第十三章 膜分离过程及应用(一处)
膜分离技术标准文档ppt

渗透压:渗透过程达平衡时半透膜两侧形成的压差 。
反渗透:在浓溶液一侧加压,使膜两侧的压差大于溶液的 渗透压(p>),溶剂从溶液一侧向纯溶剂一侧液流动。
涉及气体分离、水溶液分离、生化产品的分离与纯化等操作 的食品和饮料加工过程、工业污水处理、大规模空气分离、 湿法冶金、气体和液体燃料的生产及石油化工制品的生产等
常见的膜分离过程
过程
膜
微滤
对称细孔高分子膜 孔径0.03~10 nm
超滤
非对称多孔膜 孔径1~20 nm
反渗透
非对称性或复合膜 孔径0.1~1 nm
渗析(透析
非对称离子交换膜 孔径1~10 nm
电渗析
阴、阳离子交换膜 孔径1~10 nm
气体分离
均质膜和非对称膜
渗透汽化
复合膜
液膜
液体保存在多孔膜中
主要功能
滤除 50 nm的颗粒
滤除 5~100 nm的颗 粒
水溶液中溶解盐类 的脱除
水溶液中无机酸、 盐的脱除
水溶液中酸、碱、 盐的脱除
滤除 50 nm的颗粒
第一节膜分离技术
第一节 膜分离技术
膜分离: 一般是指利用膜对流体混合物中不同组分的选择性渗透的
特点来分离流体混合物的操作过程
膜分离的应用: (1) 分散得很细的固体,特别是与液体密度相近,胶状的可 压缩的固体微粒; (2) 低分子量的不挥发的有机物、药物与溶解的盐类; (3) 对温度、酸碱度等物理化学条件特别敏感的生物物质。
素(EC)等。
聚 尼龙-6(NY-6)、尼龙-66(NY- 具亲水性能,较耐碱而不耐酸,在酮、 酰 66)、芳香聚酰胺(PI)、芳香聚酰 酚、醚及高相对分子质量醇类中,不易 胺 胺酰肼(PPP)、聚苯砜对苯二甲酰 被浸蚀,孔径型号也较多。
膜分离原理及应用
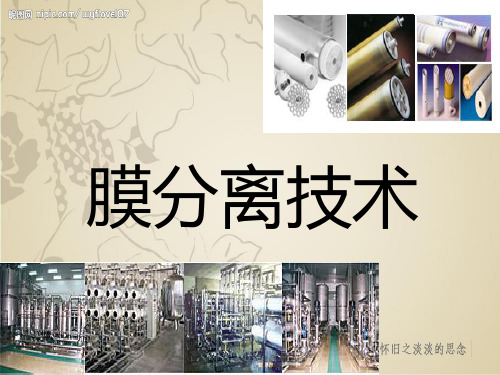
膜分离原理
在膜分离过程中,由于膜具有选择透过性, 当膜两侧存在某种推动力(如压力差、浓度 差、电位差等),原料侧组分选择性的透过 膜以达到分离提纯的目的。其传递过程极为 复杂,通过多孔型的膜有孔模型、微孔扩散 模型、优先吸附-毛细管流动模型;通过非多 孔膜的主要是溶解-扩散模型等。因而不同的 膜过程使用的膜不同,推动力不同,其传递 机理也不同。(引自:新疆大学学报——郭瑞丽,李玲著)
膜技术的应用
1) 细胞培养基的除菌; 2)发酵液或培养液中细胞的收集 和除去; 3)细胞破碎后碎片的除去; 4)目标产物部分纯化后的浓缩或 滤除小分子溶质; 5)最终产品的浓缩和洗滤除盐; 6)蛋白质的回收、浓缩和纯化 7)制备用于调制生物产品和清洗 产品容器的无热源水; 8)膜生物反应器。
膜分离技术在食品加工中的应用
膜分离技术
目录
膜分离概念
膜分离原理
膜分离技术原理 膜分离的应用 膜分离在食品工业中的应用 膜分离法 膜分离设备简介
膜分离技术是利用天然或人工制备
的具有选择透过性的膜,以外界能 量或化学单位差为推动力对双组分 的溶质和溶剂进行分离,分级,提 纯和浓缩的方法。(引自:新疆大学学报——郭瑞丽,李玲
著)
