A Combination of Shunt Hybrid Power Filter and Thyristor-Controlled Reactor for Power Quality
电力系统中英对照词汇
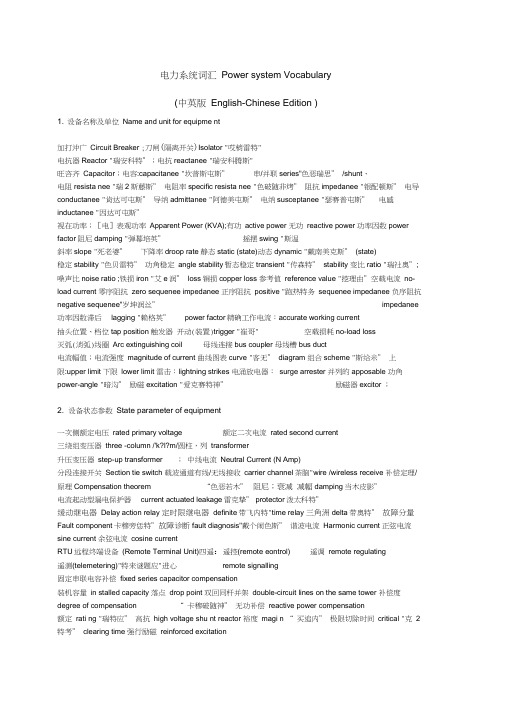
电力系统词汇Power system Vocabulary(中英版English-Chinese Edition )1. 设备名称及单位Name and unit for equipme nt加打沖广Circuit Breaker ;刀闸(隔离开关)Isolator "哎梢雷特"电抗器Reactor "瑞安科特”;电抗reactanee "瑞安科腾斯"旺咨齐Capacitor;电容:capacitanee "坎普斯屯斯”串/并联series"色恶瑞思” /shunt、电阻resista nee "瑞2斯藤斯” 电阻率specific resista nee "色破随非烤” 阻抗impedanee "银配顿斯” 电导conductanee "肯达可屯斯” 导纳admittanee "阿德美屯斯” 电纳susceptanee "瑟赛普屯斯”电感inductanee "因达可屯斯”视在功率;[电]表观功率Apparent Power (KVA);有功active power 无功reactive power 功率因数power factor阻尼damping "弹幕培英”摇摆swing "斯温斜率slope "死老婆”下降率droop rate 静态static (state)动态dynamic "戴南美克斯” (state)稳定stability "色贝雷特” 功角稳定angle stability暂态稳定transient "传森特” stability 变比ratio "瑞社奥”;噪声比noise ratio ;铁损iron "艾e润” loss铜损copper loss 参考值reference value "挖理由”空载电流no-load current 零序阻抗zero sequenee impedanee 正序阻抗positive "跑热特务sequenee impedanee 负序阻抗negative sequenee"岁坤润丝”impedanee 功率因数滞后lagging "赖格英”power factor精确工作电流:accurate working current抽头位置、档位tap position 触发器开动(装置)trigger "崔哥" 空载损耗no-load loss灭弧(消弧)线圈Arc extinguishing coil 母线连接bus coupler 母线槽bus duct电流幅值;电流强度magnitude of current 曲线图表curve "客无” diagram 组合scheme "斯给米” 上限:upper limit 下限lower limit 雷击:lightning strikes 电涌放电器:surge arrester 并列的apposable 功角power-angle "暗沟” 励磁excitation "爱克赛特神”励磁器excitor ;2. 设备状态参数State parameter of equipment一次侧额定电压rated primary voltage 额定二次电流rated second current三绕组变压器three -column /'k?l?m/圆柱,列transformer升压变压器step-up transformer ;中线电流Neutral Current (N Amp)分段连接开关Section tie switch 载波通道有线/无线接收carrier channel茶脑"wire /wireless receive 补偿定理/原理Compensation theorem “色恶若木”阻尼;衰减减幅damping当木皮影”电流起动型漏电保护器current actuated leakage雷克挚” protector泼太科特”缓动继电器Delay action relay 定时限继电器definite带飞内特"time relay 三角洲delta带奥特” 故障分量Fault component卡穆旁恁特”故障诊断fault diagnosis"戴个闹色斯” 谐波电流Harmonic current 正弦电流sine current 余弦电流cosine currentRTU远程终端设备(Remote Terminal Unit)四遥:遥控(remote eontrol) 遥调remote regulating遥测(telemetering)"特来谜题应"进心remote signalling固定串联电容补偿fixed series capacitor compensation装机容量in stalled capacity 落点drop point 双回同杆并架double-circuit lines on the same tower 补偿度degree of compensation “ 卡穆破随神” 无功补偿reactive power compensation额定rati ng "瑞特应” 高抗high voltage shu nt reactor 裕度magi n “ 买追内” 极限切除时间critical "克 2 特考” clearing time 强行励磁reinforced excitation单机无穷大系统 one machine - infinity "因费内特” bus system下降特性 droop characteristics "卡瑞特2斯特克”失去同步loss of synchronization "色佛呢瑞申”仿真分析simulation "色迷有来申” analysis "恶拿了色”传递函数 transfer function 框图 block diagram 受益人 receive-side布线系统安装 Erection “A2科神”建造;建筑物 of wiring systems绝缘子灭弧角 In sulator arcing "阿色影” hor n 常开 / 常闭触点(NO/NC) Normally open /closed con tacts机械耐久性Mecha ni cal en dura nee "银滴油润辞”负荷特性load characteristic输电线路故障 Transmission line malfunction "马疯科神” 零功率因数zero power factor标准的机组数据显示 (Sta ndard Measureme nt And Display Data)负载电流百分比显示 Percentage of Current load(%)单相 /三相电压 Voltage by One/Three Phase (Volt.) 每相电流 Current by Phase (AMP)电瓶电压表 Battery Voltage Meter怠速-快速运行选择键 Idle "爱到” Run - Normal Run Selector Switch其它故障显示及输入 Other Com mon Fault Alarm Display 特别地:In particular,, T )自适应控制方法 adaptive control process 动作速度 speed of action 行波信号 travelling wave signal 输电线路故障 transmissionline malfunction 暂态行波 transient state travelling wave负荷突然增加或减少: sudden load in creases or decreases N6 H5 @- k3 s1 f' h短路和开关操作: short circuits and switching operations.三相和对地短路:three-phase and lin e-to-grou nd faults暂态过电压和电流: tra nsie nt overvoltages and curre ntsY0相量:phasor ,通常用复数 phasors 瞬时功率:instantaneous power ; n7 A ; P1 '5 P7'/ F6 XO T正弦曲线电压或电流: A sin usoidal voltage or curre nt at con sta nt freque ncy 2 d ; 2 0/ _5 d) X $ fD3 ')e& X + w : J ; @2 e最大值: maximum value ; u 有效值:effective value 平均值:average value w6 X! ]6 z ]& F5 T坐标系实轴:real axis 坐标系虚轴:imaginary axis / B - D & b :相量图:phasor diagram for ••/ n$ b6 _3 一: ?4 D4 2 d9 V ; }4.电力词汇缩写 aa4Abbreviation "恶不入味 A 申” a for electric power ?# YADS Automatic Disconnection of supply自动切断电源 (ACE Area Control Error # "爱若” \'区域控制误差(API Application Programmi ng In terface 应用程序界面,N701;5 '!ATS Automatic Transform System 厂用电源快速切换装置ASS Automatic Synchronized "森坤奈斯的”System 自动准同期装置 BCS Burner "博呢" Control System 燃烧器控制系统常发故障永久故障 电力系统分析与计算 电力系统分路重合闸 Permanent "破莫内特” fault 电解液,电解质electrolytePower system an alysis and computati on "康培特神”Power system splitt ing “A 莱科特莱特” 功率角度曲线 Power an gle curve "课务” 整定计算短路 Setting calculation short circuit 时间电流特性 Time current characteristic"色破累特英"reclosi ng 精度等级accuracy a 安珂幽若谁” 电涌放电器;过电压吸收器;surge 下降特性 droop characteristic class arresterBMS Burner Man ageme nt System 燃烧器管理系统CCS Coordinated "考呢迪特” Control System协调控制系统CRMS Control Room Management System 控制室管理系统CRT Cathode “卡骚的” Ray Tube “特优博”阴极射线管DAS Data Acquisition "阿亏瑞申” System数据采集与处理系统DCS Distributed Control System 分散控制系统DDC Direct Digital "得知陶” Control门.殘级对辛已珀述DEH Digital Electronic Hydraulic "还招” Control 数字电液(调节系统)DPU Distributed Processi ng "普绕色色应”Un it分布式处理单元ETS Emergency “A莫真税”Trip System汽轮机紧急跳闸系统EWS Engineering Working Station 工程师工作站FCS Field bus Control System现场总线控制系统FAT Factory Acceptanee Test?工厂验收试验* Y on Site Acceptanee Test 现场验收试验P&FOP Fiber "乏恶” optic "奥佩特克”protection 光纤保护FSS Fuel Safety System燃料安全系统FSSS Furnace Safeguard Supervisory System炉膛安全监控系统GPS Global"阁楼博” Position System 全球定位系统GIS Gas In sulated Switch gear气体绝缘开关设备HGIS Hybrid Gas Insulated Switch gear半气体绝缘变电站/但它不包括母线设备。
英语基础测试试题93

Discussion on maintenance strategy of power system automationAuthor: Fu Jianjun[Abstract] to power system automation operation related to the production and life of human beings can work normally and effectively. This paper first analyzes the power system automation operation and maintenance work of the necessity, and then to maintain the maintenance of the part, and finally the maintenance strategy for a brief introduction. Hope to provide reference for maintenance personnel.[Key words] power system; automatic paste; maintenancePower as a human being widely used a secondary clean energy, to ensure that the power supply to normal is current power companies have to solve the problem. With the development of computer technology, electric power industry has set up a set of fully automatic electric power system, which can make a great contribution to the efficient and high quality supply of electric power. Power system to achieve full automation, must be the power technology, computer technology, communication technology and automatic control technology and other technology to be combined. Therefore, the whole power system automation need to use the components more, the use of technology coverage is wide, how to ensure that the power system automation is an important issue. In order to realize the stable and reliable operation of electric power system, the maintenance of the whole power system is required.The necessity of power system automation operation and maintenance workPower system in the practice of human society, with the changing of the practice of human beings, also appeared in the corresponding change. In order to meet the demand of electric power market, electric power system has been integrated with the communication technology and automation control technology, and realized the automation of electric power system, and the development direction of the power system automation is better to promote the development of electric power enterprises. The automation of electric power system not only simplifies the operation of electric power enterprises, but also realizes the operation of power system. Because of the automation operation, it also facilitates the optimization management of the power source, transmission and use of all links, so that the power enterprises in the market economy conditions, to maintain effective competitiveness plays an important role. However, the automation of power system is not a simple combination of several technical means can be achieved, but the need for ongoing maintenance. Effective maintenance work can be carried out in time and effectively to deal with the problem of data processing and operation of the system, and ensure the reliable operation ofthe whole system.Two, the need to maintain the factorAutomatic operation of the power system, the technology involved is complex, requires a lot of equipment and components to support. Therefore, the need to maintain the equipment and components are also more, for the whole system, maintenance work involves many technologies, the problem is also more. The general need to maintain the power system automation factors are as follows:(a) system of dispatching automationAlong with the progress of society, the power industry in all aspects of technology is also constantly toward a higher level. The automation technology of power system has achieved more and more achievements, and the development of power system dispatching automation is the most rapid. Power dispatching system is the automation of the entire power system to collect data for the decision-making basis, the command of the entire power system power dispatch, power plant to provide information and information. Therefore, to maintain the power system dispatching automation part, the quality of the entire power system has a very strong guarantee.