铸造模具外文文献翻译、中英文翻译
压铸模具与成型专业名词(中英文版)
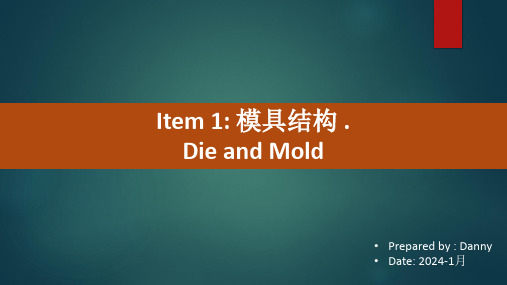
常用软件推荐(Common software recommendation)
Flow 3D / Pro cast Software(US)-目前国内小压铸厂比较多用,因为是免费软件。 Small die casting plant is more commonly used, because it is a free software. Magma-software(Germany)-汽配件大型压铸厂信赖的软件。 This software trusted by large automobile parts company for die casting. Any-casting (Korea)-国内小型压铸厂用的多些。 It was made in Korea, it was more used in the small die casting plant in China.
氮 碳 共 渗 是 在 含 有 活 性 碳 、 氮 原 子 的 介 质 中 同 时 渗 入 氮 和 碳 , 并 以 渗 氮 为 主 的 低 温 氮 碳 共 渗 工 艺 ( 530℃580℃)。氮碳共渗的渗层脆性小,共渗时间比渗氮时间大为缩短。压铸模经氮碳共渗后,可显著提高其热疲劳性 能。
电镀涂层- Electroplating Coating
Item 1: 模具结构 . Die and Mold
• Prepared by : Danny • Date: 2024-1月
压铸模具零件结构-Mold components.
✓ 前模固定板 Cavity Fixing Plate/ A Plate
✓ 料套 Sprue Bush
模具安装在压铸机上。 Tooling fixed in the die casting machine.
铸造学术语(中英文对照)

铸造学术语(中英文对照)铸造厂,铸造foundry铸造尺shrink rule铸造尺shrinkage rule铸造尺shrinkage scale铸造从业员foundry man铸造法casting process铸造方案founding method铸造方案plan of casting铸造废料foundry scrap铸造机casting machine铸造计划casting plan铸造设计,铸件设计casting design铸造性试验castability test铸造应变casting strains铸造用钉foundry nails铸造用生铁foundry pig iron铸造状态as-cast condition,as-cast铸造组织cast structure铸造作业casting manipulations铸芝模ingot mold铸芝偏析ingotism抓斗绞车装置grabbing gear专业铸造工场production foundry砖brick转变用铁水(调配成分) transition iron转动炉,转筒炉rotary furnace转换conversion转炉converter转炉钢converter steel转炉炉榇converter lining转盘混砂机rotating pan mill转速revolving speed转台,转盘rotary table转台喷粒机shot tablast转位半径transititon radius转运车transfer trolley转运翻箱装置transfer-turnover device转运盖c装置transfer-closing device转运装置transfer device装砂心coring up装载机bucket loader装载能量loading capacity追补焦split coke锥形炉腹bosh坠裂试验shatter test坠落试验drop test坠重试验drop-weight test自动电极控制automatic electrode control自动电流调整器automatic current regulator自动化automation自动化系统automatic system自动加料设备automatic charging equipment自动进给automatic feeding自动控制automatic control自动配料机automatic doser自动燃烧控制automatic combustion control自动送料(压铸) automatic ladling,die casting自动温度控制器automatic temperature controller自动造模工场automatic molding plant自动铸砂处理设备automatic sand plant自动转盘式造模机automatic turntable molding machine 自来水tap water自然腐蚀试验field test自然裂缝seasoning shake自然破裂season cracking自然干燥法(木材),自然季化处理(铸件) natural seasoning 自然时效natural aging自然通风natural draft自行除渣self-skimming自行除渣风口self-slagging tuyere自行结晶idiomorphic crystal自行退火self-annealing自硬钢self-hardening steel自硬性self-hardening自硬性造模法no-bake process自硬性粘结剂self-curing binder自由度degree of freedom自由水free water纵向裂痕longitudinal crack足尺full size阻挠元素interfering element阻销stop pin组成图constitutional diagram组成物component组成楔值constitutional wedge value组合built up组合构造composite construction组合模板built-up plate组合模型built-up pattern组合模型composite pattern组合模型pattern assembly组合砂箱built-up molding box组合砂心盒multiple core box组织,级成constitution组织成分constituent组织瑕疵structure defects钻悄(试样用) drillings钻维硬度值(韦克氏硬度) diamond pyramid hardness number,Vickers hardness 最大负载maximum load最后加工finish最适水分(模砂) optimum temper moisture作业可靠性operational reliability作业砂(生产线) production sand作业准备日程operational scheduling直立浇铸vertical pouring直立心型端承,直立砂心头vertical coreprint直立旋板心轴upright spindle直立造模vertical molding直立造模法mold on end直立铸模vertical mold直立铸造vertical casting直落砂心drop core直木纹edge grain直提砂心头tail print直通干燥炉through feed drying furnace直显照片(金相) direct print直压式合机direct pressure closing植物油vegetable oil指形进模口finger gate酯系硬化法ester-process制震能damping capacity蛭石vermiculite置冲法pour-over method置冲法transfer method置模箱set-off box滞流(铸疵) mistrun制程退火process annealing制模型铣床pattern milling machine制图,起模drawing制造熔接production welding制造冶金学process metallurgy质量效应,厚薄效应mass effect致密度consistency中间处理intermediate treatment中间检查intermediate inspection中间金属intermediate metal中间砂箱,中间模箱cheek box ,cheek flask中间砂箱,中间模箱raising middle flask中磷生铁(P0.4-0.75%) medium phosphorus pig iron 中模,中间砂箱,中间模箱cheek中碳钢medium carbon steel中途添焦spreader charge of coke中线收缩centerline shrinkage中心板,旋刮板心轴承座center plate中心规centergage中性耐火材料neutral refractory materials中性熔渣neutral slag中性砖neutral brick中周波感应电炉intermediate frequency furnace 锺,锺形塞进器bell锺青铜bell bronze重搭overlap重捣砂hard ramming重金属铸件heavy-metal castings重晶石heavy spar重力分离器gravitational separator重力滚子输送机(倾斜式) gravity roller conveyor重力偏析gravity segregation重力输送机gravity conveyor重力压铸法gravity die casting重力铸造法gravity casting重燃油heavy fuel oil重熔remelting重熔工场secondary smelter重印法(造模) print back重油heavy oil重整石英砂replenishment quartz sand重铸recasting轴shaft轴承合金bearing metal皱痕面(铸疵) creasy surface皱皮(铸疵) orange peel皱皮(铸疵) surface folding珠,粒,击,射注过程(压铸) shot珠击处理shot peening珠击机shot peening machine珠粒喷击清理shot blasting珠泡bead竹叶状液面花纹bamboo leaves pattern主成分,基本金属primary coil主模master mold主心型,主砂心body core煮材干燥法boiling seasoning助流剂fluidizer助黏剂,膨胀性粘结剂swelling binder注入槽(压铸) pouring shot注射器injector柱column柱pillar柱塞,塞罩plunger柱塞,塞罩post柱状结晶columnar crystal柱状组织columnar structurew仓壁冲击振动器impact vibration on bin wall 贮砂桶匣(砂心机用) magazine铸包camlachie cramp铸壁wall铸壁鹌鹑wall thickness铸补burning on铸补tinkering铸成率casting yield铸成试片cast-to-shape specimen铸尺contraction rule<BR>铸疵casting defect铸疵defect test铸疵,铸造缺陷foundry defects铸疵试验defect test铸锭ingot铸锭底砖spider铸锭浇口砖king brick铸锭模ingot case铸锭状态as-ingot铸钢cast steel铸钢造模料steel foundry molding compound 铸工caster铸工founder铸合金ferro-alloy铸弧pouring arc铸件castings铸件表面casting surface铸件表皮casting skin铸件飞边,铸件毛边casting fin铸件内包物cast-in insert铸件清理,最后加工finishing铸件清理图dressing shop铸件修整finishing of castings铸件应力casting stress铸焦foundry coke铸坑casting pit铸坑foundry pit铸裂(铸疵) casting crack铸瘤rising铸漏bleed铸漏break out铸漏run-out铸漏件bleeder铸模mold,mould铸模布置mold layout铸模除除掉(压铸) impression block铸模龟裂,脉状痕(铸疵) veining铸模夹具mold clamp铸模输送机mold conveyer铸模块合mold assembly铸耙rake铸皮skin铸皮孔skin holes铸砂casting sand铸砂处理foundry sand preparation铸砂处理preparation of sand铸砂处理工场foundry sand preparation plant 铸砂控制sand control铸砂控制设备sand control equipment铸砂流动性flowability of sand铸砂流动性foundry sand铸砂膨(铸疵) sand drier铸砂强度试验strength test of sand铸砂强化strengthen the sand铸砂烧结(铸疵) sand burning铸砂烧贴(铸疵) sintering point铸砂油casting iol铸生铁机pig machine铸损foundry losses铸损,不良铸件waster,foundry losses 铸铁cast iron铸铁工场iron foundry铸铁管cast iron pipe铸铁组织图cast iron diagram铸铁组织图structural diagram of cast iron 铸造founding铸造,铸件casting铸造场smith shop圆盘砂轮机disc grinder圆套筒round bush圆条测温法bar test圆筒式炉(回转炉) drum type furance圆筒形浇桶drum ladle圆头镘刀roound nose圆形砂rounded grain圆形砂粒rounded sand云母粉mica flour云母粉mica powder运轮,台车carriage运送箱tote box运原性蒙气reducing atmosphere运原状态reducing condition杂质impurities再炽,再辉recalescence再炽点,再辉点recalescent point再处理erpreparation再处理砂reconditioned sand再负载reloading再结晶recrystallization再结晶温度recrystallization temperature 再冷却系统recooling system再黏接砂rebonded sand再热炉reheating furnace再生砂reclamation sand再生铁remelted pig iron再生铁synthetic pig iron暂垫造模法mold on an oddside凿锤chipping hammer凿刀chipping chisel凿磨浇口shagging凿平chipping凿平问chipping room凿子,凿机chipper凿子,凿机chisel造模molding造模板mold board造模板molding board造模板molding plate造模板ramming plate造模材料molding materials造模材料添加剂molding material additive造模粗砂molding gravel造模地坑molding pit造模钉molding brad(pin)造模法molding method造模工具molder's tools模工作台molder's bench造模工作台molding bench造模机molding machine造模袷度molding allowance造模区molding bay造模设备molding apparatus造模性moldability造渣剂slag forming constituent造渣期slag forming period造渣石灰slag lime造渣作业slag practice增碳carbon pick-up增碳recarburization增碳剂recarburizer增碳剂recarburizing agent增碳焦recarburization coke增压冒口,威廉氏冒口atmospheric feeder(atmsopheric riser,William's riser)增压冒口,威廉氏冒口William's riser,atmospheric riser增压砂心cracker core增压砂心pencil core增压砂心penetration core增压砂心,嵌入砂心insert core增压砂心,威廉氏砂心atmospheric core,William's core渣dirt渣比,碱度slag ratio渣阱dirt trap渣孔(铸疵) slag blowhole渣棉slag wool渣壳slag crust渣桶slag ladle渣位高slag level渣窝slag pocket轧辊,辊子roll轧屑roll[ing] scale闸喉,闸口choke闸喉式流道choked runner system闸喉作用choking粘土质耐火砖fire clay brick展性,可锻性malleability展性处理malleablising展性热处理铁矿malleable ore展性退火malleablising annealing展性铸铁(可锻铸铁) malleable cast iron展性铸铁(可锻铸铁) malleable iron展性铸铁用生铁malleable pig iron辗制硅砂artifical silica sand章鱼状石墨octopus graphite胀疤expansion scab胀模(铸疵) swell胀陷,上模剥砂(铸疵) pull down罩式炉lifting furnace遮蔽电弧熔接shielded-arc welding遮热板heat shield折旧amortization折旧depreciation折缘(黑心展性铸铁) picture frame锗(Ge) germanium真空除氧法vacuum degassing process真空精炼vacuum refining真空熔解vacuum melting真空造模法,V造模法V-process,vacuum-secaled process 真空铸造vacuum casting真离心铸造法true centrifugal casting砧anvil砧台式震实造模机anvil-jolter针对铸铁acicular cast iron针孔(铸疵),销孔pin-hole针状组织acicular structure针状组织铸铁bainite cast iron振动vibration振动捣砂vibration ramming振动分配器vibrating distributor振动器vibrator振动清箱mechanical knockout by vibration振动清箱,振动清砂处shake-out振动清箱机molding box shake-out device振动清箱机,振动清砂机shake-out machine振动清箱性能shake-out property振动清箱栅shake-out grid振动清箱栅shake-out screen振动筛jigging screen振动筛shaking screen振动筛vibrating sieve震捣jolt ramming震动jolt震动板jolting plate震动废黜模板造模机jolt molding machine with turnover plate 震动机jarring machine震动清箱吊架jointing hanger震动压挤拔模造模机jolt squeeze stripper molding machine震动压挤造模机jolt squeeze molding machine震动造模机jolt molding machine震动造模机jolter震箱清砂机flask shanker蒸馏器retort蒸馏碳retort carbon蒸气脱蜡autoclave dewaxing整流器rectifier整体模型solid pattern整体模型铸模solid pattern mold整温控制thermostattic control整缘trimming整缘模具trimming dies整缘压机trimming press正常化normalizing正常偏析normal segregation正常温度normal temperature正常折曲试验normal bend test支架(压铸),垫块packing block支台,置模台set-off bench支柱(熔铸炉) prop枝形进模口bracnch gate直尺staight edge直接电弧炉direct arc furnace直接浇口drop gate直接浇铸direct pouring直接浇铸法direct casting直接进模口direct gate直接进模口slot gate直接气压式热室压铸机(压缩空气直接压于熔液) direct pressure hot chamber machine 氧化硅基砂silica base sand氧化性蒙气oxidizing atomosphere氧化性溶解oxidizing melting氧皮铝alumite氧焰割oxycut氧乙炔熔接,气焊oxyacetylene welding样板,刮板,量具template,templet样规sizing peg摇动炉rocking furnace摇斗炉shaking lade摇台cradle窑炉kilnb趸?anti-oxidant冶金焦metallurgical coke冶金术metal technology冶金学metallurgy液化liquefaction液面花纹break surface pattern液面花纹figure液面花纹play figure液态收缩liquid contraction液态收缩liquid shrinkage液体压力计manometer液相曲线liquidus curve液相线liquidus [line]液相线liquidus line液压气动砂箱升提机构hydropneumatic flasklifting mechanism液压千斤顶hydraulic jack液压清砂铸件设备hydraulic cleaning equipment液压试验hydraulic pressure test叶轮式喷砂机turbine sand blaster一氧化碳carbon monoxide一氧化铁(FeO) iron protoxide铱(Ir) iridium移动吊车mobile crane移动皮带升降机mobile belt elevator移动式烘炉portable drying oven移动式烘模机portable mold dryer移动式可倾前炉removable clay matter移动式摔砂造模机motive type sand slinger移入shunting-in移位装置shifting facilities移装(外砂心) draw back移装砂心inset core遗传性heredity乙二醇glycol乙炔acetylene乙炔发生器acetylene generator乙炔墨acetylene black(acetylene smoke)乙炔墨acetylene smoke,acetylene black乙炔熔接acetylene welding抑制剂inhibitor易开砂箱easy off slip flask易燃物inflammable易熔合金fusible alloy异形管件specials意外防止条例accident prevention regulations溢放口flow off溢放口pop off溢放口run-off溢放口strain relief溢放冒口run-off riser溢流over flow溢流道flow through溢流口hot spruing溢流口(压铸) over flow well音波试验sonic testing阴极锈法cathodic protection阴极氧化anodic oxidation铟(In)(稀金属元素) Indium银(Ag) silver银砂(无铁质硅砂) silver sand引导顶出(压铸) guided ejection英高镍(镍铬合金) Inconel英国国家标准B.S.(British Standard)英国铸铁研究协会BCIRA(British Cast Iron Research Associatin)英国铸造工程师学会IBF(Institute of British Foundrymen,London)英制热单位(B.T.U.) British Thermal Unit应变,变形(铸疵) strain应变计strain gage应力stress应力腐蚀裂痕stress corrosion cracking应力集中stress concentration应力破坏强度stress upture strength应力消除stress relief应力应变特性stress-strain characteristics 应力应变图stresss-strain diagram樱木cherry tree荧光采伤法zyglo荧光渗透剂zyglo penetrant荧光fluorescence荧光镜fluoroscope荧光探伤法fluorescent crack detection荧光透视法(检查),荧光镜试验fluorspar 萤石(CaF2) fluorite萤石(CaF2) flushing硬点hard spot硬度hardness硬度计hardness tester硬焊brazing硬化(壳模) curing硬化,淬火hardening硬化合金hardening alloy硬化剂hardening agent硬化剂,硬化合金hardener硬化加速剂hardening accelerator硬化能,淬火性hardenability硬化深度hardness penetration硬化时间curing time硬结setting硬结砂用油setting oil硬木hardwood硬砂模型板hard sand match硬质焦炭,煤焦hard coke。
