弯管常见的缺陷及其解决措施
弯曲成形缺陷解决方法

弯曲成形缺陷解决方法
1、弯曲外侧壁厚减薄
主要解决路径有:
(1)降低中性层产生拉伸变形的拉应力;
(2)改变变形区内材料应力分布,使拉应力降低,压应力增加。
2、弯曲内侧失稳起皱
主要解决路径
(1)在弯曲成形的时候正确合理使用芯棒和防皱块;
(2)弯管内通过高压液体矫形或将钢球压入弯管内。
3、横截面畸变
(1)在弯曲变形区用芯棒支撑截面,防止截面产生发生畸变;
(2)在弯曲管坯内填充固体颗粒状介质(钢球),弹性介质(橡胶、聚氨酯棒)或低熔点合金等,也可代替芯棒的作用,以防截面畸变;
(3)在弯曲变形区用模具型腔表面从管材外面限制截面形状,做与之吻合的模具型腔,防止截面歪扭,限制截面的畸变。
4、弯曲回弹
由于加载过程中弯曲变形区的内外层的应力应变性质相反,所以管材弯曲弹性变形比其塑性成形要显著,弯曲回弹问题更加突出,有文献根据塑性弯曲理论推导出了计算回弹量的表达式,但通过公式计算出的值与实际值相差太大,因此目前大都是依靠生产现场的经验数据,通过实验修正,达到相除回弹的问题。
如何解决推制无缝弯头的缺陷

如何解决推制无缝弯头的缺陷
施工过程中,我们发现推制弯头管件到货的质量主要存在以下几个方面的问题
一、管件的壁厚不均
推制弯头管件壁厚不均主要发生在管件变形最大的部位.如弯头背部的壁厚薄于其他部位;
管口与管件体的壁厚不等。
国家有关标准中规定.对于此类问题的检查,用一般的卡尺等测量工具往往难以发现,此时只有使用超声测厚仪才可测出。
二、硬度超标
推制弯头硬度超标问题的产生,主要是由于成形后的热处理工艺问题其解决的方法是用正确的热处理工艺再进行一次热处理.
三、材料及加工过程中所产生的缺陷
推制弯头对装置的安全危害最大.检查起来又比较麻烦。
产生缺陷的因素比较多也比较复杂,它既有材料本身的缺陷又有加工制造工艺问题以及热处理工艺的不正确所造成的缺陷。
弯曲件常见质量问题改善对策
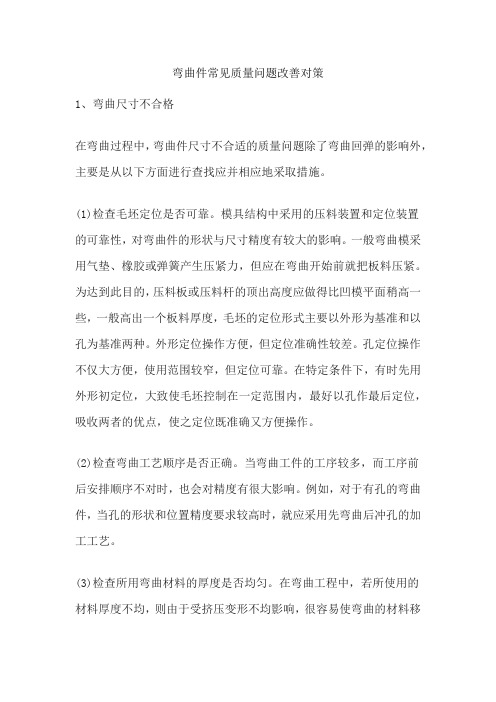
弯曲件常见质量问题改善对策1、弯曲尺寸不合格在弯曲过程中,弯曲件尺寸不合适的质量问题除了弯曲回弹的影响外,主要是从以下方面进行查找应并相应地采取措施。
(1)检查毛坯定位是否可靠。
模具结构中采用的压料装置和定位装置的可靠性,对弯曲件的形状与尺寸精度有较大的影响。
一般弯曲模采用气垫、橡胶或弹簧产生压紧力,但应在弯曲开始前就把板料压紧。
为达到此目的,压料板或压料杆的顶出高度应做得比凹模平面稍高一些,一般高出一个板料厚度,毛坯的定位形式主要以外形为基准和以孔为基准两种。
外形定位操作方便,但定位准确性较差。
孔定位操作不仅大方便,使用范围较窄,但定位可靠。