14型式优点缺点易清洗无死角适宜于处理含固体较多的料液单根管子可以调换保留体积大单位体积中所含过滤面积较小压力降大中空纤保留体积小单位体积所含过滤面积大可以逆洗操作压力较低动力消耗较低料液需要预处理单根纤维损坏时需调换整个模件螺旋卷单位体积中所含过滤面积大换新膜容易料液需预处理压力降大易污染清洗困难平板式保留体积小能量消耗界于管式和螺旋卷绕式死体积大15管式膜工业设备图
膜分离技术的特点
优点: 1)能耗低。膜分离不涉及相变,对能量要求低,与蒸馏、结 晶和蒸发相比有较大的差异; 2)分离条件温和,对于热敏感物质的分离很重要; 3)操作方便,结构紧凑、维修成本低、易于自动化。 缺点 1)膜面易发生污染,膜分离性能降低,故需采用与工艺相适 应的膜面清洗方法; 2)稳定性、耐药性、耐热性、耐溶剂能力有限,故使用范围 有限; 3)单独的膜分离技术功能有限,需与其他分离技术连用。
06-膜分离过程

6.1.2. 膜过程分类
生物分离中最常用-超滤、微滤和反渗透
膜过程分类
粒径
0. 1 1 nm 10
病毒
100
1μ m
10
100
1 mm
小分子
蛋白质
乳胶
细菌 细胞 微粒
超细胶体微粒 反渗透 微滤
超滤
一般过滤
膜分离法与物质大小(直径)的关系
6.1.3. 分离膜
(一)分离膜性能
• ★物化稳定性-膜强度、耐受压力、温度、pH、对 有机溶剂及各种化学药品的耐受性-膜寿命 ★分离透过性-选择性、渗透通量、通量衰减系数 • ①选择性-可用截留率R表示
第六章
膜分离过程
Membrane Separation
膜分离现象普遍存在,膜分离技术应用广泛
1925年以来,差不多每十年就有一项新的膜 过程在工业上得到应用 30年代 微孔过滤——人造 40年代 渗析 50年代 电渗析 60年代 反渗透(1960年Loeb和Sourirajan) 70年代 超滤 80年代 气体分离 90年代 渗透汽化 现代 EDI技术——电渗析(ED)+离子交换(IE)
膜材料
①透过速度大 ②截留盐的能力强 ③易于制备、来源丰富 ④适合作反渗透膜 ⑤不耐温(30℃) ⑥pH 范围窄,清洗困难 ⑦与氯作用,寿命降低 ⑧微生物侵袭 (1)温度范围广 (2)pH 范围广 (3)耐氯能力强 (4)孔径范围宽 (5) 操作压力低 (6)适合作超滤膜
(三)膜结构
• 对称膜,即膜截面的膜厚 方向上孔道结构或传递特 性均匀,传质阻力大,透 过通量低,容易污染,清 洗困难,微滤膜大多为对 称膜
(二)膜材料
膜材料 应用 特点 截盐能力强,使用温度 反渗透膜 醋酸纤维 和 pH 范围有限 微滤膜和超滤膜 天然高分子 再生纤维 微滤膜和透析膜
膜分离技术及其应用
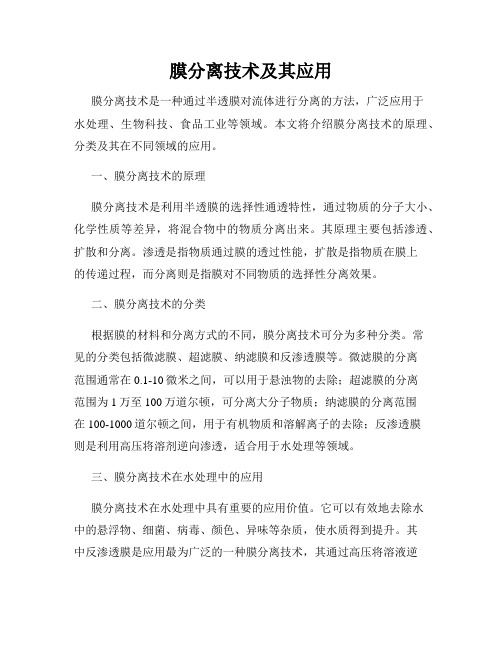
膜分离技术及其应用膜分离技术是一种通过半透膜对流体进行分离的方法,广泛应用于水处理、生物科技、食品工业等领域。
本文将介绍膜分离技术的原理、分类及其在不同领域的应用。
一、膜分离技术的原理膜分离技术是利用半透膜的选择性通透特性,通过物质的分子大小、化学性质等差异,将混合物中的物质分离出来。
其原理主要包括渗透、扩散和分离。