砂型铸造--外文翻译

附录附录1Sand CastingThe first stage in the production of sand castings must be the design and manufacture of a suitable pattern. Casting patterns are generally made from hard word and the pattern has to be made larger than the finished casting size to allow for the shrinkage that takes place during solidification and cooling. The extent of this shrinkage varies with the type of metal or alloy to be cast. For all but the simplest shapes the pattern will be made in two or more pieces to facilitate moulding. If a hollow casting is to be made the pattern design will include extension pieces so that spaces to accept the sand core are moulded into sand. These additional spaces in the mould are termed core prints.Sand moulds for the production of small and medium-sized castings are made in a moulding box. The mould is made in two or more parts in order that the pattern may be removed.The drag half of the mould box is placed on a flat firm board and the drag half of the pattern placed in position. Facing sand is sprinkled over the pattern and then the mould box is filled with moulding sand. The sand is rammed firmly around the pattern. This process of filling and ramming may be done by hand but mould production is automated in a large foundry with the mould boxes moving along a conveyor, firstly to be filled with sand from hoppers and then to pass under mechanical hammers for ramming. When ramming of the sand is complete, excess sand is removed to leave a smooth surface flush with the edges of the moulding box.The completed drag is now turned over and the upper, or cope, portion of the moulding box positioned over it. The cope half of the pattern is placed in position, correct alignment being ensured by means of small dowel pins. Patterns for the necessary feeder, runner and risers are also placed so as to give an even distribution of metal into the mould cavity. The risers should coincide with the highest readily escape from the mould. The sizes of risers should be such that the metal in them does not freeze too rapidly. An important function of a riser is to act as reservoir of liquid metal to feed solidification within the mould. A thin coating of dry parting sand is sprinkled into mould at this stage. This is to prevent the cope and drag stickingtogether when the cope half is moulded. The cope is now filled with moulding sand and this is rammed firmly into shape in the same manner as in the making of the drag.After the ramming of sand in the cope is completed the two halves of the moulding box are carefully separated. At this stage venting of the moulding box are carefully separated. At this stage venting of the mould can be done, if necessary, to increase the permeability of the mould. After venting the patterns are carefully removed from both cope and drag, and a gate or gates are carefully cut to connect the runner channel with the main cavity. Gates should be sited to allow for entry into mould with a minimum of turbulence. Any loose sand is gently blown away and if a core is to be used it the cope upon the drag and it is then ready for use. Liquid metal is poured smoothly into the mould via the feeder. Pouring ceases when liquid metal appears at the top of the risers and the feeder channel is also full.When the metal that has been poured into a sand mould has fully solidified the mould is broken and casting is removed. The casting still has the runner and risers attached to it and there will be sand adhering to portions of the surface. Runners and risers are cut off and returned to the melting furnace. Sand cores are broken and adherent sand is cleaned from the surface by vibration or by sand blasting with dry sand. Any fins or metal flash formed at mould parting lines are removed by grinding and the castings are then ready for inspection.EngineAn engine is a device that uses the energy in a fuel to do work. The energy in the chemicals of the fuel is turned into heat energy. The heat is then used to move the metal parts of a machine. There are many kinds of fuel. Most engines use gasoline, oil, kerosene, coal, or coke. The heat that comes from burning the fuel makes a gas expand. This expand gas drives pistons or turbine blades. The pistons or turbines turn shafts. The turning shafts move gears and other wheels. We use these rotating wheels and shafts to move automobiles, airplanes, and other transport. We can also use them for pumping, drilling, digging, and other such activities.Early engines burned coal or wood to heat water. The steam was used to drive steam engine. Until the middle of this century, most locomotives were powered by steam. At the beginning of the century, even some automobiles were run on steam. We still use steam engines, but most of them are being replaced by more efficient engines. Today we have powerful gasoline and diesel engines to work for us.The steam engine is an external combustion engine. This means that fuel iscombustion, or burned, outside the cylinder that produces power. Since the invention of the steam engine by James Watt in 1769s, steam engines had a great effect on the industrial revolution in the eighteenth century. Until the middle of the twentieth century, most locomotives were powered by steam. At the end of the century, even some automobiles were run on steam. Today most of the functions of steam engine have been taken over by internal combustion engines fueled by gasoline and diesel oil. However, there are many steam engines in use at sea. Steam is also used to generate electricity. The kind of steam engine that is used today does not have cylinders. It is generally a steam turbine. The steam turbine was invented by Sir Charles Parsons. Steam turbines can handle steam at higher pressures than piston engines can, and they are more compact than piston engines of similar power.The gasoline engine The engine of most automobiles and small vehicle use gasoline as fuel. The gasoline engine is a combustion engine. The fuel is burned in combustion (burning) chambers inside the engine. The combustion chambers are placed at one end of the cylinders. Pistons move up and down in the cylinders. They are pushed by the hot gases from the burning fuel. When the fuel is mixed with air it burns so quickly that it explodes. The combustion chambers and cylinder apart like a bomb, the explosion simply kicks hand against the head of the piston. It pushes it as far as it can.Each movement of a piston up or down in its cylinder is called a stroke. Most gasoline engines work on a four-stroke cycle. This means that each piston goes up and down twice for each explosion. That makes four movement or strokes. This cycle of events is repeated over and over again. On the first down stroke, the piston moves to the lowest part of the cylinder. A mixture of gasoline droplets and air is drawn into the cylinder above it. Now the piston moves up again. This is its second stroke. It squeezes the mixture into a small space. An electric lights the mixture, and it explodes. The piston is force down again for its third stroke. This is called the power stroke. For the fourth stroke, the piston moves to the top again. This time it pushes the burnt gases out of the cylinder. The gases leave the engine as exhaust fumes.The first engine that used the four-stroke cycle was made in about 1876. It was designed by a German engineer, August Otto. He used coal gas, not gasoline. The first engines to burn gasoline were developed by Karl Benz and Gottlieb. These two men were famous as automobile pioneers.A piston simply going up and down cannot push an automobile along. Its movement must be changed to a turning movement. To do this, a crankshaft is used. Each pistonof the engine is linked to part of the crankshaft. Each push it gives makes the shaft turn. The spinning shaft passes the power on to the automobile’s transmission system. It usually does this through a heavy flywheel. The transmission system transmits power to the clutch and to the propeller shaft, through a gearbox. The propeller shaft drives the road wheels by means of axles.To keep an automobile engine going, there need to be several systems. There must be a fuel system. This has to supply gasoline to the engine cylinders in the right amounts. It has also to mix it with the right amount of air, so that it will explode properly. There must be an ignition system. This has to provide sparks to ignite the explosive mixture fat exactly the right time. There has to be a cooling system, otherwise the engine would overheat. The lubrication system must keep all the moving parts oiled and moving freely. Too much friction causes wear of the metal and makes the engine overheat.The engine unit Gasoline engine has two basic parts. They are called the cylinder head and the cylinder block. The cylinder block is machined from solid metal. The metals usually cast side the cylinder blocks are the cylinders. The walls of the cylinders have to be very accurately made, and are highly polished. The pistons that move up and down in the cylinders must be accurately made, too. They have springy bands of metal around them to press tight against the cylinder walls and stop gases leaking. The bands are called piston rings. They are often made of aluminum alloy for strength and lightness.An engine may have any number of cylinders. They may be arranged in a line, or in opposite pairs. They are often arranged in a “V” shape. In many airplanes with piton engines, the cylinders are arranged in a ring around the crankshaft.The lower part of the cylinder block is called the crankcase. This is where the crankshaft lies. The crank shaft is linked to each piton by a connecting rod. The crankshaft is made in a single piece. It must be tough and accurately machined. It may spin as many as 6000 times a minute. It changes up-and-down motion. It does this by means of cranks, one for each piston. The cranks are set at different angles round the shaft. Each piston gives a push to its crank during its power stroke. During the other three strokes, the crank pushes the piston up ,down and up again. The heavy flywheel is bolted to one end of the crankshaft. It keeps the shaft turning smoothly between the power strokes. Strong main bearings support the crankshaft in its case.The cylinder head is bolted to the cylinder block. Inside it are the combustion chambers. Each combustion chamber is a space above a piston inside a cylinder. Thisis where the explosion of the mixture of fuel and air takes place. A spark plug is set into the top of the chamber. Each chamber has a pair of valves. There is an inlet valve to allow the fuel and air mixture into the chamber. The other valve is an outlet or exhaust valve. Through this pass the burnt gases after the explosion. The valves are opened and closed by push rods and springs. The push rods are moved up and down by links with the crankshaft. The linkage is through a turning shaft called the camshaft.To carry water to cool the engine, there are passages in the metal of the cylinder head and cylinder block. Oil passes through other passages. Between the cylinder head and block is a gasket.This is a thin plate of metal that acts as a