在特定条件下,有时先用外形初定位,大致使毛坯控制在一定范围内,最好以孔作最后定位,吸收两者的优点,使之定位既准确又方便操作。
(2)检查弯曲工艺顺序是否正确。
当弯曲工件的工序较多,而工序前后安排顺序不对时,也会对精度有很大影响。
例如,对于有孔的弯曲件,当孔的形状和位置精度要求较高时,就应采用先弯曲后冲孔的加工工艺。
(3)检查所用弯曲材料的厚度是否均匀。
在弯曲工程中,若所使用的材料厚度不均,则由于受挤压变形不均影响,很容易使弯曲的材料移动,产生弯曲件的高度尺寸不定。
解决措施是:将凹模修整成可换式镶块结构,通过调整弯曲模间隙的办法来解决;或更换材料,采用料厚均匀稳定的板料。
(4)检查模具两端的弯曲凹模圆角是否均匀一致。
弯曲模在长期使用过程中,常会使凹模圆角半径发生变化,且左右凹模圆角半径不对称一致,从而在弯曲过程中使弯曲件发生移动造成弯曲尺寸发生变化。
解决措施是:修磨凹模圆角半径合格,且使其左右堆成、大小一致。
(5)检查压力机的吨位、气垫压力是否合乎要求。
压力机的吨位及气垫压力会直接影响到弯曲件的尺寸精度,一般应选用吨位大些且精度较高的压力机,通常取加工力是压力机吨位70%-80%比较合适。
(6)检查并重新校核弯曲展开料是否正确。
弯曲件展开料是否正确直接影响到弯曲件尺寸是否合格。
常见弯管缺陷及措施_刘振彬
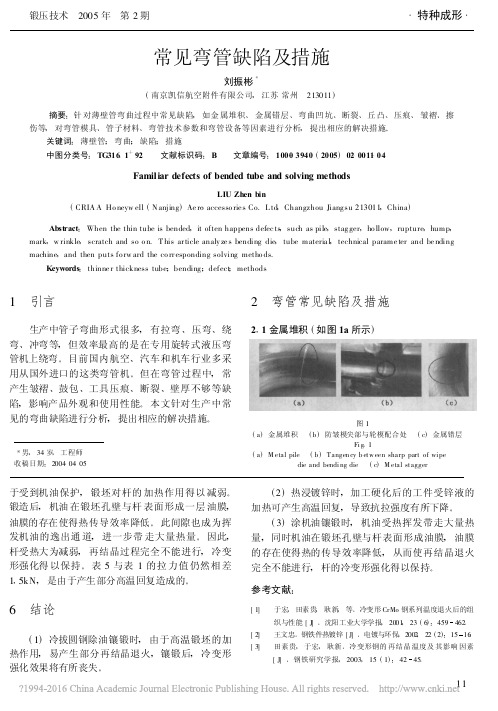
解决办法 :检查芯轴或压模型腔表面有无缺陷 , 如有需修模 ;减小助推和压模压力 , 增大压模与防 轴模间隙 ;清除模具表面金属屑和金属渣 。 2. 5 弯曲断裂 (如图 2c 所示)
12
图3 (a) 芯轴相对于轮模切点位置 (b) 轴向凸包
(c) 弯曲段芯轴球形丘凸 Fi g. 3
(a)Opposit e positi on betw een tangent point of bending die and mandrel (b)Hum p in axis (c)Round hum p of mandrel i n b end sect ion
Abstract :When the thin tube is bended , it often happens defec ts, such as pile , stag ger , ho llow , rupture , hump ,
mark , w rinkle , scratch and so o n. T his ar ticle analy ze s bending die , tube materia l, technical parame ter and be nding machine , and then puts fo rw ard the co rr esponding solving metho ds.
