冲压的材料材料特性(精)
冲压

第一章冲压冲压的定义:室温下,在压力机上通过模具对板料金属(非金属)加压,使之产生塑性变形或分离,从而获得一定尺寸、形状和性能的工件的加工方法,又叫冷冲压或板料冲压。
冲压工艺可用于加工,金属板料,非金属板料.冲压工艺特点:生产效率高;在大量生产中可获得稳定的质量;材料利用率高,生产成本低;可制造复杂形状的工件。
冲压生产的局限性:--制模成本高;--技术要求高;--不适用于单件、小批量生产。
加工硬化:在常温下,随着变形程度的增加,金属材料的强度指标增高,塑性指标降低的现象。
冲压分类:分离工序,成型工序分离工序:冲压过程中,使冲压件与板料在切应力或拉应力的作用下,沿一定的轮廓线相互分离。
分离工序主要指冲裁,包括落料、冲孔、切断、切边、剖切等工序。
普通冲裁:通过破坏分离方式所完成的冲压工序。
精密冲裁:以变形分离方式所完成的冲压工序。
成形工序:在冲压过程中,使毛坯在不破坏的条件下发生塑性变形,成为所需形状与尺寸的工件,同时冲压件应该满足尺寸精度方面的要求。
成形工序主要包括弯曲、拉伸、胀形、翻边等。
落料:用模具沿封闭轮廓线冲切,冲下部分是零件。
用于制造各种平板零件或者成形工序制坯冲孔:用模具沿封闭轮廓线冲切,冲下部分是废料。
用于冲制各类零件的孔形弯曲;把板料沿直线弯曲成各种形状,板料外层受拉伸力,内层受压缩力。
可加工形状复杂的零件毛坯区域的划分:变形区,传力区在成形过程中,毛坯的变形区和传力区是运动变化的,而且还会相互转化。
制定工艺时,必须保证:“弱区先变形,变形区应为弱区”对毛坯变形趋向性的控制,主要有以下几种方法:(1)合理确定毛坯和半成品尺寸(2)改变模具工作部分的几何形状和尺寸(3)改变毛坯与模具接触面之间的摩擦阻力(4)改变毛坯局部力学性能1、什么是冲压?它与其它加工方法相比有什么特点?2、冲压工序可分为哪两大类?他们的主要区别和特点是什么?3、如何控制冲压过程中的变形趋向?板料的冲压性能:指板料对冲压的适应能力、可成形能力间接试验:板料的受力情况和变形特点与实际冲压有一定差别,其试验结果只能间接反映板料的冲压性能。
铝合金冲压拉伸

铝合金冲压拉伸铝合金是一种具有优异力学性能、良好腐蚀性能和优异加工性能的材料,因此被广泛应用于冲压拉伸加工领域。
铝合金冲压拉伸工艺是通过对铝合金板材进行加工,使其产生形状和尺寸发生变化,达到零件成形的工艺。
铝合金冲压拉伸工艺在制造业中具有广泛的应用。
它适用于生产各种形状的零件,如汽车车身板件、飞机翼板、电子产品外壳等。
铝合金冲压拉伸工艺可以实现高效、精确和批量化生产,能够满足不同行业对零件质量和生产效率的要求。
在铝合金冲压拉伸过程中,需要考虑一系列的加工参数和工艺控制,以保证零件的成形质量和工艺效率。
以下是一些铝合金冲压拉伸相关的参考内容:1. 材料特性:- 铝合金的特性:铝合金具有良好的延展性和韧性,适合进行冲压拉伸加工。
- 材料屈服强度和延伸率:了解材料的力学性能参数,可以选择合适的拉伸方式和应变速率。
2. 设计与模具:- 零件设计:设计合理的零件几何形状、薄壁结构和布局,减少局部应力集中。
- 模具设计:确定合适的冲孔、冲剪、拉伸和压边工艺步骤,设计合适的变形区域和支撑结构。
3. 工艺参数:- 冲裁力矩:考虑材料的屈服强度、弹性模量和板材厚度,确定合适的冲裁力矩。
- 润滑剂选择:选择合适的润滑剂,减少摩擦力和热量的产生,减轻工艺过程中的摩擦损伤。
- 模具温度:控制模具的温度,以控制材料的流动和变形,避免塑性变形过大。
- 拉伸速度:根据材料的特性和零件要求,选择合适的拉伸速度,以保证良好的成形效果和表面质量。
4. 工艺控制:- 力学性能监测:通过力学性能测试,了解材料的抗拉强度、屈服强度、延伸率等指标,为工艺控制提供数据支持。
- 成形质量检测:采用三坐标测量等技术,对成形零件的尺寸和形状进行检测和修正,确保成形质量满足要求。
5. 工艺优化:- 板材切割:根据零件的几何形状和材料特性,合理选择切割方式和切割尺寸,减少材料浪费和成本。
- 工艺参数调试:通过实验和模拟分析,对工艺参数进行调整,优化冲压拉伸工艺,提高生产效率和零件质量。
板料冲压

(6) 修整 是利用修整模沿冲裁件外缘或内孔刮削一薄层 金属,去掉剪裂带和毛刺,提高冲裁件的尺寸精度 和表面精度。
2. 变形工序
—— 是使坯料的一部分相对于另一部分产生
位移而不破坏的工序。
如:拉深,弯曲,翻边,胀形等。
(1) 弯曲 ——是将坯料的一部分相对于另一部分弯曲成 一定角度的冲压加工方法。被弯材料可是板料、型 材或管料。
可采用加强筋措施 以薄材代替厚材。
3. 冲压件的精度和表面质量
在满足需要的前提下,尽量降低精度要求,而且 一般不要超过原材料的表面质量。
4.