渗透是指物质通过膜的透过性能,扩散是指物质在膜上的传递过程,而分离则是指膜对不同物质的选择性分离效果。
二、膜分离技术的分类根据膜的材料和分离方式的不同,膜分离技术可分为多种分类。
常见的分类包括微滤膜、超滤膜、纳滤膜和反渗透膜等。
微滤膜的分离范围通常在0.1-10微米之间,可以用于悬浊物的去除;超滤膜的分离范围为1万至100万道尔顿,可分离大分子物质;纳滤膜的分离范围在100-1000道尔顿之间,用于有机物质和溶解离子的去除;反渗透膜则是利用高压将溶剂逆向渗透,适合用于水处理等领域。
三、膜分离技术在水处理中的应用膜分离技术在水处理中具有重要的应用价值。
它可以有效地去除水中的悬浮物、细菌、病毒、颜色、异味等杂质,使水质得到提升。
其中反渗透膜是应用最为广泛的一种膜分离技术,其通过高压将溶液逆向渗透,将溶质与水分离,获得高纯度的水。
反渗透膜广泛用于饮用水处理、海水淡化、工业废水处理等领域。
四、膜分离技术在生物科技中的应用膜分离技术在生物科技领域有着广泛的应用,主要包括细胞培养、蛋白质纯化、基因工程等方面。
在细胞培养中,通过膜分离技术可以实现细胞和培养基的有效分离,保护细胞的生物完整性。
在蛋白质纯化方面,膜分离技术可以实现对不同大小、电荷的蛋白质的分离和富集。
而在基因工程中,膜分离技术则可以用于DNA片段的纯化和浓缩。
五、膜分离技术在食品工业中的应用膜分离技术在食品工业中有着广泛的应用,主要包括浓缩、分离和改良等方面。
在果汁加工中,膜分离技术可以实现果汁的浓缩和去除其中的水分,提高果汁的品质和口感。
膜分离 (Membrane Separation)PPT课件
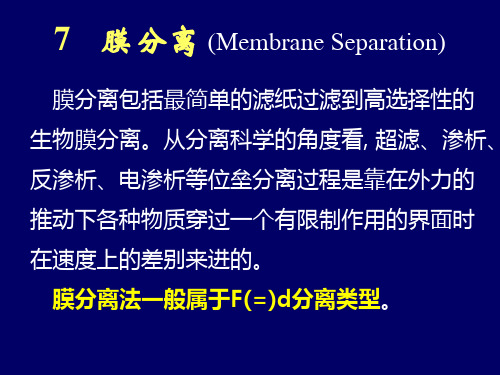
Na+ +
固定离子
Cl-
正极 阴离子交换膜 负极
高分子膜中间有足够大的孔隙,水中的离子 在膜孔隙通道(比膜厚度大得多)中电迁移运 动。例如,在水溶液中, 阴离子交换膜的活性 基团会发生离解,留下的是带正电荷的固定基 团,构成了强烈的正电场。在外加直流电场作 用下,根据异电相吸原理,溶液中带负电的阴 离子就可被它吸引、传递而通过离子交换膜到 另一侧,而带正电荷的阳离子则离子膜上固定 负电荷基团的排斥不能通过交换膜。
静压膜分离操作
1) 膜的选择性
2) 常用被分离溶质的截留率/去留率表示:
3)
R = (CF-CP)/ CF×100%
4) CF:原液浓度, CP:透过液中溶质浓度。
2) 浓度极化现象
通常沉淀溶液过滤时会出现“滤饼”现象, 使滤膜
孔洞受阻变小, 流速变慢。
对于实际过程, 膜的排除率应修正为:
(CM -CP) / (CF-CP) = exp (JV /k) JV : 膜 透 过 流 束 (cm2/cm·s) ; k : 物 质 移 动 系 数
根据溶质与流动载体之间的可逆化学反应提出了促进传递概念上世纪60年代中期bloch等采用支撑液膜研究了金属提取过程黎念之发明乳化液膜推演出了促进传递膜的新概念并导致了后来各种新型液膜的发明?湿法冶金?废水处理?核化工?气体分离?有机物分离?生物制品分离与生物医学分离?化学传感器与离子选择性电极液膜过程和萃取类似但它的萃取与反萃取分别发生在膜的两侧界面溶质从料液相萃入膜相并扩散到膜相另一侧再被反萃入接收相由此实现萃取与反萃取的内耦合