Famil iar defects of bended tube and solving methods
LIU Zhen-bin (CRIA A Ho neyw ell (N anjing) Ae ro-accesso rie s Co.3011, China)
弯管常见的缺陷及其解决措施

弯管常见的缺陷及其解决措施弯管常见的缺陷及其解决措施从工艺分析可知,常见的弯管缺陷主要有以下几种形式:圆弧处变扁严重(椭圆形)、圆弧外侧管壁减薄量过大、圆弧外侧弯裂、圆弧内侧起皱及弯曲回弹等。
随着弯管半径的不同,前四种缺陷产生的方式及部位有所不同,而且不一定同时发生,而弯曲工件的弹性回弹却是不可避免的。
弯管缺陷的存在对弯制管件的质量会产生很大的负面影响。
管壁厚度变薄,必然降低管件承受内压的能力,影响其使用性能;弯曲管材断面形状的畸变,一方面可能引起横断面积减小,从而增大流体流动的阻力,另一方面也影响管件在结构中的功能效果;管材内壁起皱不但会削弱管子强度,而且容易造成流动介质速度不均,产生涡流和弯曲部位积聚污垢,影响弯制管件的正常使用;回弹现象必然使管材的弯曲角度大于预定角度,从而降低弯曲工艺精度。
因此,应在弯制之前采取对应措施防止上述缺陷的产生,以获得理想的管件,保证产品的各项性能指标和外观质量。
在通常情况下,对于前面提到的几种常见缺陷,可以有针对性地采取下列措施:(1) 对于圆弧外侧变扁严重的管件,在进行无芯弯管时可将压紧模设计成有反变形槽的结构形式:在进行有芯弯管时,应选择合适的芯棒(必要时可采用由多节段芯棒组装而成的柔性芯棒),正确安装之,并在安装模具时保证各部件的管槽轴线在同一水平面上。
(2) 小半径弯管时圆弧外侧减薄是弯曲的工艺特点决定的,是不可避免的。
为了避免减薄量过大,常用的有效方法是使用侧面带有助推装置或尾部带有顶推装置的弯管机,通过助推或顶推来抵消管子弯制时的部分阻力,改善管子横剖面上的应力分布状态,使中性层外移,从而达到减少管子外侧管壁减薄量的目的。
(3) 对于管子圆弧外侧弯裂的情况,首先应保证管材具有良好的热处理状态,然后检查压紧模的压力是否过大,并调整使其压力适当,最后应保证芯棒与管壁之间有良好的润滑,以减少弯管阻力及管子内壁与芯棒的摩擦力。
(4) 对于圆弧内侧起皱,应根据起皱位置采取对应措施。
弯管制作质量通病防治措施
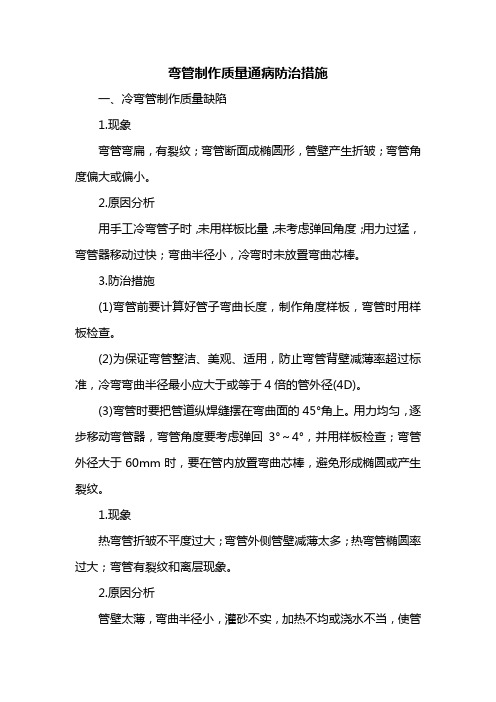
弯管制作质量通病防治措施一、冷弯管制作质量缺陷1.现象弯管弯扁,有裂纹;弯管断面成椭圆形,管壁产生折皱;弯管角度偏大或偏小。
2.原因分析用手工冷弯管子时,未用样板比量,未考虑弹回角度;用力过猛,弯管器移动过快;弯曲半径小,冷弯时未放置弯曲芯棒。
3.防治措施(1)弯管前要计算好管子弯曲长度,制作角度样板,弯管时用样板检查。
(2)为保证弯管整洁、美观、适用,防止弯管背壁减薄率超过标准,冷弯弯曲半径最小应大于或等于4倍的管外径(4D)。
(3)弯管时要把管道纵焊缝摆在弯曲面的45°角上。
用力均匀,逐步移动弯管器,弯管角度要考虑弹回3°~4°,并用样板检查;弯管外径大于60mm时,要在管内放置弯曲芯棒,避免形成椭圆或产生裂纹。
1.现象热弯管折皱不平度过大;弯管外侧管壁减薄太多;热弯管椭圆率过大;弯管有裂纹和离层现象。