seal. It is put in when the parts of the engine are bolted together. It is often made of copper.The fuel system Fuel system of the engine supplies the gasoline to be burnt. The gasoline is stored in a large tank. In a powerful car, the tank holds many gallons of fuel. The tank is placed well away from the engine, to reduce the risk of fire .The gasoline is pumped through a fuel line. The pump may be driven by links with the engine camshaft. Sometimes it has its own electric motor. Before the gasoline reaches the cylinders, it must be mixed with air. The fuel line leads to the carburetor. In the carburetor the gasoline is forced through a fine nozzle, or jet. It forms a spray of small droplets. The droplets vaporize as they mix with the air. Now the mixture is ready for ignition.The speed of the engine is controlled by a valve. Opening and closing the throttle valve regulates the amount of mixture leaving the carburetor. From the carburetor the mixture passes to the inlet valves of the combustion chambers. The mixture is delivered through a set of tubes called the inlet manifold. A similar set of tubes takes away exhaust gases form the exhaust valves of the combustion chambers. This is called the exhaust manifold. It leads to the outside air through the exhaust pipe.In some automobiles, the fuel is delivered by a different system. Instead of passing through a carburetor, the fuel is sprayed into the air stream just before the inlet valves. It is sprayed in small amounts, which are carefully metered. The system is called fuel injection.The ignition system Mixture inside each cylinder must be made to explode. A spark is used to do this. The spark must jump across the gap in the spark plug at exactly the right times, each of the autombile’s cylinders must fire in turn. The ignition system depends upon very accurate timing. If the sparks are a fraction of asecond too early or too late, the engine will not run properly.The electricity to make the sparks comes from the automobile’s electric storage battery. This battery is kept charged by a dynamo, or generator, run by the engine. The battery supplies electricity at only about 12 volts. To make a spark, volts are required. The voltage from the battery is boosted up to about 30 000 volts by means of a transformer. The transformer is called the ignition coil. The ignition coil supplies high voltage to the distributor. This is a device that distributes in surges, or pulses, to each of the spark plugs in turn. When a surge of electricity at high voltage reaches a plug, a spark leaps across a small gap. The spark is so hot that it makes the mixture of gasoline and air ignite and explode.The cooling system Heat produced by burning the gasoline in the engine is very great. The temperature inside each combustion chamber may reach more than 1 000℃ [over1 800].The engine must be constantly cooled. The cooling system supplies cool water through channels called water jack. The water jackets surround the cylinders. They carry away the excess heat as the water passes through them. The hot water is led away to be cooled in radiator. The radiator is a system of many tubes, linked together, with spaces between them. The hot water loses its heat to the air. The cooled water is then pumped to the engine again.Some automobiles do not have a water-cooled system. They use air cooling. Air from the frontOf the automobile is blown over the cylinder block and the cylinder head. The engine is filled with special cooling fins, sticking out into the air stream. These help the head to radiate more quickly. Air-cooled engines tend to be noisier than water-cooled engines. In a water-cooled engine, the water jacket helps to absorb the engine noise.To prevent the water in the cooling system from freezing in cool weather, antifreeze is usually added in water. This is often ethylene glycol or a similar compound.The lubrication system Oil is needed to keep the engine’s parts from wearing too quickly. A storage tank of oil, called the sump, is attached under the crankcase. The oil is pumped through channels to all the main bearings and the big-end bearings. Eventually it reaches the sump again. It passes through a filter to remove dirt before it is used again. Whenever metal surfaces rub against others, ting particles are worn off. The oil picks them up as it flows between the surfaces .They are trapped by the oil filter. The filter must be changed regularly. The oil itself gradually burns and becomes impure. It must be replaced at intervals.The wankel engine The wankel engine is a gasoline engine that works without pistons. It was invented in Germany by Felix Wankel. He started development of it in 1956. The pistons in an ordinary gasoline engine must move up and down, or backwards and forwards. This kind of motion is called reciprocating motion. It needs to be converted into a turning motion (rotary motion) by a crankshaft. In a Wankel engine, burning the flue produces a rotary motion directly. These is no need for a crank shaft, It is a rotary engine.A Wankel engine has a specially designed combustion chamber. It is roughly an ellipse, , I n shape. Inside is rotor. The rotor is shaped with bulging, rounded sides. Though the center of the rotor passes the driving shaft, it has teeth like a gearwheel that meet teeth inside the rotor. The rotor is shaped so that its corners just touch the walls of the chamber. The rotor can move up and down and also side to side as it turns.The rotor divides the chamber into three parts. As the rotor the shapes of the three parts change. They act like three separate combustion chambers. As in an ordinary engine, there are spark plugs, an inlet port for the gasoline and air mixture, and an outlet port for the exhaust gases.The rotor turns so that each part of chamber in turn meets the inlet. The gasoline and air mixture is drawn in. This is like the first piston down stroke of an ordinary engine. Further turning sweeps the mixture round into a smaller space .The mixture is compressed. This is like the second stroke. Now the spark plugs fires. The explosion drives the rotor further around. This is the power stroke. When the rotor has turned a little further, the exhaust gases are pushed from the chamber through the exhaust port. The process is continuous. It happens as each part of the chamber sweeps round. The Wankel engine has several advantages over an ordinary engine. It has fewer moving parts. There is less vibration. It is lighter, it costs less to produce. However, there are difficulties. The main difficulty is ensuring that the seals, where the corners of the rotor meet the chamber walls, are gastight. The Wankel engine is used successfully in several kinds of automobile.The diesel engine The diesel engine is a type of internal combustion engine that is used for heavy-duty work. It uses low-cost oil for fuel, and usually has a long life. Railroad locomotives, trail trucks, buss, tractors, and road building equipment are powered by diesel engine .Ships and electric power generating stations also use diesel engine. Small models are used to power some automobiles. The diesel engine was developed in 1897 by Rudolf Diesel.The diesel engine differs from the gasoline engine in two main ways. The diesel is a compression-ignition engine, whereas the gasoline engine is a spark-ignition engine. In a diesel engine, air is compressed in each cylinder, causing its temperatures to rise. Fuel is then injected into the cylinders. The heat of the air causes the mixture to ignite and to explode. Gasoline engines use electric sparks to ignite the fuel and air mixture in the cylinders. Diesel engines use low grade oils that require less refining than gasoline and are less expensive.Pressure of over 10500 KN per square meter [1500 lbs per square in] is built up in the cylinder of a diesel engine by compression and the subsequent explosion, or combustion. This pressure forces the piston downwards, which turns the crankshaft. Cylinder walls and most other parts of diesel engines are thicker and stronger than those parts in gasoline engines so they can stand the extra strains and stresses. There are two main types of diesel engines, the four-stroke engine and the two-stroke engine. In the four-stroke model, which is the larger and more powerful of the two, each moves down, up, down, and up to complete a cycle. The first down stroke draws air into the cylinder. The second down stroke is the power stroke .The second up stoke exhaust the gases produced by combustion.In a two-stroke diesel engine, the exhaust and intake of air occur though openings in the cylinder near the end of the power stroke. The one up stoke is the compression stroke. The down stoke is the power stroke. Two-stroke engines have twice as many power stroke recycle as four-stroke engines. Two-stroke engines are used for applications that require high power in a small engine.……附录2砂型铸造砂型铸造生产的第一步是设计并制作一个合适的模型。
压铸模具术语中英文对照

压铸模具英文对照压力铸造:die casting压铸模具:die-casting die定模:fixed die动模:moving die型腔:cavity分型面:parting line投影面积:project area收缩率:shrinkage锁模力:locking force压力中心:pressure centre充填速度:filling velocity压射速度:injection speed压射比压:injection pressure脱模斜度:draft闭合高度:die shut height最大开距:maximum opening daylight脱模距:stripper distance浇注系统:casting system直浇道:sprue横浇道:runner内浇口:gate溢流槽:overflow well排气槽:air vent定模座板:clamping plate of the fixed half 动模座板:clamping plate of the moving half 定模套板:bolster of the fixed half动模套板:bolster of the moving half支承板:support plat垫块:space block支承柱:support pillar型芯:core活动型芯:movable core螺纹型芯:threaded plug螺纹型环:threaded ring镶块:die insert定模镶块:die insert of the fixed half动模镶块:die insert of the moving half活动镶块:movable insert拼块:split斜销:angle pin弯销:angular cam滑块:slide 型芯滑块:core slide斜滑块:angled sliding split斜槽导板:finger guide plate限位块:stop block楔紧块:wedge block滑块导板:slide guide plate耐磨板:wear pad浇口套:sprue bush分流锥:sprue spreader导流块:baffle排气塞:venting plug排气板:venting plate导柱:guide pillar带头导柱:headed guide pillar带肩导柱:shouldered guide pillar矩形导柱:square guide pillar推板导柱:ejector guide pillar导套:guide bush直导套:straight guide bush带头导套:headed guide bush推板导套:ejector guide bush导板:guide plate推杆:ejector pin圆柱头推杆:ejector pin with a cylindrical head带肩推杆:shouldered ejector pin扁推杆:plat ejector pin成型推杆:forming ejector pin推管:ejector sleecve带肩推管:shouldered ejector sleeve推块:ejector pad推件板:stipping plate推杆固定板:ejector retaining plate推板:ejector plate限位钉:stop pin连接推杆:ejector tie rod推板连接推杆:ejector plate tie rod推板垫圈:ejector plate washer定位元件:locating element冷却环:cooling ring拉料杆:sprue puller pin隔流板:plug bffe。
注塑模具设计技术中英文对照外文翻译文献
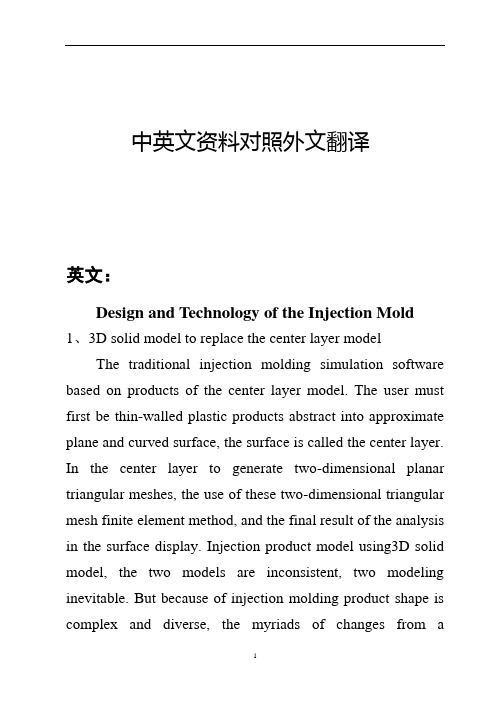