(two) substation automationSubstation automation for the safe operation of the transformer substation has a very important role, is one of the key factors for the development of the electric power enterprise. In the process of development of electric power system, substation is the weak point in development. Because of the difficulty of replacing many equipments in substation, it is generally to optimize the design of the equipment in the process of realizing automation. Because many techniques and optimization schemes are used in practice, and there is a big problem, the problem is more and more complicated in the maintenance of substation automation system.(three) distribution network automationIn power distribution network control, not long ago or the use of manual operation be controlled manner. This seriously restricted the distribution network function properly. However, with the progress of science and technology, the control of power distribution network has realized the complete automation. Using information technology and advanced sensor to realize the automatic control of the distribution network, greatly improve the efficiency of the power grid operation, better play the role of electricity.Three, the power system automation operation and maintenance strategyAutomation of electric power systems operation maintenance work, should first ensure the safety of the whole system, mainly virus protection and to prevent hacker intrusion two aspects of; secondly, to remote maintenance mode, on the power of information relevant data optimization, determine the fault and first borrow the remote technology to be solved. In the maintenance, we should make an effective troubleshooting strategy for both software and hardware failures. This article is limited to the length, only to maintain the work strategy in the part of strategy。
电动机英语作文

电动机英语作文篇一:电动机专业英语inductionmachine感应式电机horseshoemagnet马蹄形磁铁magneticfield磁场eddycurrent涡流right-handrule右手定则left-handrule左手定则slip转差率inductionmotor感应电动机rotatingmagneticfield旋转磁场winding绕组stator定子rotor转子inducedcurrent感生电流time-phase时间相位excitingvoltage励磁电压solt槽lamination叠片laminatedcore叠片铁芯short-circuitingring短路环squirrelcage鼠笼rotorcore转子铁芯cast-aluminumrotor铸铝转子bronze青铜horsepower马力random-wound散绕insulation绝缘acmotor交流环电动机endring端环alloy合金coilwinding线圈绕组form-wound模绕performancecharacteristic工作特性frequency频率revolutionsperminute转/分motoring电动机驱动generating发电per-unitvalue标么值breakdowntorque极限转矩breakawayforce起步阻力overhauling检修wind-drivengenerator风动发电机revolutionspersecond转/秒numberofpoles极数speed-torquecurve转速力矩特性曲线plugging反向制动synchronousspeed同步转速percentage百分数locked-rotortorque锁定转子转矩full-loadtorque满载转矩primemover原动机iushcurrent涌流magnetizingreacance磁化电抗line-to-neutral线与中性点间的staorwinding定子绕组leakagereactance漏磁电抗no-load空载fullload满载Polyphase多相(的)iron-loss铁损compleximpedance复数阻抗rotorresistance转子电阻leakageflux漏磁通locked-rotor锁定转子choppercircuit斩波电路separatelyexcited他励的compounded复励dcmotor直流电动机demachine直流电机speedregulation速度调节shunt并励series串励armaturecircuit电枢电路opticalfiber光纤interoffice局间的waveguide波导波导管bandwidth带宽lightemittingdiode发光二极管silica硅石二氧化硅regeneration再生,后反馈放大coaxial共轴的,同轴的high-performance高性能的carrier载波mature成熟的SingleSideBand(SSB)单边带couplingcapacitor结合电容propagate传导传播modulator调制器demodulator解调器linetrap限波器shunt分路器amplitudemodulation(am调幅FrequencyShiftKeying(FSK)移频键控tuner调谐器attenuate衰减incident入射的two-wayconfiguration二线制generatorvoltage发电机电压dcgenerator直流发电机polyphaserectifier多相整流器boost增压timeconstant时间常数forwardtransferfunction正向传递函数errorsignal误差信号regulator调节器stabilizingtransformer稳定变压器timedelay延时directaxistransienttimeconstant直轴瞬变时间常数transientresponse瞬态响应solidstate固体buck补偿转子:转轴:shaft换向器:commutator铁芯:rotorsteelcore端板:endspider 绝缘纸:rotorsteelliner槽楔(环):wedgeringU型挡圈:Utyperetainer 漆包线:fieldmagnetwire轴承:bearing绝缘漆:varnish换向片:commutatorsegment定子:铁芯:rotorsteelcore漆包线:fieldmagnetwire绝缘纸:rotorsteelliner 支架:bracket支撑组件:机壳:housing端盖:supportframe碳刷组件:碳刷:brush碳刷套:brushsleeve碳刷架(刷握):brushholder弹簧:brushspring刷辫:brushflexible刷盒:brushbox篇二:电机行业英语电机(马达)electricmotor,微电机micromotor小电机smallmotor分马力电机fractionalhorsepowermotor空调暧通电机HVacmotor(heating,ventilatingair-conditioningmotor)直流电机directcurrentmotor,dcmotor串励直流电机serieswounddcmotor并励直流电机shuntwounddcmotor复励直流电机compoundwounddcmotor直流无刷电机Brushlessdirectcurrentmotor,BLdcmotor串激电机universalmotor交流电机alternatingcurrentmotor,acmotor齿轮电机Gearedmotor,Gearmotor同步电机synchronousmotor异步电机asynchronousmotor,inductionmotor罩极电机shadedpolemotor步进电机stepmotor,steppermotor,steppingmotor混合式hybrid磁阻式variablereluctance永磁式permanentmagnet步距角精度stepangleaccuracy转轴shaft轴向负载axialload轴向窜动axialendplay径向跳动radialrunout负载onload 过载overload额定负载ratedload空载no-load电流current电压voltage 防护等级protectionclass,degreeofprotection,isolationclass绝缘等级insulationclass力距torque起动力距startingtorque最大(崩溃)转距breakdowntorque堵转lockedrotor保持力距holdingtorque共振resonance电线(电缆)cable测试程序testproc(转载于: 爱作文网)edure性能测试performancetest耐压测试dielectrictest(highpottest)功能测试functionalitytest,functiontest实地测试fieldtest寿命测试lifetest老化试验ageingtest连续运转continuousduty,continuousrunning间歇运转intermittentduty,intermittentrunning温升试验temperaturerisetest环境温度ambienttemperature峰值peakvalue供应商supplier,vendor,seller客户customer,client,buyer样品(样机)prototype,sample试生产pilotproduction,try-outproduction小批生产pre-seriesproduction批量生产seriesproduction打筋spline滚花knurl攻丝tap键槽keyway定位销stoppin螺钉screw 螺纹thread螺栓bolt螺母nut联结器(接插件)connector端子:terminal标签,铭牌labelnameplate 外形尺寸outsidedimensionoutline精度accuracy公差tolerance不符合要求non-conformity,outofspecification前端盖frontflange,frontendcover,frontendbell,frontendshield后端盖rearflange,rearendcover,rearendbellrearendshield凸台pilot齿轮,带轮pinion,gearwheel,gear滚珠轴承ballbearing含油轴承sleevebearing,bronzebearing,selflubricatingbearing转子rotor定子stator铁芯core电枢armature磁钢magnet整流子(换向器)commutator碳刷carbonbrush,brush刷握brushholder机壳housing/shell轴承室bearinghousing出轴shaftextension扁丝flat工装、夹具jigs,fixtures,tooling规gauge 引出线leadwire,leads线路板PcB(printedcircuitboard)驱动器driver,drive冲片lamination槽slot齿teeth轭yoke硅钢片siliconsteel漆包线copperwire/enamelinsulatedcopperwire胶带tape压铸diecasting注塑mouldinjection波纹垫圈wavewasher车加工machining精车:turning霍尔传感器hallsensor开关switch装配assemble,assembly生产制造make,manufacture,produce动平衡balance.balancing热处理heattreatment表面淬火casehardening穿透淬火throughhardening退火annealing正火temper表面涂覆surfacecoating 喷砂sandblast涂胶gluing滴漆varnish电泳powdercoatingE-coating 力矩速度曲线speedtorquecurve磁通flux工艺流程图processflowchart 绝缘骨架plasticbobbin止口rabbet粗糙度roughness同心度concentricity偏心度eccentricity垂直度perpendicularity平行度parallelismabscissaaxis横坐标acmotor交流电动机activecomponent有功分量activeinrespectto相对呈阻性actualvalue,effectivevalue有效值acyclicmachine单极电阻adjustable-speedrange调速范围admittance导纳airgap气隙air-gapfluxdistribution气隙磁通分布air-gapflux气隙磁通air-gapline气隙磁化线air-gapreluctance气隙磁阻algebraic代数的algorithmic算法的alternatingcurrentmotor交流电动机ampere-turns安匝(数)amplitudemodulation(am)调幅anglestability功角稳定arc,electricarc电弧armaturecircuit电枢电路armatureconductor电枢导体armaturecoil电枢线圈armaturem.m.f.wave 电枢磁势波armaturereaction电枢反应armaturereactionreactance电枢反应电抗armatureiron电枢铁心asynchronousmotor异步电机asymmetry不对称automaticV oltageregulator(aVR)自动电压调整器auxiliarymotor辅助电动机axiallyandcircumferentially轴向和环向axialmagneticattraction轴向磁拉力bandwidth带宽base基极basicfrequencycomponent基频分量bastpressure风压beltfactor分布系数bilateralcircuit双向电路bimotored 双马达的biphase双相的breakawayforce起步阻力breakdowntorque极限转矩bronze青铜brush电刷brushvoltagedrop电刷压降brushspacing电刷间距capacitance电容carrier载波cartesiancoordinates笛卡儿坐标系can屏蔽套cast-aluminumrotor铸铝转子centrifugalforce离心力characteristicfrequency固有频率choppercircuit斩波电路circuitbranch 支路circuitcomponents电路元件circuitdiagram电路图circuitparameters电路参数circumferentialorientationmotor切向永磁电机criticalwhirlingspeed临界转速claw-poles爪极电机closedloop闭环closedslot闭口槽coaxial共轴的,同轴的coggingtorque齿槽转矩coilwinding线圈绕组coincideinphasewith与….同相collector集电极commutatingpole,interpole换向极commutatorsegment换向片commutator-brushcombination换向器-电刷总线compensatingwinding 补偿绕组compensatingcoil补偿线圈compleximpedance复数阻抗compoundgenerator复励发电机compounded复励conductance电导conductor导体converter变流器copperloss铜耗correctioncoefficient 校正系数corridor通路counter-clockwise逆时针couplingcapacitor耦合电容currentattenuation电流衰减currentdensity电流密度currentgain 电流增益currentphasor电流相量currentstrength电流强度currentvector电流矢量dampingcage阻尼笼dcgenerator直流发电机dcmotor直流电动机demachine直流电机differentiation微分digitalsignalprocessor(dSP)数字信号处理器directaxistransienttimeconstant直轴瞬变时间常数direct-axistransientreactance直轴瞬态电抗direct-axiscomponentofvoltage电压直轴分量directaxis直轴direct-current直流directtorquecontrol(dTc)直接转矩控制displacementcurrent位移电流distributedwinding分布绕组distributionfactor分布因数distoritionofvoltagewaveshape电压波形畸变domain磁畴duty,load负荷dynamicresponse动态响应dynamic-stateoperation动态运行3dequivalentmagneticcircuitnetworkmethod三维等效磁路网络法3d-Emcne.m.f=electromotivefore电动势eddycurrent涡流effectivevalues有效值effectsofsaturation饱和效应electricenergy电能electricaldevice电气设备electromagneticinduction电磁感应electromagneticpower电磁功率elecironagneticclamping电磁阻尼electricpotential电位electricalfield电场electromotiveforce电动势electromagneticforce电磁力electromagneticwave电磁波electrode电极电焊条electromagnetictorque 电磁转矩endring端环endturn端部绕组endcover端盖endring端环endleakagereactance端部漏抗equivalentT–circuitT型等值电路excitationsystem励磁系统excitingvoltage励磁电压externalarmaturecircuit电枢外电路externalcharacteristic外特性fan风扇feedbackcomponent反馈元件feedbackloop反馈回路feedbacksignal反馈信号feedbacksystem反馈系统feedforwardsignal前馈信号feedforwardsystem前馈系统ferromagnetic铁磁材料fieldcoils励磁线圈fieldcurrent励磁电流fieldeffecttransistor(FET)场效应管fieldorientedcontrol(Foc)磁场定向控制fieldwinding磁场绕组,励磁绕组flatcable扁电缆fluxlinkage磁链fluxline磁通量fluxpath磁通路径fluxpulsation磁通脉冲flucdensity磁通密度fluxdistribution磁通分布forwardtransferfunction 