of the tooth surface had to be the same.Therefore,the gear positioning and tool setting should have adequate precision so that a relative high processing precision could be achieved.If the positioning precision of the gear was low or the tool setting was not accurate,large tooth profile error would be caused due to partial cutting during machining,which might result in incomplete cutting or over cutting,as shown in Fig.11.Fig.8Additive manufactured curve-face gearpairScheme 1A fabricated key groove on thespindleScheme 2Installed inner gear fixtureInt J Adv Manuf Technol4.2Principle for five-axis CNC secondary processing of curve-face gearThe standard tooth surface model was employed in the five-axis CNC secondary processing,i.e.,removing parameters Δx and Δy in the tooth profile of the tool.In Fig.12,three pa-rameters were required to machine curve-face gear using rod milling cutter:θm ,l k and h k ,where θm is the dip angle of the rod milling cutter rotating around the axis Z ,l k is the distance along the axis Z between the origins of the rod milling cutter and the face gear,and h k is the distance along the axis X between the origins of the rod milling cutter and the face gear.θm ,l k and h k are functions of the independent variable θ2.Assume that the tooth surface equation of the curve-face gearis r 2!u k ;θk ðÞ.The motion equation for the rod milling cutter r t !u k ;θk ðÞcan be obtained by transforming the coordinate sys-tem O a (X a Y a Z a )to O e (X e Y e Z e ).r t !u k ;θk ðÞ¼M eg θm ðÞM gi h k ;l k ðÞM ia θ1ðÞr 2!u k ;θk ðÞ¼M eaθm;h k;l k θ1ðÞr 2!u k;θkðÞð11ÞThere are three translational motions c x ,c y ,c z and two ro-tational motions ψa ,ψc in the five-axis CNC machine.Figure 13shows the machining principle of the curve-face gear.The processing of the face gear involved two parts:one was that the tool rotated around its central axis,while the other one was that the tooth profile of the tool transformed into the tooth profile of the generating gear and engaged with the blank of the curve-face gear.c was fixed at the center of the non-circular gear which was hypothetically engaged with the curve-face gear.O b (X b Y b Z b )was obtained via rotating O a (X a -Y a Z a )around axis X for an angle of ψa .O c (X c Y c Z c )was ob-tained via translating O b (X b Y b Z b )along axes Y ,Z ,and X for distances of K 1,C z ,and C x respectively.O d (X d Y d Z d )was ob-tained via rotating O c (X c Y c Z c )around axis Z for an angle of ψb .O e (X e Y e Z e )was obtained via translating O d (X d Y d Z d )along axis Y for distances of C y .O e (X e Y e Z e )was fixed at the center of the pitch curve tooth width of thetool.Fig.9Secondary clamping of the non-circulargearFig.10Secondary clamping of face gear(a) Balanced cutting positionThe tooth surface after milling(b) Partial cutting position (c) Over cutting positionFig.11a Balanced cutting position.b Partial cutting position.c Over cutting positionFig.12Position relationship between ball end milling cutter and generating gearInt J Adv Manuf TechnolTransforming the coordinate system Se of the rod milling cutter to the coordinate system S a of the curve-face gear as follows:r J ðÞ2 !u k ;θk ðÞ¼M J ðÞab ψc ðÞM J ðÞbc c x ;c z ðÞM J ðÞcd ψa ðÞM J ðÞde c y ÀÁr J ðÞt !u k ;θk ðÞ¼M J ðÞae ψa ;ψc c x ;c y ;c z ÀÁr J ðÞt !u k ;θk ðÞð12ÞThe transformation matrix from the rod milling cutter to the curve-face gear should be equivalent to that from the trajecto-ry of the rod milling cutter to the face gear.M J ðÞaeψa ;ψc c x ;c y ;c z ÀÁ¼M ae θm ;h k ;l k θ1ðÞ¼M −1ea θm ;h k ;l k θ1ðÞð13ÞThe angle positions of the CNC machine can be derived asfollows through comparison with the 3×3rotation matrices in Eq.(19):ψa θ2ðÞ¼θ2ψb θ2ðÞ¼θm θ2ðÞ&ð14ÞThe expression for the transitional axis of the CNC ma-chine can be obtained from the above equations as follows:c x θ2ðÞ¼h k θ2ðÞcos θm ðÞ.cos θ2ðÞþk 1tan θ2ðÞ−k 2cos θ2ðÞþk 2sin θ2ðÞtan θ2ðÞc y θ2ðÞ¼h k θ2ðÞsin θm þk 1cos θ2þsin θ2 h k θ2ðÞcos θm ðÞ.cos θ2ðÞþk 1tan θ2ðÞ−k 2cos θ2ðÞþk 2sin θ2ðÞtan θ2ðÞ þ2k 2sin θ2ðÞcos θ2ðÞc z θ2ðÞ¼l k θ2ðÞ8>>>>>>>>>><>>>>>>>>>>:ð15Þ4.3Machining processThe geometric parameters for the processing of the curve-face gear pair is shown in Table 2.In the machining of the non-circular gear,trial cut was conducted on the gear:three uniformly distributed teeth on the circle were selected for the trial cut.Then,semi-finishing and finishing were conducted.Finally,the allowance on the addendum was milled by cylindrical milling cutter.The ma-chining process is shown in Fig.14.The whole process is as follows:Powder (laser sintering and accumulating layer by lay-er)→non-circular gear with base plate (wire cutting)→non-circular gear →milling key groove using support clamp →on the top surface of the clamp,drawing a line passing through the center line and parallel to the bottom surface of the key groove for tool setting →positioning using the cylindrical surface of the support clamp and the tag line as datum,and milling the tooth surface →semi-finishing →finishing →end product.