中英文资料对照外文翻译英文:Design and Technology of the Injection Mold1、3D solid model to replace the center layer modelThe traditional injection molding simulation software based on products of the center layer model. The user must first be thin-walled plastic products abstract into approximate plane and curved surface, the surface is called the center layer. In the center layer to generate two-dimensional planar triangular meshes, the use of these two-dimensional triangular mesh finite element method, and the final result of the analysis in the surface display. Injection product model using3D solid model, the two models are inconsistent, two modeling inevitable. But because of injection molding product shape is complex and diverse, the myriads of changes from athree-dimensional entity, abstraction of the center layer is a very difficult job, extraction process is very cumbersome and time-consuming, so the design of simulation software have fear of difficulty, it has become widely used in injection molding simulation software the bottleneck.HSCAE3D is largely accepted3D solid / surface model of the STL file format. Now the mainstream CAD/CAM system, such as UG, Pro/ENGINEER, CATIA and SolidWorks, can output high quality STL format file. That is to say, the user can use any commercial CAD/CAE systems to generate the desired products3D geometric model of the STL format file, HSCAE3D can automatically add the STL file into a finite element mesh model, through the surface matching and introduction of a new boundary conditions to ensure coordination of corresponding surface flow, based on3D solid model of analysis, and display of three-dimensional analysis results, replacing the center layer simulation technology to abstract the center layer, and then generate mesh this complicated steps, broke through system simulation application bottlenecks, greatly reducing the burden of user modeling, reduces the technical requirement of the user, the user training time from the past few weeks shorter for a fewhours. Figure 1 is based on the central layer model and surface model based on 3D solid / flow analysis simulation comparison chart.2、Finite element, finite difference, the control volume methodsInjection molding products are thin products, products in the thickness direction of size is much smaller than the other two dimensions, temperature and other physical quantities in the thickness direction of the change is very large, if the use of a simple finite element and finite difference method will cause analysis time is too long, can not meet the actual needs of mold design and manufacturing. We in the flow plane by using finite element method, the thickness direction by using finite difference method, were established and plane flow and thickness directions corresponding to the size of the grid and coupling, while the accuracy is guaranteed under the premise of the calculation speed to meet the need of engineering application, and using the control volume method is solved. The moving boundary problem in. For internal and external correspondence surface differences between products, can be divided into two parts the volume, and respectively formed the control equation, the junction of interpolation to ensure thatthe two part harmony contrast.3、Numerical analysis and artificial intelligence technologyOptimization of injection molding process parameters has been overwhelming majority of mold design staff concerns, the traditional CAE software while in computer simulation of a designated under the conditions of the injection molding conditions, but is unable to automatically optimize the technical parameters. Using CAE software personnel must be set to different process conditions were multiple CAE analysis, combined with practical experience in the program were compared between, can get satisfactory process scheme. At the same time, the parts after the CAE analysis, the system will generate a large amount of information about the project ( product, process, analyzes the results ), which often results in a variety of data form, requiring the user to have the analysis and understanding of the results of CAE analysis ability, so the traditional CAE software is a kind of passive computational tools, can provide users with intuitionistic, effective engineering conclusion, to software users demand is too high, the influence of CAE system in the larger scope of application and popularization. In view of the above, HSCAE3D software in the original CAE system based on accurate calculationfunction, the knowledge engineering technology is introduced the system development, the use of artificial intelligence is the ability of thinking and reasoning, instead of the user to complete a large number of information analysis and processing work, directly provide guiding significance for the process of conclusions and recommendations, effectively solve the CAE of the complexity of the system and the requirements of the users of the contradiction between, shortening of the CAE system and the distance between the user, the simulation software by traditional " passive" computational tools to " active" optimization system. HSCAE3D system artificial intelligence technology will be applied to the initial design, the results of the analysis of CAE interpretation and evaluation, improvement and optimization analysis of3 aspects.译文:注塑模具设计的技术1.用三维实体模型取代中心层模型传统的注塑成形仿真软件基于制品的中心层模型。
模具的发展外文文献翻译、中英文翻译、外文翻译
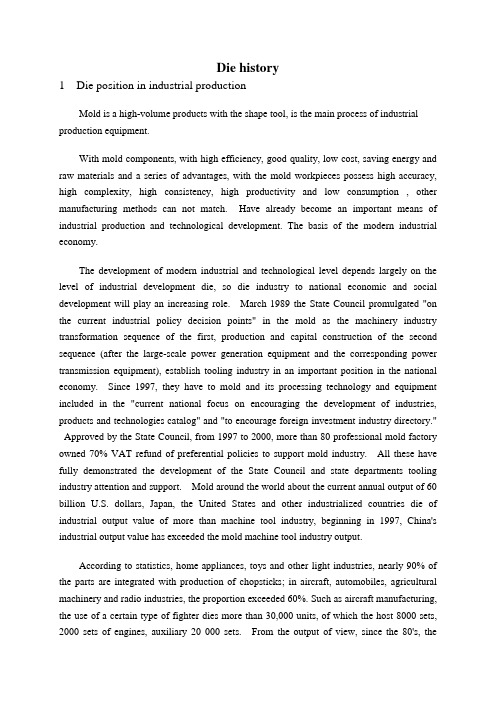
Die history1 Die position in industrial productionMold is a high-volume products with the shape tool, is the main process of industrial production equipment.With mold components, with high efficiency, good quality, low cost, saving energy and raw materials and a series of advantages, with the mold workpieces possess high accuracy, high complexity, high consistency, high productivity and low consumption , other manufacturing methods can not match. Have already become an important means of industrial production and technological development. The basis of the modern industrial economy.The development of modern industrial and technological level depends largely on the level of industrial development die, so die industry to national economic and social development will play an increasing role. March 1989 the State Council promulgated "on the current industrial policy decision points" in the mold as the machinery industry transformation sequence of the first, production and capital construction of the second sequence (after the large-scale power generation equipment and the corresponding power transmission equipment), establish tooling industry in an important position in the national economy. Since 1997, they have to mold and its processing technology and equipment included in the "current national focus on encouraging the development of industries, products and technologies catalog" and "to encourage foreign investment industry directory." Approved by the State Council, from 1997 to 2000, more than 80 professional mold factory owned 70% VAT refund of preferential policies to support mold industry. All these have fully demonstrated the development of the State Council and state departments tooling industry attention and support. Mold around the world about the current annual output of 60 billion U.S. dollars, Japan, the United States and other industrialized countries die of industrial output value of more than machine tool industry, beginning in 1997, China's industrial output value has exceeded the mold machine tool industry output.According to statistics, home appliances, toys and other light industries, nearly 90% of the parts are integrated with production of chopsticks; in aircraft, automobiles, agricultural machinery and radio industries, the proportion exceeded 60%. Such as aircraft manufacturing, the use of a certain type of fighter dies more than 30,000 units, of which the host 8000 sets, 2000 sets of engines, auxiliary 20 000 sets. From the output of view, since the 80's, theUnited States, Japan and other industrialized countries die industry output value has exceeded the machine tool industry, and there are still rising. Production technology, according to the International Association predicts that in 2000, the product best pieces of rough 75%, 50% will be finished mold completed; metals, plastics, ceramics, rubber, building materials and other industrial products, most of the mold will be completed in more than 50% metal plates, more than 80% of all plastic products, especially through the mold into.2 The historical development of moldThe emergence of mold can be traced back thousands of years ago, pottery and bronze foundry, but the large-scale use is with the rise of modern industry and developed.The 19th century, with the arms industry (gun's shell), watch industry, radio industry, dies are widely used. After World War II, with the rapid development of world economy, it became a mass production of household appliances, automobiles, electronic equipment, cameras, watches and other parts the best way. From a global perspective, when the United States in the forefront of stamping technology - many die of advanced technologies, such as simple mold, high efficiency, mold, die and stamping the high life automation, mostly originated in the United States; and Switzerland, fine blanking, cold in Germany extrusion technology, plastic processing of the Soviet Union are at the world advanced. 50's, mold industry focus is based on subscriber demand, production can meet the product requirements of the mold. Multi-die design rule of thumb, reference has been drawing and perceptual knowledge, on the design of mold parts of a lack of real understanding of function. From 1955 to 1965, is the pressure processing of exploration and development of the times - the main components of the mold and the stress state of the function of a mathematical sub-bridge, and to continue to apply to on-site practical knowledge to make stamping technology in all aspects of a leap in development. The result is summarized mold design principles, and makes the pressure machine, stamping materials, processing methods, plum with a structure, mold materials, mold manufacturing method, the field of automation devices, a new look to the practical direction of advance, so that pressing processing apparatus capable of producing quality products from the first stage.Into the 70's to high speed, launch technology, precision, security, development of the second stage. Continue to emerge in this process a variety of high efficiency, business life, high-precision multi-functional automatic school to help with. Represented by the number of working places as much as other progressive die and dozens of multi-station transferstation module. On this basis, has developed both a continuous pressing station there are more slide forming station of the press - bending machine. In the meantime, the Japanese stand to the world's largest - the mold into the micron-level precision, die life, alloy tool steel mold has reached tens of millions of times, carbide steel mold to each of hundreds of millions of times p minutes for stamping the number of small presses usually 200 to 300, up to 1200 times to 1500 times. In the meantime, in order to meet product updates quickly, with the short duration (such as cars modified, refurbished toys, etc.) need a variety of economic-type mold, such as zinc alloy die down, polyurethane rubber mold, die steel skin, also has been very great development.From the mid-70s so far can be said that computer-aided design, supporting the continuous development of manufacturing technology of the times. With the precision and complexity of mold rising, accelerating the production cycle, the mold industry, the quality of equipment and personnel are required to improve. Rely on common processing equipment, their experience and skills can not meet the needs of mold. Since the 90's, mechanical and electronic technologies in close connection with the development of NC machine tools, such as CNC wire cutting machine, CNC EDM, CNC milling, CNC coordinate grinding machine and