应用:
➢ 低聚糖的分离和精制 ➢ 果汁的高浓度浓缩
多肽和氨基酸的分离
离子与荷电膜之间存在道南(Donnan) 效应,即相同电荷排斥 而相反电荷吸引的作用。氨基酸和多肽在等电点时是中性的, 当高于或低于等电点时带正电荷或负电荷。由于一些纳滤膜带 有静电官能团, 基于静电相互作用, 对离子有一定的截留率, 可 用于分离氨基酸和多肽。纳滤膜对于处于等电点状态的氨基酸 和多肽等溶质的截留率几乎为零, 因为溶质是电中性的并且大 小比所用的膜孔径要小。而对于非等电点状态的氨基酸和多肽 等溶质的截留率表现出较高的截留率, 因为溶质离子与膜之间 产生静电排斥, 即Donnan 效应而被截留。
《膜分离技术》PPT课件

缓冲液
精选ppt
无机盐
34
2. 微 滤
以多孔薄膜为过滤介质,压力差为推动力,利用 筛分原理使不溶性粒子(0.1-10um)得以分离的 操作。操作压力0.05-0.5MPa。
精选ppt
35
• 微滤应用 1) 除去水/溶液中的细菌和其它微粒; 2) 除去组织液、抗菌素、血清、血浆蛋白 质等多种溶液中的菌体; 3) 除去饮料、酒类、酱油、醋等食品中的 悬浊物、微生物和异味杂质。
F
精选ppt
11
17.1 膜材料 与膜的制造
精选ppt
12
膜材料的特性
• 对于不同种类的膜都有一个基本要求:
– 耐压:膜孔径小,要保持高通量就必须施加较高的压 力,一般膜操作的压力范围在0.1~0.5MPa,反渗透 膜的压力更高,约为1~10MPa
– 耐高温:高通量带来的温度升高和清洗的需要 – 耐酸碱:防止分离过程中,以及清洗过程中的水解; – 化学相容性:保持膜的稳定性; – 生物相容性:防止生物大分子的变性; – 成本低;
孔膜,其孔隙大小在电镜的分辨范围内。
精选ppt
28
4完整性试验
• 本法用于试验膜和组件是 否完整或渗漏。
• 将超滤器保留液出口封闭, 透过液出口接上一倒置的 滴定管。自料液进口处通 入一定压力的压缩空气, 当达到稳态时,测定气泡 逸出速度,如大于规定值, 表示膜不合格。
× 保留液 出口封闭
压缩空气
• 透析过程中透析膜内无流体流动,溶质 以扩散的形式移动。
精选ppt
32
透析原理图
大分子
透析膜 小分子
水分子
精选ppt
33
透析法的应用
常用于除去蛋白或核酸样品中的盐、变性剂、还原剂之类 的小分子杂质,
膜分离技术的原理和应用
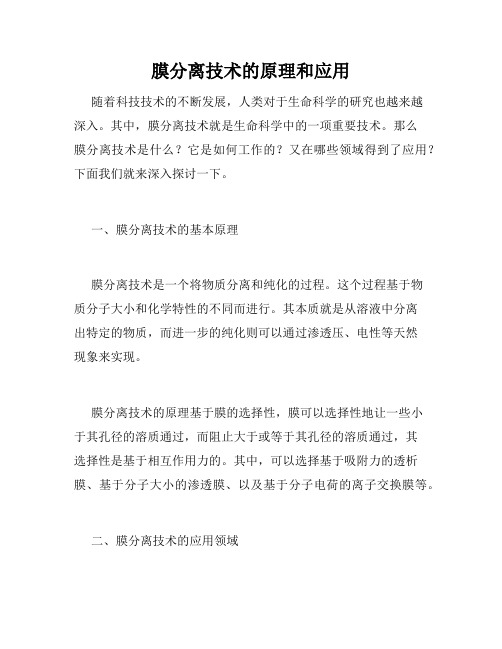
膜分离技术的原理和应用随着科技技术的不断发展,人类对于生命科学的研究也越来越深入。
其中,膜分离技术就是生命科学中的一项重要技术。
那么膜分离技术是什么?它是如何工作的?又在哪些领域得到了应用?下面我们就来深入探讨一下。
一、膜分离技术的基本原理膜分离技术是一个将物质分离和纯化的过程。
这个过程基于物质分子大小和化学特性的不同而进行。
其本质就是从溶液中分离出特定的物质,而进一步的纯化则可以通过渗透压、电性等天然现象来实现。