简化工艺、节约材料
(1) 采用冲—焊结构
用于复杂冲压件,可分别冲 压成几个简单件,然后焊接 成整体,简化工艺
(2) 采用冲口工艺 ——可以减少组合件数量
(3)在不改变使用性能的前提下,简化拉深件结构, 可减少工序并节约材料。
落料和冲孔的区别在于: 落料:冲落部分为成品,周边是废料; 冲孔:是为了获得带孔的冲裁件,冲落部分为 废料。
(1) 冲裁分离过程
冲裁时板料的变形和分离过程对冲裁件质量有 很大的影响。其过程可分为三个阶段。
弹性变形阶段→塑性变形阶段→断裂分离阶段
冲裁出的工件断面分为四个特征区,分别为圆 角带(塌角)、光亮带、剪裂带和毛刺。
板厚越大,m取 值应越大。
设计落料模时,取凹模作为设计基准,然后根 据间隙确定凸模尺寸。设计冲孔模时,取凸模作为 设计基准,然后根据间隙确定凹模尺寸。
(3) 凸凹模刃口尺寸的确定
落料件尺寸会随凹模刃口磨损而增大,因此,加
工凹模刃口时取落料件公差范围的最小尺寸;
冲孔件尺寸会随凸模刃口磨损而减小,因此,加
压边圈——防止工件起皱 压边力不能太 大,一般为 2~3MPa。
冲压基础知识
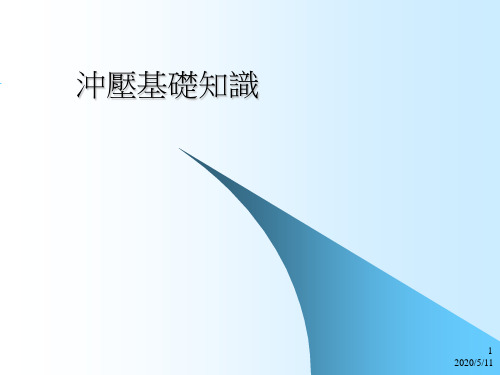
不锈钢钢板
钢铁材料之铬 (Cr)元素含量与其腐蚀率呈反比关系,当铬含量达 11~12%以上时,此效果尤其显著.所谓不锈钢,一般上是指含铬量达 11%以上之高合金钢,其主要特徵是耐腐蚀性及耐热性非常优越,具有 不锈性及表面光辉性.冲压加工用的不锈钢板种类依制造方式可分 为:热压不锈钢板及冷压不锈钢板.依金相组织之分类有: a. 麻田散铁系:不锈钢之铬含量约11.5~14.0%,含碳量一般小 於0.15%,SUS410(13% Cr)为此系列材料之代表.有SUS410S,SUS420 等 b. 肥粒铁系:不锈钢之铬含量约18%,含碳量一般小於0.12%, SUS430(18%Cr)为此系列材料之代表.有SUS434,SUS429,SUS405等. c. 沃斯田铁系:不锈钢之铬含量约17%,含碳量一般小於 0.15%,SUS304(18Cr-8Ni)是此系列代表.有SUS201,SUS202, SUS301,SUS302等.