so on. The use of computer automatic programming, control CNC machine tools to improve the efficiency in the use and scope. In recent years, has developed a computer to time-sharing by the way a group of direct management and control of CNC machine tools NNC system.With the development of computer technology, computers have gradually into the mold in all areas, including design, manufacturing and management. International Association for the Study of production forecasts to 2000, as a means of links between design and manufacturing drawings will lose its primary role. Automatic Design of die most fundamental point is to establish the mold standard and design standards. To get rid of the people of the past, and practical experience to judge the composition of the design center, we must take past experiences and ways of thinking, for series, numerical value, the number of type-based, as the design criteria to the computer store. Components are dry because of mold constitutes a million other differences, to come up with a can adapt to various parts of the design software almost impossible. But some products do not change the shape of parts, mold structure has certain rules, can be summed up for the automatic design of software. If a Japanese company's CDM system for progressive die design and manufacturing, including the importation of parts of the figure, rough start, strip layout, determine the size and standardtemplates, assembly drawing and parts, the output NC program (for CNC machining Center and line cutting program), etc., used in 20% of the time by hand, reduce their working hours to 35 hours; from Japan in the early 80s will be three-dimensional cad / cam system for automotive panel die. Currently, the physical parts scanning input, map lines and data input, geometric form, display, graphics, annotations and the data is automatically programmed, resulting in effective control machine tool control system of post-processing documents have reached a high level; computer Simulation (CAE) technology has made some achievements. At high levels, CAD / CAM / CAE integration, that data is integrated, can transmit information directly with each other. Achieve network. Present. Only a few foreign manufacturers can do it.3 China's mold industry and its development trendDue to historical reasons for the formation of closed, "big and complete" enterprise features, most enterprises in China are equipped with mold workshop, in factory matching status since the late 70s have a mold the concept of industrialization and specialization of production. Production efficiency is not high, poor economic returns. Mold production industry is small and scattered, cross-industry, capital-intensive, professional, commercial and technical management level are relatively low.According to incomplete statistics, there are now specialized in manufacturing mold, the product supporting mold factory workshop (factory) near 17 000, about 600 000 employees, annual output value reached 20 billion yuan mold. However, the existing capacity of the mold and die industry can only meet the demand of 60%, still can not meet the needs of national economic development. At present, the domestic needs of large, sophisticated, complex and long life of the mold also rely mainly on imports. According to customs statistics, in 1997 630 million U.S. dollars worth of imports mold, not including the import of mold together with the equipment; in 1997 only 78 million U.S. dollars export mold. At present the technological level of China Die & Mould Industry and manufacturing capacity, China's national economy in the weak links and bottlenecks constraining sustainable economic development.3.1 Research on the Structure of industrial products moldIn accordance with the division of China Mould Industry Association, China mold is divided into 10 basic categories, which, stamping die and plastic molding two categoriesaccounted for the main part. Calculated by output, present, China accounts for about 50% die stamping, plastic molding die about 20%, Wire Drawing Die (Tool) about 10% of the world's advanced industrial countries and regions, the proportion of plastic forming die die general of the total output value 40%.Most of our stamping die mold for the simple, single-process mode and meet the molds, precision die, precision multi-position progressive die is also one of the few, die less than 100 million times the average life of the mold reached 100 million times the maximum life of more than accuracy 3 ~ 5um, more than 50 progressive station, and the international life of the die 600 million times the highest average life of the die 50 million times compared to the mid 80s at the international advanced level.China's plastic molding mold design, production technology started relatively late, the overall level of low. Currently a single cavity, a simple mold cavity 70%, and still dominant.A sophisticated multi-cavity mold plastic injection mold, plastic injection mold has been able to multi-color preliminary design and manufacturing. Mould is about 80 million times the average life span is about, the main difference is the large deformation of mold components, excess burr side of a large, poor surface quality, erosion and corrosion serious mold cavity, the mold cavity exhaust poor and vulnerable such as, injection mold 5um accuracy has reached below the highest life expectancy has exceeded 20 million times, the number has more than 100 chamber cavity, reaching the mid 80s to early 90s the international advanced level.3.2 mold Present Status of TechnologyTechnical level of China's mold industry currently uneven, with wide disparities. Generally speaking, with the developed industrial countries, Hong Kong and Taiwan advanced level, there is a large gap.The use of CAD / CAM / CAE / CAPP and other technical design and manufacture molds, both wide application, or technical level, there is a big gap between both. In the application of CAD technology design molds, only about 10% of the mold used in the design of CAD, aside from drawing board still has a long way to go; in the application of CAE design and analysis of mold calculation, it was just started, most of the game is still in trial stages and animation; in the application of CAM technology manufacturing molds, first, the lack of advanced manufacturing equipment, and second, the existing process equipment (including the last 10 years the introduction of advanced equipment) or computer standard(IBM PC and compatibles, HP workstations, etc.) different, or because of differences in bytes, processing speed differences, differences in resistance to electromagnetic interference, networking is low, only about 5% of the mold manufacturing equipment of recent work in this task; in the application process planning CAPP technology, basically a blank state, based on the need for a lot of standardization work; in the mold common technology, such as mold rapid prototyping technology, polishing, electroforming technologies, surface treatment technology aspects of CAD / CAM technology in China has just started. Computer-aided technology, software development, is still at low level, the accumulation of knowledge and experience required. Most of our mold factory, mold processing equipment shop old, long in the length of civilian service, accuracy, low efficiency, still use the ordinary forging, turning, milling, planing, drilling, grinding and processing equipment, mold, heat treatment is still in use salt bath, box-type furnace, operating with the experience of workers, poorly equipped, high energy consumption. Renewal of equipment is slow, technological innovation, technological progress is not much intensity. Although in recent years introduced many advanced mold processing equipment, but are too scattered, or not complete, only about 25% utilization, equipment, some of the advanced functions are not given full play.Lack of technology of high-quality mold design, manufacturing technology and skilled workers, especially the lack of knowledge and breadth, knowledge structure, high levels of compound talents. China's mold industry and technical personnel, only 8% of employees 12%, and the technical personnel and skilled workers and lower the overall skill level. Before 1980, practitioners of technical personnel and skilled workers, the aging of knowledge, knowledge structure can not meet the current needs; and staff employed after 80 years, expertise, experience lack of hands-on ability, not ease, do not want to learn technology. In recent years, the brain drain caused by personnel not only decrease the quantity and quality levels, and personnel structure of the emergence of new faults, lean, make mold design, manufacturing difficult to raise the technical level.3.3 mold industry supporting materials, standard parts of present conditionOver the past 10 years, especially the "Eighth Five-Year", the State organization of the ministries have repeatedly Material Research Institute, universities and steel enterprises, research and development of special series of die steel, molds and other mold-specific carbide special tools, auxiliary materials, and some promotion. However, due to the quality is notstable enough, the lack of the necessary test conditions and test data, specifications and varieties less, large molds and special mold steel and specifications are required for the gap. In the steel supply, settlement amount and sporadic users of mass-produced steel supply and demand contradiction, yet to be effectively addressed. In addition, in recent years have foreign steel mold set up sales outlets in China, but poor channels, technical services support the weak and prices are high, foreign exchange settlement system and other factors, promote the use of much current.Mold supporting materials and special techniques in recent years despite the popularization and application, but failed to mature production technology, most still also in the exploratory stage tests, such as die coating technology, surface treatment technology mold, mold guide lubrication technology Die sensing technology and lubrication technology, mold to stress technology, mold and other anti-fatigue and anti-corrosion technology productivity has not yet fully formed, towards commercialization. Some key, important technologies also lack the protection of intellectual property.China's mold standard parts production, the formation of the early 80s only small-scale production, standardization and standard mold parts using the coverage of about 20%, from the market can be assigned to, is just about 30 varieties, and limited to small and medium size. Standard punch, hot runner components and other supplies just the beginning, mold and parts production and supply channels for poor, poor accuracy and quality.3.4 Die & Mould Industry Structure in Industrial OrganizationChina's mold industry is relatively backward and still could not be called an independent industry. Mold manufacturer in China currently can be divided into four categories: professional mold factory, professional production outside for mold; products factory mold factory or workshop, in order to supply the product works as the main tasks needed to die; die-funded enterprises branch, the organizational model and professional mold factory is similar to small but the main; township