正向传递函数fractionalpitch短节距frequency频率frequencyconversion变频frequencychangerset变频机组fringingeffect边缘效应fullload满载full-loadtorque满载转矩full-pitchwinding整距绕组fundamentalwave基波fundamentalcomponent基波分量gain增益generatorvoltage发电机电压grade等级harmonic谐波horsepower(HP)马力horseshoemagnet马蹄形磁铁hysteresisloss磁滞损耗idealsource理想电源imbricatedwinding,lapwinding叠绕组impedance阻抗impedancedrop阻抗压降impulsevoltagepeakvalue冲击电压峰值inductance电感inductiongenerator感应发电机inductionmachine感应电机inductionmotor感应电动机inductivecomponent感性(无功)分量inherentregulationofgenerator发电机固有电压调整率instanttorgue瞬态转矩instantaneouselectricpower瞬时电功率instantaneousmechanicalpower瞬时机械功率insulation绝缘insulationresistance绝缘电阻intensityofelectrialfield电场强度interturnbreakdownvoltage匝间击穿电压interturninsulating匝间绝缘interturnvoltageresistanttest匝间耐压试验interiorPermanentmagnet(iPm)内置式SurfaceinsetPermanentmagnet(SiPm)表面式internalresistance内阻inverter逆变器ironcore铁心iron-loss铁损lamination叠片laminatedcore叠片铁心laminationinsalation冲片绝缘lag滞后leadingcurrent超前电流leadingpowerfactor超前功率因数leakagecurrent漏电流leakageflux漏磁通leakagereactance漏磁电抗leakage泄漏left-handrule左手定则liftmotor电梯用电动机lightemittingdiode发光二极管lightningshielding避雷linecurrent线电流linevoltage线电压linearzone 线性区linear-motionmachine直线电机linearinductionmotor直线感应电机line-to-neutral线与中性点间的loadcharacteristic负载特性loadpowerfactor负载功率因数load-saturationcurve负载饱和曲线locked-rotortorque锁定转子转矩locked-rotorcurrent堵转电流longpithwinding长距绕组long-pithcoil长距线圈magneticamplifier磁放大器magneticcircuit磁路magneticcoupling磁耦合magneticfield磁场magneticflux磁通magnetichysteresis(creeping)磁滞magnetichysteresisloop磁滞回线magneticinduction磁感应magneticloading磁负荷magneticparticle磁粉离合器magneticpole磁极magneticsaturation磁饱和magnetictorque电磁转矩magneticyoke磁轭magnetizingreacance磁化电抗magnetizationcurve磁化曲线magnetomotiveforce(m.m.f)磁动势mainpole主极mesh网孔mid-frequencyband中频带modulator调制器modulus模motoring电动机驱动motorslip电动机转差率m.m.fwave 磁势谐波mutualflux交互(主)磁通mutual-inductor互感negativephase-sequence 负序no-load空载nominalpull-intorque标称牵入转矩non-sinusoidal非正弦numberofpoles极数numberoffieldturns磁极绕组匝数numberofslots槽数odd-orderharmonic 奇次谐波operatingpoint工作点operatingcharacteristiccurve运行特性曲线opticalfiber光纤oscillation振荡oscilloscope示波器outsidediameterofcore铁心外径overhangleakagepermeance端部漏磁导overload超负荷overlapping重叠parallel并联parallelconnexionmagnetizedwinding并励绕组parallelconnexionroadnumber并联支路数parallelwindnumber并绕根数pancakecoil扁平绕组P.d.=potentialdrop电压降peaktopeak峰峰值perunitvalue标么值percentage百分数peripheralair-gapleakage磁极漏磁performancecharacteristic工作特性permanentmagnet永磁体permanentmagnetsynchronousmotor永磁同步电机permeability导磁率periodicallysymmetrical周期性对称per-unitvalue标么值phasedisplacement相位差phase-to-phase(line-to-line)voltage相(线)电压phaseinsulation相间绝缘phasesequence相序Phasemodulation(Pm)相位调制phasereversal反相pilotexciter副励磁机plugging反向制动polarity极性pole-changingmotor变极电动机polecore磁极铁心polecoil磁极线圈polepitch极距poleshoe极靴poleendplate磁极端板polyphaserectifier多相整流器polyphaserectifier 多相整流器Polyphase多相(的)potentialtransformer电压互感器poweramplifier功率放大器powerfrequency工频propulsionmotor推进电机pureinductance纯电感purecapacitance纯电容pureresistance纯电阻punching冲片pump泵push-throughwinding插入绕组quadrature-axiscomponentofvoltage电压交轴分量quadrature-axistransienttimeconstant交轴瞬态时间常数quadrature-axiscomponent交轴分量quadrature-axistransientreactance交轴瞬态电抗quadrature-axissynchronousreactance交轴同步电抗r.m.svalues=rootmeansquarevalues均方根值radius半径radialmagneticattractionforce径向磁拉力radialairgap径向气隙random-wound散绕reactance电抗reactivecomponent无功分量reactiveinrespectto相对….呈感性reactivepower无功功率rectifier整流器reluctance磁阻referenceV oltage基准电压reluctance磁阻residualmagnetism剩磁resistance电阻resistivity电阻率reactance电抗retardingtorque制动转矩rheostat变阻器rotatingcommutator旋转(整流子)换向器rotatingmagneticfield旋转磁场rotor转子rotor(stator)winding转子(定子绕组)rotorcore转子铁芯rotorresistance转子电阻rotoryoke转子磁轭rotorlamination转子叠片rotorinter-bar转子漏阻抗roughadjustment粗调salientpoles凸极saturation饱和saturationcurve 饱和曲线saturationeffect饱和效应saturationfactor饱和系数selfexcited自励self-inductor自感semi-enclosedmortor半封闭电动机separatelyexcited他励的series串联seriesexcited串励series-paralledcircuit串并联电路shaft轴shaft-less无轴承的short-circuitingring短路环short-pitching短距shuntdisplacementcurrent旁路位移电流shunt并励,分路器shuntexcitedgenerator并励发电机shuntfield并励磁场silliconsteelplate 硅钢片simplexwavewinding单波绕组simplexlapwinding单叠绕组singleandtwo-layerwinding单双层绕组single-phasing单相运行singlesquirrelcagewinding单鼠笼绕组single-doublelayerwinding单双层混合绕组sinusoidal–densitywave正弦磁密度sinusoidaltimefunction正弦时间函数skewedslot斜槽skineffect集肤效应skin-friction表面摩擦系数slip转差率solidstate固体slot槽slotpermeance槽磁导slotcrosssection槽截面slotpitch槽距slotopening 槽口slotopening槽口宽slotwidth槽宽slotleakageconductance槽漏磁导slotleakageinductance 槽漏抗slotfillingfactor槽满率slotwinding槽绕组slotdepth槽深slotwedge,slotseal槽楔slotharmonic 槽谐波slotmodel槽形slotleakageflux槽漏磁speed-torquecharacteristic速度转矩特性speed-torquecurve转速力矩特性曲线squirrelcage鼠笼squirrelcageinductionmotor笼形感应电机stabilizer稳定器stainlesssteelsleeve不锈钢轴套stator定子statorslot定子槽statoryoke定子轭statorwinding定子绕组steppingmotor步进电机,步进马达steppermotor步进电机step-servo-motor步进伺服电机storagebattery蓄电池surfaceresistance表面电阻superconductinggenerators(ScGs)超导发电机symmetricalcomponent对称分量synchronousgenerator同步发电机synchronousreactance同步电抗synchronousreluctancemotor(SRm)同步磁阻电机synchronousspeed同步转速terminalvoltage端电压temperaturerise温升toothfluxdensity齿磁通密度totalfluxlinkage总磁链toothpitch齿距toothroot齿根toothsaturation齿部饱和toothshape齿形toothtipleakagepermeance齿端漏磁导toothtop齿顶transformer变压器transferfunction传递函数transientresponse瞬态响应transversefluxmotors(TFm)横向磁通电机inductionmachine感应式电机horseshoemagnet马蹄形磁铁magneticfield磁场eddycurrent涡流right-handrule右手定则left-handrule左手定则slip转差率inductionmotor感应电动机rotatingmagneticfield旋转磁场winding绕组stator定子rotor转inductionmachine感应式电机horseshoemagnet马蹄形磁铁magneticfield磁场eddycurrent涡流right-handrule右手定则left-handrule左手定则slip转差率inductionmotor感应电动机rotatingmagneticfield旋转磁场winding绕组stator定子rotor转子inducedcurrent感生电流time-phase时间相位excitingvoltage励磁电压solt槽lamination叠片laminatedcore叠片铁芯short-circuitingring短路环squirrelcage鼠笼rotorcore转子铁芯cast-aluminumrotor铸铝转子bronze青铜horsepower马力random-wound散绕insulation绝缘acmotor交流环电动机endring端环alloy合金coilwinding线圈绕组form-wound模绕performancecharacteristic工作特性frequency频率revolutionsperminute 转/分motoring电动机驱动generating发电per-unitvalue标么值breakdowntorque极限转矩breakawayforce起步阻力overhauling检修wind-drivengenerator风动发电机revolutionspersecond转/秒numberofpoles极数speed-torquecurve转速力矩特性曲线plugging反向制动synchronousspeed同步转速percentage百分数locked-rotortorque锁定转子转矩full-loadtorque满载转矩primemover 原动机iushcurrent涌流magnetizingreacance磁化电抗line-to-neutral 线与中性点间的staorwinding定子绕组leakagereactance漏磁电抗no-load空载fullload满载Polyphase多相(的)iron-loss铁损compleximpedance复数阻抗rotorresistance转子电阻leakageflux漏磁通locked-rotor锁定转子choppercircuit斩波电路separatelyexcited他励的compounded复励dcmotor直流电动机demachine直流电机speedregulation速度调节shunt并励series串励armaturecircuit电枢电路opticalfiber光纤interoffice局间的waveguide波导波导管bandwidth 带宽lightemittingdiode发光二极管silica硅石二氧化硅regeneration再生,后反馈放大coaxial共轴的,同轴的high-performance高性能的carrier载波mature成熟的SingleSideBand(SSB)单边带couplingcapacitor结合电容propagate传导传播modulator调制器demodulator解调器linetrap限波器shunt分路器amplitudemodulation(am调幅FrequencyShiftKeying(FSK)移频键控tuner调谐器attenuate衰减incident入射的two-wayconfiguration二线制generatorvoltage发电机电压dcgenerator直流发电机polyphaserectifier 多相整流器boost增压timeconstant时间常数forwardtransferfunction正向传递函数errorsignal误差信号regulator调节器stabilizingtransformer稳定变压器timedelay延时directaxistransienttimeconstant直轴瞬变时间常数transientresponse瞬态响应solidstate固体buck补偿operationalcalculus算符演算gain增益pole 极点feedbacksignal反馈信号dynamicresponse动态响应voltagecontrolsystem电压控制系统mismatch失配errordetector误差检测器excitationsystem励磁系统fieldcurrent励磁电流transistor晶体管high-gain高增益boost-buck升压去磁feedbacksystem 反馈系统reactivepower无功功率feedbackloop反馈回路automaticV oltageregulator(aVR)自动电压调整器referenceV oltage基准电压magneticamplifier磁放大器amplidyne微场扩流发电机self-exciting自励的limiter限幅器manualcontrol手动控制blockdiagram方框图linearzone线性区potentialtransformer电压互感器stabilizationnetwork稳定网络stabilizer稳定器air-gapflux气隙磁通saturationeffect饱和效应saturationcurve饱和曲线fluxlinkage磁链perunitvalue标么值shuntfield并励磁场magneticcircuit磁路load-saturationcurve负载饱和曲线air-gapline气隙磁化线polyphaserectifier多相整流器circuitcomponents电路元件circuitparameters电路参数electricaldevice电气设备electricenergy电能primarycell原生电池energyconverter电能转换器conductor导体heatingappliance电热器direct-current直流timeinvariant时不变的self-inductor自感mutual-inductor互感thedielectric电介质storagebattery蓄电池e.m.f=electromotivefore电动势unidirectionalcurrent单方向性电流circuitdiagram电路图loadcharacteristic负载特性terminalvoltage端电压externalcharacteristic外特性conductance电导volt-amperecharacteristics 伏安特性篇三:电动机介绍我们这里所说的电动机,一般都是指能为车辆行驶提供全部或部分动力来源的电动机。
汉译英_高级职称
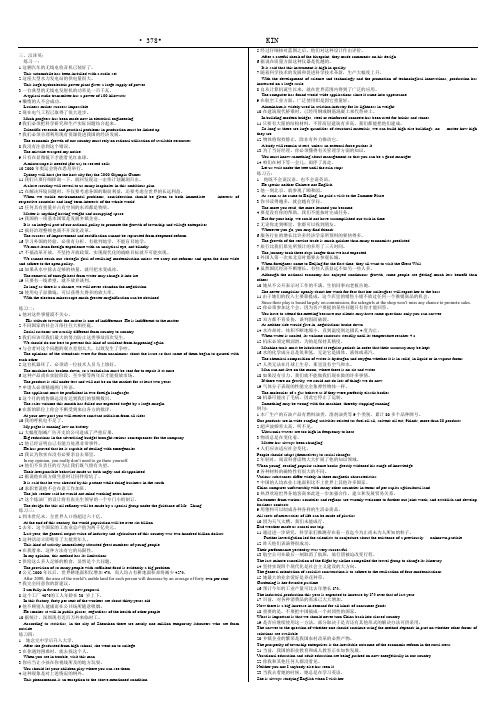
The mistake escaped my notice.
9.只有在显微镜下才能看见红血球。
A microscope is needed (for us) to see red cells.
10.2000年奥运会将在悉尼举行。
Sydneywill host (be the host city for) the 2000 Olympic Games.
After a careful check of the blueprint, they made comments on his design.
6.据说在质量方面这种仪器是优越的。
It is said that this instrument is high in quality.
2.不同国家的社会习俗往往大相径庭。
Social customs are usually different from country to country.
3.我们应该尽我们最大的努力防止这类事故再次发生。
We should do our best to prevent this kind of accident from happening again.
At the end of this century, the world population will be over six billion.
2.去年,这个国家的工农业总产值为两千亿美元。
Last year, the general output value of industry and agriculture of this country was two hundred billion dollars.