11 2010/5/10
12 2010/5/10
冲压模具组成
模具组成的零件:一般冲模零件可分为两大类: 1. 工作用零件:加工中与料条有接触,而且有直接作用 的零件,依作用方式可分为三种. a. 工作零件:达成加工要求的零件,如冲模及下模等 b. 定位导料零件:Z在工程进行中,使工件料条正确导 引,定位的零件,如先导杆 (pilot),料宽导料板 (front spacer). c. 压料及退料零件:如脱料板 (stripper plate)等.
22 2010/5/10
铜合金的种类
a. 铜锌合金-黄铜 (BRASS):比较有代表性的是7-3黄铜 (含锌量 25%~35%).JIS规格C2600~C2680系列. b. 铜鍚合金-青铜 (BRONZE):比较有代表性的是含磷的磷青铜,其耐 蚀性,耐疲劳性,耐磨耗性均佳,而弹性为最主要的特点.磷青铜的 规格依含鍚量可分为: JIS 规格:C5101系列 (含鍚量 3~5.5%) C 5191系列 (含鍚量 5.5~7.0%) C 5210系列 (含鍚量 7~9%) c. 热处理铜合金:具热处理性,比较有代表性的是铍铜,具耐蚀性佳 於时效硬化处理前,富於展性,且於时效硬化处后,却增加耐疲劳性 导电性.
冲压件

表 3(材料厚度 t)
材料 纸胶板、布胶 板 软铝
t ≤1 t>1~2 t>2~3 0.03t ~ 0.04t~0.06t 0.05t 0.04t ~ 0.05t ~ 0.06t ~ 0.06t 0.07t 0.08t 铜,软黄铜,硅 0.05t ~ 0.06t ~ 0.07t ~ 钢 片 , 软 钢 0.07t 0.08t 0.09t (0.08 ~ 0.20%C) 硬铝,硬黄铜, 0.06t ~ 0.07t ~ 0.08t ~ 硬青铜 0.08t 0.09t 0.10t 中硬钢(0.3~ 0.4%C) 硬 钢 (0.5 ~ 0.07t ~ 0.0t8 ~ 0.09t ~ 0.7%C) 0.09t 0.10t 0.10t
常用冲压件非金属材料机械性能见表
材料名称 纸胶板 布胶板 石棉板 橡皮 有机玻璃、聚氯乙烯
抗弯强度г (MPa) 用管状凸模裁切时 用普通凸模冲裁时 100~130 140~200 90~100 120~180 40~50 ----1~6 20~80 70~80 100~130
三、冲压件的设计
• 冲压件应按经规定程序批准的图纸及相 关技术文件制造、验收,并应符合国家、 行业的相关标准,以及本标准的规定。 冲压件材料应具有良好的冲压性能,选用 屈强比(б s/б b)小、弹性模数(E)大、塑性 指数高、厚向异性指数大、板平面内各 向异性指数小的材料有利于冲压的各种 塑性变形。
(一)冲裁件设计的工艺性:
• 1、 冲裁件形状尽可能设计成简单、对称,使排样时废料最少。 • 2、 冲裁件的外形或内孔应避免减角在各直线或曲线连接初宜有 适当圆角其半径最小的R值见附表1。 • 3、 冲裁件突出旋臂和凹槽的最小宽度对于普通软钢取1.2t ;硬 钢为2.0t以上。 • 4、 冲孔时,孔径不宜过小,其最小孔径与孔的形状、材料的机 械性能、厚度有关,见附表2。冲裁件最小孔边距为2t以上,并不小 于3-4mm。 5、 在拉深或弯曲件上冲孔时,其孔壁与工件直壁应保持一定 距离,孔不能在变形区内。
冲压基础知识

不銹鋼鋼板