mold business, and professional mold factory is similar. Of which the largest number of first-class, mold production accounts for about 70% of total output. China's mold industry, decentralized management system. There are 19 major industry sectors manufacture and use of mold, there is no unified management of the department. Only by China Die & Mould Industry Association, overall planning, focus on research, cross-sectoral, inter-departmental management difficulties are many.Mold is suitable for small and medium enterprises organize production, and our technical transformation investment tilted to large and medium enterprises, small and medium enterprise investment mold can not be guaranteed. Including product factory mold shop, factory, including, after the transformation can not quickly recover its investment, or debt-laden, affecting development.Although most products factory mold shop, factory technical force is strong, good equipment conditions, the production of mold levels higher, but equipment utilization rate.Price has long been China's mold inconsistent with their value, resulting in mold industry "own little economic benefit, social benefit big" phenomenon. "Dry as dry mold mold standard parts, standard parts dry as dry mold with pieces of production. Dry with parts manufactured products than with the mold" of the class of anomalies exist.4 Die trend4.1 mold CAD / CAE / CAM being integrated, three-dimensional, intelligent and network direction(1) mold software features integratedDie software features of integrated software modules required relatively complete, while the function module using the same data model, in order to achieve Syndicated news management and sharing of information to support the mold design, manufacture, assembly, inspection, testing and production management of the entire process to achieve optimal benefits. Series such as the UK Delcam's software will include a surface / solid geometric modeling, engineering drawing complex geometry, advanced rendering industrial design, plastic mold design expert system, complex physical CAM, artistic design and sculpture automatic programming system, reverse engineering and complex systems physical line measurement systems. A higher degree of integration of the software includes: Pro / ENGINEER, UG and CATIA, etc.. Shanghai Jiaotong University, China with finite element analysis of metal plastic forming systems and Die CAD / CAM systems; Beijing Beihang Haier Software Ltd. CAXA Series software; Jilin Gold Grid Engineering Research Center of the stamping die mold CAD / CAE / CAM systems .(2) mold design, analysis and manufacture of three-dimensionalTwo-dimensional mold of traditional structural design can no longer meet modern technical requirements of production and integration. Mold design, analysis, manufacturing three-dimensional technology, paperless software required to mold a new generation of three-dimensional, intuitive sense to design the mold, using three-dimensional digital model can be easily used in the product structure of CAE analysis, tooling manufacturability evaluation and CNC machining, forming process simulation and information management and sharing. Such as Pro / ENGINEER, UG and CATIA software such as with parametric, feature-based, all relevant characteristics, so that mold concurrent engineering possible. In addition, Cimatran company Moldexpert, Delcam's Ps-mold and Hitachi Shipbuilding of Space-E/mold are professional injection mold 3D design software, interactive 3D cavity, core design, mold base design configuration and typical structure . Australian company Moldflow realistic three-dimensional flow simulation software MoldflowAdvisers been widely praised by users and applications. China Huazhong University of Science have developed similar software HSC3D4.5F and Zhengzhou University, Z-mold software. For manufacturing, knowledge-based intelligent software function is a measure of die important sign of advanced and practical one. Such as injection molding experts Cimatron's software can automatically generate parting direction based parting line and parting surface, generate products corresponding to the core and cavity, implementation of all relevant parts mold, and for automatically generated BOM Form NC drilling process, and can intelligently process parameter setting, calibration and other processing results.(3) mold software applications, networking trendWith the mold in the enterprise competition, cooperation, production and management, globalization, internationalization, and the rapid development of computer hardware and software technology, the Internet has made in the mold industry, virtual design, agile manufacturing technology both necessary and possible. The United States in its "21st Century Manufacturing Enterprise Strategy" that the auto industry by 2006 to achieve agile manufacturing / virtual engineering solutions to automotive development cycle shortened from 40 months to 4 months.4.2 mold testing, processing equipment to the precise, efficient, and multi-direction(1) mold testing equipment more sophisticated, efficientSophisticated, complex, large-scale mold development, testing equipment have become increasingly demanding. Precision Mould precision now reached 2 ~ 3μm, more domestic manufacturers have to use Italy, the United States, Japan and other countries in the high-precision coordinate measuring machine, and with digital scanning. Such as Dongfeng Motor Mould Factory not only has the capacity 3250mm ×3250mm Italian coordinate measuring machine, also has a digital photography optical scanner, the first in the domestic use of digital photography, optical scanning as a means of spatial three-dimensional access to information, enabling the establishment from the measurement of physical → model output of engineering drawings → → the whole process of mold making, reverse engineering a successful technology development and applications. This equipment include: second-generation British Renishaw high-speed scanners (CYCLON SERIES2) can be realized and contact laser probe complementary probe, laser scanner accuracy of 0.05mm, scanning probe contact accuracy of 0.02 mm. Another German company GOM ATOS portable scanners, Japan Roland's PIX-30, PIX-4 desktop scanner and the United Kingdom Taylor Hopson's TALYSCAN150 multi-sensor, respectively Three-dimensional scanner with high speed, low-cost and functional composite and so on.(2) CNC EDMJapan Sodick linear motor servo drive using the company's AQ325L, AQ550LLS-WEDM have driven fast response, transmission and high positioning accuracy, the advantages of small thermal deformation. Switzerland Chanmier company NCEDM with P-E3 adaptive control, PCE energy control and automatic programming expert systems. Others also used the powder mixed EDM machining technology, micro-finishing pulse power and fuzzy control (FC) technologies.(3) high-speed milling machine (HSM)Milling is an important means of cavity mold. The low-temperature high-speed milling with the workpiece, cutting force is small, smooth processing, processing quality, processing efficiency (for the general milling process 5 to 10 times) and can process hard materials (<60HRC) and many other advantages. Thus in the mold processing more and more attention. Ruishikelang company UCP710-type five-axis machining center, machine tool positioning accur acy up to 8μm, home-made closed-loop vector control spindle with a maximum speed 42000r/min. Italy RAMBAUDI's high-speed milling, the processing range of up to 2500mm ×5000mm ×1800mm, speed up 20500r/min, cutting feed speed of20m/min. HSM generally used large, medium-sized mold, such as motor cover mold, die casting mold, large plastic surface machining, the surface precision up to 0.01mm.4. 3 rapid economic modeling techniquesShorten the product development cycle is an effective means of market competition to win one. Compared with the traditional mold process, fast economic modeling technology is a short molding cycle, the characteristics of low cost, precision, and life can meet the production needs, overall economic efficiency is more significant in the mold manufacturing technology, specifically the following main technology.(1) Rapid prototyping and manufacturing (RPM). It consists of three-dimensional laser lithography (SLA); laminated profile manufacturing (LOM); laser powder sintering prototyping (SLS); Fused Deposition Molding (FDM) and three-dimensional printing forming technology (3D-P) and so on.(2)The surface forming tooling. It refers to the use of spray, chemical corrosion, electroforming and new method for the formation of the cavity surface and a fine pattern technology.(3) Casting forming tooling. There are bismuth tin alloy tooling, zinc alloy tooling, resin composite forming technology and silicon rubber mold molding technology.(4) Cold extrusion mold technology and ultra-molded shapes.(5) Multi-point forming technology.(6) KEVRON steel blanking blanking tooling.(7) Mold blank rapid manufacturing technology. Mainly dry sand Mold Casting, Vacuum Mold Casting, Resin Sand Mold Casting Lost Wax Casting, and other technologies.(8) Other aspects of technology. Such as the use of nitrogen gas spring pressure side, discharge, quick die technology, stamping unit technology, and cutting edge technology and solid surfacing edge inserts die casting technology.4.4 mold materials and surface treatment technology developed rapidly。
模具设计模具热处理中英文对照外文翻译文献

中英文对照外文翻译Heat Treatment of Die and Mould Oriented Concurrent DesignAbstract:Many disadvantages exist in the traditional die design method which belongs to serial pattern. It is well known that heat treatment is highly important to the dies. A new idea of concurrent design for heat treatment process of die and mould was developed in order to overcome the existent shortcomings of heat treatment process. Heat treatment CAD/CAE was integrated with concurrent circumstance and the relevant model was built. These investigations can remarkably improve efficiency, reduce cost and ensure quality of R and D for products.Key words :die design; heat treatment; mouldong desires for precision,service life,development period and cost,modern die and mould should be designed and manufactured perfectly.Therefore more and more advanced technologies and innovations have been applied,for example,concurrent engineering,agile manufacturing virtual manufacturing,collaborative design,etc.Heat treatment of die and mould is as important as design,manufacture and assembly because it has a vital effect on manufacture,assembly and service life.Design and manufacture of die and mould have progressed rapidly,but heat treatment lagged seriously behind them.As die and mould industry develops,heat treatment must ensure die and mould there are goodstate of manufacture,assembly and wear—resistant properties by request. Impertinent heat treatment can influence die and mould manufacturing such as over—hard and—soft and assembly.Traditionally the heat treatment process was made out according to the methods and properties brought forward by designer.This could make the designers of die and mould and heat treatment diverge from each other,for the designers of die and mould could not fully realize heat treatment process and materials properties,and contrarily the designers rarely understood the