膜分离技术的原理基于膜的选择性,膜可以选择性地让一些小于其孔径的溶质通过,而阻止大于或等于其孔径的溶质通过,其选择性是基于相互作用力的。
其中,可以选择基于吸附力的透析膜、基于分子大小的渗透膜、以及基于分子电荷的离子交换膜等。
二、膜分离技术的应用领域膜分离技术在生命科学的很多领域得到了应用,具体应用如下:1.生物医学在生物医学领域,膜分离技术有着广泛的应用。
比如,它可以用于生物反应器的分离、酶的纯化、病原体的去除、蛋白质、激素的纯化等。
2.食品与饮料在食品和饮料领域中,膜分离技术也扮演着重要角色。
例如,它可以用于乳制品工业、饮料工业、果汁加工、酿酒业等。
3.水处理在水处理中,膜分离技术也有重要的应用。
比如,可以使用微过滤与超滤膜进行悬浮物的去除,反渗透膜和离子交换膜则可以去除水中的有害离子和重金属离子。
4.化学工业膜分离技术也可以用于化学工业。
例如,可以用于膜分离、膜萃取、膜反应、膜过滤等,可以用于分离、纯化、分子分级等。
三、膜分离技术的发展趋势目前,膜分离技术在生命科学领域中的应用越来越广泛。
未来,随着科技技术的不断进步,膜分离技术也将会得到更多的发展。
从技术角度来看,膜性能的提高是一个重要的趋势。
比如,为了摆脱基于空隙的效率限制,高分子纳米孔膜被开发出来,它们能够提供比传统低聚物和陶瓷膜更高的分离效率。
此外,疏水性、高渗透性、低粘附、抗污性等方面的改进也是开发新膜的关键。
从应用角度来看,膜分离技术的应用领域将会越来越广泛。
- 1、下载文档前请自行甄别文档内容的完整性,平台不提供额外的编辑、内容补充、找答案等附加服务。
- 2、"仅部分预览"的文档,不可在线预览部分如存在完整性等问题,可反馈申请退款(可完整预览的文档不适用该条件!)。
- 3、如文档侵犯您的权益,请联系客服反馈,我们会尽快为您处理(人工客服工作时间:9:00-18:30)。
第13章膜分离过程及工业应用13.1概述膜分离技术是利用一张特殊制造的、具有选择透过性的薄膜,在外力推动下对混合物进行分离、提纯、浓缩的一种新型分离技术。
人们对于膜现象的研究始于1748年,然而认识到膜的功能并被人们利用,却经历了200多年的漫长过程。
人们对膜进行系统的科学研究则是近几十年发展起来的,1950年朱达(W.Juda)制备出具有选择透过性的离子交换膜,奠定了电渗析实用化的基础。
1960年洛布(Loeb)和索里拉简(Sourirajan)首次研制出具有实用价值的非对称反渗透膜,这在膜分离技术发展中是一个重要的突破,使膜分离技术进入了大规模工业化应用的时代。
膜分离技术的发展历程大致为:20世纪30年代微孔过滤;40年代透析;50年代电渗析;60年代反渗透;70年代超滤和液膜;80年代气体分离;90年代渗透汽化。
此外,以膜为基础的其它新型分离过程,以及与其它分离过程结合的集成过程(Integrated Membrane Process)也日益得到重视和发展。
我国膜分离技术的发展是从1958年对离子交换膜的研究开始的,数十年来,取得了很大进步。