KUTAI ADVR-08 Universal Hybrid Analog-Digital Volt

KUTAI ELECTRONICS INDUSTRY CO., LTD.TEL : +886-7-8121771FAX : +886-7-8121775Website : Headquarters : No.3, Lane 201, Chien Fu St., Chyan Jenn Dist., Kaohsiung 80664, TAIWANADVR-08Universal Hybrid Analog-Digital Voltage Regulator Operation ManualAn Universal Hybrid Analog/Digital 2 lines sensing 8 Amp AVR with multiple power input capability such as Full Harmonic (Compound Windings), Harmonic + Auxiliary Winding, PMG and SHUNT.Compatible with Leroy Somer* R438, R448, R449 and more.Use with KUTAI IVT-1260 / IVT-2460 add-on module can boost generator motor starting capacity.SECTION 1 : SPECIFICATIONSensing Input (E1, E2) Static Power DissipationVoltage 110 - 480 Vac, 1 phase Max.6 watts90 - 130 Vac @ 110 Vac180 - 260 Vac @ 220 Vac Burden in SHUNT & PMG Wiring340 - 520 Vac @ 380 Vac 880 VA @ power input 110 Vac Frequency 50/60 Hz, DIP switch setting 1760 VA @ power input 220 VacPower Input (X1, X2, Aux1)Quadrature Droop Input (S1, S2, S3)Voltage 40 - 300 Vac, 1 phase / 3 phase CT 5A (S1-S2) or 1A (S2-S3) greater than 5VA Frequency 50 - 500 Hz Max. +/- 5% @ P.F +/- 0.71 phase (X1、X2) / 3 phase (X1、X2、Aux1)Analogue Voltage Input (A1, A2)Auxiliary Input (Aux1, Aux2)Input resistance greater than 2K ohmsVoltage 40 - 300 Vac, 1 phase Max. Input +/- 5 VdcFrequency 50 - 500 Hz Sensitivity +/- 25% Generator Volts (adjustable)Excitation Output (F+, F-)Under Frequency Protection (Factory Presets) Voltage Max. 63 Vdc @ power input 110 Vac 50 Hz system presets knee point at 45 HzMax. 125 Vdc @ power input 220 Vac 60 Hz system presets knee point at 55 Hz Current Continuous 8AIntermittent 12A for 10 secs. Over Excitation ProtectionResistance ≧8 ohms @ power input 110 Vac Set point 170 Vdc +/- 5 % @ power input 220 Vac ≧16 ohms @ power input 220 VacFuse Spec. Slow blow 5 x 20mm S505-10A Voltage Thermal DriftLess than 3% at temperature range -40 to +70 ˚C External Voltage Adjustment (VR1, VR2)Max. +/- 4% @ 500 ohms 1 watt potentiometer Under-Frequency Knee Point Thermal DriftMax. +/- 8% @ 1K ohm 1 watt potentiometer Less than +/- 0.1 Hz at -40 to +70 ˚CVoltage Regulation EnvironmentLess than +/- 0.5% ( with 4% engine governing ) Operating T emperature -40 to +70 ˚CStorage T emperature -40 to +85 ˚CBuild Up Voltage Relative Humidity Max. 95%6 Vac 25 Hz residual volts at power input terminal Vibration 3 Gs @ 100 - 2K HzSoft Start Ramp Time Dimensions4 seconds +/- 10% 171.0 (L) x 120.0 (W) x 50.0 (H) mmTypical System Response WeightLess than 20 milliseconds 820 g +/- 2%EMI SuppressionInternal electromagnetic interference filtering___________________________________________________________________________________________ 2ADVR-08SECTION 2 : OUTLINE / SIZE / INSTALLATION REFERENCEFlag Terminal (“Fast-On” terminal)Figure 1Outline Drawing___________________________________________________________________________________________ ADVR-08 3___________________________________________________________________________________________ 4ADVR-08SECTION 3 : DIP SWITCH PROGRAMMING & VR ADJUSTMENTSU/F LEDO/E LEDSet fully50 Hz System : 40 to 51 Hz (Lowest position)60 Hz System : 50 to 61 Hz (Lowest position)(See TRIM)This adjustment allows some control over the generator voltage dip when applying load.It is typically used to compensate for turbo lag, leaving the generator to operate below the UFRO knee point setting. The voltage droop ratio can be set using the DIP adjustment. The range is 10 to 3 V/Hz.HZ HZ___________________________________________________________________________________________ ADVR-085SECTION 4 : WIRING CONNECTIONSExciter fieldPMGS2-S3 N:1AS 2-S 3 N :1AS 1-S 2 N :5A C.T Stator windingsS2-S3 N:1AS1-S2 N:5A Exciter fieldS2-S3 N:1AS1-S2 N:5A C.TFigure 2 Single & Three Phase PMGFigure 3 Three Phase AuxiliaryWinding (Full Harmonic)Figure 4 Auxiliary & HarmonicFigure 5 Self-Excited (SHUNT)Exciter fieldFigure 6ADVR-08 & IVT-1260 / IVT-2460 Wiring Connection※Use only the replacement fuses specified in this user manual.※Appearance and specifications of products are subject to change for improvement without prior notice.___________________________________________________________________________________________ 6ADVR-08。
active EMI filters for automotive motor drivers

Abstract—EMI filters for automotive motor drives must achieve stringent EMI specifications while meeting tight cost constraints. This paper explores the use of low-cost active circuitry to suppress motor drive emissions, thus reducing passive filtration requirements. Challenges to the use of active EMI filters in this application are outlined, and means for addressing these challenges are presented. A voltage sense, current drive active filter is developed that greatly enhances the performance of filter capacitors. The proposed approach is applied to an input filter for an automotive electro-hydraulic power steering pump drive. Experimental results are presented that demonstrate the feasibility and high performance of this approach and illustrate its advantages over conventional filter designs.Index Terms—EMI Filter, Active EMI Filter, Active Ripple FilterI.I NTRODUCTIONulse-width modulated (PWM) motor drives are becoming widely used in automotive applications due to their high performance and efficiency. One drawback of such drives is that they generate ripple. Stringent EMI specifications limit the maximum amount of ripple allowed. Therefore, PWM converters require input filters that provide substantial attenuation at EMI frequencies (e.g., >150 kHz). These filters can prove to be quite large and costly.Typically, input EMI filters utilize capacitors to provide a low impedance shunt path for high-frequency currents. Such capacitors must be able to shunt current over a wide frequency range. To achieve this, various types of capacitors are placed in parallel. Large-capacitance electrolytic capacitors are used to shunt lower frequencies and provide voltage holdup. For mid-range frequencies, smaller tantalum or ceramic capacitors are employed. Small ceramic capacitors are used for high EMI frequencies. The relative cost per capacitance is typically higher for capacitors that perform better at higher frequencies. Large-valued electrolytics are used because of their low cost, high energy storage densities, and high ripple current capabilities, but they have poor high-frequency performance. On the other hand, ceramic capacitors have excellent high frequency performance, but are used sparingly due to cost.An alternative to the conventional passive filtering approach is to use a hybrid passive/active filter [2-13]. In this approach, a reduced passive filter is coupled with an active electronic circuit to attenuate the ripple. The passive filter serves to limit the ripple to a level manageable by the active circuit, and to attenuate ripple components that fall beyond the bandwidth of the active circuit. The active filter circuit cancels or suppresses the low frequency ripple components that are most difficult to attenuate with a passive low-pass filter, thus easing the requirements on the passive filter. Structurally, an active ripple filter comprises a sensor (current or voltage), a linear amplifier, and drive circuit (current or voltage) configured to cancel or suppress ripple components in the passive filter output. This approach can permit a significant reduction in the passive filter cost.This paper focuses on the application of active filtering techniques to input filters of pulse-width modulated (PWM) motor drives. As a design example, this paper focuses on the design of an input filter for an automotive electro-hydraulic power steering (EHPS) pump drive. Section II presents an analysis of a typical passive EMI filter for this application. This passive filter will serve as a benchmark for the active filter in terms of cost and performance. Section III will illustrate the primary design constraints of applying active filters to PWM motor drives. Section IV gives an overview of active filter techniques for input filters. Section V will explore an active filter design for this application. Section VI will present experimental results, and section VII concludes the paper.II.P ASSIVE F ILTER C HARACTERISTICSTo illustrate the tradeoffs in filtering for PWM motor drives, this paper considers an input EMI filter for the PWM inverter in an EHPS pump motor drive. This application uses an inverter to convert the 14V DC voltage into three phase AC toActive EMI Filters for Automotive Motor DrivesAlbert C. Chow David J. PerreaultLaboratory for Electromagnetic and Electronic SystemsMassachusetts Institute of TechnologyM.I.T. Rm. 10-039Cambridge, MA 02139(617) 258-6038FAX: (617) 258-6774Pdrive a brushless motor for the EHPS system. The electrical motor replaces the belt-drive for a hydraulic fluid pump, and allows for more efficient operation of the power steering system. The inverter has a fundamental switching frequency of 10 KHz and a peak input current of 70 amps.The structure of a typical passive input filter for this application is illustrated in Fig. 11. It uses a modified pi filter structure with a 3900 µF electrolytic capacitor at the input to the inverter and a 22µF ceramic capacitor at the supply interface. Separating the two capacitors are two 3.6 µH inductors providing both common mode and differential mode filtering. In addition to the electrolytic capacitor at the inverter input there is a small ceramic (1nF) capacitor in parallel with it for higher frequencies. The same is true of the large-valued ceramic capacitor (22µF). An approximate cost breakdown of this filter is illustrated in Table 1, based on commercial pricing in quantities of 20002. The high-valued ceramic capacitor costs about the same as the large electrolytic capacitor though it is physically much smaller. This passive filter will serve as a benchmark for performance and cost. Active filter techniques will be explored with the objective of improving filter cost while maintaining filter performance.III.D ESIGN C ONSIDERATIONSIn most automotive a nd commercial applications, cost is a major consideration. Historically, active filter methods have been most widely applied in applications where the need for high performance justifies additional cost. This work seeks a reduction of cost through active filtering while maintaining constant performance.1 The design of Fig. 1 closely approximates one in recent commercial production for this application.2 While this does not reflect automotive pricing scales it is a reasonable measure of relative component costs. We are unable to account for differences in how individual components costs scale to high volume.Based on the cost breakdown of Table 1 alone, any of the major components are reasonable targets for augmentation via active techniques. Power dissipation considerations, however, restrict us to utilizing active techniques in the outer stages of the filter. To understand this, consider the large electrolytic capacitor. The feasibility of applying active circuit techniques to a capacitor is dependent on the ripple current the capacitor must carry. Simulations suggest that this bulk capacitor carries peak ripple current on the order of 40A (worst-case) and up to 15A RMS, making it impractical to augment its performance via active methods. Conversely, the 22µF ceramic capacitor carries a worst-case ripple current of 0.9A (peak-to-peak), making it a more reasonable target for active techniques. The inductors could also be augmented using active techniques. However the topological complexity of doing this (see, e.g., [13]) may make this less desirable from a cost standpoint. Thus, this paper focuses on applying active circuits to replace the outer stage 22µF ceramic filter capacitor.In order for an active filter to be a commercially viable replacement for the capacitor, the entire active filter must cost under $2. The severe cost constraints in this application allow the use of only lower-end, minimal cost transistors, such as the 3904 and 3906. These transistors are standard signal-leveltransistors in a TO-92 package, and have a power dissipationlimit of around a third of a watt. Designing an amplifier to handle the full peak current ripple (0.9A peak) is difficult with such devices, and rapidly becomes cost prohibitive.The outer-stage filter capacitor sees substantial ripple current in this application. This is characteristic of PWM drive filters. In dc/dc converter applications, the fundamental switching frequency is typically in or near the frequency range covered by EMI specifications (e.g., >150 kHz), and hence is greatly attenuated by the inner filter stages. PWM motor drives, however, typically switch at very low frequencies (10 kHz in the example considered here), which are well below the frequency range covered by EMI specifications. Therefore, a significant amount of the fundamental ripple appears at the filter output. That is, it is not cost effective (or required) to filter the fundamental switching frequency and its low-order harmonics, so these components are not greatly attenuated by the inner filter elements and still appear at the outer part of the filter. This is an important factor in design of active filter circuits for this application.The large, low-frequency component in the ripple poses a substantial challenge in the active filter design because of theincreased power dissipation required to attenuate this ripple, which directly translates to an increase in cost. A saving factor lies in typical EMI specifications such as SAE J1113/41. While the majority of the ripple is due to the fundamental