鋼鐵材料之鉻 (Cr)元素含量與其腐蝕率呈反比關係,當鉻含量達 11~12%以上時,此效果尤其顯著。所謂不銹鋼,一般上是指含鉻量達 11%以上之高合金鋼,其主要特徵是耐腐蝕性及耐熱性非常優越,具有 不銹性及表面光輝性。沖壓加工用的不銹鋼板種類依製造方式可分 為:熱壓不銹鋼板及冷壓不銹鋼板。依金相組織之分類有: a. 麻田散鐵系:不銹鋼之鉻含量約11.5~14.0%,含碳量一般小 於0.15%,SUS410(13% Cr)為此系列材料之代表。有SUS410S、SUS420 等 b. 肥粒鐵系:不銹鋼之鉻含量約18%,含碳量一般小於0.12%, SUS430(18%Cr)為此系列材料之代表。有SUS434、SUS429、SUS405等。 c. 沃斯田鐵系:不銹鋼之鉻含量約17%,含碳量一般小於 0.15%,SUS304(18Cr-8Ni)是此系列代表。有SUS201、SUS202、 SUS301、SUS302等。
2011/3/7
16
磨床介紹
磨床:有平面磨床、圓筒磨床、內圓磨床、萬能磨 床、成型磨床等 a. 平面磨床:除可用於模具加工之外,亦可用於 下料沖模刄尖之再研磨,是模具保養不可或缺的工 作機械。 b. 成形磨床:成形磨床之種類很多,目前較常用 的有光學投影輪廓磨床(Optical Profile Grinder),其操作是將正確繪出之放大圖安放在銀 幕上,然後操作把手,按照擴大圖之形狀來研磨工 作物,而隨著電腦及數值控制(Numerical Control)的進步目前巳漸發展成CNC控制機械。
2011/3/7
註:CNC光學研磨其加工最小內R為0.05mm
17
電氣加工
a. 放電加工(EDM):放電加工之技術,在三十年前由蘇俄之 拉薩連科夫婦開發成功。放電加工和機械的切削加工或研磨 加工不同,它是使加工電極和工件間發生放電,而由於其熱 和爆發的火花使工件之表面發生電氣腐蝕來進行加工 b. 金屬線切割(WEDM):金屬線切割是以約0.2mm左右的細銅 或銅合金的金屬線替代一般的放電加電之電極,而以它和工 件間的放電,並利用NC裝置來控制加工,而得任意形狀的工 件。 註:線切割加工方線取決於線徑,目前最小徑為φ0.1mm, 因此其加工最小內R角為0.07以上,一般定為0.1mm
cae冲压材料参数说明

CAE冲压材料参数说明1. 引言CAE(Computer-Aided Engineering)是一种利用计算机辅助进行工程设计和分析的技术。
在冲压工艺中,CAE可以帮助工程师预测和优化材料参数,以提高产品质量和生产效率。
本文将详细说明CAE冲压材料参数的相关内容。
2. 冲压过程中的材料参数在冲压过程中,材料的物理性质和力学性能对产品的成形性能和质量起着重要作用。
以下是一些常见的冲压材料参数:2.1 材料硬度(Hardness)材料硬度是指材料抵抗局部塑性变形、划痕或穿孔等表面破坏的能力。
常用的硬度测试方法有布氏硬度、洛氏硬度等。
在CAE分析中,硬度值可以用来确定材料的变形行为和应力分布。
2.2 材料应力-应变曲线(Stress-Strain Curve)材料应力-应变曲线描述了在给定应变范围内材料的应力响应。
该曲线可以通过实验测试或经验模型获得。
在CAE分析中,应力-应变曲线用来确定材料的强度、延展性和硬化行为。
2.3 材料流变应力曲线(Flow Stress Curve)材料流变应力曲线描述了在不同应变率下材料的流动性能。
该曲线可以通过实验测试或经验模型获得。
在CAE分析中,流变应力曲线用来确定材料的流动行为和冲压过程中的应力分布。
2.4 材料摩擦系数(Friction Coefficient)材料摩擦系数是指两个接触表面之间相对滑动时所产生的摩擦阻力与垂直于接触面的压力之比。
摩擦系数对冲压过程中的摩擦力和表面质量有重要影响。
在CAE分析中,摩擦系数可以通过实验测试或经验模型获得。
2.5 材料热物性(Thermal Properties)材料热物性包括热导率、比热容和线膨胀系数等。
这些参数对冲压过程中的温度分布和冷却效果起着重要作用。
在CAE分析中,热物性参数可以用来模拟冲压过程中的热传导和热变形。