目前我国研究所涉及的领域遍及膜科学与技术的各个方面,从材料的应用到产品的开发等。
经过几十年的努力,我国在膜分离技术的研究开发方面已开发出一批具有实用价值、接近或达到国际先进水平的成果。
但从总体上讲,中国的膜分离技术与世界先进水平相比,还有不小的差距,有待进一步的研究发展。
膜分离作为一种新型的分离方法,与传统的分离方法如过滤、精馏、萃取、蒸发、重结晶、脱色、吸附等相比,具有能耗低、单级分离效率高、设备简单、无相变、无污染等优点。
因此,膜分离技术广泛应用于化工、食品、医药医疗、生物、石油、电子、饮用水制备、三废处理等领域,并对当今社会的工业技术改造产生了深远的影响。
膜分离技术被认为是“21世纪最有前途、最有发展前景的重大高新技术之一,在工业技术改造中起着战略性作用”。
许多国家都把膜分离技术及其应用列为国家重点发展项目。
13.1.1膜的分类及其制备方法膜定义为两相之间的一个不连续区间,并以特定的形式限制和传递各种化学物质。
膜具备下述两个特征:①有两个界面,通过这两个界面分别与两侧的流体相接触;②具有选择透过性。
13.1.1.1膜的分类由于膜的种类和功能繁多,分类方法有多种,比较通用的有4种方法,即按膜的结构、膜的化学组成、膜的用途以及膜的作用机理分类。
(1)按膜的结构分类膜的形态结构决定了分离机理,也决定了其应用按结构不同可分为固膜和液膜。
固膜又分为对称膜(柱状孔膜、多孔膜、均质膜)和不对称膜(多孔膜、具有皮层的多孔膜、复合膜);液膜又分为存在于固体多孔支撑层中的液膜和以乳液形式存在的液膜。
(2)按膜的化学组成分类不同的膜材料具有不同的化学稳定性、热稳定性、机械性能和亲和性能。
目前已有数十种材料用于制备分离膜,分别为有机材料的纤维素类、聚酰胺类、芳香杂环类、聚砜类、聚烯烃类、硅橡胶类等;无机材料的陶瓷(氧化铝、氧化硅、氧化锆等)、硼酸盐玻璃、金属(铝、钯、银等);天然物质改性或再生而制成的天然膜。
(3)按膜的用途分类按膜的用途可分为气相系统用膜、气-液系统用膜、液-液系统用膜、气-固系统用膜、液-固系统用膜、固-固系统用膜。
(4)按膜的作用机理分类有吸附性膜(多孔膜、反应膜)、扩散性膜(高聚物膜、金属膜、玻璃膜)、离子交换膜、选择渗透膜(渗透膜、反渗透膜、电渗析膜)、非选择性膜(加热处理的微孔玻璃、过滤型的微孔膜)。
13.1.1.2膜的制备方法13.1.2膜分离过程及其特点工业应用中常用的膜分离技术有电渗析(ED)、反渗透(RO)、微滤(MF)、超滤(UF)、纳滤(NF)、渗透汽化(PV)、蒸汽渗透(VP)、膜蒸馏(MD)、渗透蒸馏(OD)等。
膜分离与传统的分离技术(蒸馏、吸收、萃取、深冷分离等)相比,具有以下特点:①不发生相变化,是一种节能技术;②是在压力驱动下,在常温下进行的分离过程,特别适合对热敏性物质,如酶、果汁、某些药品的分离浓缩、精制等;③是一种高效的分离过程,其适用范围极广,从微粒级到微生物菌体,甚至离子级等,其关键在于选择不同的膜类型;④设备本身没有运动部件,很少需要维护,可靠度很高,操作十分简单;⑤装置简单、分离效率高,可以直接插入已有的生产工艺流程,不需要对生产线进行大的改变。