2.原因分析管壁太薄,弯曲半径小,灌砂不实,加热不均或浇水不当,使管内侧或弯曲内侧温度高低不均;弯管时施力角度与钢管不垂直;钢管材质差,加热燃料中含硫过多或浇水冷却太快,气温过低,产生离层和裂纹。
3.防治措施(1)热弯前要选择材质好、表面无锈蚀、无弯曲和管壁稍厚于安装直管的加厚管加工;热弯管的弯曲半径应大于或等于3.5~4倍的管外径;防止热弯管背部管壁减薄率和椭圆率超标。
(2)管内应灌装洗净、无杂物、粒径合格的干燥河砂,边灌边震实,灌满后用木塞堵好管口,将加热段放到烘炉或焦炭火上加热,边加热边转动管子,当加热到950℃~1000℃,管子成蛇皮状,并呈现红亮光时停止加热,放在弯管模具或平台上弯管,连续缓慢的进行弯管,当管子降温到700℃,管壁呈樱红色时停止弯管。
(3)弯管时要比预定弯曲角度略大2°~3°,并用样板放在弯管中心层处检查,合格后在受热表面上涂上一层废机油,防止氧化生锈。
(4)用气焊加热弯管时,要预热加热管段,再从起弯点开始加热,边加热、边弯曲、边用水冷却,弯曲半径一致,防止弯曲表面产生折皱。
管道焊接的常见缺陷与质量控制

管道焊接的常见缺陷与质量控制管道焊接的常见缺陷与质量控制一、概述管道焊接是一项重要的工艺,常常用于连接管道系统的各个部分。
然而,在管道焊接过程中存在一些常见的缺陷,这些缺陷可能会影响管道的正常运行和安全性。
因此,对于管道焊接的质量控制十分关键。
二、常见缺陷1.焊缝裂纹焊缝裂纹是一种常见缺陷,可能会降低焊接接头的强度和密封性。
焊缝裂纹通常分为热裂纹、冷裂纹和应力裂纹等不同类型。
2.焊缝内夹杂物焊缝内夹杂物指的是在焊接过程中,焊缝中出现的一些异物,如气孔、夹渣等。
这些夹杂物可能会导致焊缝的疏松和脆性。
3.焊缝偏离设计要求焊缝的几何形状和尺寸偏离设计要求也是一种常见的缺陷。
焊缝偏离可能导致管道连接失效或无法满足工作条件要求。
4.焊接变形焊接过程中,由于热影响和残余应力的影响,管道可能会出现焊接变形。
焊接变形可能导致管道的外观不平整和力学性能的下降。
三、质量控制措施1.材料选择在进行管道焊接前,需要选择合适的焊材和母材。
焊材和母材的材料应满足设计要求,具有良好的焊接性能和耐腐蚀性。
2.焊接操作规程制定详细的焊接操作规程是确保焊接质量的关键措施。
操作规程应包括焊接参数、预热温度、焊接顺序和质量要求等内容。
3.焊接工艺试验在进行实际焊接之前,可以进行焊接工艺试验来确认焊接工艺的可行性和优化焊接参数。
工艺试验应符合相关标准和规定。
4.非破坏性检测通过非破坏性检测方法,如X射线检测、超声波检测等,对管道焊缝进行检测,以发现可能存在的缺陷,并及时采取措施进行修复或调整。
附件:本文档附有管道焊接常见缺陷检测流程图。
法律名词及注释:1.焊接接头:指连接管道的焊接部分。
2.强度:指焊接接头的抗拉、抗压等力学性能。
3.密封性:指焊接接头的防漏功能。
4.热裂纹:指焊接过程中因焊接区域温度差引起的裂纹。
5.冷裂纹:指焊接后冷却过程中由于残余应力导致的裂纹。
6.应力裂纹:指在焊接接头处受到应力作用而产生的裂纹。
核电厂弯管缺陷分析与质量控制
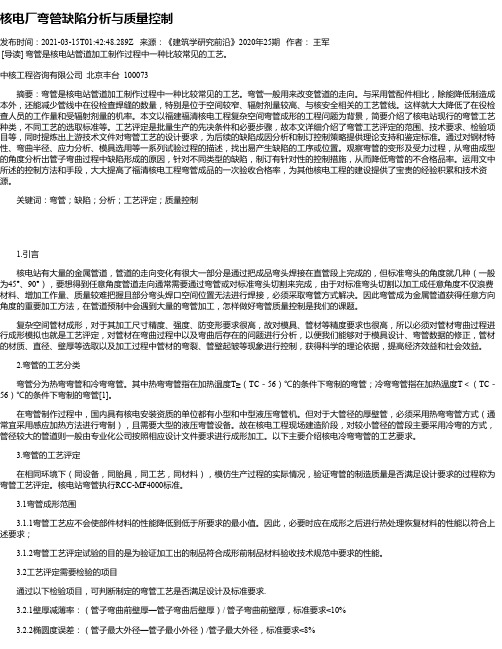