3. CAE分析中的材料参数获取为了进行CAE分析,需要获取材料参数的数值。
以下是一些常见的获取方法:3.1 实验测试实验测试是获得材料参数最直接和准确的方法之一。
板料冲压成形性能及冲压材料
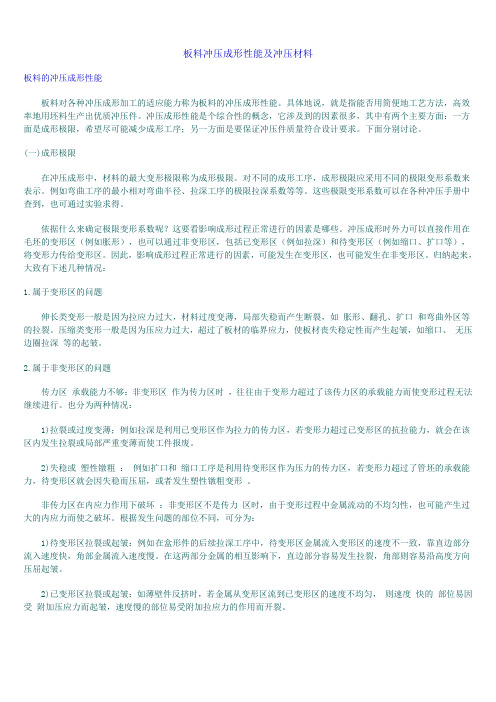
板料冲压成形性能及冲压材料板料的冲压成形性能板料对各种冲压成形加工的适应能力称为板料的冲压成形性能。
具体地说,就是指能否用简便地工艺方法,高效率地用坯料生产出优质冲压件。
冲压成形性能是个综合性的概念,它涉及到的因素很多,其中有两个主要方面:一方面是成形极限,希望尽可能减少成形工序;另一方面是要保证冲压件质量符合设计要求。
下面分别讨论。
(一)成形极限在冲压成形中,材料的最大变形极限称为成形极限。
对不同的成形工序,成形极限应采用不同的极限变形系数来表示。
例如弯曲工序的最小相对弯曲半径、拉深工序的极限拉深系数等等。
这些极限变形系数可以在各种冲压手册中查到,也可通过实验求得。
依据什么来确定极限变形系数呢?这要看影响成形过程正常进行的因素是哪些。
冲压成形时外力可以直接作用在毛坯的变形区(例如胀形),也可以通过非变形区,包括已变形区(例如拉深)和待变形区(例如缩口、扩口等),将变形力传给变形区。
因此,影响成形过程正常进行的因素,可能发生在变形区,也可能发生在非变形区。
归纳起来,大致有下述几种情况:1.属于变形区的问题伸长类变形一般是因为拉应力过大,材料过度变薄,局部失稳而产生断裂,如胀形、翻孔、扩口和弯曲外区等的拉裂。
压缩类变形一般是因为压应力过大,超过了板材的临界应力,使板材丧失稳定性而产生起皱,如缩口、无压边圈拉深等的起皱。
2.属于非变形区的问题传力区承载能力不够:非变形区作为传力区时,往往由于变形力超过了该传力区的承载能力而使变形过程无法继续进行。
也分为两种情况:1)拉裂或过度变薄;例如拉深是利用已变形区作为拉力的传力区,若变形力超过已变形区的抗拉能力,就会在该区内发生拉裂或局部严重变薄而使工件报废。
2)失稳或塑性镦粗:例如扩口和缩口工序是利用待变形区作为压力的传力区,若变形力超过了管坯的承载能力,待变形区就会因失稳而压屈,或者发生塑性镦粗变形。
非传力区在内应力作用下破坏:非变形区不是传力区时,由于变形过程中金属流动的不均匀性,也可能产生过大的内应力而使之破坏。
- 1、下载文档前请自行甄别文档内容的完整性,平台不提供额外的编辑、内容补充、找答案等附加服务。
- 2、"仅部分预览"的文档,不可在线预览部分如存在完整性等问题,可反馈申请退款(可完整预览的文档不适用该条件!)。
- 3、如文档侵犯您的权益,请联系客服反馈,我们会尽快为您处理(人工客服工作时间:9:00-18:30)。
冲压的材料材料特性
一、冲裁时材料分离过程可分为三个阶段:
1、弹性变形阶段:冲头刚接触板料的初始阶段,发生弹性变形。
2、塑料变形阶段:冲头下行压力增大,发生塑变直到出现微裂纹。
3、断裂分离阶段:冲头继续下行,压力增大,微裂纹扩展。
重合、断裂、冲裁力逐渐下降。
弹性变形阶段:冲裁力逐渐升高。
塑性变形阶段:冲裁力达到峰值。
二、普通冲裁件的断面特征:
1、塌角带由主单性变形阶段产生初始塌角,带动边塑性变形阶段。
2、光亮带产生于塑性变形阶段,断面较光洁平整,是质量最佳的一段。
3、断裂带撕裂造成的,表面粗糙而无光泽,并带有锥度。
4、毛刺区产生微裂时便产生毛刺。
三、特征与材料(板料材料)塑性的关系:
断面质量受冲裁条件的不同而不同,如:刃口间隙,刃口形状,锋利程度,冲裁力、润滑条件,板料质量(表面质量),板料种类(性能)。
冲压生产要求冲裁件有较大的光亮带,尺量减少断裂带区域的宽度。
材料塑性愈好,光亮带愈大,断裂带愈小,同时,圆角毛刺亦增大。