13.1.3膜组件任何一个膜分离过程,不仅需要具有良好分离特性的膜,还需要结构合理、性能稳定的膜分离装置。
膜分离装置的核心是膜组件,它是将膜、固定膜的支撑材料、间隔物或管式外壳等,通过一定的粘合或组装构成一个单元。
膜组件可以有多种型式,工业上应用的膜组件主要有板框式、卷式、管式、中空纤维式四种型式,它们均根据膜形状设计而成。
板框式、卷式膜组件均使用平板式,板框式等动态或静态装置。
管式和中空纤维膜组件均使用管式膜,它们可以分为内压式和外压式两种。
对于不同目的的膜分离过程,可采用不同型式的组件及装置。
性能良好的膜组件应达到的要求:①对膜能提供足够的机械支撑并可使高压原料液(气)和低压透过液(气)严格分开;②在能耗最小的条件下,使原料液(气)在膜面上的流动状态均匀合理,以减少浓差极化;③具有尽可能高的装填密度,即单位体积的膜组件中填充较多的有效膜面积,并使膜的安装和更换方便;④装置牢固、安全可靠、价格低廉和容易维护。
13.1.3.1板框式膜组件板框式膜组件是最早使用的一种膜组件,其设计类似于常规的板框过滤装置。
其基本部件有平板膜、支撑盘、间隔盘三种,三种部件相互交替、重叠、压紧,构成板框式叠放结构。
两张膜为一组构成夹层结构,两张膜的原料侧相对,由此构成原料腔室和渗透物腔室。
在原料腔室和渗透腔室中安装适当的间隔器,采用密封环和两个端板将一系列这样的单元安装在一起满足对膜面积的要求,于是构成板框式叠放结构。
板框式膜组件的组装比较简单,可以简单地增加膜的层数以提高处理量,同一设备可视生产需要而组装不同数量的膜。
膜的清洗更换比较容易,料液流通截面较大,不易堵塞,并且操作比较方便;缺点是板框式膜组件组装零件太多,装填密度低,设备笨重,对膜的机械强度要求较高,非生产的辅助时间长,阻碍了过滤效率的提高。
13.1.3.2螺旋卷式膜组件螺旋卷式膜分离装置的基本部件有:耐压套管、膜组件、穿孔管等,其主要元件是螺旋卷膜组件,它是将膜、支撑材料、膜间隔材料依次迭好,围绕一中心管卷紧即成一个膜组,若干膜组顺次连接装入外壳内。
当需要增加膜组件的面积时,可以将多个膜袋同时卷在中心管上,这样形成的单元可多个串联于同一个压力容器中。
螺旋卷式的优点是结构紧凑、装填密度高,制作简单,安装操作方便,膜面积大,湍流状况好,换膜容易,适合低流速、低压下操作,适用于反渗透;缺点是流体阻力大,制作工艺复杂,清洗困难。
13.1.3.3管式膜组件管式膜分离装置的基本部件有管状膜、圆筒形支撑体、管束板、不锈钢外壳、端部密封等。
管的流动方式又有单管及管束,液流的流动方式有管内流和管外流式。
由于单管式和管外流式的湍动性能较差,目前主要采用管内流管束式装置,其外形类似于列管式换热器。
管式膜组件有外压式和内压式两种。
对内压式膜组件,膜被直接浇铸在多孔纸上,然后外面再用管子来支撑。
对内压式膜组件,加压的料液流从管内流过,透过膜所得的渗透溶液在管外侧被收集。
对外压式膜组件,膜则被浇铸在多孔支撑管外侧面,加压的料液流从管外侧流过,渗透溶液则由管外侧渗透通过膜进入多孔支撑管内,无论是内压式还是外压式,都可以根据需要设计成串联或并联。