核电厂弯管缺陷分析与质量控制发布时间:2021-03-15T01:42:48.289Z 来源:《建筑学研究前沿》2020年25期作者:王军[导读] 弯管是核电站管道加工制作过程中一种比较常见的工艺。
中核工程咨询有限公司北京丰台 100073摘要:弯管是核电站管道加工制作过程中一种比较常见的工艺。
弯管一般用来改变管道的走向。
与采用管配件相比,除能降低制造成本外,还能减少管线中在役检查焊缝的数量,特别是位于空间较窄、辐射剂量较高、与核安全相关的工艺管线。
这样就大大降低了在役检查人员的工作量和受辐射剂量的机率。
本文以福建福清核电工程复杂空间弯管成形的工程问题为背景,简要介绍了核电站现行的弯管工艺种类,不同工艺的选取标准等。
工艺评定是批量生产的先决条件和必要步骤,故本文详细介绍了弯管工艺评定的范围、技术要求、检验项目等,同时提炼出上游技术文件对弯管工艺的设计要求,为后续的缺陷成因分析和制订控制策略提供理论支持和鉴定标准。
通过对钢材特性、弯曲半径、应力分析、模具选用等一系列试验过程的描述,找出易产生缺陷的工序或位置。
观察弯管的变形及受力过程,从弯曲成型的角度分析出管子弯曲过程中缺陷形成的原因,针对不同类型的缺陷,制订有针对性的控制措施,从而降低弯管的不合格品率。
运用文中所述的控制方法和手段,大大提高了福清核电工程弯管成品的一次验收合格率,为其他核电工程的建设提供了宝贵的经验积累和技术资源。
关键词:弯管;缺陷;分析;工艺评定;质量控制1.引言核电站有大量的金属管道,管道的走向变化有很大一部分是通过把成品弯头焊接在直管段上完成的,但标准弯头的角度就几种(一般为45°、90°),要想得到任意角度管道走向通常需要通过弯管或对标准弯头切割来完成,由于对标准弯头切割以加工成任意角度不仅浪费材料、增加工作量、质量较难把握且部分弯头焊口空间位置无法进行焊接,必须采取弯管方式解决。
因此弯管成为金属管道获得任意方向角度的重要加工方法,在管道预制中会遇到大量的弯管加工,怎样做好弯管质量控制是我们的课题。
- 1、下载文档前请自行甄别文档内容的完整性,平台不提供额外的编辑、内容补充、找答案等附加服务。
- 2、"仅部分预览"的文档,不可在线预览部分如存在完整性等问题,可反馈申请退款(可完整预览的文档不适用该条件!)。
- 3、如文档侵犯您的权益,请联系客服反馈,我们会尽快为您处理(人工客服工作时间:9:00-18:30)。
弯管常见的缺陷及其解决措施从工艺分析可知,常见的弯管缺陷主要有以下几种形式:圆弧处变扁严重(椭圆形)、圆弧外侧管壁减薄量过大、圆弧外侧弯裂、圆弧内侧起皱及弯曲回弹等。
随着弯管半径的不同,前四种缺陷产生的方式及部位有所不同,而且不一定同时发生,而弯曲工件的弹性回弹却是不可避免的。
弯管缺陷的存在对弯制管件的质量会产生很大的负面影响。
管壁厚度变薄,必然降低管件承受内压的能力,影响其使用性能;弯曲管材断面形状的畸变,一方面可能引起横断面积减小,从而增大流体流动的阻力,另一方面也影响管件在结构中的功能效果;管材内壁起皱不但会削弱管子强度,而且容易造成流动介质速度不均,产生涡流和弯曲部位积聚污垢,影响弯制管件的正常使用;回弹现象必然使管材的弯曲角度大于预定角度,从而降低弯曲工艺精度。