switching frequency of the inverter and its low-order harmonics, EMI ripple attenuation is only required from 150 kHz onward. If the active components are able to reject the low-frequency components (< 150 kHz) and operate only on the EMI frequencies, the power-driving requirement on the active filter is greatly reduced. Therefore, with appropriate design an active filter approach is viable in this application. A further constraint is that the active filter circuitry must be powered from the available 14V power supply bus. Other power supply requirements would unacceptably increase the system cost. Given these constraints, design of the active filters for this application is quite interesting and challenging.IV. A CTIVE T ECHNIQUES FOR INPUT FILTERSIn general, active ripple filters are linear amplifier circuits that enhance the performance of passive impedances. The active filter may either increase the effective impedance of a series path or reduce the effective impedance of a shunt path. For example, as illustrated in Fig. 2 (left) a series active f i lter introduces a voltage in series with a noise source, effectively increasing the impedance of that series path to noise currents. Similarly, a shunt active ripple filter is placed in shunt with a noise source, reducing the effective impedance of the shunt path (Fig. 2, right). A variety of filter structures and control methods are possible, but generally conform to one or both of these approaches.Noise suppression control can be achieved through feedforward and/or feedback. Feedforward control relies on a small but precise gain. For a perfect feedforward path gain of unity, the ripple would be entirely cancelled. However, due to gain and phase accuracy limitations in the components, feedforward cancellation alone cannot fully attenuate the ripple. On the other hand, feedback relies on a large but possibly imprecise gain. The feedback gain is directly proportional to the ripple suppression. In other words, the larger the gain the larger the ripple attenuation; an infinite gain would yield zero ripple. Stability considerations limit theachievable feedback suppression. A combination of bothfeedback and feedforward control is also possible.V.A CTIVE F ILTER D ESIGNA.Active Filter TopologyAs previously described, this paper introduces a shunt active filter circuit to replace the output (battery-side) capacitor in the motor drive filter. The active filter reduces the shunt-path impedance at the filter output by enhancing the performance of a small capacitor using a feedback control configuration. A feedback approach was selected because it was found to be less costly to implement a high gain feedback circuit than to implement an amplifier with a precise gain and low phase shift in a feedforward configuration.Capacitor enhancement can be implemented using various means including current-sense/current-drive, voltage-sense/voltage-drive, current-sense/voltage-drive, and current-sense/current-drive [11,12]. A voltage-sense/voltage drive configuration was selected for cost reasons. Although the amplifier design uses a voltage drive, the overall active filter can be thought of as using current injection. The amplifier drives a voltage across a load capacitor, which converts it into an AC current. This strategy is illustrated in F ig. 3 and provides an effective shunt-path impedance Z eq as shown there. Voltage drive enables low-loss injection to be achieved without an additional supply voltage, and voltage sensing is more economically realized than is current sensing for a given circuit gain.Although the active filter is implemented as one multistage amplifier, it is advantageous to break the design into two pieces: the sensing filter and the amplifier (see Fig. 4). The sensing filter, H(s), measures the voltage, and filters it to select which frequencies to pass onto the amplifier and which frequencies to reject. The amplifier, A, merely takes the voltage signal given by the sensing filter, amplifies it, and drives the resulting voltage across the reduced passive capacitor.B.Design of Sensing FilterThe design of the sensing filter proves to be a primary challenge of this system. It determines the power dissipation of the drive stage and sets the closed-loop dynamics. The ideal sensing filter would have a sharp cutoff, essentially goingfrom high attenuation to high gain in less than a decade, rejecting the fundamental (10 kHz) and low-order harmonics, and passing EMI frequencies (>150 kHz). Such a sharp cutoff would require a high order sensing filter, complicating the topology and making it more difficult to attain a stable feedback loop. Loop compensation may be added within the sensing filter to achieve stability, but this again adds complexity and oscillations may occur due to amplifier non-linearities3. Ultimately, amplifier nonidealities make it difficult to use a sensing filter with an order higher than one. Unfortunately, a first-order (high-pass) sensing filter does not provide enough separation between the pass band and stop band. The filter is unable to sufficiently attenuate the 10 KHz signal (to within the power limitations of the amplifier transistors), while still providing adequate gain at 150 KHz and beyond.To overcome these limitations, a low-frequency, low impedance bypass network is placed in parallel with the sensing filter, reducing the low frequency ripple voltage it3 Nonlinearities can cause the loop gain of the feedback system to decrease for certain input magnitudes, driving the system unstable. sees. The network comprises one or more medium-sized electrolytic capacitors. The low cost of electrolytics makes this a viable solution. Electrolytic capacitors have poor performance at higher frequencies, where their ESL and ESR limit their ability to shunt current. By placing an electrolytic capacitor larger than 22 µF in parallel with the active filter, the lower frequency currents, including the 10 KHz fundamental, will be shunted from the a ctive filter (see Fig 5); two 22 µF electrolytic capacitors are used in the prototype system. At higher EMI frequencies, where the electrolytic capacitor ceases to perform well, the active filter takes over and shunts the high-frequency currents. At still higher frequencies, beyond the bandwidth of the active circuit, a small ceramic capacitor serves as the shunt element.C.Design of the AmplifierThe primary functions of the amplifier are to provide the feedback loop gain and to drive the voltage across the capacitor. A three-stage amplifier is chosen for these functions, comprising a gain stage, a buffer stage, and an output stage (Fig. 6). As mentioned previously, the entire amplifier circuit is implemented with inexpensive, low-end transistors. The gain stage (first stage) uses a common emitter configuration. Common emitter amplifiers offer a large input impedance, which is ideal for voltage sensing. The gain of the overall amplifier is determined by active filter requirements. Since the suppression of the current ripple is directly proportional to the feeback loop gain, the design of the amplifier should maximize the gain. However with any feedback system, the tradeoff between gain and stability is theprimary performance limitation. The upper limit on the amountof gain achievable is set by the stability of the system. As mentioned previously, the stability is highly dependent upon the sensing filter. The maximum amount of stable gain can be easily determined by standard feedback loop design techniques (a gain of 150 is used in the prototype). Furthermore, this amplifier configuration is bandwidth limited due to the Miller effect, which multiplies capacitances by the gain of the system. Fortunately, the bandwidth of the circuit (~2MHz) is sufficient for the application.The following two stages, the buffer stage and the output stage, are closely related. The buffer stage is implemented with two emitter followers and the output stage uses a push-pull configuration. The second stage provides large input impedance for the gain stage and biases the output stage. The gain stage has a relatively large output impedance therefore a buffer stage is needed to maintain the gain of the amplifier. The output stage has been designed to minimize DC bias currents and therefore the overall dissipation of the system. A push-pull circuit has no bias current, but it does have a dead zone. In the dead zone the output voltage is zero if the input voltage is within the thermal voltage of the transistor. A smallbias current is passed through both push-pull transistors in order to eliminate the dead zone (class AB). The two transistors are biased with emitter followers, which have the extra benefit of increasing the input impedance to the drive stage. One concern of a push-pull output stage is maintaining bias stability. In this configuration, it is possible for the current to increase with out bound. Placing resistors in the emitters of the push-pull transistors is one solution. The emitter resistors serve provide bias feedback and to limit the amount of current f low. The output stage does not provide any voltage gain. It serves as a voltage buffer and a power gain stage.The voltage-sense/voltage-drive topology, which injects current, has the drawback of increased peak current, which affects the achievable bandwidth of the system. Simulation can facilitate the prediction of the peak current needed. The hybrid system is modeled as a sensing filter with lead compensation, two 22 µF electrolytic capacitors, and an ideal voltage gain driving a load capacitor (see Fig 7). Simulations show that the peak current needed is 500mA. The 3904 and 3906 transistors are not designed to handle these peaks 50B Vcurrents. Fortunately, the 2222 and 2906 can accommodate this current magnitude, cost the same, and have the same packaging. The tradeoff is that the 2222 and 2906 have a lower unity beta bandwidth than the 3904 and 3906. This is due to the larger parasitic capacitances of the 2222 and 2906. Fig. 6 shows the resulting active filter circuit, not including the two 22µF electrolytic, low-frequency, bypass capacitors.The overall active filter yields a substantial cost benefit over the purely passive filter. The active filter effectively replaces the 22µF ceramic capacitor. The total cost of the active filter is $0.70 verses $2.00, the cost of the capacitor (see Table 2). Thecomponent cost is given as US dollars per unit for a quantity of two thousand.VI.E XPERIMENTAL R ESULTSThe test setup of the system used a current noise source. The PWM motor drive can be approximated by a square wave current source, with a duty cycle of 50 percent and a peak current of 15 amps. Standard EMI measurement techniques are followed. A LISN (Line Impedance Stabilization Network) is placed between the filter and the 14 V supply. The LISN passes power frequency signals to the load, while acting as a known impedance at ripple frequencies. The voltage across the 50 ohm LISN resistor is used as the metric for input ripple performance.The performance of the hybrid filter is determined by first taking measurements without the active filter element. Essentially, the only outer-stage filter capacitance is the two medium sized (22µF) electrolytic capacitors. Measurements were then taken with the active filter in operation. Figure 8 illustrates the dramatic improvement in output voltage ripple performance that is achieved through the use of the active circuitry. The spectral measurements confirm the poor performance of the electrolytic capacitors at higher frequencies. The active circuitry provides an additional attenuation over using the electrolytic capacitors alone. Next, a performance comparison is needed between the benchmark passive filter (with the 22 µF ceramic capacitor) and the hybrid/active filter. Relative performance of these circuits is shown in Fig. 9. The performance of the two filters is the same at the higher frequencies. At the lower frequencies the ripple is slightly higher in the hybrid/active filter than the purely passive filter. The slight difference in performance between the two at lower frequencies is acceptable because the SAE EMI specification allows for more ripple at these lower frequencies. Therefore, the active filter allows expensive ceramic capacitors to be replaced with inexpensive electrolytic capacitors (plus active filter) with no degradation in performance. The demonstrated benefit of the proposed approach is that by introducing simple, signal-level active circuitry, one can dramatically reduce the filter cost for the same level of performanceVII.C ONCLUSIONActive ripple filters can effect substantial reductions in power converter input and output filter cost. This paper investigates a hybrid passive/active filter topology that uses a shunt filter approach in a feedback configuration. The desi gn of a sense filter and amplifier suitable for the application are investigated. The experimental results demonstrate the feasibility and high performance of the new approach, and illustrate its potential benefits. It is demonstrated that the proposed approach is most effective in cases where it is desirable to reduce the capacitance cost in the filter. In these cases, a cost reduction of 65% is possible, without impacting ripple performance.A CKNOWLEDGMENTThe authors would like to acknowledge the support for this research provided by the United States Office of Naval Research under grant number N00014-00-1-0381, and by the member companies of the MIT/Industry Consortium on Advanced Automotive Electrical/Electronic Components and Systems. In addition the authors would like to give special thanks to Mr. Philip Desmond of Motorola AIEG and Mr. Peter Miller of Ricardo for their valuable input in this project.R EFERENCES[1]T.K. Phelps and W.S. Tate, “Optimizing Passive Input FilterDesign,” Proceedings of Powercon 6, May 1979, pp. G1-1 - G1-10.