(a) Blank (b) Trial cutting (c) Semi-finishing(d) Finishing (e) Angle-clearing (f) End productFig.14Secondary processing of the non-circular gear.a Blank.b Trial cutting.c Semi-finishing.d Finishing.e Angle-clearing.f End productTable 2Geometric parameters for the processing of the curve-face gearpairParameter nameValue Number of teeth of non-circular gear z118Number of teeth of face gear z236Modulus m (mm)4Order of non-circular gear n12Order of face gear n24Eccentricity k0.1Addendum coefficient ha*1Headspace coefficient C*0.25Inner radius of the face gear R1(mm)70Outer radius of the face gear R2(mm)83Tooth width (mm)13abFig.13Position relationship between tool and non-circular gearInt J Adv Manuf TechnolDuring the secondary processing of the curve-face gear,the bottom surface was milled and used as datum:the gear was reversely positioned and elevated by a 50-mm-gauge block.Two passes were needed for the disc mill cutter to mill along the circumferential direction.The ma-chining process is shown in Fig.15.The whole process is as follows:Powder (laser sintering and accumulating layer by lay-er)→curve-face gear with baseplate (wire cutting)→curve-face gear →taking the shaft hole and the upper surface as datum,positioning using three-jaw chuck,and milling the lower surface →positioning using the lower surface and the shaft hole as datum,and milling the tooth surface →semi-finishing →finishing →end product.5Relevant measurement experimentsAfter the processing was complete,the gear pair was measuredby a CNC Gear measuring center.The pitch deviation and pitch cumulative error of the non-circular gear and the tooth profile deviation of the face gear were analyzed.The results were com-pared with those of the face gear pair with the same parameters fabricated by traditional CNC machining (Fig.16).The equation for the closure of the pitch curve and uniform distribution characteristic of the gear teeth can be expressed as follows [21]:Zφn 0ffiffiffiffiffiffiffiffiffiffiffiffiffiffiffiffiffiffiffiffiffiffiffiffiffiffiffiffiffiffiffiffir 2þdr .d φ 2r d φ¼n πmð16Þwhere n is the number of the pitch of teeth,m is the mod-ulus,and φn is the ideal polar angle corresponding to each pitch of teeth.The real polar angle φn ′can be obtained according to the equation θ′=arctan[r /(dr /d φ′)]+φ′,where φ0′=0°.The theoret-ical pitch of teeth can be expressed as follows:S n ¼Z φnφn −1ffiffiffiffiffiffiffiffiffiffiffiffiffiffiffiffiffiffiffiffiffiffiffiffiffiffiffiffiffiffiffiffir 2þdr .d φ 2r d φ¼πmð17ÞThe real pitch of teeth is as follows:S 0n ¼Z φ0nφ0n −1ffiffiffiffiffiffiffiffiffiffiffiffiffiffiffiffiffiffiffiffiffiffiffiffiffiffiffiffiffiffiffiffir 2þdr .d φ 2r d φð18ÞTherefore,the pitch deviation and the pitch cumulative error can be expressed as follows:Δf ptn ¼S 0n −S n ð19ÞΔF pn ¼X n i −1Δf ptnð20ÞThe measurement coordinate system and part design coor-dinate system had to be transformed into the same coordinate system for the data processing during the measurement pro-cess.The measurement coordinate system is O m ,and the de-sign coordinate system is O t ,as shown in Fig.17.Assume there is a point whose coordinate is (x m ,y m ,z m )in the measurement coordinate system.According to the above transformation matrices,its coordinate in the design coordi-nate system can be expressed as follows:x ;y ;z ðÞ¼x m ;y m ;z m ðÞM tt 0M t 0m 0M m 0mð21ÞThe normal error of the tooth profile is as follows:T ¼x −x t ðÞn !x þy −y t ðÞn !y þz −z t ðÞn !z ð22Þwhere (x t ,y t ,z t)is the theoretical coordinate and n !x ;n !y ;n !z ÀÁis the normal vector at the theoretical point.Normal errors can be obtained from the above equation.The left surfaces of the same tooth were selected for comparison.The pitch deviation and pitchcumulativeFig.16Measuring of face gear pairs obtained by combinedprocessing method and traditional CNC machining(a) Blank (b) Trial cutting (c) Semi-finishing(d ) Finishing (e) Angle-clearing (f) End prod uctFig.15Secondary processing of the curve-face gear.a Blank.b Trialcutting.c Semi-finishing.d Finishing.e Angle-clearing.f End productInt J Adv Manuf Technol。