service environment and designing thought. These divergences will impact the progress of die and mould to a great extent. Accordingly,if the process design of heat treatment is considered in the early designing stage,the aims of shortening development period,reducing cost and stabilizing quality will be achieved and the sublimation of development pattern from serial to concurrent will be realized.Concurrent engineering takes computer integration system as a carrier,at the very start subsequent each stage and factors have been considered such as manufacturing,heat treating,properties and so forth in order to avoid the error.The concurrent pattern has dismissed the defect of serial pattern,which bring about a revolution against serial pattern.In the present work.the heat treatment was integrated into the concurrent circumstance of the die and mould development,and the systemic and profound research was performed.1 Heat Treatment Under Concurrent CircumstanceThe concurrent pattern differs ultimately from the serial pattern(see Fig.1).With regard to serial pattern,the designers mostly consider the structure and function of die and mould,yet hardly consider the consequent process,so that the former mistakes are easily spread backwards.Meanwhile,the design department rarely communicates with the assembling,cost accounting and sales departments.These problems certainly will influence the development progress of die and mould and the market foreground.Whereas in the concurrent pattern,the relations among departments are close,the related departments all take part in the development progress of die and mould and have close intercommunion with purchasers.This is propitious to eliminationof the conflicts between departments,increase the efficiency and reduce the cost.Heat treatment process in the concurrent circumstance is made out not after blueprint and workpiece taken but during die an d mould designing.In this way,it is favorable to optimizing the heat treatment process and making full use of the potential of the materials.2 Integration of Heat Treatment CAD/CAE for Die and MouldIt can be seen from Fig.2 that the process design and simulation of heat treatment are the core of integration frame.After information input via product design module and heat treatment process generated via heat treatment CAD and heat treatment CAE module will automatically divide the mesh for parts drawing,simulation temperature field microstructure analysis after heat—treatment and the defect of possible emerging (such as overheat,over burning),and then the heat treatment process is judged if the optimization is made according to the result reappeared by stereoscopic visiontechnology.Moreover tool and clamping apparatus CAD and CAM are integrated into this system.The concurrent engineering based integration frame can share information with other branch.That makes for optimizing the heat treatment process and ensuring the process sound.2.1 3-D model and stereoscopic vision technology for heat treatmentThe problems about materials,structure and size for die and mould can be discovered as soon as possible by 3-D model for heat treatment based on the shape of die and mould.Modeling heating condition and phase transformation condition for die and mould during heat treatment are workable,because it has been broken through for the calculation of phase transformation thermodynamics,phase transformation kinetics,phase stress,thermal stress,heat transfer,hydrokinetics etc.For example,3-D heat —conducting algorithm models for local heating complicated impression andasymmetric die and mould,and M ARC software models for microstructure transformation was used.Computer can present the informations of temperature,microstructure and stress at arbitrary time and display the entire transformation procedure in the form of 3-D by coupling temperature field,microstructure field and stress field.If the property can be coupled,various partial properties can be predicted by computer.2.2 Heat treatment process designDue to the special requests for strength,hardness,surface roughness and distortion during heat treatment for die and mould,the parameters including quenching medium type,quenching temperature and tempering temperature and time,must be properly selected,and whether using surface quenching or chemical heat treatment the parameters must be rightly determined.It is difficult to determine the parameters by computer fully.Since computer technology develops quickly in recent decades,the difficulty with large—scale calculation has been overcome.By simulating and weighing the property,the cost and the required period after heat treatment.it is not difficult to optimize the heat treatment process.2.3 Data base for heat treatmentA heat treatment database is described in Fig.3.The database is the foundation of making out heat treatment process.Generally,heat treatment database is divided into materials database and process database.It is an inexorable trend to predict the property by materials and process.Although it is difficult to establish a property database,it is necessary to establish the database by a series of tests.The materials database includes steel grades,chemical compositions,properties and home and abroad grades parallel tables.The process database includes heat treatment criterions,classes,heat preservation time and cooling velocity.Based on the database,heat treatment process can be created by inferring from rules.2.4 Tool and equipment for heat treatmentAfter heat treatment process is determined,tool and equipment CAD/CAE system transfers the information about design and manufacture to the numerical control device.Through rapid tooling prototype,the reliability of tool and the clamping apparatus can be judged.The whole procedure is transferred by network,in which there is no man—made interference.3 Key Technique3.1 Coupling of temperature,microstructure,stress and propertyHeat treatment procedure is a procedure of temperature-microstructure—stress interaction.The three factors can all influence the property (see Fig.4).During heating and cooling,hot stress and transformation will come into being when microstructure changes.Transformation temperature-microstructure and temperature—microstructure—and stress-property interact on each other.Research on the interaction of the four factors has been greatly developed,but the universal mathematic model has not been built.Many models fit the test nicely,but they cannot be put into practice.Difficulties with most of models are solved in analytic solution,and numerical method is employed so that the inaccuracy of calculation exists.Even so,comparing experience method with qualitative analysis,heat treatment simulation by computer makes great progress.3.2 Establishment and integration of modelsThe development procedure for die and mould involves design,manufacture,heat treatment,assembly,maintenance and so on.They should have own database and mode1.They are in series with each other by the entity—relation model.Through establishing and employing dynamic inference mechanism ,the aim of optimizing design can be achieved.The relation between product model and other models was built.The product model will change in case the cell model changes.In fact,it belongs to the relation of data with die and mould.After heat treatment model is integrated into the system,it is no more an isolated unit but a member which is close to other models in the system.After searching,calculating and reasoning from the heat treatment database,procedure for heat treatment,which is restricted by geometric model,manufacture model for die and mould and by cost and property,is obtained.If the restriction is disobeyed,the system will send out the interpretative warning.All design cells are connected by communication network.3.3 Management and harmony among membersThe complexity of die and mould requires closely cooperating among item groups.Because each member is short of global consideration for die and mould development,they need to be managed and harmonized.Firstly,each item group should define its own control condition and resource requested,and learn of the request of up-and-down working procedure in order to avoid conflict.Secondly,development plan should be made out and monitor mechanism should be established.The obstruction can be duly excluded in case the development is hindered.Agile management and harmony redound to communicating information,increasing efficiency,and reducing redundancy.Meanwhile it is beneficial for exciting creativity,clearing conflict and making the best of resource.4 Conclusions(1) Heat treatment CAD/CAE has been integrated into concurrent design for die and mould and heat treatment is graphed,which can increase efficiency,easily discover problems and clear conflicts.(2) Die and mould development is performed on the same platform.When the heat treatment process is made out,designers can obtain correlative information and transfer self-information to other design departments on the platform.(3) Making out correct development schedule and adjusting it in time can enormously shorten the development period and reduce cost.References:[1] ZHOU Xiong-hui,PENG Ying-hong.The Theory and Technique of Modern Die and Mould Design and Manufacture[M].Shanghai:Shanghai Jiaotong University Press 2000(in Chinese).[2] Kang M,Park& Computer Integrated Mold Manufacturing[J].Int J Computer Integrated Manufacturing,1995,5:229-239.[3] Yau H T,Meno C H.Concurrent Process Planning for Finishing Milling and Dimensional Inspection of Sculptured Surface in Die and Mould Manufacturing[J].Int J Product Research,1993,31(11):2709—2725.[4] LI Xiang,ZHOU Xiong-hui,RUAN Xue-yu.Application of Injection Mold Collaborative Manufacturing System [J].JournaI of Shanghai Jiaotong University,2000,35(4):1391-1394.[5] Kuzman K,Nardin B,Kovae M ,et a1.The Integration of Rapid Prototyping and CAE in Mould Manufacturing [J].J Materials Processing Technology,2001,111:279—285.[6] LI Xiong,ZHANG Hong—bing,RUAN Xue-yu,et a1.Heat Treatment Process Design Oriented Based on Concurrent Engineering[J].Journal of Iron and Steel Research,2002,14(4):26—29.文献出处:LI Xiong,ZHANG Hong-bing,RUAN Xue—yu,LUO Zhong—hua,ZHANG Yan.Heat Treatment of Die and Mould Oriented Concurrent Design[J].Journal of Iron and Steel Research,2006,13(1):40-43,74模具热处理及其导向平行设计摘要:在一系列方式中,传统模具设计方法存在许多缺点。
模具注射成型毕业论文中英文对照资料外文翻译文献
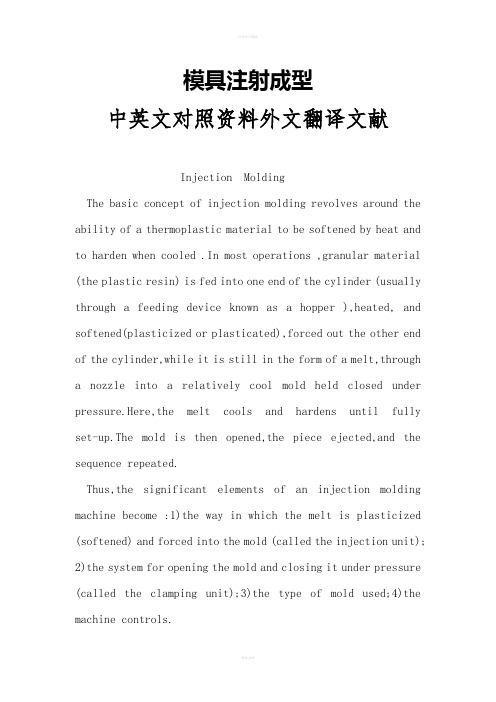