[2]M. Zhu, D.J. Perreault, V. Caliskan, T.C. Neugebauer, S.Guttowski, and J.G. Kassakian, “Design and Evaluation of anActive Ripple Filter with Rogowski-Coil Current Sensing,” IEEEPESC Record, Vol. 2, 1999, pp. 874 -880.[3]S. Feng , W. A. Sander, and T. Wilson, “Small-CapacitanceNondissipative Ripple Filters for DC Supplies,” IEEE Transactions on Magnetics, Vol. 6, No. 1, March 1970, pp. 137-142.[4] D.C. Hamill “An Efficient Active Ripple Filter for Use in DC-DCConversion,” IEEE Transactions on Aerospace and ElectronicSystems, Vol. 32, No. 3, July 1996, pp. 1077-1084.[5]N.K. Poon, J.C.P. Liu, C.K. Tse, and M.H Pong, “Techniques forInput Ripple Current Cancellation: Classification andImplementation,” IEEE Transactions on Power Electronics, Vol.15, No. 6, November 2000, pp. 1144-1152.[6]J. Walker, “Designing Practical and Effective Active EMI filters,”Proceedings of Powercon 11, 1984, I-3 pp. 1-8.Quantity Description Cost ($)/Unit2 Small Ceramic (pF) 0.041 0.22 µF Ceramic 0.072 0.47 µF Ceramic 0.112 22 µF Electrolytic BypassCapacitor0.045 Transistors 0.05Table 2: C ost break down of the components in the hybrid filter. The cost per unit is based on estimated cost attained for quantities of 2000.[7]L.E. LaWhite and M.F. Schlecht, “Active Filters for 1 MHzPower Circuits With Strict Input/Output Ripple Requirements,”IEEE Transactions on Power Electronics, Vol. PE-2, No.4,October 1987, pp. 282-290.[8]T. Farkas and M.F. Schlecht, “Viability of Active EMI Filters forUtility Applications,” IEEE Transactions on Power Electronics,Vol. 9, No. 3, May 1994, pp. 328-337.[9]M.S. Moon and B.H. Cho, “Novel Active Ripple Filter for theSolar Array Shunt Switching Unit,” Journal of Propulsion andPower, Vol. 12, No. 1, January-February 1996, pp. 78-82. [10]P. Midya and P.T. Krein, “Feed-forward Active Filter for OutputRipple Cancellation,” International Journal Electronics, Vol. 77,No. 5, pp. 805-818.[11]L.R. Casey, A. Goldberg, and M.F. Schlecht, “Issues Regarding theCapacitance of 1-10 MHz Transformers,” Proceedings IEEEAPEC, 1988, pp. 352 –359.[12] A. Goldberg, J.G. Kassakian, and M.F. Schlecht, “Issues Related to1-10-MHZ Transformer Design,” IEEE Transactions on PowerElectronics, Vol. 4, No. 1, January 1989, pp. 113-123.[13] A.C. Chow, D.J. Perreault, “Design and evaluation of an activeripple filter using voltage injection,” IEEE PESC Record, Vol.1, 2001, pp. 390 –397.。
电机英语(常用必备型+专业检索型)

电机英语(常用必备型)电机(马达)electric motor,微电机 micro motor小电机 small motor分马力电机 fractional horsepower motor空调暧通电机 HVAC motor (heating, ventilating air-conditioning motor) 直流电机 Direct current motor, DC motor串励直流电机 series wound DC motor并励直流电机 shunt wound DC motor复励直流电机 compound wound DC motor直流无刷电机 Brushless direct current motor, BLDC motor串激电机 universal motor交流电机 Alternating current motor, AC motor齿轮电机 Geared motor, Gear motor同步电机 synchronous motor异步电机 asynchronous motor, induction motor罩极电机 shaded pole motor步进电机 step motor, stepper motor, stepping motor混合式 hybrid磁阻式 variable reluctance永磁式 permanent magnet步距角精度 step angle accuracy转轴 shaft轴向负载 axial load轴向窜动 axial endplay径向跳动 radial runout负载 on load过载 overload额定负载 rated load空载 no-load电流 current电压 voltage防护等级 protection class, degree of protection, isolation class绝缘等级 insulation class力距 torque起动力距 starting torque最大(崩溃)转距 break down torque堵转 locked rotor保持力距 holding torque共振 resonance电线(电缆)cable测试程序 test procedure性能测试 performance test耐压测试 dielectric test (high pot test)功能测试 functionality test, function test实地测试 field test寿命测试 life test老化试验 ageing test连续运转continuous duty, continuous running间歇运转intermittent duty, intermittent running温升试验 temperature rise test环境温度 ambient temperature峰值 peak value供应商 supplier, vendor, seller客户 customer, client, buyer样品(样机)prototype, sample试生产 pilot production, try-out production小批生产 pre-series production批量生产 series production打筋 spline滚花 knurl攻丝 tap键槽 keyway定位销 stop pin螺钉 screw螺纹 thread螺栓 bolt螺母 nut联结器(接插件)connector端子:terminal标签, 铭牌 label nameplate外形尺寸 outside dimension outline精度 accuracy公差 tolerance不符合要求non-conformity, out of specification前端盖front flange, front end cover, front end bell, front end shield 后端盖 rear flange, rear end cover, rear end bell rear end shield凸台 pilot齿轮,带轮 pinion, gear wheel, gear滚珠轴承 ball bearing含油轴承 sleeve bearing, bronze bearing, self lubricating bearing转子 rotor定子 stator铁芯 core电枢 armature磁钢 magnet整流子(换向器)commutator碳刷 carbon brush, brush刷握 brush holder机壳 housing/shell轴承室 bearing housing出轴 shaft extension扁丝 flat工装、夹具 jigs, fixtures, tooling规 gauge引出线 lead wire, leads线路板 PCB (printed circuit board)驱动器 driver, drive冲片 lamination槽 slot齿 teeth轭 yoke硅钢片 silicon steel漆包线 copper wire/enamel insulated copper wire 胶带 tape压铸 die casting注塑 mould injection波纹垫圈 wave washer车加工 machining 精车: turning霍尔传感器 hall sensor开关 switch装配 assemble, assembly生产制造 make, manufacture, produce动平衡 balance. balancing热处理 heat treatment表面淬火 case hardening穿透淬火 through hardening退火 annealing正火 temper表面涂覆 surface coating喷砂 sandblast涂胶 gluing滴漆 varnish电泳 powder coating E-coating力矩速度曲线 speed torque curve磁通 flux工艺流程图 process flow chart绝缘骨架 plastic bobbin止口 rabbet粗糙度 roughness同心度 concentricity偏心度 eccentricity垂直度 perpendicularity平行度 parallelism串激电机:universal motor转子:转轴: shaft 换向器:commutator 铁芯:rotor steel core 端板:end spider绝缘纸:rotor steel liner 槽楔(环):wedge ring U型挡圈:U type retainer漆包线:field magnet wire 轴承:bearing 绝缘漆:varnish 换向片:commutator segment定子:铁芯:rotor steel core 漆包线:field magnet wire 绝缘纸:rotor steel liner支架:bracket支撑组件:机壳:housing 端盖:support frame碳刷组件:碳刷:brush 碳刷套:brush sleeve 碳刷架(刷握):brush holder 弹簧:brush spring刷辫:brush flexible 刷盒:brush box风机部分:定叶轮:diffuser(guide vane)动叶轮:impeller 风罩:fan cover 螺钉:screw螺帽: nut-fan 压圈:gasket-fan 衬套:bush-fan爬电距离:creepage distances specify :指定(动)附加绝缘:supplementary insulation clause :条款(名)基本绝缘:basic insulation wear :磨损(动)加强绝缘:reinforced insulation clearance :电气间隙Clearance and creepage distances over supplementary and reinforced insulation not reduced below the values specified in clause 29 as a resultof wear.accessible :易接近的,可到达的,易受影响的loose :宽松的,不牢固的Creepage distances and clearance between live parts and accessible partsnot reduced below values specified for supplementary insulation ifwires ,screws etc. becomes loose.Vaccum吸尘器 Hose:软管 Attachment :附件,附加装置 Transformer :变压器From the result of our inspection and tests on the submitted samples,we conclude that that they comply with the requirements of the standards.Submit:提交,递交 inspection : 检查 comply with : 符合All models have same constructions, and are portable,dry-pick up vaccum cleaners for household use .Different models in one series with different postfixes are same products, but marked with different powers. Refer to below table for difference between models in different series.Postfix : 后缀 refer to : 查阅提到谈到打听电动机:motor直流电动机:direct current motor交流电动机:alternating current motor交直流两用电动机:universal motor同步电动机: synchronous motor {siNkrEnEs]笼型同步电动机: cage synchronous motor同步感应电动机:synchronous induction motor磁阻电动机: reluctance motor亚同步磁阻电动机: subsynchronous reluctance motor异步电动机:asynchronous motor {eI`sINkrEnEs}感应电动机: induction motor无刷绕线转子感应电动机:brushless wound-rotor induction motor他励:separately excited自励:self-excited混励:compositely excited并励:shunt串励:series复励:compound excited复励:用以指明电机至少由两个绕组励磁,其中之一是串励绕组绕组:winding初级绕组:primary winding次级绕组:secondary winding主绕组:main winding定子绕组:stator winding转子绕组:rotor winding电枢绕组:armature winding阻尼绕组:damping winding起动绕组:starting winding辅助起动绕组: auxiliary starting winding励磁绕组: excitation winding磁场绕组: field winding试验:性能试验:performance test型式试验:type test重复试验:duplicated test检查试验:routing test 对每台电机在制造完工后所进行的试验,以判明其是否符合标准抽样试验:sampling test验收试验:acceptance test效率:efficiency 输出功率对输入功率之比总损耗:total loss(of a machine) ; power losses(of a machine ) 输入与输出功率之差热量试验:calorimetric test 从电机所产生的热量来推算损耗的试验方法空载试验:no-load test 在电机作电动机运行而轴上无有效机械输出时进行的试验轻载试验:light load test 当电机在驱动或被驱动状态下运行时,做为电动机,仅供给被驱动机械的空载损耗。
电机英文专业术语分解
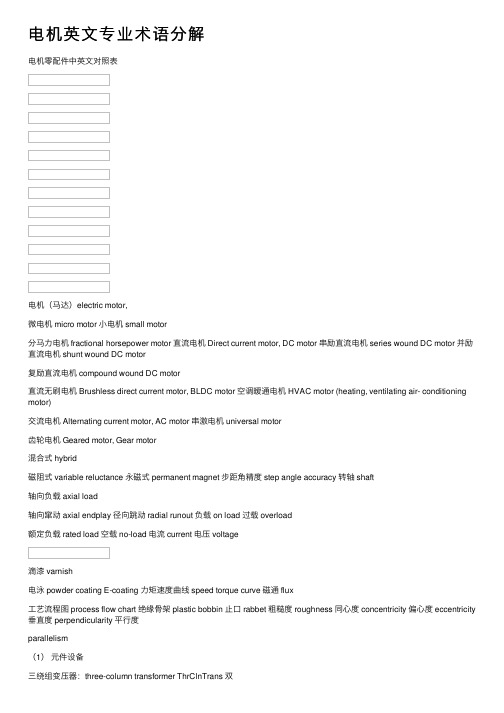
电机英⽂专业术语分解电机零配件中英⽂对照表电机(马达)electric motor,微电机 micro motor ⼩电机 small motor分马⼒电机 fractional horsepower motor 直流电机 Direct current motor, DC motor 串励直流电机 series wound DC motor 并励直流电机 shunt wound DC motor复励直流电机 compound wound DC motor直流⽆刷电机 Brushless direct current motor, BLDC motor 空调暧通电机 HVAC motor (heating, ventilating air- conditioning motor)交流电机 Alternating current motor, AC motor 串激电机 universal motor齿轮电机 Geared motor, Gear motor混合式 hybrid磁阻式 variable reluctance 永磁式 permanent magnet 步距⾓精度 step angle accuracy 转轴 shaft轴向负载 axial load轴向窜动 axial endplay 径向跳动 radial runout 负载 on load 过载 overload额定负载 rated load 空载 no-load 电流 current 电压 voltage滴漆 varnish电泳 powder coating E-coating ⼒矩速度曲线 speed torque curve 磁通 flux⼯艺流程图 process flow chart 绝缘⾻架 plastic bobbin ⽌⼝ rabbet 粗糙度 roughness 同⼼度 concentricity 偏⼼度 eccentricity 垂直度 perpendicularity 平⾏度parallelism(1)元件设备三绕组变压器:three-column transformer ThrClnTrans 双DblClmnTrans 电电抗器:Reactor 母线:Busbar输电线:TransmissionLine 发电⼚:power plant 断路器:Breaker⼑闸(隔离开关):Isolator 分接头:tap 电动机:motor (2)状态参数有功:active power档位:tap position有功损耗:reactive loss功⾓:power-angle开关 switch装配 assemble, assembly ⽣产制造 make, manufacture, produce动平衡 balance. balancing 热处理 heat treatment 表⾯淬⽕ case hardening 穿透淬⽕ through hardening 退⽕ annealing 正⽕ temper表⾯涂覆 surface coating电⼒专业英语铁损:iron loss铜损:copper loss空载电流:no-load current阻抗:impedance正序阻抗:positive sequence impedance负序阻抗:negative sequence impedance零序阻抗:zero sequence impedance电阻:resistor电抗:reactance电导:conductance电纳:susceptance⽆功负载:reactive load 或者QLoad有功负载:active load PLoad遥测:YC(telemetering)遥信:YX励磁电流(转⼦电流):magnetizing current定⼦:stator功⾓:power-angle上限:upper limit下限:lower limit并列的:apposable⾼压:high voltage低压:low voltage中压:middle voltage电⼒系统power system发电机generator励磁excitation电流current母线bus变压器transformer升压变压器step-up transformer⾼压侧high side输电系统power transmission system输电线transmission line固定串联电容补偿fixed series capacitor compensation 稳定stability电压稳定voltage stability功⾓稳定angle stability暂态稳定transient stability电⼚power plant能量输送power transfer交流AC装机容量installed capacity电⽹power system落点drop point开关站switch station双回同杆并架double-circuit lines on the same tower 变电站transformer substation 补偿度degree of compensation⾼抗high voltage shunt reactor⽆功补偿reactive power compensation故障fault调节regulation裕度magin三相故障three phase fault故障切除时间fault clearing time极限切除时间critical clearing time切机generator triping⾼顶值high limited value强⾏励磁reinforced excitation线路补偿器LDC(line drop compensation)机端generator terminal静态static(state)动态dynamic (state)单机⽆穷⼤系统one machine-infinity bus system 机端电压控制AVR 电抗reactance电阻resistance功⾓power angle有功(功率)active power⽆功电流reactive current下降特性droop characteristics斜率slope额定rating变⽐ratio参考值reference value电压互感器PT分接头tap下降率droop rate仿真分析simulation analysis传递函数transfer function框图block diagram受端receive-side裕度margin同步synchronization失去同步loss of synchronization阻尼damping摇摆 swing保护断路器 circuit breaker电抗:reactance 阻抗:impedance电导:conductance 电纳:susceptance 导纳:admittance40脉振磁场(pulsating magnetic field ):单相异步电动机的定⼦绕组是单相绕组,⼯作时定⼦绕组接在单相交流电源上,单相电流通过单相绕组产⽣与绕组轴线⼀致、⽽⼤⼩和⽅向随时间作正弦规律变化的交变磁场,称为脉振磁场。
- 1、下载文档前请自行甄别文档内容的完整性,平台不提供额外的编辑、内容补充、找答案等附加服务。
- 2、"仅部分预览"的文档,不可在线预览部分如存在完整性等问题,可反馈申请退款(可完整预览的文档不适用该条件!)。
- 3、如文档侵犯您的权益,请联系客服反馈,我们会尽快为您处理(人工客服工作时间:9:00-18:30)。
A Combination of Shunt Hybrid Power Filterand Thyristor-Controlled Reactorfor Power QualitySalem Rahmani,Abdelhamid Hamadi,Student Member,IEEE,Kamal Al-Haddad,Fellow,IEEE,andLouis A.Dessaint,Fellow,IEEEAbstract—This paper proposes a combined system of a thyristor-controlled reactor(TCR)and a shunt hybrid power filter(SHPF)for harmonic and reactive power compensation.The SHPF is the combination of a small-rating active powerfilter (APF)and afifth-harmonic-tuned LC passivefilter.The tuned passivefilter and the TCR form a shunt passivefilter(SPF) to compensate reactive power.The small-rating APF is used to improve thefiltering characteristics of SPF and to suppress the possibility of resonance between the SPF and line inductances.A proportional–integral controller was used,and a triggering alpha was extracted using a lookup table to control the TCR.A nonlinear control of APF was developed for current tracking and voltage regulation.The latter is based on a decoupled control strategy, which considers that the controlled system may be divided into an inner fast loop and an outer slow one.Thus,an exact lin-earization control was applied to the inner loop,and a nonlinear feedback control law was used for the outer voltage loop.Integral compensators were added in both current and voltage loops in order to eliminate the steady-state errors due to system parameter uncertainty.The simulation and experimental results are found to be quite satisfactory to mitigate harmonic distortions and reactive power compensation.Index Terms—Harmonic suppression,hybrid powerfilter,mod-eling,nonlinear control,reactive power compensation,shunt hybrid powerfilter and thyristor-controlled reactor(SHPF-TCR compensator),thyristor-controlled reactor(TCR).I.I NTRODUCTIONN ONLINEAR loads cause significant harmonic currents with poor input power factor(PF),which create serious problems at the power supply system.Traditionally,passive Manuscript received May4,2012;revised September7,2012,December30, 2012,and March21,2013;accepted May11,2013.Date of publication July10, 2013;date of current version October18,2013.This work was supported in part by the Canada Research Chair in Energy Conversion and Power Electronics at theÉcole de Technologie Supérieure,by the Fonds