因此,应在弯制之前采取对应措施防止上述缺陷的产生,以获得理想的管件,保证产品的各项性能指标和外观质量。
在通常情况下,对于前面提到的几种常见缺陷,可以有针对性地采取下列措施:(1) 对于圆弧外侧变扁严重的管件,在进行无芯弯管时可将压紧模设计成有反变形槽的结构形式:在进行有芯弯管时,应选择合适的芯棒(必要时可采用由多节段芯棒组装而成的柔性芯棒),正确安装之,并在安装模具时保证各部件的管槽轴线在同一水平面上。
(2) 小半径弯管时圆弧外侧减薄是弯曲的工艺特点决定的,是不可避免的。
为了避免减薄量过大,常用的有效方法是使用侧面带有助推装置或尾部带有顶推装置的弯管机,通过助推或顶推来抵消管子弯制时的部分阻力,改善管子横剖面上的应力分布状态,使中性层外移,从而达到减少管子外侧管壁减薄量的目的。
(3) 对于管子圆弧外侧弯裂的情况,首先应保证管材具有良好的热处理状态,然后检查压紧模的压力是否过大,并调整使其压力适当,最后应保证芯棒与管壁之间有良好的润滑,以减少弯管阻力及管子内壁与芯棒的摩擦力。
(4) 对于圆弧内侧起皱,应根据起皱位置采取对应措施。
若是前切点起皱,应向前调整芯棒位置,以达到弯管时对管子的合理支撑:若是后切点起皱,应加装防皱块,使防皱块安装位置正确,并将压模力调整至适当;若圆弧内侧全是皱纹,则说明所使用的芯棒直径过小,使得芯棒与管壁之间的间隙过大,或者就是压模力过小,不能使管子在弯曲过程中很好地与弯管模及防皱块贴合。
因此,应更换芯棒,并调整压紧模使压模力适当。
(5) 对于弯曲回弹现象,主要采用补偿法和校正法来加以控制。
补偿法是通过综合分析弯曲回弹的影响因素,根据弯曲时的各种条件和回弹趋势,预先估算回弹量的大小,在设计制造模具时,修正凸、凹模工作部分尺寸和几何形状,实现“过正”弯曲。
校正法是在模具结构上采取措施,使校正力集中在弯角处,改变应力状态,力图消除弹性变形,克服回弹。
如拉弯工艺,在弯曲的同时施加拉力,使整个断面都处于拉应力的作用下,卸载时弹性回复与变形方向一致,可明显减小回弹量。
弯管产品的英文对照表:预制弯管fabricated pipe bend跨越弯管cross-over bend偏置弯管 offset bend90°弯管 quarter bend环形弯管 cirele bend单侧偏置90°弯管 single offset quarter bend圆度roundness S形弯管“S”bend单侧偏置U形膨胀弯管single offset “U” bendU形弯管“U”bend双偏置U膨胀弯管 double offset expansion “U”bend斜接弯管 mitre bend三节斜接弯管 3-piece mitre bend折皱弯管corrugated bend薄壁管材的弯曲方法2009-10-24 16:02在薄壁管材的弯曲中, 经常容易在内弯壁出现起皱、弯裂、弯破等现象, 影响制件质量和外观,我们在生产实践中摸索出了一些解决的办法, 效果较好, 现介绍如下。
管材弯曲时, 若所弯圆弧半径较小一般采用弯管机, 其动轮和定轮的加工需取制件尺寸的一半, 误差应控制在一以内, 且定轮中间需加工出凸圆, 其作用是为了抵消金属在内弯处的集聚起皱及推动金属延伸, 凸圆半径取轮槽深度的一, 凸圆顶部距离凹圆弧或轮槽底部为, 结构形状如图、图所示。