模具注射成型中英文对照资料外文翻译文献Injection MoldingThe basic concept of injection molding revolves around the ability of a thermoplastic material to be softened by heat and to harden when cooled .In most operations ,granular material (the plastic resin) is fed into one end of the cylinder (usually through a feeding device known as a hopper ),heated, and softened(plasticized or plasticated),forced out the other end of the cylinder,while it is still in the form of a melt,through a nozzle into a relatively cool mold held closed under pressure.Here,the melt cools and hardens until fully set-up.The mold is then opened,the piece ejected,and the sequence repeated.Thus,the significant elements of an injection molding machine become :1)the way in which the melt is plasticized (softened) and forced into the mold (called the injection unit);2)the system for opening the mold and closing it under pressure (called the clamping unit);3)the type of mold used;4)the machine controls.The part of an injection-molding machine,which converts a plastic material from a sold phase to homogeneous seni-liguid phase by raising its temperature .This unit maintains the material at a present temperature and force it through the injection unit nozzle into a mold .The plunger is a combination of the injection and plasticizing device in which a heating chamber is mounted between the plunger and mold. This chamber heats the plastic material by conduction .The plunger,on each storke; pushes unmelted plastic material into the chamber ,which in turn forces plastic melt at the front of the chamber out through the nozzleThe part of an injection molding machine in which the mold is mounted,and which provides the motion and force to open and close the mold and to hold the mold close with force during injection .This unit can also provide other features necessary for the effective functioning of the molding operation .Moving plate is the member of the clamping unit,which is moved toward a stationary member.the moving section of the mold is bolted to this moving plate .This member usually includes the ejector holes and moldmounting pattern of blot holes or“T”slots .Stationary plate is the fixed member of the clamping unit on which the stationary section of the mold is bolted .This member usually includes a mold-mounting pattern of boles or “T” slots.Tie rods are member of the clamping force actuating mechanism that serve as the tension member of the clamp when it is holding the mold closed.They also serve as a gutde member for the movable plate .Ejector is a provision in the clamping unit that actuates a mechanism within the mold to eject the molded part(s) from the mold .The ejection actuating force may be applied hydraulically or pneumatically by a cylinder(s) attached to the moving plate ,or mechanically by the opening storke of the moving plate.Methods of melting and injecting the plastic differ from one machine to another and are constantly being improred .couventional machines use a cylinder and piston to do both jobs .This method simplifies machine construction but makes control of injection temperatures and pressures an inherently difficult problem .Other machines use a plastcating extruder to melt the plastic and piston to inject it while some hare been designed to use a screw for both jobs :Nowadays,sixty percent of the machines use a reciprocating screw,35% a plunger (concentrated in the smaller machine size),and 5%a screw pot.Many of the problems connected with in jection molding arises because the densities of polymers change so markedly with temperature and pressure.Athigh temperatures,the density of a polymer is considerably cower than at room temperature,provided the pressure is the same.Therefore,if modls were filled at atmospheric pressure, “shrinkage”would make the molding deviate form the shape of the mold.To compensate for this poor effect, molds are filled at high pressure.The pressure compresses the polymer and allows more materials to flow into the mold,shrinkage is reduced and better quality moldings are produced.Cludes a mold-mounting pattern of bolt holes or “T”slots.Tie rods are members of the clamping force actuating machanism that serve as the tension members of clamp when it is holding the mold closed.Ejector is a provision in the claming unit that actuates a mechanism within the mold to eject themolded part(s) form the mold.The ejection actuating force may be applied hydraulically or pneumatically by a cylinder(s) attached to the moving plate,or mechanically by the opening stroke of the moving plate.The function of a mold is twofold :imparting the desired shape to the plasticized polymer and cooling the injection molded part.It is basically made up of two sets of components :the cavities and cores and the base in which the cavities and cores are mounted. The mold ,which contains one or more cavities,consists of two basic parts :(1) a stationary molds half one the side where the plastic is injected,(2)Amoving half on the closing or ejector side of the machine. The separation between the two mold halves is called the parting line.In some cases the cavity is partly in the stationary and partly in the moving section.The size and weight of the molded parts limit the number of cavities in the mold and also determine the machinery capacity required.The mold components and their functions are as following :(1)Mold Base-Hold cavity(cavities) in fixed ,correctposition relative to machine nozzle .(2)Guide Pins-Maintain Proper alignment of entry into moldintrior .(3)Sprue Bushing(sprue)-Provide means of entry into moldinterior .(4)Runners-Conrey molten plastic from sprue to cavities .(5)Gates-Control flow into cavities.(6)Cavity(female) and Force(male)-Contorl the size,shapeand surface of mold article.(7)Water Channels-Control the temperature of mold surfacesto chill plastic to rigid state.(8)Side (actuated by came,gears or hydrauliccylinders)-Form side holes,slots,undercuts and threaded sections.(9)Vent-Allow the escape of trapped air and gas.(10)Ejector Mechanism (pins,blades,stripper plate)-Ejectrigid molded article form cavity or force.(11)Ejector Return Pins-Return ejector pins to retractedposition as mold closes for next cycle.The distance between the outer cavities and the primary sprue must not be so long that the molten plastic loses too much heat in the runner to fill the outer cavities properly.The cavities should be so arranged around the primary sprue that each receives its full and equal share of the total pressure available,through its own runner system(or the so-called balanced runner system).The requires the shortest possible distancebetween cavities and primary sprue,equal runner and gate dimension,and uniform colling.注射成型注射成型的基本概念是使热塑性材料在受热时熔融,冷却时硬化,在大部分加工中,粒状材料(即塑料树脂)从料筒的一端(通常通过一个叫做“料斗”的进料装置)送进,受热并熔融(即塑化或增塑),然后当材料还是溶体时,通过一个喷嘴从料筒的另一端挤到一个相对较冷的压和封闭的模子里。
- 1、下载文档前请自行甄别文档内容的完整性,平台不提供额外的编辑、内容补充、找答案等附加服务。
- 2、"仅部分预览"的文档,不可在线预览部分如存在完整性等问题,可反馈申请退款(可完整预览的文档不适用该条件!)。
- 3、如文档侵犯您的权益,请联系客服反馈,我们会尽快为您处理(人工客服工作时间:9:00-18:30)。
1 外文资料翻译 资料来源:《模具设计与制造专业英语》 文章名:Chapter 3 Casting Dies 书刊名:《English for Die & Mould Design and
Manufacturing》 作 者:刘建雄 王家惠 廖丕博 主编
出版社:北京大学出版社,2002
章 节:Chapter 3 Casting Dies 页 码:P51~P60
文章译名: 铸造模具 2
Chapter 3 Casting Dies 3.1 Casting The first castings were made during the period 4000~3000 B.C., using stone and metal molds for casting copper. Various casting processes have been developed over a long period of time, each with its own characteristics and applications, to meet specific engineering and service requirements. Many parts and components are made by casting, including cameras, carburetors, engine blocks, crankshafts, automotive components, agricultural and railroad equipment, pipes and plumbing fixtures, power tools, gun barrels, frying pans, and very large components for hydraulic turbines. Casting can be done in several ways. The two major ones are sand casting, in which the molds used are disposable after each cycle, and die casting, or permanent molding, in which the same metallic die is used thousands or even millions of times. Both types of molds have three common features. They both have a “plumbing” system to channel molten alloy into the mold cavity. These channels are called sprues, runners, and gates (Fig. 3-1). Molds may be modified by cores which form holes and undercuts or inserts that become an integral part of the casting. Inserts strengthen and reduce friction, and they may be more machinable than the surrounding metal. For example, a steel shaft when properly inserted into a die cavity results in an assembled aluminum step gear after the shot. After pouring or injection, the resulting castings require subsequent operations such trim-ming, inspection, grinding, and repairs to a greater or lesser extent prior to shipping. Premium-quality castings from alloys of aluminum or steel require x-ray soundness that will be acceptable by the customer. Certain special casting processes are precision-investment casting, low-pressure casting, and centrifugal casting. 3
3.2 Sand Casting The traditional method of casting metals is in sand molds and has been used for millennia. Simply stated, sand casting consists of (a) placing a pattern having the shape of the desired casting in sand to make an imprint, (b) incorporating a gating system, (c) filling the resulting cavity with molten metal, (d) allowing the metal to cool until it solidifies, (e) breaking away the sand mold, and (f) removing the casting (Fig. 3-2). The production steps for a typical sand-casting operation are shown in Fig. 3-3. Although the origins of sand casting date to ancient times, it is still the most prevalent form of casting. In the United States alone, about 15 million tons of metal are cast by this method each year.
Open riser Vent Pouring basin (cup)
Cope Blind Flask riser Sprue
Core (sand)
Sand
Parting line Drag Mold cavity
Choke Runner Gate Sand
Fig. 3-2 Schematic illustration of a sand mold 4
3.2.1 Sands Most sand casting operations use silica sand (SiO2), which is the product of the dis- integration of rocks over extremely long periods of time. Sand is inexpensive and is suitable as mold material because of its resistance to high temperatures. There are two general types of sand: naturally bonded (bank sand) and synthetic (lake sand). Because its composition can be controlled more accurately, synthetic sand is preferred by most foundries. Several factors are important in the selection of sand for molds. Sand having fine, round grains can be closely packed and forms a smooth mold surface. Although fine-grained sand enhances mold strength, the fine grains also lower mold permeability. Good permeability of molds and cores allows gases and steam evolved during casting to escape easily. 3.2.2 Types of Sand Molds Sand molds are characterized by the types of sand that comprise them and by the methods used to produce them. There are three basic types of sand molds: greensand, cold-box, and no-bake molds. The most common mold material is green molding sand, which is a mixture of sand, clay, and water. The term “green” refers to the fact that the sand in the mold is moist or damp while the metal is being poured into it. Greensand molding is the least expensive method of making molds. In the skin-dried method, the mold surfaces are dried, either by storing the mold in air or by drying it with torches. These molds are generally used for large castings because of their higher strength. Sand molds are also oven dried (baked) prior to pouring the molten metal; they are stronger than greensand molds and impart better dimensional accuracy and surface finish to the casting. However, this method has drawbacks: distortion of the mold is greater; the castings are more susceptible to hot tearing because of the lower collapsibility of the mold; and the production rate is slower because of the drying time required. In the cold-box mold process, various organic and inorganic binders are blended into the sand to bond the grains chemically for greater strength. These molds are dimensionally more accurate than greensand molds but are more expensive. In the no-bake mold process, a synthetic liquid resin is mixed with the sand; the mixture hardens at room temperature. Because bonding of the mold in this and in the