管式膜分离装置结构简单,适应性强,装填密度较小,单位体积内有效膜面积小,清洗安装方便,单根管子可以更换,耐高压,无死角,适用于处理高粘度及固体含量较高的料液;不足之处是体积大,压力降大,单位体积所含的过滤面积小。
13.1.3.4中空纤维膜组件中空纤维膜组件是装填密度最高的一种膜组件型式,其单位体积的膜面积大,中空纤维膜的内径通常在40~100μm,外径80~400μm。
将大量的中空纤维一端封死,另一端用环氧树脂将许多中空纤维的两端胶合在一起,形似管板,然后装入圆筒形压力容器中,就构成了中空纤维膜组件。
中空纤维膜组件在结构上是非对称的,其抗压强度靠膜自身的非对称结构支撑,故可承受6MPa的静压力而不致压实。
中空纤维膜组件具有装填密度大、结构简单、操作方便等特点,其单位体积内提供的膜面积大,液流流程短,分布均匀,且可反向清洗,可用双氧水、次氯酸钠、氢氧化钠等水溶液灭菌消毒。
并且中空纤维膜组件必须在湿态下使用和保存。
缺点是单根纤维管损坏时需要更换整个膜组件,并且清洗困难,液体在管内流动时阻力很大,易堵塞,若用于处理含有悬浮物的废水,必须预先经过过滤处理,另外损坏的膜难以发现,维护管理不便。
13.1.4膜性能的表示方法膜的性能包括物化稳定性和膜的分离透过性两个方面。
膜的物化稳定性指膜的强度、允许使用压力、温度、pH 值以及对有机溶剂和各种化学药品的抵抗性,它是决定膜寿命的主要因素。
膜的分离特性主要包括分离效率、渗透通量和通量衰减系数三个方面。
13.1.4.1分离效率对于不同的膜分离过程和分离对象可以有不同的表示方法。
在超滤、纳滤等过程中,其分离的目的是去除溶液中的微粒、盐类等,使用脱除率或截留率R 表示分离程度%1001⨯⎥⎦⎤⎢⎣⎡-=m p c c R (13-1)式中,c m ,c p 分别为高压侧膜表面处溶液的浓度和膜的透过液浓度。
而通常实际测定的是溶质的表观分离率,定义为%1001⨯⎥⎦⎤⎢⎣⎡-=b p obs c c R (13-2)式中 c b —高压侧主体溶液浓度,c b 和c m 的差别取决于浓差极化的程度。
对于由两个或多个组分构成的混合物的膜分离过程,其分离程度采用通用的表示方法,即使用分离系数(分离因子)α或βA A A A x x y y --=11α (13-3)A A x y =β (13-4)式中x A 、x B 表示原料液(气)与透过液(气)中组分A 的摩尔分数。
13.1.4.2渗透通量单位时间内通过单位膜面积的透过物量用J 表示St V J =(13-5)式中 V —透过液的容积或质量;S —膜的有效面积;t —运转时间。
13.1.4.3通量衰减系数膜的渗透通量由于过程的浓差极化、膜的压密以及膜堵塞等原因将随时间而衰减,可用下式表示mt t J J 1 (13-6)式中 J t ,J 1—膜运转th 和1h 后的渗透通量;m —通量衰减系数,将式两边取对数,得到线性方程,再对对数坐标系上画直线,其直线斜率即为m 。
对于任意一种膜分离过程,总是希望分离效率高,渗透通量大;而实际情况是,渗透通量大的膜,分离效率低,而分离效率高的膜渗透通量小。