若所弯管材圆弧过大或呈曲线形, 可制作简易弯形模在曲柄压力机上进行, 制模时应适当考虑回弹因素, 但在弯曲时凸模会施加给制件较大的冲压力, 也容易造成起皱、弯裂、弯破现象, 可采用细铁丝将一块左右的聚氨醋橡胶固定在凸模下, 防止上述现象发生, 其结构如图所示。
弯管工艺浅谈之一:“弯管”在生产生活中的广泛运用2010-03-05 22:17随着现代化生产系统的不断发展,“弯管”不断出现在人们的生活当中:1.各种护栏、扶手拐弯处地尖角慢慢被淘汰了,取而代之的是饱满的圆弧。
这样不仅提高了美观度,更重要的是安全性能大大提高了;2.各种管道中,不可避免地要用到各种弯管,比如船舶管道、汽车油管、机车传输系统、航空航天中的各种管路。
而圆弧弯管相对于其它类型的弯管有许多优势,首先,各种物料在圆弧弯管处流动平稳,对管壁冲击力小且均匀;其次,圆弧弯管本身应力集中小,强大高,抗冲击力大;3.随着现代钢制家具的兴起,办公椅、沙滩椅、行李车、购物车、童车、童床、电脑桌等等,几根金属管材构成几条明亮的线,实用,便利,安全,可靠;4.空调制冷管就基本都是弯管了,小U型管,回型弯等等;5.卫浴行业中的弯管现在是越来越多了,水龙头、毛巾架、S型附头。
6.摩托车、汽车、电动车、自行车等交通工具上,车把手、保险杠、车架等;7.健身器材,灯饰,建筑机械等等行业。
“弯管”产品带给了我们美观、舒适、实用、便利、安全、可靠,提高了我们的生活水平。
那么,这么多的弯管产品,都是怎样生产出来的呢?其生产工艺复杂吗?其实,各种直径、各种角度的圆弧弯管大多是用各种手动或机械弯管机加工生产出来的,当然,哪种配件用在哪个行业,作用不同,对于弯管的要求及其侧重点也不尽相同,这里就牵涉到了“弯管机”和“弯管工艺”!接下来,我们一起来分析:什么样的产品用什么样的弯管机械来加工?弯管工艺浅谈之二:弯管机械的区分及正确选型现在国内外常用的弯管机型式多样,有纯机械式、液压式、气动式、中频感应加热式等。
管材弯曲成型是直接靠特制的模具来实现的,通常按模具特征,大致可分为四类,如图1所示,其中图1a为冲模强制成形法,其代表就是用冲床来生产弯管件;其中图1b为滚轮弯曲法,常见于电动三辊卷弯机,其特点是只能卷制不同的弧形,目前运用最广泛地是不锈钢装饰行业;图1c为顶压滚动法,常见于电动平台式弯管机,目前液压弯管机械中的双弯机也是采用这种成型法;图1d为缠绕式弯曲法,目前市场上所有的单头液压弯管机及数控弯管机都是采用这种成型法,其特点就是产品变形度小,基本上可以避免管材表面的划伤,进行有芯弯曲时管材的椭圆度和减薄量都可以控制在最小的范围内。
若按采用芯棒情况,又可分为两在类,即有芯棒弯曲法和无芯棒弯曲法,液压弯管机和数控弯管机都是按缠绕式弯曲设计的,并都可以进行有芯弯曲和无芯弯曲。
进入二十一世纪,大部分企业都在想法设法用机械来代替越来越趋紧张的劳动力资源,再加上市场对于产品的要求也越来越严格,对于弯管类产品,产品的圆度,平行度,直线度以及外观和金相组织等皆要求越来越高,越来越多的企业都选择了缠绕式弯曲成型机械,即单头液压弯管机或数控弯管机械。