de Recherche du Quebec-Nature et Technologie(FRQNT),and by the National Science and Engineering Research Council of Canada.A.Hamadi and K.Al-Haddad are with the Canada Research Chair in Electric Energy Conversion and Power Electronics,École de Technologie Supérieure, Montreal,QC H3C1K3,Canada(e-mail:abdelhamidhamadi@yahoo.fr;kama. al-haddadl@ele.etsmtl.ca).S.Rahmani is with the Canada Research Chair in Electric Energy Conversion and Power Electronics,École de Technologie Supérieure, Montreal,QC H3C1K3,Canada,and also with the Electrical Engineering Department,High Institute of Medical Technologies of Tunis,University of Tunis El-Manar,Tunisia(e-mail:rsalem02@yahoo.fr).L.A.Dessaint is with the Electrical Engineering Department,École de Technologie Supérieure,Montréal,QC H3C1K3,Canada(e-mail:dessaint@ ele.etsmtl.ca).Color versions of one or more of thefigures in this paper are available online at .Digital Object Identifier10.1109/TIE.2013.2272271filters have been used to eliminate current harmonics of the supply network.However,these devices suffer from resonance. Recently,thyristor-switchedfilters(TSFs),which contain sev-eral groups of passivefilters,have been used to compensate reactive power[1].The compensation amount of TSFs can be adjusted with the variation of load power[2].However,the parallel and the series resonance could occur between TSF and grid impedance.Activefilters were developed to mitigate problems of passivefilters[3]–[5].They are more effective in harmonic compensation and have good performance[6]–[8]. However,the costs of activefilters are relatively high for large-scale system and require high power converter ratings[9],[10]. Hybridfilters effectively soften the problems of the passive filter and an activefilter solution and provide cost-effective harmonic compensation,particularly for high-power nonlinear loads[11]–[14].Many control techniques such as instanta-neous reactive power theory,synchronous rotating reference frame,sliding-mode controllers,neural network techniques, nonlinear control[15],feedforward control[16],Lyapunov-function-based control[17],etc.,have been used to improve the performance of the active and hybridfilters.Severalfilter topologies for compensating harmonics and reactive power have been reported in the literature[18]–[21].In [18],a multiconverter conditioner topology formed by an active conditioner operating in parallel with a hybrid conditioner has been proposed.The hybrid conditioner consists of one or more passivefilters in series with a low-rated active powerfilter (APF).The conditioner compensates harmonic distortion,im-balance,and reactive power in three-phase four-wire systems. This topology constitutes an effective solution at high-power levels,which is cost-effective because of the kilovoltampere rating reduction of the inverters.A hybrid configuration based on the combination of a three-phase three-level neutral point clamped(NPC)inverter and a series connection of a three-level H-bridge inverter with a novel control scheme to control the floating voltage source of the H-bridge stage has been presented in[19].In this topology,the NPC inverter is used to supply the total active power while the H-bridges operate as series activefilters for the harmonic compensation of the NPC output voltage.The rating of the series activefilter is reduced because the latter provides only the reactive power for the operation of thefloating capacitor.In[20],a combination of a thyristor-controlled reactor(TCR)and a resonant impedance-type hybrid APF for harmonic cancellation,load balancing,and reactive power compensation has been proposed.The control strategy0278-0046©2013IEEEof the system is based on the voltage vector transformation for compensating the negative-sequence current caused by the unbalance load without using phase-locked loops.A predictive current controller based on the Smith predictor is proposed to compensate the generalized current delay.A combined system of a static var compensator(SVC)and a small-rated APF for harmonic suppression and reactive power compensation has been reported in[21].The SVC consists of a Y-connected passive powerfilter and a delta-connected TCR.The APF is used to eliminate harmonic currents and to avoid resonance between the passive powerfilters and the grid impedance.In this paper,a new combination of a shunt hybrid power filter(SHPF)and a TCR(SHPF-TCR compensator)is proposed to suppress current harmonics and compensate the reactive power generated from the load.The hybridfilter consists of a series connection of a small-rated activefilter and afifth-tuned LC passivefilter.In the proposed topology,the major part of the compensation is supported by the passivefilter and the TCR while the APF is meant to improve thefiltering characteristics and damps the resonance,which can occur between the passive filter,the TCR,and the source impedance.The shunt APF when used alone suffers from the high kilovoltampere rating of the inverter,which requires a lot of energy stored at high dc-link voltage.On the other hand,as published by some authors[15],the standard hybrid powerfilter is unable to compensate the reactive power because of the behavior of the passivefilter.Hence,the proposed combination of SHPF and TCR compensates for unwanted reactive power and harmonic currents.In addition,it reduces significantly the voltampere rating of the APF part.The control method of the combined compensator is presented.A control technique is proposed to improve the dynamic response and decrease the steady-state error of the TCR.It consists of a PI controller and a lookup table to extract the requiredfiring angle to compensate a reactive power consumed by the load.A nonlinear control of SHPF is developed for current tracking and voltage regulation purposes. It is based on a decoupled control strategy,which considers that the controlled system may be divided into an inner fast loop and an outer slow one.The currents injected by the SHPF are controlled in the synchronous orthogonal dq frame using a decoupled feedback linearization control method.The dc bus voltage is regulated using an output feedback linearization control.The SHPF can maintain the low level of dc bus voltage at a stable value below50V.The proposed nonlinear control scheme has been simulated and validated experimentally to compute the performance of the proposed SHPF-TCR com-pensator with harmonic and reactive power compensation and analysis through the total harmonic distortion(THD)of the source and the load current.The proposed methodology is tested for a wide range of loads as discussed further.Simulation and experimental results show that the proposed topology is suitable for harmonic suppression and reactive compensation.II.S YSTEM C ONFIGURATION OFSHPF-TCR C OMPENSATORFig.1shows the topology of the proposed combined SHPF and TCR.The SHPF consists of a small-rating APF connected in series with afifth-tuned LC passivefilter.The APF consists of a three-phase full-bridge voltage-source pusle width modu-lation(PWM)inverter with an input boost inductor(L pf,R pf) and a dc bus capacitor(C dc).The APF sustains very low fundamental voltages and currents of the power grid,and thus, its rated capacity is greatly reduced.Because of these merits, the presented combined topology is very appropriate in com-pensating reactive power and eliminating harmonic currents in power system.The tuned passivefilter in parallel with TCR forms a shunt passivefilter(SPF).This latter is mainly forfifth-harmonic compensation and PF correction.The small-rating APF is used tofilter harmonics generated by the load and the TCR by enhancing the compensation characteristics of the SPF aside from eliminating the risk of resonance between the grid and the SPF.The TCR goal is to obtain a regulation of reactive power.The set of the load is a combination of a three-phase diode rectifier and a three-phase star-connected resistive inductive linear load.III.M ODELING AND C ONTROL S TRATEGYA.Modeling of SHPFThe system equations arefirst elaborated in123reference ing Kirchhoff’s voltage law,one can writev s1=L PFdi c1dt+R PF i c1+v CPF1+v1M+v MN v s2=L PFdi c2dt+R PF i c2+v CPF2+v2M+v MN v s3=L PFdi c3dt+R PF i c3+v CPF3+v3M+v MN v CPF1=L Tdi c1dt−C PF L T d2v CPF1dt2v CPF2=L Tdi c2dt−C PF L T d2v CPF2dt2v CPF3=L Tdi c3dt−C PF L T d2v CPF3dt2dv dcdt=1C dci dc.(1)The switching function c k of the k th leg of the converter(for k=1,2,3)is defined asc k=1,if S k is On and Skis Off0,if S k is Off and Skis On.(2)A switching state function d nk is defined asd nk=c k−133m=1c mn.(3)Moreover,the absence of the zero sequence in the ac currents and voltages and in the[d nk]functions leads to the following transformed model in the three-phase coordinates[15]:L PFdi c1dt=−R PF i c1−d n1v dc−v CPF1+v s1 L PFdi c2dt=−R PF i c2−d n2v dc−v CPF2+v s2 L PFdi c3dt=−R PF i c3−d n3v dc−v CPF3+v s3C dcdv dcdt+v dcR dc=d n1i c1+d n2i c2+d n3i c3.(4)Fig.1.Basic circuit of the proposed SHPF-TCR compensator.The system of(4)is transformed into the synchronous orthogo-nal frame using the following general transformation matrix:C123 dq =23cosθcos(θ−2π/3)cos(θ−4π/3)−sinθ−sin(θ−2π/3)−sin(θ−4π/3)(5)whereθ=ωt and the following equalities hold:C dq123=(C123dq )−1=(C123dq)T.Then,by applying dq transformation,the state space model of the system in the synchronous reference frame is given in the Appendix by(26).This model is nonlinear because of the existence of multi-plication terms between the state variables{i d,i q,V dc}and the switching state function{d nd,d nq}.However,the model is time invariant during a given switching state.Furthermore,the principle of operation of the SHPF requires that the three state variables have to be controlled indepen-dently.The interaction between the inner current loop and the outer dc bus voltage loop can be avoided by adequately separating their respective dynamics.B.Harmonic Current ControlA fast inner current loop,and a slow outer dc voltage loop, is adopted.Thefirst two equations in the model can be written as shown in the Appendix by(27).Note that thefirst and theFig.2.Inner control loop of the current i d .second time derivative TCR capacitor voltages have no sig-nificant negative impact on the performance of the proposed control technique because their coefficients are too low.Conse-quently,they can practically be ignored.Define the equivalent inputs by (28)as given in the Appendix.Thus,with this transformation,the decoupled dynamics of the current tracking is obtained.The currents i d and i q can be controlled independently.Furthermore,by using propor-tional integral compensation,a fast dynamic response and zero steady-state errors can be achieved.The expressions of the tracking controllers areu d =L PF (1−C PF L T ω2)+L Tdi d dt+R PF (1−C PF L T ω2)i d=k p ˜i d +k i˜i d dtu q =L PF (1−C PF L T ω2)+L Tdi q dt+R PF (1−C PF L T ω2)i q =k p ˜i q +k i˜i q dt(6)where ˜i d =i ∗d −i d and ˜i q =i ∗q −i q are current errors and i ∗dand i ∗q denote the reference signals of i d and i q ,respectively.The transfer function of the proportional–integral controllers is given asG i 1(s )=U d (s )˜i d (s )=k p 1+k i 1s G i 2(s )=U q (s )˜i q (s )=k p 2+k i 2s.(7)The inner control loop of the current i d is shown in Fig.2.The closed-loop transfer functions of the current loops areI d (s )I ∗d (s )=k p 1A s +k i 1k p 1s 2+ B +k p 1As +k i 1I q (s )I ∗q (s )=k p 2As +k i 2kp 2s 2+ B +k p 2As +ki 2(8)where A =L PF (1−C PF L T ω2)+L T and B =R PF (1−C PF L T ω2).The closed-loop transfer functions of the current loops have the following form:I d (s )I ∗d (s )=2ζωni s +ωni2ζs +2ζωni s +ω2ni(9)where ωni is the outer loop natural angular frequency and ζisthe damping factor.For the optimal value of the dampingfactorpensated voltage regulated model.ζ=√2/2,the theoretical overshoot is 20.79%.The following design relations can be derived:k p 1=k p 2=2ζωni L PF (1−C PF L T ω2)+L T−R PF (1−C PF L T ω2)k i 1=k i 2=(L PF (1−C PF L T ω2)+L T )ω2ni .The control law is given in the Appendix by (29)and (30).Note that the inputs q nd and q nq consist of a nonlinearity cancellation part and a linear decoupling compensation part.C.DC Bus Voltage RegulationIn order to maintain the dc bus voltage level at a desired value,acting on i q can compensate the losses through the hybrid power filter components.The output of the controller is added to the q -component current reference i q as shown in Fig.4.The third equation in the model (6)is rewrittenC dcdv dc dt +v dc R dc=d nq i q .(10)The three-phase filter currents are given by⎡⎣i c 1i c 2i c 3⎤⎦= 23i q ⎡⎣−sin θ−sin θ−2π3 −sin θ−2π3 ⎤⎦.(11)The fundamental filter rms current I c isI c =i q√3.(12)The q -axis active filter voltage v Mq is expressed asv Mq =q nq v dc =−Z PF1i ∗q 1(13)where Z PF1is the impedance of the passive filter at 60Hz andi ∗q 1is a dc component.An equivalent input u dc is defined asu dc =q nq i q .(14)The control effort of the dc voltage loop is deducedi ∗q 1=v dc−Z PF1i qu dc .(15)The dc component will force the SHPF-TCR compensator togenerate or to draw a current at the fundamental frequency.To regulate the dc voltage v dc ,the error ˜v dc =v ∗dc −v dc is passed through a PI-type controller given byu dc =k 1˜v dc +k 2˜v dc dt.(16)Fig.3illustrates the outer control loop of the dc bus voltage.Fig.4.Control scheme of the proposed SHPF-TCR compensator.The response of the dc bus voltage loop is a second-order transfer function and has the following form:V dc (s )V ∗dc (s )=2ζωnv s +ωnv2ζs 2+2ζωnv s +ω2nv.(17)The closed-loop transfer function of dc bus voltage regula-tion is given as follows:V dc (s )V ∗dc(s )=√3Z PF1k p I cdc C dcs +√3Z PF1k i I c dc C dc s 2+√3Z PF1k p I cdc C dcs+√3Z PF1k i I cdc C dc (18)where V dc is the average value of the dc voltage which is equalto 50V .The proportional k 1and integral k 2gains are then ob-tained as follows:k 1=2ζωnv (V dc C dc /√3Z PF1I c ),and k 2=ω2nv (V dc C dc /√3Z PF1I c ).By designing the dc bus voltage loop much slower than the current one,there would not be any interaction between the two loops.The proposed nonlinear controller of the proposed SHPF-TCR compensator is shown in Fig.4.Fig.5.TCR equivalent circuit.IV .M ODELING OF TCRFig.5shows the TCR equivalent circuit.Using Kirchhoff’s voltage law,the following equations in 123reference frame are obtained:v s 1=L T di LT1dt +L PF di c 1dt +R PF i c 1+d n 1v dc v s 2=L Tdi LPF2dt +L PF di c 2dt +R PF i c 2+d n 2v dc v s 3=L Tdi LPF3dt +L PF di c 3dt+R PF i c 3+d n 3v dc .(19)Fig.6.Susceptance versusfiring angle.Applying Park’s transformation,one obtainsL T(α)di LTddt=L T(α)ωi LTq+L PFωi q−L PFdi ddt −R PF i d−d nd v dc+v dL T(α)di LTqdt=−L T(α)ωi LTd−L PFωi d−L PFdi qdt−R PF i q−d nq v dc+v q.(20)The reactive part is chosen to control the reactive current so that v q=0and L f(α)ωi LTd=0di LTq dt =B(α)ω−L PFωi d−L PF di qdt−R PF i q−d nq v dc(21)where B(α)=1/L F(α)ωis the susceptance. An equivalent input u qT is defined asu qT=di LTqdt.(22)According to this expression,one deducesB(α)=u qTω−L PFωi d−L PF di qdt−R PF i q−d nq v dc.(23)On the other hand,the equivalent inductance is given byL PF(α)=L PFπ2π−2α+sin(2α).(24)The susceptance is given byB(α)=B 2π−2α+sin(2α)π(25)where B=1/L PFω0.Fig.6illustrates the susceptance versusfiring angle.A PI controller is used to force the reactive current of the SHPF-TCR compensator to follow exactly the reactive current consumed by the load.V.R ATING OF APF P ARTIn this proposed topology,the major part of the compensation is supported by the passivefilter and the TCR while the APF improves thefiltering characteristics and damps the resonance,TABLE IA PPARENT P OWER R ATINGS OF APF PARTwhich can occur between the passivefilter,the TCR,and the source impedance.The objective of the APF is to generate currents that are equal but opposite to the harmonic and reactive currents,thereby achieving sinusoidal supply currents in phase with supply voltages.On the other hand,the shunt APF when used alone suffers from the high kilovoltampere rating of the inverter,which requires high dc-link voltage.Hence,the proposed combination of SHPF and TCR reduces significantly the voltampere rating of the APF part.A.Case of Harmonic-Generated LoadThefilter rms current is only2.443A for the required APF, the load rms current is8.231A,the line rms voltage across the load is120V,and the dc bus voltage V dc is selected to be50V.B.Case of Reactive Power and Harmonic Type of LoadsThefilter rms current is2.49A for the required APF,the load rms current is9.7A,the line rms voltage across the load is 120V,and the dc bus voltage V dc is50V.Table I shows the apparent power ratings of the APF part for the harmonic-generated load and reactive power and harmonic type of loads.It is shown that the rating of the APF part used in the shunt hybridfilter is reduced from26%to5%for the harmonic-generated load and from15%to4.37%for the reactive power and harmonic type of loads.Thus,the rating reduction of the APF is the main contributor to the total cost reduction of the system.VI.S IMULATION R ESULTSThe system parameters are given in Table II.Simulations were performed numerically using the“Power System Block-set”simulator operating under Matlab/Simulink environment, in order to verify the operation of the proposed SHPF-TCRTABLE IIS PECIFICATION PARAMETERSFig.7.Steady-state response of the SHPF-TCR compensator with harmonic-generated load.compensator using the nonlinear control scheme shown in Figs.1and 5.The controller’s performance has been evaluated by achiev-ing a number of tests on the proposed SHPF-TCR compensator:1)steady-state response of the SHPF-TCR compensator to load-generating harmonics;2)dynamic response of the SHPF-TCR compensator to harmonic-produced load variations;and 3)response of the SHPF-TCR compensator to the harmonic and reactive power type of load variation.A.Harmonic Compensation of SHPF-TCR Compensator Fig.7shows the steady-state waveform of the SHPF-TCR compensator for harmonic elimination with a three-phase harmonic-produced load.The supply voltage (v s 1),the supply current (i s 1),the load current (i L 1),the SHPF-TCR current (i c 1)in phase 1,and the dc bus voltage (v dc )are depicted in this figure.Fig.8(a)and (b)shows the harmonic spectrum of the supply current before and after compensation.The THD of the supply current is brought down from 26%to 1.31%.It is found that the SHPF-TCR compensator offers a very good level of performance such that the supply current is close to sinusoidal and locked in phase with the supplyvoltage.Fig.8.Harmonic spectrum of source current in phase 1.(a)Before compen-sation.(b)Aftercompensation.Fig.9.Dynamic response of SHPF-TCR compensator under varying distorted harmonic type of load conditions.B.Response of SHPF-TCR Compensator to Harmonic-Produced Load VariationFig.9shows the SHPF-TCR compensator response to harmonic-produced load perturbation for phase 1.The load currents were subjected to a 100%step increase at 0.567s and a step decrease at 0.667s by the same amount.It is found that there is a smooth changeover from one load condition to another load condition.The dc bus voltage returns to the reference voltage value.The SHPF-TCR compensator is able to reduce harmonics in the supply currents,and it improves the supply PF to unity.Fig.10.Dynamic response of SHPF-TCR compensator under the harmonic and reactive power type ofloads.Fig.11.Harmonic spectrum of source current in phase 1.(a)Before compen-sation.(b)After compensation.C.Response of SHPF-TCR Compensator to Harmonic and Reactive Power CompensationIn order to observe the SHPF-TCR compensator behavior under both harmonic and reactive power type of load variation,the load-generating reactive power current was subjected from zero to a full load step increase and the other way around.The corresponding phase-1dynamic responses of the SHPF-TCR compensator for reactive power compensation and harmonic elimination are shown in Fig.10.It is observed from Fig.11that the supply current before compensation was quite distorted and has a THD of 16%;however,its THD is reduced to 1%after compensation.The compensated source current shown in this figure suggests that the proposed SHPF-TCRcompensatorFig.12.Steady-state response of the SHPF-TCR compensator with harmonic-produced load.can effectively compensate the load-generated harmonics and reactive power exchanged by both loads.VII.E XPERIMENTAL R ESULTSThe following tests are performed on a 3.5-kV A laboratory prototype of the SHPF-TCR compensator used to compensate harmonics and reactive power of loads.The nonlinear control system was implemented on a dSPACE DS 1104controller board,supported by a Matlab/Simulink Real-Time Workshop environment.The component values given in Table I were used for both simulation and experimentation.The set of loads consists of a diode rectifier and a star-connected combination of resistive and inductive loads.The experimental setup used to test the dynamic performance of the SHPF-TCR compensator has the following combined harmonic and reactive power type of loads.1)A three-phase diode rectifier followed by inductor L L 1=10mH in series with a resistor R L 1=40Ωis used as the harmonic-produced load.2)A three-phase star-connected resistive inductive load with inductor L L 2=20mH and resistor R L 2=27Ωis used experimentally to cause current to lag voltage and to make up a mixed load together with the three-phase harmonic-generated load.To verify the proposed nonlinear control algorithm per-formance,four different operating conditions are considered:1)steady-state performance of the SHPF-TCR compensator with a harmonic-produced load;2)dynamic performance of the SHPF-TCR compensator with harmonic-generated load;3)steady-state performance of the SHPF-TCR compensator with the harmonic and reactive power type of loads;and 4)dynamic performance of the system with the harmonic and reactive power type of loads.A.Steady-State Response of System With Harmonic-Generated LoadFig.12shows the steady-state experimental results of the proposed SHPF-TCR compensator for harmonic compensationFig.13.Harmonic spectrums of the source current and voltage in phase1.(a)Source current before compensation.(b)Source current after compensation.(c)Source voltage.with a load for phase1.In thisfigure,the supply voltage (v s1),supply current(i s1),load current(i L1),and SHPF-TCR current(i c1)are depicted.It can be seen that the source current has become sinusoidal and in phase with the source voltage. The harmonic spectrum of the supply current before and af-ter compensation and the supply voltage after compensation for phase1have been given in Figs.13(a),(b),and14(c), respectively.The THD of the supply current is brought down from26%before compensation to3%after compensation.The THD of the supply voltage after compensation is2.5%.The harmonic spectrums are recorded on a FLUKE43B power quality analyzer.B.Transient Response of SHPF-TCR Compensator to Harmonic-Produced Load VariationTo test the dynamic performance of the proposed nonlinear control,a step increase of100%and a decrease of100%in the harmonic-produced load were made.Fig.14(a)and(b) shows the transient responses of the SHPF-TCR compensator adopting the nonlinear control.At the transition period,the dc bus voltage falls or rises below its steady-state value when the SHPF-TCR compensator supplies or absorbs extra active power to or from the load,respectively.The SHPF-TCR compensator maintains compensation during the transient instants.Thus,the harmonic components of the load current are fully compensated by the system so that the line current is almost a sinusoidal waveform with unityPF.Fig.14.Dynamic response of the proposed SHPF-TCR compensator under varying harmonic-produced load conditions.(a)Step increase of the load current.(b)Step decrease of the loadcurrent.Fig.15.Steady-state response of the proposed SHPF-TCR compensator with harmonic and reactive power type of loads.C.Steady-State Harmonic and Reactive Power Compensation A combination of a three-phase diode-bridge ac–dc converter with an R−L load connected at the dc side and a three-phaseFig.16.Harmonic spectrums of the source current and voltage in phase1.(a)Source current before compensation.(b)Source current after compensation.(c)Source voltage.star-connected resistive–inductive load is chosen to study the transient operation of the SHPF-TCR system for harmonic and reactive power compensation.The PF of the reactive load is0.96.Fig.15shows the steady-state performance of the proposed SHPF-TCR compensator employing the proposed nonlinear control method for the simultaneous compensation of harmonics and reactive power for phase1.The supply voltage(v s1),the supply current(i s1),the load current(i L1) and the SHPF-TCR compensator current(i c1)are shown in thisfigure.The frequency analyses of supply voltage and supply current before and after compensation are shown in Fig.16(a)–(c).The THD of the supply current is brought down from15%before compensation to2.6%after compensation. The THD of the supply voltage after compensation is2.5%. The steady-state performance of the TCR providing reactive power compensation is shown in Fig.17.The waveforms shown in thisfigure are the phase-1source current(i s1),load current (i L1),hybridfilter current(i c1),and TCR current(i Lt1).From the experimental results,one can observe that the harmonic currents and reactive power could be effectively compensated with the SHPF-TCR compensator.The source current is close to sinusoidal and kept in phase with the source voltage.Moreover, harmonics generated naturally by the TCR have two possible paths,the parallel capacitor connected with the TCR or the activefilter.Since the activefilter controller is set to compensate only load harmonics,the latter act as high impedance to TCR current harmonics,obliging these harmonics toflow throughthe Fig.17.TCR providing reactive power compensation in steady-statemode. Fig.18.Dynamic response of the proposed SHPF-TCR compensator undervarying reactive power type of load conditions.capacitor.Therefore,one cannot see these harmonicsflowing through the source or the load.D.Reactive Power and Harmonic Type of Load Perturbation Response of SHPF-TCR CompensatorFig.18shows the transient waveforms of the SHPF-TCR compensator during the sudden variation of the reactive power and harmonic type of loads.It is found that,for a change of load current,the supply current always maintains its sinusoidal shape while being in phase with the supply voltage.These results confirm the fast dynamic performance and the ability of the proposed configuration adopting the nonlinear control strategy to compensate suitably the harmonics and reactive power for a rapid change in the load current.The THDs of the load current before and after the transient occurred are26%and 15%,respectively.The PF of the reactive load is0.96.The TCR is used to realize variable inductance for compen-sating the reactive power.This latter suffers from resonance which possibly occurs between its inductance,source/load impedance,and PF correction capacitors used in industrial applications.Passivefilters suffer from resonance problems and tuning problems due to component tolerances.The problem。