实际生产中,什么样的弯管机械才是最适合于自己的设备呢?其实这个问题无需问别人,就问自己的生产量就行了,量小利薄的弯管件生产想来你也不会去选择上万的设备来生产吧!反之,你就会仔细衡量是用效率高的生产设备还是用成本低但费劳力而且又担心不能按时按量生产的设备了。
由于缠绕式弯曲成型机械都是采用液压或者伺服电机来驱动,对于适合自己生产的弯管机型号的选择,这个就很简单了,因为每一款弯管机都有其最大的弯管能力,所以在购买弯管机之前,根据自己所需要弯管生产的最大管件的规格(如图2)来选择。
图2:弯管件示意图(D为管径,t为壁厚,R为弯曲半径,L为最小夹紧长度,DOB为弯曲角度)目前弯管机型号的标示有两种方式:其一,机器最大弯管件大小(比如最大弯管能力为Φ38×2.0其型号标示就是XX38XX),型号大致分为38、50、75、114;其二,按照机器的最大工艺扭矩来区分,型号大致分为25、42、63、76、89、114、127、168、219。
在实际造型过程中,应该要给机器留有余量,不能让机械满负荷生产,这其中之一的道理应该不说大家都会明白,所以在购买设备时切记为了贪图一时的小利而让机械长时间的处于满负荷生产状态,结果导致机械寿命提前结束,相比之下损失的还大得多!针对缠绕式弯曲成形法,接下来的话题就是弯管工艺系列浅谈!常见弯管缺陷的分析弯制管件被广泛应用于机械行业的多种产品中,如空调配管行业、摩托车制造行业、汽车制造业、造船业、航空航天工业、石化、卫浴洁具、五金制品、家具制造业、童车童床、休闲体育用品、运动器械、机械制造、油路管件制管、锅炉及压力容器制造行业。
但在弯管过程中由于工艺条件或操作不当等原因可能会使弯出的管件产生各种各样程度不同的缺陷,而这些缺陷的产生将直接影响到产品的安全性、可靠性以及外观质量。
如溴化锂制冷机的外部管跻,管内流动着澳化锂溶渡,该溶液对钢材有一定的腐蚀作用,如果管件有缺陷,将使管子内部不同截面的撂液流量发生变化,从而影响机组的性能,同时,溶液还会对缺陷处管壁的腐蚀加剧,降低机组的使用寿命;锅炉及压力容器由于带压运行,管件缺陷将降低其耐压强度,影响其安全性;汽车的管路如果有缺陷,在使用~段时问后会导致管路漏油漏气,从而影响汽车行驶的安全性和可靠性等。
因此,针对不同的缺陷类型找出其产生的原因从而及早采取对应的预防措施尤为重要。
一般来讲,常见弯管缺陷主要有以下几种形式:圆弧处变扁严重(椭圆形)、圆弧外侧管壁减薄量过大、圆弧外侧弯裂、圆弧内侧起皱(波浪形皱纹)等,见图1。
随着弯督半径的不同,这些缺陷产生的方式及部位有所不同,而且不一定同时发生,但由于各个行业对管件的要求不同,所以,对于要求较高的管件应在弯制之前采取对应措施加以防止,以获得理想的管件,从而保证产品的各项性能指标和外观质量。
从工艺角度分析可知,在纯弯曲的情况下,外径为D、壁厚为S的管子受外力矩M 的作用发生弯曲时,中性层外侧的管壁受拉应力ó1的作用而减薄,内侧管壁受压应力ó2的作用而增厚(见图2a)。
同时,合力F1和F2又使管子弯曲处的横截面发生变形而成为近似椭圆形(见图2b),内侧管壁在ó2的作用下可能出现失稳而起皱(见图2c)。
通常,在管子弯曲半径R≥3D 时,能获得较好的弯制管件,当弯曲半径R<2D、尤其是R/D或S/D越小时亦即弯曲半径R小、管子直径大、管壁厚度S薄时,最容易产生上述缺陷。